Технологический процесс обработки детали Лопатка КВД 7 ступени




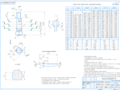
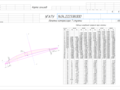
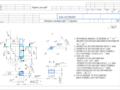
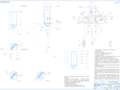
- Добавлен: 24.01.2023
- Размер: 963 KB
- Закачек: 2
Описание
Состав проекта
![]() |
![]() ![]() ![]() ![]() |
![]() ![]() ![]() ![]() |
![]() ![]() ![]() ![]() |
![]() ![]() ![]() ![]() |
![]() ![]() ![]() ![]() |
![]() ![]() ![]() ![]() |
![]() ![]() ![]() ![]() |
![]() ![]() ![]() |
![]() ![]() ![]() ![]() |
![]() ![]() ![]() ![]() |
![]() ![]() ![]() |
![]() ![]() ![]() ![]() |
Дополнительная информация
План обработки.cdw

0 Пескоструйная обработка
Схема построения профиля
5 Виброполировальная
ЛопМ.cdw

81 кг. КИМ не менее 0
Заготовка - штамповка
HRC 30 37. Группа контроля 2 ОСТ 1 00021-78
Перо лопатки изготовить методом ЭХО.
*Размеры для справок
Предельное отклонение точек профиля пера со стороны спинки
со стороны корыта не более 0
Уменьшения хорды за счет выходной кромки не более 0
Смещение профиля пера от номинального положения в
направлении оси Y-Y в сечении А4-А4 не более 0
в промежуточных сечениях до корневого -
по линейному закону. Смещение должно быть направлено в одну
Профили промежуточных сечений образуются плавным переходом
между заданными сечениями
Разность между углами И и И1 по абсалютной величине не более
При точечном методе контроля профилей допускается в каждом
как на корыте так и на спинке по две точки (но не на
кромках) выпадающих за поле допуска не более чем на 0
Выпадающие точки спинки и корыта не должны лежать друг против
При оптическом методе контролировать профиль пера по всем
сечениям на одной лопатке от комплекта. Допускается в каждом
так и на спинке по две точки (но не на
друга. В случае невыполнения данных требований весь комплект
Допускается наличие покрытия из серебра толщиной
0 мм на поверхностях Ж
Д2 не допустимо. Перед покрытием поверхность
подвергнуть легкой пескоструйной обдувке.
Лопатку виброшлифовать.
Произвести контроль ЛЮМ1-ОВ
Произвести контроль усталостной прочности.
Общие требования к изготовлению по ОСТ1 00450-82.
Ось вращения двигателя
Таблица координат профиля пера лопатки
Поверхность вращения
Мк1.frw

Код ЕВ МД ЕН Н.расх КИМ Код загот Профиль и размеры КД МЗ
наименование операции
Обозначение документа
СМ Проф. Р УТ КР КОИД ЕН ОП Кшт Тпз Тшт
наименование оборудования
Лопатка компрессора VII ступени
км Наименование детали
сб. единицы или материала Обозначение
код ОПП ЕВ ЕН КИ Н.расх.
Ультразвуковая ванна
Гальваническая ванна
Пескоструйная обработка
Сборка (слесарно-сборочная)
Слесарная (демонтаж)
ОК и КЭ_55_фрез_клин.frw

выровнять и закрепить
ПРЕ: Приспособление фрезерное специальное
Фрезеровать поверхности согласно
СИ: Скоба специальная односторонняя предельная 10.01
*Размеры для справок
Наименование операции Материал Твердость ЕВ МД Профиль и размеры МЗ КОИД
устройство ЧПУ Обозначение программы
ПИ Д или В L t i S n V
Лопатка компрессора 7 ступени
РИ: фреза ГОСТ 6469-69 ВК8В
КЭ_75_точение.frw

ШтампМ.cdw

Штампованная заготовка.
Термообработка - закалка и старение.
. Теоретический припуск по профилю пера 1 мм
по кромкам - 1 мм на
Неуказанные радиусы 2 мм
Смещение по плоскости разъема штампов не более 0
хвостовика в сторону спинки или корыта до 0
мм. На торце пера в месте бобышки облой не допускается.
Допускаются дефекты на хвостовике до половины фактического припуска на
механическую обработку.
Между сечениями равномерно-плавный переход.
Допускается увеличение припуска на 0
сечениях допускается увеличение припуска на 0
мм не более трех точек в
каждом сечении. В сечении А
допускается уменьшение припуска не более
мм по спинке и корыту суммарно в сторону уменьшения.
Допустимые дефекты по перу - по контрольному образцу.
Альфированный слой не допускается.
Маркировать шифром плавки со стороны корыта шрифтом 3 5.
Маркировать маркой материала "ВТ9" со стороны корыта
Схема построения профиля
Таблица точек профиля пера и параметров заготовки
С.Сх.ОсьX.cdw

Совмещенная схема и граф размерных взаимосвязей для оси Z
Совмещенная схема и граф размерных взаимосвязей для оси Y'
рамкаПЗ.doc
Анализ конструкции детали5
Анализ технологичности лопатки6
Обоснование выбора заготовки8
1 Выбор заготовки с точки зрения обеспечения требуемых свойств8
2 Выбор заготовки с точки зрения себестоимости9
Разработка технологического процесса11
1 Анализ базового технологического процесса11
2 Анализ разрабатываемого маршрутного технологического процесса14
Размерный анализ технологического процесса15
II.Разработка операционного технологического процесса изготовления лопатки КВД седьмой ступени компрессора29
Выбор средств технологического оснащения расчет режимов обработки норм времени для операции 75 «Токарная»29
1 Выбор средств технологического оснащения29
2 Расчет режима обработки30
3 Расчет штучного времени32
Выбор средств технологического оснащения расчет режимов обработки норм времени для операции 55 «Фрезерная»36
1 Выбор средств технологического оснащения36
2 Расчет режима обработки37
3 Расчет штучного времени38
Выбор средств технологического оснащения расчет режимов обработки норм времени для операции 115 «Электрхимическая»40
1 Процесс электрохимической обработки40
2 Выбор средств технологического оснащения41
3 Расчет режима обработки43
4 Расчет штучного времени44
III.РАЗРАБОТКА ЭЛЕКТРОДОВ – ИНСТРУМЕНТОВ48
Эффективность производства его технический прогресс качество выпускаемой продукции во многом зависит от опережающего развития производства нового оборудования машин станков и аппаратов от всемерного внедрения методов технико-экономического анализа.
Непрерывное совершенствование двигателей летательных аппаратов направлено на улучшение основных параметров их работы повышение ресурса и надежности экономичности в эксплуатации и снижение трудоемкости изготовления. В конструкциях авиационных двигателей широко применяются высокопрочные жаропрочные а также новые сплавы и стали с повышенными физико-химическими свойствами усложняется форма деталей повышаются требования к точности и качеству поверхностного слоя при изготовлении основных деталей. Все это существенно влияет на технологию производства двигателей.
В данном курсовом проекте рассматривается лопатка компрессора седьмой ступени двигателя ВК2500. Это изделие готовится к изготовлению в нашей стране и Индии.
Целью данного курсового проекта является:
Изучение рабочего чертежа конструктивных особенностей лопатки компрессора седьмой ступени и технических требований на изготовление детали свойств материала.
Разработка технологического процесса изготовления данной лопатки на основе имеющегося базового процесса.
Разработка операционных карт и карты эскизов на 3-4 операции.
Разработка электрода-инструмента и модели его профильной части.
Данная пояснительная записка содержит разделы по анализу конструкции и технологичности лопатки компрессора седьмой ступени по разработке технологического процесса размерного анализа расчет режимов обработки на токарную фрезерную электрохимическую операции расчет штучного времени на вышеперечисленные операции и контрольную операцию раздел по разработке электрода-инструмента.
В базовом технологическом процессе формообразование пера лопатки осуществляется фрезерованием. В разрабатываемом технологическом процессе данная операция заменена электрохимической обработкой. При этом улучшается обрабатываемость металла снижение трудоемкости уменьшение дефектного слоя.
I.РАЗРАБОТКА МАРШРУТНОГО ТЕХНОЛОГИЧЕСКОГО ПРОЦЕССА ИЗГОТОВЛЕНИЯ ЛОПАТКИ КВД 7-Й СТУПЕНИ
Анализ конструкции детали
Лопатки являются наиболее ответственными деталями газотурбинного двигателя так как они работают в условиях повышенных температур и значительных знакопеременных нагрузок.
В данном курсовом проекте рассматривается рабочая лопатка компрессора высокого давления седьмой ступени двигателя ВК2500. Чертеж детали 1404.222338.000 ЧД.
Поверхность пера лопатки является рабочей поверхностью она определяет функциональное назначение детали. Перо лопатки имеет сложную пространственную форму с переменными профилями в поперечных сечениях и по ее длине. Сечения повернуты относительно друг друга образуя закрутку пера – 6º31'.
Замок выполнен в виде ласточкина хвоста. Поверхности Ж подвержены фритинг-износу для уменьшения его влияния на эти поверхности наносят тонкий слой серебра толщиной 0.005-0.010 мм. Так как перо лопатки имеет большой угол разворота относительно хвостовика в конструкции предусмотрена полка. Также полка предназначена для повышения вибрационной стойкости лопаток.
Шероховатость поверхности пера лопатки Rа=0.63 мкм. Шероховатость рабочих поверхностей замка Rа = 1.6 мкм остальных поверхностей замка Rz = 20мкм.
Предельное отклонение точек профиля пера со стороны спинки не более 0.1 мм со стороны корыта не более 0.08 мм. Смещение пера от номинального положения в направлении оси Y-Y в сечении А4-А4 не более 0.2 мм в сечении А8-А8 не более 0.15 мм в промежуточных сечениях до корневого – по линейному закону.
Материал лопаток должен обладать достаточно высокой прочностью выносливостью коррозионной стойкостью (для защиты от паров воды и солей) и другими свойствами позволяющими детали работать в заданных условиях. Для лопаток компрессора работающих при температуре до 450-550ºС применяются титановые сплавы в данном случае сплав ВТ9 ГОСТ 19807-74. Химический состав этого сплава приведен в таблице 1.1. Механические свойства – в таблице 1.2. Сплав подвергается закалке и старению для снятия внутренних напряжений и структурного упрочнения. При этом увеличивается степень легированности -фазы и прочность сплава при повышенных температурах.
Таблица 1 - Химический состав материала ВТ9 %
Таблица 2 - Механические свойства при Т=20ºС материала ВТ9 в закаленном состоянии.
в предел выносливости
относительное удлинение при разрыве
относительное сужение
KCU ударная вязкость
Анализ технологичности лопатки
Под технологичностью конструкции понимается некоторая технико-экономическая характеристика изделия выражающая влияние возникающих в процессе проектирования свойств его конструкции на величину суммарных затрат живого и овеществленного труда необходимого для технологической подготовки производства и изготовления изделия на определенном предприятии-изготовителе в установленный срок и в заданном количестве [15].
Конструкция детали нетехнологична. Лопатка тонкостенная имеет малую жесткость поэтому при механической обработке необходимо уменьшать силы резания что в свою очередь увеличивает трудоемкость операции.
Нетехнологично получение хвостовика лопатки. Для соответствующей операции точения необходимо применение специального приспособления. Предшествующая и последующая слесарные операции сборки и демонтажа очень трудоемки так как включают в себя дополнительно заливку карбамидом промывку просушку притупление острых кромок.
При изготовлении лопатки проводится множество ручных работ. Это полировальные операции слесарные работы промывочные операции что увеличивает штучное время изготовления детали и себестоимость лопатки.
Из-за повышенных требований к качеству изделия точности возникает необходимость введения дополнительных контрольных операций что увеличивает время изготовления детали.
Наиболее важными операциями при изготовлении лопатки компрессора являются электрохимическая обработка пера точение замка.
От качества выполнения ЭХО зависит себестоимость трудоемкость и надежность лопатки.
При использовании ЭХО необходимо удовлетворить следующим требованиям:
Поверхность перед ЭХО должна быть очищена от окалины и других неэлектропроводных веществ.
В местах где удаление металла планируется выполнить с применением ЭХО не допускается местная зачистка поверхности.
ЭХО необходимо проводить после термической обработки заготовок. Это позволяет избежать нарушения точности за счет коробления при термообработке предотвращает появление обезуглероженного слоя в готовой детали.
Припуск не должен быть меньше предельного значения (в данном случае 1 мм) определяемого с учетом возможного растворения на обрабатываемых и соседних поверхностях где металл может раствориться за счет токов рассеяния и ускоренного съёма на кромках детали.
В технологическом процессе не предусматривают операции и переходы по удалению заусенцев и округлению кромок на поверхностях после ЭХО.
При разработке операций с обработкой резанием необходимо учитывать следующие особенности.
К числу отрицательных свойств титановых сплавов следует отнести плохую обрабатываемость резанием. Вследствие малой площади контакта между титановой стружкой и инструментом в зоне резания возникают высокие удельные давления и температуры. А так как титан обладает низкой теплопроводностью затрудняется отвод тепла из зоны резания. В результате титан налипает на инструмент и инструмент быстро изнашивается. Приваривание и налипание титана на контактируемые поверхности режущего инструмента приводят к изменению геометрических параметров резца что в свою очередь ведет к резкому возрастанию сил резания и дальнейшему повышению температуры. Наибольшее влияние на температуру оказывает скорость резания. В меньшей степени увеличение подачи влечет возрастание температуры. Глубина резания по сравнению со скоростью и подачей оказывает еще меньшее влияние на температуру. При механической обработке титановых сплавов рекомендуется работать с малыми скоростями резания при больших подачах и глубинах резания с обильной подачей охлаждающей жидкости. Материал инструментов должен иметь хорошее сопротивление истиранию высокую ударную вязкость прочность при изгибе и хорошую теплоемкость.
Обоснование выбора заготовки
1 Выбор заготовки с точки зрения обеспечения требуемых свойств
Особо ответственные детали такие например как лопатка КВД к которым предъявляются высокие требования по размеру зерна направлению волокон а также по уровню механических свойств всегда следует изготавливать из заготовки полученной обработкой давлением [4].
Основная тенденция современного машиностроения — применение материалов обеспечивающих необходимые конструктивные и эксплуатационные свойства имеющих повышенную обрабатываемость на всех стадиях передела. Иными словами материалы должны обладать необходимым запасом определенных технологических свойств – ковкостью штампуемостью жидкотекучестью свариваемостью обрабатываемостью.
Необходимым технологическим свойством для деформируемых материалов является технологическая пластичность. Чем ниже пластичность тем сложнее получить качественную заготовку методом обработки металлов давлением тем сложнее технологический процесс тем выше себестоимость детали. Так при изготовлении поковок из труднодеформируемых титановых высокопрочных сплавов осуществить необходимую степень деформации за один нагрев не всегда удается поэтому необходимо введение дополнительных промежуточных нагревов что значительно повышает себестоимость и трудоемкость изготовления поковок.
В технических условиях для ответственных тяжело нагруженных деталей для деталей работающих в условиях переменных нагрузок в специальных средах (детали турбостроения энергомашиностроения такие как валы шестерни зубчатые колеса роторы турбинные и компрессорные диски и лопатки и т.п.) указывают определенные требования к качеству материала к физико-механическим свойствам. Для подобных деталей в качестве заготовок целесообразно использовать поковки то есть заготовки полученные ковкой или штамповкой поскольку в процессе деформирования создается мелкозернистая направленная волокнистая структура значительно повышающая физико-механические свойства материала.
Кованые и штампованные заготовки (поковки) отличаются высокими механическими свойствами что обеспечивает высокую надежность и долговечность выпускаемой продукции поэтому наиболее ответственные тяжелонагруженные детали машин изготавливают из заготовок полученных ковкой или штамповкой.
Ковкой изготавливаются самые разнообразные поковки масса которых находится в пределах от нескольких десятков грамм до сотен тонн.
Таким образом следует что наиболее оптимально получать лопатку КВД седьмой ступени методом ковки.
Ковка – вид горячей обработки металлов давлением при котором металл деформируется с помощью универсального инструмента [16 с. 70].
Интервал горячей обработки давлением для титанового сплава ВТ9 – 1100-900ºС. [16 с.60].
Заготовительные технологические процессы производства заготовок лопаток компрессора ГТД должны обеспечивать:
требуемые геометрические размеры с необходимыми минимальными припусками;
оптимальную структуру и физико-механические свойства материала;
предотвращение появления потенциальных очагов разрушений;
минимальную материалоемкость;
минимальную себестоимость и трудоемкость;
минимальную последующую механическую обработку;
минимальный объем ручных работ.
Минимальные припуски на механическую обработку рассчитаны в результате размерного анализа и составили: по профилю пера – 1 мм по кромкам 0.5 мм по торцу замка – 2 мм по боковым поверхностям полки 0.5 мм.
Коэффициент использования материала:
где МД – масса детали МД = 0.00843 кг;
МЗ – масса заготовки МЗ = 0.01686 кг.
2 Выбор заготовки с точки зрения себестоимости
Сравним себестоимости штампованной заготовки и прутка.
Себестоимость заготовки из проката[14 с.30]:
где М – затраты на материал заготовки руб.;
Со.з.- технологическая себестоимость операций изготовления заготовки:
где Сп.з. – приведенные затраты приходящиеся на 1 час работ 100 рубчас [14 с.30].
Тшт – штучное время выполнения заготовительной операции 0.1 мин [14 с.30].
Затраты на материал определяются по массе проката требующегося на изготовление детали и массе сдаваемой стружки:
где Q – масса заготовки кг;
q - масса готовой детали 0.00843 кг
КИМ – коэффициент использования материала 0.3[14 с.30];
Q=0.0 8430.3=0.0281 кг
S –цена 1 кг материала заготовки 2000 руб.[14 с.30];
Sотх-цена 1 кг отхода 200 руб. [14 с.30].
Технологическая себестоимость операций изготовления заготовки:
Себестоимость заготовки из проката:
Стоимость штампованной заготовки:
где С – базовая стоимость 1 кг заготовки 2000 руб.;
kТ kС kВ kМ kП – коэффициенты зависящие от класса точности группы сложности массы марки материала и объема производства заготовок. kТ = 1 kМ = 1.21 kС=1; kВ=1 kП=1[14 с.37].
Таким образом себестоимость штампованной заготовки оказалась ниже себестоимости прутка. Это связано с тем что при изготовлении прутка коэффициент использования материала низкий по сравнению с коэффициентом использования материала штампованной заготовки.
Расчет производственной программы
Известно что в месяц производится 20 двигателей ВК2500. Количество устанавливаемых лопаток на седьмой ступени – 89. Следовательно производственная программа:
N = 12·20·89=21360 штук
Разработка технологического процесса
1 Анализ базового технологического процесса
5 Штамповка. Заготовка рассчитана на получение из нее двух деталей
0 Комплектование. Проверка наличия и качества маркировок соответствия их сопроводительной карте заполнение сопроводительной карты.
5 Фрезерная. Фрезерование торца замка. Данная поверхность служит в дальнейшем в качестве установочной базы.
0 Фрезерная. Фрезеруются боковые поверхности хвостовика в направлении оси Y'.
2 Фрезерная. Фрезерование боковых наклонных поверхностей хвостовика в направлении оси X'.
5 Слесарная. Притупление острых кромок промывка в бензине сушка сжатым воздухом.
0 Контрольная. Контроль размеров полученных на операциях 020 и 022 проверка отсутствия дефектов.
5 Сборка (слесарно-сборочная). Данная операция предусматривает предварительную очистку лопаток и сборки 89 лопаток в приспособление и заливку карбамидом.
0 Токарная. Чистовая обработка хвостовика. Полученные поверхности в дальнейшем используются в качестве установочных баз.
5 Слесарная (демонтаж). Операция включает расплавление карбамида демонтаж лопаток из приспособления промывку их в проточной воде сушку сжатым воздухом скругление острых кромок.
0 – 060 Операции: сборка (слесарно-сборочная) токарная слесарная (демонтаж) – повторяют операции 035-045 для другого конца заготовки.
5 Контрольная. Проверка наличия скруглений отсутствия дефектов контроль размеров полученных при точении.
0 Фрезерная. Фрезерование профиля лопатки.
5 Отрезная. Разделение заготовки на две части.
0 Слесарная. Притупление острых кромок.
5 Полировальная. Полирование профиля лопатки и полки для улучшения шероховатости.
0 Виброполирование. Обработка профиля для улучшения шероховатости.
5 Полировальная. Полирование переходных радиусов.
0 Фрезерная. Фрезерование облегчений на хвостовике лопатки.
5 Слесарная. Притупление острых кромок.
0 Токарная. Точение торца замка лопатки.
0 Контрольная. Проверка отсутствия дефектов скруглений острых кромок.
5 Травление. Контроль отсутствия прижогов изменений структуры материала.
5 Полировальная. Обработка входной и выходной кромки пера лопатки для улучшения шероховатости.
0 Виброполировальная. Обработка профиля лопатки для улучшения шероховатости.
5 Полировальная. Обработка переходных радиусов промывка в бензине сушка сжатым воздухом.
0 Контрольная. Проверка притуплений острых кромок отсутствия дефектов.
5 Закалка. Нагрев до 540ºС и выдержка при этой температуре 1.5-2 часа Измерение твердости на двух лопатках.
0 Виброшлифовальная. Обработка 120 лопаток в контейнере в течение 30 40 минут.
5 Виброполирование. Обработка 120 лопаток в контейнере в течение 30 40 минут.
5 Контрольная. Окончательный контроль всех чертежных размеров.
0 Вихретоковый контроль.
5 Слесарная. Визуальный контроль на наличие дефектов сравнение с эталонной лопаткой промывка в бензине.
0 Промывочная. Промывка в ультразвуковой ванне.
5 Контрольная. Ультразвуковой контроль.
5 Контрольная. Сравнение с эталонной лопаткой проверка отсутствия дефектов.
0 Подготовительная. Подготовка лопатки для нанесения покрытия. Защита поверхности не подлежащей нанесению покрытия.
0 Пескоструйная обработка. Обработка незащищенных поверхностей в операции 220.
5 Контрольная. Контроль качества пескоструйной обработки.
0 Серебрение. Нанесения слоя серебра на некоторые поверхности хвостовика лопатки толщиной 0.005-0.010 мм.
5 Контрольная. Визуальный контроль.
0 Контрольная. Контроль усталостной прочности.
5 Контрольная. Контроль перед отправкой: отсутствие дефектов сравнение с эталонной лопаткой.
0 Фрезерная. Фрезерование паза на полке со стороны корыта.
5 Фрезерная. Фрезерование паза на полке со стороны спинки.
5 Контрольная. Проверка отсутствия дефектов.
2 Анализ разрабатываемого маршрутного технологического процесса
В разрабатываемой технологии используется другая заготовка из которой получается одна деталь в отличие от базового технологического процесса в котором используется заготовка рассчитанная на получение двух деталей. Это связано с тем что фрезерная обработка пера лопатки заменена электрохимической операцией в случае использования заготовки для двух деталей при ЭХО образуются «теневые» зоны
Разработанный технологический процесс в виде маршрутной карты приведен в приложении и на плане обработки.
Были приняты следующие изменения:
- включена операция 45 «Фрезерная» здесь фрезеруется торец бобышки данная поверхность служит в качестве установочной базы; обработка ведется на станке 6Н81;
- исключены операции 050-060 базового технологического процесса «Слесарно-сборочная» «Токарная» «Слесарная (демонтаж)» так как в разрабатываемом технологическом процессе заготовка точится только с одной стороны;
- операция 070 «Фрезерная» для обработки профиля пера лопатки заменена операцией 115 «Электрохимическая» это связано с трудностью обработки материала заготовки механическим способом; при этом снижается трудоемкость уменьшается дефектный слой деталь обрабатывается на станке Искра – 38.2;
- включена операция 100 «Токарная» для того чтобы проточить бобышку лопатки поверхность которой служит базой при установке в приспособление в операциях 115 «Электрохимическая» деталь обрабатывается на фрезерном станке ТС МК 163;
- включена операция 95 «Сверлильная» здесь сверлится отверстие поверхность которой служит базой при последующей операции точения бобышки и в операции 130 «Фрезерная»; обработка - на сверлильном станке СВО 2Н125;
- включены операции 110 120 «Контрольная» для входного и выходного контроля при электрохимической обработке контроль точек пера лопатки проводится на ПОМКЛ-4;
- включена операция 125 «Маркирование» после электрохимической обработки;
- включена операция 130 «Фрезерная» для обработки входной и выходной кромки обработка - на фрезерном станке ФУ 12ШС-82;
- включены также слесарные операции 30 40 50 85 105 после соответствующих механических обработок для притупления острых кромок.
- назначение операции 135 «Отрезная» - отрезка бобышки лопатки в то время как в базовом технологическом процессе назначение данной операции – разделение заготовки на две части.
Размерный анализ технологического процесса
Для оценки величин размеров выдерживаемых в операциях технологического процесса и определения размеров заготовки а также допусков на эти размеры произведем комплексный размерный анализ. Исходными данными для размеров является план технологического процесса 1404.222338.000 чертеж детали 1404.222338.000 ЧД и заготовки. Расчет размеров заготовки проводится на основании выявленных размерных связей цепей для нахождения которой разрабатывается совмещенная схема обработки и граф размерных связей (представлены на плакате 1404.222338.000). Совмещенная схема строится в следующем порядке: изображается контур готовой детали на который начиная с последней операции наносятся все снимаемые припуски (напуски на совмещенных схемах не показываются); наносятся все технологические или операционные размеры включая размеры исходной заготовки; наносятся размеры готовой детали и обозначаются все операционные припуски.
На плане технологический процесс представлен в виде операционных эскизов на которых указаны базы обрабатываемые метод обработки технологические размеры в виде условных обозначений шероховатость точность взаимного расположения поверхностей.
Проведем размерный анализ лопатки по оси Z.
По графу размерных связей составим уравнения размерных связей.
Необходимо назначить допуски на операционные размеры. Для этого необходимо выполнить предварительный расчет номинальных значений размеров для того чтобы найти интервал размеров в который попадает технологический размер. Значение интервала необходимо для выбора нормальных окончаний технологических размеров.
Допуски назначают исходя из следующих принципов: чем выше технологических допуск тем проще его обеспечить при обработке тем ниже себестоимость этой обработки. Однако допуск на технологический размер оказывает существенное влияние на колебание припуска поэтому величины допусков выбирают стандартными соответствующими одному из квалитетов. Каждому виду обработки соответствует своя экономически целесообразная точность: грубые технологические операции по IT11-IT14 (размеры l13l18l34l24l32l42Lпрl4l1m41m40m30m2'n52n47) чистовые операции - IT8-IT11(размеры l23l46l48l19d31m27m21m22m2n5) отделочные и тонкие операции IT7 и точнее (размеры d2m17) [12 с.158].
На размеры заготовки отклонения выбираются в соответствии с таблицей по шестому классу точности [9 с.7072].
Распределение допусков начинают с самого большого уравнения – уравнения
На основании составленных уравнений размерных связей составим уравнения допусков назначим допуски на операционные размеры и размеры заготовки:
Исходя из рекомендуемых значений назначим минимальные припуски на обработку [10]:
на черновую фрезерную обработкумм
на чистовое точение мм
на чистовое фрезерование мм
на электрохимическую обработкумм
Решая уравнения размерных связей получаем:
приводим к нормальному окончанию [9 с.68] -
Приводим к нормальному окончанию [9 с.68] -
Диапазон чертежного размера – (48.5 49). Диапазон получаемого размера (48.621 48.914). Последние значения входят в диапазон требуемого размера следовательно округление верно.
Проведем размерный анализ лопатки по оси X'.
Округлим до значения-
Диапазон чертежного размера – (35.3 35.57). Диапазон получаемого размера (35.306 35.527). Последние значения входят в диапазон требуемого размера следовательно округление верно.
Приводим к нормальному окончанию -
Рассчитаем значения Д и З для других сечений.
Проведем размерный анализ лопатки по оси Y'.
приводим к нормальному окончанию -
С помощью программы «Компас» построим сечения профиля лопатки по точкам (рисунок 1). Затем эквидистантно проведем линии на расстоянии припуска z115=1 мм. Таблица с найденными точками профиля заготовки приведены на чертеже штамповки 1404.222338.000 ЧЗ.
Рисунок 1 – Схема нахождения точек профиля заготовки лопатки.
II.РАЗРАБОТКА ОПЕРАЦИОННОГО ТЕХНОЛОГИЧЕСКОГО ПРОЦЕССА ИЗГОТОВЛЕНИЯ ЛОПАТКИ КВД СЕДЬМОЙ СТУПЕНИ КОМПРЕССОРА
Выбор средств технологического оснащения расчет режимов обработки норм времени для операции 75 «Токарная»
1Выбор средств технологического оснащения
В операции 75 «Токарная» обрабатывается хвостовик лопатки.
Обработка ведется на станке ТПО АТ-600В. Выбор станка обоснован следующим:
диаметр приспособления (примерно 400 мм) не превышает максимальный диаметр обрабатываемого изделия на станке (800 мм [11 с.11]);
за счет современной жесткой компоновки станка обеспечивается необходимая точность обработки детали;
необходимые скорости вращения шпинделя (рассчитаны ниже) входят в диапазон частот вращения шпинделя – 2.5 710 обмин.
Выбор приспособления
Лопатки при сборе образуют кольцо поэтому в токарной операции они собираются в специальное приспособление «Планшайба» закрепляются прижимными винтами и прижимным кольцом. Затем заливается карбамидом.
Выбор режущего инструмента
Для обработки титановых сплавов применяют инструменты из твердых сплавов группы ВК [16 с.278]. Они обладают высокой износостойкостью и красностойкостью. Выберем материал режущего инструмента – ВК8 для чернового и чистового точения [5 с.116]. Все режущие инструменты назначили с пластинами из твердого сплава для повышения производительности [16 с.294] Для обработки торца замка лопатки на втором и пятом переходах назначим резцы по ГОСТ 18868-73 - токарные проходные отогнутые резцы предназначенные для обтачивания цилиндрических поверхностей [16 с. 293]. Для третьего и четвертого переходов – резцы ГОСТ 18880-73 – токарные подрезные отогнутые резцы предназначенные для обтачивания плоских торцовых поверхностей [16 с. 293]. Для шестого и седьмого для получения поверхности сложной формы – оправка и пластина.
Выбор измерительного инструмента
Так как производство серийное то целесообразно назначить в качестве измерительного инструмента калибры и другие предельные средства измерения. Для контроля длиновых размеров
назначили скобы специальные односторонние предельные для контроля углов и радиусов - шаблоны. Выбранные измерительные инструменты с указанием размера и допуска на который изготавливается калибр приведены в операционной карте «Токарная».
2 Расчет режима обработки
При назначении элементов режимов резания учитывают характер обработки тип и размеры инструмента материал его режущей части материал и состояние заготовки тип и состояние оборудования.
Операционная карта и карта эскизов данной операции приведены в приложении.
Элементы режима резания при точении:
глубина резания t мм;
величина подачи s ммоб;
скорость резания v мммин;
частота вращения шпинделя n обмин.
При точении припуск срезается за два прохода и более. В данной операции припуск (z75 = 0.543) со стороны торца замка снимается за два перехода (в операционной карте переходы 2 и 5) [5 с.265]. При каждом последующем проходе следует назначать меньшую глубину резания чем на предшествующем. Исходя их этого условия назначим глубину резания на втором переходе 0.343 мм на пятом переходе – 0.2 мм.
Подачу при точении выбирают в зависимости от требуемых параметров шероховатости обработанной поверхности и радиуса при вершине резца которые равны 1.6 мкм и 1 мм соответственно. Следовательно величина подачи равна 0.15 ммоб [5 с.268].
Скорость резания рассчитывают по эмпирической формуле [5 с.265]:
где Т – среднее значение стойкости при одноинструментальной обработке 30 – 60 мин; примем Т = 40 мин;
где KMv – коэффициент учитывающий влияние материала заготовки 0.5 [5 с.262];
Knv - коэффициент учитывающий влияние состояние поверхности 1 [5 с.263];
Kиv - коэффициент учитывающий влияние материала инструмента 1 [5 с.263]
Тогда скорость резания по формуле (1):
Частота вращения шпинделя:
принимаем n = 30 обмин. Тогда скорость резания из (2):
принимаем n = 35 обмин. Тогда скорость резания из (2):
Выбор смазочно-охлаждающей жидкости
Как было отмечено ранее в зоне резания возникают высокие температуры. Поэтому рекомендуется проводить обработку с обильной подачей жидкости. Также смазочно-охлаждающая жидкость необходима для обеспечения чистоты обработки. В связи со сказанным назначим смазочно-охлаждающую жидкость – эмульсия [16 262].
3 Расчет штучного времени
Техническая норма времени на обработку заготовки является одной из основных параметров для расчета стоимости изготавливаемой детали заработной платы рабочих и так далее.
Техническую норму времени определяют на основе технических возможностей технологической оснастки инструмента станочного оборудования и правильной организации рабочего места.
Норма времени является одним из основных факторов для оценки совершенства технологических процессов и выбора наиболее прогрессивного варианта обработки заготовки.
Штучное время на обработку лопатки точением рассчитаем по формуле [1 с.150]:
где Топ – оперативное время;
аабс аот. л. – соответственно время на обслуживание рабочего места отдых и личные надобности % от оперативного времени.
В свою очередь [1 c. 150]
где То – основное (машинное) время; Тв – вспомогательное время.
Основное время определяют на каждый переход после чего время всех переходов операции суммируют. Основное время [8 c.260]:
где L – расчетная длина обработки в направлении подачи мм;
sм – минутная подача мммин:
где s – подача на один оборот ммоб;
n – частота вращения шпинделя обмин.
Для второго перехода:
Для третьего перехода:
Для четвертого перехода:
Для пятого перехода:
Для шестого перехода:
Для седьмого перехода:
Суммарное основное время:
Вспомогательное время [1 c.154]:
tуст – вспомогательное время на установку и снятие детали;
t в.оп. – время связанное с выполнением операции.
tконтр – время связанное с измерением выдерживаемых размеров.
Так как в данной операции 89 лопаток собираются в специальное приспособление то вес детали с приспособлением будет до 3 кг. Следовательно время на установку и снятие равно 0.04 мин[3 c.262].
Обработка ведется полуавтоматическим циклом. Время на установку инструмента на размер при каждом переходе 0.02 мин[3 c.296].
Время связанное с выполнением операции включает в себя время на смену инструмента изменении режимов обработки включение выключение вращения шпинделя.
При втором переходе необходимо установить инструмент включить вращение шпинделя рычагом (необходимо 0.03 мин[3 c.297])установить число оборотов шпинделя (необходимо 0.08 мин[3 c.297]) установить величину подачи (необходимо 0.07 мин [3 c.297]). Суммарное время приемов на втором переходе 0.2 мин.
При третьем переходе необходимо переустановить инструмент изменить число оборотов шпинделя (необходимо 0.08 мин[3 c.297]). Суммарное время приемов на третьем переходе 0.1 мин.
При четвертом переходе необходимо переустановить инструмент Суммарное время приемов на четвертом переходе 0.02 мин.
При пятом переходе необходимо переустановить инструмент изменить число оборотов шпинделя (необходимо 0.08 мин[3 c.297]). Суммарное время приемов на шестом переходе 0.1 мин.
При шестом переходе необходимо переустановить инструмент изменить число оборотов шпинделя (необходимо 0.08 мин[3 c.297]). Суммарное время приемов на шестом переходе 0.1 мин.
При седьмом переходе необходимо переустановить инструмент выключить вращение шпинделя рычагом (необходимо 0.03 мин[3 c.297]). Суммарное время приемов на седьмом переходе 0.05 мин.
Суммарное время приемов на всех переходах 0.57 мин.
На втором переходе контролируется размер (1) k=0.026 z=0.12 u=0.3 [1 с.161] D=270 мм L5 мм (из карты эскизов):
На третьем переходе контролируются размеры:
(2) k=0.0196 z=0.168 u=0.230 [1 с.161] D=1.2 мм L5 мм (из карты эскизов);
(3) k=0.0113 z=0 u=0.368 [1 с.161] L5 мм (из карты эскизов);
(4) k=0.0196 z=0.168 u=0.230 [1 с.161] D=36 мм L5 мм (из карты эскизов):
(5) k=0.0113 z=0 u=0.368 [1 с.161] L5 мм (из карты эскизов);
(6) k=0.0196 z=0.168 u=0.230 [1 с.161] D=3.2 мм L5 мм (из карты эскизов):
На четвертом переходе контролируются размеры:
(7) k=0.0113 z=0 u=0.368 [1 с.161] L5 мм (из карты эскизов);
(8) k=0.0196 z=0.168 u=0.230 [1 с.161] D=4.1 мм L5 мм (из карты эскизов);
(9) k=0.0196 z=0.168 u=0.230 [1 с.161] D=5.7 мм L5 мм (из карты эскизов);
(10) k=0.0196 z=0.168 u=0.230 [1 с.161] D=1.2 мм L5 мм (из карты эскизов);
(11) k=0.0113 z=0 u=0.368 [1 с.161] L5 мм (из карты эскизов);
(12) k=0.0113 z=0 u=0.368 [1 с.161] L5 мм (из карты эскизов);
На пятом переходе контролируется размер (13):
k=0.026 z=0.12 u=0.3 [1 с.161] D=270 мм L5 мм (из карты эскизов):
На шестом переходе контролируются размеры:
(14) k=0.0113 z=0 u=0.368 [1 с.161] L5 мм (из карты эскизов);
(15) k=0.0196 z=0.168 u=0.230 [1 с.161] D=3.5 мм L5 мм (из карты эскизов);
(16) k=0.0196 z=0.168 u=0.230 [1 с.161] D=1.3 мм L5 мм (из карты эскизов);
(17) k=0.0113 z=0 u=0.368 [1 с.161] L5 мм (из карты эскизов);
(18) k=0.0113 z=0 u=0.368 [1 с.161] L5 мм (из карты эскизов);
(19) k=0.0113 z=0 u=0.368 [1 с.161] L5 мм (из карты эскизов);
(20) k=0.0113 z=0 u=0.368 [1 с.161] L5 мм (из карты эскизов);
(21) k=0.0196 z=0.168 u=0.230 [1 с.161] D=38.53 мм L5 мм (из карты эскизов);
На седьмом переходе контролируются размеры:
(22) k=0.0196 z=0.168 u=0.230 [1 с.161] D=3 мм L5 мм (из карты эскизов);
(23) k=0.0113 z=0 u=0.368 [1 с.161] L5 мм (из карты эскизов);
(24) k=0.0196 z=0.168 u=0.230 [1 с.161] D=5.4 мм L5 мм (из карты эскизов);
(25) k=0.0113 z=0 u=0.368 [1 с.161] L5 мм (из карты эскизов);
(26) k=0.0113 z=0 u=0.368 [1 с.161] L5 мм (из карты эскизов);
(27) k=0.0113 z=0 u=0.368 [1 с.161] L5 мм (из карты эскизов);
(28) k=0.0196 z=0.168 u=0.230 [1 с.161] D=1.3 мм L5 мм (из карты эскизов);
(29) k=0.0113 z=0 u=0.368 [1 с.161] L5 мм (из карты эскизов);
(30) k=0.0196 z=0.168 u=0.230 [1 с.161] D=4.4 мм L5 мм (из карты эскизов);
(31) k=0.0196 z=0.168 u=0.230 [1 с.161] D=4.6 мм L5 мм (из карты эскизов);
(32) k=0.0113 z=0 u=0.368 [1 с.161] L5 мм (из карты эскизов);
(33) k=0.0196 z=0.168 u=0.230 [1 с.161] D=1 мм L5 мм (из карты эскизов);
Суммарное время на измерения:
Следовательно вспомогательное время по формуле (7):
Оперативное время из (4):
Штучное время из (3):
Выбор средств технологического оснащения расчет режимов обработки норм времени для операции 55 «Фрезерная»
В данной операции обработка боковых поверхностей хвостовика образующих усеченный клин двумя фасонными фрезами одновременно. Заготовка обрабатывается на фрезерном станке ФВ 6А12Р. Выбор станка обоснован следующим:
размер приспособления с деталью не превышает размеры рабочей зоны станка (320х1250 мм)
необходимые скорости вращения шпинделя (рассчитаны ниже) входят в диапазон частот вращения шпинделя – 31.5-1600 обмин.
Для закрепления заготовки на фрезерном станке примем универсальное приспособление – тиски. Настройка положения детали относительно шпинделя станка осуществляется с помощью настроечной призмы по щупам.
Выбор режущего инструмента
Для обрабатываемого материала – титанового сплава ВТ9 - при чистовой обработке выберем материал режущей части фрезы ВК8В[6 с.12]. Для данной обработки выберем фасонную фрезу со следующими геометрическими параметрами:
ширина фрезерования B=7.7 мм.
диаметр фрезы D = 100 мм[6 с.14];
глубина фрезерования t = z55m
число зубьев z = 8 [5 с.187].
В условиях серийного производства целесообразно применять измерительные инструменты – калибры. В связи с этим на измерение длинового размера назначим скобу специальную предельную одностороннюю 10.01-0.043 для измерения угла – шаблон 4º2'±8'.
2 Расчет режима обработки
Элементы режима резания при фрезеровании:
При фрезеровании различают подачу на один зуб sz подачу на один оборот фрезы s и подачу минутную sм мммин которые находятся в следующем соотношении [5 c.282]:
где n – частота вращения фрезы обмин;
z – число зубьев фрезы.
При получаемой шероховатости Ra1.6 и дисковой фрезы со вставными ножами из твердого сплава ВК8В подача на один оборот s = 0.5 ммоб.
Тогда подача на один зуб из (8):
Скорость резания – окружная скорость фрезы[5 c.282]:
где Т – среднее значение стойкости для дисковой фрезы с диаметром D = 100мм Т = 120 мин [5 с.290];
где KMv – коэффициент учитывающий влияние материала заготовки 0.5 [5 c.262];
Knv - коэффициент учитывающий влияние состояние поверхности 0.8 [5 c.263];
Kиv - коэффициент учитывающий влияние материала инструмента 1 [5 c.263].
Тогда скорость резания из (9):
Приведем значения частоты вращения шпинделя к стандартному значению
n = 100 обмин. Тогда скорость резания:
Основное время [8 c.260]:
мммин.ошибка не 85 а100 смотреть выше
где Q – вес детали 0.016 кг[1 c.156]
а х – коэффициенты при использовании пневматического зажима с выверкой по индикатору 0.38 0.2 соответственно[1 c.156].
Время связанное с выполнением операции при фрезеровании с полуавтоматическим циклом и программным управлением равно 0.04 мин.
Контролируются размеры (1) k=0.026ошибка не нутрометр а скобасм [1] z=0.12 u=0.3 [1 с.161] D=10.01 мм L5 мм (из карты эскизов)на расстоянии 7.7 анне 5;
(2) k=0.0113 z=0 u=0.368 [1 с.161] L5 мм (из карты эскизов);
Оперативное время (4):
Выбор средств технологического оснащения расчет режимов обработки норм времени для операции 115 «Электрохимическая»
1 Процесс электрохимической обработки
В данной операции проводится электрохимическая обработка вибрирующим электродом инструментом импульсным напряжением. Частота подачи импульса и частота колебаний инструмента одинаковы и синхронизированы между собой так что импульс напряжения действует в тот момент времени когда инструмент и обрабатываемая деталь расположены друг относительно друга на минимальном расстоянии (зазоре).
При таком процессе напряжение подают в межэлектродный зазор отдельными импульсами. В паузах между импульсами анодного растворения металла не происходит а электролит протекает. За счет этого межэлектродный промежуток освобождается от продуктов обработки выравнивается температура электролита. Это способствует поддержанию расчетного режима ЭХО в течение всего периода работы на станке повышаются технологические показатели процесса. Чем больше скважность импульсов тем меньше изменяются условия протекания процесса. Одновременно с этим снижается скорость съема металла и усложняются источники питания (для компенсации снижения производительности приходится работать на токе большей силы) снижается их надежность.
При рассмотрении процесса ЭХО импульсным напряжением следует учитывать изменение следующих показателей по сравнению с обработкой постоянным напряжением:
уменьшение зазоров за счет лучшего удаления продуктов обработки из межэлектродного промежутка и возможности сближения электрода-инструмента с заготовкой во время пауз без опасения получить короткое замыкание;
снижение потерь напряжения в приэлектродных слоях за счет меньшего газонаполнения межэлектродного промежутка в период протекания тока;
уменьшение пассивационных ограничений при анодном растворении и увеличение выхода по току. Это объясняется лучшим удалением продуктов обработки из межэлектродного промежутка;
рост плотности тока в момент подачи импульса что способствует повышению качества поверхности.
2Выбор средств технологического оснащения
плотность тока в зоне обработки iобр = 80 Асм2 = 80 · 104 Ам2.
Площадь обработки лопатки схематично изображена на рисунке 2 и равна:
Площадь обработки полки изображена на рисунке 3. Средняя толщина пера ΔY лопатки 0.3 мм ширина b' – 12.3 мм. Тогда площадь обрабатываемой поверхности полки за вычетом площади под пером лопатки:
Общая площадь обработки:
Ток необходимый для обработки данной лопатки:
Рисунок 2 - Площадь обработки пера лопатки
Рисунок 3 - Площадь обработки полки лопатки
Для обработки пера лопатки и полки выбрали станок ЭХС «Искра 38.2» лопатки:
максимальная площадь обрабатываемой поверхности которого – 5 см2 внутренние размеры рабочей камеры 300х400х300 максимальное значение импульсного тока на сторону (суммарное) – 800А (1600А) что превышает требуемые значения.
Для обработки лопатки электрохимическим способом необходимо применение специального приспособления. Основные элементы приспособления: ложемент куда устанавливается лопатка токоподвод винт опорный крышка камера противодавления. Ложемент вставляется в корпус. Приспособление крепится на стол станка четырьмя винтами и базируется по двум штифтам. Подвод тока осуществляется через токоподвод к концу вала которого крепятся кабели. Электроды подводятся к лопатке через отверстия в ложементе и стенках.
Прокачка электролита осуществляется снизу через канал размерами 27×31 мм в основании корпуса и ложемента. Сверху электролит откачивается через штуцер установленный в стенке камеры противодавления. Токоподвод и закрепление лопатки осуществляется поворотом рукоятки.
Для обеспечения возможности установки детали в приспособлении применяется кассета. Преимущество применения кассеты заключается в удобстве установки кассеты в приспособлении в возможности быстрой замены ее в случае износа.
Выбор электрода-инструмента
Для электрохимической обработки лопатки в качестве электрод-инструмента выбрали электроды из стали 40Х13. Чертежи электродов: Электрод-инструмент правый 1404.222338.045 и Электрод-инструмент левый 1404.222338.046. Описание конструкции обоснование выбора материала инструмента приводится в разделе III данной пояснительной записки.
Выбор измерительного инструмента
Как было отмечено ранее в условия серийного производства целесообразно использовать калибры. При проведении операции контролируются три длиновых размера для измерения которых назначили скобы специальные односторонние предельные и координаты точек профиля пера лопатки для этого используется специальный прибор ПОМКЛ-4 здесь проверяется расположение теней в пределах поля допуска подвижной рамки экрана.
3 Расчет режима обработки
Исходя из рекомендуемых значений [7 c.218] и паспортных данных станка назначим следующие режимы обработки:
Напряжение поджига Uп = 30В напряжение рабочее Uраб =(0.5 0.75)Uп =(0.5 0.75)·30=15 22.5 В [13 с.11]. Примем Uраб =16В (рисунок 4);
длительность импульса и = 5мс;
при этом скважность будет равна [13 с.12]:
максимальное значения тока Im = 500 А и среднее - Iср=Iтq=5004 = 125А (рисунок 4);
амплитуда колебания межэлектродного зазора а = 0.2 мм (рисунок 4);
минимальный межэлектродный зазор sm
температура электролита Тэл = 25±5ºС;
электролит 10%NaNO3+2%NaCl+H2O. Выбор электролита обоснован следующим. Нитрат натрия увеливает избирательную способность при протекании процесса при этом увеличивается точность и класс шероховатости но при использовании этого электролита процесс неустойчив образуется оксидная пленка на детали. В связи с этим для компенсации влияния этих факторов в раствор добавлен хлорид натрия.
Рисунок 4 – Схема изменения межэлектродного зазора напряжения и тока во времени.
4 Расчет штучного времени
где z – припуск на электрохимическую операцию 1 мм;
vобр – линейная скорость анодного растворения 01 мммин.
Вспомогательное время [1 с.154]:
где tсбор – время на сборку лопатки в кассету;
tнанес – время на нанесение лака на торцевую поверхность кассеты со стороны пера лопатки;
tуст – время на установку и снятие детали в приспособление
tпром – время промывки лопатки в воде и ацетоне.
tвкл.выкл – время на включение выключение станка примерно 0.06 мин;
tвт – время на закрепление лопатки во втулке 0.09 мин [3 с.587]
tзакр.кр. – время на закрытие и открытие крышки приспособления и камеры примерно 0.08 мин;
tподв.ток. – время на перемещение токоподвода:
tизм – время на измерение выдерживаемых размеров;
tосм – время на внешний осмотр детали 0.09 мин [3 с.584]
где s – максимально возможный путь перемещения токоподвода 40 мм.
v – минимальная скорость перемещения токоподвода 400 мммин.
В операцию сборки в кассету входит вставка цилиндрических штифтов вручную. На закрепление одного штифта диаметром 4 мм и длиной 20 мм затрачивается 0.17 мин [2 с.343] следовательно на вставку двух штифтов уйдет 0.34 мин tсбор =034 мин.
Лак наносится на поверхность площадью (24.6-10.3)×10.01=143.1 мм2 (рисунок 5) следовательно время затрачиваемое на этот переход tнанес =0.018 мин [2 с.335].
Рисунок 5 – Схема нанесения лака на кассету
Установка лопатки производится в цанговом зажиме посредством поворота рукоятки приспособления. Следовательно время на установку лопатки [1 с.158]:
где а x y – коэффициенты 0.076 0.17 0.15 соответственно.
Dпy- диаметр цангового патрона 8 мм
Lвылу- длина вылета лопатки 34 мм.
Промывка детали водой осуществляется в ванной затрачиваемое время 0.12 мин [3 с.580]. Время на промывку ацетоном составляет 0.18 мин [3 с.581]. Суммарное время на промывку tпром= 0.3 мин.
Контролируются три длиновых размера скобами и положение точек профиля на профильном приборе ПОМК-4.
Время проведения измерений длиновых размеров:
где Dzизм – измеряемая длина детали мм;
L – расстояние на котором проводится измерение мм;
k z u – коэффициенты 0.0196 0.168 0.23 соответственно при измерении односторонними предельными скобами.
Контроль размера (30):
Контроль размера (4.1):
Контроль размера (5.2):
Контроль на ПОМКЛ-4:
где tуст. – время на установку и снятие детали примем 0.18 мин;
tк – время проведения непосредственно контроля – проверка расположения теней в пределах поля допуска подвижной рамки экрана 0.09 мин.
Тогда вспомогательное время по формуле (13):
Оперативное время по формуле (4):
Время на организационное и техническое обслуживание рабочего места отдых и личные надобности составляет 10 % от оперативного времени [1 с.162].
Тогда штучное время на обработку лопатки электрохимическим способом равно (3):
III.РАЗРАБОТКА ЭЛЕКТРОДОВ – ИНСТРУМЕНТОВ
Электроды предназначенные для обработки пера лопатки устанавливаются в вибраторы СП026.23.026.12.00.000. Фланец (поз. 2) крепится к вибратору. Для этого предусмотрено четыре отверстия под болты М8 и два отверстия под штифт. Базирование проводится по одному штифту который предназначен для угловой ориентации. Радиальная ориентация обеспечивается установкой по пояску диаметром 40 мм.
Электрод-инструмент состоит из самого электрода фланца трех винтов и двух штифтов. Установка штифтов (поз. 8) производится при выверке электродов на станке вместе с приспособлением. Выверка необходима для выдерживания зазора между электродами и соответствующими им отверстиями в приспособлении: по бокам – 0.2 мм снизу - 0.05 мм. Это необходимо для предотвращения затекания электролита в эти зазоры.
Электрод полностью выполнен из стали 40Х13. Этот материал обладает повышенной твердостью по сравнению с ранее использовавшимся материалом 12Х18Н10Т. При проведении обработки обратной полярностью появляются забоины на электрод-инструменте что приводит к дефектам на обрабатываемой лопатке. В связи с повышенной твердостью стали 40Х13 забоины возникают реже.
Также сталь 40Х13 не содержит никеля который ухудшает избирательную способность при электрохимическом процессе.
Длина электрода подобрана в соответствии с конструкцией приспособления и с учетом запаса на перебег заточку и минимальный отвод. Запас на перебег связан с износом электрода-инструмента позволяет при его повреждении перетачивать инструмент равен 10 мм. Ход станка составляет 40 мм сумма запасов на перебег и на минимальный отвод должны быть меньше хода станка приняли эту сумму равной 30 мм.
Точность формы и размеров рабочего профиля электрода-инструмента должны быть на один квалитет выше чем обрабатываемой детали. В связи с этим приняли квалитет точности седьмой. Шероховатость поверхности рабочей части не влияет на качество обрабатываемой поверхности но определяет характер течения электролита интенсивность загрязнения зазора продуктами обработки. Шероховатость рабочей части поверхности должна быть не более Ra2.5 мкм. Приняли Ra0.8.
Модели профильной части электродов-инструментов приведены на чертежах - Электрод-инструмент правый 1404.222338.045 и Электрод-инструмент левый 1404.222338.046. Точки рабочего профиля изготавливаемого электрода-инструмента указанные на чертеже соответствуют точкам профиля готовой детали. Корректировка профиля электрода-инструмента проводится путем обработки электрохимическим методом мастер–лопатки доработки шлифованием по результатам обработки пробных заготовок.
Расположение сечений рабочего профиля электрод-инструмента задано от мнимой поверхности соответствующей торцу лопатки. Нахождение положения этой мнимой поверхности схематично изображено на рисунке 6
Рисунок 6 – Схема нахождения положения мнимой поверхности – торца замка лопатки
В данном курсовом проекте был разработан технологический процесс в виде маршрутной карты. Ключевая операция – формообразование пера лопатки в базовом технологическом процессе была выполнена фрезерованием. В разрабатываемом технологическом процессе эта операция была заменена на электрохимическую обработку так как при этом улучшается обрабатываемость материала снижается трудоемкость уменьшается дефектный слой.
Рассчитаны режимы и нормы времени на операции 55 «Фрезерная» 75 «Токарная» 115 «Электрохимическая». Также назначили режущий инструмент измерительные средства на этих операциях.
Привели размерный анализ в результате которого определили припуски на формообразующие операции технологические размеры.
На основе рассчитанных значений составили операционные карты и карты эскизов на вышеперечисленные операции.
Справочник нормировщикаА.В. Ахумов Б.М.Генкин Н.Ю.Иванов и др.; Под общ. Ред. А.В.Ахумова. – Л.: Машиностроение Ленингр. отделение 1986. – 458 с. ил.
Толченов Т.В. Техническое нормирование станочных и слесарных работ М.М.Шахназаров изд. 3-е перераб. и доп. – М.: Машиностроение 1956. – 580 с. ил.
Б.А.Баранов Р.И. Хисин И.И. Шапиро. Техническое нормирование на машиностроительном заводе. Изд. 2-е перераб. и доп. – М.: Машиностроение 1964. – 610 с. ил.
Технология производства авиационных газотурбинных двигателей: Учеб. пособие для ВУЗовЮ.С. Елисеев А.Г. Бойцов В.В. Крымов Л.А. Хворостухин. М.: Машиностроение 2003. – 512 с. ил.
Справочник технолога-машиностроителя. В 2-х томах. Т. 2Под ред. А.Г.Косиловой и Р.К.Мещерякова. – 4-е изд. перераб. и доп. – М: Машиностроение 1986. 496 с. ил.
Косовский В.Л. Справочник молодого фрезеровщика. – 2-е изд. перераб. и доп. – М.: Высш. шк. 1992. – 400 с.: ил.
Амирханова Н.А. Зайцев А.Н. Зарипов Р.А. Электрохимическая размерная обработка материалов в машиностроении: Учебное пособиеН.А.Амирханова А.Н.Зайцев Р.А.Зарипов; УГАТУ. – Уфа 2004. – 258с.
Технология машиностроения: В 2 кн. Кн.1.Основы технологии машиностроения: Учеб. пособ. для вузовЭ.Л.Жуков И.И.Козарь С.Л.Мурашкин и др.; Под ред. С.Л.Мурашкина. – 3-е изд. стер. – М.: Высш. шк.2008. – 278 с.: ил.
Сборник задач по технологии авиадвигателестроения: Учебное пособие В.С.Мухин. Уфа: УГАТУ 1987. 75 с.
Зарипов Р.А. Методические указания (руководство) к выполнению курсового проекта по дисциплине «Технологии обработки концентрированными потоками энергии». УГАТУ Зарипов Р.А. – Уфа 2008. – 34 с.
Металлорежущие станки. Токарные станки: Каталог ИКФ «Каталог» 2004. – 142 с.
Мухин В.С. Основы технологии машиностроения (авиадвигателестроения): учебное пособие В.С.Мухин. - Уфа УГАТУ 2007. – 459 с.
Артамонов Б.А. Волков Ю.С. Дрожалова В.И. и др. Электрофизические и электрохимические методы обработки материалов. Учебное пособие (в 2-х томах). Т.I. Обработка материалов с применением инструмента Под ред. В.П. Смоленцева. – М.: Высш. шк. 1983. – 247 с. ил.
Горбацевич А.Ф. Шкред В.А. Курсовое проектирование по технологии машиностроения. Учебное пособиедля машиностроительных специальных вузов. – 4-е изд. перераб. и доп. – Мн.: Высш. школа 1983. – 256 с. ил.
Технология конструкционных материалов: Учебник для машиностроительных специальностей вузов А.М.Дальский И.А.Арутюнова Т.М.Барсукова и др.; Под общ. ред. А.М.Дальского. – 2-е изд. перераб. и доп. – М.:Машиностроение 1985. – 448с. ил.
КЭ_115_ЭХО1.frw

Таблица координат профиля пера лопатки
КЭ_115_ЭХО.frw

ЯВЛЯЕТСЯ ПРОДОЛЖЕНИЕМ ПРОФИЛЯ
ПРИПУСК ПО ПРОФИЛЮ ПЕРА 1 ММ.
ПРИПУСК ПО КРОМКАМ 0.5 ММ.
ПРИПУСК ПО ПОЛКЕ ХВОСТОВИКА
- ПРИПУСК ПО ПРОФИЛЮ
- ПРИПУСК ПО КРОМКАМ 0
- ПРИПУСК ПО ПОЛКЕ ХВОСТОВИКА
- ШЕРОХОВАТОСТЬ ПО ПРОФИЛЮ
ОСТАЛЬНЫЕ ТТ И РАЗМЕРЫ
ХВОСТОВИКА ПО ЧЕРЧЕЖУ.
Лопатка компрессора 7 ступени
КТК_1_после ЭХО.frw
электрохимической обработки
произвести проверку профиля
пера лопатки на предмет
выявления оплавления
и на соответствие чистоты
профиля пера эталону.
Осмотр производить визуально.
деффекты в дальнейшую работу
Профиль пера контролировать на
приборе ПОМКЛ-4 по сечениям А4-А4 А8-А8.
При проверке профиля пера по всем
расчетным сечениям концы теней
должны располагаться в пределах
поля допуска подвижной рамки экрана
Смещение профиля пера от
номинального положения в
направлении оси Y-Y в сечении А4-А4
сечениях до корневого - по линейному
закону. Смещение должно быть
напрвлено в одну сторону.
Профили промежуточных сечений
пера образуются плавным переходом
между заданными сечениями
Проверить наружным осмотром
шероховатость и волнистость
и плавность сопряжения профиля пера и полки
принимать по контрльному образцу
Наименование операции Наименование
Наименование оборудования
Контролируемые параметры Код средств ТО Наименование средств ТО Объем и ПК ТоТв
Технический контроль
Схема поля допуска профиля пера на рамке экрана прибора ПОМКЛ-4
мм. Увеличение прибора 50-кратное
ОК _75_точение.frw

подвески на планшайбу
торцу Т с точностью до 0
закрепить шестью болтами
СИ: Скоба специальная односторонняя предельная 1.2
Технические требования:
* Размеры для справок
СИ: Скоба специальная односторонняя предельная 36
СИ: Скоба специальная односторонняя предельная 3
СИ: Скоба специальная односторонняя предельная 4
СИ: Скоба специальная односторонняя предельная 5
СИ: Скоба специальная односторонняя предельная 1
СИ: Скоба специальная односторонняя предельная 38
Наименование операции Материал Твердость ЕВ МД Профиль и размеры МЗ КОИД
устройство ЧПУ Обозначение программы
ПИ Д или В L t i S n V
Лопатка компрессора 7 ступени
Снять приспособление со станка
РИ: Резец ГОСТ 18868-73 ВК8
РИ: Резец ГОСТ 18880-73 ВК8
РИ: оправка и пластина ВК8
РИ: оправка и пластина
СИ: Нутрометр цанговый
Рекомендуемые чертежи
- 24.01.2023
- 24.01.2023