Технологический процесс механической обработки детали раздаточной коробки автомобиля МАЗ




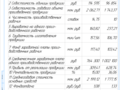
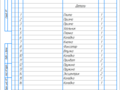
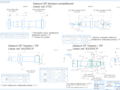
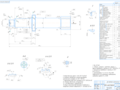
- Добавлен: 24.01.2023
- Размер: 8 MB
- Закачек: 0
Описание
Состав проекта
![]() |
![]() |
![]() ![]() ![]() |
![]() |
![]() ![]() ![]() |
![]() ![]() ![]() |
![]() ![]() ![]() |
![]() ![]() ![]() |
![]() ![]() ![]() |
![]() ![]() ![]() |
![]() ![]() ![]() |
![]() ![]() ![]() |
![]() ![]() ![]() |
![]() ![]() ![]() |
![]() ![]() ![]() |
![]() ![]() ![]() |
![]() ![]() ![]() ![]() |
![]() |
![]() ![]() ![]() ![]() |
![]() ![]() ![]() ![]() |
![]() ![]() ![]() ![]() |
![]() ![]() ![]() ![]() |
![]() |
![]() ![]() ![]() ![]() |
![]() |
![]() ![]() ![]() ![]() |
![]() |
![]() |
Дополнительная информация
Приложение Г.docx
Таблица Г1 – Капитальные вложения в здание в базовом варианте
Наименование оборудование модель
Площадь оборудования Sоб.i м2
Коэф. загрузки оборудования
Кол-во обор. i-го вида mi шт
Цена площади без НДС Цпл руб
Коэф. учит-й доп площадь Кд
Кап. влож. в здание Кзд млн. руб
Фрезерно-центровальная 2Г942;
Вертикально-сверлильная
Резьбофрезерная 5К63;
Круглошлифовальная 3А161;
Итого: капитальные вложения Кзд без НДС млн. руб
Таблица Г2 – Капитальные вложения в здание в проектном варианте
Резьбошлифовальная 5К822В;
Таблица Г3 – Расчет капитальных вложений в технологическое оборудование в базовом варианте млн. руб.
Наименование оборудования модель
Цена единицы без НДС млн. руб
Коэффициент затрат на транспортировку и монтаж
Первоначальная стоимость оборудования млн. руб
Продолжение таблицы Г3
Вертикально-сверлильная 2С132;
Итого: капитальные вложения Кзд с учетом НДС млн. руб
Таблица Г4 – Расчет капитальных вложений в технологическое оборудование в проектном варианте млн.руб.
Продолжение таблицы Г4
Таблица Г5 – Капитальные вложения в транспортные средства в базовом варианте
Фактический средний коэффициент загрузки участка kфз
Коэффициент затрат на транспортировку
Первоначальная стоимость оборудования млн. руб.
кран электрический подвесной
Итого: капитальные вложения без НДС
Итого: капитальные вложения с учетом НДС
Таблица Г6 – Капитальные вложения в транспортные средства в проектном варианте
Таблица Г7 – Капитальные вложения в универсальную технологическую
оснастку и инструмент
Наименование инструмента материал
Стойкость ч (количество промеров до полного износа тыс.)
Норма расхода на 1000 деталей
Потребное количество инструмента на программу
Цена единицы инструмента руб.
Фреза торцовая правая 03359-1
Фреза торцовая правая 03366-5
Сверло центровое 2317-0009
Сверло центровое 9341-83
Фреза червячная 9339-477-30
Фреза червячная 9339-386 (б)
Фреза червячная 9339-728
Фреза гребенчатая (б)
Круг шлифовальный (пр)
Круг шлифовальный 24А
Круг шлифовальный 24А (б)
Контрольное приспособление
Продолжение таблицы Г7
Итого для базового варианта: капитальные вложения млн. руб.
Итого для проектного варианта: капитальные вложения млн. руб
Таблица Г8 – Капитальные вложения в производственный инвентарь в базовом варианте млн. руб.
производственного инвентаря
Первоначальная стоимость оборудования. руб.
Инструментальный шкаф
Итого: капитальные вложения без НДС
Итого: капитальные вложения с учетом НДС
Таблица Г9 – Капитальные вложения в производственный инвентарь в проектном варианте млн. руб.
Первоначальная стоимость оборудования руб.
Таблица Г10 – Годовой фонд заработной платы рабочих-сдельщиков для проектного варианта
Группа рабочих по разрядам
Тарифный коэффициент i-го разряда kтар.i
Фонд основной заработной платы
Дополнительная заработная плата млн. руб
Годовой фонд заработной платы
ОЗП с учетом премий и доплат
Таблица Г11 – Заработная плата вспомогательных рабочих для базового и проектного вариантов
Вспомогательные рабочие
Фонд заработной платы с отчислениями млн. руб.
Итого расходы на оплату труда вспомогательных рабочих с отчислениями:
базовый вариант млн. руб.
проектный вариант млн. руб.
Таблица Г12 – Расходы на заработную плату работающих с отчислениями в
бюджет и внебюджетные фонды млн. руб.
Расходы на оплату труда основных рабочих всего
1 Основная заработная плата
2 Дополнительная заработная плата
3 Отчисления от ФЗП
Расходы на оплату труда вспомогательных рабочих с отчислениями
Расходы на оплату труда служащих с отчислениями
Всего расходов на оплату труда
Таблица Г13 – Расчет величины годовых амортизационных отчислений для
базового и проектного варианта
Наименование объекта
Срок полезного использования лет
чальная стоимость основных средств
Норма амортизационных отчислений %
зационные отчисления
Фрезерно-центровальный 2Г942;
Вертикально-сверлильный
Резьбофрезерный 5К63 (б);
Резьбошлифовальный 5К822В (пр);
Продолжение таблицы Г13
Итого величина годовых амортизационных отчислений на оборудование:
Транспортные средства
кран электрический подвесной (б)
Итого величина годовых амортизационных отчислений на транспорт:
базовый вариант руб.
проектный вариант руб.
Дорогостоящий инструмент и оснастка
Круг шлифовальный (б)
Итого величина годовых амортизационных отчислений
на инструмент и оснастку:
Итого величина годовых амортизационных отчислений:
Таблица Г14 – Затраты по статье «Общепроизводственные расходы» млн. руб.
Расходы по содержанию и эксплуатации оборудования:
- амортизация оборудования транспортных средств и ценного инструмента;
- эксплуатация оборудования (кроме расходов на ремонт);
- ремонт оборудования и транспортных средств;
- внутризаводское перемещение груза;
- погашение стоимости инструментов и приспособлений общего назначения.
Расходы по организации обслуживанию и управлению производством:
- оплата труда служащих (руководителей и специалистов) в том числе соответствующие отчисления;
- амортизация цеховых (производственных и административных) зданий сооружений инвентаря;
- содержание цеховых (производственных и административных) зданий;
- расходы по ремонту цеховых зданий;
- расходы на мероприятия по обеспечению нормальных условий труда техники безопасности (охрана труда);
- расходы на испытания опыты исследования рационализацию и изобретательство.
Итого затраты по статье
«Общепроизводственные расходы» млн. руб.
Таблица Г15 – Потребность в оборотном капитале млн. руб.
Элементы оборотных средств
Производственные запасы в том числе:
2Вспомогательные материалы
Незавершенное производство
Полная потребность в оборотном капитале:
Таблица Г16 – Величина полных инвестиционных вложений млн. руб.
Направления инвестирования
Инвестиции в основные средства в том числе:
1Здания и сооружения
2Рабочие машины и оборудование
3Транспортное оборудование
4Технологическая оснастка
5Производственный инвентарь
Инвестиции в оборотные средства в том числе:
1Производственные запасы
2Незавершенное производство
НДС при приобретении основных средств
Итого: полные инвестиционные вложения
Таблица Г17 – Ставки налогов и налоговых выплат исходные данные для
расчета отпускной цены и прибыли предприятия (по состоянию на 1 января 2010 года)
Норматив рентабельности единицы продукции
1 в цену (косвенные (оборотные))
- налог на добавленную стоимость (НДС)
Налоги и сборы выплачиваемые из прибыли (прямые) в том числе:
2сбор на развитие территории
%; 12% (для парка высоких технологий)
Исходные данные по вариантам проекта
Объем производства в натуральном выражении шт.
Величина полных инвестиций млн. руб. в том числе:
1 в основные средства млн. руб.
2в оборотные средства млн. руб.
Себестоимость единицы продукции руб.
Себестоимость произведенной продукции млн. руб.
Таблица Г18 – Расчет отпускной цены по базовому варианту технологического процесса
Цена предприятия без НДС
Отпускная (свободная) цена предприятия с НДС
Цотп. =ЦпрбезНДС + НДС
Таблица Г19 – Расчет прибыли от реализации и чистой прибыли предприятия
Выручка от реализации в отпускных ценах
Выручка предприятия без косвенных налоговых платежей
Прибыль от реализации
Преал = ВРпред - Сп (б)пр
Сбор на развитие территории (целевой сбор)
операционная карта.docx
Сталь 20ХН3А ГОСТ 4543-71
Оборудование устройство ЧПУ
Обозначение программы
Установить и закрепить деталь в приспособлении.
ПР Центр передний 9450-1186; Центр задний 7032-0024 Морзе 3 ВК8 ГОСТ 13214-79;
Хомутик ∅875 7107-4009 СТП 37.160.018-72
Нарезать резьбу выдерживая размеры 1 2.
ВИ Карандаш алмазный 3908-0053 ГОСТ 607-72; РИ Шлифовальный круг 4-350х8х160-3 25АМ3 9 35 мс ГОСТ 2424-83
СИ Кольцо ПР 8211-0168 6h M42x2-6h
СИ Кольцо НЕ 8211-1168 6h M42x2-6h
Накатать 16 шлицев выдерживая размеры 1 2 3.
РИ Накатник роликовый специальный; СИ Штангенциркуль ШЦ-I-125-01-2 ГОСТ 166; СИ Скоба 05519-118
Титульный лист.doc
Белорусский национальный технический университет
технологического процесса
группы 109316К.И. Кечко
Консультант по конструкторско-технологическому разделу
преподавательС.Г. Койда
Ответственный за нормоконтроль
Ст. преподавательВ.В. Бабук
операционная карта.doc
Сталь 20ХН3А ГОСТ 4543-71
Оборудование устройство ЧПУ
Обозначение программы
Установить и закрепить деталь в приспособлении.
ПР Центр передний 9450-1186; Центр задний 7032-0024 Морзе 3 ВК8 ГОСТ 13214-79;
Хомутик ∅875 7107-4009 СТП 37.160.018-72
Нарезать резьбу выдерживая размеры 1 2.
ВИ Карандаш алмазный 3908-0053 ГОСТ 607-72; РИ Шлифовальный круг 4-350х8х160-3 25АМ3 9 35 мс ГОСТ 2424-83
СИ Кольцо ПР 8211-0168 6h M42x2-6h
СИ Кольцо НЕ 8211-1168 6h M42x2-6h
Накатать 16 шлицев выдерживая размеры 1 2 3.
РИ Накатник роликовый специальный; СИ Штангенциркуль ШЦ-I-125-01-2 ГОСТ 166; Скоба 05519-118
Маршрутная карта.docx
Код наименование операции
Обозначение документа
Код наименование оборудования
2 005 4269 Фрезерно-центровальная ИОТ №–3648;
Фрезерно-центровальный полуавтомат мод. 2Г942 1 19479 4 1 1 1 1 1 17
2 010 4233 Токарная с ЧПУ ИОТ №–4836;
Токарный полуавтомат с ЧПУ мод. 16А20ф3 1 19158 3 1 1 1 1 1 497
2 015 4233 Токарная с ЧПУ ИОТ №–4836;
Токарный полуавтомат с ЧПУ мод. 16А20ф3 1 19158 4 1 1 1 1 1 273
2 020 0200 Контроль ИОТ № 9
Стол ОТК 4 30632 6 1 1 1 1
2 025 4165 Шлицефрезерная ИОТ №–4836;
Шлицефрезерный полуавтомат мод.5Б352ПФ2 1 19479 4 1 1 1 1 1 119
2 030 4165 Шлиценакатная ИОТ №–4836;
Шлиценакатной мод. Grob ZRMe 9 1 19479 5 1 1 1 1 1 432
Наименование детали сб. единицы или материала
2 035 4153 Зубофрезерная ИОТ №–4836;
Шлицефрезерный полуавтомат мод. 5Б352ПФ 1 12273 5 1 1 1 1 1 173
2 040 4214 Вертикально-сверлильная ИОТ №–48; 6014200004 2014200004
Вертикально-сверлильный мод. 2С132 1 18355 3 1 1 1 1 1 19
2 045 4135 Резьбошлифовальная ИОТ №–4836; 6014100005 2014100005
Резьбошлифовальный полуавтомат мод. 5К822П 1 17985 5 1 1 1 1 1 247
2 050 0108 Слесарная ИОТ №–98;
Верстак ОР 1960 4 18466 4 1 1 1 1
2 055 0125 Промывка
Моечная машина Н721.000.0000 3 45252 3 1 1 100 100
2 060 0200 Контроль ИОТ № 9;
2 065 04 Перемещение
14637 – 1 1 100 100
0 070 5000 Термическая обработка
0 075 04 Перемещение
2 080 4214 Вертикально-сверлильная ИОТ №–48;
Вертикально-сверлильный мод. 2С132 1 18355 3 1 1 1 1 1 097
2 085 4131 Круглошлифовальная ИОТ №–48;
Круглошлифовальный мод. 3А161 1 19630 5 1 1 1 1 1 457
2 090 4131 Круглошлифовальная ИОТ №–48;
Круглошлифовальный мод. 3А161 1 19630 5 1 1 1 1 1 34
2 095 4151 Зубошлифовальная ИОТ №–4836;
Зубошлифовальный полуавтомат мод. 5М841Ф11 1 12277 5 1 1 1 1 1 278
2 100 0125 Промывка ИТ № 37.160.140
2 105 0200 Контроль приемочный ИОТ № 9
Стол ОТК 4 30632 6010200011 2010200011
карта контроля.docx
Наименование операции
Наименование марка материала
Наименование оборудования
Контролируемые параметры
Наименование средств ТО
Внешним осмотром проверить полноту и качество механической обработки отсутствие заусенцев и острых кромок 100%
Размер 1 05511-303 Шаблон 27 -021 25%
Размеры 2 4 12 ГОСТ 162 Штангенглубиномер ШГ – 250 – 005 5%
Размер 3 05501-4105 Скоба d60 -0010; -0029 100%
Размер 5 05510-957 Скоба d60 -003; -006 100%
Размеры 7 10 11 ГОСТ 164 Штангенрейсмас ШР – 400 – 005 5%
Размеры 8 9 9691-4732 Контрольное приспособление 5%
61-7266-01 Установ 5%
Размер 13 ГОСТ 166 Штангенциркуль. ШЦ- I-125-01-2 5%
Размер 14 05640-163 Кольцо шлицевое D16х52х60f7х5h9 100%
Размер 15 9691-4979-01 Контрольное приспособление 5%
Размер 16 05119-150 Скоба 25%
Размер 17 ГОСТ 6507 Микрометр МЗ 50-2 100%
ОПЕРАЦИОННАЯ КАРТА ТЕХНИЧЕСКОГО КОНТРОЛЯ
ГОСТ 3.1404-86 Форма 3 а
Размер 18 9691-4974-01 Контрольное приспособление 5%
Размер 19 9691-4979-01 Контрольное приспособление 5%
Размер 20 8211-0168 h M42x2-6h Калибр комплексный 100%
Шероховатость Ra=063;Ra=125;Ra=25 ТУ-2-034-4-83 Профилометр
Клеймить деталь Клеймо резиновое; бескислотная жидкость
Отходы массой 54 кг направляются в ЦЗШ
Маршрутная карта.doc
Код наименование операции
Обозначение документа
Код наименование оборудования
2 005 4269 Фрезерно-центровальная ИОТ №–3648;
Фрезерно-центровальный полуавтомат мод. 2Г942 1 19479 4 1 1 1 1 1 17
2 010 4233 Токарная с ЧПУ ИОТ №–4836;
Токарный полуавтомат с ЧПУ мод. 16А20ф3 1 19158 3 1 1 1 1 1 497
2 015 4233 Токарная с ЧПУ ИОТ №–4836;
Токарный полуавтомат с ЧПУ мод. 16А20ф3 1 19158 4 1 1 1 1 1 273
2 020 0200 Контроль ИОТ № 9
Стол ОТК 4 30632 6 1 1 1 1
2 025 4165 Шлицефрезерная ИОТ №–4836;
Шлицефрезерный полуавтомат мод.5Б352ПФ2 1 19479 4 1 1 1 1 1 119
2 030 4165 Шлиценакатная ИОТ №–4836; 6014100004 2014100004
Шлиценакатной мод. Grob ZRMe 9 1 19479 5 1 1 1 1 1 432
Наименование детали сб. единицы или материала
2 035 4153 Зубофрезерная ИОТ №–4836;
Шлицефрезерный полуавтомат мод. 5Б352ПФ 1 12273 5 1 1 1 1 1 173
2 040 4214 Вертикально-сверлильная ИОТ №–48; 6014200004 2014200004
Вертикально-сверлильный мод. 2С132 1 18355 3 1 1 1 1 1 19
2 045 4135 Резьбошлифовальная ИОТ №–4836; 6014100005 2014100005
Резьбошлифовальный полуавтомат мод. 5К822П 1 17985 5 1 1 1 1 1 247
2 050 0108 Слесарная ИОТ №–98;
Верстак ОР 1960 4 18466 4 1 1 1 1
2 055 0125 Промывка ИОТ № 37.160.140
Моечная машина Н721.000.0000 3 45252 3 1 1 100 100
2 060 0200 Контроль ИОТ № 9;
2 065 04 Перемещение ИОТ №–98;
14637 – 1 1 100 100
0 070 5000 Термическая обработка ИОТ №–45–98;
0 075 04 Перемещение
2 080 4214 Вертикально-сверлильная ИОТ №–48;
Вертикально-сверлильный мод. 2С132 1 18355 3 1 1 1 1 1 097
2 085 4131 Круглошлифовальная ИОТ №–48;
Круглошлифовальный мод. 3А161 1 19630 5 1 1 1 1 1 457
2 090 4131 Круглошлифовальная ИОТ №–48;
Круглошлифовальный мод. 3А161 1 19630 5 1 1 1 1 1 34
2 095 4151 Зубошлифовальная ИОТ №–4836;
Зубошлифовальный полуавтомат мод. 5М841Ф11 1 12277 5 1 1 1 1 1 278
2 100 0125 Промывка ИОТ № 37.160.140
2 105 0200 Контроль приемочный ИОТ № 9
Стол ОТК 4 30632 6010200011 2010200011
9 110 04 Пермещение ИОТ №–98;
карта контроля.doc
Наименование операции
Наименование марка материала
Наименование оборудования
Контролируемые параметры
Наименование средств ТО
Внешним осмотром проверить полноту и качество механической обработки отсутствие заусенцев и острых кромок 100%
Размер 1 05511-303 Шаблон 27 -021 25%
Размеры 2 4 12 ГОСТ 162 Штангенглубиномер ШГ – 250 – 005 5%
Размер 3 05501-4105 Скоба d60 -0010; -0029 100%
Размер 5 05510-957 Скоба d60 -003; -006 100%
Размеры 7 10 11 ГОСТ 164 Штангенрейсмас ШР – 400 – 005 5%
Размеры 8 9 9691-4732 Контрольное приспособление 5%
61-7266-01 Установ 5%
Размер 13 ГОСТ 166 Штангенциркуль. ШЦ- I-125-01-2 5%
Размер 14 05640-163 Кольцо шлицевое D16х52х60f7х5h9 100%
Размер 15 9691-4979-01 Контрольное приспособление 5%
Размер 16 05119-150 Скоба 25%
Размер 17 ГОСТ 6507 Микрометр МЗ 50-2 100%
ОПЕРАЦИОННАЯ КАРТА ТЕХНИЧЕСКОГО КОНТРОЛЯ
ГОСТ 3.1404-86 Форма 3 а
Размер 18 9691-4974-01 Контрольное приспособление 5%
Размер 19 9691-4979-01 Контрольное приспособление 5%
Размер 20 8211-0168 h M42x2-6h Калибр комплексный 100%
Шероховатость Ra=063;Ra=125;Ra=25 ТУ-2-034-4-83 Профилометр
Клеймить деталь Клеймо резиновое; бескислотная жидкость
Отходы массой 54 кг направляются в ЦЗШ
2 ИНЖЕНЕРНАЯ ЧАСТЬ.docx
1.1 Описание объекта производства
Седельные тягачи выпускаются Минским автозаводом: МАЗ-64229 с 1987 г. МАЗ-64221 и -64224 с 1989 г (рисунок 2.1.1). Кабина - двухместная подрессоренная с двумя спальными местами откидывающаяся вперед с помощью гидроцилиндра с ручным приводом гидронасоса оборудована местами крепления ремней безопасности. Сиденье водителя - подрессоренное регулируемое по весу водителя длине высоте наклону подушки и спинки.
Основные полуприцепы: для МАЗ-64229 - МАЗ-9398 для МАЗ-64221 и-64224- МАЗ-93866. Предназначены для перевозки различных грузов в составе автопоезда
Рисунок 2.1.1 - Автомобиль МАЗ 6422
В колесной формуле 6x4 используется два задних ведущих моста и передняя управляемая ось (трехосный седельный тягач). Нагрузка на седельно-сцепное устройство (ССУ) такого тягача составляет от 19000 кг до 24000 кг. Высота ССУ от дорожного полотна без нагрузки может составлять от 1300 мм.
Таблица 2.1.1 – Технические характеристики автомобиля МАЗ 6422
Допустимая полная масса автомобиля кг
Допустимая полная масса автопоезда кг
Допустимая нагрузка на переднюю ось кг
Допустимая нагрузка на заднюю ось кг
Допустимая нагрузка на седло
Масса снаряженного автомобиля кг
Максимальная скорость кмч
Мощность двигателя. кВт (л.с.)
Число передач раздаточной коробки
Передаточное число раздаточной коробки
Передаточное число ведущих мостов
Особенности комплектации:
Водительское подрессоренное сиденье ремни безопасности шумоизоляция кабины; АБС; спойлер.
Наиболее широко седельные тягачи с колесной формулой 6x4 применяются при эксплуатации со следующими типами полуприцепов различных производителей:
тентовых полуприцепов изотермических фургонов и рефрижераторов для междугородних перевозок при общей длине автопоезда для России и Беларуси до 20 метров.
полуприцепов-контейнеровозов для перевозки контейнеров 1А 1АА 1В 1ВВ 1С 1СС.
полуприцепы цистерны топливовозы и топливозаправщики при оснащении седельного тягача комплектом ADR (для перевозки огнеопасных грузов).
бортовых полуприцепов.
самосвальных полуприцепов для перевозки сыпучих грузов при оснащении седельного тягача системой гидроотбора.
полуприцепов тяжеловозов. (тралов)
специализированных полуприцепов (сортиментовозов зерновозов щеповозов и др.).
Седельные тягачи МАЗ-MAН соответствуют всем стандартам и требованиям ЕЭК ООН уровня Евро-3 и оснащены экологически чистыми и экономичными двигателями производства MAN мощностью от 410 до 460 л.с. Автомобили МАЗ-MAН совместили общепризнанные качества автомобилей MAN а также были доработаны с учетом эксплуатации автомобилей в различных климатических зонах и наиболее тяжелых дорожных условиях (сезонное бездорожье гололед затяжные подъемы).
1.2 Назначение и условия работы детали в сборочной единице
Деталь – Вал-шестерня входит в состав раздаточной коробки седельного тягача МАЗ 6422.
Деталь – Вал-шестерня представляет собой вал на котором выполнены: резьба; шлицы двух видов – прямобочные и с эвольвентным профилем; а также нарезаны зубья и два отверстия с пересекающимися осями.
Данная деталь входит в состав раздаточной коробки. Раздаточная коробка (рисунок 2.1.2) служит для передачи крутящего момента от коробки переменных передач к переднему ведущему мосту. С ее помощью осуществляется автоматическое или принудительное включение и выключение переднего моста.
Рисунок 2.1.2 – Схема раздаточной коробки
Вал-шестерню устанавливают на шарикоподшипники которые запрессовывают в корпус раздаточной коробки. На прямобочные шлицы устанавливается соединительный фланец который служит для присоединения карданного вала привода переднего ведущего моста автомобиля. Неподвижность соединительного фланца в продольном направлении обеспечивается за счет корончатой гайки навинчиваемой на резьбу нарезаемую на хвостовике вал-шестерни.
Вал-шестерня раздаточной коробки находится в постоянном зацеплении с промежуточной шестерней на оси вторичного вала коробки передач. Благодаря этому вал-шестерня раздаточной коробки на всех передачах синхронно подключает в работу передний ведущий мост когда срабатывает муфта свободного хода.
Вал не только поддерживает нагруженные детали но и передает вращающие моменты. На валу имеется зубчатый венец зубья которого: воспринимают ударные и контактные нагрузки изнашиваются из-за трения а также воспринимают напряжения от изгиба. Также на валу имеется два вида шлицев которые работают на смятие срез и также изнашиваются из-за трения. Исходя из сказанного необходимо подобрать такой материал который бы воспринимал контактные нагрузки обладал хорошей износостойкостью выдерживал нагрузки кручения и изгиба. Поэтому вал-шестерню изготавливают из высококачественной конструкционной стали 20ХН3А ГОСТ 4543-71. Сталь этой марки используется при изготовлении шестерен валов втулок силовых шпилек болтов червяков муфт и другие цементируемых деталей к которым предъявляются требования высокой прочности пластичности и вязкости сердцевины и высокой поверхностной твердости работающих под действием ударных нагрузок и при отрицательных температурах. Заменителями данной стали являются стали 38ХА 20ХГР 20ХГНР 15Х2ГН2ТА 20ХНГ. Механические свойства и химический состав стали 20ХН3А представлены в таблицах 2.1.2 и 2.1.3
Таблица 2.1.2 - Механические свойства в зависимости от температуры отпуска
Нормализация 860 °С воздух. Закалка 810 °С масло.
Таблица 2.1.3 - Химический состав стали 20 ХНЗА В процентах
Основные требование к детали — долговечность и износостойкость зубчатых венцов поэтому она подвергается дополнительной термообработки.
Таблица 2.1.4 - Физические свойства материала 20ХНЗА
Физические свойства: Т - Температура при которой получены данные свойства [Град]; Е- Модуль упругости первого рода [МПа]; а - Коэффициент температурного (линейного) расширения (диапазон 20° - Т) [1Град]; r - Плотность материала [кгм3]; С - Удельная теплоемкость материала (диапазон 20° - Т) [Дж(кг град)]; R -Удельное электросопротивление [Ом м].
Температура критических точек материала 20ХНЗА
Ас1=730°C Ас3 (Асm) = 810°C Аr3 (Аrcm) = 700°C Аr1=615°C Мп = 340°C
К важнейшим требованиям также относиться высокое качество обработки зеркал внутренних посадочных поверхностей под подшипники и торцевой поверхности детали.
1.3 Анализ технологичности конструкции детали
В целях определения наиболее эффективного способа изготовления детали машиностроения необходимо производить анализ технологичности конструкции детали который позволит уточнить конструкторские решения с технологической точки зрения.
Оценка технологичности конструкции может быть двух видов: качественной и количественной. Качественная оценка характеризует технологичность конструкции обобщенно на основании опыта исполнителя и допускается на всех стадиях проектирования как предварительная. Количественная оценка технологичности изделия выражается числовым показателем и оправдана в том случае если они существенно влияют на технологичность рассматриваемой конструкции [26 с.31].
Рисунок 2.1.3 – Эскиз детали «Вал-шестерня»
Качественная оценка технологичности
Деталь – Вал-шестерня (рисунок 2.1.3) – изготавливается из высококачественной легированной конструкционной стали 20ХН3А ГОСТ4543-71. Данная сталь удовлетворительно обрабатывается резанием. Для уменьшения износа поверхностей вала применяется химико-термическая обработка - цементирование на глубину 12 15 мм с повторным нагревом под закалку а на шлифованных поверхностях h не менее 07 мм. Резьба от цементации предохраняется. Поверхности зубьев шлицев шлифованные поверхности должны иметь твердость 59 63 HRC торцы 54 HRC не менее сердцевина зубьев 30 45 HRC остальные обработанные поверхности 47 HRC. Заготовку можно получить двумя методами: штамповкой на КГШП или поперечно-клиновой прокаткой.
Деталь довольно проста по конструкции и имеет хорошие базовые поверхности для первоначальных операций. Форма заготовки приближена к форме детали. Имеется свободный доступ инструмента к обрабатываемым поверхностям.
В конструкции детали заложен принцип единства баз. Технологические базы в течение всего хода технологического процесса остаются неизменными что позволяет избежать дополнительных погрешностей. В соответствии с этим принципом расставлены размеры на чертеже. Размеры определяющие нерабочие поверхности детали имеют более широкие поля допусков и более грубую шероховатость чем рабочие. К валу предъявляются высокие требования по допуску на радиальное биение 0019 мм.
Контроль диаметральных размеров осуществляется с помощью скоб колец микрометра; линейных размеров – с помощью штангенциркуля шаблонов калибра; отверстия – с помощью пробки; шлицев – с помощью шлицевых комплексных шлицевых поэлементных прямобочных шлицевых проходных калибров. Для контроля резьбы применяются комплексные калибры. Шероховатость проверяется профилометром.
Следует отметить что вал жесткий (lD = 40892 = 44). Это говорит о том что имеется возможность увеличения режимов резания применения много инструментальной обработки.
На валу имеются в наличии поверхности к которым предъявляются высокие требования по точности (шейки вала резьбовые поверхности) что ведёт к увеличению трудоемкости и перерасходу средств на изготовление детали. Это ведет к увеличению себестоимости детали но в свою очередь допускает применение станков нормальной точности.
Нетехнологичными являются следующие элементы: резьба расположение двух отверстий (с пересекающимися осями и перпендикулярны образующей). При их обработке возможен увод сверла. Следовательно для их получения необходимо использовать специальное приспособление.
Также нетехнологичными элементами являются зубья; шлицы которые имеют эвольвентный и прямоугольный профили. С точки зрения механической обработки шлицевые и зубчатые поверхности нетехнологичны так как операция нарезания зубьев и шлицев со снятием стружки производится в основном малопроизводительными методами.
Вал подвергается термообработке что свидетельствует об усложненном технологическом процессе его получения.
Количественная оценка технологичности конструкции
Количественная оценка технологичности конструкции может быть осуществлена лишь при использовании соответствующих базовых показателей технологичности. К основным показателям относятся [26 с.33]:
) трудоемкость изготовления детали ТИ нормо-час
) технологическая себестоимость детали Ст руб
Необходимость использования дополнительных показателей определяется тем что на стадии разработки чертежа детали и его согласования с технологом последний руководствуется главным образом техническими критериями ввиду отсутствия в этот момент данных о трудоемкости и технологической себестоимости проектируемой детали так как технологический процесс ее изготовления еще не разработан.
При оценке детали на технологичность обязательным являются следующие дополнительные показатели (по методике В.Г. Кононенко):
коэффициент унификации конструктивных элементов
Ку.э = Qу.э Qэ (2.1.1)
где Qу.э и Qэ – соответственно число унифицированных конструктивных элементов детали и общее шт.;
коэффициент применяемости стандартизованных обрабатываемых поверхностей
Кп.ст = Do.c Dм.о (2.1.2)
где Do.c Dм.о – соответственно число поверхностей детали обрабатываемых стандартным инструментом и всех подвергаемых механической обработке поверхностей шт.;
коэффициент обработки поверхностей
Кп.о = 1-Dм.оDэ (2.1.3)
где Dм.о и Dэ соответственно число поверхностей подвергаемых механической обработке и общее число поверхностей шт.;
коэффициент использования материала
где q Q – соответственно масса детали и заготовки кг;
масса детали q = 112 кг;
максимальное значение квалитета обработки IT 6;
минимальное значение параметра шероховатости обрабатываемых поверхностей Rа = 063 мкм;
Таким образом проанализировав количественные показатели технологичности для данной детали следует сказать что к отрицательным показателям характеризующим деталь относятся: коэффициент использования материала который является ниже среднего (067 07). Это говорит о том что значительная часть материала срезается в стружку что приводит к снижению технологичности изделия а также к удорожанию детали. Коэффициент унификации конструктивных элементов показал что деталь нетехнологична так как имеет лишь четверть унифицированных конструктивных элементов.
К положительным показателям характеризующим деталь относятся: коэффициент применяемости стандартизованных обрабатываемых поверхностей – все поверхности обрабатываются стандартным инструментом.
Таким образом проанализировав качественные и количественные показатели технологичности детали «Вал-шестерня» можно сделать вывод что из-за наличия большого количества нетехнологичных элементов указанных выше высоких требований к точности обработки и необходимости термообработки данный вал является мало технологичным.
1.4 Анализ базового варианта технологического процесса
Предметом анализа является технологический процесс изготовления детали "Вал-шестерня" раздаточной коробки. Годовой объем выпуска -18000шт. Принятую в данном варианте технологического процесса общую последовательность обработки логически следует считать целесообразной так как при этом соблюдаются принципы формирования свойств обрабатываемой детали. Метод получения заготовки соответствует принятому типу производства.
Данный технологический процесс состоит из следующих операций:
5 – фрезерно-центровальная;
0 – контроль операционный;
0 – вертикально-сверлильная;
5 – резьбофрезерная;
0 –термическая обработка;
5 – круглошлифовальная;
0 – круглошлифовальная;
5 – шлицешлифовальная;
0 – зубошлифовальная;
0 – контроль приемочный
Для анализа применяемого при обработке оборудования составляется таблица 2.1.5.
Таблица 2.1.5 – Технологические возможности применяемого оборудования
Предельные или наибольшие размеры обрабатываемой заготовки
Технологические возможности метода обработки
Диаметр (ширина) d(b)
Шероховатость обрабатываемой поверхности мкм
Станки используемые на всех операциях по габаритам размера обрабатываемой заготовки достигаемой точности и шероховатость соответствуют требуемым условиям обработки заданной детали. Все станки являются относительно недорогими. Категория ремонтной сложности их не высокая.
В технологическом процессе производства детали “Вал-шестерня” применяется стандартный и унифицированный инструмент наименование режимы работы настройка инструмента применяемого в техпроцессе приведены в таблице 2.1.6.
Таблица 2.1.6 – Режущие инструменты
Наименование инструмента
Материал режущей части
Фреза торцовая правая 03359-1 Нож 03305-3
Фреза торцовая правая 03366-5 Нож 03305-4
Сверло центровое 2317-0009 ГОСТ 14952-69
Сверло центровое 9341-83
Резец 2109-4253 (К01-4977-000-06 ТУ 2-035-892-82)
Фреза червячная 9339-477-30
Фреза червячная 9339-386
Фреза червячная 9339-728
Круг шлифовальный1-600х100х305 24А25ПС2.7.К ГОСТ2424-83
Круг шлифовальный1-100х10х20 24А16ПС2.7.К ГОСТ2424-83
Круг шлифовальный 4-350х25х1275 24А25СМ1.4.К7 ГОСТ2424-83
Технологический процесс обработки деталей предусматривает использование большого числа специальных приспособлений. Это обоснованно тем что в условиях серийного производства большое значение приобретает быстрота удобство и точность установки детали в процессе обработки. При этом необходимо соблюдать принципы единства и совмещения баз. Применяемые приспособления позволяют производить угловую ориентацию заготовок что исключает выверку детали перед обработкой. В таблице 2.1.7 приведены установочно-зажимные приспособления применяемые в технологическом процессе.
Таблица 2.1.7 – Установочно-зажимные приспособления
Название приспособления
Привод приспособления
Количество приспосо-блений на станке шт.
Время на установку и снятие заготовки мин
Приспособление токарное 9675-5233
Патрон инерционный 9675-2350
Центр задний №5 7032-4024
Центр передний 7032-0035 ГОСТ 13214-79
Центр задний 7032-0112 ГОСТ 13214-79
Продолжение таблицы 2.1.7
Кондуктор 9671-16372
Центр задний 7032-0023
Приспособление 9671-16382
Центр 7032-0029 ГОСТ 13214-79
Хомутик 7107-0071 ГОСТ 16488-70
Центр передний 9460-1186
Центр задний 7032-0024 ГОСТ 13214-79
Применяемые приспособления в основном являются специальными их применение позволяет повысить точность обработки быстроту удобство и точность установки детали. Однако к недостаткам этих приспособлений следует отнести применение ручного зажима заготовок что увеличивает время установки заготовок и т.д.
Вспомогательный инструмент применяемый в технологическом процессе производства детали приведен в таблице 2.1.8.
Таблица 2.1.8 – Вспомогательные инструменты
Установка реж. инструмента
Время на смену одного инструмента мин
Оправка правая 6222-4031
Оправка левая 9488-245
Оправка для фрезы 6224-5058
Набор колец 6030-5106
Карандаш алмазный 3908-0052
Применяемый вспомогательный инструмент в технологическом процессе является специальным и стандартным. Его применение позволяет повысить быстроту и удобство установки режущего инструмента. Время необходимое на смену одного режущего инструмента во вспомогательном сравнительно невелико.
Затраты времени на смену (правку) инструмента можно снизить если применить более стойкие твердосплавные инструменты с износостойкими покрытиями.
Для анализа средств технического контроля применяемых в данном технологическом процессе приведена таблица 2.1.9.
Таблица 2.1.9 – Средства технического контроля
Наименование инструмента и эталона
Точность измерения мм
Допуск на измеря-емый размер мм
Время на одно измере-ние мин
ШЦ-II-500-0.05 ГОСТ 166
Контрольное приспособление 9692-4253
ШЦ-I-125-01-2 ГОСТ 166
Контрольное приспособление 9692-4499-01
ШЦ-II-160-005 ГОСТ 166
Скоба на D87-022 05501-5122
Контрольное приспособление
Скоба 05501-2046 D4184-013
Скоба 05523-800 d108-035
Набор радиусных шаблонов N2 ТУ 034-228-87
Шаблон на р-р 272-021 05511-302
Продолжение таблицы 2.1.9
Контрольное приспособление на
Скоба 05507-623 D39-062
Кольцо кон. 8312-6338; НЕ 8312-6340
Центра контрольные 9691-4979
Микрометр МК 125-2 ГОСТ 6507
Индикатор ИРБ ГОСТ 5584-75
Скоба 05519-118 54-008
Микрометр М350-2 ГОСТ 6507
Кольцо ПР 8211-0168 6h M42x2-6h
Кольцо НЕ 8211-1168 6h M42x2-6h
Профилометр мод. 296 ТУ-2-034-4-83
Шаблон 8102-5063 27-021
Установ 8461-7266-01
Контрольное приспособление 9691-4732
Профилометр мод. 296 ТУ-2-034-4-83 (КТО)
Контрольное приспособление 9691-4979-01
Кольцо шлицевое 05640-163 D16х52х60f7х5h9
Профилометр «Суртраник» (ЦЗЛ)
Микрометр М3 50-2 ГОСТ 6507
Можно отметить в данном технологическом процессе основная масса измерительного инструмента является специальным. Имеется также и стандартный инструмент. Применение таких типов средств технологического контроля увеличивает быстроту выполнения измерения. Точность измерений достаточно высокая. Оснащенность измерительными средствами операций обработки достаточно хорошая.
Действующий технологический процесс можно усовершенствовать следующим образом:
– для нарезания резьбы М42х2 применить многониточный шлифовальный круг;
– так же можно заменить операции 030 Шлицефрезерная и 095 Шлицешлифовальная на операцию 030 Шлиценакатная.
1.5 Определение типа и организационной формы производства
В соответствии с методическими указаниями РД 50-174-80 коэффициент закрепления операций характеризующий тип производства [26 с.52] определяется по формуле 2.1.5:
Рi – явочное число рабочих участка выполняющих различные операции при работе в одну смену.
Условное число однотипных операций выполняемых на одном станке в течение одного месяца при работе в одну смену определяется по формуле 2.1.6
где: н – планируемый нормативный коэффициент загрузки станка всеми закрепленными за ним однотипными операциями принимаемый для крупносерийного производства равным 075;
з – коэффициент загрузки станка проектируемой (заданной) операцией:
где: Тшт-к – штучно-калькуляционное время необходимое для выполнения проектируемой операции мин;
Nм – месячная программа выпуска заданной детали шт.;
Fм – месячный действительный фонд времени работы оборудования в одну смену он равен 169 ч;
kв – коэффициент выполнения норм принимается равным 13.
Подставляя в формулу 2.1.7 значения Fм и kв получим:
Определим месячную программу выпуска детали в одну смену:
Nг – годовой объем выпуска заданной детали шт; Nг = 18000шт.
После подстановки выражения 2.1.8 в формулу 2.1.6 получим зависимость для определения числа однотипных операций выполняемых на одном станке в течении месяца:
Суммарное число операций выполняемых на каждом станке за месяц формула 2.1.10
Поi = По1 + По2 + .+ Поп(2.1.11)
Необходимое число рабочих для обслуживания в течение одной смены одного станка загруженного по плановому нормативному коэффициенту
где Ni – приведенный месячный объем выпуска деталей (шт.) при загрузке станка до принятого
Ф – месячный фонд времени рабочего занятого в течение 22 рабочих дней в месяц ч: Ф = 176 ч.
После подстановки в формулу 2.1.12 значений Ф kв и Поi (формула 2.1.10) получим зависимость для определения необходимого числа рабочих для обслуживания одного станка:
Суммарное явочное число рабочих участка при работе в одну смену определяется по формуле:
Рi = Р1 + Р2 + . + Рi(2.1.14)
Произведем необходимы расчеты для операции 045 а остальные расчеты по операциям сведём в таблицу 2.1.10.
Таблица 2.1.10 – Выбор типа производства.
фрезерно-центровальная;
вертикально-сверлильная
вертикально-сверлильная;
По ГОСТ 3.1119-83 находим что тип производства крупно серийный так как выполняется условие 1Kз.о.10.
Формы организации технологических процессов в соответствии с ГОСТ 140312-74 зависит от установленного порядка выполнения операций расположения технологического оборудования количества изделий и направления их движения при изготовлении. Существуют две формы организации технологических процессов – групповая и поточная основные признаки приведены в данном стандарте.
Решение о целесообразности организации поточной формы организации производства обычно принимается на основании сравнения заданного суточного выпуска изделий и расчетной суточной производительности поточной линии при двухсменном режиме работы и ее загрузки на 65-75% [26 с.55].
Заданный суточный выпуск изделий
Где: Nг – годовая программа выпуска шт.
3 – количество рабочих дней в году.
Суточная производительность поточной линии (шт.)
где: Fc – суточный фонд времени работы оборудования (при 2-хсменном режиме работы – 960 мин.);
Тср – средняя станкоемкость основных операций мин.;
н – коэффициент загрузки станка.
Средняя станкоемкость операции
kв – средний коэффициент выполнения норм времени;
n – количество основных операций.
Произведем необходимы расчеты по вышеприведенным формула и результаты приведем в таблице 2.1.11.
Таблица 2.1.11 – Форма организации производства
По ГОСТ 140312-74 определяем что форма организации производства – поточная т.к. Кз >065 то принимаем поточную форму организации технологического процесса.
Такт производства (мин.)
где: Fэ – эффективный фонд работы оборудования ч;
N – Объем выпуска изделия в планируемый период шт.
При групповой форме организации запуск изделий в производство осуществляется партиями с определенной периодичностью что является признаком серийного производства. Количество деталей в партии для одновременного запуска определяется по методике В.А. петрова.
Рассчитывают предельно допустимые параметры партии n1 и n2:
Где – эффективный месячный фонд времени участка равный 10560 мин;
– число операций механической обработки по технологическому процессу;
– средний коэффициент выполнения норм по участку равный 13; – суммарная трудоемкость технологического процесса мин;
– средняя трудоемкость одной операции мин;
– коэффициент учитывающий затраты межоперационного времени равный 15.
отражает производительность и уровень специализации рабочих мест на участке. С помощью параметра учитывается и ограничивается объем незавершенного производства и связывания оборотных средств. Меньший из двух параметров обозначают а больший . Для дальнейшего расчета размера партии используется .
Определяют расчетную периодичность повторения партий деталей:
Где – месячная программа выпуска деталей:
Согласовывают расчетную периодичность повторения партий деталей с ее допустимыми нормативными значениями . Ближайшее большее значение принимается к расчету .
Рассчитывают размер партии согласно условию:
Условие выполняется. Размер партии определен верно.
Тип производства крупносерийный принимаем групповую форму организации производства.
1.6 Выбор оптимального метода получения заготовки
На выбор метода получения заготовки оказывают влияние: материал детали её назначение и технические требования на изготовление объем и серийность выпуска форма поверхностей и размеры детали.
Оптимальный метод получения заготовки определяется на основании всестороннего анализа названных факторов и технико–экономического расчета технологической себестоимости детали. Метод получения заготовки обеспечивающий технологичность изготовления из неё детали при минимальной себестоимости считается оптимальным [26 с.57].
Рисунок 2.1.4 – Эскиз заготовки полученной штамповкой на КГШП
Рисунок 2.1.5 – Эскиз заготовки полученной поперечно-клиновой прокаткой
В базовом технологическом процессе заготовку получают на КГШП (рисунок 2.1.4). Данный метод обеспечивает получение точных поковок без сдвига в плоскости разъема с малыми припусками. Класс точности Т4 по ГОСТ 7505-89.
Более точным и производительным методом получения заготовки для данной детали является поперечно-клиновая прокатка (рисунок 2.1.5). Этот метод позволяет снизить расход металла т.к. отсутствует облой; повысить коэффициент использования металла; повысить производительность труда; снизить себестоимость заготовки и трудоемкость последующей обработки резанием. Класс точность заготовки Т3 по ГОСТ 7505-89.
Рассчитаем стоимость получения заготовок по двум вариантам. Исходные данные для расчета сводим в таблицу 2.1.12.
Таблица 2.1.12 – Сравнение методов получения заготовок
Метод получения заготовки
Штамповка на КГШП (базовый)
Поперечно-клиновая прокатка (предлагаемый)
Стоимость 1т заготовок руб.
Стоимость 1т стружки руб.
При сравнении двух методов используем [26 с.53].
При оценки детали на технологичность необходимо учитывать коэффициент использования материала:
где: Q – масса заготовки кг;
q – масса готовой детали кг;
Коэффициент использования материала получаемой по базовому варианту техпроцесса:
Коэффициент использования материала получаемой по предлагаемому варианту:
Стоимость заготовки получаемой этими методами можно с достаточной точностью определить по формуле:
Q – масса заготовки кг;
Sотх – стоимость 1 тонны отходов руб;
Кт – коэффициент зависящий от класса точности;
Кс –коэффициент зависящий от класса сложности;
Кв –коэффициент зависящий от марки материала;
Км –коэффициент зависящий от массы заготовки;
Кп –коэффициент зависящий от объёмов производства.
Стоимость заготовки получаемой по базовому варианту техпроцесса:
Стоимость заготовки получаемой по предлагаемому варианту
Из расчета видно что заготовка полученная предлагаемым методом дешевле.
Экономический эффект от принятия получения заготовки предлагаемым методом:
Эз = (Sб – Sпр)N;(2.1.24)
где Sб Sпр – стоимость заготовки соответственно по базовому и принятому варианту получения руб;
N – годовая программа выпуска шт;
Эз = (62765 – 53940)*18000 = 1588 млн. руб.
Это говорит о том что выбранный метод более эффективен.
В результате применения нового способа получения заготовки сократится трудоемкость их последующей обработки резанием а также повысится коэффициент использования материала.
При базовом варианте коэффициент использования материала равен 067 а при планируемом – 08.
Таким образом при поперечно-клиновой прокатке будет достигнута экономия на операциях механической обработки за счет уменьшения припусков снижения времени обработки экономии инструмента и т. д.
1.8 Выбор технологических баз и оценка точности базирования
При выборе баз следует учитывать основные принципы базирования. В общем случае полный цикл обработки детали происходит при последовательной смене баз. Однако при уменьшении погрешности обработки деталей нужно стремиться к уменьшению переустановок заготовок при обработке.
На операции 005 фрезерно-центровальной для обработки торцовых поверхностей А и Б заготовка базируется в призмах с упором в торец В (рисунок 2.1.6). Так как заготовка имеет цилиндрическую форму то схема базирования в данное приспособление представляет собой базирование в призму с углом α = 90 то есть контакт поверхности с приспособлением происходит по двум точкам. Угол призмы обусловлен габаритами заготовки чем больше угол призмы тем меньше погрешность базирования. Для двух отверстий получаемых центровым сверлом при данном способе базирования технологическая и измерительная базы не совпадают следовательно погрешность базирования будет равна (при α=90) [26 с.107]:
При получении отверстия 12+043 погрешность базирования равна:
При получении отверстия 63+036 погрешность базирования равна:
Для осевого размера L1 = 408-063 измерительные базы не совпадают с технологической. Поэтому в осевом направлении возникает погрешность базирования равная допуску на размер заготовки L2 = 178±1 но она не влияет на получение размера L1 так как он зависит только от расстояния между фрезами производящими параллельную обработку торцов. Следовательно точность обработки в размер L1 обеспечивается наладкой режущих инструментов и не зависит от базирования б = 0 [26 с.45]. После чистовой обработки торца детали принимаем поверхность А в качестве настроечной базы. Следовательно при обработке поверхности Б настроечная и измерительная базы совпадают а значит б = 0.
Рисунок 2.1.6 – Схема базирования на операции 005 фрезерно-центровальной
На операции 015 токарная с ЧПУ заготовка базируется в 2-х кулачковом патроне с упором торцом и в центрах (рисунок 2.1.7). Следовательно погрешность базирования для всех диаметральных размеров будет равна нулю. Для размера 1 погрешность базирования также будет равна нулю так как технологическая и измерительная базы совпадают. Для размера 2 погрешность базирования будет равна допуску на длину вала б =063 мм.
Рисунок 2.1.7 – Схема базирования на операции 015 токарная с ЧПУ
На операции 040 заготовка базируется в приспособлении с упором торцом (рисунок 2.1.8).
Погрешность базирования при обработке отверстия 63+036 равняется
Погрешность базирования для осевого размера равна 0.
Рисунок 2.1.8 – Схема базирования на операции 040 вертикально-сверлильной
1.7 Выбор методов обработки
Выбор метода обработки зависит от конфигурации детали ее габаритов точности и качества обрабатываемых поверхностей вида принятой заготовки. Окончательное формообразование размеры и качество обработанных поверхностей в машиностроении преимущественно достигаются обработкой резанием.
Решение задач выбора метода и конкретного вида обработки облегчается при использовании справочных таблиц экономической точности обработки в которых содержатся сведения о технологических возможностях обработки резанием различными методами. С помощью этих таблиц можно выбрать метод окончательной обработки и наметить виды промежуточной [26 с.79].
Рисунок 2.1.9 – Эскиз детали
В качестве метода обработки принимаем резание.
Нарезать резьбу М42х2-6h () параметр шероховатости поверхности Ra 5(рисунок 2.1.9 поверхность 1).
Выполнение требований к точности и требуемой шероховатости поверхности можно обеспечить одним из следующих вариантов нарезания резьбы:
Фрезерование резьбы является одним из наиболее производительных методов обработки резьбы. Недостатком гребенчатых фрез является искажение угла профиля нарезаемой резьбы. Однако величина этого искажения мала и обычно укладывается в поле допуска.
Достоинством нарезания резьбы резцом является простая его конструкция технологичность и универсальность. Однако этот метод низкопроизводительный.
При вихревой обработке резьба получается абсолютно без заусенцев высокой точности с высоким качеством поверхности. Однако это дорогой метод за счет сложной наладки.
Шлифовальным кругом:
Шлифование резьбы выполняют чаще всего после термической обработки заготовок. Достоинством этого метода является низкая стоимость шлифовального круга и доступность оборудования. Однако небольшая частота вращения (n=3 10 мин -1) низкая стойкость круга и необходимость его профилировать замедляют обработку резьбы. А также на обрабатываемой поверхности образуются прижоги и абразивная пыль.
Очень непроизводительный метод обработки. Требуется большая затрата сил сложное врезание. Основной недостаток плашек – это необходимость свинчивания их по окончанию резания что производительность и несколько ухудшает качество резьбы.
В данном случае оптимальным методом обработки может быть нарезание резьбы шлифовальным кругом.
Обработка наружных шлицев z= 19 выдерживая размер параметр шероховатости поверхности Ra 5 (рисунок 2.1.9 поверхность 2)
Выполнение требований к точности и требуемой шероховатости поверхности можно обеспечить одним из следующих вариантов:
Достоинством этого метода является высокая производительность. Сравнительно низкая стоимость инструмента и доступность оборудования.
Стойкость роликов низкая и накатка коротких шлицев нецелесообразна. В процессе накатывания поверхностные слои металла сильно наклепываются причем наклеп распространяется на значительную глубину.
В данном случае оптимальным методом обработки может быть шлицефрезерование.
Обработка зубчатого колеса m=5 z=15выдерживая размер (рисунок 2.1.9 поверхность 3).
Фрезерование более производительно и более точно. При долблении погрешность приходится на последний зуб.
В данном случае оптимальным методом обработки может быть зубофрезерование.
1.9 Выбор варианта технологического маршрута по критерию минимальной себестоимости
Прежде чем принять решение о методах и последовательности обработки отдельных поверхностей детали и составить технологический маршрут её изготовления необходимо определить себестоимость обработки по отдельным вариантам и выбрать наиболее рациональный из них для данных условий производства. Критерием оптимальности является минимум приведенных затрат на единицу продукции 27 с.39.
Рассмотрим операции 045 где производится резьбофрезерование. В качестве проектного варианта предлагаем вместо резьбофрезерования для нарезания резьбы применять многониточный шлифовальный круг. Это позволит сократить время на обработку. А также операции 030 и 095 где производится шлицефрезерование и шлицешлифование соответственно. В качестве проектного варианта предлагаем заменить обе операции на одну 030 шлиценакатную. Далее сравним два варианта по другим параметрам.
Рассмотрим 2-а варианта технологического процесса:
Таблица 2.1.13 – Базовый и предлагаемый варианты обработки
5 резьбошлифовальная
Продолжение таблицы 2.1.13
Определяем стоимость механической обработки базовых операций 045резьбофрезерной 030 шлицефрезерной 090 шлицешлифовальной.
Часовые приведенные затраты
Sп.з = Sз + Sч.з. + Ен (Кс + Кз)(2.1.26)
где Sз – основная и дополнительная заработная плата с начислениями руб.ч;
Sч.з. – часовые затраты на эксплуатацию рабочего места руб.час;
Ен – нормативный коэффициент экономической эффективности капитальных вложений (Ен =015);
Кс Кз – удельные часовые капитальные вложения соответственно в станок и здание руб.час;
Sз = Стр к у(2.1.27)
где – коэффициент к часовой тарифной ставке =266;
Стр – часовая тарифная ставка станочника-сдельщика соответствующего разряда Стр= 1850 руб.час;
к – коэффициент учитывающий заработную плату наладчика к =11;
у – коэффициент штучного времени учитывающий оплату труда рабочего у =1
Sз = 266*1850*11*1 = 5400 руб.час
Часовые затраты на эксплуатацию рабочего места:
Sч..з. = Sч.з.б.п. kм.φ114(2.1.28)
где Sч.з.б.п. – практические часовые затраты на базовом рабочем месте
Sч.з.б.п. = 1360 руб.час
kм – коэффициент показывающий превышение затрат связанных с работой данного станка по сравнению с базовым. kм=12 [Бабук прил4].
φ – поправочный коэффициент:
φ = 1+033*(1-025)025=199
Sч..з.=1360*12*199114= 2850 рубчас
Далее считаем капитальные вложения в станок:
где Fэ – эффективный годовой фонд времени работы станка час;
Ц – балансовая стоимость станка руб.;
з – коэффициент загрузки оборудования;
Кс=213850004055*025=21095 рубчас
Далее считаем капитальные вложения здание:
Кз = Цпл.зд. АFэ з(2.1.30)
где Цпл.зд – стоимость 1 м2 площади механического цеха руб.;
А – производственная площадь станка с учетом проходов м2;
где: a – площадь станка м2; ka – коэффициент учитывающий дополнительную производственную площадь.
Кз = 375000*844055*025 = 3107 рубчас
Теперь подсчитаем формулу 8.1:
Sп.з = 5400+2850+015*(21095+3107) = 11880 руб.
Технологическая себестоимость операции механической обработки:
- штучно-калькуляционное время мин; - коэффициент выполнения норм =13 [2 84].
Расчеты остальных операций сведем к таблице 2.1.14.
Таблица 2.1.14 – Расчет технологической себестоимости операций механической обработки
Обработка на шлифовальном станке 5К822В
Обработка на шлиценакатном станке Grob ZRMe 9
Обработка на резьбофрезерном станке 5К63
Обработка на шлицефрезерном станке 5Б352ПФ2
Обработка на шлицешлифовальном станке МШ355
Таблица 2.1.15 – Сравнение вариантов технологического маршрута
Поперечно-клиновая прокатка
Стоимость заготовки руб.
Обработка на резьбофрезерном станке МШ355
Технологическая себестоимость обработки руб.
Приведенная годовая экономия:
ЭГ = (70348-56027)·18000 = 257778 млн. руб.
Исходя из расчетов принимаем следующую последовательность технологического процесса изготовления детали «Вал-шестерня» (таблица 2.1.16).
Таблица 2.1.16 – Принятый технологический процесс изготовления детали «Вал-шестерня»
Наименование операции
контроль операционный;
Продолжение таблицы 2.1.16
термическая обработка;
Из приведенных выше расчетов видно что применение предлагаемого варианта технологического процесса экономически выгодно по затратам т.к. в год экономится 257778 млн. руб. Следовательно выгодно использовать предложенную технологическую операцию.
1.10 Расчет припусков на механическую обработку
Рассчитаем припуск на диаметр расчетно-аналитическим способом согласно [26 с.95] а на остальные поверхности назначим согласно ГОСТ 26645-85. Заготовкой является прокат. Технологический маршрут обработки наружной поверхности состоит из следующих операций: точение черновое и чистовое шлифование. Расчет приведем в таблице 2.1.17.
Таблица 2.1.17 – Расчет припусков и предельных размеров по техническим переходам на обработку
Технологический переход обработки цилиндра
Элемент припуска мкм
Расчетный размер dp мм
Предельный размер мм
Предельное значение припуска мм
Пользуясь рабочим чертежом детали и картой техпроцесса запишем в таблицу 2.1.16 значения Rz h ρ для каждого перехода. Суммарное значение пространственных отклонений поверхности находим по формуле [26 таб. 4.28]:
Суммарное значение пространственных отклонений для заготовки данного типа определиться по формуле
к – удельная кривизна заготовок [26 таб.4.29].
Остаточные пространственное отклонение:
после предварительного обтачивания 1=006*1120=672 мкм
после окончательного обтачивания 2=004*1120=448 мкм
после шлифования мкм
Минимальное значение межоперационных припусков:
z min = 2(+ hi-1+ i-1) (2.1.36)
z min2 = 2(150+250+1120) = 2*1520 мкм.
z min3 = 2(50+50+672) = 2*167 мкм.
z min4 = 2(30+30+448) = 2*105 мкм.
dp3 = 59971+0210 = 60181 мм;
dp2 = 60181+0334 = 60515 мм;
dp1 = 60515 + 3040 = 63555 мм;
Наибольший предельный диаметр:
D maxi = Dmini + i(2.1.37)
D max1 = 63555 + 24 = 65955 мм
D max2 = 60515 + 04 = 60915 мм
D max3 = 60181 + 012 = 60301 мм
Предельные значения припусков:
z min3 = 60181 – 59971 = 0210 мм.
z max2 = 60301 – 5999 = 0311 мм.
Проверяем правильность выполнения расчетов:
Рисунок 2.1.10 – Схема графического расположения припусков допусков и предельных размеров диаметр мм
1.11 Расчет режимов резания
Произведем расчет режимов резания расчетно-аналитическим способом по [28] на операцию 045 – резьбошлифовальную и операцию 030 – шлиценакатная а на остальные операции – по нормативным данным.
Операция 030 Шлиценакатная
Рисунок 2.1.11 – Схема резания при шлиценакатывании
Материал по КД – сталь 20ХН3А ГОСТ 4543-71.
Твердость материала перед накаткой шлицев 255НВ.
1Станок Grob ZRMe 9 метод накатки – вытягивание встречное накатывания.
2Ролики 1990-4139 материал сталь Р6М5.
Минутная подача Sмин=107 мммин по паспорту станка
Частота вращения роликов n=1888 мин-1 по паспорту станка
Машинное время при максимальной длине шлиц L=68 мм состовляет:
Операция 045 Резьбошлифовальная
Рисунок 2.1.12 – Схема резания при резьбошлифовании
Исходные данные: круг 4-350х8х160-3 25А 12 М3 9 В5 35 мс Акл1; твердость обрабатываемого материала 255 (сталь 20ХН3А ГОСТ 4543-71.
Определяем глубину резания: [29 с.276]
Подача при резьбошлифовании равна шагу шлифуемой резьбы:
Определение скорости резания круга V в мс и скорости детали V в ммин и частоту вращения n число оборотов в минуту:
Скорость резания равна:
Частота вращения круга равна:
Скорость детали принимаем:
Частота вращения по паспорту станка:
Определяем основное время
Расчет режимов резания и основного времени для всех остальных технологических операций рассчитаем по [28] и результаты приведем в таблице 2.1.18.
Таблица 2.1.18 – Расчет режимов резания и основного времени
Наименование операции позиции перехода
5 фрезерно-центровальная
Фрезеровать торцы одновременно
Сверлить центровые отверстия
Продолжение таблицы 2.1.18
0 вертикально-сверлильная
Притереть центровое отверстие
5 круглошлифовальная
Шлифовать поверхность
0 круглошлифовальная
Шлифовать поверхность с подшлифовкой торца
1.12 Расчет технической нормы времени
В крупно серийном производстве норма штучного времени определяется по формуле:
Тшт = То + Тв + Тоб + Тот (2.1.44)
где То – основное время мин;
Тв – вспомогательное время состоит из затрат времени на отдельные приёмы:
Тв = (Ту.с. + Туп + Тиз)*k (2.1.45)
Ту.с – время на установку и снятие детали мин;
Туп – время на приёмы управления мин;
Тиз – время на измерение детали мин;
k – приведенный коэффициент выбирается в зависимости от такта выпуска;
Тоб – время на обслуживание рабочего места состоит из времени на организационное обслуживание Торг и времени на техническое обслуживание рабочего места Ттех:
Тоб = Торг. + Ттех(2.1.46)
Тот – время перерывов на отдых и личные надобности мин;
Произведем расчет для резьбошлифовальной операции:
Исходные данные для расчета:
Производство – поточное крупносерийное;
Масса детали –112 кг;
Основное время – 16 мин.
Расчет ведется по формуле для крупносерийного производства:
Определяем время на установку и закрепление заготовки определяем по приложению 5 [27].
Ту.с определяем по приложению 5. таблица 5.6 [27 с.199]:
Заготовка устанавливается в патрон и поджимается задним центром:
Время на управление станком:
Туп =001*2 + 008 + 006 + 003 = 019 мин
Время на измерение: Тиз = 025 мин
Определяем вспомогательное время:
Тв = (016. + 019 + 025)= 06 мин
Оперативное время определяется по формуле:
Топр = Тв + То(2.1.47)
Топр = 06+ 16 = 22 мин
Определяем время на обслуживание рабочего места:
Тоб = Торг. + Ттех(2.1.48)
Торг. = 22*18100 = 00396 мин
Ттех = 16*6100 = 0096 мин
Следовательно:Тоб = 00396+0096 = 0136 мин
Определяем время отведенные на личные надобности и отдых:
Тот = 006* Топр = 006*22 = 0132 мин
Определяем штучное время:
Тшт = 16+06+0136+0132 = 247 мин
Результаты определения Тшт записываем в таблицу 2.1.19
Таблица 2.1.19 – Сводная таблица технических норм времени по операциям
Номер и наименование операции
1.13 Определение необходимого количества оборудования и его
Каждое инженерное решение должно оцениваться как с технической так и с экономической точек зрения. К числу технических показателей технологических процессов относятся в частности погрешность изготовления качество поверхности долговечность деталей к экономическим – трудоемкость и себестоимость получения заготовок и их механической обработки расходы на эксплуатацию изделий. Экономические показатели например устанавливать оптимальную точность обработки параметры шероховатости поверхности детали при минимальной себестоимости оснастки [26 с.187].
Правильный выбор оборудования определяет его рациональное использование. При выборе станков для разработанного технологического процесса этот фактор должен учитываться таким образом чтобы исключить их простой.
Для каждого станка в технологическом процессе должны быть подсчитаны коэффициенты загрузки и использования станка по основному времени. Расчет приведем для операции 045 а все остальные подсчеты сведем в таблицу 2.1.20.
Количество единиц оборудования можно определить по следующей формуле [26 с.187]:
mp = Tшт.кNг (60Fэ)(2.1.49)
где - штучное время мин; - годовая программа выпуска
FЭ – эффективный годовой фонд времени работы единицы оборудования FЭ= 4055 ч [26 с.218].
mp = 247*18000(60*4055) = 018
Коэффициент загрузки станка определяется отношением (рисунок 2.1.13):
где mПР – округленное в большую сторону расчетное значение mP.
Коэффициент использования оборудования по основному времени (рисунок 2.1.14):
о = То Тшт.к.(2.1.51)
Данный коэффициент характеризует уровень механизации технологической операции. Определяем средний коэффициент загрузки станка:
з.ср =зi mпрi(2.1.52)
Определяем средний коэффициент использования оборудования по основному времени: o.ср =oi mпрi (2.1.53)
Таблица 2.1.20 – Расчет коэффициентов использования оборудования
Рисунок 2.1.13 - Диаграмма загрузки оборудования
Рисунок 2.1.14 – Диаграмма использования оборудования по основному времени
Проанализировав диаграммы можно сделать вывод о том что на операциях 005 085 и 095 доля основного времени ниже нормы. Из этого следует что для уменьшения доли вспомогательного времени на этих операциях необходимо применять автоматизированные приспособления элементы для крепления инструмента и т.д.
1.14 Проектирование и расчет станочного приспособления
Современные механосборочные цеха располагают большим парком приспособлений. В крупносерийном и массовом производстве на каждую обрабатываемую деталь приходится в среднем десять приспособлений. Наиболее значительную их долю (80 – 90 процентов общего парка приспособлений) составляют станочные приспособления применяемые для установки и закрепления обрабатываемых заготовок.
Использование приспособлений способствует повышению производительности и точности обработки сборки и контроля; облечению условий труда сокращению количества и снижению необходимой квалификации рабочих; строгой регламентации длительности выполняемых операций; расширению технологических возможностей оборудования; повышению безопасности работы и снижению производственного травматизма.
Применение быстродействующих и автоматизированных приспособлений совместно с управляющими и транспортирующими устройствами является одним из эффективных направлений автоматизации универсального технологического оборудования способствует внедрению многостаночного обслуживания и высвобождению рабочих.
Выбор приспособления зависит от вида и масштаба производства формы заготовок точности их размеров и технических условий на изготовление деталей.
В массовом и крупносерийном производстве характерно применение специальных приспособлений. Они обеспечивают стабильно заданную точность обработки способствуют быстрой и надежной установке заготовки на обработку и строгой регламентации длительности отдельных приемов связанных с выполнением технологических операций.
На станке модели 2С132 (операция 040 вертикально-сверлильная) при обработке двух отверстий с пересекающимися осями используется приспособление с эксцентриковым зажимом.
Особенности конструкции приспособления.
Заготовка базируется по цилиндрической поверхности в призмах фиксируется при помощи прижимной планки и эксцентрикового механизма. Кондукторная плита неподвижная. В качестве элементов определяющих положение и направление движения инструментов используются кондукторные втулки – постоянная и быстросменная.
К столу станка кондуктор крепиться неподвижно при помощи болтов.
Расчет точности приспособления
При расчете точности необходимо определить погрешность изготовления и сборки элементов приспособления в зависимости от параметров заданных в чертеже детали а именно: допуск на размер 7мм от плоскости торца вала до центра отверстия 63мм – ±018мм (рисунок 2.1.15).
Рисунок 2.1.15 – Схема базирования заготовки на операции 040 Вертикально-сверлильная
Для выполнения точностных расчетов составим схему (рисунок 2.1.16) на которой покажем элементы определяющие положение и направление движения инструмента – кондукторные втулки а также режущий инструмент – сверло.
Рисунок 2.1.16 – Схема для расчета точности кондуктора
Допуск на диаметр отверстия быстросменной кондукторной втулки для прохода сверла 63 мм установлен по посадке F8 ( ) [31].
Допуск на неточность изготовления сверла 63 мм составляет -0036 мм.
Посадка сменной кондукторной втулки в постоянную – [32]
Определим допустимую погрешность изготовления кондуктора обеспечивающую получение размера 7±018мм по формуле:
≤ [1 - ( S + е ) ] (2.1.54)
где 1 – допуск на размер заданный на чертеже детали мм; S - сумма зазоров мм; е - сумма эксцентриситетов мм.
Сумма зазоров для данного случая определится по формуле:
S = S1 + S2 (2.1.55)
где S1 S2 – максимальные зазоры между быстросменной втулкой и сверлом между постоянной и быстросменной втулками соответственно.
Рисунок 2.1.17 – Схема полей допусков
Максимальный зазор между инструментом и быстросменной втулкой определяется исходя из величин полей допусков на данные элементы:
S1 = 0035 + 0036 = 0075 мм
Максимальный зазор между постоянной втулкой и быстросменной втулкой определяется исходя из величин полей допусков на данные элементы:
S2 = 0018 + 0017 = 0035 мм
Тогда S = 0075 + 0035 = 011 мм
Эксцентриситет быстросменной кондукторной втулки принимаем е=0005.
Использование винтовых зажимных механизмов позволяет снизить погрешность закрепления детали поэтому принимаем эту погрешность равную нулю.
Таким образом допустимая погрешность обработки кондуктора обеспечивающая получение размера 7±018мм составит:
= 036 – (011 + 0005) = 0245
Следовательно необходимая точность будет обеспечена.
Расчет усилия зажима
Для обеспечения надёжного закрепления детали при обработке необходимо чтобы с помощью зажимных элементов и устройств базовые поверхности детали были прижаты к опорным элементам.
При выполнении сверления будет возникать крутящий момент который будет стремиться повернуть заготовку относительно оси обрабатываемого отверстия (рисунок 2.1.18)
Рисунок 2.1.18 – Схема действия сил резания и зажима
Момент кручения находим по формуле [29 с.277]
Мкр = 10СМDqSyKp Нм(2.1.56)
Где СМ = 00345;q = 2; y = 08; Kp= KМp
Мкр = 10003456520108085 = 17 Нм
Рассчитываем необходимое усилие зажима детали для чего составим уравнение [31 с.22]:
где r – радиус сверла;
– коэффициент запаса рассчитывается применительно к конкретным условиям обработки [31 с.199].
Кзап =k0k1k2k3k4k5k6 (2.1.61)
где k0 =15 – гарантированный коэффициент запаса для всех случаев;
k1 – коэффициент учитывающий состояние поверхностей заготовок – для чистовой заготовки k1 =1;
k2 – коэффициент учитывающий увеличение сил резания от прогрессирующего затупления инструмента для сталей k2 =1;
k3 – коэффициент учитывающий увеличение сил резания при прерывистом резании. k3 =1;
k4- коэффициент учитывающий постоянство силы зажима развиваемой силовым приводом приспособления k4=13;
k5 – коэффициент учитывающий эргономику ручных зажимных элементов – для ручного привода с удобным расположением рукоятки k5 = 1;
k6 – коэффициент учитываемый только при наличии крутящих моментов стремящихся повернуть обрабатываемую деталь k6 = 1 – обрабатываемая деталь установлена базовой плоскостью на опоры с ограниченной поверхностью контакта.
Кзап =151111311 = 195
Если в результате расчета значение коэффициента запаса окажется меньше 25 то его принимают равным этой величине [31 с.207]. Таким образом принимаем Кзап = 25
Рисунок 2.1.19 – Схема для определения сил действующих на эксцентрик
Эксцентрик (рисунок 2.1.19) используемый в конструкции кондуктора развивает усилие зажима которое рассчитывается по формуле:
где Q – исходная сила развиваемая эксцентриком [31 с.22];
Сила Q рассчитана для двух эксцентриков поэтому делим ее на два:
По таблице определяем основные размеры эксцентрика Q = 164 кН. Подставляем в формулу 2.1.50 и определяем обеспечиваемое усилие зажима.
Так как в приспособлении 2 эксцентрика то необходимо данную силу умножить на два:
W = 1463.7*2 = 29274 Н
Таким образом усилие зажима развиваемое эксцентриковым механизмом используемым в конструкции приспособления больше расчётного значения и поэтому удовлетворяет условию W ≤ [W].Определяем основные размеры эксцентрика по таблице (рисунок 2.1.20).
Рисунок 2.1.20 – Основные размеры эксцентрика
2 ЭКОНОМИЧЕСКИЙ РАЗДЕЛ
2.1 Расчет величины инвестиций
Среднее значение нормативного коэффициента загрузки оборудования (kнз) по участку при двухсменной работе для серийного производства равен 075.
Фактический средний коэффициент загрузки оборудования kфз=032; kфз=029 для проектного варианта в соответствии с пунктом 2.1.13.
Расчеты экономического раздела будем вести по [33] и [34].
Капитальные вложения в здание
Стоимость части здания занимаемой участком или поточной линией определяется исходя из величины производственной площади и цены 1 м2. Величину капитальных вложений в здание можно определить по формуле 2.2.1. Расчеты сводятся в таблицы Г1 и Г2 в приложении Г.
Цпл – цена 1 м2 производственной площади без учета НДС; принимается по рыночной стоимости на момент проведения расчетов);
– коэффициент учитывающий дополнительную площадь зависит от площади занимаемой станком;
kзi – коэффициент загрузки оборудования определяется в соответствии с пунктом 2.1.13.
Капитальные вложения в технологическое оборудование
Величину капитальных вложений в технологическое оборудование (машины и оборудование) можно определить исходя из количества оборудования конкретных видов и моделей и цены единицы оборудования.
Цены на оборудование устанавливаются по прейскурантам. К прейскурантной цене добавляются затраты транспортировку оборудования от поставщика до потребителя затраты на проведение монтажных работ и прочие расходы. Расчет ведется по формуле:
kтр – коэффициент учитывающий транспортные расходы (kтр=005 008);
kм – коэффициент учитывающий расходы на монтаж оборудования (kм=005 007);
kф – коэффициент учитывающий устройство фундамента под оборудование;
Коэффициент kф применяется только в случае устройства отдельного фундамента под конкретное оборудование. В настоящее время основная масса оборудования устанавливается на бетонные полы без сооружения специального фундамента в этом случае kф=0.
Полученные результаты сводятся в таблицы Г3 Г4.
Капитальные вложения в транспортные средства
В качестве транспорта в цеху малых серий используются тракторы-погрузчики кран-балка. Цены на транспортные средства принимаются по прейскурантам и капитальные вложения рассчитываются с учетом затрат на транспортировку и монтаж с учетом и без учета НДС как для капитальных вложений в технологическое оборудование (таблицы Г5 и Г6).
Капитальные вложения в универсальную технологическую оснастку и инструмент
Капитальные вложения в дорогостоящий инструмент и технологическую оснастку учитывают только те единицы оснастки которые во-первых относятся к инструментам и приспособлениям общего назначения во-вторых имеют срок службы более года в-третьих обладают ценой за единицу превышающей установленную Министерством финансов величину (таблица Г7).
Расчёт нормы расхода режущего инструмента j-го типоразмера на i-ой операции осуществляется по следующей формуле:
Тизн j – время полного износа инструмента j-го наименования ч;
kуj – коэффициент случайной убыли j-го инструмента.
Время полного износа инструмента определяется по следующей формуле:
где tст – стойкость инструмента между двумя заточками ч;
n – число допустимых заточек данного инструмента
Расчёт нормы расхода для измерительного инструмента j-го наименования осуществляется по следующей формуле:
где с – необходимое количество измерений на одну деталь;
kвыб – доля деталей подвергаемых выборочному контролю;
mo – количество измерений выполняемых с помощью инструмента до полного его изнашивания.
Годовой расход режущего абразивного и измерительного инструмента j-го типоразмера рассчитывается по следующей формуле:
где К0 – количество операций;
Nв – программа выпуска деталей шт.;
Нij - нормы расхода инструмента j-го типоразмера на i-ой операции.
Капитальные вложения в производственный инвентарь
К производственному инвентарю относится оргоснастка на рабочих местах: столы-верстаки стеллажи столы контрольные шкафы для инструмента и другое (таблицы Г8 и Г9).
Результаты расчета величины инвестиций в основные средства сведены в таблицу 2.2.1.
Таблица 2.2.1 – Инвестиции в основные средства млн. руб.
Категория инвестиций
Капитальные вложения в оборудование
Капитальные вложения в инструмент и оснастку
НДС при приобритении основных средств
Инвестиции в основные средства с учетом НДС
2.2 Расчет текущих затрат на объем выпуска продукции (расчет
себестоимости продукции)
Расчет затрат по статьям «Сырье и материалы» и «Возвратные отходы»
В статью «Сырье и материалы» включаются затраты на сырье и основные материалы (прокат поковки литые заготовки из чугуна или стали). В эту статью также включаются затраты на вспомогательные материалы используемые на технологические цели (смазочно-охлаждающие жидкости). Затраты на основные и вспомогательные материалы рассчитываются на деталь прямым путем исходя из утвержденных норм расхода на единицу продукции и цены этих материалов.
Расчет величины реализуемых отходов в натуральных показателях можно произвести по формуле:
Мотх=(Вчр – Вчст)(1-) N(2.2.7)
где Вчр – масса заготовки;
Вчст – чистая масса детали;
– доля безвозвратных потерь (принимается 002);
N – годовой объем выпуска деталей.
Для базового варианта: Мотх= (166–112)*(1-002)*18000=95 256 кг
Для проектного варианта: Мотх= (14 – 112)*(1-002)*18000=49 392 кг
Затраты на основные материалы за вычетом возвратных отходов на годовой объем производства определяются по формуле:
kТ-З – коэффициент учитывающий транспортно-заготовительные расходы при приобретении материалов (11);
Цм – цена одной тонны заготовок с учетом метода их получения (без учета НДС);
n – виды основных материалов;
N – годовой объем производства продукции в натуральном выражении шт.
Цены на материалы принимаются на основе прейскурантной (оптовой) цены используемых материалов.
Для базового варианта:
Для проектного варианта:
При приобретении сырья и материалов предприятие учитывает входной НДС по каждому его виду. Величина входного НДС уплачиваемая при покупке материалов рассчитывается по формуле:
где hндс – ставка налога на добавленную стоимость hндс =18 %.
Для проектного варианта:
Общие затраты включаемые в названную статью определяются по формуле:
Расчет затрат по статье «Топливо и энергия на технологические цели»
В эту калькуляционную статью себестоимости продукции включаются затраты на топливо и энергию которые непосредственно расходуются в процессе без преобразования в механическую энергию или в другие виды энергии. Это например нагрев заготовок в печах затраты топлива для вагранок затраты электроэнергии для сварочного оборудования или для электроплавильных печей при подобных процессах.
Затраты топлива и энергии на технологические цели без учёта НДС определяются по формуле:
Затраты топлива и энергии на технологические цели с учётом НДС определяются по формуле:
Расчет численности и фонда заработной платы работающих
Расчет численности основных производственных рабочих
Для участков серийного производства число рабочих определяется по каждой профессии и разряду работающих исходя из трудоемкости работ:
где Nвj – программа выпуска деталей j-го наименования;
Kд – количество наименований деталей;
Ko – количество технологических операций;
Фн – номинальный годовой фонд времени работы одного рабочего (без учета потери рабочего времени); Фн=2032 ч
kв – средний коэффициент выполнения норм выработки;
kмн - средний коэффициент многостаночного обслуживания на участке.
Списочная численность производственных рабочих рассчитывается по формуле:
где Чяв – явочное число рабочих по рабочим местам (с учетом потери рабочего времени % (10-15%).
Расчет затрат по статье «Основная заработная плата производственных рабочих»
Основная заработная плата производственных рабочих – сдельщиков определяется на основе расценки по формуле:
Рд – коэффициент учитывающий премии и доплаты (14);
N – годовая программа.
Расценка на i-ю операцию определяется на основе трудоемкости и часовой тарифной ставки принятой для тарификации работы на данной операции по формуле:
kмнi - коэффициент многостаночного обслуживания учитывающий обслуживание одним рабочим несколько станков одновременно на i-й операции.
Часовая тарифная ставка i-го разряда определяется с учетом тарифного коэффициента по формуле:
где kтар.i - тарифный коэффициент i-го разряда.
Часовая тарифная ставка первого разряда рассчитывается:
где МЗП1р - минимальная заработная плата рабочего первого разряд;
Фмес - среднемесячное количество часов работы одного рабочего устанавливаемый Министерством труда и социальной защиты на текущий год Фмес = 168 ч;
kув - коэффициент увеличения.
Дополнительная заработная плата определяется в процентах от основной заработной платы по формуле:
где НД – норматив дополнительной заработной платы по отношению к основной НД =20 %.
Суммарный фонд заработной платы (ФЗП) производственных рабочих на год:
Итоги расчета годового фонда заработной платы основных рабочих сведём в таблицу Г10.
Среднемесячная заработная плата основных производственных рабочих рассчитывается по формуле:
где Чяв - явочная численность основных производственных рабочих;
ФЗП – годовой фонд заработной платы производственных рабочих млн. руб.
Расчет затрат по статье «Отчисления в бюджет и внебюджетные фонды от средств на оплату труда»
Отчисления от средств на оплату труда в бюджет и внебюджетные фонды определяются по формуле:
где – ставка отчислений на государственное страхование в фонд социальной защиты населения (34 %);
– ставка отчислений на обязательное страхование от несчастных случаев (1 %).
Расчет заработной платы вспомогательных рабочих и служащих
Для вспомогательных рабочих годовой фонд заработной платы с отчислениями рассчитывается по формуле (таблица Г11):
ФЗПвсп = РдФраб эфЧвсп.спiЧТСi(1 + НД100)(1+ННО100) млн.руб. (2.2.21)
Рд – коэффициент учитывающий премии и доплаты к тарифному фонду вспомогательных рабочих Рд=12-15;
Фрабэф – годовой эффективный фонд времени работы одного рабочего (1789 ч);
Нд – норматив дополнительной заработной платы по отношению к основной Нд = 20 %;
Нно – ставки отчислений от средств на оплату труда Нно = = 35%.
Годовой фонд заработной платы служащих (руководителей и специалистов) рассчитывается исходя из численности среднемесячных окладов и среднего числа месяцев работы с учетом дополнительной заработной платы по формулам:
где ЗП - среднемесячная заработная плата специалистов (принимается в среднем для данной категории работников по рассматриваемому предприятию): ЗП =0896090 млн. руб.;
Ч сл - численность специалистов (принимается в процентах от численности основных и вспомогательных) чел.;
М сл – среднее число месяцев работы специалистов М сл = 114 месяцев.
Полученные результаты сведены в таблицу Г12.
Для базового и проектного варианта:
Отчисления от средств на оплату труда в бюджет и внебюджетные фонды от средств на оплату труда служащих:
для базового и проектного варианта:
Среднемесячная заработная плата по участку рассчитывается по формуле:
где - сумма фондов заработной платы
i= 1 – k - категория работников.
Расчет затрат по статье «Общепроизводственные расходы»
Эта статья затрат (Собщепр) включает в себя:
расходы по содержанию и эксплуатации оборудования (РСЭО);
расходы по организации обслуживанию и управлению производством.
Величина годовых амортизационных отчислений определяется на основе годовых норм амортизации и первоначальной стоимости соответствующих элементов основных средств по формуле (таблица Г13):
mТn - соответственно количество металлообрабатывающего оборудования; количество технологической оснастки количество подъемно-транспортных средств.
Нормы амортизационных отчислений рассчитываются по следующей формуле:
где Тп.и.i – срок полезного использования i-го элемента основных средств
kдиф – коэффициент корректировки срока службы kдиф= 1.
Амортизация цеховых (производственных и административных) зданий сооружений инвентаря определяется по формуле:
где – норма амортизации здания = 001;
- норма амортизации инвентаря = 0057;
Кинв – первоначальная стоимость производственного инвентаря млн.руб.
Результаты расчёта затрат по статье «Общепроизводственные расходы» сведены в таблицу Г14.
Расчет затрат по статье «Общехозяйственные расходы»
Величина общехозяйственных расходов (Рох) может быть рассчитана по следующей формуле:
где Сз.осн - фонд основной заработной платы производственных рабочих млн.руб.;
Нох - норматив общехозяйственных (заводских) расходов к трудовым затратам по данным базового предприятия Нох = 50-100 %.
Расчет затрат по статье «Расходы на реализацию»
Расходы на реализацию включают расходы на рекламу участие в выставках маркетинговые исследования и прочее. В условиях проекта можно рассчитать укрупненно как 1 % от общей производственной себестоимости продукции т.е.:
где Спроиз - производственная себестоимость годового выпуска продукции млн.руб.;
Нреал - норматив расходов на реализацию от производственной себестоимости Нреал = 1-4 %.
Платежи отчисления и налоги в себестоимости продукции
Данные расходы включают платежи на землю отчисления в специальные фонды (инновационный фонд) экологический налог и пр. В силу сложности прямого расчета этих налогов укрупнено эти затраты можно принять в размере 1-3 % от производственной себестоимости.
где Нпр.отч. - принятый укрупненный норматив отчислений и платежей от производственной себестоимости Нпр.отч. = 2 %.
С 1 января 2010 года в Республике Беларусь принята Особая часть Налогового кодекса определяющего порядок применения каждого из республиканских и местных налогов сборов и особых режимов налогообложения. Так налог на недвижимость входит в состав себестоимости продукции налогооблагаемая база и ставка налога не изменились и составляет 1 % от остаточной стоимости зданий сооружений.
ОСзд =КЗД–Азд..(2.2.31)
где КЗД – первоначальная стоимость зданий и сооружений в соответствии с пунктом 2.2.1 млн. руб.;
Азд – величина годовых амортизационных отчислений зданий и сооружений млн. руб.;
hнед – ставка налога на недвижимость hнед = 1%.
Результаты расчета себестоимости продукции годового выпуска приведены в таблице 2.2.2.
Таблица 2.2.2 – Себестоимость годового выпуска продукции млн. руб
Значения по вариантам
Сырье и материалы за вычетом возвратных отходов
Топливо и энергия на технологические нужды
Основная заработная плата производственных рабочих
Дополнительная заработная плата производственных рабочих
Отчисления в бюджетные и внебюджетные фонды
Общепроизводственные расходы (без амортизации)
Амортизация основных средств
Итого: цеховая себестоимость
Общехозяйственные расходы
Итого: производственная себестоимость
Расходы на реализацию продукции
Платежи отчисления и налоги в себестоимости продукции (Рпр.отч.+Ннед)
Итого: полная производственная себестоимость (Сп)
Сумма входного НДС в себестоимости по прямым затратам
Полная себестоимость продукции с НДС
Себестоимость единицы продукции определяется по следующей формуле:
где Сед.пр. – полная себестоимость единицы реализованной продукции без учета входного НДС по производственным издержкам руб.;
– себестоимость единицы продукции с учетом входного НДС по приобретенному сырью и материалам руб.;
Сп – полная производственная себестоимость продукции млн.руб.;
- сумма входного НДС по прямым затратам млн.руб.
2.3 Расчет потребности в оборотных средствах
В состав оборотных средств включаются денежные средства необходимые для создания производственных запасов основных и вспомогательных материалов комплектующих и полуфабрикатов топлива малоценных и быстроизнашивающихся предметов; образования незавершенного производства; а также для поддержания минимального запаса готовой продукции на складах участка. Все составляющие оборотных средств рассчитываются прямым счетом.
Производственные запасы
Потребность в оборотных средствах для создания производственных запасов определяется по формуле:
где Зт– величина текущего запаса т;
Ц – стоимость одной тонны материалов с учетом НДС;
Зстр – величина страхового запаса т.
Величина текущего запаса определяется по формуле:
Величина страхового запаса определяется по формуле:
где Рс – среднесуточное потребление материалов т;
Тн – норма текущего запаса в днях Тн = 20 дней;
То – количество суток на которые создается страховой запас То = 7 дней.
Среднесуточное потребление материалов определяется по формуле:
где G – потребление материала в планируемом периоде в год;
Тп – продолжительность планируемого периода (год – 360 дней).
Для базового варианта:
Аналогичным образом рассчитываются потребности в основных материалах топливе запасных частях в прочих запасах в малоценных и быстроизнашивающихся предметах (МБП).
Незавершенное производство
Норматив оборотных средств для образования незавершенного производства определяется по следующей формуле:
где – себестоимость единицы продукции с учетом НДС тыс.руб.;
Тц – длительность производственного цикла дней;
NТп – среднесуточный выпуск продукции;
Кн – коэффициент нарастания затрат.
где – материальные затраты (с учетом НДС) на единицу продукции тыс. руб.
Готовая продукция на складе предприятия
Норматив оборотных средств для создания запаса готовой продукции определяется по формуле:
где Рд – время на формирование партии отгрузки Рд = 7 дней.
Полная потребность в оборотном капитале определяется по формуле:
Для базового варианта: ОС=39423+0516+40108=80048 млн.руб.
Для проектного варианта: ОС=33249+0294+33899=67442 млн.руб.
Результаты расчетов потребности в оборотном капитале приведены в таблице Г15.
Результаты расчета общей величины инвестиций необходимых для реализации вариантов проекта сведены в таблицу Г16.
2.4 Расчет основных технико-экономических показателей
сравниваемых вариантов
Определение отпускной цены
Если деталь изготавливаемая на участке рассматривается как конечная продукция реализуемая потребителям то к цене прибавляется величина косвенных налогов.
где Сед. пр.– полная себестоимость единицы продукции руб.;
Ппл. – планируемая прибыль предприятия на единицу продукции руб.;
Нкосв – сумма косвенных налогов и отчислений в цене товара.
Планируемая прибыль на единицу продукции рассчитывается исходя из норматива рентабельности прибыли на вложенный капитал (Rе);
где Rе - норматив рентабельности единицы продукции %.
Ставки налоговых выплат по проекту и исходные данные для дальнейшего расчета сведены в таблицу Г17.
Расчет отпускной цены продукции проводится по базовому варианту технологического процесса. Порядок расчета цены сведён в таблицу Г18.
Определение прибыли предприятия
Порядок расчета прибыли от реализации и чистой прибыли предприятия после уплаты налоговых платежей сведен в таблицу Г19.
Расчет технико-экономических показателей сравниваемых проектов
Годовой экономический эффект инвестиций – это полезный результат экономической деятельности измеряемый обычно разностью между денежным доходом от деятельности и денежными расходами на ее осуществление:
где r – реальный коэффициент ставки платы за кредит r = 01;
Ко.с. – капитальные вложения в основные средства млн. руб.;
Коб.с. – инвестиции в оборотные средства млн. руб.
Период окупаемости инвестиций представляет временной отрезок использования экономического объекта в течение которого инвестиции в производство возвращаются потоком чистой прибыли рассчитывается по формуле:
где И – сумма полных инвестиционных вложений с НДС млн. руб.;
Агод – величина годовых амортизационных отчислений по элементам амортизируемых основных средств млн. руб.;
Пч – чистая прибыль млн. руб.
Рентабельность производства по чистой прибыли характеризует долю чистой прибыли предприятия получаемую на единицу инвестиций при соответственно базовом и проектном варианте инвестирования в производство продукции:
R=Пч И без НДС100%(2.2.46)
где И без НДС – величина инвестиционных вложений без НДС млн. руб.
Выработка продукции является прямым показателем производительности труда. Выработка на одного рабочего рассчитывается по формуле:
млн. руб.чел(2.2.47)
где ВРпред – выручка предприятия от реализации продукции без косвенных налогов млн. руб.;
Чосн – численность рабочих чел.
Для базового варианта: 16082 млн. руб.чел
Для проектного варианта: 23721 млн. руб.чел
Фондоотдача характеризует производство продукции в стоимостном выражении на единицу стоимости основных средств в единицу времени (один год). Она рассчитывается по формуле:
где Ф ср.г.осн – среднегодовая стоимость основных средств (принять равной величине инвестиций в основные средства без НДС млн. руб.
Для базового варианта: 108 руб.руб.
Для проектного варианта: 133 руб.руб.
Фондовооруженность труда рассчитывается как отношение среднегодовой стоимости основных средств к численности промышленно-производственного персонала:
Кво= Фср.г.осн.Чобщ.(2.2.49)
Для базового варианта: 12217 млн.чел.
Для проектного варианта: 12694 млн.чел.
Рентабельность продукции определяется по формуле:
где Преал – прибыль от реализации продукции млн.руб.;
Сп - полная себестоимость годового выпуска продукции руб.
Для базового варианта: 15%
Процент снижения трудоемкости определяется по формуле:
где Тбаз - трудоемкость детали по базовому варианту техпроцесса мин.;
Тпр - трудоемкость детали в проектируемом варианте мин.
Увеличение производительности труда за счет снижения трудоемкости:
где Те – процент снижения трудоемкости %.
Материалоемкость продукции рассчитывается как:
где См – затраты на сырье и материалы за вычетом возвратных отходов млн.руб.
Для базового варианта: рубруб
Для проектного варианта: рубруб
Рассчитанные основные технико-экономические показатели по базовому и проектному вариантам представлены в таблице 2.2.3.
Таблица 2.2.3 – Основные технико-экономические показатели проекта
Годовой объем выпуска продукции:
1В натуральном выражении
2В стоимостном выражении
Себестоимость единицы продукции
Себестоимость годового объема произведенной продукции
Численность производственных рабочих
Продолжение таблицы 2.2.3
Выработка на одного производственного рабочего
Трудоемкость изготовления продукции
Фонд заработной платы производственных рабочих
Среднемесячная заработная плата одного производственного рабочего
Прибыль от реализации продукции
Рентабельность продукции
Среднегодовая стоимость основных средств
Фондовооруженность труда
Материалоемкость продукции
Период окупаемости инвестиций
В ходе выполнения дипломного проекта в технологическом процессе механической обработки детали «Вал-шестерня» с целью снижения трудоемкости операции снижения производственных площадей и как следствие снижение себестоимости изготовления детали заменяем операции 030 и 095 «Шлицефрезерную» и «Шлицешлифовальную» соответственно на 030 «Шлиценакатную» 045 «Резьбофрезерная» на «Резьбошлифовальную». Предполагаемое усовершенствование позволяет: снизить трудоемкость на 3228%; снизить материалоемкость детали на 128% общепроизводственные расходы на 178% в следствии чего себестоимость единицы продукции снизилась на 18 108 рублей; увеличить чистую прибыль на 235416 млн.рублей.
Величина полных инвестиций в проектном варианте составила 213258млн.рублей что на 50637 млн.рублей меньше чем в базовом. Период окупаемости составил для проектного варианта 358 года что на 3 года меньше чем для базового. Рентабельность возрастает с 15% до 2606%. Таким образом внесенные изменения в технологический процесс механической обработки детали «Вал-шестерня» являются экономически выгодными.
В данном разделе рассматриваются вопросы по созданию безопасных условий труда производства детали «Вал-шестерня».
Условия труда на рабочих местах производственного помещения складываются под воздействием большого числа факторов различных по своей природе формам проявления характеру воздействия на человека.
Для технологического процесса механической обработки детали на проектируемых участках характерны опасные и вредные производственные факторы: запыленность и загазованность воздуха рабочей зоны повышенный уровень шума и вибрации недостаточная освещенность рабочей зоны травмирование при контакте с режущими и движущимися частями машин и механизмов возможность поражения электрическим током предъявляются требования к микроклимату воздуха рабочей зоны.
В соответствии с заданием на дипломное проектирование в разделе рассмотрены вопросы создания безопасных и безвредных условий труда на участке изготовления детали «Вал-шестерня». Технологический процесс на изготовление детали разработан в разделе «Инженерная часть».
При изготовлении детали «Вал-шестерня» предусматривается обработка на фрезерно-центровальном станке модели 2Г942 токарном станке модели 16А20Ф3 шлицефрезерном станке модели 5Б352ПФ2 вертикально-сверлильном станке модели 2С132 круглошлифовальном станке модели 3А161 шлицешлифовальном станке модели МШ355 зубошлифовальном станке модели 5М841Ф11 резьбошлифовальном станке модели 5К822В.
Оборудования удовлетворяют требованиям:
ГОСТ 12.2.009-99. ССБТ. Станки металлообрабатывающие. Общие требования безопасности [36].
Технологический процесс детали «Вал-шестерня» удовлетворяет требованиям:
СанПиН РБ № 11-22-94. Санитарные правила при работе со смазочно-охлаждающими жидкостями технологическими смазками и маслами: Сборник официальных документов по медицине труда и производственной санитарии. – Мн.: МЗ РБ 1998. – Ч.1.
Правила техники безопасности и производственной санитарии при холодной обработке металлов. – М.: Энергоатомиздат 1988. – 427 с.
При изготовлении детали «Вал-шестерня» на рабочих действуют вредные и опасные производственные факторы [37].
Для данного технологического процесса характерны следующие физически опасные факторы:
-режущие инструменты;
-приводные и передаточные механизмы;
-сливная (ленточная) стружка;
-отлетающая стружка и пыль металла;
-приспособления для закрепления обрабатываемого изделия;
-заготовки и готовые изделия;
-движущиеся части станков;
К физически вредным производственным факторам характерным для данного техпроцесса относятся:
-повышенная запыленность и загазованность воздуха рабочей зоны;
-высокий уровень шума и вибрации;
-недостаточная освещенность рабочей зоны;
-наличие прямой и отраженной блёсткости;
-повышенная яркость и пульсация светового потока;
-высокие влажность и скорость движения воздуха.
3.1 Производственная санитария и техника безопасности на участке изготовления детали
Вредные химические вещества вентиляция
Химически опасные производственные факторы свойственные данному технологическому процессу выделяются в процессе обработки металла резанием. Это следующие вещества:
-пары минеральных масел.
К биологически опасным факторам относятся разнообразные бактерии которые могут вызвать у работающих различные заболевания кожи (к примеру часто на руках образуются гнойнички).
В рабочей зоне при работе на токарных станках вертикально-сверлильном зубофрезерном зубодолбежном внутришлифовальном зубообкатывающем станках выделяются вредные вещества в виде паров СОЖ (эмульсии) металлическая пыль.
Абразивные и металлические пыли оказывают на организм человека раздражающее действие дыхательных путей слизистой оболочки глаз кожи а при длительном воздействии вызывают заболевания легких.
Пары СОЖ (масляной туман окись углерода) оказывают на организм человека раздражающее действия слизистых оболочек верхних дыхательных путей утомляемость головокружение отравляющее действие.
При осуществлении технологического процесса выделяются следующие вредные вещества концентрация которых не превышают ПДК. «Перечень регламентированных в воздухе рабочей зоны вредных веществ»: от 31.12.2008г. № 240 [38]:
-стальная пыль (ПДК = 6 мгм3) класс опасности 4;
-масляный туман (ПДК = 5 мгм3) класс опасности 3.
Метеорологические условия
Выполняемые на участке работы в зависимости от общих энергозатрат организма относятся к физическим работам средней тяжести (категория IIб СанПиН РБ № 9-80-98. Гигиенические требования к микроклимату производственных помещений: Сборник официальных документов по медицине труда и производственной санитарии. – Мн.: МЗ РБ 1999. – Ч. 6.) [39] – работы стоя или связанные с ходьбой и переноской тяжести более 10 кг
Допустимые микроклиматические условия для проектируемого участка механообработки;
а) для теплого времени года:
- температура 16 27 ° С;
-относительная влажность - не более 70%;
-скорость движения воздуха не более 02 05 мс;
б) для холодного времени года:
-температура 15 21 ° С;
-относительная влажность - не более 75%;
-скорость движения воздуха - не более 04 мс.
Оптимальные микроклиматические условия:
- температура 20.. .22 ° С;
- движения воздуха – не более 03 мс;
- скорость относительная влажность - не более 40.. .60%.
-температура 17 19° С;
-относительная влажность—не более 40 60%;
-скорость движения воздуха - не более 02 мс.
Интенсивность теплового облучения на рабочих местах не превышает 100Втм2 и облучению подвергаются не более 25% поверхностей тела человека что соответствует нормам [39].
Производственное освещение
Для улучшения условий зрительной работы снижения утомления травматизма на производстве повышения производительности и качества выпускаемой продукции безопасности труда в цехе предусмотрено как искусственное так и естественное освещение. К общему освещению добавляется местное на рабочих местах для соответствующих операций [40].
На проектируемом участке используется как естественное так и искусственное освещение. Искусственное освещение по своему функциональному значению является рабочим используется в темное время суток и при недостаточном естественном освещении. Естественное освещение используется в дневное время суток осуществляется через окна. Разряд зрительной работы – IIIв –высокой точности так как объект различения составляет от 030 мм до 050 мм подразряд зрительных работ – в контраст объекта различения с фоном – средний фон – средний. Нормативное значение минимальной освещенности по ТКП-45-2.04.153-2009 «Естественное и искусственное освещение. Строительные нормы. Проектирование» [40] при системе общего искусственного освещения составляет Еобщ. = 300лк.
Источниками шума на участке являются рабочее оборудование (приводы электродвигателей) и режущий инструмент (лезвийная обработка). По СанПиН 2.2.42.1.8.10-32-2002 [41] шум является широкополосным не постоянным и уровень звука за восьмичасовой рабочий день не должен изменяться во времени не более чем на 5 дБА и не превышать 80дБА. Снижение шума обеспечивается за счет динамической балансировки роторов электродвигателей применение звукоизоляции (установка звукоизолирующих кожухов и экранов).
Источниками вибрации на производственном участке являются вращающиеся неуравновешенные массы производственного оборудования. Вибрация является технологической так как возникает из-за работы стационарных машин. Для производственного участка характерно возникновение общей вибрации на рабочих местах. Это технологическая вибрация категории — 3а; ее параметры: среднегеометрическая частота – f=16 Гц виброскорость - до 1510-2 мс логарифмический уровень виброскорости— до 85 дБ что значительно ниже предельно допустимого уровня вибрации по СанПиН 2.2.42.1.10-33-2002 [39] (виброскорость до 0210-2 мс логарифмический уровень виброскорости - до 92 дБ СН РБ 9-89-98 и СН РБ 9-90-98).
Для борьбы с нежелательными вибрациями предусмотрены следующие мероприятия: фундаменты станков выполняются с акустическими разрывами заполненными пористым материалом и акустическим швом расположенными в нижней части фундамента.
Методика расчета эквивалентного уровня звука непостоянного (прерывистого) шума (шум в ступени постоянный)
Определим эквивалентный уровень звука непостоянного (прерывистого) шума по следующим исходным данным:
Таблица 2.3.1 – Исходные данные
Уровень звука по ступеням LАi дБ
Продолжительность ступени мин.
Определим поправку ΔLАi по таблице 2.3.3.
Таблица 2.3.2 – Поправки к уровням звука в зависимости от времени действия шума
Продолжительность ступени прерывистого шума мин.
для I ступени шума 30 дБА;
для II ступени шума 51 дБА;
для III ступени шума 75 дБА.
Рассчитаем уровни звука с учетом поправки т.е. LАi–ΔLАi:
для I ступени шума 80 – 30 = 770 дБА;
для II ступени шума 78 – 51 = 729 дБА;
для III ступени шума 75 – 75 = 675 дБА.
Найдем разность 2-х наиболее высоких уровней шума (для 1 и 2 ступеней):
Добавка к наиболее высокому уровню составит 15 дБА согласно таблице2.3.3.
Таблица 2.3.3 – Добавки для энергетического суммирования уровней шума
Разность двух складываемых уровней дБА
Добавка к более высокому уровню дБА
Далее рассчитаем суммарный уровень шума для I и II ступеней:
Тогда разность суммарного уровня шума на I и II ступенях и уровня шума III ступени:
Добавка согласно таблице 4 – 04 дБА.
Эквивалентный уровень непостоянного шума:
5 + 04 = 789 т.е. 79 дБА ≤ 80 дБА.
Электробезопасность (возможность поражения электрическим током)
По опасности поражения электрическим током цех относится к особо опасным помещениям в связи с наличием на участке токопроводящего бетонного пола и токопроводящей пыли (согласно ПУЭ). Для защиты от поражения электрическим током приняты следующие меры:
провода не имеющие изоляции и другие токоведущие части подвешены на высоте не менее 35 м;
конструкцией оборудования предусмотрено ограждение токоведущих частей;
для местного освещения рабочих мест применено пониженное напряжение 24 В;
двойная изоляция токоведущих частей;
защитное отключение;
применение зануления оборудования.
В процессе эксплуатации электроустановок применяют специальные средства защиты которые условно делятся на три группы: изолирующие ограждающие и предохранительные [44].
Возможность травмирования при контакте с движущимися частями машин и механизмов
При работе оборудования существуют опасные зоны:
- движущиеся части станков и механизмов;
- зоны выделения отлетающих частиц обрабатываемого материала;
- токоведущие части оборудования;
- режущий инструмент.
Для предотвращения и уменьшения действия на рабочих опасных производственных факторов а также предупреждения попадания человека в опасную зону на участке применяются защитные устройства. В качестве оградительных устройств представляющих собой физическую преграду между человеком и опасными производственными факторами на оборудовании устанавливают защитные кожухи экраны щиты. Для сведения к минимуму применяются следующие средства защиты:
- оградительные устройства (ограждаются все приводные и передаточные механизмы вращающиеся приспособления режущий инструмент и т. д.);
- предохранительные устройства которые автоматически устраняют опасность возникновения аварии;
- блокирующие устройства.
На участке применяются шлифовальные станки. Шлифовальные круги перед обработкой прошли испытания по ГОСТ 12.3.023-80 ССТБ ГОСТ 12.3.028-82.
Стружка в цеху убирается индивидуально. По внешнему виду и строению стружка подразделяется на три основных типа: сливная скалывания и надлома. На фрезерном станке стружка скалывания убирается щеткой.
Цветовая окраска станков подобрана в соответствии с указаниями по проектированию цветовой отделки машиностроительных предприятий.
Станки окрашены в зеленый цвет защитные кожухи трапы электрооборудование – в красный.
Средства индивидуальной защиты:
-очки закрытого типа;
-профилактические пасты для защиты рук;
3.2 Пожарная безопасность на участке
По НПБ 5-2005 Нормы пожарной безопасности Республики Беларусь «Категорирование помещений зданий и наружных установок по взрывопожарной и пожарной опасности» категория производства по взрывопожарной и пожарной опасности – Д так как в нем обрабатываются негорючие вещества и материалы в холодном состоянии.
По функциональной пожарной опасности цех относится к классу Ф5.1.
По огнестойкости здание цеха относится ко II-й степени огнестойкости согласно СНБ 2.02.01-98 «Пожарно-техническая классификация зданий строительных конструкций и материалов» (таблица 2.3.4) [45].
Таблица 2.3.4 – Предел огнестойкости и класс пожарной опасности строительных конструкций
Несущие элементы здания
Наружные ненесущие стены
Перекрытия междуэтажные
Элементы бесчердачных покрытий
Настилы в т.ч. с утеплителем
Марши и площадки лестниц
На производстве существуют следующие эвакуационные выходы: двери и ворота ведущие наружу.
В цехе имеется два эвакуационных выхода расположенных с двух сторон здания и ведущих на улицу. Ширина эвакуационных выходов 1500мм ширина пожарных проездов 4500мм СНБ 2.02.01-98 «Пожарно-техническая классификация зданий строительных конструкций и материалов» [46].
На данном производстве применяется противопожарное водоснабжение и первичные средства тушения пожаров. В качестве первичных средств пожаротушения на участке используются огнетушитель углекислотный ОУ-8— по одному на 600-800м2 пожарные щиты ящики с песком.
Все технологические операции обработки данной детали являются пожаробезопасными с точки зрения возможных загораний. Возможными причинами возникновения пожаров на участке являются:
-неосторожное обращение с огнем;
-короткое замыкание оборудования;
-перегрев проводов и воспламенение их изоляции;
-самовозгорание промасленной ветоши (ветошь должна храниться в специальных металлических контейнерах в специально отведенном месте);
-накапливаемое статическое электричество.
Мероприятия по пожарной профилактике:
- промасленная ветошь складируется в герметичных специальных ящиках и вывозится ежедневно;
- раз в неделю производится осмотр электрооборудования станков бригадой электриков.
Кроме того с целью предотвращение возможных пожаров на предприятии проводится целый комплекс профилактических мероприятий подразделяющихся на организационные технические режимные и эксплуатационные.
К организационным мероприятиям относят:
- вопросы касающиеся правильной эксплуатации оборудования и транспорта;
- правильное содержание зданий и сооружений а также территорий;
- противопожарный инструктаж работающих;
- организация добровольных пожарных дружин и пожарно-технических комиссий;
- издание нормативно-технической документации.
К техническим мероприятиям относят: соблюдение противопожарных норм и правил при проектировании зданий и оборудования при его монтаже и установке систем освещения вентиляции отопления.
Режимные мероприятия включают в себя: запрещение курения в запрещённым местах запрещение проведения сварочных и других огневых работ в пожароопасных помещениях.
Эксплуатационные мероприятия включают: своевременный профилактический осмотр ремонты и испытания технологического оборудования.
Своевременное проведение выше перечисленных мероприятий позволяет существенно уменьшить количество возникающих пожаров и возгораний.
Ветошь хранится в металлической таре с крышкой на которой написано «Для ветоши».
Приоритетной задачей образования является развитие и формирование у молодого человека интеллектуальных способностей которые позволили бы ему комфортно адаптироваться к быстро изменяющимся социальным условиям и создавать новое социальное пространство.
В процессе педагогического экспериментального исследования нами были решены следующие задачи: определены теоретические подходы к сущности таких понятий как «интеллект» «способности» «интеллектуальные способности»; уточнены основные методы активизации интеллектуальных способностей; разработана модель активизации интеллектуальных способностей у студентов технического вуза.
На основании полученных экспериментальных данных нами были сделаны рекомендации по активизации интеллектуальных способностей.
С целью активизации интеллектуальных способностей следует применять педагогические условия:
-Положительная мотивация учебно-познавательной деятельности;
-Организация учебно-познавательной деятельности в соответствии с принципами развивающего обучения;
-Учет индивидуально-психологических и возрастных особенностей обучаемых;
-Творческий характер учебно-познавательной деятельности;
-Приоритет гуманного демократического стиля общения в процессе управления учебно-творческой деятельностью обучаемых;
-Реализация дифференцированного обучения в процессе активизации интеллектуальных способностей;
-Сотрудничество (сотворчество) педагога и учащихся (осуществление совместных поисков условий и средств активизации интеллектуальных способностей и др.;
Формы организации учебно-воспитательной работы: диспуты семинары конференции КВН экскурсии творческие уроки факультативы индивидуальное обучение индивидуальный подход к учащимся дифференциация обучения коллективные формы обучения исследовательская и опытническая работа викторины научно-технические общества олимпиады лекции и др.;
Методы активизации интеллектуальных способностей: мозговая атака обратная мозговая атака корабельный совет синектика инновационная игра эвристическая беседа метод моделирования метод гирлянд ассоциаций и метафор и др.
В инженерной части дипломного проекта на основе анализа базового технологического процесса разработаны предложения по модернизации в результате которых достигнут ряд технико-экономических показателей. Так например: была изменена масса заготовки изменением метода получения заготовки были заменены: операция 045 резьбофрезерная на 045 резьбошлифовальная а также две операции 030 шлицефрезерная и 095 шлицешлифовальная на одну 030 шлиценакатную.
Разработана конструкция сверлильного приспособления предназначенного для установки и закрепления заготовки на вертикально-сверлильном станке 2С132 и используемого для сверления двух отверстий с пересекающимися осями.
В экономической части проекта представлено экономическое обоснование разработанного варианта технологического процесса рассчитаны величины капитальных вложений и оборотных средств для осуществления технологического процесса механической обработки проведён расчёт себестоимости единицы продукции (96 487.) рентабельности производства (2606 %) и период возврата инвестиций (358 года).
В разделе «Охрана труда» разработаны требования для участка механического цеха по обработке детали «Вал-шестерня». Приведены требования к освещению шуму электробезопасности даны рекомендации по противопожарной безопасности.
СПИСОК ИСПОЛЬЗОВАННЫХ ИСТОЧНИКОВ
Векслер Д. Исследование интеллекта дошкольников и младших школьников Д. Векслер. – М. 1966.
Веккер Л.М. Психика и реальность: единая теория психических процессов Л.М. Веккер. М. 1998
Кроль В.М. Психология и педагогика: Уч. пособие для техн. вузов В.М.Кроль – М.: Высшая школа 2001. – 319с.
Холодная М.А. Психология интеллекта: парадоксы исследования. Томск. Изд-во Том. Ун-та; М.: Барс 1997
Рубинштейн С.Л. О мышлении и путях его исследования С.Л. Рубинштейн. – М. 1958
Лобанов А.П. Интеллект и когнитивные способности А.П. Лобанов. Орша Диаль 2006. – 304 с.
Андреева И.Н. Эмоциональный интеллект: исследования феномена И.Н. Андреева Вопросы психологии. – 2006. – №3. – С. 78-86
Андреева И.Н. Предпосылки развития эмоционального интеллекта И.Н. Андреева Вопросы психологии. – 2007. – №5. – С. 57-65
Педагогическое мышление и интеллект авт.сост. В.Н. Пунчик Н.С. Самсонова. – Минск: Красико-Принт 2010. – 176с. – (Педагогическая мастерская)
Платонов К.К. Проблемы способностей. М.: Наука 1972.
Способности и склонности под ред. Голубевой Э.А. – М. Педагогика 1989.
Шадриков В.Д. Деятельность и способности. М.: Perse 1994.
Педагогика: Большая современная энциклопедия сост.
Е.С. Рапацевич. – Минск: «Современное слово» 2005. – 720с.
Ларина Т.А. Развитие интеллектульных умений студентов среднего профессионального образования: автореф. дис. канд. педагогических наук: 13.00.08 Т.А. Ларина. – СПб. 2004
Дубынина М.Г. Развитие психометрического интеллекта у студентов технического вуза: автореф. дис. канд. психологических наук: 19.00.07 М.Г. Дубынина. – Ярославль 2006. – 21с.
Гиль Л.Б. Развитие интеллектуальных умений и способности к саморазвитию студентов технического вуза в процессе математической подготовки: автореф. дис. канд психологических наук Л.Б. Гиль. – Томск 2010. – 22с
Немов Р.С. Психология. Кн1. – М. Просвещение «Владос» 1997. – 688с.
Видинеев Н.В. Природа интеллектуальных способностей человека Видинеев Н.В. – М.: Мысль 1989. – 175с.
Соколов В.Н. Педагогическая эвристика: введение в теорию и методику эвристической деятельности В.Н. Соколов. – М. 1995
Хуторской А.В. Методика личностно-ориентированного обучения. Как обучать всех по-разному: пособие для учителя А.В. Хуторской – М. 2005
Цыркун И.И. Инновационное образование педагога: на пути к профессиональному творчеству: пособие И.И. Цыркун Е.И. Карпович. – Минск 2006
Селевко Г.К. Энциклопедия образовательных технологий. В 2 т. Т. 1. М.: НИИ школьных ттехнологий. 2006. 816 с.
Айзенк Г. Новые IQ тесты. – М.: Эксмо 2003. – 192с.
Беар Ж.-М. Узнайте Ваши IQ и EQ Ж.-М. Беар и др. Журнал PSYCHOLOGIES. Июль 2007
Бабук В.В. Проектирование технологических процессов механической обработки в машиностроении В.В. Бабук [и др.]; под ред. В.В. Бабука. Минск: Выш. шк. 1987. – 255 с.
Горбацевич А.Ф. Курсовое проектирование по технологии машиностроения: Учеб. пособие для машиностроит. спец. вузов А.Ф. Горбацевич В.А. Шкред. – 4-е изд. перераб. и доп. – Минск: Выш. школа 1983. – 256 с.
Барановский Ю.В. Режимы резания металлов: Справочник Ю.В.Барановский. М: Машиностроение 1972 – 407 с.
Косилова А.Г. Справочник технолога-машиностроителя. В 2-х т. Т.2 А.Г. Косилова Р.К. Мещерякова; под ред. А.Г. Косиловой и Р.Е. Мещерякова. – М.: Машиностроение 1985. – 496 с.
Обработка металлов резанием: Справочник технолога А.А. панов В.В. Аникин. Н.Г. Бойм и др.. Под общ. Ред. А.А. Панова. – М.: Машиностроение. 1988. – 736с.
Антонюк В.Е. Конструктору станочных приспособлений.: Справ. Пособие. – Минск: Беларусь 1991. – 400с.
Ваганов В.М. Проектирование и расчет кондукторов: учебное пособие. – Псков: Издательство ППИ 2008. – 20 с.
Бабук И.М. Расчет Экономической эффективности внедрения новых технологических процессов: учебно-методическое пособие для студентов машиностроительных специальностей (курсовое и дипломное проектирование) И.М.Бабук А.А. Королько С.И. Адаменкова Е.Н. Костюкевич. – Минск: БНТУ 2010. – 52 с.
Сачко Н.С. Планирование и организация машиностроительного производства. Курсовое проектирование: учеб. пособие Н.С. Сачко И.М. Бабук. – Минск: Новое знание 2009. – 240 с.
ГОСТ 12.2.009-99 ССБТ. Станки металлообрабатывающие. Общие требования безопасности.
НПБ 5-2005. Категорирование помещений зданий и наружных установок по взрывопожарной и пожарной опасности.
СНБ 2.02.01-98. Пожарно-техническая классификация зданий строительных конструкций и материалов.
ГОСТ 12.2.009-99. ССБТ. Станки металлообрабатывающие. Общие требования безопасности.
Перечень регламентированных в воздухе рабочей зоны вредных веществ: Сборник официальных документов по медицине труда и производственной санитарии: СанПиН РБ № 11-19-94 – Минск.: МЗ РБ 1998. – Ч. 2.
Гигиенические требования к микроклимату производственных помещений: Сборник официальных документов по медицине труда и производственной санитарии: СанПиН РБ № 9-80 РБ98 – Минск.: МЗ РБ 1999. – Ч. 6.
Естественное и искусственное освещение. Строительные нормы. Проектирование: ТКП-45-2.04153-2009.
Шум на рабочих местах в помещениях жилых общественных зданий и на территории жилой застройки: СанПиН 2.2.42.1.8.10-32-2002 – Минск.: МЗ РБ 2002.
Методические указания по выполнению раздела «Охрана труда» дипломных проектов для студентов приборостроительного факультета: учебное издание М.А. Лазаренков [и др.]. – Минск.: БНТУ 2010. – 44 с. прил. 2.
ТЭП.cdw

1 В натуральном выражении
2 В стоимостном выражении
Себестоимость единицы продукции
Себестоимость годового объема
произведенной продукции
Численность производственных
Выработка на одного произ-
водственного рабочего
Трудоемкость изготовления
Фонд зароботной платы произ-
Среднемесячная заработная плата
одного производственного рабочего
Прибыль от реализации продукции
Рентабельность продукции
Среднегодовая стоимость
Фондовооруженность труда
Материалоемкость продукции
Период окупаемости инвестиций
ДП-109316.11-2011-ИЧ-06
Технико-экономические
Технико-экономические показатели проекта
Спецификация.spw

Эскизы лист №1 А1.cdw

Фреза торцовая левая
Фреза торцовая правая
выдерживая размеры 1
* Размеры для справок.
ПИ 1 Сверло центровое 2317-0009
ПИ 2 Сверло центровое 9341-83
Сверлить центровые отверстия
выдерживая размеры 2-9.
Операция 010 Токарная с ЧПУ.
Станок мод. 16А20Ф3С39
Операция 015 Токарная с ЧПУ.
выдерживая размеры 1-4
выдерживая размеры 3
Точить канавки. выдерживая размеры 14
ДП-109316.11-2011-ИЧ-03
Заготовка.cdw

степень сложности С2
исходный индекс 15 ГОСТ 7505-89.
Неуказанные радиусы 3 5 мм.
Неуказанные уклоны 7
Очистка от окалины дробью.
Остальные ТТ по ГОСТ 8473-70.
базы механической обработки.
ДП-109316.11-2011-ИЧ-02
поперечно-клиновая прокатка
Кондуктор 9671-16372.cdw

Отклонение от перпердикулярности оси поверхности Б относительно
поверхности А не более 0
Отклонение от параллельности оси поверхности В относительно
Отклонение от соосности поверхности Г относительно
поверхности Д не более 0
ДП-109316.11-2011-ИЧ-05
Эскизы лист №2 А1.cdw

Станок мод. 5Б352ПФ2
Фреза червячная 9339-386
выдерживая параметры таблицы.
Допуск на рад. биение
нормали (по 3-му зубу)
Операция 040 Вертикально-сверлильная.
-350х8х160-3 25А 12 М3 9 В5 35 мс Акл.1
Операция 045 Резьбошлифовальная.
Оперция 030 Шлиценакатная.
Станок мод. Grob ZRMe 9
Накатник роликовый специальный
выдерживая размеры 1
*Размеры обеспечить инструментом.
ДП-109316.11-2011-ИЧ-04
Сверлить 2 отверстия
Вал-шестерня 55165-1802110.cdw

Степень точности по
Предельные отклонения
измерит. межос. расст.
Толщина зуба по хорде
Высота зуба до хорды
Длина общей нормали при
Допуск на радиальное биение
зубчатого венца относительно Г
Допуск на колебание длины
Предельные отклонения шага
Допуск на погрешность профиля
Допуск на погрешность направ-
Радиус кривизны активного профиля
Обозначение чертежа сопряженного
кривизны перх. кривой
Номер величины зерна 6 8по ГОСТ 5439-82.
Контроль прямобочных шлицев производить
комплексными калибрами по ГОСТ 7951-81.
Неуказанные пред. откл. размеров по ОСТ 3.001.246-82.
* Размеры обеспечить инструментом.
** До пересечения с окружностью Л.
Допуск непостоянства диаметра в продольном и
поперечном сечениях поверхности К - не более 0
другие требования к прокату по ГОСТ 7505-89 кл. Т4.
Технические требования к прокату по ГОСТ
поверхность И от цементации предохранить;
сердцевина зубьев 30 45 HRC.
ДП-109316.11-2011-ИЧ-01
Рекомендуемые чертежи
- 07.09.2016
- 02.05.2022
- 04.11.2022