Технологический процесс изготовления шибера № 5.3М.001-01


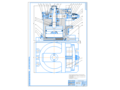
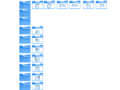
- Добавлен: 21.12.2022
- Размер: 4 MB
- Закачек: 0
Описание
Курсовой проект по технологии машиностроения
Состав проекта
![]() ![]() ![]() |
![]() ![]() ![]() |
![]() ![]() ![]() ![]() |
![]() ![]() ![]() ![]() |
![]() ![]() ![]() ![]() |
![]() ![]() ![]() ![]() |
![]() |
![]() |
![]() ![]() ![]() ![]() |
![]() ![]() ![]() ![]() |
![]() ![]() ![]() |
![]() |
![]() ![]() ![]() ![]() |
![]() ![]() ![]() ![]() |
![]() ![]() ![]() |
![]() ![]() ![]() ![]() |
![]() ![]() ![]() ![]() |
![]() ![]() ![]() |
![]() ![]() ![]() |
![]() ![]() ![]() |
![]() ![]() ![]() |
![]() ![]() ![]() ![]() |
![]() ![]() ![]() ![]() |
Дополнительная информация
спецификация сб большая.doc
Белорусско-Российский
университет гр.ТМА-021
Курсовая ТМА-021.doc
Министерство образования и науки Российской Федерации
Государственное учреждение высшего профессионального образования
Белорусско-Российский университет
Кафедра “Технология машиностроения”
По дисциплине: “Технология машиностроения”
На тему: “Технологический процесс изготовления шибера № 5.3М.001-01”
Назначение и конструкция детали .
Анализ технологичности конструкции детали
Определение типа производства
Анализ базового техпроцесса
Принятый маршрутный техпроцесс .
Расчет припусков на обработку
Расчет режимов резания
1 Расчет режимов резания аналитическим методом
2 Расчет режимов резания по нормативам
Расчет норм времени . .
Расчет точности операции
Экономическое обоснование принятого варианта техпроцесса . .
Расчет и проектирование станочного приспособления
1 Назначение и устройство приспособления .
2 Выбор и расчет привода приспособления .. .
3 Расчет приспособления на прочность ..
4 Расчет приспособления на точность
Список использованных источников
Приложение А. Комплект документов на технологический процесс изготовления шибера 5.3М.001-01
Повышение эффективности машиностроительного производства переход к рыночным принципам ведения хозяйства усиление конкуренции предполагает расширение номенклатуры изделий уменьшение их числа в серии. В результате этого возрастает число предприятий и цехов ориентированных на серийный и мелкосерийный типы производства. Особенности современного машиностроительного производства стремление к его интенсификации в условиях частой сменяемости выпускаемой продукции выдвигают на первый план задачу сокращения сроков разработки технологических процессов и повышения качества проектных решений.
Проектирование технологического процесса с учётом характера производства и оперативная возможность корректировки технологического процесса в зависимости от изменения производственной ситуации во многом предопределяет эффективность работы производственной системы. Обновление современного промышленного потенциала должно осуществляться в условиях роста фондооснащенности технического перевооружения и модернизации производства ускоренного обновления основного капитала сокращений жизненного цикла новой техники что влечёт за собой сокращение сроков её разработки и освоения повышения конкурентоспособности продукции. Такая стратегия предусматривает привлечение научного потенциала страны её ученых к разработке инновационных проектов.
Прогнозируя перспективы развития машиностроения Беларуси следует иметь в виду два направления: так называемое «естественное» то есть развитие на базе фундаментальных и теоретических исследований в области естественных наук и развитие технологий машиностроения связанное с состоянием экономики и динамикой организационных преобразований в промышленности.
Первое направление предусматривает увеличение объёма высокоэффективных технологий на основе новых физических принципов развитие технологии воздействия на конструкционные материалы. В ближайшие годы ожидается прогресс в разработке качественно новых средств автоматизации техпроцессов максимально вытесняющих субъективный фактор из системы обеспечения и воспроизводимости требуемого качества машиностроительных конструкций.
В последние годы в машиностроительном комплексе Беларуси предельно низок уровень использования производственных мощностей используется морально и физически устаревшие технологии и оборудование. Существующие методы разработки технологических процессов не направлены на повышение гибкости современного производства и не позволяют принимать решения на основе данных о реальной производственной ситуации. Таким образом необходимо разработать технологию которая была бы в максимальной степени адаптирована к производству и позволяла бы реализовать все возможности производственной системы.
Одним из путей повышения производительности труда и снижения себестоимости изготовления изделий является совершенствование действующих технологических процессов и их замена более прогрессивными.
Эта работа проводится на основе комплексного анализа как конструкции изделий (деталей) так и технологии их изготовления начиная с выбора более прогрессивных видов заготовки. Серьёзное внимание уделяется повышению качества выпускаемых изделий повышению их надёжности и долговечности.
Учитывая то что предприятия Республики Беларусь на сегодняшний день не имеют достаточных средств на приобретение нового технологического оборудования основное внимание уделяется совершенствованию технологических процессов на основе имеющегося оборудования применению более совершенных приспособлений и инструментов.
В данном курсовом проекте даётся оценка существующим технологическим процессам и пути их улучшения анализ точности обработки и качества обработки поверхности.
Основой проекта является детально разработанная технологическая часть. Решение всех остальных частей проекта производиться на основании данных и требований технологического процесса.
Изменение технологического процесса позволяет не только улучшить форму организации производства но и в некоторых случаях получить ощутимый эффект от внедрения новых методов получения заготовки и обработки детали.
Назначение и конструкция детали
Шибер 5.3М.001-01 по конструкции близок к деталям типа “корпусные”. Он является составной частью вентиля для регулировки подачи нефтепродуктов по трубопроводу. Деталь является очень ответственной поскольку неточность ее изготовления приведет к заклиниванию механизма либо к утечке топлива.
Поверхности 1 и 2 предназначены для перекрытия движения топлива в трубопроводе и являются основными поверхностями. Размер 30 выполняться по 8-му квалитету точности с допуском 0033 мм. К поверхностям предъявляются следующие требования: допуск параллельности поверхности 1 относительно 2 не должен превышать 004 мм.; допуск перпендикулярности поверхности 1 относительно 2 не должен превышать 01 мм.; шероховатость поверхностей составляет Ra = 008 мкм; не допускается чернота окалина выбоины и вмятины.
Эти поверхности подвергаются азотированию с целью повышения твёрдости поверхностного слоя его износостойкости и увеличения предела выносливости и сопротивления коррозии. Азотирование производится при температурах 500-520Со в течение 54 часов и глубина азотированного слоя составляет 03 05 мм. Твёрдость поверхностей после азотирования составляет 18 45 HV.
Поверхности 3 и 4 предназначены для работы в непосредственном контакте с корпусом вентиля и являются вспомогательными. Для предотвращения перекоса шибера в корпусе к ним предъявляются требования перпендикулярности по отношению к поверхности 1 (допуск составляет 01 мм.) и значение шероховатости Ra = 25 мкм.
Все поверхности Т-образного паза детали служат для надёжной фиксации её с захватывающим устройством которое двигает шибер внутри корпуса. Эти поверхности являются вспомогательными и выполняются по 14-му квалитету точности.
Поверхность ø65 является вспомогательной и выполняет функцию регулятора количества нефтепродуктов которое необходимо пропустить через трубопровод. Поскольку нет необходимости в точной регулировке пропускной способности вентиля то размер 65 выполняется по 12-му квалитету точности и допуск составляет 03 мкм.
Все остальные поверхности являются свободными и выполняются по 14-му квалитету точности.
Шибер изготавливается из стали 38Х2МЮА по ГОСТ4543-75. Химический состав стали приведен в таблице 1.1 механические свойства в таблице 1.2.
Таблица 1.1 – Химический состав стали 38Х2МЮА ГОСТ4543-75
Таблица 1.2 – Механические свойства стали 38Х2МЮА ГОСТ4543-75
Анализ технологичности конструкции детали
Анализ технологичности конструкции детали будем производить в соответствии с рекомендациями изложенными в [1].
Выполним качественную оценку технологичности конструкции детали.
Формы и размеры заготовки максимально не приближены к форме и размерам детали что увеличивает потери на стружку и понижает коэффициент использования материала.
При получении заготовки есть возможность получить отверстие что приведёт к снижению металлоемкости и уменьшению числа операций.
При обработке заготовок учитываются технологические особенности. Практически все поверхности для точения и фрезерования доступны и обрабатываются стандартным режущим инструментом. Исключение составляет фрезерование Т-образного паза которое выполняется Т-образной специальной фрезой. Шлифовальные операции выполняются на универсальном широко применяемом оборудовании. Технологические и конструкторские базы совмещаются следовательно принцип постоянства баз выполняется.
Проанализировав чертёж детали и технологический процесс её изготовления делаем вывод о том что данная деталь с качественной стороны является технологичной.
Выполним количественную оценку технологичности конструкции изделия. Составляем таблицу точности обработки таблица 2.1 и таблицу шероховатости поверхностей детали таблица 2.2.
Таблица 2.1 – Точность обработки детали
Квалитет точности IT
Количество размеров П
По формуле вычислим средний коэффициент точности обработки Kт.ч.
где Аср. – средний квалитет точности;
Тогда по формуле (2.1)
Таблица 2.2 – Шероховатость поверхностей детали
Шероховатость Ra мкм
Количество поверхностей П
Коэффициент шероховатости поверхности Kт.ч определяем по формуле
где Rаср – средняя шероховатость поверхностей мкм;
Тогда по формуле (2.3)
Так как расчетное значение коэффициента точности обработки больше нормативного равного 08 и значение коэффициента шероховатости поверхностей также больше нормативного равного 018 (ГОСТ 14.201-83) можно сделать вывод о том что с количественной оценки конструкция вала технологична.
Проанализировав технологичность детали с качественной и количественной стороны можно сделать вывод о том что деталь достаточно технологична. Отсюда следует что получение детали не требует применения сложных и дорогостоящих видов и методов обработки а соответственно больших затрат металла и материальных ресурсов.
Определение типа производства
Тип производства определяем ориентировочно по годовому объему выпуска используя указания [1].
Рассчитаем число деталей в партии nпо формуле
где N – годовой объем выпуска N = 9500 шт.;
a –количество дней запаса деталей на складе a = 8 дней;
m – число рабочих дней в году m = 251;
По полученному значению величины партии и массе детали принимаем среднесерийный тип производства.
Окончательное уточнение значения типа производства произведем после расчетов норм времени на каждую операцию в разделе 9.
Анализ базового техпроцесса
Анализ базового техпроцесса будем проводить с точки зрения обеспечения качества детали и организации технологического процесса.
В базовом техпроцессе применен нерациональный способ получения заготовки. Существует возможность получения заготовки из круглого сортового проката путём осадки с последующим применением прошивки что снижает стоимость изделия и позволяет увеличить коэффициент использования металла.
Последовательность получения точности поверхностей правильная однако с целью увеличения площади контакта кулачка четырёхкулачкового патрона токарную операцию следует производить перед операциями получения Т-образного паза.
Так как производство шибера среднесерийное то применение токарного станка с ЧПУ целесообразно это позволяет увеличить производительность и снизить затраты на производство единицы изделия. На фрезерных операциях используются дорогие иностранные станки производительность которых не превышает производительность отечественных станков.
На фрезерных операциях связанных с получением наклонных поверхностей применяются обычные станочные тиски которые не позволяют рабочему установить заготовку на требуемый угол с минимальными затратами времени.
В базовом техпроцессе не рассматривается возможность одновременной обработки которая позволила бы снизить время на установку и снятие заготовок.
Для обеспечения точности и высоких скоростей резания в базовом техпроцессе используются токарные резцы с механическим креплением твердосплавных пластин Т15К6 а также осевой инструмент из быстрорежущей стали Р6М5.
Для фрезерования паза используется приспособление с механическим приводом что не позволяет автоматизировать операцию. Приспособление позволяет обеспечить заданную точность так как выполняется принцип постоянства баз.
На токарной операции целесообразно использовать РТК. РТК представляет собой совокупность единицы технологического оборудования промышленного робота и средств оснащения (устройства накопления ориентации поштучной выдачи заготовок). Промышленный робот в составе РТК выполняет загрузку-разгрузку деталей с фиксированной позиции. Создание РТК позволит значительно сократить затраты времени на ряд вспомогательных операций связанных с транспортировкой хранением ориентацией поворотом заготовок. Внедрение РТК целесообразно лишь в том случае если размер партии запуска составляет более 100 штук.
Учитывая все рекомендации по выбору заготовок изложенных в [4] метод получения заготовки принимаем аналогичным базовому техпроцессу - поковка однако вводим дополнительную заготовительную операцию – прошивку.
Согласно базовому техпроцессу выбираем в качестве заготовки по ГОСТ 2590-71 сортовой круглый прокат обычной точности ø150 мм длиной 6 м. Маршрутный техпроцесс изготовления заготовки шибера сводим в таблицу 5.1.
Технические требования к прокату:
кривизна прутка не должна превышать 05% длины;
допустимая кривизна реза прутка не должна превышать 5 мм.
Таблица 5.1 – Маршрутный техпроцесс изготовления заготовки шибера 5.3M.001-01
Наименование и краткое содержание операции
Отрезать заготовку ø150 L=54
Ковать заготовку в размер ø240 H=38
Прошить отверстие ø48мм
Продолжение таблицы 5.1
Принятый маршрутный техпроцесс
После анализа базового техпроцесса в проектируемый вариант был внесен ряд изменений.
В принятом варианте черновые и чистовые технологические базы остались аналогичными базовому техпроцессу при выполнении принципа постоянства и единства баз. Выбор баз полностью обоснован с позиции получения требуемой точности размеров детали.
В базовом техпроцессе изготовление шибера ведется в цеху с групповым расположением станков применение такого метода в условиях среднесерийного производства нецелесообразно. Поэтому в проектируемом варианте были изменены модели и число металлорежущих станков.
Разрезка проката на заготовки дисковой пилой на станке модели 8В662 применяемая в исходном техпроцессе приемлема для проектируемого варианта поэтому способ обработки и модель станка приняты без изменений.
Фрезерные станки на всех операциях были заменены станками отечественного производства модели 6Р12.Ф3 в связи с более низкой стоимостью. Эта замена позволила сэкономить и место в цеху так как станок 6Р12.Ф3 занимает на 30% меньше площади по сравнению со станком FSS450R. Кроме того на операции 005 на установах В Г Д и Е был применён способ обработки пяти заготовок одновременно. При получении наклонных поверхностей на 025 и 035 фрезерных операциях были применены поворотные тиски что увеличило точность обработки и снизило время на закрепление заготовок. На токарной операции станок 1В62Г был заменён станком с ЧПУ 16К20.Ф3 в связи с потребностями среднесерийного производства. Также на данной операции был применён четырёхкулачковый патрон с независимым перемещением кулачков что позволило избежать применения специального приспособления это в свою очередь снизило себестоимость изготовления единицы продукции. Сама же операция точения стала выполняться перед фрезерными операциями связанными с получением Т-образного паза и наклонными поверхностями что позволило увеличить площадь контакта кулачка четырёхкулачкового патрона с поверхностью заготовки. Плоскошлифовальные операции выполняемые на плоскошлифовальном станке модели 3М150 с применением магнитной плиты были приняты в проектируемом варианте без изменений.
Для обработки поверхности мм рассчитываем необходимое количество переходов по коэффициенту уточнения.
Необходимое общее уточнение рассчитывается по формуле
где – допуск на изготовление заготовки мм;
– допуск на изготовление детали мм.
Допуск заготовки мм допуск детали мм.
Для обработки поверхности принимаем следующий маршрут:
– шлифование предварительное;
– шлифование тонкое.
Из таблицы 5 справочника [12] выписываем допуски на межоперационные размеры: мм (квалитет точности IT12); мм (квалитет IT8); мм (квалитет IT56).
Рассчитываем промежуточное значение уточнений по формулам 6.2
Определяем общее уточнение для принятого маршрута обработки по формуле 6.3
Полученное значение показывает что при принятом маршруте точность обработки поверхности обеспечивается так как т.е. 15061511.
Окончательный вариант проектируемого техпроцесса изготовления вала представляем в таблице 6.1.
Таблица 6.1 - Маршрутный техпроцесс изготовления заготовки шибера
Наименование оборудования
Технологические базы. Режущий инструмент
Фрезерование плоскости.
Базы: поверхность заготовки 240.
Р.И.: фреза торцовая насадная 315 ГОСТ 24359-80.
Базы: отверстие в заготовке плоскости 1 и 2 240.
Продолжение таблицы 6.1
Базы: плоскости 1 2 и 3.
Базы: плоскости 1 и 2 240.
Базы: плоскости 1 2 и 5.
Расточить отверстие 65.
Базы: плоскости 1 3 4 5 и 6.
Р.И.: Резец Расточной h×b=20×20; Р=40мм; φ=60о; Т15К6 ГОСТ 18882-73.
Фрезеровать паз выдерживая размеры:В×Н=16×26.
Р.И.: Фреза концевая 16 мм Р6М5 ГОСТ 17025-71.
Фрезеровать паз выдерживая размеры: В×Н=36×13.
Р.И.: Фреза Т-образная специальная (36×13) Р6М5.
Фрезеровать угол с двух сторон последовательно (15о15)
Базы: плоскости 4 5 и 6.
Базы: плоскости 3 5 и 6.
Плосколифовальная 3М150.
Шлифовать поверхности 1 и 2 в размер .
Р.И.: Шлифовальный круг 300×40×127 40СМ2 ГОСТ 17123-79.
Фрезеровать угол с двух сторон последовательно (37о)
Термическая термопечь США 5756 №040128.
Азотировать поверхности 1 и 2 (глубина слоя h=03 05 мм) время обработки 54 часа.
Р.И.: Шлифовальный круг 300×40×127 40СМ2К6 ГОСТ 17123-79.
Расчет припусков на обработку
Технологический маршрут обработки поверхности состоит из трех операций: фрезерной и двух плоскошлифовальных. Расчеты сводим в таблицу в которую записываем соответствующие заготовке и технологическому переходу значения элементов припуска.
Таблица 1 - Расчет припусков и предельных размеров по технологическим переходам обработки поверхности
Предельный размер мм
Предельное значение припуска мкм
Расчет минимальных значений припусков производим пользуясь основной формулой:
Zmin = Rzi-1 + Тi-1 + ri-1
ri – суммарное значение пространственных отклонений на i-м переходе мкм.
Минимальные припуски:
Zmin3 =150 + 200 + 222 = 572 мкм
Zmin2 =100+ 100 + 133 = 333 мкм
Zmin1 = 30 + 30 + 89 = 149 мкм.
Графу “Расчетный размер Lр “ заполняем начиная с конечного размера путем сложения минимального припуска каждого технологического перехода:
Lр2 = 30 + 0149 = 30149 мм.
Lр3 = 30149 + 0333 = 30752 мм.
Lр4 = 30419 + 0572 = 31324 мм.
Записав в соответствующей графе расчетной таблицы значения допусков на технологический переход и заготовку в графе “Номинальный предельный размер” определяем их значения для технологического перехода округляя расчетный размеры. Наибольшие предельные размеры вычисляем прибавлением допуска к наименьшему предельному размеру:
Lmax1 = 30 + 0033 = 30033 мм.
Lmax2 = 30149 + 0050 = 30199 мм.
Lmax3 = 30752 + 0300 = 31 мм
Lmax4 = 313 + 1000 = 323 мм
Предельное значение припуска Zпрmax определяем как разность наибольших предельных размеров и Zпрmin – как разность наименьших предельных размеров предшествующего и выполняемого переходов
Zпрmax1 = 30199 – 30033 = 0166 мм
Zпрmax2 = 31 – 30199 = 0801 мм
Zпрmax3 =323 – 31 = 13 мм
Zпрmin1 = 30149 – 30 =0149 мм
Zпрmin2 = 307 – 30149 =0551 мм
Zпрmin3 = 313 – 307 =06 мм
Величину номинального припуска определяем с учетом несимметричности расположения поля допуска заготовки:
Zoном = Zоmin + Hз - Hд
где Hз – нижнее отклонение размера заготовки;
Hд – нижнее отклонение размера детали.
Zoном = 1300 + 300 – 33 = 1567 мкм
Lом = 30 + 1567 = 31567 316 мм
Проверка правильности расчетов:
Zпрmax – 2Zпрmin = dmax - dmin
67 – 1300 = 1000 – 33 = 967 мкм
Расчеты выполнены верно.
Графическая схема расположения припусков и допусков на обработку поверхности мм представлена на рисунке 7.1.
Рисунок 7.1 Схема графического расположения припусков и допусков на обработки поверхности
Рассчитаем припуски на обработку и промежуточные предельные размеры на поверхность ø65 мм используя [1].
Технологический маршрут обработки поверхности ø мм состоит из чернового обтачивания. Суммарное значение пространственных погрешностей ρз мм вычисляем по формуле
где rк.о. – общая кривизна заготовки мм;
rц – погрешность зацентровки мм;
где Dк – удельная кривизна Dк = 06 мкммм;
(выбираем по таблице стр71 после т.о.)
L – диаметр заготовки L = 205 мм;
Погрешность зацентровки определим по формуле
где з – допуск на поверхность используемой в качестве базовой на данной операции з = 23 мм (по ГОСТ 2590-71);
Остаточное пространственное отклонение rост мкм для чернового обтачивания вычислим по формуле
где kу – коэффициент уточнения формы для чернового точения kу = 006.
После чернового обтачивания rост
Расчет минимальных значений припусков zmin мкм производим по формуле
ρi-1 – суммарное значение пространственных отклонений образованных на предшествующей операции мкм.
Под черновое обтачивание
Определим расчетный размер dр мм для заготовки
Наименьшие предельные размеры вычислим путем вычитания допуска от округленного наименьшего предельного размера
Предельное значение минимального припуска мм определяем как разность наибольших предельных размеров
Предельное значение максимального припуска мм определяем как разность наименьших предельных размеров
Рассчитаем общие припуски zоmin zоmax мм суммируя промежуточные припуски
Номинальный припуск zоном мм в данном случае определяем с учетом несимметричного расположения поля допуска заготовки
где Нз – нижнее отклонение размера заготовки мм;
Нд – нижнее отклонение допуска детали мм;
Тогда номинальный размер заготовки dзном мм находим по формуле
Проверка правильности расчетов
Проверка выполнена.
Все расчеты сводим в таблицу 7.1.
Таблица 7.1 – Расчет припусков по технологическим переходам на обработку поверхности вала ø мм.
Технологические переходы обработки поверхности ø90
Элементы припуска мкм
Предельные значения припусков мкм
Расчет режимов резания
1Расчет режимов резания аналитическим методом
Рассчитаем режимы резания на две операции по эмпирическим формулам теории резания используя формулы и данные из таблиц [3].
Операция № 010 токарная с ЧПУ расточить отверстие øмм .
Определим скорость резания v ммин
где Сv – коэффициент учитывающий обрабатываемый материал Сv =350 (табл. 17);
T – стойкость инструмента T = 60 мин. (табл. 14);
t – глубина резания t = 1 мм (табл. 38);
s – подача s = 05 ммоб (табл. 12);
y – показатель степени y = 035 (табл. 17);
m – показатель степени m = 020 (табл. 17);
Кv – общий поправочный коэффициент на скорость резания.
Определим коэффициент Кv по формуле
где Кмv – коэффициент учитывающий качество обрабатываемого материала;
Киv – коэффициент учитывающий материал инструмента Киv=1 (табл. 6);
Кпv – коэффициент учитывающий состояние поверхности Кпv=1 (табл. 6);
Значение коэффициента Кмv рассчитаем по формуле
где GB – предел прочности GB = 610 МПа;
KГ – коэффициент учитывающий группу стали KГ = 10 (табл. 2);
nv – показатель степени nv = 09 (табл. 2);
Тогда по формуле (8.1.2) скорость резания
Определим главную составляющую силы резания Pz Н
где Ср – коэффициент учитывающий обрабатываемый материал Ср = 300 (табл.22);
v – скорость резания ммин;
Кр – общий поправочный коэффициент на силу резания;
y – показатель степени y = 075 (табл.22);
n – показатель степени n = -015 (табл.22);
где Kmp - коэффициент учитывающий влияние качества обрабатываемого материала;
Kφp – поправочный коэффициент учитывающий влияние геометрических параметров режущей части инструмента Kφp = 1 (табл.23);
Kγp – поправочный коэффициент учитывающий влияние геометрических параметров режущей части инструмента Kγp = 11 (табл.23);
Kλp– поправочный коэффициент учитывающий влияние геометрических параметров режущей части инструмента Kλp= 1 (табл.23);
Krp– поправочный коэффициент учитывающий влияние геометрических параметров режущей части инструмента Krp= 093 (табл.23);
Значение коэффициента Кмp рассчитаем по формуле:
Тогда по формуле (8.1.6) общий поправочный коэффициент:
Тогда по формуле (8.1.5) главная составляющая силы резания Pz Н:
Определим крутящий момент на шпинделе по формуле Мкр Hм
Определим эффективную мощность резания Nе кВт по формуле
Операция № 045 плоскошлифовальная.
Чистовое шлифование плоскости ø30
Эффективная мощность NкВт
где СN – коэффициент учитывающий обрабатываемый материал СN =07 (табл. 56);
з – скорость вращения заготовки з = 50 ммин (табл. 55);
d – диаметр шлифования в нашем случае отсутствует;
s – продольная подача s = 8 ммоб (табл. 55);
t – глубина шлифования t = 001 мм (табл. 55);
r – показатель степени r = 07 (табл. 56);
y – показатель степени q = 05 (табл. 56);
q – показатель степени в нашем случае отсутствует (табл. 56);
2Расчет режимов резания по нормативам
Все расчеты производим по формулам и таблицам из [6].
Операция № 005 фрезерная.
Установ А: фрезерование поверхности ø255 мм.
Длина рабочего хода Lр.х мм
где Lрез – длина резания Lрез = 255 мм;
у – длина подвода врезания y = 10 мм (стр. 303);
Средняя ширина фрезерования bср мм
где F – площадь фрезеруемой поверхности;
Lрез – длина резания;
Выберем подачу на зуб фрезы sz ммзуб (карта Ф-2 стр. 85)
Определим стойкость инструмента Tр мин (карта Ф-3 стр. 85)
Определяем рекомендуемую нормативную скорость резания v ммин
где vтабл – табличная скорость резания vтабл = 350 ммин (стр. 96);
K1 – коэффициент зависящий от размеров обработки K1 = 1 (стр. 96);
К2 – коэффициент зависящий от обрабатываемого материала К2 = 07 (стр. 100);
К3 – коэффициент зависящий от стойкости и материала инструмента К3 = 07 (стр.100);
Определяем рекомендуемую частоту вращения шпинделя n мин-1
где D – диаметр обработки D = 255 мм;
Станок 6Р12 имеет частоту вращения шпинделя равную 250 мин-1.
Определим скорость резания по принятым оборотам шпинделя ммин
Определим расчётную минутную подачу sm мммин
где zu – число зубьев фрезы zu =18;
Определим основное машинное время обработки tм мин
Операция № 010 токарная с ЧПУ.
Переход 1: чистовое точение поверхности ø65.
Длина рабочего хода суппорта Lр.х. мм
где Lрез – длина резания Lрез = 30 мм;
у – длина подвода резца y = 15 мм;
Выберем подачу суппорта на оборот шпинделя sо ммоб (табл. 14 стр. 268)
Назначим глубину резания на последний чистовой проход t мм (стр. 265)
Определяем нормативную скорость резания v ммин
где vтабл – табличная скорость резания vтабл = 110 ммин;
K1 – коэффициент учитывающий материал обработки K1 = 075 (стр. 32);
К2 – коэффициент учитывающий стойкость резца К2 = 155 (стр. 33);
К3 – коэффициент учитывающий вид обработки К3 = 1 (стр. 34);
Определяем рекомендуемую частоту вращения шпинделя n мин-1 по формуле
где d – диаметр обработки d = 65мм;
Так как станок 16К20Ф3 имеет бесступенчатое регулирование частоты вращения шпинделя то принимаем рекомендуемую частоту вращения.
Определим основное машинное время обработки tм мин по формуле
Аналогично рассчитываем режимы резания на все стальные операции и результаты записываем в таблицу 8.1.
Таблица 8.1 – Сводная таблица режимов резания
Наименование операции перехода
Глубина резания t мм
Длина резания Lрез мм
Подача sо(sр) ммоб (ммзуб)
Частота вращения n мин-1
Минутная подача sм мммин
Основное время tо мин
Фрезерование плоскости 1.
Фрезерование плоскости 2.
Фрезерование плоскости 3.
Фрезерование плоскости 4.
Фрезерование плоскости 5.
Фрезерование плоскости 6.
Шлифование поверхности1
Шлифование поверхности2
Рассчитаем нормы времени для операций на которые рассчитаны режимы резания в разделе 8 пользуясь формулами приведенными в [1].
Рассчитаем штучное время tшт мин
где tо – основное время мин;
tв – вспомогательное время мин;
tобс – время на обслуживание рабочего места мин;
tотд – время на отдых и личные надобности мин.
где tп.з. – подготовительно-заключительное время мин;
n – число деталей в партии.
Переход 1: черновое растачивание.
Определяем основное время обработки tо1 мин
где Lрез – длина резания мм; Lрез=30 мм;
у – величина врезания и перебега мм; у=2 мм;
sо – минутная подача ммоб; sо = 1 ммоб;
n – частота вращения заготовки мин-1; n=6747 мин-1;
Переход 2: чистовое растачивание.
Определяем основное время обработки tо2 мин
n – частота вращения заготовки мин-1; n=3813 мин-1;
Тогда основное время для всей операции составит tо мин
Определяем вспомогательное время tв мин
где tус. – время на установку и снятие детали tус. = 023 мин (прилож. 5 табл. 5.1 [1]);
tз.о – время на закрепление и открепление детали tз.о = 011 мин (прилож. 5 табл. 5.7 [1]);
tуп – время на приемы управления станком tуп = 021 мин (прилож. 5 табл. 5.8 и табл. 5.9 [1]);
tиз. – время на измерение детали tиз. = 012 мин (табл. 5.16 [1]);
к поправочный коэффициент к = 185 [1];
Время на отдых и обслуживание рабочего места выбираем по таблице 6.1 [1]
Операция № 045 плоскошлифовальная (переход 1).
где Lр.х. – длина рабочего хода шлифовального круга Lр.х. = 205 мм;
sо – минутная подача при шлифовании sо = 0008 ммоб;
n – частота вращения круга n=1590 обмин;
Определяем вспомогательное время для двух установов операции tв мин с учетом поправочного коэффициента на серийность производства
где tус. – время на установку и снятие детали tус. = 0057 мин (прил. 5 табл. 5.4 [1]);
tз.о – время на закрепление и открепление детали tз.о = 0048 мин (приложение 5 табл. 5.7 [1]);
tуп – время на приемы управления станком tуп = 0185 мин (приложение 5 табл. 5.8 и табл. 5.9 [1]);
tиз. – время на измерение детали tиз. = 152 мин (табл. 5.15 и 5.16 [1]).
Время на отдых и обслуживание рабочего места выбираем по таблице 6.2 [1]
Таблица 9.1 Сводная таблица норм времени
Наименование операции
Основное время to мин
Вспомогательное время tв мин
Оперативное время toп мин
tобс и отдыха tотд мин
Штучное время tшт мин
Подготовительно –заключит. время tп.з мин
Штучно – калькуляцион. время tшт-к мин
На основании рассчитанных норм времени производим уточнения типа производства используя данные таблицы 9.1. Все расчеты сводим в таблицу 9.2.
Определяем расчетное количество станков mр по формуле
где N – годовой объем выпуска деталей N = 9500 шт.;
tшт-к – штучно-калькуляционное время;
FД – действительный фонд времени FД = 4029 ч;
з.н. – нормативный коэффициент загрузки оборудования з.н. = 085 [1].
Фактический коэффициент загрузки рабочего места з.ф. вычисляется по формуле
где P – принятое количество станков.
Количество операций О выполняемых на рабочем месте определяется по формуле
Рассчитанные параметры по приведенным формулам заносим в сводную таблицу 9.2.
Таблица 9.2 – Параметры для уточнения типа производства
Определим коэффициент закрепления операций Кз.о.
По ГОСТ 3.1121-84 рассчитанному коэффициенту закрепления операций соответствует среднесерийный тип производства (Кз.о. = 10 20).
Расчёт точности операции
Расчёт точности выполним для операции чистового шлифования плоскости шибера 30() которая выполняется на шлифовальном станке методом автоматического получения размеров в соответствии с порядком изложенным в [7]. В результате проведения расчёта необходимо подтвердить достижение точности на данной технологической операции. Это значит что величина суммарной погрешности не должна превышать величины допуска на получаемый размер.
расчетный диаметр обработки dр = 9022 мм;
величина поля допуска получаемая при чистовом точении = 57 мкм;
расчетная длина обработки L = 1235 мм;
подача при чистовом точении sпр = 0074 ммоб.
Величина суммарной погрешности обработки DS по диаметральным и продольным размерам в общем виде в серийном производстве определяется по формуле
где Dи – погрешность обусловленная износом инструмента мкм;
Dн – погрешность настройки станка мкм;
Dсл – поле рассеяния погрешности обработки обусловленных действием случайных факторов мкм;
eу – погрешность установки заготовки мкм.
Погрешность обработки обусловленную износом режущего инструмента рассчитаем по формуле
где uо – относительный износ инструмента uо = 003 мкмкм (табл. 3.4 Бабук);
l – путь резания при обработке деталей l=205мм.
где Dш.к - диаметр шлифовального круга Dш.к = 300 мм;
t – припуск на сторону t = 0075 мм;
nш.к – число оборотов шлифовального круга в минуту nш.к = 1590 мин-1;
В – ширина шлифования В = 85 мм;
n – количество деталей в настроечной партии n = 25;
nс – число двойных ходов стола в минуту nс = 1;
s1 – подача круга на один двойной ход s1 =1272 мммин;
Определяем погрешность настройки станка
где Dсм – смещение центра группирования размеров пробных деталей относительно середины поля рассеивания размеров мкм;
Dрег – погрешность регулирования положения режущего инструмента на станке Dрег = 10 мкм (табл.3.11);
Dизм – погрешность измерения пробных деталей Dизм = 15 мкм (табл.3.13).
где m – количество пробных деталей m = 5 шт;
Dсл – мгновенная погрешность обработки Dсл = 12 мкм (по таблице 3.7).
Таким образом по формуле (10.4)
Поскольку обработка заготовки производиться на магнитной плите то:
Суммарная погрешность обработки по формуле (10.1)
При сравнении с точностью заданного размера суммарной погрешности обработки можно сделать вывод о том что в данных условиях имеется возможность обеспечить требуемую точность обработки так как выполняется условие
Экономическое обоснование принятого варианта техпроцесса
Экономическое сравнение базового и принятого техпроцессов проводим по текущим и приведенным капитальным затратам на единицу продукции для токарной операции (базовый) и токарной с ЧПУ (проектируемый) в соответствии с порядком изложенным в главе 12 [8].
Исходные данные экономического обоснования сводим в таблицу 11.1.
Таблица 11.1 Исходные данные для экономического обоснования.
Общая площадь на один станок м2
Мощность электродвигателя кВт
Годовой объем выпуска изделий шт.
Проектируемый вариант
Приведенные затраты З руб для двух сравниваемых вариантов техпроцесса рассчитываются по формуле
где C – технологическая себестоимость руб.;
Ен – коэффициент экономической эффективности капитальных вложений (Ен = 05);
Кс и Кз – удельные капитальные вложения в станок и здание соответственно.
Расчет технологической себестоимости по сравниваемым операциям производим по формуле
где Сз – основная и дополнительная зарплата с начислениями руб.;
Сэксп – часовые затраты по эксплуатации рабочего места руб.
Расчет основной и дополнительной зарплаты с начислениями выполняется по формуле
где Сч – часовая тарифная ставка рабочего 5 – го разряда Сч = 1900 руб.час;
Кд – коэффициент учитывающий дополнительную зарплату и начисления (Кд = 17);
Зн – коэффициент учитывающий зарплату наладчика (Зн = 10);
Ко.м – коэффициент учитывающий оплату рабочего при многостаночном обслуживании (Ко.м = 17).
Зарплата рабочего-станочника 5 разряда для сравниваемых вариантов будет
Расчёт часовых затрат по эксплуатации рабочего места Сэксп руб выполняется по формуле
где Сч.з. – часовые затраты на базовом рабочем месте Сч.з .= 890 Сч.з. = 1090 руб.час для базового и проектируемого варианта соответственно;
Км – коэффициент показывающий во сколько раз затраты связанные с работой данного станка больше чем аналогичные расходы у базового станка Км = 07 Км = 14 для базового и проектируемого варианта соответственно.
Определяем часовые затраты по эксплуатации рабочего места базового варианта
Определяем часовые затраты по эксплуатации рабочего места проектируемого варианта
Технологическая себестоимость сравниваемой операции для базового варианта по формуле (11.2) будет равна
Технологическая себестоимость сравниваемой операции для проектируемого варианта будет равна
Рассчитаем капитальные вложения.
Удельные капитальные вложения включают в себя вложения в технологическое оборудование и здание приходящие на единицу продукции.
Капитальные вложения в оборудование Кс млн. руб. рассчитываются по формуле
где Цс – отпускная цена станка млн.руб.;
Км – коэффициент учитывающий затраты на транспортировку и монтаж (Км = 11);
Сп – принятое число станков на операцию;
N – годовой объем выпуска деталей.
Определим капитальные вложения в оборудование для базового варианта
Определим капитальные вложения в оборудование для проектируемого варианта
Удельные капитальные вложения в здание рассчитываются по формуле
где Спл – стоимость одного квадратного метра площади Спл = 300000 рубм2;
Пс – площадь занимаемая одним станком с учетом проходов м2;
Сп – принятое число станков на операцию (Сп = 10).
где f – площадь станка в плане (длина к ширине) м2;
Кс – коэффициент учитывающий дополнительную производственную площадь (К = 35 при f = 2 4 м2; К = 3 при f = 4 6 м2 К = 4 при f 2 м2).
Тогда площадь занимаемая одним станком с учетом проходов Пс для базового и проектируемого варианта будет соответственно равна
Определим удельные капитальные вложение в здание по базовому варианту
Удельные капитальные вложения в здание по принятому варианту
Рассчитаем величину годового экономического эффекта для чего определяем приведенные затраты для базового и проектируемого техпроцесса по формуле (11.1)
Годовой экономический эффект на единицу Э руб. продукции от внедрения принятого варианта техпроцесса определяем по формуле
где Збаз – приведенные затраты по базовому техпроцессу на единицу изделия;
Зпр – приведенные затраты по проектируемому техпроцессу на единицу изделия;
Все полученные результаты сводим в таблицу 11.2.
Таблица 11.2 Расчет удельных капитальных затрат на оборудование
Расчет и проектирование станочного приспособления
1Назначение и устройство приспособления
Проектируемое приспособление предназначено для фрезерования шпоночного паза на фрезерной операции с ЧПУ на вертикально-фрезерном станке модели 6Р12Ф3.
По сравнению с базовым вариантом в конструкцию приспособления был внесен ряд усовершенствований:
был изменён способ зажима заготовок с ручного на пневматический;
для обеспечения точности базирования к приспособлению прикрепляются сменные опорные уголки.
Окончательную конструкцию приспособления приводим в приложении Б. Базирование заготовки в приспособлении происходит по трём поверхностям что обеспечивает очень высокую точность.
Базирование приспособления на стол станка осуществляется по плоскости плиты 16.
В результате подачи воздуха в поршневую полость пневмоцилиндра неподвижного корпуса 1 клиновой шток 7 поступательно двигаясь вертикально вверх воздействует на ролик 10 плунжера 8 сообщая ему поступательное движение влево. В свою очередь правый торец плунжера связан с прижимной пластиной 15 которая движется совместно с плунжером и прижимает заготовки деталей к поверхностям опорного уголка. При прекращении подачи воздуха поршень 16 с клиновым штоком перемещаясь под действием собственного веса вниз перестает воздействовать на ролик плунжера из-за чего под воздействием сжатых пружин 21 и 22 отжимает обработанные заготовки.
Регулировка положения заготовок в приспособлении производится путём прикрепления уголков и опор различных размеров. Управление работой приспособления осуществляется при помощи двухходового кранового распределителя.
2Выбор и расчет привода приспособления
Для расчета усилия зажима пневмопривода произведем расчет сил резания при фрезеровании паза.
Рассчитаем режимы резания фрезерной операции (фрезерование паза H = 26 b = 16) по эмпирическим формулам теории резания используя формулы и данные из таблиц [3].
где Сv – коэффициент учитывающий обрабатываемый материал Сv =12 (табл. 39);
D – диаметр фрезы D=16 мм;
T – стойкость инструмента T = 85 мин. (табл. 40);
t – глубина фрезерования t = 59 мм (табл. 38);
sz – подача на зуб sz = 04 ммзуб (табл. 39);
z – число зубьев фрезы z = 6 (табл. 39);
q – показатель степени q = 03 (табл. 39);
y – показатель степени y = 025 (табл. 39);
u – показатель степени u = 0 (табл. 39);
p – показатель степени p = 0 (табл. 39);
m – показатель степени m = 026 (табл. 39);
Киv – коэффициент учитывающий материал режущего инструмента Киv=1 (табл.6);
Кпv – коэффициент учитывающий состояние поверхности Кпv=1 (табл.6);
KГ – коэффициент учитывающий группу стали KГ = 10 (табл.2);
nv – показатель степени nv = 09 (табл.2);
Тогда скорость резания по формуле (12.2.1)
где Ср – коэффициент учитывающий обрабатываемый материал Ср = 682 (табл.41);
z – число зубьев фрезы z = 6;
D – диаметр фрезы D =16 мм;
n – частота вращения фрезы обмин;
Кмр – общий поправочный коэффициент на силу резания;
y – показатель степени y = 072 (табл.41);
u – показатель степени u = 10 (табл.41);
q – показатель степени p = 086 (табл.41);
w – показатель степени w = 0 (табл.41);
где n – показатель степени учитывающий материал инструмента n = 09 (табл.9);
Рассчитаем величину развиваемого усилия закрепления на штоке пневмоцилиндра Q Н используя формулы из [9]
где D – диаметр поршня цилиндра D = 170 мм;
p – давление воздуха в цилиндре p = 04 МПа;
– коэффициент полезного действия пневмоцилиндра = 09;
Определим силу закрепления заготовки W Н передаваемую клиноплунжерным механизмом
где Q усилие закрепления на штоке пневмоцилиндра Q = 8167 Н;
α угол клина α = 5°50';
φпр приведенный угол трения;
tg φ2 tg φ1 коэффициенты трения tg φ2 = tg φ1 = 01;
Схему сил действующих в приспособлении при зажиме заготовки представляем на рисунке 3.
Определим необходимую силу закрепления заготовки Wн Н по методике изложенной в [10].
где Pz главная составляющая силы резания Pz = 1450 Н;
угол в плане клинового поводка =45°;
Rз расстояние от оси устройства до точки приложения силы Rз = 425 мм;
Сравниваем требуемое значение силы закрепления Wн и фактическое развиваемое Q
Делаем вывод о том что пневмопривод приспособления позволяет вести обработку на заданных режимах резания.
Рисунок 3 – Схема сил действующих в приспособлении при закреплении заготовки.
3Расчет приспособления на прочность
Произведем проверку на прочность болтовых соединений неподвижного корпуса с плитой пользуясь рекомендациями [11]. По формуле 1.32 [11] рассчитаем необходимый внутренний диаметр резьбы d1 мм
где Fр – суммарная нагрузка на болт Н;
допускаемое напряжение = 160 МПа (табл.1.1и 1.2);
Вычислим расчетную суммарную нагрузку на болт по формуле
где Fзат сила затяжки болта Н;
F внешняя нагрузка Н;
где F1 главная составляющая силы резания F2 = 1450 Н;
F1 горизонтальная составляющая силы резания F1 = 400 Н;
F3 величина усилия зажима F3 =8167 Н;
n – число болтов крепящих неподвижный корпус n = 4;
где Кзат коэффициент затяжки Кзат = 4 (стр.41 [11]);
Тогда по формуле (12.3.1)
По полученному значению внутреннего диаметра резьбы выбираем болт М16.
4Расчет приспособления на точность
Расчет приспособления на точность будем производить в соответствии с методикой изложенной в [12].
Определяем допуск на изготовление приспособления Тпр мм для обеспечения точности размера 26+0.5 (глубина паза) по формуле:
где Т – допуск на обработку мм;
Kт – коэффициент учитывающий отклонение рассеяния значений составляющих величин от закона нормального распределения kт = 18;
Kт1 коэффициент учитывающий уменьшение предельного значения погрешности базирования при работе на настроенных станках kт1 = 08;
Kт2 коэффициент учитывающий долю погрешности обработки в суммарной погрешности вызванной факторами не зависящими от приспособления kт2 = 07;
б погрешность базирования заготовки мм;
з погрешность закрепления мм;
у погрешность установки приспособления на станке мм;
и погрешность связанная с износом элементов приспособления мм;
п погрешность от перекоса режущего инструмента мм;
w экономическая точность обработки паза w = 0140 мм (табл. П10 [12]);
Погрешность базирования заготовки в соответствии с рекомендациями таблицы 3.1 [12] принимаем равной
Погрешность закрепления исключаем из расчетов т.к. пневмопривод обеспечивает постоянное усилие зажима.
Вследствие надежного контакта установочной плоскости приспособления с плоскостью стола станка принимаем погрешность установления приспособления на станке равной
Погрешность связанную с износом элементов приспособления принимаем равной и = 0 так как приспособление предусматривает регулировку которая производится сменными призмами.
Так как в приспособлении присутствуют направляющие элементы то погрешность от перекоса инструмента будет равна
Таким образом по формуле (12.4.1) имеем
Делаем вывод что допуск параллельности зажимающей шпильки приспособления относительно плоскости плиты должен составлять Т = 0074 мм.
В результате выполнения данного курсового проекта был проведен полный анализ и разработка технологического процесса получения шибера в условиях крупносерийного производства. Важнейшим этапом проектирования технологии является назначение маршрутного техпроцесса обработки выбор оборудования режущего инструмента и станочных приспособлений.
В ходе курсового проекта была проведена проверка соответствия выбранной заготовки размерам получаемой детали путем расчетов припусков на обработку.
По отношению к базовому техпроцессу был предложен ряд изменений:
изменена последовательность операций для получения более высокого качества получения размеров;
заменены модели металлорежущего оборудования и режущего инструмента.
В курсовом проекте были рассчитаны режимы резания для всех операций двумя методами – аналитическим и по нормативам. Расчет режимов резания позволил не только установить оптимальные параметры процесса резания но и определить основное время на каждую операцию сократив тем самым время обработки.
Экономические расчеты показали что проектируемый вариант технологического процесса изготовления вала является более эффективным так как обеспечивает минимум приведенных затрат на единицу продукции.
Также в курсовом проекте была усовершенствована конструкция станочного приспособления для обработки шпоночных пазов что позволило снизить его металлоемкость и сложность. Были проведены расчеты на прочность и точность подтвердившие правильность нововведений.
Горбацевич А.Ф. Курсовое проектирование по технологии машиностроения Шкред В.А.. - Мн.: Выш. школа 1983 – 256 с.
Справочник технолога-машиностроителя: Т.1 Под ред. А.Г. Косиловой и Р.К. Мещерякова. 4-е изд. перераб. и доп. М.: Машиностроение 1985.
Справочник технолога-машиностроителя: Т.2 Под ред. А.Г. Косиловой и Р.К. Мещерякова. 4-е изд. перераб. и доп. М.: Машиностроение 1985.
Обработка металлов резанием: Справ. Под ред. Г.А. Монахов В.Ф. Жданович Э.М. Радинский и др. М.: Машиностроение 1974. 600 с.: ил.
Руденко П.А. Проектирование и производство заготовок в машиностроении: Учеб. пособие Ю.А. Харламов В.М. Плескач; К.: Выща шк. 1991.247 с.; ил.
Режимы резания металлов: Справочник Под ред. Ю.В. Барановского – М.: Машиностроение 1972.
Дипломное проектирование по технологии машиностроения: Учеб. пособие для вузов В.В. Бабук П.А. Горезко К.П. Забродин и др.; Под ред. В.В. Бабука. Мн.: Выш. школа 1979. 464 с. ил.
Проектирование технологических процессов в машиностроении: Учеб. пособие для вузов И.П. Филонов Г.Я. Беляев Л.М. Кожуро и др.; Под ред. И.П. Филонова. Мн.: УП ”Технопринт” 2003. 910 с.
Ансеров М.А. Приспособления для металлорежущих станков. М.: Машиностроение 1975. 651с.: ил.
Технологическая оснастка. Учебник для студентов машиностроит. специальностей вузов М.Ф. Пашкевич Ж.А. Мрочек Л.М. Кожуро В.М. Пашкевич; Под ред. М.Ф. Пашкевича. – Мн .:Адукацыя и выхаванне 2002. – 320 с .: ил.
Иванов М.Н. Детали машин: Учеб. для студентов втузов Под ред. В.А Финогенова. 6-е изд. перераб. М.: Высш. школа 1998. 383 с.: ил.
Горохов В.А. Проектирование и расчет приспособлений: Учеб. пособие для студентов вузов машиностроительных специальностей Мн.: Выш. шк. 1986. – 238 с.: ил.
Лукашенко В.А. Курсовое проектирование по технологии машиностроения. Методические указания по курсовому проектированию для студентов специальности Т.03.01.00 – Технология и автоматизация машиностроения. – Могилев: МГТУ 2001. 48 с.
Комплект документов на технологический процесс
изготовления вала № 5.3М.001-01
Эскизы.cdw

Операция 005 - фрезерная с ЧПУ
Операция 025 - фрезерная с ЧПУ
Операция 045 - плоскошлифовальная
Размер обеспечивается инструментом
Белорусско-Российский
Операция 010 - токарная с ЧПУ
Операция 015 - фрезерная с ЧПУ
Операция 020 - фрезерная с ЧПУ
Карты контроля.frw

Наименование оборудования
Белорусско-Российский
Прибор ТПП-2 (по Виккерсу)
ность и параллельность
Проверить наличие фасок и
отсутствие заусенцев
Проверить шероховатость
Образцы шероховатости
Проверить угловые размеры
Наименование операции
Сталь 38Х2МЮА ГОСТ 4548-75
Проверитьперпендикуляр-
Приспособление контрольное спе-
Проверить линейные размеры:
Микрометр МК(0-25) ГОСТ6507-80
Деталь.cdw

Общие допуски по ГОСТ 30893.1 - m.
На поверхностях 1 и 2 не допускаются чернота
мм. притупить с двух сторон R 0
Карты операционные (все).frw

Тиски станочные 7200-0225-03 ГОСТ 16518-96; фреза торцовая насадная
Патрон четырёхкулачковый с независимым перемещением кулачков ГОСТ 3890-72; резец расточной Т15К6
ГОСТ 18882-73; скоба СР 100 ГОСТ 11098-75;
пробка 8221-3111 7Н ГОСТ 17758-72
Патрон четырёхкулачковый с независимым перемещением кулачков ГОСТ 3890-72;
резец 2100-2195 ЦМ-32
; скоба СР 100 ГОСТ 11098-75;
Приспособление фрезерное; фреза концевая
Приспособление фрезерное; фреза Т- образная специальная (36
Тиски станочные 7200-0450-01 ГОСТ 14904-69; фреза торцовая насадная
прибор 8734-4084; эталон 8736-4087;
Магнитная плита ГОСТ 16528-81 (320 круг 300 Микрометр
МК(25-50) ГОСТ 6507-80;
прибор 8744-4084; эталон 8746-4087;
Наименование операции
Обозначение программы
Сталь 38Х2МЮА ГОСТ 4548-75
ГОСТ 3.1404-86 Форма 3
Установ Г 4. Фрезеровать поверхность 4
Установ Д 5. Фрезеровать поверхность 5
Установ Е 6. Фрезеровать поверхность 6
Установ А 1. Фрезеровать поверхность 1
Установ Б 2. Фрезеровать поверхность 2
Установ В 3. Фрезеровать поверхность 3
Контроль рабочим 100%
Точить поверхность 1
Фрезеровать поверхности 1
Установ А 1. Фрезеровать угол поверхность 1
Установ Б 2. Фрезеровать угол поверхность 1
Установ А 1. Шлифовать поверхность 1
Деталь.cdw

Общие допуски по ГОСТ 30893.1 - m.
На поверхностях 1 и 2 не допускаются чернота
мм. притупить с двух сторон R 0
Заготовка.cdw

Кривизна прутка не должна превышать 0
Допустимая кривизна реза прутка не должна превышать 5 мм.
Твёрдость прутка менее 20 HRC.
Поковку получить в четыре перехода.
Размеры после отрезной операции
Размеры после осадки
Размеры после прошивки
Н=54мм и диаметр отверстия
Курсовая ТМА-021.doc
Министерство образования и науки Российской Федерации
Государственное учреждение высшего профессионального образования
Белорусско-Российский университет
Кафедра “Технология машиностроения”
По дисциплине: “Технология машиностроения”
На тему: “Технологический процесс изготовления шибера № 5.3М.001-01”
Назначение и конструкция детали .
Анализ технологичности конструкции детали
Определение типа производства
Анализ базового техпроцесса
Принятый маршрутный техпроцесс .
Расчет припусков на обработку
Расчет режимов резания
1 Расчет режимов резания аналитическим методом
2 Расчет режимов резания по нормативам
Расчет норм времени . .
Расчет точности операции
Экономическое обоснование принятого варианта техпроцесса . .
Расчет и проектирование станочного приспособления
1 Назначение и устройство приспособления .
2 Выбор и расчет привода приспособления .. .
3 Расчет приспособления на прочность ..
4 Расчет приспособления на точность
Список использованных источников
Приложение А. Комплект документов на технологический процесс изготовления шибера 5.3М.001-01
Повышение эффективности машиностроительного производства переход к рыночным принципам ведения хозяйства усиление конкуренции предполагает расширение номенклатуры изделий уменьшение их числа в серии. В результате этого возрастает число предприятий и цехов ориентированных на серийный и мелкосерийный типы производства. Особенности современного машиностроительного производства стремление к его интенсификации в условиях частой сменяемости выпускаемой продукции выдвигают на первый план задачу сокращения сроков разработки технологических процессов и повышения качества проектных решений.
Проектирование технологического процесса с учётом характера производства и оперативная возможность корректировки технологического процесса в зависимости от изменения производственной ситуации во многом предопределяет эффективность работы производственной системы. Обновление современного промышленного потенциала должно осуществляться в условиях роста фондооснащенности технического перевооружения и модернизации производства ускоренного обновления основного капитала сокращений жизненного цикла новой техники что влечёт за собой сокращение сроков её разработки и освоения повышения конкурентоспособности продукции. Такая стратегия предусматривает привлечение научного потенциала страны её ученых к разработке инновационных проектов.
Прогнозируя перспективы развития машиностроения Беларуси следует иметь в виду два направления: так называемое «естественное» то есть развитие на базе фундаментальных и теоретических исследований в области естественных наук и развитие технологий машиностроения связанное с состоянием экономики и динамикой организационных преобразований в промышленности.
Первое направление предусматривает увеличение объёма высокоэффективных технологий на основе новых физических принципов развитие технологии воздействия на конструкционные материалы. В ближайшие годы ожидается прогресс в разработке качественно новых средств автоматизации техпроцессов максимально вытесняющих субъективный фактор из системы обеспечения и воспроизводимости требуемого качества машиностроительных конструкций.
В последние годы в машиностроительном комплексе Беларуси предельно низок уровень использования производственных мощностей используется морально и физически устаревшие технологии и оборудование. Существующие методы разработки технологических процессов не направлены на повышение гибкости современного производства и не позволяют принимать решения на основе данных о реальной производственной ситуации. Таким образом необходимо разработать технологию которая была бы в максимальной степени адаптирована к производству и позволяла бы реализовать все возможности производственной системы.
Одним из путей повышения производительности труда и снижения себестоимости изготовления изделий является совершенствование действующих технологических процессов и их замена более прогрессивными.
Эта работа проводится на основе комплексного анализа как конструкции изделий (деталей) так и технологии их изготовления начиная с выбора более прогрессивных видов заготовки. Серьёзное внимание уделяется повышению качества выпускаемых изделий повышению их надёжности и долговечности.
Учитывая то что предприятия Республики Беларусь на сегодняшний день не имеют достаточных средств на приобретение нового технологического оборудования основное внимание уделяется совершенствованию технологических процессов на основе имеющегося оборудования применению более совершенных приспособлений и инструментов.
В данном курсовом проекте даётся оценка существующим технологическим процессам и пути их улучшения анализ точности обработки и качества обработки поверхности.
Основой проекта является детально разработанная технологическая часть. Решение всех остальных частей проекта производиться на основании данных и требований технологического процесса.
Изменение технологического процесса позволяет не только улучшить форму организации производства но и в некоторых случаях получить ощутимый эффект от внедрения новых методов получения заготовки и обработки детали.
Назначение и конструкция детали
Шибер 5.3М.001-01 по конструкции близок к деталям типа “корпусные”. Он является составной частью вентиля для регулировки подачи нефтепродуктов по трубопроводу. Деталь является очень ответственной поскольку неточность ее изготовления приведет к заклиниванию механизма либо к утечке топлива.
Поверхности 1 и 2 предназначены для перекрытия движения топлива в трубопроводе и являются основными поверхностями. Размер 30 выполняться по 8-му квалитету точности с допуском 0033 мм. К поверхностям предъявляются следующие требования: допуск параллельности поверхности 1 относительно 2 не должен превышать 004 мм.; допуск перпендикулярности поверхности 1 относительно 2 не должен превышать 01 мм.; шероховатость поверхностей составляет Ra = 008 мкм; не допускается чернота окалина выбоины и вмятины.
Эти поверхности подвергаются азотированию с целью повышения твёрдости поверхностного слоя его износостойкости и увеличения предела выносливости и сопротивления коррозии. Азотирование производится при температурах 500-520Со в течение 54 часов и глубина азотированного слоя составляет 03 05 мм. Твёрдость поверхностей после азотирования составляет 18 45 HV.
Поверхности 3 и 4 предназначены для работы в непосредственном контакте с корпусом вентиля и являются вспомогательными. Для предотвращения перекоса шибера в корпусе к ним предъявляются требования перпендикулярности по отношению к поверхности 1 (допуск составляет 01 мм.) и значение шероховатости Ra = 25 мкм.
Все поверхности Т-образного паза детали служат для надёжной фиксации её с захватывающим устройством которое двигает шибер внутри корпуса. Эти поверхности являются вспомогательными и выполняются по 14-му квалитету точности.
Поверхность ø65 является вспомогательной и выполняет функцию регулятора количества нефтепродуктов которое необходимо пропустить через трубопровод. Поскольку нет необходимости в точной регулировке пропускной способности вентиля то размер 65 выполняется по 12-му квалитету точности и допуск составляет 03 мкм.
Все остальные поверхности являются свободными и выполняются по 14-му квалитету точности.
Шибер изготавливается из стали 38Х2МЮА по ГОСТ4543-75. Химический состав стали приведен в таблице 1.1 механические свойства в таблице 1.2.
Таблица 1.1 – Химический состав стали 38Х2МЮА ГОСТ4543-75
Таблица 1.2 – Механические свойства стали 38Х2МЮА ГОСТ4543-75
Анализ технологичности конструкции детали
Анализ технологичности конструкции детали будем производить в соответствии с рекомендациями изложенными в [1].
Выполним качественную оценку технологичности конструкции детали.
Формы и размеры заготовки максимально не приближены к форме и размерам детали что увеличивает потери на стружку и понижает коэффициент использования материала.
При получении заготовки есть возможность получить отверстие что приведёт к снижению металлоемкости и уменьшению числа операций.
При обработке заготовок учитываются технологические особенности. Практически все поверхности для точения и фрезерования доступны и обрабатываются стандартным режущим инструментом. Исключение составляет фрезерование Т-образного паза которое выполняется Т-образной специальной фрезой. Шлифовальные операции выполняются на универсальном широко применяемом оборудовании. Технологические и конструкторские базы совмещаются следовательно принцип постоянства баз выполняется.
Проанализировав чертёж детали и технологический процесс её изготовления делаем вывод о том что данная деталь с качественной стороны является технологичной.
Выполним количественную оценку технологичности конструкции изделия. Составляем таблицу точности обработки таблица 2.1 и таблицу шероховатости поверхностей детали таблица 2.2.
Таблица 2.1 – Точность обработки детали
Квалитет точности IT
Количество размеров П
По формуле вычислим средний коэффициент точности обработки Kт.ч.
где Аср. – средний квалитет точности;
Тогда по формуле (2.1)
Таблица 2.2 – Шероховатость поверхностей детали
Шероховатость Ra мкм
Количество поверхностей П
Коэффициент шероховатости поверхности Kт.ч определяем по формуле
где Rаср – средняя шероховатость поверхностей мкм;
Тогда по формуле (2.3)
Так как расчетное значение коэффициента точности обработки больше нормативного равного 08 и значение коэффициента шероховатости поверхностей также больше нормативного равного 018 (ГОСТ 14.201-83) можно сделать вывод о том что с количественной оценки конструкция вала технологична.
Проанализировав технологичность детали с качественной и количественной стороны можно сделать вывод о том что деталь достаточно технологична. Отсюда следует что получение детали не требует применения сложных и дорогостоящих видов и методов обработки а соответственно больших затрат металла и материальных ресурсов.
Определение типа производства
Тип производства определяем ориентировочно по годовому объему выпуска используя указания [1].
Рассчитаем число деталей в партии nпо формуле
где N – годовой объем выпуска N = 9500 шт.;
a –количество дней запаса деталей на складе a = 8 дней;
m – число рабочих дней в году m = 251;
По полученному значению величины партии и массе детали принимаем среднесерийный тип производства.
Окончательное уточнение значения типа производства произведем после расчетов норм времени на каждую операцию в разделе 9.
Анализ базового техпроцесса
Анализ базового техпроцесса будем проводить с точки зрения обеспечения качества детали и организации технологического процесса.
В базовом техпроцессе применен нерациональный способ получения заготовки. Существует возможность получения заготовки из круглого сортового проката путём осадки с последующим применением прошивки что снижает стоимость изделия и позволяет увеличить коэффициент использования металла.
Последовательность получения точности поверхностей правильная однако с целью увеличения площади контакта кулачка четырёхкулачкового патрона токарную операцию следует производить перед операциями получения Т-образного паза.
Так как производство шибера среднесерийное то применение токарного станка с ЧПУ целесообразно это позволяет увеличить производительность и снизить затраты на производство единицы изделия. На фрезерных операциях используются дорогие иностранные станки производительность которых не превышает производительность отечественных станков.
На фрезерных операциях связанных с получением наклонных поверхностей применяются обычные станочные тиски которые не позволяют рабочему установить заготовку на требуемый угол с минимальными затратами времени.
В базовом техпроцессе не рассматривается возможность одновременной обработки которая позволила бы снизить время на установку и снятие заготовок.
Для обеспечения точности и высоких скоростей резания в базовом техпроцессе используются токарные резцы с механическим креплением твердосплавных пластин Т15К6 а также осевой инструмент из быстрорежущей стали Р6М5.
Для фрезерования паза используется приспособление с механическим приводом что не позволяет автоматизировать операцию. Приспособление позволяет обеспечить заданную точность так как выполняется принцип постоянства баз.
На токарной операции целесообразно использовать РТК. РТК представляет собой совокупность единицы технологического оборудования промышленного робота и средств оснащения (устройства накопления ориентации поштучной выдачи заготовок). Промышленный робот в составе РТК выполняет загрузку-разгрузку деталей с фиксированной позиции. Создание РТК позволит значительно сократить затраты времени на ряд вспомогательных операций связанных с транспортировкой хранением ориентацией поворотом заготовок. Внедрение РТК целесообразно лишь в том случае если размер партии запуска составляет более 100 штук.
Учитывая все рекомендации по выбору заготовок изложенных в [4] метод получения заготовки принимаем аналогичным базовому техпроцессу - поковка однако вводим дополнительную заготовительную операцию – прошивку.
Согласно базовому техпроцессу выбираем в качестве заготовки по ГОСТ 2590-71 сортовой круглый прокат обычной точности ø150 мм длиной 6 м. Маршрутный техпроцесс изготовления заготовки шибера сводим в таблицу 5.1.
Технические требования к прокату:
кривизна прутка не должна превышать 05% длины;
допустимая кривизна реза прутка не должна превышать 5 мм.
Таблица 5.1 – Маршрутный техпроцесс изготовления заготовки шибера 5.3M.001-01
Наименование и краткое содержание операции
Отрезать заготовку ø150 L=54
Ковать заготовку в размер ø240 H=38
Прошить отверстие ø48мм
Продолжение таблицы 5.1
Принятый маршрутный техпроцесс
После анализа базового техпроцесса в проектируемый вариант был внесен ряд изменений.
В принятом варианте черновые и чистовые технологические базы остались аналогичными базовому техпроцессу при выполнении принципа постоянства и единства баз. Выбор баз полностью обоснован с позиции получения требуемой точности размеров детали.
В базовом техпроцессе изготовление шибера ведется в цеху с групповым расположением станков применение такого метода в условиях среднесерийного производства нецелесообразно. Поэтому в проектируемом варианте были изменены модели и число металлорежущих станков.
Разрезка проката на заготовки дисковой пилой на станке модели 8В662 применяемая в исходном техпроцессе приемлема для проектируемого варианта поэтому способ обработки и модель станка приняты без изменений.
Фрезерные станки на всех операциях были заменены станками отечественного производства модели 6Р12.Ф3 в связи с более низкой стоимостью. Эта замена позволила сэкономить и место в цеху так как станок 6Р12.Ф3 занимает на 30% меньше площади по сравнению со станком FSS450R. Кроме того на операции 005 на установах В Г Д и Е был применён способ обработки пяти заготовок одновременно. При получении наклонных поверхностей на 025 и 035 фрезерных операциях были применены поворотные тиски что увеличило точность обработки и снизило время на закрепление заготовок. На токарной операции станок 1В62Г был заменён станком с ЧПУ 16К20.Ф3 в связи с потребностями среднесерийного производства. Также на данной операции был применён четырёхкулачковый патрон с независимым перемещением кулачков что позволило избежать применения специального приспособления это в свою очередь снизило себестоимость изготовления единицы продукции. Сама же операция точения стала выполняться перед фрезерными операциями связанными с получением Т-образного паза и наклонными поверхностями что позволило увеличить площадь контакта кулачка четырёхкулачкового патрона с поверхностью заготовки. Плоскошлифовальные операции выполняемые на плоскошлифовальном станке модели 3М150 с применением магнитной плиты были приняты в проектируемом варианте без изменений.
Для обработки поверхности мм рассчитываем необходимое количество переходов по коэффициенту уточнения.
Необходимое общее уточнение рассчитывается по формуле
где – допуск на изготовление заготовки мм;
– допуск на изготовление детали мм.
Допуск заготовки мм допуск детали мм.
Для обработки поверхности принимаем следующий маршрут:
– шлифование предварительное;
– шлифование тонкое.
Из таблицы 5 справочника [12] выписываем допуски на межоперационные размеры: мм (квалитет точности IT12); мм (квалитет IT8); мм (квалитет IT56).
Рассчитываем промежуточное значение уточнений по формулам 6.2
Определяем общее уточнение для принятого маршрута обработки по формуле 6.3
Полученное значение показывает что при принятом маршруте точность обработки поверхности обеспечивается так как т.е. 15061511.
Окончательный вариант проектируемого техпроцесса изготовления вала представляем в таблице 6.1.
Таблица 6.1 - Маршрутный техпроцесс изготовления заготовки шибера
Наименование оборудования
Технологические базы. Режущий инструмент
Фрезерование плоскости.
Базы: поверхность заготовки 240.
Р.И.: фреза торцовая насадная 315 ГОСТ 24359-80.
Базы: отверстие в заготовке плоскости 1 и 2 240.
Продолжение таблицы 6.1
Базы: плоскости 1 2 и 3.
Базы: плоскости 1 и 2 240.
Базы: плоскости 1 2 и 5.
Расточить отверстие 65.
Базы: плоскости 1 3 4 5 и 6.
Р.И.: Резец Расточной h×b=20×20; Р=40мм; φ=60о; Т15К6 ГОСТ 18882-73.
Фрезеровать паз выдерживая размеры:В×Н=16×26.
Р.И.: Фреза концевая 16 мм Р6М5 ГОСТ 17025-71.
Фрезеровать паз выдерживая размеры: В×Н=36×13.
Р.И.: Фреза Т-образная специальная (36×13) Р6М5.
Фрезеровать угол с двух сторон последовательно (15о15)
Базы: плоскости 4 5 и 6.
Базы: плоскости 3 5 и 6.
Плосколифовальная 3М150.
Шлифовать поверхности 1 и 2 в размер .
Р.И.: Шлифовальный круг 300×40×127 40СМ2 ГОСТ 17123-79.
Фрезеровать угол с двух сторон последовательно (37о)
Термическая термопечь США 5756 №040128.
Азотировать поверхности 1 и 2 (глубина слоя h=03 05 мм) время обработки 54 часа.
Р.И.: Шлифовальный круг 300×40×127 40СМ2К6 ГОСТ 17123-79.
Расчет припусков на обработку
Технологический маршрут обработки поверхности состоит из трех операций: фрезерной и двух плоскошлифовальных. Расчеты сводим в таблицу в которую записываем соответствующие заготовке и технологическому переходу значения элементов припуска.
Таблица 1 - Расчет припусков и предельных размеров по технологическим переходам обработки поверхности
Предельный размер мм
Предельное значение припуска мкм
Расчет минимальных значений припусков производим пользуясь основной формулой:
Zmin = Rzi-1 + Тi-1 + ri-1
ri – суммарное значение пространственных отклонений на i-м переходе мкм.
Минимальные припуски:
Zmin3 =150 + 200 + 222 = 572 мкм
Zmin2 =100+ 100 + 133 = 333 мкм
Zmin1 = 30 + 30 + 89 = 149 мкм.
Графу “Расчетный размер Lр “ заполняем начиная с конечного размера путем сложения минимального припуска каждого технологического перехода:
Lр2 = 30 + 0149 = 30149 мм.
Lр3 = 30149 + 0333 = 30752 мм.
Lр4 = 30419 + 0572 = 31324 мм.
Записав в соответствующей графе расчетной таблицы значения допусков на технологический переход и заготовку в графе “Номинальный предельный размер” определяем их значения для технологического перехода округляя расчетный размеры. Наибольшие предельные размеры вычисляем прибавлением допуска к наименьшему предельному размеру:
Lmax1 = 30 + 0033 = 30033 мм.
Lmax2 = 30149 + 0050 = 30199 мм.
Lmax3 = 30752 + 0300 = 31 мм
Lmax4 = 313 + 1000 = 323 мм
Предельное значение припуска Zпрmax определяем как разность наибольших предельных размеров и Zпрmin – как разность наименьших предельных размеров предшествующего и выполняемого переходов
Zпрmax1 = 30199 – 30033 = 0166 мм
Zпрmax2 = 31 – 30199 = 0801 мм
Zпрmax3 =323 – 31 = 13 мм
Zпрmin1 = 30149 – 30 =0149 мм
Zпрmin2 = 307 – 30149 =0551 мм
Zпрmin3 = 313 – 307 =06 мм
Величину номинального припуска определяем с учетом несимметричности расположения поля допуска заготовки:
Zoном = Zоmin + Hз - Hд
где Hз – нижнее отклонение размера заготовки;
Hд – нижнее отклонение размера детали.
Zoном = 1300 + 300 – 33 = 1567 мкм
Lом = 30 + 1567 = 31567 316 мм
Проверка правильности расчетов:
Zпрmax – 2Zпрmin = dmax - dmin
67 – 1300 = 1000 – 33 = 967 мкм
Расчеты выполнены верно.
Графическая схема расположения припусков и допусков на обработку поверхности мм представлена на рисунке 7.1.
Рисунок 7.1 Схема графического расположения припусков и допусков на обработки поверхности
Рассчитаем припуски на обработку и промежуточные предельные размеры на поверхность ø65 мм используя [1].
Технологический маршрут обработки поверхности ø мм состоит из чернового обтачивания. Суммарное значение пространственных погрешностей ρз мм вычисляем по формуле
где rк.о. – общая кривизна заготовки мм;
rц – погрешность зацентровки мм;
где Dк – удельная кривизна Dк = 06 мкммм;
(выбираем по таблице стр71 после т.о.)
L – диаметр заготовки L = 205 мм;
Погрешность зацентровки определим по формуле
где з – допуск на поверхность используемой в качестве базовой на данной операции з = 23 мм (по ГОСТ 2590-71);
Остаточное пространственное отклонение rост мкм для чернового обтачивания вычислим по формуле
где kу – коэффициент уточнения формы для чернового точения kу = 006.
После чернового обтачивания rост
Расчет минимальных значений припусков zmin мкм производим по формуле
ρi-1 – суммарное значение пространственных отклонений образованных на предшествующей операции мкм.
Под черновое обтачивание
Определим расчетный размер dр мм для заготовки
Наименьшие предельные размеры вычислим путем вычитания допуска от округленного наименьшего предельного размера
Предельное значение минимального припуска мм определяем как разность наибольших предельных размеров
Предельное значение максимального припуска мм определяем как разность наименьших предельных размеров
Рассчитаем общие припуски zоmin zоmax мм суммируя промежуточные припуски
Номинальный припуск zоном мм в данном случае определяем с учетом несимметричного расположения поля допуска заготовки
где Нз – нижнее отклонение размера заготовки мм;
Нд – нижнее отклонение допуска детали мм;
Тогда номинальный размер заготовки dзном мм находим по формуле
Проверка правильности расчетов
Проверка выполнена.
Все расчеты сводим в таблицу 7.1.
Таблица 7.1 – Расчет припусков по технологическим переходам на обработку поверхности вала ø мм.
Технологические переходы обработки поверхности ø90
Элементы припуска мкм
Предельные значения припусков мкм
Расчет режимов резания
1Расчет режимов резания аналитическим методом
Рассчитаем режимы резания на две операции по эмпирическим формулам теории резания используя формулы и данные из таблиц [3].
Операция № 010 токарная с ЧПУ расточить отверстие øмм .
Определим скорость резания v ммин
где Сv – коэффициент учитывающий обрабатываемый материал Сv =350 (табл. 17);
T – стойкость инструмента T = 60 мин. (табл. 14);
t – глубина резания t = 1 мм (табл. 38);
s – подача s = 05 ммоб (табл. 12);
y – показатель степени y = 035 (табл. 17);
m – показатель степени m = 020 (табл. 17);
Кv – общий поправочный коэффициент на скорость резания.
Определим коэффициент Кv по формуле
где Кмv – коэффициент учитывающий качество обрабатываемого материала;
Киv – коэффициент учитывающий материал инструмента Киv=1 (табл. 6);
Кпv – коэффициент учитывающий состояние поверхности Кпv=1 (табл. 6);
Значение коэффициента Кмv рассчитаем по формуле
где GB – предел прочности GB = 610 МПа;
KГ – коэффициент учитывающий группу стали KГ = 10 (табл. 2);
nv – показатель степени nv = 09 (табл. 2);
Тогда по формуле (8.1.2) скорость резания
Определим главную составляющую силы резания Pz Н
где Ср – коэффициент учитывающий обрабатываемый материал Ср = 300 (табл.22);
v – скорость резания ммин;
Кр – общий поправочный коэффициент на силу резания;
y – показатель степени y = 075 (табл.22);
n – показатель степени n = -015 (табл.22);
где Kmp - коэффициент учитывающий влияние качества обрабатываемого материала;
Kφp – поправочный коэффициент учитывающий влияние геометрических параметров режущей части инструмента Kφp = 1 (табл.23);
Kγp – поправочный коэффициент учитывающий влияние геометрических параметров режущей части инструмента Kγp = 11 (табл.23);
Kλp– поправочный коэффициент учитывающий влияние геометрических параметров режущей части инструмента Kλp= 1 (табл.23);
Krp– поправочный коэффициент учитывающий влияние геометрических параметров режущей части инструмента Krp= 093 (табл.23);
Значение коэффициента Кмp рассчитаем по формуле:
Тогда по формуле (8.1.6) общий поправочный коэффициент:
Тогда по формуле (8.1.5) главная составляющая силы резания Pz Н:
Определим крутящий момент на шпинделе по формуле Мкр Hм
Определим эффективную мощность резания Nе кВт по формуле
Операция № 045 плоскошлифовальная.
Чистовое шлифование плоскости ø30
Эффективная мощность NкВт
где СN – коэффициент учитывающий обрабатываемый материал СN =07 (табл. 56);
з – скорость вращения заготовки з = 50 ммин (табл. 55);
d – диаметр шлифования в нашем случае отсутствует;
s – продольная подача s = 8 ммоб (табл. 55);
t – глубина шлифования t = 001 мм (табл. 55);
r – показатель степени r = 07 (табл. 56);
y – показатель степени q = 05 (табл. 56);
q – показатель степени в нашем случае отсутствует (табл. 56);
2Расчет режимов резания по нормативам
Все расчеты производим по формулам и таблицам из [6].
Операция № 005 фрезерная.
Установ А: фрезерование поверхности ø255 мм.
Длина рабочего хода Lр.х мм
где Lрез – длина резания Lрез = 255 мм;
у – длина подвода врезания y = 10 мм (стр. 303);
Средняя ширина фрезерования bср мм
где F – площадь фрезеруемой поверхности;
Lрез – длина резания;
Выберем подачу на зуб фрезы sz ммзуб (карта Ф-2 стр. 85)
Определим стойкость инструмента Tр мин (карта Ф-3 стр. 85)
Определяем рекомендуемую нормативную скорость резания v ммин
где vтабл – табличная скорость резания vтабл = 350 ммин (стр. 96);
K1 – коэффициент зависящий от размеров обработки K1 = 1 (стр. 96);
К2 – коэффициент зависящий от обрабатываемого материала К2 = 07 (стр. 100);
К3 – коэффициент зависящий от стойкости и материала инструмента К3 = 07 (стр.100);
Определяем рекомендуемую частоту вращения шпинделя n мин-1
где D – диаметр обработки D = 255 мм;
Станок 6Р12 имеет частоту вращения шпинделя равную 250 мин-1.
Определим скорость резания по принятым оборотам шпинделя ммин
Определим расчётную минутную подачу sm мммин
где zu – число зубьев фрезы zu =18;
Определим основное машинное время обработки tм мин
Операция № 010 токарная с ЧПУ.
Переход 1: чистовое точение поверхности ø65.
Длина рабочего хода суппорта Lр.х. мм
где Lрез – длина резания Lрез = 30 мм;
у – длина подвода резца y = 15 мм;
Выберем подачу суппорта на оборот шпинделя sо ммоб (табл. 14 стр. 268)
Назначим глубину резания на последний чистовой проход t мм (стр. 265)
Определяем нормативную скорость резания v ммин
где vтабл – табличная скорость резания vтабл = 110 ммин;
K1 – коэффициент учитывающий материал обработки K1 = 075 (стр. 32);
К2 – коэффициент учитывающий стойкость резца К2 = 155 (стр. 33);
К3 – коэффициент учитывающий вид обработки К3 = 1 (стр. 34);
Определяем рекомендуемую частоту вращения шпинделя n мин-1 по формуле
где d – диаметр обработки d = 65мм;
Так как станок 16К20Ф3 имеет бесступенчатое регулирование частоты вращения шпинделя то принимаем рекомендуемую частоту вращения.
Определим основное машинное время обработки tм мин по формуле
Аналогично рассчитываем режимы резания на все стальные операции и результаты записываем в таблицу 8.1.
Таблица 8.1 – Сводная таблица режимов резания
Наименование операции перехода
Глубина резания t мм
Длина резания Lрез мм
Подача sо(sр) ммоб (ммзуб)
Частота вращения n мин-1
Минутная подача sм мммин
Основное время tо мин
Фрезерование плоскости 1.
Фрезерование плоскости 2.
Фрезерование плоскости 3.
Фрезерование плоскости 4.
Фрезерование плоскости 5.
Фрезерование плоскости 6.
Шлифование поверхности1
Шлифование поверхности2
Рассчитаем нормы времени для операций на которые рассчитаны режимы резания в разделе 8 пользуясь формулами приведенными в [1].
Рассчитаем штучное время tшт мин
где tо – основное время мин;
tв – вспомогательное время мин;
tобс – время на обслуживание рабочего места мин;
tотд – время на отдых и личные надобности мин.
где tп.з. – подготовительно-заключительное время мин;
n – число деталей в партии.
Переход 1: черновое растачивание.
Определяем основное время обработки tо1 мин
где Lрез – длина резания мм; Lрез=30 мм;
у – величина врезания и перебега мм; у=2 мм;
sо – минутная подача ммоб; sо = 1 ммоб;
n – частота вращения заготовки мин-1; n=6747 мин-1;
Переход 2: чистовое растачивание.
Определяем основное время обработки tо2 мин
n – частота вращения заготовки мин-1; n=3813 мин-1;
Тогда основное время для всей операции составит tо мин
Определяем вспомогательное время tв мин
где tус. – время на установку и снятие детали tус. = 023 мин (прилож. 5 табл. 5.1 [1]);
tз.о – время на закрепление и открепление детали tз.о = 011 мин (прилож. 5 табл. 5.7 [1]);
tуп – время на приемы управления станком tуп = 021 мин (прилож. 5 табл. 5.8 и табл. 5.9 [1]);
tиз. – время на измерение детали tиз. = 012 мин (табл. 5.16 [1]);
к поправочный коэффициент к = 185 [1];
Время на отдых и обслуживание рабочего места выбираем по таблице 6.1 [1]
Операция № 045 плоскошлифовальная (переход 1).
где Lр.х. – длина рабочего хода шлифовального круга Lр.х. = 205 мм;
sо – минутная подача при шлифовании sо = 0008 ммоб;
n – частота вращения круга n=1590 обмин;
Определяем вспомогательное время для двух установов операции tв мин с учетом поправочного коэффициента на серийность производства
где tус. – время на установку и снятие детали tус. = 0057 мин (прил. 5 табл. 5.4 [1]);
tз.о – время на закрепление и открепление детали tз.о = 0048 мин (приложение 5 табл. 5.7 [1]);
tуп – время на приемы управления станком tуп = 0185 мин (приложение 5 табл. 5.8 и табл. 5.9 [1]);
tиз. – время на измерение детали tиз. = 152 мин (табл. 5.15 и 5.16 [1]).
Время на отдых и обслуживание рабочего места выбираем по таблице 6.2 [1]
Таблица 9.1 Сводная таблица норм времени
Наименование операции
Основное время to мин
Вспомогательное время tв мин
Оперативное время toп мин
tобс и отдыха tотд мин
Штучное время tшт мин
Подготовительно –заключит. время tп.з мин
Штучно – калькуляцион. время tшт-к мин
На основании рассчитанных норм времени производим уточнения типа производства используя данные таблицы 9.1. Все расчеты сводим в таблицу 9.2.
Определяем расчетное количество станков mр по формуле
где N – годовой объем выпуска деталей N = 9500 шт.;
tшт-к – штучно-калькуляционное время;
FД – действительный фонд времени FД = 4029 ч;
з.н. – нормативный коэффициент загрузки оборудования з.н. = 085 [1].
Фактический коэффициент загрузки рабочего места з.ф. вычисляется по формуле
где P – принятое количество станков.
Количество операций О выполняемых на рабочем месте определяется по формуле
Рассчитанные параметры по приведенным формулам заносим в сводную таблицу 9.2.
Таблица 9.2 – Параметры для уточнения типа производства
Определим коэффициент закрепления операций Кз.о.
По ГОСТ 3.1121-84 рассчитанному коэффициенту закрепления операций соответствует среднесерийный тип производства (Кз.о. = 10 20).
Расчёт точности операции
Расчёт точности выполним для операции чистового шлифования плоскости шибера 30() которая выполняется на шлифовальном станке методом автоматического получения размеров в соответствии с порядком изложенным в [7]. В результате проведения расчёта необходимо подтвердить достижение точности на данной технологической операции. Это значит что величина суммарной погрешности не должна превышать величины допуска на получаемый размер.
расчетный диаметр обработки dр = 9022 мм;
величина поля допуска получаемая при чистовом точении = 57 мкм;
расчетная длина обработки L = 1235 мм;
подача при чистовом точении sпр = 0074 ммоб.
Величина суммарной погрешности обработки DS по диаметральным и продольным размерам в общем виде в серийном производстве определяется по формуле
где Dи – погрешность обусловленная износом инструмента мкм;
Dн – погрешность настройки станка мкм;
Dсл – поле рассеяния погрешности обработки обусловленных действием случайных факторов мкм;
eу – погрешность установки заготовки мкм.
Погрешность обработки обусловленную износом режущего инструмента рассчитаем по формуле
где uо – относительный износ инструмента uо = 003 мкмкм (табл. 3.4 Бабук);
l – путь резания при обработке деталей l=205мм.
где Dш.к - диаметр шлифовального круга Dш.к = 300 мм;
t – припуск на сторону t = 0075 мм;
nш.к – число оборотов шлифовального круга в минуту nш.к = 1590 мин-1;
В – ширина шлифования В = 85 мм;
n – количество деталей в настроечной партии n = 25;
nс – число двойных ходов стола в минуту nс = 1;
s1 – подача круга на один двойной ход s1 =1272 мммин;
Определяем погрешность настройки станка
где Dсм – смещение центра группирования размеров пробных деталей относительно середины поля рассеивания размеров мкм;
Dрег – погрешность регулирования положения режущего инструмента на станке Dрег = 10 мкм (табл.3.11);
Dизм – погрешность измерения пробных деталей Dизм = 15 мкм (табл.3.13).
где m – количество пробных деталей m = 5 шт;
Dсл – мгновенная погрешность обработки Dсл = 12 мкм (по таблице 3.7).
Таким образом по формуле (10.4)
Поскольку обработка заготовки производиться на магнитной плите то:
Суммарная погрешность обработки по формуле (10.1)
При сравнении с точностью заданного размера суммарной погрешности обработки можно сделать вывод о том что в данных условиях имеется возможность обеспечить требуемую точность обработки так как выполняется условие
Экономическое обоснование принятого варианта техпроцесса
Экономическое сравнение базового и принятого техпроцессов проводим по текущим и приведенным капитальным затратам на единицу продукции для токарной операции (базовый) и токарной с ЧПУ (проектируемый) в соответствии с порядком изложенным в главе 12 [8].
Исходные данные экономического обоснования сводим в таблицу 11.1.
Таблица 11.1 Исходные данные для экономического обоснования.
Общая площадь на один станок м2
Мощность электродвигателя кВт
Годовой объем выпуска изделий шт.
Проектируемый вариант
Приведенные затраты З руб для двух сравниваемых вариантов техпроцесса рассчитываются по формуле
где C – технологическая себестоимость руб.;
Ен – коэффициент экономической эффективности капитальных вложений (Ен = 05);
Кс и Кз – удельные капитальные вложения в станок и здание соответственно.
Расчет технологической себестоимости по сравниваемым операциям производим по формуле
где Сз – основная и дополнительная зарплата с начислениями руб.;
Сэксп – часовые затраты по эксплуатации рабочего места руб.
Расчет основной и дополнительной зарплаты с начислениями выполняется по формуле
где Сч – часовая тарифная ставка рабочего 5 – го разряда Сч = 1900 руб.час;
Кд – коэффициент учитывающий дополнительную зарплату и начисления (Кд = 17);
Зн – коэффициент учитывающий зарплату наладчика (Зн = 10);
Ко.м – коэффициент учитывающий оплату рабочего при многостаночном обслуживании (Ко.м = 17).
Зарплата рабочего-станочника 5 разряда для сравниваемых вариантов будет
Расчёт часовых затрат по эксплуатации рабочего места Сэксп руб выполняется по формуле
где Сч.з. – часовые затраты на базовом рабочем месте Сч.з .= 890 Сч.з. = 1090 руб.час для базового и проектируемого варианта соответственно;
Км – коэффициент показывающий во сколько раз затраты связанные с работой данного станка больше чем аналогичные расходы у базового станка Км = 07 Км = 14 для базового и проектируемого варианта соответственно.
Определяем часовые затраты по эксплуатации рабочего места базового варианта
Определяем часовые затраты по эксплуатации рабочего места проектируемого варианта
Технологическая себестоимость сравниваемой операции для базового варианта по формуле (11.2) будет равна
Технологическая себестоимость сравниваемой операции для проектируемого варианта будет равна
Рассчитаем капитальные вложения.
Удельные капитальные вложения включают в себя вложения в технологическое оборудование и здание приходящие на единицу продукции.
Капитальные вложения в оборудование Кс млн. руб. рассчитываются по формуле
где Цс – отпускная цена станка млн.руб.;
Км – коэффициент учитывающий затраты на транспортировку и монтаж (Км = 11);
Сп – принятое число станков на операцию;
N – годовой объем выпуска деталей.
Определим капитальные вложения в оборудование для базового варианта
Определим капитальные вложения в оборудование для проектируемого варианта
Удельные капитальные вложения в здание рассчитываются по формуле
где Спл – стоимость одного квадратного метра площади Спл = 300000 рубм2;
Пс – площадь занимаемая одним станком с учетом проходов м2;
Сп – принятое число станков на операцию (Сп = 10).
где f – площадь станка в плане (длина к ширине) м2;
Кс – коэффициент учитывающий дополнительную производственную площадь (К = 35 при f = 2 4 м2; К = 3 при f = 4 6 м2 К = 4 при f 2 м2).
Тогда площадь занимаемая одним станком с учетом проходов Пс для базового и проектируемого варианта будет соответственно равна
Определим удельные капитальные вложение в здание по базовому варианту
Удельные капитальные вложения в здание по принятому варианту
Рассчитаем величину годового экономического эффекта для чего определяем приведенные затраты для базового и проектируемого техпроцесса по формуле (11.1)
Годовой экономический эффект на единицу Э руб. продукции от внедрения принятого варианта техпроцесса определяем по формуле
где Збаз – приведенные затраты по базовому техпроцессу на единицу изделия;
Зпр – приведенные затраты по проектируемому техпроцессу на единицу изделия;
Все полученные результаты сводим в таблицу 11.2.
Таблица 11.2 Расчет удельных капитальных затрат на оборудование
Расчет и проектирование станочного приспособления
1Назначение и устройство приспособления
Проектируемое приспособление предназначено для фрезерования шпоночного паза на фрезерной операции с ЧПУ на вертикально-фрезерном станке модели 6Р12Ф3.
По сравнению с базовым вариантом в конструкцию приспособления был внесен ряд усовершенствований:
был изменён способ зажима заготовок с ручного на пневматический;
для обеспечения точности базирования к приспособлению прикрепляются сменные опорные уголки.
Окончательную конструкцию приспособления приводим в приложении Б. Базирование заготовки в приспособлении происходит по трём поверхностям что обеспечивает очень высокую точность.
Базирование приспособления на стол станка осуществляется по плоскости плиты 16.
В результате подачи воздуха в поршневую полость пневмоцилиндра неподвижного корпуса 1 клиновой шток 7 поступательно двигаясь вертикально вверх воздействует на ролик 10 плунжера 8 сообщая ему поступательное движение влево. В свою очередь правый торец плунжера связан с прижимной пластиной 15 которая движется совместно с плунжером и прижимает заготовки деталей к поверхностям опорного уголка. При прекращении подачи воздуха поршень 16 с клиновым штоком перемещаясь под действием собственного веса вниз перестает воздействовать на ролик плунжера из-за чего под воздействием сжатых пружин 21 и 22 отжимает обработанные заготовки.
Регулировка положения заготовок в приспособлении производится путём прикрепления уголков и опор различных размеров. Управление работой приспособления осуществляется при помощи двухходового кранового распределителя.
2Выбор и расчет привода приспособления
Для расчета усилия зажима пневмопривода произведем расчет сил резания при фрезеровании паза.
Рассчитаем режимы резания фрезерной операции (фрезерование паза H = 26 b = 16) по эмпирическим формулам теории резания используя формулы и данные из таблиц [3].
где Сv – коэффициент учитывающий обрабатываемый материал Сv =12 (табл. 39);
D – диаметр фрезы D=16 мм;
T – стойкость инструмента T = 85 мин. (табл. 40);
t – глубина фрезерования t = 59 мм (табл. 38);
sz – подача на зуб sz = 04 ммзуб (табл. 39);
z – число зубьев фрезы z = 6 (табл. 39);
q – показатель степени q = 03 (табл. 39);
y – показатель степени y = 025 (табл. 39);
u – показатель степени u = 0 (табл. 39);
p – показатель степени p = 0 (табл. 39);
m – показатель степени m = 026 (табл. 39);
Киv – коэффициент учитывающий материал режущего инструмента Киv=1 (табл.6);
Кпv – коэффициент учитывающий состояние поверхности Кпv=1 (табл.6);
KГ – коэффициент учитывающий группу стали KГ = 10 (табл.2);
nv – показатель степени nv = 09 (табл.2);
Тогда скорость резания по формуле (12.2.1)
где Ср – коэффициент учитывающий обрабатываемый материал Ср = 682 (табл.41);
z – число зубьев фрезы z = 6;
D – диаметр фрезы D =16 мм;
n – частота вращения фрезы обмин;
Кмр – общий поправочный коэффициент на силу резания;
y – показатель степени y = 072 (табл.41);
u – показатель степени u = 10 (табл.41);
q – показатель степени p = 086 (табл.41);
w – показатель степени w = 0 (табл.41);
где n – показатель степени учитывающий материал инструмента n = 09 (табл.9);
Рассчитаем величину развиваемого усилия закрепления на штоке пневмоцилиндра Q Н используя формулы из [9]
где D – диаметр поршня цилиндра D = 170 мм;
p – давление воздуха в цилиндре p = 04 МПа;
– коэффициент полезного действия пневмоцилиндра = 09;
Определим силу закрепления заготовки W Н передаваемую клиноплунжерным механизмом
где Q усилие закрепления на штоке пневмоцилиндра Q = 8167 Н;
α угол клина α = 5°50';
φпр приведенный угол трения;
tg φ2 tg φ1 коэффициенты трения tg φ2 = tg φ1 = 01;
Схему сил действующих в приспособлении при зажиме заготовки представляем на рисунке 3.
Определим необходимую силу закрепления заготовки Wн Н по методике изложенной в [10].
где Pz главная составляющая силы резания Pz = 1450 Н;
угол в плане клинового поводка =45°;
Rз расстояние от оси устройства до точки приложения силы Rз = 425 мм;
Сравниваем требуемое значение силы закрепления Wн и фактическое развиваемое Q
Делаем вывод о том что пневмопривод приспособления позволяет вести обработку на заданных режимах резания.
Рисунок 3 – Схема сил действующих в приспособлении при закреплении заготовки.
3Расчет приспособления на прочность
Произведем проверку на прочность болтовых соединений неподвижного корпуса с плитой пользуясь рекомендациями [11]. По формуле 1.32 [11] рассчитаем необходимый внутренний диаметр резьбы d1 мм
где Fр – суммарная нагрузка на болт Н;
допускаемое напряжение = 160 МПа (табл.1.1и 1.2);
Вычислим расчетную суммарную нагрузку на болт по формуле
где Fзат сила затяжки болта Н;
F внешняя нагрузка Н;
где F1 главная составляющая силы резания F2 = 1450 Н;
F1 горизонтальная составляющая силы резания F1 = 400 Н;
F3 величина усилия зажима F3 =8167 Н;
n – число болтов крепящих неподвижный корпус n = 4;
где Кзат коэффициент затяжки Кзат = 4 (стр.41 [11]);
Тогда по формуле (12.3.1)
По полученному значению внутреннего диаметра резьбы выбираем болт М16.
4Расчет приспособления на точность
Расчет приспособления на точность будем производить в соответствии с методикой изложенной в [12].
Определяем допуск на изготовление приспособления Тпр мм для обеспечения точности размера 26+0.5 (глубина паза) по формуле:
где Т – допуск на обработку мм;
Kт – коэффициент учитывающий отклонение рассеяния значений составляющих величин от закона нормального распределения kт = 18;
Kт1 коэффициент учитывающий уменьшение предельного значения погрешности базирования при работе на настроенных станках kт1 = 08;
Kт2 коэффициент учитывающий долю погрешности обработки в суммарной погрешности вызванной факторами не зависящими от приспособления kт2 = 07;
б погрешность базирования заготовки мм;
з погрешность закрепления мм;
у погрешность установки приспособления на станке мм;
и погрешность связанная с износом элементов приспособления мм;
п погрешность от перекоса режущего инструмента мм;
w экономическая точность обработки паза w = 0140 мм (табл. П10 [12]);
Погрешность базирования заготовки в соответствии с рекомендациями таблицы 3.1 [12] принимаем равной
Погрешность закрепления исключаем из расчетов т.к. пневмопривод обеспечивает постоянное усилие зажима.
Вследствие надежного контакта установочной плоскости приспособления с плоскостью стола станка принимаем погрешность установления приспособления на станке равной
Погрешность связанную с износом элементов приспособления принимаем равной и = 0 так как приспособление предусматривает регулировку которая производится сменными призмами.
Так как в приспособлении присутствуют направляющие элементы то погрешность от перекоса инструмента будет равна
Таким образом по формуле (12.4.1) имеем
Делаем вывод что допуск параллельности зажимающей шпильки приспособления относительно плоскости плиты должен составлять Т = 0074 мм.
В результате выполнения данного курсового проекта был проведен полный анализ и разработка технологического процесса получения шибера в условиях крупносерийного производства. Важнейшим этапом проектирования технологии является назначение маршрутного техпроцесса обработки выбор оборудования режущего инструмента и станочных приспособлений.
В ходе курсового проекта была проведена проверка соответствия выбранной заготовки размерам получаемой детали путем расчетов припусков на обработку.
По отношению к базовому техпроцессу был предложен ряд изменений:
изменена последовательность операций для получения более высокого качества получения размеров;
заменены модели металлорежущего оборудования и режущего инструмента.
В курсовом проекте были рассчитаны режимы резания для всех операций двумя методами – аналитическим и по нормативам. Расчет режимов резания позволил не только установить оптимальные параметры процесса резания но и определить основное время на каждую операцию сократив тем самым время обработки.
Экономические расчеты показали что проектируемый вариант технологического процесса изготовления вала является более эффективным так как обеспечивает минимум приведенных затрат на единицу продукции.
Также в курсовом проекте была усовершенствована конструкция станочного приспособления для обработки шпоночных пазов что позволило снизить его металлоемкость и сложность. Были проведены расчеты на прочность и точность подтвердившие правильность нововведений.
Горбацевич А.Ф. Курсовое проектирование по технологии машиностроения Шкред В.А.. - Мн.: Выш. школа 1983 – 256 с.
Справочник технолога-машиностроителя: Т.1 Под ред. А.Г. Косиловой и Р.К. Мещерякова. 4-е изд. перераб. и доп. М.: Машиностроение 1985.
Справочник технолога-машиностроителя: Т.2 Под ред. А.Г. Косиловой и Р.К. Мещерякова. 4-е изд. перераб. и доп. М.: Машиностроение 1985.
Обработка металлов резанием: Справ. Под ред. Г.А. Монахов В.Ф. Жданович Э.М. Радинский и др. М.: Машиностроение 1974. 600 с.: ил.
Руденко П.А. Проектирование и производство заготовок в машиностроении: Учеб. пособие Ю.А. Харламов В.М. Плескач; К.: Выща шк. 1991.247 с.; ил.
Режимы резания металлов: Справочник Под ред. Ю.В. Барановского – М.: Машиностроение 1972.
Дипломное проектирование по технологии машиностроения: Учеб. пособие для вузов В.В. Бабук П.А. Горезко К.П. Забродин и др.; Под ред. В.В. Бабука. Мн.: Выш. школа 1979. 464 с. ил.
Проектирование технологических процессов в машиностроении: Учеб. пособие для вузов И.П. Филонов Г.Я. Беляев Л.М. Кожуро и др.; Под ред. И.П. Филонова. Мн.: УП ”Технопринт” 2003. 910 с.
Ансеров М.А. Приспособления для металлорежущих станков. М.: Машиностроение 1975. 651с.: ил.
Технологическая оснастка. Учебник для студентов машиностроит. специальностей вузов М.Ф. Пашкевич Ж.А. Мрочек Л.М. Кожуро В.М. Пашкевич; Под ред. М.Ф. Пашкевича. – Мн .:Адукацыя и выхаванне 2002. – 320 с .: ил.
Иванов М.Н. Детали машин: Учеб. для студентов втузов Под ред. В.А Финогенова. 6-е изд. перераб. М.: Высш. школа 1998. 383 с.: ил.
Горохов В.А. Проектирование и расчет приспособлений: Учеб. пособие для студентов вузов машиностроительных специальностей Мн.: Выш. шк. 1986. – 238 с.: ил.
Лукашенко В.А. Курсовое проектирование по технологии машиностроения. Методические указания по курсовому проектированию для студентов специальности Т.03.01.00 – Технология и автоматизация машиностроения. – Могилев: МГТУ 2001. 48 с.
Комплект документов на технологический процесс
изготовления вала № 5.3М.001-01
Карты контроля.frw

Наименование оборудования
Белорусско-Российский
Прибор ТПП-2 (по Виккерсу)
ность и параллельность
Проверить наличие фасок и
отсутствие заусенцев
Проверить шероховатость
Образцы шероховатости
Проверить угловые размеры
Наименование операции
Сталь 38Х2МЮА ГОСТ 4548-75
Проверитьперпендикуляр-
Приспособление контрольное спе-
Проверить линейные размеры:
Микрометр МК(0-25) ГОСТ6507-80
Карты операционные (все).frw

Тиски станочные 7200-0225-03 ГОСТ 16518-96; фреза торцовая насадная
Патрон четырёхкулачковый с независимым перемещением кулачков ГОСТ 3890-72; резец расточной Т15К6
ГОСТ 18882-73; скоба СР 100 ГОСТ 11098-75;
пробка 8221-3111 7Н ГОСТ 17758-72
Патрон четырёхкулачковый с независимым перемещением кулачков ГОСТ 3890-72;
резец 2100-2195 ЦМ-32
; скоба СР 100 ГОСТ 11098-75;
Приспособление фрезерное; фреза концевая
Приспособление фрезерное; фреза Т- образная специальная (36
Тиски станочные 7200-0450-01 ГОСТ 14904-69; фреза торцовая насадная
прибор 8734-4084; эталон 8736-4087;
Магнитная плита ГОСТ 16528-81 (320 круг 300 Микрометр
МК(25-50) ГОСТ 6507-80;
прибор 8744-4084; эталон 8746-4087;
Наименование операции
Обозначение программы
Сталь 38Х2МЮА ГОСТ 4548-75
ГОСТ 3.1404-86 Форма 3
Установ Г 4. Фрезеровать поверхность 4
Установ Д 5. Фрезеровать поверхность 5
Установ Е 6. Фрезеровать поверхность 6
Установ А 1. Фрезеровать поверхность 1
Установ Б 2. Фрезеровать поверхность 2
Установ В 3. Фрезеровать поверхность 3
Контроль рабочим 100%
Точить поверхность 1
Фрезеровать поверхности 1
Установ А 1. Фрезеровать угол поверхность 1
Установ Б 2. Фрезеровать угол поверхность 1
Установ А 1. Шлифовать поверхность 1
Маршрутная.DOC
Белорусско-Российский университет
Сталь 38Х2МЮА ГОСТ 4543-75
Код наименование операции
Обозначение документа
Код наименование оборудования
1 Заготовительная ИОТ № 69
5Фрезерная с ЧПУ ИОТ № 67
Р12.Ф3 3 15 1 100 19 2549
0Токарная с ЧПУ ИОТ № 65
К20.Ф3 5 11 1 100 6 15619
Р12.Ф3 3 15 1 100 14 0604
0Фрезерная с ЧПУ ИОТ № 67
Р12.Ф3 3 15 1 100 14 0675
ГОСТ 3.1404-86 Форма 1
Р12.Ф3 3 15 1 100 9 106
0Плоскошлифовальная ИОТ № 66
М150 2 11 1 100 7 2484
Р12.Ф3 3 15 1 100 9 0907
0Термическая ИОТ № 80
термопечь 5756 №040128. 3 1 40 1100
5Плоскошлифовальная ИОТ № 66
М150 2 11 1 100 8 39483
Эскизы.cdw

Операция 005 - фрезерная с ЧПУ
Операция 025 - фрезерная с ЧПУ
Операция 045 - плоскошлифовальная
Размер обеспечивается инструментом
Белорусско-Российский
Операция 010 - токарная с ЧПУ
Операция 015 - фрезерная с ЧПУ
Операция 020 - фрезерная с ЧПУ
Приспособа.cdw

Допуск параллельности поверхности
Допуск перпендикулярности поверхности
Общие допуски по ГОСТ 30893.1 - m.
спецификация сб большая.doc
Белорусско-Российский
университет гр.ТМА-021
Маршрутная.DOC
Белорусско-Российский университет
Сталь 38Х2МЮА ГОСТ 4543-75
Код наименование операции
Обозначение документа
Код наименование оборудования
1 Заготовительная ИОТ № 69
5Фрезерная с ЧПУ ИОТ № 67
Р12.Ф3 3 15 1 100 19 2549
0Токарная с ЧПУ ИОТ № 65
К20.Ф3 5 11 1 100 6 15619
Р12.Ф3 3 15 1 100 14 0604
0Фрезерная с ЧПУ ИОТ № 67
Р12.Ф3 3 15 1 100 14 0675
ГОСТ 3.1404-86 Форма 1
Р12.Ф3 3 15 1 100 9 106
0Плоскошлифовальная ИОТ № 66
М150 2 11 1 100 7 2484
Р12.Ф3 3 15 1 100 9 0907
0Термическая ИОТ № 80
термопечь 5756 №040128. 3 1 40 1100
5Плоскошлифовальная ИОТ № 66
М150 2 11 1 100 8 39483
Заготовка.cdw

Кривизна прутка не должна превышать 0
Допустимая кривизна реза прутка не должна превышать 5 мм.
Твёрдость прутка менее 20 HRC.
Поковку получить в четыре перехода.
Размеры после отрезной операции
Размеры после осадки
Размеры после прошивки
Н=54мм и диаметр отверстия
Приспособа.cdw

Допуск параллельности поверхности
Допуск перпендикулярности поверхности
Общие допуски по ГОСТ 30893.1 - m.
Рекомендуемые чертежи
- 24.01.2023
- 29.08.2014
- 29.08.2014