Проект установки гфу производительностью 690 тыс.


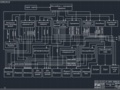
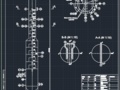
- Добавлен: 22.08.2022
- Размер: 4 MB
- Закачек: 2
Описание
Цель работы – проектирование установки ГФУ, расчет основного аппарата, оценка рентабельности производства.
Предмет исследования – проект установки ГФУ.
В результате ВКР была разработана установка газофракционирования. Представлен материальный баланс по топливному варианту с глубокой переработкой нефти, разработана технологическая схема установки, представлен расчет основного и вспомогательного оборудования. Также рассмотрена безопасность и экологичность установки, доказана рентабельность производства.
Работа включает: 106 страниц, 38 таблиц, 4 рисунка, 5 графических листов; использованных источников – 42
Состав проекта
![]() ![]() ![]() ![]() |
![]() ![]() ![]() |
![]() ![]() ![]() ![]() |
![]() ![]() ![]() ![]() |
![]() ![]() ![]() ![]() |
![]() ![]() ![]() ![]() |
Дополнительная информация
схема молниезащиты.dwg

СибГУ им. М.Ф. Решетнева
Наименование параметра
Высота молниеотвода hм
Радиус горизонтального сечения rx
Диплом_Трофимова В.Ю..docx
Федеральное государственное бюджетное образовательное учреждение
«Сибирский государственный университет науки и технологий
имени академика М.Ф.Решетнева»
Направление 18.03.01 Химическая технология
Кафедра химической технологии твердых ракетных топлив нефтепродуктов и полимерных композиций
ВЫПУСКНАЯ КВАЛИФИКАЦИОННАЯ РАБОТА
Вид ВКР: бакалаврская работа
ПРОЕКТ УСТАНОВКИ ГФУ ПРОИЗВОДИТЕЛЬНОСТЬЮ 690 ТЫС. ТГОД
Допускается к защите
имени академика М.Ф. Решетнева»
Заведующий кафедрой ХТПК
НА ВЫПУСКНУЮ КВАЛИФИКАЦИОННУЮ РАБОТУ
в форме бакалаврской работы .
Обучающийся Трофимова Вероника Юрьевна
фамилия имя отчество
Группа БХМ16-01 Направление 18.03.01. Химическая технология .
направленность (профиль) Химическая технология природных энергоносителей и углеродных материалов .
Тема выпускной квалификационной работы проект установки ГФУ производительностью 690 тыс.тгод
Утверждена приказом по университету от 26.03.20№ 647
Руководитель ВКР – Н.В. Андриевская доцент кафедры ХТПК кандидат химических наук СибГУ им. М.Ф.Решетнева
инициалы фамилия должность ученое звание и место работы
Исходные данные для ВКР установка ГФУ производительностью 690 тыс.тгод нефть Северо-варьеганская
Перечень разделов ВКР содержание введение технико-экономическое обоснование технологические решения безопасность и экологичность проекта эффективность инвестиций заключение
Перечень графического материала (с указанием обязательных чертежей при необходимости) поточная схема НПЗ технологическая схема ГФУ сборочный чертеж этановой колонны схема молниезащиты этановой колонны основные технико-экономические показатели
Срок сдачи обучающимся первого варианта ВКР – « 8 » июня 2020 г.
Срок сдачи обучающимся окончательного варианта ВКР – « 15 » июня 2020 г.
подпись инициалы и фамилия
к бакалаврской работе
«Проект установки ГФУ производительностью 690 тыс.тгод»
Трофимова Вероника Юрьевна
Ключевые слова: технологическая схема газофракционирование этановая колонна экологичность безопасность эффективность инвестиций.
Цель работы – проектирование установки ГФУ расчет основного аппарата оценка рентабельности производства.
Предмет исследования – проект установки ГФУ.
В результате ВКР была разработана установка газофракционирования. Представлен материальный баланс по топливному варианту с глубокой переработкой нефти разработана технологическая схема установки представлен расчет основного и вспомогательного оборудования. Также рассмотрена безопасность и экологичность установки доказана рентабельность производства.
Работа включает: 106 страниц 38 таблиц 4 рисунка 5 графических листов; использованных источников – 42.
Технико-экономическое обоснование7
Технологические решения8
1Характеристика исходной нефти8
2Выбор варианта и технологической схемы переработки нефти11
3Характеристика установок по переработке нефти13
4Материальный баланс предприятия17
4.1Материальный баланс НПЗ с глубокой переработкой нефти17
4.2Сводный материальный баланс НПЗ с глубокой переработкой нефти 22
5Описание технологического процесса газофракционирования24
5.1Характеристика сырья газофракционирующей установки24
5.2Теоретические основы процесса24
5.3Характеристика процесса25
5.4Основные химические реакции26
5.5Влияние основных технологических параметров на конечные результаты процесса27
5.6Технологическая схема ГФУ27
5.7Характеристика продуктов процесса и их применение28
6Выбор основного оборудования31
6.1Обоснование выбора типа основных аппаратов и оборудования установки31
7Расчет основного оборудования34
7.1Расчет деэтанизатора ГФУ34
7.2Расчет подогревателя сырья деэтанизатора54
7.3Расчет кипятильника деэтанизатора56
Безопасность и экологичность проекта57
1Безопасность проекта58
1.1Анализ опасных и вредных производственных факторов на участке газофракционирования58
1.2Общая характеристика опасности проектируемого производства64
1.3Организационные мероприятия по улучшению условий труда66
1.4Мероприятия по производственной безопасности67
1.5Производственная санитария71
1.6Пожарная безопасность74
2Экологичность проекта75
2.1Охрана атмосферного воздуха75
2.2Охрана и рациональное использование водных ресурсов77
2.3Утилизация отходов охрана почв от загрязнения78
Эффективность инвестиций80
1Режим работы цеха эффективный фонд работы оборудования80
2Расчёт стоимости основных производственных фондов83
2.1Расчёт стоимости зданий и сооружений83
2.2Расчёт стоимости технологического оборудования транспортных средств инструмента и инвентаря83
3Расчёт текущих затрат86
3.1Расчёт численности персонала86
3.2Расчет фондов заработной платы персонала89
3.3Планирование себестоимости продукции93
3.4Расчёт себестоимости продукции95
3.5Планирование прибыли97
Список использованных источников102
Нефть и газ составляют основу энергетического баланса нашей страны. Добыча нефти и газа а также строительство новых нефтеперерабатывающих заводов сейчас продвигается в дальние регионы нашей страны Восточную Сибирь Дальний Восток а особенно в северные регионы.
Одной из ключевых задач развития нефтеперерабатывающей промышленности является повышение глубины переработки нефти за счёт увеличения доли вторичных процессов. К числу вторичных процессов переработки нефти относится процесс газофракционирования предельных газов.
Сжиженные углеводородные газы (СУГ) наряду с природными являются наиболее экологичным и удобным в использовании традиционным видом топлива и при этом является относительно недорогим.
Исходя из повышающегося потребления СУГ в качестве моторного топлива и сырья нефтехимии целью данной выпускной квалификационной работы является расчет установки газофракционирования предельных газов а также обоснование выбора схемы переработки нефти. В качестве сырья для переработки на НПЗ предложена северо-варьеганская нефть.
Технико-экономическое обоснование
С экономической точки зрения рентабельнее транспортировать сырье (нефть) к месту концентрированного потребления нефтепродуктов чем перевозить нефтепродукты с заводов расположенных вблизи промыслов. Поэтому нефтеперерабатывающий завод следует размещать именно в районах с высокой долей потребления нефтепродуктов. Нефтеперерабатывающая промышленность выполняет вспомогательную функцию и не является отраслью специализации Ханты-Мансийского автономного округа где и ведется добыча северо-варьеганской нефти. Наибольшая часть добытой нефти по системе нефтепроводов отправляется за пределы округа в западных и частично восточных направлениях на нефтеперерабатывающие заводы (НПЗ) страны и на экспорт.
Нефтеперерабатывающий завод в состав которого входит проектируемая газофракциониующая установка является предприятием топливного направления перерабатывающий северо-варьеганскую нефть. Данная нефть отличается малой плотностью небольшим содержанием силикагелевых смол асфальтенов и серы.
Установка газофракционирования относится к установкам вторичных процессов переработки нефти. Мощность установки по продукту 690 тыс. тгод. Установка предназначена для переработки нестабильных головок получаемых на установке атмосферно-вакуумной перегонки нефти (АВТ) а также жирных газов риформинга с получением следующих продуктов:
- сухого газа (используется как топливо в технологических печах);
-пропановой фракции (используется как сырье пиролиза бытовой сжиженный газ хладагент для многих технологических установок);
-изобутановой фракции (служит сырьем для установок алкилирования и производства синтетического каучука);
-н-бутановой фракции (применяется как сырье пиролиза производства синтетического каучука зимой добавляется к товарным автомобильным бензинам для обеспечения требуемого давления паров летом используется как компонент бытового сжиженного газа);
- фракции С5 и выше (применяется как компонент автобензина).
Перспективное увеличение потребности в углеводородных газах вполне обосновано. Углеводородные газы НПЗ являются ценным сырьем для нефтехимических процессов и используются как энергетическое и бытовое топливо. А использование сжиженного газа для коммунально-бытового потребления рентабельно с экономической точки зрения. Также перспективно расширение применения сжиженных углеводородных газов в автотранспорте с целью экономии автомобильного бензина.
Резюмируя выше сказанное можно сделать вывод о том что данный проект является эффективным как с технической точки зрения так и с экономической.
Технологические решения
1Характеристика исходной нефти
Сырьем для нефтеперерабатывающего завода является нефть Северо-Варьеганского месторождения.
Для выбора варианта и схемы переработки нефти приводится её характеристика. Характеристика северо-варьеганской нефти представлена в виде таблиц взятых из пособия [1]. В характеристике нефти приводятся: характеристика фракций выкипающих до 350°С физико-химические свойства групповой углеводородный состав характеристика легких керосиновых дистиллятов характеристика дизельных топлив и компонентов свойств определяющих шифр нефти и ее состав по истинным температурам кипения (ИТК).
По материалам таблицы 1 и таблицы 2 и стандарту ГОСТ Р 51858-2002 устанавливается шифр нефти который является основой для выбора варианта и схемы переработки нефти.
В таблице 1 приведена физико-химическая характеристика северо-варьеганской нефти
Таблица 1 - Физико-химическая характеристика северо-варьеганской нефти[1]
Наименование показателей
Плотность при 20 0С кгм3
Кинематическая вязкость мм2с:
Температура застывания:
(с термообработкой) 0С
(без термообработки) 0С
– сернокислотных смол
– силикагелевых смол
Кислотное число мг КОН на 1 кг. нефти
Температура вспышки в закрытом тигле 0С
Выход фракций в % весовых:
Разгонка северо-варьеганской нефти и характеристика полученных фракций представлена в таблице 2.
Таблица 2 - Разгонка северо-варьеганской нефти и характеристика полученных фракций [1]
Температура выкипания фракции
2Выбор варианта и технологической схемы переработки нефти
Исследование нефти для ее последующей классификации проводится для оценки перспективных возможностей производства различных нефтепродуктов из данной нефти и выбор оптимальной схемы ее переработки.
Существует несколько вариантов технологических схем переработки нефти. В общем виде эти схемы могут быть сведены к трем-четырем основным типам:
)топливная с неглубокой переработкой нефти;
)топливная с глубокой переработкой нефти
)топливно-нефтехимическая.
Схема нефтеперерабатывающего завода определяется потребностью в нефтепродуктах конкретного ассортимента качеством перерабатываемой нефти состоянием разработки технологических процессов. Решающим фактором выступает потребность в нефтепродуктах того района где находится предприятие. Кроме того балансом производства и потребления нефтепродуктов предусматривается их перевозки с минимумом расходов.
Северо-варьеганская нефть по технологической классификации нефтей согласно ГОСТ Р 51858-2002 имеет шифр: 1.1.1.2 то есть относится к малосернистым (до 060 % вкл) имеет выход фракций до 350°С (60-658%) относительная плотность (не более 0830) не высокое содержание смолистых соединений (силикагеливые смолы не более 12%) в бензиновых фракциях значительно высокое содержание нафтеновых углеводородов (30-47%).
По классификации нефти видно что она подходит для переработки по топливному варианту. В таком случае выбираем схему завода по топливному варианту с глубокой переработкой нефти.
авод имеет в своём составе установки первичной и вторичной переработки. Из первичной - это обессоливание обезвоживание нефти перегонка на разделение бензиновой керосиновой дизельной фракций; вторичной перегонки - когда бензиновая фракция делится на три узкие фракции одна из них направляется на изомеризацию вторая - на установку каталитического риформинга для получения бензола толуола третья - (тяжёлый бензин) подвергается каталитическому риформингу в режиме производства высокооктанового бензина. Керосиновая и дизельная фракции очищаются от сернистых соединений на установке гидроочистки; часть дизельной фракции депарафинизируется с получением жидких парафинов С10-С20 и зимнего дизельного топлива. Газовые потоки AT и риформинга поступают на ГФУ для получения товарных сжиженных газов - пропана н- бутана изо-бутана и т.д. Тяжёлый остаток AT – мазут – выпускается как товарное котельное топливо.
На рисунке 1 представлена схема завода по топливному варианту с глубокой переработкой нефти.
Рисунок 1 - Поточная схема завода с глубокой переработкой нефти по топливному вариант
3Характеристика установок по переработке нефти
Нефть сырая из резервуаров хранения поступает на установку ЭЛОУ-АВТ которая является головной.
Назначение установки- разделение нефти на фракции для дальнейшей переработки. Процесс производится с помощью физико-химических методов: обессоливание обезвоживание очистки от сернистых соединений; физических методов: ректификации теплообмена. Перегонка осуществляется на атмосферных трубчатых (АТ) и атмосферно-вакуумных трубчатых (АВТ) установках. Сначала перегонку ведут при атмосферном давлении с выделением бензиновой и других высококипящих фракций; остаток – мазут – перегоняют в вакууме для предотвращения расщепления углеводородов при действии высокой температуры. Установка предназначена для получения из нефти углеводородного газа бензиновой фракции керосиновой фракции дизельной фракции (атмосферный гайзоль) мазута вакуумных дистиллятов (вакуумных газойлей) гудрона.
Назначение установки каталитического риформинга и экстракции ароматических углеводородов – получение высокооктанового компонента автомобильных бензинов концентрата для производства индивидуальных ароматических углеводородов а также технического водорода. В качестве сырья используются фракции отбираемые в пределах 62-85°С и 85-105°С. Сырьё с блока риформинга вводится в экстрактор в верхнюю часть которого подаётся экстрагент. В качестве продукции получаем – углеводородный газ головку стабилизации катализат водородсодержащий газ индивидуальные ароматические углеводороды.
Прямогонные бензиновые фракции (85-105°С105-140°С140-180°С) являются сырьём установки каталитического риформинга. Процесс заключается в ароматизации бензиновых фракций происходящих в результате реакций каталитического преобразования нафтеновых и парафиновых углеводородов в ароматические при этом значительно возрастает октановое число. Выход высокооктанового компонента бензина составляет 80-88% (масс.) его октановое число 80-85 (моторный метод) против 30-40 для сырья. В процессе применяют катализаторы риформинга. Они относятся к классу окисно-металлических катализаторов. Современные катализаторы – полиметаллические представляют собой оксид аллюминия промотированный хлором с равномерно распределенными по всему объемами платиной и металлическими промоторами (рений кадмий). Продуктами каталитического риформинга являются:
а) стабильный катализат – служит компонентом товарного автобензина;
б) водородсодержащий газ – используется на установках гидроочистки дизельного топлива гидроочистки керосина изомеризации углеводородов каталитического крекинга;
в) нестабильная головка – является сырьём газофракционирующей установки;
г) углеводородный газ.
В качестве сырья установки гидроочистки керосина используется фракция 140-180 и 180-230 °С. Установка спроектирована для улучшения качества и повышения стабильности светлых дистиллятов сырья каталитического крекинга в результате использования реакций деструктивного гидрирования сероорганических соединений и гидрирования непредельных углеводородов. Целевым продуктом процесса является гидроочищенный керосин бензин-отгон сероводород.
В качестве исходного дистиллята гидроочистки дизельного топлива используются керосин-газойлевые фракции с температурами выкипания 180 – 230 230 - 350°С (метод разгонки стандартный) дистилляты вторичного происхождения газойли коксования).
Процессы протекают в среде водорода на алюмокобальтмолибденовом или алюмоникельмолибденовом катализаторе путём удаления серы кислорода смолистых соединений непредельных соединений. Процесс гидроочистки повышает стабильность топлив снижает коррозионную активность улучшает цвет и запах.
Сырьём установки карбамидной депарафинизации дизельного топлива является гидроочищенное диз.топливо. Процесс предназначен для получения зимних и арктических дизельных топлив с требуемыми температурами застывания (зимнее – имеет температуру застывания минус 40°С арктическое – минус 60°С) и низкотемпературными свойствами также процесс предназначен для получения низкоплавких парафинов. В процессе карбамидной депарафинизации используется водный насыщенный при 70°С раствор карбамида в смеси воды и изопропанола. Особенностью реакции комплексообразования в таких условиях является быстрое уменьшение концентрации карбамида за счёт его вступления в комплекс с нормальными парафиновыми углеводородами исходного сырья. Поэтому комплексообразование проводят в переменном температурном режиме.
Процесс газофракционирования предназначен для получения индивидуальных легких углеводородов или углеводородных фракций высокой чистоты из нефтезаводских газов. Газофракционирующие установки подразделяются по типу перерабатываемого сырья на ГФУ предельных и ГФУ непредельных газов. На ГФУ предельных газов сырьем являются газы с установок АВТ каталитического риформинга и гидрокрекнга. Газы первичной перегонки проходят очистку 15% раствором МЭА от сероводорода (процесс абсорбции). Очищенная смесь углеводородных газов и головка каталитического риформинга подаются на блок ректификации где выделяются узкие углеводородные фракции:
а) пропановая – используется как бытовой сжиженный газ применяется в качестве хладагента и сырья для пиролиза;
б) изобутановая – применяется в качестве сырья для производства синтетического каучука;
в) бутановая - используется как бытовой сжиженный газ добавляется к автомобильным бензинам для повышения давления паров;
г) изопентановая – служит компонентом высокооктановых бензинов;
д) пентановая – является сырьём для процессов изомеризации;
е) сухой газ – выводится в топливную сеть.
В качестве исходного сырья на установке изомеризации используется фракция пентановая выделенная на ГФУ предельных газов бензиновая фракция н.к.-62°С полученная на установке АТ. В качестве водорода подпитки используется водородсодержащий газ с установки каталитического риформинга. Установка изомеризации предназначенна для повышения октанового числа нефтяных фракция С5 –С6 путем превращения парафинов нормального строения в их изомеры имеющие более высокое октановое число. Установка состоит из двух блоков – ректификации и изомеризации. В блоке ректификации сырьё предварительно разделяется на пентановую и гексановую фракции направляемые на изомеризацию после которой проводится стабилизация полученного продукта и получение из него товарных изопентана и изогексана. В блоке изомеризации выделяют изомеризаты. Процесс изомеризации проводится в реакторе со стационарным слоем катализатора. На российских НПЗ применяются отечественные катализаторы типа СИ-1 и катализаторы изготовленные компанией ЮОП. Целевые продукты изомеризации применяются для производства высокооктановых компонентов бензинов а также сырья для нефтехимической промышленности.
В качестве сырья установки гидрокрекинга используется широкая гамма нефтяная фракция тяжелых остатков (мазута и гудрона). В качестве подпитки – водород с водородной установки. Назначение установки – получение дополнительного количества светлых нефтепродуктов каталитическим разложением тяжелого сырья в присутствии водорода. Используют одноступенчатые и двухступенчатые процессы системы с неподвижным движущимся и суспендированными катализаторами. С установки выводят сжиженный газ бензины легкий газойль дизельную фракцию сероводород.
Сырьем установки производства серы служит сероводород выделенный на установках в процессе переработки нефти. Сероводород получают с помощью 15%-ного водного раствора моноэтаноламина из соответствующих потоков с установок гидроочистки и гидрокрекинга. На установке производства серы смонтирован блок регенерации сероводорода из насыщенных растворов моноэтаноламина. Регенерированный моноэтаноламин возвращается на установки гидроочистки где вновь используется для извлечения сероводорода. Основные стадии процесса производства серы и технического сероводорода: термическое окисление сероводорода кислородом воздуха с получением серы и диоксида серы; взаимодействие диоксида серы с сероводородом в реакторах (конвекторах) загруженных катализатором. Продукт установки – элементарная сера с её содержанием не менее 9998 % (масс.).
Сырьем битумной установки является подготовленный для окисления гудрон мазут с установки АВТ. В состав установки входят: блок вакуумной перегонки мазута и блок окисления гудрона. В блоке ВТ принята одноколонная схема вакуумной переработки мазута обеспечивающая получение гудрона удовлетворяющего по качеству требованиям предъявляемым к сырью для производства битумов методом окисления. Технологическая схема битумного блока - двухпоточная что дает возможность одновременно получать разные марки битумов: строительные и дорожные. Отработанные газы окисления состоящие из азота водяных паров диоксида и оксида углерода остаточного кислорода и органических веществ выводят из окислительного аппарата на термическое обезвреживание - сжигание. Продукцией установки являются дорожные и строительные битумы.
Получение нефтяного кокса выработка дополнительного количества светлых нефтепродуктов из тяжелых остатков производится на установке коксования. Сырьем является гудрон. Основным требованием к качеству сырья является коксуемость – 10-20% содержание серы при получении электродного кокса – не выше 15%. Продукция с установки: нефтяной кокс газ и головка стабилизации бензин керосино-газойлевые фракции.
Производство водорода. Получение водорода из природного газа конверсией метана с водяным паром. В итоге получается обратимая смесь которая называется синтез-газом. Каталитическая конверсия природного газа — основной метод получения водорода в промышленности. [45]
4Материальный баланс предприятия
4.1Материальный баланс НПЗ с глубокой переработкой нефти
В таблице 3 приведен материальный баланс НПЗ по топливному варианту с глубокой переработкой нефти.
Таблица 3 – Материальный баланс НПЗ по топливному варианту с глубокой переработкой нефти
% на сырье установки
Атмосферно-вакуумная перегонка
газ и головка стабилизации
Каталитический риформинг и экстракция ароматических углеводородов
Продолжение таблицы 3
водородсодержаший газ
головка стабилизации
Каталитический риформинг
тяжелый бензин гидрокрекинга
бензины-отгоны гидроочистки
водородсодержащий газ
Гидроочистка керосина
гидроочищенный керосин
Гидроочистка дизельных фракций
легкий газойль коксования
гидроочищенное дизельное топливо
Гидродепарафинизация дизельного топлива
гидроочищенная фракция 240-350°С
Газофракционирование предельных газов
газ и головка атмосферно-вакуумной перегонки
головка кат. риформинга
головка гидрокрекинга
водород содержащий газ
Производство битумов
поверхностно-активные вещества
водород с водородной установки
гудрон (коксуемость 16 %)
Газофракционирование непредельных газов
газ и головка каталитического крекинга
газ и головка коксования
пропан-пропиленовая фракция
бутан-бутиленовая фракция
газовый бензин (С5 и выше)
Алкилирование бутан-бутиленовой фракции изобутаном
в том числе изобутан
Производство водорода
хим. очищенная вода (на реакцию)
водород технический 96 %
в том числе водород 100 %
4.2Сводный материальный баланс НПЗ с глубокой переработкой нефти
В таблице 4 представлен сводный материальный баланс НПЗ при работе по топливному варианту с глубокой переработкой нефти.
Таблица 4 - Сводный материальный баланс НПЗ при работе по топливному варианту с глубокой переработкой нефти
Топливный вариант с глубокой переработкой
Поверхностно-активные вещества на производство битума
Вода на производство водорода
Автомобильный бензин в том числе:
катализат риформинга
рафинат от производства ароматических углеводородов
бензин каталитического крекинга
легкий бензин гидрокрекинга
Керосин гидроочищенный
Дизельное топливо летнее в том числе:
легкий газойль гидрокрекинга
легкий газойль каталитического крекинга
промежуточная фракция депарафинизации
Дизельное топливо зимнее
Ароматические углеводороды в том числе:
Сжиженные газы в том числе:
Продолжение таблицы 4
пропан и бутан-пентаны алкилирования
Битумы дорожные и строительные
Сырье для производства технического углерода – фракция 280-420 °С каталитического крекинга
Котельное топливо в том числе:
тяжелый газойль коксования
фракция выше 420 °С каталитического крекинга
фракция выше 350 °С гидрокрекинга
отгоны производства битумов и гидроочистки масел
экстракты производства масел
фильтрат обезмасливания гача
ловушечный нефтепродукт
Смазочные масла в том числе:
остаточный компонент
Отходы (кокс выжигаемый газы окисления)
Потери безвозвратные
5Описание технологического процесса газофракционирования
5.1Характеристика сырья газофракционирующей установки
Сырьём газофракционирующей установки являются нестабильные головки АТ и каталитического риформинга и гидрокрекинга. Качество сырья определено стандартами предприятия (СТП).
В таблице 5 приведена характеристика качества сырья поступающего на установку.
Таблица 5 - Характеристика качества сырья
Углеводородный состав % масс.:
- содержание метана не более
- содержание этана не более
- содержание пропана не менее
- содержание изобутана не менее
- содержание норм. бутана не менее
- содержание суммы С5 не менее
- содержание суммы С6 и выше не более
Плотность при 200С кгм3
Массовая доля сероводорода % не более
5.2Теоретические основы процесса
Природные и нефтяные газы представляются источником ценного углеводородного сырья для нефтехимической и химической промышленности. Основной компонент этих газов – метан. На газоперерабатывающих заводах для извлечения этана и высших углеводородов применяют абсорбцию низкотемпературную сепарцию адсорбцию и т.д.
Нефтезаводские газы являются в основном углеводородными газами с большим содержанием примесей. Переработка газового сырья включает в себя очистку газа от примесей удаление тяжёлых углеводородов осушку и разделение на фракции или индивидуальные компоненты хранение одоризацию.
Для разделения смесей на индивидуальные компоненты широкое распространение в промышленной практике получил метод ректификации. Для очистки газов от примесей сероводорода двуокиси углерода влаги широко используется метод абсорбции.
Направление переработки газовых фракций зависит от профиля завода и потребности рынка. На проектируемом заводе для производственных нужд необходим «сухой газ» в качестве топлива фракция н-бутана для вовлечения в товарный бензин с целью повышения давления насыщенных паров бензина. Основным товарным продуктом является углеводородный сжиженный топливный газ для коммунально-бытового потребления также спросом на рынке пользуются фракция изобутана и смеси углеводородов для нефтехимии.
5.3Характеристика процесса
ГФУ предназначена для переработки нестабильных головок АТ и каталитического риформинга газа стабилизации каталитического риформинга газов АТ.
Прежде чем направить заводские газы на разделение их необходимо подвергнуть очистке. При очистке удаляются сернистые соединения представленные в нефтяных газах в основном сероводородом. Так же в газах присутствуют диоксиды углерода и меркаптаны. Присутствие сероводорода в газе исключено вследствие его корродирующих и токсичных свойств а также в связи с отравляющим воздействием на катализаторы. Диоксид углерода меркаптаны сероводород создают условия для коррозии металлов снижают эффективность каталитических процессов в которых используются газы. Содержание сероводорода и меркаптанов в товарной продукции регулируется ГОСТами и ТУ. Содержание меркаптанов в сжиженном газе для коммунально-бытовых целей обязательно но должно быть не более 0013%. Присутствующий в газообразном топливе диоксид углерода уменьшает теплоты сгорания топлив.
Для очистки нефтяных и природных газов от сероводорода диоксида углерода и других серо- и кислородосодержащих соединений применяем абсорбционные процессы. Для очистки углеводородов обычно используют водные растворы моноэтаноламина диэтаноламина диизопропаноламина дигликольамина. Нежелательные компоненты при контакте с этими растворителями претерпевают химические реакции. По физико-химическим свойствам и технико-экономическим показателям используем метод очистки газов с помощью моноэтаноламина (МЭА).
Очистка МЭА является типичным примером кругового сорбционного процесса. Сероводород поглощается из газа раствором реагента в одном аппарате и выделяется из раствора в результате его отпаривания в другом. Регенерированный таким образом реагент возвращают на поглощение сероводорода. Очистка газа происходит путем хемосорбции сероводорода 15-30%-ным водным раствором моноэтаноламина.
Выбор схемы промышленной установки газоразделения зависит в основном от состава нефти. Ректификационный метод разделения без предварительной абсорбции или конденсации применяется обычно для разделения деэтанизированных фракций. В нашем случае в состав сырья ГФУ входит этан при этом он находится в газообразном состоянии с примесями более тяжёлых газов. Для разделения необходимо применить предварительную конденсацию газов атмосферной перегонки и в смеси с нестабильными головками подвергнуть ректификации. [6]
5.4Основные химические реакции
В процессе газофракционирования химические реакции возможны только при очистке газов от примесей.
При взаимодействии МЭА с сероводородом протекает следующая химическая реакция:
HОСH2СH2NH2 + H2S (HОСH2СH2NH3)2S + H2S 2(HОСH2СH2NH3)HS
Растворимость H2S в растворе МЭА повышается с увеличением парциального давления H2S в газе. При повышении температуры абсорбции и концентрации раствора МЭА растворимость H2S снижается. Глубина извлечения H2S из газа составляет 99%.
При взаимодействии СО2 с МЭА протекает следующая химическая реакция:
СО2 + 2HОСH2СH2NH2 + H2О (HОСH2СH2NH3)2СО3 + СО2 + H2О
С увеличением давления возрастает скорость реакции с ростом температуры уменьшается эффективность абсорбции. Чем выше давление и концентрация СО2 в газе тем ниже экономичность процесса. Степень извлечения СО2 из газа 98%.
Очистку раствором МЭА проводят в самом начале процесса газофракционирования. Далее очищенное сырьё отправляют на переработку.
По окончании процесса ректификации проводят доочистку товарных продуктов которую называют тонкой. Известным и давно применяемым зарекомендовавшим себя процессом тонкой очистки газов от СО2 является щелочная очистка растворами едкого натра. Основная реакция этого процесса:
NaОH + СО2 Na2СО3 + H2О
При увеличении температуры с 25 до 45 С °скорость абсорбции СО2 возрастает в 15 раза. Остаточное содержание СО2 в газе после очистки не превышает 0001-0002%.
Едким натром производится доочистка от H2S и меркаптанов:
NaОH + RSH NaSR + H2О
Щёлочь взаимодействует и с другими соединениями серы:
СS2 + 2NaОH СОS + Na2S + H2О
СОS + 4NaОH Na2S + Na2СО3 + H2О
Остаточное содержание H2S в газе не более 1 мгм3.
Регенерацию МЭА проводят на специальной установке при температуре 110-130 0С в десорбере. Из выделенного H2S получают элементарную серу [6].
5.5Влияние основных технологических параметров на конечные результаты процесса
Установки фракционирования газа путём ректификации характеризуются некими особенностями. Необходимость полной или частичной конденсации головного погона принуждает проводить процесс ректификации под давлением которое тем больше чем легче головной погон. Однако повышенное давление затрудняет разделение.
Повышенное давление затрудняет разделение так уменьшается относительная летучесть компонентов.
Предполагаемое использование компонентов газа требует чёткого их разделения. Для этого колонны в установках газофракционирования содержат большое количество тарелок. Разрешенная скорость паров в колоннах является функцией разности плотностей стекающей горячей флегмы и понимающихся в том же сечении паров. Так как повышение давления до 1-2 МПа увеличивает плотность паров в 10-20 раз допустимая скорость паров в колоннах не должна превышать 02-025 мс.
Разделение смесей происходит при относительно маленькой разнице температур верха и низа колонны это сказывается и на режиме ректификации уменьшает пределы рабочих температур изменение которых приводит к нарушению режима колонны и установки в общем.
5.6Технологическая схема ГФУ
Нестабильная головка АТ поступает в буферную ёмкость Е-3 в которую подаётся также и нестабильная головка отпарки из секции каталитического риформинга. Смесь углеводородов из Е-3 насосом Н-11 направляется через холодильник Х-1 где охлаждается оборотной водой системы до 400С в экстрактор сероочистки сжиженных газов К-5. Сероочистка проводится 15% водным раствором моноэтаноламина который подаётся в экстрактор с установки регенерации МЭА. Раствор МЭА охлаждается в холодильнике Х-2 до температуры 350С и подаётся в верхнюю часть экстрактора. Насыщенный раствор МЭА из экстрактора К-5 поступает в сепаратор С-5 где происходит сепарация углеводородных газов из раствора МЭА.
Очищенная от сероводорода смесь углеводородов из К-5 поступает в буферную ёмкость сырья ректификации Е-6. Также в неё поступает нестабильная головка каталитического риформинга и смесь углеводородов из ёмкости Е-7. Сырьё ректификации через теплообменник Т-11 где нагревается фракцией «С5 и выше» через подогреватель Т-2 насосом Н-15 подаётся в деэтанизатор К-1. Деэтанизатор К-1 работает в режиме неполной конденсации верхнего продукта (в режиме абсорбции). Газ из верхней части колонны поступает в ёмкость Е-7. Газ из Е-7 выводится в линию сухого газа. Конденсат из Е-7 под собственным давлением подаётся в ёмкость Е-6. В качестве орошения верха колонны К-1 используется сырьё из Е-6 которое подаётся насосами Н-15 16 и 16а. Нижний продукт К-1 под собственным давлением подаётся в дебутанизатор К-2.
Верхний продукт К-2 после охлаждения в воздушных конденсаторах-холодильниках ХК-101111а в водяном холодильнике Х-7 конденсируется и поступает в ёмкость Е-9. Конденсат из Е-9 насосом Н-2122 подаётся частично в колонну К-2 в качестве орошения а балансовый избыток направляется в ёмкость сырья пропановой колонны Е-8. Кубовый продукт К-2 фракция «С5 и выше» проходит по трубкам теплообменника Т-11 где отдаёт тепло сырью деэтанизатора воздушный холодильник Х-6а водяной холодильник Х-6 где охлаждается оборотной водой до температуры 40 0С и направляется в Е-19 19а. Сырьё пропановой колонны К-3 из Е-8 забирается насосами Н-1920 через подогреватель Т-7 подаётся в питательную секцию К-3. Верхний продукт К-3 поступает в воздушные конденсаторы-холодильники ХК-1213 где конденсируется затем охлаждается в Х-10 и поступает в Е-10. Конденсат из Е-10 насосами Н-2324 подаётся частично на орошение в К-3 а балансовый избыток через холодильник Х-3 поступает в ёмкость Е-13. Из Е-13 фракция выводится с установки в ПСГ. Кубовый продукт К-3 под собственным давлением поступает в изобутановую колонну К-4.
Отгонная и укрепляющая части изобутановой колонны выполнены в виде двух последовательно соединённых аппаратов К-41 и К-42. Верхний продукт К-41 после охлаждения в воздушных конденсаторах-холодильниках ХК-141515а проходит холодильник Х-9 и поступает в ёмкость Е-11. Конденсат из Е-11 насосами Н-2930 подаётся частично на орошение в К-41 а балансовый избыток (изобутановая фракция) через холодильник Х-4 поступает в ёмкость Е-15. Из Е-15 фракция выводится с установки в ПСГ. Горячее орошение из куба К-41 насосами Н-2728 подаётся наверх колонны К-42. Пары из К-42 по шламовой линии поступают в нижнюю часть К-41. Нижний продукт К-42 (н-бутановая фракция) насосами Н-2526 через холодильник Х-5 поступает в отстойник Е-17. Н-бутановая фракция выводится с установки в ПСГ. Технологическая схема ГФУ приведена на графическом листе 2.
5.7Характеристика продуктов процесса и их применение
Состав и качество получаемых продуктов определяется составом исходного сырья и технологическим режимом процесса.
Конечными продуктами ГФУ являются:
а) сухой газ в топливную сеть;
б) пропановая фракция с содержанием пропана не менее 96 % вес. с примесями этана и изобутана. Пропановая фракция применяется в качестве сырья для пиролиза хладагента и других целей;
в) изобутановая фракция с содержанием изобутана не менее 97 % вес. с примесями пропана и н-бутана. Изобутановая фракция применяется в качестве сырья для производства синтетического каучука алкилирования и других целей;
г) н-бутановая фракция с содержанием н-бутана не менее 975 % вес. с
примесями изобутана и более тяжелых углеводородов. Н-бутановая фракция применяется в качестве сырья для получения дивинила в производстве синтетического каучука для пиролиза и других целей;
д) сжиженные углеводородные газы для коммунально-бытового потребления;
е) фракция "С5 и выше" с примесями н-бутана применяется как компонент товарного автобензина.
Качество конечных продуктов ГФУ определено соответствующими стандартами предприятия и техническими условиями:
СТП П1-02.02 СП-0052 ЮЛ-101"Сухой газ
СТП № П1-02.02 СП-0049 ЮЛ-101"Фракция пропановая
СТП № П1-02.02 СП-0050 ЮЛ-101"Фракция изобутановая
СТП № П1-02.02 СП-0048 ЮЛ-101"Фракция н-бутановая
СТП № П1-02.02 СП-0043 ЮЛ-101"Газы углеводородные сжиженные для коммунально-бытового потребления
СТП № П1-02.02 СП-0081 ЮЛ-101 "Фракция С5 и выше
ТУ 38.101490–89 "Фракция пропановая
ТУ 38.101492–79 "Фракция изобутановая
ТУ 38.101497–79 "Фракция нормального бутана
ГОСТ 20448–80 "Газы углеводородные сжиженные топливные для коммунально-бытового потребления".
Качество вырабатываемой продукции представлено в таблице 6.
Таблица 6- Характеристика качества вырабатываемой продукции
Характеристика качества
Наименование показателя
ТУ0272-023-00151638-99
Углеводородный состав %вес
Изобутановая фракция
Продолжение таблицы 6
Фракция С5 и выше (кубовый продукт
Сумма метана и этана
Сумма iС4Н10 и нС4Н10
Сумма iС5Н12 и нС5Н12
Фракционный состав оС
Бутан-изопентановая фракция колонны
Газы углеводородные сжиженные для ком-мунально – бытового потребления (ПТ)
Массовая доля компонента %
Объемная доля жидкого остатка
Газы углеводородные сжиженные для ком-мунально – бытового потребления (СПБТ)
6Выбор основного оборудования
6.1Обоснование выбора типа основных аппаратов и оборудования установки
Основными аппаратами установки ГФУ является экстрактор десорбер ректификационные колонны теплообменные аппараты сепараторы и емкости. На НПЗ для разделения нефтезаводских газов применяются преимущественно 2 типа газофракционирующих установок: ректификационный и абсорбционно-ректификационный — АГФУ. На рисунке 2 приведена принципиальная схема проектируемой ГФУ для разделения предельных газов ректификационного типа. [7]
Рисунок 2 - Принципиальная схема газофракционирующей установки (ГФУ):
— деэтанизатор; 2 — пропановая колонна; 3 — бутановая колонна; 4 — изобутановая колонна;5 — пентановая колонна; 6 — изопентановая колонна; I — сырье; II — сухой газ;III — пропановая фракция; IV — изобутановая фракция; V — бутановая фракция; VI — изопентановая фракция;VII — пентановая фракция; VIII — фракция С6 и выше
Массообменные процессы (ректификация экстракция абсорбция и др.) являются одними из самых энергоемких и их эффективность часто определяет экономику производства в целом. Более 50 % энергии расходуется на их осуществление около 15 % от общей массы оборудования технологической линии составляют колонные аппараты.
Ректификация наиболее часто применяемый метод для разделения продуктов и подготовки сырья в химической технологии. Она проста и дает возможность получить очень чистый продукт.
В данном проекте ГФУ будет использоваться непрерывная ректификация. Непрерывная ректификация многокомпонентных смесей осуществляется в установках состоящих из ряда ректификационных колонн непрерывного действия соединение которых в общую схему может быть различным. Каждая простая колонна разделяет поступающую в нее смесь на два продукта один из которых дистиллят а второй – кубовый остаток. Поэтому при наличии хотя бы трех компонентов в исходной смеси их разделение на три продукта в одной простой колонне невозможно. [3]
Для отделения сухого газа используем деэтанизатор который работает как фракционирующий абсорбер. То есть он работает в режиме неполной конденсации верхнего продукта. За счет многоступенчатого контакта газовой и жидкой фаз в верхней части аппарата поглощается наиболее тяжелая часть газа стекая вниз она встречается с все более горячими парами десорбированными из жидкости стекающей в нижнюю часть колонны. В результате с верха уходит сухой газ содержащий углеводороды С1-С2 а снизу выводятся углеводороды С3 – С5. [8]
Ректификационные колонны нефтеперерабатывающих заводов представляют собой вертикальные цилиндрические аппараты снабженные внутри ректификационными тарелками (насадками) и другими вспомогательными устройствами в виде отбойников различных конструкций распределителей ввода сырья перераспределителей потоков штуцеров для отбора фракций и другим оборудованием. Отбойные устройства устанавливаются в определенных местах по высоте колонн и служат для отделения от паров увлекаемых ими частиц жидкости. Устройства ввода предназначены для обеспечения равномерного распределения по сечению колонны потоков жидкости (сырья орошения) и паров (парового орошения).
Основным типом контактных устройств массообменных аппаратов являются тарельчатые устройства которые благодаря их простоте относительно низкой стоимости надежности и удобству в эксплуатации нашли широкое применение практически во всех процессах разделения. Они имеют: высокую производительностью по пару и жидкости и эффективность разделения; низкое гидравлическое сопротивление; широкий диапазон устойчивой работы; высокая надежность и долговечность в том числе и в условиях загрязненных сред сред с повышенной вспениваемостью и т.д.
В ректификационных и абсорбционных колоннах применяются тарелки различных конструкций (колпачковые клапанные струйные провальные и т. п.) существенно различающиеся по своим рабочим характеристикам и технико-экономическим данным. При выборе конструкции контактного устройства учитывают как их гидродинамические и массообменные характеристики так и экономические показатели работы колонны при использовании того или иного типа контактных устройств.
Широко применяют перекрестно-прямоточные клапанные тарелки. Основная особенность их состоит в том что на полотне тарелки расположены клапаны прямоугольной формы над которыми размещен общий для всех клапанов подвижной балласт. Наличие подвижного балласта обеспечивает равномерное открытие всех клапанов при минимальных нагрузках по пару и регулируемый переход от перекрестного движения фаз к однонаправленному при больших нагрузках по пару. Благодаря такому конструктивному решению клапанная балластная тарелка по сравнению с клапанной прямоточной значительно раньше вступает в работу и имеет во всем диапазоне на 1520 % более высокую эффективность разделения и на 1015 % ниже гидравлическое сопротивление. Использование прямоугольных клапанов вместо круглых позволило на 30 % снизить отходы металла (один прямоугольный клапан эквивалентен восьми круглым) сократились на 25 % трудовые затраты на сборку тарелки. По своим массообменным и гидродинамическим характеристикам клапанная балластная тарелка имеет широкую область применения но наиболее предпочтительна она для процессов разделения под вакуумом и умеренным давлением.
Для процессов разделения в которых требуется обеспечить низкое гидравлическое сопротивление используется ситчатая тарелка с отбойниками. Такие тарелки отличаются высокой производительностью по жидкости простотой конструкции и сравнительно небольшой металлоемкостью. По принципу действия тарелка относится к классу перекрестно-прямоточных конструкций. Основание тарелки выполнено из просечно-вытяжного листа ячейки которого имеют наклон 30 и обращены в сторону слива жидкости благодаря чему часть энергии пара используется для организации движения жидкости по тарелке обеспечивая равномерную работу по всей ее плоскости. Для предотвращения уноса жидкости на тарелке поперек движения жидкости установлены отбойные элементы из просечно-вытяжного металла с большим свободным сечением. Ситчатая тарелка обладает низким гидравлическим сопротивлением высокой производительностью и эффективностью. Недостаток конструкции – относительно узкий диапазон эффективной работы.
Исходя из вышеперечисленного для проектируемой установки газофракционирования выбираем экстрактор сероочистки с ситчатыми тарелками этановую колонну с клапанными тарелками которая работает в режиме абсорбции (неполной конденсации верхнего продукта); дебутанизатор пропановая колонна изобутановая колонна– с клапанными тарелками.
Так же для выбранного оборудования необходимо подобрать теплообменные аппараты. Наиболее характерным признаком для классификации теплообменных аппаратов является их назначение: нагрев охлаждение конденсация испарение жидкостей газов или их смесей.
В нефтеперерабатывающей и нефтехимической промышленности распространение получили поверхностные рекуперативные теплообменные аппараты позволяющие осуществлять теплообмен без смешения потоков теплоносителей. Из аппаратов этой группы в нефтепереработке наиболее широко применяются кожухотрубчатые теплообменные аппараты аппараты воздушного охлаждения и теплообменники труба в трубе.
Выбираем кожухотрубчатые теплообменные аппараты.
Перекачка жидких продуктов является одной из основных операций осуществляемых в технологических процессах нефтеперерабатывающей промышленности. Перекачка производится при помощи насосов подразделяемых по принципу действия на лопастные у которых перемещение жидкости производится непрерывным потоком за счет энергии лопасти вращающегося колеса и объемные у которых подача жидкости осуществляется за счет перемещения ее отдельных объемов в нагнетательный трубопровод.
Основные типы лопастных насосов центробежные осевые диагональные; объемных поршневые плунжерные винтовые шестеренные пластинчатые и др. Из числа лопастных насосов на нефтеперерабатывающих заводах наибольшее применение имеют центробежные из числа объемных- поршневые( плунжерные) шестеренные вихревые.
Центробежные насосы имеют следующие преимущества: непрерывность потока небольшая занимаемая площадь относительная простота конструкции и составляют основную часть насосного хозяйства нефтеперерабатывающего завода. По роду перекачиваемой жидкости центробежные насосы НПЗ подразделяются на:
нефтяные- для перекачки нефти нефтепродуктов сжиженных газов;
химические- для перекачки химически активных жидкостей;
насосы общего назначения- для перекачки воды и других жидкостей (применяются в общезаводском хозяйстве).
Выбираем центробежные консольныенасосы[9].
7Расчет основного оборудования
7.1Расчет деэтанизатора ГФУ
Рассчитать этановую колонну газофракционирующей установки при следующих исходных данных: производительность колонны по сырью Gс=821428571 кгч.
Состав попутного газа-сырья подвергающегося отбензиниванию:
Таблица 7- Состав питания колонны (мольные доли):
7.1.1Материальный баланс аппарата
Производительность аппарата кмольч:
где Mс – средняя мольная масса сырья.
Подставляя известные значения в формулу (2) получаем Mс=5686084.
Расчет материального баланса этановой колонны приведен в таблице 8.
Таблица 8 - Расчет материального баланса этановой колонны
Содержание Сi’ мольн. доли
Количество Fi=F*Сi’ кмольч
Степень извлечения φ’мольн. доли
Количество Ri= Fi φ’ кмольч
Содержание XRi= мольн.
Количество Di=Fi-Ri кмольч
Содержание Y’Di= мольн.
7.1.2Температура и давление в аппарате
Температура верхнего продукта колонны на выходе из конденсатора может быть принята равной tо=-30С и выше. Более низкая температура достигается в случае применения аммиачной фреоновой или этановой холодильной установки.
Принимается температура на выходе из конденсатора tо=75С. Если принять давление в емкости орошения равным давлению на выходе из конденсатора то его величина найдется по уравнению изотермы паровой фазы дистиллята путем последовательного приближения:
Константы фазового равновесия определяются по номограмме [10]. Результаты расчета представлены в таблице 9.
Итак давление в емкости орошения D=2.3 МПа.
Составы орошения и дистиллята различны (табл. 8) поэтому пары V1 уходящие с верха колонны будут представлять паровую смесь дистиллята и орошения. Чтобы рассчитать состав паров V1 необходимо знать количество орошения gо подаваемого на верх колонны. Его можно определить зная флегмовое число колонны которое находится по уравнению Андервуда:
в котором значение параметра φ рассчитывается по формуле:
где α i – коэффициент относительной летучести компонента при средней температуре в колонне.
Давление на верху колонны 1 с учетом перепада давления в конденсаторе принимается на 004 Мпа выше давления емкости орошения:
= D+004=23+004=234 МПа.
Давление в секции питания с учетом сопротивления укрепляющих тарелок принимается на 002 Мпа выше давления на верху колонны:
f= 1+002=234+002=236 МПа.
Температура сырья подаваемого в колонну не должна превышать 125С. На основе промышленных данных примем tf=86С.
Расчет степени конденсации сырья при этой температуре и давлении f=236 МПа ведется по уравнению:
методом последовательного приближения заданием нескольких числовых значений степени отгона е’. Результаты расчета даны в таблице 9.
При температуре tf=100С и давлении f=236 МПа половина сырья будет в паровой фазе а половина в конденсате. Заметим что состав паровой фазы сырья сравнительно близок к составу дистиллята поэтому от укрепляющей части колонны не требуется большей разделительной мощности.
Принимается что давление нижней части колонны (или кипятильнике) на 004 МПа больше чем в секции питания. Тогда:
R= f+0.04=236+0.04=24 МПа.
Температура в нижней части колонны (в кипятильнике) при найденном давлении определяется последовательным приближением по уравнению изотермы жидкой фазы остатка:
Таблица 9 - Расчет давления в емкости орошения этановой колонны
Кi при tD=26С D=23 МПа
Таблица 10 - Расчет доли отгона сырья этановой колонны
Ki при tf=86С f=236 МПа
Предварительные расчеты показывают что температура наверху колонны t1=30С (в дальнейшем эта температура уточняется). Поэтому средняя температура и давление в колонне равны:
При этой температуре и среднем давлении в колонне ср=237 МПа находятся константы равновесия компонентов сырья и относительные летучести их при принятии за эталонный компонент нормального пентана. (таблица 12)
Методом последовательного приближения по уравнению Андервуда найдется числовое значение параметра φ. Его величина лежит между значениями относительных летучестей распределенных компонентов т.е. этана и пропана. (Расчет приведен в таблице 12)
Итак параметр в уравнении Андервуда φ=12.
После подстановки значения φ в уравнение Андервуда для расчета rmin получается:
Расчет температуры низа колонны представлен в таблице 11.
Таблица 11 - Расчет температуры низа колонны tR
Итак температура в кипятильнике колонны (низ колонны) равна tR=100С.
Таблица 12 - Расчет параметра φ
Ki при ср=237 МПа tср=72С
Продолжение таблицы 12
Коэффициент избытка орошения находится по соотношению:
Тогда рабочее флегмовое число будет равно:
Подставим значения в формулу 10:
По всей укрепляющей части колонны флегмовое число принимается постоянным.
Количество горячего орошения или флегмы находящейся при температуре начала кипения определяется так:
g=458 · 1205687=5522046 кмольч.
Количество паров приходящихся на любое сечение в диаметральной плоскости укрепляющей части колонны найдется по уравнению материального баланса:
V=1205687 · (458+1)=6727733 кмольч.
Состав паров уходящих с первой тарелки (верхней) тарелки колонны определяется по уравнению концентраций укрепляющей части:
(gо+D)y’1i=gоx’оi+Dy’Di (13)
где gо=g=5522046 кмольч- количество орошения поступающего на первую тарелку;
x’оi- мольная доля компонента в орошении подаваемом на верх колонны (табл. 9).
Из этого уравнения получается:
Расчет состава паров с первой тарелки дан в таблице 13.
Температура верха колонны t1 определяется последовательным приближением по уравнению изотермы паровой фазы уходящей с верхней тарелки колонны:
Таблица 13 - Расчет состава паров с первой тарелки этановой колонны
Расчет температуры верха этановой колонны представлен в таблице 14.
Таблица 14 - Расчет температуры верха этановой колонны
Ki при t1=40 С 1=234 МПа
Итак температура верха колонны t1=40С. Перепад температуры в укрепляющей части невелик и составляет:
7.1.3Материальные потоки секции питания
При расчете секции питания необходимо показать какое количество проходящих через неё потоков удовлетворяют уравнению материального баланса для укрепляющей и отгонной части аппарата.
Материальные потоки секции питания колонны схематически изображены на рисунке 3.
Рисунок 3 - Схема секции питания колонны
Количество парового орошения над верхней отгонной тарелкой рассчитывается по формуле:
где s- паровое число над верхней отгонной тарелкой.
Найти его можно по формуле:
количество парового орошения наверху отгонной части
Vо=0399 · 1324060887=5283 кмольч
количество флегмы с нижней укрепляющей тарелки:
Подставим значения в формулу 17:
gn=458 · 1205687=5522046 кмольч
количество паров поступающих под нижнюю тарелку укрепляющей части:
Vm=5522046 +1205687=6727733 кмольч
количество паровой фазы сырья находим как:
Vс=e’F=01 · 144463=1444629 кмольч
количество жидкой фазы сырья как:
gс=F(1-e’)= 144463· (1-01)=1300167 кмольч
количество флегмы стекающей на верхнюю отгонную тарелку:
gm=gn+gс=5522046 +1300167 =18523713 кмольч
количество паров поднимающихся с верхней отгонной тарелки:
Vо=gm-R=18523713 -132406=5283104 кмольч.
Для проверки вычисляется количество паров поступающих на укрепляющую часть:
Vm=Vс+Vо=5283104 +1444629 =6727733 кмольч.
7.1.4Число тарелок в колонне
Минимальное число теоретических тарелок колонны находятся по уравнению Фенске-Андервуда:
Для определения числа теоретических тарелок в колонне используется уравнение
Соотношение числа теоретических тарелок Nr в укрепляющей и Ns в отгонных частях колонны определяется по уравнению Керкбрайда:
Nr+Ns=N=13914 то решение двух последних уравнений дает Ns=11914 и Nr=2.
В соответствии с имеющимися рекомендациями для колонны принимается клапанная тарелка.
В виду отсутствия надежного метода расчета среднего к.п.д. тарелки для колонн разделяющих многокомпонентные смеси этот параметр в первом приближении рассчитывается (в %) по уравнению:
где (g’V’)ср- среднее мольное отношение встречных на одном уровне жидкого и парового потоков;
- вязкость жидкого сырья при средней температуре в колонне tср=72С Па*с;
hL- глубина погружения центра тяжести прорези колпачка м;
- коэффициент относительной летучести для ключевых компонентов равный (таблица 7)
Сырье принимается за этан (Mf=34) тогда по данным [10] =600*10-6 Па*с.
Далее определяется среднее мольное отношение потоков жидкости и пара:
Поскольку гидравлический расчет тарелки не делается пренебрежение последним слагаемым правой части уравнения (29) приводит к получению несколько заниженного результата:
Число рабочих тарелок рассчитывается по формуле:
Следовательно число тарелок равно:
7.1.5Тепловая нагрузка конденсатора колонны
Из предыдущего изложения следует что дистиллят колонны D получается из емкости орошения в парах при температуре tD=26С. Следовательно в конденсаторе колонны происходит частичная конденсация паров поступающих в него из верхней части колонны. Образующихся из этих паров конденсат подается на орошение колонны. Тепловая нагрузка конденсатора для этого случая найдется по уравнению:
Qk=gо (H1-hо) +D (H1-HD)(33)
где gо=g - количество орошения;
H1- энтальпия паров уходящих с верха колонны при температуре t1=40С и давлении 1=234 МПа кДжмоль;
hо- энтальпия орошения подаваемого на верх колонны при температуре tD=26С кДжмоль;
HD- энтальпия паров дистиллята при температуре tD=26С и давлении D=23 МПа кДжмоль.
Мольные массы потоков рассчитываются на основе данных приведенных в таблице 13.
Дальнейший расчет дает следующие данные:
пары поднимающиеся с верха тарелки колонны
=16 · 00636 + 30 · 03055 + 44 · 06317=379774(34)
MD=16 · 02156 + 30 · 04248 + 44 · 03594=320072(35)
=16 · 00303 + 30 · 02795+ 44 · 06912=392826(36)
Энтальпии потоков (кДжкмоль) находятся по графику [10].
H1=4061 · 379774=1542262 кДжкмоль;
hо=586 · 392826=230196 кДжкмоль;
HD=3349 · 320072=1071921 кДжкмоль.
Тепло конденсатора по формуле 33 равно:
Qk=5522046 (1542262 -230196)+1205687(1542262 -1071921)= 781 ·106 кДжч =217010 кВт(37)
Это тепло снимается в конденсаторе так как должна быть достигнута температура tD=26С.
7.1.6 Тепловая нагрузка кипятильника колонны
Перепад температур по высоте отгонной части составляет:
поэтому количества парового орошения внизу и наверху отгонной части будет значительно отличаться одно от другого. Количество паров внизу отгонной части может быть найдено если известно тепло кипятильника Qp. Это тепло определяется из уравнения теплового баланса колонны:
FQf+Qp=DHD+RhR+Qk(38)
где Qf- энтальпия сырья подаваемого в колонну при температуре tf=100С кДжкмоль;
hR- энтальпия остатка колонны при температуры tR=118С кДжкмоль [10].
Энтальпия сырья рассчитывается по формуле:
где e’- мольная доля отгона сырья;
- энтальпия паровой фазы сырья кДжкмоль;
-энтальпия жидкой фазы сырья кДжкмоль [10].
Вначале находят необходимые исходные данные (таблица 10):
=16 · 009+30 · 00944+44 · 04162+58 · 02128+72 · 00945=4173;
=16 · 001+30 · 00295+44 · 0287+58 · 02727+72 · 02356=5837;
средняя молекулярная масса остатка колонны (таблица 8):
=30 · 00005+44 · 02945+58 · 03381+72 · 03665=5897.
Энтальпия потоков (по графику) кДжмоль [10]:
=4187 · 4173=17472351 кДжкмоль;
=1711 · 5837=9987107 кДжкмоль;
==4396 · 5897=25923212 кДжкмоль.
Согласно уравнению 39:
Из уравнения (40) получим:
QR=1205687· 1071921 +1324060887· 25923212 +7810000- 144462968 · 1073563 =279173026=2791 · 106 кДжч = 775480 кВт
Масса парового орошения VR подаваемого из кипятильника под нижнюю отгонную тарелку без большой ошибки может быть найдена из уравнения:
где - теплота испарения орошения равная разности его энтальпии в паровой и жидкой фазах при температуре tR=100С и давлении R=24 МПа кДжмоль.
Для этого предварительно вычисляются:
средняя молекулярная масса паров орошения (табл. 11):
=30 · 0002185+44 · 05332+58 · 03181+72 · 01523=5294
=6531 · 5294=34575114 кДжкмоль
=4354 · 5294=23050076 кДжкмоль.
Количество парового орошения кмольч найдем по уравнению:
Паровое число внизу колонны равно:
7.1.7 Диаметр колонны
Диаметр колонны рассчитывается по формуле:
где Vсек- секундный объемный расход паров наверху колонны м3ч;
- допустимая скорость паров в свободном поперечном сечении над верхней тарелкой колонны мс.
Объем паров на верху (над верхней укрепляющей тарелкой) колонны определяется по известной формуле:
где z- коэффициент сжимаемости паров определяемый по графику в зависимости от приведенных температур Tпр и давления Рпр [10].
Знание состава паров (табл. 13) и критических констант компонентов [10] (метан этан пропан) позволяет рассчитать критические константы для смеси:
Подставляем данные в формулы соответственно:
Приведенные параметры равны:
По графику [10] находится z (093; 054) =07
По формуле 45 объем паров составляет:
Максимально допустимая скорость паров в свободном сечении над верхней тарелкой колонны рассчитывается по формуле:
где С- коэффициент определяемый из выражения при этом:
ht=05м- принятое расстояние между тарелками;
С’- коэффициент зависящий от поверхностного натяжения на границе на границе «пар-жидкость» на верхней тарелке колонны определяемый из графика зависимости С’=f используемый при определении скорости паров в колоннах для разделения углеводородных газов.
Величина поверхностного натяжения находится по формуле Этвиша:
где - мольная масса орошения стекающего с верха тарелки равная (табл. 14)
=16 · 00085+30 · 01608+44 · 08423=4202;
- плотность этого орошения при температуре t1=40С на верхней тарелке [11];
Ткр- критическая температура остатка равная:
Ткр=1905 · 00085+3052 · 01608+3698 · 08423=36217 К
Подстановка найденных величин в формулу Этвиша дает:
По графику на рисунке 2.3 найдем числовое значение С’=077.
С=009 · 05 · 077=0034.
Рисунок 4 – График зависимости С’=f используемый при определении скорости паров в колоннах для разделения углеводородных газов
Плотность паров уходящих с верхней тарелки равна:
Максимально допустимая скорость паров наверху колонны согласно формуле 50 составляет:
Диаметр колонны в ее верхнем поперечном сечении по формуле 44 равен:
В соответствии с нормативным рядом диаметров по ГОСТ 9617-76 принимается диаметр колонны D=1400 мм=14 м.
Объем паров под нижней отгонной тарелкой рассчитывается по формуле:
где z- коэффициент сжимаемости паров при температуре tR=100С и давлении R=24 Мпа [10].
Критические параметры из формул (46) и (47) равны:
По графику [10] находится z (088; 066) =055
Объем паров по формуле 54 составляет:
Для определения максимально допустимой скорости под нижней отгонной тарелкой рассчитывают данные:
Поверхностное натяжение по формуле Этвиша:
где - плотность остатка при температуре tR=100С кгм3[3].
Ткр- критическая температура остатка равная из формулы 52:
Ткр=3052 · 00005+3698 · 0295+425 · 0065+408 · 02727+461 · 01309+
Плотность остатка равна =555 кгм3.
По графику на рисунке 4 найдем числовое значение С’=067.
Плотность паров орошения на выходе из кипятильника равна:
Плотность паров орошения равна:
Максимально допустимая скорость паров составляет:
Диаметр колонны в ее нижнем поперечном сечении равен:
В соответствии с нормативным рядом диаметров по ГОСТ 9617-76 принимается диаметр колонны D=2400 мм=24 м.
7.1.8 Высота колонны
На основании практических данных принимается:
расстояние между верхним днищем колонны и ее верхней укрепляющей тарелкой h1=1 м;
высота секции питания h3=15 м;
расстояние между нижним днищем и нижней отгонной тарелкой h5=2 м;
расстояние между тарелками hT=05 м; высота юбки h7= 4м. [12]
Тогда рабочая высота колонны будет равна:
Hp=h1+(Nrp-1)hT+h3+(Nsp-1)hT+h5(57)
Hp =1+(3-1)*05+15+(15-1)*05+2=125 м;
Высота занятая укрепляющими тарелками h2 м:
Высота занятая отгонными тарелками h4 м:
h4=(Nsp-1)hT=(15-1)*05=7 м;
Расстояние от нижней тарелки до днища принимается с таким учетом чтобы количество жидкости в кубе колонны обеспечило работу в течении 10 минут приемных насосов для исключения «сброса» в случае прекращения подачи сырья h6 м:
где V – объем газа внизу колонны м3;
F – площадь поперечного сечения низа колонны м2.
Н= h1+ h2+ h3+ h4+h5+ h6+ h7=1+1+15+7+2+7+4=235 м.
7.1.9 Конструирование ректификационной колонны
Принимаем расстояние от нижней тарелки до шва соединяющего обечайку с эллиптическим днищем 3000мм.
Высота полуэллипса с отбортовкой в верхней части 700 мм.
Высота полуэллипса с отбортовкой в нижней части 1200 мм.
Высота опорной обечайки равна 4000 мм для свободного прохода под обвязкой колонны.
Расстояние от верхней тарелки до свода колонны принимаем 1000 мм для лучшего распределения пара и орошения под верхней тарелкой.
Опорную обечайку принимаем одинакового сечения с колонной.
Для расчетов штуцеров необходимых для обвязки колонны определимся с линейными скоростями паров и жидкостей в трубах согласно [12].
Скорость жидкости принимаем 12 мс.
Скорость паров принимаем 01 мс.
Диаметры штуцеров определим согласно таблицы 10.1 [13].
Штуцер ввода питания в колонну-200 мм
Штуцер вывода паров с верха колонны-300 мм
Штуцер ввода орошения в колонну-175 мм
Штуцер вывода кубового остатка-175 мм
Штуцер вывода кубового остатка для нагрева в кипятильнике-500 мм
Штуцер ввода пара в кипятильник-600 мм
Питание колонны обычно подают в 2-3 точках по высоте колонны для лучшего распределения жидкости. Питание подаем на 1513 тарелки. Питание подается непосредственно в карманы.
Орошение в колонну подаем на 18 тарелку разделяя поток на две части разделительным коллектором.
Пар из кипятильника подаем под нижнюю тарелку через маточник.
Внизу колонны установим сетку для предотвращения попадания в трубопроводы посторонних предметов.
Крепление тарелок к корпусу колонны производим с помощью струбцин крепящихся к опорным столикам. Крепление секций между собой с помощью пружинных уголков болтов и гаек.
Выбор металла для изготовления колонны основывается на климатических условиях работы физико-химических свойств веществ участвующих в процессе внешних нагрузок параметров процесса.
Для изготовления корпуса колонны и контактных устройств трубопровода выбираем легированную сталь марганцовистую 09Г2С 10Г2 согласно таблице 6.1 [12].
Чертеж общего вида этановой ректификационной колонны с диаметром в верхнем сечении 1400 мм и с диаметром в нижнем сечении 2400 мм приведен на графическом листе 3.
7.2Расчет подогревателя сырья деэтанизатора
Расчет подогревателя заключается в подборе типового кожухотрубчатого теплообменника по необходимой поверхности теплообмена с учетом потерь при теплопередаче. Нагрев и испарение производим с помощью водяного пара. Давление водяного пара Р = 7 кгссм2 температура водяного пара при этом давлении согласно [10] равна t = 165°С и удельная теплота парообразования r = 2066 кДжкг.
Найдем расход водяного пара:
Средний температурный напор:
Средняя температура сырья:
По трубному пространству теплообменника пропускаем сырье с массовой скоростью w = 7371 кгм2с тогда необходимое сечение труб:
Диаметры труб в теплообменниках лежат в пределах обычно 20-25 мм. Примем трубы диаметром 252 мм и определим количество труб в пучке:
К дальнейшим расчетам принимаем одноходовой кожухотрубчатый теплообменник с линзовым компенсатором на корпусе.
Коэффициент К принимаем исходя из экспериментальных данных в нашем случае теплообмен происходит между водяным паром и сжиженным газом. Согласно таблице 3.45 [14] принимаем К=120 кВтм2К. Необходимая площадь теплообмена:
F = 76694* 103120* 3345= 191 м2
По таблице XXXI [14] выбираем типовой подогреватель ТН с трубами диаметром 25 х 2 мм по ГОСТ 15122-79; диаметр 1000 мм число труб в пучке 747одноходовой с длиной труб 3 м горизонтальный.
7.3Расчет кипятильника деэтанизатора
Расчет кипятильника заключается в подборе типового кожухотрубного теплообменника по необходимой поверхности теплообмена с учетом потерь при теплопередаче. Нагрев и испарение производим с помощью водяного пара. Давление водяного пара Р = 7 кгсм2 температура водяного пара при этом давлении согласно [10] равна t=165°С и удельная теплота парообразования r = 2066 кДжкг. Найдем расход водяного пара с помощью формулы (61):
Gпара=2761*1062066=1336399 кгч=371 кгс
Средний температурный напор:
Средняя температура кубового остатка:
По трубному пространству теплообменника пропускаем кубовый остаток с массовой скоростью w = 885 кгм2с тогда необходимое сечение труб:
S = 8214286885*3600 = 026 м2
Диаметры труб в теплообменниках лежат в пределах обычно 20-25 мм. Примем трубы диаметром 252 мм и определим количество труб в пучке:
n = 026*4314*00252 = 510 шт
К дальнейшим расчетам принимаем одноходовой кожухотрубный теплообменник с линзовым компенсатором на корпусе.
Коэффициент К принимаем исходя их экспериментальных данных в нашем случае теплообмен происходит между водяным паром и сжиженным газом. Согласно табл. 3.45 [14] принимаем К = 280 кВтм2К
Необходимая площадь теплообмена по формуле 64:
F = 76694* 103280*328 = 8351 м2
По таблице XXXI [3] выбираем типовой подогреватель ТК с трубами диаметром 25 х 2 мм по ГОСТ15122-79; диаметр 1000 мм число труб в пучке 747 одноходовой с длиной труб 3 м вертикальный.
Безопасность и экологичность проекта
На промышленном предприятии приоритетными задачами являются обеспечение безопасности труда работников сохранность здоровья населения а также сохранение благоприятной окружающей среды на основе использования современных технологий. Четкое соблюдение требований промышленной безопасности и охраны труда всеми работниками предприятия играет ключевую роль в обеспечении безопасности.
Данный раздел посвящен основным аспектам промышленной безопасности на объектах повышенной опасности охране труда и обеспечению комплекса мер по охране окружающей среды.
1Безопасность проекта
1.1Анализ опасных и вредных производственных факторов на участке газофракционирования
Установка газофракционирования относится к пожаро- и взрывоопасным производствам.
Продуктами определяющими взрывоопасность установки будут углеводородные газы и пары бензина (фракция С5 и выше) которые горят а также в смеси с кислородом воздуха образуют смеси взрывающиеся при наличии огня или искры. Характеристика токсичности и взрывопожароопасности веществ применяемых на установке приведена в таблице 15 и таблице 16.
Возникает опасность выделения токсичных легковоспламеняющихся и взрывоопасных жидкостей и газов при нарушениях технологического режима процесса газофракционирования правил по охране труда при проведении ремонтов. Вследствие возникает и вероятность отравления обморожения обслуживающего персонала вероятность возникновения пожаров и взрывов.
Анализ опасных и вредных производственных факторов установки газофракционирования выполнен в соответствии с ГОСТ 12.0.003-2015 [16]. Результаты анализа представлены в таблице 17.
Таблица 15 - Характеристика токсичности веществ применяемых на установке [1516]
Агрегатное состояние
воздействия на организм
Меры и средства первой помощи
Оказывает наркотическое действие. Обладаетсвойством удушающего характера.
искусственное дыхание
Противогазы шланговыес принудительной подачей воздуха.
Пары бензина (фракция С5 и выше)
Вызываюттошноту головную боль раздражение кожи.
Вызываетрасстройство
органовдыханиякровообра-щения ЦНС печени.
Свежий воздух промывание глаз искусственное дыхание
Спец.одежда противогаз марки А или БКФ
Вызывает удушье вследствие недостатка кислорода
Свежий воздух глюкоза внутривенно
Специальные маски защитные очки
Сероводород с углеводородами
Вызывает головную боль головокружение.
Обильное промывание лица и открытых участков кожи водой
Противогазы изолирующие
ИП-5средства защиты кожи.
Таблица 16 - Характеристика взрывопожароопасных веществ применяемых на установке [15]
Параметры взрывопожароопасных свойств веществ
Температурные пределы воспламенения(взрываемости) °С
Склон-ностьк самовозгоранию
воспламенения (взрываемости)
В смеси с кислоро-дом воздуха
Сероводород с углеводородами
МЭА 15% водный раствор
Таблица 17 - Анализ опасных и вредных производственных факторов [15]
Наименование оборудования
Опасные и вредные производственные факторы
Характер воздействия
Фактическое значение факторов
Подвижные части производственного оборудования
Вращающийсявал насоса
При несоблюде-нии ТБ
Повышенный уровень шума нарабочем месте
Заболевания центральной нервной системы глухота
Работа электродвигателя насоса
Необходимо применение СИЗ
Повышенное значение напряжения в электрической цепи замыкание которой может произойти через тело человека
Питание электродви-гателя 4 кВ
Повышенный уровень статического электричества
Вращение ротора электродви-гателя.
Необходимо заземление
Повышенная загазованность
Отравления заболевания
Выделение УВД в зазоры фланц. соед-й 035-065мм
Потенциальная опасность разгерметизации
Повышенный уровень стат. электричества
Движение нефтипо трубопро-воду
Вытяжная вентиля-ция
Повышенный уровень шума
Вращающийся вентилятор вытяжной вентиляции
Продолжение таблицы 17
Наимено-вание оборудо-вания
Характер воздействия на организм
Повышенная загазован-ность
При разгерметизации оборудования
Приточная вентиляция
Повышенная подвижность воздуха.
Теплопотери организма
Принудительная подача воздуха для поддержания кратности воздухообме-на
При повышенной загазованности
Повышенная загазован-
При дренировании МЭА смывании загрязнений нефтепродукта с пола.
Недостаток естественного света
Закрытое помещение насосной (характер зрительных работ VIIIв)
Дополни-тельное освещение
Повышенная температура поверхности оборудования
Высокая температура греющей среды;
Необходима теплоизоляция
Движение нефтепродук-
Экстракториректиф. колонны
Высокая температура процесса
Наименование оборудо-вания
Повышенная загазован-ностьУВД сероводоро-дом
При разгермети-зации оборудования
Движение нефтепродук-тов
Воздушные холодильники
Движущиеся части вентиляторов
Вращающий-сявал вентилятора
При несоблю-дении правил ТБ
Работа электродвигателя вентилятора
1.2Общая характеристика опасности проектируемого производства
Согласно СанПиН 2.2.1.2.1.1.2555-09 производства по переработке нефти попутного нефтяного и природного газа относятся к I санитарному классу так как на предприятии будет перерабатывается углеводородное сырьё содержащее серу. Следовательно проектируемый нефтеперерабатывающий завод составной частью которого является установка ГФУ относится к I санитарному классу. В целях безопасности нефтеперерабатывающие заводы строят на расстоянии от населённых пунктов с учётом санитарного класса санитарной зоны предприятия. Санитарно-защитная зона для предприятия I класса 1000 метров [17].
Все здания установки ГФУ будут иметь несущие конструкции из железобетона с применением листовых и плиточных негорючих материалов которые по степени огнестойкости относятся к I степени.
Характеристика производственных помещений наружных установок и отдельных видов оборудования по пожаровзрывоопасности приведена в таблице 18.
Таблица 18 - Характеристика производственных помещений по взрывопожарной и пожарной опасности [18192021]
ипожарной опасности помещений по СП.12.13130-209
Класс взрывоопасной зоны по ГОСТ Р51330.9-99.ТР ФЗ№123
Класс помещения опасности поражения электрическим током согласно ПУЭ
Вид объекта по молниезащи-те согласно СО153-34.21.122-2003
Помещение операторной
Помещения без повышенной опасности
Специальные объекты представляю-щие опасность для непосредствен-ного окружения
Венткамера приточная
Помещения с повышенной опасностью
Воздушные конденсаторы холодильники
К категории А относятся помещения в которых обращаются горючие газы легковоспламеняющиеся жидкости с температурой вспышки не более 28°С в таком количестве что могут образовывать взрывоопасные парогазовоздушные смеси при воспламенении которых развивается расчетное избыточное давление взрыва в помещении превышающее 5 кПа и (или) вещества и материалы способные взрываться и гореть с водой кислородом воздуха или друг с другом в таком количестве что избыточное давление взрыва в помещении превышает 5 кПа.
К категории Д отнесено помещение в котором обращаются негорючие вещества и материалы в холодном состоянии.
К категории АН относятся установки если в них присутствуют горючие газы ЛВЖ с температурой вспышки не более 28°С вещества и материалы способные гореть при взаимодействии с водой кислородом воздуха или друг с другом.
Класс помещений насосной по степени опасности поражения людей электрическим током – помещения особоопасные. В таких помещениях присутствуют одновременно два условия повышенной опасности - токопроводящие железобетонные полы и возможность одновременного прикосновения человека к металлоконструкциям имеющих соединение с землёй и к металлическим кожухам электродвигателей. Вдобавок к этому в помещениях при утечке углеводородов через неплотности оборудования образовывается органическая среда.
По ГОСТ Р 51330.9-99 помещения насосных установки ГФУ относятся к взрывоопасными к 1-му классу взрывоопасной зоны. 1 класс подразумевает что при правильной и нормальной эксплуатации взрывоопасные смеси независимо от НПВ (нижний предел воспламенения) с воздухом не образуются а возможны только в результате нарушений и аварий. Наружная аппаратура относится к взрывоопасным зонам 2-го класса.
Помещение компрессорной и закрытой насосной по степени огнестойкости относятся ко II степени огнестойкости так как эти здания с несущими конструкциями из железобетона с применением листовых и плитных негорючих материалов в покрытиях которых допускается применение незащищённых стальных конструкций. [20]
Согласно СО 153-34.21.122-2003 предприятие относится к специальным объектам представляющим опасность для непосредственного окружения. [22]
1.3Организационные мероприятия по улучшению условий труда
Для организации работы по охране труда на проектируемом НПЗ создается служба охраны труда. За организацию охраны труда на предприятии несет ответственность руководитель предприятия. Но обычно полномочия передаются главному инженеру или его заместителю по вопросам безопасности труда.
Ответственность за соблюдение законодательства о труде правил и норм охраны труда пожарной безопасности в подчиненных им структурных подразделениях (отделах цехах участках) несут начальники этих подразделений. Выполнение работ по охране труда контролирует заместитель главного инженера подчиняющийся главному инженеру.
Обеспечение и контроль за безопасностью на технологических объектах НПЗ будут осуществлять службы: отдел главного технолога отдел главного механика отдел главного метролога отдел технического надзора отдел главного энергетика отдел главного теплотехника отдел защиты окружающей среды газоспасательный отряд.
Каждому кто становится работником на заводе необходимо пройти теоретическое и практическое обучение безопасным приемам и методам труда. [23].
Вводный инструктаж (при поступлении на работу) будет проводится работниками службы охраны труда газоспасательного отряда и пожарной части.
Первичный инструктаж будет проводится на рабочем месте начальником подразделения или его заместителем запись производится в личной карточке инструктажа. Работника будут знакомить с безопасными приемами и методами труда его рабочего места.
Периодические проверки знаний охраны труда будут проводится 1 раз в год.
Во всех производственных подразделениях на рабочих местах необходимо держать инструкции по охране труда пожарной и газовой безопасности. Каждая служба обязана иметь инструкции по безопасной эксплуатации соответствующего оборудования.
На проектируемом предприятии будет установлена рабочая неделя продолжительностью 40 часов продолжительностью смен 8 часов. В предпраздничные дни рабочий день сокращен на 1 час. Сверхурочные работы производятся в случаях предусмотренных законодательством.
Всем работникам завода будет предоставляется ежегодный отпуск с сохранением места работы и среднего заработка.
1.4Мероприятия по производственной безопасности
Безопасная работа установки будет зависеть от строгого соблюдения требований и правил охраны труда пожарной безопасности и соблюдения норм технологического режима а также от квалификации обслуживающего персонала.
Для предотвращения аварийных ситуаций аварий и создания надлежащих условий труда необходимо систематически следить за исправностью включения в работу приборов контроля и автоматики систем сигнализации и автоматических блокировок. В эксплуатации установки должна четко контролироваться работа предохранительных клапанов всех насосов и компрессоров должны немедленно устранятся пропуски торцевых уплотнений во фланцевых соединениях. Не допускается загазованность территории и помещений установки.
Во избежание ожогов необходимо поддерживать в исправности теплоизоляцию всех аппаратов и трубопроводов с температурой превышающей 60 °С.
Ремонтные и другие слесарные работы во взрывоопасных цехах необходимо проводить специальным неискрящим при ударах омеднённым инструментом.
В производственных помещениях необходимо обеспечивать исправность всех систем вентиляции и эксплуатацию их в соответствии с режимом утверждённым главным инженером завода.
Необходимо исключить попадание продуктов производства в обратную воду канализационные системы паровой конденсат. Сброс сточных вод в канализацию производится через гидрозатворы установленные на выходе из цеха.
Все движущиеся части машин и механизмов следует оградить и снабдить предупредительными плакатами.
С целью предупреждения преждевременного износа технологического оборудования и аварий а также поддержания в работоспособном состоянии оборудования всю аппаратуру подвергать текущему и среднему капитальному ремонту. Ремонт необходимо производить только при снятом напряжении с вывешиванием плакатов на пусковых кнопках: «не включать работают люди».
Аппараты и коммуникации перед подачей в них взрывоопасных продуктов необходимо продувать азотом.
Всё технологическое оборудование за исключением насосов будет размещено на открытой площадке что обеспечит более безопасную его работу.
Комплексная автоматизация производственных процессов включает в себя автоматический контроль и сигнализацию управление регулирование защиту и блокировку. Для защиты от поражения электрическим током и защиты от статического электричества необходимо применять:
Устройства защитного заземления и зануления электрооборудования автоматического отключения нетоковедущих металлических частей оборудования (кожухи насосов компрессоров электродвигателей воздушных холодильников);
Rзазем=2 Ом [21] Rизол=05 мОм [21]
Электрооборудование осветительная арматура в помещениях категории А необходимо установливать во взрывозащищённом исполнении;
Изолирующие электрозащитные средства для персонала обслуживающих электроустановки от поражения электрическим током;
Создать условия недоступности всех токоведущих частей;
К работе допускаются рабочие имеющие присвоенную квалификационную группу или наряд для производства работ;
Знаки безопасности – плакаты и надписи.
Проектируемоепроизводствовключаеттранспортированиенефтепродуктов установки газофракционирования что будет сопровождатся электризацией. Поэтому необходимо заземлить все оборудование (колонны емкости трубопроводы и т.д.).
Для отвода статического электричества накапливающегося на людях особенно при выполнении ручных операций (промывка чистка) необходимо использовать одежду из антисинтетических материалов время от времени снимать накопившийся заряд статического электричества становясь на заземлённые участки пола и браться за заземлённые перила или ограждения.
Удары молнии могут быть особо опасны для информационных систем систем управления контроля и электроснабжения. Для электронных устройств установленных в объектах разного назначения требуется специальная защита. Газофракционирующая установка относится к объектам представляющим опасность для непосредственного окружения. Отсюда следует необходимость применения молниезащиты.
Молниезащита будет представлять собой систему обеспечивающую перехват молнии и отвод её в землю тем самым защищая конструкции от повреждений и пожаров. В момент прямого удара молнии в объект молниезащитное устройство будет принимать на себя ток молнии и отводить его по токоотводам всистему заземления где энергия разряда безопасно рассеивается.
Далее представлен расчет молниезащиты ректификационной колонны установки ГФУ.
По карте территории Российской федерации по среднегодовой продолжительности гроз определяем среднегодовую грозовую деятельность. Газофракционирующая установка будет находиться на открытой площадке в местности с интенсивностью грозовой деятельности 20 – 40 часов в год.
Ожидаемое количество N поражений молнией в год для сосредоточенных сооружений (этановая колонна) не оборудованных молниезащитой вычисляют по формуле:
где h – наибольшая высота сооружения м;
n – среднегодовое число ударов молнии в 1 км2 земной поверхности в месте расположения сооружения [24].
Определяем h = 235 м; n = 2.
Подставляя эти значения в формулу (65) получим:
Исходя из значений требуемой надежности(P3=099) и высоты молниеотвода hм выбираем для защиты одиночный стержневой молниеотвод. [22].
Высоту одиночного стержневого молниеотвода находим по формуле:
где – радиус колонным;
Затем рассчитываем зону защиты создаваемую одностержневым молниеотводом. Стандартной зоной защиты одиночного стержневого молниеотвода высотой hм является круговой конус высотой h0 hм вершина которого совпадает с вертикальной осью молниеотвода Находим высоту конуса по формуле:
Радиус конуса по формуле:
Полуширина rx зоны защиты требуемой надежности на высоте hx от поверхности земли определяется выражением:
На уровне hx = 235 м от земли радиус горизонтального сечения на высоте защищаемого объекта rx = 125 м. При данных параметрах этановая колонна вписывается в зону защиты создаваемую одностержневым молниеотводом.
Одиночный стержневой молниеотвод будет состоять из стержневого молниеприемника установленного на колонне и токоотвода соединяющего молниеприемник с системой заземлителей. Стержневой молниеприемник – это стальной стержень высотой не менее 200 мм покрытый антикоррозийной краской. Токоотвод изготовлен из стали с сечением не менее 50 мм2. Заземлитель представляет собой стальной вертикальный стержень длиной 45-5 м.
На графическом листе 4 показана зона защиты одиночного стержневого молниеотвода высотой 263 м.
Для защиты зданий от вторичных проявлений молнии металлические корпуса насосов электродвигателей и компрессоров установленных в производственных помещениях присоединяют к заземляющему устройству [21222425].
Защита от заноса высокого потенциала по внешним наземным коммуникациям будет осуществлена путем их присоединения на вводе в здание к контуру заземления электроустановок.
ГФУ предусматривает защиту каждой колонны стержневым молниеотводом установленным на их корпусах.
Для защиты от молний зданий насосных предусмотрена установка на крыши зданий молниезащитной сетки.
1.5Производственная санитария
Категория выполняемых работ по тяжести на установке ГФУ для операторов и мастеров – IIа (физические работы средней тяжести).
В таблице 19 приводятся нормы температуры относительной влажности и скорости движения воздуха в рабочей зоне.
Таблица 19 - Оптимальные и допустимые нормы параметров микроклимата
Температура воздуха 0С
Относительная влажность %
Скорость движения воздуха мс
Работа технологического персонала будет связана с длительным пребыванием на холоде в зимнее время и на жаре в летнее время поэтому для персонала необходимо предусмотреть специально оборудованные помещения для периодического обогрева или охлаждения с определённым микроклиматом.
Центральная система водяного отопления будет поддерживать необходимую температуру микроклимата всех помещений проектируемого предприятия.
Температура нагрева поверхности радиаторов не должна превышать 75-80 0С вследствие чего не будет происходить подгорания пыли на поверхности батареи. А температура помещения операторной не будет превышать 14-200С что безопасно в противопожарном отношении.
Для нормализации воздушной среды в помещении будет делается приточная и вытяжная вентиляция которая предупреждает действие на людей токсических веществ образующихся на установке. Кроме этого необходимо осуществление естественной вентиляции. За счет ветрового потока за счёт разности температур и давления воздуха в помещении и вне его воздух будет поступать и удаляться из помещения через неплотности здания.
Согласно стандартов уровень шума при умственной работе точному графику с инструкцией (операторская) точной категории зрительных работ не должна превышать 80 дБА [26].
Для уменьшения звукового давления на ГФУ также будут предусмотрены определённые мероприятия:
разработка и применение шумобезопасной техники;
применение средств коллективной защиты – ограждение конструкций облицовка помещений звукопоглощающими материалами обустройство оборудования специальными кожухами;
для обслуживающего персонала предусмотрено дополнительное средство индивидуальной защиты – противошумовые наушники рекомендовано периодическое пребывание в зоне с пониженным уровнем шума.
Для ослабления шума и вибрации на оборудовании ГФУ необходимо прежде всего сокращать их в самом источнике образования. То есть прежде всего при монтаже фундаменты под оборудованием необходимо изготавливать заглубленным способом изолированным со всех сторон демпфирующими материалами (резину пластмассы пробку войлок и т. д.) обладающие высоким внутренним трением на преодоление которого расходуется энергия вибрации.
При монтаже оборудования необходимо точно соблюдать нормы и допуски в сочлененных деталях выполнять качественную центровку оборудования.
Для защиты рук работающих с вибрацией необходимо применять рукавицы со специальными вкладками или виброзащитными прокладками. А для защиты от вибрации передаваемой через ноги обувь со специальной подошвой. [27]
Работа на установке будет связана с напряжением зрения рабочих поэтому необходимо правильное и полное освещение рабочего места. Предусматриваем естественное и искусственное освещение.
В помещениях операторной насосной и помещении цеха естественное освещение (боковое двухстороннее) будет осуществляться через окна.
Искусственное освещение помещений операторной и насосной будет осуществляться светильниками с люминесцентными лампами. В здании операторной характеристика зрительной работы малой точности. Разряд зрительной работы - Vв. Нормативная освещенность на рабочей поверхности - 200 лк. К.Е.О.-3%. [28]
В помещениях насосных характеристика зрительной работы - средней точности. Разряд зрительных работ - IVв. Нормативная освещенность на рабочей поверхности - 100 лк. Система искусственного освещения общая. Необходимо применить взрывозащищенные светильники прямого света с люминесцентными лампами.
Расположение светильников предусмотрено с учётом площади проектируемого помещения на равном друг от друга расстоянии.
Проектом предусмотрено аварийное освещение. Оно предназначено для продолжения работы при аварийном отключении рабочего освещения. Оно создаёт освещённость на рабочих поверхностях равную 2лк. Светильники рабочего освещения и светильники освещения безопасности в производственных и общественных зданиях и на открытых пространствах должны питаться от независимых источников.
Лампы ДРЛ ДРИ ДРИЗ и ДНаТ прожекторы могут применяться для освещения открытых территорий. [28]
Установку ГФУ необходимо обеспечить соответствующими санитарно-бытовыми помещениями и устройствами. По СНиП 2.09.04-2001 установка относится к группе производственных процессов 3б. Санитарная характеристика процесса: процессы вызывающие загрязнение веществами 1-го и 2-го классов опасности а также веществами обладающими стойким запахом (тела и одежды). Что подразумевает организацию душевых гардеробных и специальных бытовых помещений:
- Расчетное число человек:
на одну душевую – 3;
- Тип гардеробных число отделений шкафа на 1-го человека: раздельные по одному отделению.
- Специальные бытовые помещения и устройства: химчистка искусственная вентиляция мест хранения специальной одежды.
Стены и перегородки гардеробных спецодежды душевых преддушевых умывальных уборных помещений для сушки обеспыливания и обезвреживания спецодежды должны быть выполнены на высоту 2 м из материалов допускающих их мытье горячей водой с применением моющих средств. Стены и перегородки указанных помещений выше отметки 2 м а также потолки должны иметь водостойкое покрытие. [29]
Проектом предусмотрена своя система водоснабжения НПЗ которая обеспечивает горячей и холодной водой установки и хозяйственно – питьевой водопровод.
Питьевая вода будет поступать через систему фильтров расположенных на водопроводе бытового водоснабжения. Также в зданиях будут установлены бойлерные установки с чистой питьевой водой. Питьевые точки будут располагаться на расстоянии не более 75 метров от установки.
Противопожарный водопровод будет устроен по объединённой схеме с производственным водопроводом [30].
На проектируемом заводе также необходимо предусмотреть столовую буфет кухню. Все эти помещения будут находиться в здании заводоуправлении и иметь дневной режим работы. Помимо столовых и буфетов в цехах будут оборудованы комнаты для приема пищи.
В соответствии с ТК РФ Статья 221 на работах с вредными и (или) опасными условиями труда а также на работах выполняемых в особых температурных условиях или связанных с загрязнением работникам бесплатно выдается специальная одежда специальная обувь и другие средства индивидуальной защиты а также смывающие и (или) обезвреживающие средства.
Для защиты кожи рук и тела обслуживающего персонала от механических повреждений термических и химических ожогов от вредных действий нефтепродуктов обслуживающий персонал установки необходимо снабжать по установленным нормам спецодеждой защитными очками и рукавицами. Во время работы рабочим необходимо находиться в установленной для них спецодежде и спецобуви. Работать в открытой обуви (босоножки сандалии) запрещается.
1.6Пожарная безопасность
Пожарная безопасность предприятия должна обеспечиваться системами предотвращения пожара и противопожарной защиты в том числе организационно-техническими мероприятиями.
На предприятии будет располагаться пожарная часть которая будет оснащена пожарными машинами и всем необходимым специальным оборудованием.
На установке проектом предусмотрен монтаж автоматической установки (системы) пенного пожаротушения предназначенные для локализации или тушения пожара и одновременно выполняющие функции автоматической пожарной сигнализации. Станции пенного пожаротушение справляются с огнем за короткий промежуток времени не позволяя ему распространиться. При этом данная система весьма проста для монтажа. [31]
Основным средством пожарной сигнализации в помещении насосных будет извещатель пожарный комбинированный который предназначен для обнаружения загораний в помещениях с взрывоопасной средой всех категорий по взрывной и пожарной опасности различных производственных административных и других объектов включая склады и помещения для переработки или хранения нефтепродуктов сжиженного газа и прочего.
Также необходимо установить пожарные извещатели ручного действия. Наружная противопожарная водопроводная сеть будет расположена вдоль дорог на расстоянии 5 м от установки через каждые 100 м будут размещены пожарные гидранты к которым можно присоединить пожарные рукава.
В операторные пожарные краны устанавливают на высоте 135 м от пола на лестничных клетках у входов в коридорах. Рядом с ними будет расположен шкаф с пожарным рукавом.
В качестве первичных средств пожаротушения предусматриваются огнетушители. Для больших коммерческих и производственных помещений необходимы водоэмульсионные (ОВЭ) или другие гасители с емкостью от 25 л.
Выбираем огнетушители ОВЭ – 5 ОВП – 10 и ОУ – 5. Их необходимо разместить на расстоянии не менее 12 м от проёма двери и на стенах (посредством специальных креплений-кронштейнов) и в пожарных шкафах совместно с пожарными рукавами на высоте не более 15 м от уровня пола [31-35].
2Экологичность проекта
2.1Охрана атмосферного воздуха
Источники вредных выбросов в атмосферу на нефтеперерабатывающем заводе - резервуары с нефтью и нефтепродуктами очистные сооружения технологические установки. Главными же источниками загрязнения атмосферы в результате нефтеперерабатывающей промышленности являются организованные источники (дымовые трубы) и неорганизованные источники (выбросы с установок за счет не герметичности аппаратов оборудования от резервуарных парков очистных сооружений). Основными вредными веществами выбрасываемыми в атмосферу будут являться углеводороды сероводород окись углерода аммиак фенол окислы азота окислы серы нефтяные кислоты.
Загрязнение атмосферного воздуха происходит на всех этапах технологического процесса переработки нефти и ее компонентов. На технологических установках имеются как неорганизованные так и организованные источники выбросов. Причиной выделения в атмосферу углеводородов сероводорода аммиака фенолов является несовершенство технологического процесса. Вредные вещества выделяются через неплотности в насосно-компрессорном оборудовании и арматуре из открытых лотков незакрытых воздушников отдельных аппаратов.
Характеристика источников загрязнения атмосферного воздуха приведена в таблице 20.
Таблица 20 – Источники загрязнения атмосферного воздуха и их характеристика [34]
Уд. норма выброса на ед. сырья
Количество выбросов по видам
Условия ликвидации обезврежива-ния утилизации
Периоди-чность выбросов
Установ-ленная норма содержа-ния загрязне-ний в выбросах
Вентиляционные выбросы из закрытой насосной реагентов
Воздух с примесью углеводородов
не предусматри-вается
Углеводо-роды до 1000 мгм3
Вентиляционные выбросы из закрытой насосной
Неорганизованные выбросы (продувка аппаратов утечки через неплотности и пр.)
Углеводоро-дные газы
Продувка аппаратов при подготовке к ремонту
Инертный газ с примесью углеводоро-дов 2000м3ч
Периоди-чески 1 раз в год
Углеводо-родные газы 100 мгм3
Для защиты атмосферного воздуха в проекте установки предусмотрены следующие мероприятия:
сброс от предохранительных клапанов будет осуществляется в закрытую систему на факел;
работу всех открытых аппаратов производить под подушкой азота или углеводородного газа со сбросом в факельную линию;
исключить все постоянные выбросы продуктов на факел и в атмосферу за счет герметизации оборудования и насосов;
технологический процесс необходимо осуществлять в герметически закрытой аппаратуре под избыточным давлением;
дымовые газы будут удаляться через дымовую трубу высота которой равна 180 метров и обеспечивает должное рассеивание SО2 в атмосфере в соответствии с санитарными нормами [1536].
На предприятии предусмотрен монтаж факельной установки основная задача которой предотвращение попадания газа в атмосферу за счет его сжигания. Газы и пары которые попадают в факельную систему могут поступать в нее из технологических установок от предохранительных клапанов в аварийных ситуациях. Также в процессе возможно постоянное образование газов и паров которые по технологии отводятся в факел для сжигания. Сжигание сбрасываемых газов на факельных установках позволяет сильно уменьшить загрязнение атмосферы токсичными и горючими веществами. По технологии налива сжиженных газов необходимо периодически сбрасывать давление газов с наливных рукавов цистерн и сжигать поскольку утилизировать их нецелесообразно. Сбрасываемые газы будут направлять через сепаратор и гидрозатвор на сжигание в факельную трубу. Конденсат из сепаратора будут возвращать в производство или сливать в канализацию. Факельная труба оснащается 4 дежурными горелками.
2.2Охрана и рациональное использование водных ресурсов
Отходы нефтеперерабатывающего завода попадая в водную среду отрицательно влияют на качество воды и санитарные условия жизни и водопользования населения. Это вызвано особенностями поведения веществ сбрасываемых вместе со сточными водами нефтеперерабатывающего завода в водоемы и прежде всего нефти. Обычно стоки НПЗ содержат в себе такие вещества как: нефтепродукты масла парафины жирные кислоты сульфаты ПАВ фенол карбамид циклические органические углеводороды аммонииные ионы и др. В настоящее время на основании анализа фактических данных базового предприятия установлено что количество улавливаемых нефтепродуктов находится в пределе от 06 до 15 % от перерабатываемой нефти. Загрязнение водных ресурсов нефтепродуктами приводит к значительным изменениям условий для жизнедеятельности организмов заселяющих верхние горизонты воды. О том как влияют нефтяные загрязнения на гидросферу известно еще недостаточно. Общее воздействие нефтепродуктов на состояние водных организмов - это:
прямое отравление организмов с летальным исходом;
опасные нарушения физиологической активности организмов;
прямое окутывание птиц и морских животных нефтепродуктами;
болезненные изменения в водных организмах возбужденные введением углеводородов;
изменение химических биологических и биохимических свойств среды обитания для организмов.
Характеристика сточных вод с установки ГФУ приводится в таблице 21.
Таблица 21– Характеристика сточных вод установки газофракционирования [15]
Условие(метод) ликвидации обезвреживания утилизации
Периодичность сбросов
Установленная норма содержания загрязненийв стоках мгл
Утечка эмульсионной воды от насосов Н-7÷Н-32
Отводятсяна очистные сооружения
Всеть промлив-невой канализации
Сброс с аппаратов захолаживания пара
Отводятсяна сооружения механической затем биохимической очистки
Сброс воды после промывкии пропарки аппаратуры
раз в год при подготовке аппаратовк ремонту
Сточные воды с установки газофракционирования будут направляться на биологические очистные сооружения сточных вод проектируемого НПЗ.
Технологическая схема механической очистки сточных вод будет состоять из решеток и песколовок отстойников и нефтеловушек. Химическая очистка предполагает нейтрализацию а очистка вод от фенола производится на экстракционных установках.
Полная биологическая очистка будет проходить в бассейнах с большими размерами в которых токсичные вещества окисляются подобно естественным водоемам [36].
2.3Утилизация отходов охрана почв от загрязнения
В настоящее время в условиях нарастающего антропогенного воздействия над подавляющим количеством НПЗ нависла трудная проблема загрязненности грунтов нефтепродуктами. Загрязнение почв и грунтов нефтью и продуктами ее переработки вызывают сильные иногда необратимые повреждения природных экосистем. Углеводороды при попадании в зоны низкой плотности и аэрации пермещаются вплоть до водоносных горизонтов.
На проектируемом НПЗ может накапливаться такой углеводород как бензапирен-12. Он считается одним из достаточно сильных канцерогенов и опасен для человека даже небольшой концентрации. Загрязнение почвы нефтепродуктами в том числе и бензапиреном может негативно сказываться на экологической обстановке близких к НПЗ территорий. Для восстановления плодородия нарушенных земель предлагается применять рекультивацию земель. Предварительно проводят техническую рекультивацию в которой используются сорбенты. Затем проводится биологическая рекультивация. Техническая рекультивация земель должна осуществляться предприятием осуществляющим производственную деятельность. [37]
Характеристика отходов с установки газофракционирования продемонстрирована в таблице 22.
Таблица 22 – Характеристика отходов установки газофракционирования [36]
Место складирования транспорт
Условия (метод) и место захоронения обезвреживание утилизация
Отработанный раствор щелочи
Коллектор сернисто-щелочных стоков
По мере снижения концентрации
На механическую очистку на очистные сооружения НПЗ
Обтирочный материал загрязненный нефтепродуктами
Металлические контейнеры
При техническом обслуживания насосов
Термическое обезвреживание на установке «Факел»
Отработанная щёлочь применяемая для защелачивания сжиженных газов по коллектору сернисто-щелочных стоков будет поступать на механическую очистку на очистные сооружения.
Твердые и жидкие остатки необходимо складировать в преднамеренно отведенных местах и периодично утилизировать [36].
Также ценной составляющей является благоустройство и озеленение территории НПЗ с целью сохранения и санирования среды окружающей человека на производстве сохранение здоровья рабочих организация условий положительно влияющих на психофизиологическое самочувствие человека.
Площадь озеленяемых участков определяется из расчёта не менее 3 м2 на одного работающего но наибольший размер участков не должен быть выше 15 % от площади завода. Главными субъектами озеленения будут газон и локальные виды древесно – кустарниковых лесонасаждений.
Пешеходные дорожки предусматриваются по длине всех магистральных и производственных дорог свободно от интенсивности пешеходного движения. [38]
Эффективность инвестиций
1Режим работы цеха эффективный фонд работы оборудования
Режим работы газофракционирующей установки характеризуется непрерывной рабочей неделей числом смен в сутки и продолжительностью рабочей смены в часах.
Календарный фонд времени (Тк) равен количеству календарных дней в плановом периоде. Тк=365 дней или 365*24=8760 часов.
Номинальный фонд времени (Тн) равен числу дней работы оборудования в зависимости от установленного режима производства без учёта простоев оборудования в ремонтах и регламентированных остановок.
Эффективный фонд времени (Тэф) равен разнице между Тн и временем простоя оборудования в ремонтах (Трем) находим по формуле:
При непрерывном технологическом процессе Тн = Тк.
Продолжительность простоя оборудования в ремонтах определяется по нормативам [3940].
В непрерывных производствах Тн зависит от продолжительности рабочей недели количества смен в сутки и их продолжительность.
Продолжительность простоя оборудования в ремонтах определяется по нормативам. Время простоя оборудования в ремонтах находят суммированием произведений количества ремонта на время простоя по каждому виду ремонта.
Номинальный фонд времени () равен числу дней работы оборудования в зависимости от установленного режима производства без учета простоев оборудования в ремонтах и регламентированных остановок принимаем номинальный фонд времени равным календарному.
Ремонтный цикл – 365 дней.
Количество капитальных ремонтов – 1.
Время простоя в капитальном ремонте – 7 день.
Время работы оборудования между средними ремонтами – 91 дней.
Время простоя в среднем ремонте – 4 дня.
Время работы оборудования между текущими ремонтами – 40 дней.
Время простоя в текущем ремонте – 1 день.
Количество средних ремонтов Рср = 365 91 – 1 = 4 – 1 = 3.
Время простоя в средних ремонтах: 3 * 1 = 3дн = 72 часа.
Количество текущих ремонтов Ртек = 365 40 – 3 – 1 = 5.
Время простоя в текущих ремонтах: 1 * 5 = 5дн = 120 часов.
Время простоя в капитальных ремонтах: Рк = 7*1 = 7 дн = 168 часов.
Подставляя эти значения в формулу (2) получим:
= Рк + Рср + Рт (72)
где Рк – капитальный ремонт.
= 7+ 3 + 5 = 15 дней = 360 часов.
Итоги расчёта заносим в таблицу 23.
Таблица 23 - Баланс рабочего времени оборудования
Календарный фонд времени
Выходные праздничные дни
Номинальный фонд времени
Простои оборудования
Технические остановки
Итого простои в ремонтах
Эффективный фонд времени
Объём производства указан в задании на дипломное проектирование и равен 690 тыс. т. в год.
Задачей является подтвердить возможность выпуска заданного объёма продукции выбранным в технологическом проекте оборудованием.
Производственную мощность предприятия рассчитываем:
где М – производственная мощность цеха (предприятия) в натуральных единицах
Пр – часовая производительность ведущего оборудования
Тэф – эффективный фонд времени оборудования табл.23
К – количество единиц ведущего оборудования.
Исходя из формулы (73) определяем:
М =82148400=690000 т
2Расчёт стоимости основных производственных фондов
2.1Расчёт стоимости зданий и сооружений
Единовременные затраты (капитальные вложения) включают в себя стоимость строительства необходимых зданий и сооружений а также затраты на закупку поставку и монтаж оборудования. Расчет сводится в таблицы 24 -27.
Таблица 24 - Нормативы стоимости строительства тыс. руб. за 1 м3.
Объём здания тыс. м3.
Промышленные здания:
В данном производстве:
насосные – одноэтажные: объем 90х20х10 м – 18000 м3;
стоимость строительства промышленных зданий 09 тыс. руб. за 1 м3 – 16200 тыс. руб.
операторная – двухэтажная: объем 40х20х10 м – 8000 м3;
стоимость строительства промышленных зданий 13 тыс. руб. за 1 м3 – 10400 тыс. руб.
Стоимость сооружений и передаточных устройств примем в размере 35 % от стоимости зданий.
Таблица 25 – Затраты на строительство зданий и сооружений
Наименование строения
Сооружения и передаточные устройства
2.2Расчёт стоимости технологического оборудования транспортных средств инструмента и инвентаря
Для расчёта стоимости технологического оборудования по технологии производства выбирается только основное технологическое оборудование. Прочее мелкое технологическое оборудование (фильтры смесители и т. д.) отдельно не рассчитывается и принимаем его стоимость в размере 20 % от стоимости основного оборудования.
Дополнительно к стоимости оборудования добавляют транспортные расходы (на перевозку разгрузку хранения на складе) которые принимаем в размере 20 % от стоимости оборудования согласно указаниям.
Расчёт стоимости оборудования сводится в таблице 26.
Таблица 26 – Полная стоимость технологического оборудования
I. Основное технологическое оборудование:
Установка ЛК-6 УС ГФУ секция 400
деэтанизатор - корпус
изобутановая колонна
холодильник-конденсатор
аммиачный холодильник-конденсатор
насос с эл.двигателем
II. Прочее оборудование (20 % от стоимости основного технологического оборудования)
III. Транспортные монтажные спецработы (20 % от общей стоимости технологического оборудования)
IV.Всего: полная стоимость технологического оборудования
ИТОГО п. I + п. II + п. III
После этих расчётов определяем итоговую стоимость основных фондов цеха и амортизационные отчисления.
Стоимость инструмента и инвентаря отдельно не рассчитывают а принимаем в размере 1 % от полной стоимости оборудования (таблица 26).
Стоимость транспортных средств принимаем в размере 10% от полной стоимости технологического оборудования (таблица 26).
Расчёт суммы амортизационных отчислений проводится по нормам приведённым в приложении по формуле:
где А – годовая сумма амортизационных отчислений по каждой группе основных фондов тыс. руб;
Ф – стоимость соответствующих основных фондов тыс. руб;
На – норма амортизационных отчислений %.
Итоги расчетов заносим в таблицу 27.
Таблица 27 – Амортизация основных фондов
Группы основных фондов
Стоимость основных фондов тыс.руб.
Сумма аморт. отчислений тыс. руб.
Технологическое оборудование
Транспортные средства
Инструменты и инвентарь
3Расчёт текущих затрат
3.1Расчёт численности персонала
В текущем разделе приводится расчёт численности персонала по категориям: рабочие руководители технические исполнители специалисты.
Категория «рабочие» подразделяется на три подгруппы: основные вспомогательные прочие.
Основные рабочие обеспечивают основной технологический процесс (выпуск продукции) и работают по графику принятого технологического режима – непрерывный.
Обеспечение обслуживания основного технологического процесса лежит на вспомогательных рабочих. Они подразделяются на две группы: дежурные и ремонтные.
Дежурный персонал работает вместе с основными рабочими по такому же графику. Так как технологический режим непрерывен они работают по графикам сменности.
Ремонтные рабочие работают в одну смену независимо от технологического режима (прерывный график).
Прочие рабочие выполняют различные подсобные функции и работают как правило по прерывному графику.
Для расчёта численности рабочих необходимо составить график сменности (для непрерывного режима работы) и годовой баланс рабочего времени одного рабочего. Исходными данными для баланса являются: технологический режим (непрерывный) количество рабочих смен количество планируемых невыходов (по данным базового предприятия). [4142]
В непрерывном производстве в зависимости от условий труда применяются 4-х бригадные графики работы (нормальные и вредные условия труда) и 5-ти бригадные графики - (особо вредные условия труда).
-х бригадный график работы.
Режим работы рабочих – непрерывный (круглосуточный).
Условия труда – вредные и тяжёлые.
Сменооборот – 12 дней.
Условное обозначение бригад: А Б В Г.
Таблица 28 – Четырех бригадный график
Число выходов за сменооборот – 9 число выходных – 3.
Количество сменооборотов за год:
Количество выходных за год:
Далее составляем годовой баланс рабочего времени одного рабочего. Данные заносим в таблицу 29.
Таблица 29 – Примерный годовой баланс рабочего времени одного рабочего
-ти дневная рабочая неделя
Календарный фонд времени дни
Номинальный фонд времени дни
I. Планируемые невыходы:
Очередные и дополнительные отпуска дни
II. Эффективный фонд времени дни
III. Продолжительность рабочей смены часы
IV. Эффективный фонд времени часы
Для учёта рабочих находящихся в отпусках отсутствующих по болезни и другим разрешённым законом причинам необходимо рассчитать коэффициент резерва.
где Тном – номинальный годовой фонд времени рабочего дни
Тэф – эффективный годовой фонд времени рабочего дни.
Согласно таблице 29:
Таблица 30 – Расчёт численности рабочих
Число рабочих в смену
Явочное число рабочих в смену
Штатная числен-ность чел.
Списочная численность чел
Старший оператор технологических установок
Оператор технологических установок
II. Вспомогательные рабочие
Машинист технологических насосов
Дежурный персоналом выступают рабочие по уходу и надзору за технологическим оборудованием. Они работают по графику сменности как основные производственные рабочие. По прерывному режиму в одну смену работает ремонтный персонал – это рабочие для текущего ремонта технологического оборудования.
3.2Расчет фондов заработной платы персонала
Расчёт фондов зарплаты рабочих считается раздельно по каждой группе рабочих. Связано это с тем что зарплата каждой группы присутствует в разные статьи калькуляции себестоимости продукции.
Тарифные ставки рабочих их списочный состав и эффективный фонд времени являются основой для расчета.
Из таблицы 30 переносим списочный состав. На основе часовых тарифных ставок базового предприятия принимаем часовые тарифные ставки. Эффективный фонд времени одного рабочего берем из таблицы 29. Фонд всех рабочих высчитываем произведением графы 4 на графу 2 а тарифный фонд зарплаты получаем произведением графы 3 на графу 5.
Таблица 31 – Расчёт тарифного фонда зарплаты рабочих
Наименование профессии
Часовая тарифная ставка руб.
Эффективный фонд времени часы
Тарифный фонд зарплаты тыс. руб.
Определяем годовой фонд заработной платы рабочих после расчёта тарифного фонда зарплаты. Результаты расчётов заносим в таблицу 32.
Доплаты к тарифу складываются из:
-премий (15 %) и доплат за:
За работу в вечернее и ночное время.
Доплаты предусматриваются лишь для рабочих работающих по графикам сменности (непрерывный режим). За работу в вечернее время доплаты составят 20% от часовой тарифной ставки рабочего за каждый час работы в вечернее время. Доплаты за работу в ночное время - 40% в соответствии. Итого доплаты в среднем за сутки (за год) составят:
Работу в праздничные дни (2 %). Только для рабочих работающих по непрерывному графику.
Профессиональное мастерство.
Совмещение профессий.
Начальство бригадой неосвобождённым бригадирам.
Сумму доплат по пунктам 3 – 6 принимаем в размере 10 %. Общую сумму доплат проставляем в графу 3. Графу 4 получаем умножением графы 2 на графу 3. Графу 5 рассчитываем суммированием графы 2 и графы 4.
Из оплаты перерывов кормящим матерям и доплат подросткам за неполный рабочий день также складываются доплаты к часовому фонду. Доплаты принимаем равными 1 %. Графу 7 находим произведением графы 5 на графу 6 а графу 8 - суммируя графы 5 и 7.
Доплаты к дневному фонду складываются из:
оплаты очередных и дополнительных отпусков.
оплаты учебных отпусков.
оплаты за время исполнения государственных обязанностей.
оплаты за время нахождения на курсах повышения квалификации с отрывом от производства.
Выплат выходных пособий. Вознаграждений за выслугу лет.
Доплаты по пунктам 1-4 составляют:
где О1 О2 О3 О4 – число дней отпуска по пунктам 1-4
Тэф – эффективный фонд времени дни.
В графу 9 проставляем общий процент доплат к дневному фонду зарплаты. Графу 10 определяем с помощью произведения графы 8 на графу 9. Графу 11 находим суммой графы 8 и графы 10. Графа 12 вычисляется произведением графы 11 на значение районного коэффициента по заработной плате. Для г. Ачинск он составляет: РК = 30% Северные надбавки – 30%. Итого общие надбавки по РК будут равны 60% (общий РК = 16).
Таблица 32 - Расчёт годового фонда зарплаты рабочих
Тарифный фонд тыс.руб.
Часовой фонд тыс.руб.
Доплаты к часовому фонду
Дневной фонд тыс.руб.
Доплаты к дневному фонду
Годовой фонд тыс.руб.
Годовой фонд с учетом РК тыс.руб.
Исходя из типовых схем управления цехом с учётом их совершенствования рассчитывают цеховой персонал. Расчёт фонда зарплаты цехового персонала производят на основе схемы должностных окладов.
Таблица 33 - Расчёт фонда зарплаты цехового персонала
Должностной оклад руб.
Доплата за вредность руб.
Годовой фонд зарплаты тыс. руб.
Годовой фонд с учётом РК тыс. руб.
Начальник установки
Старший механик установки
Технические исполнители
3.3Планирование себестоимости продукции
В данном разделе производится расчёт цеховой и полной себестоимости продукции.
Расчёт общезаводских и внепроизводственных расходов производится по укрупнённым нормативам.
Смета расходов по содержанию и эксплуатации оборудования представлена в таблице 34.
Таблица 34 - Смета расходов по содержанию и эксплуатации оборудования
Сумма расходов тыс. руб.
Содержание оборудования и других рабочих мест
а) зарплата дежурного персонала
б) единый социальный налог (ЕСН)
в) смазочные и обтирочные материалы
г) услуги мастерских
Текущий ремонт оборудования
а) зарплата ремонтного персонала
в) материалы для ремонта
% от ст. 4 табл. 2.3
г) услуги вспомогательных цехов
Амортизация оборудования и других активных фондов
Ст. 3 4 5 табл. 2.4 гр.4
Содержание транспорта и расходы по его эксплуатации
% от ст. 4 табл. 2.4 гр.2
Износ малоценного инвентаря
% от ст. 5 табл. 2.4 гр.2
Таблица 35 - Смета цеховых расходов
Сумма расходов тыс.руб.
Содержание цехового персонала
а) Зарплата цехового персонала
II. Содержание здания цеха и сооружений
% ст.1-2 табл.2.4 гр.2
III. Текущий ремонт зданий и сооружений
IV. Амортизация здания цеха и сооружений
Ст.1-2 табл.2.4 гр.4
V. Расходы по охране труда и ТБ
% от зарплаты всех рабочих
VII. Прочие цеховые расходы
Поскольку отдельно не рассчитывалась стоимость основных фондов всего предприятия численность персонала заводоуправления и других подразделений а также другие общепроизводственные расходы величину общезаводских расходов можно принять в размере 15% от цеховой себестоимости а внепроизводственных – 3% от производственной себестоимости. Результаты расчета вносим в таблицу 36.
3.4Расчёт себестоимости продукции
Объем товарной продукции рассчитываем в условных единицах так как а установке газофракционирования из исходного сырья получается несколько видов продукции.
Объём производства:
продукта 1- пропана составляет 1490398 т (цена 15000 руб.)
продукта 2- фракции н-бутана 227714 т (цена 13450 руб.)
продукта3-газа углеводородного сжиженного топливного для коммунально-бытового потребления 4485409 т (цена 15300 руб.).
За условную единицу примем продукт 2. По каждому виду продукции определяем переводные (калькуляционные) коэффициенты как отношение оптовой цены продукта к цене продукта 2 принятого за единицу.
После этого определяем объём производства каждого вида продукта в условных единицах как произведение количества продукции в натуральных единицах на переводной коэффициент. Общий объём товарной продукции в условных единицах находим суммированием всех видов продукции в условных единицах.
Объём товарной продукции в условных единицах составит:
Калькуляционная единица: 1 тонна.
Годовой выпуск: 445772239 т. в условных единицах.
Цена: 13450 тыс. руб.
Таблица 36 - Калькуляция себестоимости продукции
Расходы на весь выпуск
А. Сырьё и основные материалы
Нестабильные головки С-100АТС-200
Б. Вспомогательные материалы:
В. Энергия пар вода топливо на технологические цели
Продолжение таблицы 36
Зарплата основных рабочих
Расходы по содержанию и эксплуатации оборудования
Цеховая себе-стоимость
Общезаводские расходы
ИТОГО производственная себестоимость
Внепроизводственные расходы
ИТОГО полная себестоимость
3.5Планирование прибыли
Условно принимают что остатки готовой продукции на складе на начало и конец месяца равны тогда объём реализованной продукции будет равен величине товарной продукции рассчитанной в производственной программе.
Таблица 37 - Расчёт прибыли от реализации продукции
Наименование продукции
Реализуемая продукция
По полной себестоимости
Коли-чество тонн в год
Себесто-имость единицы руб.
Газы углеводородные сжиженные топливные для коммунально-бытового потребления
Для определения уровня рентабельности производства необходимо знать стоимость основных фондов всего предприятия и общий норматив оборотных средств. Для этого к стоимости основных фондов цеха прибавляют стоимость фондов предприятия которые принимаем в размере 150 % от стоимости фондов цеха (таблица 27). Оборотные средства принимаем в размере 5 % от полной стоимости основных фондов. Внепроизводственные расходы принимаем в размере 13% от производственной стоимости (таблица 36).
Определяем рентабельность производственных фондов:
где Пр – прибыль от реализации тыс. руб.;
Фо – стоимость основных фондов тыс. руб.;
Ос – стоимость оборотных средств тыс. руб.
Рассчитываем фондоотдачу по формуле:
где РП – реализованная продукция тыс. руб.
Фо – стоимость основных фондов предпрятия тыс. руб.
Определяем производительность труда по формуле:
Ч – общая численность персонала чел.
Рассчитываем затраты на рубль товарной (реализованной) продукции:
где С – полная себестоимость продукции тыс. руб.
РП – реализованная продукция тыс. руб.
Определяем срок окупаемости предприятия:
где Фо – полная стоимость основных фондов тыс. руб.
Пр – прибыль от реализации продукции за вычетом налога на прибыль (20%)тыс.руб.
Чистая прибыль составит 1992509104 тыс. рублей.
После расчёта показателей эффективности составляем общую таблицу показателей. В таблице 38 представлены основные экономические показатели.
Таблица 38 – Основные экономические показатели
Годовой выпуск продукции:
а) в натуральном измерении тонн
б) в денежном измерении тыс. руб.
Численность персонала:
Себестоимость единицы продукции руб.
Себестоимость годового выпуска тыс.руб.
Затраты на рубль товарной продукции руб.
Прибыль от реализации тыс.руб.
Рентабельность производства %
Срок окупаемости предприятия лет
В ходе дипломного проекта на основании свойств северо-варьеганской нефти была разработана установка газофракционирования производительностью 690 тыс. тонн в год.
В процессе расчета был составлен материальный баланс предприятия по топливному варианту с глубокой переработкой нефти. Также представлена технологическая схема установки рассчитано основное технологическое оборудование (этановая колонна). Подобрано вспомогательное обоудование (кипятильник и подогреватель).
Дипломный проект содержит раздел безопасность и экологичность в рамках которого рассматривается анализ вредных производственных факторов и приводится расчет и схема молниезащиты для этановой колонны.
Выполнен раздел эффективности инвестиций в котором были расчитаны основные технико-экономические показатели установки: рентабельность установки составила 2322% фондоотдача составила 0709 рубруб срок окупаемости предприятия 489 лет.
Список использованных источников
Поляков Б.В. Разработка поточной технологической схемы и материального баланса НПЗ и НХЗ на базе нефтей Западной Сибири. Учебное пособие по курсовому проектированию Поляков Б.В Н.В. Андриевская; Сибирский государственный технологический университет. – Красноярск: СибГТУ 2016. - 88 с. – Текст: непосредственный.
Кузнецов А. А. Расчеты основных процессов и аппаратов переработки углеводородных газов. Справочное пособие. А.А. Кузнецов Е.Н. Судаков – Москва; Химия 1983. - 224 с. – Текст: непосредственный.
Общий курс процессов и аппаратов химической технологии: учебник для вузов В. Г. Айнштейн М.К. Захаров Г.А. Носов [и др.] ; ред. В. Г. Айнштейн. - Москва: Логос: Высшая школа 2003 – 1758 с.
Ахметов С.А. Технология глубокой переработки нефти и газа С.А. Ахметов - Москва: Химия 2002. -672 с.
Бекиров Т. М. Промысловая и заводская обработка природных и нефтяных газов. Т.М. Бекиров – Москва: Недра 1980. -293 с.
Технология и оборудование процессов переработки нефти и газа С. А. Ахметов Т. П. Сериков И. Р. Кузеев М. И. Баязитов; под ред. С. А. Ахметова. – Санкт – Петербург; Недра 2006. - 871 с.
Смидович Е.В. Технология переработки нефти и газа. Часть 2. Крекинг нефтяного сырья и переработка углеводородных газов. 3-е изд. пер. и доп. Е.В. Смидович. - Москва: Химия 1980. - 328 с.
Справочник нефтепереработчика: Справочник под ред. Г. А. Ластовкина Е. Д. Радченко М. Г. Рудина. -Л.: Химия 1986. -648 с.
Чернышев А. К. Сборник номограмм для химико-технологических расчетов. А.К. Чернышев К.Л. Поплавский Н.Д. Заичко - Л.: Химия 1969. - 279 с.
Лащинский А.А. Конструирование сварных химических аппаратов А.А. Лащинский; под ред. А.Р.Толчинского. Л. 1981. - 385 с.
ГОСТ 12.1.005-88 ССБТ Общие санитарно-гигиенические требования к воздуху рабочей зоны = General sanitary requirements for working zone air : межгосударственный стандарт : издание официальное : утвержден и введен в действие Постановлением Государственного комитета СССР по стандартам от 29.09.88 N 3388 : взамен ГОСТ 12.1.005-76 : дата введения 1989-01-01 разработан Министерством здравоохранения СССР Всесоюзным Центральным Советом Профессиональных Союзов. – Москва: Стандартинформ 2008. – Текст: непосредственный.
СанПиН 2.2.12.1.1.1200-03 Санитарно-защитные зоны и санитарная классификация предприятий сооружений и иных объектов = : государственные санитарно-эпидемиологические правила и нормативы: утверждены и введены в действие постановлением Главного государственного санитарного врача Российской Федерации от 25 сентября 2007 г. № 74 опубликованы в Российской газете 9 февраля 2008 г. № 28 (4585) разработаны: НИИ экологии человека и гигиены окружающей среды им. А.Н. Сысина РАМН (д.м.н. проф. М.А. Пинигин д.м.н. проф. 3.Ф. Сабирова); Российской Академией последипломного образования (проф. К.А. Буштуева к.м.н. доцент Л.Е. Беспалько к.м.н. доцент Т.Е. Бобкова); Управлением Роспотребнадзора по г. Москве (к.м.н. С.Г. Фокин); Управлением Роспотребнадзора по Свердловской области (В.Б. Гуревич); Федеральной службой по надзору в сфере защиты прав потребителей и благополучия человека (О.И. Аксенова О.А. Кулагина Н.Д. Антипова). – Москва: Новая редакция 2008. – Текст: непосредственный.
ГОСТ 30852.9-2002 Электрооборудование взрывозащищенное. Часть 10. Классификация взрывоопасных зон = Explosion-proof electrical equipment. Part 10. Classification of hazardous areas : национальный стандарт Российской Федерации : издание официальное : введен в действие в действие приказом Федерального агентства по техническому регулированию и метрологии с 15 февраля 2014 г. подготовлен Автономной некоммерческой национальной организацией «Ex - стандарт» (АННО «Ex - стандарт»). – Москва: Стандартинформ 2014. – Текст: непосредственный.
СП 12.13130.2009 Определение категорий помещений зданий и наружных установок по взрывопожарной и пожарной опасности (с Изменением N 1) = Definition of categories of premises buildings and outdoor installations for explosion and fire hazard: свод правил: утвержден и введен в действие Приказом МЧС России от 25 марта 2009 г. №182 разработан ФГУ ВНИИПО МЧС России. - Москва: ФГУ ВНИИПО МЧС России 2009. – Текст: непосредственный.
Технический регламент о требованиях пожарной безопасности (с изменениями на 27 декабря 2018 года) = technical regulation on fire safety requirements (as amended on December 27 2018): федеральный закон: принят Государственной Думой 4 июля 2008 года одобрен Советом Федерации 11 июля 2008 года.
Правила устройства электроустановок (ПУЭ). Глава 7.3. Электроустановки во взрывоопасных зонах (Издание шестое)
Охрана труда. Учебное пособие Законодательные и нормативно- правовые акты по охране труда под ред. Ю.С. Москаленко 2-е изд. исп. и доп.- Красноярск: СибГТУ 2008. - 661 с. - Текст: непосредственный.
И-72 Инструкция по устройству молниезащиты зданий сооружений и промышленных коммуникаций. - Москва: «НЦ ЭНАС»2004. – 46 с. - Текст: непосредственный.
ГОСТ 12.4.124-83 Система стандартов безопасности труда (ССБТ). Средства защиты от статического электричества. Общие требования безопасности = Occupational safety standards system (SSBT). Protective equipment against static electricity. General safety requirements : межгосударственный стандарт: утвержден и введен в действие Постановлением Государственного комитета СССР по стандартам от 27 января 1983 г. № 428 разработан: Всесоюзным Центральным Советом Профессиональных Союзов Министерством внутренних дел СССР Министерством высшего и среднего специального образования СССР Министерством химической промышленности СССР Министерством электротехнической промышленности СССР. – Москва: ИПК Издательство стандартов 2003. – Текст: непосредственный.
ГОСТ 12.1.003-2014 Система стандартов безопасности труда (ССБТ). Шум. Общие требования безопасности (Переиздание) = Occupational safety standards system (SSBT). Noise. General Safety Requirements (Reprint) : межгосударственный стандарт: принят Межгосударственным Советом по стандартизации метрологии и сертификации (протокол от 5 декабря 2014 г. N 46) разработан Открытым акционерным обществом "Научно-исследовательский центр контроля и диагностики технических систем" (АО "НИЦ КД"). – Москва: Стандартинформ 2019. – Текст: непосредственный
ГОСТ 12.1.012-2004 ССБТ Вибрационная безопасность. Общие требования = Vibration safety. General requirements: межгосударственный стандарт: издание официальное: внесен Госстандартом России: взамен ГОСТ 12.1.012-90: взамен ГОСТ 12.1.012-90: дата введения 2008-07-01 разработан Открытым акционерным обществом "Научно-исследовательский центр контроля и диагностики технических систем". – Москва: Стандартинформ 2010. – Текст: непосредственный.
СП 52.13330.2011 Естественное и искусственное освещение. Актуализированная редакция СНиП 23-05-95 = Natural and artificial lighting. Updated edition of SNiP 23-05-95: свод правил: утвержден приказом Министерства регионального развития Российской Федерации от 27 декабря 2010 г. N 783 и введен в действие с 20 мая 2011 г. внесен Техническим комитетом по стандартизации ТК 465 "Строительство". – Москва: Минрегион России 2011. – Текст: непосредственный.
СП 44.13330.2011 Административные и бытовые здания. Актуализированная редакция СНиП 2.09.04-87 (с Поправкой с Изменениями N 1 2 3) = Administrative and domestic buildings. Updated version of SNiP 2.09.04-87 (as amended as amended by N 1 2 3): свод правил: утвержден приказом Министерства регионального развития Российской Федерации (Минрегион России) от 27 декабря 2010 г. N 782 и введен в действие с 20 мая 2011 г. внесен Техническим комитетом по стандартизации ТК 465 "Строительство". – Москва: Минрегион России 2011. – Текст: непосредственный.
СП 31.13330.2012 Водоснабжение. Наружные сети и сооружения. Актуализированная редакция СНиП 2.04.02-84 (с Изменениями N 1 2 3 4) = Water supply. External networks and facilities. Updated edition of SNiP 2.04.02-84 (as Amended by N 1 2 3 4): свод правил: утвержден приказом Министерства регионального развития Российской Федерации (Минрегион России) от 29 декабря 2011 г. N 63514 и введен в действие с 01 января 2013 г. внесен Техническим комитетом по стандартизации ТК 465 "Строительство" Федеральным автономным учреждением "Федеральный центр нормирования стандартизации и технической оценки соответствия в строительстве" (ФАУ "ФЦС"). – Москва: Стандартинформ 2019. – Текст: непосредственный.
ГОСТ Р 50800-95 Установки пенного пожаротушения автоматические. Общие технические требования. Методы испытаний. = Automatic foam fire extinguishing installations. General technical requirements. Test methods: государственный стандарт Российской Федерации: принят и введен в действие Постановлением Госстандарта России от 5 июля 1995 г. N 347 внесен Госстандартом России. – Москва: ИПК Издательство стандартов 1995. – Текст: непосредственный.
ГОСТ Р 12.3.047-2012 Система стандартов безопасности труда (ССБТ). Пожарная безопасность технологических процессов. Общие требования. Методы контроля. = Occupational safety standards system (SSBT). Fire safety of technological processes. General requirements. Control methods: национальный стандарт Российской Федерации: утвержден и введен в действие Приказом Федерального агентства по техническому регулированию и метрологии от 27 декабря 2012 г. N 1971-ст внесен Техническим комитетом по стандартизации ТК 274 "Пожарная безопасность". – Москва: Стандартинформ 2014. – Текст: непосредственный.
ГОСТ 12.4.009-83 Система стандартов безопасности труда (ССБТ). Пожарная техника для защиты объектов. Основные виды. Размещение и обслуживание (с Изменением N 1) = Occupational safety standards system (SSBT). Fire fighting equipment to protect objects. The main types. Accommodation and service (with Change N 1): межгосударственный стандарт: утвержден и введен в действие Постановлением Государственного комитета СССР по стандартам от 10.10.83 N 4882 разработан и введен Министерством внутренних дел СССР. – Москва: ИПК Издательство стандартов 2005. – Текст: непосредственный.
Приказ об утверждении Федеральных норм и правил в области промышленной безопасности "Общие правила взрывобезопасности для взрывопожароопасных химических нефтехимических и нефтеперерабатывающих производств" от 11 марта 2013 года N 96. – Текст : непосредственный.
СНиП 21-01-97 Пожарная безопасность зданий и сооружений (с Изменениями N 1 2) = SNiP 21-01-97 Fire safety of buildings and structures (as Amended by N 1 2): строительные нормы и правила Российской Федерации: приняты и введены в действие с 1 января 1998 г. постановлением Минстроя России от 13.02.97 г. N 18-7 внесены Управлением технормирования Минстроя России. Госстрой России. - Москва: ГУП ЦПП 2002. – Текст: непосредственный.
Экологический паспорт Ачинский НПЗ ВНК. – Ачинск 2005. – 68 с. – Текст: непосредственный.
Рекультивация земель загрязненных продуктами нефтепереработки учредитель Волгоградский государственный университет; главный редактор журнала Новочадов В.В. – 2011 -. – Волгоград 2012 -. – 58-64 с. - В настоящее время не выходит. –Текст: электронный.
Кузичкин С.И Экономика и управление производством: Методические указания для курсового и дипломного проектирования для студентов всех специальностей всех форм обучения ФХТ С.И. Кузичкин В.В. Абрамкин. – Красноярск: СибГАУ 2016. - 42с. – Текст: непосредственный.
Шепеленко Г.И. Экономика организация и планирование производства на предприятии: Учебное пособие. Г.И. Шепеленко. -Москва: ИКЦ «МарТ»; Ростов-на-Дону: Издательский центр «МарТ» 2003. -592 с. – Текст: непосредственный.
Экономика предприятия: Учебник для вузов В.Я. Горфинкель В.А. Швандар [и др.] – 3-е изд. пер. и доп. – Москва: ЮНИТИ – ДАНА 2001. – 718с. - Текст: непосредственный.
Григорьев В.Д. Экономика предприятия химических отраслей промышленности: Учебное пособие В.Д. Григорьев. – Москва: 2004 – 300с. - Текст: непосредственный.
тех.схема.dwg

Нестабильная головка АТ
Блок получения товарной продукции
Регенерированный раствор
Пропановая фракция с установки
Смесь н-бутана и фракции С5 для сырья пиролиза
Изобутановая фракция с установки
Фракция С5 на изомеризацию
Технологическая схема
БР-180301 000000.091.Т3
СибГУ им. М.Ф. Решетнева
Наименование оборудования
Изобутановая колонна (укрпеляющая часть)
Изобутановая колонна (отгоняющая часть)
Экстрактор сероочистки сжиженых газов
Подогреватель сырья деэтанизации
Кипятильник деэтанизатора
Кипятильник дебутанизатора
Подогреватель сырья пропановой колонны
Кипятильник пропановой колонны
Кипятильник изобутановой колонны
Теплообменник сырья деэтанизатора- фракции С5 и выше
Воздушный холодильник фракции С5 и выше
Воздушный холодильник н-бутановой фракции
Воздушный конденсатор - холодильник дебутанизатора
Воздушный конденсатор - холодильник пропановой колонны
Воздушный конденсатор - холодильник изобутановой колонны
Водяной холодильник сырья экстракта
Водяной холодильник раствора МЭА
Водяной холодильник пропановой фракции
Водяной холодильник изобутановой фракции
Водяной холодильник н-бутановой фракции
Водяной холодильник фракции С5 и выше
Водяной холодильник пропан-бутановой фракции
Буферная емкость сырья экстрактора
Емкость насыщенного раствора МЭА
Емкость регенерированного раствора МЭА
Буферная емкость сырья ректификации
Рефлюксная емкость деэтанизатора
Буферная емкость сырья пропановой колонны
Рефлюксная емкость дебутанизатора
Рефлюксная емкость пропановой колонны
Рефлюксная емкость изобутановой колонны
Емкость пропанновой фракции
Емкость изобутановой фракции
Емкость фракции С5 и выше
Сепаратор насыщенного раствора МЭА
поточная схема.dwg

Газофракционирование
БР-180301 000000.091.Т2
СибГУ им. М.Ф. Решетнева
Этановая колонна.dwg

СибГУ им. М.Ф. Решетнева
Ввод парожидкостной смеси
Выход кубового остатка
Переток жидк. в кипятильник
Для замера температуры
Для магнитного замера уровня
экономика.dwg

БР-180301 000000.091.ЭП
СибГУ им. М.Ф. Решетнева
Наименование показателей
Годовой выпуск продукции:
а) в натуральном измерении
б) в денежном измерении
Численность персонала:
Себестоимость единицы продукции
Себестоимость годового выпуска
Стоимость основных фондов
Затраты на рубль товарной продукции.руб.
Прибыль от реализации
Рентабельность производста
Срок окупаемости предприятия
Рекомендуемые чертежи
- 25.01.2023
- 23.08.2014
- 23.08.2014
- 23.08.2014
- 23.08.2014