Технологический процесс изготовления вала для подъемно-транспортных машин




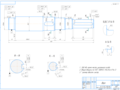
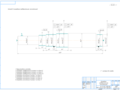
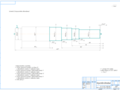
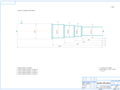
- Добавлен: 24.01.2023
- Размер: 544 KB
- Закачек: 2
Описание
Состав проекта
![]() |
![]() |
![]() ![]() ![]() |
![]() |
![]() ![]() ![]() ![]() |
![]() |
![]() |
![]() ![]() ![]() ![]() |
![]() |
![]() |
![]() ![]() ![]() ![]() |
![]() ![]() ![]() ![]() |
![]() |
![]() |
![]() ![]() ![]() ![]() |
![]() |
![]() ![]() ![]() ![]() |
![]() ![]() ![]() ![]() |
![]() ![]() ![]() ![]() |
![]() ![]() ![]() ![]() |
![]() |
![]() |
![]() ![]() ![]() ![]() |
![]() |
![]() ![]() ![]() |
Дополнительная информация
таблица.docx
Расчётное значение n мин-1
Принятое значение n мин-1
- Установ В (черновое обтачивание)
- Установ Г (черновое обтачивание)
- Установ Г (получистовое обтачивание)
- Установ Д (получистовое обтачивание)
Штучно-калькуляционное время:
Расчётная мощность N кВт
- Установ А (шлифование предварительное)
- Установ А (шлифование окончательное)
- Установ Б (шлифование предварительное)
- Установ Б (шлифование окончательное)
6.Установ Г(токарная получистовая).cdw

Точить получисто в размер 4 на длине 6
Точить канавку по размерам 7
Получистовое обтачивание
Сталь45 ГОСТ 1050-88
Установ Г (получистовое обтачивание).
4.Установ В(черновое обтачивание).cdw

Общие допуски по ГОСТ 30893
Переустановить заготовку.
Точить начерно в размер 1 на длине 8.
Точить начерно в размер 2 на длине 7.
Точить начерно в размер 3 на длине 6.
Точить начерно в размер 4 на длине 5.
Черновое обтачивание
Сталь45 ГОСТ 1050-88
Установ В (черновое обтачивание).
2.Установ А(торцевание).cdw

Сверлить центровое отверстие по условиям эскиза.
Центровое отверстие B6
*- размеры для справок.
Общие допуски по ГОСТ 30893
Сталь45 ГОСТ 1050-88
Установ А (торцевание
центрование заготовки).
9.Установ Б(шлифование).cdw

Шлифовать предварительно в размер 6 на длине 8.
Шлифовать предварительно в размер 4 на длине 9.
Шлифовать предварительно в размер 2 на длине 10.
Шлифовать окончательно в размер 7 на длине 8.
Шлифовать окончательно в размер 5 на длине 9.
Шлифовать окончательно в размер 3 на длине 10.
Шлифовать окончательно в размер 1 на длине 11.
Сталь45 ГОСТ 1050-88
Установ Б (шлифование предварительное
*- размеры для справок.
3.Установ Б(торцевание).cdw

Подрезать торец справа с соблюдением размера 1.
Сверлить центровое отверстие по условиям эскиза.
*- размеры для справок.
Общие допуски по ГОСТ 30893
Центровое отверстие B6
Сталь45 ГОСТ 1050-88
Установ Б (торцевание
центрование заготовки).
1.Заготовительная.cdw

Сталь45 ГОСТ 1050-88
*- размеры для справок.
7.Установ Д(токарная получистовая).cdw

Общие допуски по ГОСТ 30893
Переустановить заготовку.
Точить получисто в размер 4 на длину 10
с образованием галтели 9
Точить получисто в размер 3 обеспечивая размер 11
с образованием галтели 8
Точить получисто в размер 2 обеспечивая размер 12
с образованием галтели 7
Точить получисто в размер 1 обеспечивая размер 13
с образованием галтели 6
Получистовое обтачивание
Сталь45 ГОСТ 1050-88
Установ Д (получистовое обтачивание).
10.Вал (общий вид).cdw

размер обеспеч. инстр.
Сталь45 ГОСТ 1050-88
8.Установ А (шлифование).cdw

Шлифовать окончательно в размер 2 на длине 3.
Сталь45 ГОСТ 1050-88
*- размеры для справок.
Установ А (шлифование предварительное
5.Установ Г(черновое обтачивание).cdw

Общие допуски по ГОСТ 30893
Переустановить заготовку.
Точить начерно в размер 1 на проход.
Точить начерно в размер 2 на длине 3 за 2 прохода.
Сталь45 ГОСТ 1050-88
Установ Г (черновое обтачивание).
Технологический процесс изготовления детали.docx
Выбор вида финишной обработки конструктивных элементов
Выбор способа установки заготовки для её обработки 5
Выбор вида определение размеров заготовки типа и
типоразмера центровых отверстий ..6
Составление укрупнённого маршрута изготовления детали .. .7
Разработка операций по формированию контура детали 8
Составление плана токарной и шлифовальной обработок
Выбор и расчёт режимов резания .19
Определение затрат времени на токарную и шлифовальную
Список используемой литературы 28
Анализ технологических требований изготовления детали.
Деталь изготавливается в условиях единичного производства из стали 45 ГОСТ 1050-88 твердостью НВ 280 термообработка - нормализация. Она представляет собой 6-ти ступенчатый вал длиной 400 мм. Относится к группе цилиндрических изделий. Внутри - сплошной. Основное предназначение вала – передавать крутящий момент в редукторе тихоходной ступени.
Рисунок 1. Схема вала
– ступень вала под МУВП; 2 – ступень вала под уплотнение; 3 – ступень вала под подшипник; 4 - ступень вала под зубчатое колесо; 5 - заплечник вала;
– ступень вала под подшипник;
10 1112 – нерабочие торцы; 7 – канавка; 8 – рабочий торец.
Первая ступень диаметром 40 мм и длиной 100 мм имеет шпоночный паз и служит для посадки МУВП обрабатывается с допуском n7 шероховатостью Rа = 08 мкм.
Вторая ступень диаметром 48 мм и длиной 34 мм служит для посадки манжетного уплотнения обрабатывается с допуском h9 шероховатостью Rа = 08 мкм;
Третья ступень диаметром 55 мм и длиной 48 мм служит для посадки подшипника обрабатывается с допуском k6 шероховатостью Rа = 08 мкм.
Четвертая ступень диаметром 63 мм и длиной 56 мм имеет шпоночный паз для посадки зубчатого колеса 7 степени точности. Обрабатывается с допуском p6 и шероховатостью Ra = 08 мкм.
Пятая ступень диаметром 67 мм и длиной 130 мм служит упором для зубчатого колеса и подшипника специально не обрабатывается.
Шестая ступень диаметром 55 мм и длиной 32 мм служит для посадки подшипника обрабатывается с допуском k6 шероховатостью Rа = 08 мкм.
На шестой ступени под подшипник 55 k6 протачивается канавка при помощи канавочного резца на токарном станке т.к. торец 8 является рабочим. Все остальные торцы являются не рабочими.
Для удобства монтажа делаем фаски на ступенях: 1 2 3 4 6. которые подрезаются на токарном станке при помощи проходного резца. Фаски не являются рабочими поэтому точность и шероховатость обеспечивается инструментом.
На поверхностях 1 и 4 необходимо нарезать шпоночные пазы.
При изготовлении детали необходимо выдерживать допуски формы и расположения.
Допуск цилиндричности (табл. 24.2 [8]);
- для поверхностей 3 и 6 (55 k6 )
Тo = 05 .19 = 95 мкм. Принимаем Тo = 001 мм;
- для поверхности 1 (40 n7)
Тo = 05 .25 = 125 мкм. Принимаем Тo=001 мм;
- для поверхности 4 (63 p6)
Тo = 05 .19 = 95 мкм. Принимаем Тo=001 мм;
Допуск соосности расположения
- для поверхностей 3 и 6 (55 k6)
Т = 01 .В1 .Ттабл (табл. 22.5 [1]);
где В1 – ширина подшипника;
Т = 01 . 32 .4 = 128 мкм. Принимаем Т=001 мм.
При 7 степени кинематической точности передачи для зубчатого колеса с делительным диаметром 280 мм. (по табл. 22.7 [8]) степень точности допуска соосности 6). Т = 25мкм (табл. 22.6 [8]). Принимаем Т=002 мм.
Допуск перпендикулярности упорного буртика под подшипник
- для шарикого подшипника – степень точности допуска 8 (табл. 22.4 [8]);
Т = 0025 мм (табл. 22.8 [8]); Принимаем Т = 002мм
Допуски параллельности и симметричности шпоночного паза
- зубчатого колеса 18N9
Т = 05.tшп. (табл. 24.2 [1]);
Т = 05.43 = 215 мкм. Принимаем Т = 002мм;
Т = 2.tшп (по табл. 24.2 [1]);
Т = 2.43 = 86 мкм. Принимаем Т = 008мм
где tшп - допуск ширины шпоночного паза.
Выбор вида финишной обработки конструктивных элементов детали.
Для обрезки заготовки в размер сверления центровых отверстий и формирования профиля вала применим токарный станок 16К20.
Для поверхности 5 (67h14) с шероховатостью Rz 80 назначаем только черновое точение.
Для поверхностей 3 и 6 (55k6) с шероховатостью Ra 08 назначаем окончательное шлифование.
Для поверхности 2 (48h9) под уплотнение с Ra 08 назначаем окончательное шлифование.
Для поверхностей 1 (40n7) и 4 (63p6) с шероховатостью Ra 08 назначаем окончательное шлифование.
Фаски галтели и центровые отверстия получаем на токарном станке при закреплении заготовки в патрон.
Для получения шпоночных канавок используем концевые фрезы.
Выбор способа установки заготовки для её обработки.
Рассчитаем средний диаметр заготовки как:
где:n – число конструктивных элементов;
– диаметр и длина конструктивного элемента;
Определим коэффициент жесткости:
Т.к. 4Кж10 то применяем установку в центрах.
Выбор вида определение размеров заготовки типа и типоразмера центровых отверстий.
Для условий единичного или мелкосерийного производства и при несущественном перепаде диаметров (от 4 до 12мм) для детали типа вал применяется в качестве заготовки круглый горячекатаный сортовой прокат.
При максимальном диаметре детали 67 мм и при К = 72 рекомендуемый диаметр заготовки 72 мм.
Из номенклатуры круглого сортового проката выбираем сталь горячекатаную круглую ГОСТ 2590 – 88 обычной степени точности (В) 72 мм с предельными отклонениями +05; -11 допуск на заготовку составляет 16 мм (Т = 16мм) что соответствует 16 квалитету.
Определим длину заготовки:
где Zто – припуск на торцевую обработку. При номинальном диаметре проката свыше 50 мм до 80 мм Zто = 3мм. (по табл. П7 [10])
Центровые отверстия для токарной и шлифовальной обработки выбираем согласно ГОСТ 14034-74. Для детали 72 мм рекомендовано центровое отверстие В 63.
Выбираем: отверстие центровое В 63 ГОСТ 14034-74.
Рис. 2 Центровое отверстие
Составление укрупнённого маршрута изготовления детали.
Отрезать заготовку от проката круглого сечения обычной степени точности 72мм длиной 406мм.
Заготовку подвергнуть термообработке – нормализации до НВ 280.
Выполнить обработку торцов в размер 400 h14 и сверлить два центровых отверстия В63 ГОСТ 14034-74. За несколько технологических переходов выполнить обработку по формированию контура детали. Точить фаски канавку.
0 Кругло-шлифовальная
Выполнить предварительную и окончательную обработку шеек детали.
Фрезеровать два шпоночных паза окончательно.
Очистить детали от загрязнений;
Выполнить контроль детали по условиям чертежа;
Разработка операций по формированию контура детали.
1. Расчёт числа стадий обработки по каждому конструктивному элементу.
Ужесточение точности:
Число стадий обработки:
n1 = n3 = n6 = n4 = 4
2. Расчёт точности промежуточных размеров заготовки по стадиям обработки.
Определим точность заготовки по каждой стадии механической обработки для каждой поверхности. При расчете шаг уменьшения квалитетов по стадиям механической обработки должен изменяться по закону убывающей арифметической прогрессии. Расчет ведём в табличной форме.
Таблица 1. Расчет точности промежуточных размеров 3-ей; 6-ой поверхностей вала: 55k6 и 4-ой 63р6
Обтачивание черновое
Обтачивание чистовое
Шлифование предварительное
Шлифование окончательное
Таблица 2. Расчет точности промежуточных размеров 2-ой поверхности на участке вала под войлочное уплотнение: 48h9
Для получения размера 5-ой поверхности с 67 h14 используем только обтачивание черновое.
Таблица 3. Расчет точности промежуточных размеров 1-ой
поверхностей вала: 40n7
3. Определение промежуточных размеров по стадия механической обработки
Расчет ведем в табличной форме используя следующие формулы:
где: - припуск на обработку поверхности принимается из ;
d - текущий диаметр;
d() - диаметр предшествующей обработки;
- исходный размер ступени вала;
– максимальный размер ступени вала;
Таблица 4. Расчет припусков на промежуточные размеры 3-ей и 6-ой поверхностей вала под подшипник 55k6
Расчёт промежуточных размеров
Обтачивание получистовое
Таблица 5. Расчет припусков на промежуточные размеры 4-ой
поверхности вала 63р6
Характеристика размера
Точение получистовое
Таблица 6. Расчет припусков на промежуточные размеры 2-ой ступени вала на участке под уплотнение 48h9
Таблица 7. Расчет припусков на промежуточные размеры 1-ой
поверхности вала 40n7
Таблица 8. Расчет припусков на промежуточные размер 5-ой ступени
Окончательно выбираем из сортамента прокат 72мм.
Составление плана токарной и шлифовальной обработок детали
Расчёт выполняем из условия применения станка 16К20 имеющего следующие характеристики:
- допустимая мощность резания N = 75 кВт;
- максимальный диаметр заготовки до 400 мм;
- максимальная длина заготовки 1400 мм;
- частота вращения шпинделя 125 1600 обмин (регулирование ступенчатое);
- продольная подача суппорта 005 28 ммоб (регулирование ступенчатое).
1. Расчет предельно-допустимых глубин резания при черновом обтачивании.
Глубину резания для технологического перехода рассчитываем по формуле:
и сравниваем полученное значение с предельно допустимым для данного диаметра:
если обработка осуществляется за один переход
если обработка осуществляется за несколько технологических переходов.
Применим формулу с коэффициентом «01» т.к. Кж = 7212.
При этом назначаем подачу инструмента и сравниваем мощность резания с допустимой мощностью на шпинделе (75 кВт).
Четвёртя ступень: 6371
следовательно обработка по диаметрам возможна за 1 проход.
Выполняем анализ по мощности:
При подаче инструмента S = 04 ммоб и глубине резания t = 414 мм мощность N 71 кВт что меньше 75кВт. (по табл. П13 [10]).
Третья ступень: 5568
При подаче инструмента S = 04 ммоб и глубине резания t = 402 мм мощность N 71 кВт что меньше 75кВт. (по табл. П13 [10]).
Вторая ступень: 4856
При подаче инструмента S = 04 ммоб и глубине резания t = 356 мм мощность N 71 кВт что меньше 75кВт. (по табл. П13 [10]).
При подаче инструмента S = 04 ммоб и глубине резания t = 393 мм мощность N 71 кВт что меньше 75кВт. (по табл. П13 [10]).
следовательно обработка по диаметрам возможна за 1 проход. (по табл. П13 [10]).
При подаче инструмента S = 06 ммоб и глубине резания t = 25 мм мощность N 71 кВт что меньше 75кВт.
Шестая ступень: 5568
следовательно обработка по диаметрам возможна за 2 прохода.
При подаче инструмента S = 06 ммоб и глубине резания t = 283мм мощность N 71 кВт что меньше 75кВт. (по табл. П13 [10]).
2. План токарной обработки
Операция 015. Токарная.
Установ А (торцевание центрование заготовки)
Установить закрепить снять заготовку.
Подрезать торец "как чисто".
Сверлить центровое отверстие по условиям эскиза.
Установ Б (торцевание центрование заготовки)
Переустановить заготовку.
Подрезать торец справа с соблюдением размера 1.
Сверлить центровое отверстие по условиям эскиза.
Установ В (черновое обтачивание).
Точить начерно в размер 1 на длине 8.
Точить начерно в размер 2 на длине 7.
Точить начерно в размер 3 на длине 6.
Точить начерно в размер 4 на длине 5.
Установ Г (черновое обтачивание).
Точить начерно в размер 1 на проход.
Точить начерно в размер 2 на длине 3 за 2 прохода.
Получистовое обтачивание:
Точить получисто в размер 4 на длине 6 подрезать торец.
Точить канавку по размерам 789.
Установ Д (получистовая обтачивание).
Точить получисто в размер 4 на длину 10
с образованием галтели 9 подрезать торец.
Точить получисто в размер 3 обеспечивая размер 11
с образованием галтели 8 подрезать торец.
Точить получисто в размер 2 обеспечивая размер 12
с образованием галтели 7 подрезать торец.
Точить получисто в размер 1 обеспечивая размер 13
с образованием галтели 6 подрезать торец.
3. План шлифовальной обработки
Операция 020 шлифовальная
Установ А (шлифование предварительное окончательное)
Установить закрепить снять заготовку.
Шлифовать предварительно в размер 1 на длине 3.
Шлифовать окончательно в размер 2 на длине 3.
Установ Б (шлифование предварительное окончательное)
Переустановить заготовку.
Шлифовать предварительно в размер 6 на длине 8.
Шлифовать предварительно в размер 4 на длине 9.
Шлифовать предварительно в размер 2 на длине 10.
Шлифовать окончательно в размер 7 на длине 8.
Шлифовать окончательно в размер 5 на длине 9.
Шлифовать окончательно в размер 3 на длине 10.
Шлифовать окончательно в размер 1 на длине 11.
Выбор и расчёт режимов резания.
1. Токарная обработка.
При черновом обтачивании применяем проходной резец с главным углом в плане φ = 450 стойкостью Т = 60 мин из материала Т15К6.
-для чернового обтачивания принимаем значение подачи из пункта 7.1.
-для получистового обтачивания:
. SТАБЛ = 087 при Rz = 40. (по табл. П11 [10])
где К3 = 045 (по табл. П11 [10])
Из нормального ряда продольных подач суппорта станка принимаем значение S = 04 ммоб.
Cv - коэффициент скорости зависящий от значения величины подачи.
Принимаем согласно (по табл. П14 [10]);
Т – расчётная стойкость резца в минуту. Принимаем согласно (по табл. П13 [10]);
t – глубина резания;
Коэффициент корректировки.
КMV – коэффициент учёта влияния материала заготовки на скорость резания; КПV – коэффициент учёта влияния состояния поверхности на скорость резания (по табл. П18 [10]);
КИV – коэффициент учёта влияния инструментального материала на скорость резания для материала Т15К6 (по табл. П19 [10]);
КφV – коэффициент учёта влияния главного угла в плане резца на скорость резания (по табл. П20 [10]).
КГ - коэффициент характеризующий группу стали по обрабатываемости.
Принимаем согласно (по табл. П17 [10]);
- предел выносливости. Принимаем согласно [4 табл.2] =600 МПа
nv – показатель степени. Принимаем согласно (по табл. П16 [10]).
Результаты вычислений сведены в таблицу 9.
3. Расчёт режимов шлифования.
Шлифование выполняем на шлифовальном станке 3Б151 который имеет следующие характеристики:
-наибольший диаметр и длина шлифуемой заготовки: 180 х 630(800) мм;
-диаметр и ширина шлифовального круга: 600 х 63 мм;
-частота вращения детали: 63 400 обмин (бесступенчатое регулирование);
-скорость продольного перемещения рабочего стола: 01 06 ммин (бесступенчатое регулирование);
-поперечная подача шлифовального круга (глубина шлифования): 00025 005 мм на один ход рабочего стола с шагом 00025 мм;
-непрерывная подача шлифовального круга при врезном шлифовании: 01 2 мммин;
-мощность электродвигателя привода шлифовального круга: 7 кВт.
3.1. Расчёт режимов предварительного шлифования.
Согласно [32] с. 302 для предварительного шлифования принимаем:
-скорость вращения шлифовального круга: vШЛ.КР. = 30 мс;
-скорость вращения заготовки: vЗАГ. = 20 ммин;
-продольная подача шлифовального круга: S = (03 07)ВШЛ.КР. = 189 441 ммоб. Принимаем S = 30 ммоб;
-глубина шлифования tШЛИФ = 001 мм;
-количество проходов шлифовального круга:
Частота вращения шлифовального круга:
Частота вращения заготовки:
Результаты вычислений сведены в таблицу 10.
3.2. Расчёт режимов окончательного шлифования.
Согласно [32] с. 302 для окончательного шлифования принимаем:
-скорость вращения шлифовального круга: vШЛ.КР. = 35 мс;
-скорость вращения заготовки: vЗАГ. = 35 ммин;
-продольная подача шлифовального круга: S=(02 04)ВШЛ.КР.=126 256 моб. Принимаем S = 20 ммоб;
-глубина шлифования tШЛИФ = 0005 мм;
Определение затрат времени на токарную и шлифовальную обработку
Расчёт времени выполняем для каждого технологического перехода в соответствии с картой эскизов.
1. Определение затрат времени на токарную обработку
Штучно-калькуляционное время:
где ТШ.Т. – затраты времени непосредственно на обработку детали;
ТП.З. – подготовительно-заключительное время ТП.З.= 12 мин. [10];
N – число деталей в партии. N = 1;
где КД – коэффициент учёта дополнительных затрат времени для токарной обработки КД = 007 (по табл. П30 [10]);
tОП. – оперативное время;
где - затраты времени на установку закрепление и снятие заготовки
- вспомогательное время связанное с конкретным технологическим переходом для чернового обтачивания = 025 мин для получистового обтачивания = 04 мин [10];
- затраты времени в данном технологическом переходе на перемещение инструмента при котором происходит обработка поверхности;
где - длина перемещения инструмента по обрабатываемой поверхности на данном технологическом переходе;
- частота вращения детали на данном технологическом переходе;
- продольная подача резца на данном технологическом переходе;
2. Определение затрат времени на шлифовальную обработку
Затраты времени на шлифовальную обработку рассчитываем по формулам (9.1) (9.2) (9.3) :
k – дли предварительного шлифования k = 12; для окончательного k = 14.
Для шлифовальной обработки КД = 009 (по табл. П30 [10]);
Для предварительного шлифования = 025 мин. I = 5 и S = 30 ммоб для окончательного шлифования = 045 мин. I = 6 и S = 20 ммоб [10].
В ходе курсовой работы был разработан технологический процесс на изготовление детали – ступенчатый вал. Оформлена технологическая документация на операции и переходы применяемые в ходе получения детали. Установлены и применены в ходе разработки техпроцесса основные принципы и приёмы используемые при обработке металлов резанием.
Воробьёв Л.Н.Технология машиностроения и ремонт машин-
М.: «Высшая школа» 1983
Справочник технолога-машиностроителя: 3-е издание в 2-х т. под ред. Косиловой А.Г. Мещерякова Р.К. -М. “Машиностроение” 1972.
Справочник технолога-машиностроителя: 4-е издание в 2-х т. под ред. Косиловой А.Г. Мещерякова Р.К. -М. “Машиностроение” 1985.
Краткий справочник металлиста 3-е издание под ред. Орлова П.Н. Скороходова Е.А. -М.: «Машиностроение» 1987.
Панов А.А. Обработка металлов резанием. Справочник технолога -М.: «Машиностроение» 1988.
Дальский А.М. Справочник технолога-машиностроителя: в 2-х т. -М.: «Машиностроение» 2004.
Технология машиностроения: в 2-х т. т. 1. Основы технологии машиностроения Бурцев В.М. Васильев А.С. Дальский А.М. и др. – М.: МГТУ им. Н.Э. Баумана 1999.
Конструирование узлов и деталей машин под ред. Дунаева П.Ф. Леликова О.П. М.: Издательский центр “Академия” 2003.
Справочник технолога авторемонтного производства. – М.: «Транспорт» 1977.
Проектирование технологических процессов изготовления деталей подъёмно-транспортных строительных и дорожных машин. 2-я часть В.И. Фомин – М: «МИИТ» 2009.
Рекомендуемые чертежи
- 14.11.2019
- 24.01.2023