Токарно-револьверный станок 1К341




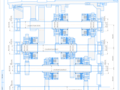
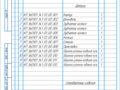
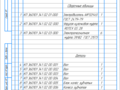
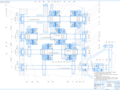
- Добавлен: 25.01.2023
- Размер: 1 MB
- Закачек: 0
Описание
Токарно-револьверный станок 1К341
Состав проекта
![]() |
![]() |
![]() ![]() ![]() ![]() |
![]() ![]() ![]() ![]() |
![]() ![]() ![]() |
![]() |
![]() ![]() ![]() ![]() |
![]() ![]() ![]() ![]() |
![]() ![]() ![]() |
![]() ![]() ![]() ![]() |
Дополнительная информация
Спецификация 2 лист.spw

КП 360101 341 02 01 000
Электродвигатель АИР132М4У3
КП 360101 341 02 02 000
Упругая кулачковая муфта
КП 360101 341 02 03 000
муфта Э1М82 ГОСТ 21573
КП 360101 341 02 00 001
КП 360101 341 02 00 002
КП 360101 341 02 00 003
КП 360101 341 02 00 004
КП 360101 341 02 00 005
КП 360101 341 02 00 006
КП 360101 341 02 00 007
КП 360101 341 02 00 008
КП 360101 341 02 00 009
КП 360101 341 02 00 010
КП 360101 341 02 00 011
КП 360101 341 02 00 012
КП 360101 341 02 00 013
КП 360101 341 02 00 014
КП 360101 341 02 00 015
КП 360101 341 02 00 016
КП 360101 341 02 00 017
КП 360101 341 02 00 018
КП 360101 341 02 00 019
КП 360101 341 02 00 020
КП 360101 341 02 00 021
КП 360101 341 02 00 022
КП 360101 341 02 00 023
КП 360101 341 02 00 024
КП 360101 341 02 00 025
КП 360101 341 02 00 026
КП 360101 341 02 00 027
КП 360101 341 02 00 028
КП 360101 341 02 00 029
КП 360101 341 02 00 030
Подшипник 305 ГОСТ 8338-75
Подшипник 205 ГОСТ 8338-75
Подшипник 204 ГОСТ 8338-75
Подшипник 1000909 ГОСТ 8338-75
Подшипник 1000908 ГОСТ 8338-75
Кольцо A45.65Г ГОСТ 13943-86
Кольцо A65.65Г ГОСТ 13943-86
Кольцо A40.65Г ГОСТ 13943-86
Кольцо A30.65Г ГОСТ 13943-86
Кольцо A60.65Г ГОСТ 13942-86
Кольцо A20.65Г ГОСТ 13942-86
Кольцо A15.65Г ГОСТ 13943-86
Кольцо A25.65Г ГОСТ 13943-86
Кольцо A60.65Г ГОСТ 13943-86
Кольцо A35.65Г ГОСТ 13943-86
Кольцо A20.65Г ГОСТ 13943-86
Кольцо A50.65Г ГОСТ 13943-86
Манжета 1.1-20x47-1 ГОСТ 8752-79
Болт М18-6gx60 ГОСТ 7805-70
Шайба A 18.37 ГОСТ 10450-78
Гайка М18-7H ГОСТ 2524-70
Шпонка 10х8х28 ГОСТ 23360-78
Болт М6-6gx20 ГОСТ 11738-84
Винт А.М8-6gx16 ГОСТ 1478-93
Винт А.М8-6gx18 ГОСТ 1478-93
3 лист шпиндельный узел.cdw

установлении теплового равновесия не должен превышать 70
Узел обкатывать в течение 30 минут на 1600 мин
Для смазки зубчатых передач и подшипников использовать масло
индустриальное 30 ГОСТ 20799-75.
Течи масла из под крышек
уплотнений и по местам соединений
КП 360101 341 03 00 000
спецификация 3 лист.spw

КП 360101 341 03 00 001
КП 360101 341 03 00 002
КП 360101 341 03 00 003
КП 360101 341 03 00 004
КП 360101 341 03 00 005
КП 360101 341 03 00 006
КП 360101 341 03 00 007
КП 360101 341 03 00 008
КП 360101 341 03 00 009
Лабринтное уплотнение неподвижная часть
КП 360101 341 03 00 010
Лабиринтное уплотнение подвижная часть
КП 360101 341 03 00 011
Лабиринтное уплотнение неподвижная часть
КП 360101 341 03 00 012
Лабиритное уплотнение подвижная часть
Подшипник 3182120 ГОСТ 7634-78
Подшипник 8117 ГОСТ 6874-87
Подшипник 8117 ГОСТ 46117-78
Винт А.М5-6gx16 ГОСТ 1491-80
Болт М6-6gx16 ГОСТ 7805-70
Болт М16-6gx50 ГОСТ 7805-70
Шайба 68.37 ГОСТ 11872-89
Шайба 48.37 ГОСТ 11872-89
Шпонка 14х9х80 ГОСТ 23360-78
1 лист кинематическая схема, структурная сетка, график частот.cdw

Наибольший диаметр обрабатываемой заготовки
Наибольшая длина обрабатываемого изделия
Диапазон частот вращения шпинделя
Высота оси центров над плоскими направляющими станины
Мощность электродвигателя главного движения
Наибольший диаметр обработки над поперечными
Наибольший диаметр прутка
проходящего через отверстие
Наибольшая длина обтачивания
Пределы шагов нарезаемых резьб:
числь ниток на 1" 56-0
Максимально допустимый вес устанавливаемого изделия:
КП 360101 341 01 00 000
Структурная сетка привода главного движения
Кинематическая схема станка
График частот привода главного движения
коробка со шпинделем.cdw

пояснительная записка.docx
Непрерывное совершенствование и развитие машиностроения связано с прогрессом станкостроения поскольку металлорежущие станки с некоторыми другими видами технологических машин обеспечивают изготовление любых новых видов оборудования.
На предприятиях функционирующих в условиях рынка к станку предъявляются особые требования необходимые при изготовлении конкурентоспособной продукции. К важнейшим требованиям относятся экономичность в изготовлении и эксплуатации удобство и безотказность обслуживания надёжность и долговечность.
Для обеспечения этих требований детали станка должны удовлетворять ряду критериев важнейшие среди которых - прочность надёжность износостойкость жёсткость виброустойчивость теплостойкость технологичность.
Конструкции металлорежущих станков изменяются во времени. Появляются новые механизмы расширяются технологические возможности повышаются производительность и качество обработки. Поэтому задачей курсового проекта является модернизация токарно-револьверного станка модели 1К341 в соответствии с современными веяньями в области станкостроения.
Назначение станка выполняемые операции. Задачи проектирования (модернизации)
На станках токарной группы обрабатывают детали типа валов дисков и втулок осуществляя обтачивание наружных цилиндрических поверхностей торцов и уступов прорезание канавок и отрезку растачивание отверстий (цилиндрических конических и фасонных) обтачивание конических и фасонных поверхностей сверлений зенкерование и развёртывание отверстий нарезание наружной и внутренней резьбы резцом нарезание резьбы метчиком и плашкой вихревое нарезание резьбы накатывание рифлёных поверхностей.
Главным движением определяющим скорость резания является вращение шпинделя несущего заготовку. Движением определяющим величины продольных и поперечных подач является движение суппорта в котором закрепляют резцы а при обработке концевым инструментом движение подачи получает задняя бабка станка. По классификации токарные станки относятся к первой группе.
Токарно-револьверный станок модели 1К341 предназначен для выполнения разнообразных токарных и резьбонарезных работ.
На станке обеспечивается возможность нарезания метрической дюймовой и модульной резьб.
Рисунок1.1- Станок-прототип 1К341Целью модернизации является:
- изменение диапазона регулирования привода главного движения и обеспечение частот вращения шпинделя от 315 до 2800 мин-1;
- замена стандартного электродвигателя на двухскоростной асинхронный электродвигатель;
- замена ремня привода главного движения на поликлиновый;
- обеспечение заданную эффективную мощность станка 2 кВт;
- изменение максимального диаметра изготавливаемого изделия с 250 на 200 мм;
- разработка коробки скоростей и шпиндельного узла для обеспечения необходимых режимов обработки в замен стандартных.
Рисунок 1.2 – Кинематическая схема станка-прототипа
Определение технических характеристик станка
Выбор электродвигателя произведём по эффективной мощности заданной по условию 2 кВт. По заданию двигатель должен быть асинхронный и иметь две скорости.
N = Nэф075 .085 = 48(075 .085) = 64 54 кВт
Выбираем асинхронный электродвигатель 4А112М4У3 мощностью 55 кВт при частоте вращения 1445мин-1
Основные технические данные сведём в таблицу (характеристики подвергнутые модернизации выделены).
Техническая характеристика станка:
Высота центров мм:130
Наибольший диаметр изготавливаемого изделия мм: 300
Расстояние между центрами мм:500
Наибольшая длина обточки мм:500
Шаг нарезаемой резьбы (наименьший наибольший):
метрической мм: 02 48
дюймовой число ниток на 1”:24 05
модульной в модулях:02 30
Число резцов в резцедержателе:4
Наибольшее перемещение суппорта (продольн. поперечн.) мм:
Выключающие упоры:Есть
Цена одного деления лимба (продольн. поперечн.) мм:01 002
Перемещение на один оборот лимба (продольн. поперечн.) мм:20 3
Конус в пиноле задней бабки:Морзе №3
Наибольшее перемещение пиноли мм: 85
Габаритные размеры мм:
Диапазон частот вращения шпинделя от-до мин-1:315-2800
Эффективную мощность станка: 48 кВт
ВЫБОР СТРУКТУРЫ И КИНЕМАТИЧЕСКИЙ РАСЧЁТ ПРИВОДА
1 Выбор структуры привода главного движения
Приводы главного движения токарно-винторезных станков бывают нераздельными и раздельными. Нераздельный привод выполняется в виде комплекса коробки скоростей и шпиндельного узла помещаемых в общий корпус. Такая конструкция компактна но часто имеет неудовлетворительные динамические характеристики и теплостойкость так как колебания и выделяемая в коробке теплота передаются на шпиндель.
Раздельный привод состоит из коробки скоростей и шпиндельной бабки выполненных в разных корпусах. Шпиндельный узел в раздельном приводе нагревается меньше. Колебания возникающие в коробке скоростей на шпиндельный узел не передаются.
Так как рассматриваемый станок относится к классу Н (нормальной точности) принимаем нераздельный привод.
Выбранная структура привода представлена на рисунке 3.1.
Рисунок 3.1 - Структура привода
КИНЕМАТИЧЕСКИЙ РАСЧЁТ ПРИВОДА
Кинематический расчёт коробки скоростей заключается в подборе оптимального его конструктивного и кинематического варианта и определении оптимальных передаточных отношений и чисел зубьев зубчатых передач. Коробка скоростей является множительным механизмом и состоит из последовательно расположенных элементарных двухваловых передач переключение которых обеспечивается передвижными блоками. Совокупность передач связывающих вращение двух соседних валов называется группой передач. Она характеризуется диапазоном регулирования количеством передач в группе и величиной их передаточных отношений.
Максимальная частота:
Минимальная частота:
Диапазон регулирования привода является отношением предельных частот вращения ведомого вала при последовательном переключении всех передач данной группы:
Знаменатель геометрического ряда =141 т.к. в станке необходимо обеспечить достаточно большой диапазон частот вращения шпинделя.
Число ступеней вращения привода:
Определяем частоты вращения шпинделя.
Таблица 3.1 - Частоты вращения шпинделя
Составим структурную формулу привода:
Z=14=2(1) 2(2) 2(4) 2(6);
Строим структурную сетку привода:
Рисунок 3.2 – Структурная сетка привода
Рисунок 3.3 - Кинематическая схема шпиндельной бабки
Исходя из кинематической схемы привода и структурной сетки привода строим график частот:
Рисунок 3.4 - График частот вращения шпинделя
Определяем передаточные отношения для каждой передачи.
Таблица 3.2 - Передаточные отношения
Суммарное число зубьев z
Определяем фактические частоты и их отклонения от стандартных значений:
Отклонение от стандартного значения:
Аналогично находим значения для других частот (таблица 3.3).
Таблица 3.3 - Частоты и их отклонения от стандартных значений
Отклонения фактических оборотов не превышают допустимый процент.
Определение моментов на валах и КПД привода главного движения
Определяем крутящие моменты на валах по расчётной цепи:
Определим расчётную частоту вращения шпинделя и построим расчётную цепь:
По графику частот (рисунок 3.4) принимаем np=n7=125 мин-1.
Общий КПД привода главного движения:
где α – число зубчатых зацеплений;
– число пар подшипников качения.
РАСЧЁТ ЭЛЕМЕНТОВ КОРОБКИ СКОРОСТЕЙ
1 Расчёт зубчатых передач
Проектный расчёт цилиндрической зубчатой передачи на выносливость зубьев при изгибе
Рассчитаем самую нагруженную зубчатую передачу с передаточным отношением i=025. Данная передача является прямозубой и состоит из шестерни 1 с числом зубьев z1 и колеса 2 с числом зубьев z2.
Соответственно при расчете параметрам шестерни приписываем индекс - 1 а параметрам колеса - 2. Выбираем твердость термическую обработку и материал зубчатых колес. Так как у нас на данную передачу приходится значительная часть нагрузки то термообработка колеса и шестерни одинаковые –объемная закалка. Материал для колеса и шестерни: Сталь 40Х.
Модуль передачи (мм) должен удовлетворять условию [4]:
где km - вспомогательный коэффициент; для прямозубых передач km=13;
M1 - исходный расчетный крутящий момент на шестерне;
kf - коэффициент нагрузки для шестерни; kf=13;
z1 - число зубьев шестерни; z1=18;
yf1- коэффициент учитывающий форму зуба; yf1=375;
bm- отношение ширины колеса b к модулю m;
Рекомендуется ширину венца принимать равной 6-10 модулям: bm=10.
Допустимое напряжение при изгибе:
где Flimb - предел выносливости материала зубьев МПа.
Выбираем материал шестерни – сталь 40Х.
Для этого материала НRCэ = 40 55.
kFL -коэффициент долговечности kFL=21;
FP=04115021=966 МПа;
Определим основные геометрические параметры передачи:
Делительные диаметры найдём по формуле:
Межосевое расстояние передачи а:
Найдём диаметры вершин и диаметры впадин зубьев:
Подставив значения в формулы 4.1.6 и 4.1.7 получим:
Диаметры вершин зубьев:
Диаметры впадин зубьев:
df2=216-253=2085 мм;
b1= m bm =3 (6 10)=30 мм;
b2= b1-5=30-5=25 мм.
Основные геометрические параметры зубчатых передач шпиндельной бабки
Рассчитаем делительные диаметры исходя из назначенных модулей зубчатых колёс тi и количества зубьев Zi по формуле 4.4 диаметры вершин и впадин зубьев а также ширину венца по формулам 4.6 4.7 4.8 и сведём полученные результаты в таблицу 4.1.
Таблица 4.1 – Геометрические параметры зубчатых передач
Межосевое расстояние найдём по формуле 4.1.5:
между I и II валами:
между II и III валами:
между III и IV валами:
между IV валом и шпинделем (V валом):
Допуски на межосевые расстояния при виде сопряжения В [4]:
Если 80 aw 125 (мм) то fа=70 мкм;
Δ=±(06 07)·fа=42 49 мкм; принимаем Δ=±0045 мм.
Если 125 aw 190 (мм) то fа=80 мкм;
Δ=±(06 07)·fа=48 56 мкм; принимаем Δ=±0055 мм.
Проектный расчёт передачи на контактную выносливость зубьев
Начальный диаметр шестерни должен удовлетворять условию [2]:
где kd - вспомогательный коэффициент; kd=770 для прямозубых передач;
kH - коэффициент нагрузки; kH=13;
bd - отношение рабочей ширины венца передачи к начальному диаметру шестерни bd=043;
Допускаемое контактное напряжение для прямозубых передач:
SH-коэффициент безопасности SH=11;
Условие не выполняется следовательно принимаем закалку с нагревом ТВЧ для шестерни.
Условие выполняется.
Проверочный расчет на выносливость зубьев при изгибе
Удельная расчетная окружная сила (Н) :
где Ft - расчётная окружная сила Н;
b - ширина венца по основанию зуба мм;
kFV - коэффициент учитывающий динамическую нагрузку в зацеплении которая возникает вследствие колебаний масс колёс и ударов в зацеплении;
kF - коэффициент учитывающий неравномерность распределения нагрузки по ширине венца которая возникает вследствие погрешностей изготовления колёс упругих деформаций валов зазорах в подшипниках;
kF - коэффициент учитывающий при расчёте прямозубых передач распределение нагрузки между зубьями.
Коэффициенты: kFV=1; kF=12; kF=07.
Расчётное напряжение изгиба зубьев:
где YF - коэффициент формы зуба;
Y - коэффициент учитывающий перекрытие зубьев: Y=1;
Y - коэффициент учитывающий наклон зуба;
Получаем YF=42; Y =1.
Подставив значения в формулу 4.1.12 получим:
Допускаемое напряжение при расчёте зубьев на выносливость при изгибе:
Уточняем допускаемое напряжение при расчёте зубьев на выносливость при изгибе:
kFg - коэффициент учитывающий влияние шлифования переходной поверхности зубьев;
kFa - коэффициент учитывающий влияние упрочнения переходной поверхности зубьев в результате механической обработки;
kFc - коэффициент учитывающий особенности работы зубьев при
передаче реверсивной нагрузки;
kFL - коэффициент режима нагружения и долговечности;
YS - коэффициент отражающий чувствительность материала к
концентрации напряжений;
YR - коэффициент учитывающий параметры шероховатости переходной поверхности зуба;
SF - коэффициент безопасности;
Найдём данные коэффициенты:
kFg=1; kFa=13; kFc=075; k kFL=10;
YS=11m-009=113-009=099; YR=12;
Коэффициент безопасности находим по формуле:
где S’F - коэффициент безопасности учитывающий нестабильность свойств материала зубчатого колеса и ответственность зубчатой передачи:
S’’F - коэффициент учитывающий способ получения заготовки:
Подставив значения в формулу получим:
В нашем случае FP1=96045>F1=1918 и FP2=96045>F2=1918 т.е. проверка на выносливость зубьев при изгибе выполняется.
Расчёт диаметров валов и предварительный выбор подшипников
Ориентировочно диаметры валов определяем из соотношения [4]:
где Т-момент на соответствующем валу;
[]k – допускаемое напряжение на кручение []k = 10 20 Нмм2.
Диаметр выходного конца электродвигателя d=32 мм.
Диаметры валов необходимо принять несколько больше так как подача смазочной жидкости будет осуществляться через отверстия в валах.
Предварительно выбираем подшипники:
Шариковые радиальные однорядные ГОСТ 8338-75: 204 (2 шт.);
Шариковые радиальные однорядные ГОСТ 8338-75: 205 (2 шт.);
Шариковые радиальные однорядные ГОСТ 8338-75: 305 (2 шт.);
На 5 валу (шпиндель):
Шариковые радиально-упорные однорядные ГОСТ 831-75: 46216(2 шт.);
Роликовые радиальные двухрядные подшипники с короткими цилиндрическими роликами: ГОСТ 8328-75 3182120К (1 шт.).
3.2 Силовой расчет вала
Рисунок 4.1 - Схема приложения нагрузки
Наиболее нагруженным валом в коробке скоростей является IV на который действует силы в зубчатом зацеплении.
Определим окружную силу в зацеплении [4]:
где d10=mz10=393=186 мм – делительный диаметр колеса;
Т4=979 Нм – крутящий момент на колесе.
где =20 - угол зацепления;
где =20 - угол зацепления.
По чертежу определяем места расположения сил и расстояние до точек их приложения переносим их на рисунок. Для облегчения расчёта применим относительную систему координат совпадающую с направлениями сил Fr Ft.
С учетом полученной величины a получаем линейные размеры:
Радиальные реакции опор:
MA=0; -Ft2l1+Ft1 (l1+l2)+RBY(l1+l2+l3) =0
RBY= (Ft2 (l1)-Ft1(l2+l1) (l1+l2+l3) = (3625 ×110+1052×192)402= 489 H
MB=0; -RAY (l1+l2+l3)+Ft2 (l2+l3)-Ft1 l3=0
RAY= (Ft2 (l2+l3)- Ft- l3) (l1+l2+l3)=(3625 × 292+1050 × 210)402= 2084 H
Y= RAY + RBY+Ft1-Ft2 = 489+2084+1052-3625= 0
MA=0; RBX(l1+l2+l3)= -Fr1 (l1+l2)+Fr2 l1
RBX= (-383×110 +1320×192)402= 525 Н
MB=0; RАX(l1+l2+l3)= Fr1 (l2+l3) -Fr2 l3
RAX=(1320 ×210-383 ×110)402=411 Н
X= RAX+ RBX+Fr1- Fr2 =411+525+383-1320=0
Силы реакции в опорах:
Строим эпюры изгибающих и крутящих моментов (рисунок 4.3.2).
Рисунок 4.2 - Эпюры изгибающих и крутящих моментов
Расчёт вала на сопротивление усталости [4]
Диаметр вала в этом сечении dк=34 мм. Концентратор напряжений в сечении С – посадка скользящая ступицы цилиндрического колеса на вал а также шлицевой участок вала.
Принимаем материал вала Сталь 40Х для которого:
В=900 МПа;Т=750 МПа; -1=410 МПа;-1=240 МПа.
Для каждого из концентраторов напряжений определим отношения ККd и К Кd.
Скользящая посадка ступицы цилиндрического колеса. При В=900 МПа для диаметра вала d =34 мм и посадки III линейным интерполированием ККd =272 и К Кd =202.
Шлицевой участок вала. При В=900 МПа для валов с прямобочными шлицами К=17 и К=265. Для d =45 мм (сталь легированная) линейным интерполированием коэффициент Kd=071 (при изгибе и кручении). Тогда ККd =17071=239 и К Кd=265071=373.
Таким образом из двух концентраторов напряжений в качестве расчётного принимаем скользящую посадку на вал ступицы колеса т. к. для данного концентратора напряжений получены наибольшие отношения ККd и ККd.
Так как поверхность вала дополнительно не упрочняется то KV=1.
Суммарные коэффициенты КD и КD:
КD= (ККd+ KF-1) KV=(272+1-1)1=272;
КD = (Кt Кd+ KF-1) KV=(202+1-1)1=202.
Результирующий изгибающий момент в рассматриваемом сечении С:
Для сечения С вала диаметром d=34 мм с прямобочными шлицами:
осевой момент сопротивления сечения:
= 1205 – для шлицев средней серии.
полярный момент сопротивления сечения:
Амплитуда напряжений цикла:
а=И=MW=424×1034647=91 МПа;
а=K 2=MK2WK=98×1032×9294=53 МПа
где MK – крутящий момент в сечении С.
Среднее напряжение цикла:
=002+2×10-4В=002+2×10-4×900=02;
Коэффициенты запаса по нормальным и касательным напряжениям:
Коэффициент запаса прочности по усталости в сечении С:
Сопротивление усталости в сечении С обеспечивается.
Расчёт вала на статическую прочность
Проверка статической прочности проводится по условию [4]:
где Е – эквивалентное напряжение;
[]=08T=08750=600 МПа – предельное допускаемое напряжение;
КП=16 – коэффициент перегрузки;
Условие прочности выполняется.
5 Расчёт соединений вал-ступица
Рассчитаем прямобочное шлицевое соединение 6х28х34х6 [4].
Боковые поверхности зубьев шлицевого соединения работают на смятие а основание их - на изгиб и срез. Основным является расчёт на смятие:
где Т=979 - вращающий момент передаваемый соединением Нм;
=075 - коэффициент учитывающий неравномерность распределения
нагрузок по рабочим поверхностям зубьев;
F - площадь всех боковых поверхностей зубьев с одной стороны на
rСР - средний радиус мм;
[] - допускаемое напряжение на смятие (для подвижных соединений
Для прямобочных соединений:
где z=6 - число зубьев;
DВ =34 - наружный диаметр зубьев вала мм;
dа =28 - диаметр отверстия шлицевой втулки мм;
f =04 - размер фаски мм;
r =03 - радиус закругления мм.
Тогда напряжение смятия:
Предварительно выбранное шлицевое соединение подходит.
Проверочный расчет подшипников по динамической грузоподъемности
Сопоставим расчетную динамическую грузоподъемность Срасч с
Для радиальных подшипников 305 условие имеет вид [4]:
где Сr расч – расчетная радиальная грузоподъемность Н;
Рr – эквивалентная радиальная динамическая нагрузка Н;
р=103=333 – для подшипников;
n=1600 мин-1 – частота вращения внутреннего кольца подшипника;
Lh=12104 ч – требуемая долговечность подшипника;
КНЕ=018 – коэффициент режима нагрузки (средний нормальный режим нагружения);
Сr=114 кН – базовая радиальная динамическая грузоподъемность.
Pr=V·X·Rr·KБ·КТ Н; (4.36)
где V=1 – коэффициент вращения;
Х=040 – коэффициент радиальной нагрузки;
Rr=2124 H – наибольшая радиальная нагрузка действующая на подшипник;
КБ=14 – коэффициент безопасности;
КТ=1 – температурный коэффициент.
Pr=10402124141=1190 Н.
Следовательно выбранный радиальный подшипник 305 подходит по динамической грузоподъемности может быть применён в качестве опор рассматриваемого IV вала.
Проверку на статическую грузоподъемность не проводим так как подшипники не работают на частотах ниже 10 мин-1.
Рассмотрим современные муфты от ведущего немецкого производителя компании KTR [5] применяемые для передачи крутящего момента от вала электродвигателя к первому валу коробки скоростей станка.
Рисунок 4.5.1 – Муфта ROTEX
ROTEX –муфта отличаются малыми размерами малоймассойинизкимимаховымимоментамиприпередачезначительныхкрутящихмоментов. Точная машинная обработка муфты положительновлияетнаеёрабочиехарактеристикиизначительноувеличиваетсрокслужбы.
Рисунок 4.5.2– Муфта POLY-NORM
POLY-NORM-муфтыпередаюткрутящиймоментикомпенсируютсмещениясоединяемыхвалов.
Рисунок 4.5.3– Муфта BoWex
BoWex – зубчатая муфта с круговыми зубьями является гибким соединением валов передаёт крутящий момент геометрическим замыканием и применяется для компенсации осевого радиального и углового смещения. Муфты отличаются высокой износостойкостью.
Проанализировав конструкцию присоединительного фланца электродвигателя можно сделать вывод что ось вала электродвигателя расположена на одной линии с осью вала I вследствие чего радиальные и угловые смещения минимальны. Т.к. муфты POLY-NORM иBoWex предназначены для компенсации осевых радиальных и угловых смещений то для разработанной конструкции их применение не целесообразно.
Из трёх предложенных вариантов муфт наиболее полно условиям эксплуатации удовлетворяет упругая муфта ROTEX. Муфта имеет наименьшие габариты и массу что позволяет уменьшить часть корпуса в месте крепления двигателя как следствие экономия металла при производстве корпуса коробки скоростей. Цена муфты на 10% ниже по сравнению с предложенными аналогами.
6 Выбор электромагнитных муфт
Выбор электромагнитных муфт контактного типа Э1М 2 производится в зависимости от крутящего момента на валу и угловой скорости [2].
где k=13 – коэффициент запаса.
где п – частота вращения вала мин-1
Выбираем электромагнитные муфты типоразмера 09
Разработка конструкции расчет шпиндельного узла на точность жесткость виброустойчивость
1 Разработка конструкции шпиндельного узла[4]
Определим диаметр шпинделя из условия работоспособности:
Р - мощность резания кВт
Конструктивно после прочерчивания стандартного переднего конца шпинделя определяем длину вылета шпинделя а и диаметр шеек под подшипники d. Получаем а=125мм d=80 мм.
Длина участка вала между опорами:
Определяем диаметр переднего конца шпинделя:
dПК= d(1 13)=80(1 13)=80 110 мм
Принимаем по ГОСТ 24644-81 диаметр dПК=105 мм.
По ГОСТ 24644-81 принимаем основные размеры конца шпинделя.
Определим характеристику быстроходности шпинделя dnmax:
dnmax=802800=02210 5мммин-1
Схему компоновки шпиндельного узла принимаем аналогичную станку прототипу. Передней опорой шпинделя служит двухрядный роликоподшипник 3182120 ГОСТ 7634-75 . Задней опорой служит радиальн0-упорный шарикоподшипник 46117 ГОСТ 831-62 .
2 Расчет шпиндельного узла на точность
Станок нормальной точности обеспечивает получение деталей с размерами по 8 квалитету точности. Лимитирующий размер обрабатываемой детали задан по условию: Dmax=300 мм
Рисунок 5.1 Схема к расчету шпиндельного узла на точность
Максимальная точность получаемая при точении 7 квалитет. Допуск на размер 300 по 8 квалитету дет=81 мкм. Приняв допустимое радиальное биение переднего конца шпинделя:
Для станков нормального класса точности рекомендуется применять в передней и задней опоре подшипники 5 класса точности.
Проверим обеспечивает ли данная компоновка заданный допуск радиального биения:
где 1– радиальное биение подшипников в передней опоре мм (1 = 0005 мм)
– радиальное биение подшипников в задней опоре мм (2 = 0005 мм)
m1– число подшипников в передней опоре (m1=1)
m2– число подшипников в задней опоре (m2=1)
где l–расстояние между опорами шпинделя мм
a– расстояние от передней опоры до плоскости измерения
Даже при самой неблагоприятной сборке шпиндельного узла когда ориентация эксцентриситетов колец не отрегулирована можно получить необходимую точность и максимальное радиальное биение 8 мкм укладывается в придел до 27 мкм.
3 Расчет шпиндельного узла на жёсткость
Вычислим радиальное перемещение переднего конца шпинделя:
где 1– перемещение вызванное изгибом тела шпинделя;
– перемещение вызванное податливостью опор;
– сдвиг вызванный защемляющим моментом.
Когда приводной элемент расположен между его опорами перемещение переднего конца шпинделя без учета защемляющего момента в передней опоре:
где Е=21105 МПа – модуль упругости материала шпинделя;
=04 – коэффициент защемления в передней опоре;
I1 - среднее значение осевого момента инерции сечения консоли мм4;
I2 - среднее значение осевого момента инерции сечения шпинделя в пролете между
Найдём силу резания исходя из мощности и скорости резания на расчётной частоте:
где V-скорость резания
Определим осевые моменты инерции:
где D-наружный диаметр участка шпинделямм;
d-наружный диаметр участка шпинделя мм.
где d2=75 мм – диаметр шпинделя в передней опоре;
d1=30 мм – диаметр отверстия в шпинделе.
где d1 d2- наружный и внутренний диаметры шпинделя в задней опоре мм.
Определим радиальную жесткость подшипников в опорах шпинделя:
Рассмотрим переднюю опору шпинделя где установлен роликовый радиальный двухрядный подшипник с короткими цилиндрическими роликами серии 3182120.
Радиальная жёсткость подшипника находится по графику и равна:
Рассмотрим заднюю опору которая представлена однорядным радиально-упорным 46117 шарикоподшипником . Определим радиальную жёсткость по справочнику
По ГОСТ 18097-93 допустимое радиальное перемещение шпинделя токарного станка составляет 001мм. Полученное значение соответствует требуемой точности.
4 Расчет шпинделя на виброустойчивость
Приближенный расчет собственной частоты шпинделя не имеющего больших сосредоточенных масс можно проводить по формуле:
где т– масса шпинделякг;
где:V – объём шпинделя мм3;
ρ – плотность материала шпинделя ρ = 7800 кгм3
тогда масса шпинделя:
m = 119·10-4 ·7800 =93 кг
- относительное расстояние между опорами
- коэффициент зависящий от .
Полученная частота собственных колебаний удовлетворяет требованиям к данному типу станков(допустимая минимальная частота 500-600 Гц).
Описание кинематической схемы станка
Цепь главного движения
Привод вращения шпинделя и подачи револьверного суппорта помещены в общем корпусе и составляют один узел – коробку скоростей и подач.
На корпусе коробки закреплен фланцевый электродвигатель который передаёт крутящий момент через упругую кулачковую муфту ROTEX на первый вал. На валу I расположены 2 зубчатых колеса которые передают на вал II две различных частоты. Переключение скоростей осуществляется ЭММ блока . Далее со II на III вал можно получить 2 варианта передаточных чисел с помощью ЭММ на III валу. Далее со III на IV вал можно получить 2 варианта передаточных чисел с помощью ЭММ на IV валу. Коробка скоростей имеет два диапазона чисел оборотов шпинделя получаемых с помощью передвижного зубчатого блока.С IV на V также можно получить 2 варианта передаточных чисел. Таким образом коробка обеспечивает 14 частот вращения.
Рисунок 6.1 – Кинематическая схема станка
Коробка подач закрытого типа позволяет нарезать метрические резьбы всех стандартных шагов от 02 до 48 мм дюймовые резьбы— с числом ниток на дюйм от 24 до 05 модульные — с модулем от 02 до 30 мм и получать подачи в пределах от 001 до 3 ммоб. Величина поперечных подач равна половине продольных.
Для нарезания резьб повышенной точности механизм подач позволяет производить прямое соединение ходового винта с гитарой минуя механизм подач. При этом каждый шаг подбирается только сменными шестернями гитары.
Выбор системы смазывания станка привода
Рассмотрим систему смазки шпиндельного узла.
Опорами шпиндельного узла являются роликовый радиальный двухрядный подшипник с короткими цилиндрическими роликами серии 3182120 и однорядный радиальный шарикоподшипник 46117 ГОСТ 831-75. Т.к. характеристика быстроходности узла dnmax=2210 5 мммин-1 и шпиндель расположен горизонтально то в качестве смазочного материала применяем масло индустриальное 30 ГОСТ 1707-51.
Минимально допустимый расход жидкого смазочного масла для смазывания шпиндельных опор определяем по зависимости:
где dm-средний диаметр подшипников мм
n-частота вращения шпинделяобмин
i-число рядов тел качения в подшипнике
v-вязкость масла при рабочей температуре опорым2·с
k1-коэффициентхарактеризующиц тип подшипника
k2-коэффициентхарактеризующиц условия нагружения
k3-коэффициентхарактеризующиц условия выхода масла из рабочей зоны подшипника
k4-коэффициентзависящий от рабочей температуры подшипника
Для передней опоры получим:
Для задней опоры получим:
Схема расположения смазываемых и смазочных устройств показана на рисунке. Электромагнитные муфты коробки скоростей и подач смазываются централизованно от насоса гидропривода. Масло необходимое для смазки и охлаждения дисков подводится маслоподводящими трубками индивидуально к каждой муфте и поливает диски через щелевой паз ленточной струей направленной по радиусу муфты. От этого насоса смазываются направляющие станины. Для этого оттягивается на себя рукоятка и масло поступает в маслосборник установленный на верхней плоскости суппорта.Смазка механизма привода шпинделя осуществляется системой обильного смазывания циркуляционным методом. Выбор такой системы смазывания обусловлен необходимостью отвода тепла от опор и смазывания зубчатых передач.
Смазка шпиндельных подшипников осуществляется независимой системой смазки от индивидуального шестеренчатого насоса расположенного в средней части тумбы станка. На станке предусмотрена блокировка не допускающая пуск шпинделя без пуска насоса смазки. Масляный бачок емкостью 8 литров можно наполнить двумя способами:
)снять крышку передней бабки и залить масло которое по сливному шлангу поступит в бачок;
)через заливное отверстие масляного бачка.
Следует иметь в виду что при заливке первым способом масло должно быть подвергнуто тонкой очистке. Масло из бачка подается насосом к проволочному фильтру а затем по трубе к маслораспределителю в передней бабке. От маслораспределителя масло поступает к подшипникам шпинделя в лоток для смазки шестерни и подшипников. В случае если масло в глазок передней бабки не поступает работа на станке недопустима.
Предохранительный клапан отрегулирован на давление 5 ат соответствующее 80% засорению фильтра. В случае срабатывания клапана необходимо проверить не засорились ли трубопроводы или фильтр. Фильтр следует промывать после его засорения но не реже одного раза в год.
Перед заливкой в бачок масло следует тщательно профильтровать. Перед сменой масла следует вынуть бачок и тщательно промыть его.
Смазка механизмов фартука направляющих станины и суппорта осуществляется плунжерным насосом установленным на нижней стенке фартука. Масло насосом подается к верхнему глазку фартука. Появление масла в глазке произойдет не сразу а через 10—15 минут работы насоса. Вверху на правом торце фартука находится кран имеющий два положения: 1—смазка фартука и 2—смазка суппорта. В зависимости от положения крана масло поступает либо к шестерням либо к направляющим станины и суппорта. Поворот крана производится вручную периодически в зависимости от состояния смазки на направляющих. При повороте крана в положение 2 масло в глазок не поступает и о работе насоса можно судить по наличию смазки на направляющих.
Смазка механизмов редуктора и коробки подач осуществляется разбрызгиванием масла залитого в корпус каждого узла. Маслоуказатели редуктора и масляного бачка находятся внутри тумбы станка. Для наблюдения за уровнем масла в этих резервуарах необходимо периодически снимать заднюю и левую торцовую крышки станка под которыми находятся эти маслоуказатели.
Рисунок 7.1-Схема смазки
Техника безопасности при работе на станке
1 Правила безопасной при работе на металлообрабатывающих станках
Общие требования перед началом работы.
Проверить хорошо ли убрано рабочее место и при наличии неполадок в работе станка в течение предыдущей смены ознакомиться с ними и с принятыми мерами по их устранению.
Принести в порядок рабочую одежду. Застегнуть обшлага рукавов убрать волосы под головной убор.
Проверить состояние решетки под ногами ее устойчивость па полу.
Проверить состояние ручного инструмента: ручки напильников и шабера должны иметь металлические кольца предохраняющие их от раскалывания; гаечные ключи должны быть исправными и при закреплении болтов (гаек) размер их зева должен соответствовать размеру гоповки болта (гайки); не допускается применение прокладок и их удлинение с помощью труб.
Привести в порядок рабочее место: убрать все лишнее подготовить и аккуратно разложить необходимые инструменты и приспособления так чтобы было удобно и безопасно пользоваться ими (то что надо брать левой рукой должно находиться слева а то что правой - справа); уложить заготовки в предназначенную для них тару а саму тару разместить так чтобы было удобно брать заготовки и укладывать обработанные детали без лишних движений рук и корпуса.
При наличии местных грузоподъемных устройств проверить их состояние. Приспособления массой более 16 кг устанавливать на станок только с помощью этих устройств.
Проверить состояние станка: убедиться в надежности крепления стационарных ограждений в исправности электропроводки заземляющих (зануляющих) проводов рукояток и маховичков управления станком. Разместить шланги проводящие СОЖ электрические провода и другие коммуникации так чтобы была исключена возможность их соприкосновения с движущимися частями станка или вращающимся инструментом.
Подключить станок к электросети включить местное освещение и отрегулировать положение светильника так чтобы рабочая зона была хорошо освещена и свет не слепил глаза.
На холостом ходу проверить исправность кнопок "Пуск" и "Стоп" действие и фиксацию рычагов и ручек включения режимов работы станка системы принудительного смазывания а также системы охлаждения. Далее произвести или проверить наладку станка в соответствии с технологической документацией.
Подготовить средства индивидуальной защиты и проверить их исправность. Для предупреждения кожных заболеваний при необходимости воспользоваться средствами дерматологической защиты.
О всех обнаруженных недостатках не приступая к работе( сообщить мастеру.
Общие требования во время работы.
и габаритные размеры обрабатываемых заготовок должны соответствовать паспортным данным станка.
При обработке заготовок массой более 16 кг устанавливать и снимать с помощью грузоподъемных устройств причем не допускать превышения нагрузки установленной для них. Для перемещения применять специальные строповочно-захватные приспособления. Освобождать обработанную деталь от них только после надежной укладки а при установке-только после надежного закрепления на станке.
При необходимости пользоваться средствами индивидуальной защиты. Запрещается работать в рукавицах и перчатках а также с забинтованными пальцами без резиновых напальчников на станках с вращающимися обрабатываемыми заготовками или инструментами.
Перед каждым включением станка убедиться что его пуск ни для кого не опасен; постоянно следить за надежностью крепления станочного приспособления обрабатываемой заготовки а также режущего инструмента.
При работе станка не переключать рукоятку режимов работы измерений регулировки и чистки. Не отвлекаться от наблюдения за ходом обработки самому и не отвлекать других.
Если в процессе обработки образуется отлетающая стружка установить переносные экраны для защиты окружающих и при отсутствии на станке специальных защитных устройств надеть защитные очки или предохранительный щиток из прозрачного материала. Следить за своевременным удалением стружки как со станка так и с рабочего места остерегаться наматывания стружки на заготовку или инструмент не удалять стружку руками а пользоваться для этого специальными устройствами; запрещается с этой целью обдувать сжатым воздухом обрабатываемую заготовку и части станка.
Правильно укладывать обработанные детали не загромождать подходы к станку периодически убирать стружку и следить за тем чтобы пол не был залит охлаждающей жидкостью и маслом обращая особое внимание на недопустимость попадания их на решетку под ноги.
При использовании для привода станочных приспособлений сжатого воздуха следить за тем чтобы отработанный воздух отводился в сторону от станочника.
Постоянно осуществлять контроль за устойчивостью отдельных деталей или штабелей деталей на местах складирования а при размещении деталей в таре обеспечивать устойчивое положение их а также самой тары. Высота штабелей не должна превышать для мелких деталей 05 м для средних - 1 м для крупных - 15 м.
Обязательно выключать станок при уходе далее на короткое время при перерывах в подаче электроэнергии или сжатого воздуха при измерении обрабатываемой детали а также при регулировке уборке и смазывании станка.
При появлении запаха горящей электроизоляции или ощущения действия электрического тока при соприкосновении с металлическими частями станка немедленно остановить станок и вызвать мастера. Не открывать дверцы электрошкафов и не производить какую-либо регулировку электроаппаратуры.
Общие требования по окончании работы.
Выключить станок и привести в порядок рабочее место. Разложить режущий вспомогательный и измерительный инструмент по местам хранения предварительно протерев его.
Стружку смести в поддон или на совок щеткой; труднодоступные места очистить кистью или деревянной заостренной палочкой обернутой ветошью. Во избежание несчастного случая И попадания стружки в механизмы запрещается для чистки станка использовать сжатый воздух.
Проверить качество уборки станка выключить местное освещение и отключить станок от электросети.
О всех неполадках в работе станка если они имели место на протяжении смены сообщить сменщику или мастеру.
Осуществить санитарно-гигиенические мероприятия.
Кроме указанного каждый станочник обязан:
работать только на том станке к эксплуатации которого он допущен и выполнять ту работу которая поручена ему администрацией цеха;
без разрешения мастера не допускать к работе на станке других лиц;
заметив нарушение правил по охране труда со стороны других станочников предупредить их и потребовать соблюдения требований безопасности;
в обязательном порядке требовать от администрации цеха проведения внепланового инструктажа при переводе на эксплуатацию станка другой модели или при привлечении к разовым работам не входящим в круг обязанностей станочника;
о всяком несчастном случае немедленно ставить в известность мастера и обращаться в медицинский пункт;
уметь оказывать первую помощь пострадавшему применять первичные средства пожаротушения и проводить работы по устранению последствий аварийных ситуаций или пожара.
2 Указание мер безопасности при эксплуатации станка
- При работе на токарных станках необходимо соблюдать все основные правила техники безопасности указанные выше.
- Перед первоначальным пуском рабочий обслуживающий станок должен изучить устройство станка и управление им по инструкции по эксплуатации и строго соблюдать данные в нем указания.
- Перед началом обработки изделий следует тщательно проверить:
-надежность закрепления инструмента в шпинделе;
-надежность закрепления заготовки на станка;
-исправность инструмента.
3 Технические средства защиты рабочего
Защита станков представлена защитным экранам выполненным из прозрачного пластика. Щиток защищает рабочего летящей в процессе резания стружки.
Также необходимо использовать очки.
При выполнении данного курсового проекта произвели проектирование привода главного движения и шпиндельного узла. В итоге получили необходимую эффективную мощность резания 48 кВт.
Новая коробка скоростей обеспечивает 14 частот вращения шпинделя. Также увеличен диапазон регулирования частот 315-2800 мин-1.
В целом спроектированный станок удовлетворяет современным нормам точности жёсткости и виброустойчивости что даёт возможность получать на нём изделия заданной точности.
Список используемых источников
Дунаев П.Ф. Леликов О.П. Конструирование узлов и деталей машин: Учебное пособие для машиностроительных специальностей ВУЗов. – 4-е изд. перераб. и доп. – М.: Высшая школа 1985.
Кочергин А.И. Конструирование и расчет металлорежущих станков и станочных комплексов. Курсовое проектирование. Учебное пособие для ВУЗов. – Мн.: Вышэйшая школа 1991.
Металлорежущие станки: Учебник для машиностроительных ВТУЗовПод ред. В. Э. Пуша. – М.: Машиностроение 1985.
Санюкевич Ф.М. Детали машин. Курсовое проектирование: Учебное пособие – Брест: БГТУ 2003.
РТМ 38 40528-74 Ремни поликлиновые и шкивы. Размеры. Расчет передач – М.: НИИРП 1975.
Решетов Д.Н. Детали и механизмы металлорежущих станков. Т. 2– М.: Машиностроение 1972.
2 лист коробка скоростей.cdw

допуск на осевое смещение не более 0
Работа шестерни должна быть спокойной
Осевой допуск валов не более 0
Обкатку коробки скоростей производть в течении 20 минут
с последовательным переключением скоростей
минут на максимальной скорости.
КП 360101 341 02 00 000
Рекомендуемые чертежи
- 14.03.2022
Свободное скачивание на сегодня
Другие проекты
- 22.08.2014