Конвейер горизонтально-замкнутый для сборки КПП




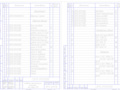
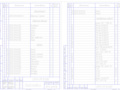
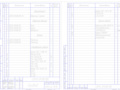
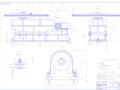
- Добавлен: 25.10.2022
- Размер: 3 MB
- Закачек: 1
Описание
Состав проекта
![]() |
![]() |
![]() ![]() ![]() |
![]() |
![]() ![]() ![]() ![]() |
![]() ![]() ![]() ![]() |
![]() ![]() |
![]() ![]() |
![]() ![]() ![]() ![]() |
![]() |
![]() |
![]() ![]() ![]() ![]() |
![]() ![]() ![]() |
![]() ![]() |
![]() ![]() |
![]() ![]() ![]() ![]() |
![]() ![]() |
![]() |
![]() ![]() |
![]() ![]() ![]() ![]() |
![]() |
Дополнительная информация
Реферат.doc
В дипломном проекте представлена конструкция сборочного грузоведущего тележечного конвейера для сборки коробок передач тракторов МТЗ.
Цель проекта – разработка конструкции грузоведущего тележечного конвейера для сборки коробок передач всех моделей тракторов МТЗ.
В процессе работы проведен анализ существующих конструкций грузоведущих тележеных конвейеров.
Дано техническое обоснование использование данного решения и дано экономическое обоснование применимой конструктивной схемы конвейера.
Произведены технические расчеты и разработаны чертежи сборочных единиц конвейера.
Разработаны мероприятия по охране труда.
Экономические расчеты показали что экономический эффект при внедрении данного конструктивного варианта составляет 15 млн. бел. руб.
Спецификация - привод.dwg

Общий вид СБ.dwg

Тип конвейера - приводной горизонтально-замкнутый.
Режим работы конвейера:
1. Рабочий - непрерывный с позиционной остановкой от
механизма позиционной остановки.
2. Наладочный - непрерывный с остановкой от кнопок
3. Рабочий - непрерывный с плавным регулированием
Шаг позиций конвейера
Плавно регулируемая
1 . Электродвигатель
с частотным преобразователем
2. Редуктор КДВ-350М2-III
Передаточное число 1382.
3. Предохранительное устройство привода - срезной
палец на приводной звездочке
Максимальный крутящий момент
Тяговое усилие на приводном
Технические требования.
выполнить по контуру прилегания свариваемых деталей.
Точность СК: Р3 ГОСТ 30021-93.
*Размеры для справок.
**Размеры для контроля.
Общие допуски по ГОСТ 30893.1-2002: ±IT142.
Монтаж металлоконструкции средней частиконвейера
производить после монтажа станции приводной.
Конвейер после полной сборки прокрутить в холостом
режиме в течение суток
затем под нагрузкой в течение
при этом проверить правильность и
качество сборки конвейера.
Особое внимание обратить на прохождение секций цепи
по радиусным направляющим станций приводной и натяжной.
Выявленные недостатки устранить
разрешается работа конвейера.
Во время прокручивания конвейера смазать шарниры секций
цепи по всей длине жидкой смазкой.
На перекрытие станции приводной
станции поворотной нанести сигнальную разметку
запрещающую размещение на перекрытиях посторонних предметов
Окончательную установку механизма позиционной остановки
произвести после опробования работы механизма в составе
1. Поверхности без лакокрасочного покрытия подготовить к
окраске согласно ГОСТ 9.401-91; ГОСТ 9.402-2004; ГОСТ 22133-86.
Покрытие: Грунтовка ГФ-021 ГОСТ 25129-82
Эмаль ПФ-115 ГОСТ 6465-76.IV.УХЛ2
Ролики секции от покрытия предохранить.
Коэффициент условий производства работ по РСН 8.01.104-2007
приложение Г и п.3.1.
Конвейер горизонтально-
Спецификация - подставка.dwg

привод СБ.dwg

*Размеры для справок.
Допуск соосности вала электродвигателя поз. 17 и входного вала
редуктора поз. 15 - 0
Все резьбовые поверхности покрыть тонким слоем солидола марки
После сборки привод обкатать без нагрузки.
Техническая характеристика
Технические требования
ПЗ.doc
ИСТОЧНИКОВ ПО ТЕМЕ ДИПЛОМНОГО ПРОЕКТА 10
РАСЧЕТ МОЩНОСТИ ПРИВОДА КОНВЕЙЕРА .43
РАСЧЕТ ПРЕДОХРАНИТЕЛЬНОГО УСТРОЙСТВА 47
ТЕХНОЛОГИЧЕСКИЙ ПРОЦЕСС ИЗГОТОВЛЕНИЯ СЕКТОРА
1 НАЗНАЧЕНИЕ И ВЫБОР ЗАГОТОВКИ 50
2 РАЗРАБОТКА МАРШРУТА ОБРАБОТКИ ДЕТАЛИ 50
3 ОПРЕДЕЛЕНИЕ РЕЖИМОВ РЕЗАНИЯ . 52
РАСЧЕТ ЭКОНОМИЧЕСКОЙ ЭФФЕКТИВНОСТИ
1 РАСЧЕТ ЗАТРАТ ПО СРАВНИВАЕМЫМ ВАРИАНТАМ
ТЕХНИЧЕСКИХ РЕШЕНИЙ 61
2 РАСЧЕТ СУММАРНОГО ЭКОНОМИЧЕСКОГО ЭФФЕКТА 66
1 ТРЕБОВАНИЯ К РАЗМЕЩЕНИЮ КОНВЕЙЕРОВ В
ПРОИЗВОДСТВЕННЫХ ЗДАНИЯХ .70
2 ТРЕБОВАНИЯ К СРЕДСТВАМ ЗАЩИТЫ 74
3 ТРЕБОВАНИЯ К КОНСТРУКЦИИ ..76
СПИСОК ИСПОЛЬЗОВАННЫХ ИСТОЧНИКОВ .80
К машинам непрерывного транспорта относят конвейеры установки гидравлического и пневматического транспорта (для перемещения грузов в несущей среде). Особую группу составляют работающие совместно с ними вспомогательные устройства: спуски скаты бункеры питатели.
Машины непрерывного транспорта классифицируют по области применения способу передачи и характеру приложении к перемещаемому грузу движущей силы конструкции роду перемещаемых грузов назначению и положению на производственной площадке.
В зависимости от области применения различают машины общего назначения и специальные. Первые применяют во многих отраслях хозяйства (например ленточные конвейеры общего назначения) а вторые — в какой-либо одной отрасли (например подземные скребковые конвейеры в горной промышленности) [1].
По способу передачи перемещаемому грузу движущей силы различают машины действующие при помощи механического электрического гидравлического пневматического или комбинированного привода самотечные (гравитационные) устройства в которых груз перемещается под действием собственной силы тяжести устройства пневматического и гидравлического транспорта в которых движущей силой являются соответственно поток воздуха или струя волы.
По характеру приложения движущей силы и конструкции машины непрерывного транспорта подразделяют на машины с тяговым элементом (лентой цепью канатом и др.) для передачи движущей силы и без него.
Тяговый элемент имеют ленточные пластинчатые скребковые ковшовые люлечные конвейеры и элеваторы. К машинам без тягового элемента относят винтовые инерционные роликовые и шаговые конвейеры а также транспортирующие трубы.
По роду перемещаемых грузов различают машины для транспортирования насыпных материалов (ленточные пластинчатые ковшовые скребковые винтовые конвейеры ковшовые элеваторы транспортирующие трубы) штучных грузов (ленточные пластинчатые тележечные люлечные подвесные роликовые шаговые конвейеры люлечные и полочные элеваторы) и пассажиров (ленточные и пластинчатые конвейеры эскалаторы).
По положению на производственной площадке различают машины стационарные переставные переносные и передвижные.
Направления развития машин. Задачи повышения производительности труда и снижения стоимости продукции предопределяют и обусловливают основные направления развития машин непрерывного транспорта:
создание конвейеров для бесперегрузочного транспортирования грузов по трассам большой протяженности;
повышение производительности конвейеров;
повышение надежности машин и упрощение их обслуживания;
автоматизация управления машинами и комплексными системами машин;
снижение металлоемкости и уменьшение размеров машин;
создание конструкций конвейеров основанных на новых принципах транспортирования (на магнитном и воздушном подвесе грузонесушего элемента с приводом от линейных асинхронных двигателей и т. п.);
улучшение условий труда исключение возможности потерь транспортируемого груза полная изоляция транспортирующих устройств от окружающей среды;
унификация и нормализация оборудования на базе единых унифицированных сборочных единиц [1].
Целью дипломного проекта является проектирование горизонтально-замкнутого конвейера для сборки коробок передач.
ОБЗОР ЛИТЕРАТУРНЫХ И ПАТЕНТНЫХ ИСТОЧНИКОВ ПО ТЕМЕ ДИПЛОМНОГО ПРОЕКТА
Тележечный груз о несущий конвейер состоит из замкнутого контура тяговой цепи с постоянно прикрепленными к ней тележками (платформами) движущимися по направляющим путям; на тележках располагаются транспортируемые грузы-изделия; тележки и направляющие пути являются непосредственными составными частями конвейера. В этом состоит принципиальное отличие грузонесущих тележечных конвейеров от напольных грузоведущих конвейеров [2].
Тележечные грузонесущие конвейеры предназначены для перемещения грузов по отдельным технологическим операциям поточного производственного процесса. Их применяют для транспортирования изделий от одного рабочего места к другому в процессе сборки для перемещения литейных форм в процессе сборки заливки охлаждения выбивки возврата пустых опок в литейном цехе для межоперационной передачи изделий от одного рабочего места к другому в процессе изготовления а также для выполнения ряда других операций подобного назначения. Широкое разнообразие использования тележечных конвейеров обусловило большое число их конструктивных разновидностей.
Основными признаками классификации тележечных конвейеров являются расположение тягового элемента и направляющих путей и положение тележек на ветвях конвейера. По первому признаку различают конвейеры вертикально замкнутые и горизонтально замкнутые; последние могут быть расположены как в одной горизонтальной плоскости так и в пространстве. По положению тележек на обратной ветви различают вертикально замкнутые конвейеры с опрокидывающимися и неопрокидывающимися тележками. Горизонтально замкнутые конвейеры бывают с напольным и настольным (на уровне высоты столов рабочих мест) перемещением тележек. По характеру перемещения изделий известны конвейеры с непрерывным (с постоянной и регулируемой скоростью) и пульсирующим движением тележек.
Выбор того или иного типа конвейера зависит от характера технологического процесса обслуживаемого конвейером характеристики перемещаемого груза и планировки производственного помещения.
Вертикально замкнутые конвейеры наиболее компактны так как у них обратная ветвь помещается под рабочей ветвью однако при опрокидывающихся тележках может быть полезно использована только верхняя ветвь; для использования обеих ветвей (при неопрокидывающихся тележках) конструкция конвейера усложняется. При значительной продолжительности производственного процесса обслуживаемого конвейером длина вертикально замкнутого конвейера становится большой; это усложняет планировку производственного помещения.
В горизонтально замкнутых конвейерах для работы используются обе ветви но для их размещения требуется большая производственная площадь. На конвейерах этого типа грузы могут совершать круговые движения без съема с тележек что позволяет рационально использовать конвейер при сравнительно меньшей длине помещения для длительных производственных процессов (например при охлаждении или сушке изделий на конвейере) а также как подвижный склад [3].
Выбор типа конвейера зависит также от характеристики груза. Для перемещения в процессе сборки сравнительно тяжелых и громоздких изделий (например автомашин тракторов моторов и т. п. и их узлов) применяют как правило вертикально замкнутые а для легких малогабаритных — горизонтально замкнутые конвейеры. Технологические конвейеры с длительными и различными по времени операциями (например литейные конвейеры конвейеры испытательных станций и т. п.) делают как правило горизонтально замкнутыми с одно плоскости ой и пространственной трассами.
Основные параметры тележечного конвейера — грузоподъемность и размеры тележки-платформы конвейера. Они определяются габаритными размерами и массой транспортируемого груза. Грузы как правило рекомендуется располагать длинной стороной вдоль продольной оси конвейера и в соответствии с этим выбирать длину тележки (размер вдоль продольной оси конвейера) больше ее ширины . Рекомендованное соотношение размеров позволяет применять более экономичные длиннозвенные тяговые цепи и обусловливает большие удобства для выполнения технологических операций. В отдельных случаях для узких длинных изделий применяют поперечную укладку часто на двух раздельных тележках двухцепных конвейеров. Номинальный ряд ширины тележек: 200 320 400 500 650 800 1200 мм. Грузоподъемность тележек 10-8000 кг [4].
К вертикально замкнутым тележечным конвейерам можно с некоторой условностью отнести также цепепесущие конвейеры у которых перемещаемый груз (например шасси автомобиля или трактора) устанавливается на специальные опоры (гнезда) жестко прикрепленные к пластинам тяговых цепей или же непосредственно на уширенные пластины цепей. Роль тележки при этом выполняют непосредственно тяговые цепи с ходовыми катками.
Особую группу современных тележечных конвейеров представляют распределительные настольные тележечпые конвейеры с автоматической разгрузкой тележек по заданным рабочим местам при помощи системы автоматического адресования. Эти конвейеры бывают вертикально и горизонтально замкнутые и в отдельных случаях с пространственной трассой.
Вертикально замкнутый тележечный конвейер с опрокидывающимися тележками (рисунок 1.1 и 1.2) состоит из тягового элемента 2 (см. рисунок 1.1) с прикрепленными к нему тележками 3 движущимися по направляющим путям опорной конструкции конвейера 4 привода 1 и натяжного устройства 5.
Рисунок 1.1- Вертикально замкнутый тележечный конвейер с опрокидывающимися тележками для сборки автомобильных двигателей:
а — схема конвейера; б — схема нагрузок на тележки
У сборочных конвейеров тележки обычно снабжают установочными кондукторами (рисунок 1.2) поворотными приспособлениями 2 и другими устройствами для облегчения процесса сборки. Металлоконструкция с боковых сторон закрывается съемным предохранительным ограждением 4 из стальных листов или сетки а верхняя ветвь отделяется от нижней сплошным перекрытием 3. Выполненное в виде короба из стальных листов перекрытие предохраняет рабочих - сборщиков от несчастных случаев препятствует попаданию инструмента крепежных деталей и других посторонних предметов на нижнюю ветвь конвейера и служит маслосборником.
Тележки конвейеров жестко крепятся к одному из звеньев цепи. Эти конвейеры выполняют одноцепными или двухцепными в зависимости от колеи и базы тележки и тягового усилия. Приблизительно можно считать что при размере колеи тележки А 4 шагов цепи для устойчивого положения тележки достаточно применять одну цепь а при А > 4 шагов целесообразно использовать две тяговые цепи [5].
Рисунок 2.2 - Поперечные сечения конвейеров с опрокидывающимися тележками:
а - для сборки автомобильных двигателей; б — для сборки автомобиля
Для направления движения тележек во время их опрокидывания на участке приводной звездочки устанавливают неподвижные направляющие контршины по которым движутся катки тележки при опрокидывании а на валу натяжной звездочки размещают два опорных диска (рисунок 1.3) передвигаемых вместе с валом и звездочкой при натягивании цепи. Диаметр дисков выбирают таким чтобы рама тележки на повороте прижималась к ним под действием натяжения цепи.
Конвейеры с неопрокидывающимися тележками (рисунок 1.4) имеют две тяговые цепи располагаемые с двух сторон вне габарита тележки по ширине. Каждая тележка конвейера имеет две оси. Ведущая (ВЩ) ось тележки шарнирно прикреплена к тяговым цепям а ведомая (ВМ) остается свободной. Чтобы тележки свободно проходили между цепями у приводных и натяжных звездочек последние устанавливают на консольных осях так чтобы между ними по середине конвейера оставался свободный промежуток достаточный для прохода тележек. На поворотных участках тележки могут перемещаться с небольшим наклоном в сторону (рисунок 1.4.) и совершать плоскопараллельное движение оставаясь в горизонтальном положении на всем протяжении поворота (рисунок 1.4б). Такой характер перемещения тележки (как при первом так и при втором способах) достигается при помощи установки па поворотных участках системы специальных механизмов и направляющих путей [6].
Рисунок 1.3 - Узел натяжной звездочки с направляющими дисками:
— тележка; 2 — тяговая цепь; 3— диск; 4 — звездочка
Конвейеры с неопрокидывающимися тележками могут иметь только прямолинейную горизонтальную трассу. Консольное крепление звездочек усложненное крепление тележек к цепям и наличие дополнительных механизмов и направляющих на участках поворота усложняют и удорожают конструкцию конвейеров этого типа поэтому они сравнительно мало распространены. Их преимуществом является возможность перемещения грузов как на верхней так и на нижней ветвях конвейера. Это преимущество используется в литейных цехах: на верхней ветви конвейера производят сборку и заливку горячим металлом заформованных а па нижней ветви — охлаждение залитых опок и подачу их на выбивку. Поэтому конвейеры такого типа применяют в литейных цехах при сравнительно небольшой массе литейных форм (примерно до 300 кг) а также в других случаях когда в условиях ограниченной производственной площади (особенно по длине помещения) по производственному процессу необходим конвейер увеличенной длины для выполнения технологических операций различных ритмов (например сборка заливка охлаждение и сборка окраска сушка и т. п.).
Тяговым элементом вертикально замкнутых тележечных конвейеров служат одна или две цепи: пластинчатые втулочные и роликовые с шагом 80 — 320 мм по ГОСТ 588-81 (наиболее частый случай) разборные с шагом 100 и 160 мм по ГОСТ 589-74 пластинчатые комбинированные и иногда (при малых нагрузках) пластинчатые безвтулочные [7].
Опорные устройства и тележки должны обеспечивать удобную надежную и простую установку и съем грузов и их устойчивое положение на всей длине конвейера т. е. на всех его рабочих местах в процессе сборки изделия. В случае необходимости на опорном устройстве должны быть предусмотрены крепления фиксаторы зажимы а также приспособления для наклона поворота или подъема изделия необходимые в процессе сборки. Центр тяжести изделия-груза должен находиться внутри опорного контура тележки на всех позициях сборки. Если же по условиям сборки необходимо иметь консольное расположение изделия на тележке (например при сборке крыла самолета или заднего моста автомобиля) то для обеспечения устойчивости его положения конвейер снабжают дополнительными контршинами или упорами. Для громоздких тяжелых или длинных изделий применяют двухцепные конвейеры с раздельными небольшими тележками прикрепленными отдельно к каждой тяговой цепи (рисунок 1.5). Катки тележки как правило устанавливают на подшипниках качения.
Рисунок 1.4 - Схема вертикально замкнутого тележечного конвейера с неопрокидывающимися тележками перемещающимися с ветви ни ветвь:
а — наклонно; б — плоскопараллельно;
— приводная ветвь; 3 -тележка: 4 — цепь; 5 –путь
Рисунок 1.5 - Схема двух цепного конвейера с раздельными тележками для длинномерных грузов:
- натяжное устройство; 2- тележка; 3- тяговая цепь; 4— привод
Привод — обычного типа размещается на месте расположения поворотной звездочки как правило с единым редуктором или с одной дополнительной цепной или зубчатой передачей (см. рисунок 1.1). Первую применяют при установке привода в приямке под полом чтобы не загромождать производственного помещения и обеспечить удобный съем грузов в конце конвейера а вторую в приводе конвейера с неопрокиды-вающимися тележками при консольном расположении приводных звездочек.
Конвейер с непрерывным движением как правило имеет в приводе вариатор для плавного изменения скорости движения тележки. Для предохранения конвейера от поломок при случайных перегрузках или случайном застопорении цепн на приводной звездочке или на передаче устанавливают предохранительный срезной штифт который при увеличении тягового усилия сверх допускаемого срезается и конвейер останавливается. Кроме того конвейеры с опрокидывающимися тележками снабжают обычно предохранительным устройством в виде конечного выключателя КВ (рисунок 1.1а) сблокированного с электродвигателем которое останавливает конвейер если тележка с неснятым грузом подходит к поворотной звездочке [8].
Натяжное устройство — винтовое или пружинно-винтовое обычного типа; последнее предпочтительнее на конвейерах большой длины. В натяжных устройствах для двухцепных конвейеров одна звездочка закрепляется на оси шпонкой а другая свободно вращается на оси для обеспечения самоустановкн относительно расположения зубьев звездочек при разнице в длинах двух цепей из-за возможного неравенства шагов их звеньев.
Ход натяжного устройства обычно 400 — 500 мм. При чрезмерном износе цепи заменяют полным комплектом для обеспечения постоянства шага тележек.
Цспенесущий конвейер имеет две вертикально замкнутые тяговые цепи (обычно пластинчатые катковые) на пластинах которых через определенный шаг укреплены упоры — гнезда. На упоры (или на торцы уширенных пластин цепи) укладывают транспортируемый груз. Цепи движутся па катках по направляющим путям.
Цепенесущие конвейеры имеют горизонтальную прямолинейную или комбинированную трассу (рисунок 1.6). При комбинированной трассе начальный или конечный (или тог и другой) участок делают наклонным для размещения натяжного устройства и привода в приямке под полом в целях удобства установки и съема изделий с конвейера и предупреждения загромождения пола производственного помещения.
По конструкции цепенесушие конвейеры значительно проще обычных тележечных однако их можно использовать только для изделий с удобными опорными поверхностями.
Цепенесущие конвейеры применяют для перемещения автомобилей тракторов и других подобных изделий на линиях главной сборки для межоперационного транспортирования крупных деталей для транспортирования горячих изделий в процессе их охлаждения а также в качестве подвижного пода нагревательных печей. На конвейере для сборки автомобилей (см. рисунок 1.6) в процессе сборки изделие проходит через покрасочную и сушильную камеры обслуживаемые отдельным самостоятельным участком 11 конвейера. Разделение конвейера на три участка сделано для того чтобы не допустить загрязнения краской всего конвейера. Конвейер приводится в движение от одного общего привода. Отдельные участки соединены друг с другом цепными передачами которые на участках 1 — III являются передаточными устройствами для перемещения изделия с одного участка на другой.
Рисунок 1.6. Схема цепенесущего конвейера для сборки грузовых автомобилей:
— натяжное устройство; 2 — тяговые цепи; 3 — направляющие пути; 4 — передаточное устройство; 5 — покрасочная и сушильные камеры; 6 — пластинчатые конвейеры; 7 — привод
Для транспортирования бутылок консервных банок и других однородных грузов-изделий применяют однорядные и многорядиые цепенесущне конвейеры с вильчатой цепью (рисунок 1.7). Вильчатая цепь — стальная (литая или штампованная) или пластмассовая характеризуется увеличенными зазорами в шарнире благодаря чему конвейеры с такой цепью могут иметь пространственную трассу. Цепь располагается в узком желобе и скользит по его дну; боковые стенки желоба служат направляющими на горизонтальных поворотах трассы. Изделия устанавливаются непосредственно на звенья цепи и движутся внутри желоба [9].
Рисунок 1.7 - Схема много рядного цепенесущего конвейера с пространственной вильчатой цепью:
а - схема трассы одного ряда цепи;
б - средняя часть конвейера с разветвлениями
Цепенесущие конвейеры с пространственной вильчатой цепью получнлн широкое распространение на участках наполнения мойки упаковки сортирования бутылок и банок и других транспортно-технологических линиях.
При повышенных нагрузках цепь снабжают катками.
Выбор параметров и тяговый расчет цепенееущих конвейеров выполняют так же как и вертикально замкнутых тележечных или подвесных пространственных конвейеров.
Наибольшее распространение имеют тележечные конвейеры трех типов для перемещения литейных форм: конвейеры с раздельными тележками-платформами для транспортирования форм по горизонтально замкнутой одноплоскостной (тип Г рисунок 1.8) и пространственной (тип П рисунок 1.9) трассам и конвейеры с перекрывающими платформами (со сплошным настилом) с одноплоскостной трассой (тип ГС). Основные параметры этих конвейеров регламентированы в ГОСТ 5938-73 [10].
Горизонтально замкнутый напольный тележечный конвейер типа Г (рисунок 1.8) состоит из центрально расположенной тяговой цепи 3 (оси шарниров которой располагаются вертикально) с прикрепленными к ней тележками-платформами 2 движущимися по двум направляющим путям 4; привода 5 и натяжного устройства . Ходовая часть конвейера (рисунок 1.10) состоит из пластинчатой катковой цепи 2 одноосных тележек 3 жестко прикрепленных к пластинам цепи платформ 5 на которые устанавливают транспортируемые опоки и щит ков 4 предохраняющих цепь от загрязнения землей и брызгами металла. Каждая платформа опирается на две тележки и соединяется с ними при помощи штырей причем на одной тележке (ведущей) отверстие для штыря выполняют круглым а на другой — овальным для компенсации сокращения расстояния между тележками на криволинейных поворотных участках трассы.
На втулках тяговой цепи устанавливают катки 1 снабженные шарикоподшипниками или коническими роликоподшипниками катки движутся между направляющими шинами и исключают возможность бокового сдвига тележек с рельсовых путей.
Секцию тяговой цепи приходящуюся на одну платформу составляют из двух или четырех звеньев причем в четырехзвенной секции шаг звеньев цепи может быть различным (например 250 и 400 мм) в зависимости от шага платформ (рисунок 1.10 б и в). В каждой секции в звене между платформами один шарнир делают подвижным для чего отверстия во внутренних пластинах с одной стороны выполняют удлиненными (рисунок 1.10 г). Подвижные шарниры допускают некоторое сокращение длины цепи при действии усилий сжатия и позволяют в отдельных случаях устанавливать конвейеры этого типа без натяжных устройств компенсируя возможное несоответствие в длинах цепи и контура направляющих путей.
Наличие отдельных одноосных тележек с безребордными катками прикрепленных к пластинам катковой цепи и шарнирное крепление платформ к тележкам обеспечивают возможность поворота ходовой части конвейера в любую сторону в горизонтальной плоскости по сравнительно небольшим радиусам. Благодаря этому качеству ходовой части конвейеры могут иметь трассы самого разнообразного очертания (рисунок 1.11).
Общая длина трассы конвейера определяется как сумма длин отдельных его участков по обслуживаемым технологическим зонам литейного процесса (рисунок 1.11). Участок формовки и сборки составляет обычно около 30 — 50 м заливки 10—15 м охлаждения 40 — 60 м выбивки 3 — 10 м.
Рисунок 1.8 - Горизонтально замкнутый одноплоскостной тележечный конвейер типа Г для литейных форм
Рисунок 1.9 - Схема пространственного тележечного конвейера типа П для литейных форм
Рисунок 1.10. Ходовая часть конвейера типа Г для транспортирования литейных форм:
а — общий вид; б—схема сборки цени с одинаковым шагом; в—схема сборки цепи с разным шагом; г — узел шарнира тяговой цепи между платформами; д — узел шарнира тяговой цепи под платформой
Рисунок 1.11 - Схема трассы горизонтально замкнутых теле-жечных конвейеров типов Г и ГС конструкции:
R — привод; НУ — натяжное устройство
Основными преимуществами конвейеров этого типа являются легкая приспособляемость трассы к производственным условиям возможность использования всей длины конвейера высокая надежность и возможность широкой механизации загрузки и разгрузки.
Рисунок 1.12 - Ходовая часть конвейера конструкции типа П
Конвейер с раздельными тележками и пространственной трассой типа П (см. рисунок 1.9) имеет в принципе такую же конструкцию как и конвейер типа Г с той лишь разницей что у него тяговая цепь снабжена дополнительным шарниром с горизонтальным валиком (рисунок 1.12) для обеспечения поворота ходовой части в вертикальной плоскости. Основными преимуществами конвейеров с пространственной трассой являются рациональное использование производственной площади улучшение санитарных условий работы в литейном цехе когда участки формовки и заливки размещаются на первом этаже а участки охлаждения и выбивки — в изолированном подвале. Радиусы поворота ходовой части в вертикальной плоскости 5 —8 м наибольший угол подъема 6°.
У тележечных конвейеров типа ГС конструкции со сплошным настилом (рисунок 1.13) для транспортирования литейных форм платформы имеют полукруглое (выпуклое с одной и вогнутое — с другой стороны) очертание торцовых сторон. Такое расположение платформ образует сплошной настил на прямолинейных и поворотных участках конвейера и надежно защищает его ходовую часть и пути от загрязнения и заплесков металла. Конвейер не имеет тяговой цепи; функции грузонесущего и тягового элементов выполняют платформы с тележками.
Секция ходовой части конвейера (рисунок 1.13 б) состоит из тележки 8 платформы 2 продольной балки 3 и соединительных звеньев 1. Тележка имеет горизонтальную ось 11 с ходовыми катками 12 и роликами 10 и 9 для опоры платформ вертикальную ось 7 которая является шарниром для соединения продольных балок 3 смежных секций и коромысло 4 с горизонтальными катками 5. Ролики 10 расположенные ближе к продольной оси платформы служат для опоры платформы своей секции а ролики 9 — для опоры платформы смежной секции. Наличие опорных роликов уменьшает потери на трение при поворотах платформ. Коромысло с катками 5 обеспечивает направленное движение тележки на поворотных участках путей. Конвейер имеет гусеничный привод и пружинно-винтовое натяжное устройство. В середине балки 3 закреплен ролик 6 при помощи которого толкатель гусеничного привода перемещает ходовую часть конвейера.
Тяговым элементом горизонтально замкнутых тележечных конвейеров для литейных форм служит одна пластинчатая катковая цепь по ГОСТ 588 — 81 с увеличенной подвижностью некоторых шарниров (см. рисунок 110 г).
Тяговым элементом пространственных конвейеров (см рисунок 1.9) является двухшарнирная цепь которая имеет вертикальные и горизонтальные шарниры позволяющие звеньям цепи свободно отклоняться в любую сторону или обычная пластинчатая цепь с креплением к тележкам при помощи шарнира ось которого перпендикулярна осям шарниров цепи. Тележки-платформы у пространственных конвейеров имеют упоры предохраняющие сползание грузов на наклонных участках [10].
Рисунок 1.13 - Горизонтально замкнутый тележечный конвейер конструкции типа ГС:
- общий вид; 6 - ходовая часть
Платформы конвейеров для транспортирования литейных форм имеют три исполнения (рисунок 1.14): с плоской плитой с роликовым настилом и с поворотными плитами Плоские плиты изготовляют из чугуна; с нижней стороны их укрепляют ребрами для жесткости и предохранения от коробления а с наружной — выполняют канавки для свободного выхода газов из нижней опоки Платформы с плоскими плитами применяют главным образом для тяжелых форм при загрузке и разгрузке конвейера краном или электроталью или для весьма легких форм при загрузке и разгрузке вручную. Платформы с роликовым настилом применяют для форм массой до 2000 кг при загрузке с роликовых конвейеров и разгрузке при помощи толкателя. Роликовый настил выполняют в виде двух секций прикрепленных шариирно к раме платформы и отклоняемых в сторону для удобства удаления из-под роликов просыпавшейся земли.
Платформы с поворотными плитами изготовляют шириной до 650 мм и применяют для транспортирования безопочного литья. Разгрузка такой платформы производится автоматически при помощи наклона плиты на криволинейной шине. На шину при движении конвейера накатывается ролик укрепленный сбоку плиты отчего плита принимает наклонное положение (см. рисунок 1.4 б) и форма сползает с нее на выбивную решетку Катки тележек конвейера делают из чугуна СЧ 15 с отливкой в кокиль или чаще из стали 45 с поверхностной закалкой обода токами высокой частоты и снабжают подшипниками качения (шариковыми или коническими роликовыми) для уменьшения тягового усилия. Из-за весьма тяжелых условий работы в литейных цехах узел подшипников должен иметь надежное лабиринтное уплотнение для предохранения их от засорения.
Привод — гусеничный (см. рисунок 1.8 и 1.15) состоит из вертикально замкнутой приводной цепи 9 (см. рисунок 1.8) с кулаками 1 приводной 7 и натяжной 1 звездочек зубчатой передачи 6 редуктора 8 вариатора 15 клиноремениых передач 14 электродвигателя 13 и металлоконструкции 12. Толкатели приводной цепи (рисунок 1.16) упираются в катки тяговой цепи конвейера и приводят ее в движение. Для выхода толкателя из зацепления с катком шаг толкателей иа приводной цепи должен быть на 3 — 5 мм меньше шага катков цепи конвейера. Вследствие этого последующий толкатель включается в работу раньше выхода из зацепления предыдущего благодаря чему обеспечивается непрерывная без рывков передача усилия с приводной цепи на тяговую цепь конвейера.
Для предохранения механизмов привода от поломки при внезапной перегрузке зубчатое колесо приводного вала снабжают предохранительным срезным штифтом. Привод как правило устанавливают после наиболее загруженного участка например после основной части охладительного участка перед участком выбивки форм.
Рисунок 1.14 - Платформы тележечных конвейеров для транспортирования литейных форм:
а — с плоской плитой (для конвейеров типов Г. ГС и II); и — с роликовым настилом (для конвейеров типа Г); в — с поворотными плитами (для конвейеров типа Г)
Рисунок 1.15 - Схема гусеничного привода тележечного конвейера :
— приводная звездочка;
— толкатель гусеничной цепи; 3 — направляющие шины; 4 — тяговая цепь конвейера; 5 —платформа; 6 — натяжная звездочка; 7— приводная (гусеничная) цепь
Рисунок 1.16 - Приводная цепь с толкателями
Типовые приводы имеют расстояния между звездочками 2010 — 2675 мм и электродвигатели мощностью 15 — 15 кВт [10].
Натяжное устройство (рисунок 1.17) устанавливают на повороте конвейера на 180°. Оно представляет собой прочную раму 4 на которой крепят криволинейные участки рельсов 2 и направляющих путей 1. Рама опирается на опоры 3 и перемещается по ним при помощи натяжного винта 5. Ход натяжного устройства обычно составляет 500 — 600 мм. Концы рельсовых и направляющих путей натяжного устройства сопрягаются с неподвижными их частями при помощи раздвижных стыков.
Рисунок 1.17- Натяжное устройство горизонтально замкнутого тележечного конвейера
Натяжное устройство необходимо обязательно устанавливать на конвейерах со сложной горизонтальной и пространственной трассой (см. рисунок 1.11 б — г е и ж) а также на конвейерах большой длины (более 50 м). На тихоходных конвейерах с простой трассой (см. рисунок 1.11 а) при небольшой длине (до 50 м) натяжные устройства можно не применять при условии обеспечения повышенной точности изготовления и монтажа конвейера. На конвейерах с прямоугольной трассой (см. рисунок 1.11 д) натяжные устройства также не устанавливают так как они получаются громоздкими и сложными Ходовые пути состоят из опорных и направляющих частей. Опорные пути выполняют из железнодорожных рельсов типа Р11 Р24 и Р33 последние — для наиболее тяжелых конвейеров. Направляющие между которыми движутся катки тяговой цепи изготовляют из уголков (обычно 60х60х6 или 75х 60х6 мм). Пути крепят болтами к сварным или литым опорным башмакам [11].
Размеры платформы выбирают по габаритным размерам и массе перемещаемых грузов и принимают обычно на 100—150 мм больше габаритных размеров опок. По размерам тележек-платформ выбирают их шаг кратный длине секции цепи. Среднюю расчетную скорость конвейеров для сборочных работ определяют по ритму технологических операций и по заданной производительности с учетом коэффициентов загрузки и использования конвейера по времени. По принятой скорости (обычно в пределах 12 — 75 ммин) проверяют и корректируют длины различных технологических участков и время нахождения грузов на них. Тяговый расчет конвейера выполняют обычным порядком по точкам путем последовательного определения и суммирования сопротивлений иа отдельных участках трассы конвейера. Массу ходовой части конвейера выбирают. Первоначальное натяжение принимают равным 1 — 15 кН.
Сопротивления на криволинейных участках определяют в зависимости от конструкции тележек и поворотного устройства конвейера раздельно — для тележек и цепи. Сопротивления движению на вертикальных перегибах конвейеров с пространственной трассой вычисляют так же как и для подвесных конвейеров.
Горизонтально замкнутые напольные тележечные конвейеры применяют не только для транспортирования литейных форм но и для перемещения других разнообразных грузов-изделий (например газовых плит холодильников и т. п.) в различных технологических процессах (на сборке мойке окраске и т. п.). Их конструкции разнообразны но значительно проще и легче чем конструкции литейных конвейеров. Их выполняют с центральным и боковым расположением тяговой цепи (с консольными тележками) двухрельсовыми и однорельсовыми с приводом от поворотной звездочки или гусеничной цепи. Известны безцепные горизонтально замкнутые тележечные конвейеры с приводом от вращающейся трубы стационарно установленной вдоль трассы перемещения тележек. Тележка имеет поворотный ведущий диск который соприкасается с приводной трубой. Силы трения между диском и трубой обеспечивают перемещение тележки; поворот диска по отношению к оси трубы обусловливает скорость движения тележки. Когда диск располагается перпендикулярно к продольной оси трубы тележка не движется. Управление движением тележек осуществляется при помощи направляющих шин воздействующих на положение ведущего диска тележки.
На распределительном настольном тележечном конвейере (рисунок 1.18 а б) тележки прикреплены к тяговой цепи и движутся по направляющим путям опорной металлоконструкции на уровне рабочих мест (обычно на высоте 700 — 800 мм). Транспортируемые грузы — швейные или обувные изделия детали приборов радиоприемников телевизоров мелкие детали машин и т. п укладывают на тележку непосредственно или в специальной производственной таре — открытом коробе — контейнере. Загрузка может быть ручная или автоматическая. При автоматической загрузке тара с грузом перемещается со стола рабочего места на тележку автоматически управляемым пневматическим или механическим толкателем.единицы изделия и тары обычно составляет 01-25 кг.
Рисунок 1.18 - Настольный тележечный конвейер:
а — вертикально замкнутый: в — горизонтально замкнутый:
— пульт управления: 2 — тележка: 3 — адресоноситель автоматического адресования; 4 — короб для изделий (контейнер);
—толкатель для автоматической подачи короба на тележку
Тележки конвейера (иногда контейнеры — открытые короба для грузов) имеют адресоносители для автоматического адресования грузов по рабочим местам автоматической разгрузки На рабочих местах которые расположены вдоль конвейера в пунктах разгрузки устанавливают считыватели и площадки приема грузов. Опорные плиты тележки делают поворотными или наклонными с управляемыми упорами; последние необходимы только для грузов транспортируемых в коробах-контейнерах. При совпадении адреса адресоносителя тележки с адресом считывателя установленного у рабочего места поворотная плита тележки наклоняется при помощи включенной управляемой направляющей шины и транспортируемый груз-изделие соскальзывает на рабочее место. Эта же операция выполняется при наклонной плите когда по сигналу считывающего устройства упор опускается и тара с грузом под действием силы тяжести соскальзывает с тележки на приемный стол рабочего места.
Конвейеры могут иметь централизованное управление адресованием грузов с центрального пульта по установленной программе или местное с рабочего места. В последнем случае рабочий выполнив свою операцию и положив изделие на свободную тележку сам назначает адрес дальнейшего следования изделия. Тележки конвейера могут иметь непрерывное (обычно со скоростью 05 — 6 ммин) или пульсирующее (со скоростью 8—10 ммин) движение управляемое с центрального пульта.
По конфигурации трассы и расположению тяговой цепи распределительные конвейеры бывают вертикально замкнутыми с неопрокидывающимися и опрокидывающимися тележками горизонтально замкнутыми (рисунок 118 б) и пространственными.
Конструкции распределительных тележечных конвейеров разнообразны в зависимости от технологических особенностей обслуживаемых ими производственных процессов (рисунок 1.19).
Рисунок 1.19 - Поперечное сечение полуавтоматического горизонтально замкнутого настольного тележечного конвейера для транспортирования полуфабрикатов обуви:
— тяговая цепь; 2 — тележка; 3 — катки тележки; 4 — пути;
- контейнер с обувью; 6 — защелка для удержания контейнера на тележке конвейера
Распределительные тележечные конвейеры предназначаются для межоперационного транспортирования грузов-изделий между рабочими местами при поточном массовом и серийном производстве в легкой (швейной обувной) радиоэлектронной прибора - и машиностроительной промышленности Благодаря широким возможностям автоматического адресования изделий и конструктивным особенностям распределительных конвейеров их применяют даже при отсутствии строгой последовательности в расстановке технологического оборудования по производственному процессу а также для одновременного обслуживания нескольких производственных бригад выполняющих операции с различным ритмом. Последнее возможно потому что производственные операции в данном случае выполняются не непосредственно на тележках конвейера (как на сборочных конвейерах) а на рабочих местах рядом с конвейером и распределение грузов-изделий производится самим рабочим или диспетчером по заранее обусловленной программе Поэтому тележки с изделиями могут циркулировать по трассе конвейера и подавать .изделия (разгружаться) на любое заданное рабочее место.
Основные параметры распределительных тележечных конвейеров: грузоподъемность тележки 10 25 50 кг; ширина платформ 250 — 300 мм длина соответственно 400-800 мм. Применяемая производственная тара — стандартная
Распределительно-сортировочный те-лежечный конвейер фирмы Телефлекс (Франция) с пространственной трассой (рисунок 1.20) имеет тележки прикрепленные к пластинам двух шарнирной цепи 5. Грузонесущая часть тележки состоит из двух полок 1 которые могут поворачиваться вокруг оси 2 при воздействии на направляющий каток 4. Тележки движутся по путям 6 а цепь — по путям 7 из гнутых тонкостенных профилей. В местах загрузки или разгрузки каток 4 встречается с направляющей шиной и наклоняет полку 1 для приема груза или его скольжения в приемное устройство. Управление погрузочно-разгрузочными пунктами автоматизировано. Загрузка конвейера производится при помощи автоматически управляемых роторных загрузочных устройств.
Рисунок 1.20 - Поперечное сечение тележечного конвейера фирмы Телефлекс (Франция) с автоматической нагрузкой и разгрузкой
Конвейер предназначен для перемещения и сортирования посылок кип мешков свертков и других массовых штучных грузов.
Параметры конвейеров: грузоподъемность тележки — 10 30 и 70 кг при длине соответственно 600 900 и 1200 мм. Благодаря широкому применению пластмасс в деталях цепи и тележки скорость тележек достигает 150 ммин. Цепь имеет шаг 203 мм радиус поворота пути 06 — 18 м; привод — угловой или гусеничный тяговое усилие 8 — 15 кН.
Тяговым элементом распределительных конвейеров основных типов служит как правило одна тяговая цепь — пластинчатая роликовая с шагом 80-100 мм по ГОСТ 588-81; двухшарнирная с шагом 160 — 200 мм иногда приводная пластинчатая цепь с шагом 254 — 381 мм; известно также применение круглозвенных цепей В вертикально замкнутых конвейерах с неопрокидывающимися тележками используют две стандартные тяговые пластинчатые цепи по ГОСТ 588 — 81. Двухшарнирные цепи применяют для горизонтально замкнутых конвейеров со сложной трассой а также главным образом для пространственных конвейеров [11].
Тележки выполняют с гладкой горизонтальной или наклонной плитой или с роликовым настилом. Каркас тележки жестко прикреплен к звену цепи и иногда снабжен дополнительным направляющим катком (см. рисунок 1.19). При применении двухшарнирной цепи тележка собственных катков может не иметь.
Натяжное устройство — винтовое или пружинно-винтовое.
Привод как правило редукторный такой же конструкции как и угловой привод подвесных конвейеров с верхним расположением приводного вала и размещением приводной звездочки над редуктором. У конвейеров с пульсирующим движением в приводе устанавливают колодочный тормоз для ликвидации свободного выбега ходовой части и точной фиксации остановки тележек.
Металлоконструкцию средней части выполняют из прокатных профилей и труб с боковых сторон закрывают щитами для обеспечения требований техники безопасности. Часто ее оснащают регулируемыми по высоте сиденьями для рабочих ступеньками и погрузочно-разгрузочными столами на уровне рабочих мест.
Системы автоматического адресования в распределительных конвейерах служат для распределения грузов по заданным пунктам разгрузки — адресам а также для количественного и номенклатурного учета транспортируемых изделий. Конструкции применяемых систем адресования разнообразны но наиболее часто используют бесконтактную систему с местным управлением.
Тележка разгружается при наклоне поворотной плиты на которой находится груз или при перемещении запорного штифта препятствующего сдвигу тары с грузом.
При движении после разгрузки тележка специальным рычагом снова устанавливает исполнительный механизм в рабочее положение. Конвейер имеет автоматическую систему блокирования исключающую возможность разгрузки тележки на занятое рабочее место. Если заданный адрес занят то тележка не разгрузится и пойдет к следующему рабочему месту с этим адресом или же сделает полный кругооборот по трассе конвейера.
Расчет распределительных конвейеров выполняют так же как и расчет других тележечных конвейеров.
В задачи научных исследований конвейеров входят:
) экспериментальное определение коэффициентов сопротивления движению ходовой части конвейера на всех участках трассы сложного профиля в реальных условиях эксплуатации;
) определение динамических нагрузок на цепь при пуске конвейера с пространственной трассой;
) выбор оптимального расположения привода на конвейере для литейных форм со сложной пространственной трассой;
) определение сопротивления движению ходовой части на горизонтальных поворотах тележечного конвейера для литейных форм;
) определение спектра нагрузок на катки тележек конвейера для литейных форм со сложной пространственной трассой за один цикл движения цепи по контуру трассы;
) оптимальная организация работы распределительного конвейера при различном ритме выполнения рабочих операций;
) организация работы распределительного конвейера в качества транспортного и склада — накопителя [11].
РАСЧЕТ МОЩНОСТИ ПРИВОДА КОНВЕЙЕРА
Тяговая сила конвейера находится из выражения
где - сопротивление движению для холостой ветви конвейера Н;
- сопротивление движению для груженой ветви конвейера Н.
Находим сопротивление движению для холостой ветви конвейера
где - основное сопротивление движению секций цепи на подшипниках качения Н;
- дополнительное сопротивление движению секций цепи на подшипниках качения Н.
Основное сопротивление движению секций цепи на подшипниках качения
где - коэффициент трения качения ();
- масса секции цепи кг ();
- количество холостых секций цепи ()
Дополнительное сопротивление движению секций цепи на подшипниках качения
где - коэффициент сопротивления движению цепи
где - коэффициент увеличения сопротивления на катках с ребордами из-за трения реборд о направляющие ();
- наружный диаметр вала на котором вращается каток см ();
Тогда дополнительное сопротивление движению секций цепи на подшипниках качения равно
Тогда сопротивление движению для холостой ветви конвейера равно
Сопротивление движению для груженой ветви конвейера
где - основное сопротивление движению секций цепи с тележками-подставками и груза на подшипниках качения Н;
- дополнительное сопротивление движению секций цепи с тележками- подставками и груза на подшипниках качения Н.
Основное сопротивление движению секций цепи с тележками-подставками и груза на подшипниках качения
где - количество нагруженных секций цепи ();
- количество рабочих позиций ();
- сумма масс узлов коробок передач на позициях конвейера кг
Дополнительное сопротивление движению секций цепи с тележками- подставками и груза на подшипниках качения
Тогда сопротивление движению для груженой ветви конвейера равно
Отсюда тяговая сила конвейера равна
Необходимая мощность привода при [12]
где - линейная скорость перемещения секций цепи с тележками- подставками мс ()
С учетом возможной перегрузки мощность приводного электродвигателя равно
Выбираем электродвигатель АИР100L6У3 IP55 мощностью 22 кВт и частой вращения от 22 до 940 обмин [13].
Частота вращения приводной звездочки
где - диаметр приводной звездочки м ()
Передаточное число привода
Выбираем редуктор КДВ-350М2-III передаточным числом 1382 [13].
Кинематическая схема привода приведена на рисунке 2.1.
Определяем крутящий момент на валу двигателя
где - мощность двигателя кВт ();
- пределы частот вращения двигателя об мин ()
Максимальное тяговое усилие тяги конвейера равно
Рисунок 2.1 – Кинематическая схема привода конвейера:
– электродвигатель; 2 – муфта; 3 – редуктор; 4 – приводная звездочка
РАСЧЕТ ПРЕДОХРАНИТЕЛЬНОГО УСТРОЙСТВА
Предохранительное устройство предназначено для аварийной остановки конвейера в случае его резкого торможения.
При резком торможении конвейера происходит срезание пальца и ступица звездочки вращается вхолостую. Предохранительное устройство препятствует перегреву двигателя или поломке редуктора в случае резкого торможения.
Произведем расчет диаметра предохранительного пальца. Исходные данные для расчета:
- окружное (тяговое) усилие на приводной звездочке конвейера - ;
- допускаемая перегрузка по окружному усилию - 25 %[11].
Требуемый диаметр предохранительного пальца находим с учетом материала пальца и его термообработки. Палец изготовлен из пружинной стали марки Сталь 65Г с закалкой и охлаждением в масле с пределом прочности на срез [13].
На рисунке 3.1 представлена схема для расчета пальца на срез
Рисунок 3.1 – Схема для расчета пальца на срез.
Диаметр пальца находим по формуле [13]
где - допускаемое напряжение на срез МПа ();[13].
- усилие срезания пальца Н
- диаметр пальца в месте среза мм.
Требуемый диаметр пальца равен
Т.е. диаметр в месте среза пальца должен быть равен 10мм.
ТЕХНОЛОГИЧЕСКИЙ ПРОЦЕСС ИЗГОТОВЛЕНИЯ СЕКТОРА МЕХАНИЗМА ПОВОРОТА СТОЛА
1 НАЗНАЧЕНИЕ ДЕТАЛИ И ВЫБОР ЗАГОТОВКИ
Изготавливаемая деталь (рисунок 4.1) – сектор материал – Сталь 45 ГОСТ 1050-88 служит для передачи крутящего момента в механизма поворота стола.
Рисунок 4.1 – Сектор
В качестве заготовки будущей детали принимаем прокат: Круг . Длина заготовки равна длине детали с учётом припуска на обработку (подрезку торцов и отрезку).
2 ПРОЕКТИРОВАНИЕ МАРШРУТА ОБРАБОТКИ.
ВЫБОР ОБОРУДОВАНИЯ И ИНСТРУМЕНТА
Маршрут обработки выбранной заготовки включает следующие операции:
5 –Отрезная (Отрезать от круга заготовку длиной 30 мм);
Переход 1 (Сверлить отверстие диаметром 30 мм);
Переход 2 (Расточить отверстие до диаметра 34 мм);
5 – Токарная (Подрезать торцы);
Переход 1 (Точить наружную поверхность);
Переход 2 (Снять фаски);
5 – Фрезерная (Фрезеровать сектор);
0 - Зубофрезерная (Фрезеровать зуба);
5 - Протяжная (Протянуть шлицы);
0 – Термическая (Закалить заготовку);
5 – Шлифовальная (Шлифовать зубья);
В таблице 4.1 сведен выбор оборудования и инструмента в соответствии с операциями.
Таблица 4.1 – Применяемое оборудование и инструмент при изготовлении зубчатого колеса
Станок токарный 1К625
Сверло 2301-0028 ГОСТ 10903-77;
резец расточной 2145-0041 1 ВК6М ГОСТ 18063-72
Резец 2102-0073 ВК8 ГОСТ 18877-73
Резец 2102-0073 ВК8 ГОСТ 18877-73; резец 2112-0051 ВК8 ГОСТ 18880-73
Станок фрезерный 6Т80Ш
Фреза 2214-0003 ГОСТ 24359-80
Зубофрезерный станок
Фреза модульная 2510-4065 ГОСТ 9324-80
Горизонтально-протяжной станок 7А523
Протяжка 2402-1066 ГОСТ 24818-81
Зубошлифовальный полуавтомат 5А833
П 250x10x76 91А 16Н СМ1 7 К5 35мс А1 кл ГОСТ 3434-83
Продолжение таблицы 4.1
Штангенциркуль ШЦ-II- 250-630-01-1 ГОСТ 166-89
индикатор часового типа ИЧ02-0001 ГОСТ 577-68; штатив Ш-II Н ГОСТ 10197-70 нутромер 18-50-0001 ГОСТ 9244-75.
Комплект документов на технологический процесс изготовления зубчатого колеса представлен в Приложении А.
3 РАСЧЕТ РЕЖИМОВ ОБРАБОТКИ И НОРМ ВРЕМНИ
Расчет режимов обработки ведем по методике изложенной в [11] [12] и [13]
Операция 010 – Токарная
Переход 1: Сверление отверстия 30 мм.
Подача выбирается по таблице 25 из [11] so=01ммоб.
По паспорту станка принимаем подачу s=01ммоб.
Скорость резания определяется по формуле:
где Сv - постоянный коэффициент (Сv=85);
Т - период стойкости мин ();
m y - показатели степени.
По таблицам из [11] m=02; y=05;
Кv - общий поправочный коэффициент на скорость резания учитывающий отличные от табличных условия резания.
где Кmv - коэффициент учитывающий марку обрабатываемого материала (Кmv=08);
Кuv - коэффициент на инструментальный материал (Кuv=09);
Расчет частоты вращения шпинделя станка:
Уточняем частоту вращения шпинделя по паспорту станка:
Произведем уточнение скорости резания по принятой частоте вращения:
Крутящий момент и рассчитываются по формуле из [12]:
Согласно таблице 32 из [12]: Cm=00345; y=08; q=2.
Необходимая мощность станка
где - кпд станка ().
Мощность электродвигателя токарного станка 1К625 8 кВт следовательно условия резания выполняются.
Определяем длину рабочего хода суппорта
– длина резания мм ();
– величина подвода врезания перебега инструмента мм ();
–дополнительная длина хода инструмента вызванная особенностями наладки или конфигурации детали мм ();
Рассчитаем основное технологическое время
где L– длинa рабочего хода суппорта мм;
n – частота вращения шпинделя обмин ();
Переход 2: Растачиваем сквозное отверстие диаметром до диаметра длиной .
Глубина резания при снятии припуска за один рабочий проход
Назначаем период стойкости резца
где – скорость резания ммин ();
– коэффициент зависящий от обрабатываемого материала ();
– коэффициент зависящий от типа материала и стойкости инструмента ();
– коэффициент зависящий от диаметра прутка при его обработке ();
Рассчитываем число оборотов шпинделя станка
где – диаметр отверстия до которого нужно обработать поверхность детали мм ();
– скорость резания ммин ().
Корректируем частоту вращения по данным станка и устанавливаем действительную частоту вращения .
Тогда уточним величины ммин по принятым значениям обмин
– величина подвода врезания перебега инструмента мм () ;
где – длинa рабочего хода суппорта мм ();
– частота вращения шпинделя обмин ();
где – осевая сила резания кН ();
– глубина резания мм ();
где – сила резания кН ();
– скорость резания ммин ();
Мощность токарного станка 1К625 8 кВт и следовательно обработка возможна.
Операция 015 – токарная
Подрезаем торец детали с величину .
Назначаем подачу. По [11] .
Назначаем период стойкости резца в минутах основного времени .
где – диаметр обрабатываемой поверхности детали мм ();
где – сила резания кВт ();
Мощность токарного станка 1К625 8 кВт следовательно обработка возможна.
Операция 020 – токарная
Переход 1: Протачиваем наружную поверхность детали с .
Назначаем подачу. по [10] .
Мощность токарного станка 16К20 8 кВт следовательно обработка возможна.
Операция 030 – протяжная
По таблице 3.19[11] находим: подачу Sz =005 мм на зуб; рабочую скорость резания Vрх = 25 ммин; обратная скорость протяжки по паспорту станка Vох = 20 ммин.
Необходимое усилие резания определяется по таблице 3.28 [13] .
где – ход инструмента;
– количество одновременно обрабатываемых деталей;
где P– сила резания кВт ;
Vд – скорость резания ммин;
Мощность электродвигателя станка 7А525 55 кВт следовательно условия резания выполняются.
Определяющей задачей экономической оценки технического решения при ремонте башенного крана с восстановлением кольцевой рамы башенного крана является обоснование целесообразности его внедрения в народное хозяйство. Общая цель экономической оценки новой техники – установить насколько проектируемые конструкции машин отвечают требованиям высокой эффективности насколько они способны привнести экономических плюсов по сравнению с уже используемыми машинами и механизмами.
Экономическую эффективность определяют при обосновании создания или модернизации выпускаемой техники; при обосновании и анализе производства и использовании новой техники; при обосновании решений и реализации организационных мероприятий и мероприятий связанных с управлением производством; при обосновании цен производимой в отрасли продукции и др.
Далее представлен расчет экономической эффективности от внедрения конвейера по сборке КПП произведенный с помощью программы составленной в Microsoft Excel 97 на кафедре «Строительные и дорожные машины» БНТУ.
1 РАСЧЕТ ЗАТРАТ ПО СРАВНИВАЕМЫМ ВАРИАНТАМ ТЕХНИЧЕСКИХ РЕШЕНИЙ
Цена базовой машины 350 млн.руб.
Рассчитаем налоги (по белорусскому законодательству).
Отчисление единым платежом в фонд поддержки производителей сх продукции и в дорожный фонд (ставка налога 2%100%)
Отчисления в жилищный фонд ставка налога по г. Минску 075%
Налог на добавленную стоимость (НДС) ( ставка налога 20%100%)
где - добавленная стоимость
где - материальные затраты в цене продукции принимаем на уровне 582% от цены (5238млн.руб)
Следовательно налог на добавленную стоимость (НДС) равен
Прибыль балансовая Пбал определяется по следующему выражению
где ФЗП - фонд заработной платы средний по машиностроению 1% от цены изделия тыс.руб.
- отчисления на социальное страхование 35 % от ФЗП млн.руб:
- отчисления в фонд занятости 1% от ФЗП млн.руб.
- амортизация среднюю норму амортизации примем на уровне 12% от стоимости капиталовложений (Кб=245 млн.руб. - расчеты приведены ниже)тыс. руб.
Балансовая прибыль на изготовление составит
Налог на недвижимость определяется по следующему выражению(ставка - 1%)
Налог на прибыль ставка 25% определяется следующим выражением
Определим чистую прибыль по следующему выражению
Отчисления на содержание детских дошкольных учреждений 5% от ФЗП
Чрезвычайный налог на ликвидацию последствий аварии на Чернобыльской АЭС 4% от ФЗП
Полную себестоимость определим по формуле
где ФЗП - фонд заработной платы примем на среднем уровне по машиностроению 1% от Ц т.е. ФЗП=35 млн.руб.
А - амортизация А=29 млн.руб.
Осс - отчисления на социальное страхование 35% от ФЗП
Оф з - отчисления в государственный фонд занятости 1% от ФЗП
Найдем рентабельность по себестоимости по следующему выражению
Найдем рентабельность по инвестициям
Полную себестоимость определим методом удельных показателей по следующей формуле:
где - соответственно масса базового и проектируемого конвейера т
где - полная себестоимость млн. руб.
Рассчитаем прибыль при производстве машины результаты сводим в таблицу 5.1.
Таблица 5.1 – Результаты расчетов
Полная себестоимость
Фонд заработной платы
Отчисления на соцстрах и фонд занятости
Чрезвычайный налог и отчисления на ДДУ
Капитальные вложения Ко
Материальные затраты
Цена за вычетом Осх и Ож
Налог на недвижимость
2 РАСЧЕТ СУММАРНОГО ЭКОНОМИЧЕСКОГО ЭФФЕКТА
Годовой экономический эффект полученный в результате инвестирования проектируемого технического решения за счет средств хранящихся на банковском счете определяется по следующей формуле
где - годовая дополнительная прибыль остающаяся на нужды предприятия при инвестициях обеспечивающий реализацию проектируемого технического варианта;
И - величина инвестиций в проектируемом техническом варианте определяется по формуле
где - капитальные вложения соответственно по базовому и проектируемому вариантам тыс. руб.
Соотношение капвложений в производство и себестоимостью для базового варианта 07 а для проектируемого принимаем равным 075 вследствие незначительной сложности монтажа и освоения новых технологий применяемых для изготовления изделия. - реальный банковский процент за пользование кредитом в десятичном виде. Он определяется по следующей формуле
где - номинальный банковский процент за пользование кредитом в десятичном виде;
d - среднегодовой дефлятор.
Определим экономический эффект от выпуска одной для производства
Теперь найдем экономический эффект от производства одной машины для потребителя.
Таблица 5.2 - Исходные данные
Цена продажи машины (Ц) млн.руб.
Доставка (5% от цены) ( Т ) млн.руб.
Производительность(Пр) у.е.ч
Расход электроэнергии ( Q ) (млн.рубч)
Стоимость ТОиР млн.руб
Срок эксплуатации ( Г ) лет
Норма амортизации ( А ) %
Зарплата оператора млн. рубч
Зарплата рабочих на ТО и Р млн.рубч
Количество маш-час работы в году ч
Цена продажи услуг (Цм) млн.руб
Прямые затраты на годовую выработку определим по формуле
где - затраты на зарплату основных и дополнительных рабочих млн.рубч.;
- затраты на электроэнергию млн.руб.ч.;
- затраты на ТО и ремонт млн.руб.год.;
и - часовая оплата труда основных и дополнительных рабочих;
Ч- количество часов работы в году.
Результаты расчетов затрат сводим в таблицу 5.3 прибыли в таблицу 5.4.
Таблица 5.3 - Результаты расчетов затрат.
Таблица 5.4 - Результаты расчетов прибыли.
Сумма млн.руб по базовой машине
по отремонтированной
Объем выработки у.е.год
Продолжение таблицы 5.4
Фонд заработной платы
Полная себестоимость выработки
Выручка за вычетом Осх и Ож
Добавленная стоимость
Экономический эффект потребителя Ээ
Экономический эффект в народном хозяйстве
Таблица показателей экономической эффективности дана на листе 8 дипломного проекта.
При проектировании сборочного конвейера были учтены все требования изложенные в ГОСТ 12.2.022-80 Системы Стандартов безопасности труда « Конвейеры. Общие требования безопасности» и «Межотраслевых правилах по охране труда при эксплуатации конвейерных трубопроводных и других транспортных средств непрерывного действия »[19].
Настоящий стандарт распространяется на конвейеры применяемые во всех отраслях народного хозяйства и устанавливает общие требования безопасности к их конструкции и размещению.
Стандарт не распространяется на конвейеры предназначенные для перевозки людей конвейеры устанавливаемые на судах в шахтах и карьерах а также конвейеры являющиеся составными частями (узлами) производственного (технологического) оборудования или машин.
Стандарт полностью соответствует СТ СЭВ 1339—78.
1 ТРЕБОВАНИЯ К РАЗМЕЩЕНИЮ КОНВЕЙЕРОВ В ПРОИЗВОДСТВЕННЫХ ЗДАНИЯХ
Конвейеры кроме подвесных следует устанавливать так чтобы расстояние по вертикали от наиболее выступающих частей конвейера требующих обслуживания до нижних поверхностей выступающих строительных конструкций (коммуникационных систем) было не менее 06 м а от транспортируемого груза — не менее 03 м.
При размещении стационарных конвейеров должна быть предусмотрена возможность применения в доступных местах трассы конвейера механизированной уборки из-под него просыпавшегося (счищенного) груза.
В производственных зданиях галереях тоннелях и на эстакадах вдоль трассы конвейеров должны быть предусмотрены проходы для безопасного обслуживания монтажа и ремонта.
Ширина проходов для обслуживания должна быть не менее;
5 м - для конвейеров всех видов (кроме пластинчатых);
м - для пластинчатых конвейеров;
м - между параллельно установленными конвейерами;
м - между параллельно установленными пластинчатыми конвейерами.
Ширина прохода между параллельно установленными конвейерами закрытыми по всей трассе жесткими или сетчатыми ограждениями может быть уменьшена до 07 м.
При наличии в проходе между конвейерами строительных конструкций (колонн пилястр и т. п.) создающих местное сужение прохода расстояние между конвейером и строительными конструкциями должно быть не менее 05 м на длине прохода до 10 м. Эти места прохода должны быть ограждены
На участках трассы конвейера над которыми перемещаются погрузочные и разгрузочные устройства ширина проходов с обеих сторон конвейера должна быть не менее 10 м. Требование не распространяется на ленточные конвейеры с лопастными питателями размещенные в подштабельных галереях.
Ширина проходов для монтажа и ремонта конвейеров должна быть не менее 04 м.
Высота проходов должна быть не менее:
м — для конвейеров с постоянными рабочими местами установленных в производственных помещениях;
м — для конвейеров не имеющих рабочих мест установленных в производственных помещениях;
м — для конвейеров установленных в галереях тоннелях и на
эстакадах. При этом потолок не должен иметь острых выступающих частей.
По ширине прохода вдоль трассы конвейеров размещенных в галереях имеющих наклон к горизонту 6—12° должны быть установлены настилы с поперечинами а при наклоне более 12° — лестничные марши.
Через конвейеры длиной более 20- м размещенные на высоте не более 12 м от уровня пола до низа наиболее выступающих частей конвейера в необходимых местах трассы конвейера должны быть сооружены мостики огражденные поручнями высотой не менее 10 м) м для прохода людей и обслуживания конвейеров.
Мостики через конвейеры должны размещаться на расстоянии друг от друга не более:
м — в производственных помещениях;
0 м — в галереях на эстакадах.
Мостики должны устанавливаться так чтобы расстояние от их настилов до низа наиболее выступающих строительных конструкций (коммуникационных систем) было не менее 20 м.
Ширина мостиков должна быть не менее 10 м.
Конвейеры у которых оси приводных и натяжных барабанов шкивов и звездочек находятся выше 15 м от уровня пола должны обслуживаться со стационарных или передвижных площадок. Допускается в технически обоснованных случаях сооружать площадки начиная от высоты расположения осей механизмов 18 м над уровнем пола.
Расстояние по вертикали от настила площадки до низа выступающих строительных конструкций (коммуникационных систем) должно быть не менее 20 м.
Площадки должны быть ограждены поручнями высотой не менее 10 м со сплошным закрытием высотой не менее 015 м от уровня настила.
При использовании конвейеров в комплекте с дробильно-сортировочными установками высота сплошного закрытия площадки должна быть не менее 01 м.
Лестницы переходных мостиков площадок для обслуживания
конвейеров должны иметь угол наклона к горизонту:
не более 45° — при постоянной эксплуатации;
не более 60° — при эксплуатации 1—2 раза в смену;
° — при эксплуатации не чаще одного раза в смену.
Ширина лестниц должна быть не менее 07 м. Допускается изготовлять вертикальные лестницы шириной от 04 до 06 м.
Применение вертикальных лестниц допускается только в случае невозможности размещения маршевых лестниц.
Вертикальные лестницы высотой более 2 м должны иметь
ограждение в виде дуг (хомутов) со стороны спины рабочего
перемещающегося по лестнице.
Лестницы должны быть ограждены поручнями высотой не менее 10 м.
Настилы мостиков и площадок должны быть сплошными и нескользкими.
Конструкцией конвейера должен быть предусмотрен легкий безопасный доступ к элементам блокам и контрольным устройствам требующим периодической проверки а также устройствам регулирования загрузки и разгрузки люкам управляемым вручную или механически.
2 ТРЕБОВАНИЯ К СРЕДСТВАМ ЗАЩИТЫ
Движущиеся части конвейеров (приводные натяжные и
отклоняющие барабаны натяжные устройства канаты и блоки
натяжных устройств ременные и другие передачи муфты и т.п. а также опорные ролики и ролики нижней ветви ленты в зонах рабочих мест конвейеров) к которым возможен доступ обслуживающего персонала и лиц работающих вблизи конвейеров должны быть ограждены.
Защитные ограждения должны быть снабжены приспособлениями
для надежного удержания их в закрытом (рабочем) положении
и в случае необходимости быть сблокированы с приводом
конвейера для его отключения при снятии (открытии) ограждения.
Конструкция ограждения должна быть такой чтобы его удаление или перемещение в случае необходимости было возможным лишь с помощью инструмента.
Ограждения следует изготовлять из металлических листов
сетки и других прочных материалов.
В сетчатых ограждениях размер ячейки должен быть выбран таким чтобы исключался доступ к огражденным частям конвейера.
В зоне возможного нахождения людей должны быть ограждены
смотровые люки пересыпных лотков бункеров и т. п. установленных в местах загрузки и разгрузки конвейеров периодически очищаемые обслуживающим персоналом;
проходы (проезды) под конвейерами сплошными навесами выступающими за габариты конвейеров не менее чем на 1м;
участки трассы конвейеров (кроме подвесных конвейеров) на которых запрещен проход людей при помощи установки вдоль трассы перил высотой не менее 10 м от уровня пола.
Конвейеры передвигающиеся по рельсам если они не за
крыты специальными кожухами и конвейеры установленные в
производственных зданиях ниже уровня пола должны быть ограждены по всей длине перилами высотой не менее 10 м от уровня пола.
Перила ограждающие конвейеры установленные ниже уровня пола должны быть закрыты на высоту не менее 015 м от уровня пола.
На конвейерах входящих в автоматизированные транспортные или технологические линии должны быть предусмотрены устройства для
автоматической остановки привода при возникновении аварийной ситуации.
На технологической линии состоящей из нескольких последовательно установленных и одновременно работающих конвейеров или из конвейеров в сочетании с другими машинами (питателями дробилками и т. п.) приводы конвейеров и всех машин должны быть сблокированы так чтобы в случае внезапной остановки какой-либо машины или конвейера предыдущие машины или конвейеры автоматически отключались а последующие продолжали работать до полной нагрузки с них транспортируемого груза.
Конвейеры в головной и хвостовой частях должны быть
оборудованы аварийными кнопками для остановки конвейеров.
В местах повышенной опасности конвейеры должны быть дополнительно оборудованы выключающими устройствами для остановки конвейера в аварийных ситуациях в любом месте со стороны прохода для обслуживания.
В схеме управления конвейерами должна быть предусмотрена блокировка исключающая возможность повторного включения привода до ликвидации аварийной ситуации.
На участках трассы конвейеров находящихся вне зоны видимости оператора с пульта управления должна быть установлена двусторонняя предупредительная предпусковая звуковая или световая сигнализация включающаяся автоматически до включения привода конвейера.
Двусторонняя сигнализация должна обеспечивать не только оповещение о пуске конвейера лиц находящихся вне зоны видимости с пульта управления конвейером но и подачу ответного сигнала на пульт управления с участков трассы невидимых оператору о готовности конвейера к пуску.
На рабочих местах должны быть помещены таблички поясняющие значения применяемых средств сигнализации и порядок управления конвейером.
Конвейеры транспортирующие горячие грузы должны иметь средства защиты обслуживающего персонала от ожогов.
Конвейеры предназначенные для транспортирования пылевидных пыле- паро- и газовыделяющих грузов должны снабжаться пылеподавляющими или пылеулавливающими системами в местах выделения пыли отводами к местной вытяжной вентиляции в местах выделения пара или местными отсосами для подключения абсорбционных устройств в местах выделения газа.
Конвейеры предназначенные для транспортирования мокрых грузов должны быть закрыты кожухами или щитами в местах возможного брызгообразования.
Места периодической смазки конвейеров должны быть доступны без снятия защитных устройств.
3 ТРЕБОВАНИЯ К КОНСТРУКЦИИ
В установленных на конвейерах загрузочных и разгрузочных устройствах не допускается заклинивание и зависание груза образование просыпей. Не допускается загрузка конвейера сверх расчетных норм для нормальных эксплуатационных условий.
Не допускается падение груза с конвейера или машины в местах передачи транспортируемого груза с одного конвейера на другой конвейер или машину.
Приемная часть конвейеров загружаемых вручную штучными грузами должна быть расположена на горизонтальном или наклонном участке конвейера с уклоном не более 5° в сторону загрузки.
На наклонных конвейерах (наклонных участках конвейеров) штучные грузы при транспортировании должны находиться в неподвижном состоянии по отношению к плоскости грузонесущего элемента конвейера и не менять положения принятого при загрузке.
Не допускается самопроизвольное перемещение в обратном направлении грузонесущего элемента с грузом при отключении привода в конвейерах имеющих наклонные или вертикальные участки трассы. Неприводные конвейеры (роликовые дисковые) должны иметь в разгрузочной части ограничительные упоры и приспособления для снижения скорости движущегося груза.
На трассах конвейеров с передвижными загрузочными и
разгрузочными устройствами должны быть установлены конечные
выключатели и упоры ограничивающие ход загрузочно-разгрузочных
Грузовые натяжные устройства конвейеров должны иметь концевые упоры для ограничения хода натяжной тележки и конечные выключатели отключающие привод конвейера при достижении натяжной тележкой крайних положений.
Наклонные и вертикальные участки цепных конвейеров должны быть снабжены ловителями для захвата цепи в случае ее обрыва угрожающего обслуживающему персоналу.
В конструкциях составных частей конвейеров массой более
кг подлежащих подъему или перемещению грузоподъемными
средствами при транспортировании монтаже демонтаже и
ремонте должны быть предусмотрены соответствующие приливы
отверстия или рым-болты если без них применение стропов и других такелажных средств является опасным.
Шумовые характеристики конвейеров не должны превышать указанные в ГОСТ 12.1.003—83.
Вибрационные характеристики на рабочих местах обслуживания конвейеров — по ГОСТ 12.1.012-90.
Концентрация вредных веществ в воздухе рабочей зоны обслуживания конвейеров находящихся в помещении и предназначенных для транспортирования грузов выделяющих вредные вещества не должна превышать значений установленных ГОСТ 12.1.005-88.
Требования к электрооборудованию монтажу электрических цепей и заземлению конвейеров установлены в соответствии с «Правилами устройства электроустановок» ТКП 181-2009 «Правила технической эксплуатации электроустановок потребителей».
Неисправности электрооборудования могут стать источником возникновения пожароопасной ситуации. Поэтому вблизи пульта управления предполагается установка пожарного стенда с набором первичных средств пожаротушения в том числе огнетушителя углекислотного которым разрешается тушить электрооборудование без отключения от сети [19].
В представленном дипломном проекте был разработан грузоведущий конвейер для сборки коробок передач тракторов МТЗ.
Конвейер проектировался с учётом современных требований к подъемно-транспортным машинам.
Компоновка конвейера производилась исходя из анализа самых последних разработок ведущих мировых и отечественных производителей подъемно-транспортной техники.
При сравнительно небольшом принципиальном изменении конструкции значительно усложняются задачи возлагаемые на грузоведущие тележечные конвейеры возрастают их параметры – протяженность скорость производительность полезные нагрузки; резко увеличивается их производственное значение.
Благодаря пространственной гибкости пути конвейер может обслуживать большое количество транспортно-технологических операций в одном или нескольких цехах расположенных на различных этажах.
При такой трассе конвейер не загромождает производственную площадь цеха оставляет свободными проходы и проезды и легко обходит встречающиеся на его пути препятствия не нарушая производственную работу цеха и предприятия.
Характерной особенностью данной конструкции грузоведущего тележечного конвейера является наличие усовершенствованной тележки с кантователем что позволяет увеличить производительность при всборе коробок передач и уменьшить эксплуатацию ручного труда при погрузочно-разгрузочных работах. Также конвейер снабжен предохранительным устройством для предотвращения поломке привода.
По моему мнению данный тип машин будет пользоваться спросом как у нас в стране так и зарубежом.
СПИСОК ИСПОЛЬЗОВАННЫХ ИСТОЧНИКОВ
Дьячков В.К. Грузоведущие конвейеры. Изд.3-е перераб. и доп. М.Машиностроение 1976 253 с.
ГПИ Союзпроммеханизация. Конвейеры грузоведущие оборудование. Сб. Н6-72 ч. 2. М. ОТИ СПМ 1972 21 с
ГПИ Союзпроммеханизация. Конвейеры грузоведущие оборудование. Сб. Н6-72 ч. I. M. ОТИ СПМ 1972 76 с.
Ратнер И. Я. Проектирование конвейеров. М. «Машиностроение» 1969 142 с
ВНИИПТМАШ. Оборудование грузоведущего конвейера. Альбом № 1. М изд. ВНИИПТМАШа 1973 44 с
Ивашков И. И. Исследование работы тяговых цепей. ВНИИПТМАШ 1958 90 с
Дьячков В. К Исследование прочности и жесткости кронштейнов каретки конвейера. Труды ВНИИПТМАШа 1967 вып. 5 (78) с. 64—83.
Дьячков В. К. Заводские испытания конвейеров с многодвигательным приводом. Сб. № 22. М. ОНТИ ВНИИПТМАШ 1958 с. 125—136.
Чусов В. И. Толкающие конвейеры.— «Механизация и автоматизация производства» 1962 № 5 с. 12—19.
Крячко С. Н. Толкающие конвейеры с автостопом. Обзорная информация. Сб. 6-72-37. М. НИИИНФОРМТЯЖМАШ 1972 29 с
ВНИИПТМАШ. Расчеты грузоведущих конвейеров Изд. 3-е. М. «Машиностроение» 1971 357 с.
Анурьев В.И. Справочник конструктора-машиностроителя. В 3 т. Т 1. М. :Машиностроение.1985.496 с. ил.
Анурьев В.И. Справочник конструктора-машиностроителя. В 3 т. Т 3 М. :Машиностроение.1985.560 с. ил.
Справочник технолога-машиностроителя. В 2-х т. Т. 2 Под ред. А. Г. Косиловой и Р. К. Мещерякова. – 4-е изд. перераб. и доп. – М.: Машиностроение 1986. 496 с. илъ
Панов А.А. Аникин В.В. и др. Обработка металлов резанием Справочник технолога М.: "Машиностроение"1988г
Косилова А.Г. Мещерякова Р.К. Справочник технолога-машиностроителя Т1-2М.: "Машиностроение"1986г.
Нефедов Н.А. Осипов К.А. Сборник задач и примеров по резанию металлов и режущему инструменту – 5е изд. перераб. и доп. - М.: Машиностроение 1990. 489 с. ил.
Арсёнов В. В. Учебно-методическое пособие «Технико-экономическое обоснование инвестиционных проектов нового изделия». Мн. 2001.
ГОСТ 12.2.022-80 “Конвейеры. Общие требования безопасности”
(Комплект документов на технологический процесс изготовления сектора)
Спецификация - Общий вид.dwg

средней части (L=2450)
средней части (L=1300)
средней части (L=2500)
Механизм позиционной
Стойка промежуточная
Болт М12-6gх40.58.019
Лист 2 ГОСТ 19903-74
Лист 3 ГОСТ 19903-74
Лист 5 ГОСТ 19903-74
Подставка.dwg

Максимальный крутящий момент привода
Максимальный допустимый крутящий
Максимальный допустимый крутящий момент на
*Размеры для справок.
Все резьбовые поверхности покрыть тонким
слоем солидола марки "С" ГОСТ 4366-76.
Покрытие: грунтовка ГФ-021 ГОСТ 25129-82эмаль ПФ-115
ГОСТ 6465-76. Подготовку поверхностей и окраску производить по
Остальные ТТ по СТБ 1022-96
Техническая характеристика
Технические требования