Цилиндрический 2-х ступенчатый редуктор DOC CDW




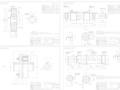

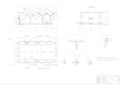
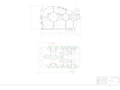
- Добавлен: 24.01.2023
- Размер: 1 MB
- Закачек: 0
Описание
Состав проекта
![]() |
![]() |
![]() ![]() ![]() ![]() |
![]() ![]() ![]() |
![]() ![]() ![]() ![]() |
![]() |
![]() ![]() ![]() ![]() |
![]() ![]() ![]() ![]() |
![]() ![]() ![]() ![]() |
![]() ![]() ![]() |
![]() ![]() ![]() |
![]() ![]() ![]() |
![]() ![]() ![]() ![]() |
![]() ![]() ![]() |
![]() ![]() ![]() |
![]() ![]() ![]() |
![]() ![]() ![]() ![]() |
![]() ![]() ![]() ![]() |
![]() ![]() ![]() ![]() |
![]() ![]() ![]() |
Дополнительная информация
Спецификация Ведомость.dwg

Ведомость курсового проекта
Эскизный проект редуктора
Сборочный чертеж муфты
Пояснительная записка
Анотация.doc
Расчёт ведётся по следующим исходным данным:
Частота вращения окружная сила Ft = 2.8кН;
скорость движения ленты V = 1.05 мс;
диаметр барабана D = 0.250 м;
срок службы Lh = 24·103 час.
В ходе выполнения курсового проекта подбирается электродвигатель выполняется кинематический расчёт привода расчёт быстроходной цилиндрической передачи редуктора расчёт тихоходной цилиндрической передачи редуктора расчёт цепной передачи предварительный расчёт валов конструктивный расчёт зубчатых колёс конструктивные расчёт размеров корпуса и крышки редуктора первый этап компоновки редуктора второй этап расчёта валов проверочный расчёт подшипников на долговечность второй этап компоновки редуктора проверка прочности шпоночных соединений уточнённый расчёт валов посадки зубчатого колеса звездочки и подшипников выбор сорта масла сборка редуктора выбор муфты и проверочный расчёт.
Редуктор компонуется и вычерчивается на формате А1 в соответствии с техническими требованиями.
Данный редуктор предназначен для работы в умеренных условиях эксплуатации.
Спецификация Редуктора.dwg

Спецификация Редуктора 2.dwg

Эскизная компановка А1.dwg

Планы скоростей механизма
Планы ускорений механизма
ДМ 07.06.03.00.000 ЭП
Спецификация Муфты.dwg

Контрольная2.doc
Предварительный расчет валов выполняю на кручение по пониженному допускаемому напряжению []К = 15 35 МПа с учётом деформации изгиба и концентрации напряжений
Ориентировочный диаметр входного участка вала [4 с. 7]
Где ТК1 – крутящий момент возникающий в расчетном сечении вала
[]К – допускаемое напряжение на кручение МПа;
Диаметр входного конца вала согласовую с диаметром вала электродвигателя dэ = 28
dВ1 = (0.8 1.2) · 28 = 22.4 33.6
Диаметр вала под подшипник [4 с. 8]
dП1 = 25 + 5 = 30 мм
Принимаю dП1 = 30 мм
Диаметр буртика под подшипник [4 с. 9]
dБП1 = 30 + 5 = 35 мм
Диаметр вала под шестерней
Принимаю dШ1 = 35 мм
Если диаметр впадин зубьев шестерни:
df1 ≤ dБП1 + (7 9) · m
где – m модуль зацепления быстроходной передаче
85 ≤ 35 + (7 9) · 2 = 49 53
Так как 37.85 ≤ 49 53 мм то шестерню выполняю за одно с валом
Диаметр вала под колесом и шестерней [4 с. 7]
Где ТК2 – крутящий момент возникающий в расчетном сечении вала
Принимаю dК2 = 35 мм
dП2 = 35 – 5 = 30 мм
Принимаю dП2 = 30 мм
Определяю положение шестерни на валу
Если df1 ≥ dБП2 + (7 9) · m
где – m модуль зацепления тихоходной передаче
≥ 35 + (7 9) · 2.5 = 52.5 57.5
Так как 80 ≥ 52.5 57.5 мм то шестерню выполняю насадной
Тихоходный вал проектирую в той же последовательности что и быстроходный.
Ориентировочный диаметр выходного вала [4 с. 7]
Где ТК3 – крутящий момент возникающий в расчетном сечении вала
Принимаю dВ3 = 35 мм
dП3 = 35 + 5 = 40 мм
Принимаю dП3 = 40 мм
dБП3 = 40 + 5 = 45 мм
Диаметр вала под колесо
Принимаю dK3 = 45 мм
Конструктивные размеры зубчатых колес [2 с. 18]
1 Быстроходная ступень
Шестерню выполняю за одно с валом ее размеры:
d1 – делительный диаметр шестерни
da1 – диаметр окружности вершин зубьев шестерни
df1 – диаметр окружности впадин зубьев шестерни
b1 – ширина шестерни
где b2 – ширина колеса
b1 = 40 + (5 10) = 45 50
Принимаю конструктивно b1 = 45 мм
d2 – делительный диаметр колеса
da2 – диаметр окружности вершин зубьев колеса
df2 – диаметр окружности впадин зубьев колеса
Диаметр ступицы колеса:
где dК2 – диаметр промежуточного вала под колесом
dст = 1.6 · 35 = 56 мм
Принимаю dст = 56 мм
Длина ступицы колеса:
Принимаю lст = 48 мм
Толщина обода колеса:
где m – модуль быстроходной ступени
= (2.5 4) · 2 = 5 8 мм
Толщина диска колеса:
с = 0.3 · 40 = 12 мм
Диаметр центровой окружности:
D = 0.5 · (D0 + dст)
D0 = 152.14 – 2 · 8 = 136.14 мм
D = 0.5 · (136.14 + 56) = 96.07 мм
Принимаю dотв = 20 мм
2 Тихоходная ступень
Шестерня изготовлена штамповкой
b1 = 28 + (5 10) = 33 38
Принимаю конструктивно b1 = 38 мм
где dК3 – диаметр тихоходного вала под колесом
dст = 1.6 · 45 = 72 мм
Принимаю dст = 72 мм
Принимаю lст = 54 мм
= (2.5 4) · 2.5 = 6.25 10 мм
с = 0.3 · 28 = 8.4 мм
Толщина центровой окружности:
D0 = 190 – 2 · 8 = 174 мм
D = 0.5 · (174 + 72) = 123 мм
Принимаю dотв = 26 мм
Конструктивные размеры корпуса редуктора [5 с. 12]
1 Толщина стенки редуктора ≥ 8
2 Толщина стенки крышки редуктора 1 ≥ 8
= 0.02 · 140 + 3 = 5.8 мм
3 Толщина верхнего фланца корпуса
S = (1.5 1.75) · 8 = 12 14
4 Толщина нижнего фланца корпуса
S2 = 2.35 · 8 = 18.8 мм
5 Толщина фланца крышки редуктора
S1 = (1.5 1.75) · 8 = 12 14 мм
6 Диаметр фундаментных болтов
Принимаю болты диаметром d1 = 16 мм с резьбой М16
7 Число фундаментных болтов
где L0 B0 – длина и ширина основания корпуса мм. Во всех случаях Z ≥ 4
8 Диаметр болтов стягивающих корпус и крышку у бобышек
d2 = (0.7 0.75) · 16 = 11.2 12 мм
Принимаю болты диаметром d2 = 12 мм с резьбой М12
9 Диаметр болтов стягивающих фланцы корпуса и крышки
d3 = (0.5 0.6) · 16 = 8 9.6 мм
Принимаю болты диаметром d3 = 8 мм с резьбой М8
10 Ширина опорных поверхностей нижнего фланца корпуса
m = 40 + 1.5 · 8 = 52 мм
11 Толщина ребер корпуса
С1 = (0.8 1) · 8 = 6.4 8 мм
12 Минимальный зазор между колесом и корпусом
b = 1.2 · 8 = 9.6 мм
13 Координата стяжного болта d2 у бобышки
С2 = (1.0 1.2) · 12 = 12 14.4 мм
Компановка редуктора
Первый этап компановки цилиндрического двух ступенчатого редуктора.
Компановку редуктора выполняю в два этапа.
Первый этап компановки редуктора выполняю с целью определения положения зубчатых колёс и звёздочки цепной передачи относительно опор.
1 Компановачный чертёж выполняю в одной проэкции разрез по осям валов. Провожу параллельные линии (оси валов на межосевом расстоянии быстрроходной и тихоходной ступени) вычерчиваю цилиндрическиелёса упрощенно в виде прямоугольников.
2 Отчерчиваю внутренюю стенку корпуса.
Растояние от внутренней стенки редуктора до торца вращающейся детали е1 = (1.0 1.2) ·
е1 = (1.0 1.2) · 8 = 8 9.6
Рстояние от торца подшипника качения до внутренней стенки корпуса редуктора е = S при v 3 мс
е = 8. Наименьший зазор между внутренней стенкой крышки и колесом b = 1.2 S
Растояние между вращающимся колесами смежных ступений
е2 = (0.5 2.0) · 8 = 12 16 мм
Растояние от окружности выступа наибольшего колеса до внутренней поверхности днища
b0 = (5 10) ·2.5 = 12.5 25 мм
3 Предварительно намечаю радиально шариковые подшипники лёгкой серии
Условное обозначение
4 Решаю вопрос осмазывании подшипников. Принимаю для подшипников пластичный смазывающий материал.
Для предотвращения вытекания смазки внутрь корпуса и вымывания пластичного смазывающего материалла жидким маслом из зоны зацепления устанавливаю мазеудерживающие кольца.
Из первого этапа компановки для быстроходного вала
Для промежуточного вала
Для тихоходного вала
Второй этап расчета валов
Рис. 9.1 – Схема нагружения валов
Из ранее полученных расчетов:
Окружная сила Ft1 = 496.3 H;
Радиальная сила Fr1 = 184.34 H;
Сила муфты Fм = 360 Н.
Из первого этапа компоновки редуктора:
1.1 Определяю реакцию опор
4.34 + 184.34 – 184.34 – 184.34 = 0;
– 360 + 496.3 + 496.3 - 30 - 604 = 0
1.2 Изгибающие моменты
1.3 Суммарные изгибающие моменты
По найденным значениям строю эпюры изгибающих моментов
1.4 Построение эпюр крутящего момента
Крутящий момент на быстроходном валу:
1.5 Определение диаметра вала в предположетельно опасном сечении
Мприв – приведенный момент Нм
По полученным значениям строю эпюры приведенных моментов.
Наиболее опасное сечение в точке С.
Принимаю [-1] = 70мП
Из предварительного расчета валов диаметр в точке С равен 30 мм условие прочности выполняется.
Окружная сила Ft2 = 1757.6 H;
Радиальная сила Fr2 = 653 H;
Из первого этапа компановки редуктора:
2.1 Определение реакций опор
-184.34 - 184.34 + 653 - 142 - 142 = 0;
6.3 – 1757.6 + 496.3 + 383 + 383 = 0
Так как вал симетричен считаю моменты только одной половины вала.
2.2 Изгибающие моменты
По найденным значениям строю эпюры изгибающих моментов.
2.3 Суммарные изгибающие моменты
2.4 Построение эпюр крутящего момента
2.5 Определение диаметра вала в предположетельно опасном сечении
Наиболее опасное сечение в точке D.
Из предварительного расчета валов диаметр в точке В равен 30 мм то условие прочности выполняется.
Из первого этапа компоновки редуктора:
3.1 Определение реакций опор
48 – 1757.6 + 1285 -1376 = 0
-1757 + 879 + 879= 0
3.2 Изгибающие моменты
3.3 Суммарные изгибающие моменты
3.4 Построение эпюр крутящего момента
3.5 Определение диаметра вала в предположетельно опасном сечении
Наиболее опасное сечение – под подшипником в точке А.
Из предварительного расчета валов диаметр в точке А равен 35 мм условие прочности выполняется.
Провеорчный расчет подшипников качения на долговечность
1.1 По условиям работы пошипникового узла ранее был выран для обеих опор наиболее дешевый шариковый радиальный подшыпник легкой серии 206.
1.2 Для этих подшипников находим из [6с.24n1] базовую динамическую грузоподъемность Сr = 15.3 кН и базовую стическую радиальную грузоподъемность С0 = 10.2 кН.
1.3Сумарная радиальная нагрузка
1.4 Так как подшипники радиальные то осевые состовляющие Rs = 0
Рис. 10.1 – Быстроходный вал
1.5 Эквивалентная динамическая нагрузка
Эквивалентная динамическая нагрузка рассчитывается для наиболее нагруженного подшипника. Наиболее нагруженным является подшипник в точке В.
Где Ra – осевая сила
XY – коэффициенты радиальной и осевой нагруок выбираются в зависимости от отношения
V – коэффициент вращения учитыввающий зависимость долговечности подшипника от условий вращения внутреннего кольца подшипника
kt = коэффициент учитывающий влияниетемпературы на долговечность подшипника при температуре до 100°C
1.6 Расчетная (требуемая) динамическая радиальная грузоподъемностьподшипника
где – угловая скорость вала
Lh – требуемый ресурс
m – коэффициент для шариковых подшипников
Условие пригодности соблюдены. Принимаем подшипник 206 удовлетворяющий заданному режиму работы.
1.7 Ресурс предварительно выбранного шарикового радиального подшипника легкой серии 206
Расчётная долговечность больше требуемой следовательно принятый подшипник 206 пригоден.
2.1 По условиям работы пошипникового узла ранее был выран для обеих опор наиболее дешевый шариковый радиальный подшыпник легкой серии 206.
2.2 Для этих подшипников находим из [6с.24n1] базовую динамическую грузоподъемность Сr = 15.3 кН и базовую стическую радиальную грузоподъемность С0 = 10.2 кН.
2.3Сумарная радиальная нагрузка
2.4 Так как подшипники радиальные то осевые состовляющие Rs = 0
Рис. 10.2 – Промежуточный вал
2.5 Эквивалентная динамическая нагрузка
2.6 Расчетная (требуемая) динамическая радиальная грузоподъемностьподшипника
2.7 Ресурс предварительно выбранного шарикового радиального подшипника легкой серии 206
3.1 По условиям работы пошипникового узла ранее был выран для обеих опор наиболее дешевый шариковый радиальный подшыпник легкой серии 206.
3.2 Для этих подшипников находим из [6с.24n1] базовую динамическую грузоподъемность Сr = 32 кН и базовую стическую радиальную грузоподъемность С0 = 17.8 кН.
3.3Сумарная радиальная нагрузка
3.4 Так как подшипники радиальные то осевые состовляющие Rs = 0
Рис. 10.3 Тихоходный вал
3.5 Эквивалентная динамическая нагрузка
3.6 Расчетная (требуемая) динамическая радиальная грузоподъемностьподшипника
Условие пригодности соблюдены. Принимаем подшипник 208 удовлетворяющий заданному режиму работы.
3.7 Ресурс предварительно выбранного шарикового радиального подшипника легкой серии 208
Расчётная долговечность больше требуемой следовательно принятый подшипник 208 пригоден.
Вотрой этап компоновки редуктора
Второй этап компановки имеет целью конструктивно оформить зубчастые колеса вала подшипниковые узлы подготовить данные для проверки прочности валов и некоторых других деталей.
Вычерчиваю зубчатые колеса и валы по конструктивным размерам найденным ранее.
Коструирую узел ведущего вала:
)Наношу осевые линии удаленные от середины редуктора на расстояние . Используя эти линии вычерчиваю в разрезе подшипники качения.
)Между торцом подшипников и внутренней стенкой корпуса вычерчиваю мазеудерживающие кольца. Их торцы должны выступвть внутрь корпуса на 1- 2 мм от внутренней стенки. Вэтом случае эти кольца будут выполнять одновременно роль маслоотбрасывающих колец.
)Вычерчиваю крышки подшипников с уплотнениями покладками толщиной около 1 мм и болтами.
Длину присоединительного конца вала определяю длиной соединительной полумуфты.
Аналогично конструирую узел пормежуточного вала. При этом обращаю внимание на следующие особенности:
)Для фиксации зубчатых колес предусматриваю буртик с одной стороны и установку распорной втулки с другой стороны.
)Место перехода диаметра вала от dк к dп смещаю на 2-3 мм внутрь распорной втулки с тем чтобы гарантировать прижатие мазеудерживающего кольца к торцу втулки а не к заплечнику вала.
)Вычерчиваю подшипники мазеудерживающие кольца крышки подшипниковых узлов с покладками и болтами.
Проверка прочности шпоночных соединений.
Шпонки призматические с округлёнными торцами. Размеры сечений шпонок и пазов а так же длину шпонок – по ГОСТ 23360-78 [8с.169табл.8.9]
Материал шпонок – сталь 45 нормализованная.
Напряжение смятия и условие прочности определяю по формуле:
где Т – момент передаваемый валом
t - глубина паза вала
Допускаемые напряжения смятия при стальной ступице:
1 Быстроходный вал.
Выбираю шпонку под муфтой:
2 Промежуточный вал.
Выбираю шпонки под колесами:
Выбираю шпонку под шестерней:
Выбираю шпонки под колесом:
Выбираю шпонки под звездочкой цепной передачи:
Условие не выполнено.
Так как больше допускаемого напряжения смятия то установим 2 шпонки под углом 180° тогда каждая шпонка воспримет половину нагрузки.
Уточнение расчетов валов
Уточнённый расчёт состоит в определении коэффициентов запаса прочности для опасных сечений и сравнении их с требуемыми (допускаемыми) значениями .
Прочность соблюдена при .
Для валов редуктора:
Расчет провожу для предположительно опасных сечений каждого из валов.
Примем что нормальные напряжения от изгиба изменяются по симметричному циклу а касательные от кручения – по нулевому (пульсирующему).
Рис.13.1 – Опасное сечение быстроходного вала.
Момент вала тот же что для шестерни (шестерня выполнена за одно целое с валом) т.е сталь 45 с термообработкой улучшение
По [8с.34. табл. 3.3] при диаметре заготовки 50мм среднее значение в = 440 мПа
Предел выносливости при симметричном цикле изгиба
Пределы выносливости при симметричном цикле касательных напряжений;
Это сечение при передачи вращательного момента от эл. двигателя через муфту рассчитываю на кручение. Концентрацию напряжений вызывает наличие шпоночной канавки.
Коэффициент запаса прочности:
где – v = m – амплитуда и среднее напряжение от нулевого цикла.
Принимаю k = 1.7[7c.165табл.8.5]; = 0.1[7c.166табл.8.5]; = 0.785[7c.165табл.8.5].
Такой большой коэффициент запаса прочности обусловлен тем что диаметр вала был увеличен для соединения его стандартной муфтой с валом электродвигателя.
Рис.13.1 – Опасное сечение промежуточного вала.
Материал вала – сталь 45 нормализованная как и в предыдущем случае.
Предел выносливости при симметричном цикле изгиба;
Предел выносливости при симметричном цикле касательных напряжений;
Диаметр вала в этом сечении Концентрация напряжений обусловлена наличием шпоночной канавки:
Момент сопротивления кручению:
Принимаю k = 1.49[7c.165табл.8.5]; = 0.1[7c.166табл.8.5]; = 0.73[7c.165табл.8.5].
Коэффициент запаса прочности по нормальным напряжениям
Момент сопротивления изгибу:
Принимаю k = 1.59[7c.165табл.8.5]; = 0.15[7c.166табл.8.5]; = 0.85[7c.166табл.8.5].
Результирующий коэффициент запаса прочности для сечения А – А;
Такой большой коэффициент запаса прочности обусловлен тем что диаметр вала был увеличен для подбора стандартного подшипника.
Рис.13.1 – Опасное сечение тихоходного вала.
Материал вала – сталь 45 термообработка - улучшение.
По [8.с.34 табл. 3.3] при значении диаметра до 90 мм среднее =570МПа.
Рассчитываем сечение Б – Б. Концентрация напряжений обусловлена наличием шпоночного паза под звездочку цепной передачи.
Коэффициент запаса прочности;
где - амплитуда и среднее напряжение от нулевого цикла.
Посадки зубчастых колес звездочки подшипников
Посадки деталей на валы редуктора назначаю в соответствии с ГОСТ 25347 – 82.
Посадка полумуфты на быстроходный вал редуктора
Посадка зубчастого колеса на вал
Посадка звездочки цепной передачи на тихоходный вал редуктора
Шейки валов под подшипники выполняю с отклонением вала к6. Отклонения отверстий в корпусе под наружные кольца по Н7.
Смазывание зубчатого зацепления производится окунанием зубчатого колеса промежуточного вала в масло заливаемое внутрь корпуса до уровня обеспечивающего погружения колеса примерно на 10 мм.
Согласно [8с.253табл.10.8] устанавливаем вязкость масла. При контактных напряжениях и скорости рекомендуемая вязкость масла должна быть примерно равна . По [8с.253табл.10.10] принимаю масло индустриальное И-30А (по ГОСТ 20799-75).
Камеры подшипников заполняем пластичным смазочным материалом
УТ-1 периодически пополняем его через пресс-маслёнки.
Перед сборкой внутреннюю полость корпуса редуктора тщательно очищают и покрывают маслостойкой краской.
Сборку производят в соответствии со сборочным чертежом редуктора начиная с узлов валов.
- на ведущий вал насаживаем мазеудерживающие кольца и шарикоподшипники предварительно нагретые в масле до 80-100°С
- в промежуточный вал закладываем три шпонки 10 х 8 х 45 и напрессовывают шестерню до упора в буртик затем надевают распорную втулку и насаживают зубчатые колеса – одно до упора в буртик другое до упора во втулку напрессовывают мазеудерживающие кольца и устанавливают шарикоподшипники предварительно нагретые в масле.
- в тихоходный вал закладываем шпонки и напрессовываем зубчатое колесо до упора в бурт вала затем надеваем распорную втулку мазеудерживающие кольца и устанавливаем шарикоподшипники предварительно нагретые в масле.
Нормальная работа подшипников осуществляется с помощью их регулировки для чего применяю наборы тонких металлических прокладок устанавливаемых под фланцы крышек подшипников. Необходимая толщина набора прокладок может быть составлена из тонких металлических колец толщиной 01; 02; 04; 08 мм.
Собранные валы укладываем в основание корпуса редуктора и надеваем крышку корпуса покрывая предварительно поверхности стыка крышки и корпуса спиртовым лаком. Для центровки устанавливаем крышку на корпус с помощью двух конических штифтов; затягиваем болты крепящие крышку к корпусу.
После этого в подшипниковые камеры закладываем пластичную смазку ставим крышки подшипников с комплектом металлических прокладок для регулировки.
Перед постановкой сквозных крышек в проточки закладывают войлочные уплотнения пропитанные горячим маслом.
Проверяем проворачиванием валов отсутствие заклинивания подшипников (валы должны проворачиваться от руки) и закрепляем крышки винтами.
Далее на конец быстроходного вала в шпоночную канавку закладываем шпонку одевают муфту закрепляют ее торцевым креплением; винт торцевого крепления стопорят специальной планкой.
После этого на конец тихоходного вала в шпоночные канавки закладываем 2 шпонки 10 х 8 х20 устанавливаем звездочку и закрепляем ее торцевым креплением винт торцевого крепления стопорят специальной планкой.
Затем ввёртывают пробку маслоспускного отверстия с прокладкой и жезловым маслоуказателем.
Заливают в корпус масло и закрывают смотровое отверстие крышкой с прокладкой из технического картона закрепляют крышку болтами.
Собранный редуктор обкатывают и подвергают испытанию на стенде по программе устанавливаемой техническими условиями.
Выбор муфты и проверочный расчет
Для соединения вала электродвигателя и быстроходного вала редуктора выбираю упругую втулочно-пальцевую муфту по большему диаметру соединяемых валов. Материал полумуфт сталь 30 пальцев – сталь 45. Упругие элементы изготовлены из специальной резины.
Муфты выбирают по расчетному моменту и большему диаметру соединяемых валов.
- количество пальцев;
- диаметр расположения центров пальцев;
Пальцы рассчитывают на изгиб по условию прочности:
МПа 80МПа условие выполняется.
Втулка рассчитывается на смятие
181МПа 2МПа условие выполняется.
Аналитический обзор.doc
Редуктором называют механизм состоящий из зубчатых или червячных передач выполненный в виде отдельного агрегата и служащий для передачи вращения от вала двигателя к валу рабочей машины. Кинематическая схема привода может включать помимо редуктора открытые зубчатые передачи цепные или ремённые передачи.
Назначение редуктора – понижение угловой скорости и соответственно повышения вращающего момента ведомого вала по сравнению с ведущим. Механизмы для повышения угловой скорости выполненные в виде отдельных агрегатов называют ускорителями или мультипликаторами.
Редуктор состоит из корпуса (литого чугунного или сварного стального) в котором помещают элементы передачи – зубчатые колёса валы подшипники и т. д. В отдельных случаях в корпусе редуктора размещают также устройства для смазывания зацеплений и подшипников (например внутри корпуса редуктора может быть помещён шестерённый масляный насос) или устройства для охлаждения (например змеевик с охлаждающей водой в корпусе червячного редуктора).
Редуктор проектируют либо для привода определённой машины либо по заданной нагрузке (моменту на выходном валу) и передаточному числу без указания конкретного назначения. Второй случай характерен для специализированных заводов на которых организованно серийное производство редукторов.
Редукторы классифицируют по следующим основным признакам:
а) типу передачи (зубчатые червячные или зубчато-червячные);
б) числу ступеней (одноступенчатые двухступенчатые и т. д.);
в) типу зубчатых колёс (цилиндрические конические коническо-цилиндрические и т. д.);
г) относительному расположению валов редуктора в пространстве (горизонтальные вертикальные);
д) особенностям кинематической схемы (развёрнутая соосная с раздвоенной ступенью и т. д.).
Наиболее распространены двухступенчатые горизонтальные редукторы выполненные по развернутой схеме. Эти редукторы отличаются простотой но из-за несимметричного расположения колес на валах повышается концентрация нагрузки по длине зуба. Поэтому в этих редукторах применяют жесткие валы.
Соосная схема позволяет получить меньшие габариты по длине; это ее основное преимущество.
В соосных редукторах быстроходная ступень зачастую недогружена так как силы возникающие в зацеплении колес тихоходной ступени значительно больше чем в быстроходной а межосевые расстояния ступеней одинаковы
аwБ = awт. Указанное обстоятельство является одним из основных
недостатков соосных редукторов.
Кроме того к их недостаткам относят также:
а)большие габариты в направлении геометрических осей валов по сравнению с редукторами выполненными по развернутой схеме;
б)затруднительность смазывания подшипников расположенных в средней части корпуса;
в)большое расстояние между опорами промежуточного вала поэтому требуется увеличить его диаметр для обеспечения достаточной прочности и жесткости.
Очевидно применение соосных редукторов ограничивается случаями когда нет необходимости иметь два выходных конца быстроходного или тихоходного вала а совпадение геометрических осей входного и выходного валов удобно при намеченной общей компоновке привода.
Часто быстроходную ступень выполняют косозубой а тихоходную — прямозубой (это относится как к соосным так и к несоосным редукторам).
При раздвоенной быстроходной (или тихоходной) ступени колеса расположены симметрично относительно опор что приводит к меньшей концентрации нагрузки по длине зубьев чем при применении обычной развернутой или соосной схемы. Это позволяет иметь менее жесткие валы. Быстроходный вал редуктора должен иметь свободу осевого перемещения («плавающий» вал) что обеспечивается соответствующей конструкцией подшипниковых узлов; в редукторе с шевронными тихоходными колесами свободу осевого перемещения должен иметь и тихоходный вал. При соблюдении указанного условия нагрузка распределяется поровну между параллельно работающими парами зубчатых колес.
Двухступенчатые цилиндрические редукторы обычно применяют в широком диапазоне передаточных чисел: по ГОСТ 2185-66 u = 63 ÷ 63. Крупные двухступенчатые цилиндрические редукторы выпускаемые НКМЗ имеют
От целесообразной разбивки общего передаточного числа двухступенчатого редуктора по его отдельным ступеням в значительной степени зависят габариты редуктора удобство смазывания каждой ступени рациональность конструкции корпуса и удобство компоновки всех элементов передач.
Возможности получения больших передаточных чисел при малых габаритах обеспечивают планетарные и волновые редукторы.
В данном проекте разрабатывается механический привод с открытой цепной передачей.
Титульный лист.doc
Восточноукраинский национальный университет имени Владимира Даля
ПОЯСНИТЕЛЬНАЯ ЗАПИСКА
К курсовому проекту по дисциплине: «Детали машин»
Тема: «Привод ленточного конвейера».
студент гр. ОХП 27аз
проектаКравцова Э.М.
Северодонецк 2010 г.
Корпус А1.dwg

Планы скоростей механизма
Планы ускорений механизма
Неуказанные радиусы скруглений 3 мм max.
Неуказанные отклонения размеров: Отверстий -
валов - h 14; остальные IT142.
ДМ.07.06.03.00.001.СБ
Контрольная1.doc
1 Мощность на выходном валу редуктора.
2 Коэффициент полезного действия привода [1c.6 табл.1]
- к.п.д. закрытой цилиндрической передачи;
- к.п.д. пары подшипников;
- к.п.д. цепной передачи;
4 Требуемая мощность электродвигателя
5 Выбираю электродвигатель согласно справочным данным и условию. Рэд трехфазный асинхронный короткозамкнутый серии 4А100L4УЗ основного исполнения по ГОСТ 19523 у которого
6 Угловая скорость электродвигателя
7 Передаточное число привода
8 Разбиваем передаточное число по ступеням в соответствии с рекомендациями [1c.8 табл.2]
Предварительно принимаем согласно рекомендации
Для двухступенчатого редуктора выполненного по развернутой схеме
Принимаем Uб = 355 [1c.10 табл.4] тогда
Отклонение передаточного числа от заданного
9 Угловые скорости вращения всех валов:
вал электродвигателя:
быстроходного вала редуктора:
промежуточного вала редуктора:
тихоходного вала редуктора:
10 Мощность на валах:
на валу электродвигателя
на быстроходном валу редуктора
на промежуточном валу редуктора
на тихоходном валу редуктора
на выходном валу барабана
11 Вращающие моменты на валах:
на выходном валу привода
Расчёт цилиндрической зубчатой передачи
Быстроходная ступень
Вращающий момент на колесе Т2 = 782=39 (Н·м)
Скорость вращения колеса = 4214 (радс)
Передаточное число передачи U = 355
Время работы передачи Lh = 2·103(час).
1.Выбор материала и термической обработки для изготовления колес.
Согласно [2c.10табл.1] выбираю для изготовления колеса сталь 45 с термообработкой – нормализация и твердостью поверхности зубьев НВ (179 207) ; для шестерни – сталь 45 с термообработкой – улучшение и твердостью поверхности зубьев НВ (192 240) предел текучести
2 Расчет допускаемых напряжений.
Допускаемые контактные напряжения и напряжения изгиба определяем отдельно для колеса []H2 []F2 и шестерни []H1 []F1 в зависимости от материала термообработки с учетом времени работы.
где коэффициенты долговечности [2 с.8]:
Число циклов перемены напряжений за время работы передачи [2 с.8]
Число циклов перемены напряжений определяю в зависимости от средней твердости материала колес по графику [2 с.8 рис.5]
Средняя твердость материалов.
Число циклов перемены напряжений соответствующее пределу контактной выносливости:
коэффициенты долговечности для колеса
коэффициенты долговечности для шестерни
КHL1=KHL2=1; КFL1=KFL2=1 т.к. N1 > NHO1 и N1 > N2 >
для всех типов сталей
Согласно [2c.9табл.1] определяем [s]HO и [s]FO
Согласно [2с.9 табл.1] принимаем модуль передачи .
Допускаемые контактные напряжения и напряжения изгиба с учётом времени работы передачи:
Расчетные допускаемые напяжения:
Поскольку передача имеет косой зуб напряжения определяем по формуле [2с.9]
3 Проектировочный расчет зубчатой передачи
3.1 Межосевое расстояние передачи [2 с.10]
для косозубой передачи [2 с.10] Ка = 4300 – коэффициент концентрации напряжений при постоянной нагрузке.
при постоянном нагружении
Принимаю режим нагрузки средний III = 05.
а – коэфициент который принимают из ряда стандартных значений.
Тогда межосевое расстояние
Округляя до стандартного значения принимаю
3.2 Предварительные размеры колеса:
делительная окружность [2c.12]
где коєффициент Km = 58 – для косозубых передач [2c.13]
Найденное значение модуля округляю в большую сторону до стандартного [1с12 табл.4]
6 Угол наклона и суммарное число зубьев
Минимальный угол наклона зубьев [2c.12]
Суммарное число зубьев
Полученное значение ZΣ округляю в меньшую сторону до целого числа и определяю действительное значение угла:
Действительное значение угла наклона зубьев
3.4 Число зубьев шестерни и колеса
Число зубьев шестерни
округляю до целого большего значения
3.5 Фактическое передаточное число
Отклонение U от нужного:
3.6 Диаметры зубчатых колёс.
3.7 Делительные диаметры:
3.8 Диаметры окружностей вершин и впадин
3.9 Определяю силы в зацеплении [2c.13]
где a = 20° tga = 0364 для стандартного угла
3.10 Проверочный расчет зубьев колёс по напряжениям изгиба
Окружная скорость колеса
По [2c.14табл.6] степень точности передачи 9 поэтому КНα = 14
Коэффициент концентрации напряжения для колес которые прирабатываются во время работы КF0 = 1 [1c.15]
КFv = 104 – находим по таблице [2c.15 табл.8]
Коэффициент Y – находим по формуле [2c.16]
Коэффициент Yf2 = 361 Yf1 = 390 по [2c.16табл.9]
Расчётное напряжение изгиба в зубьях колеса и шестерни
что меньше []F2 = 19879×106 [Па];
что меньше []F1 = 216·106 (Па). Следовательно прочность на изгиб зубьев колёс обеспечена.
13 Проверка зубьев колеса на контактую прочность
Значения коэффициентов Кнα = 11; Кн = 27·105 – для косозубых колес [2с.16];
КН = 1; Кнv = 108 [2c.17табл.10]
Передаточное число UФ = 36.
По расчёту имеем: Т2 = 39 Н·м;
а = 01 м; b2 = 004 м.
Тогда расчётное контактное напряжение
что меньше []н = 39159 [МПа].
Вращающий момент на колесеТ2 = 17137 (Н·м)
Скорость вращения колеса2 = 187 (радс)
Передаточное число передачиU = 225
Время работы передачиLh = (час)
1 Выбор материала и термической обработки для изготовления колес [2c.9табл.1].
Выбираем для колеса сталь 45 с термической обработкой – улучшение твердостью поверхности поверхности зубьев – НВ (235 262);
для шестерни – сталь 45 с термической обработкой – улучшение твердостью поверхности зубьв – HB (269 302); .
2 Расчет допускаемых напряжений
Расчет ведем по допустимым напряжениям [2 с.8]
Средняя твердость материалов
Число циклов перемены напряжений соответствующее пределу контактной выносливости определяем по графику [2 с.8 рис.5]
KHL1= KHL2 =1; KFL1= KFL2 =1 т.к. N1 > NHO1 и N1 >
За расчетное допускаемое напряжение для прямозубых колес принимаю
[]H = [] =5143 [МПа]
Проектировочный расчет зубчатой передачи
3 Межосевое расстояние [2 с.10]
для прямозубой передачи [2 с.10] Ка = 4950 - коэф. концентрации напряжений
коэффициент концентрации напряжения при постоянном нагружении
Принимаю режим нагрузки средний III x = 05
коэфициент ширины колеса по межосевому расстоянию примем
(симитричное расположение)
Полученое межосевое растояние округляю в большую сторону до стандартного значения с ряда принимаю
4 Предварительные размеры колеса:
Принимаю ближайшее стандартное [2c.12]
где коєффициент Km = 66 – для прямозубых передач [2c.13]
Найденое значение модуля округляю в большую сторону до стандартного
6 Суммарное число зубьев
7 Число зубьев шестерни и колеса:
округляю до значения
8 Фактическое передаточное число
б96% 4% что можно допустить
9.1 Делительные диаметры:
9.2 Диаметры окружностей вершин и впадин
10 Определяю силы в зацеплении [2c.13]
11 Проверочный расчет на контактную прочность и напряжение напряжение изгиба.
Зубъя колёс проверяют на напряжения изгиба .
Расчетное значение напряжения изгиба в зубъях колеса
где - кэффициент который зависит от угла наклона
для прямозубых колес
Степень точночности определяю по скорости колеса
По [2c.14табл.6] степень точности передачи 9
Коэффициент концентрации напряжения для колес которые прирабатываются во время работы КF = 1 [2c.15табл.5]
Коэффициент динамической нагрузки принимаю по [2c.14табл.8]
Коэффициент формы зуба YF находим по [2c.15табл.9] в зависимости от числа зубъев шестерни и колеса
Проверяю зубъя колес на контактную прочность
где КНα = 111 КН = 11
КНV – коэффициент динамической нагрузки принимаю [2c.16табл.10] по окружной скорости и степени точности КНV = 11
что меньше []н = 5143 (МПа).
Расчёт цепной передачи
Рис.1. Схема цепной передачи
Мощность на малой (ведущей) звёздочке Р1 = 32 (кВт)
Частота вращения малой звёздчки
Передаточное число i = 22
Кратковременные перегрузки ТmaxTnom = 11
Угол наклона передачи к горизонту = 0
Число смен работы в сутки - две
1 Выбор числа зубьев малой (ведущей) звёздочки по [3c.16табл.П.1]. При передаточном числе i = 22 и частоте вращения n1 = 178 (обмин) число зубьев:
2 Определяем число зубьев большой (ведомой) звёздочки
Принимаем число зубьев Z2 = 55
3 Уточняем передаточное отношение цепной передачи
4 Коэффициент динамической нагрузки
Кд=1 [3c.16табл.П.2] поскольку нагрузка близка к равномерной и кратковременные перегрузки ТmaxТnom ≤ 11.
5 Коэффициент режима (продолжительности работы в течение суток)
Креж=125 поскольку принята двухсменная работа передачи [3c.18табл.П.11].
6 Коэффициент наклона передачи к горизонту
Кн=1 так как угол наклона передачи к горизонту =0о [3c.16табл.П.3].
7 Коэффициент способа регулировки натяжения цепи
Крег = 1 [3c.16табл.П.14].
8 Коэффициент смазки и загрязнения передачи
Предварительно принята скорость цепи V=115 мс. Передача открытая запылённая качество смазки удовлетворительное.
Кс=13 [3c.19табл.П.14].
9 Коэффициент межосевого расстояния
Кα=1 [3c.18табл.П.10] так как по соображениям долговечности цепи предварительно принято межосевое расстояние = 40Рц [3.c18табл.П.7]. Число шагов в цепи в межосевом расстоянии Рц = 40.
10 Коэффициент эксплуотации [3c.11]
11 Коэффициент числа зубьев [3c.12]
Базовое число зубьев (Z01 Z1) принимаем Z01=25 [3c.16табл.П.5]
12 Коэффициент частоты вращения [3c.12]
Базовую частоту вращения n0 определяем как ближайшую к расчётной [3c.16табл.П.5]. При n1 = 178(обмин)
13 Расчётная мощность [3c.12]
По [3c.16табл.П.5] при базовой частоте вращения n01 = 200 обмин ближайшая к n1 = 178 (обмин) и базовом числе зубьев Z01 = 25 выбираем допускаемую расчётную мощность [Pp] = 11 кВт.
Этой мощности соответствует цепь однорядная роликовая ПР-254-56700
14 Определяю параметры роликовой однорядной цепи [3c.17табл.П.6]
Разрушающая силаQ = 56700 Н
Диаметр роликаdр = 1588 мм
Масса одного метра цепиq = 257 кгм
Ширина цепиВвн = 2261 мм
15 Пригодность выбранной цепи проверяем по наибольшему допустимому шагу [Рц]ma 254 508 мм. Выбранная цепь пригодна для данных условий работы.
По скорости уточняем коэффициент смазки [3c.19табл.П.14]. Коэффициент остаётся без изменения.
17 Межосевое расстояние цепной передачи [3c.13]
18 Длина цепи в шагах (число звеньев в цепи)
Целое число шагов L'p =120
19.Уточняем межосевое расстояние при длине цепи 120 шагов цепи
Передача работает лучше при небольшом провисании холостой ветви цепи поэтому расчётное межосевое расстояние уменьшаем на (0002 0004)Окончательное межосевое растояние
Принимаю α = 49155 мм =0491 м.
20.Усилия в передаче:
Натяжение цепи от центробежных сил
Коэффициент провисания определяем по [3c.19табл.П.13]
Кf = 6 так как передача расположена горизонтально (=0).
Сила предварительного натяжения от массы цепи
где g = 981 мс2 – ускорение свободного падения.
Давление цепи на вал
Здесь сила Fmax – большее из двух значений Fv и F0. В данном случае F0 > Fv поэтому Fmax = F0= 7427 Н.
Натяжение ведущей ветви цепи
Натяжение ведомой ветви цепи
21.Размеры звёздочек
Делительный диаметр ведущей звёздочки
Делительный диаметр ведомой звёздочки
Диаметр окружности вершин зубьев ведущей звёздочки
Диаметр окружности вершин зубьев ведомой звёздочки
Диаметр окружности впадин зубьев ведущей звёздочки
Диаметр окружности впадин зубьев ведомой звёздочки
Ширина зубчатого венца звёздочки для однорядной цепи
Содержание.doc
Выбор электродвигателя и кинематический расчёт привода10
Расчёт быстроходной цилиндрической зубчатой передачи16
Расчёт тихоходной цилиндрической передачи26
Расчёт цепной передачи34
Предварительный расчёт валов40
Конструктивный расчёт зубчатых колёс44
Конструктивные размеры корпуса и крышки49
Первый этап компоновки редуктора51
Второй этап расчёта валов54
Проверочный расчёт подшипников на долговечность67
Второй этап компоновки редуктора73
Проверка прочности шпоночных соединений74
Уточнённый расчёт валов77
Выбор муфты и проверочный расчёт86
Литература.doc
Методические указания - «Расчет цепных передач» Северодонецк 2003г.
Методические указания - «Расчет цилиндрических зубчатых
передач» Северодонецк 2003г.
Киркач Н.Ф. Баласанян Р.А. «Расчёт и проектирование деталей машин» 4.1. - X.: Высшая школа 1988-142 с.
Киркач Н.Ф. Баласанян Р.А. «Расчёт и проектирование деталей машин» 4.2. - X.: Высшая школа 1988-142 с.
Методические указания - «Расчет радиальных и радиально-
упорных подшипников качения» Северодонецк 2003г.
Чернавский С.А. Боков К.Н. «Курсовое проэктирование деталей
мащин» - М.: Машиностроение 1988 - 416 с.
Детали А3.dwg

ДМ.07.06.02.00.000.CБ
Направление линии зуба
Номинальный исходный контур
Коэффийиент смещения
НВ192 240 2. Радиусы скруглений 1.6мм max. 3. Неуказанные предельные отклонения размеров Н12
НВ 260 285 2.Неуказанные радиусы скруглений 2 мм max. 3.Неуказанные предельные отклонения размеров Н12
Коэффициент смещения
НВ 241 285 2.Неуказанные радиусы скруглений 2 мм max. 3.Неуказанные предельные отклонения размеров Н12
Сборочный редуктора А1.dwg

Планы скоростей механизма
Планы ускорений механизма
Техническая характеристика 1. Мощность на выходном валу 2
кВт 2. Угловая скорость вращения тихоходного вала 18
радс 3. Передаточное число редуктора 17
4. Вращающий момент на тихоходном валу 171
Нм Технические требования 1. Зазоры в зацеплении и пятно контакта по степини i-3
точности 8-В ГОСТ 1643-81 i0
Редуктор обкатать без нагрузки в течении двух часов 3. Сборку
окраску и консервацию редуктора производить по заводским техническим условиям 4. Вредуктор залить 2
л масла И-30А 5. Размеры для справок
ДМ.07.06.03.00.000.СБ
Спецификация Редуктора 3.dwg

Введение.doc
Основными требованиями предъявляемыми к машинам являются работоспособность надёжность технологичность и экономичность.
При конструировании и изготовлении машин должны строго соблюдаться Государственные стандарты (ГОСТы).
Основными направлениями развития отечественного машиностроения являются: увеличение мощности и производительности машин быстроходности и равномерность хода повышение коэффициента полезного действия автоматизация рабочих циклов машин точность работы машины стандартизация и взаимозаменяемость деталей и узлов удобство и безопасность обслуживания компактность.
Рекомендуемые чертежи
- 25.01.2023
- 25.01.2023
- 25.01.2023