Разработка технологического процесса сборки зубчатого цилиндрического двухступенчатого редуктора




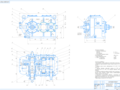
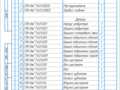
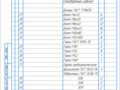
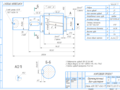
- Добавлен: 24.01.2023
- Размер: 1018 KB
- Закачек: 4
Описание
Разработка технологического процесса сборки зубчатого цилиндрического двухступенчатого редуктора
Состав проекта
![]() |
![]() ![]() ![]() ![]() |
![]() ![]() ![]() ![]() |
![]() ![]() ![]() ![]() |
![]() ![]() ![]() ![]() |
![]() ![]() |
![]() ![]() ![]() ![]() |
![]() ![]() ![]() ![]() |
![]() ![]() ![]() |
![]() ![]() ![]() ![]() |
![]() ![]() ![]() |
Дополнительная информация
спец 2.cdw

Прокладка смотрового люка
Муфта предохранительная
фрикционная ГОСТ 15622-96
Подшипники ГОСТ 8338-75
Шайба 12 65Г ГОСТ 6402-70
Шайба стопорная многолапчатая
вал-шестерня.cdw

Общие допуски по ГОСТ 30893.1: H14
Кромки зубьев притупить R 0
Сталь 40Х ГОСТ 4543-71
СПИ ИжГТУ Гр. Б03-721-1 зт
Направление линии зуба
Схема размерной цепи.cdw

СПИ ИжГТУ Б03-721-1 зт
Размерная цепь для метода max-min
Размерная цепь для метода регулирования
Схема сборки редуктора.cdw

мой вал.m3d

Специф 3.cdw

Редуктор (СБ).cdw

Технические параметры
Двигатель электрический
Число оборотов n = 940 обмин
Максимальный крутящий момент
на тихоходном валу 900 кг*см
Общее передаточное число i = 15
Смазка : а) зацепления жидкая
б) подшипников густая
Технические требования:
Все резьбовые и гладкие поверхности перед сборкой промаслить.
Подшипники перед установкой в корпус смазать смазкой УС ГОСТ
Редуктор залить маслом: индустриальным И-Т-С-320 ТУ 38
увеличивая нагрузку от 25% от
номинальной до 50; 75; 100 % до получения заданного пятна
В обкатанном редукторе проверить боковой зазор в зацеплении и
величину пятна контакта
которые должны соответствовать
степени точности 8 ГОСТ 1843-81.
Допускается эксплуатировать редуктор с отклонением от
горизонтального положения на 5
. При этом должен быть обеспечен
достаточный для смазки зацепления.
Общие допуски согласно ДСТУ ISO 2768-mK.
содержание.docx
1.Служебное назначение принцип работы изделия2
2.Служебное назначение и описание детали Вал-шестерня3
3.Анализ технических требований узла4
4.Анализ технологичности и ремонтопригодности
конструкции изделия5
5.Определение типа производства6
Технологическая часть8
1.Размерный анализ и расчет сборочных размерных цепей8
2.Описание технологического процесса сборки12
3.Технологическая схема сборки16
4.Выбор технологических баз на общей и узловых сборках19
5.Технический контроль его виды и основные цели20
6.Нормирование сборочных операций22
Специф 1.cdw

Крышка смотрового люка
Крышка подшипника сквозная
Крышка подшипника глухая
Прокладка крышки подш.
пояснительная записка.docx
В данном курсовом проекте разрабатывается технологический процесс сборки зубчатого цилиндрического двухступенчатого редуктора с муфтой предельного момента предназначенного для передачи исполнительному механизму крутящего момента. Выполняется расчет технологических параметров сборки:
Выявление и расчет сборочных размерных цепей;
Нормирования времени на сборку редуктора.
Нормирование сборочных операций.
Курсовой проект выполнен в современных программных пакетах таких как «КОМПАС-3D».
Объектом данного курсового проекта является привод в котором используются в основном детали и узлы общемашиностроительного применении основным устройством в данном приводе является двухступенчатый цилиндрический редуктор.
Назначение редуктора - изменение кинематических и силовых характеристик от двигателя к исполнительному звену агрегата.
Редуктор состоит из литого чугунного корпуса в котором помещают элементы передачи - зубчатые колеса валы подшипники и т.д.
Целью проекта является анализ технических требований технологичности конструкции а также размерный анализ изделия. В качестве изделия выбран двухступенчатый цилиндрический редуктор. Проектируемой деталью является деталь вал-шестерня.
Характеристика объекта производства
1.Служебное назначение принцип работы изделия
В производственных машинах необходим большой вращательный момент при угловой скорости меньшей чем у двигателя.
Для передачи движения от двигателя к производственной машине и изменения при этом угловой скорости и вращательного момента служат различные вращательные механизмы. Редукторы являются зубчатыми приводами предназначенными для изменения крутящих моментов и частоты вращения различных машин и механизмов.
Назначения редуктора - понижение угловой скорости и соответственно повышения вращающего момента ведомого вала по сравнению с ведущим. Механизмы для повышения угловой скорости выполненные в виде отдельных агрегатов называют ускорителями или мультипликаторами.
Принцип работы редуктора заключается в следующем: когда к входному валу прикладывается вращающий момент он как и закрепленное на нем зубчатое колесо приводится в движение. Посредством цилиндрической передачи усилие передается от колеса входного вала к колесу находящемуся с ним в зацеплении. Колеса изготавливаются разных диаметров и с разным количеством зубьев причем колесо с меньшим числом зубьев называется шестерней а с большим – колесом. Вращающий момент последовательно передается с входного вала на промежуточный а с промежуточного на выходной (в случае двухступенчатого редуктора).
Преимущества цилиндрических редукторов:
Они отличается высоким коэффициентом полезного действия;
Обладают повышенной нагрузочной способностью. Они в состоянии практически без потерь передавать большие мощности;
Они отличаются высокой кинематической точностью;
Хорошо работают как при неравномерных нагрузках так и при любых количествах запусков и остановок;
В этих изделиях отсутствует самоторможение поэтому у любого из них имеется возможность провернуть выходной вал;
Благодаря высокому коэффициенту полезного действия цилиндрические редукторы очень мало нагреваются в результате почти вся энергия передается потребителю;
Цилиндрический редуктор обладает хорошей надежностью;
Большой количество вариантов зубчатых передач позволяет подобрать самый подходящий редуктор для требуемого передаточного движения.
Недостатки цилиндрических редукторов: повышенный уровень шума обладают низким передаточным числом.
Использование цилиндрических редукторов:
Изделия нашли свое применение в металлорежущих станках их устанавливают в мешалках измельчителях в валковом и другом оборудовании. Практически ограничений для их использования нет за исключением тех случаев когда целесообразнее будет использовать другие типы редукторов.
2. Служебное назначение и описание детали Вал-шестерня
Деталь “Вал” предназначен для передачи вращательного движения и крутящего момента исполнительному механизму для базирования зубчатого колеса с муфтой. Исполнительными поверхностями детали являются цилиндрические посадочные поверхности поверхности паза торцевая поверхность. К этим поверхности предъявляются высокие требования по шероховатости и качеству обработки. Вал базируется на подшипниках в корпусе. Все базовые поверхности подвергаются термической обработке затем шлифуются.
Опорами валов служат подшипники качения смонтированные в корпусе. Шейки вала под подшипники шлифуют для точного расположения вала в корпусе редуктора. Подшипники фиксируются на валу в осевом перемещении специальными винтами. Крышки предохраняют подшипники от попадания пыли.
Проектируемой деталью является деталь вал-шестерня. Данная деталь предназначена для передачи крутящего момента по средствам шестерен и зубчатых колес в редукторе.
Вал-шестерня является очень ответственной деталью. Прочность вала определяет механическую надежность машины в эксплуатации. Прямолинейность и прочность вала зависят не только от правильного расчета и выбора конструктивных размеров но и от технологических процессов обработки вала и сборки насаживаемых на него деталей.
Данная деталь представляет собой вал с выполненной на нем косозубой шестерней имеет шпоночный паз шлицы отверстие для смазки шлицевого соединения и поверхности для установки подшипников.
На основании изучения условий работы детали в узле изделия предъявляемых к ней технических требований а также учитывая годовую программу выпуска можно сказать что конструкция детали достаточно технологична. Жесткость вала допускает получение высокой точности обработки.
В качестве материала для детали учитывая условия эксплуатации используется конструкционная легированная сталь 40Х ГОСТ4543-71.
3. Анализ технических требований узла
Технические параметры
Двигатель электрический
Мощность N = 19 л. с.
Число оборотов n = 940 обмин
Максимальный крутящий момент
на тихоходном валу 900 кг*см
Общее передаточное число i = 156
Смазка : а) зацепления жидкая
б) подшипников густая
Технические требования:
Все резьбовые и гладкие поверхности перед сборкой промаслить.
Подшипники перед установкой в корпус смазать смазкой УС ГОСТ 1033-79.
Редуктор залить маслом: индустриальным И-Т-С-320 ТУ 38 101413-78.
Редуктор обкатать увеличивая нагрузку от 25% от номинальной до 50; 75; 100 % до получения заданного пятна контакта.
В обкатанном редукторе проверить боковой зазор в зацеплении и
величину пятна контакта которые должны соответствовать степени точности 8 ГОСТ 1843-81. Если превысить верхнее отклонение то ухудшится качество зацепления зубчатых колёс КПД понизится. Если нижнее отклонение будет меньше заданного то усилится уровень звукового давления усилится износ.
Допускается эксплуатировать редуктор с отклонением от горизонтального положения на 5°. При этом должен быть обеспечен уровень масла достаточный для смазки зацепления.
Общие допуски согласно ДСТУ ISO 2768-mK.
Таким образом анализ технических требований показал что они назначены конструктором обоснованно и соответствуют служебному назначению редуктора. Невыполнение этих требований приведет к некачественной работе редуктора к его повышенному износу а некоторые требования обеспечивают работоспособность изделия в целом.
4. Анализ технологичности и ремонтопригодности конструкции изделия
Анализ технологичности и ремонтопригодности конструкции объекта с учетом требований предъявляемых к конструкции изделия приведены в таблице:
Возможность сборки из отдельно подсобранных составных частей и сокращение длительности цикла общей сборки за счет осуществления параллельной сборки и испытания этих составных частей;
Использование стандартных деталей и узлов (что снижает себестоимость изготовления изделия и упрощает снабжение и комплектование);
Нормализация крепежных и других деталей (что позволяет сократить номенклатуру сборочных инструментов);
Возможность удобного подвода механизированного сборочного инструмента к местам соединений;
Удобство и доступность сборки без применения сложных приспособлений путем использования простых движений;
Несложность проведения регулировочных работ;
Отсутствие или сокращение до минимума пригоночных работ;
Легкая отделяемость быстроповреждающихся сопряжений (что позволяет организовать узловой метод ремонта);
Наличие компенсаторов регулировочных устройств и легкосменных деталей (втулок колец вкладышей) снижающих трудоемкость ремонтных операций.
Под технологичностью понимается свойство конструкции позволяющее в полной мере использовать при изготовлении наиболее экономичный технологический процесс обеспечивающий полное качество при надлежащем количественном выпуске.
При сборке имеется свободный подход простых стандартных инструментов к местам крепления сопрягаемых деталей представляется полная возможность исключения операций механической подгонки деталей при сборке.
Количество деталей в сборочном узле доведено до минимума а стандартных и нормализованных использовано достаточно.
В процессе выполнения сборочных операций и при окончательной сборке узла осуществляются методы контроля сборочных параметров и консервации.
Конструкция редуктора является технологичной с точки зрения удобства сборки обслуживания во время эксплуатации и необходимого ремонта.
5. Определение типа производства
Намеченный годовой выпуск изделий (программа выпуска) характеризует тип производства и предопределяет степень дифференциации технологического процесса.
Характер сборочного процесса во многом зависит от такта сборки. Такт сборки представляет собой интервал времени через который производится сборка изделий определенного наименования типоразмера и исполнения. При заданном режиме работы сборочного производства такт сборки Т зависит от числа собираемых изделий за определенный промежуток времени:
где F - фонд времени (годовой месячный сменный) ч;
N - программа выпуска изделий за тот же промежуток времениНоминальный (расчетный) годовой фонд времени рабочего места сборщика в 2016 году равен 1974 ч. Действительный годовой фонд времени Fa работы сборочного оборудования:
где - коэффициент учитывающий потери времени на ремонт сборочного оборудования.
Для неавтоматизированного сборочного оборудования принимая
равным 098; получим значения 1934 ч ;
Рассчитаем трудоемкость сборки изделия по формуле (1):
Согласно полученным данным тип производства является мелкосерийным. В общем случае этот тип производства характеризуется периодическим изготовлением разнообразных изделий ограниченной номенклатуры и малых объемов выпуска одновременно запускаемых в производство партиями регулярно повторяющимися через определенные промежутки времени. Так как производство мелкосерийное применяем стационарную сборку без расчленения сборочных работ не поточную.
Технологическая часть
1. Размерный анализ и расчет сборочных размерных цепей
Технологические размерные цепи решают задачу по обеспечению точности при изготовлении машин. Они устанавливают связь размеров деталей на разных этапах технологического процесса. Технологическая размерная цепь определяет расстояния между поверхностями изделия при выполнении операций обработки или сборки при настройке станка или расчете межоперационных размеров и припусков.
Размерные цепи отражают объективные размерные связи в конструкции машины при сборке а также размерные связи в технологических процессах обработки или измерения деталей. Размерные цепи позволяют составить метрическую модель изделия и оптимизировать требования к точности геометрических параметров с целью обеспечения показателей качества функционирования в заданных пределах при установленных затратах на производство. Для данного редуктора расчет производим для промежуточного вала по 2- м методам.
Метод максимума-минимума:
Расчет ведем по методу максимума - минимума при котором допуск замыкающего размера определяют арифметическим сложением допусков составляющих размеров. Этот метод учитывает только предельные отклонения звеньев и самые неблагоприятные их сочетания.
Для удобства составим таблицу с номинальными размерами составляющих звеньев цепи и допусками на эти размеры по 14 квалитету (допуски на подшипники выберем из каталога) данные занесем в таблицу «Решения проектировочной задачи методом максимума-минимума».
Номинальный размер A0 будет равен:
Максимальный размер :
Минимальный размер :
Исходя из расчетов номинальный размер = 5 мм а допуски мм.
Метод регулирования:
Под этим методом понимают расчет размерных цепей требуемая точность исходного звена достигается изменением одного из звеньев которое называется компенсационным. Роль компенсатора обычно выполняют специальные звенья конструкторского плана в нашем случае компенсационным звеном будет служить звено А8 (маслоотражающее кольцо) рис. 2.2. Зазор для данного метода примем равному мм. Все остальные составляющие звенья мы занесли ранее в таблицу. В данном случае компенсатор является уменьшающим звеном. номинальное рассчитывается по формуле 6 и равно 10 мм.
Номинальный размер компенсатора 10 мм будем считать что набор состоит из одной постоянной прокладки с толщиной = 5 мм и нескольких сменных количество которых зависит от действительных размеров деталей собираемого редуктора. Число сменных прокладок примем равным 10:
Принимаем стандартное значение толщины прокладок по ГОСТ 481-80 S = 05 мм. Величину - (можно принять в качестве допуска на изготовление прокладок.
2 Описание технологического процесса сборки
Сборка - это образование разъёмных и неразъёмных соединений составных частей сборочных единиц или изделия.
По объёму выполняемых работ сборка делится на общую(объём объявляется изделием в целом) и узловую. Организационные формы сборки.
Различают две основные организационные формы сборки: стационарную и подвижную. Стационарная сборка машины характеризуется тем что она выполняется одним рабочим или группой рабочих (бригадой) на одном неподвижном рабочем месте к которому подаются все детали и сборочные единицы собираемой машины. Стационарная сборка может выполняться без расчленения процесса сборки на узловую и общую и с расчленением этого процесса. Подвижная сборка осуществляется с расчленением процесса. Изделие в процессе сборки перемещается от одного рабочего места к другому на которых бригадой или группой рабочих находящихся постоянно на этих местах выполняется одна и та же повторяющаяся операция. В данном случае применяем стационарную сборку с расчленением процесса на узловую (валы редуктора) и общую (редуктор).
Перед сборкой внутреннюю полость редуктора тщательно очищают и покрывают маслостойкой краской.
Детали выполняются по требованиям чертежей и технологических карт перед сборкой детали должны быть проверены и приняты ОТК. Все детали поступающие на сборку не должны иметь заусенцев и пройти промывку от загрязнения.
Сборку производят в соответствии со сборочным чертежом редуктора начиная с узлов валов:
на быстроходный вал устанавливаем подшипники шариковые радиальные однорядные предварительно нагретые в масле до 80-100°С;
в промежуточный вал закладываем шпонку 12х8х32 и напрессовываем зубчатое цилиндрическое косозубое колесо до упора в бурт вала; затем надеваем распорное кольцо устанавливаем подшипники шариковые радиальные однорядные предварительно нагретые в масле;
в тихоходный вал закладываем шпонку 14х9х56 и напрессовываем зубчатое цилиндрическое косозубое колесо до упора в бурт вала; затем надеваем распорное кольцо и устанавливаем подшипники шариковые радиальные однорядные предварительно нагретые в масле.
Собранные валы укладываем в основание корпуса редуктора в соответствующие гнёзда расточек под подшипники в корпусе редуктора и надеваем крышку корпуса покрывая предварительно поверхности стыка крышки и корпуса спиртовым лаком а затем пастой «Герметик». Для центровки устанавливаем крышку на корпус с помощью двух конических штифтов; соединяем корпус с крышкой редуктора при помощи стяжных болтов пружинных шайб и гаек.
В подшипниковые камеры предварительно закладываем пластичную смазку типа ЛИТОЛ-24. Проверяем проворачиванием валов отсутствие заклинивания подшипников устанавливаем крышки подшипников и закрепляем их винтами.
На выходной конец ведущего вала устанавливаем шпонку 6х6х20а затем устанавливаем муфту упругую втулочно-пальцевую и фиксируем ее на втулке установочным винтом с коническим концом.
Устанавливаем жезловый маслоуказатель. Вкручиваем пробку в комплекте с уплотняющей прокладкой из маслостойкой резины в маслосливное отверстие. Заливаем в корпус масло индустриальное И-Т-С-320 крепим винтами крышку смотрового отверстия в комплекте с прокладкой. В крышку смотрового отверстия вкручиваем отдушину.
Собранный редуктор обкатывают и подвергают испытанию на стенде по программе установленной техническими условиями.
Эскиз сборочной единицы (промежуточный вал) приведен на рисунке
Эскиз сборочной единицы
Технологическая схема сборки промежуточного вала
В состав технологического процесса включаются при необходимости подготовительные пригоночные регулировочные контрольные и др. работы (операции и переходы).
Технологические процессы оборки фиксируют в маршрутных и операционных картах оформляемых в соответствии со стандартами ЕСТД.
Технологическая операция сборки вала:
- Закрепить вал шестерню 12 в приспособлении;
- Запрессовать шпонку 46 а затем цилиндрическое зубчатое колесо 14;
- Протереть и установить распорную втулку 18 маслоотражающее кольцо 22 и стопорное кольцо 49;
- Смазать и установить подшипники 40;
- Свинтить шайбы 26 с валом шестерней болтами 27;
- Проверить легкость вращения вала 12.
Разработка технологического процесса сборки редуктора
За базу при сборке редуктора принимаем корпус редуктора.
Технологический процесс сборки редуктора
Содержание операции переходов
Сборка входного вала-шестерни 11
Закрепить вал шестерню 11 в приспособлении протереть и установить маслоотражающие кольца 21 и стопорное кольцо 49 напрессовать и смазать подшипники 38 свинтить шайбу 25 с валом болтами 27.Установить распорную втулку 17.
Сборка промежуточного вала-шестерни 12
Закрепить вал шестерню 12 в приспособлении. Запрессовать шпонку 46 а затем цилиндрическое зубчатое колесо 14. Протереть и установить распорную втулку 18 маслоотражающее кольцо 22 и стопорное кольцо 50. Смазать и установить подшипники 39. Свинтить шайбы 26 с валом шестерней болтами 27.
Сборка выходного вала 13
Закрепить вал 13 в приспособлении протереть и установить распорную втулку 19 затем установить зубчатое колесо 15. Запрессовать шпонку 47 и фрикционную предохранительную муфту 37. Протереть и установить маслоотражающее кольцо 23 и стопорное кольцо 51. Смазать и установить подшипники 40. Затянуть гайку 36.
Установить корпус 3 на стол установить валы в сборе 111213.Установить штифты 48. Установить и затянуть болтами 3132 крышку корпуса редуктора 4. Установить крышки подшипников 6-10 с прокладками 20 и затянуть болтами 2930. Затем протереть и установить распорную втулку 16 на выходной вал затянуть гайкой 35 и установить шплинт 44. Закрутить рым болты 41 . Установить маслоуказатель 1 и сливную пробку 2. Залить масло через отверстие смотрового люка. Установить прокладки 24 крышку смотрового люка 5 и затянуть болтами 28.
Проверка работы и герметичность редуктора
3. Технологическая схема сборки
Изучив сборочный чертеж и уяснив конструкцию собираемого объекта необходимо расчленить его на составные части - детали и узлы.
Деталь – это изделие (составная часть изделия) изготовленное из однородного по наименованию и марке материала без применения сборочных операций но с использованием при необходимости защитных или декоративных покрытий. Характерный признак детали отсутствие в ней разъёмных и неразъёмных соединений. Деталь – это первичный сборочный элемент каждого изделия.
Сборочная единица (узел) - это изделие составные части которого подлежат соединению между собой сборочными операциями (свинчиванием сочленением клепкой сваркой пайкой опрессовкой развальцовкой склеиванием сшивкой). В узел могут входить не только детали но и подузлы подгруппы. Характерный признак узла - возможность его обособленной сборки.
Основные принципы которыми следует руководствоваться технологу при разбивке изделия на сборочные единицы и разработке схем сборки следующие:
-сборочная единица не должна быть слишком большой по размерам и массе и состоять из значительного количества деталей и сопряжений но в то же время излишнее дробление на сборочные единицы так же нерационально;
-сборочная единица должна быть выделена в особую если в процессе её сборки требуется проведение испытаний обкатка специальная слесарная доработка пригонка и т.п.;
-сборочная единица при последующем монтировании её в машине не должна подвергаться разборке (если этого избежать нельзя то разборочные работы необходимо предусмотреть в технологии);
-сборочные единицы должны включать также детали крепления резьбовые соединения с тем чтобы сократить количество отдельных деталей подаваемых непосредственно на общую сборку;
-сборочные единицы должны быть примерно одинаковыми по трудоемкости;
-сборку следует начинать с установки на рабочем месте (стенде конвейере) базовой детали или базовой сборочной единицы к которой последовательно будут присоединяться остальные детали и сборочные единицы;
-сборку следует начинать с деталей имеющих размеры
входящие в качестве составляющих звеньев в ту размерную цепь при помощи которой решается наиболее ответственная задача;
-последовательность сборки определяется возможностью и удобством присоединения деталей;
-каждая ранее смонтированная деталь или сборочная единица не должна мешать последующей сборке;
-детали или сборочные единицы выполняющие наиболее ответственные функции или которые являются общими звеньями в параллельно связанных размерных цепях желательно монтировать в первую очередь;
-в процессе сборки необходимо обеспечить минимальное количество переустановок.
Конструкция механизма имеет несколько сборочных узлов которые возможно собирать независимо друг от друга поэтому возможна узловая сборка изделия. Но невозможно одновременное присоединение нескольких узлов к базовому элементу из-за его конструкции.
При последовательном соединении возможна механизация процесса сборки.
При сборке редуктора доступ инструментов к деталям свободный. Большинство крепежных изделий - стандартные что позволяет применять простой инструмент.
В данном изделии основным базовым элементом является корпус к которому присоединятся все детали и узлы.
Технологическая схема сборки показывает в какой последовательности необходимо присоединять и закреплять друг к другу элементы из которых собирается изделие. Такими элементами являются детали комплекты узлы подузлы и сборочные единицы.
Под деталью при составлении сборки понимают первичный элемент изделия (базовая деталь) характерным признаком которого является отсутствие в нем разъемных и неразъемных соединений. Сборочная же единица представляет собой элемент изделия состоящий из двух или более деталей соединенных в одно целое не распадающееся при перемене положения в узле или подузле. Характерным отличительным признаком сборочной единицы является - возможность ее сборки независимо от других элементов изделия.
Для составления технологической схемы сборки все сборочные единицы входящие в изделие условно разделим на группы и подгруппы. Группой будем считать сборочную единицу входящую в изделие.
Технологическую схему сборки составляем на основе сборочного чертежа изделия которая показывает в какой последовательности необходимо присоединять друг к другу элементы из которых состоит изделие.
Каждый элемент изделия будем изображать в виде прямоугольника разделенного на три части. В его верхней части дается наименование изделия в левой нижней части указываем числовой индекс соответствующий номеру данного элемента на сборочном чертеже и согласно принятой спецификации в правой нижней части количество присоединяемых элементов.
Порядок составления технологической схемы сборки начинаем с назначения базового элемента. Базовым элементом назовем деталь с которой начинаем сборку изделия.
При определении последовательности сборки заранее анализируем сборочные размерные цепи. Если изделие имеет несколько размерных цепей то сборку следует начинать с наиболее сложной и ответственной размерной цепи.
Для более ясного представления о порядке составления технологической схемы сборки указываем необходимые технические требования на сборку. Под техническими требованиями понимаем разные надписи - сноски поясняющие характер выполнения сборочных работ когда они не ясны из схемы.
Такой алгоритм составления технологической схемы сборки облегчает последующее проектирование технологического процесса сборки позволяет оценить технологичность конструкции изделия с точки зрения возможности расчленения сборки на общую и узловую и гарантирует от пропуска деталей входящих в изделие.
Разработанная технологическая схема сборки червячного редуктора представлена на листе формата А2 графической части курсового проекта.
4. Выбор технологических баз на общей и узловых сборках
Технологическая база - это поверхность сочетание поверхностей ось или точка принадлежащая заготовке и используемая для определения ее положения в процессе изготовления. Базирование при механической обработке - это придание заготовке с помощью комплекта баз требуемого положения для ее обработки. В значительной степени маршрут операций технологического процесса предопределяется выбором и назначением комплектов технологических баз. Комплект баз для деталей не являющихся телами вращения определяется как правило тремя базами: установочной направляющей и опорной.
При сборки каждого из валов берем за основу т.е базу сам вал. При сборке редуктора принимаем за базу корпус редуктора.
При сборке изделия в качестве базового элемента на начальном этапе применяют корпус редуктора базирующийся на нижней опорной плоскости. Для реализации направляющей и опорной баз используем отверстия в нижней части корпуса предназначенные для крепления редуктора на фундаментеопорной плите. Такое базирование обеспечивает возможность ручной механизированной автоматизированной сборки в приспособлениях обеспечивающих точное положение сопрягаемых деталей удобство и доступность сборки без переустановки.
Узловая сборка редуктора осуществляется следующим образом:
при сборке вала позиция №9 принимаем в качестве базовой детали вал базирующийся на наружной поверхности диаметром 30 мм.
при сборке вала позиция №10 принимаем в качестве базовой детали вал базирующийся по наружной поверхности зубчатого колеса.
при сборке вала позиция №11 принимаем в качестве базовой детали вал базирующийся по наружной поверхности диаметром 45 мм.
5. Технический контроль его виды и основные цели
Качество продукции во многом зависит от усилий в производственной среде — на ее повышение должна быть нацелена вся производственная система.
Одним из элементов системы управления качеством является организация технического контроля на предприятии.
Подтехническим контролемпонимается проверка соблюдения требований предъявляемых к качеству продукции на всех стадиях ее изготовления и всех производственных условий обеспечивающих его.
Основнойзадачей технического контроляявляется обеспечение выпуска высококачественной и комплектной продукции соответствующей стандартам и техническим условиям.
Поформамтехнический контрольможет бытьпассивнымкогда просто фиксируются данные о качестве продукции (констатируется факт) иактивнымкогда не только оценивается качество по и оказывается активное воздействие на технологический процесс с целью управления качеством.
Основнымитребованиями предъявляемыми к рациональной организации технического контроля являются:
)профилактичность т. е. организация технического контроля с целью предупреждения выпуска некачественной продукции;
)достаточная степень точности и объективности определения качества продукции и выявления брака;
)оптимальные затраты труда и средств на проведение технического контроля;
)широкое привлечение рабочих и специалистов к выполнению функций технического контроля?
Для решения задач стоящих перед ОТК необходимо правильно выбрать вид технического контроля.
По назначениютехнический контроль различают:
входнойопределяющий соответствие закупаемых для производства сырья материалов полуфабрикатов и комплектующих изделий требованиям научно-технической документации (НТД). Проверяется наличие у них сертификатов качества. При этом контролируются комплектность поставок правильность оформления сопроводительной документации и маркировки продукции;
предварительныйосуществляется с целью предотвращения поступления в производство бракованных предметов труда и заключается в проверке качества сырья материалов полуфабрикатов и комплектующих изделий до начала их обработки (сборки);
промежуточныйосуществляется в процессе изготовления какого-либо объекта по отдельным операциям. Он может быть пооперационным (проверка после каждой операции) и групповым — проверка после нескольких операций;
окончательныйпроизводится при приемке готовых изделий для выявления некачественной продукции. Он сопровождается специальными испытаниями и анализом уровня качества в соответствии со стандартами и техническими условиями.
По возможности использованияпродукции контроль может бытьразрушающийинеразрушающий(акустический магнитный оптический радиационный).
По месту выполненияконтрольных операций различают:
стационарныйконтроль— производится на специально оборудованном постоянном рабочем месте контролера куда поставляются объекты контроля. Целесообразно применять такой контроль при проверке большого количества однородных объектов;
подвижнойконтроль— осуществляется на том рабочем месте где выполняются операции и применяется для проверки громоздких не удобных для транспортировки объектов контроля а также когда не требуются специальные сложные приборы для контроля.
По степени охватаконтроль может бытьсплошным(проверке подвергаются все без исключения объекты контроля одного наименования) ивыборочным(проверке подвергается часть партии однородных объектов с использованием статистических методов контроля).
Инспекционному контролюподвергается продукция из которой изъят ранее выявленный брак. По его результатам судят о качестве работы служб контроля качества.
Выбор вида контроля — сложная и ответственная задача решение которой требует сопоставления затрат на контроль с возможными потерями от брака по разным вариантам контрольных операций.
Распространенной формой контроля сталсамоконтроль осуществляемый исполнителем. На самоконтроле могут работать отдельные рабочие бригады участки и целые цехи. Право работы на самоконтроле дается отделом технического контроля (ОТК) в случае если рабочий (подразделение) в течение длительного времени стабильно сдает продукцию ОТК с первого предъявления. При этом рабочим дают личное клеймо которым он помечает изготовленную продукцию.
6. Нормирование сборочных операций
Расчет режимов операций разборки и сборки агрегатов рекомендуется выполнять по установленным методикам приведенным в справочной литературе. Так например при расчете режимов сборки резьбовых соединений рассчитываются силы действующие на одно болтовое соединение крутящий момент при сборке соединения. При нормировании операций технологического процесса рассчитывается штучно-калькуляционное время выполнения операций. Составляющие штучного времени определяются по справочникам и нормативам.
При нормировании операций технологического процесса серийного производства определяют штучно-калькуляционное время по зависимости:
где - подготовительно-заключительное время связанное со сборкой партии изделий;
n – число изделий в партии;
Для серийногомассовогоиавтоматизированногопроизводств подготовительно-заключительное время равно нулю. Штучное время вычисляют как сумму основного Tо вспомогательного Tв времен и времени на организационно-техническое обслуживание рабочего места Tдоп.
Составляющие времен определяют по справочной и методической литературе.
Завертывание винтов: To = (0020x+0517)m
где m - количество одинаковых элементов используемых при сборке.
Если сборочная операция имеет несколько переходов то основное время на операцию определяется суммированием основных времен отдельных переходов. Вспомогательное время по данным работы составляет 15 60% от основного:
Если учесть что дополнительное время на сборочные операции составляет примерно 6 10% от оперативного а подготовительно-заключительное – 3 6% то штучно-калькуляционное время можно подсчитать по формуле:
= (006 010)+(003 006)n+
Разборочные работы нормируются по тем же зависимостям но значения времен увеличиваются на 15%.
Завертывание гаек:( X = 6 мм.; m = 15 шт.)
Завертывание болтов:( X = 60 мм.; m = 61 шт.)
Установка шплинтов и штивтов: :( X = 70 мм.; m = 3 шт.)
Установка шайб прокладок втулок:( X = 175 мм.; m = 23 шт.)
Установка крышек и головок по направляющим:( X = 30 мм.; m = 6 шт.)
Установка валов и осей:( X = 323 мм.; m = 3 шт.)
Установка зубчатых колес (cо шпонкой):( X = 80 мм.; m = 2 шт.)
Запрессовка шарикоподшипников:( X = 245 мм.; m = 6 шт.)
Таким образом 307+357+24+1+3291+132+1764 = 2099 мин.
В данной работе спроектированы технологические процессы сборки цилиндрического двухступенчатого редуктора. Расчет и проектирование технологических процессов проводили для мелкосерийного типа производства с учетом оборудования присущего ему. Это универсальные и станки с ЧПУ.
В результате разработки курсового проекта ознакомились с методом проектирования технологического процесса с учетом такта выпуска деталей и нормировать сборочные операции.
В курсовом проекте проведен анализ служебного назначения изделия и детали. Выполнен размерный анализ сборочных размерных цепей. Заложенные в конструкцию нормы точности не обеспечивали сборку по методу полной взаимозаменяемости поэтому были подобраны комплекты регулировочных прокладок обеспечивающих требуемые зазоры между подшипниками и их крышками. Выбраны технологические базы для общей и узловой сборки.
Курсовой проект выполнен в современных программных пакетах а именно в «Компас-3DV16» «Microsoft Office Word 2007» и др. позволяющих наиболее быстро и удобно осуществить разработку конструкторской и технологической документации выполнить проверку на моделях конструкторских решений выявить возможные ошибки и неточности в чертежах до запуска изделий в производство.
Ибрагимов А.У. Голубков Н.С. Механические передачи и их расчет. – Ижевск.: электронный учебник 2007г.
Смелягин А.И. Структура механизмов и машин: учебное пособие для вузов. – М.: Высшая школа 2006г.
Чурнилевский Д.М. детали машин и основы конструирования. – М.: машиностроение 2006г.
Иванов М.Н. Финогенов В.А. Детали машин. – М.: Высшая школа. 2010г.
Дунаев П.Ф. Леликов О.П. Конструирование узлов и деталей машин: Учеб. пособие для технических спец. вузов. - 6-е изд. исп. - М.: Высшая школа 2000.
Куклин Н.Г. Куклина Г.С. Житков В.К. Детали машин: учебник -М.: Высшая школа2005.
Скойбеда А.Т. Кузьмин А.В. Макейчик Н.Н. Детали машин и основы конструирования: учебное пособие- М.: Высшая школа 2006.
Михайлов А.В. "Разработка технологических процессов сборки изделия" Метод. указания Тольятти: Тольяттинский Государственный Университет 2001.
Базров Б.М. Основы технологии машиностроения: учебник для вузов. М.: Машиностроение 2005.
Рекомендуемые чертежи
- 23.04.2016
- 13.04.2024