Башенный кран г/п 15 тонн




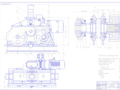
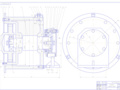
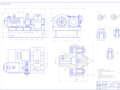
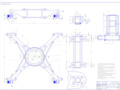
- Добавлен: 25.10.2022
- Размер: 16 MB
- Закачек: 2
Описание
Состав проекта
![]() |
![]() |
![]() ![]() ![]() ![]() |
![]() |
![]() |
![]() |
![]() ![]() ![]() ![]() |
![]() ![]() ![]() ![]() |
![]() ![]() ![]() ![]() |
![]() |
![]() ![]() |
![]() |
![]() |
![]() |
![]() ![]() |
![]() |
![]() ![]() |
![]() ![]() ![]() ![]() |
![]() ![]() |
![]() ![]() |
![]() |
![]() ![]() |
![]() ![]() |
![]() ![]() ![]() ![]() |
![]() |
![]() |
![]() ![]() |
![]() ![]() |
![]() |
![]() |
![]() ![]() |
![]() ![]() |
![]() ![]() ![]() ![]() |
![]() |
![]() ![]() ![]() ![]() |
![]() ![]() ![]() ![]() |
![]() ![]() ![]() ![]() |
![]() |
![]() ![]() |
![]() ![]() ![]() ![]() |
![]() ![]() |
![]() ![]() |
![]() |
![]() ![]() |
![]() ![]() |
![]() |
![]() ![]() |
![]() ![]() |
![]() ![]() ![]() ![]() |
![]() |
![]() ![]() ![]() ![]() |
![]() |
![]() |
![]() |
![]() ![]() |
![]() ![]() |
![]() ![]() |
![]() |
![]() ![]() |
![]() ![]() |
![]() |
![]() |
![]() ![]() ![]() ![]() |
![]() |
![]() ![]() |
![]() ![]() |
![]() |
![]() |
![]() ![]() |
![]() |
![]() |
![]() ![]() |
![]() ![]() ![]() ![]() |
![]() |
![]() |
![]() ![]() |
![]() ![]() |
![]() |
![]() |
![]() ![]() |
![]() |
![]() ![]() |
![]() |
![]() ![]() ![]() ![]() |
![]() ![]() |
![]() |
![]() ![]() ![]() |
![]() ![]() ![]() |
![]() ![]() ![]() |
![]() ![]() ![]() |
![]() ![]() ![]() |
![]() ![]() ![]() |
![]() ![]() ![]() |
![]() ![]() ![]() |
![]() ![]() ![]() |
![]() ![]() ![]() |
![]() ![]() ![]() |
![]() ![]() ![]() |
Дополнительная информация
Рама ходовая _ ДП 02.00.000.dwg

Тележка ходовая ведомая
Болт М30х175 ГОСТ 7808-70
Болт М30х155 ГОСТ 7808-70
Болт М30х35 ГОСТ 7808-70
Шайба 10Л ГОСТ 6402-70
Шплинт 5х70 ГОСТ 397-79
Шплинт 4х50 ГОСТ 397-79
патент_ ДП.00.00.002.dwg

Грузозахватное устройство
Механизм поворота _ ДП 12.00.000.dwg

Шайбы по ГОСТ 11371-78
Кольцо запорное 70 МН. 470-61
Тележка ходовая.dwg

Допускаемая нагрузка на тележку
Скорость передвижения
Диаметр ходового колеса
Механизм подъема груза _ ДП 11.00.000.dwg

Винт М10х22.48 ГОСТ 1476-75
Электродвигатель MTF 311-6
Кольцо запорное 70 МН 470-61
Рама ходовая.dwg

заполнить смазкой графитной УСсА ГОСТ 3333-55 или солидолом
Непараллельность верхней плоскости поворотной роликовой
опоры относительно общей опорной плоскости ходовых колес не
более 11000 радиуса.
Отклонение от опорной плоскости ходовых колес одной из опор
ходовой рамы от уровня головки рельса не более 45 мм в
незагруженном состоянии крана.
Общая неплоскостность поверхности ходовой рамы с опорой при
действии максимально допустимых нагрузок не более 1 мм.
Величина момента затяжки каждого болта должна
соответствовать 122 кгс
Боковой зазор в зацеплении шестерни механизма поворота с
венцом опоры выдержать 0
Барабан.dwg

Кран башенный _ ДП 00.00.000 ВО.dwg

Магнитный контроллер
Механизм подъема груза
Платформа поворотная
Опорно-поворотный круг
Тележка ходовая ведомая
Кран башенный.dwg

на наибольшем вылете
Высота подъема крюка
на максимальном вылете
на минимальном вылете
Промежуточная секция башни
подъема (опускания) груза
транспортирование крана
Угловая скорость поворота
Радиус вращения поворотной платформы
Число приводных колес
Установленная мощность
Механизм подъема груза - изменен.dwg

Все соединения должны быть законтрены.
Допускаемые значения валов электродвигателя и редуктора
Несоосность валов устранить компенсирующими шайбами.
В редуктор залить индустриальное масло И-30А
Привод обкатить без нагрузки согласно программе и методике
Тормоз поз.29 не показан
Обзор.dwg

Механизм поворота.dwg

Все соединения должны быть законтрены.
Допускаекмые смещения валов электродвигателя и редуктора
Несоосность устранить компенсирующими шайбами.
В редуктор залить индустриальное масло И-30А.
Привод обкатить без нагрузки согласно программе и методике
Тормоз поз.29 не показан
Экономика.dwg

Капитальные вложения
Эксплуатационная производительность:
Годовые текущие затраты
Себестоимость единицы работы
Годовой экономический эффект
Технико-экономические
Технико-экономические показатели
вал.dwg

Тележка ходовая ведущая _ ДП 01.00.000.dwg

Колесо ходовое ведущее
Втулка дистанционная
Электродвигатель МТF-211-6
Барабан _ ДП 11.01.000.dwg

СОДЕРЖАНИЕ.docx
1Общий обзор конструкций кранов 6
2Обзор конструкций стреловых кранов 1617
3Конструкции крановых механизмов 1820
4Патентный обзор 2831
Описание проектируемой конструкции 4145
1Конструкция башенного крана КБ - 405.1А 4145
2Электропривод башенного крана КБ - 405.1А 4348
Расчет крановых механизмов 4851
1Расчет механизма подъема груза 4851
2Проверочный расчет механизма подъема груза 5254
3Расчет механизма передвижения крана 5959
4Расчет механизма поворота крана 6264
Прочностные расчеты 6769
1Расчет барабана механизма подъема груза 6769
2Подбор подшипников оси барабана 6870
3Расчет шпоночного соединения 6972
4Расчет оси барабана на статическую прочность 7073
5Расчет сварного соединения стрелы крана 7174
Технология машиностроения 7376
1Анализ технологичности детали 7376
2Выбор типа производства 7376
3Выбор заготовки 7578
4Расчет припусков на механическую обработку 7578
5Расчет режимов резания и норм времени 7679
Охрана труда и защита окружающей среды 8284
1Задачи в области охраны труда 8284
2Характеристика Башенного крана с точки зрения охраны труда 8284
3Охрана труда при изготовлении детали 8587
4Расчет модернизируемого крана на устойчивость 8689
Экономический раздел 90
1 Расчет себестоимости и цены модернизируемой техники 90
2 Расчет годовой эксплуатационной производительности техники 92
3 Расчет годовых текущих затрат на эксплуатацию техники 93
4 Определение удельных показателей 98
Список использованных источников 102
6 Охрана труда и защита окружающей среды.docx
1 Задачи в области охраны труда
Основными задачами служб ТБ являются: подготовка комплексных планов улучшения условий труда; контроль выполнения мероприятий; правил и норм по ОТ; анализ производственного травматизма и профессиональных заболеваний; контроль качества проектов производства работ и т.д.
Превращение всех производств в безопасные с переходом от техники безопасности к безопасной технике является долговременной и глобальной задачей и области БЖД.
К безопасной технике относится : создание машин и оборудования которые не только обеспечивают безопасность и безвредность труда но и улучшают условия труда; применение машин с заниженным уровнем генерации шума вибрации электрических и магнитных полей; создание необходимых санитарно-гигиенических условий в рабочей зоне и другое. Эти задачи должны быть выполнены и учтены при проектировании разработки новых машин.
2 Характеристика башенного крана с точки зрения охраны труда
Объектом исследования является башенный кран КБ-405.1А. Для применения крана в работах он снабжен разными приборами и средствами которые позволяют обеспечить охрану труда и защиту окружающей среды.
Работа крановщика относится к третьей - тяжелой категории работ так как связана со значительными напряжениями органов чувств и нервной системы. Рабочее место машиниста - кабина выполнена из металлического сварного каркаса из уголковой стали обшит снаружи стальным листом а изнутри фанерой. Между обшивками проложен теплоизоляционный материал. Пол кабины выложен из досок покрыт фанерой и линолеумом. Дверь кабины - распашная с ручкой и замком открывается внутрь и имеет в верхней части остекление. Передняя часть кабины представляет собой остекленный фонарь обеспечивающий хороший обзор рабочей зоны. Лобовое стекло фонаря открывается наружу при открывании фиксируется и двух положениях. Для очистки стекол установлены стеклоочистители. Для предотвращения замерзания стекла лобового фонаря оно оборудовано электрическим подогревом - тепловым электронагревателем с рефлекторами для направления потока воздуха. Для поддерживания нормальной температуры воздуха внутри кабины которая должна быть в пределах 14-28 °С влажность 75% установлены подогреватели с переключением подогрева (рисунок 6.1).
Запрещается работа крана: при отсутствии достаточного освещении при сильном тумане и ливне при сильной грозе при силе ветра 15 мс и более и при других крайне неблагоприятных погодных условиях. На кране должен быть установлен анемометр.
В настоящем дипломном проекте длина стрелы увеличивается на 5 м. Возникающую вибрацию уменьшают с помощью отделки кабины также за счет изоляции в кабине доводят до стандартных параметров уровень шума.
На кран подается напряжения 220 и 380 В через трехфазную четырехпроводную сеть обеспечивающую мощность не менее 75 кВт. Напряжение в сети должно находиться в пределах 95% -110% от номинального напряжения.
Схемой электропривода предусмотрены следующие виды защит. Защита от коротких замыканий силовых цепей а также цепей управления и освещении с помощью автоматических выключателей. Защита фазных двигателей от перегрузок осуществляется с помощью максимальных реле включенных в одну фазу электродвигателя. Схемой предусмотрена тепловая защита короткозамкнутых электродвигателей: вспомогательного а также двигателей механизма подьем-спуск стрелы и передвижения отключающая двигатели от перегрузок.
Вся наружная электропроводка по крану выполнена резиновыми кабелями КГ и HPШЛ. Кабели идущие с поворотной платформы на ходовую раму провисают и образуют без кольцевой токоприемник.
При работе с небольшим числом промежуточных секций и башне шлейф укладывается в бухту на поворотную платформу за шкафом управлении. При перевозке крана по шоссейным дорогам на транспортных тележках в случае демонтажа кабины шлейф и кабели стрелы отсоединяются от клеймных наборов кабины. Разводка и кабине выполнена проводами марки ПВ1 и ПB2 уложенными в металлорукаве и кабелями типа КГ. Заземление крана проходит по технической документации приложенной к паспорту крана.
Для освещения рабочей зоны на кране установлены: прожекторы Л6 и Л12 на стреле Л7 и Л8 на флюгерах ходовой рамы светильник Л10 для освещения механизмов поворотной платформы. Включение прожекторов производится автоматическими выключателями расположенными на лицевой панели шкафа управления.
Для освещения кабины установлен светильник Л9. Звонок громкого боя включается в кабине педалью НВ1. Отопление кабины производится электронагревательными приборами ЭП1 и ЭП2 а обогрев стекла фонаря кабины - трубчатым нагревателем ЭН. В шкафу комплектного устройства в кабине установлены розетки на 12В. Габаритные огни Л14 Л15 установленные на оголовке и стреле включаются выключателем В8 на ходовой раме. В кабине предусмотрен огнетушитель марки ОУ-5 на случай возникновении пожара.
2 - выключатели отопления кабины; 34 - выключатели прожекторов; 5 - выключатель подогрева стекол; 6 - выключатель освещения кабины; 7 - вольтметр; 8 - анемометр; 9 - шкаф управления; 10 - релейный блок ограничителя грузоподъемности; 11 - панель сигнализации ограничителя грузоподъемности; 12 - осветительная лампа; 13 15 - стеклоочистители; 14 -обогреватель стекол; 16 - сигнальная лампа линейного контактора; 17 - аварийный выключатель; 18 - розетка напряжением 12 В; 19 - указатель вылета; 20 - кнопка линейного контактора; 21 - розетка напряжением 12 В; 22 - командоконтроллер стреловой лебедки; 23 - командоконтроллер механизма поворота; 24 - ножной выключатель тормоза поворота; 25 - педаль звукового сигнала; 26 - командоконтроллер грузовой лебедки; 27 - командоконтроллер механизма передвижения; 28 - кресло машиниста; 29 - электропечка; 30 - шкаф для одежды.
Рисунок 6.1 - Кабина крана
Фактический уровень шума в кабине крана составляет 50 дБ; фактический уровень вибрации составляет 17 дБ.
На кране установлены следующие контрольно-измерительные приборы в устройства безопасности: ограничитель грузоподъемности анемометр указатель вылета ограничитель вылета ограничитель высоты подъема. ограничитель нижнего положения крюка ограничитель поворота передвижении выдвижении башни счетчик моточасов блокировка грузовой тележки при обрыве каната.
Регистрация крана в Ростехнадзоре осуществляется по письменному заявлению владельца при условии предъявления паспорта на этот кран. В заявлении должно быть указано что предприятие располагает работниками и специалистами по обслуживанию крана прошедшими обучение и контроль знаний. А так же в заявлении должно быть подтверждено что данный кран находится в техническом состоянии допускающем его эксплуатацию. Должны быть представлены документы о том что монтаж башенного крана произведен в соответствии с действующими инструкциями.
Кран подлежит перерегистрации после реконструкции машины после ремонта если следствием ремонта явилось составление нового паспорта на машину. После передачи крана другому владельцу.
Крановщик должен быть не моложе 18 лет. Он проходит специальное медицинское освидетельствование. Подготовки и аттестация крановщика осуществляется в центрах имеющих лицензию Ростехнадзора. Аттестация должна проводится не реже одного раза в двенадцать месяцев.
3 Охрана труда при изготовлении детали
В разделе технологии машиностроения был разработан процесс изготовления детали - оси. Технологический процесс изготовления детали состоит из трех операций: фрезерно-отрезной токарно-винторезной кругло-шлифовальной.
Материал детали - Сталь 40Х ГОСТ 4543 74 Сталь относится к веществам пыль которых оказывает на организм человека преимущественно фиброгенное действие вызывая раздражение слизистых оболочек дыхательных путей и оседая в легких. Эта пыль образуется при металлообработке.
Нормированное содержание металлической пыли в воздухе рабочей зоны установлено по ГОСТ 12.1.005 - 88 и составляет 6 мгм3.
Перечисленные выше технологические операции относятся к физическим работам средней тяжести 2б для которых установлены следующие допустимые условия по ГОСТ 12.12.005-88.
В холодный и переходный период времени:
- температура воздуха 15 21 °С;
- относительная влажность не менее 75 %;
- скорость движения воздуха не более 03 мс.
В теплый период года:
- температура воздуха 16.. .22 °С;
- скорость движения воздуха не более 04 мс.
К разряду зрительной работы высокой точности (2В) относятся фрезерно-отрезная и токарно-винторезная операции что требует качественный подбор персонала.
Нормирование естественного освещении для цехов с металлорежущими станками по СниП 23-05-95:
- освещенность лампами накаливания суммарное общее и местное 750 лк в том числе общее 300 лк;
- допустимый коэффициент пульсации не более 10..20%.
В соответствии с ГОСТ 12.1.012-90 «Система стандартов безопасности труда. Вибрация общие требования безопасности» колебания частотой 15.. 18 Гц ощущаются как толчки а выше - вибрация. Очень опасны колебания с частотой 6 8 Гц при большой амплитуде. На рабочих местах колебания не превышают 5 Гц.
По HПБ-105-03 производство относится по пожарной опасности к категории Д производства зона класса П-1 по ПУЭ.
Электрооборудование должно иметь пылезащищенное исполнение допускаются открытые светильники. В производственном цеху общей площадью 70 м должно находится не менее двух огнетушителей. Вентиляция помещения предусматривает возможность местного отсоса воздуха.
4 Расчет модернизируемого крана на устойчивость
Все передвижные поворотные краны должны обладать достаточной для их безопасной работы устойчивостью обеспечивающей невозможность опрокидывания крана. Проверка крана на устойчивость производится при рабочемположении крана с грузом находящимся на максимальном вылете при этом уклон местности и ветровую нагрузку принимают такими чтобы они способствовали опрокидыванию крана.
Исходные данные для расчета на устойчивость модернизируемого крана:
Общий вес крана G = 1164000 H;
Грузоподъемность Q = 15000 кг;
Высота подъема груза H = 634 м;
Вылет стрелы L = 30 м;
Угол наклона крана = 1°;
Скорость подъема груза = 051 мс;
Частота вращения поворотной части = 0075 с -1;
Основные данные КБ-405.1А представлены в таблице 6.1.
Схема крана для расчета на устойчивость крана представлена на рисунке 6.2.
Таблица 6.1 - Вес основных элементов крана
Расстояние от оси крана м
Противовес на тележке
Механизмы и поворотная платформа
(1 - 1) - ось вращения крана; т.А - ребро опрокидывания; Ц.Т. - точка центра тяжести крана;
а - расстояние между линией приложения силы Q и осью вращения крана м;
b - расстояние между ребром опрокидывания и осью вращения крана м;
с - расстояние между линией приложения силы G и осью вращения крана м.
Рисунок 6.2 Схема крана для расчета на устойчивость крана
Расстояние от центра тяжести крана до ребра опрокидывания l рассчитываем по формуле (6.1):
Расстояние b конструктивно принимаем равным 3 м;
Расстояние с рассчитываем по формуле:
Gi - вес элемента крана кH.
с = (63 27 - 216 046 + 242 11 - 500 31) 1164 = 01 м
Момент удерживающий кран от опрокидывания относительно ребра А:
Mуд = G (b +c) (6.2)
Подставляя значения получаем:
Mуд = 1164 (3 + 01) = 36084 103 Нм
Опрокидывающий момент от действия инерционных сил в период неустановившегося движения при времени пуска t = 1с рассчитывается по формуле (6.3):
М1д = Q V (a - b) g t (6.3)
где V = 1 - объем груза.
М1д = 15 103 1 (27 - 3) 981 1 = 367 103 Нм
Опрокидывающий момент от центробежной силы при вращении крана считая что груз приподнят над головкой рельса на один метр определяем по формуле (6.4):
М2д = Q n2 a h 900 – H n2 (6.4)
где n = 0075 - угловая скорость вращения крана c -1.
М2д = 15 103 00752 27 442 900 – 634 0.0752 = 4193 103 Нм
Опрокидывающий момент от ветра действующий на кран рассчитываем по формуле (6.5):
М3д = Рв ка кр Fд (6.5)
где Fд - подветренная площадь крана м2;
Рв = 270 - ветровая нагрузка кН.
Fд = 03 442 = 1326 м2
= 05 h = 05 442 = 221 м2
Подставляем значения в формулу (6.5):
М3д = 270 14 04 1326 221 = 443 103 Нм
Грузовой опрокидывающий момент рассчитываем по формуле (6.6):
Мгр = Q (a - b) (6.6)
Мгр = 11 103 (27 – 3) = 264 103 Нм
Коэффициент грузовой устойчивости рассчитываем по формуле (6.7):
К = (Муд – Мiд) Мгр (6.7)
где Муд - момент удерживающий кран от опрокидывания в сторону груза Нм;
Подставляя полученные значения по формулам (6.1 - 6.6) в формулу (6.7) получаем:
K = (36084 - 367 - 4193 - 443) 103 264 103 = 118
Следовательно кран устойчив.
Модернизация башенного крана состоящая в удлинении стрелы базового крана на 5 метров привела к уменьшению коэффициента грузовой устойчивости но не ниже допустимого.
введение и обзор.docx
Грузоподъемные машины являются машинами прерывного транспорта и характеризуются тем что в рабочем цикле периоды действия отдельных механизмов перемещаются с паузами при которых работают другие механизмы.
Современные поточные технологические и автоматизированные линии межцеховой и внутрицеховой транспорт погрузочно-разгрузочные операции связаны с применением разнообразных грузоподъемных машин и механизмов обеспечивающих непрерывность и ритмичность производственных процессов.
Правильный выбор грузоподъемного оборудования является основным фактором нормальной работы и высокой эффективности производства. Переходя от применения отдельных видов подъемно-транспортной техники к внедрению высокопроизводительных комплексов.
Создаются принципиально новые системы грузоподъемных машин для комплексной механизации и автоматизации погрузочно-разгрузочных транспортных и складских работ. Современные высокопроизводительные грузоподъемные машины имеющие высокие скорости и большую грузоподъемность появились в результате постепенного совершенствования машин в течение долгого промежутка времени. Еще в глубокой древности производились строительные работы связанные поднятием и перемещением больших тяжестей.
Темпы развития подъемно-транспортного машиностроения технологический уровень и качество выпускаемого оборудования позволяют обеспечить выполнение всевозрастающего объема погрузочно-разгрузочных работ в самых различных областях народного хозяйства.
Обзор существующих конструкций
1 Общий обзор конструкции кранов
Грузоподъемными машинами обеспечивается механизация всех подъемно-монтажных и значительная часть перегрузочных операций на строительной площадке [1]. Ими также обслуживаются производственные процессы в ремонтных и других цехах.
По конструкции и виду выполняемых работ грузоподъемные машины разделяют на домкраты лебедки подъемники и краны.
Домкраты выполняют в виде толкателей - винтовых реечных или поршневых гидравлических поднимающих грузы на небольшую высоту обычно в пределах до 06 м их используют при монтажных работах.
Лебедки выполняют в виде приводного барабана с тяговым органом - стальным канатом. Они служат для прямолинейного перемещения грузов и используются как самостоятельные машины и как составные части механизмов более сложных машин.
Подъемники применяют для вертикального подъема грузов (грузовые) или людей (пассажирские) размещенных в кабинах или на площадках. Подъемники которые вместе с грузами могут перемещать и людей называют грузопассажирскими. Различают такие типы подъемников как: шахтные мачтовые ковшовые выжимные и рычажные.
Краны - универсальные грузоподъемные машины состоящие из остова в виде металлической конструкции и нескольких установленных на нем механизмов называемых крановыми. Общая классификация кранов показана на рисунке 1.1.
Большое применение в промышленности имеют передвижные консольные настенные краны (рисунок 1.2) передвигающиеся по рельсам укрепленным на стене здания [2]. Для изменения вылета стрелы эти краны обычно снабжаются тележкой или электроталью передвигающейся по горизонтальной стреле а в некоторых конструкциях стрела имеет еще дополнительную возможность поворота относительно вертикальной оси что облегчает управление краном.
Наиболее широко в промышленности используются краны мостового типа. Такой кран показан на рисунке 1.3. Он состоит из моста 11 имеющего возможность перемещения на ходовых колесах 3 которые установлены на концевых балках 4 по подкрановым путям 2 уложенным на выступах верхней части стены или колонн цеха. По верхнему (а в некоторых конструкциях - по нижнему) поясу балок моста поперек пролета цеха передвигается крановая тележка 8 снабженная подъемным механизмом 7 с грузозахватным элементом.
Рисунок 1.1 – Классификация кранов
Рисунок 1.2 – Консольный кран с тележкой
В зависимости от назначения крана на тележке можно размещать различные типы механизмов подъема или два механизма подъема один из которых является главным 7 а второй меньшей грузоподъемности - вспомогательным 6. Механизм передвижения крана 13 установлен на мосту крана; механизм передвижения тележки 12 - непосредственно на тележке. Управление всеми механизмами совершается из кабины 1 прикрепленной к мосту крана.
Ток для питания электродвигателей подается по цеховым троллеям обычно изготовляемым из прокатной стали углового профиля прикрепляемым к стене здания. Для подачи тока на кран применяют токосъемы скользящего типа прикрепляемые к металлоконструкции крана башмаки которых скользят по троллеям при перемещении моста крана. Для обслуживания цеховых троллеев на кране предусмотрена специальная площадка 10.
Для осуществления токоподвода к двигателям расположенным на тележке обычно используются троллеи изготовляемые из круглой или угловой стали. Для их установки требуются специальные стойки на площадке идущей вдоль главной балки. Поэтому в последних конструкциях мостовых кранов токоподвод к тележке осуществляется с помощью гибкого кабеля 5. В этом случае между двумя стойками установленными около концевых балок натягивается проволока 9 к которой на специальных подвесках подвешен по спирали гибкий кабель складывающийся при подходе тележки к одному концу моста а при подходе тележки к другому концу моста - растягивающийся с небольшим провесом. Применение гибкого токоподвода упростило конструкцию повысило надежность эксплуатации и снизило массу крана так как позволило отказаться от стоек и площадки для их размещения и обслуживания.
Рисунок 1.3 – Мостовой электрический кран
К кранам мостового типа относятся также козловые краны и мостовые перегружатели. При установке моста крана на двух высоких опорах перемещающихся по рельсам уложенным на уровне земли получатся козловой кран (рисунок 1.4).
Для удобства монтажа козловые краны часто изготовляют как самомонтирующиеся.
Рисунок 1.4 – Козловой самомонтирующийся кран
В этом случае мостовое строение 1 (рисунок 1.4) собирают на подставках на небольшом расстоянии от земли что облегчает производство монтажа. Поддерживающие ноги 2 соединяются шарнирами с мостом 1 и с балансирными тележками. Для подъема моста ноги соединяются полиспастами канаты от которых закреплены на барабанах 5 стягивающих механизмов имеющих ручной привод. Когда мост занимает рабочее положение балансирные тележки 4 соединяются балкой 3 а полиспастная система разбирается. В случае если одна опора крана передвигается по рельсу уложенному на фундаменте а вторая опора по рельсу расположенному на эстакаде или подкрановым балкам укрепленных на стене здания получается так называемый полукозловой кран.
В зданиях оборудованных мостовыми кранами между границами предельного приближения крюков двух соседних пролетов образуются полосы площади слабо используемые для производственных целей - так называемые «мертвые зоны». Площадь этой зоны составляет 15-20 % площади цехов. Для более полного обслуживания всей площади цеха вместо мостовых кранов опорного типа применяются так называемые подвесные краны ходовые тележки которых перемещаются по рельсовому пути уложенному не на подкрановые колонны цеха (как для опорных кранов) а по подвесному рельсовому пути.
При применении подвесных кранов снижается необходимая высота производственного помещения так как вертикальный габарит подвесного крана значительно меньше вертикального габарита опорного мостового крана. Кроме того применение подвесных кранов позволяет осуществить передачу грузов из пролета в пролет что достигается путем стыкования несущих балок двух подвесных кранов расположенных в соседних пролетах или путем стыкования несущей балки крана с однорельсовым путем соседних пролетов что дает возможность грузовой тележке с грузом перейти на несущую состыкованного с ним соседнего подвесного крана или на однорельсовый путь.
Подвесной кран (рисунок 1.5) представляет собой легкую двух опорную или многоопорную металлическую конструкцию подвешенную за ходовые каретки передвигающиеся вдоль цеха по крановым путям двутаврового сечения прикрепленным к строительным фермам перекрытия здания. Для больших пролетов эти балки могут снабжаться шпренгелем и горизонтальными и вертикальными фермами жесткости.
Управление подвесным краном может производиться из кабины подвешенной к металлоконструкции крана (неподвижная кабина) или к грузовой тележке (подвижная кабина). При малых скоростях движения крана он может иметь управление с пола. Выбор той или иной схемы управления зависит от планировки оборудования в цехе скорости передвижения крана от наличия или отсутствия переходных устройств для передачи груза в другой пролет.
Сравнительно с мостовыми кранами опорного типа подвесные краны обладают значительно меньшей массой. Грузоподъемность 8 12 и 20 т обеспечивается нормальными механизмами подъема груза унифицированными с механизмами подъема нормальных опорных мостовых кранов.
Для обслуживания больших складских или производственных площадей применяются кабельные краны (рисунок 1.6) состоящие из двух башен 1 и 7 с натянутым между ними несущим канатом 3 специальной закрытой конструкции заменяющим пролетное строение мостового перегружателя.
По несущему канату с помощью тягового каната 5 и лебедки 8 передвигается грузовая тележка 2 с грузозахватным устройством. Тяговый канат 5 огибает блоки расположенные на обоих башнях и барабан тяговой лебедки 8 и образует замкнутое кольцо с прикрепленной к нему тележкой 2. Для подъема и опускания груза в любой точке пролета крана используется подъемный канат 6 прикрепленный одним концом к тележке или к противоположной опорной башне а другим - к барабану подъемной лебедки 9. Для уменьшения провисания подъемного и тягового канатов служат поддержки 4.
Опорные башни кабельного крана могут выполняться стационарными или подвижными перемещающимися по параллельным подкрановым путям. В радиальных кабельных кранах одна из опор неподвижная а вторая перемещается по рельсовому пути представляющему собой часть окружности. В этом случае кран обслуживает площадь сектора круга. Пролеты кабельных кранов обычно равны 150 - 600 м но иногда превышают 1000 м.
Рисунок 1.5 – Подвесной двух опорный кран
Рисунок 1.6 – Схема кабельного крана
В строительных работах широко используются башенные краны различного типа передвигающиеся вдоль внешних стен строящегося здания. Изменение вылета таких кранов производится либо при перемещении грузовой тележки по однорельсовому пути прикрепленному к стреле крана либо при подъеме стрелы в вертикальной плоскости. Башенный кран (рисунок 1.7) состоит из ходовой части 1 и поворотной платформы 2 дающей возможность поворота башни 4 вместе со стрелой 5 относительно вертикальной оси. Ходовая часть и поворотная платформа связаны между собой опорно-поворотным устройством. На поворотной платформе размещаются механизм подъема груза 9 механизм поворота 10 механизм подъема и складывания стрелы в походное положение 8 противовес 7 и нижняя кабина управления 3. К головке башни подвешена верхняя кабина управления 6. Трубчатый башенный кран (рисунок 1.8) обеспечивает строительство зданий до 10 - 12 этажей имеет высоту подъема до 42 м при вылете стрелы изменяющемся от 10 до 20 м.
На рисунке 1.9 представлен портальный кран предназначаемый для погрузки и выгрузки штучных и насыпных грузов в морских и речных портах отличающихся высоким грузооборотом а также находящий применение в судостроении и на строительных работах. Он имеет жесткий четырехстоечный портал перемещающийся по рельсовому пути уложенному вдоль фронта работ. На портале установлена поворотная часть крана со стрелой подвижным противовесом и механизмами подъема и изменения вылета стрелы. Стрела представляет собой шарнирный четырехзвенник стороны которого подобраны таким образом что при изменении вылета стрелы груз практически не изменяет своего положения по вертикали. При этом мощность механизмов изменения вылета стрелы расходуется на преодоление трения в шарнирах на перекатывание канатов по блокам и на преодоление ветровых и инерционных нагрузок. Кроме того мощность расходуется на преодоление в некоторых положениях стрелы небольшого неуравновешенного момента от веса самой стрелы.
Широкое применение для работы в портах на строительствах и ремонтных работах при монтаже буровых вышек в море а также при устранении последствий аварий имеют плавучие краны (рисунок 1.10) устанавливаемые на самоходных или буксируемых понтонах. Самоходные понтоны оснащаются комплексом оборудования необходимого для навигации. Энергоснабжение крана осуществляется от силовых установок размещенных на понтоне. Приводы механизмов крана - электрические обычно постоянного тока по системе генератор-двигатель.
Автомобильные краны устанавливаются на стандартных усиленных или специальных шасси передвигающихся на пневмоколесном ходу. Автомобильные краны подразделяются на краны общего назначения используемые только при работе с грузовым крюком; полууниверсальные краны работающие с крюком и грейфером; универсальные краны работающие с любым видом сменного оборудования как кранового так и землеройного назначения (краны-экскаваторы).
Рисунок 1.7 - Башенный Рисунок 1.8 – Башенный
строительный кран с трубчатый кран
телескопической башней
На рисунке 1.11 представлен общий вид гидравлического автомобильного крана. Автомобильные краны с гидравлическим приводом имеют некоторые преимущества перед кранами с другими видами приводов. Гидравлический привод позволяет получить большое тяговое усилие без применения сложных и громоздких передач и осуществлять в широких пределах плавное регулирование скорости движения механизмов. Управление краном с гидравлическим приводом значительно проще чем кранами с механическим приводом.
Рисунок 1.9 – Портальный кран
Рисунок 1.10 – Полноповоротный плавучий кран
Рисунок 1.11- Схема автомобильного крана
2 Обзор конструкции стреловых кранов
Стреловые краны предназначены для подачи строительных конструкций и материалов на строящиеся объекты а также для механизации погрузочно-разгрузочных работ на складах [3]. В процессе монтажных работ краны используют также для поддержания конструкций при их закреплении на месте монтажа. Стреловые самоходные краны общего назначения относятся к классу грузоподъемных машин; они делятся на пневмоколесные гусеничные на специальном шасси (автомобильного типа) на автомобильные и на рельсоколесные.
Пневмоколесные и гусеничные краны различаются между собой лишь типом движителя (ходовым устройством); в остальном они имеют общую классификационную характеристику. По приводу механизмов стреловые краны делятся на две группы: с одномоторным приводом когда все рабочие механизмы приводятся одним или несколькими двигателями работающими на один вал; с многомоторным (индивидуальным) приводом механизмов когда каждый механизм приводится от отдельного двигателя. Одномоторный привод может быть механическим или комбинированным многомоторный привод - электрическим (дизель-электрическим) гидравлическим или комбинированным.
В зависимости от грузоподъемности краны делятся на три группы: легкие грузоподъемностью до 10 т; средние - грузоподъемностью от 10 до 25 т и тяжелые - грузоподъемностью 25 т и более.
На рисунке 1.12 показаны схемы стрелового крана с гусеничным и пневмоколесным типами шасси.
В стреловых кранах различают две основные части - неповоротную и поворотную. Неповоротная часть 1 (рисунок 1.12) включает в себя ходовую раму и ходовое устройство. Эта часть представляет собой основную опору обеспечивающую устойчивое положение крана и возможность его перемещения по основанию своим ходом.
Q - сила тяжести; 1 - длина стрелы; L - вылет стрелы; К колея крана; В - база крана; Н - высота подъема крюка
Рисунок 1.12- Схемы стреловых кранов
У кранов с индивидуальным приводом на раме ходового устройства расположен механизм передвижения крана вместе с приводом. Неповоротная часть гусеничных кранов выполнена в виде гусеничных тележек пневмоколесных - в виде специальных тележек на колесах с пневматическими баллонами. Поворотная часть 3 крана включает в себя сварную раму на которой смонтирована силовая установка грузовая и стреловая лебедки механизмы поворота и передвижения. На поворотной раме находится двуногая стойка к которой канатами прикреплена головная часть рабочего оборудования (стрелы башни). Основание рабочего оборудования с помощью шарниров крепят непосредственно к раме поворотной платформы. На поворотной раме расположена кабина машиниста с пультом управления. Поворотная рама с помощью опорно-поворотного устройства выполненного в виде шарикового или роликового круга опирается на раму ходового устройства крана. Такая конструкция соединения поворотной рамы с ходовым устройством дает возможность рабочему оборудованию вращаться вокруг вертикальной оси крана в любую сторону и на любой угол.
Стреловое оборудование крана может быть выполнено в виде основной стрелы 5 башенно-стрелового оборудования или стрелового оборудования с гуськом 6 выдвижной стрелы. Оголовок стрелы поддерживается канатно-блочным устройством (полиспастом). Стрела оснащена стреловым полиспастом 8 и грузозахватным устройством в виде крюка 7 для подъема штучных грузов или грейфера для подъема сыпучих и кусковых материалов. Привод 4 на гусеничных и пневмоколесных кранах может быть одно- и многомоторным. В первом случае используют дизель во втором - дизель-электрические установки; от них приводятся в движение все механизмы крана. На кранах с дизель-электрическими установками каждый механизм приводится в движение от индивидуального электродвигателя; при одномоторном приводе все механизмы получают движение от общего двигателя через систему промежуточных передач.
Грузовая лебедка служит для подъема и опускания груза стреловая - для подъема и опускания стрелы. Механизм поворота крана предназначен для вращения поворотной рамы в любую сторону.
3 Конструкции захватных устройств
В стреловых кранах в качестве тягового органа для механизмов основного и вспомогательного подъема полиспаста подъема стрелы и грейфера применяют стальные проволочные канаты. Канат состоит из стальных проволочек свитых в пряди. Пряди в свою очередь навиты вокруг сердечника из органического волокна пропитанного смазочным материалом. Сердечник служит источником смазывания внутренних проволочек каната при его изгибах на барабанах и блоках. В отдельных случаях применяют канаты с металлическим сердечником. По направлению свивки проволочек и прядей в канате различают канаты односторонней свивки и канаты крестовой свивки. При односторонней свивке проволочки в пряди и пряди в канате свиты в одном направлении. Такие канаты обладают достаточной гибкостью но легко раскручиваются. При крестовой свивке направление проволочек в прядях и прядей в канате противоположно что делает их более устойчивыми против раскручивания. На стреловых кранах применяют в основном канаты крестовой свивки.
а) шестипрядной односторонней свивки б) шестипрядной крестовой свивки
Рисунок 1.13- Стальные канаты
В зависимости от диаметра проволочек различают канаты нормальной структуры (пряди состоят из проволочек одного диаметра) и комбинированной структуры (пряди состоят из проволочек различного диаметра). Кроме того стальные канаты разделяются на обыкновенные и нераскручивающиеся которые после удаления концевых перевязок не раскручиваются. Нераскручивающиеся канаты особенно эффективны для грузовых полиспастов кранов с большой высотой подъема крюка.
По роду касания проволочек в прядях различают три типа канатов: с точечным касанием - ТК; с линейным касанием - с точечным и линейным касанием - TЛK. В кранах рекомендуется применять канаты ЛK и TЛK. На кранах применяют стальные канаты из шести прядей с числом проволочек 19 или 37 марки 1. Для стропов используют канаты с числом проволочек 37 и более а для расчалок 19. Для характеристики стальных канатов включающей их основные данные применяют условное обозначение. На первом месте указывают диаметр каната на втором - назначение каната на третьем - механическое свойство проволоки на четвертом — условия работы на пятом - сочетание направлений свивки элементов каната на шестом - способ свивки на последнем месте - маркировочную группу по временному сопротивлению разрыва проволоки. В конце приводят номер ГОСТа в соответствии с которым изготовлен канат. Так условное обозначение стального каната диаметром 345 мм крестовой свивки грузового назначения из светлой проволоки марки 1 для легких условий работы JIC нераскручивающегося Н с маркировочной группой по временному сопротивлению разрыву 180 кгсмм2: Канат 345-Г-1-ЛС-Н-180 ГОСТ 3077-69.
Работоспособность каната в значительной степени зависит от его качества которое характеризуется чистотой каната и отсутствием петель. Петли на канате образовываются в результате его неправильного разматывания из бухты или катушки; при натяжении каната петли вызывают заломы. В местах заломов проволоки перегибаются и ломаются деформируется все сечение каната включая сердечник. Деформированные места каната при работе подвергаются интенсивному изнашиванию а сердечник размочаливается и выходит из строя. При обнаружении в канате обрывов проволочек уменьшения диаметра каната а также вмятин раскрученных прядей работа на кране должна быть немедленно прекращена. На изнашивание каната и надежность работы влияют соответствие диаметра каната диаметру барабана лебедки и блоков качество навивки на барабан способ крепления внешнее состояние. Концы канатов должны быть надежно закреплены на барабанах лебедок в крюковой блочной обойме на полиспастной обойме на металлоконструкциях крана. Нарушение надежного крепления каната может привести к серьезной аварии крана повреждению поднимаемых деталей и даже к человеческим жертвам.
Существуют следующие способы закрепления канатов: с помощью клина накладных прижимающих планок клиновых зажимов петли на зажимах петли на заплетке втулки с заливкой металлом. К барабану канат крепят посредством клина прижимающего канат к стенкам барабана или с помощью накладных планок зажимающих болтами канат на поверхности барабана. Последнее крепление наиболее распространено так как позволяет достаточно просто его контролировать и регулировать натяжение болтов. При креплении каната учитывают его вытягивание под действием наибольшего усилия во время работы. На частях крана канат закрепляют с помощью петли на конце каната или клиновым зажимом. Петли всегда накладывают на стальной коуш который предохраняет канат от резкого изгиба. Свободный конец каната петли должен быть надежно закреплен на основной ветви. Чаще всего закрепляют конец каната петлей на сжимах. Применяют обыкновенные или рожковые сжимы (рисунок 1.14). Количество сжимов на канате зависит от нагрузки на него и определяется расчетным путем; их должно быть не менее трех.
а) стальной коуш; б) обыкновенный сжим; в) рожковый сжим; г) соединение концов канатной петли сжимами
Рисунок 1.14- Способы закрепления каната
Производительность стреловых самоходных кранов и безопасность производства работ в большой степени зависят от правильного выбора и рациональной эксплуатации грузозахватных и монтажных съемных приспособлений.
Грузозахватные и монтажные приспособления и устройства разделяются на две группы: съемные навешиваемые на крюк крана и съемные устанавливаемые на монтируемых элементах. В первую группу входят универсальные и специальные стропы (рисунок 1.15) универсальные и специальные траверсы захваты клещевые и подхваты электромагнитные и вакуумные захваты грейферы бадьи. Ко второй группе относятся кондукторы. Каждый стреловой самоходный кран снабжен комплектом грузозахватных приспособлений и приспособлений для временного закрепления и выверки монтируемых конструкций. Количество и номенклатура этих приспособлений должны соответствовать технологической карте монтажа данного объекта или оборудования. Наиболее распространенными и простыми по конструкции устройствами для захвата различных грузов и подвеса их на крюке крана являются стропы и траверсы. Стропы и траверсы предназначенные для подъема различных грузов деталей и конструкций называются универсальными. Стропы и траверсы конструкция которых рассчитана для подъема ограниченного количества элементов называются специальными.
а) универсальный на сплетке; б) универсальный на сжимах; в) облегченный с петлей; г) облегченный с петлей и крюком; д) облегченный с петлей и карабином; 1 - сплетки; 2 - сжим; 3 петля; 4 - крюк; 5- карабин.
Рисунок 1.15 — Стропы
Облегченный строп представляет собой отрезок каната на концах которого прочно закрепляют крюки скобы серьги или карабины. С помощью петли строп надевают на крюк крана. Все детали стропа за исключением карабина глухие неразъемные; их используют для образования петель при обвязке поднимаемых грузов а также для временного соединения с монтажными петлями скобами и крюками закрепляемыми на строительных конструкциях и деталях. Для подъема плит перекрытий длинномерных и пакетированных грузов применяют двух- и четырех ветвевые стропы. Последние представляют собой облегченные стропы (два - четыре) подвешенные к кольцу или скобе. В четырехветвевом стропе "пауке" (рисунок 1.16) канаты попарно соединяют через две скобы которые в свою очередь надевают на третью скобу. Такая конструкция обеспечивает равномерное распределение нагрузок от поднимаемых деталей на все четыре ветви стропа.
Стропы отличаются следующими недостатками: при подъеме крупногабаритных конструкций гибкие стропы занимают значительную полезную высоту подстрелового пространства; в поднимаемых элементах и деталях при небольших углах наклона стропов к горизонтали возникают сжимающие усилия которые в ряде случаев превышают расчетные нагрузки; осложнены а иногда и невозможны подъем и установка колонн в вертикальном положении. Отмеченные недостатки устраняются при использовании стропов с жесткими элементами - траверс и захватов.
- скобы; 2 - гайка; 3 - канат; 4 – карабин
Рисунок 1.16- Четырехветвевой строп «Паук»
Крупногабаритные перегородочные панели поднимают балансирной траверсой (рисунок 1.17) оснащенной жесткими металлическими тягами с петлями по концам. В эти петли закладывают штыри на которые опираются перегородки.
Железобетонные балки и фермы поднимают траверсами с гибкими захватами удерживающими монтируемые элементы в двух - четырех точках.
С помощью вилочного подхвата или траверсы с коромыслами к концам которых закрепляют цепи с крюками можно поднимать одновременно несколько плит покрытий. На монтажных работах и на складских операциях для подъема и перемещения тавровых и двутавровых железобетонных и стальных балок иногда используют клещевые захваты. Клещевой захват состоит из шарнирно соединяемых рычагов - клещей. Клещи с помощью жестких или гибких цепных подвесок закрепляют по концам траверсы подвешиваемой па крюк крана. Клещевые захваты не требуют монтажных петель и скоб в железобетонных элементах. Для временного закрепления монтируемых элементов предназначены кондукторы. Конструктивные исполнения кондукторов различны: они зависят от вида монтируемых элементов и места установки. Для временного закрепления и выверки колонн многоэтажных зданий устанавливаемых на оголовки нижестоящих колонн применяют кондукторы. Монтажные и грузозахватные приспособления должны быть стандартными заводского изготовления. Кроме того они должны иметь клеймо или прикрепленную бирку. Каждое приспособление эксплуатируемое в строительно-монтажной организации получает инвентарный номер. Данные на бирке выбивает завод-изготовитель а величины этих данных вносит монтажная организация. Сначала ставят наименование приспособления номер его зарегистрированный в книге и год изготовления затем грузоподъемность приспособления в тоннах; далее число месяц и год очередного испытания.
– серьга; 2 – канат; 3 – рейка для крепления крюка; 4 – траверса; 5 – крюк; 6 – петля.
Рисунок 1.17- Балансирная траверса для подъема перегородок
При использовании грузозахватных приспособлений необходимо помнить что запрещается эксплуатация приспособлений имеющих какой-либо дефект; трещины искривления изломы обрывы проволочек (сверх допускаемого количества) неполное количество или помятые витки резьбовых соединений и др. В период временной консервации при перерывах в работе приспособления необходимо хранить в закрытых помещениях на стеллажах или в ящиках; металлические элементы и части должны быть окрашены масляной или другой антикоррозионной краской а трущиеся сочленения покрыты смазочным материалом; на стройке должен быть ответственный для наблюдений за правильным использованием и хранением приспособлений.
Крюки служат для захватывания грузов которые подвешивают с помощью съемных грузозахватных устройств. Крюки вместе с подвижными блоками полиспаста образуют отдельный узел - крюковую подвеску (рисунок 1.18).
а) грузоподъемностью 63 т; б) грузоподъемностью 16 т.
Рисунок 1.18 – Крюковые подвески
Крюковая подвеска грузоподъемностью 16 т состоит из крюка 1 траверсы 3 щек 4 и блоков 13. Крюк с хвостовиком входит в траверсу и удерживается гайкой 19 стопорящейся шайбой 5 и винтами. Свободное вращение крюка обеспечивается упорным подшипником 17 заключенным в кольцо 18. Траверса закреплена в щеках 4 подвески оседержателями. Щеки соединены между собой втулками 14. Оси блоков удерживаются от выпадения и проворачивания в щеках специальными гайками. В верхней части щек подвески закреплена ось 15 на втулке которой помещается коуш с грузовым канатом. Крюковые подвески кранов различают по грузоподъемности количеству и расположению блоков. Крюковые подвески грузоподъемностью 63 т не имеют блоков и грузовой канат 12 закрепляется в коуше 11 соединяемом с верхней траверсой 8 с помощью серег 10.
Наибольшая грузоподъемность крюка устанавливается в зависимости от режима работы и типа привода. По этим признакам различают три категории крюков: для ручного привода для легкого и среднего режимов и для тяжелого режима работы. Крюки по наибольшей грузоподъемности разделены на номера от 1 до 26. Для каждого номера принято три крюка. Для стреловых кранов грузоподъемностью от 63 до 100 т крюки выбирают соответственно от номера 14 до номера 26 для легкого и среднего режима работы.
Крюки предназначаемые для подъема грузов на основной и удлиненных стрелах называются крюками механизма основного подъема (основными крюками); крюки используемые для подъема грузов на гуськах называются крюками механизма вспомогательного подъема (вспомогательными крюками).
Форма крюка препятствует выпадению чалочных канатов колец стропой и серег из его зева. Кроме того грузовые крюки должны быть снабжены предохранительным замком 2 (рисунок 1.18) удерживающим съемное грузозахватное приспособление от самопроизвольного выпадения. Согласно «Правилам» Ростехнадзора крюки без предохранительного замка можно применять при условии использования гибких грузозахватных приспособлений. Крюки кранов грузоподъемностью 25 т и выше применяемых на монтажных работах снабжают предохранительными замками. Машинист должен следить за тем чтобы износ крюка в зеве не превышал 10 % проектной высоты сечения в этом месте. На крюке не должно быть трещин надрывов или искривлений. Поломка крюка может вызвать аварию крана травму людей. На крюке обязательно должен быть указан его номер по ГОСТу наименование завода-поставщика и год изготовления.
В зависимости от вида выполняемых работ (погрузочно-разгрузочных монтажных вертикального транспортирования грузов) используют различные стрелы [4].
По способу изменения вылета крюка (перемещения груза) различают подъемные стрелы и балочные стрелы с грузовыми тележками. Наиболее распространенны подъемные стрелы. Стрела представляет собой металлическую конструкцию предназначенную для обеспечения требуемой величины вылета и высоты подъема крюка. Стрела прямоугольного или треугольного поперечного сечения состоит из основания промежуточных секций и головной секции (головки). Основание стрелы оканчивается пятой с отверстиями в которые закладывают оси или пальцы для соединения с проушинами поворотной платформы. На одной оси на головке стрелы помещают грузовые и стреловые канатные блоки а также устанавливают ограничитель высоты подъема крюка.
Сжимающие нагрузки от массы поднимаемого груза массы стрелы усилий в канатах воспринимаются в основном поясными элементами стрелы. Раскосы и диафрагмы стрелы служат для восприятия скручивающих усилий и поперечных сил. Стрела приспособлена к работе в основном на сжатие и восприятие момента от собственного веса. Практически стрела мало приспособлена к восприятию изгибающих нагрузок которые могут возникнуть в частности при отклонении грузового полиспаста из плоскости подвеса стрелы. Существует два способа соединения секций стрел и гуськов: шарнирное (пальцевое) и жесткое (болтовое). Шарнирное соединение обеспечивает меньшую трудоемкость сборки и разборки рабочего оборудования кранов с помощью собственных механизмов без дополнительных грузоподъемных средств. Подъемную стрелу подвешивают к двуногой стойке установленной на поворотной платформе стреловым полиспастом. Конец каната полиспаста направляется на барабан стреловой лебедки. Подъем или опускание стрелы сопровождается подъемом или опусканием груза который описывает при этом криволинейную траекторию в пространстве. Головные секции стрел могут быть оборудованы специальным жестким наголовником с грузовым полиспастом. Наголовник позволяет увеличить подстреловое пространство и поднимать крупногабаритные тяжелые грузы на минимальном вылете крюка.
Стрелу с помощью которой поднимают груз массой равной максимальной грузоподъемности крана называют основной. Длина основной стрелы в зависимости от грузоподъемности крана (16 - 100 т) принимается от 10 до 20 м. Для монтажных работ используют удлиненные стрелы. Чтобы удлинить основную стрелу ее снабжают промежуточными типовыми сменными секциями. В ряде случаев стрелы длиной свыше 40 м изготовляют с применением трубчатых элементов а не составляют из типовых секций на базе основной стрелы.
Стрелы кранов в основном выполняют прямолинейными. На кранах грузоподъемностью до 10 т часто применяют основную стрелу ломаной конфигурации. Стрелы изготовляют решетчатыми сварными из уголков и труб или из элементов коробчатого сечения из стального листа. Стрела состоит из четырех (трех) основных поясных уголков (труб) соединенных на сварке раскосами.
Выдвижная стрела стоит из двух или нескольких секций - опорной (неподвижной) и выдвижной телескопически входящей внутрь опорной для изменения ее длины без рабочей нагрузки. Перемещается выдвижная секция по направляющим опорным каткам с помощью канатной передачи гидро- или пневмопривода.
Коробчатые выдвижные стрелы часто изготовляют с отверстиями в боковых стенках для снижения их массы. На оголовке подвижной секции установлены грузовые канатные блоки а на опорной части закреплены канаты для выдвижения секций.
Гуськи позволяют увеличивать зону обслуживаемую краном как в горизонтальной так и в вертикальной плоскостях и применять второй грузовой крюк для подъема более легких грузов. Гусек представляет собой дополнительную стрелу шарнирно закрепляемую на оголовке основной или удлиненной стрелы что дает возможность изменять ее положение в вертикальной плоскости. Перестановка гуська в зависимости от конструктивного исполнения является установочной или рабочей операцией. Гуськи которые не изменяют вылет с грузом относительно стрелы называются неуправляемыми (установочными). Гуськи изменяющие вылет с грузом на крюке называются управляемыми (маневровыми).
Неуправляемый гусек представляет собой конструкцию треугольной формы изготовленную из уголков и швеллеров или из труб. На оголовке гуська закреплены грузовые блоки внутри гуська установлен отводной ролик для направления грузового каната к лебедке вспомогательного подъема расположенной на поворотной платформе. Неуправляемый гусек удерживается неподвижно во время работы на стреле канатными тягами. Канатные тяги соединяют хвостовую часть гуська с опорной секцией стрелы. Вылет крюка изменяют путем увеличения или уменьшения длины канатных тяг с помощью стяжных приспособлений - фаркопфов. Длина неуправляемых гуськов в зависимости от грузоподъемности крана колеблется от 4 до 12 м длина управляемых - 30 м и более.
Управляемый гусек представляет собой решетчатую конструкцию из уголков или груб и состоит из опорной головной и промежуточных сменных секций. На головной секции закреплены грузовые блоки и ограничители высоты подъема крюка. Опорная секция гуська шарнирно соединена со стрелой а головная секция подвешена на канатных тягах к подстрелку. Хвостовая часть подстрелка удерживается с помощью полиспаста канат которого проходит у основания стрелы и направляется на лебедку. Вылет управляемого гуська изменяют с помощью стреловой лебедки.
Управляемые гуськи на наклонных стрелах улучшают параметры крана - увеличивают высоту подъема и вылет крюка. Однако наклонная стрела ограничивает полезное подстреловое пространство вследствие чего снижаются ширина и высота монтируемого краном сооружения. Поэтому применяют краны с башенно-стреловым оборудованием (рисунок 1.19) т. е. с вертикально или под небольшим углом установленной башней на верху которой шарнирно закреплена дополнительная стрела (маневровый гусек) подвешенная на канатных тягах. Вылет стрелы изменяется с помощью полиспаста и стреловой лебедки. В этом случае верхняя часть башни удерживается канатными тягами а основание шарнирно соединяется с платформой.
Башенно-стреловое оборудование позволило расширить границы применения стреловых краном: их используют вместо башенных передвижных кранов при возведении многоэтажных зданий и сооружений башенного типа. Грузоподъемность кранов с башенно-стреловым оборудованием при одинаковой высоте подъема крюка превышает в 2-3 раза грузоподъемность кранов с наклонной стрелой.
Сменное башенно-стреловое оборудование увеличивает универсальность стреловых кранов при этом их мобильность и маневренность сохраняются. Трудоемкость монтажно-демонтажных операций башенно-стрелового оборудования значительно ниже чем башенных передвижных кранов.
На стреловых кранах с гидроприводом также предусматривается башенно-стреловое оборудование с дополнительными телескопическими (выдвижными) стрелами и выдвижными башнями.
а) стрела с маневровым гуськом; б) башня с подъемной стрелой;
в) телескопическая башня со стрелой оборудованной грузовой тележкой
Рисунок 1.19 - Башенно-стреловое оборудование кранов
В результате проведения патентного обзора были выявлены следующие пути модернизации башенных кранов:
4.3 Грузозахватные устройства
4.4 Предохранительные устройства
Известна грузоподъемная лебедка содержащая основной и дополнительный приводы барабан и суммирующую зубчатую передачу включающую в себя цилиндрический и планетарный редукторы причем водило последнего кинематически связано с барабаном причем водило планетарного редуктора выполнено полым и закреплено в опоре а электродвигатели основного и дополнительного приводов расположены соосно с противоположных сторон планетарного редуктора причем вал планетарного редуктора соединенный с электродвигателем дополнительного привода расположен внутри водило планетарного редуктора.
Недостатком лебедки является громоздкость конструкции и неудобство сборки.
Наиболее близкой к изобретению является грузоподъемная лебедка содержащая полую центральную неподвижную ось выполненную с радиальным уширением в средней части в котором как в корпусе размещен двухступенчатый редуктор. Ведущая шестерня первичного вала редуктора кинематически связана с зубчатыми колесами установленными каждое на одном из по меньшей мере трех вторичных валов шестерни которых в свою очередь кинематически связаны с зубчатым венцом соединенным с барабаном.
Недостатком этой лебедки является недостаточная надежность за счет большого числа конструктивных элементов входящих в ее состав.
Достоинствами изобретения являются снижение веса и габаритов лебедки повышение технологичности конструкции и удобство сборки.
Лебедка [6] относится к грузоподъемным механизмам в частности к лебедкам.
Известна ручная лебедка содержащая смонтированные в корпусе червяк и червячное колесо с кольцевым пазом для каната имеет опору на корпусе и ось контактирующую с продольным пазом Н-образной стойки одна из частей которой выполнена в виде зубчатой рейки находящейся в зацеплении с зубчатым сектором закрепленным на червячном колесе а опорная пластина стойки установлена асимметрично при этом в качестве захватного приспособления используется карабин.
Недостатком этой ручной лебедки являются ограниченные технологические возможности и значительные требования к физическим данным человека.
Наиболее близкой к изобретению является ручная лебедка содержащая приводной вал и барабан выполненные на одной оси и состоящие из ряда осей расположенных под углом 90° причем угол между приводной и приемной осью составляет также 90°. В результате этого происходит пропорциональное изменение плеч тягового усилия и веса человека относительно оси.
Недостатком этой лебедки является недостаточная надежность.
Использование предлагаемого технического решения позволяет механизировать процесс работы и значительно снизить требования к физическим данным человека.
Устройство [7] относится к области буксирных систем в которых поддерживается электрическая связь с буксируемым объектом.
Известна лебедка в которой на барабане лебедки намотан кабель трос который в разветлителе делится на две ветви - силовую и сигнальную. Ветвь поступает на токопереход и ветвь на пульт. Пульт установлен на настиле через шариковую опору и окружен жестко связанным с ним ограждением. Линия питания указанного пульта подведена через токопереход. Сигнальная ветвь помещена в металлическую гофрированную трубу (сильфон) которая в свою очередь расположена в неподвижной трубе. Труба имеет на конце фланец соединенный с корпусом и крышкой. Уплотнение фланца и сильфона осуществлено резиновыми кольцами. Со стороны опоры закрепление трубы и сильфона аналогичное. Пространство между сильфонами и трубой заполнено машинным маслом заливаемым через горловину.
Недостатком этой лебедки является узкий спектр эксплуатационных возможностей.
Наиболее близкой к изобретению является лебедка (рисунок 1.20) содержащая барабан связанный с приводом импульсивной передачей состоящей из эксцентрика установленного на ведущем валу и связанного с барабаном храповым колесом взаимодействующим с собачками на эксцентрике установлено с возможностью вращения водило шарнирно связанное с храповым колесом с внутренним зацеплением а собачки кинематически связаны с барабаном.
Достоинством данного изобретения является автоматическое изменение передаточного числа импульсивной передачи в зависимости от нагрузки.
Рисунок 1.20 – Лебедка
Изобретение [8] относится к грузоподъемным устройствам.
Известна грузовая лебедка содержащая гидромотор вал которой через управляемую муфту связан с опорной рамой и планетарный редуктор в виде отдельного модуля связанного с барабаном для каната и включающего в себя солнечную шестерню первого планетарного ряда связанную с валом гидромотора и зацепленную через сателлиты с коронной шестерней этого ряда сателлиты второго планетарного ряда зацепленные с коронной шестерней этого ряда связанной с упомянутым барабаном и водила для обоих рядов обеспечивающие поперечную и продольную ориентацию сателлитов.
Недостатком данного изобретения является невозможность контактирования сателлитов со стенками корпуса редуктора и как следствие не ограничение их перемещения в осевом направлении.
Наиболее близкой к изобретению является лебедка содержащая неподвижный корпус барабан с тросом встроенный цилиндрический планетарный редуктор и центральный приводной вал. Редуктор включает две концентрично расположенных на одном водиле группы сателлитов. Каждая группа сателлитов входит в зацепление со своим центральным колесом размещенным на приводном валу и с охватывающими их зубчатыми венцами. Два зубчатых венца неподвижно размещены на корпусе а один - на барабане. Сателлиты находящиеся в зацеплении с зубчатыми венцами корпуса выполнены на единой ступице. Центральные колеса жестко связаны между собой приводным валом имеющим возможность осевого перемещения вдоль оси барабана. Лебедка имеет два режима работы. При рабочем режиме работы вращение барабана осуществляется оператором от приводного вала через планетарный редуктор к зубчатому венцу барабана. При холостом режиме работы оператор извлекает приводной вал разъединяя друг от друга центральные колеса что приводит к разрыву кинематической связи между группами сателлитов и прикладывая усилие к разматываемому тросу осуществляет вращение барабана.
Достоинством данного изобретения является повышенная надежность лебедки и экономичность энергозатрат.
Изобретение [9] относится к подъемно-транспортным машинам а именно к устройствам которые могут быть применены в области промышленного и гражданского строительства.
Известен башенный кран (рисунок 1.21) содержащий неповоротную башню стрелу с грузовой тележкой поворотно-передаточное устройство с
кронштейнами для подвеса траверс поднимаемых вспомогательным грузоподъемным механизмом.
Недостатком данного крана является его узко ограниченное применение из-за неповоротной башни.
Наиболее близким к изобретению является грузоподъемный кран (рисунок 1.22) содержащий смонтированную на транспортном средстве колонну ни подшипнике и платформу на катковой опоре причем ни платформе установлены каркас и стрела. Также кран снабжен балансирами шарнирно прикрепленными к платформе и колонне причем стрела и каркас шарнирно смонтированы на балансирах.
Рисунок 1.21 - Башенный кран
Достоинством данного изобретения является снижение веса металлоконструкций крана и строительных затрат.
Изобретение [10] относится к подъемно-транспортным машинам а именно к устройствам которые могут быть применены в области промышленного и гражданского строительства.
Известен кран-манипулятор включающий опору с установленной на ней поворотной платформой стреловой механизм шарнирно установленный на
поворотной платформе выполненный в виде стрелы гуська оттяжки и противовеса шарнирно соединенных между собой с образованием уравновешенного многозвенника шарниры соединения гуська и противовеса с оттяжкой которого расположены выше шарниров соединения гуська и противовеса со стрелой силовые элементы шарнирно соединенные с уравновешенным многозвенником стрелового механизма.
Недостатком данного крана является усложненная конструкция манипулятора.
Наиболее близким к изобретению является кран-манипулятор содержащий колонну несущую шарнирно закрепленную стрелу с рабочим органом механизм ориентации которого выполнен с гидроцилиндром а на осях шарниров соединения стрел установлены направляющие блоки равного диаметра через которые запасованы тросы одни концы которых закреплены на штоках гидроцилиндров а другие - запасованы на блоках жестко соединенных с осями механизма ориентации причем намотка троса произведена в одном направлении.
Достоинством данного изобретения является упрощение конструкции манипулятора.
Известен башенный кран [11] содержащий смонтированную в горизонтальных направляющих тележку с ходовой рамой на которой установлена башня с оголовком стрелой и консолью и балласт состоящий из набора плит снабженный закрепленными по углам ходовой рамы стойками при этом верхняя плита балласта выполнена с отверстиями в которых размещены стойки и установлена с зазором относительно ходовой рамы а нижняя плита выполнена с катками размещенными в горизонтальных направляющих (рисунок 1.23).
Преимущество этого крана - долговечность недостатком же является усложнение конструкции.
Рисунок 1.22 - Грузоподъемный кран
Рисунок 1.23 - Башенный кран
Изобретение [12] относится к области подъемно-транспортного машиностроении а именно к грузозахватным устройствам.
Известна грузозахватная траверса (рисунок 1.24) содержащая консольную балку подвижный контргруз серьги для подвеса балки к главному и вспомогательному крюкам грузоподъемной машины и грузозахват закрепленный на консоли балки.
Недостатком данного изобретения является малая грузоподъемность и невозможность увеличения радиуса действия траверсы. Наиболее близким к изобретению является грузозахватное устройство (рисунок 1.25) содержащее траверсу несущую балку с тремя парами строп при этом каждая пара строп соединена между собой в средней части жесткой связью причем длина ветвей
каждой последующей пары строп короче предыдущей не менее толщины плиты.
Рисунок 1.24 - Грузозахватная траверса
Недостатком данного изобретения является ограниченная область его применения. Устройство используется преимущественно для транспортирования плит перекрытий.
Достоинствами данного изобретения являются исключение соударений транспортируемых изделий и последовательная укладка на перекрытие.
Изобретение [13] относится к области подъемно-транспортного машиностроения а именно к грузозахватным устройствам.
Известно грузозахватное устройство (рисунок 1.26) содержащее корпус с прорезью подвешенный через блочную обойму на грузовом канате к грузоподъемному механизму шарнирно закрепленный на корпусе захватный крюк подпружиненную защелку и механизм отстроповки который содержит вертикально установленный на корпусе подпружиненный шток нижний конец которого связан с закрепленным на корпусе угловым рычагом взаимодействующим с подпружиненной защелкой а на верхнем - закреплен двуплечий рычаг снабженный вилкой взаимодействующей с установленным на грузовом канате упором.
Недостатком данного изобретения является недостаточная надежность за счет большого числа конструктивных элементов входящих в его состав.
Наиболее близким к изобретению является грузовой полиспаст переменной кратности для кранов содержащий канат огибающий блоки подвижной крюковой подвески и промежуточной обоймы попеременно фиксирующейся со стрелой крана и с подвижной крюковой подвеской в зависимости от кратности полиспаста и фиксаторы; промежуточная обойма выполнена по крайней мере из двух блочных подвесок снабженных фиксаторами для соединения их между собой и с крюковой подвеской или металлоконструкцией крана в зависимости от требуемой кратности.
Рисунок 1.25 – Грузозахватное устройство
Достоинством данного изобретения является увеличение числа возможных перемен кратности полиспаста.
Схема устройства показана на рисунке 1.27.
Изобретение [14] относится к области подъемно-транспортного машиностроения а именно к устройствам обеспечивающих безопасность при эксплуатации кранов.
Известна выносная опора грузоподъемного крана включающая шарнирный четырехзвенник с опорной пятой и гидроцилиндр шток которого связан тягой с верхним звеном четырехзвенника.
Недостатком данного изобретения является большой ход гидроцилиндра.
Наиболее близким к изобретению является опорное устройство грузоподъемной машины содержащее закрепленные на опорной раме машины винтовые якоря взаимодействующие с опорной поверхностью и снабженные приводным механизмом который консольно смонтирован на поворотной платформе машины на расстоянии от ее оси вращения равном расстоянию от каждого винтового якоря до упомянутой оси.
Недостатком данного изобретения является то что оно применимо только для кранов с поворотной платформой.
Достоинством изобретения является упрощение конструкции за счет использования одного приводного механизма для выдвижения всех винтовых якорей.
Схема устройства показана на рисунке 1.28.
Рисунок 1.26 – Грузозахватное устройство
Рисунок 1.27 – Грузовой полиспаст переменной кратности для канатов
Изобретение [15] относится к области подъемно-транспортного машиностроения а именно к устройствам обеспечивающих безопасность при эксплуатации кранов. Известен противоугонный рельсовый захват для кранов содержащий шарнирно-сочленненые клещевые захватные рычаги смонтированные в корпусе ходовой тележки и взаимодействующие с головкой рельса.
Недостатком данного изобретения является недостаточная надежность работы.
Рисунок 1.28 - Опорное устройство грузоподъемной машины
Наиболее близким к изобретению является грузоподъемное устройство автоматического действия (рисунок 1.29) содержащее подвижный мост с перемещающейся по нему тележкой несущей механизм подъема телескопическую колонну выполненную из грузовой кабины промежуточной секции и рамы с захватами и страхующие груз подхваты установленные в нижней части грузовой кабины а к раме с захватами подвешена рамка с упругой сеткой закрывающая тару во время движения.
Недостатком данного изобретения является его узкий профиль применения преимущественно для межоперационного распределения груза при обслуживании поточных линий автоматизированными транспортными системами.
Достоинством данного изобретения является его повышенная безопасность.
Изобретение [16] относится к области подъемно-транспортного машиностроения а именно к устройствам обеспечивающих безопасность при эксплуатации кранов.
Известен ограничитель размотки каната лебедки содержащий установленный на внутренней части оболочки барабана подпружиненный шток одним концом взаимодействующий через отверстие в оболочке с контрольным витком каната а другим - с исполнительным механизмом.
Недостатком данного изобретения является недостаточная точность отключения привода лебедки.
Наиболее близким к изобретению является предохранительное устройство лебедки (рисунок 1.30) снабженное амортизационным механизмом выполненным из двух торцевых храповиков один из которых прикреплен к барабану лебедки а второй горизонтально-подвижно на шлицах соединен с опорой лебедки и кинематически связан с приводом сцепления храповиков который снабжен толкателем связанным с подвижным храповиком и имеющим ползун с шарнирно соединенными с ним подпружиненными тягами и вильчатым рычагом противоположное плечо которого кинематически связано с профильной поверхностью подвижного диска скрепленного с валом амортизационного механизма причем подпружиненные тяги вторым концом шарнирно прикреплены к шарнирным стрежням связанным с опорой лебедки а рычаг снабжен дополнительно рукояткой для ручного управления.
Рисунок 1.29 – Грузоподъемное устройство автоматического действия
Недостатком данного изобретения является его недостаточная надежность за счет большого количества конструктивных элементов входящих в его состав.
Достоинством данного изобретения является повышенная защищенность привода лебедки и амортизационного механизма при перегрузках.
Рисунок 1.30 - Предохранительное устройство лебедки
4.6 Крановые механизмы
Изобретение [17] относится к области подъемно-транспортного машиностроения а именно к механизмам обеспечивающим непрерывность технологического процесса.
Известно прижимное устройство для каната лебедки содержащее расположенный вдоль образующей барабана ролик установленный с возможностью вращения на валу закрепленный на подпружиненных поворотных рычагах смонтированных в кронштейнах рамы лебедки.
Недостатком данного изобретения является сложность конструкции а также его большие габариты.
Наиболее близким к изобретению является канатоукладчик содержащий прижимной ролик закрепленный на одном из плеч подпружиненного рычага и воздействующий на канат наматываемый на барабан приводной лебедки; на свободном плече рычага шарнирно смонтирована жесткая тяга соединенная с исполнительным механизмом взаимосвязанным с приводным двигателем лебедки.
Достоинством данного изобретения является обеспечение постоянства скорости подъема груза при многослойной навивке каната.
Схема устройства показана на рисунке 1.31.
Рисунок 1.30 - Канатоукладчик
Изобретение [18] относится к области подъемно-транспортного машиностроении а именно к устройствам обеспечивающим безопасность и непрерывность технологического процесса.
Известен грузоупорный тормоз содержащий ведущий тормозной диск соединенный с валом посредством винтовой нарезки ведомый тормозной диск жестко закрепленный на валу и опорный диск стопорного механизма установленный между ведущим и ведомым тормозными дисками.
Недостатком данного изобретения является недостаточная надежность удержания груза из-за нестабильности тормозного момента.
Наиболее близким к изобретению является устройство для стопорения крана содержащее установленный на подкрановых путях тупиковый упор и подвижный удерживающий стержень с головкой вводимой в зацепление с ходовой тележкой крана посредством управляющего приспособления и удерживаемой в сцепленном положении фиксирующим элементом; тупиковый упор снабжен направляющими в которых установлен с возможностью поворота относительно их продольной оси стержень а управляющее приспособление выполнено в виде закрепленной на стержне рукояти служащей противовесом фиксирующим стержень с головкой в сцепленном положении.
Недостатком данного изобретения является недостаточная надежность удерживающего стержня с головкой.
Достоинством данного изобретения является простота его конструкции. Схема устройства показана на рисунке 1.32.
Рисунок 1.32 - Устройство для стопорения крана
Описание проектируемой конструкции
1 Конструкция башенного крана КБ - 405.1 А
Башенный кран КБ - 405.1 А (рисунок 2.1 ) предназначен для механизации строительства жилых многоэтажных и промышленных зданий при температуре окружающего воздуха от - 40 до +40°С.
- ходовая ведущая тележка 2 - ходовая рама 3 - противовес 4 - стреловая лебедка 5 - канат стреловой 6 - канат грузовой 7 - оголовок 8 - расчал стреловой 10 - крюковая подвеска 11 стрела 12 - кабина 13 - башня 14 основание башни 15 - механизм поворота 16 - ходовая рама.
Рисунок 2.1 - Общий вид крана
Кран КБ-405ЛА является строительным башенным краном с поворотной платформой и унифицированными механизмами. Монтаж крана производится собственными механизмами и вспомогательным автокраном. Башня крана подращивается снизу отдельными секциями по мере возведения здания. Кран перевозится в собранном виде на специальных подкатных тележках переоборудованных автомобильным тягачом. Секции башни стрелы плит противовеса перевозятся стандартным автотранспортом. По железной дороге кран перевозится отдельными узлами.
Управление краном производится командоконтроллерами из навесной кабины машиниста расположенной в верхней части крана.
Кран содержит механизмы подъема груза передвижения крана вылета стрелы поворота.
Управление механизмами при монтаже и испытании крана осуществляется с выносного унифицированного пульта управления башенного крана.
Кран снабжен ограничителями высоты подъема крюка изменения вылета высоты подъема башни грузоподъемности поворота передвижения а также указателями вылета грузоподъемности и анемометром.
Ходовая рама представляет собой кольцо коробчатого сечения сварной конструкции с проушинами для крепления четырех поворотных флюгеров расположенных по диагоналям.
Поворотная платформа состоит из кольцевой рамы коробчатого сечения и приваренных к ней двух боковых балок и одной задней балки. На боковых балках платформы приварены две трубчатые шпренгельные фермы соединенные между собой поперечными связями.
Башня крана состоит из оголовка верхней секции нити промежуточных секций портала и подвижной обоймы. Башня решетчатой конструкции выполнена из горячекатаных и холоднотянутых труб. Раскосы и поперечные связи башни имеют сплющенные штампованные концы. Стыки секций башни - болтовые на фигурных фланцах проходящих по направляющим роликам при выдвижении башни. Заделка башни в рабочем положении производится только в нижнем ярусе. При этом башня опирается через подвижную обойму на четыре угловые балки.
Портал представляет собой две трехгранные фермы соединенные в двух ярусах коробчатыми балками.
Оголовок состоит из металлоконструкции распорки с канатной оттяжкой монтажной стойки с оттяжкой стойки и лестницы для обслуживания блоков и анемометра. В нижней части оголовка как и в промежуточной секции предусмотрен настил с откидным люком и поручнем.
Противовес расположен на поворотной платформе и состоит из шести блоков которые крепятся стяжкой к поворотной платформе. На блоках имеются скосы для монтажного подкоса. Блоки - бетонные (марка бетона М300) окантованные уголком.
Навесная кабина машиниста имеет металлический сварной каркас из уголковой стали обшитый с наружи стальным листом а изнутри - фанерой. Между обшивками проложен теплоизоляционный материал. Пол кабины выполнен из досок покрыт фанерой и линолеумом.
Лебедка стреловая предназначена для монтажа крана и подъема стрелы в горизонтальное или наклонное положение. Она представляет собой моноблочную безрамную трехопорную конструкцию и прикрепляется к поворотной платформе крана четырьмя болтами через сферические опоры.
Стрела крана балочного типа одноподвесная секционная. Пояса по всей длине параллельны между собой. Стрела состоит из четырех секций. Верхний пояс стрелы раскосы и связи выполнены из груб. Нижние пояса стрелы - коробчатого сечения сваренные из дух не равнобоких угольников.
Расчал стреловой состоит из каната и подвижной обоймы. Подвижная обойма состоит из щек внутри которых расположены блоки стрелоподъемного полиспаста.
Крюковая подвеска служит для подвешивания такелажных приспособлений при помощи которых зачаливается груз. Крюковая обойма двухблочная с расстоянием между канатами 1200 мм (для предотвращения закручивания канатов).
Используя авторское свидетельство №998317 предлагается к балочной стреле содержащей пролетную и консольную части стреловой расчал удерживающий стрелу направляющие блоки установленные на нижней части головки стрелы конце стрелы и на оголовки башни огибаемые грузовым канатом установить дополнительные блоки один из которых - в первой пролетной части стрелы сверху а другой во второй пролетной части стрелы снизу огибаемые грузовым канатом.
При такой конструкции усилие в ветви грузового каната снижает величину максимального изгибающего момента в плоскости подвеса стрелы как на консольной части так и в пролетной части. За счет этого мы увеличиваем длину стрелы базовой модели чем увеличиваем рабочую зону крана.
2 Электропривод башенного крана КБ - 405.1 А
Привод крана электрический от генератора типа ЕСС5-4М101 мощностью 375 кВт. На кране возможно совмещение подъема (опускания) крюка или стрелы с вращением поворотной платформы.
Принципиальная схема электрооборудования стрелового крана показана на рисунке 2.2. Все электродвигатели применяемые на кране кранового исполнения переменного тока напряжением 380 В и частотой 50 Гц.
При работе заземление крана осуществляется присоединением нулевого провода генератора к металлоконструкции крана.
При работе необходимо провести следующие переключения: трех полюсный пакетный переключатель SA7 перевести в положение «Генератор» что соответствует замыканию контактов 32-М1 33-М2 34-M3 включить автоматический выключатель QF1 переключатель приборов SA6 перевести и положение «Кран» что соответствует замыканию контактов 71-72 запустить двигатель.
Проверяется работа приборов контроля двигателя работы звукового сигнала и осветительных приборов устанавливается универсальный переключатель SA4 в положение «Нормальная работа» контроллеры — в нулевое положение переключатель грузовых характеристик на релейном блоке ОГП-1 устанавливается на соответствующую характеристику кратко временным нажатием на кнопку SB7 возбуждают генератор. После этого нажатием кнопки SB1 подают питание от сети трех фазного тока к катушкам магнитных пускателей КМ1 и КМ2 в результате чего замыкаются вспомогательные контакты 12-24 пускателя КМ1 который переходит на самопитание а через главные контакты магнитного пускателя КМ1 подается питание от переключателя SA7 к контроллерам. Пускатели КМ1 и КМ2 включены вспомогательные контакты пускателя КМЗ замыкаясь включают пускатель КМ5. После этого можно включать любой механизм крана включением соответствующего контроллера а механизм стрелы - нажатием кнопки SB4 или SB5.
Электродвигатель механизма подъема груза M1 подключен к сети через кулачковый контроллер SA1 и магнитный пускатель КМЗ контроллер включается в сеть фазами Л1 и Л2. При переводе ручки на себя (подъем) замыкаются контакты пускателя КМ1 и КМ5 и подается питание на электродвигатель и привод тормоза. Остановка осуществляется путем перевода рукояти контроллера груза SA1 в нулевое положение при этом происходит отключение двух фаз в цепи электродвигателя и тормоза.
Регулирование скорости подъема и опускания груза происходит путем переключения контроллером резистора в цени ротора. При первом положении рукояти контроллера SA1 соответствующем включению всего сопротивления резистора в цепи ротора пусковой момент электродвигателя соответствующий первому и второму положению контроллера и груз в этом случае не поднимается. Для подъема таких грузов рукоять контроллера переводят в третье а затем в четвертое и пятое положение.
При опускании груза питание электросхемы (электродвигателя) может осуществляться двумя способами: от сети переменного тока и от сети постоянного тока что обеспечивает понижение скорости. При питании электродвигателя от сети переменного тока универсальный переключатель SA4 находится в положении «Нормальная работа» и рукоять контроллера SA1 переводится на спуск. При этом замыкаются контакты КМ1 КМ2 КМЗ.
Работа всей остальной пускорегулирующей аппаратуры аналогична работе соответствующей подъему груза будет при первом положении рукояти контроллера SA1 а максимальная при пятом положении. Не разрешается опускать грузы по массе близким к номинальным при первом и втором положениях контроллера SA1 во избежании разноса электродвигателя. При работе крана без динамического торможения универсальный переключатель должен находиться в положении «Нормальная работа».
Рисунок 2.2 - Принципиальная схема электрооборудования крана
Регулировка скорости опускания груза осуществляется контроллером SA1 за счет введения резисторов в цепь ротора электродвигателя. Перевод контроллера с первого на второе третье и последующие положения производится с выдержкой на каждой позиции не менее трех секунд так как быстрое переключение может вызвать падение груза. При переводе рукояти контроллера SA1 в положение «Спуск» опять произойдет опускание груза с динамическим торможением. Для аварийного отключения подъема следует нажать кнопку SB3 что вызовет отключение всей пускорегулирующей аппаратуры и приведет к остановке механизма.
Управление электродвигателем М2 и тормозом вспомогательной лебедки осуществляется контроллером SA2 путем перевода его в положение «Подъем» или «Спуск». При этом в первом положении контроллера пусковой момент подъема - наименьший а в пятом положении - наибольший. При переводе контроллера в нулевое положение производится отключение электродвигателя и торможение лебедки.
Поворот рукояти контроллера механизма вращения вправо и влево соответствует направлению вращения крана. Минимальная скорость может быть получена в первом положении контроллера а максимальная в пятом. Для остановки механизма переводит рукоять контроллера в нулевое положение.
Поднимается и опускается стрела нажатием кнопок SB4 и SB5 соответственно которые включают реверсивный магнитный пускатель. Остановка механизма производится кнопкой SB6 отключающей этот пускатель. Реверсирование электродвигателя производится только после остановки кнопкой SB6.
На кране установлены конечные выключатели ограничения хода рабочих органов механизмов. Конечные выключатели SQ1 и SQ2 отключают пускатель КМ1 при достижении крюком крайнего верхнего положения. При его срабатывании необходимо рукоять контроллеров поставить в нулевое положение нажать кнопку SBI и произвести опускание груза.
По окончании работы нажатием кнопки SB3 в цепи управления кабель отключают сначала от внешней цепи а затем от зажимов силового щита.
4 Прочностные расчеты.docx
1 Расчет барабана механизма подъема груза
Так как Lб 3Dб то проверку на общую прочность и устойчивость не проводим.
Канат крепим на барабане прижимными планками. Схема крепления показана на рисунке 4.1.
Рисунок 4.1 – Схема крепления каната на барабане
По формуле (4.1) рассчитываем усилие затяжки: +
где z = 3 – число планок;
f = 015 – коэффициент трения между канатом и барабаном;
f1 – коэффициент трения между канатом и барабаном;
f1 = f sin = 015 sin40 = 0233
Угол обхвата рассчитываем по формуле (4.2):
где 1 = 3 - угол обхвата неприкасаемыми витками рад;
По формуле (4.2) получаем:
Подставляем полученные значения в формулу (4.1) получаем:
Задаемся диаметром болта М8 из стали 45 улучшенной с т = 360 МПа. Болт испытывает напряжение растяжения с кручением а также изгиб.
Обеспечение заданной прочности проверяем выражением (4.3):
где [] = т п = 360 4 = 90 – допустимое напряжение МПа;
п = 4 – коэффициент запаса при неконтролируемой затяжке;
Условие прочности выполняется.
Диаметр вала барабана из расчета по пониженным допускаемым напряжениям на кручение определяется по формуле (4.4):
По формуле (4.4) получаем:
Принимаем диаметр вала dв = 50 мм.
2 Подбор подшипников оси барабана
Ra = Rб = G 2 = 150 2 = 75 кНм
По статической грузоподъемности намечаем подшипник № 410 с параметрами: d = 50 мм; D = 130 мм; B = 31 мм; C = 1067 кН; C0 = 825 кН.
Так как осевая нагрузка отсутствует то эквивалентная радиальная динамическая нагрузка определяется по формуле (4.5):
Pэ = V Rа Kб Kт (4.5)
где V = 1 – вращается наружное колесо;
Kб = 1 3 – коэффициент учитывающий умеренные толчки;
Kт = 10 – температура эксплуатации меньше 100С;
Подставив значения в формулу (4.5) получаем:
Pэ = 1 75 13 1 = 975 кН
Долговечность подшипника в миллионах оборотов:L
Долговечность подшипника в часах работы:
где [Lh] = 200 тыс.час. Условие долговечности подшипника выполняется.
3 Расчет шпоночного соединения
Используем призматические шпонки с скругленными торцами (ГОСТ 23360-78). Материал – Сталь 45 нормализованная.
Напряжение смятия проверяем условием прочности (4.6):
где Т – крутящий момент на валу Нмм;
d – диаметр вала мм;
t1 – глубина паза в валу мм;
[см] = 80 МПа – допускаемое напряжение смятия для чугуна;
[см] = 150 МПа - допускаемое напряжение смятия для Стали 45;
Проверим по условию (4.6) шпонку которая устанавливается на вал электродвигателя механизма подъема груза:
d = 36 мм; Т = 195103 Нмм; По диаметру вала принимаем шпонку с размерами: h = 8 мм; b = 10 мм; t1 = 5 мм.
Проверим по условию (4.6) шпонку которая устанавливается на быстроходный вал редуктора механизма подъема груза:
d = 28 мм; Т = 195103 Нмм; По диаметру вала принимаем шпонку с размерами: h = 7 мм; b = 8 мм; t1 = 4 мм.
4 Расчет оси барабана на статическую прочность
Так как в конструкции барабана механизма подъема груза присутствует ось следовательно рассчитываем ее на статическую прочность.
Мх = Ra l = 75 0135 = 10125 кНм
Ось проверяется условием прочности (4.7):
где d = 50 мм – диаметр оси;
[] = (50 80) – допускаемое напряжение изгиба для Стали 45 Нмм;
5 Расчет сварного соединения стрелы крана
Наиболее нагружены швы соединяющие фасонку с нижним поясом. Схема сварного узла представлена на рисунке 4.2.
Рисунок 4.2 – Схема сварного узла
где SH = 1164 – усилие действующее на нижний пояс кН;
Длину второго шва определяем по формуле (4.8):
где с = 07 – коэффициент для ручной сварки;
Принимаем катет второго шва hШ2 = 4 мм;
[]CB = 07[] = 07 160 = 112 МПа
По формуле (4.8) получим:
Принимаем катет первого шва hШ1 = 5 мм;
Длину первого шва находим по формуле (4.9):
Список использованных источников.docx
Вайсон А.А. Подъемно-транспортные машины. М.: Машиностроение 1975. – 431 с.
Александров М.П. и др. Подъемно-транспортные машины. Атлас конструкций. М.: Машиностроение 1987. – 127 с.
Справочник по кранам. Под редакцией Гохберга. М.М.Т.1 2 М.: Машиностроение 1988.
Руденко Н.Ф. и др. Курсовое проектирование грузоподъемных машин. – М.: Машиностроение 1971. – 464 с.
А.с. 206164 СССР кл. В 66 d 122. Лебедка. – 1986.
А.с. 930015 СССР кл. В 66 d 102. Ручная лебедка. – 1983.
А.с. 206164 СССР кл. В 66 d 122. Лебедка. – 1983.
А.с. 206164 СССР кл. В 66 d 122. Грузовая лебедка. – 1987.
А.с. 206164 СССР кл. В 66 d 122. Башенный кран для строительно-монтажных работ. – 1972.
А.с. 206164 СССР кл. В 66 d 122. Кран-манипулятор. – 1984.
А.с. 206164 СССР кл. В 66 d 122. Башенный кран. – 1972.
А.с. 206164 СССР кл. В 66 d 122. Грузозахватная траверса для консольного подъема и транспортирования груза. – 1974.
А.с. 206164 СССР кл. В 66 d 122. Грузозахватное устройство. – 1973.
А.с. 206164 СССР кл. В 66 d 122. Выносная опора подъемного крана. – 1971.
А.с. 206164 СССР кл. В 66 d 122. противоугонный рельсовый захват для кранов. – 1974.
А.с. 206164 СССР кл. В 66 d 122. Ограничитель размотки каната лебедки. – 1972.
А.с. 206164 СССР кл. В 66 d 122. Прижимное устройство для каната лебедки. – 1972.
А.с. 206164 СССР кл. В 66 d 122. Грузоупорный тормоз. – 1972.
Курсовое проектирование грузоподъемных машин. Казак С.А. и др. – М.: Машиностроение 1989. – 319.
Правила устройства и безопасной эксплуатации грузоподъемных кранов. ПБ – 382-00. М.: Ростехнадзор 2000. – 296 с.
Горбацевич А.Ф. Шкред В.А. Курсовое проектирование по технологии машиностроения. – Мн.: Высшая школа 1983. – 256.
Дунаев П.Ф. Леликов О.П. Конструирование узлов и деталей машин. – М.: Высшая школа 1985. – 416.
Филиппов Б.И. Охрана труда при эксплуатации строительных машин. – М.: Высшая школа 1984. – 247.
Анурьев В.И. Справочник конструктора-машиностроителя. – М.: Машиностроение 1980. – Т.1. – 728 с.
Справочник технолога-машиностроителя Под ред. А.Н. Малова – М.: Машиностроение 1972. – Т.3.
Проектирование строительной и дорожной техники и технологии производства работ. Экономические расчеты. Сост. Е.А. Шевырина; ЯГТУ. –Ярославль 2005. – 32.
РЕФЕРАТ.docx
БАШЕННЫЙ КРАН БАШНЯ СТРЕЛА ЗАПАСОВКА ХОДОВАЯ ПЛАТФОРМА МОЩНОСТЬ МОНТАЖ ПРИВЕДЕННЫЕ ЗАТРАТЫ ТЕХНИКО-ЭКОНОМИЧЕСКИЕ ПОКАЗАТЕЛИ ГОДОВАЯ ПРОИЗВОДИТЕЛЬНОСТЬ.
Объектом исследования является башенный кран предназначенный для механизации строительства многоэтажных жилых и промышленных зданий.
Цель работы - разработка новой запасовки грузового каната увеличение стрелы а также компоновка и выбор: двигателя редуктора тормоза и соединительных муфт для механизмов подъема передвижения и поворота башенного крана.
В результате проведенных расчетов была разработана и сконструирована стрела башенного крана а также рассчитаны все основные механизмы крана.
Основные технико-экономические и конструктивные показания: производительность годовой эффект удлинение стрелы при простоте и относительной недороговизне конструкции.
5 ТЕХНОЛОГИЯ МАШИНОСТРОЕНИЯ.docx
1 Анализ технологичности детали
Данные о детали: наименование - ось материал - сталь 40 ГОСТ 1050-74 масса - 11 кг. Неуказанные предельные отклонения размеров: валов - h 14 остальных - по IT±142.
Анализируемая деталь представляет собой сочетание цилиндрических поверхностей диаметральные размеры которых убывают от одного торца до другого. В средней части оси имеются две шейки 90К6 под подшипники. На одном из торцов имеется резьбовой хвостовик М80х2. Деталь достаточно жесткая так как LD = 17588 = 2. Габаритные размеры: L = 175 мм dmax = 120 мм. В местах перехода ступеней детали предусмотрены унифицированные канавки с галтелями.
Заданная чертежом точность размеров поверхностей их отклонения от взаимного расположения и параметры качества поверхностных слоев могут быть достаточно экономично обеспечены традиционными методами механической обработки. Вместе с тем предусмотренная чертежом форма выточки (D = 88 мм В = 30 мм) не технологична так как требует использования прорезного резца большой ширины или многопроходной обработки.
В целом конструкция детали технологична обладает достаточной жесткостью обеспечивает свободный доступ инструмента к обрабатываемым поверхностям что позволяет при обработке использовать высокопроизводительные режимы резания и типовую оснастку.
2 Выбор типа производства
Задаемся годовым объемом выпускаемых деталей Nп = 400 штгод. Определим штучное время на выполнение основных операций технологического процесса.
Расчет штучного времени проводим по приближенным формулам.
Технологический процесс изготовления детали состоит из трех операций: фрезерно-отрезной токарно-винторезной кругло-шлифовальной.
Фрезерно-отрезная операция:
Т1 = 019 1252 10-3 = 3 мин
Токарно-винторезная операция:
Т2' = 0037 1252 2 10-3 = 12 мин
Т2" = 017 (122 35 + 92 110 + 80 30 + 24 10) 10-3 = 3 мин
Т2'" = [017 (120 25 + 90 110) + 019 80 30] 10-3 = 27 мин
T2 = 12 + 3 + 27 = 59 мин
Кругло-шлифовальная операция
Т3 = 025 90 40 2 10-3 = 18 мин
Определим штучно-калькуляционное время с учетом коэффициента перехода:
Тшк1 = 184 3 = 55 мин
Тшк2 = 214 59 = 126 мин
Тшк3 = 21 18 = 38 мин
Определим количество станков необходимых для выполнения каждой технологической операции:
Округлив mpi до ближайшего целого числа получим количество рабочих мест для выполнения каждой операции:
Р1 = 1; Р2 = 1; Р3 = 1
Определим фактические коэффициенты загрузки оборудования:
зф1 = 002; зф2 = 005; зф3 = 0015
Определим количество операций закрепленных за каждым рабочим местом:
Определим коэффициент закрепления операции:
Тип производства – мелкосерийный.
При выборе способа получения заготовки необходимо стремиться к максимальному приближению формы и размеров заготовки и детали что позволит снизить трудоемкость технологического процесса.
Анализ конструкции детали а также масштабы ее производства указывают на то что наиболее рациональным способом получения заготовки будет производство ее из сортового горячекатаного круглого проката нормальной точности. Круг В 125 ГОСТ 2591-71.
4 Расчет припусков на механическую обработку
Определим промежуточные и исходные размеры заготовки для шейки оси под подшипник 90 к6 Ra = 125 материал детали – сталь 40 ГОСТ 1050-74 заготовка – круглый прокат обработка в центрах с поводковым патроном.
Заданная точность изготовления и качество поверхности достигаются за четыре технологических перехода:
- шлифование предварительное;
- шлифование окончательное.
Так как обработка детали производится в центрах то погрешность установки Еi равна нулю. Суммарное значение пространственных погрешностей определяется по формуле:
где ко – общая кривизна заготовки мкм;
ц – погрешность зацентровки мкм;
где К – удельная кривизна профиля К = 5 мкммм;
ко = 5 165 = 825 мкм
где - допуск на диаметр базовой поверхности заготовки используемый при зацентровке = 24 мм.
Остаточные величины пространственных отклонений:
ч.т.=006 1175 = 705 мкм
чист.т.=004 1175 = 47 мкм
шл.и.=002 1175 = 235 мкм
Расчет минимальных значений припусков ведем по формуле:
Zmin = 2(Rzi-1 + Ti-1 + i-1) (5.4)
i-1 - пространственное отклонение в расположении обрабатываемых поверхности относительно технологических баз на предшествующем технологическом переходе мкм.
Наибольшие предельные размеры вычисляются как:
d(i-1)max + d(i-1)min + (i-1) (5.5)
Определим предельные значения припусков с учетом того что черновое точение выполняется по 13 квалитету точности чистовое точение - по 11 квалитету предварительное шлифование по 9 квалитету а чистовое шлифование – по 6 квалитету точности:
Zmax(i) = dmax(i-1) – dmax(i) (5.6)
Предельные значения припусков 2Zmin определяются по формуле:
Zmin(i) = dmin(i-1) – dmin(i) (5.7)
Результаты расчета сведены в таблицу 5.1.
5 Расчет режимов резания и норм времени
Расчет режимов резания и норм времени выполнен для чернового точения токарно-винторезной операции.
Исходные данные для расчета:
диаметр до обработки - D = 995 мм;
диаметр после обработки - d = 91 мм;
длина резания - 30 мм.
Определим глубину резания по формуле:
где D – диаметр заготовки до обработки мм;
d – диаметр заготовки после обработки мм.
t = (995 - 91)2 = 425 мм
В зависимости от глубины резания t и диаметра детали выбираем величину подачи:
Определяем скорость резания по формуле:
где Cv – коэффициент зависящий от материала детали и условий работы;
Kv – поправочный коэффициент;
Т – стойкость резца мин.
Cv = 340; х = 015; m = 020; y = 045; Т = 60 мин
где Kn - поправочный коэффициент учитывающий влияние состояния поверхности заготовки на скорость резания Kn = 09;
Ku - коэффициент учитывающий влияние материала инструмента на скорость резания Ku = 1.
Тогда K = 107 09 1 = 096
Определим расчетное число оборотов шпинделя станка:
По паспорту станка 16К20 принимаем число оборотов шпинделя n = 500 обмин.
Тогда фактическая скорость резания равна:
Тангенциальная составляющая силы резания определится п формуле:
Pz = 10Cp tx Sy vn Kp (5.12)
где Cp = 300; х = 10; y = 075; n = -015
Кр = Кнр Кр Кр Кр Кгр (5.13)
Кр = 089; Кр = 10; Кр = 10; Кгр = 104;
Кр = 095 0.89 10 10 104 = 088
Pz = 10 300 42510 06075 143 -015 088 = 3614 Н
Определим потребную мощность станка по формуле:
где - КПД станка = 085.
Мощность станка модели 16К20 равна 10 кВт.
Определим штучное время по формуле:
Тшт = Тосн + Твсп + Тобсл + Тп (5.15)
где Тосн – основное технологическое время мин;
Твсп – вспомогательное время мин;
Тобсл – время на техническое обслуживание мин;
Тп – время перерывов мин.
где L – расчетная длина обработки мм;
i – число рабочих ходов.
y – величина врезания и перебега инструмента мм.
L = 140 + 0 = 140 мм
Твсп = Твц + Твп (5.18)
где Твц – вспомогательное время на установку закрепление и снятие детали мин;
Твп – вспомогательное время связанное с переходом мин.
Твц = 13 мин; Твп = 07 мин.
Твсп = 13 + 07 = 2 мин
где tсм – время на смену инструмента tсм = 25 мин;
Т – расчетная стойкость резца Т = 60 мин.
Топ = 05 + 2 = 25 мин
Время на организацию обслуживания рабочего места берется 17% от операционного:
Время на отдых берется 6% от операционного:
Тшт = 05 + 2 + 054 + 042 + 015 = 361 мин
Таблица ТМС.docx
Технологические переходы
Элементы припуска мкм
Предельный размер мм
Предельное значение припусков мм
Предварительное шлифование
7 ЭКОНОМИЧЕСКИЙ РАЗДЕЛ.docx
Необходимость модернизации обусловлена успешным внедрением на отечественный рынок ПТМ машин зарубежных производителей. Машины российских производителей существенно отстают в развитии и не могут и не могут составить конкуренцию импортным.
В данном разделе производится расчет основных технико-экономических показателей эксплуатационной производительности экономического эффекта модернизированной машины и сделан вывод об эффективности модернизации.
1 Расчет себестоимости и цены модернизируемой техники
Модернизации подвергается рабочий орган (РО) башенного крана – стрела.
За базовый РО принимаем стрелу весом 5125 кг.
За счет удлинения стрелы масса РО увеличится на 20% (6300 кг).
Материалы используемые для конструкции РО: уголок 75х75х8 труба 121х7 труба 73х4 труба 32х3.
Расчет проектной себестоимости рабочего оборудования (Сро) модернизированной техники (НТ) производится по удельным показателям:
Расчет себестоимости нового оборудования может быть выполнен поузловым методом руб :
себестоимость новой техники руб
себестоимость отдельных узлов рабочего оборудования руб
номенклатура узлов деталей изготовляемых на заводе
себестоимость комплектующих узлов и деталей руб
номенклатура комплектующих узлов и деталей
коэффициент учитывающий затраты на сборку деталей и узлов
Себестоимость отдельных узлов и деталей руб :
где цена 1 т материала руб;
масса узла детали т;
часовая тарифная ставка; Тс = 150 руб.;
трудоемкость 1 т конструкции ч; Твд = 170 ч;
коэффициент премирования рабочих
коэффициент учитывающих дополнительную заработную плату
коэффициент учитывающий отчисления на нужды социального страхования
коэффициент учитывающий величину накладных расходов
Суз.нт = 37000 63 + (((150 170 63) 1 12) 148)+((150 170 63) 1) 25 = 9200394 руб
Суз.бт = 37000 5125 + (((150 170 5125) 1 12) 148)+((150 170 5125) 1) 25 = 7484448 руб
Сро.нт = 9200394 14 = 12880552 руб
Сро.бт = 7484448 14 = 10478227 руб
Цена рабочего органа:
где СП полная себестоимость узла;
R рентабельность изделия.
СП = СРО.НТ + РК (7.3)
где РК внепроизводственные расходы.
Принимаем РК = 005СРО.НТ ; R = 17%.
СП.НТ = 12880552 + 005 · 12880552 = 1352458 руб
СП.БТ = 10478227 + 005 · 10478227 = 1100214 руб
Так как расчет является укрупненным то стоимость базового шасси и крановых механизмов возьмем равной стоимости БТ тогда цена всей машины составит:
ЦНТ = ЦБТ + ЦБТ.без РО (7.4)
ЦНТ =1582376 + 5000000 = 6582376 руб
ЦБТ =1287250 + 5000000 = 6287250 руб
Первоначальная стоимость новой и базовой техники в сфере их эксплуатации:
СПЕР(БТ.НТ)= Ц(БТ;НТ) · КД (7.5)
где КД коэффициент доставки и монтажа техники.
СПЕР(БТ)= 6287250 · 12 = 7544700 руб
СПЕР(НТ)= 6582376 · 12 = 7898851 руб
2 Расчет годовой эксплуатационной производительности техники
Годовая эксплуатационная производительность базовой техники и новой техники определяется по формуле:
ПТГ = ПТч · ТГ (7.6)
где ПТч среднечасовая эксплуатационная производительность тч;
ТГ годовой режим работы техники ч;
Среднечасовая эксплуатационная производительность:
где Q грузоподъемность т;
K коэффициент продолжительности работы в час;
Годовой режим работы:
ТГ = [365 (52 · 2 + 15)] ·КРС · КС (7.8)
где 365 - количество календарных дней в рабочем периоде;
- количество выходных дней в рабочем периоде;
– количество праздничных дней за рабочий период;
КРС нормативная производительность техники часов в смену
КС коэффициент сменности работ техники (количество смен).
Принимаем КРС = 8 часов; КС = 2.
ТГ = [365 (52 · 2 + 15)]8 · 2 = 3936 ч.
Так как на величину ТГ влияют конкретные условия производства работ – территориальные метеорологические и другие то введем поправочный коэффициент равный 06-08.
ТГ =07 ·2008 = 2755 ч.
Исходя из выше подсчитанного:
ПТГ БТ = 38 · 2755 = 104690 тгод
ПТГ НТ = 438 · 2755 = 121220 тгод
3 Расчет годовых текущих затрат на эксплуатацию техники
Годовые затраты на содержание техники составляют:
ЦГ = А + Р + Б + З + Э + С + П (7.9)
где А амортизационные отчисления на полное восстановление руб.год;
Р затраты на ремонт и ТО техники руб.год;
З заработная плата персонала руб.год;
Э затраты на энергоносители руб.год;
С Затраты на смазочные материалы руб.год;
Г затраты на гидравлическую жидкость руб.год;
П затраты на перебазировку техники руб.год.
Расчет амортизационных отчислений:
где НА норма годовых амортизационных отчислений на реновацию техники.
Принимаем НА = 125%.
Расчет затрат на выполнение ремонтов и ТО:
где НР норма годовых затрат на текущий и капитальный ремонт.
Принимаем НР = 18 %.
Расчет затрат на сменную оснастку:
где МБ.Ч. количество быстроизнашивающихся частей данного вида одновременно заменяемых на машине шт.;
ТБ.Ч. срок службы быстро изнашивающихся частей ч.
По техническим данным на кран быстроизнашивающиеся части: гибкий кабель – 6 шт.; канат стальной – 2 шт.
Гибкий кабель: МБ.Ч. = 6 шт.; ТБ.Ч. = 3000 ч.; = 2400 руб.
Канат стальной: МБ.Ч. = 2шт.; ТБ.Ч. = 2000ч.; = 4200 руб.
Б = 13225 + 11572 = 24797 руб.год
Расчет заработной платы персонала:
где З1 З2 – заработная плата основного и вспомогательного персонала;
З = КНР · КР · КП · СТ ТГ (7.14)
где КНР коэффициент накладных расходов КНР =13;
КР среднепоясной коэффициент тарифной ставки КР =1105;
КП коэффициент премирования КП = 14;
СТ годовая тарифная ставка;
ТГ годовой фонд времени ТГ = 27552 ч.
Для основного и вспомогательного персонала соответственно принимаем:
СТ1 = 177 руб.ч.; СТ2 = 142 руб.час.
З1 = 13 · 1105 · 14 · 177 27552 = 980754 руб.год
З2 = 13 · 1105 · 14 · 142 27552 = 786820 руб.год
З = 980754 + 786820 = 1767574 руб.год
Расчет затрат на энергоносители:
ЭЭ =11· N · КМ ·КВ· СПЕР.Э ·ТГ (7.15)
где N номинальная мощность электродвигателя кВт;
КМ коэффициент использования двигателя по мощности КМ = 05-08;
КВ коэффициент использования двигателя по времени КВ = 06-09.
СПЕР.Э=Ц. Э ·К Д (7.16)
где ЦЭ – цена электроэнергии руб.кВт-ч; ЦЭ = 38 руб.кВт-ч;
КД – коэффициент доставки КД = 11-13.
Принимаем: КМ = 07; КВ = 08; КД = 12.
ЭЭ = ( 11 · 75 · 07 08 · 38 · 12 + 11 · 106 · 06 06 · 38 · 12 + 11 · 63 · 05 07 · 38 · 12 + 11 · 75 · 06 07 ·38 ·12)·27552 = 258524 руб.год.
Расчет затрат на перебазировку.
Так как перебазировка башенного крана происходит на прицепе с его демонтажем и монтажом и погрузкой (разгрузкой) на прицеп то искомые затраты рассчитываются по формуле:
ППр-д =[(ПЗТ + ПЗП + ПЗМС)В1 + (ЗПЧ + ЗПДЧ) В2] + (ПЗКР ВКР)
где ПЗТ – прямые затраты на эксплуатацию тягача руб.маш.час;
Принимаем ПЗТ = 1680 руб.маш.час;
ПЗП – прямые затраты на эксплуатацию прицепа руб.маш.час;
Принимаем ПЗП = 450 руб.маш.час;
ПЗМС – прямые затраты на эксплуатацию машины сопровождения руб.маш.час; Принимаем ПЗМС = 600 руб.маш.час;
В1 – время в течение которого тягач и машина сопровождения заняты в перебазировке маш.час; Принимаем В1 = 3 час.;
ЗПЧ – часовая заработная плата машиниста перебазируемой техники руб.маш.час; Принимаем ЗПЧ = 70 руб.маш.час;
ЗПДЧ – часовая заработная плата звена рабочих дополнительно привлеченных к перебазировке техники руб.маш.час;
В2 – время участия машиниста в перебазировке техники маш.час;
Принимаем В2 = 5 час.;
ТП – средняя продолжительность нахождения техники на одном объекте час.; Принимаем ТП = 300 час.;
ПЗКР – прямые затраты на эксплуатацию крана руб.маш.час;
Принимаем ПЗКР = 3200 руб.маш.час;
ВКР – продолжительность использования крана в процессе перебазировки маш.час; Принимаем ВКР = 5 час.;
Подставив значения в формулу получаем:
ППр-д =[(1680 + 450 + 600) 3 + (70 + 50) 5] + (3200 5) = 116149 руб.год
Годовые затраты на смазку:
где Тмч – число моточасов работы машины в году;
Тг – годовой фонд рабочего времени час;
N – мощность силовой установки кВт;
k – удельный коэффициент расхода смазочных материалов 1кВт (03..06);
Ссм – цена смазочного материала;
C = 58 045 60 = 1566 руб.год
Полные текущие затраты на эксплуатацию техники аналоговой и новой машины соответственно равны:
U’БТ = 942278 + 1358046 + 24797 + 1767574 + 258524 + 1566 = 4352785 руб.год
U’НТ = 986362 + 1421793 + 24797 + 1767574 + 258524 + 1566 = 4460617 руб.год
Величина затрат руб.год
Амортизационные отчисления
Затраты на выполнение видов ремонта
Затраты на замену быстроизнашивающихся частей
Заработная плата персонала
Затраты на энергоносители
Затраты на смазочные материалы
Затраты на перебазровку машин
Таблица . Годовые текущие затраты на эксплуатацию КБ-405.1А
В результате расчета годовых текущих затрат на эксплуатацию базовой и новой техники достигается незначительная переплата в размере 107832 рублей в год.
4 Определение удельных показателей
Расчет удельных капитальных вложений:
КУД.(БТ;НТ) = (7.18)
Удельная себестоимость:
СУД.(БТ;НТ) = (7.19)
СУД.(БТ) = = 41 руб.т
СУД.(НТ) = = 37 руб.т
Величина экономического эффекта:
ЭПТ = (ПТ ГНТ ПТ ГБТ)СУД.НТ (7.21)
ЭПТ = (121220 104690) · 37 = 611610 руб.год
Расчет срока окупаемости год:
Таблица . Технико-экономические показатели в сфере эксплуатации техники
Технико-экономические показатели
Капитальные вложения руб
Эксплуатационная производительность:
Годовые текущие затраты руб
Себестоимость единицы работы руб.ед
Годовой экономический эффект руб
Срок окупаемости год
После модернизации крана башенного КБ-405.1А капитальные вложения на покупку новой техники увеличивабтся с 7544700 руб. до 7898851 руб. Часовая эксплуатационная производительность возрастает с 38 тч до 438 тч следовательно возрастает и годовая эксплуатационная производительность с 104690 тгод до 121220 тгод. Годовые текущие затраты на содержание экскаватора увеличиваются с 4352785 руб. до 4460617 руб; удельная себестоимость единицы продукции сокращается с 41 рубед до 37 рубед. В результате этой модернизации мы получаем экономический эффект в размере 611610 руб. и срок окупаемости составит 3 года.
Заключение.docx
Спроектированный башенный кран дает ряд преимуществ перед существующими конструкциями:
- увеличенная рабочая зона крана;
- надежность металлоконструкции стрелы крана;
- простота эксплуатации.
В процессе проектирования был произведен расчет основных узлов и механизмов крана: подъема груза передвижения крана поворота крана устойчивости крана. Также в дипломный проект входят прочностные расчеты элементов крана.
Результаты проведенного экономического расчета показывают что себестоимость единицы работы удельные приведенные затраты удельные капитальные вложения уменьшились. Эксплуатационная производительность увеличилась.
На основании выше изложенного целесообразно рекомендовать спроектированную машину предприятиям имеющим башенные краны и ремонтно-механическую мастерскую.
3 РАСЧЕТ КРАНОВЫХ МЕХАНИЗМОВ.docx
1 Расчет механизма подъема груза
Принципиальная схема механизма подъема представлена на рисунке 3.1.
Рисунок 3.1 – Схема механизма подъема груза
Натяжение каната на барабане при подъеме груза определяем по формуле (3.1):
где mгр – масса груза mгр = 15000 кг;
бл – КПД блока принимаем бл = 098;
Zk – рядность полиспаста Zk = 1;
an – кратность полиспаста An = 2;
t – число отклоняющих блоков t = 2;
Тогда по формуле (3.1) получим:
КПД полиспаста определяется по формуле (3.2):
После подстановки получаем:
По правилам Ростехнадзора разрывное усилие рассчитывается по формуле (3.3):
где Zp = 71 – коэффициент запаса прочности для режима работы 5М;
Тогда по формуле (3.3) получаем:
Fо = 77368 71 = 549313 Н = 5493 кН
Выбираем канат: 29 – Г – В – К – Н – 1960 (200) ГОСТ 7668-80
диаметр каната dk = 29 мм = 0029 м;
предел прочности в = 1960;
Диаметр барабана рассчитываем по формуле (3.4):
где n1 = 224 – коэффициент выбора для режима 5М;
тогда по формуле (3.4) получаем:
Dб = 224 0029 = 065 м
где Dбл – диаметр блока м;
Принимаем шаг нарезки на барабане р = 16;
Длину нарезаемого участка определяем по формуле (3.5):
lн = р(zp+zн+zкр) (3.5)
где zн = 15 – число запасных витков;
zкр = 32 – число витков крепления;
По формуле (3.5) имеем:
lн = 16 (71 + 15 + 32) = 1888 мм
Общая длина барабана с учетом крепления на станке для точения канавок состоит lб = 240 мм.
Так как lб 3Dб то проверку на прочность и устойчивость не проводим.
Минимальная толщина стенки барабана:
= 001Dб + 3 мм = 001 650 + 3 = 95 мм
С учетом износа принимаем = 15 мм.
Напряжение сжатия на внешней поверхности барабана находим по формуле (3.6):
где [] = 160 МПа – допускаемое напряжение для Сталь3;
Статическую мощность электродвигателя определяем по формуле (3.7):
где гр = 051 мс – скорость подъема груза;
м = 085 – КПД механизма;
Подставив в формулу (3.7) получим:
По каталогу выбираем электродвигатель серии MTF 311-6 со следующими параметрами:
Номинальная мощность: Pном = 11 кВт – для ПВ = 40%;
Частота вращения вала электродвигателя: п = 945 обмин;
Максимальный пусковой момент: Ммах = 320 Н м;
Момент инерции ротора: Ip = 0225 кгм2;
Требуемое передаточное отношение редуктора определяем по формуле (3.8):
где nбар – частота вращения барабана механизма подъема определяем по формуле (3.9):
Подставляя значения получаем:
Подставляя (3.9) в формулу (3.8) получаем:
Момент на тихоходном валу рассчитываем по формуле (3.10):
Подставляя значения в формулу (3.10) получаем:
По каталогу выбираем редуктор Ц2У-250 с передаточным числом 355 мощностью на быстроходном валу 104 кВт номинальным моментом на тихоходном валу Мтихн = 4 кНм радиальной нагрузкой на тихоходном валу = 16 кН и КПД = 097;
Тормоз выбираем по расчетному тормозному моменту:
где К = 15 – коэффициент запаса торможения;
Мст – статический крутящий момент при торможении Нм;
где общ = ред п бар м = 096 095 098 098 = 087
Подставляя значении в формулу (3.12) получаем:
Подставляя (3.12) в формулу (3.11) получаем:
Мт = 15 660 = 990 Нм
По каталогу выбираем тормоз ТКГ-400 с Мт = 1500 Нм и регулируем его на 1000 Нм.
Выбираем шкив-муфту МУВП-1 с тормозным шкивом диаметром – 200 мм наибольшим передаваемым моментом – 500 Нм и моментом инерции Iм = 0125 кгм2.
2 Проверочный расчет механизма подъема груза
Проверку двигателя на нагрев проведем по эквивалентному крутящему моменту из условия:
где Мэ – эквивалентный крутящий момент;
Мдв.н. – номинальный крутящий момент на валу электродвигателя;
где Мст.под Мст.оп – статический момент при подъеме и опускании j-го груза;
tp.j – время разгона при работе с j-м грузом;
ty.под. ty.оп. – время установившегося движения при подъеме и опускании;
Принимаем что за рабочий цикл производится 10 подъемов и опусканий груза. На рисунке 3.2 представлен график загрузки механизма подъема для режима работы 5М.
Рисунок 3.2 – График нагрузки механизма подъема для режима работы 5М
Q1 = Qн = 1472 кН – 2 раза;
Q2 = 075Qн = 1104 кН – 4 раза;
Q3 = 0195Qн = 287 кН – 1 раз;
Q4 = 005Qн = 74 кН – 3 раза;
По формулам (3.15) и (3.16) получаем:
Время разгона при подъеме и опускании груза находим по формулам (3.17) и (3.18) соответственно:
где дв.п = nдв 30 = 314 94530 = 9891 с -1;
где с – синхронная частота с-1;
где р = 3 – число пар полюсов;
f = 50 – частота Гц;
с = 2 314 50 3 = 1047 с-1
дв.о = 2 1047 – 9891 = 1105 с-1
Среднепусковой момент двигателя рассчитываем по формуле (3.19):
Мп.ср = Мдв.н (3.19)
где = 2 – кратность среднепускового момента;
Мдв.н = Nдв дв = 58000 1047 = 554 Н м
Подставив в формулу (3.19) получим:
Мп.ср = 2 554 = 1108 Н м
Момент инерции механизма рассчитываем по формуле (3.20):
Iмех = Iвр + Iпост (3.20)
где Iвр – момент инерции вращающихся частей кгм2;
Iпост – момент инерции поступательно движущихся частей кгм2;
Iвр = 115(Iдв + Iмуф) = 115(0225 + 0125) = 04 кгм2
где Iмуф – момент инерции муфты кгм2;
Момент инерции поступательно движущихся частей находим по формуле (3.21):
Подставляя полученные значения в формулу (3.20) получаем:
Iмех1 = 04 + 0625 = 1025 кгм2
Iмех2 = 04 + 0468 = 0868 кгм2
Iмех3 = 04 + 0122 = 0522 кгм2
Iмех4 = 04 + 0031 = 0431 кгм2
Подставляя полученные значения в формулы (3.17) и (3.18) получаем:
tp.j = 2(113+006)+4(025+006)+(006+005)+3(004+004) = 4 с
Время установившегося движения находим по формулам (3.22) и (3.23):
где Нср = (05 08)Н – средняя высота подъема м;
под – скорость подъема груза мс;
оп – скорость опускания груза мс;
под = дв.п rб Uмех = 9891 0325 54 = 06 мс
оп = дв.о rб Uмех = 1105 0325 54 = 067 мс
Подставив значения в формулы (3.22) и (3.23) получим:
tу.п. = 10 533 = 533 с
tу.о. = 10 478 = 478 с
= 065 – коэффициент учитывающий ухудшение охлаждения двигателя в процессе пуска.
Подставив значения полученные по формулам (3.15-3.19) и (3.22-3.23) в выражение (3.14) получим:
Мэ Мдв.н так как заданное условие выполняется следовательно двигатель перегреваться не будет.
3 Расчет механизма передвижения крана
Исходя из анализа существующих конструкций принимаем массу крана мкр равную 1164 т.
Рисунок 3.3 – Схема механизма передвижения крана
По таблице 2.11 [19] принимаем ходовое колесо диаметром 500 мм и рельс Р43 (ГОСТ 7173-74).
Сопротивление передвижению крана рассчитываем по формуле (3.24):
W = Wmp + Wу + Wв + Wин + W2 (3.24)
где Wmp – сопротивление от силы трения кН;
Wу – сопротивление от уклона пути кН;
Wв – сопротивление от ветровой нагрузки кН;
Wин – сопротивление от силы инерции кН;
Wmp – сопротивление от подвеса кН.
Сопротивление от силы трения находим по формуле (3.25):
где G = g (мкр+мгр) = 981 (116400+15000) = 1289 кН;
= 04 – коэффициент трения качения для колеса мм;
f = 0015 – приведенный коэффициент трения в подшипниках;
dц = 100 – диаметр цапфы мм;
Dк = 500 диаметр ходового колеса мм;
кдоп = 20 – коэффициент дополнительных сопротивлений;
Подставив значения в формулу (3.25) получим:
Wmp = 1289 2 04 + 0015 100 2 500 = 115 кН
Сопротивление от уклона пути находим по формуле (3.26):
где = 0002 – уклон пути;
По формуле (3.26) получаем:
Wу = 0002 1289 = 269 кН
Сопротивление от ветровой нагрузки находим по формуле (3.27):
Wв = q k c n F (3.27)
где q = 450 – динамическое давление МПа;
k = 12 – коэффициент высоты;
c = 12 – аэродинамический коэффициент;
n = 10 – коэффициент перегрузки;
F = 80 – площадь груза и конструкции м2;
Wв = 450 12 12 1 80 = 512 кН
Сопротивление от силы инерции рассчитываем по формуле (3.28):
Wин = тпост а (3.28)
Подставляя значения в формулу (3.28) получаем:
Wин = 125 127400 01 = 159 кН
Сопротивление от подвеса находим по формуле (3.29)
W2 = (тгр + тпод) а (3.29)
где тпод = 100 – масса подвеса кг;
W2 = (15000 + 100) 01 = 15 кН
Подставляя полученные значения по формулам (3.25-3.29) в формулу (3.24) получаем:
W = 115 + 269 + 512 + 159 + 15 = 822 кН
Мощности двигателя определяем по формуле (3.30):
где кр = 045 – скорость передвижения крана мс;
пр = 06 – КПД привода;
п = 16 – кратность пускового момента;
Nдв = 822 045 06 16 = 115 кВт
Принимаем два электродвигателя серии МТ 211-6 с параметрами при ПВ = 40%:
Мощность на валу двигателя: Nдв = 63 кВт;
Частота вращения вала электродвигателя: п = 975 обмин;
Момент инерции ротора: Ip = 00046 кгм2;
Число оборотов колеса пк = 60 кр Dк = 60 045 314 05 = 175 обмин;
Передаточное число: U = пдв пк = 975 175 = 357
По формуле (3.31) находим момент на тихоходном валу редуктора:
Мтих = 9550 24 357 075 975 = 629 кНм
По каталогу принимаем редуктор РЧУ-120; Up = 29;
Расчетный тормозной момент при движении порожнего крана под уклон при отсутствии реборд определяется по формуле (3.32):
Мтр = Му0 + Мин0 + Мв0 + Мтр0 (3.32)
где М0 – моменты создаваемые уклоном инерцией ветром трением приведенным к валу тормоза Нм;
где к-т = 07 – КПД механизма на участке «колесо-тормоз»;
Wу0 = Gкр = 0002 116400 981 = 228 кН
Wин0 = ткр а = 125 116400 01 = 145 кН
Wв0 = q k c n F1 = 450 12 12 1 70 = 453 кН
Подставляем полученные значения в формулу (3.33) получаем:
Выбираем двухколодочный тормоз ТТ-200 с номинальным тормозным моментом Мном = 200 Нм и моментом инерции Iин = 001 кгм2;
Максимально допустимое ускорение при котором обеспечивается запас сцепления рассчитывается по формуле (3.34):
где т = 2 – число приводных колес;
п = 4 – общее число колес;
ксц = 12 – запас сцепления;
= 015 – коэффициент сцепления;
Время пуска при максимально допустимых ускорениях:
tn = v атах = 045 045 = 1 с
Статический момент сопротивления передвижению определяется по формуле (3.35):
где Wв0 – сопротивление от ветровой нагрузки Нм;
Момент инерции подвижных масс приведенный к валу двигателя рассчитывается по формуле (3.36):
Iпр = (Iр + Iт.ш.) + Мс0 (3.36)
где Iт.ш. = 001 – момент инерции тормозного шкива кгм2;
Iпр = 115 (00046+001)+000055 = 00017 кгм2
Номинальный момент двигателя:
Мн = Nдв дв = 24000 30 314 975 = 2352 Нм
Средний пусковой момент по каталогу:
Мпуск = 20 Мн = 20 2352 = 4704 Нм
Фактическое время пуска:
Фактический запас сцепления проверяется условием (3.37):
где [ксц] = 12 – допускаемый коэффициент сцепления;
После подстановки значений в формулу (3.37) получаем:
Условие сцепления выполняется.
4 Расчет механизма поворота крана
Механизм поворота служит для приведения во вращение металлоконструкцию крана и груза. Принципиальное отличие работы механизма поворота от рассмотренных выше механизмов подъема груза и перемещения крана заключается в том что при повороте отсутствуют поступательно движущиеся массы – имеются только вращающиеся массы.
Схема привода механизма поворота показана на рисунке 3.4.
Исходные данные для расчета привода механизма поворота:
Угловая скорость поворота = 0075 с -1;
Высота подъема груза Н = 634 м;
Расстояние между опорами h = 175 м;
Расстояние b = (025 03)L = 03 35 = 105 м;
Расстояние а = 0875 м – конструктивно принятый параметр;
Диаметры цапф под подшипники:
d1 = d2 = 007h = 007 175 = 0093 м 90 мм
d3 = (06 07) d1 = 60 мм
Рисунок 3.4 – Схема привода механизма поворота крана
Принимаем что противовес выполнен из бетона находим требуемый объем и размеры по формуле (3.38):
где тпр = 50000 – масса противовеса кг;
б = 3200 – плотность бетона кгм3;
Реакции в подшипниках определяем по формулам (3.39) и (3.40):
где тпов = 21600 – масса поворотной части кг;
Находим значение реакции R’H:
R’H = RH 2 cos45 = 18378 2 cos45 = 10811 Н
По статической грузоподъемности подбираем подшипники:
Для верхней опоры – радиальный сферический № 1218 по ГОСТ 5721-57 с размерами d = 90 мм; D = 160 мм; B = 30 мм; статистическая грузоподъемность = 52400 кН;
Для Верхней опоры – шариковый упорный однорядный подшипник по ГОСТ 6874-54 с размерами d = 50 мм; D = 90 мм; Н = 18 мм; статистическая грузоподъемность 32 кН;
Для нижней опоры – 8 радиальных шариковых № 208 по ГОСТ 8338-75 с размерами d = 40 мм; D = 80 мм; H = 20 мм; статическая грузоподъемность 15 кн;
Момент сопротивления повороту рассчитываем по формуле (3.41):
Тс = Ттр + Тв + Тин (3.41)
где Ттр – момент сопротивления сил трения Нм;
Тв – момент ветровой нагрузки Нм; Тв = 0;
Ти – момент сил инерции Нм;
Момент сопротивления от силы трения находим по формуле (3.42):
Ттр = Ттрв + Ттрн (3.42)
Момент сил трения в нижней опоре:
Момент сил трения в верхней опоре:
Подставляя полученные значения в формулу (3.42) получим:
Ттр = 328 + 585 = 913 Нм
Момент сил инерции определяется по формуле (3.43):
где - угловое ускорение с -2;
= [a] L = 01 30 = 00033 с -2
где = 12 14 – коэффициент учета инерции вращающихся частей;
к = 13 14 – коэффициент приведения геометрических радиусов к радиусу инерции;
J = 12 13 (15000 252 + 21600 1052 + 50000 1752) = 10835136 кгм2
По формуле (3.43) получаем:
Тин = 10835136 00033 = 4334 Нм
Подставляем значения в формулу (3.41):
Тс = 913 + 4334 = 5247 Нм
Мощность электродвигателя рассчитываем по формуле (3.44):
где пр = 07 08 – КПД привода;
ср = 16 – средняя кратность пускового момента для двигателей серии 4А;
Принимаем электродвигатель 4АА71А4У3 с частотой вращения n = 1370 обмин и мощностью Р = 025 кВт.
Передаточное число привода:
Принимаем червячный горизонтальный редуктор РЧУ-40 с передаточным отношением Up = 40 b передаваемой мощностью Р = 04 кВт.
Передаточное число открытой зубчатой передачи:
Uз = U Uр = 686 40 = 1715
Принимаем параметры зубчатой передачи:
Модуль зацепления m = 25 мм;
Число зубьев шестерни z1 = 20;
Число зубьев колеса z2 = z1 Uз = 20 1715 344;
Делительные диаметры колес:
d1 = m z1 = 25 20 = 50 мм
d2 = m z2 = 25 344 = 860 мм
Момент на быстроходном валу:
Расчетный тормозной момент:
Мт = Мдв кт = 172 15 = 258 Нм
Принимаем тормоз ТКТ-100 и регулируем его на момент 3 Нм.
Рекомендуемые чертежи
Свободное скачивание на сегодня
Другие проекты
- 24.04.2014