Технологическая схема сборки двухступенчатого редуктора


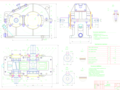
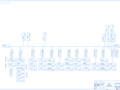
- Добавлен: 24.01.2023
- Размер: 330 KB
- Закачек: 1
Узнать, как скачать этот материал
Подписаться на ежедневные обновления каталога:
Описание
Технологическая схема сборки двухступенчатого редуктора
Состав проекта
![]() |
![]() |
![]() ![]() ![]() ![]() |
![]() ![]() ![]() |
![]() ![]() ![]() ![]() |
Дополнительная информация
Контент чертежей
Готов Ворож.cdw

сбор пз.docx
Севастопольский национальный технический университет
по дисциплине «Технология сборки изделий»
ТЕХНОЛОГИЧЕСКОЙ СХЕМЫ СБОРКИ РЕДУКТОРА ДВУХСТУПЕНЧАТОГО
Пояснительная записка
Назначение условия работы и технические требования к собираемому (разбираемому) узлу
Редуктор предназначен для передачи исполнительному элементу вращения.
Редуктор состоит из 1 ступени прямозубых цилиндрических передач
Корпус с крышкой образует замкнутый объём редуктора они отливаются из чугуна в них позиционируются все составные элементы. В нижней части имеются лаповые плоскости в которых позиционируются цекованные отверстия с помощью которых редуктор крепится на раму. В крышке корпуса сверху в приливах расположены смотровое отверстие закрываемое крышкой. В крышке располагается пробковая отдушина для нормализации давления в редукторе с атмосферным давлением и предотвращения разрушения манжет.
Слив масла осуществляется через отверстие пробки с цилиндрической резьбой при её отвинчивании.
Она позиционируется под зубчатым колесом в приливе на корпусе. Заливка и контроль уровня масла производится визуально по рискам щупа
Вал-шестерня фиксируется с помощью двух подшипников. Вал позиционируется на корпусе с помощью двух шариковых подшипников. Фиксируется прижатием внешнего кольца подшипника крышками через втулки.
Вал позиционируется так же по внешнему кольцу подшипника и фиксируется прижатием внешнего кольца подшипника крышкой и фланцем с помощью распорных втулок. На валу расположено зубчатое колесо. Оно фиксируется прижатием с одной стороны к буртику вала а с другой стороны распорной втулкой. Фиксация от поворота осуществляется призматической шпонкой.
Все подшипники запрессованы на валы по посадке с натягом L0к6. Зубчатое колесо запрессовано по посадке Н7r6.
.Сборочные единицы первого и высших порядков
Сборочные единицы первого порядка:
Сборочные единицы второго порядка:
Крышка подшипника в сборе поз7.
Крышка подшипника в сборе поз8.
Крышка подшипника в сборе поз9.
Крышка подшипника в сборе поз10.
Анализ технологичности и ремонтопригодности конструкции узла.
Под технологичностью конструкции изделия понимают совокупность свойств конструкции позволяющих вести технологическую подготовку производства изготавливать эксплуатировать и ремонтировать изделие при наименьших затратах труда средств времени и материалов по сравнению с однотипными конструкциями изделий того же назначения при обеспечении установленных показателей качества (ГОСТ 18831-73). Технологичность конструкции сборочной единицы являющейся составной частью изделия должна иметь те же свойства и обеспечивать технологичность изделия в состав которого она входит.
По области проявления технологичности различают производственную технологичность конструкции и эксплуатационную. Производственная технологичность проявляется в сокращении затрат средств и времени на конструкторскую подготовку производства (КПП) технологическую подготовку производства (ТПП) процессы изготовления деталей сборку и испытание; эксплуатационная— в сокращении затрат средств и времени на техническое обслуживание и ремонт изделия.
Технологичность конструкции оценивается качественно и количественно.
К качественным характеристикам технологичности конструкции относятся:
взаимозаменяемость — свойство конструкции составной части изделия обеспечивающее возможность ее применения вместо другой без дополнительной обработки (подбора или компенсации) с сохранением заданных качеств изделия;
регулируемость — свойство обеспечивающее возможность регулирования конструкции при сборке техническом обслуживании и ремонте для достижения и поддержания работоспособности;
контролепригодность — свойство обеспечивающее возможность и надежность контроля конструкции при изготовлении испытании техническом обслуживании и ремонте;
инструментальная доступность — свойство обеспечивающее доступ инструмента к элементам конструкции при изготовлении испытании обслуживании и ремонте.
Для количественной оценки технологичности служат следующие основные показатели:
трудоемкость изготовления — суммарная трудоемкость технологических процессов изготовления изделия без учета составных частей являющихся покупными изделиями;
технологическая себестоимость — себестоимость выражаемая суммой затрат на осуществление технологических процессов изготовления изделия без учета покупных изделий;
уровень технологичности конструкции по трудоемкости изготовления— отношение достигнутой трудоемкости к базовому показателю;
уровень технологичности по себестоимости изготовления — отношение достигнутой технологической себестоимости к базовому показателю.
Базовыми показателями при сравнительной оценке технологичности конструкции могут служить показатели передовых образцов однотипных изделий (отечественных или зарубежных) достигнутые в некотором предыдущем периоде времени или найденные теоретическим или практическим путем и утвержденные как отраслевые стандарты.
Кроме указанных имеется ряд количественных технико-экономических и технических показателей которые характеризуют технологичность в связи с процессом сборки.
Коэффициент сборности Ксб— отношение числа сборочных единиц Ne изделия включая покупные к общему числу составных частей NЧ с учетом деталей NД не вошедших в состав сборочных единиц но без стандартных крепежных NД.К:
Коэффициент эффективности взаимозаменяемости Квз — отношение трудоемкости сборки изделия осуществляемой по принципу полной взаимозаменяемости (без пригонки подбора или регулирования) Твз к общей трудоемкости сборки изделия Ти:
Коэффициент унификации изделия Ку — отношение числа унифицированных сборочных единиц Ne.у изделия и его унифицированных
деталей Nд.у не вошедших в состав сборочных единиц к общему числу составных частей изделия без учета стандартных крепежных деталей (к унифицированным составным частям относятся заимствованные покупные и стандартные непокупные сборочные единицы и детали):
Коэффициент стандартизации изделия Кст — отношение числа стандартных сборочных единиц Nе.ст изделия и его стандартных деталей Nд.ст не вошедших в состав сборочных единиц к общему числу составных частей изделия без учета стандартных крепежных деталей:
Указанные коэффициенты могут быть использованы для сравнительной оценки технологичности конструкции сборочных единиц в состав которых в общем случае входят помимо деталей покупные изделия и более мелкие сборочные единицы — конструктивно-технологические узлы
Редуктор имеет четко выраженные базовые детали (корпус и крышка корпуса) которые служат основой для процесса сборки.
При сборке имеется свободный подход простых стандартных инструментов к местам крепления сопрягаемых деталей представляется полная возможность исключения операций механической подгонки деталей при сборке.
Количество деталей в сборочном узле доведено до минимума а стандартных и нормализованных использовано достаточно.
В процессе выполнения сборочных операций и при окончательной сборке узла осуществляются методы контроля сборочных параметров и консервации.
Следует также отметить что все посадки осуществляемые в процессе
сборки производятся по методам полной взаимозаменяемости.
Обоснование и разработка технологического процесса сборки (разборки) заданного узла.
Составление технологической схемы сборки (разборки) заданного объекта.
Все валы редуктора собираются отдельно а затем устанавливаются в корпус. После сборки редуктор подвергают механическим испытаниям.
Технологические требования.
Перед началом сборочных работ необходимо проверить состояния приспособлений. Приспособления должны быть чистыми.
Перед монтажом манжет и подшипников их уплотнительные и посадочные поверхности смазать маслом МК-8 ГОСТ 6457-66 и проверить отсутствие острых кромок на заходных фасках.
Расконсервацию подшипников проводить в горячем масле при t = 80 90 С с последующей промывкой в чистом нефрасе. Перед окончательным монтажом поверхности их тел вращения и смазать смазкой ЦИАТИМ – 210 ГОСТ 6267-74.
При сборке редуктора разрешается использование нормального инструмента без шифра если они удовлетворяют техники безопасности и обеспечивают качественную сборку.
Для данного редуктора предлагается следующая схема сборки.
Корпус редуктора поз.1 установить на верстак.
Установить валы в сборе.
Сборка вала-шестерни:
а.На вал поз.4 запрессовать шпонку 8× 7×32 поз.28 с помощью молотка
б.На вал поз.4 напрессовать 2 подшипника 206 поз.33 по посадке l0K6 с помощью двух оправок. Оборудование - пресс реечный.
Сборка тихоходного вала:
а.На вал поз.5 запрессовать 2 шпонки 14× 9×40 поз.27 и 10×8×50 поз.29 с помощью молотка.
б.Колесо зубчатое поз. 6 напрессовывается на вал по посадке Н7r6 с помощью оправки . Оборудование - пресс реечный.
в.Установить втулку поз.11.
г.2 подшипника 208 поз.34 напрессовать на вал по посадке l0K6 с помощью двух оправок. Оборудование - пресс реечный.
Герметизировать плоскость разъема герметиком УТ – 34 ГОСТ 24285 – 80.
Установить 2 штифта поз.48.
Закрутить 4 комплекта К1 - болт М6×25 ГОСТ 7808-70 поз.21 шайба 6 Шайба 6 65Г ГОСТ 6402-70 поз. 25 гайка М6 ГОСТ 2524-70 поз.23.
Закрутить 6 комплектов К2 – болт М8×75 ГОСТ 2524-70 поз.23 шайба 8 65Г ГОСТ 6402-70поз.26 гайка М8 ГОСТ 2524-70 поз. 24.
Закрутить 2 болта М6× ГОСТ 7808-70 поз.20.
Установить крышку поз.7 в сборе с уплотнительной прокладкой поз.16 и регулировочной прокладкой поз.18.
Закрутить 4 комплекта К3 - болт М6×25 ГОСТ 7808-70 поз.21 шайба 6 Шайба 6 65Г ГОСТ 6402-70 поз. 25.
Установить крышку поз8. в сборе с уплотнительной прокладкой поз.16 и манжетой I-30×52 ГОСТ 8752-79 поз.31
Установить крышку поз.9 в сборе с уплотнительной прокладкой поз.17 и манжетой I-40×60 ГОСТ 8752-79 поз.32.
Установить крышку поз.10 в сборе с уплотнительной прокладкой поз.17 и регулировочной прокладкой поз.18.
Закрутить сливную пробку поз.12 в сборе с прокладкой поз.13
Установить прокладку поз.14.
Закрутить маслоуказатель жезловый в сборе поз.3.
Залить масло И-30А ГОСТ 20799-75 (приблизительно 4л).
Установить прокладку поз.15
Установить крышку поз.2 .
Закрутить 4 болта М6× ГОСТ 7808-70 поз.20.
Расчет величины усилия запрессовки (выпрессовки) для указанного в задании соединения с натягом.
Соединения с натягом широко применяются в конструкции машин. В зависимости от величины усилия запрессовки подбирается необходимое оборудование для выполнения сборочной операции поэтому его выбор является важным моментом при ее разработке.
В практике существуют следующие виды запрессовки деталей:
запрессовка ударами молотка или кувалды
запрессовка методом давления развиваемого прессами или специальными приспособлениями
запрессовка тепловыми способами запрессовка с охлаждением деталей.
Существует способ запрессовки деталей с помощью груза и крана (при отсутствии необходимого оборудования). В этом случае масса груза принимается на 20—25% больше усилия запрессовки данной детали на прессе используются специальные надставки накладываемые на торец запрессовываемой детали. Такой способ запрессовки эффективен но требует опыта и осторожности (соблюдения правил безопасности).
Запрессовка давлением. Соединение деталей давлением сравнительно широко используется в конструкциях машин. Основным оборудованием для выполнения прессовых соединений служат различные переносные приспособления: с ручным винтом пневматическим гидравлическим и пневмогидравлическим приводами; универсальные и специальные стационарные прессы и установки приспособления к ним. Применение различных приспособлений для запрессовки деталей значительно ускоряет работу и повышает ее качество.
Рассчитываем запрессовку подшипника :
При сборке соединений с натягом под действием осевой силы необходимо точное центрирование деталей. В процессе сборки к одной из двух деталей охватываемой (валу) или охватывающей втулке прикладывается осевая сила в Н которая растет от нуля до максимальной величины определяемой по уравнению:
где - коэффициент трения при запрессовке;
- давление на поверхности контакта МПа;
Давление на контактной поверхности определяется по формуле:
где - наибольший расчетный натяг;
и - модули упругости материалов охватывающей (отверстие) и охватываемой вал деталей МПа;
- длина контактной поверхности сопряжения;
- номинальный диаметр сопряжения.
Величина коэффициента трения зависит от материала деталей шероховатости поверхностей наличия и характера смазки и принимается по справочным данным[1]. Коэффициент трения для стальной охватываемой детали (сталь с содержанием углерода от 03 до 05%) в зависимости от материала охватывающей детали и способа запрессовки .
и - безразмерные коэффициенты зависящие от материала сопрягаемых деталей и отношения их диаметров:
- коэффициенты Пуассона для тех же материалов;
- диаметр наружной поверхности втулки;
- диаметр отверстия пустотелого вала (при сплошном вале =0 и ).
Значения модуля упругости материалов
Модуль упругости Па Нм2
Сталь и стальное литье
Вследствие натяга на поверхности контакта возникает давление которое определяет характер деформации деталей.
Значения коэффициентов и
При запрессовке наружный диаметр охватывающей детали увеличивается на а внутренний диаметр охватываемой детали уменьшается на . Эти изменения необходимо учитывать если указанные размеры ограничены допусками:
Обычно натяг определяют по номинальным размерам охватываемой и охватывающей деталей. Однако сминание микронеровностей во время запрессовки вызывает уменьшение натяга и ослабление посадки. Поэтому расчетный натяг определяют с учетом высоты микронеровностей и сопрягаемых поверхностей:
где - номинальный (табличный) натяг определяемый как разность нижнего отклонения отверстия и верхнего отклонения вала;
и - высоты микронеровностей сопрягаемых поверхностей деталей их значения берут из рабочих чертежей деталей (при расчетах можно принять = = 32 мкм).
Все расчеты по зависимостям (4.1) – (4.4) и далее рекомендуется выполнять в системе СИ. Например если диаметр вала равен 40 мм то м шероховатость 32 мкм то м.
Расчет резьбового соединения (нормирование затяжки) для указанного в задании резьбового соединения
Надежность резьбовых соединений определяется прежде всего их прочностью и стабильностью силы затяжки. Степень предварительной затяжки резьбового соединения определяется функциональным назначением узла (плотностью стыка герметичностью и т. п.).
В затянутом резьбовом соединении внешняя сила передается на болт (шпильку) частично при этом полная нагрузка на болт:
где - сила предварительной затяжки Н;
- коэффициент основной нагрузки (при расчете ответственных резьбовых соединений рассчитывают по одному из известных способов);
и - коэффициенты податливости соответственно болта (шпильки) и стягиваемых деталей;
- дополнительная сила передаваемая на болт (шпильку) Н.
Минимальная сила затяжки должна удовлетворять условию плотности соединения (нераскрытия стыка):
где - запас по плотности обеспечивающий нераскрытие стыка при увеличении внешней нагрузки в раз. Значение для постоянных нагрузок; для переменных. По условиям герметичности при мягких прокладках; при плоских металлических прокладках.
где - площадь сечения болта (шпильки) по внутреннему диаметру.
Верхний предел напряжений затяжки принимают с учетом некоторого запаса прочности:
для ответственных силовых соединений ;
для силовых соединений и обычных крепежных деталей
Механические свойства болтов винтов и шпилек из углеродистых и легированных сталей
Предел текучести Нмм2 не менее 19612
Марка стали 10 10кп Ст3сп3 Ст3кп
В процессе эксплуатации узла предварительная затяжка резьбового соединения изменяется из-за температурных деформаций соединений релаксации напряжений в стержне болта (шпильки) и соединяемых деталях пластического обмятия контактирующих поверхностей. Поэтому влияние этих факторов следует учитывать при назначении силы предварительной затяжки.
Приведенный средний диаметр резьбы. Значение среднего диаметра резьбы увеличенное для наружной или уменьшенное для внутренней резьбы на суммарную диаметральную компенсацию отклонений шага и угла наклона боковой стороны профиля называют приведенным средним диаметром.
Для наружной резьбы d2пр = d2изм +fp + fm ;
для внутренней - D2пр = D2изм - fp – fm.
Здесь d2изм и D2изм —измеренные (действительные) значения среднего диаметра наружной и внутренней резьб. При этом в формулу для определения d2пр fp и fm всегда входят со знаком плюс а в формулу для D2пр - со знаком минус.
Коэффициенты трения и в зависят от наличия и вида покрытия и смазочных материалов состояния трущихся поверхностей повторяемости сборки скорости завинчивания и т.п. Согласно методики НИИТмаша (Волгоград) коэффициенты трения и определяются в зависимости от вида покрытий и смазочных материалов .
Коэффициенты трения в резьбовых соединениях при различных покрытиях и смазочных материалах
Покрытие болтов и гаек
Без смазочного материала
При точном определении значения приведенного диаметра необходимо учитывать отклонения формы боковых поверхностей и другие погрешности резьб.
- угол подъема винтовой линии град;
- угол трения в резьбе град;
- приведенный коэффициент трения в резьбе;
- угол профиля резьбы град;
- приведенный радиус действия сил трения на опорной
поверхности гайки (головки винта);
и - наружный и внутренний диаметры опорной кольцевой поверхности соответственно
Наружный и внутренний диаметры опорной кольцевой поверхности
Прикладываемый при затяжке к гайке (головке болта) вращающий момент (момент на ключе) уравновешивается моментом сил трения в резьбе и моментом сил трения по торцу гайки (головки винта) и соприкасающейся с ней детали. При постоянстве коэффициентов трения в резьбе и по опорной поверхности гайки (головки винта) момент пропорционален силе затяжки :
где - средний диаметр резьбы мм;
Нормирование сборочных операций.
При нормировании операций технологического процесса серийного производства определяют штучно-калькуляционное время по зависимости:
где – подготовительно-заключительное время связанное со сборкой партии изделий;
– число изделий в партии;
Для массового и автоматизированного производств подготовительно-заключительное время равно нулю. Штучное время вычисляют как сумму основного вспомогательного времен времени на организационно-техническое обслуживание рабочего места и отдых .
Составляющие времен определяют по справочной и методической литературе. Определить основное время сборочных работ с 5 15 % точностью можно на основе имеющихся эмпирических зависимостей приведенных в таблице [6 с.149].
Установка шплинтов и штифтов
Установка шайб прокладок втулок
Установка крышек и головок по направляющим
Установка валов и осей
Установка шестерен зубчатых колес муфт и секторов на валы и оси (со шпонкой)
Запрессовка шарико- и роликоподшипников
Если сборочная операция имеет несколько переходов то основное время на операцию определяется суммированием основных времен отдельных переходов. Вспомогательное время по данным работы [6] составляет 15 60% от основного:
Если учесть что дополнительное время на сборочные операции составляет примерно 6 10 % от оперативного а подготовительно-заключительное – 3 6 % то штучно-калькуляционное время можно подсчитать по формуле:
Разборочные работы нормируются по тем же зависимостям но значения времен увеличиваются на 15%.
Библиографический список
«Проектирование технологических процессов сборки машин» Учебник Под общей ред.проф. А.А. Жолобова. Мн.: Новое знание 2005. – 410 с.
Ю.Н. Соломенцев. “Проектирование технологий” Москва. Машиностроение. 1990. – 416 с.
Иванов М.Н. и Иванов В.Н. «Детали машин. Курсовое проектирование» Учеб. Пособие для машиностроит. вузов. М.: Высшая школа 1975. – 551 с.
«Расчёты деталей машин» И.М.
Чернин А.В. Кузьмин Г. М. Ицкович. 2-е изд. перераб. и доп. М.: Высшая школа 1978. – 472 с.
Сборка и монтаж изделий машиностроения: Справочник.
В 2-хт. Т. 1. Сборка изделий машиностроения Под ред. В.С.Корсакова В.К.Замятина. - М:Машиностроение 1983. - 480 с.
«Курсовое проектирование деталей машин» Учеб. Пособие для техникумов С.А. Чернавский Г.М. Ицкович К.Н. Боков и др. М.: Машиностроение 1980. – 351 с.
Методические указания к контрольной работе по дисциплине "Технология машиностроения" для студентов для студентов направления 06.09.02 "Инженерная механика" заочной формы обучения
Сост. Ю.К.Новосёлов А.Ю.Тараховский - Севастополь: Изд-во
редуктор.frw

окончательной сборке.
Необработанные поверхности красить:
внутри редуктора маслостойкой краской
снаружи - серой нитроэмалью.
Редуктор залить маслом индустриальным
И-30А ГОСТ 20799-75 (приблизительно 4л).
Технические требования
Передаточное число U = 4.
Вращающий момент на выходном валу
Частота вращения быстроходного вала
Техническая характеристика
Модуль зубьев нормальный
Число зубьев шестерни
Коэффициент смещения шестерни
Коэффициент смещения колеса
Ширина зубчатого венца
Степень точности по
Характеристика зацепления
Рекомендуемые чертежи
- 24.01.2023
- 24.01.2023
- 17.04.2018
Свободное скачивание на сегодня
Обновление через: 21 час 11 минут