Бульдозер-рыхлитель Б10М




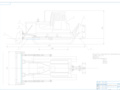
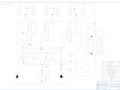
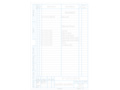
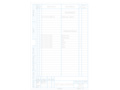
- Добавлен: 25.10.2022
- Размер: 1 MB
- Закачек: 1
Описание
Состав проекта
![]() |
![]() ![]() ![]() ![]() |
![]() ![]() ![]() ![]() |
![]() ![]() |
![]() |
![]() ![]() |
![]() ![]() |
![]() ![]() |
![]() ![]() ![]() ![]() |
![]() ![]() |
![]() ![]() |
![]() ![]() ![]() ![]() |
![]() ![]() |
![]() ![]() |
![]() ![]() ![]() ![]() |
![]() |
![]() ![]() |
![]() ![]() ![]() |
![]() ![]() |
Дополнительная информация
Схема гидропривода бульдозера-рыхлителя _ КР 32.01.42.000.ГС.dwg

Бульдозер-рыхлиель _ 32.01.42.000.ВО.dwg

Зуб рыхлителя.dwg

Зуб рыхлителя _ КР.32.01.42.000..dwg

Бульдозер-рыхлитель _ КР 32.01.42.000 ВО.dwg

Гидроцилиндр поъема отвала
пояснительная записка.docx
Выбор и обоснование типа рабочего оборудования хода привода и системы управления .7
Описание схем привода рабочего оборудования9
Обзор конструкции и описание технологии работы бульдозера-рыхлителя10
1. Описание работы бульдозера-рыхлителя10
1. Определение параметров рабочего оборудования и мощности двигателя12
2. Выбор базовой машины16
3. Расчет устойчивости18
4.Расчёт сопротивлений22
5. Расчёт производительности25
6.Определение нагрузок на рабочее оборудование27
7.Прочностной расчёт29
8.Расчёт привода рабочего оборудования33
9.Технико-экономический расчёт36
Автоматизация рабочего процесса42
Список используемой литературы45
В настоящее время около 95 % земляных работ в строительстве осуществляется механическим способом. При выполнении земляных работ используется широкая номенклатура различных по назначению конструкции и принципу действия машин.Земляным работам в строительстве как правило предшествуют подготовительные работы.Для всех этих подготовительных работ применяются специальные машины созданные на базе гусеничных тракторов оснащенных специальным навесным оборудованием. Иногда для этих целей можно использовать и бульдозеры наиболее мощные из которых в настоящее время снабжаются вторым рабочим органом - рыхлителем.
Бульдозер-рыхлительприменяется при производстве строительных работ когда появляется необходимость в земляных работах требующих механизации. К ним относятся например послойное копание грунта его перемещение на расстояние от 60 до180 метров а также укладка и планировка.
Параметры и технические требования к бульдозерам регламентированы ГОСТ EN 474-1-2012 и ГОСТ EN 474-2-2013 согласно которым:
Бульдозеры должны быть обеспечены соответствующими системами доступа к рабочему месту оператора и к местам технического обслуживания проводимого оператором в соответствии с руководством по эксплуатации. Средства доступа должны иметь такую конструкцию чтобы сводить к минимуму возможность скопления мусора.
Рабочее место оператора находящееся на машине должно быть сконструировано и изготовлено таким образом чтобы установленная кабина обеспечивала пространство для оператора и риск для него не увеличивался а сама кабина должна защищать оператора от предполагаемых неблагоприятных климатических условий. Должна быть обеспечена возможность установки системы вентиляции регулируемой системы отопления и системы оттаивания стекол.
Машины с эксплуатационной массой менее 1500 кг могут не оборудоваться кабиной.Машины с эксплуатационной массой равной или более 1500 кг должны быть оборудованы кабиной в том случае когда предусмотренные неблагоприятные погодные условия не позволяют осуществлять круглогодичную эксплуатацию машины без кабины (по договору между изготовителем и потребителем).
Машины должны быть оборудованы кабиной и системой защиты от загрязнений если машина предназначена для использования в неблагоприятных условиях окружающей среды например загрязненные зоны (по договору между изготовителем и потребителем).
Если существует опасность выброса обломков например при работе с гидравлическим или отбойным молотком то требуется соответствующая защита например ударопрочное стекло сеточное ограждение или эквивалентная защита.
Система выпуска отработавших газов должна отводить отработавшие газы в сторону от оператора и места забора воздуха в кабину.Двери окна и люки должны быть надежно закреплены в своих функциональных положениях; должны быть приняты меры для предотвращения их непреднамеренного открытия. Специальное устройство фиксации должно удерживать двери в рабочем (их) положении (ях). Основной проем который в рабочем положении должен оставаться в открытом положении должен иметь возможность закрываться с рабочего места оператора.
Окна должны быть изготовлены из безопасного стекла или другого материала который обеспечивает аналогичные характеристики безопасности .Окна в крыше не требуют дополнительного механического ограждения. Переднее и заднее окна должны быть оборудованы стеклоочистителем (ями) и стеклоомывателем (ями) с механизированным приводом. Бачок стеклоомывателя должен быть легкодоступен.
Кабина должна быть оборудована стационарной системой внутреннего освещения способной функционировать при выключенном двигателе для освещения рабочего места оператора и для возможности чтения руководства по эксплуатации в темное время суток.
Машины которые управляются оператором в положении сидя должны быть оборудованы регулируемым сиденьем удерживающим оператора в положении которое позволяет ему управлять машиной в предусмотренных условиях эксплуатации.
Бульдозеры должны быть сконструированы так чтобы опасное движение машины или ее основного иили сменного оборудования было невозможным без воздействия на органы управления при пускеостанове двигателя.
Машины должны быть сконструированы и изготовлены так чтобы плановая смазка и техническое обслуживание могли быть проведены безопасно по возможности при выключенном двигателе. Если работы по проверке или техническому обслуживанию могут выполняться только при работающем двигателе то безопасный порядок проведения работ должен быть описан в руководстве по эксплуатации.
Выбор и обоснование типа рабочего оборудования хода привода и системы управления
Рабочее оборудование бульдозера - рыхлитель который обеспечивает эффективное рыхление плотных и мёрзлых грунтов. Рабочий орган рыхлителя состоит из несущей рамы зубьев подвески и гидроцилиндров управления. Зубья имеют сменные наконечники лобовая поверхность которых защищена износостойкими пластинами для защиты от абразивного износа.
Для интенсификации процесса рыхления на зубья рыхлителей устанавливают уширители которые позволяют за один проход разрушать большие объемы материала и выталкивать каменные глыбы на поверхность. Уширители обеспечивают более устойчивое движение базового трактора и работу рыхлителя практически сплошное разрушение материала между соседними бороздами снижение общего количества проходов.
В зависимости от назначения рыхлителя и вида выполняемых работ число зубьев может быть от одного до пяти. На тяжелых работах при рыхлении горных пород и мерзлых грунтов применяются однозубые рыхлители; для рыхления обычных тяжелых грунтов можно применять пятизубые рыхлители. Зубья выполняют прямыми или изогнутыми и обычно снабжают съемными наконечниками. Подъем и заглубление рабочего органа производятся гидроцилиндрами.
Для выполнения подготовительных работ на раму бульдозера навешивают дополнительные виды рабочего оборудования – рыхлитель навешиваемый сзади машины. Установленный рыхлитель на бульдозер представляет собой рыхлительно-бульдозерный агрегат чаще всего называемый бульдозером-рыхлителем или просто рыхлителем. Бульдозеры-рыхлители оснащаются одно- и трезубым навесным рыхлительным оборудованием заднего расположения с гидравлическим управлением. Рыхлительное оборудование навешивают на гусеничные бульдозеры с тягачами классов 10 25 35 50 и 75 мощностью 118 636 кВт. Главным параметром бульдозеров-рыхлителей является тяговый класс базового трактора. Основными базовыми тракторами использующими рыхлители являются Т10М (Т-170) и бульдозера Б10М (Б-170) EC-10.
По типу ходового оборудования бульдозеры подразделяют на гусеничные и пневмоколесные. В первом случае базовыми машинами являются гусеничные тракторы а во втором — пневмоколесные тягачи и колесные тракторы. Бульдозеры на гусеничном ходу имеют высокую проходимость при этом типе хода тяговое усилие при одной и той же мощности большее чем у пневмоколесных. Пневмоколесные более маневренны и быстроходны их ходовая часть в эксплуатационных условиях более долговечна.
По способу установки отвала бульдозеры разделяют на машины с неповоротными и поворотными отвалами и универсальные. К первым относят бульдозеры у которых в процессе работы изменяется только угол резания остальные же установочные углы остаются постоянными. У бульдозеров с поворотными отвалами изменяются углы резания и захвата универсальных — все установочные углы. Бульдозер – рыхлитель является машиной с неповоротным отвалом.
Описание схем привода рабочего оборудования
Рабочее оборудование бульдозера-рыхлителя состоит из наконечник - 1; стопорное устройство - 2;стойка - 3; флюгер -4; балка - 5;рабочая балка - 6; нижняя тяга - 7; верхняя тяга – 3;гидроцилиндр - 9; опорная рама – 10.
Рис.1. Конструктивная схема навесных рыхлителей (a – трехзвенный б – четырёхзвенный)
Трехзвенная подвеска (рис. 1 а) отличается простотой конструкции и малой металлоемкостью. Вместе с тем существенный недостаток ее—зависимость угла резания зубьев от их заглубления; он изменяется от максимального в начале заглубления до минимального на полной глубине рыхления.
Четырехзвенная подвеска рыхлителя (рис. 1 б) применяется чаще так как угол резания остается почти постоянным что увеличивает срок службы наконечников рабочих органов. Существенным преимуществом такой подвески является и то что рабочий орган при опускании на грунт отодвигается от базового тягача вследствие чего исключается заклинивание кусков породы между рабочим органом и гусеницами трактора. Четырехзвенная подвеска позволяет разрушать грунт .при подъеме рабочего органа что невозможно при подвеске трехзвенной.
Обзор конструкции и описание технологии работы бульдозера-рыхлителя
Рис.2. Схема бульдозера – рыхлителя
1.Описание работы бульдозера-рыхлителя
Бульдозеры-рыхлители разрушают скальные и мерзлые породы под воздействием двух сил: сжатия зубом и разрыва массива наконечником и стойкой. Лучше всего рыхлить этими машинами трещиноватые и слоистые породы: известняки песчаники сланцы фосфориты бурые и каменные угли.
На рис. 3 показаны четыре оптимальные схемы рыхления: продольно-кольцевая спиральная челночная со смещением продольнопоперечная. Выбор схемы рыхления зависит от прочности и природы разрабатываемых пород.
Рис.3. Схемы рыхления грунтов
По окончании рабочего цикла выглубляют рыхлитель и проверяют наличие съемного наконечника. При его утере можно повредить носок стойки и он не будет удерживать наконечник. В этом случае стойку заменяют.
-общего назначения (глубина рыхления до 1 м);
-специальные (глубина рыхления больше 1 м).
По типу движения базовой машины:
-на гусеничном ходу;
По номинальному тяговому усилию и мощности базового трактора:
- сверхтяжелые более 300кН (мощность более 294 кВт);
- тяжелые от 200 до 300 кН (184-294 кВт);
- средние – от 135 до 200 кН (1176 – 183 кВт);
- легкие – до 135 кН (1176 кВт).
По способу крепления зуба к раме:
-жесткое крепление зуба (не имеет возможности поворота в горизонтальной плоскости);
- флюгерное крепление (имеет возможность поворота в горизонтальной плоскости на угол 10-20 ` от оси в ту и другую сторону).
По виду выпускаемых зубьев:
- прямолинейные с предварительным изгибом;
1. Определение параметров рабочего оборудования и мощности двигателя
Таблица 1. Бульдозеры с неповоротным отвалом
Тяговый класс – 100 кН.
Рис.4. Линия тренда зависимости массы бульдозера от тягового класса
Рис.5. Линия тренда зависимости массы рабочего оборудования от тягового класса
Рис.6. Линия тренда зависимости мощности двигателя от тягового класса
Рис.7. Линия тренда зависимости ширины толкающего бруса от тягового класса
Рис.8. Линия тренда зависимости высоты толкающего бруса от тягового класса
Рис.9. Линия тренда зависимости максимальной толщины срезаемой стружки грунта от тягового класса
Рис.10. Линия тренда зависимости объема грунта в призме волочения от тягового класса
= 19692 2531 55 кг – масса рабочего оборудования;
N = 07374 131277 кВт – мощность двигателя;
В = 84186 357487 мм – ширина толкающего бруса;
H = 40695 134645 мм – высота толкающего бруса;
Vгр = 258 459 м3 – объем грунта в призме волочения.
2. Выбор базовой машины
Выбираем бульдозер – рыхлитель Б10М.0100-1ЕР.
Таблица 1. Параметры бульдозера - рыхлителя Б10М.0100-1ЕР
Высота грунтозацепов мм
Номинальная мощность кВт (л.с.)
Рабочий объем двигателя л
Удельный расход топлива при эксплуатационной мощности гкВт.ч. (гл.с.ч) не более
Механическая с восьмискоростной коробкой передач
Скорость движения без буксирования кмч
по передачам вперед нормальн.ускорен.назад
полужесткая подвеска с балансирной поперечной рессорой
Число опорных катков (с каждой стороны)
Число поддерживающих катков (с каждой стороны)
Дорожный просвет мм не менее
Колея трактора мм не менее
Площадь опорной поверхности кв.м.
Давление на грунт кгскв.см. не более
Рыхлительное оборудование
Регулируемый трехзубый
Макс. Заглубление мм.
Бульдозерное оборудование
Высота подъема над опорной поверхностью мм.
Заглубление отвала мм.
Макс. Регулировка наклона (перекос) градусов
Габаритные размеры трактора без навесного оборудования
Эксплуатационная масса (стандартной комплектации с полной заправкой отвал заднее навесное оборудование машинист) не более т
3. Расчет устойчивости
3.1. Продольная устойчивость бульдозера
Землеройно-транспортные машины необходимо проверять на устойчивость при работе так как они часто преодолевают значительные продольные и поперечные уклоны. Машины могут опрокидываться при перемещении и работе на больших уклонах а шарнирно-сочлененные машины — при повороте на горизонтальной площадке.
При больших продольных уклонах машина может остановиться вследствие ее опрокидывания или из-за недостаточного сцепления ее ведущих колес с грунтом ввиду перераспределения нагрузок между осями машины при движении на подъем.
Рис. 11. Схема для определения продольной устойчивости машины на подъем и уклон
При подъеме трактор может опрокинуться вокруг т. О (рисунок 11а). Трактор находится в состоянии устойчивости при выполнении условия:
где G – вес машины G = 15475 15181 кН
hG – высота центра тяжести м
l – расстояние от задней оси до вертикали проходящей через центр тяжести м
Максимально допустимый угол подъема:
Трактор будет находиться в состоянии устойчивости при подъеме если угол подъема не превышает 35°.
Условие опрокидывания:
Условие опрокидывания выполняется.
На спуске трактор может опрокинуться вокруг т.О (рисунок 11б). Бульдозер находится в состоянии устойчивости при выполнении условия:
l1 – расстояние от передней оси до вертикали проходящей через центр тяжести м
Бульдозер будет находиться в состоянии устойчивости при спуске если угол наклона не превышает 24°.
Условие устойчивости при спуске:
Условие устойчивости выполняется.
3.2. Поперечная устойчивость бульдозера
Рис.12. Схема для определения поперечной устойчивости машины на подъем и уклон
При движении поперек уклона трактор может опрокинуться вокруг т.О (рисунок 12).
Угол бокового наклона дороги:
Трактор будет находиться в состоянии устойчивости при движении поперек уклона если угол бокового наклона не превышает 34°.
Условие устойчивости при поперечном наклоне:
4. Расчёт сопротивлений при работе машины
Сопротивление движению бульдозера:
Сопротивление резанию грунта:
Сопротивление трению грунта по отвалу:
Сопротивление волочению призмы грунта впереди отвала:
Результирующая сила сопротивлений слагается из сил сопротивления:
Значение величин приведены в таблице 2 и 3.
Удельное сопротивление резанию К0 кНм2
Объёмная масса (плотность)г тм3
Коэффициент разрыхления Кр
Коэффициент внутреннего трения 2
Коэффициент трения грунта о сталь 1
Коэффициент сопротивления перемещению бульдозера f
Коэффициент сцепления сц
Угол естественного откоса град
Сопротивление грунта резанию W1 Н
Сопротивление перемещения призмы волочения W2 Н
Сопротивление от перемещения бульдозера-рыхлителя W3 Н
Сопротивление перемещения грунта вверх бульдозера по отвалуW4 Н
Суммарное сопротивление ΣW кН
5. Расчёт производительности
- продолжительность цикла
- время на один поворот = 8 c;
– время на переключение передачи = 4 с;
– время на подъем и опускание отвала за цикл = 6 с.
Lох = LК + Lп + Lразр
Рассчитанные значения приведены в таблицах 5 и 6 и отображены на графике (Рис.14).
Производительность м3ч
6. Определение нагрузок на рабочее оборудование
Сопротивление заглубления отвала:
Усилие заглубления отвала:
Сопротивление резанию грунта при выглублении отвала:
Вес грунта поднимаемого вместе с отвалом:
Усилие подъема отвала:
Критическое усилие подъема отвала:
Результаты расчетов приведены в таблице 7.
Sпкр тогда находим усилие подъема при остановленном бульдозере.
Sпкр – условие выполняется.
7. Прочностной расчет
На центральный зуб при максимальной глубине рыхления действуют максимальные величины Rx и Ry и 05Rz (Рис.15.) (учитывается не полностью т.к. при вертикальных нагрузках на зуб близких к максимальным значительно уменьшаются тяговосцепные качества базового трактора).
Рис. 15. Расчетная схема зуба рыхлителя
Рис.16. Эпюры нагрузок действующих на зуб рыхлителя: а) эпюра изгибающих моментов; б) эпюра продольных сил.
Опорные реакции в шарнирах крепления зуба:
By = Ay – Ry = 1173 – 32 = 853кН
Геометрическая характеристика сечения II –II:
Изгибающий момент в сечении в плоскости ZOX:
M1 = = 120000 = 13307500 Н
Изгибающий момент в плоскости YOZ:
= = 924132 +632099 = 1556231 Нсм2
Моменты сопротивления:
Изгибающий момент в плоскости XOZ
= 5 = 120000 +050906 = 37625568 Н
Изгибающий момент в плоскости YOZ
= = 32000 = 1024000 Н
S = - 5 =120000 = 133920 Н
Напряжение в сечении III – III
11442+1172564+239143= 2723149 Нсм2
Зуб изготавливается из стали с пределом прочности 45000-60000 Нсм2. Действующее напряжение с проверенных сечениях меньше чем предел прочности стали значит необходимый запас прочности обеспечен.
8. Расчёт привода рабочего оборудования
Рис.16. Схема автоматизированного объёмно-аккумуляторного гидропривода бульдозера-рыхлителя
Диаметр цилиндра (поршня):
Δр = (рн — рс) — перепад давления в каждом гидроцилиндре при работе под нагрузкой при номинальной частоте вращения коленчатого вала дизеля и установившейся температуре жидкости в гидросистеме Δр = 156— 05 = 151 МПа;
гм.ц— гидромеханический КПД цилиндра гм.ц = 095.
Диаметр гидроцилиндров подъема-опускания рыхлителя:
Условие прочности стенок цилиндра:
К найденной по формуле минимальной толщине стенки min цилиндра прибавляется припуск на механическую обработку металла. Для диаметров цилиндра D = 30 180 мм он принимается равным 05 10 мм.
Трубопроводы являются тонкостенными.
Расчёт на продольный разрыв прямых тонкостенных трубопроводов (Dн>16) нагруженных внутренним давлением рmax производится по условию прочности:
где Dн- наружный диаметр трубопровода;
Условия прочности выполнены.
9. Технико-экономический расчёт
Расчет капитальных вложений
В объемах капиталовложений необходимых для расчета эффективности учитываются непосредственные капиталовложения и единовременные затраты необходимые для создания и использования. Капитальные затраты по базовой и новой технике включают в себя оптовую цену и затраты на доставку техники:
где Зб - оптовая цена техники руб.;
kб - коэффициент учитывающий затраты на доставку техники.
Оптовая цена базовой техники (БТ) за базовый бульдозер Т-170.
Оптовую цену новой техники (НТ) можно получить путем прибавления к цене базового бульдозера стоимости рыхлительного оборудования (165000руб.).
Капитальные затраты по новой технике:
Расчет количества машино-часов работы в год
Годовой фонд рабочего времени машины определим по зависимости:
где Дв – число выходных и праздничных дней за год;
Дп – число дней на перебазировку техники (Дп = 30);
Дш – средняя продолжительность простоя машины по метеоусловиям (Дш = 20);
р – количество смен (р=2);
– простой техники в ремонте (=004);
– продолжительность рабочего дня.
Дв = 522+8+10=122 дней.
Годовая эксплуатационная производительность равна:
где Пэч – часовая эксплуатационная производительность;
кв – коэффициент перехода от часовой производительности к эксплутационной с учетом простоев техники (кв = 075).
Тогда годовая производительность будет равна:
Определение годовых текущих затрат
Годовые текущие затраты в общем случае определяются по формуле
где Сзп - расход на заработную плату;
Сар - годовые амортизационные отчисления;
Сс - расходы на содержание и эксплуатационную технику.
Расчет общего фонда заработной платы с начислениями для усредненных условий использования техники:
λ = 14 - коэффициент перехода от тарифного фонда к общему фонду зарплаты
Величина амортизационных отчислений:
где Кар = 01 - коэффициент амортизационных отчислений при сроке службы бульдозера 10 лет.
Затраты на капитальный ремонт:
где Акр = 5% - норма отчислений на капитальный ремонт.
Затраты на техническое обслуживание и текущий ремонт:
где Sэрн = 30750 руб - стоимость ТО и ТР на 1000 часов работы.
где СТОП.ДЗ = 37 рубл - стоимость 1 литра дизельного топлива;
Кв = 025 - коэффициент использования бульдозера по времени (для среднего режима работы);
Ф – годовой фонд работы бульдозера;
RДЗ = 456 лчас - паспортный часовой расход дизельного топлива;
Затраты на масло смазочные и вспомогательные материалы:
где Е = 01 - коэффициент затрат;
Общая стоимость годовых текущих затрат:
Определение основных удельных показателей
Расчет основных показателей произведем на 1 тонну переработанного груза.
Удельные текущие затраты определяются по формуле:
Удельные капиталовложения на переработку груза определяются по формуле:
Удельные приведенные затраты:
где ЕН = 015 - нормативный коэффициент эффективности.
Расчет экономического эффекта
Экономический эффект определяется по формуле
Срок окупаемости новой машины:
где Zн.т. - приведенные затраты новой машины;
где р - доля отчислений на реставрацию;
где Ен.п. – норматив приведения; Ен.п.=01;
Тсл – срок службы бульдозера; Тсл=10 лет;
Себестоимость машино-часа
Стоимость машино-часа определяется по формуле:
где Сар-ч – амортизационные отчисления на полное восстановление;
Сзп-ч – оплата труда рабочих;
Скр-ч – затраты на капитальный ремонт;
Сэр-ч – затраты на техническое обслуживание и текущий ремонт;
СТОП-ч – затраты на топливо;
Ссм-ч – затраты на масло смазочные и вспомогательные материалы;
Стоимость разработки одного кубометра грунта:
С1м3 = 132905 51271 = 2592 рубм3
Автоматизация рабочего процесса
Для повышения производительности при планировочных работах имеет автоматическое управление отвалом бульдозера. Анализ работы бульдозеров на планировочных операциях земляной поверхности под заданную отметку показал что наиболее трудоемкими операциями для бульдозериста являются управление высотным положением отвала движением машины по курсу и выглублением отвала при перегрузке двигателя.
Система «Автоплан-10» предназначена для автоматической стабилизации положения отвала бульдозера с гидравлическим управлением рабочего органа.
Аппаратура системы обеспечивает:
автоматическую стабилизацию углового положения толкающей рамы отвала относительно горизонтальной плоскости в диапазоне ± 30°;
дистанционное (кнопочное) изменение заданного угла толкающей рамы отвала в диапазоне ± 5°.
В состав аппаратуры «Автоплан-10» (рис.5) входят: блок управления 1 пульт управления 2 датчик углового положения 3 исполнительное устройство – электрогидравлический золотник 4 типа ЗСУ-5. Питание системы осуществляется от бортового аккумулятора 5. Установка задания производится задатчиком на блоке управления; ручное управление (кнопочное) – с пульта управления.
Рис. 18. Аппаратура системы «Автоплан-10» (а) и ее расположение на бульдозере (б).
В данном курсовом проекте спроектирован бульдозер рыхлитель на базе трактора Т-170 который служит для рыхления грунта и его перемещения. При выполнении курсового проекта были получены навыки конструирования бульдозера и рыхлителя изучены различные способы расчетов и применение их на практике.
Список использованной литературы
Абрамов Н.Н. «Курсовое и дипломное проектирование по дорожно-строительным машинам» М. «Высшая школа» 1972г.
Алексеева Т.В. «Машины для земляных работ» М. Машиностроение 1972.
Бородачёв И.П.Справочник конструктора дорожных машин. Изд. 2-е переработ и доп. М. Машиностроение 1973 504 с.
А.Н. Витушкин; В.П. Шаронов «Экономика производства и эксплуатации строительных и дорожных машин: методические указания по технико-экономическому обоснованию дипломных проектов»
Гаркави Н. Г. Аринченков В. И. Карпов В. В. Гарбузов З. Е. Батулов А. И. Донской В. М. «Машины для земляных работ»– М.: Высшая школа 1982. – 335 с.
С.А.Волков С.А.Евтюков «Строительные машины» Учебник для строительных вузов. Санкт-Петербург Издательство ДНК 2012