Автогудронатор ДС–142Б




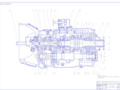
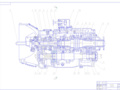
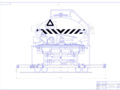
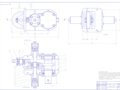
- Добавлен: 25.10.2022
- Размер: 3 MB
- Закачек: 0
Описание
Состав проекта
![]() |
![]() |
![]() ![]() ![]() ![]() |
![]() ![]() ![]() ![]() |
![]() ![]() ![]() ![]() |
![]() ![]() ![]() ![]() |
![]() ![]() ![]() ![]() |
![]() ![]() ![]() ![]() |
![]() ![]() ![]() ![]() |
![]() ![]() ![]() ![]() |
![]() ![]() ![]() ![]() |
![]() ![]() ![]() ![]() |
![]() ![]() ![]() ![]() |
![]() ![]() |
![]() ![]() |
![]() ![]() |
![]() ![]() |
![]() ![]() |
![]() ![]() |
![]() ![]() |
![]() ![]() |
![]() ![]() |
![]() ![]() |
![]() ![]() |
![]() |
![]() |
![]() ![]() ![]() |
![]() ![]() ![]() |
![]() |
![]() ![]() ![]() |
![]() |
![]() ![]() |
![]() ![]() ![]() |
![]() ![]() ![]() |
![]() ![]() ![]() |
![]() |
![]() ![]() ![]() |
![]() ![]() ![]() |
![]() ![]() ![]() |
![]() ![]() ![]() |
![]() ![]() ![]() |
![]() ![]() ![]() |
![]() ![]() ![]() |
![]() ![]() ![]() |
![]() ![]() |
![]() ![]() |
![]() ![]() |
![]() ![]() |
![]() ![]() |
![]() ![]() |
![]() ![]() |
![]() ![]() |
![]() ![]() |
![]() ![]() |
![]() ![]() |
![]() ![]() |
Дополнительная информация
Лист4 - Коробка передач.dwg

Лист5 - Коробка передач в сборе.dwg

отбора мощности автогудронатора
Лист7 - Коробка отбора мощности.dwg

Вращение шестерён должно быть плавным
При подаче воздуха в пневмокамеру 0
МПа ведомая шестерня
поз. 14 должна переместится в крайнее правое положение
при подаче давления в противоположную пневмокамеру
возвращаться в исходное положение.
КОМ обкатать вхолостую 0
часа. Неравномерный шум и
Лист1 - Общий вид автогудронатора.dwg

Вместимость цистерны
Максимальная скорость
Максимальная мощность двигателя
Лист6 - Промежуточный вал в сборе.dwg

Лист9 - Корпус КОМ.dwg

мощности автогудронатора
Неуказанные радиусы в отливке 2..3 мм
Формовочные уклоны по ГОСТ 3212-57
Неуказанные допуски на размеры в отливке по ГОСТ 1855-55 кл.
неуказанные размерам 8
Неуказанные предельные отклонения размеров:
Покрытие внутренних необработанных поверхностей эмалью или
грунтовкой с учётом условий эксплуатации У1 или Т1
На поверхностях внутренних расточек и на привалочных
плоскостях раковины не допускаются
Допускается изготовление из СЧ20 или СЧ15 ГОСТ1412-79
После обработки толщина стенок в зоне Ж должна быть не
Лист3 - Графики тягового расчёта.dwg

График мощностного баланса
Внешняя скоростная характеристика двигателя
График силового баланса..
Лист2 - Общий вид автогудронатора.dwg

Лист8 - Деталировка.dwg

Допуск на радиальное биение
Допуск на погрешность
сердцевина зубьев 22..34 HRC
Радиус закругления у вершины и основания зуба 4
* размер для справок.
Разрешается изготовление из стали 40ХНЗА ГОСТ 4543-71
Разрешается изготовление из стали 40ХН ГОСТ 4543-71
сердцевина зубьев 22..34 HRCэ остальные поверхности не менее
Разрешается изготовление из стали 20ХНЗА и 25Х ГОСТ 4543-71
.На поверхностях З и И допускаются следы инструмента глубиной 2мм.
* Размер. обеспеч. инстр.
Нормальный исходный контур
Коэффициент смещения
Степень тосности по ГОСТ 1643-81
Предельное отклонение шага
Лист10 - ФСА.dwg

отбора мощности автогудронатора
проектируемый вариант
Диаграммы значимость - стоимость
Диаграммы важность - качество
Лист4 - Коробка передач1.dwg

Смазывание коробки отбора мощности производится за счет
Экономика.doc
Функционально-стоимостной анализ (ФСА) модернизации коробки отбора мощности автогудронатора.
ФСА проводят как при проектировании новых конструкций так и при совершенствовании освоенных в производстве изделий. Главная предпосылка ФСА - предположение о том что в каждой конструкции заложены резервы снижения себестоимости выполняемые оптимизацией конструкторско-технологических решений. Таким образом задачей ФСА является прежде всего минимизация затрат на реализацию необходимого комплекса функций при заданном качестве.
При использовании ФСА конкретное изделие (машина узел механизм) рассматривается не только как совокупность составляющих его элементов: сборочных единиц деталей (т.е. материальных носителей) но и как объект реализации конкретных функций. Выделяют с точки зрения полезности необходимости следующие разновидности функций:
- основные функции соответствующие прямому назначению изделия
отражающие его потребительские качества;
- вспомогательные функции обеспечивающие выполнение основных
- ненужные функции необязательные в изделии часто просто
В реальных конструкциях удельный вес затрат связанных с выполнением ненужных функций составляет 5-12% себестоимости изготовления изделия. Проведение ФСА в дипломном проектировании может быть рекомендовано для случаев когда нет возможности выполнить сравнительный технико-экономический анализ проектируемой конструкции а также для поиска путей снижения себестоимости без ухудшения заданных технических характеристик изделия. ФСА включает следующие этапы:
Информационный этап. Сбор информации об объекте (планируемый
объем выпуска себестоимость рентабельность чертежи спецификации ГОСТ ОСТ ТУ стандарты предприятия патентные источники рекламации и т.д.).
Аналитический этап. Выявление и классификация функций
построение функционально-структурной модели изделия определение
важности и значимости функций распределение по функциям материальных
затрат расчет затрат на каждую функцию построение функционально-
стоимостной диаграммы.
Творческий этап. Поиск возможных путей устранения точек
рассогласования или уменьшения стоимости реализации функций. Широко
используются такие формы коллективного творчества как мозговая атака
конференция идей творческие совещания метод контрольных вопросов и
т.п. При поиске альтернативных вариантов реализации отдельной функции
используют морфологический анализ и картотеку типичных решений.
Исследовательский этап состоит в рассмотрении преимуществ и
недостатков предложенных вариантов реализации функций и в оценке затрат.
Обсуждение оценка и отбор вариантов - не менее важная задача чем их
поиск. Прежде всего варианты рассматривают с позиций:
- работоспособности (работоспособные неработоспособные);
- времени осуществления (неосуществимые по техническим причинам
предлагаемые для перспективного внедрения. предлагаемые для
безотлагательного внедрения);
- экономической эффективности.
Варианты предлагаемые для внедрения подвергаются экспертной оценке по уровню выполнения технических требований и ранжируются по обеспечиваемым свойствам и по степени приближения к «цели по затратам».
Выбор «цели по затратам» - особенность именно функционально-стоимостного анализа. Один из возможных способов ее определения заключается в том чтобы найти для каждой функции вариант с минимальными затратами т.е. наиболее дешевый способ ее реализации.
Суммируя затраты по этим вариантам определяют минимально возможную себестоимость проектируемого изделия. Однако снизить затраты до этого теоретического минимума практически не удается так как для объединения частных решений в единое целое могут потребоваться очень большие дополнительные средства. Тем не менее степень приближения к этому минимуму может служить основанием для ранжирования предложенных вариантов.
Рекомендательный этап заключается в подготовке необходимой
документации в виде чертежей эскизов расчетов пояснительных записок по
принятым вариантам реализации функций.
Характерные особенности ФСА - специфический предмет анализа (функции изделия) строго определенная последовательность проведения широкое использование различных коллективных форм творчества непрерывно осуществляемая экономическая оценка - позволяют рассматривать его как отдельное и весьма эффективное направление технико-экономического анализа.
Особенностью метода ФСА является использование элементов
коллективного творчества при решении конструкторских изобретательских
задач с целью избавиться от стереотипности индивидуального мышления при
поиске лучшего решения («мозговой штурм» «конференция идей»
морфологический анализ метод контрольных вопросов и т.д.).
Методологию ФСА при проектировании можно применять для
различных иерархических уровней конструкции: схемы сборочных единиц
деталей. Для уровня «схема конструкции» применение ФСА возможно в двух
направлениях: 1) выбор принципиальной схемы конструкции - при
проектировании новых изделий; 2) анализ вариантов исполнения
конструкции в пределах существующей принципиальной схемы - при
текущем совершенствовании изделий.
При использовании ФСА на уровне «сборочная единица» внимание сосредоточивают на анализе вариантов исполнения сборочной единицы в пределах конкретной принципиальной схемы. Рассматривают возможность изменения числа элементов их размещения взаимодействия и т.д.
Для иерархического уровня «деталь» метод ФСА может быть использован при анализе конкретного исполнения детали (габариты масса число поверхностей обработки размеры обрабатываемых поверхностей взаимное расположение поверхностей характеристики качества обработки поверхностей и т.д.) в пределах выбранной конструкции сборочной единицы и принципиальной схемы.
ФСА объекта проектирования.
В результате данного анализа в базовом варианте необходимо обнаружить функциональные и структурные элементы системы обладающие экономической несостоятельностью или функциональной недостаточностью.
Порядок проведения корректирующей формы ФСА.
Построение структурной модели разрабатываемой системы (объекта).
Структурная модель (СМ) - это упорядоченное представление элементов объекта и отношений между ними дающее представление о составе материальных составляющих объекта их основных взаимосвязях и уровнях
иерархии. Для построения СМ рекомендуется использовать методику логической цепочки (FAST).
Структурная модель базового варианта представлена в таблице 3.1.
Структурная модель проектируемого варианта представлена в таблице 3.5.
Построение функциональной модели (ФМ) объекта.
Функциональная модель базового варианта представлена в таблице 3.2 (значимость функций в числовом выражении – таблица 3.3).
Функциональная модель проектируемого варианта представлена в таблице 3.6 (значимость функций в числовом выражении – таблица 3.7).
ФМ - это логико-графическое изображение состава и взаимосвязей функций объекта получаемое с помощью их формулировки и установления порядка подчинения.
ФМ также должна строиться на основе техники систематизированного анализа функций (FAST).
При этом необходимо руководствоваться следующими правилами:
а)линии критического пути ФМ должны соответствовать тем функциям которые должны быть выполнены обязательно для реализации главной функции изделия;
б)соответствие выделяемой функции как частным целям данной составляющей объекта так и общим целям ради которых создается объект;
в)четкая определенность специфики действий обуславливающих
содержание выделяемой функции;
г)соблюдение строгой согласованности целей и задач определивших
выделение данной функции с действиями составляющими ее содержание;
д)функции верхнего уровня должны являться отражением целей для
функций нижестоящего уровня;
е)сигналом к завершению построения ФМ должна являться
невозможность дальнейшей дифференциации функций без перехода от
функций к предметной форме их исполнения.
Построение совмещенной функционально-стоимостной модели (ФСМ) объекта.
ФСМ объекта пригодна для выявления ненужных функций и элементов в объекте (бесполезных и вредных); определения функциональной достаточности и полезности материальных элементов объекта; распределения затрат по функциям; оценки качества исполнения функций; выявления дефектных функциональных зон в объекте; определения уровня функционально-структурной организации изделия.
Построение ФСМ осуществляется путем суперпозиции ФМ и СМ объекта.
ФСМ базового варианта представлена в виде таблицы 3.4.
ФСМ проектируемого варианта представлена в виде таблицы 3.8.
Сводный ФСМ обоих вариантов представлен в виде таблицы 3.9.
Оценка значимости функции ведется последовательно по уровням ФМ (сверху вниз) начиная с первого. Для главной и второстепенной т.е. для внешних функций объекта при оценке их значимости исходным является распределение требований потребителей (показателей качества параметров свойств) по значимости (важности).
Ниже приведены формулы для построения ФСМ.
Нормирующим условием для функции является следующее:
n - количество функций расположенных на одном уровне ФМ и относящихся к общему узлу вышестоящего уровня.
Для внутренних функций определение значимости ведется исходя из их роли в обеспечении функций вышестоящего уровня.
Определение относительной важности функции R.
Учитывая многоступенчатую структуру ФМ наряду с оценкой значимости функций по отношению к ближайшей вышестоящей определяется показатель относительной важности функции любого i - го уровня Rij по отношению к изделию в целом:
где G - количество уровней ФМ.
В случае если одна функция участвует одновременно в обеспечении нескольких функций верхнего уровня ФМ ее значимость определяется для каждой из них отдельно а относительная важность функции для объекта в целом рассчитывается как сумма значений Rij по каждой ветви ФМ (от i - го уровня до первого) проходящей через эту функцию.
Оценка качества исполнения функций.
Обобщенный (комплексный) показатель качества варианта исполнения функций оценивается по формуле:
где n - значимость n - го потребительского свойства;
Pnv - степень удовлетворения n - го свойства в v - ом варианте;
m - количество свойств.
Важным элементом качества исполнения функций является функциональная организованность изделий которая определяется следующими показателями:
-показатель актуализации функций определяется коэффициентом
где FP - необходимые функции;
Fob - общее количество действительных функций;
-показатель сосредоточения функций определяется коэффициентом
где Fosn - количество основных функций;
Fob - общее количество функций;
- показатель совместимости функций определяется коэффициентом совместимости:
где Fc - функции согласования;
Роб - общее количество функций;
- показатель гибкости функций определяется коэффициентом гибкости:
где FP - количество потенциальных функций;
FR - количество необходимых функций.
Учитывая (3.4) (3.5) (3.6) (3.7) выражение качества выполнения функций будет иметь вид:
Определение абсолютной стоимости функций.
Функционально необходимые затраты - минимально возможные затраты на реализацию комплекса функций объекта при соблюдении заданных требований потребителей (параметров качества) в условиях производства и применения (эксплуатации) организационно-технический уровень которых соответствует уровню сложности спроектированного объекта.
Абсолютная стоимость реализации функций Sabs определяется по формуле:
Str - затраты связанные с трудоемкостью реализации функции;
Sen - энергозатраты на реализацию функции;
Sproch - прочие затраты на реализацию функции (отвод земли изыскания плата за загрязнение и пр.).
Определение относительной стоимости реализации функций. Относительная стоимость реализации функций SotnF определяется по формуле:
где ΣSabs - суммарная абсолютная стоимость функционирования объекта определяется путем суммирования значений абсолютных стоимостей реализации функций;
SabsFij - абсолютная стоимость реализации i - ой функции j - го уровня ФМ.
Построение функционально-стоимостных диаграмм (ФСД) и диаграмм качества исполнения функций (КИФ).
Данные диаграммы строятся для базового проектного варианта исследуемого объекта. Они имеют целью выявление зон диспропорции т.е. зон избыточной затратности реализации функции а также определение зон функциональной недостаточности (низкого качества исполнения функций).
Диаграммы ФСД и КИФ строятся для базового варианта (до принятия и реализации проектного решения) и проектного варианта.
На основании сравнения этих диаграмм можно судить о степени полезности и экономической целесообразности курсового проекта.
Структурная модель базового варианта.
Функционально модель базового варианта.
Значимость функций модели базового варианта.
Функционально-стоимостная модель базового варианта.
Качество исполнения [Q]
Поддерживающая функция
Обеспечивает вращение вед. шестерни
Обеспечивает вращение пром. шестерни
Воспринимает давление
Приводит вдвижение насос
Обеспечивает вращение вала - шестерни
Структурная модель проектируемого варианта.
Функционально модель проектируемого варианта.
Значимость функций модели проектируемого варианта.
Функционально-стоимостная модель проектируемого варианта.
Сравнение вариантов исполнения коробки отбора мощности.
Относительное изменение параметра %
Число деталей в изделии %
В конструкцию и технологию изготовления коробки отбора мощности были внесены изменения повлиявшие на стоимость её изготовления.
В частности сварной корпус был заменён на литой корпус новой конструкции что значительно уменьшило цену его изготовления. Также в результате применения литого корпуса (корпус теперь разъёмный ранее процесс сборки был усложнен небольшим окном в корпусе) упростился процесс сборки.
Были применены бронзовые втулки в местах трения промежуточной оси о корпус что повысило ремонтопригоность. Изменение конструкции промежуточной оси упростило её изготовление. Изменение конструкции выходного вала позволило снизить расход металла на его изготовление. Применение более прогрессивного техпроцесса повлияло на стоимость его изготовления.
Изменение механизма включения повысило надежность его работы однако за счет некоторого удорожания его стоимости. Изменение способа крепления подшипников на валу - замена колец (соответственно и исчезают операции по обработке канавок под них) на более надёжное крепление упорами крышки. А также то что большинство стандартных крепёжных деталей стали одного типа (болты М8) позволило снизить время сборки коробки отбора мощности.
Таблица 3.10.doc
Функционально-стоимостная модель базового варианта.
Функционально-стоимостная модель проектируемого варианта.
БЖД1.doc
Анализ шума и вибрации автогудронатора пути их снижения
Для снижения шума автогудронатора машины нужно рассмотреть прежде всего использование виброизоляции и вибропоглощения звукоизоляции и звукопоглощения. Это первая совокупность методов и средств разумное использование которых приводит к снижению шума автомобиля. Другая совокупность методов и средств которую необходимо использовать с целью снижения шума базируется на организации рабочих процессов автомобиля и разработке конструкции обеспечивающих минимальное акустическое излучение и основанных на соответствующих критериях минимизации.
Зубчатые передачи автомобиля являются основной частью динамической колебательной системы всей силовой передачи автомобиля (двигатель — ведущие колеса). Они могут быть источниками акустического излучения вследствие ряда причин в том числе от пересопряжения зубьев изгибных и крутильных колебаний валов и т. д. Для снижения шума данных агрегатов наиболее целесообразным хотя и трудным путем является воздействие на конструкцию например ужесточение валов и их тщательное центрирование улучшение качества зацепления зубчатых колес. В то же время наличие широкополосного возбуждения действующего на редуктор осложняет проблему борьбы с шумом от зубчатых зацеплений.
Шум от редуктора излучается наружными поверхностями картера поэтому прежде всего рассматривают колебательное движение этих поверхностей.
Причинами шума зубчатых передач являются усилия развивающиеся в точках контакта зубьев и подшипниках. При ударе зубьев от нагрузки возникающая вибрация передается через шестерню вал и подшипник на картер а затем излучается в виде звука. При этом 90% слышимых звуковых волн проходит по путям передачи а 10% излучается в точке зацепления при некотором демпфировании картером. На шум зубчатых колес влияют в основном передаваемый крутящий момент и частота вращения. Уровни шума тихой и шумной коробок передач измеренные на третьей передаче в кузове легкового автомобиля различаются на 4 – 5 дБА; эта разность возрастает на 5 дБ при удвоении частоты вращения. Если крутящий момент увеличивается то уровень шума возрастает на 3 дБ. Спиральные зубчатые колеса снижают шум на 20 дБ при углах 0—25° и свыше 35°.
Уменьшение шума на 5 дБ зубчатых передач автогудронатора вследствие увеличения коэффициента контакта профиля с 119 до 207 вследствие меньшего возбуждения вибрации более тонкого и высокого зуба с частотой его зацепления. Меньший шум (на 4 дБ) обусловливают также небольшие значения угла нормального давления и нормальный подшипник установленный вместо подшипника с увеличенным в 10 раз зазором. Шум зубчатых колес снижается на 7 дБ при коррекции боковой части зуба на величину до 003 мм и на 3—4 дБ после притирки хонингования и ударного наклепа поверхности зуба. Частоты собственных колебаний картера зубчатой передачи машины равны 400 800 1600 и 3200 Гц и при его колебании с амплитудой 00005 мм уровень излучаемого шума L = 90 дБ. Уровень шума чугунного картера со стенками толщиной 15 мм и подшипниками скольжения на 15 дБ меньше чем картера с толщиной стенки 5 мм и шарикоподшипниками.
Важнейшим условием улучшения виброакустических характеристик подшипников является уменьшение волнистости и огранности тел качения и желобов колец и отклонений размеров тел качения. В последние годы освоен промышленный выпуск малошумных подшипников с индексом «Ш» или изготовленных по шестому классу точности которые отличаются значительно меньшей волнистостью и огранностью рабочих поверхностей и нормируемым и контролируемым уровнем вибрации. Виброакустические характеристики машины могут быть значительно улучшены при предварительном осевом нагружении наружного кольца. Также важно выбрать соответствующую посадку наружного кольца подшипника в гнездо узла следить за соосностью гнезд в корпусе машины выбрать нужный сорт смазки и т.д.
Сертификаты машины по шуму и вибрации
Нормативный документ
Сертификат соответствия
Правила ЕЭК ООН №51 (-01)
Внешний шум (в транспортном режиме)
Орган по сертификации автомототехники – механических транспортных средств запасных частей и принадлежностей (ОС АНО – ЦССАМТ) Российская Федерация
Сертификат соответствия
№ РОСС RU. MT25. B02825 от 28.04.2001 года.
Внешний шум (в технологическом режиме)
Центр сертификации продукции строительного дорожного и коммунального машиностроения Фонда «СКМ» (ЦС «СКМ») Российская Федерация
№ РОСС RU. MT15. B01884 от 14.11.2003 года.
Внутренний шум (в транспортном режиме)
№ РОСС RU. MT25. B05002 от 21.07.2003 года.
Шум на рабочем месте оператора (в технологическом режиме)
Содержание вредных веществ в воздушном объеме кабины
№ РОСС RU. MT25. B05000 от 21.07.2003 года.
Вибрационные характеристики
Согласно Правилам ЕЭК ООН №51 (серия 01) допустимый уровень внешнего шума в транспортном режиме для машины категории М2 не должен превышать 80 дБ.
Согласно ГОСТ Р 51616 – 2000 допустимый шум на месте водителя должен быть не более 78 дБ.
Согласно ГОСТ Р 50631 – 93 внешний шум в технологическом режиме не должен превышать 85 дБ и внутренний шум – не более 86 дБ.
По внешним и внутренним шумовым и вибрационным характеристикам машина КО-318 удовлетворяет требованиям ГОСТа.
Пути повышения экологических качеств автогудронатора
Сертификат соответствия токсичности выхлопных газов стандартам
Правила ЕЭК ООН №49 (-02А)
Выделение загрязняющих газообразных веществ с отработавшими газами двигателей с воспламе- нением от сжатия
№ РОСС RU. MT25. B04409 от 05.12.2002 года.
К основным загрязнителям атмосферы относятся: сернистый газ взвешенные частицы СО СО2 NОx фотоокислители и реакционноспособные углеводороды свинец ртуть кадмий хлорированные органические соединения нефтепродукты микротоксины аммиак фреоны металлы радиоактивные вещества и т. д.
В ОГ дизелей доминируют такие токсичные вещества как оксиды азота и сажа; кроме того также необходимо обращать внимание на дымность и запах. Одним из средств уменьшения выделения оксидов азота с ОГ дизелей является применение рециркуляции ОГ.
Дымность ОГ двигателей может быть уменьшена применением специальных устройств корректирующих работу циркулятора. Эти устройства часто выполняют в виде амортизатора который ограничивает скорость перемещения рейки топливного насоса относительно положения соответствующего максимальной подаче.
Применение нейтрализаторов. В настоящее время наибольшее распространение получили каталитические нейтрализаторы в которых в качестве катализатора используются редкоземельные элементы (платина палладий радий) позволяющие существенно снизить порог энергии при котором начинаются окислительно-восстановительные реакции. В мировой практике широкое применение находят нейтрализаторы тройного действия (СОСНNOх). Максимальная эффективность таких нейтрализаторов достигается при их работе в контуре автоматической системы управления подачей топлива содержащей помимо непосредственно нейтрализатора кислородный датчик и электронный блок управления.
Нейтрализаторами называют аппараты в которых токсичные компоненты отработавших газов ОГ превращаются в нетоксичные т. е. нейтрализуются. Нейтрализаторы устанавливают в выпускной системе вместо глушителей. К ним относят нагнетатели пульсаторы эжекторы фильтры для задержания аэрозольных частиц которые предназначены в основном для окисления (дожигания) продуктов неполного сгорания топлива до С02 и Н20. При наличии в топливе серы часть сернистого ангидрида образовавшегося при горении превращается в серный (SО2 в S03) и далее в серную кислоту Н2SО4. В жидкостных аппаратах альдегиды и МОХ связываются между собой. Нейтрализаторы способствуют снижению токсичности двигателей особенно карбюраторных. Однако применение их для обезвреживания ОГ образующихся при горении смесей стехиометрического состава или смесей с недостатком кислорода предусматривает принудительную подачу в агрегаты дополнительных количеств воздуха что требует дополнительного расхода энергии ухудшает мощностные и экономические показатели двигателя. При окислении топлива в нейтрализаторах образуется дополнительное количество NOХ а также паров серной кислоты.
Эффективность очистки нейтрализатором ОГ по всем компонентам составляет около 90% при температуре 750 °С.
Сажа. С увеличением нагрузки на двигатель в цилиндр поступает большее количество топлива что способствует неравномерности макрораспределения его по объему камеры сгорания: часть топлива сгорает сразу же после испарения с капель и повышает степень концентрации сажи в отработанных газах (ОГ).
Частота вращения коленчатого вала на концентрацию сажи в выпуске оказывает неоднозначное влияние. С одной стороны увеличение числа оборотов приводит к интенсификации смесеобразования а следовательно к сокращению числа зон с дефицитом кислорода и снижает концентрацию сажи с другой — уменьшение времени процесса горения образовавшихся частиц твердого углерода неизбежно увеличивает содержание сажи в ОГ. Обусловливаемый этими закономерностями минимум является индивидуальным для каждой конструкции дизеля и зависит прежде всего от организации процесса перемешивания заряда в стадии распространения по нему горячего пламени.
Окислы азота. Концентрации окислов азота в ОГ лишь в незначительной степени зависят о частоты вращения коленчатого вала и повышаются с увеличением нагрузки на двигатель. Максимальный выброс N0 в пересчете на N2О5 не превышает 34 гм3.
Окись углерода. При Ре =01 МПа концентрация СО равна 005% по объему. С увеличением нагрузки до Ре=03 МПа выброс СО снижается из-за уменьшения количества альдегидов являющихся исходными компонентами реакций образования СО в стадии распространения голубого пламени. Дальнейшее изменение концентрации альдегидов при Ре=03 МПа невелик. Однако на образование СО начинают оказывать воздействие другие факторы а именно образование в цилиндре сажи окисление которой до СО2 идет через образование СО образующейся в процессе диффузионного горения последних капель топлива. Кроме того увеличивается вероятность диссоциации двуокиси углерода.
Рост Ре ведет за собой увеличение выброса СО особенно заметного при Ре>05—055 МПа.Максимальный выброс окиси углерода Ссо=03% соответствует Реmax.
Альдегиды. Образование альдегидов происходит в холодно-пламенной стадии процесса воспламенения топлива. Максимум их токсичных выбросов приходится на малые нагрузки и равен 0015 гм3 при ре=01МПа. С увеличением ре до
МПа концентрация альдегидов в ОГ резко уменьшается затем по закону близкому к линейному снижается до 0003 гм3 при полной нагрузке.
Углеводороды. По мере увеличения ре от ре = 01 МПа до реmax концентрации углеводородов увеличиваются вдвое достигая качения ССН = 01 гм3 что вполне согласуется с представлением о реакционно-кинетической природе их образования.
Удельная токсичность выпуска дизелями окислов NОХ и СО СН альдегидов и сажи находится в зависимости от изменения нагрузки. Основным компонентом определяющим токсичность ОГ является группа N0х особенно при средних нагрузках. При малых ре значимость NОх снижается за счет альдегидов при больших — за счет СО.Доля углеводородов в общей токсичности не превышает десятых долей процента
Использование автогудронатора в зонах радиационного и химического заражения.
В результате крупных производственных аварий катастроф на химически и радиационно опасных объектах при перевозке сильнодействующих ядовитых веществ люди а также окружающая среда в том числе здания и сооружения транспортные средства и техника вода продовольствие пищевое сырье могут поражены СДЯВ и РВ. Население сел и городов также может получать заражения при массовых инфекционных заболеваниях людей и животных.
Для того чтобы исключить вредное воздействие на человека и животных радиоактивных отравляющих сильнодействующих ядовитых веществ и болезнетворных микробов обеспечить нормальную жизнедеятельность необходимо выполнить комплекс работ по обеззараживанию территории помещений техники приборов оборудования мебели одежды обуви открытых частей тела. При чем делать это надо только в средствах индивидуальной защиты (противогазах респираторах резиновых перчатках сапогах переднике или комбинезоне) при строгом соблюдении мер безопасности.
Обеззараживание предусматривает прежде всего механическое удаление а также нейтрализацию химическим физическим способами вредного вещества и уничтожение болезнетворных микробов угрожающих здоровью и даже жизни людей.
Обеззараживание – это широкое понятие. Оно включает выполнение таких работ как дезактивацию дегазацию дезинфекцию зараженных поверхностей а также проведение санитарной обработки людей.
Дезактивация — это удаление радиоактивных веществ с зараженных объектов которое исключает поражение людей и обеспечивает их безопасность.
Объектами дезактивации могут быть жилые и производственные здания участки местности оборудование транспорт и техника одежда предметы домашнего обихода продукты питания и вода.
Конечная цель дезактивации — обеспечить безопасность людей исключить или уменьшить вредное воздействие ионизирующего излучения на организм человека.
Характерной особенностью дезактивационных мероприятий является строго дифференцированный подход к определению объектов которые следует дезактивировать. Такой подход позволяет из большого количества объектов выделить наиболее важные для жизнедеятельности людей и при ограниченных силах и средствах провести запланированные работы.
Дезактивация неразрывно связана с источниками и условиями радиоактивных загрязнений которые определяются механизмом образования природой радионуклидным составом и другими особенностями этих загрязнений. По существу она является процессом обратным процессу радиоактивного загрязнения.
Радиоактивные вещества загрязняющие местность могут находиться в различном агрегатном состоянии – твердом жидком и газообразном. Попадая на объекты они закрепляются на их поверхностях. В зависимости от условий различают поверхностное и глубинное загрязнение по отношению к воздушной и жидкой среде – объемное.
В условиях поверхностного загрязнения радионуклиды находятся лишь на наружной части объектов. В зависимости от агрегатного состояния вещества это могут быть загрязнения поверхности радиоактивной жидкостью твердыми частицами структурированными системами например комками грязи вязкими растворами. Часть радионуклидов находящихся в воздухе или в воде в виде молекул или ионов могут также закрепляться на поверхности(этот процесс называется адсорбцией).
Во всех случаях дезактивация заключается в удалении радиоактивных загрязнений с внешней стороны поверхности объекта.
В случае глубинного загрязнения радионуклиды проникают вглубь материала. Поэтому процесс дезактивации не ограничивается только удалением радиоактивных веществ с внешней стороны поверхности их нужно извлечь еще из глубины.
Радионуклиды в виде молекул или ионов способны самопроизвольно проникать вглубь материала (лакокрасочные покрытия металл полимерные и другие материалы). Этот процесс называется диффузией. Если загрязненный объект имеет пористую структуру например кирпич некоторые сорта бетона грунт песок сыпучие строительные материалы то радионуклиды растворенные в жидкости способны проникать на значительную глубину через пористое пространство.
Глубина проникновения зависит от свойств и сортамента этих материалов состояния радионуклидов условий загрязнения (например времени контакта с поверхностью) и колеблется в довольно широких пределах. Ориентировочно можно считать что глубина проникновения составляет: для некоторых металлов – до 1 мм лакокрасочных покрытий бетона и кирпича – до 55 мм грунта – до 7 см.
Существующие способы дезактивации можно классифицировать по различным признакам которые с одной стороны определяются особенностями радиоактивного загрязнения а с другой – условиями проведения самой дезактивации выбор которой диктуется спецификой радиоактивного загрязнения различных объектов.
В основу классификации основных способов обеззараживания положены агрегатное состояние дезактивирующей среды и особенности проведения собственно дезактивации. В зависимости от агрегатного состояния дезактивирующей среды все способы можно разделить на безжидкостные (струей газавоздуха пылеотсасыванием снятием загрязненного слоя изоляцией загрязненной поверхности) жидкостные (струей воды под давлением дезактивирующими растворами пеной стиркой и экстракцией) и комбинированные (паром при помощи дезактивирующих пленок использованием сорбентов).
Повысить эффективность удаления радиоактивных частиц при проведении дезактивационных работ позволяют дезактивирующие вещества и растворы. К ним относят поверхностно-активные моющие вещества отходы промышленных предприятий органические растворители сорбенты ионообменные материалы.
Чтобы повысить моющие способности воды в нее добавляют поверхностно-активные вещества (ПАВ). Добавляют их примерно 01 – 05%. ПАВ способствуют отрыву и выведению в дезактивирующий раствор радиоактивных частиц.
К поверхностно-активным веществам обладающим моющим действием относятся обычное мыло гардиноль сульфонол препараты ОП-7 ОП-10 и др.
Автогудронатор представляет собой машину предназначенную для розлива жидкости. Это дает возможность проводить механизированную дезактивацию асфальтобетонных покрытий дорог аэродромов территорий цехов предприятий Автогудронатор должен быть перед началом дезактивации оборудован защитным экраном или же водитель должен быть в радиозащитном комбинезоне. Емкость для орошения заполняется водным раствором дезактивирующего вещества. Во время уборки раствор проникает в щели покрытия что позволяет проводить глубокую и быструю дезактивацию дорог.
Надо помнить что дезактивация дорог и проездов не устраняет полностью опасности облучения человека но все же значительно снижает ее.
Дегазация — это уничтожение (нейтрализация) сильнодействующих ядовитых и отравляющих веществ или их удаление с поверхности таким образом чтобы зараженность снизилась до допустимой нормы или исчезла полностью.
Известно немало способов дегазации но чаще всего прибегают к механическому физическому или химическому.
Механический – удаление отравляющих или СДЯВ с какой-то поверхности территории техники транспорта и других отдельных предметов. Обычно зараженный слой грунта срезают и вывозят в специально отведенные места для захоронения или засыпают песком гравием щебнем.
При физическом способе верхний слой прожигают паяльной лампой или специальными огнеобразующими приспособлениями. Из растворителей используют дихлорэтан четыреххлористый углерод бензин керосин спирт.
Наибольшее распространение нашел химический способ дегазации основанный на применении веществ окисляющего и хлорирующего действия – хлорной извести двухосновной соли гипохлорита кальция (ДС-ГК) дветретиосновной соли гипохлорита кальция (ДТС-ГК) хлористого сульфурила (ХС) монохлорамина Б (ДТ-1) дихлорамина Б (ДТ-2) а из веществ основного характера – едкого натра аммиака гашеной извести сернистого натрия углекислого натрия двууглекислого аммония.
Дегазация территории – трудоемкий процесс поэтому как правило первоначально обеззараживают не всю площадь предприятия учреждения животноводческой фермы а только те места где возможно передвижение людей животных и техники. Остальные участки обносят знаками ограждения.
Если грунт рыхлый дегазацию дорог и проходов производят следующим способом: зараженный участок засыпают порошком хлорной извести из расчета 1 кг на квадратный метр и перепахивают его на глубину 3 – 4 см а затем повторно покрывают хлорной известью.
Зараженные участки на твердом грунте асфальтовом бетонном покрытии обрабатывают хлорной известью или ДТС-ГК (05 кг на квадратный метр) а затем через 20 минут поливают водой (доза – 1 л на квадратный метр). При ветреной погоде делают наоборот.
Водитель должен быть в защитном комбинезоне. Емкость для орошения заполняется любым раствором дегазационного вещества: бензин керосин раствор гашеной извести. Во время уборки раствор проникает в щели покрытия что позволяет проводить глубокую и быструю дегазацию дорог.
Список использованной литературы.doc
“Тяговый расчёт автомобиля. “ методичёские указания к выполнению курсового проекта и курсовой работы для студентов специальностей 150100 150200 230100 240400. Курган 1999 г.
Методичёские указания к выполнению курсовой работы по теме “кинематический расчёт привода” для студентов специальностей 15.01; 12.02; 21.03; 12.05; 07.01; 07.11. Курган 1989 г.
Д. Н. Решетов “Детали машин” Москва “Машиностроение” 1989 г.
Методичёские указания к выполнению курсовой работы по теме “Расчёт цилиндрических передач” для студентов специальностей 1501 0504 0513 0534 1609. Курган 1987 г.
Методичёские указания к выполнению курсовой работы по теме “Расчёт валов и подбор подшипников” для студентов специальностей 12.01 02.02 12.06 15.02 15.05. Курган 1989 г.
Б.М. Тверсков “Трансмиссии автомобилей” Справочный материал для выполнения курсовых и дипломных проектов студентами специальности 150100 “Автомобиле- и тракторостроение”. Курган 2002 г.
“Автогудронатор ДС – 142Б” Техническое описание и инструкция по эксплуатации автогудронатора ДС – 142Б ДС – 142Б.00.00.000 ТО
Заключение.doc
В частности сварной корпус был заменён на литой корпус новой конструкции что значительно упростило его производство. Также в результате применения литого корпуса (корпус теперь разъёмный ранее процесс сборки был усложнен небольшим окном в корпусе) упростился процесс сборки.
Были применены бронзовые втулки в местах трения промежуточной оси о корпус что повысило ремонтопригоность. Изменение конструкции промежуточной оси упростило её изготовление. Изменение конструкции выходного вала позволило снизить расход металла на его изготовление. Применение более прогрессивного техпроцесса повлияло на стоимость его изготовления.
Изменение механизма включения повысило надежность его работы однако за счет некоторого удорожания его стоимости. Изменение способа крепления подшипников на валу - замена колец (соответственно и исчезают операции по обработке канавок под них) на более надёжное крепление упорами крышки. А также то что большинство стандартных крепёжных деталей стали одного типа (болты М8) позволило снизить время сборки коробки отбора мощности.
титул.doc
РОССИЙСКОЙ ФЕДЕРАЦИИ
КУРГАНСКИЙ ГОСУДАРСТВЕННЫЙ УНИВЕРСИТЕТ
Коробка передач и левая коробка отбора мощности автогудронатора
Д И П Л О М Н Ы Й П Р О Е К Т
РАСЧЕТНО-ПОЯСНИТЕЛЬНАЯ ЗАПИСКА
Студент группы ТС -
Специальность: "Автомобиле- и тракторостроение" (150100)
Доцент канд. техн. наук
Технологическая часть – ст. преп.
Экономическая часть – доц.к.э.н.
БЖД и ЗОС –доц. канд. техн. наук
Заведующий кафедрой
Автомобили" профессор
Допол.doc
Проверочный расчёт производится в форме проверки коэффициента запаса прочности. ось рассматривают как тело имеющее объёмное неоднородное напряжённое состояние при переменных напряжениях.
Силы на валы передаются через насаженные на них детали. При расчётах принимают что насаженные на вал детали передают силы и моменты валу на середине своей ширины.
При переходе от конструкции к расчётной схеме производят также схематизацию опор и формы вала. Форму вала принимают в виде невесомого бруса постоянного сечения.
Для нахождения реакций Ra составим уравнение моментов вокруг точки В:
Для нахождения Rb составим уравнение равновесия сил вдоль оси Y
Для установления опасных сечений построим эпюру моментов вокруг оси Х (см. рис. )
Опасным является сечение вдоль которого действует сила Fr.
Для этого сечения определим запас сопротивления усталости и сравним их с допускаемыми.
где а – амплитуда напряжений цикла.
Напряжения в опасных сечениях определяют по формуле:
где М – изгибающий момент в рассчитываемом сечении вала;
W – осевой момент сопротивления сечения. который определяется по формуле:
К – эффективный коэффициент концентрации напряжений при изгибе который назначается в зависимости от вида концентратора и его характеристик.
-1 – предел выносливости гладких образцов при симметричном цикле изгиба.
Кd – коэффициент влияния абсолютных размеров поперечного сечения.
КF – коэффициент влияния шероховатости.
КV – коэффициент влияния поверхностного упрочнения.
расчёт шестерён промежуточного вала КП.doc
Основными видами повреждений зубьев являются выкрашивание и смятие активной поверхности а также поломки. Повреждения могут быть результатом усталости материала при длительном действии циклически изменяющихся напряжений или однократного действия максимальной (пиковой) динамической нагрузки. Для проверки достаточно ли сопротивление зубьев усталости выполняют расчеты на контактную усталость активных поверхностей и усталость при изгибе а достаточно ли сопротивление зубьев однократным пиковым нагрузкам — соответствующие расчеты на прочность. Расчеты на усталость выполняют по расчетному моменту Мр используя при этом и такие параметры расчетного нагрузочного режима как расчетная частота вращения nр. Расчеты на прочность выполняют по максимальному динамическому моменту Мjmax.
Расчёт шестерни 5 привода промежуточного вала.
Методику расчёта возьмем из [4].
Расчет на контактную усталость.
Первый этап. Определяют параметр расчетного контактного напряжения (МПа)
и предельного контактного напряжения при базе испытаний NНО циклов
где — параметр предела контактной выносливости при базе испытаний NНО.
Если получено выполняют второй и третий этапы расчета; если расчет заканчивают.
Расчетная окружная сила (Н) для цилиндрического зубчатого колеса имеющего одно зацепление
где Мр — расчетный момент на валу рассматриваемого зубчатого колеса Н-м. Его определяют из расчетного момента на первичном валу коробки передач с учетом передаточного числа КПД и наличия узлов деления момента;d— начальный диаметр зубчатого колеса мм.
Единичноеконтактное напряжение (коэффициент контактного напряжения) ZH для цилиндрической передачи определяют по формуле:
при этом для прямозубой передачи cos2=1 αn=α.
Коэффициент Z для цилиндрических и конических передач с прямыми зубьями принимают равными единице.
Коэффициент находят из соотношения () где - учитывает повышение интенсивности нагрузки на наклонных контактных линиях у околополюсных участков вследствие меньшей суммарной деформации зубьев в средней фазе зацепления по сравнению с суммарной деформацией в начальной и конечной фазах; — учитывает неточность распределения нагрузки между зубьями. Для передач с прямыми зубьями принимают = =1.
Коэффициент определяют по формуле:
где — коэффициент учитывающий неравномерность распределения нагрузки по ширине венца в начальный период работы передачи;
— коэффициент учитывающие влияние приработки зубьев в процессе эксплуатации.
Коэффициент приближенно определяют по графикам (рис .[ ])
Предварительно следует рассчитать (1.3.12)
Значения коэффициента приведены в табл. [ ]
Коэффициент и при окружной скорости не более
мс принимают равным единице. В общем случае
() и () где и учитывают соответственно динамическую нагрузку обусловленную погрешностями зубчатых колёс и динамическую нагрузку от воздействия звеньев внешних по отношению к зубчатой передаче. Приближённые значения и можно определить по графикам рис. 327 [ ]
Коэффициент определяют с учетом свойств применяемого смазочного материала и характера работы зубчатого колеса в передаче. При использовании смазочных материалов рекомендуемых в настоящее время инструкциями по техническому обслуживанию узлов трансмиссии следует принимать .
Для зубчатых колес имеющих d700 мм принимают .
Пределы выносливости Hlimb сHlimb устанавливают при стендовых испытаниях зубчатых колес с заданными конкретными размерами способом термообработки и чистотой поверхностей зубьев. Для зубчатых колес с d 300 мм и модулем (т тn тпт) 3 4 мм значения пределов выносливости соответствующие вероятности неразрушения 90% у казаны в табл. 3.5[]. Значения предела выносливости при изгибе зубьев сHlimb относятся к знакопеременному симметричному циклу при базе испытаний NFO. Между пределом контактной выносливости (МПа) и его параметром (МПа) имеется следующая зависимость:
Значения коэффициента ZR приведены в табл. 3.6[ ].
ПН 09ПНРО. Второй и третий этапы расчёта не требуются.
Расчет зубьев на усталость при изгибе
Первый этап. Определяют расчетное напряжение изгиба (МПа)
и предельное напряжение изгиба при базе испытаний NF0 циклов
где – предел выносливости при изгибе при базе испытаний NF0 и симметричном цикле перемены напряжения; YR и KFc – коэффициенты зависящие соответственно от способа обработки зубьев и характера цикла.
Если получено выполняют второй и третий этапы расчета. Если расчет заканчивают.
Единичное напряжение изгиба (коэффициент напряжения изгиба Yf) находят по номинальному значению коэффициента Y0F для зубчатых колес внешнего зацепления по графику (рис. 323[ ])
Расчетное значение коэффициента напряжения изгиба
где ru rα rρ и r — коэффициенты учитывающие параметры парного зубчатого колеса угол профиля радиус кривизны переходной кривой профиля зуба ρf принятое перераспределение толщин сопряженных зубьев.
Для шестерни Цилиндрической передачи внешнего зацепления
где X — коэффициент суммы смещений (х1 + х2); Z — -эквивалентное число зубьев; Zф — число зубьев условного парного колеса передачи для которой рассчитаны точки на графике (см.рис. );
Для зубчатых колес исходный контур которых удовлетворяет ГОСТ 13755–81 (α = 20° r*I = 04) принимают rα = rρ = 1.
В цилиндрических передачах r = 1.
Коэффициент Y для цилиндрических и конических передач с прямыми зубьями принимают равными единице.
Коэффициент KFα принимают также в зависимости от степени точности передачи по нормам плавности: при степени точности 6
Коэффициент приближенно определяют по графикам (рис.3.253.26[ ]) Предварительно следует рассчитать (1.3.20).
Значения коэффициента приведены в табл. 3.2[ ]
КF = 095 – для ведомого зубчатого колеса передачи внешнего зацепления.
Коэффициент КFX определяют по табл. 3.4 [ ] в зависимости от модуля и диаметра зубчатого колеса.
Пределы выносливости Hlimb сHlimb устанавливают при стендовых испытаниях зубчатых колес с заданными конкретными размерами способом термообработки и чистотой поверхностей зубьев. Для зубчатых колес с d 300 мм и модулем (т тn тпт) 3 4 мм значения пределов выносливости соответствующие вероятности неразрушения 90% у казаны в табл. 3.5[ ]. Значения предела выносливости при изгибе зубьев сHlimb относятся к знакопеременному симметричному циклу при базе испытаний NFO.
Значение YR для зубчатых колес с неотшлифованной переходной поверхностью без грубых следов обработки не подвергавшихся упрочняющей обработке дробью принимается равным единице.
Коэффициент KFC можно определить в зависимости от характера нагружения зубчатого колеса следующим образом. При явно выраженном знакопеременном цикле нагружения (например промежуточных зубчатых колес в реверсивных однорядных передачах сателлитов с внешним и внутренним зацеплением в планетарных передачах) или периодическом реверсировании при одинаковой продолжительности работы в обоих направлениях KFC = 1. В случае одностороннего отнулевого цикла или цикла достаточно близкого к нему (например зубчатых колес низших передач в коробках передач) КFC = 13.
F 09FPO. Второй и третий этапы расчёта не требуются.
Расчет на прочность включает определение коэффициента максимальной динамической нагрузки максимальных напряжений и проверку прочности.
Коэффициент максимальной динамической нагрузки определяют как отношение максимального динамического момента МJmax к расчетному моменту Мр по которому выполняется расчет на усталость:
Моменты MJmax и Мр должны быть отнесены к одному и тому же валу и определены для одной и той же передачи. При расчете зубчатого колеса работающего под нагрузкой на нескольких передачах устанавливают передачу на которой значение MJmax наибольшее.
Двигатель работает в режиме максимальной мощности и следовательно KJM = 1.
Параметр максимального контактного напряжения на активных поверхностях зубьев
Максимальное контактное напряжение
Максимальное напряжение изгиба
В формуле (1.3.24) окружная сила Ft и все коэффициенты кроме KJM имеют те же числовые значения что и при расчете того же зубчатого колеса на усталость на той же передаче.
Условие достаточной контактной прочности активных поверхностей зубьев:
где HlimM – предельное контактное напряжение при котором возможно повреждение активной поверхности зуба (смятие продавливание растрескивание упрочненного слоя) от однократного действия динамической нагрузки. Условие достаточной прочности зуба при изгибе:
где FlimM – предельное напряжение изгиба при котором возможны появление остаточной деформации зуба или его хрупкая поломка от однократного действия динамической нагрузки.
1.1. Анализ конструкции.doc
1. Анализ конструкции и обоснование выбора конструктивной схемы коробки отбора мощности.
Коробка отбора мощности предназначена для отбора мощности от коробки передач для привода различных агрегатов. Она обеспечивает длительный отбор мощности (до 30 – 40% от мощности двигателя). В случае крепления коробки отбора мощности к коробке передач она крепится к фланцу люка коробки передач.
По конструкции коробки отбора мощности могут иметь от одного до трёх валов (в зависимости от агрегата куда подключается коробка наличием передач в самой коробке отбора мощности).
Также имеются различия по способу включения коробок отбора мощности это может быть и принудительное включение с места водителя или автоматическое при использовании механизма для которого происходит отбор мощности.
В зависимости от перечисленных особенностей конструкции коробок отбора мощности зависят и их эксплуатационные качества такие как процент отбираемой мощности от агрегата надёжность включения коробки и невозможность самопроизвольного выключения долговечность и надёжность в течении всего срока службы.
Наиболее предпочтительными являются коробки отбора мощности с наименьшим числом агрегатов т.е. наиболее простой конструкцией автоматическим включением и выключением.
Коробка отбора мощности служит для привода гидронасоса. Отбор мощности производится с блока шестерён заднего хода через зубчатое зацепление.
Коробка отбора мощности состоит из корпуса в котором на подшипниках установлены валы механизм включения шестерни находящейся в постоянном зацеплении с шестерней привода промежуточного вала коробки передач автомобиля КамАЗ. При включении зубчатого зацепления мощность от первичного вала коробки передач передаётся через промежуточный вал коробки передач далее через шестерню находящуюся в постоянном зацеплении с шестерней
привода промежуточного вала коробки передач затем на шестерню на промежуточной оси и на выходной вал коробки отбора мощности.
Включение коробки отбора мощности осуществляется при помощи сжатого воздуха. При подаче воздуха в пневмокамеру воздух действует на поршень вызывая тем самым перемещение оси с посаженным на него зубчатым колесом. Колесо входит в зацепление с шестерней на выходном валу и с шестерней находящейся в постоянном зацеплении с шестерней привода промежуточного вала коробки передач.
При подаче давления воздуха с другого конца поршень возвращает ось в исходное положение – происходит отключение коробки отбора мощности.
1.3 Кинематический расчёт привода КОМ (2).DOC
Методику расчёта возьмем из [2].
Целью кинематического привода является определение мощности и момента на каждом валу привода и проверка возможности работы при заданных условиях.
Параметры насоса: насос регулируемый 313.3.56
Номинальная частота вращения – 1500 обмин
Номинальная потребляемая мощность – 29 кВт
Кинематическая схема привода приведена на рисунке 1.
Кинематическая схема коробки отбора мощности приведена на рисунке 2.
Расчёт частоты вращения валов и колёс коробки отбора мощности.
Число оборотов двигателя вычисляем исходя из номинальных оборотов насоса по формуле:
U - передаточное число коробки передач (КП)
Данные по числам зубьев коробки передач возьмём из [6]
- передаточные числа ступеней КОМ
U1 - передаточное число между шестерней 2 и колесом 1 коробки отбора мощности.
U2 - передаточное число между шестерней 4 и колесом 3 коробки отбора мощности.
U3 – передаточное число между коробкой передач и колесом 4 коробки отбора мощности.
Число оборотов шестерни 2 и 3 коробки отбора мощности вычисляется по формуле:
Число оборотов шестерни 4 коробки отбора мощности вычисляется по формуле:
Число оборотов промежуточного вала коробки передач
Расчёт мощностей на валах коробки отбора мощности.
Мощности на валах определяются с учётом потерь в элементах привода.
где NT – мощность на валу КОМ
Передачи прямозубые следовательно = 097
NТ1 – мощность на ведомом валу КОМ = номинальной мощности насоса.
NТ23 – мощность на передаваемая шестернями 2 и 3
NТ23 – мощность на передаваемая шестернёй 4
NT5 – мощность на промежуточном валу коробки передач
Расчёт моментов на валах коробки отбора мощности.
Для расчёта моментов на валах необходимо учитывать момент который отбирает коробка отбора мощности.
Моменты на i-ом валу привода определяются по формуле:
где Ni и ni – мощность в кВт и частота вращения в обмин i-го вала.
Где Т1 –момент на выходном валу КОМ Т23 – момент передаваемый шестернями 2 и 3 Т4 –момент передаваемый шестернёй 4 Т5 – момент на промежуточном валу КП.
Расчёт возможности работы коробки отбора мощности.
Необходимо найти запас мощности при работе КОМ. Для этого составим уравнение мощностного баланса:
где Ne.тр – требуемая мощность двигателя NКОМ – мощность необходимая для работы КОМ.
Мощность двигателя при 650 обмин составляет 33.7 кВт (данные берём из тягового расчета с внешней скоростной характеристики двигателя).
Запас мощности составляет:
1.4.Расчёт коробки отбора мощности.doc
Расчёт картера коробки отбора мощности.
Методику расчёта возьмем из [3].
Рекомендуемые толщины наружных стенок чугунных отливок выбирают в зависимости от приведённого габарита отливки N:
где L В Н – соответственно длина ширина и высота отливки.
Данные приведены в таблице 1.4.1.
Расчёт зубчатых колёс.
Методику расчёта возьмем из [4].
Проверочный расчёт на контактную выносливость.
Для полюса зацепления расчётное контактное напряжение определяется по формуле:
где КНα – коэффициент учитывающий распределение нагрузки между зубьями; для прямозубых передач КНα = 1; КН – коэффициент учитывающий расположение шестерни относительно опор; КНV – коэффициент динамической нагрузки возникающей в зацеплении.
Ведущая шестерня. (z4 см рис 1)
[Н] определяется по формуле:
ZR – коэффициент учитывающий шероховатость поверхности зубьев;
КHL – коэффициент долговечности определяемый по формуле:
где с – число зубчатых колёс находящихся в зацеплении с рассчитываемым; n – частота вращения рассчитываемого зубчатого колеса мин-1; t – продолжительность работы передачи под нагрузкой за расчётный срок службы ч.
SHlimb = HB ZR = 09 SH = 12 (см. [4])
Окружная сила Ft находится по формуле:
Для определения КНV необходимо знать степень точности шестерни и окружную скорость в мс.
Окружная скорость находится по формуле:
Для расчёта КН необходимо рассчитать bd (см. [4]):
Промежуточная шестерня. . (z3 см рис 1)
Расчёт ведомой шестерни проведём по аналогичной методике.
КНα = 1 КН = 1015 КНV = 13
Промежуточная шестерня. . (z2 см рис 1)
Ведомая вал - шестерня. (z1 см рис 1)
Проверочный расчёт зубьев на выносливость по напряжениям изгиба
Расчётное напряжение изгиба на переходной поверхности зуба шестерни определяется по формуле:
где КFα – коэффициент учитывающий распределение нагрузки между зубьями; для прямозубых передач КFα = 1; КF – коэффициент учитывающий неравномерность распределения нагрузки по ширине венца ориентировочно можно принять КF = КFV – коэффициент динамической нагрузки; YF – коэффициент формы зуба определяемый в зависимости от коэффициента смещения х и числа зубьев z прямозубого колеса; Y – коэффициент учитывающий повышение изгибной прочности косого зуба по сравнению с прямым; для прямозубых передач Y = 1. Все значения коэффициентов берутся из [4].
Ведущая шестерня (z4 см рис 1)
[F] определяется по формуле:
YR – коэффициент учитывающий шероховатость поверхности зубьев;
KFC – коэффициент учитывающий влияние двустороннего приложения нагрузки (реверсирования); КFC = 1 – односторонняя нагрузка;
КFL – коэффициент долговечности определяемый по формуле:
где с – число зубчатых колёс находящихся в зацеплении с рассчитываемым; n – частота вращения рассчитываемого зубчатого колеса мин-1; t – продолжительность работы передачи под нагрузкой за расчётный срок службы ч (см. [6]).
SFlimb = 850 HB YR = 11 SF = 2
Для определения КFV необходимо знать степень точности шестерни и окружную скорость в мс.
Промежуточная шестерня (z3 см рис 1)
Расчёт промежуточной шестерни проведём по аналогичной методике.
Промежуточная шестерня. (z2 см рис 1)
Ведомая шестерня (z1 см рис 1)
Проверочный расчёт валов.
Методику расчёта возьмем из [5]. Все необходимые коэффициенты берём из этой же методики.
Проверочный расчёт производится в форме проверки коэффициента запаса прочности. Вал рассматривают как тело имеющее объёмное неоднородное напряжённое состояние при переменных напряжениях.
Основными нагрузками на валы являются силы от передач.
Силы на валы передаются через насаженные на них детали. При расчётах принимают что насаженные на вал детали передают силы и моменты валу на середине своей ширины.
При переходе от конструкции к расчётной схеме производят также схематизацию опор и формы вала. Форму вала принимают в виде невесомого бруса постоянного сечения.
где tgα = 200 – угол профиля; – угол наклона зуба для прямозубой передачи = 00.
Для нахождения реакций Ra составим уравнение моментов вокруг точки В:
Для нахождения Rb составим уравнение равновесия сил вдоль оси Y
Для нахождения Rb составим уравнение равновесия сил вдоль оси X
Для установления опасных сечений построим эпюру моментов вокруг оси Х (см. рис.1)
Опасным является сечение вдоль которого действует сила Fr.
Для этого сечения определим запас сопротивления усталости и сравним их с допускаемыми.
Допускаемые напряжения определяются по зависимости:
где а – амплитуда напряжений цикла.
Напряжения в опасных сечениях определяют по формуле:
где М – изгибающий момент в рассчитываемом сечении вала;
W – осевой момент сопротивления сечения. который определяется по формуле:
К – эффективный коэффициент концентрации напряжений при изгибе который назначается в зависимости от вида концентратора и его характеристик.
-1 – предел выносливости гладких образцов при симметричном цикле изгиба.
Кd – коэффициент влияния абсолютных размеров поперечного сечения.
КF – коэффициент влияния шероховатости.
КV – коэффициент влияния поверхностного упрочнения.
Методику расчёта возьмем из [6]. Все необходимые коэффициенты берём из этой же методики.
Расчёт подшипников сводится к определению потребной долговечности (ресурса) L которые связаны с эквивалентной динамической нагрузкой Р следующей зависимостью:
где m = 3 – для шариковых подшипников.
С и Р измеряются в Н а L – в млн. оборотов.
Эквивалентная динамическая нагрузка Р для радиальных подшипников определяется по формуле:
где Fr и Fа – радиальная и осевая нагрузки действующие на подшипник;
V – коэффициент вращения зависящий от того какое колесо вращается (при вращении внутреннего колеса V = 1 наружного - V = 12);
К – коэффициент безопасности который учитывает характер нагрузки;
КТ – температурный коэффициент;
X Y – коэффициенты радиальной и осевой нагрузок.
Подшипник 204 С = 12700 Н
Зная ресурс работы подшипника в млн. оборотов можно определить его ресурс в часах по следующей зависимости:
где n – частота вращения вала в обмин.
Подшипник 210 С = 35100
1.2 Тяговый расчет.doc
Методику расчёта возьмем из [1].
Тяговый расчёт выполняется для выбора необходимых параметров для расчёта работы коробки отбора мощности.
Построение внешней скоростной характеристики двигателя.
Рассчитывают величины эффективной мощности Ne и крутящего момента Те в зависимости от частоты вращения двигателя nе при полном открытии дроссельной заслонки или полной подаче топлива по уравнениям:
Расчёт произведён с помощью Microsoft Excel. Данные расчёта приведены в таблице 2.2.
Зависимость Ne и Те от оборотов двигателя.
По данным таблицы 1.2. строится внешняя скоростная характеристика
Силовой баланс автомобиля.
По методу А.Е. Чудакова силовой баланс строят зная тяговую характеристику автомобиля и силы сопротивления дороги и воздуха.
Уравнение силового баланса имеет вид:
Тяговую силу на ведущих колёсах автомобиля определяют по выражению:
Величину силы тяги определяют на всех передачах.
Силу сопротивления дороги находят как:
где – коэффициент суммарного сопротивления дороги.
Для горизонтальной дороги = может быть определён по формуле:
где 0 – коэффициент сопротивления качению для сухого асфальтового покрытия при Vа = 10 – 15 кмч; Vа – скорость автомобиля кмч.
Сила сопротивления воздуха рассчитывается по формуле:
Скорость автомобиля на каждой передаче определяют по формуле:
Расчёт произведён с помощью Microsoft Excel. Данные расчёта приведены в таблицах 1.3 и 1.4.
Зависимость РТ и V от включённой передачи и оборотов двигателя.
Изменение сил сопротивления движению от скорости.
Пользуясь данными таблиц 1.3 и 1.4 строим график силового баланса.
Динамическая характеристика автомобиля.
Динамический Фактор определяют при полной нагрузке автомобиля по формуле:
Пользуясь рассчитанными значениями РТ и РВ считают динамический фактор и результаты заносят в таблицу 1.5. Расчёт произведён с помощью Microsoft Excel.
Зависимость динамического фактора от скорости.
Мощностной баланс автомобиля.
По аналогии с уравнением силового баланса уравнение мощностного баланса можно записать в следующем виде:
Решить это уравнение можно графически для чего построим график мощностного баланса. На этот график нанесём зависимости на всех передачах мощности двигателя (Nв) на высшей передаче мощности заданного дорожного сопротивления (Nд) и суммарной мощности дорожного и воздушного сопротивления (Nд + Nв) от скорости движения автомобиля.
Тяговая мощность определяется по уравнению:
и строится на каждой передаче в зависимости от скорости движения соответствующей частоте вращения для которой определялась мощность по скоростной характеристике.
Эффективная мощность двигателя (Nе) строится в зависимости от скорости только на высшей передаче.
Мощности дорожного сопротивления и сопротивления воздуха рассчитывают в зависимости от скорости автомобиля по уравнениям:
Расчёт произведён с помощью Microsoft Excel. Данные расчёта приведены в таблице 1.6 и 1.7. По ним строят график мощностного баланса.
Изменение мощности сопротивления от скорости.
Ускорение автомобиля
Расчёт ускорения автомобиля производится по горизонтальной дороге по уравнению:
где j – ускорение автомобиля;
– коэффициент сопротивления дороги соответствующий расчётной скорости движения автомобиля;
g – ускорение свободного падения мс2;
– коэффициент учёта вращающихся масс определяемый по уравнению:
Для грузовых автомобилей В = 004 – 005.
Расчёт произведён с помощью Microsoft Excel. Данные расчёта приведены в таблице 1.8. По ним строят график ускорения автомобиля.
Ускорение автомобиля.
Время и путь разгона автомобиля
Определение времени и пути разгона проведём по методу
Время разгона определяют зная ускорение и скорость автомобиля.
При ускоренном движении автомобиля ускорение равно:
Так как отсутствует аналитическая связь между ускорением j и скоростью Va то решение проводим графоаналитическим методом пользуясь графиком ускорения автомобиля. Кривую ускорений разобьём на ряд интервалов и предположим что в каждом интервале скоростей автомобиль разгоняется с постоянным средним ускорением (jср). Величину определим по формуле:
где j1J2 – ускорения соответственно в начале и конце интервала скорости (V1V2).
Для точности расчётов интервал скорости берут равным 2 – 3 кмч на первой передаче 10 – 15 кмч – на высшей передаче и 5 – 10 кмч – на промежуточных передачах.
Если взять интервал скоростей от V1 – V2 например то среднее ускорение на этом участке (jср) равно:
Следовательно время разгона в том же интервале изменения скорости определяется как:
Пользуясь полученным выражением определим время разгона и на всех других интервалах скоростей.
Общее время разгона составит:
используя данные таблицы 1.8 все расчётные величины вносим в таблицу 1.9.
Время разгона автомобиля.
По значениям Δt определённым для различных скоростей строим кривую времени разгона начиная её от значения Vm для скорости V3 – значение времени разгона (Δt1 + Δt2) и т. д. Время переключения передач (tпп) не учитываются.
Путь разгона S зависит от скорости автомобиля и его времени разгона:
Тогда путь разгона например в интервале скоростей равен:
Пользуясь полученным выражением рассчитывают путь разгона на всех выбранных интервалах начиная с Vmin. Для последующих скоростей расчёт пути разгона ведётся аналогично времени разгона.
Общий путь разгона от Vmin до Vn равен:
Кривую пути разгона от скорости автомобиля строят для тех же интервалов скорости что и кривую времени разгона.
Используя таблицу 1.9 заносят результаты вычислений в таблицу 1.10.
Путь разгона автомобиля.
Содержание.doc
1. Анализ конструкции и обоснование выбора конструктивной схемы коробки отбора мощности.
2. Тяговый расчёт автомобиля
3.Расчёт коробки передач
4.Расчёт коробки отбора мощности
Технологическая часть
Экономическая часть
Экологическая часть
Список использованной литературы
Введение.doc
Автогудронатор предназначен для эксплуатации при температурах окружающей среды от плюс 50С до плюс 400С.
Автогудронатор обеспечивает выполнение следующих операций:
наполнение и опорожнение цистерны;
передача битума в постороннюю ёмкость минуя цистерну;
розлив битума на подготовленную поверхность дорог или площадок;
подогрев битума в цистерне до рабочей температуры.
Коробка отбора мощности осуществляет отбор мощности для обеспечения работы системы распределения битума.