Гравитационный бетоносмеситель с объёмом замеса 5 м3




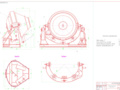
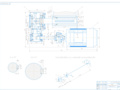
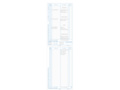
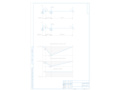
- Добавлен: 25.10.2022
- Размер: 2 MB
- Закачек: 2
Описание
Состав проекта
![]() |
![]() ![]() ![]() |
![]() |
![]() ![]() ![]() ![]() |
![]() ![]() |
![]() ![]() ![]() ![]() |
![]() ![]() |
![]() ![]() ![]() ![]() |
![]() ![]() |
![]() ![]() |
![]() ![]() ![]() ![]() |
![]() ![]() |
Дополнительная информация
СБ-103.00.000.000 ПЗ.docx
1.Гравитационные бетоносмесители3
3.Классификация бетоносмесителей7
Общий расчёт гравитационного бетоносмесителя10
1.Расчёт геометрических размеров барабана10
2.Частота вращения барабана10
3.Определение требуемой мощности11
4.Производительность бетоносмесителя13
Расчёт привода вращения барабана15
1.Расчёт передаточных чисел привода16
2.Силовые параметры привода16
3.Материалы и допускаемые напряжения зубчатых колёс18
4.Определение межосевых расстояний зубчатых колёс19
5.Уточнение геометрических параметров зубчатой передачи20
6.Проверка прочности зубчатых колёс23
7.Расчёт валов и выбор подшипников25
9.Выбор посадок для сборки29
Расчёт тихоходного вала на моменты изгиба и кручения30
1.Определение реакций опор31
2.Построение эпюр и определение опасного сечения вала33
Список использованной литературы37
Цементобетон является ведущим материалом в строительстве: его широко применяют в различных промышленных коммунальных гидротехнических дорожных и других сооружениях. Из него выполняют монолитные (изготовленные на месте строительства) сборные (изготовляемые индустриальным способом) элементы различных сооружений (фундаменты колонны перекрытия и др.) дорожные и аэродромные покрытия. Широкое применение бетона в разнообразных областях строительства объясняется тем что изделию из него можно придавать требуемые свойства и размеры вид поверхности а также тем что бетонные работы можно выполнить в короткие сроки и в любое время года. Основную массу компонентов бетона составляют заполнители которые в большинстве случаев представляют собой местные материалы или отходы производства.
Для обеспечения строительных объектов и заводов железобетонных изделий бетонной смесью и раствором промышленность выпускает
как отдельные виды оборудования так и комплексы в виде бетоносмесительных установок. Бетоносмесители входят в комплект оборудования бетонных заводов или бетоносмесительных цехов заводов ЖБИ. В бетоносмесителях используется механический способ приготовления смесей.
Промышленностью выпускаются гравитационные бетоносмесители циклического действия (БГЦ) с объёмом по загрузке 100 ÷ 3000 л
и непрерывного действия которые используются на заводах большой производительности (св. 100 м ч). В данной курсовой работе спроектирован гравитационный бетоносмеситель циклического действия с большим объёмом замеса по сравнению с существующими прототипами цель проектирование – повышение производительности заводов ЖБИ.
Выбор базовой машины
1.Гравитационные бетоносмесители
Для приготовления бетонов и растворов методом смешивания исходных материалов (щебня песка цемента воды и др.) применяют различные растворо- и бетоносмесители. Основные факторы определяющие принцип
их действия конструкцию и параметры – состав и свойства требуемой смеси технологи.
Бетоносмеситель – технологическое средство предназначенное
для приготовления бетонных иили растворных смесей состоящих из цемента наполнителей твердых добавок и воды.
Гравитационные смесители работают за счет естественного падения смеси (под действием силы тяжести) во вращающемся барабане. Лопатки закрепленные на внутренних стенках барабана не позволяют частицам компонентов скользить по стенкам при вращении а поднимают
их над горизонтом на угол трения между средами и сбрасывают с поднятой высоты за счет чего и обеспечивается перемешивание. При этом образуются определенные радиальные и осевые потоки движения смеси благодаря чему различные частицы материала равномерно перераспределяются по объему замеса. Однородность смеси обеспечивается при 30 – 40 циклах подъема
Гравитационные бетоносмесители непрерывного действия обычно имеют цилиндрический барабан с горизонтальной осью. Такие смесители непрерывно загружают сверху через загрузочную воронку готовая смесь также непрерывно выгружается с противоположного конца. Производительность регулируют меняя производительность дозаторов.
Такие бетоносмесители хорошо зарекомендовали себя при приготовлении смеси одной марки. При переналадке на смесь новой марки они уступают
смесителям циклического действия. Бетоносмесители изготовляют
с наклоняющимися и ненаклоняющимися барабанами. Смесительные барабаны могут быть грушевидной конусной и цилиндрической формы.
Устройства гравитационного бетоносмесителя цикличного действия представлено на рисунке 1.1.
Рисунок 1.1. Устройство гравитационного бетоносмесителя
Бетоносмеситель с грушевидным барабаном устроен следующим образом. Отдозированные сыпучие материалы поступают в загрузочный ковш который перемещается по направляющим. Ковш поднимается канатом проходящим по отклоняющемуся блоку на полиспаст состоящий
из неподвижной и подвижной обоймы блоков которая перемещается гидроцилиндром. При взаимодействии нижних роликов ковша с упором установленным в направляющих днище ковша открывается и образуется лоток по которому материалы поступают в смесительный барабан установленный на траверсе которая пальцами опирается на стойки прикрепленные к раме. Вращение барабану передается двигателем через редуктор размещенный в траверсе. Готовая смесь выгружается при наклоне барабана в результате поворота траверсы гидроцилиндром зубчатым сектором и шестерней насаженной на палец траверсы. Смеситель оборудован гидроприводом состоящим из двигателя гидронасоса и распределительной арматуры.
По способу выгрузки гравитационные смесители бывают: опрокидными в которых выгрузка замеса осуществляется наклоном барабана в сторону выгрузочного отверстия; реверсивными выгружаемыми
в результате обратного вращения что обеспечивает движение материала
в сторону выгрузочного отверстия; с вводным лотком по которому смесь выгружается из барабана.
На сегодняшний день наибольшее распространение получили бетоносмесители цикличного действия. В бетоносмесителях цикличного действия загрузка компонентов производится после выгрузки готового бетона. Поэтому в отличие от смесителей непрерывного действия работу цикличных смесителей можно разбить на три этапа (цикла): загрузка компонентов смеси; смешивание; выгрузка готового материала. В таблице 1.1 представлены характеристики существующих гравитационных бетоносмесителей цикличного действия.
В качестве прототипа будет выбран бетоносмеситель СБ-103
по наибольшему объёму замеса среди существующих.
Бетоносмеситель СБ-103 входит в комплект оборудования бетонных заводов и установок и бетоносмесительных цехов заводов железобетонных изделий. Бетоносмеситель состоит из рамы опорных стоек смесительного барабана траверсы привода вращения барабана и пневмоцилиндра
для опрокидывания барабана.
Смесительный барабан представляет собой металлическую емкость
в виде двух конусов соединенных цилиндрической обечайкой внутренняя поверхность которой снабжена футеровкой из сменных листов
из износостойкой стали. В барабане на кронштейнах закреплены три передние и три задние лопасти. К цилиндрической обечайке барабана с внешней стороны на прокладках приварен зубчатый венец и к торцу переднего конуса фланец.
Характеристики гравитационных бетоносмесителей цикличного действия
Модель бетоносмесителя
Вместимость по загрузке
Объём готового замеса
Частота вращения барабана
Наибольшая крупность заполнителя мм
Производительность техническая
Мощность электродвигателя
Траверса представляет собой сварную конструкцию коробчатого сечения выполненную в виде полукольца с цапфами на концах. Цапфы
с подшипниками закреплены на стойках и служат для поворота смесительного барабана. На траверсе смонтированы опорные и поддерживающие ролики обеспечивающие вращение и удержание барабана при разгрузке. На наружной стенке левой стойки установлен - пневмопривод. На правой стойке находится выводная коробка и два конечных выключателя крайних положений барабана. Опорный ролик вращающийся в подшипниках установлен
на эксцентриковой оси позволяющей регулировать положение роликов
для нормального зацепления шестерни и зубчатого венца при монтаже
и изнашивании роликов. Оси установлены на двух опорах и крепятся к стойке траверсы болтами. Поддерживающие ролики также смонтированы
в подшипниках на эксцентриковых осях позволяющих регулировать зазор между коническими поверхностями зубчатого венца и ролика. Для смещения ролика в осевом направлении предусмотрены регулировочные шайбы.
Описание пневмокинематической схемы СБ-103: двухступенчатый редуктор закреплен на вертикальной стенке траверсы. Движение
от электродвигателя через муфту и редуктор передается шестерне и зубчатому венцу барабана.
Пневмопривод служит для опрокидывания барабана при разгрузке готовой смеси возврата и фиксации его в рабочем положении и заключает
в себя пневмоцилиндр воздухораспределитель маслораспределитель запорный вентиль резинотканевые рукава и трубы. Пневмоцилиндр выполнен с тормозным устройством позволяющим изменять скорость движения поршня в конце опрокидывания и подъема барабана.
3.Классификация бетоносмесителей
Смесители классифицируют по ряду признаков (рисунок 1.2). Смесители бывают стационарными и передвижными. Передвижные смесители применяют на объектах с небольшими объемами работ стационарные – на заводах. По способу смешивания различают смесители принудительного действия и гравитационные. Принудительное смешивание осуществляется при вращении лопастей или других элементов в неподвижной емкости – барабане а в гравитационных смесителях – в результате подъема
и сбрасывания смеси внутри вращающегося барабана (рисунок 1.3).
Гравитационные смесители проще по конструкции и способны перемешивать бетоны с более крупным заполнителем. По режиму работы смесители бывают цикличного и непрерывного действия. Смесители цикличного действия работают последовательными циклами.
Рисунок 1.2. Классификация смесителей
Рисунок 1.3. Схемы смесителей:
На рисунке 1.3 представлено: а) гравитационного (барабанного)
в положении I смешивания и II разгрузки; б) принудительного действия
с вертикально расположенным центральным валом привода и соединенными с ним лопастями (тарельчатыми); в) тарельчатого роторно-планетарного
с вертикально расположенным центральным валом привода и соединенными с ним лопастями и дополнительным валом с лопастями и приводом вращения от центрального вала через планетарный редуктор; г) и д) принудительного действия (лопатковые) с горизонтально расположенными смесительными валами соответственно одновального и двухвального; е) принудительного действия; ж) гравитационного действия (корпус 1 вращающийся
с закрепленными на его внутренней поверхности лопастями 2); 1 – корпус;
– лопасть; 3 – загрузка материала; 4 – выгрузка смеси.
Общий расчёт гравитационного бетоносмесителя
1.Расчёт геометрических размеров барабана
Принимаем форму барабана двухконусную с центральной цилиндрической частью тип бетоносмесителя Б (рисунок 2.1).
Геометрические размеры барабана зависят от диаметра цилиндрической части. Величина диаметра цилиндрической части барабана определяется
где – объём загрузки компонентов в барабан смесителя согласно теме курсовой работы
При проектировании рекомендуется задаться следующими параметрами: число лопастных пар – три; вид потокообразования – перекрестный; форма лопастей - плоская; угол установки горловинной лопасти ; угол установки донной лопасти – ; угол между образующими переднего конуса и осью вращения барабана- ; угол между осью вращения барабана и образующими переходного конуса днища –
В таблице 2.1 представлены геометрические размеры барабана и их зависимость от диаметра цилиндрической части.
2.Частота вращения барабана
Частоту вращения смесительного барабана определяют исходя
из условия предотвращения отрицательного влияния центробежных сил прижимающих частицы смешиваемых компонентов к стенкам барабана.
В ходе решения уравнения равновесия частицы лежащей
на поверхности лопасти выводится приближённая формула для определения частоты вращения барабана.
Геометрические размеры барабана
Диаметр заднего закрытого торца
Диаметр переднего открытого загрузочного торца
Длина цилиндрической части
Длина заднего конуса
Длина переднего конуса
Высота лопасти от поверхности барабана в цилиндрической части
Формула для определения скорости вращения барабана принимает вид:
3.Определение требуемой мощности
Мощность электродвигателя привода вращения барабан
с перемешиваемой смесью расходуется на подъем материала во вращающемся барабане и на преодоление трения в его механизмах вращения:
где – сила требуемая на подъем материала во вращающемся барабане кВт; – сила требуемая на преодоление трения в механизмах вращения барабана кВт; – окружная скорость бандажа ;
Сила требуемая на подъем материала во вращающемся барабане определяется из условия что число циркуляций смеси за один оборот барабана равно двум:
где – вес бетонной смеси Н; – внутренний радиус барабана .
Вес бетонной смеси определяется по формуле:
где – плотность бетонной смеси ; – ускорение свободного падения .
Определим силу требуемую на подъем материала во вращающемся барабане по формуле 2.4:
Сила требуемая на преодоление трения в механизмах вращения барабана определяется по формуле:
где – вес барабана ; – радиус опорного ролика ; – радиус бандажа ;
– коэффициент (плечо) трения качения ; – угол установки опорных роликов на траверсе бетоносмесителя .
Теперь согласно формуле 2.3 определим требуемую мощность электродвигателя:
По полученной требуемой мощности по ГОСТ 19523-74 выбираем электродвигатель с ближайшей большей мощностью.
Выбираем электродвигатель фланцевый 3-х фазный с короткозамкнутым контуром серии 4А250 типоразмера 4А250М8У3 его технические характеристики представлены в таблице 2.2.
Технические характеристики электродвигателя
Номинальная частота вращения обмин
Номинальный крутящий момент
Диаметр выходного вала
Длина выходного вала
4.Производительность бетоносмесителя
Вначале определим часовую производительность циклического гравитационного бетоносмесителя по формуле:
где – количество замесов в час; – коэффициент использования смесителя по времени .
Количество замесов в час рассчитывается по формуле:
где – длительность цикла с.
Длительность цикла представляет собой сумму времени затрачиваемого на каждый цикл:
где – время загрузки барабана ; – время перемешивания
; – время разгрузки барабана ; – время возврата барабана ; – коэффициент времени перемешивания .
Тогда длительность цикла:
Определим количество замесов в час по формуле 2.8:
Тогда часовая производительность согласно формуле 2.7 равна:
Далее определим сменную производительность бетоносмесителя:
где – количество часов в смене .
Годовая производительность рассчитывается по формуле:
где – количество смен в сутки ; – количество рабочих дней в году .
Расчёт привода вращения барабана
Рисунок 3. 1. Кинематическая схема бетоносмесителя
Привод бетоносмесителя состоит из электродвигателя втулочно-пальцевой упругой муфты между редуктором и электродвигателем двухступенчатого цилиндрического прямозубого редуктора на конце тихоходного вала которого установлена прямозубая шестерня которая передаёт крутящий момент зубчатому венцу барабана. Двухступенчатый редуктор закреплен на вертикальной стенке траверсы.
1.Расчёт передаточных чисел привода
Общее передаточное число привода определяется по формуле:
Рассчитаем передаточное число для каждой ступени приняв для третьей ступени .
Передаточное число двухступенчатого закрытого редуктора определим из выражения:
Передаточное число тихоходной ступени редуктора найдём
Передаточное число первой быстроходной ступени привода редуктора:
Далее вычислим мощности числа оборотов угловые скорости
и крутящие моменты на всех зубчатых колёсах привода.
2.Силовые параметры привода
Мощность каждого зубчатого колеса будет рассчитываться по формуле:
Число оборотов определяется согласно формуле:
где – число оборотов зубчатого колеса.
Крутящий момент определяется зависимостью:
По формулам 3.2 – 3.4 определим мощность число оборотов и крутящий момент для каждого зубчатого колеса:
Зубчатые колёса 2 и 3 находятся на одном валу следовательно
их силовые параметры равны.
Зубчатые колёса 4 и 5 находятся на одном валу следовательно
Результаты расчётов сведены в таблицу 3.2.
Предварительные силовые параметры привода
3.Материалы и допускаемые напряжения зубчатых колёс
Для колёс закрытого зубчатого редуктора выбираем материалы представленные в таблице 3.3.
Материалы для зубчатых колёс редуктора
Вычислим допускаемые контактные напряжения для первой пары зубчатых колёс:
Допускаемые напряжения изгиба для каждой шестерни и каждого колеса зубчатых пар закрытого редуктора определяются по формулам:
Для шестерни напряжение изгиба согласно равенству 3.6:
Для колеса согласно формуле 3.7 напряжение изгиба равно:
Для пары шестерня – венец выбранные материалы представлены
Определим контактные напряжения и допускаемые напряжения изгиба для третьей пары:
Материалы для третьей пары зубчатых колёс
4.Определение межосевых расстояний зубчатых колёс
В приводе барабана бетоносмесителя рекомендуется применять прямозубые зубчатые колёса. Для каждой пары зубчатых колёс межосевое расстояние вычисляется по формуле:
Для первой пары зубчатых колёс межосевое расстояние равно:
5.Уточнение геометрических параметров зубчатой передачи
Зададим число зубьев ведущего колеса первой пары и ведущего колеса второй пары . Тогда число зубьев ведомых колёс
тех же пар будут равны:
При расчёте количества зубьев округляя их до целого значения изменились передаточные числа ступеней которые необходимо уточнить:
Далее следует вычислить модули зацепления и подобрать ближайшие значения согласно ГОСТ 9563-60:
Для пары 3 модуль зацепления рассчитывается по другой формуле:
Округляем оба модуля до ближайшего стандартного значения:
Зная модули числа зубьев вычислим делительные диаметры зубчатых колёс:
Определим уточнённые межосевые расстояния привода по формуле:
Определим ширину каждого зубчатого колеса. Вначале определяется ширина ведомого колеса по формуле:
Ширина ведущего зависит от ширины ведомого и определяется по формуле:
Для первой зубчатой пары:
Для второй зубчатой пары:
Для третьей зубчатой передачи:
Для дальнейших расчётов нам понадобятся диаметры вершин зубчатых колёс и диаметры окружностей впадин:
Сведём все рассчитанные данные передач в таблицу 3.5.
Геометрические размеры цилиндрических колёс
Диаметр делит. окруж.
Диаметр окруж. впадин
Диаметр окруж. вершин
6.Проверка прочности зубчатых колёс
В процессе расчёта геометрических параметров передачи производились округления. После данной операции необходимо совершить проверочный расчёт зубьев зубчатых колёс по контактным напряжениям
и напряжениям изгиба.
Контактные напряжения определяются по формуле для каждой пары:
Напряжения изгиба вычисляются по формуле для зубьев каждого зубчатого колеса:
где – окружные усилия зубчатой пары Н; – коэффициент зацепления .
Окружные усилия зубчатой пары определяется как отношение удвоенного наибольшего крутящего момента в паре к делительному диаметру выбранного колеса:
Определим напряжения для первой пары по формулам 3.17 – 3.19:
Условия прочности соблюдены.
Напряжения для второй пары:
Напряжения для третьей пары:
Согласно результатам расчётов можно сделать вывод о том
что контактные напряжения и напряжения изгиба не превышают предельно допустимых кроме того имеется достаточный запас прочности.
7.Расчёт валов и выбор подшипников
Диаметр валов определяется исходя из допускаемого напряжения кручения и крутящего момента на нём:
где – допускаемое напряжение кручения
Валы располагаются в корпусе редуктора в подшипниках диаметры цапф определяется по формуле:
где – высота заплечика подшипника выбирается по таблице сходя
от размера вала. Следует учесть что на валу 3 будут стоять два различных подшипника ближе к выходу вала нагрузка на подшипники будет выше
для обеспечения надёжности рассчитывается диаметр цапфы вала
в зависимости от фаски подшипника и по полученному значению выбирается второй подшипник.
Высота заплечика подшипника и координата фаски подшипника r
Диаметр вала под зубчатым колесом определяется по формуле:
Длина валов зависит от наибольшего расстояния между внешними поверхностями вращающихся деталей редуктора которая определяется
Определим зазор между вращающимися деталями и внутренними стенками корпуса редуктора:
Расстояние между торцовыми поверхностями колёс редуктора рассчитывается по формуле:
Определим геометрические размеры вала 1 по формулам 3.20 – 3.22:
Округляем полученные значения до ближайшего размера согласно ГОСТ 6636-69. Диаметр цапфы округляем до ближайшего размера внутреннего диаметра выбираемого подшипника по ГОСТ 8338-75.
Принимаем: Длина выходного конца быстроходного вала:
Аналогично определим геометрические размеры вала 2 и 3:
под шестерню определяется зависимостью
Принимаем: . Длина выходного конца вала 3 определяется как:
На рисунках 3.2 – 3.4 представлены эскизы валов сведём расчётные данные валов в таблицу 3.7.
Рисунок 3.2. Быстроходный вал редуктора (Вал 1)
Рисунок 3.3. Промежуточный вал редуктора (Вал 2)
Рисунок 3.4. Тихоходный вал редуктора (Вал 3)
Так же необходимо знать диаметр и длину заплечника второго подшипника на валу 3 которые определяются зависимостями:
На основании геометрических размеров валов выбираем подшипники качения по ГОСТ 8338-75 данные подбора сведены в таблицу 3.8.
Геометрические размеры валов
Диаметр вала под колесомшестер.
Длина выход. концов вала мм
Вспомогательные размеры мм
Характеристики выбранных подшипников
Диаметры цапфы вала
Подшипники шариковые
радиальные однорядные
Наружный диаметр подшипника
Тип присоединения колёс к валам является шпоночный.
По ГОСТ 23360-78 подберём размеры шпонок и занесём результаты
Выбор муфты осуществляется по расчётному крутящему моменту передаваемого муфтой и диаметром соединительных валов.
Расчётный крутящий момент муфты рассчитывается по формуле:
где – коэффициент запаса .
Выбираем муфту упругую втулочно-пальцевую по ГОСТ 21424-93
с номинальным крутящим момент одна из полумуфт
диаметром 75 исполнения 1 вторая диаметром 65 исполнения 2:
МУВП 710-75-1-65-2 ГОСТ 21424-93.
9.Выбор посадок для сборки
Для обеспечения условия сборки конструкции цилиндрического редуктора назначаем посадки результаты выбора занесены в таблицу 3.10.
Посадки для сбора деталей
Цилиндрическое колесо – вал
Крышка подшипника сквозная – корпус редуктора
Крышка подшипника глухая – корпус редуктора
Наружное кольцо подшипника – корпус редуктора
Внутреннее кольцо подшипника – вал
Расчёт тихоходного вала на моменты изгиба и кручения
Сведём необходимые для расчёта данные в таблицу 4.1.
Данные для расчёта тихоходного вала
Механические характеристики
Временное сопротивление
Допускаемое напряжение при кручении
Предел выносливости при растяжении
Предел выносливости при кручении
Крутящий момент на валу
Силы действующие на колесо 4
Силы действующие на колесо 5
Расстояния между опорами и мест приложения сил
От середины первого подшипника вала (А) до середины колеса 4
От середины колеса 4 до середины второго подшипника вала (B)
От середины второго подшипника вала до середины зубчатого колеса 5
На рисунке 4.1 представлена схема действующих на вал сил и крутящего момента в изометрии.
Рисунок 4.1. Схема действующих на вал сил и крутящего момента
1.Определение реакций опор
Определим реакции опор в плоскости 0yz (рисунок 4.2) из условия
что сумма моментов равна нулю.
Рисунок 4.2. Схема нагрузок на вал в плоскости 0yz
Необходимо сделать проверку сумма всех сил должна равняться нулю:
Сумма сил равна нулю реакции опор определены верно.
Далее по аналогии определим реакции опор в плоскости 0xz
Рисунок 4.3. Схема нагрузок на вал в плоскости 0xz
2.Построение эпюр и определение опасного сечения вала
По полученным данным выполняем построение эпюр
Для построения эпюры горизонтальной плоскости необходимо определить моменты в характерных точках а именно в сечении вала
под колесом 4 и в точке B:
Для построения эпюры вертикальной плоскости также необходимо определить моменты в тех же характерных точках:
Эпюра крутящих моментов располагается между зубчатым колесом 4
и 5 так как скручивается только этот участок.
Построенные эпюры изгибающих и крутящего моментов представлены на рисунке 4.4.
Рисунок 4.4. Эпюры изгибающих и скручивающих моментов
Анализируя характер эпюр определяем что опасным в данном случае является сечение вала в точке B так как в этом сечении все моменты наибольшие.
Определяем приведённый суммарный момент в опасном сечении:
3.Проверка прочности вала по его диаметру
Определим необходимый диаметр вала в сечении и сравним его
с полученным в третьей части курсовой работы.
Требуемые диаметр вала определяется по формуле:
где – допускаемое напряжение текучести.
Допускаемое напряжение текучести определяется как:
Тогда требуемый диаметр вала по формуле 4.1 равен:
Точка B является серединой ширины второго подшипника тихоходного вала диаметры цапфы которого что больше требуемого диаметра. Это говорит о том что диаметр вала в опасном сечении способен выдержать изгибающий момент.
В данной курсовой работе был спроектирован гравитационный бетоносмеситель циклического действия с объёмом замеса . Проектирование заключалось в увеличении производительности бетонных заводов или бетоносмесительных цехов заводов ЖБИ путём увеличения
по сравнение с существующими установками объёма замеса.
В результате расчёта производительность проектируемого бетоносмесителя составила что превышает почти в 2 раза производительность ближайшего конкурента – СБ-103 производительность которого равняется . Это говорит о том что производительность заводов ЖБИ способна увеличиться почти в 2 раза с внедрением проектируемого бетоносмесителя.
В связи с увеличением объёма замеса относительно аналога для работы устройства потребовалась большая мощность. В связи с этим был произведён расчёт привода с проверкой тихоходного вала на моменты изгиба и кручения. Расчёт показал что вал достаточно прочный и выдержит приложенные к нему силы зубчатых передач и крутящий момент.
Список использованной литературы
Баловнев В. И. Дорожно-строительные машины и комплексы: Учебник для вузов по спец. "Строительные и дорожные машины и оборудование" В. И. Баловнев А. Б. Ермилов А. Н. Новиков. – Москва: Машинстроение 1988. – 384 с.
Белецкий Б. Ф. Строительные машины и оборудование: Справочное пособие для производственников-механизаторов инженерно-технических работников строительных организаций а также студентов строительных вузов факультетов и техникумов Б. Ф. Белецкий И. Г. Булгакова В. А. Пенчук. – Ростов : Феникс 2005. – 608 с.
Борщевский А. А. Механическое оборудование для производства строительных материалов и изделий А. А. Борщевский А. С. Ильин А. Н. Новиков. – Москва : Высшая школа 1987. – 366 с.
Гоберман Л. А. Основы теории расчёта и проектирования строительных и дорожных машин: Учебник для техникумов Л. А. Гоберман Ш. М. Мерданов В. В. Шефер. – Москва : Машиностроение 1988. – 464 с.
Карнаухов Н. Н. Эксплуатация подъёмно-транспортных строительных и дорож- ных машин. Строительные машины : учебник Н. Н. Карнаухов Ш. М. Мерданов В. В. Шефер. – Тюмень : ТюмГНГУ 2012. – 456 с.
Каспер Е. А. Технология бетона строительных изделий и конструкций: методические указания к выполнению курсовой работы для обучающихся направления 08.03.01 «Строительство» Е. А. Каспер О. С. Бочкарёва В. А. Пенчук. – Тюмень : Издательский центр БИК ТюмГНГУ 2016. – 53 с.
Ким Б. Г. Строительные машины и оборудование стройиндустрии: учеб. пособие Б. Г. Ким Н. Н. Тур В. А. Пенчук. – Владимир : ВлГУ 2015. – 279 с.
Курмаз Л. В. Конструирование узлов и деталей машин: Справочное учебно-методическое пособие Л. В. Курмаз О. Л. Курмаз А. Н. Новиков. – Москва : Высшая школа 2007. – 455 с.
Лещинский А. В. Основы теории и расчета оборудования бетоносмесительных установок А. В. Лещинский А. С. Ильин А. Н. Новиков. – Хабаровск : ХГТУ 2004. – 76 с
Мерданов Ш. М. Наземные транспортно-технологические комплексы и средства: учебное пособие Ш. М. Мерданов А. А. Серебренников Д. В. Райшев. – Тюмень : ТИУ 2019. – 324 с.
Сергеев В. П. Строительные машины и оборудование: Учебник для вузов по спец. "Строительные машины и оборудование" В. П. Сергеев А. С. Ильин А. Н. Новиков. – Москва : Высшая школа 1987. – 376 с.
эпюры.dwg

Вертикальная плоскость (0yz)
СБ-103.00.000.000 ВО.dwg

Гравитационный бетоносмеситель с объёмом замеса 5 м3
Техническая характеристика Объем замеса
м3 Число циклов в час
не менее Частота вращения барабана
обмин Мощность электродвигателя
СБ-103.03.000.000 СБ.dwg

с объёмом замеса 5 м
СБ-103.03.000.000 СБ
Схема действия сил и моментов на тихоходный вал
СБ-103.03.000.000 СБ (спец).dwg

Привод гравитационного
c объёмом замеса 5 м
с объёмом замеса 5 м
СБ-103.03.001.000 СБ
Редуктор цилиндрический
смесительного барабана
Двигатель асинхронный
А250М8У3 ГОСТ19523-74
Муфта упругая втулочно-пальцевая
0-75-1-65-2 ГОСТ 21424-93
Рекомендуемые чертежи
Свободное скачивание на сегодня
- 24.01.2023