Специальное приспособление для закрепления



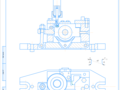
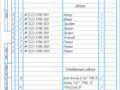
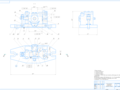
- Добавлен: 25.01.2023
- Размер: 154 KB
- Закачек: 1
Описание
Специальное приспособление для закрепления
Состав проекта
![]() |
![]() ![]() ![]() |
![]() ![]() ![]() ![]() |
![]() ![]() ![]() ![]() |
![]() ![]() ![]() ![]() |
Дополнительная информация
ПЗПР.docx
В данной работе рассматривается конструкция приспособления для обработки фрезерованием концевой фрезой по контуру детали на сверлильно-фрезерном станке с ЧПУ. Описывается назначение всех его элементов. Описывается принцип работы изделия. Проводится расчёт сил резания и проверка зажимного механизма на обеспечение недвижимости закрепления заготовки.
Исходные данные для проектирования ..6
Анализ исходных данных . 7
Выбор типа приспособления основных его элементов и узлов . ..10
Расчёт режимов и силы резания .. .12
Расчёт зажимной силы приспособления .. 14
Описание конструкции и порядка работы приспособления 16
Список использованных источников . 18
В работе будем рассматривать операцию фрезерования поверхности уступа. Закрепляемая в рассматриваемом приспособлении деталь относится деталям типа корпус . Приспособление используется для обработки концевой фрезой 8 мм. Двух криволинейных наружных поверхностей уступа корпуса. Причём обрабатывается сначала одну поверхность затем другую. Обработка осуществляется на сверлильно-фрезерном станке с ЧПУ. Задачей данной работы является расчёт сил резания и проверка усилия зажима при возникающих силах резания.
Исходные данные для проектирования
Исходными данными для проектирования являются:
-чертеж детали с технологическими требованиями;
-чертеж заготовки с технологическими условиями на ее изготовление;
-операционный эскиз детали и операционная карта на ее обработку;
-чертежи технологической оснастки.
Анализ исходных данных
Деталь корпус входит в состав электроспуска предназначенного для дистанционного управления работой спускового механизма. Внутри корпуса имеется втулка служащая магнитопроводом . Кроме того катушка и втулка служат для направления движения якоря. Бронзовая прокладка уменьшает время отпускания электроспуска. В корпусе имеются два отверстия в которых размещаются толкатели вместе с пружинами датчиков СОП .
Деталь изготавливается из стали 35ХГСА химический состав которой приведён в таблице 1.
Таблица 1 - Химический состав стали 35ХГСА
Содержание элементов %
Основные физико-химические свойства:
-плотность 84 кгм3 при 20 0С
-твердость - 212- 248 НВ
-хорошая обрабатываемость резанием
-свариваемость - ограниченная. Способы сварки: РДС АДС под флюсом и газовой защитой.
Деталь представляет собой неразъёмную корпусную деталь сложной формы образованную криволинейными и прямолинейными поверхностями. Деталь можно разбить на две составных части:
) “параллепипед” с наклонной нижней поверхностью под углом 15º имеющий в верхней части ухо шириной 16 мм. с радиусом скругления верхней части R8 и толщиной 21 ммсо ступенчатым отверстием 10 мм и 7 мм причём меньшее отверстие имеет глубину 5 мм.
В центральной части данной фигуры выполнено ещё одно ступенчатое отверстие 26 мм и 7 мм с переходом от большего диаметра к меньшему конусной поверхностью с углом 120. Симметрично от осей отверстия 26 мм на передней поверхности расположены четыре резьбовых отверстия М3-74 находящиеся на расстоянии 23 мм друг от друга.
В нижней правой четверти передней поверхности выполнено два отверстия с радиусами R3 и R25 переходящие одно в другое причём нижний край меньшего отверстия находится на расстоянии 05 мм от верхнего края резьбы.
) Эта часть представляет собой цилиндр с уступами на наружной поверхности. В нижней части цилиндра имеется прямоугольный сквозной паз шириной 35 мм с левой стороны имеется выступ высотой 24мм в нижней части которого имеется наклонная поверхность под углом 30 высотой 11 мм. С правой стороны имеется такой же уступ плавно сопрягающийся с первой составной частью.
На передней поверхности этого уступа выполнены два несквозных отверстия 1005 мм расположенных на высоте 22 мм от верхнего торца цилиндра. Расстояние между отверстиями 384 мм.
В верхней части уступа ширина которого равна 38 мм на расстоянии 6±01 мм от верхнего торца цилиндра и на расстоянии 55±01 мм от передней поверхности уступа имеется отверстие 58 мм ось которого перпендикулярна оси цилиндра и осям вышеописанных отверстий 1005 мм.. Верхняя часть уступа имеет фаску 3х45 мм.
Цилиндр имеет сквозное вертикальное отверстие 48 мм на внутренней поверхности которого расположены две канавки. Первая канавка кольцевая. Она расположена в нижней части отверстия и имеет высоту 35 мм и диаметр 525 мм. Вторая канавка расположена на расстоянии 19 мм от верхнего торца цилиндра. Высота канавки 6 мм. Канавка образованна сопряжением окружности радиусом 28 мм центр которой совпадает с центром отверстия 48 мм и двух окружностей радиуса 20 мм центры которых смещены относительно осей отверстия 48 мм (если смотреть на деталь сверху).
В нижней части детали расположена канавка с полукруглым сечением радиуса 225 мм проходящая через всю деталь по большему размеру.
Выбор типа приспособления основных его элементов и узлов
Исходя из программы выпуска деталей (крупносерийное производство) и особенностей операции (обработка криволинейной поверхности концевой фрезой на станке с ЧПУ) выбираем специальное приспособление с ручным приводом.
Выбор установочных элементов
Необходимо отметить что установочные элементы приспособлений могут быть двух видов:
Основные установочные элементы приспособлений предусматриваются схемой базирования и определяют положение детали в соответствии с правилом шести точек. В качестве основного установочного элемента в данном приспособлении применяются плоские упорная пластины. Две большие пластины крепятся пятью болтами М10 маленькая пластина крепится на двух болтах М6 и двух штифтах 25 мм.
Рисунок 1 - Пластина упорная маленькая
Рисунок 2 - Пластины упорные большие
Поверхности установочных деталей и механизмов должны обладать большой износоустойчивостью поэтому их изготавливают из сталей 15 и 20 с цементацией на глубину 08 12 мм с последующей закалкой до твердости HRC=50 55.
В данном приспособлении используется комбинированный рычажно-винтовой механизм. Принципиальная схема его приведена ниже.
Рисунок 3 - Принципиальная схема приспособления
Расчёт режимов и силы резания
) Расчёт длины рабочего хода
Где LРЕЗ = 24мм – длина обработки измеренная в направлении резания
По таблице стр.301 [1]
У = 6 мм – длина подвода врезания и перебега инструмента
Тогда LP.X. = 24 + 6 = 30 мм.
) Выберем подачу на зуб по карте Ф2 стр.83 [1]
) Определяем стойкость инструмента по нормативам ТР в минутах резания по карте Ф3 стр. 87 [1]
Где - коэффициент резания каждого инструмента
кф – коэффициент учитывающий количество инструментов в наладке
ТМ – стойкость фрезы в минутах машинной работы
Тогда ТР = 1 60 08 = 48 мин.
) Расчёт скорости резания числа оборотов шпинделя минутной подачи
а) Определяем рекомендуемую нормативную скорость резания по карте Ф4 стр. 88 [1]:
б) Рассчитываем число оборотов шпинделя
По паспорту станка принимаем n = 1500 мин -1
в) Уточним скорость резания по принятым оборотам шпинделя
г) Рассчитаем минутную подачу по принятому значению числа оборотов шпинделя
Z – число зубьев инструмента
SM = 0025 4 1500 = 150 мммин
) Рассчитаем основное машинное время обработки
) По параметрам фрезы и режимам резания определяем условную среднюю окружную силу резания:
По табл. 80([2] стр.40) имеем:
сP=82; хP=11; yP=08; zP=095; qP=-11
Pzy=82111002508100958-114=15500 Н
) Находим поправочный коэффициент учитывающий скорость резания. Так как V 100 ммин то по табл. 81 ([2] стр.41) kv=088;
) Находим поправочный силовой коэффициент учитывающий значение переднего угла. По табл. 81(там же) k=0.9
) Определяем истинную среднюю окружную силу резания:
Pz= Pzykvk=1550880.9=12276 Н
Расчёт зажимной силы приспособления
Рабочий закрепляет заготовку в приспособлении с помощью накидного ключа с длиной рукоятки 260 мм прикладывая при этом силу W= 100H. Тогда схема закрепления с учётом действия сил резания выглядит следующим образом выглядит следующим образом:
Рисунок 4 - Схема закрепления заготовки
PY = 0.4 PZ = 4910.4 H
где - КПД рычажного механизма (09)
Q1 – сила создаваемая винтовым механизмом
где W - усилие прилагаемое рабочим (100Н)
lключа – длина рычага ключа (260 мм.)
dcp – средний диаметр резьбы (9 мм)
ПР - приведённый угол трения (550’)
f – коэффициент трения на торце гайки (01)
Q3 – сила создаваемая винтовым механизмом
Видно что силы зажима гораздо больше чем силы стремящиеся сдвинуть заготовку во время обработки . Следовательно приспособление удовлетворяет условиям обработки детали на данной операции.
Описание конструкции и порядка работы приспособления.
Данное приспособление представляет собой некое подобие тисков приводимых в действие винтовым механизмом который закручивается рабочим с помощью ключа и взаимодействия с рычажным механизмом зажимают заготовку с двух сторон. Данный вид зажимного механизма выбран исходя из того что приспособление используется для обработки заготовки на станке с ЧПУ где очень важную роль играют габариты приспособления и его вес.
Приспособление устанавливается на столе станка с помощью двух болтов. Положение заготовки определяется с помощью трёх упорных пластинок и одной сменной регулировочной пластины крепящейся к корпусу приспособления с помощью винтов. Прижим заготовки осуществляется с помощью двух рычажных прижимов: бокового и нижнего. На нижнем прижиме который продвигает заготовку к верхним упорам крепится подвижный v-образный упор обеспечивающий равномерный прижим заготовки к верхним упорным пластинам. Боковой прижим продвигает заготовку в угол до упора с регулировочной пластиной и зажимает её. Для предотвращения поворота заготовки в результате обработки её одевают на палец упирают в боковую поверхность корпуса и закрепляют гайкой через гайку большого диаметра.
Последовательность работы приспособления в процессе выполнения операции.
Заготовка одевается отверстием на палец закручивается гайка пальца и заготовка прижимается к боковой поверхности.
Затягивается гайка рычажно-винтового механизма и заготовка продвигается до упора вверх и в угол и зажимается.
После окончания обработки процесс раскрепления происходит в обратном порядке.
В данной работе были выбраны тип приспособления необходимого для обработки заготовки его основные элементы и узлы. Также была рассчитана сила Q развиваемая на прижимах приспособления и необходимая для надежного закрепления заготовки в приспособлении она равна 13332 кН и 16106 кН.
Были определены размеры приспособления отвечающего требованиям надежного закрепления заготовки в приспособлении в процессе резания.
Список использованных источников.
Режимы резания металлов. Справочник под ред. Ю.В. Барановского – М.: Машиностроение 1972 – 407с.
Бобров В. Ф. Основы и теории резания материалов. М. «Машиностроение» 1975
Ансеров М.А. Приспособления для металлорежущих станков М. Машиностроение 1964г. 652 стр.
Станочные приспособления т.1 под ред. Вардашкина Б.Н. и Шатилова А.А. М. Машиностроение 1984г. 591 стр.
Горошкин А.К. Приспособления для металлорежущих станков. Справочник М. Машиностроение 1979г.303 стр.
1.spw

Винт М8х30.88.35 ГОСТ 11738-72
Болт 7002-0578 ГОСТ 14724-69
Шайба 7019-0465 ГОСТ 4087-69
Шпонка 7031-0653 ГОСТ 14739-69
Штифт 2.5х16 ГОСТ 12207-79
Штифт 12т6х30 ГОСТ 3128-70
Приспособление.cdw

А42 06 005 оп 0190 (станок КСС 2Ф3)
При выполнении операции 0190
ся. Приспособление монтировать на подставку ЛК7273-4958
Остальные ТТ по СТП АДЛ 0001-76)
Схема обработки.cdw

Рекомендуемые чертежи
- 19.09.2022