Технологический процесс изготовления Корпус коронки КНШ-130




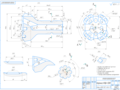
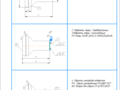
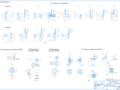
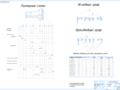
- Добавлен: 24.01.2023
- Размер: 3 MB
- Закачек: 3
Описание
Состав проекта
![]() |
![]() |
![]() ![]() ![]() ![]() |
![]() ![]() ![]() |
![]() ![]() ![]() ![]() |
![]() ![]() ![]() ![]() |
![]() ![]() |
![]() |
![]() |
![]() |
![]() |
![]() ![]() ![]() ![]() |
![]() ![]() ![]() ![]() |
![]() ![]() ![]() ![]() |
![]() ![]() ![]() ![]() |
![]() ![]() ![]() ![]() |
![]() ![]() ![]() ![]() |
![]() ![]() ![]() ![]() |
![]() ![]() ![]() ![]() |
![]() ![]() ![]() ![]() |
Дополнительная информация
!Т5.cdw

Подрезать торец 1 предварительно
Подрезать торец 1 окончательно
Р.И. Резец PCLNR 2020-12 CNMG120408-GN
Сверлить центровое отверстие
Р.И. Сверло центровочное СР-6889 ГОСТ
В.И. Патрон для сверла СП-327872.00.01
А.Поджать заготовку задним центром
В.И.Центр вращающийся КМ4
Точить поверхность 10 предварительно и
сверлить отверстие 6
Сверло ГОСТ 10903-77 D=25
Р.И. Резец канавочный
(Т) Приспособление специальное
Сверлить отверстие d22.
Р.И. Сверло спиральное Р6М5
Сверлить отверстие d12 7 отверстий
Сверлить отверстие d14 8 отверстий
Фрезеровать поверхность 17 однократно
Р.И. Фреза концевая 2210-0061 ГОСТ 9304-69
(Т) Приспособление - трехкулачковый патрон
Фрезеровать 8 шлицов предварительно
Р.И. Фреза дисковая 2210-54 ГОСТ 7210-69
Фрезеровать 8 шлицов окончательно
Фрезеровать пазы R30 и R60 однократно
Точить поверхность 15 под углом 37
однократно и точить пов. 18 одновременно
Точить поверхность 14 однократно
Подрезать торец 19 однократно
Р.И. Резец DJJNR 2020-12 DNMG 130608-SF
Подрезать торец 3 и снять
Точить поверхность 2 окончательно
Точить поверхность 10 окончательно
Р.И. Резец SVJNR 2020-11 VNMG11T304-SF
Точить поверхность 7 под углом 45
Точить поверхность 13 под углом 10
Сверлить отверстие d14
Технологические переходы
0 Горизонтально-фрезерная (6Р81Ш)
5 Токарная с ЧПУ (16К20Ф3)
5 Вертикально-фрезерная (6Р81Ш)
0 Радиально-сверлильная (2К52-2)
!КПТМ_Захаров.doc
I.ТЕХНОЛОГИЧЕСКАЯ ЧАСТЬ
Анализ исходных данных
1.Служебное назначение детали . 4
2. Количественный анализ технологичности детали . 5
Определение типа производства . . ..7
Выбор вида заготовки и метода ее получения . .. .. . .9
Нумерация поверхностей .. .. .. ..14
Синтез технологического процесса . . . . 15
План обработки детали . .. . .. . .18
Выбор оборудования .. . . .25
Размерный анализ .. .. 30
Назначение и корректировка допусков на линейные технологические размеры .33
Проверка размерных цепей с замыкающим звеном - припуском .37
Определение промежуточных припусков на диаметральные размеры 38
Таблица запаса прочности 39
Расчет размерных цепей . . 40
Выбор режимов резания ..43
Расчет технической нормы времени .53
II. КОНСТРУКТОРСКАЯ ЧАСТЬ
Список используемой литературы
Курсовой проект состоит из двух частей. В первой части описывается этап технологической подготовки производства. В этом контексте рассматривается методика последовательности разработки технологического процесса механообработки корпусной детали выявление и расчёта размерных цепей режимов резания и норм времени. Вторая часть относится к конструкторской подготовке производства и содержит методику создания установочно-зажимного приспособления на проектируемую деталь. В этой части рассматриваются вопросы разработки схемы установки заготовки расчёта необходимого усилия зажима и проведение точностного расчёта приспособления.
В приложении к работе приводится комплект конструкторско-технологической документации в виде спецификации и различных технологических карт.
Задание на курсовой проект
по ТЕХНОЛОГИИ МАШИНОСТРОЕНИЯ
Разработать и оформить единичный технологический процесс механической обработки детали Корпус коронки КНШ-130К. Годовая программа выпуска 10000шт.
Последовательность работ:
Технологическая часть.
анализ исходных данных определение типа производства заданной детали;
оценка детали на технологичность с последующим внесением в конструкцию чертежа с предприятия;
нумерация обрабатываемых поверхностей;
выбор вида заготовки и метода ее получения с последующим определением общих припусков на обработку;
составление планов обработки каждой нумерованной поверхности в соответствии с этапами принципиальной схемы механообработки;
определение количества и последовательности выполнения технологических операций на основании принятых планов обработки;
предварительный выбор для каждой операции станочного оборудования технологической оснастки и синтез схем базирования;
моделирование эскизов на каждую операцию в соответствии с правилами оформления и указанием переходов в каждой операции ;
определении операционных допусков и припусков на обрабатываемые поверхности аналитическим и табличным методами;
определение операционных размеров на обрабатываемые поверхности входе выполнения размерного анализа технологического процесса;
выбор режимов резания для каждой операции аналитическим и табличным методами;
определение норм времени на каждую операцию;
оформление основных технологических документов по ЕСДП.
Конструкторская часть.
Разработка схемы установки на одну из операций;
Выполнение расчёта приспособления на точность;
Разработка схемы закрепления и выполнение расчёта по определению усилий зажима заготовки;
Выбор механизированного привода и определение его основных характеристик.
Курсовая проект включает:
Пояснительную записку со всеми необходимыми текстами пояснениями расчетами расчетными схемами и таблицами на листах формата А4.
Комплект технологических документов (МККЭОК)
4 листа графических работ на формате А1 (совмещённый чертёж детали и заготовки иллюстрации технологического процесса размерный анализ технологического процесса сборочный чертёж установочно-зажимного приспособления.)
Работа выполняется на основе «карты процесса выполнения курсовой
работы» с соблюдением сроков завершения каждого этапа.
Исполнитель: студент гр. М – 45011 Захаров П.Н.
Руководитель: Шилов Ю.С.
I.ТЕХНОЛОГИЧЕСКАЯ ЧАСТЬ
Анализ исходных данных.
1. Служебное назначение детали.
Название детали: корпус коронки КНШ-130К
Материал детали: Сталь 40ХН ГОСТ 4543-71.
Габаритные размеры: 130*190 мм.
Наибольшая шероховатость внутренней поверхности:
Наибольшая шероховатость наружной поверхности:
Неуказанная предельная шероховатость:
Неуказанные предельные отклонения размеров: Н14 h14
В задание представлена корпусная деталь – Корпус коронки КНШ-130К.
Буровые (штыревые) коронки предназначены для разрушения горных пород при бурении взрывных скважин погружными пневмоударниками.
Шаровое соединение буровой коронки с пневмоударником повышая надежность и прочность самого соединения обеспечивает быструю смену инструмента. Лезвия коронок армированы твердым сплавом. Буровая коронка имеет рациональную форму корпуса каналы для подвода отработанного воздуха к забою скважин х-образное положение породоразрушающих лезвий.
Конструкция должна обеспечить необходимую точность как в нагруженном так и в статическом состоянии при эксплуатации. Деталь должна обеспечить достаточную прочность жесткость виброустойчивость сопротивление температурным деформациям и удобство эксплуатации.
Технологичность конструкции должна обеспечить достижение оптимальных затрат производстве эксплуатации и ремонте для заданных показателей качества объема выпуска и условий работ.
2. Количественный анализ технологичности детали
Для оценки технологичности будем рассматривать 4 коэффициента :
)Коэффициент используемого материала детали.
) Коэффициент точности обработки.
А- квалитет точности обработки.
ni-число размеров соответствующего квалитета точности
- наивысший квалитет точности для механообработки.
) Коэффициент шероховатости обрабатываемой поверхности
Где ni- число поверхностей подлежащих механообработке.
- признак величины шероховатости.
Где Rai- параметр шероховатости i поверхности в мкм.
– наибольшая высота микронеровностей в мкм.
Значение Кш не превышает 0.32 то деталь считается технологичной по данному показателю.
) Коэффициент унификации
Qуэ – количество унифицированных поверхностей на детали или количество приведённых к единообразию.
Qэ – количество обрабатываемых поверхностей.
Деталь считается технологичной если коэффициент больше 06. В случае получения низкого значения коэффициента необходимо предусмотреть изменение в конструкции детали.
Определение типа производства.
детали определил дана. m=701кг.
Тип производства ориентировочно определяем по таблице [1] исходя из массы детали и годового объема выпуска.
Объем годового выпуска N шт.
в зависимости от типа производства
Так как заданный объем годового выпуска деталей составляет 10000то при массе детали 701 кг тип производства можно считать среднесерийным.
Размер партии деталей запускаемых одновременно в производство определяется по формуле:
где N- годовой выпуск деталей шт.
Sn- количество запусков в год.
Sn=12 (для серийного производства)
Серийное производство характеризуется ограниченной номенклатурой изделий изготовляемых периодически повторяющимися партиями и сравнительно большим объемом выпуска чем в единичном типе производства.
При серийном производстве используются универсальные станки оснащенные как специальными так и универсальными и универсально-сборными приспособлениями что позволяет снизить трудоемкость и себестоимость изготовления изделия.
С увеличением размера партии уменьшаются затраты времени на переналадку станков но с другой стороны возрастают затраты на незавершенное производство складирование заготовок и готовых деталей.
Выбор вида заготовки и метода ее получения.
Главным при выборе заготовки является обеспечение заданного качества готовой детали при ее минимальной себестоимости.
Заготовка по возможности должна иметь простую конфигурацию которая не требует при изготовлении сложной и дорогой оснастки.
Выбор способа производства зависит от материала изделия назначения и технологических требований размеров и массы заготовки требований к точности и шероховатости определяемых заданным квалитетом масштаба и серийности производства технико-экономических показателей возможностями данного производства его оснащенностью. Учитываются также новые технологии машиностроения.
В данном случае: деталь - корпус коронки КНШ-130К материал – сталь 40ХН ГОСТ 4543-71 масса 701 кг производство среднесерийное – 10000 штук в год.
Способ производства – штамповка на ГКМ выполняют в штампах с двумя плоскостями разъема.
1 Определение размеров и допусков на размеры исходной заготовки
Он определяется исходя из следующих параметров:
)Расчетная масса поковки
Исходные данные для определения припусков по ГОСТ 7505 – 89:
Класс Т1 Т2 Т3 Т4 или Т5
При назначении группы стали определяющим является среднее массовое содержание углерода и легирующих элементов (Si Mn Сг Ni Мо W V).
- сталь с массовой долей углерода до 035%
включ. и суммарной массовой долей легирующих
элементов до 20 % включ.;
- сталь с массовой долей углерода свыше 035
до 065 % включ. или суммарной массовой долей
легирующих элементов свыше 20 до 50 % включ.
- сталь с массовой долей углерода свыше
5% или суммарной массовой долей легирующих элементов свыше 50%
Степень сложности С – отношение массы поковки к массе простой фигуры в которую вписывается поковка
поверхности разъема штампа
Ис – симметрично изогнутая;
Ин – несимметрично изогнутая.
класс точности поковки – Т5 (кривошипные горячештамповочные прессы открытая штамповка);
группа стали – М2 (сталь 40ХН ГОСТ 4543 -71 – содержание углерода 04%) ;
степень сложности – С1 так как
Определение расчетной массы поковки:
расчетный коэффициент для деталей типа «втулка»
т.е. степень сложности С1;
конфигурация поверхности разъема штампа – плоская П.
По табл.П6 ГОСТ 7505 – 89 определяем исходный индекс для назначения припусков допусков и предельных отклонений размеров поковки:
при массе поковки 1038 кг для М2 С1 и Т5
Исходный индекс 14 используем для назначения общих припусков на обработку по таблице [2] ГОСТ 7505-89 в зависимости от толщины длины ширины диаметра глубины и высоты детали и шероховатости обработанной поверхности заданной параметром - среднее арифметическое отклонение профиля от средней линии мкм.
2.Определение припусков допусков на обрабатываемые поверхности.
Припуски и допуски могут быть определены расчетно-аналитическим и табличным методами по ГОСТу. Величина припуска назначается на сторону а допуск – на размер. При двухсторонней обработки поверхности величину припуска удваивают. Припуски и допуски на размеры по табличному методу назначаются по ГОСТ 7505-89.
Дополнительный припуск учитывает коробление и смещение штампа дополнительный припуск на диаметр - 03 мм на линейные размеры – 05 мм.
Номинальное значение размера окончательно принимается по результатам размерного анализа.
Нумерация поверхностей
Нумерацию поверхностей производим в предполагаемой последовательности обработки согласно выработанной ранее концепции. При этом поверхности имеющие размеры расположенные в одной координатной плоскости нумеруем характерным образом например только нечётными числами. Пронумеровав поверхности в одной плоскости переходим к другой и нумеруем оставшиеся поверхности опять сначала. В конце нумеруем поверхности явно не относящиеся ни к одной плоскости оставшимися цифрами.
Такой метод нумерации поверхностей удобен для проведения последующего размерного анализа который выполняется по координатным осям.
Синтез технологического процесса.
В первую очередь определяем каким образом будут получены те или иные поверхности. Определив вид обработки определяем количество переходов необходимых для получения данной поверхности. Стартовыми данными будут являться сам размер поверхности и класс точности который необходимо получить.
1 Определение этапов обработки занумерованных поверхностей.
Для получения поверхностей заданного чертежом качества и точности должна планироваться обработка в несколько этапов поэтому при необходимости назначаются промежуточные поверхности.
2 Правило формирования токарно-револьверной операции
Все цилиндрические поверхности обрабатываются инструментами установленными на револьверной головке.
Перечень переходов для обработки заготовки.
Подрезать торец 1 предварительно
Подрезать торец 1 окончательно
Точить поверхность 2
Подрезать торец 3 однократно.
Фрезеровать 8 шлицов предварительно
Фрезеровать 8 шлицов окончательно
Точить поверхность 7 под углом 45 однократно
Сверлить отверстие 9
Точить поверхность 10
Сверлить отверстие 11
Фрезеровать пазы R30 и R60 окончательно
Точить поверхность 13 под углом 10
Точить поверхность 14
Точить пов. 15 под углом 37 однократно
Сверлить отверстие 16
Точить поверхность 18 однократно
План обработки детали
Выбор технологического оборудования
Токарный станок с ЧПУ мод. 16К20Ф3
Широкоуниверсальный консольно-фрезерный станок мод. 6Р81Ш
Радиально-сверлильный станок мод. 2К52-2
Обоснование выбора оборудования
Операция 005 Токарный станок с ЧПУ (16К20Ф3)
Токарные станки с ЧПУ данной серии поставляются с системой управления Fanuc или Siemens. Современная система ЧПУ с графической поддержкой обеспечивает простоту программирования файлообмена настройки и наладки станка. Встроенная система автоматической смазки.
Станок 16К20Ф3 патронно-центровой предназначен для токарной обработки наружных и внутренних поверхностей деталей типа тел вращения со ступенчатым и криволинейным профилями в один или несколько проходов в замкнутом полуавтоматическом цикле а также для нарезания крепежных резьб (в зависимости от возможностей системы ЧПУ).
Токарно-винторезный станок модели 16К20Ф3
Наименование параметров
Наибольший диаметр устанавливаемого изделия над станиной
Наибольшая длина устанавливаемого изделия в центрах
Наибольший диаметр обрабатываемого изделия над станиной
Наибольший диаметр обрабатываемого изделия над суппортом
Наибольший ход суппортов по оси Хпо оси Z
Максимальная скорость быстрых перемещений:
МинимальнаяМаксимальная скорость рабочих подач:
Регулирование частот вращения шпинделя
Количество ступеней регулирования частот вращения шпинделя
Частоты вращения шпинделя на ступени IIIIII (с эл.двигателем 1500 обмин)
Количество управляемыходновременно управляемых координат
Количество входныхвыходных сигналов
Память управляющих программ
Емкость архива управляющих программ
Максимальное число кадров управляющих программ
Габаритные размеры станка:
Операция 010 Горизонтально - фрезерная
Широкоуниверсальный консольно-фрезерный станок мод. 6Р81Ш имеет дополнительный шпиндель поворачивающийся вокруг вертикальной и горизонтальной осей. Имеются также широкоуниверсальные станки с двумя шпинделями (горизонтальным и вертикальным) и столом поворачивающимся вокруг горизонтальной оси. Шпиндель может быть установлен под любым углом к обрабатываемой заготовке.
Технические характеристики станка
Размеры рабочей поверхности стола
Наибольшее перемещение стола:
Угол поворота вертикальной фрезерной головки в плоскости параллельной:
продольному ходу стола:
Частота вращения шпинделя обмин
Мощность электродвигателя главного движения квт
Габаритные размеры обмин
Операция 015 Вертикально - фрезерная
Операция 020 Вертикально - фрезерная
Операция 025 Радиально-сверлильная
Сверлильный станок 2К52-2 является переносным и обеспечивает обработку отверстий в мелких средних и крупногабаритных деталях.
Оригинальная конструкция радиально-сверлильного станка 2К52-2 обеспечивает широкие возможности и позволяет:
- поворачивать сверлильную головку и рукав вокруг своих осей на 360*;
- производить обработку отверстий в любой пространственной ориентации;
- вести обработку отверстий расположенных ниже уровня "пола";
- производить обработку отверстий в ограниченном пространстве.
Предусмотрена возможность выставки станка относительно обрабатываемой поверхности при помощи винтовых опор. Для переноса станка к месту обработки имеется рым-болт.
Технические данные и характеристики радиально-сверлильного станка 2К52-2
Наибольший условный диаметр сверления мм в стали
Наибольший диаметр нарезаемой резьбы в стали
Вылет шпинделя (maxmin) мм
Расстояние от торца шпинделя до плиты (maxmin) мм
(220 ниже плоскости плиты)
Расстояние от оси шпинделя до пола
при его горизонтальном положении (maxmin) мм
Суммарный угол поворота рукава град
Суммарный угол поворота сверлильной головки град
Размеры рабочей поверхности плиты мм
Размеры Т-образных пазов мм
Число ступеней частот вращения шпинделя
Частота вращения шпинделя мин-1
Мощность привода главного движения кВт
Производительность устройства
охлаждения лмин не менее
Привод подъема рукава по колонне
электромеханический ручной
Размер съемного коробчатого стола мм
Габаритные размеры станка (LxBxH) мм не более
Масса станка кг не более
Габаритные размеры упаковки (LxBxH) мм
Размерная схема технологического процесса
В соответствии с размерной схемой формируются исходный граф производный граф и после их суммирования смешанный граф.
На графе поверхности необходимо показывать окружностями которые называются вершинами графа а размеры показывать прямыми или дугами которые называются рёбрами.
На исходном графе указываются замыкающие размеры цепи. В технологической цепи в качестве замыкающих звеньев выступают конструкторские размеры и минимальные припуски.
Назначение и корректирование допусков на линейные технологические размеры.
Проверка размерных цепей с замыкающим звеном – конструкторским размером.
Выявление технологических размерных цепей.
В каноническом уравнение замыкающее звено записывается со знаком минус. Если движение идет из меньшей вершины к большей то составляющие звенья цепи записывают со знаком «+» если наоборот то «-».
Уравнение разменной цепи
Проверка размерных цепей с замыкающим звеном - припуском.
Корректировка не требуется
Определение промежуточных припусков для диаметральных размеров.
поверхность однократно
Точить поверхность предварительно
Точить поверхность однократно
Таблица запаса прочности
Конструкторский размер по чертежу
Конструкторский размер обеспечиваемый техническим процессом
Расчет размерных цепей
Сначала рассчитываем двухзвенные звенья с одним неизвестным.
Последовательно после определяем каждое звено во всех остальных цепях.
Рассчитываем размерные цепи с замыкающим звеном – припуском.
Находим номинальный размер
Находим номинальный размер
ВЫБОР РЕЖИМОВ РЕЗАНИЯ.
Для токарного станка с ЧПУ.
Инструмент применяемый на токарном станке с ЧПУ стандартизирован и выбирается в соответствии с ГОСТ. Инструмент крепится при помощи оправок размеры которых также стандартизированы по ГОСТ.
Выбор режущей части инструмента:
Для чернового точения по корке при относительно равномерном сечении среза выбираем резец – PCLNR 2020-12 CNMG 120408-GN. Для чистового точения выбираем DJJNR 2020-15 DNMG 130608-SF. Для супер чистового точения выбираем SVJNR 2020-11 VNMG 11T304- SF.
При назначении режимов резания учитывают характер обработки тип и размера инструмента материал заготовки тип оборудования.
Элементы режимов резания обычно устанавливают в данном порядке:
Глубина резания t. При черновой обработке назначают максимальную глубину резания равную припуску или его большей части. При чистовой обработке глубину резания назначают в зависимости от точности размеров и шероховатости обрабатываемой поверхности.
Подача S. При черновой обработке выбирают максимальную подачу исходя из жесткости системы СПИД. При чистовой обработке подачу выбирают в зависимости от требуемой степени точности шероховатости обрабатываемой поверхности.
Скорость резания V. Выбирают по таблице и корректируют в зависимости от Кv:
Kт - коэффициент зависящий от периода стойкости
Км - коэффициент зависящий от обрабатываемого материала
Кс - коэффициент зависящий от состояния металла
Кr - коэффициент зависящий от материала режущей части инструмента
Кh - коэффициент зависящий от наличия корки или окалины
Кg - коэффициент зависящий от поперечного сечения резца
Кφ - коэффициент зависящий от главного угла в плане
Кφ1 - коэффициент зависящий от вспомогательного угла в плане
Кp - коэффициент зависящий от вида работ
Определение частоты вращения:
В соответствии с паспортными данными станка принимаем ближайшую частоту вращения меньшую по значению.
Затем уточняем скорость резания по принятому значению оборотов шпинделя:
Эффективная мощность резания при точении растачивании рассчитывается по формуле:
Где - постоянная и показатели степени [3 стр.273 таб. 22]
- коэффициент учитывающий фактические условия обработки [3 стр.275 таб.23]
Результаты расчетов сведем в таблицу 12.
Таблица режимов резания (Токарная с ЧПУ)
Матер. режущей части инстр.
Размеры обрабат. Поверхностей
Мощность резания Ne кВт
Для поверхности 10 (переход: точить поверхность 10 предварительно) посчитаем режимы и силы резания. Выбор инструмента: Для данного вида обработки выберем резец из твердосплавной пластинки CNMG. Размеры державки инструмента 20х20мм.
Глубина резания t=1мм
Подача выбирается по таблице приведённой в таблице [7 стр. 17 таб.12]
Скорость резания при наружном продольном и поперечном точении и растачивании выбирают из таблицы а затем умножают на поправочные коэффициенты:
Т=30мин - стойкость инструмента мин
Определяем величину оборотов в минуту шпинделя:
Теперь необходимо полученную величину оборотов скорректировать по паспорту станка (принимаем меньшее значение) а затем по скорректированным оборотам пересчитать скорость резания.
Сила резания: Силы резания выбираются по справочнику режимов резания металлов [6стр.20 табл. 21]
Результаты сведены в таблицу 12 5-й переход.
0 Горизонтально-фрезерная
Выбор инструмента: Выбираем концевую фрезу с коническим хвостовиком из материала Т5К10 по ГОСТ 17026-71. Обозначение: 2225-5012
Диаметр инструмента равен 12мм.
Длина инструмента L=96мм
Длина режущей части инструмента l=26мм
Конус Морзе 1.[3стр.174 таб.66]
Глубина резания: Глубина резания t=30мм
Подача на зуб Sz=006мм тогда можно посчитать подачу на оборот где Z – количество зубьев фрезы.
Рассчитаем скорость резания:
Где Кv=Киv *Kmv*Knv. – поправочный коэффициент для скорости.
По справочнику выбираем элементы формулы : [3 стр.286таб.39]
T=80мин (стойкость инструмента)
Cv=145 тогда скорость:
Рассчитаем силу резания :
Найдем величину оборотов в минуту:
Принимаем ближайшее стандартное значение по паспорту станка:
Найдя величины поправочных коэффициентов и показателей степеней из справочника рассчитаем силу резания :
Крутящий момент для данной силы :
Радиальная и тангенциальная составляющая силы :
Px=0.5Pz=0.5*2950=1475 H
Py=0.3*Pz=0.3*2950=885 H
«Режимы резания заготовки»
Консольно-фрезерный 6Р81Ш.
Составляющие силы резания Н
5 Вертикально-фрезерная
Выбор инструмента: Выбираем дисковую фрезу из материала Т5К10 по ГОСТ 17026-71. Обозначение: 2225-5012
Диаметр инструмента равен 140мм.
Длина инструмента L=100мм
Длина режущей части инструмента l=80мм
Число зубьев Z=10 [3стр.174 таб.66]
Глубина резания: Глубина резания t=50мм
Px=0.5Pz=0.5*2424=1212 H
Py=0.3*Pz=0.3*2424=727 H
0 Радиально-сверлильная
Выбор инструмента: Выбираем сверло спиральное с коническим хвостовиком ГОСТ 2092-77
Диаметр сверла – d=22 мм.
Материал режущей части сверла – Р6М5
Исходя из обрабатываемого материала и диаметра сверления назначим подачу на зуб: Sz=024 мм
Глубина резания рассчитывается по формуле:
t=0.5*D= 0.5*22=11 мм
Рассчитаем скорость резания :
Где Кv. – поправочный коэффициент для скорости.
По справочнику выбираем элементы формулы :
Cv=9.8 тогда скорость:
CM =0.0345 ; q = 2.0 ; y= 0.8 ; Kp = 0.73 ;
Сведем найденные значения в таблицы :
Радиально-сверлильный
РAСЧЕТ ТЕХНИЧЕСКОЙ НОРМЫ ВРЕМЕНИ.
Представляет собой min необходимое время выполнения операций в определенных наиболее благоприятных организационно – технических условиях. Норма времени при выполнении станочных работ состоит из нормы подготовительно – заключительного времени и нормы штучного времени.
tш= tосн + tвсп + tорганиз + tотдыха [4 стр.150]
Норма подготовительно – заключительного Тпз задается на партию заготовок ni
Норма штучного – калькуляционного времени определяется как
tшк = tш + [4 стр.150]
Сумма основного и вспомогательного времени это есть оперативное время
где L – расчетная длина обработки.
L=l1+l2+l3 [4 стр.151]
Состоит из трех слагаемых:
l1 – длина обрабатываемой поверхности
l2 – длина на врезание инструмента
l3 – длина перебега инструмента
При определении нормы времени для токарно-револьверной операции необходимо определить вспомогательное время на установку и снятие заготовки вспомогательное время для каждого технологического перехода и основные времена наиболее длительных технологических операций выполняемой в каждой отдельной позиции. Все полученные времена нужно сложить. В результате получиться время на операцию. Зная время на операцию можно определить время на обслуживание рабочего места и время на личные надобности.
Общая сумма составит норму штучного времени.
Результаты расчета сведены в табл. 15
Определение оперативно – штучного времени.
Вспомогательное время мин
Длина обр. поверхности
На контрольные измерения
Операция 005 токарно-револьверная
Установить и закрепить деталь
Подрезать торец 1 предвар.
Сверлить центровочное отв.
Точить пов.10 и сверлить отв.6 окончат.
Точить поверхность 2 оконч.
Точить пов. 10 оконч.
Точить поверхность 7 под углом 45
Точить пов. 13 под углом 10
Точить пов.14 однократно
Точить поверхность 15 под углом 37 и точить пов.18
Операция 010 Горизонтально-фрезерная
Фрезеровать поверхность 17 однократно.
Операция 015 Вертикально-фрезерная
Фрезеровать 8 шлицов предварит.
Фрезеровать пазы R30 и R60
Операция 020 Радиально-сверлильная
Установить и закрепить деталь.
Время перерывов на отдых:
tотд = 4%*489=019мин
Время обслуживания рабочего места:
tорм = 5%*489=024мин
tшт = 489*1.09 =533мин.
Подготовительно – заключительное на партию:
Tп.з. =19+12+10 =41 мин;
на единицу продукции
Tп.з.ni = 41338 = 012мин
Штучно – калькуляционное время:
tшт.к = 533+ 012 = 545 мин
0 Горизонтально-фрезерная.
tотд = 10%tо [4стр.162 таб.4.10]
tотд = 10%*403=04мин
tорм = 12% tо [4стр.163 таб.4.10]
tорм = 12%*403=048мин
tшт = 403*1.09 =439мин.
Tп.з. =26+12+10 =48 мин;
Tп.з.ni = 48338 = 014мин
tшт.к = 439+ 014 = 453 мин
5 Вертикально-фрезерная.
tотд = 4%*413=016мин
tшт = 413*1.09 =45 мин.
Tп.з. = 19+11+10=40 мин;
Tп.з.ni = 40338 = 011мин
tшт.к = 45+ 011 = 461 мин
tотд = 4%*161=006мин
tорм = 5%*161=008мин
tшт = 161*1.09 =175мин.
tшт.к = 175+ 011 = 186 мин
Схема базирования и закрепления.
Назначение приспособления:
Обеспечить строго определённое положение каждой детали партии запуска относительно режущего инструмента станка на котором производится обработка заготовки.
Обеспечить неподвижность заготовки в процессе работы станка исключив неблагоприятное воздействие всех сил смещающих заготовку в процессе резания.
Точностной расчет приспособления.
Точностной расчет приспособления заключается в анализе погрешностей возникающих при установке заготовки в приспособление.
Для получения требуемой точности изготавливаемой детали в приспособлении необходимо выбрать такую схему приспособления при которой фактические погрешности базирования заготовки в приспособлении ф были бы меньше или равны допустимым значениям доп.
На основе выбранной схемы установки рассчитаем фактическую погрешность установки заготовки.
Фактическая погрешность установки:
где б - погрешность базирования возникает при несовпадении измерительной и установочной базы. В данном варианте б =0.
закр - погрешность закрепления возникает в виде смещения или деформации заготовки когда к ней приложена сила закрепления. В данном варианте смещения не возникает и погрешность не учитывается обработка происходит в достаточно жестком приспособлении з =0.
пр - погрешность приспособления возникает в результате неточного изготовления и сборки приспособления и износа его установочных элементов
Примем операционный допуск на размер 074 мм в металл( операционный размер - 62-074 - согласно 14 квалитету).
Посчитаем фактическую погрешность:
Погрешность базирования:
Погрешность приспособления принимаем в пределах 13-110 от операционного допуска. ( Согласно Справочнику «Технология Машиностроения» под редакцией Косиловой»):
Погрешность закрепления :
Таким образом фактическая погрешность равна:
Едоп согласно конструкторской предпосылке равно 045 мм следовательно Еф Едоп условие точности выполняется.
Выбор режущего инструмента типа и размера станка режима резания и расчет силы резания.
Выберем необходимые элементы для дальнейшего расчета:
станок и инструмент:
Станок: вертикально-сверлильный 2К52-2
Инструмент: Сверло спиральное с коническим хвостовиком ГОСТ 2092-77
Диаметр сверла - 22 мм.
t=0.5*D= 0.5*14=7 мм
Рассчитаем скорость резания :
Cp = 68 ; q = 1.0 ; y= 0.7 ; Kp = 0.73 ;
Расчет потребной силы закрепления.
К-коэффициент надежности закрепления
K=K0*K1*K2*K3*K4*K5*K6
K0=15 – гарантированный коэф. запаса надежности.
K1=12 – учитывает увеличение силы резания из - за неровностей для черновой обработки.
K2=115– учитывает увеличение силы резания вследствие затупления инструмента.
K3=10 – учитывает увеличение силы резания при прерывистом резании.
K4=10 – учитывает непостоянство зажимного усилия для пневмоцилиндров.
K5=10 – учитывает степень удобства расположения рукояток.
K6=10 – для установочных элементов имеющих ограниченную поверхность контакта.
K=15*12*115*10*10*10=207
f1=015 – коэф. трения
f2=025 – коэф. трения.
Выбор типа силового механизма и определение необходимого исходного усилия.
Исходя из силы закрепления определяем диаметр поршня и выбираем пневмоцилиндр.
Схема для определения усилия в штоковой области
Рассчитаем усилие на штоковой области:
где - коэффициент трения между плоскостью и плунжером.
- коэффициент трения между плоскостью клина и основанием.
Теперь определяем диаметр поршня пневмоцилиндра.
где - усилие на штоке привода
- коэффициент полезного действия
Необходимый диаметр поршня пневмоцилиндра равняется 220 мм.
Принимаем: вращающийся пневмоцилиндр двух стороннего действия ЦВ250
ГОСТ 15608-81 с диаметром поршня D=250мм.
Список используемой литературы:
«Справочник технолога машиностроителя» Т1 под. Ред. Косиловой А.Г. Мещеряковой Р.К. Машиностроение 1986г.
«Размерный анализ при технологическом проектировании» В.Н. Ашихмин В.В. Закураев. ГОУ ВПО УГТУ-УПИ 2005г.
«Справочник технолога машиностроителя » Т2 пол. Ред. Косиловой А.Г. Мещеряковой Р.К. Машиностроение 1985г.
«Справочник нормировщика» А.В. Ахумов Б.М. Генкин Н.Ю. Иванов. Машиностроение 1986г.
«Точность обработки заготовки и припуски в машиностроении » Косилова А.Г. Мещеряков Р.К. Калинин М.А. Машиностроение 1976г.
«Курсовое проектирование по технологии машиностроения» А.Ф. Горбацевич В.А.Шкред 1983г.
«Режимы резания металлов» Ю.В. Барановский; Москва 1995г.
«Станочные приспособления» Т1 Б.Н.Вардашкин 1984г.
«Станочные приспособления» Т2 Б.Н.Вардашкин 1984г.
«Приспособления для металлорежущих станков» М.А.Ансёров 1975г.
«Обработка металлов резанием» Панов А.А. 2004г.
!А1-Размерный_Захаров.cdw

L-технологический размер
Сводная таблица расчёта размерных цепей.
0 Радиально-сверлильная
0 Горизонтально-фрезерная
5 Вертикально-фрезерная
!A2-Корпус КНШ-130К.cdw

Твердость НВ 363 415
Острые кромки притупить R0
* Размеры для справок
** Размеры обеспечиваемые инструментом.
Сталь 40ХН ГОСТ 4543-71
КЭ 020.frw

КЭ 005-5.frw

КЭ 005-4(б).frw

КЭ 005-1.frw

КЭ 010.frw

КЭ 015.frw

КЭ 005-3.frw

КЭ 005-2.frw

!А1-Иллюстрация к тех процессу Захаров.cdw

** - Размеры обеспечиваемые инструментом
к технологическому процессу.
Изготовление коронки КНШ-130
5 Токарная с ЧПУ (16К20Ф3)
5 Радиально-сверлильная (2К52-2)
0 Горизонтально-фрезерная (6Р81Ш)
Рекомендуемые чертежи
- 24.01.2023