Автомобильный кран г/п 25 т.



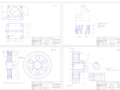

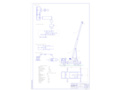
- Добавлен: 25.10.2022
- Размер: 2 MB
- Закачек: 0
Описание
Состав проекта
![]() |
![]() |
![]() |
![]() ![]() ![]() ![]() |
![]() ![]() ![]() ![]() |
![]() ![]() ![]() ![]() |
![]() ![]() |
![]() |
![]() ![]() |
![]() ![]() |
![]() ![]() |
![]() ![]() |
![]() ![]() |
![]() |
![]() ![]() ![]() |
![]() ![]() ![]() |
![]() ![]() ![]() |
Дополнительная информация
Чертеж Лист 2.dwg

Чертеж Лист1.dwg

Гидродвигатель 310.1.12
Диаметр гидроцилиндра 220 мм
Давление в гидросистеме 25 МПа
Гидродвигатель 310.2.28
Кинематическа схема лебедки
Кинематическая схема механизма поворота
Кинематическая схема механизма телескопирования стрелы
Кинематическая схема запасовки каната
Техническая характеристика.
Грузоподъемность 25т
Высота подъема груза 20м
Скорость подъема груза 0.5 мс
Частота вращения крана 1.2 обмин
Режим работы средний
-Г-1-ОЖ-Н-1666(170) ГОСТ 2688
Механизм подъема груза
Разрывное усилие 318кН
Гидродвигатель 312.25
Чертеж Лист3.dwg

Направление навивки пружины - правое.
Число рабочих витков n=13;
Общее число витков n
Радиусы скруглений 1
равномерно по окружности
Неуказанные литейные радиусы r=3 5 мм
Спецификация.doc
КС-5571-01.00.000.СБ
Автомобиль КамАЗ 65115
КС-5571-02.00.000.СБ
КС-5571-03.00.000.СБ
Опорно-поворотный круг
КС-5571-04.00.000.СБ
Поворотная платформа
КС-5571-05.00.000.СБ
КС-5571-06.00.000.СБ
КС-5571-07.00.000.СБ
КС-5571-08.00.000.СБ
Корневая секция стрелы
КС-5571-09.00.000.СБ
Выдвижная секция стрелы
КС-5571-10.00.000.СБ
Корпус гидроцилиндра
КС-5571-11.00.000.СБ
КС-5571-12.00.000.СБ
КС-5571-13.00.000.СБ
Курсяк.docx
ФЕДЕРАЛЬНОЕ ГОСУДАРСТВЕННОЕ БЮДЖЕТНОЕ ОБРАЗОВАТЕЛЬНОЕ УЧЕРЕЖДЕНИЕ ВЫСШЕГО ПРОФЕССИОНАЛЬНОГО ОБРАЗОВАНИЯ
«ВОРОНЕЖСКИЙ ГОСУДАРСТВЕННЫЙ
АРХИТЕКТУРНО-СТРОИТЕЛЬНЫЙ УНИВЕРСИТЕТ»
Кафедра строительной техники и инженерной механики
имени проф.Н.А.Ульянова
По дисциплине: «Подъемно-транспортные машины и оборудование»
Техническое задание3
Раздел 1. Расчет грузоподъемной лебедки
1. Определение группы классификации (режима) механизма подъема3
2.Выбор грузового крюка3
3.Выбор грузоподъемного каната3
4.Расчет крюковой обоймы4
5.Определение параметров барабана 7
6.Определение параметров двигателя10
8.Тормоз механизма подъема 11
Раздел 2.Общий расчет автомобильного крана
1.Выбор базового автомобиля 15
2.Определение масс узлов автокрана15
3.Определение геометрических параметров крановой установки16
Раздел 3.Проверка устойчивости крана от опрокидывания 24
1.Проверка устойчивости при статических испытаниях 24
2.Проверка устойчивости при динамических испытаниях 24
3. Проверка устойчивости при номинальных нагрузках 27
4.Построение грузовысотной характеристики автокрана 28
Раздел 4.Расчет механизма поворота 31
1.Исходные данные для расчета механизма поворота 31
2. Определение моментов сил сопротивления повороту 31
3. Кинематический расчет редуктора механизма поворота 34
4. Проверка прочности вала и ведущей шестерни механизма поворота..35
Раздел 5.Расчет механизма наклона стрелы 38
Список использованной литературы ..41
Пример расчета автомобильного крана
Исходные данные задания по варианту10
Грузоподъемность Q– 25 т.
Грузовой момент макс.Mгр – 80 тм.
Высота подъема крюка макс.H – 20м.
Скорость подъема груза макс.Vгр– 05 мс.
Скорость поворота макс. nкр-12 обмин.
Время подъема стрелы из транспортного положения в положение минимального вылета t–55с.
Грузооборот П - 160 тчас.
Номер нагрузочного графика 10.
Занятость крана – односменная (время хронометража).
Нормативный срок службы кранаZн =16 лет.
Расчет грузоподъемной лебедки
1. Определение группы классификации(режима) механизма подъема.Режим работы механизма подъема определяем по табл. 1 прил. 4 Правил устройства и безопасной эксплуатации грузоподъемных кранов ПБ10-382-00 [14]. Для этого предварительно определяем коэффициент распределения нагрузки Кр согласно заданному нагрузочному графику по формуле
Число циклов нагружений при односменной работе и числе рабочих дней в году 260 за нормативный срок службы определяем по формуле
=[1(16025)]8124716 =505856циклов.
Полученный коэффициент распределения нагрузок относится к тяжелому режиму нагруженияQ4. Число циклов нагружений соответствует классу использования U6. Группа классификации механизма подъема груза соответствует режиму М8 который определяет общий режим крана какА8.
2. Выбор грузового крюка. Крюк выбираем по ГОСТ 6627 (табл.П.6 [11]). Режиму работы А8 при грузоподъемности 25 т соответствует крюк № 21 с резьбойна хвостовике Тр100×12. Крюк должен быть установлен в траверсе на упорном шариковом подшипнике№ 8420 легкой серии с допустимой статической нагрузкой 330 кН.Внутренний диаметр подшипника 100 мм наружный – 270мм высота подшипника 35 мм.
3. Выбор грузоподъемного каната. Исходя из существующей практики при грузоподъемности 25 т применяют 4-х 6-и кратные полиспасты. Принимаем полиспаст с кратностью in = 6. Схема проводки (запасовки) каната в полиспасте показана на рис. 1. КПД такого полиспаста с блоками на подшипниках качения принимаем п= 095 (табл. П.2.1 [11]).
Разрывное усилие каната должно быть не менее
Fр≥ Qgkзап iпп= 259817.16095 = 305.48 кН
где kзап= 7.1 – минимальный коэффициент запаса прочности каната табл. П.1.3 [11].
По табл. П.3.1[11] выбираем:
Канат 24-Г-1-ОЖ-Н-1666(170)-ГОСТ 2688-80.
Диаметр канатаdк =24 мм; разрывное усилие Fр = 318кН.
Фактически действующее рабочее усилие в ветви каната идущей на барабан будет
Fф≥ Qg iпп= 25981 6095 = 43 кН.
4. Расчет крюковой обоймы.Схему крюковой обоймы принимаем по рис. П.6.1.в [10]. Конструктивноеисполнение элементов крюковой обоймы принимаем по рис. 1.7. а.[11] Минимальный диаметр канатных блоков по ручью согласно табл.П.1.3 [11] будет
dбл=kблdк=2524 =600 мм.
Принимаем диаметр блока по ручьюdбл= 600 мм. Основные размерыблока (рис. 2) принимаем по табл. П.5[11] в соответствиис диаметром каната и режимом работы:
ширина блока по ребордам В2 = 95 мм;
высота реборды h = 45 мм;
внешний диаметр блока dнб= dбл+2h =600+245 =690 мм;
ширина ступицы Вст =В2+10 = 105 мм (рис.1).
Диаметр ступицы определяем после определения диаметра оси блоков и выбора подшипников. Предварительно толщину щек крюковой обоймы принимаем щ= 14 мм.Расчетная длина lоси блоков складывается из суммы ширин ступиц блоков необходимых зазоров между самими блоками зазоровмежду блоками и щеками з=3÷5 мм и половинной толщины щек.
l= 3Вст+ 4 з+ 2 щ 2 = 3105+45+14 = 349 мм 035 м
Расчетная схема оси блоков и траверсы крюка показана на рис. 3. Реакции опор (растягивающее щеки усилие) при подъеме испытательного груза
Ra= Rb = 125Qg2 = 1252598121533 kH.
Усилие каждого блока полиспаста действующее на ось
Fбл = 125Qg 3 = 125259813 1022 kH.
Максимальный момент изгибающийосьблоков будет
Мизо =Ral2 - Fбл .l =15330352 -10220109 = 155kHм.
Минимальный диаметр оси блоков из стали 45 с термообработкой на улучшение и [изг] = 06т = 06315 =189 МПа
Диаметр оси корректируем по шариковому подшипнику. Каждый блок устанавливаем на два шарикоподшипника № 219 с допустимой статической нагрузкой 709 кН. Они имеют посадочный диаметр на ось dп= 95 мм внешний диаметр Dп=170 мм ширину B = 32 мм. Диметр ступицы блока принимаем dст=02 м.
Расчетная схема траверсы крюка (рис. 3) учитывает равномерно распределенную нагрузку от упорного подшипника № 8320 на который опирается крюк. Подшипникиме
ет размеры 100×170×55 мм и допустимую статическую нагрузку 330 кН. Конструкция траверсы показана на рис. 4. Максимальный изгибающий момент Миз т действующий на траверсу от равномерно распределенной нагрузкиqподшипниковой опоры крюка
q = Q с = 250022 1136 кНм
определяем по формуле
Миз т = (125Qg4)(l - 05c) = (12525981 4) (035 - 05022) =1839kHм
Размеры поперечного сечение траверсы принимаем по размерам сопрягаемых с ней деталей: размер отверстияDгу по диаметру хвостовика выбранного ранее грузового крюка Dгу= d1 + 2 мм = 01+ 2 = 0 102 м;ширину траверcы крюка Втпринимаем по диаметру опорного подшипникаВт = Dп+20 мм= 017+002 = 019 м; высоту траверсы hтпринимаем по длине хвостовика крюкаhт=L- диаметр цапфы траверсыпринимаем таким же как и для оси блоков Dц = 009 м.
Момент сопротивления траверсы по сечению А - А
Wт = (Bт – Dгу)hт2 6 = (019-0102)0182 6 = 47510-6 м3.
Допускаемыенапряжения изгиба в траверсе из стали 20 с термообработкой на улучшение имеющейнапряжения текучестит = 195МПа должны быть не более[из]= 06т = 06195 =117 МПа.Максимальные действующие напряжения изгиба в траверсе
= М W = 183103 47510-6 = 3852 МПа [].
Толщину щеки из стали 09Г2С имеющей напряжения текучести т = 330 МПаидопускаемые напряжения растяжения [р]= 06т = 198 МПа определяем на основеформулы Ламе где R =01 м ;do=.0085 м (рис. 5).
Ширинаbсечения щеки из расчета на растяжение должна бытьне менее
b = 125Qg 2 [p] = 12525103981 20013198106 006м.
Конфигурация щеки может быть прямой или фигурной для экономии металла. Крюковую обойму часто приходится утяжелять для исключения закручивания канатов полиспаста. Принимаем прямую форму щеки.
5. Определение параметров барабана. Конструкцию барабана предполагаем литой из стали 35 Л-1 с последующей механической обработкой. Минимально допустимый наружный диаметр барабанаDбопределяем по рекомендациям Правил (табл. П.7) [11].
Dб = кdк = 224 24 = 538 мм.
Диаметр витка каната по его оси на барабане будет
Dв =Dб +dк = 538+24 = 562 мм
Длина барабанаLб при однослойной навивке и шагом Св намотки каната
Св=dк+ 1 мм=24 +1 мм= 25 мм
Lб =[(Hin Dв)+15]185 =[(201036314562)+15]25 =656мм.
Такие параметры барабана принимаем окончательно. Влияние изгиба и кручения барабана считаются незначительными. Толщину стенки барабана определяем из условия сжатия тела барабана витками каната
= Fф14 [б] Св = 4310314 1001060025= 0024 м.
Принимаем толщину стенки барабана 25 мм.
При отношении Dб = 538 25 = 245 25 стенку барабана можно не проверять на устойчивость (табл.V.2.15) [15].
Частота вращения барабана для обеспечения заданной скорости подъема груза должна быть
nб = 60Vгр iDв = 60056 314056240 мин-1.
Принимаем конструкцию соединения барабана с редуктором Ц2 специального исполнения с выходным валом в виде зубчатой полумуфты. Эскиз барабана показан на рис. 6.
Барабан опирается на две консольно
закрепленные в нем оси. Диаметр реборд барабана должен бытьтаким чтобы за последним слоем навитого кантабыло не менее двух dк .
Dр = Dб + 4 dк = 538+424 = 634 мм.
Крепление каната на барабане осуществляем с помощью клина в теле барабана.
Подшипники опор барабана выбираем по максимальной нагрузке от грузоподъемного каната при подъеме испытательного груза. Радиальная нагрузка на подшипник будет максимальной при расположении ветви каната рядом с ребордой
Fр=Fмах= FфLб(Lб+b2)= 4308(08+008) 39kH.
Осевая нагрузка на подшипник Foпри угле отклонении каната на барабане = arctg (05LбLс мин) = arctg (05078) = 2°30'.
Fo =Fмахsin = 39sin 2°30' =19кН.
Выбираем шариковые двухрядные сферические подшипники средней широкой серии № 1616 с размерами 80×150×51 с допустимой статической грузоподъемностью Со= 454 кН;динамической грузоподъемностью С = 107 кН углом контакта тел качения α = 14° и е = 042ctg α 168
Требуемая долговечность подшипника должна быть не менее
Lt= (tпоZ)60 = (1121680) 60 =2028часов
где tпо = 0025(HV) = 0025(2005) = 1 мин
Проверка подшипника на долговечность выполняется по формуле
гдер= 3– показатель степени долговечности для шариковых подшипников;
Р = (XVFр+YFо)KK =(1143+168168)121.05= 5773 кН – эквивалентная динамическая нагрузка
где Х=1- коэффициент радиальной нагрузки при
Y= 042ctgα=168– коэффициент осевой нагрузки при
При требуемой долговечности подшипника 2028 часа и его расчетной долговечности 5062 часов межремонтный срок по замене подшипника составит
Zp= ZHLp Lt = 1250622048 25 года
Проверка оси барабана на статическую прочность. Расчетная схема оси барабана показана на рис. 8. Размер b1 выбран с учетом размеров подшипника и защитной крышки.
Рис. 8. Расчетная схема оси барабана
Максимальный изгибающий момент действующий на ось
Мo =125Fрb1 =12539006 295 кНм
Момент сопротивления оси изгибу
Wо = 01dп3 = 010083 = 51210-5м3.
из = Мo Wо = 29103 51210-5 = 05664108 Па = 5664 МПа.
Коэффициент запаса прочности оси из стали 45 с термообработкой на улучшение и пределом текучести т= 350 МПа
nт = т из = 3505664 = 61
Проверка оси барабана на усталостную прочность.Ось вращается вместе с барабаном и в ней возникают переменные изгибные напряжения симметричного цикла. Коэффициент запаса по нормальным напряжениям при симметричном изгибе определяем по формуле
где -1= 043в= 043570 = 245 МПа – предел выносливости стали 45 при симметричном цикле изгиба [9];
а=Fрb1 Wо = 386006 51210-5= 45703 МПа – амплитудные нормальные напряжения цикла при изгибе;
т = 0 – средние напряжения цикла;
k = 15 - эффективный концентратор напряжений в галтели вала;
=1 – коэффициент упрочнения (без упрочнения);
5–масштабный фактор при диаметре вала 80 мм из углеродистой стали;
kд=093 - принимают по графику на рис. 2.20 [9] в зависимости от отношения zбz0= 2007106 5106 4. Для валов диаметром до 100 ммz0 = 5106 циклов. Число циклов оси барабана zб= 60nбLt = 60402028 =1241106.
6. Определение параметров двигателя. В современных автомобильных кранах для привода механизмов применяют гидродвигатели. Рабочее давление рном в гидросистеме принимаем из нормативного ряда давленийпо ГОСТ 12445 рном= 20 МПа.Выбираемрегулируемый двигатель аксиально-поршневого типа спредполагаемым номинальнымчислом оборотов nдв=1200 обмин.В течение цикла нагрузка на двигатель механизма подъема постоянна.Определяем рабочий объем гидродвигателяqдвпо формуле
qдв = 2Мдв Δрдв =231409610317106091=00791610-3м3=791см3
гдеМдв=FфDбnб2nдвред = 430540 21200095 =096кНм–требуемыйноминальный момент на валу двигателя;
Δр = 085рном= 08520 = 17 МПа – предполагаемый перепад давлений между напорной и сливной магистралями;
дв = 091 – КПД гидродвигателя.
По каталогу выбираем типоразмер гидродвигателя 310.3.160.00 который имеет следующие номинальные параметры:
максимальный - 64лмин;
давление на входе МПа:
максимальное – 35 номинальное – 20;
частота вращения вала обмин:
максимальная – 3000 номинальная - 1800 минимальная – 60;
7. Выбор редуктора. Редуктор должен обеспечить передаточное число от барабана к двигателю
ip =nдв nб = 120040 = 30.
Вращающий момент на тихоходном валу
Мтв= FфDб 2 = 43053 2=1139кНм
консольная нагрузка принята равной 14 кН частота вращения быстроходного вала составляет41 с-1.
По табл. П.9.2 [9] выбираем редуктор Ц2-400 который обеспечивает в режиме работы М8 следующие показатели: передаточное число вращающий момент на тихоходном валуМт = 14кНм;допустимая консольную нагрузку на тихоходный вал -14кН.
8. Тормоз механизма подъема. Для удержания груза навесу приме-
няемпростой нормально замкнутый ленточный тормоз с углом охвата тормозного шкива лентой α = 270°.Тормоз должен обеспечивать тормозной момент не менее
Мт=кзапМтвред ip = 17511409530 = 0613 кНм.
Чертеж ленточного тормоза показан на рис. 9.
Исходя из возможности размещения грузового барабана и тормозногошкива при межцентровом расстоянии валов редуктора принимаем диаметр тормозного Dтш = 05 м. Тогда необходимое усилие на сбегающем конце ленты должно быть
где α = 270° - угол охвата лентой тормозного шкива;
f = 038 – коэффициент трения фрикционной накладки тормозной ленты по стальному шкиву. Фрикционная накладка на асбестовой основе при каучуковом связующем допускает удельные давления [q] = 08 МПа и температуру 240° С.
Максимальное набегающее усилие
Fнаб = Fсбefα = 0628271035471 =309кН.
Требуемая ширина ленты
Вл= 2 Fнаб ([q]) = 2309103 0810603 = 0097 м.
Принимаем ширину ленты Вл = 100 мм а ширину тормозного шкива – 110 мм. Толщина ленты выполненной из стали 45 должна быть не менее
=Fнаб [] Вл =309103 18010601 =1710-4 м.
По технологическим соображениям для возможности обеспечения крепления фрикционной накладки заклепками принимаем толщину стальной ленты 16 мм.Радиальный зазор между лентой и шкивом устанавливаем =1 мм. Ход сбегающего конца ленты
Х = (α360°)2 = 314(270°360°)21= 471 мм 5 мм
Расчет замыкающей пружины тормоза. Пружина сжатия имеетлинейную характеристику показанную на рис. 9.
Рисунок10. Характеристика пружины сжатия
Усилие пружиныFсб 2 при размыкании тормоза принимаем на 20% больше усилияFсб 1 необходимого для создания требуемого тормозного моментаFсб 2= 12Fсб 1 = 12 0628= 0753 кН.Характеристика пружины построена с учетом рабочего хода пружины Х = 5 мм. Определяем осадкупружины из подобия треугольников аОб и ООс
λ =5Fсб 2 Fсб 2-Fсб=507(07 – 062) = 43 мм.
Выбираем для пружины стальную углеродистую проволоку II класса по ГОСТ 9389 у которой в = 1400 МПа. Допускаемые касательные напряжения будут [] = 04 в = 041400 = 560 МПа. Задаваясь индексом пружины с = 6 вычисляем коэффициент k
k = (4с + 2)(4c-3) =(46 +2)(46-3) = 124.
Определяем диаметр проволоки
Принимаем диаметр проволоки d = 5 мм. D0 = cd = 65 =30 мм. Число рабочих витков определяем по формуле
Принимаем z=13. Полное число витков zп =15.Шаг пружины
t = d + λz + 01d = 5+4313+015 = 7808мм.
Высота пружины при полном сжатии витков
Нс = (zп – 05)d = (15 - 05)5 =725 мм.
Высота свободной пружины
Н0 = Нc+z(t - d) = 725 +13(808 – 5) = 1125 мм.
Сборочный чертеж грузоподъемной лебедки выполнен в соответствии с рекомендациям [9]. Все узлы лебедкиустановлены на специальной сварной раме. Чертеж выполнен в масштабе 1:4. На чертеже проставлены установочные (межцентровые) габаритные присоединительные (посадочные) размеры. Проставлены позиции сборных узлов оригинальных и стандартных деталей деталей крепежа. На рис. 10 показан пример выполнения сборочного чертежа лебедки.
Рис. 11. Сборочный чертеж грузоподъемной лебедки
Общий расчет автомобильного крана
1. Выбор базового автомобиля. Изучив существующие конструкции отечественных автомобильных кранов в качестве прототипа принят автомобильный кран КС – 55713 "Клинцы" (табл. 2.1. [1]). Кран имеет следующие параметры:
- грузоподъемность – 25т;
- длина стрелы макс. – 28 м;
- масса крана трансп. – 2065 т;
- масса крановой установки mку– 126т;
- размеры опорного контура 49×58 м
- базовый автомобиль – КамАЗ 65115
2. Определение масс узлов автокрана.Исходную расчетную схему автомобильного крана принимаем по рис. 12 с обозначенными на ней позициями основных узлов и агрегатов.
Первоначально определяем общую массу крана по графику на рис. 2.2 [1] в зависимости от заданного грузового момента. При грузовом моменте 100 тм ориентировочная масса крана составит mкр 21 т.Общая масса крановогооборудования будет
mко= mкр – m1 = 16 – 805 =8т
где m1 - снаряженная масса шасси базового автомобиля.
Массы отдельных элементов кранового оборудования вычисляем по рекомендуемым соотношениям [1]. Массы других элементов принимаем по аналогии с прототипом если они существенным образом не связаны с массой кранового оборудования:
- масса опорной рамы m2= 018mко= 0188 = 16 т;
- масса ОПУ m3= 003mко = 0031295 = 024 т;
- масса поворотной платформы m4 = 018mко = 0188 =144 т;
- масса контргруза m5 = 015mко = 0158 = 12 т;
- масса грузовой лебедки m6 = 006mко = 0068 = 048 т;
- масса механизма поворота m7 = 003mко = 0038 = 024 т;
- масса стрелы m8= qlc= 012186= 223т
где lc (H-28)sq= 012 тм – погонная масса стрелы.Приняв стрелу состоящей из трех секций массу каждой секции определяем в соответствии с табл. 2.3 [1].
- m8-1= 055m8= 055223 = 122т;
-m8-2= 045m8= 045223 = 1 т;
- гидроцилиндр с вдвинутым штоком m9+m10=005mко= 0058 = 04 т.
- шток гидроцилиндра m10 = 025(m9+m10) = 02504 = 01 т;
- кабина управления принимаем m11 = 045 т
- грузовой полиспаст m12 = 0015Qгр = 001225 = 038 т;
Полученные значения масс элементов крана заносим в табл. 2.1.
Расчетная масса крановой установки
mку= m2+ m3+ m4+ m5+ m6+ m7+ m8+ m9+ m10+ m11+ m12= 26+039+23+19+08+039+24+065+045+038 876Т.
3. Определение геометрических параметров крановой установки. Принимаем конфигурацию опорного контура квадратной т.е размерБ вдоль крана равен размеру К поперек крана. По графику на рис. 2.3 [1] определяем для грузового момента 100 тм К 6 м. Вычислив по формуле 2.1 [1] этот же параметр получим
Сравнив с прототипом принимаем окончательно размеры опорного контураК×Б =52×52 м.
ШиринаШ опорной рамы принимается равной ширине рамы автомобиля. Длину рамыБ вместе с концевыми балками под выносные опоры принимаем 55 м. Высоту опорной рамы принимаем hор = 2 hл = 2250 = 500 мм. Высота лонжерона hл= 250 ммавтомобиля КамАЗ 65115 определена по прил. 5 с учетом масштаба рисунка [1].
Номер роликового опорно-поворотного устройства выбираем по графику на рис.2.4 [1] в зависимости от вертикальной нагрузки на негоV и отрывающего моментаМотр.
V= (mку+ Q)g = (876+25)981 531кН 033МН;
Мотр = 12Мотрg =1280981=941кНм09МНм.
Полученным параметрам отвечает опорно-поворотное устройство № 6. Его геометрические размеры принимаем из табл. 2.4.[1]
Dопу = 1600мм ;hопу = 115 мм; m3 = 610 кг; z=102; m =12 мм.
Схематичный чертеж шасси КамАЗ 65115 с опорной рамой показан на рис.10.
Рис. 2.1. Чертеж базового автомобиля для крана с опорной рамой
Поворотную платформу со стреловым оборудованием выполняем в соответствии с рис. 11[1] по следующим размерам:
- диаметр опорного листа при толщине 20 мм
Д = Dопу+ 200 мм=1600+200 =1800 мм;
- расстояние от оси вращения до шарнира стрелы по горизонтали
rшс= 05Dопу+300 мм = 051600+300 =1100 мм;
- высота шарнира стрелы от плоскости ОПУ
hшс= hка–(hра+hор+hопу)+100 мм=2825-(1010+500+115)+100=1300 мм
где hка= 2825 мм –высотакабины автомобиля от земли (прил. 5 [1]);
hра= 1010 мм– высота лонжерона автомобиля от земли;
Рис. 2.2. Схема построения конфигурации поворотной платформы
- задний габарит поворотной платформы
rзг = rшс+ h8-1 +1000 мм = 1100+500+1000=2600 мм;
- высоту консоли поворотной платформы для установки грузовой лебедки принимаем конструктивно h8-1=200;
- высоту сечения корневой секции стрелы предварительно принимаем по прототипу h8-1=500 мм;
b8-1= 08h8-1= 08500= 400 мм;
- длина корневой секции
- расстояние отопорного шарнира стрелы до шарнира крепления гидроцилиндра
- ход и диаметр штока гидроцилиндра подъема стрелы принимаем по прототипуdгц= 200 мм;
- минимальная длина гидроцилиндра по осям проушин
- максимальная длина гидроцилиндра по осям проушин
- максимальный угол наклона стрелы к горизонту
arc cos = [(MQ)+ rшс] lc =[(8025)+11]186 75°.
Рис. 2.3. Схема для определения точек крепления гидроцилиндра наклона стрелы
Расчетная схема крана на рис. 2.4 скомпанована на основе схем по рис. 2.1 2.2 2.3. Схема выполнена в масштабе 1: 25. На схему нанесены центры тяжести элементов крана как плоских фигур и координатные оси. Ось Х проходит по опорной поверхности крана. Ось У совмещена с осью вращения крана. Координаты центров тяжести элементов крана в принятых осях также занесены в таблицу 2.1. Для каждого элемента крана в таблице вычислены статические моменты по осям Х и У. Результаты определения координат центров тяжести неповоротной поворотной частей крана и центр тяжести крана в целом определены в табл. 2.2 и нанесены на расчетную схему рис. 2.4.
Рабочая таблица для определения центра тяжести автокрана
Позиция на схеме к рис. 2.1
Масса узла автокрана
Координата Х центра тяжестиузла м
Статический момент узла по оси Х
Координата У центра яжеститузла м
Статический момент узла по оси У
Опорно-поворотный круг
Сумма неповоротных частей Н
Поворотная платформа
Корневая секция стрелы
Корпус гидроцилиндра
Сумма поворотных частей В
Суммарные параметры крана К
Параметры максимального груза
Результаты определения координат центров тяжести частей крана
Координата центра тяжести по оси Х м
Координата центра тяжести по оси У м
Хцтн= Мстнх Gн = - 1968
Уцтн= Мст ну Gн = 0937
Хцтв= Мствх Gв = - 047
Уцтв= Мст в у Gв= 618
Хцтк= Мсткх Gk = -135
Уцтк= Мст ку Gк= 307
Рис. 13. Расчетная схема для определения центра тяжести автомобильного крана
Результаты расчета фронтальной нагрузки на кран от ветраприведеныв
табл. 2.3. Формулы для расчета этой нагрузки даны в оголовке табл. 2.3.
Фронтальная рабочая ветровая нагрузка автокрана
Фронтальная площадь Sф = bh м2
Сила давления ветра
Координата У центра тяжести узла м
Опрокид. момент ветра
Опорная рама с опорами
Размеры b h определены соответственно вдоль осей Z Y.
Расчетное давление ветра для рабочего состояния крана принятоqp = 0125 кПа; 3. Коэффициенты учитывающие высоту hэлементов над уровнем земли принимают: приh = 0 10 м – кв = 10; при h= 10 20 м – кв = 125; при h = 20 40 м – кв= 155; для промежуточных значений высот квопределен линейной интерполяцией.
Аэродинамический коэффициент Са для автомобильных кранов с телескопической стрелой принятСа = 12.
Опорная рама и опорно-поворотное устройство находятся в тени ветровой площади базового автомобиля. l b h – неповоротных частей крана соответствуют габаритным размерам базового автомобиля. Контргруз лебедка грузовая механизм поворота находятся в тени ветровой площади поворотной платформы и вписываются в размеры l b h поворотной платформы. Гидроцилиндр со штоком для наклона стрелы находятся в тени ветровой площади ее корневой секции. При определении фронтальной ветровой нагрузкиэлементы находящиеся в тени элементов большей ветровой площадиветровую нагрузку не воспринимают и в расчетах устойчивости от опрокидывания она не учитывается.
Результаты определения боковой ветровой нагрузки на кран приведены
Боковая ветровая рабочая нагрузка автокрана
Боковая площадь Sб = lh м2
Опрокидывающий момент ветра Мвб = FвбУ кНм
Радиус вращения центра тяжести узла ±r
Момент сопротивления ветра повороту Мв =Fвб(±r)кНм
Н Неповоротных частей
В поворотных частей
Размеры l hопределены соответственно вдоль осей X Y.
Давление ветра для рабочего состояния крана принято qp = 0125 кПа; 3. Коэффициенты учитывающий высоту h элементов над уровнем земли приняты: при h = 0 10 м – кв = 10; при h = 10 20 м – кв = 125; приh = 20 40 м – кв = 155; для промежуточных значений высот кв определены линейной интерполяцией.
Боковая ветровая нагрузка определена при расположении стрелы крана вдоль оси Х.
Результаты определения динамических нагрузок при вращении крана приведены в табл. 2.4.
Таблица определения динамических нагрузок на автокран
КоординатаУ центра тяжести узла м
Расстояние от осивращения до центра тяжести узлаr м
Опрокидывающий момент
Момент силы инерции узла в начале вращения крана
Мсип = n J955 tp кНм
Н неповоротных частей
Параметры номинального груза
Угловая скорость крана определенадля заданной частоты вращения крана n обмин.
= п 30 с-1= 314130 = 0105 с-1.
Расстояние от оси вращения крана до центра тяжести узла принято "+r" для узлов у которых центр тяжести находится по одну сторону со стрелой от оси вращения крана; для остальных узлов расположенных противоположно стреле принято "-r".
Время разгона механизма поворота для автомобильных кранов грузоподъемностью 5 – 50 т принимают в зависимости от грузоподъемности соответственноtp= 2 ÷ 5 с.
Проверка устойчивости крана от опрокидывания
Устойчивость крана от опрокидывания гарантируется при выполнении неравенства определяемого формулой
где m0– коэффициент условий работы;
Mу– удерживающий момент относительно ребра опрокидывания;
k– коэффициент перегрузки от случайных нагрузок;
MНо – опрокидывающий момент нормативных нагрузок относительно того же ребра опрокидывания.
1.Проверка устойчивости при статических испытаниях выполнена при следующих условиях: кран поднял и удерживает груз на 25 % превышающий номинальную грузоподъемность крана без воздействия дополнительных нагрузок. Коэффициент условий работы
m0=т1 т2 =10948 = 0948
гдеm1 – коэффициент вовлечения веса крана в создание удерживающего момента. При работе крана на выносных опорах m1=1;
m2 - коэффициент однородности учитывающий отклонение масс отдельных частей крана от их номинального значения.
m2= (095ΣМ*- 105ΣМ**) (ΣМ*- ΣМ**) = (095726-105) (726-151)=0948.
ΣМ* = 726 кНм – суммамоментов веса частей крана относительно ребра опрокидывания совпадающие по направлению с удерживающим моментом (см. табл. 2.5).
ΣМ** = 144 кНм – суммамоментов веса частей крана относительно ребра опрокидывания совпадающие по направлению с опрокидывающим моментом (см. табл. 2.5).
Mу = Gкр(Хцтк+ Б2) = 157(135 + 62) = 6829 кНм.
MНо=Mоис=(125Gгр+025Gкан)b=(1252452+025246118)21= 630кНм.
Коэффициент устойчивости при статических испытаниях
кус =0948775 1645 = 103.
2. Проверка устойчивости при динамических испытанияхвыполнена при следующих условиях: кран поднимает и совершает все возможные движения с грузом на 10 % превышающим номинальную грузоподъемность крана при воздействии дополнительных нагрузок. Коэффициент условий работы будет иметь прежнее значение: m0 = 0948.
Моменты сил тяжести частей крана
относительно ребра опрокидывания
Сила тяжести узла Gi кН
Расстояние от ЦТ узла до ребра опро-кидыванияе м
Момент сил тяжести до ребра опрокиды-ванияМ = Gie кНм
Опорно-поворотный круг*
Поворотная платформа*
Корневая секция стрелы*
Корпус гидроцилиндра*
Грузовой полиспаст**
Сумма моментов веса частей крана относительно ребра опрокидывания совпадающие по направлению с удерживающим моментом ΣМ*= 70602
Сумма моментов веса частей крана относительно ребра опрокидывания совпадающие по направлению с опрокидывающим моментом ΣМ**= 793
Удерживающий момент также принимаем прежнимMу = 6829 кНм.
Опрокидывающий момент при динамических испытаниях определяем по формуле
MНо=Mоид =Mиг+Mип +Mив = 566 +191+298 =630 кНм
Нормативный опрокидывающий момент груза при динамических испытаниях
Mиг =11Gгр b =11245223 = 620356 кНм.
Момент от нормативных динамических нагрузок при подъеме стрелы и груза
Потенциальная энергия системы "кран – груз"
Ао= ΣВGУцтв+Gгрhгр= 8591325+11245220= 5685= 468103 кДж.
Кинетическая энергия груза при совмещении операций подъема стрелы и груза
Егр = 05[Vгр2+(сlс)2](11Q+m11)=
[052 +(002186)2](1125+045) = 54 к Дж.
Угловая скорость крюковой обоймы при изменении угла наклона стрелы от горизонтального до 75° за заданное время полного изменения вылета
с =2 360tвыл = 23147536060 = 002 с-1.
Кинетическая энергия стрелы
Ес = 05Jcc2 = 05256103 0022 =774 008 кДж.
Момент инерции стрелы относительно опорного шарнира как стержень с равномерно распределенной массой
Jc=(m8-1+m8-2)lc23=(1220+1000)18623 = 256103кгм2 .
Момент от динамической нагрузки при вращении крана
Mив=(11QhгрLгр– GврХцтвУцтв)кр2=
= (11252245 - 927029594)01052=168 кНм
Угловая скорость крана кр= п30 = 314130 = 0105 с-1.
Коэффициент устойчивости при динамических испытаниях
ку = m0Mу kMНо = 094868921630 =13>1
3. Проверка устойчивости при номинальных нагрузках (рабочей устойчивости) выполнена как и в предыдущих случаях по формуле
кур = m0Mу кMНог ≥ 1.
Коэффициентm0 и Mу удерживающий момент определены в предыдущих расчетах: m0 = 0948; Mу = 6829 кН. Коэффициент перегрузки к при проверке рабочей устойчивости учитывает влияние случайных составля
к=1+к1 к2 =1+50.075 =137
к1 = 5 – коэффициент надежности при выполнении работ не оговоренных особыми условиями.
- коэффициентизменчивости нагрузки.
ΣМsi2=Msгр2 + Msвк2+ Msвг2+ Msпг2 + Msвр2 – среднеквадратичные отклонения случайных составляющих нагрузок
гдеMsгр= ксгMгр =ксгGгрbгр= 004245223 =225кНм – моментот среднеквадратичного отклонения случайнойсоставляющей веса груза;
Msвк =125ксвкMвкН =125 012194 = 2918 кНм – момент от среднеквадратичного случайной ветровой нагрузки на кран;
Msвг = 01MвгН = 0136 = 36 кНм - момент от среднеквадратичного случайной ветровой нагрузки на груз;
Msпг=кдп MгрН= 0013398 = 517 кНм - момент от среднеквадратичного отклонения динамической нагрузки при работе механизма подъема
гдекдп – коэффициент динамичности.
кр– коэффициент режима включений численно равен индексу режима работы;
ку = 045 – коэффициент управления для автокранов с гидроприводом.
Msвр= 0006 Gгрhгр= 0006245220 =294 кНм – момент от среднеквадратичного отклонения динамических нагрузок при повороте крана.
Опрокидывающий момент при определении грузовой устойчивости опре
MНог = Mиг+Mвк +Mвг = 439 + 143 +34 = 4883 кНм.
Коэффициент рабочей устойчивости
кур = 0948815 1374883 = 115> 1
4. Построение грузовысотной характеристики автокрана
Предварительно вычисляем расстояниеот шарнира стрелы до ее центра тяжести в соответствии с рис. 2.4:
секции стрелы втянуты
секции стрелы выдвинуты
lсв=(rшс+05h8-1+01+xцтс)cos75°=[1+0507+01+137]0259=102 м .
Удерживающий момент неповоротных частей крана относительно ребра опрокидывания
Мун = ΣН G(Xцтн+d) = 964(202+22) = 4068 кНм.
Удерживающий момент от поворотных частей крана без стрелы
Мув = ΣВG(Хцтв+d) = 5734(107 +22) = 22347кНм.
Удерживающий момент от стрелы при втянутых секциях
Мусс= (G8-1+G8-2)(rшс+d – lцтссcos) =
(119+98)(1+22-471cos) = 2117(32 – 4715cos).
Удерживающий момент от стрелы при выдвинутых секциях
Мусв= (G8-1+G8-2)(rшс+d–lцтсвcos)=2117(32 -102cos)
Опрокидывающий моментот груза и грузового полиспаста
Мо = (Gгр+Gгп)(lсвcos –rшс – d) =(Gгр+Gгп)(102cos –32)
Грузовысотная характеристика крана построена в координатах " вылет – высота и масса поднимаемого груза" в соответствии с расчетной схемой на рис. 2.4. Расчетные значения точек графической грузовысотной характеристики при увеличении угла наклона стрелы через каждые 10 ° приведены в табл. 2.6. Графическое отображение грузовысотной характеристики крана показано на рис. 2.5.
Табличная грузовысотная характеристика со втянутой стрелой
Угол наклона стрелы ° и cos
Вылет крюка Lгр= lсcos - rшс=
Высота крюка h = hшс+lcsin =
Масса удерживаеого груза
m=(Mун+Mув+Mусв)14g(lсвcos-rшс-d) =
Табличная грузовысотная характеристика со выдвинутой стрелой
Высота крюка h = hшс+lcsin=
Масса удерживаеогогруза
Рис. 2.5.Грузовысотная характеристика
Рис. 2.5. Графические грузовысотные характеристики крана со втянутой (12) и выдвинутой (34) стрелой: 1 3 – грузовые характеристики; 2 4 – высотные характеристики
Расчет механизма поворота
1. Исходные данные для расчета механизма поворота.
Для расчета механизма поворота используем расчетную схему крана изображенную на чертеже общего вида формата А1 полученную в результате общего расчета крана.
Кинематическую схему механизма поворота принимаем по рис. 3.1.
Максимальная грузоподъемность крана на минимальном вылете Lмин = 41м согласно грузовой характеристике составляет Q = 25 т.
Частота вращения крана согласно заданиюn = 12обмин.
Сила тяжести поворотной части принимаем из табл. 1.1.
Расстояние от оси вращения крана до центра тяжести его поворотной части хцтв = - 047 м (табл.1.2).
Диаметр выбранного роликового опорно-поворотного устройства
по осям тел качения D1опу = 16 м; диаметр делительной окружности зубчатого венца ddк= 1218 мм; число зубьев на венце zк = 102; модуль зубьевm =12 ; ширина зубьев колеса bк= 102 мм.
Момент сопротивления ветра повороту Мсвп = 166кНм (табл. 2.4).
Предельно допустимый уклон опорной рамы крана ≤ 3°.
Группу режима работы механизма поворота принимаем такую же как и для всего крана.
2. Определение моментов сил сопротивления
Активными силами сопротивления повороту являются силы трения в опорно-поворотном устройстве сила давления ветра на боковую площадь крана составляющая сил тяжести поворотной части при угле уклона поворотной платформы ≤ 3°.
Момент сил трения в опорно-поворотном устройстве определяем в зависимости от отношения Мопу Fgопу.
Суммарная вертикальная нагрузка на ОПУ
Fgопу = ΣGв +gQ = 668+ 98125 = 31205.
Момент от нормативных составляющих нагрузок действующих на ОПУ относительно оси проходящей через центр ОПУ нормально к плоскости подвеса стрелы в соответствии с рис. 2.4.
Мопу= QgL + ΣMв пч+Mв гр- GΣвXцтв=
= 2598141 + 803 + 357–668047 = 1017 кНм.
ЗначенияΣMв пч и Mв гр принимаем из табл. 3.1
Отношение Мопу Fgопу.= 101731205 = 32 >Dопу4 = 16004 = 04 по этому момент сил трения в ОПУ определяем по формуле
Сопротивление вращению от давления ветра в табл. 2.4 представлены моментами сопротивления ветра действующими на поворотную часть крана ΣВ – Мвбк = 166кНм и на груз Q – МвбQ = 871 кНм.
Фронтальная рабочая ветровая нагрузка на поворотную часть автокрана
Максимальное сопротивление вращению вызванное возможным наклоном поворотной платформы к горизонту на допустимый угол = 3° определяем по формуле
Му макс = (Q + т12)gsinLмин+ΣGвsinХцтв =
= (25+038)981sin3°41 + 6680 sin3°(- 047) 517 кНм.
Момент от сил инерции при пуске и торможении механизма поворота
Момент инерции груза Jгр как точечной массы
Jгр = Q10³ Lгр² = 2510³41² 450250 кгм².
Момент инерции поворотной платформы относительно оси вращения
Jпч = Σтпч10³ Хцтв ² = 87110³(-047²) = 7424 кгм².
Максимальный момент сопротивления вращению крана при расчете элементов механизма поворота на прочность
Ммакс= Мтопу+Мвбк+МвбQ+Му+Мин=282+166+871+517+14=10427 кНм.
Реальная (среднеквадратичная) мощность необходимая для поворота крана с грузом
Приняв рабочее давление в гидросистеме крана р = 20 МПа принимаем решение применить для привода механизма поворота крана аксиально-поршневой реверсируемый гидродвигатель. По табл. П17.3 – П 17.6 [11] останавливаемся на гидродвигателях типа 310.2. При номинальном числе оборотов вала двигателя 1800 обмин крутящий момент на его валу должен быть
Мдвп = 955Nnдв = 955941800=00498 кНм 50 Нм.
Требуемый номинальный рабочий объемqгидродвигателя определяем по формуле
q =2МдвпΔpм=2314004910³1710609 18 см3 .
Номинальная подача должна быть при объемном кпдгидродвигателя
Q = q10-3nдвоб = 1810-3180009 36лмин.
Выбираем типоразмер гидродвигателя 310.2.28.00 с номинальными параметрами:
Крутящий момент М Нм – 84 ;
Рабочий объем этого двигателя q = 28 см3 .
Число оборотов вала двигателя с таким рабочим объемом будет составлять при подаче 36 лмин
nдв = Qq10-3 =36092810-3 = 1157 обмин.
Общее передаточное число механизма поворота будет
iмп = nдвnкр =115712= 964
Назначаем число зубьев ведущей шестерни механизма поворота
zш =19. Тогда передаточное число открытой зубчатой передачи при принятом опорно-поворотном устройстве механизма поворота будет
iоп =zк zш = 88 19 463
Передаточное число редуктора механизма поворота
iрп = iмп iоп = 1157463 = 24989
3. Кинематический расчет редуктора механизма поворота
Принятая схема редуктора (рис. 3.1) представляет собой трехступенчатый редуктор состоящий из простой цилиндрической передачи первой ступени z1-z2и двух планетарных ступенейz3-z4-z5-H2иz6-z7-z8-H3 где Н2 и Н3 обозначены соответственно водила второй и третьей ступеней. Назначаем передаточное число первой ступени редуктора i1 = 2 и количество зубьев шестерни z1 из условия неподрезания ножки зуба шестерни z1 = 20. Тогда z2 = i1 z1 = 220 = 40. Передаточное число второй ступени редуктора принимаем i2=10. Тогда передаточное число третьей ступени будет
i3 = iрп i1i2 = 24989210 = 124.
Принимаем число зубьев шестерни z3 = 24 и число сателлитов Z2=3.Число зубьев неподвижного колеса z5находим из кинематического условия планетарной передачи
z5 = z3 (i2Н2 - 1)=24(10 – 1)=216
Разность чисел z5 – z3 должна быть четным числом.
z5 – z3 = 216 – 24 = 192 – число четное.
Число зубьев сателлитовz4 находим из условия соосности передачи
z4 = (z5 – z3) 2 = (216 – 24)2 = 96
Условие соседства сателлитов
66 > 0816 – условие выполнено.
По условиям сборки планетарной передачи выражение (z3+z5)Z2 должно быть целом числом. (24+216)3 = 80 – условие сборки выполнено.
Третья ступень редуктора по кинематике аналогична второй его ступени. Принимаем z6 = 20 и число сателлитовZ3 = 3. Число зубьев неподвижного колеса z8 определяем из выражения
z8 = z6 (i6Н2 - 1)=20(124 – 1)= 228
Разность чисел z8 – z6 должна быть четным числом. Принимаем
z8– z6 =228 – 20 = 208– число четное.
Число зубьев сателлитовz7 находим из условия соосности передачи
z7 = (z8– z6) 2 = (208 – 20)2 =94
66 > 0842 – условие выполнено.
По условиям сборки планетарной передачи выражение (z6+z8)Z2 должно быть целом числом. (20+208)4 = 57– условие сборки выполнено.
4. Проверка прочности вала и ведущей шестерни
Определяем диаметр начальной окружности ведущей шестерни при назначенном количестве зубьев шестерни zш = 19 и модуле зубьев опорно-поворотного устройства m =14
dш = zш m = 19 14 = 266 мм = 0266 м.
bш = bк + 10 мм =102+10 = 112 мм
Конструктивное исполнение выходного вала редуктора поворота с установленной ведущей шестерней показано на рис. 3.2. Проработка установки выходного вала осуществляем после предварительного определения его диаметра из условия передачи им максимального крутящего момента Мкрв.
Мкрв = Ммакс dш dопу=10427 266 1218 = 227 кНм
. На вал действуют окружное Fокри радиальное усилие Fрад от взаимодействия ведущей шестерни с колесом опорно-поворотного устройства.
Fокр = 2Мкрв dш = 22270266 =1706 кН
Fрад = 2Мкрвtg20°dш = 226503640266 = 6212kH.
С учетом действия на вал изгибающего и крутящего моментов принимаем решение изготовить вал из прокатной стали 40Х по ГОСТ 4543 с термообработкой на улучшение и пределом прочности при растяжении
в = 685 МПа пределом текучести т = 540 МПа. Допускаемые напря
жения на изгиб при симметричном нагружении[и-1] 043 т = 045540 243 МПа; Допускаемые напряжения при кручении [-1] 022 т = 022540 119 МПа. Ориентировочный диаметр вала из расчета на кручение
Проверку прочности вала с учетом долговечности выполняем после определения условий размещения опорных и передаточных элементов (рис. 3.2). Размер е2 10 мм обусловлен толщиной стенки крышки подшипника 4 6 мм и необходимостью зазора между шестерней и крышкой подшипника 5 7 мм. Размер bм = 2×12 = 24 мм определен толщиной уплотнительных манжет для диаметра вала 100 мм. Для надежного уплотнения вращающегося вала ставят 2 или 3 манжеты. Подшипники предварительно выбираем по диаметру вала. Учитывая консольное расположение ведущей шестерни на выходном редуктора и значительную радиальную нагрузку выбираем роликовый сферический подшипник с допустимой статической нагрузкой приблизительно в 2 раза больше чем окружное усилие в зубчатом зацеплении. Этому условию отвечает подшипник
№ 3524 с допустимой статической нагрузкой 375 кН и размерами d×D×b -120×215×58 мм. Второй подшипник № 3519 имеет размерыd×D×b - 90×160× 40 и допустимую статическую нагрузку 175 кН.
Размер е1 100 мм принимаем конструктивно приблизительно равным или несколько меньше диаметра вала в основном подшипнике. Расчетная схема вала показана на рис 3.3
Рис. 3.3. Расчетная схема выходного вала к рис. 3.2 (на схеме вал условно расположен горизонтально)
Длинышеек валов определяем в соответствии с рис. 3.2.
а1 = bш 2+e2+bм+5 мм+ bп 2=1122+10+24+5+582 =124 мм
а2 =bп 2 +e1+bп 2=582+100+402 = 149 мм.
По полученным размерам определяем опорные реакции в подшипниковых узлах и изгибающий момент на валу в плоскости X - Z
R1z=Fокр(а1+а2)а2 =18424(124+149)149 = 365 кН;
R2z=Fокра1а2 =18424124149 = 15332кН;
Мизгz =Fокра1 =184240124 = 228кНм.
Опорные реакции и изгибающий момент в плоскости Х - У
R1х=Fрад(а1+а2)а2 =6935(124+149)149 = 12706 кН;
R2х=Fрада1а2 =6935124149 = 577 кН;
Мизг х =Fрада1 =69350124 = 85 кНм.
Суммарная реакция в опоре 1
Суммарная реакция в опоре 2
Суммарныйизгибающий момент в опасном сечении
Проверка статической прочности выходного вала редуктора.
Нормальные напряжения от изгибающего момента на опоре 1
изг = Мизг Σ Wизг = 2510³01012³ =140 МПа.
Запас прочности по нормальным напряжениям
п = т изг = 540140 = 385.
Касательные напряжения от крутящего момента и перерезывающей силы
= Мкрв Wкр+133R1Σ 0785d² =
= 22710³ 02012³ +133385106 0.785012² =1102 МПа
Запас прочности по касательным напряжениям
п = т =06540 1102 = 294.
Запас прочности при совместном действии нормальных и касательных напряжений
Упрощенная проверка вала на усталостную прочность заключается в проверке условия сопротивления усталости при действии эквивалентного момента
Эквивалентные напряжения в опасном сечении
экв =Мэкв10³ 01d³ =3325010³01120³=1924 МПа.
Кзап= [и-1] экв=243 1924= 126.
Механизм наклона стрелы.
Изменение вылета на автомобильных кранах осуществляется двумя способами:
а) путем изменения наклона стрелы;
б) путем удлинения стрелы (телескопирования).
Из предыдущих расчетов используем следующие исходные данные данные :
Сила тяжести номинального грузаGгр=2452 кН
Усилие грузоподъемного канатаFф=43 кН
Центробежная силы инерции грузаFцг=124 кН
Сила давления ветра на грузFвг=40
Сила тяжести стрелыGc=2124
Положение центра тяжести стрелыlgc=102
Угол наклона стрелы к горизонтуα=75º
Центробежная силы инерции стрелыFцc=29 H
Сила давления ветра на стрелуFвc=12кН
Давление в гидросистемеp=25 МПА
Ход штока гидроцилиндраlш=15м
Время полного изменения вылетаtв=60с
Расчетные геометрические параметры принимаем с общей схемы крана с учетом масштаба чертежа: k=03 м m=113м r=143м.
Усилие штока гидроцилиндра определяем в соответствии с расчетной схемой рис.4.1
При принятом рабочем давлении р (МПа) в гидросистеме и механическом КПД гидроцилиндра мгц = 095 требуемая площадь поршня гидроцилиндра должна быть не менее
Sп = Fгц p мгц = 1080103 25106 095=00450 м2
Диаметр поршня гидроцилиндра
Расход гидравлической жидкости при изменении вылета при объемном КПД гидроцилиндра оц = 099
Qв= Sпlшtв оц=004501560099=00011м3с=11 лс
Максимальная мощность потребляемая насосом при увеличении наклона стрелы крана с учетом потерь давления в трубопроводах (Δртр = 05 МПа) и КПД насоса (н 09):
N = (25 + 05)10600011 09=311кВт.
Список использованной литературы
Автомобильные краны. Конструкция и расчет: учеб.- метод. пособие
Ю.И. Калинин Ю.Ф. Устинов В.А. Жулай В.А. Муравьев; Воронеж
ский ГАСУ – Воронеж 2014 - 150 с.
Проектирование механизмов грузоподъемных кранов.: учеб.-метод. Пособие Ю.И. Калинин Ю.Ф. Устинов В.А.Жулай В.А.Муравьев;Воронеж.Гос. арх.-строит. ун-т.-Воронеж 2010.-156с.
Стреловые самоходные краны : учеб.-метод.пособие для студ.спец. 190205 Ю.И.Калинин Ю.Ф.Устинов ; Воронеж. Гос. Арх.-строит. ун-т.-
Спецификация 2.docx
Шайба пр. 10 ГОСТ 6402-80
Болт М14х40 ГОСТ 7798-81
Шайба пр. 14 ГОСТ 6402-80
Болт М27х100 ГОСТ 7798-81
Шайба пр. 27 ГОСТ 6402-80
Гайка М27 ГОСТ 5915-81
Болт М10х30 ГОСТ 7798-81
Гайка М16 ГОСТ 2528-82
Шайба 16 ГОСТ 6958-82
Шплинт 4х30 ГОСТ 397-79
Шпилька М16х50 ГОСТ 11769-82
Шайба пр. 16 ГОСТ 6402-80
Гайка М16 ГОСТ 5915-81
Болт М36х90 ГОСТ 7798-81
Гайка М36 ГОСТ 5915-81
Шайба пр. 36 ГОСТ 6402-80
Болт М27х90 ГОСТ 7798-81
Подшипник 1315 ГОСТ 5720-75
Манжета 1-75х100 ГОСТ 8752-79