Технологический процесс получения многослойного теплозащитного покрытия с анкерным эффектом




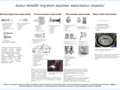
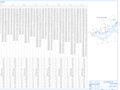
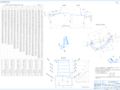
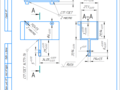
- Добавлен: 25.01.2023
- Размер: 24 MB
- Закачек: 1
Описание
Состав проекта
![]() |
![]() |
![]() ![]() ![]() |
![]() |
![]() |
![]() ![]() |
![]() ![]() |
![]() |
![]() ![]() |
![]() ![]() |
![]() ![]() |
![]() ![]() |
![]() ![]() |
![]() ![]() |
![]() ![]() |
![]() ![]() ![]() |
![]() |
![]() |
![]() |
![]() |
![]() |
![]() |
![]() |
![]() |
![]() |
![]() |
![]() |
![]() |
![]() |
![]() |
![]() |
![]() |
![]() |
![]() |
![]() |
![]() |
![]() |
![]() |
![]() |
![]() |
![]() ![]() ![]() ![]() |
![]() ![]() ![]() ![]() |
![]() ![]() ![]() ![]() |
![]() ![]() ![]() ![]() |
![]() ![]() ![]() ![]() |
![]() ![]() ![]() ![]() |
![]() ![]() ![]() ![]() |
![]() ![]() ![]() ![]() |
![]() ![]() ![]() ![]() |
![]() ![]() ![]() ![]() |
![]() ![]() ![]() ![]() |
![]() ![]() ![]() ![]() |
![]() ![]() ![]() ![]() |
![]() ![]() ![]() ![]() |
![]() ![]() ![]() ![]() |
![]() ![]() ![]() ![]() |
![]() ![]() ![]() ![]() |
![]() ![]() ![]() ![]() |
![]() ![]() ![]() ![]() |
![]() ![]() ![]() ![]() |
![]() ![]() ![]() ![]() |
![]() ![]() ![]() ![]() |
![]() ![]() ![]() ![]() |
![]() |
![]() ![]() ![]() ![]() |
![]() ![]() ![]() ![]() |
![]() ![]() ![]() ![]() |
![]() ![]() ![]() ![]() |
![]() ![]() ![]() ![]() |
![]() ![]() ![]() ![]() |
![]() ![]() ![]() ![]() |
![]() ![]() ![]() ![]() |
![]() ![]() ![]() ![]() |
![]() ![]() ![]() ![]() |
![]() ![]() ![]() ![]() |
![]() ![]() ![]() ![]() |
![]() ![]() ![]() ![]() |
![]() ![]() ![]() ![]() |
![]() |
![]() ![]() ![]() ![]() |
![]() ![]() ![]() ![]() |
![]() ![]() ![]() ![]() |
![]() ![]() ![]() ![]() |
![]() |
![]() |
![]() |
![]() |
![]() ![]() ![]() ![]() |
![]() ![]() ![]() ![]() |
![]() ![]() ![]() ![]() |
![]() ![]() ![]() ![]() |
![]() ![]() ![]() ![]() |
![]() |
![]() |
![]() |
![]() |
![]() ![]() ![]() ![]() |
![]() ![]() ![]() ![]() |
![]() |
![]() ![]() ![]() ![]() |
![]() ![]() ![]() ![]() |
![]() ![]() ![]() ![]() |
![]() |
![]() |
![]() ![]() ![]() ![]() |
![]() |
![]() |
![]() |
![]() |
![]() |
![]() ![]() ![]() ![]() |
![]() |
![]() |
![]() ![]() ![]() ![]() |
![]() |
![]() |
![]() ![]() ![]() ![]() |
![]() ![]() ![]() ![]() |
![]() ![]() ![]() ![]() |
![]() |
![]() ![]() ![]() ![]() |
![]() |
![]() |
![]() ![]() ![]() ![]() |
![]() ![]() ![]() ![]() |
![]() ![]() ![]() |
Дополнительная информация
Приложение В.doc
005 ВХОДНОЙ КОНТРОЛЬ ГЕОМЕТРИИ ЗАГОТОВКИ
010 ШЛИФОВАЛЬНАЯ (ПОДОШВЫ ЧЕРНОВАЯ)
015 ШЛИФОВАЛЬНАЯ (ПОДОШВЫ ПОЛУЧЕРНОВАЯ)
020 ОТРЕЗКА ЛИТНИКА ПЕРА
030 ШЛИФОВАЛЬНАЯ (ТОРЦА ПЕРА)
035 СВЕРЛИЛЬНАЯ (ЦЕНТРОВКА ТОРЦА ПЕРА)
040 ШЛИФОВАЛЬНАЯ (ПОЛКИ ЗАМКА С КОРЫТА)
060 ШЛИФОВАЛЬНАЯ (ПОЛКИ ЗАМКА СО СПИНКИ)
065 ШЛИФОВАЛЬНАЯ (ТОРЦА КОЗЫРЬКА С ВЫХ. КРОМКИ)
070 ШЛИФОВАЛЬНАЯ (ТОРЦА КОЗЫРЬКА С ВХ. КРОМКИ)
075 СЛЕСАРНАЯ (СНЯТИЕ ФАСОК)
080 СЛЕСАРНАЯ (СНЯТИЕ ЗАУСЕНЦЕВ)
090 КОМПЛЕКТОВКА (НА ЭЛЕКТРОЭРОЗИЮ)
095 ЭРОЗИОННАЯ (15 ОТВ.)
100 ПРОМЫВКА (В БЕНЗИНЕ И В АЦЕНТОНЕ)
105 ПРОКАЧКА (БЕНЗИНОМ)
110 КОНТРОЛЬ 15 ОТВ.
115 СЛЕСАРНАЯ (СНЯТИЕ ФАСКИ У ОТВЕРСТИЙ)
120 СЛЕСАРНАЯ (СНЯТИЕ ЗАУСЕНЦЕВ)
125 СЛЕСАРНАЯ (ВЫХОДНОЙ ЩЕЛИ)
130 ГИДРОАБРАЗИВНАЯ ОБРАБОТКА (ВНУТРЕННЕЙ ПОЛОСТИ 15 ОТВЕРСТИЙ ПЕРФОРАЦИИ ЩЕЛИ ВЫХОДНОЙ КРОМКИ)
135 ПРОКАЧИВАНИЕ (ВОДОЙ)
140 СЛЕСАРНАЯ (ВСКРЫТИЕ ОБРАЗЦА)
145 КОНТРОЛЬ (ВНУТРЕНЕЙ ПОЛОСТИ)
150 ГИДРОАБРАЗИВНАЯ ПО УСЛОВИЯМ ОПЕР. №40130
155 ПРОКАЧИВАНИЕ (ВОДОЙ) (СЛУЧ.) ПО УСЛОВИЯМ ОПЕР. №40135
160 СЛЕСАРНАЯ (ВСКЫТИЕ ОБРАЗЦА) (СЛУЧ.) ПО УСЛОВИЯМ ОПЕР. №40140
165 КОНТРОЛЬ (ВНУТРЕНЕЙ ПОЛОСТИ) (СЛУЧ.) ПО УСЛОВИЯМ ОПЕР. №40145
170 ПРОКАЧКА (БЕНЗИНОМ)
000 РЕНТГЕНКОНТРОЛЬ (ЧИСТОТЫ ВНУТР. ПОЛОСТИ)
190 СЛЕСАРНАЯ (ИЗГОТОВЛЕНИЕ ОБРАЗЦА ПРОРЕЗАНИЕ РИСКИ)
205 КОМПЛЕКТОВКА (НА ХРОМОАЛИТИРОВАНИЕ)
000 ХРОМОАЛИТИРОВАНИЕ
220 СЛЕСАРНАЯ (ПРОРЕЗАНИЕ РИСКИ НА ТВХОДНОМ ТОРЦЕ ХВОСТОВИКА)
225 ВХОДНОЙ КОНТРОЛЬ
230 СЛЕСАРНАЯ (ПОДРЕЗКА ВЫХОДНОЙ ЩЕЛИ)
235 СЛЕСАРНО-ПОЛИРОВАЛЬН (ВЫХОДНОЙ КРОМКИ)
240 СЛЕСАРНО-ПОЛИРОВАЛЬН (ВЫХОДНОЙ ЩЕЛИ)
245 СЛЕСАРНАЯ ПО УСЛОВИЯМ ОПЕР. 40120
247 ПРОКАЧКА (БЕНЗИНОМ) ПО УСЛОВИЯМ ОПЕР. 40170
255 ШЛИФОВАЛЬНАЯ (ПОДОШВЫ)
260 ШЛИФОВАЛЬНАЯ (КЛИНА)
265 СЛЕСАРНАЯ (СНЯТИЕ ЗАУСЕНЦЕВ)
270 ШЛИФОВАЛЬНАЯ ("ЕЛКИ")
275 КОНТРОЛЬ ("ЕЛКИ")
280 ШЛИФОВАЛЬНАЯ (ПОДОШВЫ)(СЛУЧАЙНАЯ)
285 ШЛИФОВАЛЬНАЯ (ПОЛКИ ЗАМКА СО СПИНКИ)
290 ШЛИФОВАЛЬНАЯ (ПОЛКИ ЗАМКА С КОРЫТА)
295 ШЛИФОВАЛЬНАЯ (ТОРЦА КОЗЫРЬКА С ВХ. КРОМКИ)
300 ШЛИФОВАЛЬНАЯ (ТОРЦА КОЗЫРЬКА С ВЫХ. КРОМКИ)
305 ШЛИФОВАЛЬНАЯ (ТОРЦА ЗАМКА С ВЫХ. КРОМКИ)
310 СЛЕСАРНАЯ (ПРИТУПЛЕНИЕ КРОМОК НА «ЕЛКЕ»)
315 ШЛИФОВАЛЬНАЯ (ТОРЦА ЗАМКА С ВХ. КРОМКИ)
320 ШЛИФОВАЛЬНАЯ (УСТУПА)
325 СЛЕСАРНАЯ (ПРИТУПЛЕНИЕ КРОМОК НА «ЕЛКЕ»)
335 ОТРЕЗНАЯ (ТЕХНОЛОГИЧ. БАБЫШКИ)
340 ШЛИФОВАЛЬНАЯ (ТОРЦА ПЕРА)
350 ШЛИФОВАЛЬНАЯ (КОЗЫРЬКА С ВЫХОДА)
355 ШЛИФОВАЛЬНАЯ (КОЗЫРЬКА С ВХОДА)
360 СЛЕСАРНАЯ (КОЗЫРЬКОВ)
380 ПРОКАЧКА (ВОДОЙ)
385 СЛЕСАРНАЯ (ВСКРЫТИЕ ОБРАЗЦА)
390 КОНТРОЛЬ (ВНУТРЕННЕЙ ПОЛОСТИ)
400 ПРОМЫВКА И СУШКА
405 КОНТРОЛЬ ЛЮМ1-ОВ
410 СЛЕСАРНАЯ (ИСПРАВЛ.)
415 КОНТРОЛЬ ВИХРЕТОКОВЫЙ
420 КОНТРОЛЬ (ГЕОМЕТРИИ)
425 СЛЕСАРНАЯ (СЛУЧАЙНАЯ) (ИСПРАВЛЕНИЕ)
430 ПРОКАЧИВАНИЕ (БЕНЗИНОМ)
435 ПРОМЫВКА (БЕНЗИНОМ)
440 ПРОМЫВКА (АЦЕТОНОМ)
450 ПРОМЫВКА И СУШКА
460 КОМПЛЕКТОВАНИЕ (НА ПОКРЫТИЕ АЖ-8+CRAL)
000 НАНЕСЕНИЕ ПОКРЫТИЯ АЖ-8
000 ХРОМОАЛИТИРОВАНИЕ (НАРУЖНОЙ ПОВЕРХНОСТИ)
480 КОНТРОЛЬ ВХОДНОЙ
495 РАЗМЕТКА (ЩЕЛЕЙ)
500 ЭРОЗИОННАЯ (1-ОЙ ЩЕЛИ)
505 ЭРОЗИОННАЯ (2-ОЙ ЩЕЛИ)
510 ЭРОЗИОННАЯ (ЗАПЯТОЙ)
515 РАЗМЕТКА (ОТВ. ДИАМ. 11)
520 ЭРОЗИОННАЯ (ОТВ. ДИАМ. 11)
523 РАЗМЕТКА (ОТВ. ДИАМ. 1)
525 ЭРОЗИОННАЯ (ОТВ. ДИАМ. 1)
527 ПРОМЫВКА (В БЕНЗИНЕ И АЦЕТОНЕ)
529 ЧЕХЛЕНИЕ (РЕЗ. ЧЕХОЛ)
490 РАСЧЕХЛЕНИЕ (РЕЗ. ЧЕХОЛ)
555 СЛЕСАРНАЯ (ХВОСТОВИКА)
560 СЛЕСАРНАЯ (КАНАВОК)
570 ПРОКАЧИВАНИЕ (БЕНЗИНОМ)
575 КОНТРОЛЬ ЛЮМ1-ОВ
580 СЛЕСАРНАЯ (ИСПРАВЛ.)
590 КОНТРОЛЬ (ГЕОМЕТРИИ)
595 КОМПЛЕКТОВАНИЕ (НА СВАРКУ)
600 СЛЕСАРНАЯ (ЗАЧ. ПОД ПЛАСТИНЫ)
610 ПРОМЫВКА (В АЦЕТОНЕ)
640 ПРОЛИВ (НА РАСХОД ВОДОЙ)
650 КОМПЛЕКТОВКА (НА НАНЕСЕНИЕ КЕРАМИЧЕСКОГО ПОКРЫТИЯ)
000 НАНЕСЕНИЕ КЕРАМИЧЕСКОГО ПОКРЫТИЯ ПО ТЕХНОЛОЛОГИИ ЛМЗ НПО «САТУРН»
000 ТЕРМООБРАБОТКА ПОСЛЕ НАНЕСЕНИЯ КЕРАМИЧЕСКОГО ПОКРЫТИЯ ПО ТЕХНОЛОЛОГИИ ЛМЗ НПО «САТУРН»
675 КОНТРОЛЬ ВХОДНОЙ
685 ОПРЕДЕЛЕНИЕ СТАТИЧЕСКОГО МОМЕНТА (ПО УСЛОВИЯМ «РОТОР ТВД»)
690 ПОСТАНОВКА ЛОПАТОК В ДИСК (ПО УСЛОВИЯМ ТП «РОТОР ТВД»)
695 ШЛИФОВАЛЬНАЯ (ПО УСЛОВИЯМ ТП «РОТОР ТВД»)
700 СЛЕСАРНАЯ (РАЗЛОПАЧИВАНИЕ) (ПО УСЛОВИЯМ ТП «РОТОР ТВД»)
705 СЛЕСАРНАЯ (ПО УСЛОВИЯМ ТП «РОТОР ТВД»)
710 ПРОКАЧКА (БЕНЗИНОМ)
715 ПРОМЫВКА (В БЕНЗИНЕ И АЦЕТОНЕ)
730 КОНТРОЛЬ ВХОДНОЙ
735 КОНТРОЛЬ ЛЮМ1-ОВ
740 СЛЕСАРНАЯ (ИСПРАВЛ.)
745 КОНТРОЛЬ УСТАНОВКИ
750 УПРОЧНЕНИЕ (ЗАМКА МИКРОШАРИКАМИ)
755 ПРОКАЧИВАНИЕ БЕНЗИНОМ
770 КОМПЛЕКТОВКА (НА КОНТРОЛЬ РЕКРИСТАЛЛИЗАЦИИ)
000 КОНТРОЛЬ РЕКРИСТАЛЛИЗАЦИИ
000 КОНТРОЛЬ ВНУТРЕННИХ ОСТАТОЧНЫХ НАПРЯЖЕНИЙ
000 УСТАЛОСТНЫЕ ИСПЫТАНИЯ
815 КЛЕЙМЕНИЕ (КЛЕЙМО КОНТРОЛЕРА)
кожух.m3d

Лопатка 117a.m3d

корпус.m3d

первая половина экрана.m3d

Лопатка 117б.m3d

вторая половинка экрана.m3d

Лопатка 117в.m3d

Лопатка 117.m3d

корпус1.m3d

справка.doc
дипломного или курсового проектирования
Название разрабатываемого объекта
Технологический процесс получения многослойного теплозащитного покрытия с анкерным эффектом
Аналогичное техническое решение (страна № патента или заявки МПК название изобретения дата публикации)
Многослойное высокотемпературное теплозащитное керамическое покрытие
Опубликовано: 27.09.2005
Основные признаки разрабатываемого объекта
Основные признаки аналога
согласно формуле изобретения
Многослойное высокотемпературное теплозащитное керамическое покрытие преимущественно для рабочих лопаток турбин газотурбинных двигателей состоит из двух или более слоев с первым подслоем содержащим 90 % ВПр36 и 10 % ПВНХ16Ю6Ит дискретного по толщине вдолль поверхности детали. Материалы первого подслоя соединяющего керамические слои с поверхностью детали выбираны таким образом чтобы обеспечить с одной стороны смачиваемость поверхности детали с другой стороны - анкерный эффект в керамических слоях. с целью обеспечения анкерного эффекта выполняют диффузионный вакуумный отжиг при температуре плавления припоя в течение двух-трех часов.
Многослойное высокотемпературное теплозащитное керамическое покрытие преимущественно для рабочих лопаток турбин газотурбинных двигателей состоит из двух или более слоев разделенных металлическими слоями. Материалы слоев соединяющих керамические слои выбирают таким образом чтобы материал имеющий меньший коэффициент теплового расширения располагался в зоне действия более высоких температур а материал имеющий больший коэффициент теплового расширения находился в зоне действия меньших температур. Высота керамических волокон не превышает его двадцати максимальных характерных поперечных размеров.
Отличительные признаки разрабатываемого объекта
Технико-экономические преимущества разрабатываемого объекта
Подслой содержащий 90 % припоя ВПр36 и 10 % ПВНХ16Ю6Ит нанесенный сквозь перфорированный экран с целью дискретности толщины по поверхности детали.
Технической задачей изобретения является увеличение адгезии покрытия и повышение ресурса детали.
Ф.И.О.__Латыган А.В. Руководитель дипломного проекта
МК14.frw

Обозначение документа
СМ Проф. Р УТ КР КОИД ЕН ОП Кшт Тпз Тшт
наименование оборудования
км Наименование детали
сб. единицы или материала Обозначение
код ОПП ЕВ ЕН КИ Н.расх.
Горизонтально-фрезерная
МК3.frw

Обозначение документа
СМ Проф. Р УТ КР КОИД ЕН ОП Кшт Тпз Тшт
наименование оборудования
км Наименование детали
сб. единицы или материала Обозначение
код ОПП ЕВ ЕН КИ Н.расх.
Промывка растворителем
Контроль геометрических параметров
Моечная машина ПБ-2618
МК17.frw

Обозначение документа
СМ Проф. Р УТ КР КОИД ЕН ОП Кшт Тпз Тшт
наименование оборудования
км Наименование детали
сб. единицы или материала Обозначение
код ОПП ЕВ ЕН КИ Н.расх.
Плазменное напыление островкового подслоя
МК19.frw

Обозначение документа
СМ Проф. Р УТ КР КОИД ЕН ОП Кшт Тпз Тшт
наименование оборудования
км Наименование детали
сб. единицы или материала Обозначение
код ОПП ЕВ ЕН КИ Н.расх.
Промывка растворителем
МК12.frw

Обозначение документа
СМ Проф. Р УТ КР КОИД ЕН ОП Кшт Тпз Тшт
наименование оборудования
км Наименование детали
сб. единицы или материала Обозначение
код ОПП ЕВ ЕН КИ Н.расх.
Нанесение покрытия АЖ-8
Хромалитирование наруж. поверхности
МК8.frw

Обозначение документа
СМ Проф. Р УТ КР КОИД ЕН ОП Кшт Тпз Тшт
наименование оборудования
км Наименование детали
сб. единицы или материала Обозначение
код ОПП ЕВ ЕН КИ Н.расх.
МК15.frw

Обозначение документа
СМ Проф. Р УТ КР КОИД ЕН ОП Кшт Тпз Тшт
наименование оборудования
км Наименование детали
сб. единицы или материала Обозначение
код ОПП ЕВ ЕН КИ Н.расх.
МК1.frw

наименование операции
Обозначение документа
СМ Проф. Р УТ КР КОИД ЕН ОП Кшт Тпз Тшт
наименование оборудования
Заготовка-отливка цеха 1б
Контроль геометрии входной
Сбор технол. отходов
МК4.frw

Обозначение документа
СМ Проф. Р УТ КР КОИД ЕН ОП Кшт Тпз Тшт
наименование оборудования
км Наименование детали
сб. единицы или материала Обозначение
код ОПП ЕВ ЕН КИ Н.расх.
МК6.frw

Обозначение документа
СМ Проф. Р УТ КР КОИД ЕН ОП Кшт Тпз Тшт
наименование оборудования
км Наименование детали
сб. единицы или материала Обозначение
код ОПП ЕВ ЕН КИ Н.расх.
МК2.frw

Обозначение документа
СМ Проф. Р УТ КР КОИД ЕН ОП Кшт Тпз Тшт
наименование оборудования
км Наименование детали
сб. единицы или материала Обозначение
код ОПП ЕВ ЕН КИ Н.расх.
Контроль геом. парам.
МК7.frw

Обозначение документа
СМ Проф. Р УТ КР КОИД ЕН ОП Кшт Тпз Тшт
наименование оборудования
км Наименование детали
сб. единицы или материала Обозначение
код ОПП ЕВ ЕН КИ Н.расх.
Контроль геометрических параметров
МК9.frw

Обозначение документа
СМ Проф. Р УТ КР КОИД ЕН ОП Кшт Тпз Тшт
наименование оборудования
км Наименование детали
сб. единицы или материала Обозначение
код ОПП ЕВ ЕН КИ Н.расх.
МК20.frw

Обозначение документа
СМ Проф. Р УТ КР КОИД ЕН ОП Кшт Тпз Тшт
наименование оборудования
км Наименование детали
сб. единицы или материала Обозначение
код ОПП ЕВ ЕН КИ Н.расх.
Слесарная (исправл.)
МК22.frw

Обозначение документа
СМ Проф. Р УТ КР КОИД ЕН ОП Кшт Тпз Тшт
наименование оборудования
км Наименование детали
сб. единицы или материала Обозначение
код ОПП ЕВ ЕН КИ Н.расх.
МК13.frw

Обозначение документа
СМ Проф. Р УТ КР КОИД ЕН ОП Кшт Тпз Тшт
наименование оборудования
км Наименование детали
сб. единицы или материала Обозначение
код ОПП ЕВ ЕН КИ Н.расх.
Промывка в растворителе
МК18.frw

Обозначение документа
СМ Проф. Р УТ КР КОИД ЕН ОП Кшт Тпз Тшт
наименование оборудования
км Наименование детали
сб. единицы или материала Обозначение
код ОПП ЕВ ЕН КИ Н.расх.
Плазменное напыление ТЗП
Определение статич. момента
МК10.frw

Обозначение документа
СМ Проф. Р УТ КР КОИД ЕН ОП Кшт Тпз Тшт
наименование оборудования
км Наименование детали
сб. единицы или материала Обозначение
код ОПП ЕВ ЕН КИ Н.расх.
Контроль вихретоковый
МК21.frw

Обозначение документа
СМ Проф. Р УТ КР КОИД ЕН ОП Кшт Тпз Тшт
наименование оборудования
км Наименование детали
сб. единицы или материала Обозначение
код ОПП ЕВ ЕН КИ Н.расх.
Контроль объем. напр.
Усталостные испытания
МК11.frw

Обозначение документа
СМ Проф. Р УТ КР КОИД ЕН ОП Кшт Тпз Тшт
наименование оборудования
км Наименование детали
сб. единицы или материала Обозначение
код ОПП ЕВ ЕН КИ Н.расх.
Промывка растворителем
МК5.frw

Обозначение документа
СМ Проф. Р УТ КР КОИД ЕН ОП Кшт Тпз Тшт
наименование оборудования
км Наименование детали
сб. единицы или материала Обозначение
код ОПП ЕВ ЕН КИ Н.расх.
Промывка растворителем
Контроль геометрических параметров
Титульник ТП.frw

механической обработки детали
ГОСТ 3.1105-84 Форма 2
Руководитель проекта
УФИМСКИЙ ГОСУДАРСТВЕННЫЙ АВИАЦИОННЫЙ
ТЕХНИЧЕСКИЙ УНИВЕРСИТЕТ
МК16.frw

Обозначение документа
СМ Проф. Р УТ КР КОИД ЕН ОП Кшт Тпз Тшт
наименование оборудования
км Наименование детали
сб. единицы или материала Обозначение
код ОПП ЕВ ЕН КИ Н.расх.
Промывка растворителем
плакат спец.cdw

Рисунок 3.2 ? Диаграмма состояния сплавов системы медь-никель
Рисунок 3.3 ? Диаграмма состояния сплавов системы медь-фосфор
Рисунок 3.4 ? Диаграмма состояний сплавов системы серебро-палладий
сборочный.cdw

Таблица2.cdw

Общий1.1 пл.cdw

порошкового распылителя:
- подача порошка (осевая);
- подача порошка (радиальная);
рисунок 2.Схема высокоскоростного
проволочного распылителя:
- направляющая трубка.
Распылитель с двойным воздушным соплом:
- дополнительное воздушное сопло;
Схема установки газопламенного напыления:
- порошковый распылитель;
- проволочный распылитель;
- порошковый питатель;
- бухта проволоки на вращающемся столе;
- ротаметры газовые;
- воздушный ротаметр;
Схема порошкового распылителя:
Схема плазменного распылителя:
Плазменные распылители:
а - с самоустанавливающейся дугой;
б - с фиксированной дугой.
Схемы плазменных распылителей:
б - проволочного ("проволока - анод
Схемы подачи порошка в
- в плазменную струю;
- подача охлаждающей воды;
- подача плазмообразующего газа;
Схема осаждения покрытий методом ВПТВЭ
- поток осаждаемого вещества;
Плотность покрытий достигает 99%.
В качестве наносимого материала
используют порошки карбидов
Cu и др.Для увеличения скорости
частиц увеличивают скорость
истечения продуктов сгорания путем
повышения давления в камере
конструкцию соплового аппарата
вводят сопло Лаваля.
б - расширяющееся (сопло Лаваля).
рисунок 5-Проволочный распылитель
Современный проволочный газопламенный
распылитель типа MDP - 115
(рис. 5) с приводом от электродвигателя
мощностью 150Вт работает на проволоке
материалов ( коррозионно - стойкие и
никелевой и кобальтовой основах). Производительность по цветным металлам -
по стали и сплавам - до 9 кгч
расход кислорода - 50 лмин
ацетилена или пропана - до 20 л мин. Давление воздуха - 0
Современная автоматическая установка плазменного напыления
ТСЗП-MF-P-1000 работает на смеси газов аргона
при расходе аргона до 100 лмин
транспортирующего газа - до 30 лмин.
Производительность напыления по металлическим сплавам -
Плотность порошковых покрытий - 92 - 99%
сцепления - 30 80 МПа
Сущность анкерного эффекта заключается в напылении прерывистого
подслоя содержащего до 90% припоя
остальное - ПВНХ16Ю6Итм
(аналог СДП-2). При напылении на него ТЗП и дальнейшей
термообработке припой смачивает ТЗП
повышая таким образом адгезию.
Вывод: несмотря на перечисленные возможности рассмотренных методов напыления
метод плазменного напыления с использованием анкерного эффекта
является наиболее оптимальным с точки зрения получения более высоких эксплуатационных свойств покрытий
Установка для осаждения покрытий методом ВПТВЭ
АПН-250 с установленными лопатками ТВД
Современные установки для вакуумного напыления предназначены для
нанесения покрытий со скоростью порядка 70-100 мкмч
электропроводящих материалов. Недостатком является отсутствие
технологических справочников и методик назначения режимов
Высокоскоростное напыление
Газопламенное напыление
Плазменное напыление
Анализ методов получения защитных жаростойких покрытий
Чертеж совмещенной схемы.cdw

Чертеж кожуха.cdw

экономика1.1 пл.cdw

заготовка1.2.cdw

ЖС32-ВИ ТУ 1-809-1025-98
Вид заготовки - отливка по выплавляемой модели с
монокристальной структурой кристалографической ориентацией в
соответствии с техническими условиями № 104.03.ТУ43
Допуски на размеры и шероховатость литых необрабатываемых
поверхностей согласно чертежу и ОСТ 1.41793-78 класс точности
Выходная кромка обработана электрохимическим способом с
припуском на окончательную обработку
Шероховатость необрабатываемых поверхностей спинки
плавность перехода между
сечениями и переходов пера в полку
сопряжение радиусов R с
поверхностями корыта и спинки. Расположение маркировки-по
контрольному образцу.
Отклонение наружного профиля во всех заданных сечениях от
теоретического профиля
включая разворот и смещение в пределах
Отклонение внутренней полости в зоне замка от оси X-X не
Заготовка поставляется с заверенутой до упора и запаянной
прошедшая все виды контроля. С
заключением о испытании механических свойств
карте изготовления за контроль рентгенопросвечиванием
риски и другие механические повреждения на
поверхностях пера и полок не допускаются
Затекание припоя на поверхность пера в зоне заглушки не
Заготовка имеет маркировки :
а) чертежный номер "020" на ножке со стороны спинки
ЭХ" высота шрифта 3 5 мм
б) индивидуальный номер на клине со стороны корыта
в) индивидуальный номер на ножке со стороны корыта
На каждую заготовку оформляется карта изготовления с
отметками о выполненной работе и годности детали
Заготовка оправляется в механический цех в ячейковой таре
обработка лист 1.cdw

оп. 40095 Электроэрозионная
оп. 41000 Рентгенконтроль
оп. 42205 Комплектовка
оп. 43000 Хромоалитирование
оп.44315 Шлифовальная
оп.40005 Шлифовальная
оп.40010 Шлифовальная
оп.40030 Шлифовальная
оп.40035 Сверлильная
ОП.40040 Шлифовальная
оп.40060 Шлифовальная
оп.40065 Шлифовальная
оп.40070 Шлифовальная
оп.44255 Шлифовальная
оп.44260 Шлифовальная
оп.44270 Шлифовальная
ОП.44285 Шлифовальная
оп.44290 Шлифовальная
оп.44295 Шлифовальная
оп.44300 Шлифовальная
оп.44305 Шлифовальная
граф.cdw

Чертеж первой половины экрана.cdw

Экран изготавливается из перфорированного листа Д16
ГОСТ4784-97 толщиной 3 мм штамповкой.
Прилегание экрана к лопатке обеспечить доводкой внутренней
поверхности по контрольному образцу.
* - размеры для справок.
Допуски на свободные размеры:
Координаты сечений внутреннего профиля экрана
Лопатка ТВД 2.cdw

полке по контрольному образцу
Размеры по роликам для
до базовой плоскости
притупить по контуру
проходящая через точку К
Скруглить по контуру зуба
Скруглить по контуру
до скругления и полировки
ЖС32-ВИ ТУ 1-809-1025-98
Отливка лопатки с монокристальной структурой
кристаллографической
отклонение от оси Z лопатки не более 10
Литье производить с термовремменной обработкой расплава по техническим
условиям №104.03ТУ43 с обеспечением
. Обеспечивается по ОСТ1 42314-89.
Проверить рентгенпросвечиванием полноту удаления керамики из
внутренней полости. Наличие керамики не допускается.
Внутреннюю полость окончательно обработанной
контролировать прокачкой воды под давлением 19
) на входе в лопатку.
Расход воды при одновремменой проливке (отв.Е
через входную щель - (185
контролировать на истечение.
Обеспечить по ОСТ1 42314-89.
Допуски на размеры и шероховатости литых
поверхностей по ОСТ1 41793-78
Выходную кромку в заготовке выполнять с технологическим приливом
выполненным за пределами хорды
прилив удалить электрохимической
. Испытания по определению внутренних остаточных напряжений
производить по 104.01.И66 в соответствии с разделом 3
Шероховатость необрабатываемых поверхностей пера
плавность перехода между сечениями и переходов пера в полку
радиусов R с поверхностями корыта и спинки
шероховатость зубьев
расположения маркировки и клейм - по контрольному
Размеры геометрии профиля пера по сечениям
размеры: толщина стенок
радиусов сопряжения пера с полкой
наружной поверхности замковой полки -
до нанесения покрытия.
Предел выносливости контролировать по техническим условиям
Отклонения наружного профиля во всех заданных сечениях от
теоретического профиля
включая разворот и смещение в пределах (
Координаты даны без учета покрытия. Допускается отклонение наружного
) мм в одном сечении на длине 15 мм.
Во всех сечениях расстояние между контуром корыта и спинки
внутренней полости лопатки обеспечить инструментом в пределах (
Контролировать разрезкой по технологической документации завода
Выходную кромку со стороны корыта и спинки проверить токовихревым
методом до нанесения покрытия по технологической документации.
Смещение размера ножки Т
в плоскости Y-Y относительно оси
симметрии хвостовика X-X - не более 0
мм при этом максимальный перекос
относительно плоскости
Отклонение плоскости замера смещения от плоскости Y-Y- 1 мм.
Смещение плоскости симметрии хвостовика относительно плоскости
Взаимное смещение продольных образующих рабочих поверхностей одной
гребенки относительно другой в плоскостях параллельных плоскостях
симметрии X-X не более 0
Замерять в плоскости Y-Y. Допускается отклонение по плоскости Y-Y-1
Взаимный перекос рабочих поверхностей зубьев одной гребёнки
относительно другой 0
Замерять на расстоянии 2 мм от торцев хвостовика.
на длине хвостовика - не более 0
Разность отклонений размеров - не более М
Припой ВПр 36 ТУ1 595-160-83. Пайка и контроль пайки по
технологической документации. Пайку производить до покрытия поверхности
Допуск перпендикулярности продольных образующих рабочих
поверхностей профиля хвостовика относительно плоскости Y-Y-0
подвергнуть гидроаброзивной обработке по
технологической документации.
Наличие дефектного слоя материала в отв. Л
после АЖО не допускается.
Контролировать разрезкой одной лопатки от партии 3000 шт.
Размеры определяющие профиль хвостовика проверять по
технологической документации.
Шероховатость поверхностных элементов пера лопатки и других
поверхностей обработанных методом электроэрозии - по контрольному
изготавливать методом электроэрозии в плоскости
параллельной оси ОZ. Расстояние от края отверстия до наружного профиля
Допускается (до покрытия поверхн. Я) обработка наружной поверхности
профиля по высоте пера
зачистка отдельных мест поверхности замковой
полки с шероховатостью по контрольному образцу.
притупить с последующей АЖО по
технологической документации. Принимать по контрольному образцу.
Окончательную механическую обработку профиля пера и поверхности Г
выходной кромки производить до покрытия поверхности Я.
Места перехода от обработанных поверхн. хвостовика к литым
поверхностям ребер и ножки хвостовика притупить по контрольному образцу.
Переход радиуса выходной кромки пера к полке по контрольному образцу.
Все подполочные поверхности (радиус перехода полки
подошву хвостовика) обработать микрошариками по
При изготовлении лопатки по варианту исполнения каналы Ш
подошвехвостовика заглушить контактной точечной сваркой деталей поз. 4
и 5. Перекрытие каналов Ш
деталями поз. 4 и 5 обеспечить
Выступание дет. поз. 4 и 5 за поверхности Р
Внешний вид принимать по контрольному образцу.
алитировать шликерным методом после
окончательной обработки в последующей сборочной единице по
технологческой документации. Толщина алитированного слоя 0
Допускается перекрытие многокомпонентнтго покрытия алитированным слоем
на участках шириной до 1
Принимать по контрольному образцу. Допускается местное наличие
алитированного слоя на поверхностях Ю и Щ принимать по контрольному
Калибровку и нарезку резьбы отв. М
производить по оси литого
отверстия. Деталь поз. 3 завернуть до упора.
Установку дет. поз. 3 проверить рентгенпросвечиванием.
Принимать по контрольному образцу - рентгеновскому снимку.
Допускается частичное перекрытие верхнего отверстия Л
Контроль профиля пера
прилегающих к перу поверхн. полки хвостовика
обработку хвостовикаи контроль смещения хвостовика
неперпендикулярности продольных образующих рабочих поверхностей
хвостовика производить от одних технологических баз.
Допускается след от упора приспособления на поверхности полки.
Принимать по контрольному образцу.
Подготовка поверхности Я (перо
радиус перехода и полку под покрытие
по технологической документации.
Шероховатость поверхностей
Допускаются следы мехобработки на поверхности Я после подготовки под
покрытие. Принимать по контрольному образцу.
и места притупления кромок выходной щели
нанести многокомпонентное покрытие из сплава ВСДП-11 (AlSiY) методом
ваккумно-плазменной технологии высоких энергий (ВПТВЭ) по 104.03ТУ44.
Допускается утонение покрытия до 0
0 мм на полке шириной 15 мм
выходной кромки лопатки со стороны спинки и корыта.
Допускается наличие покрытия на торцевых поверхностях полки
на необрабатываемых литейных поверхностях ножки.
Шероховатость поверхности после покрытия . Допускается участки с
шероховатостью суммарной площадью не более 5% поверхности пера.
Допускается наличие многокомпонентного покрытия на поверхности отв. Л
На внутреннюю поверхеность нанести покрытие CrAl по
технологической документации. Толщина покрытия 0
Допускается отсутствие покрытия на поверхности отв. Л
выхода на спинку пера.
Наружную поверхность до и после нанесения покрытия подвергнуть АЖО
Прилегающие к поверхностям Ю
щелей притупить после окончательной обработки в последующей
Наличие рекристализованного слоя на зубьях хвостовика
и на торцах хвостовика не допускается.
Поверхность внутренней полости лопатки до и после нанесения
покрытия подвергнуть гидроабразивной обработке по технологической
Замер толщин стенок производить по технологической документации
- в сечениях согласно табл. 2
при разрезке профиля согласно пункту 9. Замер
толщин m и n в сеч. А
производить согласно табл. 3 при
разрезке профиля согласно пункту 9.
Разностенность корыта и спинки (
Допускается при замере толщин
перемещение датчика на 1
мм от номинального положения в любом направлении
min в сеч. А1-А1 А5-А5 согласно табл. 2 перемещение мерителя
) мм от номинального положения в направлении параллельной оси ОZ.
Допускается увеличение на 0
допуска толщин стенок пера в одной точке в каждом сечении кроме толщин
Изготовление мат. части вести с учётом инструкции 96ФП.01И38.
Маркировать шрифтом 3 5
допускается маркировать последние три
допускается нанесение других маркировок на торце лопатки
допускается местное удаление окисной пленки.
Допускается маркировать шрифтом 3 5 номер плавки.
Маркировать номер комплекта и номер паза в пследующей сборочной
Размеры в скобках- после сборки.
Размеры обеспечить инструментом.
Размеры и сечения для справок.
Диаметр измерительного ролика по ГОСТ 2475-88 класс 1.
Размеры в плоскости а-а
Общие требования к изготовлению - по ОСТ1 00450-82.
Толщины стенок т и п
Координаты отверстий П1
от базовой плоскости
Притупить по контрольному образцу
по контуру до покрытия
Чертеж второй половины экрана.cdw

Экран изготавливается из перфорированного листа Д16
ГОСТ4784-97 толщиной 3 мм штамповкой.
Прилегание экрана к лопатке обеспечить доводкой внутренней
поверхности по контрольному образцу.
* - размеры для справок.
Допуски на свободные размеры:
Профиль верхней крышки повторяет наружний профиль экранов в
Координаты сечений внутреннего профиля экрана
корпус.cdw

МК14.frw

Обозначение документа
СМ Проф. Р УТ КР КОИД ЕН ОП Кшт Тпз Тшт
наименование оборудования
км Наименование детали
сб. единицы или материала Обозначение
код ОПП ЕВ ЕН КИ Н.расх.
Горизонтально-фрезерная
МК3.frw

Обозначение документа
СМ Проф. Р УТ КР КОИД ЕН ОП Кшт Тпз Тшт
наименование оборудования
км Наименование детали
сб. единицы или материала Обозначение
код ОПП ЕВ ЕН КИ Н.расх.
Промывка растворителем
Контроль геометрических параметров
Моечная машина ПБ-2618
МК17.frw

Обозначение документа
СМ Проф. Р УТ КР КОИД ЕН ОП Кшт Тпз Тшт
наименование оборудования
км Наименование детали
сб. единицы или материала Обозначение
код ОПП ЕВ ЕН КИ Н.расх.
Плазменное напыление островкового подслоя
МК19.frw

Обозначение документа
СМ Проф. Р УТ КР КОИД ЕН ОП Кшт Тпз Тшт
наименование оборудования
км Наименование детали
сб. единицы или материала Обозначение
код ОПП ЕВ ЕН КИ Н.расх.
Промывка растворителем
МК12.frw

Обозначение документа
СМ Проф. Р УТ КР КОИД ЕН ОП Кшт Тпз Тшт
наименование оборудования
км Наименование детали
сб. единицы или материала Обозначение
код ОПП ЕВ ЕН КИ Н.расх.
Нанесение покрытия АЖ-8
Хромалитирование наруж. поверхности
МК8.frw

Обозначение документа
СМ Проф. Р УТ КР КОИД ЕН ОП Кшт Тпз Тшт
наименование оборудования
км Наименование детали
сб. единицы или материала Обозначение
код ОПП ЕВ ЕН КИ Н.расх.
МК15.frw

Обозначение документа
СМ Проф. Р УТ КР КОИД ЕН ОП Кшт Тпз Тшт
наименование оборудования
км Наименование детали
сб. единицы или материала Обозначение
код ОПП ЕВ ЕН КИ Н.расх.
МК1.frw

наименование операции
Обозначение документа
СМ Проф. Р УТ КР КОИД ЕН ОП Кшт Тпз Тшт
наименование оборудования
Заготовка-отливка цеха 1б
Контроль геометрии входной
Сбор технол. отходов
МК4.frw

Обозначение документа
СМ Проф. Р УТ КР КОИД ЕН ОП Кшт Тпз Тшт
наименование оборудования
км Наименование детали
сб. единицы или материала Обозначение
код ОПП ЕВ ЕН КИ Н.расх.
МК6.frw

Обозначение документа
СМ Проф. Р УТ КР КОИД ЕН ОП Кшт Тпз Тшт
наименование оборудования
км Наименование детали
сб. единицы или материала Обозначение
код ОПП ЕВ ЕН КИ Н.расх.
МК2.frw

Обозначение документа
СМ Проф. Р УТ КР КОИД ЕН ОП Кшт Тпз Тшт
наименование оборудования
км Наименование детали
сб. единицы или материала Обозначение
код ОПП ЕВ ЕН КИ Н.расх.
Контроль геом. парам.
МК7.frw

Обозначение документа
СМ Проф. Р УТ КР КОИД ЕН ОП Кшт Тпз Тшт
наименование оборудования
км Наименование детали
сб. единицы или материала Обозначение
код ОПП ЕВ ЕН КИ Н.расх.
Контроль геометрических параметров
МК9.frw

Обозначение документа
СМ Проф. Р УТ КР КОИД ЕН ОП Кшт Тпз Тшт
наименование оборудования
км Наименование детали
сб. единицы или материала Обозначение
код ОПП ЕВ ЕН КИ Н.расх.
МК20.frw

Обозначение документа
СМ Проф. Р УТ КР КОИД ЕН ОП Кшт Тпз Тшт
наименование оборудования
км Наименование детали
сб. единицы или материала Обозначение
код ОПП ЕВ ЕН КИ Н.расх.
Слесарная (исправл.)
МК22.frw

Обозначение документа
СМ Проф. Р УТ КР КОИД ЕН ОП Кшт Тпз Тшт
наименование оборудования
км Наименование детали
сб. единицы или материала Обозначение
код ОПП ЕВ ЕН КИ Н.расх.
МК13.frw

Обозначение документа
СМ Проф. Р УТ КР КОИД ЕН ОП Кшт Тпз Тшт
наименование оборудования
км Наименование детали
сб. единицы или материала Обозначение
код ОПП ЕВ ЕН КИ Н.расх.
Промывка в растворителе
МК18.frw

Обозначение документа
СМ Проф. Р УТ КР КОИД ЕН ОП Кшт Тпз Тшт
наименование оборудования
км Наименование детали
сб. единицы или материала Обозначение
код ОПП ЕВ ЕН КИ Н.расх.
Плазменное напыление ТЗП
Определение статич. момента
МК10.frw

Обозначение документа
СМ Проф. Р УТ КР КОИД ЕН ОП Кшт Тпз Тшт
наименование оборудования
км Наименование детали
сб. единицы или материала Обозначение
код ОПП ЕВ ЕН КИ Н.расх.
Контроль вихретоковый
МК21.frw

Обозначение документа
СМ Проф. Р УТ КР КОИД ЕН ОП Кшт Тпз Тшт
наименование оборудования
км Наименование детали
сб. единицы или материала Обозначение
код ОПП ЕВ ЕН КИ Н.расх.
Контроль объем. напр.
Усталостные испытания
МК11.frw

Обозначение документа
СМ Проф. Р УТ КР КОИД ЕН ОП Кшт Тпз Тшт
наименование оборудования
км Наименование детали
сб. единицы или материала Обозначение
код ОПП ЕВ ЕН КИ Н.расх.
Промывка растворителем
МК5.frw

Обозначение документа
СМ Проф. Р УТ КР КОИД ЕН ОП Кшт Тпз Тшт
наименование оборудования
км Наименование детали
сб. единицы или материала Обозначение
код ОПП ЕВ ЕН КИ Н.расх.
Промывка растворителем
Контроль геометрических параметров
Титульник ТП.frw

механической обработки детали
ГОСТ 3.1105-84 Форма 2
Руководитель проекта
УФИМСКИЙ ГОСУДАРСТВЕННЫЙ АВИАЦИОННЫЙ
ТЕХНИЧЕСКИЙ УНИВЕРСИТЕТ
МК16.frw

Обозначение документа
СМ Проф. Р УТ КР КОИД ЕН ОП Кшт Тпз Тшт
наименование оборудования
км Наименование детали
сб. единицы или материала Обозначение
код ОПП ЕВ ЕН КИ Н.расх.
Промывка растворителем
общий 07.doc
1Разработка маршрутного технологического процесса изготовления рабочей лопатки ТВД12
1.1Анализ конструкции и условия работы детали в изделии13
1.2Анализ технологичности конструкции детали17
1.3Качественная оценка технологичности18
1.4Количественная оценка технологичности21
1.5Обоснование выбора исходной заготовки22
1.5.1Выбор заготовки с точки зрения обеспечения требуемой точности22
1.5.2Выбор заготовки с точки зрения себестоимости25
1.6Разработка технологического процесса26
1.6.1Анализ базового технологического процесса26
1.6.2Анализ разрабатываемого маршрутного технологического процесса27
1.7Размерный анализ технологического процесса27
2Разработка операционного технологического процесса изготовления рабочей лопатки ТВД31
2.1Выбор средств технологического оснащения расчет режимов обработки норм времени для операции №51020 «Плазменное напыление островкового подслоя»31
2.1.1Выбор средств технологического оснащения33
2.1.2Расчет режима обработки38
2.1.3Расчет штучного времени39
2.2Выбор средств технологического оснащения расчет режимов обработки норм времени для операции № 50510 «Электроэрозионная»41
2.2.1Выбор средств технологического оснащения41
2.2.2Расчет режима обработки42
2.2.3Расчет штучного времени45
2.3Выбор средств технологического оснащения расчет режимов обработки норм времени для операции №40010 «Шлифовальная»46
2.3.1Выбор средств технологического оснащения46
2.3.2Расчет режима обработки47
2.3.3Расчет штучного времени49
Конструкторская часть51
1Разработка приспособления для плазменного напыления анкерного подслоя многослойного керамического покрытия на деталь «Рабочая лопатка ТВД»52
2Описание построения «островкового» подслоя с анкерным эффектом52
3Разработка способа получения теплозащитного покрытия с островковой переходной зоной для лопаток турбины ГТД.54
4Рассмотрение составных элементов в приспособлении для напыления
5Расчет приспособления на точность57
6Расчет элемента приспособления58
7Подбор электродвигателя60
8Подбор оборудования для автоматизации процесса нанесения покрытия61
9Подбор дополнительных элементов оснастки64
10Проектирование экранов64
11Порядок сборки оснастки65
1Припои на медной основе68
1.2Медно-цинковые припои69
1.3Медно-никелевые припои73
1.4Медно-фосфорные припои76
1.5Медно-германиевые припои77
2Серебряные припои78
3Палладиевые припои81
5Жаропрочные и коррозиционно-стойкие припои на никелевой основе86
6Марганцевые припои90
Организационно-экономическая часть проекта95
1SWOT – анализ предлагаемого способа создания жаростойкого покрытия96
2Определение трудоемкости выполнения НИР97
3Построение сетевого графика выполнения НИР102
4Определение плановой себестоимости проведения НИР102
5 Определение прибыли и договорной цены НИР107
6Оценка показателей технического уровня (инновационного потенциала)108
Безопасность и экологичность проекта114
1Шум в производственных условиях115
1.1Физические характеристики шума115
1.2Нормирование шума на рабочих местах116
1.3Воздействие шума на организм человека. Средства и методы защиты от шума117
1.4Средства и методы защиты от шума в производственных условиях118
1.5Звукоизоляция и звукопоглощение119
1.6Средства индивидуальной защиты человека от шума119
1.7Расчет звукоизолирующей кабины120
2Очистка сточных вод121
Список литературы129
Рабочие лопатки турбины являются наиболее нагруженными деталями в основном определяющими эффективность надежность и в конечном счете ресурс газотурбинных двигателей. Ресурс работы лопаток в двигателях для военной авиации составляет 500 1000 ч. Лопатки работают в условиях высоких температур воздуха (газа) достигающих для турбины 800 1200 0С. Многократное изменение тепловых режимов работы двигателя - быстрый нагрев в момент запуска и быстрое охлаждение при остановке двигателя - вызывает циклическое изменение термических напряжений характеризуемое как тепловая усталость.
Профильная часть пера и хвостовик лопаток помимо растяжения и изгиба от центробежных сил изгиба и кручения от газового потока испытывают переменные напряжения от вибрационных нагрузок амплитуда и частота которых изменяются в широких пределах.
Надежность рабочих лопаток турбины зависит не только от конструктивной прочности сопротивления циклическим и длительным статическим нагрузкам но и от технологии их изготовления [1].
Деталь «Рабочая лопатка ТВД» (1402.140100.887 ЧД) изготовлена из сложнолегированного никелевого сплава ЖС32 важнейшим преимуществом которого является высокая термическая стабильность термостойкость высокая сопротивляемость разрушению при термической и малоцикловой усталости. Все эти качества позволяют успешно использовать ЖС32 в качестве материала для ответственной детали двигателя типа АЛ-31Ф истребителя «Су-27» [2 с.92].
Увеличение температуры газа в авиационных ГТД и рост агрессивности топлива используемого в промышленных и корабельных ГТУ привели к тому что однослойные многокомпонентные покрытия Me-Cr-Al-Y получаемые конденсацией в вакууме все же исчерпывают свой защитный ресурс за весьма ограниченное время (300-6000 ч). Усовершенствования в технологии нанесения металлических покрытий не привели к кардинальному решению вопроса по созданию покрытий более стойких к высокотемпературной газовой коррозии и эрозии чем однослойные покрытия типа Me-Cr-Al-Y. В современных ГТД для защиты охлаждаемых лопаток от воздействия теплового потока необходимо чтобы жаростойкие защитные покрытия обладали не только высокой стойкостью к высокотемпературной газовой коррозии и эрозии в агрессивной среде продуктов сгорания топлива но и служили термическим барьером по отношению к тепловому излучению газового потока (рисунок 1.1). Для этого необходимо разработать новые многослойные покрытия которые обеспечат мультипликацию необходимых свойств.
Рисунок 1.1 - Схема иллюстрирующая влияние теплозащитного покрытия на снижение средней температуры стенки турбинной лопатки
В данном проекте были поставлены следующие задачи:
изучение рабочего чертежа детали анализ ее конструкции и условия работы в изделии;
оценка технологичности изготовления детали;
выбор и обоснование метода получения заготовки оценка КИМ;
разработка плана обработки детали расчет операционных размеров;
разработка операционных технологических процессов (на 3÷4 операции) выбор инструмента расчет режимов обработки нормы штучного времени;
разработка технологии нанесения жаростойкого многослойного покрытия с температурой жаростойкости до 1050 0С.
Технологическая часть
1Разработка маршрутного технологического процесса изготовления рабочей лопатки ТВД
Создание авиационных газотурбинных двигателей (ГТД) 4 - го поколения на рубеже 70 - 80-х годов потребовало разработки новых жаропрочных сплавов и перехода от равноосной кристаллической структуры литых лопаток турбин высокого давления (ТВД) к лопаткам с направленной и монокристаллической структурой что было вызвано ростом температуры рабочего газа на входе в турбину с 1500 до 1700-1750 К и более.
Значительное повышение температуры газа на входе в турбину высокая доля затрат энергии на охлаждение сопловых и рабочих лопаток турбины и необходимость снижения этих затрат энергии обусловили рост рабочей температуры лопаток турбин на 50 – 100°С и более что привело к резкому снижению защитных свойств традиционных диффузионных жаростойких покрытий и ресурса лопаток турбин до 50 – 100 часов. Низкие защитные свойства диффузионных покрытий при высоких температурах невысокая их пластичность склонность к образованию трещин термоусталости неудовлетворительная точность процессов их получения привели к снижению надежности их работы. Поэтому в конце 70 – х и начале 80–х годов возникла острая необходимость в разработке новых покрытий и создании принципиально новых технологических процессов получения покрытий.
Выходом в сложившейся ситуации стали разработанные в ВИАМ вакуумно-плазменные технологии высоких энергий (ВПТВЭ) получения защитных покрытий.
Но в настоящее время имеется тенденция к увеличению рабочей температуры лопаток турбины вследствие увеличения мощности двигателя что приводит к необходимости разработки новых ТЗП. В данной работе рассматривается технология нанесения многослойного керамического ТЗП с анкерным эффектом.
1.1Анализ конструкции и условия работы детали в изделии
Деталь «Рабочая лопатка ТВД» - это деталь входящая в состав газотурбинного двигателя АЛ-31Ф и представляющая собой деталь сложного геометрического профиля. Данная деталь работает при высоких температурах и сильных знакопеременных циклических нагрузках следовательно при ее проектировании необходимо обеспечить высокую жаропрочность и высокую сопротивляемость разрушению при термической и малоцикловой усталости. Поэтому лопатку изготовляют полой с циклонно-вихревой системой охлаждения. В переднюю полость лопатки воздух поступает через отверстия в наружной полке а затем через отверстия в дефлекторе обеспечивает струйное охлаждение внутренних стенок и выходит через отверстия перфораций во входной кромке. Отверстия перфораций изготавливают электроэрозионным способом. Они предназначены для пленочного охлаждения воздухом так как температура в зоне входной кромки очень высокая ( Т 1000 ºС) [2 c.8]. Кроме того удлиненная ножка способствует уменьшению количество тепла передаваемого от лопатке к диску. Данные полости невозможно получить другим путем кроме как литья по выплавляемым моделям. Так как сплав ЖС32 наиболее сильно подходит по всем предъявляемым требованиям выбираем его. Единственный недостаток данного сплава - черезвычайная трудность при обработке. Поэтому заготовку получают как можно более приближенной в детали. При изготовлении каждая деталь подвергается контролю а детали - представители - лабораторным испытаниям.
В процессе работы рабочие лопатки турбины высокого давления подвергаются окислению и газодинамической коррозии т. е. физическому разрушению. Несмотря на то что тугоплавкие металлы (Cr Ta Nb Mo W Re) имеют высокую температуру плавления они не обладают термодинамической устойчивостью в окислительной атмосфере. Вот почему напыление температурозащитных покрытий на рабочие лопатки ТВД является столь важной стадией обработки. Наиболее жаростойкими являются керамические покрытия.
Конструкция детали черезвычайно сложная что приводит к трудностям изготовления. Для формирования елочного профиля замка применяется метод глубинного шлифования а большинство остальных операций формообразования выполняются либо методами КПЭ (электроэрозия) либо шлифованием.
Главный недостаток детали – изготовление из труднообрабатываемого сплава и высокая точность (отклонения фактического наружнего профиля лопатки от теоретического во всех сечениях не должно превышать ±03 мм [2 с. 94]) что приводит к существенному увеличению времени изготовления детали. Для уменьшения времени обработки возможно применение станков с ЧПУ и автоматизированных линий обработки.
Перо лопатки имеет протяженную сложную пространственную форму и спроектировано по определенному закону для обеспечения максимальной тяги. Длина рабочей части пера составляет 58 мм с переменным профилем в поперечных сечениях вдоль оси Z. Эти сечения строго ориентированы относително базовой расчетной плоскости и профиля замка. В поперечных сечениях заданы расчетные значения точек определяющих теоретический профиль спинки и корыта лопатки в координатной системе XY. Значения этих координат задаются табличным способом.
Смещение каждого сечения профиля от номинального расположения в направлении оси X и оси Y не более 03 мм. Разворот каждого сечения профиля от номинального расположения вокруг оси Z-Z не более 30'.
Рабочие лопатки турбины являются роторными. Роторные лопатки вместе с блоком сопловых лопаток ТВД составляют первую ступень турбины высокого давления основные данные которой приведены в таблице 1.1.
Таблица 1.1 - Основные данные ТВД
Степень понижения полного давления газа
КПД турбины по параметрам заторможенного потока
Окружная скорость мс
Частота вращения ротора обмин
Температура газа на входе в турбину 0С
Расход топливаGт кгс
Турбина высокого давления предназначена для привода компрессора высокого давления и агрегатов установленных на коробках приводов двигательных и самолетных агрегатов. Турбина состоит из ротора и статора. Ротор турбины состоит из рабочих лопаток диска цапфы и вала. На диске крепится 90 рабочих лопаток. Вал представляет собой тонкостенную оболочку с двумя фланцами по которым осуществлено соединение вала с дисками компрессора и турбины. Цапфа обеспечивает опирание ротора о роликовый подшипник. Статор турбины состоит из наружнего кольца блока сопловых лопаток внутреннего кольца аппарата закрутки устройства стабилизации радиального зазора клапанного аппарата и воздухо-воздушного теплообменника. Напряженные состояния рабочих лопаток турбины приведены в таблице 1.2.
Таблица 1.2 - Напряженные состояния рабочих лопаток турбины
система автоматического управления.
Химический состав сплава лопатки представлен в таблице 1.3 физические свойства – в таблице 1.4.
Материал лопатки относится ко второй группе контроля которая предусматривает тщательную проверку качества каждой лопатки (ЛЮМ1-ОВ ультразвуковой травления на прижоги и макроструктуру предела усталости готовой лопатки).
Таблица 1.3 - Химический состав в % материала ЖС32-ВИ (по ТУ 1-92-177-91)
Таблица 1.4 - Прочностные свойства материала ЖС32-ВИ
Предел прочночти при разрыве В (температура испытания Т=9000С) МПа
Предел длительной прочности (при времени испытания не менее 100 ч и температуре
Относительное удлинение после разрыва Δ %
1.2Анализ технологичности конструкции детали
В процессе дипломного проектирования так же как и в производственных условиях любая конструкция должна быть самым тщательным образом проанализирована. Целью такого анализа является – выявление недостатков конструкции по сведениям содержащимся в чертежах и технических требованиях а также возможное улучшение технологичности рассматриваемой конструкции.
Под технологичностью литых деталей подразумевают такое их конструктивное оформление которое не снижая основных требований к конструкции способствует получению заданных физико-механических и эксплуатационных свойств размерной точности и чистоты (шероховатости) поверхности отливок при минимальной трудоемкости изготовления их и рациональном использовании дефицитных основных металлов.
Рабочая лопатка ТВД является ответственной деталью двигателя АЛ-31Ф. Известно что в месяц выпускаются 5 двигателей. Количество устанавливаемых лопаток на первую ступень ТВД двигателя - 90 штук. Следовательно годовая программа выпуска лопатки составляет:
с учетом потерь деталей на брак и испытания примем шт.год.
Данный технологический процесс изготовления рабочей лопатки относится к серийному типу.
Различают следующие виды оценок технологичности:
Качественная оценка.
Количественная оценка.
В процессе оценки технологичности проводится качественный анализ изделия с целью выявления наиболее рациональных форм размеров материалов обеспечивающих применение наиболее прогрессивных методов изготовления.
Качественная оценка предшествует количественной оценке и определяет целесообразность ее проведения. Количественная оценка технологичности выражается определенными показателями численное значение которых характеризует степень удовлетворения требований к технологичности.
В качестве количественных показателей рассматриваются коэффициенты использования материала точности шероховатости.
1.3Качественная оценка технологичности
Единым критерием технологичности конструкции изделия является ее экономическая целесообразность при заданном качестве и принятых условиях производства эксплуатации и ремонта. Отработка конструкции изделия на технологичность должна обеспечивать снижение трудоемкости и себестоимости изготовления изделия и снижения трудоёмкости цикла и стоимости работ по обслуживанию изделия при эксплуатации.
Данная лопатка относится к так называемым «лопаткам без припуска по перу» с циклонно-вихревой системой охлаждения. После получения литой заготовки не требуется механическая обработка пера лопатки это весьма технологично так как основная рабочая поверхность получается за одну операцию сразу после литья. Обработке подвергается лишь замок и верхний край пера лопатки. При получении пера лопатки литьем с одной стороны происходит снижение трудоемкости изготовления по механическим операциям а также коэффициента использования материала. С другой стороны повышается трудоемкость процесса литья. Для достижения повышенной степени точности жаропрочных отливок (лопаток) необходимо регламентировать многие технологические параметры (изготовление пресс-форм и контроль их качества контроль качества моделей и блоков контроль технологических режимов изготовления стержней и оболочковых литейных форм и др.). Данную лопатку получают методом литья по выплавляемым моделям.
В основном поверхности детали имеют сложную форму (профиль пера лопатки составляют кривые Безье) получаемые на стадии заготовки поэтому они технологичны но существуют трудность при дальнейшей обработке получение шероховатости на некоторых поверхностях детали Ra08 и Ra16 также допуски отклонения поверхностей 002 мм 003 мм и операции нанесения покрытия.
Основные требования к материалам использующих для изготовления деталей ГТД является: высокая удельная прочность жаропрочность и жаростойкость сопротивление коррозии стабильность и воспроизводимость механических свойств хорошая обрабатываемость современными методами заготовительного производства размерной обработки сварки и т.д .
Турбина высокого давления:
- лопатки (узел и требования к нему) диапазон рабочих температур 1000-1250 0С усталостная прочность сопротивление эрозии сопротивление агрессивной среде горячих продуктов сгорания топлива.
-материалы: жаростойкие сплавы на никелевой основе.
Никель (Ni) является одним из основных составляющих жаропрочных сплавов который используют при изготовлении ответственных деталей и узлов ГТД и энергетических установок. Он также составляет основу современных жаростойких и коррозионных сплавов.
Никель имеет температуру плавления 1455°С кипения – 2900°С его атомная масса равна 5869 плотность – 89 гсм³ Никель имеет гранецентрированную кубическую кристаллическую решетку с параметром а = 0352387 нм атомным радиусом r = 0.125 нм.
Никель обладает высокой коррозионной стойкостью в ряде агрессивных сред. При нагреве на воздухе он взаимодействует с кислородом образуя оксид никеля NiO.
Наиболее вредными примесями никеля является сера углерод и кислород. Они при кристаллизации растворяются и выделяются в виде эвтектик: Ni-NiS Ni-NiO Ni-C(графит по границам зерен).
Многие жаропрочные сплавы (ЖС) разрабатывались на основе никеля. В целях улучшения жаропрочности и других специфических свойств они легируются другими жаропрочными элементами. Основными легирующими элементами в жаропрочных сплавах являются хром алюминий и титан.
Рассматриваемая лопатка ТВД изготавливается из жаропрочного литейного сплава на основе никеля ЖС32-ВИ химический состав которого приведен в таблице 1.3.
Использование сложнолегированных никелевых сплавов позволило повысить температуру газов на входе в турбину с 800 до 1000 °С что привело к значительному повышению мощности тягового усилия скорости уменьшению потребляемого топлива увеличению ресурса и надежности работы ГТД.
Сравнительные исследования образцов из различных сплавов и с различной структурой показали что не у всех сплавов с монокристаллической структурой наблюдается выигрыш по жаропрочности. Например для образцов из сплава ЖС32-ВИ: увеличение жаропрочности при 975°С на 10% наблюдается на образцах с направленной структурой (250 МПа) по сравнению с образцами равноосной структурой (230 МПа) а на образцах с монокристаллической структурой (265-275 МПа) существенное увеличение не получено. Если при средних температурах 700 - 800°С практически все серии сплавов ЖС32-ВИ дают выигрыш свойств в варианте монокристалла то при повышенных температурах (950-1050°С) этот выигрыш для этих сплавов становится ничтожным [9].
Таким образом для выращивания лопаток с монокристаллической структурой подходит не каждый литейный жаропрочный сплав.
Технологические аспекты выращивания лопатки с монокристаллической структурой также зависят от ряда факторов связанных с выбором сплава а именно с физико-химическим составом жаропрочного сплава (химическим составом тепло–температуропроводностью теплоемкостью).
Для изготовления лопатки рассматриваемой в данной работе применяется жаропрочный сплав ЖС32-ВИ. Данный сплав соответствует множеству условий предъявляемых к изготовлению лопаток с монокристаллической структурой. Он обладает хорошими показателями жаропрочности с монокристаллической структурой по сравнению с образцами с другими структурами.
Учитывая все сказанное выше можно сделать вывод что деталь является технологичной.
1.4Количественная оценка технологичности
Технологичность конструкции изделия оценивают количественно посредством системы показателей которые характеризуют технологическую рациональность конструктивных решений и преемственность конструкции или пригодность к использованию в составе других изделий.
Количественная оценка технологичности производится на основе анализа значений показателей технологичности изделия.
Коэффициент использования материала определяется по формуле:
Для детали «Рабочая лопатка ТВД» коэффициент использования материала составит:
Высокий коэффициент использования материала объясняется использованием литой конструкцией лопатки так как при использовании отливок полученная заготовка максимально приближена по формам размерам точности к параметрам готовой детали. Такая конструкция лопатки является более технологичной.
При изготовлении лопатки проводится множество ручных работ. Это полировальные операции слесарные работы промывочные операции что увеличивает штучное время изготовления детали и себестоимость лопатки. Из-за повышенных требований к качеству изделия точности возникает необходимость введения дополнительных контрольных операций что увеличивает время изготовления детали. Всё вышеперечисленное отрицательно сказывается на технологичности изготовления детали.
1.5Обоснование выбора исходной заготовки
1.5.1Выбор заготовки с точки зрения обеспечения требуемой точности
В технических условиях для ответственных тяжело нагруженных деталей для деталей работающих в условиях переменных нагрузок в специальных средах (детали турбостроения энергомашиностроения такие как валы шестерни зубчатые колеса роторы турбинные и компрессорные диски и лопатки и т.п.) указывают определенные требования к качеству материала к физико-механическим свойствам.
При выборе заготовок учитывают форму размеры и массу детали материал масштаб производства периодичность повторения размеры припусков на обработку и точность размеров.
Материал заготовок обычно задается на рабочем чертеже конструктором. Вид заготовки форму и размеры определяют исходя из условий наибольшей простоты и экономичности обработки с учетом конкретных производственных возможностей заготовительных цехов и сроков окупаемости капитальных затрат на подготовку производства.
Правильное решение в выборе заготовок если по техническим условиям применимы различные их виды можно получить только на основе технико-экономических расчетов путем составления технологической себестоимости детали при том или другом виде заготовки. Однако при выборе заготовок можно руководствоваться некоторыми общими соображениями. Заготовки в виде поковок получаемых ковкой и штамповок изготовляемых в штампах применяют для деталей работающих преимущественно на изгиб растяжение и кручение при значительной разнице в поперечных сечениях. С точки зрения экономии материала снижения объема механической обработки целесообразно заготовку приближать по формам размерам и качеством материала поверхностного слоя к параметра готовой детали но при этом будут существенно возрастать затраты на получение заготовки в заготовительных цехах.
С другой стороны упрощение формы заготовки снижение требований к её точности качеству поверхностного слоя ведет к удешевлению заготовительного производства при одновременном увеличении затрат на механическую обработку и одновременно с этим коэффициента использования материала. Поэтому при проектировании технологического процесса и выбора варианта исходной заготовки рекомендуется рассматривать несколько вариантов и выбрать тот который позволит получить минимальную сумму технологических затрат по заготовительным и механообрабатывающим цехам.
В машиностроении для получения заготовок наиболее широко применяют следующие методы:
)обработку металлов давлением;
)комбинации этих методов.
Каждый метод содержит большое число способов получения заготовок.
Вид заготовок и способ их изготовления для конкретной детали определяются такими показателями как:
)конструктивная форма;
)серийность производства;
Материал является одним из важных признаков определяющих метод получения заготовок. Рабочие лопатки ТВД изготавливают из жаропрочного сплава на никелевой основе ЖС32 который является литейным сплавом. Деталь имеет сложную пространственную конфигурацию в том числе внутренние каналы охлаждения. Производство лопаток является среднесерийным.заготовки 028 кг.
Учитывая все выше перечисленное выбирают метод получения заготовки – литье по выплавляемым моделям.
При выборе данного способа получения заготовки и разработке технологического процесса (ТП) учитывались следующие пункты:
необходимость получения детали сложной формы со сложной внутренней конфигурацией;
создание заготовки с минимальным припуском по перу лопатки;
применение метода ориентирования исходной заготовки в технологической системе относительно профиля с целью распределения (оптимизации) припуска на различных этапах обработки;
использование отделочных методов обработки шлифованием и полированием с гарантированием качественных показателей поверхностей.
Процесс литья по выплавляемым моделям базируется на следующих основных принципах:
)копия или модель конечной детали (рабочей лопатки ТВД) изготавливается из воска с добавлением мочевины. В месте расположения дефлектора вставляется керамический стержень. В вершине формы располагают затравку;
)модель погружается в кремообразную гипсовую массу (огнеупорную суспензию) методом окунания и высушивается. Данный процесс осуществляется поэтапно: вначале наносят один слой огнеупорной суспензии и высушивают затем - второй слой огнеупорной суспензии и снова высушивают. Таким образом наносят еще 5 слоев. В конечном итоге модель затвердевает и образует форму;
)при последующем нагревании (прокалке) формы восковая модель расплавляется и удаляется а именно вытапливается паром по давлением 8-10 атмосфер при температуре 175 ºС на установке «Бойлерклав»;
)в оставшуюся на месте удаленного воска полость заливается металл который точно воспроизводит исходную восковую модель. Благодаря затравке достигается направленность структуры материала. Стержни удаляют в расплаве бифторида калия КН
)отрезается литник для дальнейших исследований;
)проводится операция «опескоструивание».
1.5.2Выбор заготовки с точки зрения себестоимости
С точки зрения себестоимости процесс получения заготовок литьем по выплавляемым моделям значительно дороже получения заготовок штамповкой либо ковкой. Но необходимость получения сложной внутренней пространственной структуры диктует невозможность какого-либо иного способа получения заготовки кроме как литься по выплавляемым моделям.
1.6Разработка технологического процесса
1.6.1Анализ базового технологического процесса
Исходной информацией для проектирования технологического процесса (ТП) служат: чертежи детали технические требования регламентирующие точность параметры шероховатости поверхности и другие требования качества.
Заготовку выбираем исходя из минимальной себестоимости готовой детали для рассчитанного годового выпуска. В технологическом процессе используется литье по выплавляемым моделям.
Формирование параметров рабочей лопатки ТВД осуществляется на механическом и электроэрозионном участках после проведения входного контроля исходной заготовки. В процессе контроля проверяются сопроводительные документы наличие маркировочных клейм и осуществляется внешний осмотр.
Процесс обработки условно можно разделить на три части.
В первой части ТП (операции №№ 40000 - 40170) осуществляется выбор баз для черновой и получерновой обработки точное ориентирование заготовки относительно профиля пера лопатки обновляются базовые установочные поверхности. Выполняется съем основного припуска у заготовки. Производится специальная оперция КПЭ (операция № 40095) – обработка в режиме вибро-ЭЭО 15 отверстий. Эта часть ТП заканчивается проведением контроля качества материала и проверкой размеров заготовки. Таким образом используем оборудование и приспособления класса точности 4 рабочих 4 и 3 разрядов.
Во второй части ТП (операции №№ 41000 - 52000) проводятся получистовые и чистовые операции для основных элементов лопатки и последующие операции КПЭ. Производится окончательная доводка рабочих поверхностей лопатки производится нанесения покрытия на внутреннюю (хромалитирование) и наружнюю (керамика) части лопаток. Таким образом используем оборудование и приспособления класса точности 3 рабочих преимущественно 5 и 4 разрядов.
В третьей части ТП (операции №№ 53670 – 63820) проводится визуальный осмотр и окончательный контроль геометрических параметров лопатки также выполняется контроль микроструктуры и механических свойств материала. Таким образом используем оборудование и приспособления класса точности 4 рабочих 4 и 5 разрядов.
Базовый ТП на изготовление «Рабочей лопатки ТВД» приводится в Приложении В.
1.6.2Анализ разрабатываемого маршрутного технологического процесса
При разработке базового ТП использовалось оборудование и методы обработки доступные на тот момент. Но так как технологии машиностроения постоянно совершенствуются то возникает необходимость изменения базового ТП с учетом доступного оборудования и методов. Так как в данной работе рассматривается процесс нанесения многослойного ТЗП с анкерным эффектом то в базовый ТП внесем следующие изменения:
операцию 51000 «НАНЕСЕНИЕ КЕРАМИЧЕСКОГО ПОКРЫТИЯ ПО ТЕХНОЛОЛОГИИ ЛМЗ НПО «САТУРН»» заменим на операцию «Нанесение многослойного ТЗП газотермическим методом».
Разрабатываемое ТЗП по сравнению с используемым обладает повышенной жаростойкостью и адгезией продлевая срок службы и увеличивая предел рабочей температуры лопаток ТВД.
1.7Размерный анализ технологического процесса
При проектировании оснастки для операции 51020 «Нанесение островкового подслоя» необходимо провести размерный анализ сопрягаемых поверхностей. Так как перо лопатки не подвергается снятию припуска и его точность обеспечивается на этапе отливки то остается провести анализ тех поверхностей которые подвергаются механической обработке. На чертеже 1402.140100.887 ЛР представлена схема размерных связей ТП изготовления “Рабочей лопатки ТВД”.
Исходными данными для размерного анализа ТП являются чертеж детали (1402.140100.887 ЧД) чертеж заготовки (1402.140100.887 ЧЗ) план обработки (1402.140100.887 ТП).
Основными этапами расчетов являются:
) составляется совмещенная схема на которой указываются:
все необходимые операционные размеры с нумерацией в порядке их получения;
) преобразование совмещенной схемы в граф;
) выявление размерных цепей и их решение.
Построение совмещенной схемы (приложение Б) заключается в следующем: на эскизе детали со всеми чертежными размерами на каждой поверхности указываются припуски снимаемые на операциях при обработке. Ниже такого «одетого» припусками эскиза детали указывают операционные размеры в порядке принятой последовательности обработки.
За начальную точку (корень графа) берется поверхность которая является базой при получении первой поверхности. С этой вершины строится исходный граф (приложение Г) в котором используются все чертежные размеры и припуски (1402.140100.887 ЛР).
Составим систему уравнений для оси Z исходя из размерных связей представленных на графе (см. 1402.140100.887 ЛР). Система уравнений используется для определения номинальных значений операционных размеров:
Z340 - A - C + B +l4 = 0
Для определения численных значений искомых размеров необходимо вначале распределить допуски замыкающих звеньев по составляющим звеньям по условиям взаимосвязи исходного и составляющего звеньев размерной цепи который выражается в том что допуск замыкающего звена должен быть большим или равным сумме допусков составляющих звеньев. Такая взаимосвязь выражается следующими неравенствами и уравнениями:
Допуски на чертежные размеры заданы по чертежу.
Допуски на размеры заготовки выбраны в зависимости от метода получения заготовки – литье по выплавляемым моделям.
Допуски на операционные размеры назначаем исходя из параметра шероховатости (Ra16) размера детали и вида операции - чистовое либо черновое шлифование (3 с.332).
Последовательно решим каждое уравнение:
l2 = 086+008 + 2428±0015 = 2518±0015 мм.
Z15min = Rz + hc = 028 мм.
l1 = 2518±0015 + 028+008 = 255±0025 мм.
B = 255±0055 + 06+03 = 2625±0065 мм.
A =726-003 + 2625±0065 - 1418±0055 + 08+05 = 897±011 мм.
Таким образом в результате размерного расчёта для оси получены следующие операционные и исходные размеры:
2Разработка операционного технологического процесса изготовления рабочей лопатки ТВД
2.1 Выбор средств технологического оснащения расчет режимов обработки норм времени для операции №51020 «Плазменное напыление островкового подслоя»
Восстановление поверхности или придание ей особых свойств за счет нанесения дополнительного материала — покрытия связано с необходимостью прочного взаимодействия покрытия с подложкой. В процессе нанесения покрытий не должен быть снижен уровень прочности и выносливости материала подложки.
Наиболее полно этим требованиям отвечает газотермическое покрытие (ГТП) при котором формирование слоя покрытия происходит дискретными частицами материала в расплавленном или пластичном состоянии.
Метод газотермического напыления (ГТН) характеризуется широтой технологических возможностей:
Покрытия можно наносить на объекты любых размеров: мосты суда трубопроводы строительные конструкции котлы коленчатые валы лопатки турбин пресс-инструмент и др.
Толщина покрытия может быть от 001 до 10 и более миллиметров.
Покрытия могут иметь заданную пористость (от нуля до 30 и более процентов).
Покрытия могут быть из любых материалов имеющих точку плавления или интервал размягчения.
В качестве подложки могут быть дерево стекло пластмассы керамика композиционные материалы металлы.
Нанесение покрытий может производиться в условиях широкого диапазона состава температуры давления среды — от динамического вакуума в специальной камере и атмосферы воздуха до подводного напыления.
Система удаления запыленного воздуха снабжается фильтрами сухого и мокрого типа полностью улавливающими пыль. Таким образом процесс напыления является экологически чистым.
Газотермические покрытия применяются при придании рабочим поверхностям деталей особых свойств. В зависимости от назначения покрытия и условий его работы меняются требования к точности соблюдения основных параметров покрытия — его толщины и плотности. Повышение требований к покрытию обусловливает более высокие требования к оборудованию которое должно автоматически поддерживать постоянными технологические режимы напыления. Новейшие разработки и применение последних цифровых технологий позволяют максимально точно воспроизводить процесс газотермического напыления. Для полной автоматизации работы должны быть стабильными по составу и размеру исходные материалы различного назначения газы топливные и плазмообразующие (с контролем их массового расхода) а также стандартизованы методики оценки качества покрытий в соответствии с требованиями отраслей промышленности.
На операции № 51020 ведется плазменное напыление «анкерного» подслоя жаростойкого многослойного покрытия.
Назначение режимов плазменного осаждения покрытия выполняется в зависимости от требования чертежа детали в следующей последовательности:
назначают параметры режима обеспечивающие заданные физико-химические свойства покрытий;
задают расположение детали и размеры обрабатываемой зоны обеспечивающие заданную точность;
при выполнении первых заданных условий выбирают режимы с максимальной производительностью.
Плазмотрон F4 (таблица 1.5) предназначен для нанесения одно- многослойных покрытий на детали любой конфигурации.
Таблица 1.5 - Техническая характеристика плазмотрона F4
Максимальная мощность кВт
Плазмообразующие газы
Аргон водород азот гелий
Давление на входе МПа:
Производительность напыления кгч
Сложность назначения расчета режимов обработки обусловлена тем что совместное действие управляющих факторов приводит к большому разбросу параметров покрытий.
Операционная карта на данную операцию представлена в комплекте документов на технологический процесс.
2.1.1Выбор средств технологического оснащения
В данной работе предполагается рассчитать основные характеристики плазмотрона косвенного действия. Исходные данные к работе:
- рабочий газ – водород транспортирующий - аргон;
-начальная температура газа Тн = 300 К;
-конечная температура газа Тк = 4500 К;
-расход газа G = 1410-5 кгс;
- давление рабочего газа (воздуха) на выходе из плазмотрона p = 105 Па;
-стабилизация дуги – газовихревая;
-ресурс работы плазмотрона – не менее 50 часов.
Схема рассчитываемого плазмотрона представлена на рисунке 1.2. Основными узлами рассматриваемого плазмотрона являются катодный сопловой и узел завихрения рабочего газа. Последний обеспечивает наилучшие условия формирования столба дуги из всех прочих схем стабилизации дуги. Стержневой нерасходуемый электрод-катод выполняется в виде медного охлаждаемого. Формирующие сопла являются наиболее теплонапряженными элементами плазмотронов и поэтому требуют тщательного конструктивного выполнения. Как показал длительный опыт эксплуатации плазмотронов наилучшим материалом для изготовления сопел является медь высокой чистоты обладающая высокой теплопроводностью. Сопло плазмотрона может быть выполнено с искусственным охлаждением. Узел завихрения рабочего газа определяет качество стабилизации столба плазменной дуги. В данном плазмотроне рабочий газ поступает в камеру через несколько тангенциальных отверстий просверленных в корпусе плазмотрона. Несколько отверстий обеспечивают большую равномерность распределения газа по окружности но при этом усложняется система подачи газа в плазмотрон.
Жесткая механическая связь электродного и соплового узла осуществляется с помощью изолятора. При выборе материала и конструкции изолятора следует учитывать что он должен выдерживать высокое напряжение осциллятора сохраняя механическую прочность и плотность при повышенной температуре и влажности кроме того он должен хорошо поддаваться точной механической обработке. Наиболее полно этим требованиям удовлетворяет эпоксидная смола обладающая высокими изолирующими свойствами и хорошим сцеплением с металлом сохраняющая свои свойства при повышенных температурах стойкая по отношению к влаге и различным агрессивным парам и газам.
Одним из условий стабильного горения дуги является точная центровка электрода и сопла при сборке плазмотрона. Отклонение в несколько десятых долей миллиметра может привести к образованию двойной дуги. Высокая точность центровки электрода и сопла может быть достигнута лишь при жесткой фиксации их взаимного расположения.
Важным условием стабильного горения дуги в плазмотронах прямого действия является выполнение определенных размерных соотношений между диаметром катода dK диаметром сопла dc и длиной канала сопла lс. На опыте эксплуатации плазмотронов установлено что возможность двойного дугообразования исключается при двух условиях: dк dc и dc lс. Величина диаметра катода определяется током дуги.
Определению подлежат следующие параметры: рабочие значения тока I и напряжение дуги U тепловой коэффициент полезного действия h кинематические параметры относительного движения обеспечивающие необходимую толщину напыляемого покрытия - 20 мкм.
Рисунок 1.2 - Расчётная схема плазмотрона: 1 – медный катододержатель; 2 – катод; 3 – сопло; 4 – обрабатываемая деталь; 5 – подача газа.
Для расчета размеров плазмотрона зададимся следующими константами [4]:
критическая скорость при 4500 К акр = 2886 мс;
плотность газа при 4500 К кгм3;
начальная энтальпия Джкг
Для расчета электрических и тепловых характеристик плазмотрона будем использовать следующую систему уравнений:
вольтамперной характеристики [5 с. 77]:
теплового КПД плазмотрона [5 с. 77]:
мощности вкладываемой в дугу:
энергии истекающей струи:
условие отсутствия шунтирования дуги на стенку сопла:
где d – диаметр разрядного канала;
l – длина разрядного канала.
Представленная система уравнений не замкнута поэтому необходимо ввести ещё одно условие устанавливающее взаимосвязь между искомыми параметрами. Это условие определяет отсутствие теплового запирания в разрядном канале. С этой целью внутренний диаметр сопла выбирается на 10-30% больше критического. В нашем расчете примем d=117dкр.
Тогда мы можем рассчитать диаметр разрядного канала плазмотрона по следующей формуле:
подставив исходные значения получим:
Решая данную систему уравнений с помощью MathCAD получим следующие характеристики:
длина разрядного канала сопла:
Мощность рассматриваемого плазмотрона:
Таким образом выбираем плазмотрон F4 характеристики которого удовлетворяют рассчитанным.
Основные элементы приспособления: кожух для установки лопатки в экране (поз. 3) перфорированный экран опорные винты (поз. 5) втулка (поз. 4) подшипник (поз. 7) ведомые колеса (поз. 2) корпус (поз. 1) электродвигатель. Лопатка в экране устанавливается в кожух и закрепляется там опорными винтами. При обработке движение от вала электромотора передается к шестерне от неё - в колесам соединенным в свою очередь через вал кожуха с кожухом. Четное количество обрабатываемых лопаток (десять) обеспечивает условие соседства зубчатых колес.
Контроль операции проводится с помощью измерения привеса на весах ВЛКТ-500.
2.1.2Расчет режима обработки
Задаваясь технологическими режимами напыления можно рассчитать толщину однопроходного покрытия [6 с.27]:
где Gр - производительность 0001 кгс;
Ким - коэффициент использования материала;
V0 - скорость относительного перемещения пятна примем 1 мс;
γ - плотность материала слоя 7800 кгм3;
ρ - радиус рассеивания равен четвертой части ширины одного шага;
- коэффициент наслоения единичных полос равен 2 [6 с. 28].
при этом разнотолщинность равна 3% [6 с. 28].
Расстояние напыления примем 115 125 мм так как на большем расстоянии аргон сильно смешивается с воздухом и начинается процесс окисления а на меньшем расстоянии возможен перегрев детали струей плазмы. Напряжение и сила тока а так же расход были рассчитаны выше.
2.1.3Расчет штучного времени
Норма штучного времени на обработку изделия определяется по формуле:
Тшт = То + Твсп + Тоб + Тд мин(1.8)
где То – основное время мин; Т всп – вспомогательное время мин; Т об – время обслуживания рабочего места мин; Т д – дополнительное время мин.
Основное время определяем по формуле:
где t1 - установка лопатки в гнездо установки мин; t2 - нанесение первого слоя покрытия мин; t3 - охлаждение лопатки (т.к. то технологическому процессу температура заготовок не должна превышать 300 0С) мин; t4 - снятие сетчатого экрана мин; t5 - нанесение второго слоя мин; t6 - охлаждение лопатки мин; t7 - нанесение третьего слоя покрытия мин; t8 - охлаждение лопатки мин; t9 - снятие лопатки из гнезда мин; n1 - количество деталей в одной садке шт.
Специфика нанесения покрытий такова что требует промывки сушки и активации поверхности обрабатываемой детали перед обработкой и тщательного контроля на всех этапах. Отсюда определяем по формуле:
где t10 - входной контроль деталей мин; t11 - установка лопаток в приспособление мин; t12 - промывка лопаток в бензине и ацетоне мин; t13 - сушка после промывки мин; t14 - активация обрабатываемой поверхности пескоструйной обработкой (с использованием абразива из карбида кремния с размером зерен 05-15 мм ГОСТ 3647-80 марок К3 К4 с давлением воздуха 04-07 МПа дистанцией обработки 008-015 м углом встречи 60-900 расходом абразива 300-500 кгч) мин; t15 - выходной контроль мин.
Время обслуживания рабочего места определяем из следующего соотношения:
где t16 – время очистки камеры и оснастки мин;
t17 – время замены расходных элементов (керамического порошка и проволоки припоя) мин;
n2 - количество деталей обработанных за период между очистками шт.
Дополнительное время выделяется на отдых и регламентируется условиями работы. Согласно литературе Тдоп=7% от То.
Примем что t1 = 4 мин; t2 = 2 мин; t3 = 2 мин; t4 = 2 мин; t5 = 2 мин; t6 = 2 мин; t7 = 2 мин; t8 = 2 мин; t9 = 2 мин; n1 = 10Тогда:
Примем что t10 = 3 мин; t11 = 4 мин; t12 = 20 мин; t13 = 5 мин; ; t14 = 1 мин; t15 = 5 мин. Подставляя получим:
Примем что t16 = 80 мин; t15= 40 мин; n3= 180Получаем:
Тдоп = 007·2=014 мин.
Тогда норма штучного времени определится как:
Тшт = 2+067 = 267 мин.
2.2Выбор средств технологического оснащения расчет режимов обработки норм времени для операции № 50510 «Электроэрозионная»
2.2.1Выбор средств технологического оснащения
Для операции №50510 «Электроэрозионная» (запятой) по размерам обрабатываемой детали ёе массе и по необходимому классу точности выбираем станок 4Г721 (таблица 1.6) с генератором
Таблица 1.6 - Станок электроэрозионный копировально-прошивочный 4Г721
Класс точности станка по ГОСТ 8-82 (НПВАС)
Длина рабочей поверхности стола мм
Габариты станка Длинна Ширина Высота (мм)
Мощность двигателя кВт
Пределы частоты вращения шпинделя MinMax обмин
Число инструментов в магазине
В качестве источника технологического тока в комплект станка входит одноконтурный широкодиапазонный генератор импульсов А2 с адаптивно-программным управлением типа ШГИ-80-440М2А (таблица 1.7) в котором трехфазный ток промышленной частоты преобразуется в импульсный ток повышенной частоты. Полярность электродов или обратная или (для обработки твердых сплавов)- прямая.
В качестве рабочей жидкости для станка рекомендуется смесь керосина КО30-50% ±10% ТУ38.401.58-10-90 с маслом И12А ГОСТ 20799-75.
Таблица 1.7 - Основные технические характеристики станка 4Г721
Механическая система
Максимальный ход пиноли не менее
Максимальное расстояние от планшайбы до рабочего стола не менее
Размеры рабочего стола длина Х ширина
Диапазон рабочих подач
Максимальная скорость быстрых перемещений не менее
Разрешающая способность привода подач
Максимальный вес устанавливаемого инструмента
Амплитуда вибрации не менее
Разброс амплитуды колебаний по оси Z
Смещение колеблющегося электрода-инструмента по осям X и Y не более
Генератор технологического тока и система управления
Максимальный технологический ток в импульсе не менее
Диапазон рабочих напряжений
Диапазон изменения длительности импульса
Максимальный средний ток
Частота подачи импульсов
Габариты длина Х ширина Х высота
Вес стойки генератора и системы управления не более
Потребляемая мощность
2.2.2Расчет режима обработки
Режимы для электроэрозионной операции 50510 назначаются и рассчитываются по [10]. Для перехода №1 (черновая обработка):
) Напряжение холостого хода при разомкнутых электродах:
UO = 110 – 140 В – при электроискровом режиме [10 с. 11];
Среднее значение напряжения пробоя:
Uср = (05 075)·UO = (05 075)·(110 140) = 50 – 105 В;
) Ток короткого замыкания:
Iк = (10 15)А – при черновой обработке [11 с. 12];
Iср = (05 075)·Iк = (05 075)·(10 15) = (5 1125) А;
) Частота импульсов: f = 88 Гц;
Длительность импульсов с:
) Найдем энергию импульса Дж:
) Рассчитаем производительность:
= 075 – при высокой частоте импульсов;
а = 1152 мм3 – объём расплавленного металла снимаемого импульсом с энергией 1 Дж
) Рассчитаем скорость линейной подачи электрода – инструмента:
гдеQ – производительность;
S – площадь проекции обрабатываемой поверхности
Для перехода №2 (чистовая обработка):
Iк = (2 3)А – при чистовой обработке [11 с. 12];
Iср = (05 075)·Iк = (05 075)·(2 3) = (1 2) А;
) Частота импульсов: f = 300 Гц;
S – площадь проекции обрабатываемой поверхности.
2.2.3Расчет штучного времени
Основное время обработки «запятой»:
гдеz1 = 14 мм – глубина паза черновой обработки;
z2 = 04 мм – глубина паза чистовой обработки;
Основное время обработки для прожига «запятой» составляет Tосн = 025 мин.
Величина штучного времени:
где– основное машинное время мин;
– вспомогательное время на операцию мин;
– время обслуживания рабочего места ;
– время перерывов в работе ;
Вспомогательное время для прожига детали «Рабочая лопатка ТВД» складывается из:
)установитьснять деталь в приспособление 05 мин;
)установитьснять электрод 075 мин;
)закрытьоткрыть ванну станка 019 мин;
)заполнить ванну рабочей жидкостью 03 мин;
)подвестиотвести электрод 02 мин
)включитьвыключить станок 008 мин;
)включитьвыключить обработку 008 мин;
)спустить рабочую жидкость 03 мин;
)время на измерение штангенциркулем 088 мин;
)время на контроль шероховатости по образцу 02 мин.
Тобсл = 004 · (025+349) = 015 мин;
Тот = 003 · (025+349) = 011 мин.
Штучное время рассчитывается по формуле (1.18):
2.3Выбор средств технологического оснащения расчет режимов обработки норм времени для операции №40010 «Шлифовальная»
2.3.1Выбор средств технологического оснащения
Операция № 40010 выполняется на плоскошлифовальном станке 3E711В. При обработке используется шлифовальный круг 250х25х76 23А-25А 25-20 СТ1-СТ2 К 35 МС. Шлифуется подошва лопатки. Обработка ведется в среде эмульсии. Из базового ТП и паспорта станка известны следующие данные:
Деталь – рабочая лопатка ТВД.
Операция – черновое шлифование (плоское).
Обрабатываемый материал – жаропрочный сплав на никелевой основе ЖС6У-ВИ.
Характер заготовки – необработанная (отливка).
Вес заготовки – 02 кг.
Станок - плоскошлифовальный с крестовым столом модель 3E711В (таблица 1.8).
Инструмент – шлифовальный круг.
Приспособление – универсальное.
Таблица 1.8 - Паспортные данные станка 3E711В [7]
Размеры рабочей поверхности стола мм
Наибольшие размеры обрабатываемых заготовок мм
Точностные параметры максимально достигаемые на образце-изделии
шероховатость поверхности обработанной периферией шлифовального круга Ra
Мощность привода главного движения кВт
Габаритные размеры мм
Размеры шлифовального кругамм
Предел скоростей продольного перемещения стола ммин
Предел вертикальных подач шлифовальной головки мм
2.3.2Расчет режима обработки
Операция шлифования состоит из 1 перехода:
Шлифовать поверхность 1 выдерживая размер 1.
Поверхность 1 показана в операционной карте.
Обработку производят шлифовальным кругом 250х25х76 23А-25А 25-20 СТ1-СТ2 К 35 МС.
Режимы резания назначают по таблице 130 [5 с.439].
Глубина шлифования t мм (вертикальная подача S в ммдв.ход).
Обычно при плоском шлифовании глубина шлифования принимается при предварительной обработке t = 015-004 мм а при окончательной - t=0005-001 мм на двойной ход. Назначим Sверт = 01-005 мм.
Продольная подача Sпр ммоб - это перемещение шлифуемой поверхности за один оборот круга. Величина подачи определяется по формуле:
гдеВ - ширина круга мм;
b - коэффициент шлифования.
Величину В можно принять по паспорту станка. Коэффициент шлифования для предварительной обработки 04 - 07 а для окончательной 025-035.
Sпр = 04 × 25 = 10 ммоб.
Скорость перемещения детали определяется по формуле:
где Сv - коэффициент принимаемый : при шлифовании незакалённой стали - 1550; при шлифовании закалённой стали - 1525; при шлифовании чугуна и медных сплавов - 1590; Т - период стойкости круга (30-40 мин).
Скорость Vд должна быть в пределах указанных в паспорте выбранного станка что выполняется.
Число двойных ходов стола:
где L - расчётный ход стола мм.
где l - длина шлифуемой поверхности мм.
Скорость вращения шлифовального круга:
гдеDк - диаметр шлифовального круга (по паспорту станка) мм;
nк – частота вращения круга (по паспорту станка) 1мин.
Основное технологическое время мин при плоском шлифовании с двойным ходом стола определяется по формуле:
гдеН - ширина шлифования мм;
h - припуск на обработку мм;
Sпоп – поперечная подача ммдв.ход.
При обычном шлифовании Sпоп =0005-1 ммдв.ход. При чистовом - Sпоп =0003-0005 ммдв.ход. К - коэффициент учитывающий точность шлифования и износ круга. При обычном шлифовании К =12-14 а при чистовом К =13-17.
2.3.3Расчет штучного времени
Нормативные значения вспомогательного и подготовительно-заключительного времени предствлены в таблице 1.9.
Таблица 1.9 - Вспомогательное и подготовительно-заключительное время
Затраченное время мин
Установить и закрепить деталь
Установка инструмента
Вспомогательное время (таблица 1.9) мин.
Время затрачиваемое на обслуживание рабочего места и личные надобности рабочего берущееся в процентах от оперативного времени:
Таким образом в данном разделе приведены:
расчет возможного режима напыления «анкерного» подслоя и времени обработки;
анализ установочных размеров экрана;
анализ принципиальной схема приспособления для напыления.
Для разрабатываемой операции подобрано оборудование даны характеристики обрабатываемого материала.
Конструкторская часть
1Разработка приспособления для плазменного напыления анкерного подслоя многослойного керамического покрытия на деталь «Рабочая лопатка ТВД»
Для реализации данного предложения необходимо:
)рассмотреть составные элементы в приспособлении для напыления лопаток ГТД;
)провести расчет формы и размеров экрана приспособления для напыления дискретного подслоя островковой формы;
)произвести необходимые расчеты (точностной прочностной) приспособления.
2Описание построения «островкового» подслоя с анкерным эффектом
Одной из задач данной выпускной квалификационной работы является разработка конструкции ТЗП содержащего:
замковую переходную зону состоящую из дискретного (островкового) слоя содержащего высокотемпературный припой ВПР36 (таблица 2.1) и ПВНХ16Ю6Ит (аналог СДП-2) толщиной 20-25 мкм;
внешний газотермический керамический слой толщиной 120 мкм из диоксида циркония стабилизированного иттрием ЦрОИ-7 (система ZrO2-8%Y2O3).
Высокотемпературные припои на никелевой основе и технологии пайки обеспечивают [13] жаростойкость паяных соединений на уровне жаростойкости основного материала; жаропрочность стыковых соединений на уровне 07-09 жаропрочности основного материала; совмещение пайки с термообработкой основного материала; пайку тонкостенных конструкций с минимальной эрозией основного материала; возможность ремонта литых деталей из жаропрочных никелевых сплавов включая монокристаллические сплавы. Исходя из основного материала лопатки (ЖС32) и рабочей температуры соединения а также возможности его напыления газотермическим методом выбираем припой марки ВПр36 [13].
Таблица 2.2 - Характеристики высокотемпературных припоев на никелевой основе
Рабочие температуры соединений
Порошок и аморфная лента
Коррозионностойкие сплавы
Предлагаемое ТЗП (рисунок 2.1) представляет собой следующую конструкцию. На поверхность основного материала лопатки 1 с использованием разработанной маски нанесен дискретный слой 2 представляющий собой смесь припоя ВПР-36 и жаростойкого порошка ПВНХ16Ю6Ит (аналог СДП-2) толщиной 20-25 мкм и состоящий из расположенных в шахматном порядке островков круглой формы 5 диаметром 14 – 20 мм и дистанцией между ними - 25 3 мм. На образованную поверхность также газотермическим методом нанесен внешний керамический слой 3 диоксида циркония стабилизированного иттрием марки ЦрОИ-7 (система ZrO2-8%Y2O3). После нанесения покрытие подвергнуто диффузионному отжигу.
Рисунок 2.1 - Конструкция предлагаемого ТЗП с островковой переходной зоной: 1 – основной материал детали; 2 – островковый слой ВПР44 и ПВНХ16Ю6Ит; 3 - внешний керамический слой
3Разработка способа получения теплозащитного покрытия с островковой переходной зоной для лопаток турбины ГТД.
Одной из следующих задач данной курсовой работы является создание способа получения разработанного ТЗП с островковой переходной зоной. Предлагаемое техническое решение было основано на идее создания замка который удерживал бы внешний керамический слой за счет сил механического сцепления (соединения). Сущность разработанного способа заключается в следующем.
Способ получения теплозащитного покрытия с ОПЗ (рисунок 2.2) для рабочих лопаток турбин газотурбинных двигателей включающий очистку электрокорундом поверхности 2 детали 1 под нанесение на него газотермическим методом дискретного подслоя 3 из смеси высокотемпературного припоя ВПР36 и жаростойкого порошка ПВНХ16Ю6Ит (аналог СДП-2) в виде островковых участков на дискретный слой 3 и открытые участки поверхности 2 газотермическим способом наносят внешний сплошной керамический слой 4 толщиной 120 мкм. В качестве материала внешнего керамического слоя 4 (рисунок 2.6) используют ZrO2-Y2O3 в соотношении Y2О3 – 8% вес ZrO2 – остальное.
Нанесение слоев с 3 по 4 теплозащитного покрытия осуществляют газотермическим методом. После нанесения покрытия производят его диффузионный отжиг.
Рисунок 2.2 – Схема формирования ТЗП ОПЗ: 1 – основа (деталь); 3 – поверхность детали; 4 – островковый слой
4Рассмотрение составных элементов в приспособлении для напыления лопаток ГТД
Рисунок 2.3 – Приспособление для плазменного напыление: 1 - корпус; 2 - подшипник ; 3 - ведомое колесо; 4 - ведущая шестерня; 5 - ось установки кожуха с кожухом; 6 - втулка
Рисунок 2.4 - Кожух (часть приспособления)
В кожух (рисунок 2.4) устанавливается деталь лопатка ТВД в двухстворчатом экране. Лопатка с экраном фиксируется винтом. Вращающее движение передается от электродвигателя к кожуху посредством зубчатого зацепления (рисунок 2.3).
5Расчет приспособления на точность
Цель расчета на точность заключается в определении требуемой точности изготовления приспособления по выбранному параметру и задании допусков размеров деталей и элементов приспособления.
Необходимость данного расчета обуславливается тем что до изготовления приспособления известны допуски обработки и по эмпирическим формулам оценены погрешности связанные с базированием закреплением (способом закрепления) износом трущихся и контактирующих поверхностей и т.д. Иногда достаточно трудно изготовить приспособление с высокой точностью это связано с повышенной стоимостью операций. Производя же расчет на точность до изготовления приспособления можно определить необходимую точность и тем самым не переплачивать за «лишние микроны».
Погрешность изготовления приспособления определяется по формуле [11]:
где – допуск выполняемого при обработке размера детали; исходя из условий обработки а также с учетом маршрутной технологии обработки = 002 мм;
kT – коэффициент учитывающий отклонение рассеяний значений составляющих величин от закона нормального распределения kT = 1 [11];
kT1 – коэффициент учитывающий уменьшение предельного значения погрешности базирования при работе на настроенных установках kT1 = 06 [11];
б – погрешность базирования детали в приспособлении б = 0015;
з – погрешность закрепления детали в результате действия сил зажима з = 0 (силы зажима в рассматриваемом приспособлении не присутствуют);
у – погрешность установки приспособления на столе у = 001;
и – погрешность положения детали возникающая при изнашивании элементов приспособления [11]:
где – постоянная зависящая от вида установочных элементов и условий контакта = 0005;
N – количество контактов детали и приспособления в год N = 1000.
Найдем погрешность положения детали возникающую при изнашивании элементов приспособления по формуле (2.2):
Найдем погрешность изготовления приспособления по формуле (2.1):
Таким образом при погрешности изготовления приспособления
пр ≤001 мм обеспечивается заданный допуск на обработку поверхности детали.
6Расчет элемента приспособления
Прочность – одно из основных требований предъявляемых к деталям и приспособлениям в целом.
По известным данным газотермической установки можно рассчитать силу действующую на устройство вращения лопатки. Примем что скорость частиц в потоке v 700 мс расстояние х 180 мм начальная скорость частиц v0 равна
a = (v-v0 )t = (2.4)
гдеt – подлета частиц до обрабатываемой поверхности;
a – ускорение частиц при подлете до обрабатываемой поверхности;
F – результирующая сила действующая на частицы;
m – масса напыляемых частиц в секунду времени принимаем равной массовому расходу G = 25 кгч.
a = 700(036700) = 1036 = 28 мc2
По найденным значениям можно определить силу действующую на лопатку:
F= 00069·28 =00193 H.(2.8)
Зная силу действующую на лопатку и ее размеры можно рассчитать действующий момент. Так как значение силы 00193 Н а плечо равно 18 мм (половина ширины лопатки) то момент будет равен 00003 Нм. Для учета действия газовой струи и облегчения расчетов в дальнейшем примем момент равным 1 Нм.
Для расчета диаметра вала необходимо рассчитать напряжения действующие на него. В качестве материала вала выберем ст45 с пределом прочности при кручении [t]=136 МПа и временным сопротивлением [s]=275 МПа. Тогда при силе воздействия 1 Н длине детали 50 мм и диаметре детали 36 мм получим что наименьшие диаметры будут равны:
Таким образом диаметр вала должен быть не менее 1 мм. На лопатку и оснастку кроме силы воздействия газопламенной струй действуют и другие силы (сила тяжести сила трения) которые сравнимы по величине с моментом действия газопламенной струи таким образом диаметр вала необходимо увеличить. Для удобства сборки и разборки оснастки возьмем диаметр вала равным 4 мм.
Для крепления вала используем подшипники 60024 шариковые с одной защитной планшайбой с внутренним диаметром 4 мм внешним диаметром 13 мм и шириной 5 мм с посадкой H7k6 [12 с.276]. Ведомые зубчатые колеса имеют следующие размеры: радиус сцепления 40172 мм ширина 5 мм [3 с. 152] диаметр отверстия 4 мм зацепление с валом - шпоночное. Ведущая шестерня устанавливается на электродвигателе.
7Подбор электродвигателя
Скорость перемещения плазмотрона относительно поверхности вращающейся детали должна составлять примерно 10 ммин с подачей 8 - 10 ммоб и обязательным перекрытием напыленных полос на 13 размера пятна напыления. Диаметр пятна напыления 10-25 мм.
Для определения частоты вращения изделия необходимо знать его диаметр и длину. В нашем случае рассматривается лопатка рабочая ТВД с максимальным диаметром d = 36 мм и длиной 50 мм. Тогда при линейной скорости относительного перемещения = 60 ммин = 100 ммс время затраченное на один оборот t будет равно:
При подаче Δl 105 ммоб вертикальная скорость перемещения плазмотрона будет равна:
что должно обеспечиваться выбранным роботом-манипулятором. Частота вращения детали f при этом будет равна
Покрытие наносят в один проход напыляя 20 - 25 мкм. Каждый новый проход нужно начинать с исходной точки. Для предотвращения нагревания изделий до температуры более 300 0С следует постоянно контролировать их температуру. Такой контроль осуществляют термоиндикаторными карандашами. Номер карандаша (140 200 250 300 и т. п.) указывает на температуру изменения цвета. При достижении предельной температуры процесс необходимо прекратить и охладить деталь до температуры 50 100 0С. При толщине покрытий более
- 20 мм возможно образование трещин охлаждение в этом случае следует производить в термостабилизирующем агенте например асбестокрошке песке и т. п.
В итоге по частоте вращения и требуемому моменту вращения выберем моментный двигатель MST130 производства фирмы BOSH (см. таблицу 2.2) предназначенного для установки непосредственно в корпус разрабатываемого приспособления.
Таблица 2.2 - Технические характеристики двигателей MST130
Номи-нальная скорость мин-1
Скорость вращения при максимальном моменте
Номи-нальный момент Нм
Макси-мальный момент Нм
Момент инерции ротора кгм2
Рисунок 2.5 - Двигатель MST130
8Подбор оборудования для автоматизации процесса нанесения покрытия
Для точного нанесения покрытия необходимо помимо разработки оснастки подобрать оборудование такое как манипулятор установка ГТН источник питания вентиляционно-очистительные системы воздушные компрессоры.
В качестве манипулятора выберем промышленный робот-манипулятор KUKA KR-16 (рисунок 2.6) предназначенный для перемещения устройства напыления (плазмотрона высокоскоростного газопламенного пистолета).
Технические характеристики:
число степеней свободы - 6;
грузоподъемность на руке - 16 кг;
дополнительная нагрузка - 10 кг;
точность позиционирования +-01 мм;
объем рабочего пространства - 145м3;
скорость линейной интерполяции ммc:
максимальная - 2000;
система управления роботом:
количество дискретных входоввыходов - 32128 (опция);
количество дискретных входоввыходов - 188 (опция);
число аналоговых входоввыходов - 188;
объем оперативной памяти Мб - RAM-32 (64);
объем жесткого диска Гб - 64;
возможность подключения принтера клавиатуры и мыши;
потребляемая мощность - 8 КВт (15 КВт при комплекции дополнительными осями);
пульт управления роботом - выносной с цветным жидко - кристаллическим дисплеем с разрешением 640 х 480 пикселей;
джойстик 6-координатный тип - "SpaceMouse";
радиус рабочей зоны - 1600 мм.
Рисунок 2.6 – Манипулятор KUKA KR-16
Для установки приспособления выберем однопозиционный стол - вращатель деталей (рисунок 2.7). Однопозиционный стол имеет электропривод с регулируемой частотой вращения и ручное изменение угла наклона оси вращения.
Рисунок 2.7 - Однопозиционный стол - вращатель деталей
Система управления стола может быть подключена к роботу. Робот осуществляет управление электроприводом стола как дополнительной степенью свободы и обеспечивает их согласованную работу. Технические характеристики приведены в таблице 2.3.
Таблица 2.3 - Технические характеристики стола - вращателя деталей
Диаметр планшайбы мм
Число оборотов планшайбы обмин
Вычислим массу оснастки. Объем равен 1486629024267 мм3 (объем 3D-модели полученной в программе «Компас») материал - дюралюминий и сталь (сталь не учитываем ввиду незначительности её объема). Плотность дюралюминия 00026 гмм3 масса оснастки - 5 кг.электродвигателя 2 кг масса десяти лопаток с экранами 20 кг суммарная масса 27 кг. Таким образом данный стол-вращатель деталей удовлетворяет основным условиям.
9Подбор дополнительных элементов оснастки
При обработке деталей возможно заклинивание лопаток в приспособлении. В этом случае электродвигатель будет перегружен и может сгореть. Для предотвращения данной ситуации предлагается использовать муфту соединяющую вал электродвигателя и ведущее колесо. Наиболее технологичным будет применение шариковых муфт. Передача вращающего момента шариковой муфтой обеспечивается взаимным зацеплением шариков установленных в гнездах полумуфт. В замкнутом положении шарики удерживаются пружиной при достижении предельного момента шарики преодолевая силу пружины выходят из зацепления и начинают проскальзывать относительно друг друга. Достоинством шариковых муфт является технологичность обусловленная применением высококачественных стандартных шариков подшипников качения. Для подбора конкретной муфты необходимо знать диаметр вала двигателя. Но так как данный параметр не приводится можно лишь рекомендовать вид муфты.
10Проектирование экранов
Для получения островкового покрытия необходимой конфигурации нужно спроектировать специальные экраны. Экраны должны быть двухстворчатыми и по внутренней форме полностью повторять лопатку. Толщина экранов 3 мм материал - алюминий или дюралюминий. Диаметр отверстий в экране около 2 мм расстояние между центрами отверстий - 3 мм. Конечную форму экранов можно получить либо с использованием электрохимических методов обработки материалов либо штамповкой. Кроме того экраны должны легко сниматься с лопатки а разделяться они должны по средней линии пера лопатки.
11Порядок сборки оснастки
Для сборки оснастки необходимо выполнить следующие пункты:
Поставить корпус на стол-вращатель деталей;
установить подшипники в корпус защитной шайбой вниз;
установить втулку на вал кожуха;
установить зубчатые колеса на валы кожуха с применением шпоночного соединения;
установить на вал шайбу и зафиксировать вал кожуха с помощью гайки;
установить электродвигатель в корпус;
установить на вал электродвигателя муфту;
установить ведущий вал в муфту;
установить через шпоночное зацепление ведущую шестерню и закрепить её;
одеть на лопатки защитные экраны;
установить лопатки с экранами в кожух и зафиксировать винтами.
Таким образом в данном разделе спроектировано приспособление для нанесения «анкерного» подслоя произведены рассчеты на точность и прочность подобрано необходимое оборудование.
Высокотемпературные припои для деталей ГТД с эффектом жаростойкости при температурах выше 1050 0С
Свойства и качество паяного соединения определяющим образом зависят от свойств применяемых припоев. Температура плавления припоя должна быть не менее чем на 60 100 °С ниже температуры солидуса наиболее легкоплавкого из соединяемых материалов. Нагрев при пайке не должен вызывать потери механических и физико-химических свойств материалов. Припой должен обеспечивать заданные эксплуатационные характеристики паяного соединения.
В процессе пайки припой смачивает соединяемые поверхности паяемых деталей и затекает в сборочный зазор. При кристаллизации в итоге растворно-диффузионных процессов образуется соединение обеспечивающее механические свойства и герметичность не ниже оговоренных конструкторской документацией.
Различие коэффициентов термического расширения плотности электро- и теплопроводности электрохимических потенциалов коррозионной стойкости припоя и паяемых материалов должно быть наименьшим. При невозможности соблюдения данного требования следует из всех пригодных по составу припоев выбрать с наиболее высокими механическими свойствами. В зависимости от назначения изделия может предъявляться ряд специфических требований например по электропроводности теплопроводности коррозионной стойкости в специальных средах деформации в горячем и холодном состояниях и др. При всех вышеперечисленных требованиях необходимо учитывать стоимость (припой должен быть наиболее дешевым и наименее дефицитным). Следует ограничивать необоснованное применение припоев содержащих драгоценные и остродефицитные металлы (золото серебро платину палладий вольфрам молибден германий висмут).
Классификация припоев предусмотрена ГОСТ 19248-90 и приведена в [13].
Припои классифицируют:
по химическому составу - медные серебряные золотые палладиевые платиновые никелевые железные марганцевые оловянно-свинцовые индиевые цинковые висмутовые галлиевые титановые и др.;
по технологическим свойствам: самофлюсующие - способствующие удалению припоем окислов с паяемой поверхности и композиционные - состоящие из смеси тугоплавких и легкоплавких порошков позволяющих производить пайку узлов с большими зазорами;
по содержанию активных компонентов (титана циркония и др.) повышающих смачиваемость припоем окисленных поверхностей паяемых материалов;
по температуре плавления; к низкотемпературным припоям относятся припои с Тт 450 °С к высокотемпературным - с Тт > 450 °С. Низкотемпературные припои выплавляют на основе олова свинца висмута кадмия цинка индия галлия. Высокотемпературные припои в основе имеют медь серебро никель кобальт железо алюминий и др.;
по сортаменту - пластичные припои изготавливают в виде проволоки ленты фольги полос; хрупкие припои изготавливают специальными технологиями в виде аморфизированных или мелкокристаллических лент фольги проволоки прутков а также традиционным литьем. Хрупкие припои могут поставляться в виде порошка порошковых лент на органической связке паяльных паст.
Для удобства использования а также с целью повышения производительности труда и качества паяных соединений некоторые припои изготавливают в виде проволоки и прутков внутри заполненных флюсом а также с флюсовой обмазкой.
Так как эффект жаростойкости искомого припоя должен проявляться при температурах выше 1050 0С в дальнейшем будем рассматривать лишь высокотемпературные припои.
1Припои на медной основе
Группу медных припоев составляют медь и сплавы на ее основе следующих систем: Cu-Zn Cu-Ni Cu-Mn-Ni Cu-Mn-Zn Cu-P и др.
Из всех припоев с низкой упругостью пара для пайки в вакууме наиболее широко применяют медь. Недостатком меди как припоя является возникновение в соединениях выполненных кислородсодержащей медью (марки Ml М2 и др.) газовых пор и кристаллизационных трещин при пайке в окислительной среде (вследствие образования эвтектики Cu-Cu2O). Обладая хорошей жидкотекучестью и растекаемостью медь легко затекает в капиллярные зазоры. Эту особенность наиболее эффективно используют тогда когда необходимо получить соединения с малыми зазорами и большой протяженностью (более 15 20 мм).
При пайке стальных изделий в вакууме или в восстановительных газовых средах где требуется большая протяженность швов медь на паяемую поверхность наносят электролитическим слоем 3 15 мкм (например в производстве свертных труб из малоуглеродистой стали). Химический состав меди различных марок приведен в таблице 3.1 механические свойства паянных медью соединений - в таблице 3.2.
1.2Медно-цинковые припои
Медно-цинковые припои представляют собой двойные сплавы меди и цинка в различных соотношениях. Диаграмма состояния сплавов системы Cu-Zn приведена на рисунке 3.1. Наибольший интерес представляют сплавы содержащие менее 39% Zn и имеющие однофазную структуру (α-твердый раствор). С увеличением содержания цинка в припое его пластичность значительно снижается. Недостатком медно-цинковых припоев является сильное испарение цинка при пайке что приводит к повышению температуры плавления припоя и образованию пористости в паяном шве.
Для снижения температуры плавления и повышения технологических свойств медно-цинковых припоев в их состав вводят в небольших количествах олово и кремний (до 1 %). Добавка олова снижает температуру плавления припоя и увеличивает его жидкотекучесть; кремний понижает испарение цинка; введение в припой небольших количеств бора придает ему флюсующие свойства. ГОСТ 23137-78 определяет три марки медно-цинковых припоев с повышенным содержанием цинка и пониженной температурой плавления (таблица 3.3).
Припои на медной основе содержащие кроме цинка небольшое количество олова и кремния имеют лучшие технологические свойства и обеспечивают более высокую плотность и герметичность шва. К этим припоям относят латуни марок ЛОК59-1-03 и ЛКБ062-02-004-05 ЛК62-05 и др.
Таблица 3.1 - Химический состав литой и деформированной меди (ГОСТ 859-2001)
Массовая доля элемента %
Таблица 3.2 - Механические свойства паяных соединений
Марка паяемого материала
Прочность паяного соединения при
Рисунок 3.1 – Диаграмма состояния сплавов системы медь-цинк
Таблица 3.3 - Химический состав и назначение медно-цинковых припоев
содержащей до 68 % Cu
Для пайки медных сплавов
содержащих Cu свыше 68 %
Для пайки меди бронзы и стали
Наиболее известные и употребляемые латунные припои их физические свойства химический состав и область применения даны в таблице 3.4 и таблице 3.5.
Таблица 3.4 - Латунные припои
Полного расплав-ления
Пайка углеродистых конструкционных и высоко-легированных сталей (кроме сталей мартенситного класса) меди никеля чугуна
Таблица 3.5 - Химический состав латунных припоев
Содержание основных элементов % (масс.) (Zn - остальное)
Следует иметь в виду что введение Sn и Si в больших количествах охрупчивает латуни и не позволяет получать пластичные паяные соединения Прочность паяных соединений выполненных этими припоями повышают введением в состав припоев Ni Mn Fe. Многокомпонентные латуни широко применяют для пайки тяжелонагруженных изделий например всех видов паяного режущего инструмента (резцы фрезы и др.) и изделий в процессе эксплуатации подвергающихся вибрационным ударным и другим видам нагрузок.
Таким образом медно-цинковые и латунные припои не обладают необходимой температурой плавления (более 1050 0С) что исключает их применение.
1.3Медно-никелевые припои
Медь с никелем образуют ряд твердых растворов (рисунок 3.2). Для увеличения жаростойкости и прочности при повышенных температурах в медно-никелевые припои вводят хром марганец железо кремний и алюминий. Составы и температура пайки медно-никелевыми припоями с небольшим содержанием марганца приведены в таблице 3.6 а с содержанием марганца и серебра - в таблице 3.7.
Рисунок 3.2 – Диаграмма состояния сплавов системы медь-никель
Таблица 3.6 - Медно-никелевые припои для пайки стальных изделий
Содержание элементов % (масс.) (Cu - остальное)
Температура пайки °С
Таблица 3.7 - Медно-никелевые припои с марганцем и серебром
Пайка высоколе-гированных сталей и соединений сталь-медь сталь-бронза
В печах с восстано-вительной газовой средой или в вакууме
Пайка углеродистой и коррозионно-стойкой стали в том числе трубопроводов
Газопламенная индукционная в печах в том числе в атмосфере аргона
ПрАНМц 06-4-2 полосы
ТУ 48-21-674-91 ОСТ 48-184-81
Пайка быстрорежущей стали и твердых сплавов
Индукционная газопламенная
ВПр1 полосы ВПр4 полосы
Пайка легированных и высоко-легированных сталей коррозионно-стойких и жаропрочных сплавов в том числе теплообменников
Индукционная в печах с восстановительной газовой средой и в вакууме электро-контактная. Припой ВПр1 -также газопламенная
ВПр2 полосы порошок ВПр13 полосы лента
ОСТ 1.90082-73 ТУ 14-1-3143-81 ТУ 48-1-354-75
ВПр45 (Cu-Mn-Sn-Ni-основа) прово-лока лист
Пайка коррозионно-стойких сталей и сплавов высокая коррозионная стойкость
Печной газопламенный
Пайка высоко-легированных сталей коррозионно-стойких и жаропрочных сплавов
Индукционная в печах с восстановительной газовой средой и в вакууме газопламенная
1.4Медно-фосфорные припои
Двойные сплавы меди с фосфором близкие к эвтектическому составу имеют сравнительно невысокую для среднеплавких припоев температуру плавления (рисунок 3.3) и высокие технологические свойства при пайке меди и медных сплавов что в ряде случаев делает возможным использовать припои этой группы в качестве заменителей серебряных. Кроме того они недефицитны и имеют сравнительно невысокую стоимость. Широкое использование припоев системы Cu-Р для пайки меди обусловлено также тем что они являются по отношению к ней самофлюсующими. За счет диффузии меди в паяный шов снижается в приграничной зоне содержание фосфора и улучшаются свойства паяного соединения. Пайка без применения флюса или с его ограниченным применением сокращает время пайки и повышает качество так как избыток флюса может служить источником образования шлаковых включений в паяном шве. Таким образом медно-фосфорные припои не обладают необходимой температурой плавления (более 1050 0С) что исключает их применение.
Рисунок 3.3 – Диаграмма состояния сплавов системы медь-фосфор
1.5Медно-германиевые припои
Полным аналогом золотых и серебряных припоев в производстве электровакуумных приборов и полупроводниковых приборов являются припои на основе системы медь-германий (таблица 3.8) имеющие низкую упругость пара и необходимые физико-механические и технологические характеристики.
Таблица 3.8 - Медно-германиевые припои
Детали и узлы электровакуумных приборов
ПМГрОБ10-1-0.1У (№417)
Электровакуумные и полупроводниковые приборы
Медные сплавы прочное и коррозионно-стойкое соединение
Имея относительно низкую для среднеплавких припоев температуру плавления серебряные припои обладают наиболее высокими тепло- и электропроводностью пластичностью коррозионной стойкостью и технологичностью. В силу своих уникальных свойств нашли применение с древнейших времен (при пайке ювелирных изделий) с развитием техники - в самых широких ее областях.
Серебро имеет температуру плавления 960 °С но в качестве припоя его применяют достаточно редко. В промышленности используют припои на основе серебра с содержанием меди цинка кадмия олова фосфора и других элементов.
Для увеличения прочности и коррозионной стойкости при повышенных температурах в состав припоев вводят никель или никель в сочетании с марганцем что положительно сказывается и на их термостойкости (таблица 3.9 таблица 3.10) Однако серебряно-марганцовистые припои обладают низкой коррозионной стойкостью в условиях тропиков и солевого тумана. Таким образом серебряные припои не обладают необходимой температурой плавления (более 1050 0С) что исключает их применение.
Таблица 3.9 - Серебряные припои с никелем индием и марганцем
Область применения припоя
Легированные и высоколегированные стали коррозионно-стойкие и жаропрочные сплавы
Титан и его сплавы высоколегированные стали в вакууме водороде и защитных газах
Титан и его сплавы сталь с медью металлизированная керамика
Титан и его сплавы высоколегированная сталь с титановыми сплавами коррозионно-стойкие сплавы в вакууме водороде инертных газах
Медь никель бронза сталь. Пайка стальных и медных деталей работающих до 600 °С газопламенная в печах индукционная в расплавах солей
Коррозионно-стойкие стали пайка индукционная в печах газопламенная
ПСрМцМн49 литые прутки 11 мм
Детали полупроводниковых и электровакуумных приборов
Таблица 3.10 - Химический состав серебряных припоев с никелем
Содержание основных элементов %(масс.) (Cu-остальное)
Палладий (Тпл = 1555 °С) и его сплавы применяются прежде всего для пайки тугоплавких металлов и сплавов например таких как молибден вольфрам ниобий платина Сплавы палладия с никелем кобальтом хромом серебром золотом применяются для пайки жаропрочных сплавов и сталей. Палладиевые припои применяются также для пайки изделий из высокотемпературной керамики с тугоплавкими металлами например ниобием танталом молибденом вольфрамом. Сплавы палладия с серебром и золотом используются для пайки конструкций из палладия (мембраны для очистки водорода). Палладий вводимый в качестве компонента высокотемпературных припоев значительно повышает их коррозионную стойкость пластичность а также способность растекаться и смачивать паяемую поверхность.
Добавка палладия в припои приводит к снижению их способности проникать в паяемый материал и разъедать его т.е. возможности возникновения контактной эрозии что позволяет проводить пайку тонкостенных изделий. В качестве припоев применяют как двойные сплавы системы серебро-палладий обладающие высокой пластичностью так и многокомпонентные припои в состав которых входят серебро медь никель марганец и другие металлы
Палладий с серебром образуют ряд твердых растворов (рисунок 3.4) с небольшим интервалом кристаллизации. Меняя соотношение палладия и серебра в припое можно регулировать температуру плавления от 1000 до 1500 °С. Палладий с медью (табл. 3.6) также образуют ряд твердых растворов с различной температурой плавления (1100 1550°С).
Рисунок 3.4 – Диаграмма состояний сплавов системы серебро-палладий
Таблица 3.11 - Серебряные и медные припои с палладием
Содержание элементов %
Температура полного расплавления °С
Припои системы серебро-палладий-медь имеют низкую упругость пара и паяные соединения работают в вакууме в длительном режиме при температуре 500 °С. Припои предназначенные для пайки жаростойких сплавов должны обладать большей высокотемпературной прочностью и сопротивлением ползучести и изготавливаются на основе систем Ag-Pd-Mn Ni-Mn-Pd Cu-Pd-Ni-Mn и Pd-Ni. Добавки лития и бора повышают смачиваемость этими припоями.
Палладиевые припои используемые в реакторо- и ракетостроении а также в строительстве газовых турбин представлены в таблице 3.12. Припой ПЖК-1000 широко применяют при изготовлении ответственных узлов в различных отраслях машиностроения при пайке соединений жаропрочных и коррозионностойких сплавов и обеспечивает высокие механические и коррозионностойкие свойства при высоких температурах (таблица 3.13) и в контакте с агрессивными средами.
В таблице 3.14 приведены свойства содержащих палладий припоев с низкой упругостью пара а также паяемые ими материалы в производстве электровакуумных приборов.
Таблица 3.12 - Наиболее жаростойкие припои с палладием
Химический состав % (масс.) (Pd - остальное)
ТУ 48-1-408-83 полосы)
Таблица 3.13 - Механические свойства соединений полученных при пайке различных материалов припоем ПЖК-1000 (при 20 0С и высоких температурах)
в МПа при температурах 0С
ср МПа при температурах 0С
Таблица 3.14 - Свойства припоев с низкой упругостью пара паяемые материалы
Физико-механические свойства при 20 °С
относительное удлинение %
Молибден вольфрам металлокера-мические узлы особого назначения
Медь ковар кобальтовые сплавы никель и его сплавы титан цирконий. молибден вольфрам
Припои на основе золота обладают высокими показателями пластичности коррозионной стойкостью электропроводностью теплопроводностью и еще целым рядом положительных свойств.
Золото в чистом виде как припой применяется редко но оно образует твердые растворы со многими металлами чем пользуются при разработке пластичных припоев. Однако применение их ограничивается высокой стоимостью и дефицитностью золота поэтому золотые припои используют только там где это оправдано (пайка вакуумных приборов с вакуумно-плотными соединениями электроконтактов и т.д.).
При пайке изделий с вакуумно-плотными соединениями применяют в основном сплавы золота с серебром и медью.
Минимальная температура плавления сплава с 80 % Au и 20 % Cu - 889 °С. Введение в состав медно-золотых припоев серебра с которым золото образует также ряд твердых растворов позволяет несколько снизить температуру их плавления. Эти припои нашли использование при пайке молибдена и графита с металлами. Дальнейшего снижения температуры плавления этих припоев достигают введением в их состав цинка кадмия и индия.
Сплавы золота с германием при содержании примерно 12 % Ge и 6 % Si пластичны и плавятся соответственно при температурах 365 и 370 °С.
Для пайки золотых изделий или изделий покрытых золотом применяют припой с содержанием 46% Au 32% Sb 18% Zn 3% Si и 1%Ni. Он имеет сравнительно низкую температуру плавления (590 °С) хорошо растекается по паяемой поверхности и не растворяет паяемый материал. Припой с более высокой температурой пайки (740 °С) ЗЛСрМ-583-80 содержит 583% Au 13 14% Ag 10% Cd 5 6% Zn Cu - остальное.
Таким образом золотые припои не обладают необходимой температурой плавления (более 1050 0С) что исключает их применение.
5Жаропрочные и коррозиционно-стойкие припои на никелевой основе
Никелевые припои широко применяют в качестве припоев для пайки коррозионно-стойких жаропрочных сталей и сплавов. Они позволяют получать паяные соединения обладающие высокими прочностью и коррозионной стойкостью как при комнатной так и при высоких температурах. Наибольшее применение получили никелевые припои легированные хромом кремнием марганцем железом бором фосфором. Хром значительно повышает жаропрочность и жаростойкость никелевых сплавов и температуру плавления. Понижают температуру плавления также введением кремния бора фосфора марганца. Вольфрам и ниобий повышая жаростойкость несколько понижают температуру плавления никелевых сплавов.
Отечественными припоями на никелевой основе группы «ВПр» (таблицы 3.15 3.16) широко применяемыми в самолето- и двигателестроении паяют высоколегированные коррозионностойкие стали и жаропрочные сплавы. Пайку осуществляют в восстановительной или защитной газовой среде а в некоторых случаях возможен индукционный или электроннолучевой нагрев.
Таблица 3.15 - Жаростойкие и жаропрочные припои на никелевой основе
Стандарт вид поставки
Пайка в печах в вакууме нейтральных газах высоколегированных коррозионно-стойких и жаропрочных сплавов
ТУ 1-809-108-83 порошок
Пайка в аргоне и вакууме сплавов типа ЖС6 и деформированных никелевых. Паяные соединения работают до 800 °С
Пайка в вакууме восстановительной газовой среде коррозионно-стойких и жаропрочных сталей и сплавов
ОПТУ 1-809-832-87; ТУ 1-595-81 порошок
Пайка в вакууме жаропрочных сплавов типа ЖС6. Рабочая температура до
ТУ 1-595-162-83; ТУ 1-595-6-204-85 аморфная лента
Пайка в аргоне вакууме жаропрочных сплавов типаЖС6 ВЖЛ 14. Рабочая температура до
Продолжение таблицы 3.15
ВПр36 (Ni-Cr-W-Co-B)
ТУ 595-6-160-93 порошок
Пайка в вакууме жаропрочных сплавов типа ЖС26 рабочая температура до
Порошок паста аморфная лента
Пайка в вакууме аргоне жаропрочных сплавов и сталей обеспечивает жаропрочность и жаростойкость
Пайка в вакууме жаропрочных сплавов типа ЖС32
Пайка в вакууме жаропрочных сплавов типа ЖС6 и ВЖЛ12. Соединения работают до 1050 °С
ТУ 1-595-6-489-96 порошок
Пайка в вакууме жаропрочных сплавов и коррозионно-стойкой стали. Соединения работают до 1000 °С
ВПр50 (Ni-Cr-Al-Si-B)
ТУ 1-595-4-581-2000 порошок
Пайка в вакууме коррозионно-стойких и жаропрочных сплавов. Коррозионная стойкость и жаростойкость до 1000°С
Таблица 3.16 - Прочность паянных припоями группы «ВПр» соединений коррозионно-стойких жаростойких и жаропрочных сплавов
Временное сопротивление разрыву в МПа
Предел прочности на срез ср МПа
Для изготовления паяных высоконагруженных конструкций из жаропрочных сплавов и коррозионно-стойких сталей работающих в условиях температур не ниже 9500С и в агрессивных средах нашли применение при пайке реакторных материалов [15] порошки композиционных припоев. В качестве основы композиционных никелевых припоев используются две марки припоев ПХ13Н75С7Р и ПХ12Н75С8Р в количестве 80 90 % а в качестве тугоплавкого наполнителя - порошки тугоплавкого сплава ПХ18Н15 молибдена или вольфрама. В таблицах 3.17 и 3.18 приведены никелевые аморфные припои выпускаемые «МИФИ-АМЕТО» в виде пластичной ленты шириной 20 мм и толщиной
Таблица 3.17 - Марки аморфных припоев на никелевой основе
Рекомендуемая температура пайки °С
ТУ 1842-001-13293050-96
Электроконтактная пайка на воздухе с флюсами ПВ200 ПВ201; пайка коррозионно-стойких дисперсионно-упроч-ненных сталей жаростойких сплавов фехраля нихрома
ТУ 1842-004-13293050-96
Пайка в вакууме инертных газах. Индукционная или газопламенная с флюсами ПВ200 ПВ201. Паяемый материал - стали + твердые сплавы типа ВКТ5К10
Таблица 3.18 - Химический состав аморфных припоев
Содержание элементов % (масс.)* (Ni - остальное)
Полного расплавления
Основным компонентом в марганцевых припоях является никель (таблица 3.19).
Таблица 3.19 - Марганцевые припои
Содержание элементов % (масс.)
Марганец с никелем образуют ряд твердых растворов и при содержании 395 %Ni сплав Mn-Ni имеет температуру плавления 1005 °С. Припои на основе марганца обладают хорошей растекаемостью и способностью смачивать паяемый металл а также высокой пластичностью. Применяются они для пайки коррозионно-стойких сталей инконеля нихрома и др. Пайку этими припоями выполняют при нагреве в печах или ТВЧ в среде нейтральных газов. Нагрев желательно производить быстро во избежание испарения марганца из припоя.
Титан относится к числу активных металлов имеет высокую температуру плавления (1668 °С) сравнительно низкую плотность достаточно высокую удельную прочность и обладает хорошими геттерными свойствами. При нагреве выше 400 °С на воздухе титан и его сплавы активно окисляются; в среде водорода и азота титан образует гидриды или нитриды. Припои с титаном обладают повышенной активностью и способностью смачивать поверхности тугоплавких металлов и металлов покрытых окислами а также минералокерамику; их применяют для пайки тугоплавких металлов титана и его сплавов. Пайку производят в нейтральных газах (аргон гелий) не содержащих кислород азот и водород или в вакууме 1333 000133 Па
Некоторые припои с титаном приведены в таблице 3.20. Припои на основе титана представляют собой эвтектики титана с медью никелем кобальтом и другими металлами они весьма хрупки и их применяют в виде порошка или паст.
Таблица 3.20 - Состав и свойства титановых припоев
Содержание элементов % (масс.) (Ti - остальное)
Хрупкость припоев содержащих титан препятствует изготовлению из них ленты (полос) фольги или проволоки традиционными методами обработки давлением. Современные технологии высокоскоростного затвердевания из расплава со скоростями охлаждения 105 106 °Сс позволяют получать титановые припои в виде пластичных лент и тонких порошков (таблица 3.21).
Таблица 3.21 - Химический состав титановых припоев
Содержание основных элементов % (масс.) (Ti - остальное)
Возможно образование этих припоев и в процессе пайки вследствие контактного плавления. При пайке в зазор между паяемыми изделиями из титана укладывают фольгу из медно-никелевого сплава толщиной 01 03 мм или титановую фольгу гальванически покрытую медью и никелем. При пайке в интервале температур 960 1100°С вследствие контактного плавления образуется титано-медно-никелевая эвтектика являющаяся припоем.
Для конструкций из тугоплавких сплавов работающих при высоких температурах применяют припои приведенные в таблице 3.20. Пайка этими припоями затруднена из-за отсутствия специального нагревательного оборудования особенно для изделий больших габаритов. Нагрев в процессе пайки осуществляют в вакуумных печах ТВЧ плазменными горелками электроконтактным способом и электронным лучом.
В таблице 3.21 приведены наиболее применяемые в отечественной практике титановые припои и их химический состав.
Таким образом из всех рассмотренных припоев можно рекомендовать припои систем Cu-Ni Cu-Pd Ag-Pd Pd-Ni Ni-Cu-Pd Ni-Pd-Cu-Ge Ni-Pd-Cr-Ge Ni-Cr-W-Co-B. Палладий вводимый в припои в качестве компонента значительно повышает их коррозионную стойкость пластичность электропроводность теплопроводность а так же способствуют растеканию их по паяемой поверхности. Палладий с серебром медью никелем образуют ряд твердых растворов поэтому припои содержащие их имеют высокую пластичность паяных соединений. Добавки палладия в припои снижают их способность проникать в паяемый металл и разъедать его. Введение в состав припоев кремния повышает жаропрочность припоя меди - повышает жидкотекучесть и растекаемость серебра - увеличивает тепло- и электропроводность пластичность коррозионную стойкостью и технологичность. Хром значительно повышает жаропрочность и жаростойкость никелевых сплавов и температуру плавления. Понижают температуру плавления также введением кремния бора фосфора марганца. Вольфрам и ниобий повышая жаростойкость несколько понижают температуру плавления никелевых сплавов. Германий повышает жаростойкость припоя. Кобальт увеличивает жаропрочность и механические свойства.
Так как рассматривается пайка никелевого сплава ЖС32 и металлокерамики то выбираем никелевые припои. По совокупности свойств наилучшим из рассмотренных вариантов представляется припой ВПр36 обладающий необходимой жаростойкостью и рядом технологичностью. Для большего увеличения жаростойкости возможно добавление небольшого количества (10-15%) алюминидного порошка состава СДП-2.
Организационно-экономическая часть проекта
В данном разделе рассматривается SWOT – анализ предлагаемого в данной ВКР способа а также представлено технико-экономическое обоснование научно-исследовательской работы прикладного характера.
Все эксперименты происходят на действующем лабораторном оборудовании не требующем дополнительных затрат по его обновлению.
1SWOT – анализ предлагаемого способа создания жаростойкого покрытия
В данной работе для определения сильных и слабых сторон а также возможностей и угроз исходящих из его ближайшего окружения (внешней среды) по разработанному способу создания жаростойкого покрытия применяется SWOT – анализ.
Применение SWOT – анализа создает прекрасные предпосылки для разработки тактики конкурентной борьбы и обеспечения конкурентных преимуществ а также позволяющее систематизировать проблемные ситуации лучше осознать структуру ресурсов на которые следует опираться в совершенствовании деятельности и развитии организации.
При проведении SWOT – анализа необходимо заполнение специальной матрицы (таблица 4.1). При этом сначала необходимо составить перечень параметров по которым будет производиться оценка. Затем выделить наиболее важные из них и определить в какой квадрант матрицы необходимо отнести соответствующий параметр. Определение параметров а также ранжирование их по уровню значимости проводилось с привлечением экспертов. В качестве основных параметров использовались: 1) организация; 2) новизна; 3) финансы; 4) производство; 5) интеллектуальная защита; 6) качество получаемой поверхности и др. В итоге получим оценку актуальности рассматриваемого процесса.
Таблица 4.1 – SWOT – анализ
высокий уровень квалификации руководящих сотрудников предприятия
новый способ с решением задачи повышения эксплуатационно-адгезионной прочности на границе керамика-металл
низкая стоимость модернизации оборудования; отсутствие необходимости проектирования и изготовления сложной технологической оснастки
простота процесса; низкая стоимость модернизации оборудования; отсутствие необходимости проектирования и изготовления сложной технологической оснастки
заявки: два патента прошли с положительным решением и две на стадии экспертизы по существу
повышение эксплуатационных свойств
необходимость обеспечения экологичности проекта
неопределенный срок окупаемости проекта
отсутствие стабильного финансирования
необходимость создания высокоточной оснастки
плотная интеграция с заводами авиационной техники
развитие новых отраслей потребителей
выход на рынок иностранных компаний
усиление позиций отечеств технологии
наличие конкуренции на рынке в виде существующих технологий
уменьшение госзаказов на производство авиационной техники
2Определение трудоемкости выполнения НИР
В соответствие с темой дипломного проекта определяются этапы НИР и их содержание (таблица 4.2). Этапы НИР необходимо максимально детализировать.
Таблица 4.2 – Этапы НИР и их содержание
Занятость по теме дней
Сбор и изучение научно-технической литературы
Младший научный сотрудник
Проведение патентных исследований
Анализ состояния вопросов по теме НИР
Формулирование возможных направлений решения задач
) Старший научный сотрудник
) Младший научный сотрудник
Разработка общей методики проведения исследований
) Руководитель подразделения
Разработка рабочих гипотез построение моделей объекта исследований обоснование допущений
Подготовка образцов для проведения экспериментов
Подготовка испытательного оборудования для проведения экспериментов
Исследование возможных режимов напыления
Проведение процесса напыления покрытия
Оценка адгезтонной прочности и изотермической жаростойкости и термостойкости
Продолжение таблицы 4.2
Исследования структуры образцов
Исследование фазового состава образцов (рентгеноструктурные исследования)
Проведение дополнительных экспериментов (при необходимости)
Обработка и анализ полученных результатов
Отработка режимов (оптимизация)
Оценка полноты решения поставленных задач
Проведение дополнительных исследований (при необходимости)
Составление и оформление отчета
Рассмотрение результатов проведенной НИР и приемка работы в целом
) Руководитель подразделения
) Старший преподаватель
Трудоемкость выполнения НИР определяется по сумме этапов и видов работ оцениваемых экспертным путем в человеко-днях и носит вероятностный характер так как зависит от множества трудно учитываемых факторов и поэтому применяются оценки минимально возможной трудоемкости выполнения отдельных видов работ - ai максимально возможной - bi и наиболее вероятной - mi.
По этим величинам оценивается ожидаемое значение трудоемкостей Ti и их дисперсии Di :
Экспертные оценки и расчетные величины трудоемкости и дисперсии сводятся в таблицу 4.3.
Таблица 4.3 – Расчетные значения трудоемкости и дисперсии
Оценка адгезионной прочности и изотермической жаростойкости и термостойкости
Исследование структуры образцов
Продолжение таблицы 4.3
Анализ проведенных расчетов позволяет сделать вывод о том что расчетное ожидаемое время выполнения работы приближается к наиболее вероятному времени и разброс временных параметров располагается в интервале от 011 до 044. Это говорит о том что при проведении работ необходимо строго соблюдать временной режим.
3Построение сетевого графика выполнения НИР
Одной из основных целей планирования НИР является определение общей продолжительности их проведения.
С целью обеспечения наглядности представления всех видов работ по теме и максимального сокращения времени за счет параллельного выполнения работ график проведения НИР отображается обычно в виде диаграммы Ганта (приложение Д) для оптимизации сроков выполнения НИР и нахождения работ с критическим сроком исполнения.
4Определение плановой себестоимости проведения НИР
Целью планирования себестоимости проведения НИР является экономически обоснованное определение величины затрат на ее выполнение. В плановую себестоимость НИР включаются все затраты связанные с ее выполнением независимо от источника их финансирования.
Определение затрат на НИР производится путем составления калькуляции плановой себестоимости.
Калькуляция составляется по следующим статьям затрат:
) основные и вспомогательные материалы;
) спецоборудование для научных (экспериментальных) работ;
) основная заработная плата;
) дополнительная заработная плата;
) отчисления на социальное страхование;
) расходы на служебные командировки;
) затраты по работам выполняемым сторонними организациями и предприятиями;
) прочие прямые расходы;
) накладные расходы.
) На статью «Материалы» относят затраты на сырье основные и вспомогательные материалы покупные полуфабрикаты и комплектующие изделия необходимые для выполнения конкретной НИР (за вычетом возвратных отходов). Затраты определяются по действующим ценам (с учетом транспортно-заготовительных расходов (ТЗР) величина которых составляет 7 – 10% от стоимости материалов покупных полуфабрикатов и комплектующих изделий (таблица 4.4)
Таблица 4.4 – Расчет стоимости материалов
Наименование материала
Сумма с учетом ТЗР руб.
Циркония окись стабилизированная (порошок)
ВПР-36 + система алюминидного порошка ВСДП-11
Баллон под азот о.с.ч.
Баллон под аргон о.с.ч.
ТУ 2114-002-49632579-2006
Электрокорунд 25А или 14А зернистостью 80
Ацетон технический марок "Ч
) На статью «энергия» относят затраты на энергию. При проведении операции напыления потребляемая мощность 204 КВтч процесс напыления проводится 10 дней по 8 рабочих часов итого – 80 часов или 16016 Квт. При цене 118489 рубМВт-ч получаем 18977 руб. Затраты на проведение остальных экспериментов не предполагают высокого энергопотребления.
) На статью «Спецоборудование для научных (экспериментальных) работ» относят затраты на приобретение или изготовление специальных приборов стендов аппаратов и другого специального оборудования необходимого для выполнения конкретной НИР (с учетом транспортно - заготовительных расходов и затрат связанных с установкой и монтажом спец. оборудования величина которых составляет 12 – 15% от договорной цены специального оборудования) (таблица 4.6).
Таблица 4.6 - Расчет затрат по статье «специальное оборудование для научных (экспериментальных) работ»
Специальное оборудование
Цена за аренду тыс. руб.
Сумма с учетом ТЗР руб
Микроскоп оптический
Транспортно-заготовительные расходы
) На статью основная заработная плата (зп) в качестве базы для расчета зп принимается месячный оклад (таблица 4.2) соответствующего исполнителя работ с учетом доли участия в проекте (таблица 4.7).
Таблица 4.7 – Расчет основной заработной платы
Ставка за 1 рабочий день руб. *
Заработная плата руб.
Руководитель подразделения
Старший научный сотрудник
Младший научный сотрудник №1
Младший научный сотрудник №2
Примечание: * размер ставки рассчитывается исходя из того что месячный оклад выплачивается за 23 рабочих дня (таблица 4.2).
) В научных учреждениях дополнительная заработная плата составляет 10 –15% от основной заработной платы а с учетом различных надбавок составляет 69787 руб.
) На статью «Отчисления на социальное страхование» относятся отчисления на оплату перерывов в работе по временной нетрудоспособности.
В научных учреждения отчисления на социальное страхование составляют 12 – 14% от суммы основной и дополнительной заработной платы или 380738 руб.
) На статью «Расходы на служебные командировки» относятся расходы на все виды служебных командировок работников выполняющих задания по конкретной НИР.
В научных учреждениях расходы на служебные командировки учитываемые в плановой себестоимости проведения НИР составляют 2 – 3% от основной заработной платы сотрудников занятых ее выполнением.
Производственные командировки условиями договора не предусмотрены.
) На статью «Затраты по работам выполняемым сторонними организациями и предприятиями» относятся затраты по оплате всех видов работ выполняемых для конкретной НИР сторонними организациями и предприятиями а также подчиненным опытными производствами состоящими на самостоятельном балансе.
Контрагентные работы не проводились расходы отсутствуют. Оплата услуг опытного производства находящегося на самостоятельном балансе не проводилась.
) На статью «Прочие прямые расходы» относятся расходы на приобретение и подготовку материалов специальной научно-технической информации за использование средств связи и др. расходы необходимые при проведении конкретной НИР.
Общевузовские расходы. По условиям договора берутся 15% от заработной платы и составляют 371243 руб.
Расходы на научно-техническую информацию отсутствуют.
Расходы на зарубежные лицензии и патенты отсутствуют.
) В статью «Накладные расходы» включаются расходы на управление и хозяйственное обслуживание которые в равной степени относятся ко всем выполняемым НИР (заработная плата аппарата управления и общехозяйственных служб затраты на содержание и текущий ремонт зданий амортизационные отчисления) составляют от 40% до 50% от заработной платы или 9900 руб.
На основании полученных данных по отдельным статьям затрат составляется калькуляция себестоимости в целом по НИР (таблица 4.8).
Таблица 4.8 - Калькуляция плановой себестоимости проведения НИР
Спецоборудование для научных (экспериментальных работ)
Основная заработная плата
Дополнительная заработная плата
Отчисления на социальное страхование
Расходы на служебные командировки
Затраты по работам выполняемым сторонними организациями и предприятиями
Прочие прямые расходы
Плановая себестоимость
5Определение прибыли и договорной цены НИР
Плановая прибыль по каждой теме НИР рассчитывается по формуле:
гдеП - плановая прибыль по теме тыс. руб.;
Цд - договорная цена по теме тыс. руб.;
Сп - плановая себестоимость по теме тыс. руб.
Для фундаментальных и поисковых НИР а также в случае невозможности по объективным причинам рассчитать величину экономического эффекта по прикладным НИР договорная цена устанавливается по формуле
гдеФзп - заработная плата сотрудников непосредственно участвующих в выполнении НИР тыс.руб;
Н р - нормативная рентабельность % (24%);
К - коэффициент учитывающий заработную плату обслуживающих и управленческих подразделений что составляет 16%.
Из формул (4.3) и (4.4) следует что значение прибыли равно:руб.
6Оценка показателей технического уровня (инновационного потенциала)
Для анализа инновационной деятельности предприятия необходим анализ-прогноз будущих факторов успеха в условиях неопределенности и обоснование затрат будущего периода. В отличие от детерминированных экономических процессов текущего производства процессы внедрения новой техники и технологии с их последующей коммерциализацией имеют стохастический характер. Поэтому анализ влияний на прибыль следует строить на основе методов прогнозирования методов экспертных оценок множественного регрессионного анализа а также ситуационного и имитационного моделирования.
В условиях рыночной экономики анализ эффективности инновационной деятельности усложняется приобретая многоступенчатый и многостадийный характер.
Выбор показателей наиболее существенных свойств для оценки технического уровня производился с привлечением консультанта по ВКР (таблица 4.9). Оценка важности (весомости) выбранных показателей производиться методом экспертных оценок (непосредственного оценивания). При этом эксперты должны осуществить прямое оценивание важности каждого выделенного свойства по шкале относительной значимости в диапазоне значений оценок от 1 до 10. Понятно что чем важнее показатель качества тем больше оценивающий его коэффициент весомости. Правда есть одно ограничение: сумма коэффициентов для всех существенных свойств (d1 d2 dn) должна быть равна1.
Таблица 4.9 - Оценивание показателей технического уровня
Показатель патентной защиты
Длительность процесса
Экологичность процесса
Возможность автоматизации процесса
Повышение адгезионных свойств
Повышение теплозащитных свойств
Повышение ресурса эксплуатации
Использование дополнительной оснастки
Квалификация исполнительного персонала
Определения искомых значений коэффициентов весомости оцениваемых свойств осуществляется по формуле:
n– число исследуемых объектов;
k – количество экспертов.
Расчет коэффициентов весомости приведен в таблице 4.10.
Таблица 4.10 – Расчет коэффициентов весомости
Коэффициент весомости
Отклонение от средней суммы баллов
Квадрат отклонения от средней суммы баллов
Сред-няя сум-ма бал-лов
При использовании экспертных методов мнения экспертов часто совпадают не полностью. Поэтому необходимо количественно оценивать меру согласованности мнений экспертов. Согласованность мнений экспертов можно оценить по величине коэффициента конкордации:
гдеk – количество экспертов;
n – количество объектов экспертизы;
S – сумма квадратов отклонений средней суммы баллов от суммы баллов каждого объекта.
Коэффициент конкордации имеет границы . При полной согласованности мнений экспертов W =1 при отсутствии - W=0. При W 03 – согласованность мнений экспертов неудовлетворительная; при 03 W 07 – средняя; при W > 07 – высокая. О согласии экспертов можно говорить начиная с величины 042.
Отсюда следует что согласованность экспертов средняя.
Определение оценок (Б1 Б2 Бn) по выбранной предварительно шкале измерения характеристик технического уровня по существующим и предлагаемому способам (таблица 4.11).
Таблица 4.11 – Определение оценок по существующим и предлагаемому способам
Примечание: I – Предлагаемый способ; II- Технология получения жаростойкого покрытия разработанная ВИАМ в 80-х гг; III - Технология получения жаростойкого покрытия разработанная ВИАМ наших дней.
Для наглядности технического уровня по каждому из способов на основании значений таблицы 4.11 приведем диаграмму на рисунке 4.3.
-12 - номер соответствующего показателя из таблицы 4.11.
Рисунок 4.3 - Диаграмма технитеских уровней способов нанесения жаростойких покрытий
Вычисления величины средневзвешенного арифметического показателя технического уровня произведем по формуле:
n – количество объектов экспертизы.
В качестве базовой модели примем способ №3.
Определение коэффициента эксплуатационно-технической эквивалентности произведем по формуле:
где УТнов - показатель технического уровня по новому способу;
УТнов - показатель технического уровня по базовому способу.
Таким образом наиболее предпочтительным способом является предлагаемый способ получения жаростойкого покрытия.
Рассчитанные основные технико-экономические показатели НИР приведены в таблице 4.12.
Таблица 4.12 – Технико-экономические показатели НИР
Значение показателей
Трудоемкость выполнения НИР
Длительность проведения НИР
Плановая себестоимость проведения НИР
Вывод: таким образом приведенный расчет показывает что предлагаемый в данной НИР способ получения жаростойкого покрытия является востребованным.
Безопасность и экологичность проекта
Обеспечение безопасных условий работы оператора установки для нанесения покрытий открытой плазмой
Охрана труда играет важную роль в трудовой жизни человека. Правильная организация труда значительно повышает его производительность и резко снижает возможность производственных травм увечий и пр. Это в свою очередь оказывает и непосредственное положительное влияние на экономическую сторону труда: происходит снижение на оплату больничных листов и лечения сотрудников уменьшается количество и размер компенсаций за работу во вредных условиях и пр. По статистическим подсчетам затраты на необходимые мероприятия и средства для охраны труда и безопасности жизнедеятельности обходятся в десять раз меньше чем расходы из-за несчастных случаев и т.п. [15 с. 24-35]
Таким образом учитывая вышеизложенное можно говорить об актуальности необходимости изучения проблем производственной безопасности.
Цель: обеспечение защиты персонала от опасных и вредных производственных факторов; обеспечение экологичности производства.
Разработать и рассчитать средства защиты от шума;
Рассмотреть и рекомендовать способы очистки сточных вод.
1Шум в производственных условиях
1.1Физические характеристики шума
В документах Международной организации труда под шумом понимают любой звук который может вызвать потерю слуха или быть вредным для здоровья или опасным в другом отношении [23]. Определенное таким способом понятие "шум" включает в себя звуковые колебания (от 20 до 20 000 Гц) и колебания на инфразвуковых (ниже 20 Гц) и ультразвуковых (выше 21 000 Гц) частотах. Под звуком понимают периодические и не периодические колебания давления воздуха. Однако не только в воздухе но и во всех газах и жидкостях и твердых телах могут возникать подобные колебания которые воспринимаются как звук. В настоящее время звуком называют любые механические колебания твердой жидкой или газовой среды в которой звуковые волны передают энергию возмущения от источника в диапазоне частот воспринимаемом человеческим ухом от 16 Гц до 20 кГц. Колебания ниже 16 Гц называют инфразвуком выше 20 кГц — ультразвуком. В газообразной среде изменение давления и плотности в звуковой волне малы поэтому скорость звука будет равна:
где Ро – статистическое давление;
r - плотность среды;
g - коэффициент адиабаты.
1.2Нормирование шума на рабочих местах
Нормативными документами регламентирующими уровень шума на рабочих местах являются ГОСТ 12.1.003—83 и СН 2.2.42.1.8.562—96. При нормировании используют понятия:
— эквивалентный (по энергии) уровень звука LA экв дБ(А) непостоянного шума — это уровень звука постоянного широкополосного шума который имеет такое же среднеквадратичное звуковое давление что и данный непостоянный шум в течение определенного интервала времени.
предельно допустимый уровень (ПДУ) шума – это уровень фактора шума который при ежедневной работе но не более часа в неделю в течение всего рабочего стажа не должен вызывать заболеваний или в отдаленные сроки жизни настоящего и последующих поколений. Соблюдение ПДУ шума не исключает нарушения здоровья у сверхчувствительных лиц;
допустимый уровень шума – это уровень который не вызывает у человека значительного беспокойства и существенных изменений показателей функционального состояния систем и анализаторов чувствительных к шуму.
Нормируемые параметры ограничивающие уровень шума зависят от вида шума.
Таблица 5.1 - Предельно допустимые уровни звука и эквивалентные уровни звука на рабочих местах для трудовой деятельности разных категорий тяжести и напряженности дБ(А) [24]
Категория напряженности трудового процесса
Категория тяжести трудового процесса
Легкая физическая нагрузка
Средняя физическая нагрузка
Тяжелый труд 1-й степени
Тяжелый труд 2-й степени
Тяжелый труд 3-й степени
Напряженность легкой степени
Напряженность средней степени
Напряженность тяжелой степени
Напряженность сверхтяжелой степени
1.3Воздействие шума на организм человека. Средства и методы защиты от шума
К настоящему времени накоплены многочисленные данные позволяющие судить о характере и особенностях влияния шумового фактора на слуховую функцию. Кратковременное понижение остроты слуха под воздействием шума с быстрым восстановлением функции после прекращения действия фактора рассматривается как проявление адаптационной защитно-приспособительной реакции слухового органа. Адаптацией к шуму принято считать временное понижение слуха не более чем на 10—15 дБ с восстановлением его в течение 3 мин после прекращения действия шума [16 с. 56-62]. Длительное воздействие интенсивного шума может приводить к перераздражению клеток звукового анализатора и его утомлению а затем к стойкому снижению остроты слуха.
Слуховой анализатор обладает высокой чувствительностью позволяет человеку воспринимать широкий диапазон звуков окружающей среды и анализировать их по силе высоте тона отмечать изменения по интенсивности и частотному диапазону. Острота слуха не постоянна. В тишине она возрастает под влиянием шума снижается. Такое временное изменение чувствительности слухового аппарата называется адаптацией слуха. Адаптация играет защитную роль против продолжительно действующих шумов. Длительное воздействие шума большой интенсивности приводит к патологическому состоянию слухового органа к его утомлению.
Появление утомления органа слуха следует рассматривать как ранний сигнал угрозы развития тугоухости и глухоты. Синдромом заболевания слухового рецептора являются головные боли и шум в ушах иногда потеря равновесия и тошнота.
Помимо действия шума на органы слуха установлено его вредное влияние на многие органы и системы организма в первую очередь на центральную нервную систему функциональные изменения в которой происходят раньше чем диагностируется нарушение слуховой чувствительности. Поражение нервной системы под действием шума сопровождается раздражительностью ослаблением памяти апатией подавленным настроением изменением кожной чувствительности и другими нарушениями в частности замедляется скорость психических реакций наступает расстройство сна и т. д. У работников умственного труда происходит снижение темпа работы ее качества и производительности.
Таким образом воздействие шума может привести к сочетанию профессиональной тугоухости (неврит слухового нерва) с функциональными расстройствами центральной нервной вегетативной сердечно-сосудистой и других систем которые могут рассматриваться как профессиональное заболевание — шумовая болезнь. Профессиональный неврит слухового нерва (шумовая болезнь) чаще всего встречается у рабочих различных отраслей машиностроения текстильной промышленности и проч [17 с. 201-207].
1.4Средства и методы защиты от шума в производственных условиях
В соответствии с ГОСТ 12.1.029—80 средства и методы защиты от шума по отношению к защищаемому объекту классифицируются следующим образом: средства и методы коллективной защиты; средства индивидуальной защиты. Из средств коллективной защиты по отношению к источнику возбуждения шума выделим средства снижающие шум на пути его распространения от источника до защищаемого объекта.
Из средств и методов коллективной защиты от шума в зависимости от способа реализации выделим акустические средства защиты от шума которые в зависимости от принципа действия классифицируются на:
средства звукоизоляции;
средства звукопоглощения;
средства виброизоляции;
средства демпфирования;
1.5Звукоизоляция и звукопоглощение
Средства звукоизоляции в зависимости от конструкции подразделяются на:
звукоизолирующие ограждения зданий и помещений;
звукоизолирующие кожухи;
звукоизолирующие кабины;
акустические экраны выгородки.
Акустические поглощающие материалы обычно бывают пористыми или волокнистыми. Внутренняя структура материала такова что падающая звуковая энергия преобразуется там в тепловую за счет трения в порах. Такие материалы как минеральное волокно маты из стекловолокна асбест и т.д. являются хорошими акустическими поглощающими материалами.
1.6Средства индивидуальной защиты человека от шума
Средства индивидуальной защиты человека от шума в зависимости от конструктивного исполнения подразделяются на:
противошумные наушники закрывающие ушную раковину снаружи;
противошумные вкладыши перекрывающие наружный слуховой проход или прилегающие к нему;
противошумные шлемы и каски;
противошумные костюмы.
Применение средств индивидуальной защиты от интенсивных шумов является эффективным если они рационально выбраны и систематически используются.
Исследования проведенные с помощью современных физиологических методов показали что индивидуальные средства значительно защищают организм от раздражающего действия шума обеспечивая предупреждение различных глубоких функциональных нарушений и расстройств. Однако использование средств индивидуальной защиты не решает проблемы борьбы с шумом в целом. Только правильно разработанный комплекс описанных выше мероприятий может полностью предотвратить вредные воздействия шума на организм работающих [ стр 201-207].
1.7Расчет звукоизолирующей кабины
При нанесении покрытий с помощью плазмотрона звуковое давление около него достигает 90 дБ(А). Из таблицы 5.1 предельно допустимый уровень звука при данных условиях труда равен 70 дБ(А) а значит для безопасных условий труда необходимо защитить человека от воздействия звука. Пути решения данного вопроса заключаются в двух частных случаях. Так как процесс автоматизирован то в первом случае возможно использование шумоизолирующей камеры. При этом органы управления выносятся наружу. Но так как может возникнуть производственная необходимость по работе вблизи установки (например при отработке новой технологии) то необходимо использовать индивидуальные средства защиты в данном случае предпочтителен костюм так как при напылении атмосфера частично непригодна для дыхания.
Рассчитаем толщину звукоизолирующего слоя. При конструкции стенки камеры представляющей собой двухслойное ограждение средняя звукоизолирующая способность рассчитывается по формуле [20 с. 97]:
R = 135lgQ+13+Δ дБ(5.2)
где Q - вес 1 м2 стен в кг
Δ - аддитивный член величина которого зависит от ширины l воздушного промежутка.
Таблица 5.2 - Зависимость величины Δ от l
Для заполнения промежутка используем минераловатные плиты. Тогда при толщине 40 мм вес 1 м2 будет равен 2 кг а Δ будет равно 3 дБ.
R = 135lg2 + 13 + 3 = 2006 дБ.
Таким образом достигается понижение шума с 90 до 6994 дБ что меньше 70дБ(А).
2Очистка сточных вод
При нанесении покрытий открытой плазмой степень использования материала равна в среднем 70%. Это значит что 30% материала не осаждаются и в результате атмосфера производственного помещения загрязняется. Если из воздуха данные частицы уносятся вентиляцией то с пола выпавшую грязь убирают влажной очисткой. Воду после этого нельзя использовать так как в большинстве наносимых материалов присутствуют тяжелые металлы. Таким образом сточные воды необходимо очищать от вредных примесей.
Задача очистки сточных вод усложняется малыми размерами удаляемых частиц например частицы керамики имеют размер 20 – 15 мкм.
В производстве нашли наибольшее применение следующие способы очистки воды от мелкодисперсных частиц [21]:
Очистка в поле гравитационных сил – способ отстоя;
Очистка в поле центробежных сил – в центрифугах;
Фильтрация под давлением через тканевые и металлические сетки;
Очистка в поле магнитных сил;
Комбинированный способ очистки.
Отстаивание сточных вод производят в специальных отстойниках. Этот способ очистки имеет ограниченное применение из-за большой продолжительности (5—8 ч) отстаивания.
Конструктивно отстойники могут выполняться горизонтальными (модификация горизонтальных – наклонные); радиальными и вертикальными.
Очистка от крупных частиц может проводиться в отстойнике с непрерывным отводом очищенной воды и периодическим удалением шлама.
Устройство для очистки сточных вод способом отстаивания представляет собой бак 1 с нижней частью конусообразной формы. В ней отстаивается шлам 2 который через кран 3 удаляется в тару 4 (рисунок 5.1)
Рисунок 5.1 - Устройство для очистки сточных вод
Центрифугирование — это процесс удаления из жидкости твердых частиц т. е. шлама под действием центробежных сил. Протекает этот процесс в специальных агрегатах—центрифугах. Применение центрифуг обеспечивает хорошую очистку при центробежном критерии Фруда Fr≥600:
где=(*n)30 – угловая скорость вращения ротора (барабана);
r – внутренний радиус ротора (барабана);
g – ускорение силы тяжести.
Стоимость полного удаления твердых частиц центрифугами примерно в 10 раз превышает стоимость менее эффективного фильтрования.
Удаление из воды частиц средних размеров можно осуществить посредством гидроциклонов использующихся в пищевой промышленности а для более тонкой очистки применить гидрореактивную центрифугу.
Очистка в гидроциклоне сочетает принципы отстойников и аппаратов центробежного разделения.
Тангенциальный подвод воды в гидроциклоне вызывает вращательное движение потока воды вокруг отводящего патрубка.
Возникающая центробежная сила действует на взвешенные в воде частицы вызывая их осаждение на внутреннюю поверхность корпуса гидроциклона.
Основным элементом гидрореактивной центрифуги является ротор с двумя насадками для истечения воды. Ротор приводится во вращение реакцией истекающих струй воды.
При фильтровании загрязненную частицами воду пропускают через фильтрующую ткань с мельчайшими отверстиями. Для этого способа очистки применяют фильтры-прессы.
Сетчатые фильтры устанавливаются как в нагнетающей так и во всасывающей магистрали. Изготовляются такие фильтры из мелкоячеистых сеток в нержавеющем исполнении. Размеры ячеек сетки определяют степень очистки воды и находятся в соответствии с величиной частиц.
Существенным недостатком фильтрования под давлением является забивание фильтрирующей поверхности шламом что приводит к быстрому снижению скорости фильтрования и увеличению перепада давления воды на фильтре. Это вызывает частую промывку фильтра. В связи с этим разработаны конструкции фильтров с непрерывным смывом продуктов фильтрации потоком циркулирующей воды. Недостатком также является громоздкость и сравнительно большое потребление электроэнергии.
Достоинством фильтр-пресса является то что благодаря высокому давлению фильтрования (15 кгсм2) он позволяет получить спрессованный шлам с влажностью 15 – 20 % пригодный для дальнейшей транспортировки и переработки. Фильтр-пресс работает на автоматическом режиме или на кнопочном управлении пооперационно.
Вакуум-фильтр барабанный с ножевым съемом осадка (БОН) широко распространен в промышленности используется для разделения среднедисперсных суспензий (сточных вод и пр).
Вакуум-фильтр барабанный со съемом осадка сходящим полотном – предназначены для фильтрования труднофильтруемых высокодисперсных суспензий.
Вакуум фильтр дисковый – высокопроизводительный фильтр для угольной промышленности обладает большой площадью фильтрования.
Вакуум-фильтр ленточный – предназначен для разделения быстрорасслаивающихся суспензий.
Конструкция барабанного вакуум-фильтра со сходящим полотном представлена на рисунке 5.2 [18].
Вакуум-фильтр со сходящим полотном состоит из горизонтально расположенного цилиндрического полого барабана частично (на 35 40%) погруженного в корыто с фильтруемой суспензией. Разделенный внутри на изолированные секции барабан вращается на валу один конец которого соединен с электроприводом а другой имеет распределительную головку. Назначение распределительной головки заключается в последовательном сообщении отдельных секций барабана с вакуумной и напорной линиями. При вращении барабана часть его поверхности погружена в находящуюся в емкости суспензию. Фильтрат под действием вакуума проходит через фильтровальную ткань секции барабана и отводится наружу. Фильтровальная ткань при вращении барабана сходит на систему роликов. При прохождении ее через разгрузочно-продувочный ролик кек продувается и снимается ножом. При дальнейшем движении ткани происходит ее промывка с обеих сторон.
Рисунок 5.2 - Схема устройства вакуум-фильтра
Преимущества вакуум-фильтров: высокая производительность надежность длительный срок службы отсутствие расходных материалов низкая стоимость эксплуатации.
Недостатки: высокая первоначальная стоимость (в том числе вакуумный насос влагоотделитель вакуум-бак или барометрическая труба).
Флотацию используют для удаления нерастворимых диспергированных примесей которые самопроизвольно плохо отстаиваются. В неких вариантах флотацию употребляют и для удаления растворенных веществ к примеру ПАВ. Таковой процесс называют «пенной сепарацией» либо «пенным концентрированием». Флотацию используют для очистки сточных вод многих производств. Она употребляется также для выделения активного либо после биохимической очистки.
Достоинствами флотации являются непрерывность процесса широкий спектр внедрения небольшие капитальные и эксплуатационные издержки обычная аппаратура селективность выделения примесей по сравнению с отстаиванием крупная скорость процесса а так же возможность получения шлама более низкой влажности (90-95%) высокая степень очистки (95-98%) возможность рекуперации удаляемых веществ. Флотация сопровождается аэрацией сточных вод понижением концентрации пав и легкоокисляемых веществ микробов и микроорганизмов. Все это способствует удачному проведению последующих стадий очистки сточных вод.
Элементарный акт флотации заключается в следующем: при сближении подымающегося в воде пузырька воздуха с жесткой гидрофобной частицей разделяющая их прослойка воды при неком критической толщине прорывается и происходит слипание пузырька с частицей. Потом комплекс пузырек – частица подымается на поверхность воды где пузырьки собираются и возникает пенный слой с более высокой концентрацией частиц чем в исходной воде.
Возможность прилипания зависит от смачиваемости частицы которая характеризуется величиной краевого угла . Чем больше краевой угол смачивания тем больше возможность прилипания и крепкость удержания пузырька на поверхности частицы. Прилипание происходит при столкновении пузырька с частицей либо при возникновении пузырька из раствора на поверхности частицы. На величину смачиваемости поверхности взвешенных частиц влияют адсорбционные явления и присутствие в воде примесей пав электролитов и др.
Пав – реагенты-собиратели адсорбируясь на частицах снижают их смачиваемость т.е. делают их гидрофобными. В качестве реагентов-собирателей употребляют: масла жирные кислоты и их соли амины и др. Повышения гидрофобности частиц можно достичь и сорбцией молекул растворенных газов на их поверхности.
Эффект разделения флотацией зависит от размера и количества пузырьков воздуха. По неким данным лучший размер пузырьков равен 15-30 мкм. При этом нужна высокая степень насыщения воды пузырьками либо огромное газосодержание. Удельный расход воздуха снижается с повышением концентрации примесей так как возрастает возможность столкновения и прилипания. Огромное значение имеет стабилизация размеров пузырьков в процессе флотации. Для данной цели вводят разные пенообразователи которые уменьшают поверхностную энергию раздела фаз. Некие из этих веществ владеют собирательными и пенообразующими качествами.
Вес частиц не обязан превосходить силы прилипания её к пузырьку и подъемной силы пузырьков. Размер частиц которые отлично флотируются зависит от плотности материала и равен 02-15 мм.
Различают следующие методы флотационной обработки: с выделением воздуха из растворов; с механическим диспергированием воздуха; с подачей воздуха через пористые материалы электрофлотацию и химическую флотацию.
При напылении металлосодержащих покрытий для очистки воды может быть использована очистка в поле магнитных сил.
Магнит в очистном устройстве притягивает магнетит и осуществляет очистку. Применение магнитного поля для очистки вод не содержащих магнетитов и магнитных окислов не дает существенного эффекта.
Эксперименты по изучению влияния ультразвука и электростатического поля на скорость осаждения шлама показали что ультразвук и электростатическое поле не оказывают существенного влияния на скорость осаждения шлама из воды.
Комбинированный способ применяется в основном для тонкой очистки воды а соответствующий агрегат представляет совокупность различных очистных аппаратов.
Необходимость очистки сточных вод от шлама определяется особенностями процессов нанесения покрытий и зависит во многом от их технологических параметров например от размеров наносимых частиц.
Качество очистки воды проверяют с помощью специальных приборов — мутномеров. При отсутствии таких приборов или при необходимости проверки правильной их работы качество очистки оценивают по контрольной дозе которую отстаивают в течение 1—3 ч.
В данном разделе: 1) выполнен расчет шумозащитной камеры; 2) рассмотрены и рекомендованы способы очистки сточных вод.
Таким образом в результате выполнения данной работы:
изучен рабочий чертеж детали проанализирована ее конструкция и условия работы в изделии;
дана оценка технологичности изготовления детали;
выбран и обоснован метод получения заготовки дана оценка КИМ;
разработан план обработки детали произведен расчет операционных размеров;
разработаны операционные технологические процессы выбран инструмент расчитаны режимы обработки нормы штучного времени;
разработана технология нанесения подслоя жаростойкого многослойного покрытия с температурой жаростойкости до 1050 0С.
Производство газотурбинных двигателей Под ред. В.В. Крымова. М.: Машиностроение Машиностроение – Полет 2002. 376 с. ил.
Турбореактивный двухконтурный двигатель с форсажной камерой сгорания АЛ-31Ф: Учеб. пособие Под редакцией А.П. Назарова. - ВКНА им Жуковского 1987 363 с.
Справочник технолога-машиностроителя. В 2-х т. Т.1 Под редакцией А.Г. Косиловой и Р.К. Мещерякова.-4-е изд.перераб. И доп.-М: Машиностроение 1986 656 с.;ил.
Варгафтик Н. Б. Справочник по теплофизическим свойствам газов и жидкостей Н. Б. Варгафтик .— 2-е изд. доп. и перераб. — Москва : Наука 1972 .— 720 с. : ил.
Пузряков А. Ф. Теоретические основы технологии плазменного напыления : А. Ф. Пузряков .— М. : Изд-во МГТУ им. Н. Э. Баумана 2003 .— 360 с. : ил.
Газотермическое напыление: учеб. пособие под ред. Л.Х. Балдаева. М.: Маркет ДС 2007. - 344 с ил.
Станок плоскошлифовальный 3е711в. Руководство по эксплуатации. – Минск : «Полымя» 1983. – 28 с. ил.
Горбацевич А.Ф. Шкред В.А. Курсовое проектирование по технологии машиностроения: учебное пособие для машиностроит. спец. вузов. – 4-е изд. перераб. и доп. – Мн.: Выш. школа 1983. – 256 с. ил.
Марочник сталей и сплавов сост. М. М. Колосков [ и др.]; под ред. А. С. Зубченко .— М. : Машиностроение 2001 .— 672 с.
Общемашиностроительные нормативы времени и режимов резания для нормирования работ выполняемых на универсальных и многоцелевых станках с числовым программным управлением. Нормативы режимов резания. -М: Экономика 1990-208с.
Анурьев В. И. Справочник конструктора – машиностроителя: В 3 т. Т. 2 – 8-е изд. перераб. и доп. Под ред И. Н. Жестоковой. – М.: Машиностроение 2001. – 920 с.: ил.
Допуски и посадки : справочник : в 2-х ч. Ч.2. В. Д. Мягков [и др.] .— Л. : Машиностроение 1983 — 448с. : ил.
Лашко С. В. Лашко Н. Ф. Пайка металлов. М.: Машиностроение 1988. 376 с.
Понимаш И. Д. Орлов А. В. Рыбкин Б. В. Вакуумная пайка реакторных материалов. М.: Энергоатомиздат. 1995. - 191 с.
Основы безопасности жизнедеятельности Т.А. Хван П.А. Хван. – Изд. 4-е. – Ростов нД: Феникс 2007.
Безопасность жизнедеятельности: Учебник Под ред. Проф. Э.А. Арустамова. – 12-е изд. перер. и доп. – М.: Издательско торговая корпорация «Дашков и К» 2007. – 56-62 стр.
Безопасность технологических процессов и производств: Учеб. Пособие для вузов П.П.. Кукин В.Л. Лапин Н.Л. Пономарев и др. – 2-е изд. испр. и доп. М.: Высш. шк. 2005. – 201-207стр.
Безопасность жизнедеятельности: Учебник для студентов средних спец.учеб.заведений С.В. Белов. В.А. Девисилов А.Ф. Козьяков и др.; Под. общ. Ред. С.В. Белова. – 3-е изд. испр. и доп. – М.: Высш. шк. 2005. – 189-195 стр.
Графкина М.В. Михайлов В.А. Нюнин Б.Н. Безопасность жизнедеятельности: учебник под общ. ред. Б.Н. Нюнина.- М.: ТК Велби Изд-во Проспект 2007. – 156-196 стр.
Алексеев С.П. Казаков А.М. Колотилев Н.Н. Борьба с шумом и вибрацией в машиностроении. - М.: Машиностроение 1980. - 95-97 стр.
Роев Г.А. Очистные сооружения. Охрана окружающей среды М. Недра 1993.
Комарова Л.Ф. Полетаева М.А. Использование воды на предприятиях и очистка сточных вод в различных отраслях промышленности: учебное пособие. - Барнаул АлтГТУ 2010. - 174 стр.
Конвенция № 148 Международной организации труда
Санитарные нормы СН 2.2.42.1.8.562-96 "Шум на рабочих местах в помещениях жилых общественных зданий и на территории жилой застройки
Справочник технолога-машиностроителя. В 2-х т. Т.2 Под редакцией А.Г. Косиловой и Р.К. Мещерякова.-4-е изд.перераб. И доп.-М: Машиностроение 1986 656 с.;ил.
Анурьев В. И. Справочник конструктора – машиностроителя: В 3 т. Т. 1 – 8-е изд. перераб. и доп. Под ред И. Н. Жестоковой. – М.: Машиностроение 2001. – 920 с.: ил.
Анурьев В. И. Справочник конструктора – машиностроителя: В 3 т. Т. 3 – 8-е изд. перераб. и доп. Под ред И. Н. Жестоковой. – М.: Машиностроение 2001. – 920 с.: ил.
Комплект технологической документации перспективного технологического процесса
Совмещенная схема обработки
Базовый ТП изготовления детали
Граф размерных связей
Рекомендуемые чертежи
- 24.01.2023
- 09.03.2014
- 24.01.2023