Экструдер



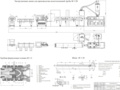
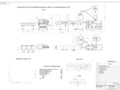
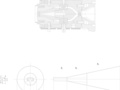
- Добавлен: 25.10.2022
- Размер: 2 MB
- Закачек: 3
Описание
Состав проекта
![]() |
![]() |
![]() ![]() ![]() ![]() |
![]() ![]() ![]() |
![]() ![]() ![]() |
![]() ![]() ![]() |
![]() ![]() ![]() |
![]() ![]() ![]() ![]() |
Дополнительная информация
Линия экструзионная, формующая головка, шнек.dwg

Пресс червячный (экструдер)
Устройство для нагрева и подсушки гранул
Устройство охладительное
Устройство тянуще-отрезное
Формующая головка М1:20
Техническая характеристика
Производительность по непластифицированному ПВХ
кгч Мощность электродвигателя
кВт Мощность электронагревателей
кВт Расход сжатого воздуха
м с Расход воды на охлаждение
мс Габаритные размеры
мм длина ширина высота Масса
014 13080 1340 3186 5485"
rryessssrrs_.docx
кафедра строительных машин автоматики и электротехники
по курсу: «Механизация и автоматизация технологии отделочных и изоляционных материалов и изделий».
тема: «Червячные формующие машины. Экструдеры».
Руководитель проекта: Чичканов В.В.
Изделие: поручень ПВХ (непластифицированный) (рис. 1). Масса: 069 кгп.м.
Рис. 1. Изделие (поручень)
-диаметр гребня Dч = 80 мм;
-отношение длины червяка к его диаметру LDч = 15;
-радиальный зазор между гребнем червяка и рабочим цилиндром = 1 мм;
-глубина винтового канала червяка h = 7 мм;
-толщина гребня e = 7 мм;
-шаг винта t = 80 мм;
-частота вращения червяка n = 05 с-1.
ПРОЕКТИРОВАНИЕ И РАСЧЕТ ОФОРМЛЯЮЩЕЙ ГОЛОВКИ ЭКСТРУДЕРА
Формующая (оформляющая) головка – это профилирующий инструмент придающий расплавленному полимеру выходящему из рабочего цилиндра экструдера необходимую форму. Внутри головки проходит канал сечение которого плавно меняется от круглого до сечения соответствующего профилю изделия на выходе.
От степени совершенства конструкции головки в значительной мере зависит точность поперечных размеров экструдируемого изделия и качество его поверхности.
Конструкция головки должна удовлетворять следующим требованиям:
)она должна способствовать формирования поперечного сечения потока соответствующего форме сечения экструдируемого изделия;
)геометрические размеры профилирующей щели и углы выхода должны обеспечивать возможность работы экструдера с максимальными значениями производительности при которых еще не наблюдается «эластической турбулентности»;
)конфигурация канала должна исключать образование в нем зон застоя;
)головка должна обладать достаточным сопротивлением чтобы на выходе из рабочего цилиндра создавалось противодавление обеспечивающее качественное смешение и гомогенизацию полимера;
)конструкция профилирующих органов должна быть достаточно жесткой чтобы при любых рабочих давлениях сечение проточной части оставалось неизменным;
)конструкция головки должна обеспечивать возможность регулирования распределения объемного расхода по периметру струи для устранения влияния неточностей расчета и изготовления на профиль экструдируемого изделия.
В простейшем случае экструзионная головка состоит из 4-х участков по ходу движения расплава: цилиндрического участка конического участка сужающегося участка (сечение плавно меняется от круглого до сечения соответствующего профилю изделия на выходе) и призматического формующего участка с постоянными размерами сечения.
Подвод расплава к формующему каналу головки должен осуществляться плавно. Каналы по которым расплав перетекает к формующей части называются подводящими они имеют переменное в направлении течения сечение. Назначение подводящих каналов состоит в преобразовании формы потока от сравнительно простой на входе (круглой овальной прямоугольной) к фигурной в месте стыка с формующей частью.
Форма и размеры подводящих каналов оказывают непосредственное влияние на качество экструдируемой заготовки.
Поверхность рабочих каналов головки кроме ее формующей зоны может быть гладкой или с винтовой нарезкой позволяющей улучшить процесс гомогенизации расплава.
Для получения качественных изделий необходимо чтобы заключительный отрезок пути расплав перемещался некоторое время по каналу с постоянными размерами сечения. В этом случае происходит наиболее полное выравнивание скоростей движения расплава проходят релаксационные процессы ликвидируется пульсация и т. д.
Расчетная схема канала оформляющей головки приведена на рис. 2 3.
Рис. 2. Расчетная схема канала оформляющей головки
Рис. 3. Расчетная схема канала оформляющей головки
Сечение канала на выходе оформляющей головки экструдера приведено на рисунке 4.
Рис. 4. Сечение канала на выходе оформляющей головки
При конструировании проводящего канала головки для расчетов используются уравнения течения ньютоновской или неньютоновской жидкости через каналы различного поперечного сечения. Выбор вида уравнения зависит от конкретных целей расчета наличия сведений о реологических свойствах материала а также границ применения выбранного уравнения течения.
Перепад давления в канале заданной геометрии определяется на основе формул гидравлики для вязких жидкостей:
сопротивление канала течению (геометрический фактор) см-3;
объемный расход см3с;
эффективная вязкость (реологический фактор) кгссм2.
Сопротивление канала течению см-3:
где – коэффициент геометрической формы канала см3.
Сложная геометрическая форма канала головки условно разбивается на части наиболее характерные и простые по геометрической форме: цилиндр конус кольцо и т.п. Значение коэффициента геометрической формы рассчитывается для каждого участка канала затем вычисляется суммарный коэффициент.
Общий коэффициент геометрической формы канала см3:
коэффициенты геометрической формы отдельных участков канала см3.
Коэффициент геометрической формы цилиндрического участка канала см3:
Коэффициент геометрической формы конического участка канала см3:
наибольший диаметр канала см;
наименьший диаметр канала см;
Коэффициент геометрической формы сужающегося (клиновидного) участка канала см3:
наибольшая высота канала см;
наименьшая высота канала см;
Коэффициент геометрической формы призматического формующего участка канала см3:
площадь поперечного сечения канала см2;
коэффициент формы канала; f = 095;
Общий коэффициент геометрической формы канала:
Сопротивление канала течению:
ПРОЕКТИРОВАНИЕ И РАСЧЕТ ЧЕРВЯКА
Червяк – это основной рабочий орган экструдера предназначенный для перемешивания нагрева и пластификации материала и подачи расплава под давлением в экструзионную головку.
Расчетная схема червяка приведена на рисунке 5.
Рис. 5. Расчетная схема червяка
L – длина червяка; D – диаметр гребня червяка; h – глубина винтового канала червяка;
t – шаг винта; – толщина гребня; α – угол подъема винтовой линии.
Червяк забирает непластифицированный материал (гранулы или порошок) от загрузочного отверстия пластифицирует и перемешивает его и равномерно подает в виде гомогенного расплава к оформляющей головке. В результате уплотнения из материала удаляется захваченный вместе с гранулами (или порошком) воздух и удельный объем материала уменьшается. Для компенсации уменьшения удельного объема материала канал червяка выполняется с уменьшающимся объемом витка. Поэтому глубина (h) винтового канала червяка на выходе всегда меньше чем на входе.
По характеру процессов протекающих на каждом участке червяка его можно разделить на три основные зоны:
-зона питания (или зона загрузки) – участок на котором перерабатываемый материал находится в твердом состоянии;
-зона сжатия (или зона плавления) – участок на котором почти полностью происходит плавление материала;
-зона дозирования (зона нагнетания) – участок на котором материал находится в расплавленном вязкотекучем состоянии.
Параметры червяка (по заданию):
-длина червяка Lч = 1200 мм;
-радиальный зазор между гребнем червяка и рабочим цилиндром λ = 1 мм;
-глубина винтового канала (нарезки) червяка h = 7 мм;
-толщина гребня = 7 мм;
Глубина винтового канала в начале червяка (в зоне загрузки) мм:
Глубина винтового канала в конце червяка (в зоне дозирования) мм:
где для непластифицированного ПВХ
Средняя глубина винтового канала мм:
Диаметр сердечника червяка в зоне питания мм:
Диаметр сердечника червяка в зоне нагнетания мм:
Длина зоны нагнетания (зоны дозирования) мм:
Глубина винтового канала червяка в начале зоны дозирования мм:
Диаметр сердечника червяка в начале зоны питания мм:
Угол винтовой нарезки:
РАСЧЕТ ПРОИЗВОДИТЕЛЬНОСТИ ЭКСТРУДЕРА
Определяющее влияние на производительность машины оказывает дозирующая зона червяка. Производительность дозирующей зоны сильно зависит от геометрических параметров самого червяка. Производительность же экструдера в целом зависит не только от геометрических размеров шнека и числа оборотов но и в значительной степени – от конструкции формующей головки.
На основе гидродинамического подхода к анализу взаимодействия рабочих органов с перерабатываемым материалом в дозирующей зоне экструдера принято рассматривать три составляющие потока движения расплава:
-прямой (вынужденный) поток – поток расплава движущийся по межвитковому пространству в направлении от зоны загрузки к зоне дозирования вдоль оси шнека возникающий вследствие вращения шнека относительно цилиндра;
-обратный поток поток расплава движущийся в противоположном направлении что вызвано перепадом давления по длине шнека;
-поток утечек поток утечки движущийся в зазоре между наружной поверхностью витков шнека и внутренней поверхностью материального цилиндра в направлении от зоны дозирования.
Подобное разделение на три потока в канале шнека следует считать условным так как противотока практически не существует а имеет место некоторое ограничение прямого потока возникающее в результате сопротивления головки.
Объемная производительность экструдера м3с:
коэффициент геометрической формы канала головки м3;
частота вращения червяка с-1;
константа прямого потока м3;
константа обратного потока м3;
константа потока утечек м3.
Константы прямого обратного потока и потока утечек для зоны дозирования червяка с переменной глубиной нарезки м3:
число заходов винтовой нарезки;
радиальный зазор между гребнем червяка и рабочим цилиндром м;
длина зоны нагнетания (зоны дозирования) м;
коэффициенты характеризующие конструкцию червяка;
глубина винтового канала червяка в начале зоны дозирования м;
глубина винтового канала в конце червяка (в зоне дозирования) м;
диаметр сердечника червяка в начале зоны питания м;
диаметр сердечника червяка в зоне нагнетания м;
Торнер Р.В. Акутин М.С. «Оборудование заводов по переработке пластмасс». – М.: Химия 1986.
Володин В.П. «Экструзия профильных изделий из термопластов». – СПб.: Профессия 2005.
Соколов М.В. Клинков А.С. «Автоматизированное проектирование и расчет шнековых машин». – М.: «Издательство Машиностроение - 1» 2004.
Гиберов З.Г. Вернер Е.В. «Механическое оборудование предприятий для производства полимерных и теплоизоляционных изделий». – М.: Машиностроение 1973.
Клинков А.С. Шашков И.В. «Оборудование и технология вторичной переработки отходов полимерных материалов». – Тамбов: «Издательство Тамбовского государственного технического университета» 2007.
Абраменков Э.А. «Червячные формующие машины. Экструдеры»: учебное пособие. – Новосибирск: НГАСУ (Сибстрин) 1992.
Гиберов З.Г. Журавлев М.И. «Оборудование заводов пластических масс»: атлас конструкций. – М.: Машиностроение 1973.
rryessssrrs.docx
кафедра строительных машин автоматики и электротехники
по курсу: «Механизация и автоматизация технологии отделочных и изоляционных материалов и изделий».
тема: «Червячные формующие машины. Экструдеры».
Руководитель проекта: Чичканов В.В.
ПРОЕКТИРОВАНИЕ И РАСЧЕТ ОФОРМЛЯЮЩЕЙ ГОЛОВКИ ЭКСТРУДЕРА ..
ПРОЕКТИРОВАНИЕ И РАСЧЕТ ЧЕРВЯКА
РАСЧЕТ ПРОИЗВОДИТЕЛЬНОСТИ ЭКСТРУДЕРА ..
РАСЧЕТ МОЩНОСТИ ПРИВОДА ЭКСТРУДЕРА .
ТЕХНИКА БЕЗОПАСНОСТИ .
Одним из основных методов переработки полимеров является экструзия. Экструзия (от позднелат. extrusio – выталкивание) – технология получения изделий путем продавливания расплава материала через формующее отверстие. В промышленности переработки полимеров методом экструзии изготавливают различные погонажные изделия такие как трубы листы плёнки профильные полосы оболочки кабелей и т.д.
Экструдер – машина для формования пластичных материалов путем придания им формы при помощи продавливания (экструзии) через профилирующий инструмент (экструзионную головку).
Экструдер состоит из: корпуса с нагревательными элементами; рабочего органа размещённого в корпусе; экструзионной головки; узла загрузки перерабатываемого материала; силового привода; системы задания и поддержания температурного режима других контрольно-измерительных и регулирующих устройств.
В зависимости от конструкции рабочего органа экструдеры подразделяются:
-плунжерные (поршневые);
Наибольшее распространение получили одно- и многочервячные экструдеры.
Диаметр червяка D промышленных одночервячных экструдеров равен 45-90 мм длина 15-40 D. Наблюдается тенденция к увеличению параметра LD что позволяет увеличить степень гомогенизации расплава.
Современные экструдеры оснащаются микропроцессорной техникой осуществляющей управление машиной; на многих машинах устанавливаются промышленные компьютеры с выводом на экран основных параметров процесса.
Изделие: поручень ПВХ (непластифицированный) (рис. 1). Масса: 0126 кгп.м. Площадь поперечного сечения F = 91 мм2 = 9110-5 м2.
Рис. 1. Изделие (поручень)
-диаметр гребня Dч = 80 мм;
-отношение длины червяка к его диаметру LDч = 15;
-радиальный зазор между гребнем червяка и рабочим цилиндром = 1 мм;
-глубина винтового канала червяка h = 7 мм;
-толщина гребня e = 7 мм;
-шаг винта t = 80 мм;
-частота вращения червяка n = 05 с-1.
ПРОЕКТИРОВАНИЕ И РАСЧЕТ ОФОРМЛЯЮЩЕЙ ГОЛОВКИ ЭКСТРУДЕРА
Формующая (оформляющая) головка – это профилирующий инструмент придающий расплавленному полимеру выходящему из рабочего цилиндра экструдера необходимую форму. Внутри головки проходит канал сечение которого плавно меняется от круглого до сечения соответствующего профилю изделия на выходе.
От степени совершенства конструкции головки в значительной мере зависит точность поперечных размеров экструдируемого изделия и качество его поверхности.
Конструкция головки должна удовлетворять следующим требованиям:
)она должна способствовать формирования поперечного сечения потока соответствующего форме сечения экструдируемого изделия;
)геометрические размеры профилирующей щели и углы выхода должны обеспечивать возможность работы экструдера с максимальными значениями производительности при которых еще не наблюдается «эластической турбулентности»;
)конфигурация канала должна исключать образование в нем зон застоя;
)головка должна обладать достаточным сопротивлением чтобы на выходе из рабочего цилиндра создавалось противодавление обеспечивающее качественное смешение и гомогенизацию полимера;
)конструкция профилирующих органов должна быть достаточно жесткой чтобы при любых рабочих давлениях сечение проточной части оставалось неизменным;
)конструкция головки должна обеспечивать возможность регулирования распределения объемного расхода по периметру струи для устранения влияния неточностей расчета и изготовления на профиль экструдируемого изделия.
В простейшем случае экструзионная головка состоит из 4-х участков по ходу движения расплава: цилиндрического участка конического участка сужающегося участка (сечение плавно меняется от круглого до сечения соответствующего профилю изделия на выходе) и призматического формующего участка с постоянными размерами сечения.
Подвод расплава к формующему каналу головки должен осуществляться плавно. Каналы по которым расплав перетекает к формующей части называются подводящими они имеют переменное в направлении течения сечение. Назначение подводящих каналов состоит в преобразовании формы потока от сравнительно простой на входе (круглой овальной прямоугольной) к фигурной в месте стыка с формующей частью.
Форма и размеры подводящих каналов оказывают непосредственное влияние на качество экструдируемой заготовки.
Поверхность рабочих каналов головки кроме ее формующей зоны может быть гладкой или с винтовой нарезкой позволяющей улучшить процесс гомогенизации расплава.
Для получения качественных изделий необходимо чтобы заключительный отрезок пути расплав перемещался некоторое время по каналу с постоянными размерами сечения. В этом случае происходит наиболее полное выравнивание скоростей движения расплава проходят релаксационные процессы ликвидируется пульсация и т. д.
Расчетная схема канала оформляющей головки приведена на рис. 2 3.
Рис. 2. Расчетная схема канала оформляющей головки
Рис. 3. Расчетная схема канала оформляющей головки
Сечение канала на выходе оформляющей головки экструдера приведено на рисунке 4.
Рис. 4. Сечение канала на выходе оформляющей головки
При конструировании проводящего канала головки для расчетов используются уравнения течения ньютоновской или неньютоновской жидкости через каналы различного поперечного сечения. Выбор вида уравнения зависит от конкретных целей расчета наличия сведений о реологических свойствах материала а также границ применения выбранного уравнения течения.
Перепад давления в канале заданной геометрии определяется на основе формул гидравлики для вязких жидкостей:
сопротивление канала течению (геометрический фактор) см-3;
объемный расход см3с;
эффективная вязкость (реологический фактор) кгссм2.
Сопротивление канала течению см-3:
где – коэффициент геометрической формы канала см3.
Сложная геометрическая форма канала головки условно разбивается на части наиболее характерные и простые по геометрической форме: цилиндр конус кольцо и т.п. Значение коэффициента геометрической формы рассчитывается для каждого участка канала затем вычисляется суммарный коэффициент.
Общий коэффициент геометрической формы канала см3:
коэффициенты геометрической формы отдельных участков канала см3.
Коэффициент геометрической формы цилиндрического участка канала см3:
Коэффициент геометрической формы конического участка канала см3:
наибольший диаметр канала см;
наименьший диаметр канала см;
Коэффициент геометрической формы сужающегося (клиновидного) участка канала см3:
наибольшая высота канала см;
наименьшая высота канала см;
Коэффициент геометрической формы призматического формующего участка канала см3:
площадь поперечного сечения канала см2;
коэффициент формы канала; f = 095;
Общий коэффициент геометрической формы канала:
Сопротивление канала течению:
ПРОЕКТИРОВАНИЕ И РАСЧЕТ ЧЕРВЯКА
Червяк – это основной рабочий орган экструдера предназначенный для перемешивания нагрева и пластификации материала и подачи расплава под давлением в экструзионную головку.
Расчетная схема червяка приведена на рисунке 5.
Рис. 5. Расчетная схема червяка
L – длина червяка; D – диаметр гребня червяка; h – глубина винтового канала червяка;
t – шаг винта; – толщина гребня; α – угол подъема винтовой линии.
Червяк забирает непластифицированный материал (гранулы или порошок) от загрузочного отверстия пластифицирует и перемешивает его и равномерно подает в виде гомогенного расплава к оформляющей головке. В результате уплотнения из материала удаляется захваченный вместе с гранулами (или порошком) воздух и удельный объем материала уменьшается. Для компенсации уменьшения удельного объема материала канал червяка выполняется с уменьшающимся объемом витка (с переменным шагом нарезки или с переменной глубинной нарезки).
По характеру процессов протекающих на каждом участке червяка его можно разделить на три основные зоны:
-зона питания (или зона загрузки) – участок на котором перерабатываемый материал находится в твердом состоянии;
-зона сжатия (или зона плавления) – участок на котором почти полностью происходит плавление материала;
-зона дозирования (зона нагнетания) – участок на котором материал находится в расплавленном вязкотекучем состоянии.
Параметры червяка (по заданию):
-длина червяка Lч = 1200 мм;
-радиальный зазор между гребнем червяка и рабочим цилиндром z = 1 мм;
-глубина винтового канала (нарезки) постоянная h = 7 мм;
-толщина гребня = 7 мм;
-шаг винта постоянный t = 80 мм;
-число заходов червяка
Угол винтовой нарезки:
Процессы переработки пластических масс в червячных машинах ведутся при значительных давлениях достигающих 50 МПа что определяет повышенные требования к прочностным характеристикам деталей и узлов машин.
Расчетная схема нагружения червяка приведена на рисунке 6.
Рис. 6. Расчетная схема нагружения червяка
На червяк действует аксиальная сила Р крутящий момент Мкр и равномерно распределённая нагрузка g от собственной массы червяка. Силы Р и g вызывают прогиб червяка. Задачей прочностного расчёта является проверка предварительно определённых размеров червяка и определение допустимого прогиба.
Червяк предварительно проверяется на гибкость по формуле:
коэффициент зависящий от метода крепления конечной части вала; k = 2;
радиус инерции сечения м.
Радиус инерции сечения м:
момент инерции поперечного сечения вала червяка м4;
площадь поперечного сечения червяка м2.
Момент инерции поперечного сечения вала червяка м4:
диаметр гребня червяка м;
отношение диаметров червяка;
диаметр тела червяка м;
Площадь поперечного сечения червяка в сечении А-А м2:
λ 50 следовательно расчет червяка ведется по первому варианту расчета.
Прочностной расчет производится на максимально возможные усилия возникающие в червячных машинах.
Максимальное давление () развивается червяком когда отверстие в головке закрыто и нет выхода материала из машины (производительность равна нулю).
производительность машины м3с;
константа прямого потока м3;
константа обратного потока м3;
частота вращения червяка с-1;
коэффициент формы прямого потока; ;
средняя по длине червяка вязкость перерабатываемого материала кгсм2.
Максимальное давление кгм2:
Значение средней вязкости материала определяется из соотношения:
где – перепад давления в экструзионной головке кгм2;
Максимальное осевое усилие действующее на шнек Н:
где – площадь поперечного сечения червяка м2;
где – диаметр гребня м;
Крутящий момент действующий на червяк Нм:
мощность затрачиваемая на продвижение материала по каналу червяка Вт;
Максимальные касательные напряжения на поверхности червяка Нм2:
где – полярный момент сопротивления м3;
Нормальные напряжения вызываются осевой силой и распределенной нагрузкой q. Максимальные напряжения будут возникать в месте закрепления червяка (у первого подшипника).
Нормальные напряжения Нм2:
максимальный изгибающий момент от распределенной нагрузки червяка Нм;
осевой момент сопротивления относительно нейтральной оси м3;
Максимальный изгибающий момент от распределенной нагрузки червяка Нм:
плотность материала червяка кгм3;
ускорение свободного падения мс2;
площадь поперечного сечения червяка м2;
Осевой момент сопротивления относительно нейтральной оси м3:
По третьей теории прочности:
где – допускаемое для материала и заданных условий его работы напряжение Нм2; для стали
Максимальный прогиб червяка от распределенной нагрузки q:
модуль упругости материала червяка Нм2; для стали
момент инерции сечения м4;
распределенная нагрузка от собственной массы Нм;
РАСЧЕТ ПРОИЗВОДИТЕЛЬНОСТИ ЭКСТРУДЕРА
Определяющее влияние на производительность машины оказывает дозирующая зона червяка. Производительность дозирующей зоны сильно зависит от геометрических параметров самого червяка. Производительность же экструдера в целом зависит не только от геометрических размеров шнека и числа оборотов но и в значительной степени – от конструкции формующей головки.
На основе гидродинамического подхода к анализу взаимодействия рабочих органов с перерабатываемым материалом в дозирующей зоне экструдера принято рассматривать три составляющие потока движения расплава:
-прямой (вынужденный) поток – поток расплава движущийся по межвитковому пространству в направлении от зоны загрузки к зоне дозирования вдоль оси шнека возникающий вследствие вращения шнека относительно цилиндра;
-обратный поток поток расплава движущийся в противоположном направлении что вызвано перепадом давления по длине шнека;
-поток утечек поток утечки движущийся в зазоре между наружной поверхностью витков шнека и внутренней поверхностью материального цилиндра в направлении от зоны дозирования.
Подобное разделение на три потока в канале шнека следует считать условным так как противотока практически не существует а имеет место некоторое ограничение прямого потока возникающее в результате сопротивления головки.
Объемная производительность экструдера м3с:
коэффициент геометрической формы канала головки м3;
константа потока утечек м3.
Константы прямого обратного потока и потока утечек для зоны дозирования червяка с постоянными геометрическими размерами м3:
глубина винтового канала (нарезки) м;
число заходов винтовой нарезки;
угол винтовой нарезки;
радиальный зазор между гребнем червяка и рабочим цилиндром м;
длина зоны нагнетания (зоны дозирования) м;
При плотности материала ρ = 1380 кгм3 объемная производительность экструдера кгч:
При массе изделия m = 0126 кгп.м производительность экструдера п.м.ч:
РАСЧЕТ МОЩНОСТИ ПРИВОДА ЭКСТРУДЕРА
Мощность привода потребляемая в зоне загрузки расходуется на преодоление сил трения при движении пробки материала значение её не велико (около 10% от суммарной потребляемой мощности) и им можно пренебречь. Исключение составляют червячные машины с продольными канавками на внутренней поверхности цилиндра в зоне загрузки. В этом случае потребляемая на продвижение пробки гранул мощность в 2-5 раз больше чем в машинах с гладким цилиндром.
В зоне плавления мощность затрачивается на преодоление сопротивления движению пробки в тонком слое расплава вблизи стенки цилиндра а также на преодоление сил трения пробки о сердечник червяка и витки нарезки. Следует отметить что по длине зоны плавления происходит изменение состояния перерабатываемого материала. Размеры пробки гранул непрерывно уменьшаются а сама пробка покрывается слоем расплавленного материала. Одновременно меняются теплофизические и реологические характеристики материала что вызывает определенные трудности при аналитическом описании процесса в зоне плавления.
Мощность затрачиваемая в зоне дозирования определяется суммой мощностей расходуемых на принудительное проталкивание массы по винтовому каналу червяка на срез материала в зазоре между вершиной витка нарезки и стенкой цилиндра на создание циркуляционного потока в витках нарезки червяка N3.
Мощность привода потребляемая в зоне дозирования с постоянными геометрическими размерами червяка Вт:
эффективная вязкость материала в винтовом канале кгсм2;
эффективная вязкость материала в зазоре между гребнем нарезки червяка и цилиндром кгсм2;
перепад давления в экструзионной головке кгм2;
Значением мощности N3 (на создание циркуляционного потока) в виду ее малости можно пренебречь.
Общая (технологическая) мощность затрачиваемая на продвижение материала в цилиндре червячной машины Вт:
Величины эффективной вязкости 1 и 2 для различных перерабатываемых материалов определяются по реологическим кривым в зависимости от скоростей сдвига и температуры ( = f(TS)).
Скорость сдвига в винтовом канале червяка с-1:
Скорость сдвига в зазоре между гребнем нарезки и цилиндром с-1:
Эффективная вязкость непластифицированного ПВХ (определяются по реологическим кривым):
Перепад давления в экструзионной головке кгм2:
где – перепад давления на i-том участке канала экструзионной головки кгм2.
Падение давления на i-том участке канала экструзионной головки кгм2:
объемная производительность экструдера м3с;
эффективная вязкость (реологический фактор) кгсм2.
коэффициент геометрической формы i-того участка канала м3:
Величины эффективной вязкости i определяются по реологическим кривым в зависимости от скоростей сдвига и температуры ( = f(TS)).
Скорость сдвига при движении материала через цилиндрический участок канала с-1:
Скорость сдвига при движении материала через конический участок канала с-1:
наибольший диаметр канала м;
наименьший диаметр канала м;
Скорость сдвига при движении материала через сужающийся (клиновидный) участок канала с-1:
наибольшая высота канала м;
наименьшая высота канала м;
Скорость сдвига при движении материала через призматический формующий участок канала с-1:
площадь поперечного сечения канала м2;
толщина стенки изделия м;
Общие потери давления в оформляющей головке кгм2:
Технологическая мощность экструдера:
КПД передаточного механизма установки принимается равным 08.
Требуемая мощность электродвигателя Вт:
Принимается асинхронный двигатель переменного тока 4А160М8У3. Основные характеристики электродвигателя приведены в таблице 1.
Основные характеристики электродвигателя 4А160М8У3
Синхронная частота вращения вала обмин
Номинальная мощность кВт
Требуемое передаточное отношение привода:
частота вращения вала двигателя обмин;
частота вращения червяка обмин;
ТЕХНИКА БЕЗОПАСНОСТИ
Современные экструзионные агрегаты – крайне сложные устройства. Микропроцессорные системы предназначены для непрерывного контроля и корректировки значений технологических параметров и тем не менее учитывая так называемый «человеческий фактор» при работе необходимо неукоснительно соблюдать определенные правила техники безопасности. К основным из них относятся:
Эксплуатация экструдера и всей линии допускается только после получения протоколов завершения монтажа актов сдачи-приемки актов сдаточных испытаний и работ.
При эксплуатации экструдера должен неукоснительно соблюдаться график профилактических и ремонтных действий.
Перед запуском экструдера для всех полимеров кроме полиолефинов необходимо проводить чистку цилиндра и шнека фильтра-решетки и формующей головки.
Экструдер запускают только после нагрева до заданной температуры с предварительной выдержкой при ее значении в течении 25-30 мин.
При переработке галогеносодержащих полимеров оператор экструзионной машины в обязательном порядке должен использовать индивидуальные средства защиты (респиратор противогаз перчатки)
В экструзионном помещении в обязательном порядке обеспечивается приточно-вытяжная вентиляция соответствующая установленным нормам.
Для очистки червяка головки цилиндра при проведении регламентных работ для чистки поверхностей деталей разрешается использовать только латунные или медные скребки.
Чистку оборудования производят незамедлительно после его остановки и в условиях пока оно не охладилось более чем на 10-20 градусов ниже температуры плавления (но не температуры переработки).
Запуск экструдера проводят только после прогрева до требуемых значений температур начиная с минимальной частоты вращения червяка и плавно увеличивая его до номинального значения. Технологические отходы производства следует незамедлительно направлять на повторную подготовку сырья (дробление нагрев) и переработку.
Вращение червяка в незаполненном магистральном цилиндре допускается только в течении времени предусмотренного регламентом.
При эксплуатации экструдеров и экструзионных агрегатов следует соблюдать чистоту на рабочих местах не допускать захламленности рабочей площадки соблюдать нормы свободных расстояний между соседним оборудованием.
Ремонт экструдеров и агрегатов технологических линий производят в ремонтно-механических подразделениях предприятий или их смежников.
Эксплуатация экструзионного оборудования разрешается только при получении письменных свидетельств служб контролирующих технику безопасности состояние противопожарного обеспечения соблюдения санитарных норм.
Все работники допущенные к эксплуатации экструзионных линий должны провести соответствующий инструктаж по технике безопасности с записью в журнале и росписью там инструктируемого.
Торнер Р.В. Акутин М.С. «Оборудование заводов по переработке пластмасс». – М.: Химия 1986.
Володин В.П. «Экструзия профильных изделий из термопластов». – СПб.: Профессия 2005.
Соколов М.В. Клинков А.С. «Автоматизированное проектирование и расчет шнековых машин». – М.: «Издательство Машиностроение - 1» 2004.
Гиберов З.Г. «Механическое оборудование заводов пластических масс». – М.: Машиностроение 1967.
Гиберов З.Г. Вернер Е.В. «Механическое оборудование предприятий для производства полимерных и теплоизоляционных изделий». – М.: Машиностроение 1973.
Клинков А.С. Шашков И.В. «Оборудование и технология вторичной переработки отходов полимерных материалов». – Тамбов: «Издательство Тамбовского государственного технического университета» 2007.
Абраменков Э.А. «Червячные формующие машины. Экструдеры»: учебное пособие. – Новосибирск: НГАСУ (Сибстрин) 1992.
Гиберов З.Г. Журавлев М.И. «Оборудование заводов пластических масс»: атлас конструкций. – М.: Машиностроение 1973.
Кравчик А.Э. Шлаф М.М. «Асинхронные двигатели серии 4А. Справочник». – М.: Энергоиздат 1982.
Пояснительная записка.docx
1Назначение и совершенствование процесса экструдирования4
2Конструктивные схемы шнеков экструзионных машин5
3Конструктивные схемы оформляющих головок экструдера5
4Физическая сущность процесса экструдирования5
Технологические схемы линий экструдирования7
1Конструкция экструдера7
2Схема технологической линии экструзии труб9
Определение параметров экструдера10
1Расчетная схема сил вращающегося червяка10
2Технические особенности геометрической формы канала оформляющей головки11
3Коэффициенты геометрической формы канала головки11
4Производительность экструдера12
5Мощность червячного экструдера13
6Расчет коэффициентов вязкости14
7Давление в дозирующей зоне червяка14
Техника безопасности16
В данном курсовом проекте требуется изготовить экструзионным способом трубу из композиционного материала на основе полиэтилена.
Форма и размеры трубы указаны в исходных данных.
-разработать оформляющую головку;
-определить производительность экструдера;
-мощность экструдера;
-проверить геометрическую устойчивость червяка.
Диаметр червяка (D) – 008 м;
LD=25 длина транспортирования (L) – 2 м;
Радиальный зазор между гребнем червяка и цилиндром () – 0001 м;
Ширина гребня (e) – 0007 м;
Шаг винтового канала (t) – 0.075 м;
Глубина винтового канала (h) – 0007 м;
Частота вращения канала (n) – 05 с-1;
Рисунок 1 – Схема рабочих зон червяка
Изделие труба П14 диаметром D=32 мм и d=248мм по ГОСТ 18599-2001;
Масса (m) – 0329 кгп.м.;
Материал полиэтилен ρ=950 кгм3.
Рисунок 2 – Труба П 14
Назначение принципиальные схемы и процесс экструдирования
1Назначение и совершенствование процесса экструдирования
Экструзия – процесс получения из исходного полимерного материала (в виде гранул порошка или расплава) изделия заданной формы путём непрерывного продавливания расплава полимера через формующую головку с последующим охлаждением изделия. Экструзией получают листы трубы плёнки прокладки поручни для лестниц и другие профили. Метод экструзии применяется так же для нанесения полимерной изоляции на провода и кабели для покрытия полимерными материалами бумаги картона фольги и т.п. Получение гранулированных пластмасс моноволокон сеток также основано на экструзии расплавов полимеров.
Основными параметрами экструзии являются: температура расплава в цилиндре и формующей головке; давление расплава в головке; частота вращения червяка. Режим экструзии зависит от многих факторов: вид термопласта его молекулярной массы состава композиционного материала; от вида размеров и конфигурации изделия; от типа используемого оборудования.
При выборе температурного режима экструзии рекомендуется температуру цилиндра повышать от загрузочной зоны к головке по возможности плавно. Температуру вблизи загрузочного бункера задают на 10 150С выше температуры плавления материала. Температура формующей головки может быть равна или ниже на 5 100С температуры цилиндра последней зоны что способствует улучшению гомогенизации расплава.
Давление расплава в головке обусловливается сопротивлением головки и фильтрующих сеток и способствует высокому качеству перемешивания расплава. Недостаточное давление расплава приводит к различным дефектам экструдата: «оспины» на поверхности листов шероховатость на трубах раковины тусклая поверхность снижение механических свойств изделия.
Частота вращения червяка определяет производительность экструзионного процесса и влияет на качество изделия. С увеличением частоты вращения червяка в расплаве за счёт внутреннего трения возникают большие тепловыделения что может быть причиной деструкции материала снижающей физико-механические характеристики изделия или привести к пульсирующему режиму течения материала. Отмеченное обусловливает огрубление бугристость поверхности экструдата снижающие качество изделия.
2Конструктивные схемы шнеков экструзионных машин
Червяк предназначен для транспортирования материала от загрузочного бункера перемешивания и создания определённого давления у выхода цилиндра достаточного для продавливания расплава через профилирующую головку.
Геометрические параметры червяка: шаг угол наклона нарезки и глубина винтового канала оказывают основное влияние на количество тепла выделяющегося за счёт сил внутреннего трения в процессе деформации полимера а следовательно и на технологическую мощность.
Сжатие материала по мере его продвижения к головке достигается за счёт уменьшения объёма винтового канала которое может быть плавным ступенчатым или комбинированным. Характер изменения объёма винтового канала по длине червяка зависит от перерабатываемого материала.
При проектировании червяка важное значение уделяется конструктивному выполнению окончания червяка. От формы окончания червяка зависят достижение наибольшей однородности расплава создание определённого градиента давления в головке и беспульсирующее течение потока.
3Конструктивные схемы оформляющих головок экструдера
Назначение головки экструдера – формирование расплавленного полимера в изделие. Внутри головки проходит канал сечение которого меняется от круглого до сечения соответствующего профилю изделия на выходе.
4Физическая сущность процесса экструдирования
По мере прохождения термопласта в червячном экструдере меняется его состояние – от твёрдого в области загрузочной воронки до расплавленного в дозирующей зоне и головке.
Обычно расчёт производительности и давления в экструдере ведётся по дозирующей зоне т.к. течение расплава описывается изученными гидродинамическими законами вязкой жидкости.
Общий поток расплава в дозирующей зоне складывается из трёх отдельных потоков: вынужденного обратного и утечек.
Вынужденный поток возникает вследствие адгезии расплава к неподвижной стенке цилиндра. Максимального значения вынужденный поток достигает при отсутствии давления на выходе т.е. когда экструдер работает без головки как транспортирующая машина.
Обратный поток возникает при установке на выходном конце экструдера головки фильтрующего элемента решётки или клапана которые оказывают сопротивление потоку расплава. По мере продвижения материала к головке давление возрастает и материал из зоны большего давления начинает перетекать в зону меньшего. Т.к. прямой поток значительно больше обратного имеет место только уменьшение его на величину обратного потока.
Поток утечек возникает также при наличие градиента давления вдоль винтового канала и возникает между гребнями витков червяка и внутренней поверхностью цилиндра. Радиальный зазор между гребнями витков и цилиндром весьма незначителен поэтому величина потока утечек намного меньше вынужденного и обратного потоков.
Технологические схемы линий экструдирования
1Конструкция экструдера
Червячные прессы классифицируют по производительности конструкции и в зависимости от назначения которые между собой увязаны.
Например производительность машин с диаметром червяка 9 500 мм составляет 15 3000 кгчас. При этом у машин может быть различное соотношение диаметров и длин червяков: с коротким червяком – L 10D и длинным червяком L > 100D. Кроме того различают машины с тихоходными червяками 25 Гц и быстроходными > 25 Гц.
Одношнековый экструдер состоит из станины 1 приводного устройства корпуса со шнеком оформляющей головки и аппаратуры.
Приводное устройство имеет электродвигатель от которого шкив 2 клиноременной передачи приводной вал 3 пару шестерен 4 цилиндрическую зубчатую передачу 5 и вал 6 приводится во вращение червяк 7. Осевые усилия возникающие при работе шнека воспринимаются упорным шарикоподшипником 8. Число оборотов шнека определяется тахогенератором 9.
Рисунок 3 – Экструдер одношнековый
Шнек установленный в цилиндрическом корпусе 10 обогреваемый с помощью индукционных нагревателей 11. Воздух для охлаждения цилиндра подается вентилятором 12 через клапаны 13 с независимым регулированием для каждой зоны.
Процесс непрерывного выдавливания во многом зависит от температуры в различных зонах цилиндра и шнека. В связи с этим предусмотрен тепловой автоматический контроль и регулирование температуры по зонам. Температура регулируется терморегуляторами получающими импульсы от термопары 14.
Рабочий процесс переработки термопластичного материала заключается в следующем.
Из бункера 15 через вибрирующий подающий желоб 16 материал поступает в загрузочную воронку 17 а оттуда в приемную часть корпуса 10 где захватывается шнеком 7 который транспортирует массу вперед. При прохождении вдоль корпуса материал нагревается расплавляется и при определенном давлении проталкивается через оформляющую головку 18 из которой выходит изделие требуемого профиля.
Вращающийся шнек проталкивает массу вперед одновременно стремится повернуть ее вызывая опасность пробуксовки массы относительно внутренних стенок цилиндра. Возникающий при этом крутящий момент тем меньше чем меньше величина коэффициента трения материала о поверхность шнека. Для уменьшения величины коэффициента трения шнек охлаждают водой подаваемой через патрубок 19 по трубе 20 во внутреннюю полость шнека. Отводится вода через патрубок 21. Подающий желоб 16 установлен на плоских пружинах 22. Под желобом расположен электрический вибратор 23 переменного тока заставляющий вибрировать желоб в плоскости перпендикулярной к пружинам. При регулировке напряжения изменяются амплитуда колебаний и объем загружаемого материала.
Несмотря на разнообразие червячных прессов основные сборочные узлы и детали у них общие и с основной частью машины от которой зависят размеры производительность и качество изделий является червяк. Вид изделий и номенклатура определяется оформляющей головкой. Одним из следственных параметров червяка является величина степени сжатия материала которая находится в пределах от: V1:V3=15:1 до V1:V3=5:1 на участке одного шага (V1 V3 – объёмы винтового канала в зонах питания и нагнетания).
2Схема технологической линии экструзии труб
Расплав из экструдера 1 оснащённого формующей головкой 2 непрерывно выдавливается в виде заготовки кольцевого сечения. Заготовка поступает в калибрующее устройство 3 где происходит её предварительное охлаждение и калибрование по геометрическим размерам а в охлаждающей ванне 4 труба окончательно охлаждается. Вытяжка и транспортирование раскладки производится тянущим устройством 5 состоящим из двух гусеничных транспортёров с зажимающими башмаками гусениц. Привод транспортёра через вариатор от электродвигателя. Трубы разрезаются на обрезки заданных размеров специальным устройством 6 например дискового или фрезерного типа и укладываются на тележку 7.
Рисунок 4 – Схема технологической линии экструзии труб
Определение параметров экструдера
1Расчетная схема сил вращающегося червяка
На червяк действует аксиальная сила Р крутящий момент Мкр и равномерно распределённая нагрузка g от собственной массы червяка. Силы Р и g вызывают прогиб червяка. Задачей прочностного расчёта является проверка предварительно определённых размеров червяка и определения допускаемого прогиба.
Рисунок 5 – Схема к расчету червяка
Для определения расчетной схемы червяк предварительно проверяется на гибкость по формуле:
где k – коэффициент зависящий от метода крепления конечной части вала k=2;
L – длина червяка м;
Ri – радиус инерции сечения м.
где J – момент инерции поперечного сечения вала червяка м4;
F – площадь поперечного сечения червяка м2;
где – отношение диаметров червяка (по середине высоты гребня).
условие выполняется.
2Технические особенности геометрической формы канала оформляющей головки
Композиционные материалы на основе полиэтилена подвержены деструкции следовательно переход от цилиндрической части экструдера к профилю изделия выходного окончания оформляющей головки должен быть плавным.
Головка разбивается на три условные характерные по геометрической форме части: две части круглого конического сечения плавно переходящие одна в другую и круглый кольцевой канал постоянного сечения по длине.
3 Коэффициенты геометрической формы канала головки
Коэффициент геометрической формы для канала круглого конического сечения к1:
где L – длина зоны канала м;
D – наибольший диаметр зоны головки м;
d – наименьший диаметр зоны головки м.
Коэффициент геометрической формы для канала круглого конического сечения к2:
Коэффициент геометрической формы для канала круглого кольцевого сечения к3:
где Rн – наружный радиус части канала круглого кольцевого сечения м;
Rв – внутренний радиус части канала круглого кольцевого сечения м;
L – длина зоны канала м.
Общий коэффициент сопротивления оформляющей головки:
4Производительность экструдера
Производительность определяется с учетом протяженности зоны формования:
где k – общий коэффициент сопротивления оформляющей головки
φ – константа прямого потока м3
– константа обратного потока м3
γ – константа потока утечек м3
n – частота вращения червяка с-1
Расчет константы прямого потока по формуле:
где α – угол наклона винтовой линии
m – число заходов червяка принимается m=1.
Расчет угла наклона винтовой линии по формуле:
Расчет константы обратного потока по формуле:
где L – протяженность зоны формования экструзионной головки L = 0215 м.
Расчет константы потока утечек по формуле:
При плотности материала ρ = 950 кгм3
5Мощность червячного экструдера
Согласно зависимости при n=05с-1
6Расчет коэффициентов вязкости
Коэффициенты вязкости 1 и 2 определяются по значению градиента скорости собственно в канале червяка и в зазоре между гребнем червяка и цилиндром экструдера:
Воспользовавшись реологической кривой полиэтилена и найденными значениями градиентов скоростей определяем на графике при соответствующей температуре значения и :
7Давление в дозирующей зоне червяка
Процесс экструзии возможен если давление p в дозирующей зоне червяка будет больше сопротивления Δp головки экструдера или равно ему т.е.
Как это следует из зависимости от производительности:
где и - динамическая вязкость и коэффициент сопротивления соответствующего канала. Таким образом следует:
Падение давления для первого канала «круглый конический»:
Падение давления для второго канала «круглый конический»:
Падение давления для третьего канала «круглый кольцевой»:
Общие потери давления в оформляющей головке:
Таким образом давление в оформляющей головке
и технологическая мощность экструдера
Если к.п.д. передаточного механизма принять равным 08 то мощность электродвигателя должна быть
Техника безопасности
Современные экструзионные агрегаты – крайне сложные устройства. Микропроцессорные системы предназначены для непрерывного контроля и корректировки значений технологических параметров и тем не менее учитывая так называемый «человеческий фактор» при работе необходимо неукоснительно соблюдать определенные правила техники безопасности. К основным из них относятся:
Эксплуатация экструдера и всей линии допускается только после получения протоколов завершения монтажа актов сдачи-приемки актов сдаточных испытаний и работ.
При эксплуатации экструдера должен неукоснительно соблюдаться график профилактических и ремонтных действий.
Перед запуском экструдера для всех полимеров кроме полиолефинов необходимо проводить чистку цилиндра и шнека фильтра-решетки и формующей головки.
Экструдер запускают только после нагрева до заданной температуры с предварительной выдержкой при ее значении в течении 25-30 мин.
При переработке галогеносодержащих полимеров оператор экструзионной машины в обязательном порядке должен использовать индивидуальные средства защиты (респиратор противогаз перчатки)
В экструзионном помещении в обязательном порядке обеспечивается приточно-вытяжная вентиляция соответствующая установленным нормам.
Для очистки червяка головки цилиндра при проведении регламентных работ для чистки поверхностей деталей разрешается использовать только латунные или медные скребки.
Чистку оборудования производят незамедлительно после его остановки и в условиях пока оно не охладилось более чем на 10-20 градусов ниже температуры плавления (но не температуры переработки!).
Запуск экструдера проводят только после прогрева до требуемых значений температур начиная с минимальной частоты вращения червяка и плавно увеличивая его до номинального значения. Технологические отходы производства следует незамедлительно направлять на повторную подготовку сырья (дробление нагрев) и переработку.
Вращение червяка в незаполненном магистральном цилиндре допускается только в течении времени предусмотренного регламентом.
При эксплуатации экструдеров и экструзионных агрегатов следует соблюдать чистоту на рабочих местах не допускать захламленности рабочей площадки соблюдать нормы свободных расстояний между соседним оборудованием.
Ремонт экструдеров и агрегатов технологических линий производят в ремонтно-механических подразделениях предприятий или их смежников.
Эксплуатация экструзионного оборудования разрешается только при получении письменных свидетельств служб контролирующих технику безопасности состояние противопожарного обеспечения соблюдения санитарных норм.
Все работники допущенные к эксплуатации экструзионных линий должны провести соответствующий инструктаж по технике безопасности с записью в журнале и росписью там инструктируемого.[5]
Гиберов З.Г. Механическое оборудование заводов пластических масс – М. Машиностроение 1967. – 240 с. ил.
Гиберов З.Г. Вернер Е.В. Механическое оборудование предприятий для производства полимерных и теплоизоляционных материалов – М. Машиностроение 1973. – 409 с. ил.
Гиберов З.Г. Журавлев М.И. Оборудование заводов пластических масс. Атлас конструкций. – М. Машиностроение 1973. – 112 с. ил.
Абраменков Э.А. Механическое оборудование. Червячные формующие машины экструдеры. Методические указания. Новосибирск НИСИ 1992.
Производство изделий из полимерных материалов: Учеб. пособиеВ.К. Крыжановский М.Л. Кербер В.В. Бурлов А.Д. Паниматченко. – СПб.: Профессия 2004. – 464 с. ил.
Одночервячный экструдер
Устройство для нагрева и подсушки гранул
Устройство тянуще - отрезное
Устройство намоточное
rsrsrrsssrs-rrrrrryer-sryessssrrsr.dwg

Технологическая линия. Шнек. Формующая головка..dwg

Подготовка формы t=27
Транспортиро- вание t=12
Транспортиро- вание t=22
Линейный график изготовления одного изделия
Технологическая карта на изготовление ферм
Прочность при сжатии
Складирование арматурных изделий
Пост доводки и выдержки изделий
Организация рабочих мест
- тележка для вывоза готовых изделий
- кассета с готовыми изделиями
- тележка для ввоза арматурных изделий
Характеристика армирования
Циклограмма работ изготовления ферм
Трудоем- кость в чел-мин
Продол- житель- ность
Условное обозна- чение рабочих
Предваритель- ное натяжение стержней
Закрывание бортов формы
Укладка и уплотнение бе- тонной смеси
Заглаживание поверхности изделия
Закрывание крышки камеры
Открывание крышки камеры
Передача напря- жения на бетон
Открывание бортов формы
Извлечение изделий из формы и транспорти- рование на склад
Режим труда и отдыха
Завод работает в две смены
продолжительность смены 8 часов. 1 смена: 8.00-8.15 - подготовительная работа 8.15 - 12.00 - оперативная работа 12.00 -13.00 - обеденный перерыв 13.00 -16.45 - оперативная работа 16.45 - 17.00 - заключительная работа 2 смена: 17.00-17.15 - подготовительная работа 17.15 - 21.00 - оперативная работа 21.00 -22.00 - обеденный перерыв 22.00 -01.45 - оперативная работа 01.45 - 02.00 - заключительная работа Предусматриваются технологичские перерывы по 15 минут через каждые 2 часа
Пооперационный контроль основных операций подлежащих контролю
Техника безопасности
Наименование оборудования
Правильность упаковки изделий Прочность бетона
тележка для вывоза готовых изделий
кассета с готовыми изделиями
тележка для ввоза арматурных изделий
*Проверка положения изделий ипрокладок в штабеле
маркировка *Отпускная и марочная прочностьбетона и других структурно-механические свойства. *Прочность
трещиностойкость *Приемка по совокупностипоказателей качества готовых изделий. *Проверяется толщина защитного слоя. * Проверяется наличие и расположение монтажных петель
Метод и средства контроля
Переодичность и обьем контроля
Комплектация рабочих чертежей
Состояние формово- чного оборудования
Установка и закреп- ление каркасов
зак- ладных деталей и фиксаторов
Приготовление бе- тонной смеси
Подготовка и смазка формы
Укладка бетонной смеси
ТВО и условия твер- дения
Распалубливание. Подготовка к сдаче продукции
Наличие технической документации (ТУ
Колебани виброплощадки 2.Таррировка монометров 3.Тарировачные таблицы 4.Техническое состояние оборудования
Марка стали 2. Соответствие размеров арматуры рабочим чертежам 3. Сверка чертжей и сеток 4. Антикорозионная защита
Сравнение с перечнем проекта
Раз в месяц и при изготов- лении новой партии изделий
Посты формования и натяжения арматуры. Лаборатория
Сравнение с побразцовыми манометрами и динамометров. Виброграф. Паспорт
п. 2 и 3 - раз в 6 месяцев каждый прибор; п 1 и 4 - ежемесячно
Механическая прочность. 2. Размеры швов. 3. Соосность стержней 4.Наличие дефектов
Сварочный пост. Лаборатория
Отбор проб и испытание
Раз в месяц п. 2 - 4 - постоянно; п. 1 - 4 - выборка.
Соответствие рабочим чертежам. 2. Защитный слой. 3. Укладка облицовочного слоя 4. Положение арматурного каркаса
Обмер стальной рулеткой
мерной линейкой. Визуальный
Раз в смену. Выборка
Точность дозирования. 2. Время перемешивагия. 3. Консистенция. 4. Температура
Дозаторы. Бетоносмесители
Наблюдение за приборами. 2. Проверка
тарирование прибороа 3. Отбор проб и испытание 4. Термометр
п. 1 - раз в смену п. 2 - каждый замес п. 3-4 - 2 раза в сену и при новом составе смеси
Соответствие форм проектным размерам 2. Качество очистки и сазки 3. Качество эмульсии
Рост распалубливания 2. Место сборки перед укладклй бетонной смеси 3. Емкость
Обмер рулеткой и уровнем. 2 Осмотр 3. Отбор проб и испытание
п. 1 - раз в квартал
поштучно п. 2 - раз в смену. Выборка п. 3 - раз в месяц
Величина натяжения и упругое удлинение арматуры 2. Прочность бетона
Стенд 2. Лаборатория
пружинные частот- ные приборы(ИПН
п. 1 - поштучно п. 2 - серия контрольных образцов -кубов
Толщина слоя 2. Время виброуплотнения 3. Плотность укладки 4. Прочность бетона 5. Средняя плотность
Камера тепловлажностной обработки
Приборы автоматики и регулирования
- серия контрольных кубов
п. 1-3 - пост формования п. 4-5 - лаборатория
п. 1 - замер линейкой п. 2 - секуедомер п. 3 - плотнометр п. 4
- отбор проб и последущее испытание их
Соблюдение заданного режима тепловлажностной обработки
В процессе обработки через 2 часа. Партия в камере
Внешний вид 2. Наличие дефектов 3. Соответствие расположения изделий схеме складирования
Пост распалубливания
склад готовой продукции
- поштучно п. 3 - 2 раза в смену
- визуально п. 3 - стальная рулетка
Колебания виброплощадки 2.Техническое состояние оборудо- вания
НГАСУ (Сибстрин) 462 гр.
Функциональная и электрическая схемы
Управление дверями и толкателем в туннельной печи
Функциональная схема
Схема силовых цепей двигателей
Гидравлический толкатель
Диаграмма замыкания контактов концевых выключателей толкателя
Наимено- вание контактов
Диаграмма замыкания контактов концевых выключателей дверей
Диаграмма замыкания контактов избирателя режимов работы SA
Наимено- вание контакта
Диаграмма замыкания контакта реле времени KT2
Диаграмма замыкания контактов КЭПа
Передняя дверь закрыта
Задняя дверь открыта
Задняя дверь закрыта
Задняя дверь заклинила (открытие)
Толкатель исходное застрял
Толкатель в печь застрял
Звуковая и световая сигнализация заклинивания дверей
Реле сигнализации аварийного состояния дверей
закрытия дверей и работы толкателя
Управление толкателем
Управление задней дверью
Управление передней дверью
Звонок громкого боя МЗ-1
Сигнальная арматура АСС-38
Золотник гидравлического толкателя
Конечный выключатель ВК-200
Универсальный переключатель УП-5314
Магнитный пускатель ПА-324
Кнопочный пост управления КУ 122-3 м
Диаграмма замыкания контакта реле времени KT3
Передняя дверь открыта
Задняя дверь заклинила (закрытие)
Передняя дверь заклинила (открытие)
Передняя дверь заклинила (закрытие)
Световая сигнализация положения дверей и толкателя
Реле сигнализации аварийного состояния толкателя
НГАСУ (Сибстрин) 563 гр.
Технологическая линия. Шнек. Формующая головка.
Червячные формующие машины. Экструзионная линия для производства полиэтиленовой трубы
Экструзионная линия для производства полиэтиленовой трубы М 1:20
Техническая характеристика
Производительность по наполненой смеси ПЭ до 10 кгч Мощность электродвигателя в кВт 1
Расход сжатого воздуха в м с 0
1 Расход воды на охлаждение м с 0
014 Габаритные размеры в мм: длина 13080 ширина 1340 высота 3186 Масса в кг 5485
Трубная формующая головка М 1:2
фланец 2. пакет сеток 3. решетка 4. отверстия под термопары 5. дорнодержатель 6. формующая матрица 7. дорн 8. фасонная гайка 9. установочные винты 10. канал 11. штуцер 12. канал заготовки 13. рассекатель 14. корпус 15. нагреватели сопротивления 16. болты
участок гомогенизации (перемешивания) расплава 2. участок расплавления и сжатия расплава 3. участок загрузки гранул
Нарезка винтовая правая с постоянным шагом
Рекомендуемые чертежи
Свободное скачивание на сегодня
- 24.01.2023