Проектирование элементов гибкой производственной системы механической обработки корпусных деталей



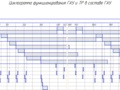
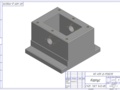
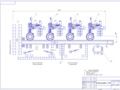
- Добавлен: 14.06.2022
- Размер: 3 MB
- Закачек: 1
Описание
основная часть ПЗ, состоящая из разделов
1) технологического. Раздел включает:
Чертеж детали (выполненный с применением 3D IT-технологий).
Технологический процесс неавтоматизированной обработки детали.
Анализ технологичности детали и возможности автоматизации ее обработки.
Полный маршрут обработки детали.
Операционную технологию обработки детали на неавтоматизированном и автоматизированном оборудовании. Выбор оборудования осуществить самостоятельно. Распределение операций между оборудованием. Временную диаграмму. Разработку компоновку ГПС и описание автоматизированного оборудования для обработки детали.
2) автоматического управления (или моделирования) системы. Раздел включает:
Алгоритм автоматизированной обработки детали.
Управляющую программу обработки детали.
3) конструкторского. Раздел включает:
Описание и обоснование устройства и принципа действия средства автоматизации.
Выбор и расчет АТСС ГПС для своего типа детали.
Выбор и расчет АСИО ГПС для своего типа детали.
Расчет надежности и производительности ГПС.
4) технико-экономического. Раздел включает:
Технико-экономическое обоснование выбранного варианта автоматизации техпроцесса. Оценку экономической эффективности ГПС.
список использованных источников (раздел без нумерации);
приложения.
Графический материал (чертежи схемы, алгоритмы в соответствии с вариантом задания).
Состав проекта
![]() |
![]() |
![]() |
![]() |
![]() ![]() ![]() |
![]() |
![]() |
![]() ![]() ![]() ![]() |
![]() ![]() ![]() ![]() |
![]() ![]() ![]() ![]() |
![]() |
![]() ![]() ![]() ![]() |
![]() |
![]() |
![]() ![]() |
![]() ![]() |
![]() |
![]() |
![]() ![]() |
![]() ![]() |
Дополнительная информация
записка.docx
учреждения высшего образования
«МОСКОВСКИЙ ПОЛИТЕХНИЧЕСКИЙ УНИВЕРСИТЕТ»
Кафедра автоматизации производства и информационных технологий
По дисциплине: «Автоматизация производственных процессов»
ТЕМА: Проектирование элементов гибкой производственной
системы механической обработки корпусных деталей (вариант №15)
НА КУРСОВОЙ ПРОЕКТ ПО ДИСЦИПЛИНЕ
«АВТОМАТИЗАЦИЯ ПРОИЗВОДСТВЕННЫХ ПРОЦЕССОВ»
Студенту группы КТО-__
(фамилия имя отчество)
ТЕМА ПРОЕКТА: Проектирование элементов гибкой производственной
(наименование детали и номер варианта задания)
Тип производства серийное
МЕТОДИЧЕСКИЕ УКАЗАНИЯ
Расчетно-пояснительная записка должна содержать:
титульный лист; задание на КП; реферат;
содержание; обозначения и сокращения;
введение (является разделом ПЗ но не нумеруется);
основная часть ПЗ состоящая из разделов
) технологического. Раздел включает:
Чертеж детали (выполненный с применением 3D IT-технологий).
Технологический процесс неавтоматизированной обработки детали.
Анализ технологичности детали и возможности автоматизации ее обработки.
Полный маршрут обработки детали.
Операционную технологию обработки детали на неавтоматизированном и автоматизированном оборудовании. Выбор оборудования осуществить самостоятельно. Распределение операций между оборудованием. Временную диаграмму. Разработку компоновку ГПС и описание автоматизированного оборудования для обработки детали.
) автоматического управления (или моделирования) системы. Раздел включает:
Алгоритм автоматизированной обработки детали.
Управляющую программу обработки детали.
Циклограмму работы ПР в составе РТК.
) конструкторского. Раздел включает:
Описание и обоснование устройства и принципа действия средства автоматизации.
Выбор и расчет АТСС ГПС для своего типа детали.
Выбор и расчет АСИО ГПС для своего типа детали.
Расчет надежности и производительности ГПС.
) технико-экономического. Раздел включает:
Технико-экономическое обоснование выбранного варианта автоматизации техпроцесса. Оценку экономической эффективности ГПС.
список использованных источников (раздел без нумерации);
Графический материал (чертежи схемы алгоритмы в соответствии с вариантом задания).
РЕКОМЕНДУЕМАЯ ЛИТЕРАТУРА
Автоматизация производственных процессов в машиностроении: Учеб. пособие Под ред. Н.М. Капустина. – М.: Машиностроение 2007.
Схиртладзе А.Г. Шамов Н.П. Тимирязев В.А. Мелетьев Г.А.. Автоматизация технологии сборки и механической обработки. Учебное пособие. – М.: Славянская школа 2003. – 519 с.
Вороненко И.П. Соломенцев Ю.М. Схиртладзе А.Г. Проектирование машиностроительного производства. – М.: МЦ МГТУ «СТАНКИН» Янус-К 2002. – 348с.
Волчкевич Л.И. Автоматизация производственных процессов: Учеб. пособие. – М.: Машиностроение 2005. - 380 с: ил.
Шишмарев В.Ю. Автоматизация производственных процессов в машиностроении. – М.: Изд. центр «Академия» 2007. -368с.
Трухин В.В. Проектирование гибких производственных систем: учеб. Пособие ГУ КузГТУ. – Кемерово 2005. – 107с.
Справочник технолога-машиностроителя Под ред. Р.К.Мещерякова А.Г.Косиловой. T.1. – М.: Машиностроение 1985.
Проектирование технологии автоматизированного машиностроения: Учеб.Под ред. Ю.М. Соломенцева. – М.: Высш.шк. 1999. – 415 с.:ил..
Рогов В.А. Чудаков А.Д. Средства автоматизации производственных систем машиностроения: Учеб. пособие для вузов. – М.: Высш. шк. 2005. – 399 с.:ил.
Хватов Б.Н. Гибкие производственные системы. Расчет и проектирование: учеб. пособие Б.Н. Хватов. – Тамбов: Изд-во Тамб.гос. техн. ун-та 2007. – 112 с.
Высоцкий В.Т. Лукашенко В.А. Проектирование вибрационных бункерных загрузочно-ориентирующих устройств. Учебное пособие. – Могилев: Изд-во «БРУ» 2009. – 26 с.
Проектирование автоматизированных участков и цехов: Учебник Под ред. Ю.М. Соломенцева. – М.: Высш.шк. 2003. – 272 с.:ил.
Промышленные роботы в машиностроении: Альбом схем и чертежей Под ред. Ю.М. Соломенцева. – М.:Машиностроение 1987.
Роботизированные технологические комплексы и ГПС в машиностроении: Альбом схем и чертежей Под ред. Ю.М. Соломенцева. – М.:Машиностроение 1989.
Технологически основы ГПС Под ред. Ю.М. Соломенцева. – М.: Высш. шк. 2000. -255с.
Романов П.С. Автоматизация производственных процессов в машиностроении. Часть 1. Производственные процессы и их автоматизация. Учебное пособие для направления подготовки 151900.62 Конструкторско-технологическое обеспечение машиностроительных производств. – Коломна: КИ (ф) МГМУ (МАМИ) 2014. – 118 с.
Романов П.С. Автоматизация производственных процессов в машиностроении. Часть 2. – Коломна: КИ (ф) МГОУ 2009. – 130 с.
Романов П.С. Автоматизация производственных процессов в машиностроении. Часть 3. – Коломна: КИ (ф) МГОУ 2009. – 152 с.
Романов П.С. Автоматизация производственных процессов в машиностроении. Учебное пособие (лабораторный практикум) 2- изд. – Коломна: КИ (ф) МГОУ 2013. – 178 с.
Тема курсового проекта – проектирование элементов гибкой производственной системы механической обработки корпусных деталей.
Пояснительная записка содержит 60 листов формата А4. Графическая часть выполнена на листах форматаи А2.
В курсовом проекте разработаны чертёж и 3D-модель корпусной детали составляющие графическую часть работы. Построения 3D-модели велись в системах автоматизированного проектирования «Компас».
Проведён технологический анализ детали на основе которого составлен технологический процесс обработки детали на неавтоматизированной и на автоматизированной производственных линиях. Рассмотрена возможность улучшения технологического процесса путём автоматизации (с применением станков с ЧПУ) и обоснована получаемая при этом технико-экономическая выгода.
В проекте так же приведены описание устройства и принципа действия используемых средств автоматизации – высокопроизводительный многоцелевой обрабатывающий центр фрезерный горизонтальный ИР-500 и ГАУ «Талка-500.3».
Построены диаграммы распределения времени между операциями.
Разработана программа обработки детали для операционного центра автоматизированной линии.
Раздел технологический10
2 Технологический процесс неавтоматизированной обработки детали типа корпус11
3 Анализ технологичности детали и возможность обработки детали в автоматизированном производстве17
4 Полный маршрут обработки детали19
5 Описание станка ИР500ПМФ422
6 Операционная технология обработки детали на обрабатывающему центре фрезерном горизонтальным с ЧПУ ИР500ПМФ4. Распределение операций между оборудованием23
7 Временная диаграмма26
8 Разработка компоновки28
9 Вывод по разделу31
Раздел автоматического управления системы32
1 Алгоритм автоматизированной обработки детали.32
2 Управляющая программа обработки детали32
3 Циклограмма работы РТК в соответствии с разработанным алгоритмом33
4 Разработка функционирования транспортной системы ТС-500 в составе ГАУ34
5 2.5. Вывод по разделу40
Конструкторский раздел41
1 Расчет надежности и производительности системы42
2 Расчет АТСС для транспортирования корпусных деталей44
3 Вывод по разделу49
Технико-экономический раздел51
1 Технико-экономическое обоснование выбранного варианта автоматизации техпроцесса.51
Список использованной литературы.55
АПП – автоматизация производственных процессов
БЗУ – бункерное загрузочное устройство
ПР – промышленный робот
РТК – роботизированная технологическая линия
СУ – система управления
ТП – технологический процесс
УП – управляющая программа
ЧПУ–числовое программное управление
ЦП - центральный процессор
ОЗУ - оперативное запоминающее устройство
ПЗУ - постоянное запоминающее устройство
УУ - устройство управления
ИЗВМ – интерфейс связи с ЭВМ верхнего ранга
УВВ – устройство вода вывода
БУП – блок управления приводом
БУСП – блок управления следящим приводом
БУМ – блок умножения
БЦА – блок цифровой автоматике
ПО – пульт оператора
АТСС - автоматизированная транспортно-складская система
ОЦ – операционный центр.
Современное машиностроительное производство характеризуется экспоненциальным развитием и все более широким использованием высокопроизводительных машин и прогрессивных технологий. При этом важно качественно в заданные сроки и с минимальными затратами изготовить продукцию. Для решения этих задач широко используются ЭВМ высокопроизводительные станков с ЧПУ промышленные роботы гибкие производственные системы позволяющие быстро и эффективно перестраивать технологические процессы на изготовление новых изделий.
К мероприятиям по разработке новых прогрессивных технологических процессов относится и автоматизация на ее основе проектируется высокопроизводительное технологическое оборудование осуществляющее рабочие и вспомогательные процессы без непосредственного участия человека.
Одна из основных закономерностей развития техники на современном этапе заключается в том что автоматизация проникает во все отрасли техники во все звенья производственного процесса вызывая в них качественные изменения раскрывая невиданные ранее возможности роста производительности труда повышение качества и увеличение выпуска продукции облегчение условий труда. Однако еще имеется ряд проблем от решения которых зависит ускорение развития средств автоматизации.
Темой данного проекта является разработка элементов гибкой производственной системы механической обработки корпусных деталей.
Поставленная задача решается путём модернизации стандартного комплекса станочного оборудования для обработки детали корпуса в автоматизированную систему.
Прилагается технико-экономическое обоснование получаемой при этом выгоды.
Разработка схем чертежей и 3D-модели в курсовом проекте было проведено при помощи САПР «Компас» что демонстрирует возможности компьютерного моделирования применительно к созданию автоматизированных систем. Вышеуказанная система значительно облегчают конструирование добавляет ему наглядности. Параметризация 3D-модели позволяет при необходимости быстро поменять размеры детали без нарушения её целостности и связанных с ней программ обработки на станках с ЧПУ.
Так же в оформлении работы использовался текстовый редактор «MicrosoftWord» а для вычислений и построения диаграмм - табличный процессор «MicrosoftExcel».
Раздел технологический
Наименование детали – корпус.
Корпусные детали — это базовые детали служащие для размещения в них сборочных единиц и отдельных деталей. Характерная особенность корпусов - наличие опорных достаточно протяженных и точных плоскостей и отверстий.
Материал – Серый чугун СЧ-25 ГОСТ1412-85.
Заготовка – отливка.
Масса заготовки –5664 кг масса детали –472 кг.
Рисунок 1.1 – Деталь корпус с применением 3D IT – технологий.
Годовой объём выпуска шт.: N = 2000.
Определение типа производства.
Определить тип производства можно по коэффициенту k.
где с - средний производственный такт;
tшс - среднее штучное время изготовления детали по всем
где Fдс - действительный фонд рабочего времени;
При k > 1 будет серийное производство (заданно условием КП).
2Технологический процесс неавтоматизированной обработки детали типа корпус
В курсовой работе приведены ТП неавтоматизированной и автоматизированной обработки детали разработанный при помощи системы КОМПАС.
Автоматизированный процесс включает в себя такие же операции как и неавтоматизированный но в другой последовательности. Основное отличие – увеличение производительности труда в автоматизированном процессе обработки заготовки за счёт автоматической смены инструмента в каждом операционном центре и автоматической транспортировки заготовки по автоматизированному производственному участку. При расчете времени на обработку детали для неавтоматизированного производственного участка не учитывалось время на транспортировку заготовки по участку а также время на отдых персонала.
Рисунок 1.2 - Алгоритм неавтоматизированной обработки детали Корпус
Технологический процесс неавтоматизированной обработки заготовки.
Наименование и содержание операции
Фрезеровать поверхность 1
Вертикально фрезерный станок 6Р13
Фреза торцевая Р6М5 ГОСТ 9304-69
Фрезеровать поверхность 234
станок продольно-фрезерный двухстоечный трехшпиндельный 6606
Фрезеровать поверхность 56
Сверлить отверстие 8
К40СФ4 станок координатно-расточный
Сверло перовое 45мм ВК8
Рассверлить отверстие 8
Сверло перовое 40мм ВК8
Сверлить 8 отверстие 7
Сверло спиральное 67 Р6М5 ГОСТ 12121-71
Нарезать резьбу 8 отв.7
Метчик с проходным хвостовиком Р18 М8-7H ГОСТ
Сверлить отверстия 6 отв. 10
Сверло спиральное 14 Р6М5 ГОСТ 12121-71
Нарезать резьбу 6 отв. 10
Метчик с проходным хвостовиком Р18 М16-7H ГОСТ
Контроль размеров детали и расположения отверстий
Плита2-2 600х600 10905-86
Плита 2-2 600х600 10905-86
Калибр-резьба М8х1 М12х15
3Анализ технологичности детали и возможность обработки детали в автоматизированном производстве
При разработке автоматизированных производств большое внимание уделяется технологичности детали. Оценка технологичности конструкции детали является важным этапом технологической подготовки производства. Конструкция детали является технологичной если при ее изготовлении и эксплуатации затраты материала времени и средств минимальны.
Деталь представляет собой корбчатое тело типа корпус с отверстиями фасками резьбой. Исходя из этого её поверхности следует обрабатывать фрезерованием и сверлением. Чтобы максимально приблизить форму заготовки к форме будущей детали и уменьшить расход материала используем литую заготовку.
Обрабатываемые плоские поверхности расположены под прямыми углами друг к другу прямолинейные. Все стороны имеют значительные размеры и прямолинейны - могут быть использованы в качестве технологических баз.
Для закрепления детали при фрезеровании базовой поверхности используются стандартное станочное приспособление типа прижымных планок.
Учитывая предъявляемые к детали типа корпус технические требования по шероховатости точности размеров его следует обрабатывать в 1 проход.
Перевод детали в автоматизированное производство возможен так как имеют место следующие критерии:
)Обоснованный выбор материала детали и увязка требований качества по верхностного слоя с маркой материала детали;
) Достаточная жёсткость заготовки и возможность ее жёсткого закрепления в приспособлении.
) Наличие технологических баз используемых при обработке и захвате заготовки промышленным роботом;
) Возможность обработки максимального числа поверхностей заготовки за один установ;
) Серийный тип производства и замкнутость обработки (отсутствие спе- циальных операций выполняемых вне маршрута автоматизированного производства).
4Полный маршрут обработки детали
Таблица 1.2– Полный маршрут обработки детали
5Описание станка ИР500ПМФ4
ИР-500ПМФ4 – Станок фрезерный горизонтальный многоцелевой с ЧПУ и АСИ класс точности П
Сверлильно-фрезерно-расточной станок с числовым программным управлением ИР-800 с автоматической сменой инструмента (АСИ) и сменой обрабатываемых деталей предназначен для высокопроизводительной обработки корпусных деталей массой до 700 кг из конструкционных материалов от легких сплавов до высокопрочных сталей.
Широкий диапазон частоты вращения шпинделя и скоростей подач станка позволяет производить сверление зенкерование развертывание растачивание точных отверстий связанных координатами фрезерование по контуру с линейной и круговой интерполяцией нарезание резьбы метчиками.
Основные параметры станка
Класс точности по ГОСТ 8-82П
Размеры рабочей поверхности стола (длина х ширина) мм 500 х 500
Перемещение поперечное стола (ось X) мм800
Перемещение вертикальное шпиндельной бабки (ось Y) мм500
Перемещение продольное стойки (ось Z) мм500
Вращение индексируемого поворотного стола (ось B) град5° 72 поз.
Наибольший диаметр сверления в стали мм40
Наибольший диаметр растачиваемого отверстия мм160
Наибольший диаметр торцовой фрезы мм160
Точность позиционирования по осям X Y мм0.018 0.015
Точность позиционирования по осям Z мм0.022
Рабочая подача по осям X Y Z мммин1..2000
Скорость быстрых установочных перемещений по осям X Y Z ммин8..10
Наибольшее допустимое усилие подачи стола и стойки по осям X Z Н8000
Наибольшее допустимое усилие подачи шпиндельной бабки (вертикальное) по оси Y Н4000
Расстояние от оси шпинделя до стола мм50..550
Модель устройства ЧПУ2С45-65
Количество управляемых координат3
Количество одновременно управляемых координат при линейной круговой интерполяции33
6 Операционная технология обработки детали на обрабатывающему центре фрезерном горизонтальным с ЧПУ ИР500ПМФ4. Распределение операций между оборудованием
Рисунок 1.3 - Поверхности обрабатываемые на станке ИР500ПМФ4
Таблица 1.3 – Операционная технология обработки детали на ИР500ПМФ4
Установить и закрепить заготовку
Переустановить деталь и закрепить
Фрезеровать поверхность 2
Фрезеровать поверхность 3
Фрезеровать поверхность 4
Фрезеровать поверхность 5
Фрезеровать поверхность 6
Сверлить отверстие 7
Рассверлить отверстие 7
Сверлить 8 отверстия 8
Нарезать резьбу 8 отв. 8
метчик машинный быстрорежущий
Нарезать резьбу 10 отв. 11
Метчик с проходным хвостовиком Р18 М16-7H ГОСТ 3266-81
Контроль исполнителем 100%
Распределение операций между оборудованием.
Нарезать резьбу 6 отв.9
7Временная диаграмма
Диаграмму составляем по технологическому процессу учитывая характер производства и все вспомогательные операции выполняемые рабочим.
При подсчете общего времени затрачиваемого на обработку детали не
учитывалось время на изготовление отливки. Данное время может иметь весомый вклад в общее время необходимого для изготовления изделия однако в курсовой работе требуется автоматизировать процесс непосредственно механической обработки детали.
Диаграмма показывает как распределяется основное технологическое время между операциями при автоматизированной и неавтоматизированной обработке детали.
Исходные данные для диаграммы.
Рисунок 1.4 - Временная диаграмма
При расчете штучного времени затрачиваемого на выполнение операции оказалось что значительную его долю составляет вспомогательное время затрачиваемое на выполнение следующих действий:
Установка на столе станка (операция фрезерная);
Выполнение перехода;
Изменение числа оборотов шпинделя;
Изменение величины и направления подачи;
Установка и снятие инструмента;
Перемещение рабочих органов станка.
Также в штучное время входит:
Время на обслуживание рабочего места;
Подготовительно-заключительное время на партию;
Время перерывов на отдых и личные надобности.
Оптимизации процесса механической обработки детали будет способствовать применение станков с ЧПУ. Станок с ЧПУ может выполнять практически неограниченное количество различных согласованных между собой перемещений рабочих органов с точностью определяемой конструкцией станка и системой ЧПУ а также осуществлять необходимые по технологическому циклу обработки включения вспомогательных органов. При этом точность обработки и затраченное на нее время не зависят от уровня квалификации и психологического состояния обслуживающего этот станок станочника-оператора. Последовательность обработки может быть точно повторена неограниченное число раз и через любой промежуток времени.
Применение станков с ЧПУ имеет следующие преимущества:
Автоматизация процесса обработки и снижение физической и психологической утомляемости станочника-оператора а также снижение требований к его квалификации даже при обработке сложных и точных деталей.
Повышение производительности обработки в результате: концентрации операций и их совмещения а в ряде случаев за счет появляющейся возможности исключения отдельных операций и переустановки обрабатываемой заготовки;
Оптимизации режимов резания и возможности много инструментальной обработки увеличения удельного веса машинного времени в общем балансе штучно-калькуляционного времени за счет сокращения потерь на пробные проточки и измерения что особенно ощутимо при обработке крупногабаритных деталей сложной формы с большим числом обрабатываемых поверхностей с точными размерами.
8Разработка компоновки
ГАУ «Талка-500.3» включает в своем составе пять ГПМ ИР500ПМ1Ф4 и транспортную систему объединяющую модули и другие участки.
Рисунок 1.5 Стандартная компоновка ГАУ
На участке подготовки столов-спутников производится установка и закрепление в приспособлении подготовленных заготовок (профрезерованный низ заготовки корпуса служит базовой опорной поверхностью).
После подготовки столы - передаются на транспортную тележку которая перемещает готовый стол с заготовкой к обрабатывающему станку в накопитель забирает обработанную заготовку и перемещает в следующую позицию. Полностью обработанная деталь перемещается к моечной машине где очищается от остатков стружки и остатков СОЖ.
Стандартная компоновка в составе 5-ти однотипных станков имеет недостаток: производится обработка только 4-х из 5-ти доступных к обработке сторон заготовки.
В виду особенности обработки детали (обрабатывается 5 из 6-ти сторон) целесообразно включение с состав ГАУ модуля ИР500ПМ1Ф4 в исполнении ГЦ500ПМФ4 позволяющего производить обработку 5-ти сторон детали.
Также модуль ИР500ПМ1Ф4 предназначенный для операции 005 целесообразно включить в общую линию которую обслуживает транспортная система. Это сократит время установки-снятия заготовки на станок.
Основной цикл обработки заготовки принимаем с начала обработки заготовки на операции 010 т.к. операция 005 для ГАУ является вспомогательной и необходима для подготовки баз для основной обработки.
Рисунок 1.6 Модуль ИР-ГЦ500ПМФ4
При введении в ГАУ модулей ГЦ500ПМФ4 увеличивается занимаемая ею площадь. Конфигурация ГАУ - изменятся мало в сторону увеличения длины транспортной линии.
Расположение станков «в ряд» позволяет наиболее экономно использовать производственную площадь и позволяет достаточно легко организовать отвод остатков производства (чугунная стружка) при помощи автоматических шнековых вибрационных или скребковых конвейеров располагаемых между станками.
Рисунок 1.7Компоновочное решение ГАУ
На основании чертежа Корпус и исходных данных был произведён анализ технологичности и разработан неавтоматизированный техпроцесс который впоследствии был усовершенствован применением ГАУ произведена оценка технологичности детали в условиях автоматизированного производства разработаны маршрутный ТП автоматизированной обработки детали и операционная технология обработки.
В ходе исследований получены следующие результаты:
Разработан автоматизированный ТП включающий 3 операции:
- сверлильная с ЧПУ (сверление и рассверливании отверстий);
- резьбонарезная с ЧПУ.
Разработана ГАУ предусматривающая взаимное расположение и взаимодействие роботов станков и других элементов комплекса. Разработанная ГАУ включающая в своем составе 4 ГПМ типа ИР-500ПМФ4.
Построена временная диаграмма свидетельствующая о сокращении штучного времени после автоматизации на 37% (Тонеавт.=1275 сек.; Тоавт.= 970 сек.).
Раздел автоматического управления системы
1Алгоритм автоматизированной обработки детали.
Алгоритм автоматизированной обработки детали Корпус представлен на рисунке 2.1.
Рисунок 2.1. - Алгоритм автоматизированной обработки детали корпус
2Управляющая программа обработки детали
Управляющая программа обработки детали создается при помощи программы «Компас 3D V20» в специальном на CNC mill основе построенной 3D модели. Использование данной программы является одним из средств автоматизации подготовки УП позволяющие значительно сократить время подготовки УП повысить производительность данного процесса просмотреть процесс обработки на 3D модели.
Обработка поверхности 1 фрезерование плоскости:
Рисунок 2.2 Окно обработки детали с помощью программы фрезерная ЧПУ
Выбор инструмента для поверхности 4 фрезерование плоскости и сверления и нарезания резьбы шести отверстий 9
Рисунок 2.3 Выбор инструмента для обработки детали
Текст управляющей программы в приложении.
3Циклограмма работы РТК в соответствии с разработанным алгоритмом
Применительно к роботизированным технологическим комплексам (РТК) циклограмма должна включать в выбранной последовательности все основные и вспомогательные операции (переходы) изготовления изделия а также операции (переходы) для возможных изменений технологического маршрута.
Для построения циклограммы функционирования РТК необходимо:
проанализировать компоновку РТК и определить все движения (переходы)
основного и вспомогательного оборудования (робота станка накопителя)
необходимые для выполнения заданного цикла обработки детали;
определить (составить перечень) всех механизмов основного и вспомогательного оборудования участвующих в формировании заданного цикла;
задать исходное положение механизмов робота станка транспортера и т.д.;
составить последовательность движений оборудования (механизмов) за цикл в виде таблицы;
определить время выполнения каждого движения ti по формулам:
i i - соответственно паспортные скорости углового и линейного
перемещения механизмов по соответствующей координате.
Время цикла обработки детали:
где Тр - основное время;
Тк - время контроля;
Тси - время смены инструмента;
Тп - время позиционирования.
Время обслуживания станка манипулятором Тоб равно времени смены заготовки Тсз.
4Разработка функционирования транспортной системы ТС-500 в составе ГАУ
Функционирование системы ТС-500 в составе ГАУ напрямую зависит от времени затрачиваемого на обработку и перемещение заготовки и инструмента внутри станочных модулей.
Таблица 2.1Параметры транспортирующих устройств
В состав системы ТС-500 включаем передаточную тележку ТР-016 с грузоподъемностью 016т. и 2-мя транспортируемыми позициями.
Величина цикла обработки заготовки ограничивается наиболее продолжительной по времени операцией обработки (для данной детали - это операция 010 с продолжительностью 1744мин). Для непрерывности обработки весь цикл строим относительно продолжительности обработки на этой операции.
ТР - транспортный робот (тележка);
М-ХХХ - обрабатывающий модуль ХХХ - номер операции.
УПСС - участок подготовки столов-спутников.
Для обработки детали в модуле за необходимы движения:
-загрузка заготовки со столом спутником в накопитель модуля из накопителя ТР;
-поворот накопителя к столу станка;
-загрузка заготовки со столом спутником из накопителя модуля на рабочий стол;
-разгрузка заготовки со столом спутником в накопитель модуля со стола станка;
-поворот накопителя от стола станка к тележке;
-разгрузка заготовки со столом спутником из накопителя модуля в накопитель ТР.
Для полной обработки заготовки в составе ГАУ необходимы движения ТР:
-загрузка заготовки со столом-спутником УПСС в накопитель ТС;
-транспортировка заготовки к М-005;
-загрузка заготовки со столом-спутником в накопитель М-005 из накопителя ТР;
-разгрузка обработанной заготовки со столом-спутником из накопителя М-005 в накопитель ТР.
-разгрузка обработанной заготовки со столом-спутником из накопителя ТР на УПСС;
-транспортировка заготовки к М-010;
-загрузка заготовки со столом-спутником в накопитель М-010 из накопителя ТР;
-разгрузка обработанной заготовки со столом-спутником из накопителя М-010 в накопитель ТР;
-.транспортировка заготовки к М-015;
-загрузка заготовки со столом-спутником в накопитель М-015 из накопителя ТР;
-разгрузка обработанной заготовки со столом-спутником из накопителя М-015 в накопитель ТР;
-транспортировка заготовки к М-020;
-загрузка заготовки со столом-спутником в накопитель М-020 из накопителя ТР;
-разгрузка обработанной заготовки со столом-спутником из накопителя М-020 в накопитель ТР;
-транспортировка заготовки к М-025;
-загрузка заготовки со столом-спутником в накопитель М-025 из накопителя ТР;
-разгрузка обработанной заготовки со столом-спутником из накопителя М-025 в накопитель ТР;
-транспортировка заготовки к моющей машине (030);
-загрузка заготовки со столом-спутником в моющую машину (030);
-возврат в исходную позицию.
В цикле ГАУ участвуют движения
-смена заготовки со столом-спутником - рабочий стол накопитель;
-обработка заготовки;
-поворот накопителя.
Транспортный робот ТР:
-загрузка-выгрузка стола-спутника;
-перемещение руки вдоль горизонтальной оси.
Исходное положение оборудования и его механизмов:
-ТР в начале линии накопитель пуст;
-стол станка в нулевой позиции в инструментальном магазине - полный комплект инструментов; накопитель заготовок - заполнен;
-заготовка расположена на столе станции загрузки-выгрузки напротив ТР.
Рис. 2.4Циклограмма работы ГАУ.
Из рисунка циклограммы видно что наименее продолжительной является операция 005 что позволяет произвести подготовку столов-спутников.
Время цикла ТР 344с. что позволяет ему произвести обслуживание модуля М-005 без задержек по времени.
Алгоритм функционирования транспортного робота - на рис. 2.5.
Рисунок 2.5 Алгоритм функционирования ТР.
52.5. Вывод по разделу
На основании разработанной операционной технологии был создан алгоритм автоматизированной обработки детали. Опираясь на компоновку РТК был разработан алгоритм функционирования участка. На основе этого алгоритма был произведен расчет циклограммы работы участка. Можно сделать вывод о том что коэффициент эффективного использования основного технологического оборудования (станков с ЧПУ) будет достаточно высоким вследствие малых простоев по вине вспомогательного оборудования. Применение более производительного вспомогательного оборудования (ПР поворотный стол кран-штабелер) создаст предпосылки для сокращения времени простоя станков до минимума.
Спроектированная в технологическом разделе ГАУ была проанализирована в аспекте автоматического управления. В ходе исследований получены следующие результаты:
- разработан алгоритм автоматизированной обработки детали который включает в себя 5 операции обработки детали а также 7 операции смены инструмента.
Конструкторский раздел
Рисунок 3.1-Конструкция станции загрузки-разгрузки
В корпусе 1 (рис 3.1) в двух конических подшипниках установлен вал 2 на верхнем торце которого закреплена плита 3 для базирования сменных столов-спутников. Поворот плиты на 180град. осуществляется зубчатой рейкой 4 которая зацеплена с колесом 5. Привод рейки выполняют гидроцилиндры 6 установленные с обеих сторон рейки. При подходе к крайним положениям - скорость уменьшается с помощью регулируемых дросселей 7 с обратными клапанами 8 встроенными в крышки гидроцилиндров. Точное угловое положение плиты при повороте определяется двумя регулируемыми упорами 9 закрепленными на корпусе и пятами 10. Контроль поворота в ту или иную сторону осуществляют путевые выключатели 11 и 18.
На верхнем торце плиты 3 имеются продольные планки 12 по которым происходит перемещение столов-спутников. Перемещение столов осуществляют 2 гидроцилиндра 13 давление в которые передается через гидромуфту 14 и отверстия в валу 2 и плите 3. Параллельно гидроцилиндрам 13 установлены штанги 15 по которым направляются захватные устройства 16 закрепленные на штоках цилиндров. Интенсивность торможения штоков регулируется дросселями 17. Контроль крайних положений захватных устройств выполняют путевые выключатели.
1Расчет надежности и производительности системы
Надежность - это способность машин и механизмов выполнять заданные функции сохраняя во времени значения эксплуатационных показателей в заданных пределах соответствующих установленным режимам и условиям использования.
Надежность является важнейшим фактором эффективности новой техники так как влияет напрямую на производительность машин и число обслуживающего персонала. При низких показателях надежности рост отказов и простоев сокра- щает фактический выпуск продукции по сравнению с номинальным.
Надежность машин обусловливается такими свойствами как безотказность ремонтопригодность долговечность сохраняемость.
Безотказность - свойство объекта непрерывно сохранять работоспособное сос-тояние в течение некоторого времени или наработки.
Ремонтопригодность - свойство объекта заключающееся в приспособленнос-ти к поддержанию и восстановлению работоспособного состояния путем тех-нического обслуживания и ремонта.
Долговечность - свойство объекта сохранять работоспособное состояние до наступления предельного состояния при установленной системе технического обслуживания и ремонта.
Поскольку отказы и поломки носят вероятностный характер то вышеуказанные характеристики определяются на основе большого числа наблюдений измерений и их математической обработки.
При расчете надежности системы без совершения ее пробных запусков и соответственно без получаемых экспериментальных значениях используют комплексный показатели надежности - коэффициент технического использования. Он интегрирует показатели и безотказности и ремонтопригодности. Коэффициент вычисляется по формуле:
- интенсивность отказов
- среднее время единичного простоя
Т - длительность цикла.
Время затрачиваемое РТК на обработку одной заготовки составляет 1264 с = 2107 мин (см. табл. 1.5). Но время передачи манипулятором готовой детали на конвейер для контроля составляет значительно меньше. Это обусловлено тем что РТК включает в себя 2 одновременно работающих ОЦ. Поэтому время на обработку одной детали принимаем равное сумме времени на обработку на наиболее загруженном станке и времени на переустановки заготовки с ОЦ на конвейер и установку с конвейера на ОЦ. Примем это вспомогательное время равным 36 сек. Тогда длительность цикла Т=1264+36=1300 с = 2166 мин. Примем интенсивностьот-
казов и время простоя = 003 и = 10 мин соответственно.
Производительность определяется количеством годных деталей выпускаемых в единицу времени. Производительность является величиной обратно пропорциональной длительности цикла. Вычислим производительность за смену:
Тсм= 60 мин * 8 ч. * 2 = 960 мин. (время работы в 2 смены)
Q = 960Т=9602166=443 детсут.
Это теоретическая производительность комплекса при отсутствии простоев.
Найдём фактическую производительность с учетом коэффициента технического использования:
Qф=443*0986 =436798 детсут.
Принимаем Q=43 детсут. (Т=2107 мин.).
Считаем что РТК для обработки деталей типа каретка работает в 2 смены. По табличным данным определяем годовой фонд рабочего времени РТК: 3950 часов (2 смены).
Основное технологическое время на обработку детали Т=2107 мин.
Для годового производства 15000 деталей типа корпус потребуется времени:
2Расчет АТСС для транспортирования корпусных деталей
) Определение характеристики стеллажей. Расчетными характеристиками стеллажа являются: вместимость; длина; количество рядов; количество ярусов.
Длина количество рядов и ярусов стеллажа определяются в зависимости от вместимости стеллажа габаритов и характера транспортируемых деталей.
Основной расчетной характеристикой стеллажа является его вместимость которая определяется исходя из числа спутников необходимого для полной загрузки станков во время работы комплекса.
Максимальное число деталеустановок различных наименований которые могут быть обработаны на комплексе:
где Фст= 3322 ч - месячный фонд отдачи станка работающего в 2 смены;
nст– число станков в комплексе или ГПС; tоб - средняя трудоемкость обработки одной деталей установки ч; N - среднемесячная программа выпуска деталей одного наименования.
Полученное число деталей установок определяет число ячеек стеллажа при условии что для обработки одного наименования деталей установки используется один спутник. Так как автоматизированные комплексы позволяют обрабатывать широкую номенклатуру деталей которая может меняться в процессе эксплуатации то целесообразно иметь запас ячеек в стеллаже на случай увеличения числа обрабатываемых деталей. Таким образом рассчитанное число ячеек необходимо увеличить на 10 %.
) Расчет числа позиций загрузки и разгрузки. Функционально позиции загрузки и разгрузки могут быть либо разделены либо объединены. При разделении функций позиции должно быть минимум два рабочих места. При объединении на одном рабочем месте операций загрузки-разгрузки позиция может быть одна если на ней успевают выполнить весь объем работ за месяц. Число позиций определяют по формуле:
где t = tзагр – время для позиций загрузки мин; t = tразгр – время для позиций разгрузки мин; t = tзагр + tразгр – время для совмещенной позиции загрузки-разгрузки мин; Кдет=KнаимN - число деталеустановок проходящих через позицию в течение месяца (см. (4)); Фпоз=Фст - месячный фонд времени работы позиции ч. (см.(4)).
Если полученные nпоз>1 то необходимо ввести дополнительную позицию и рассчитать коэффициент загрузки позиций по времени
где nпоз.расч - рассчитанное по формуле (5) число позиций; nпоз.прин - принятое число позиций.
При варианте функционального разделения позиций загрузки-разгрузки в случае выхода из строя например позиции загрузки позиция разгрузки не сможет принять на себя ее функции. Поэтому если имеются две позиции с разделенными функциями загрузки-разгрузки целесообразно иметь одну резервную позицию с совмещенными функциями загрузки-разгрузки или еще по одной позиции загрузки и разгрузки.
) Расчет числа позиций контроля. В производстве как правило первая а затем каждая n-я деталеустановка проходит контроль. При этом если деталь обрабатывается на нескольких станках то контроль производится после обработки на каждом из них. В автоматизированных комплексах у которых отсутствует активный контроль на станках в процессе обработки деталей необходимо вести проверку получаемых размеров деталей на специальной позиции контроля. На этой позиции наладчик отвечающий за качество выпускаемых деталей проверяет полученные размеры. Если размеры находятся в требуемых пределах то он разрешает обработку следующих n деталей установок этим инструментом. В противном случае подается команда коррекции или замены инструмента.
Необходимое число позиций контроля nпоз.к (округление до целого в большую сторону) в автоматизированном комплексе:
где - суммарное время контроля одной деталеустановки мин; Кдет.к– число деталеустановок проходящих контроль за месяц шт.;
где n - число деталей установок через которые деталь выводится на контроль;
где n1 - число деталей установок через которые деталь выводится на контроль по требованию технолога; k1= 115 - коэффициент учитывающий контроль первой деталей установки; k2 - 105 - коэффициент учитывающий вывод на контроль в связи с работой нового инструмента.
) Определение числа подвижных транспортных механизмов. Функции передачи спутников на станки позиции контроля загрузки-разгрузки на стеллаж выполняют подвижные транспортные механизмы (ШТ1 ШТ2) расположенные по обе стороны стеллажа.
Штабелер ШТ1 расположенный со стороны станков должен передавать контейнеры с заготовками по маршрутам: стеллаж - станок; станок - стеллаж.
Для определения числа штабелеров ШТ1 необходимо знать усредненный маршрут обработки деталей по станкам. Зная число обрабатываемых деталей установок число деталей установок уходящих на контроль и возвращающихся с контроля а также маршрут движения деталеустановок по станкам можно подсчитать число
перемещений штабелера расположенного со стороны станков. Суммарное время работы штабелера (Тобсл ч.):
где Кстел-ст - число перемещений между стеллажом и станками; tстел-ст - среднее время затрачиваемое на передачу контейнера со стеллажа на станок или со станка на стеллажи мин; Кст-ст - число перемещений между станками.
Время выполнения штабелером одной операции передачи равно времени выполнения им двух кадров управляющей программы. Время передачи (мин) контейнера штабелером:
где t1 - время отработки кадра "Подойти к месту (ячейке стеллажа) где находится спутник и взять его" мин; t2 - время отработки кадра "Подойти к месту куда надо поставить спутник" мин;
где tK - время расчета и передачи кадра на систему ЧПУ штабелера; tK=15 10 с;
tпод - время подхода к указанному месту мин; tв = tп - время выполнения операции "Взять контейнер" "Поставить спутник"; tв = tп = 015 025 мин;
где L V Vx = 60 ммин Vy = 6 ммин.
Для упрощения расчетов будем использовать среднюю длину перемещений Lcp вдоль каждой оси:
где L n - число принятых перемещений.
Коэффициент загрузки штабелера:
где Фш = Фст - фонд времени работы штабелера за месяц ч.
Если Кзагр> 1 то необходимо пересчитать число штабелеров и коэффициенты их загрузки.
После того как определено число штабелеров расположенных со стороны станков желательно рассчитать допустимое суммарное время простоев штабелера во время смены. Это необходимо для того чтобы знать время которым будет располагать обслуживающий персонал комплекса на устранение неисправностей штабелера не допуская при этом простоев оборудования.
Допустимое время простоев штабелеров во время смены:
где Кдн = 22 - число рабочих дней в месяце; mу– коэффициент учитывающий число устройств управляемых от одной системы ЧПУ; mу = 15 для 5 устройств.
В данном разделе было произведено обоснование выбора устройств автоматизации описан принцип их действия с учетом разработанной ранее операционной технологии обработки детали. Выбранное основное технологическое оборудование (ИР500ПФ4) повышает производительность точность обработки а в совокупности с автоматизированной транспортировкой детали с помощью ПР образует комплекс оборудования позволяющий практически исключить участие человека в его работе. Технические характеристики оборудования позволяют обрабатывать на нем довольно широкую номенклатуру деталей что является несомненным плюсом данного комплекса в условиях серийного производства.
На основании разработанного ТП автоматизированной обработки детали былпроизведен расчет производительности и надежности РТК. Расчеты дают достаточно хорошие показатели производительности (Q=43дет.сут.) и высокий коэффициент технического использования (=0986).
Также произведено обоснование выбора и расчет АТСС участка. Применение промышленного робота и загрузочного устройства позволяет сократить простои из-за смены инструмента и заготовки что при серийном типе производства оказывает большое влияние на производительность.
Технико-экономический раздел
1Технико-экономическое обоснование выбранного варианта автоматизации техпроцесса.
Технико-экономическое обоснование выбранного варианта автоматизации техпроцесса ведётся в сравнении проектируемого автоматизированного ТП и неавтоматизированного существующего ТП.
В проектируемом ТП по сравнению с базовым применяется концентрация операций на станках с ЧПУ с автоматической сменой инструмента. Это позволяет уменьшить вспомогательное время исключает разметку и слесарные операции по снятию заусенцев и т.д. Анализируя варианты ТП можно оценить величины штучного времени отдельно взятых операций например операции по смене инструмента. В неавтоматизированном ТП tшт=0225 мин в автоматизированном ТП tшт=0154мин.
Расчет экономической эффективности внедрения станков с ЧПУ проводится по инструкции МУ2.5-81. Для предварительных расчетов экономической эффективности внедрения станков с ЧПУ (при определении целесообразности приобретения станка) учитывают лишь заработную плату станочника (оператора) и амортизационные отчисления на полное восстановление станка которые представляют основной элемент экономии и затрат. Расчет ведут по формуле:
где Ц1 и Ц2 — соответственно цены базового и нового станков руб.;
X — коэффициент роста производительности нового станка по сравнению с базовым;
Р1 Р2 — соответственно доля амортизационных отчислений от балансовой стоимости на полное восстановление базового и нового станков;
Eн = 015 — нормативный коэффициент эффективности капитальных вложений
а= 11 — коэффициент учитывающий затраты на доставку и установку станка включая пуско-наладочныеработы;
НС1 и НС2 — среднегодовая заработная плата станочника (оператора) по сравниваемым вариантам;
KCM = 2 — коэффициент сменности' работы станка с ЧПУ;
dl и d2 — соответственно число базовых и новых станков обслуживаемых одним рабочим.
В курсовом проекте разработаны элементы автоматизации технологического оборудования участка механической обработки корпусных деталей. Сравнение неавтоматизированного и автоматизированного ТП выявило преимущество последнего как в технологическом так и в экономическом планах. Штучное время автоматизированного ТП составило 2107 мин неавтоматизированного ТП – 335 мин. Получили сокращение штучного времени в 159 раза. При этом годовой экономический эффект от внедрения составил 500 у.е. В итоге получены следующие результаты: созданы чертеж и параметрическая 3D-модель детали;
исследование технологичности и возможности обработки детали в автоматизированном производстве;
произведено сравнение автоматизированного и неавтоматизированного ТП;
составлен полный маршрут автоматизированной обработки детали;
операционная технология обработки детали на многоцелевом горизонтально фрезерном станке с ЧПУ ИР-500ПМФ4
составлена временная диаграмма обработки;
составлен алгоритм автоматизированной обработки детали;
алгоритм функционирования участка;
описание и обоснование устройства и принципа действия средства автоматизации;
расчет надежности и производительности системы;
произведён расчет АТСС участка;
написана программа ЧПУ для фрезерных и сверлильных операций;
произведено технико-экономическое обоснование выбранного варианта автоматизации техпроцесса.
Применение станков с ЧПУ и обслуживающих роботов позволило увеличить производительность при уменьшении себестоимости детали сократить долю человеческого труда в производстве что наиболее полно отвечает потребностям современных машиностроительных предприятий в особенности для серийного производства. Как показал опыт внедрения робототехника является новой формой технической и организационной ячейки наиболее полно отвечающей потребностям современного производства. Робототехника - гибкая экономная и рациональная форма обработки деталей и изделий более высокой стоимости и лучшего качества средними и малыми сериями.
Список использованной литературы.
Справочник технолога-машиностроителя Под ред. Р.К.Мещерякова А.Г.Косиловой. T.I. -M: Машиностроение 1985.
Автоматические производственные процессы: Учебное пособие Под ред. А. И. Дащенко. -М.: Высш. шк. 1991. -480с.
Промышленные роботы в машиностроении: Альбом схем и чертежей Под ред. Ю.М. Соломенцева. - М.Машиностроение 1987.
Автоматизация производственных процессов в машиностроении: Учеб. пособие Под ред. Н.М. Капустина. - М.: Машиностроение 1991. .
Основы технологии машиностроения Под ред. B.C. Корсакова. - Л. 1977.
Маталин А.А. Технология машиностроения. Л 1985.
Волчкевич Л.И. Автоматизация производственных процессов: Учеб. пособие. -М.: Машиностроение 2005. - 380 с: ил.
Б.Н.Вардашкина. -М.1984..
Вороненко И.П. Соломенцев Ю.М. Схиртладзе А.Г. Проектирование машиностроительного производства Под ред. Ю.М. Соломенцева. - М.: МЦ МГТУ «СТАНКИН» Янус-К 2002. - 348с.
Рогов В.А. Чудаков А.Д. Средства автоматизации производственных систем машиностроения: Учеб. пособие для вузов. - М.: Высш. шк. 2005. - 399 с.:ил.
Технологически основы ГПС Под ред. Ю.М. Соломенцева. - М.: Высш. шк. 2000. -255с.
Проектирование технологии автоматизированного машиностроения: Учеб.Под ред. Ю.М. Соломенцева. - М.: Высш.шк. 1999. - 415 с.:ил..
Фрезерная обработка установ 1
N001 G71 G90 G40 G17
N007 G0 X0 Y140 Z100
N009 G1 X0 Y140 Z4 F500
N049 G1 X175 Y-27.5 Z100 F500
Установ 2 Фрезерование плоскости сверление отверстий и нарезания резьбы
N009 G1 X0 Y0 Z4 F500
N044 G1 X125 Y162.5 Z100 F500
N049 X-83 Y-110 Z100
N051 G1 X-83 Y-110 Z1.5 F500
N054 G1 X-80 Y0 Z20 F500
N055 G1 X-80 Y0 Z1.5
N056 G1 X-80 Y0 Z-10 F50
N058 G1 X-80 Y110 Z20 F500
N059 G1 X-80 Y110 Z1.5
N060 G1 Y110 Z-10 F50
N062 G1 X80 Y110 Z20 F500
N063 G1 X80 Y110 Z1.5
N064 G1 X80 Z-10 F50
N066 G1 X80 Y0 Z20 F500
N070 G1 X83 Y-110 Z20 F500
N071 G1 X83 Y-110 Z1.5
N072 G1 X83 Y-110 Z-10 F50
N074 G1 X83 Y-110 Z100 F500
N086 G1 X80 Y0 Z20 F500
N088 G1 X80 Y0 Z-10 F150
N093 G1 X80 Y110 Z20 F500
N094 G1 X80 Y110 Z2.5
N095 G1 Y110 Z-10 F150
N100 G1 X-80 Y110 Z20 F500
N101 G1 X-80 Y110 Z2.5
N102 G1 X-80 Z-10 F150
N107 G1 X-80 Y0 Z20 F500
N108 G1 X-80 Y0 Z2.5
N109 G1 Y0 Z-10 F150
N114 G1 X-83 Y-110 Z20 F500
N115 G1 X-83 Y-110 Z2.5
N116 G1 X-83 Y-110 Z-10 F150
компоновка ГАУ.cdw

корпус 3D.cdw

корпус.cdw

Неуказанные предельные отклонения по IT142.
циклограмма.cdw

Циклограмма функционирования ГАУ и ТР в составе ГАУ
Заготовка 2.m3d

заготовка.m3d

фрезерная сверлилная нарезания резьбы.m3d

Фрезерная установ 1.m3d

Рекомендуемые чертежи
- 24.01.2023