Совершенствование технологического процесса механической обработки вала дифференциала редуктора агрегата МЗПП в условиях ЗАО МРК




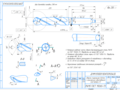
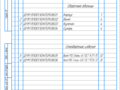
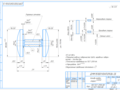
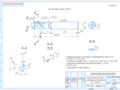
- Добавлен: 24.01.2023
- Размер: 1 MB
- Закачек: 0
Описание
Совершенствование технологического процесса механической обработки вала дифференциала редуктора агрегата МЗПП в условиях ЗАО МРК
Состав проекта
![]() |
![]() |
![]() ![]() ![]() |
![]() ![]() ![]() ![]() |
![]() |
![]() |
![]() |
![]() ![]() ![]() |
![]() ![]() ![]() |
![]() ![]() ![]() |
![]() ![]() ![]() |
![]() ![]() ![]() |
![]() ![]() ![]() |
![]() ![]() |
![]() ![]() ![]() |
![]() ![]() ![]() |
![]() ![]() ![]() |
![]() ![]() ![]() |
![]() ![]() ![]() |
![]() ![]() ![]() |
![]() ![]() ![]() |
![]() ![]() ![]() |
![]() ![]() ![]() |
![]() ![]() ![]() |
![]() ![]() ![]() |
![]() ![]() ![]() ![]() |
![]() ![]() ![]() ![]() |
![]() |
![]() |
![]() |
![]() ![]() ![]() ![]() |
![]() ![]() ![]() ![]() |
![]() ![]() ![]() ![]() |
![]() ![]() ![]() ![]() |
![]() ![]() ![]() ![]() |
![]() ![]() ![]() |
![]() ![]() ![]() ![]() |
![]() |
![]() |
![]() |
![]() |
![]() ![]() ![]() ![]() |
![]() |
![]() ![]() ![]() |
Дополнительная информация
Титл техпроцесс.doc
Федеральное агентство по образованию
Государственное образовательное учреждение высшего профессионального образования
Магнитогорский государственный технический университет им. Г.И. Носова
Кафедра Технологии машиностроения
ТЕХНОЛОГИЧЕСКИЙ ПРОЦЕСС МЕХАНИЧЕСКОЙ ОБРАБОТКИ
Совершенствование технологического процесса механической
четырехкулачковый патрон 1к2.cdw

с независимым перемещением
кулачков ГОСТ3890-82
Вал дифференциала -020 Разметочная.doc
МЕХАНИЧЕСКОЙ ОБРАБОТКИ
НАИМЕНОВАНИЕ ОПЕРАЦИИ
Наименование и марка материала
Сталь 38ХМ ГОСТ 4543-71
Оборудование (наименование модель)
Приспособление (наименование код)
Плита разметочная ГОСТ 10905-86
Инструмент (код наименование)
Установить и закрепить
Разметить 2 шпоночных
паза B=12мм на длину
Разметить отверстие
карта эскизов - оконч точениевд.doc
Кафедра технологии машиностроения
К А Р Т А Э С К И З О В
Вал дифференциала -015 Токароно-винторезная - окончат 74 мин на обр.DOC
Кафедра технологии машиностроения
МЕХАНИЧЕСКОЙ ОБРАБОТКИ
НАИМЕНОВАНИЕ ОПЕРАЦИИ
Наименование и марка материала
Сталь 38ХМ ГОСТ 4543-71
Оборудование (наименование модель)
Приспособление (наименование код)
Патрон четырехкулачковый с независимым
Токарный станок 1М65
перемещением кулачков ГОСТ 3890-82
Инструмент (код наименование)
Установить и закрепить
ГОСТ 3.1105-74 Форма 5 а
Кафедра технологии машиностроения
К А Р Т А Э С К И З О В
ГОСТ 3.1404-74 Форма 1а
длину L=152 мм чисто
длину L=152 мм тонко
Точить канавку 92-087
Нарезать резьбу М95х2
длину L=152 мм начерно
на длину L=152 мм чисто
Точить канавку 92-087
длину L=35 мм начерно
Вал дифференциала -035 Разметочная.doc
МЕХАНИЧЕСКОЙ ОБРАБОТКИ
НАИМЕНОВАНИЕ ОПЕРАЦИИ
Наименование и марка материала
Сталь 38ХМ ГОСТ 4543-71
Оборудование (наименование модель)
Приспособление (наименование код)
Плита разметочная ГОСТ 10905-86
Инструмент (код наименование)
Установить и закрепить
Вал дифференциала Контрольная.doc
Кафедра технологии машиностроения
ТЕХНИЧЕСКОГО КОНТРОЛЯ
НАИМЕНОВАНИЕ ОПЕРАЦИИ
Наименование марка материала
Наименование оборудования
Плита контрольная ГОСТ 10905-86
Приспособление (код наименование)
Измерительный инструмент (код наименование)
Контролировать линейные размеры
Штангенциркуль ШЦ-II 250 ГОСТ 166-89
Контролировать диаметральные размеры
Микрометр гладкий МК 125 ГОСТ 6507-90
Контролировать шпоночный паз
шпоночный ГОСТ 24116-80
Контролировать отверстие 180H7(+0.04)
Калибр-пробка ГОСТ 2849-94
Контролировать метрическую резьбу
Калибр для метрической резьбы ГОСТ 24997-81
Контролировать шероховатость
Эталоны шероховатости
Вал дифференциала -055 Круглошлифовальная.doc
МЕХАНИЧЕСКОЙ ОБРАБОТКИ
НАИМЕНОВАНИЕ ОПЕРАЦИИ
Наименование и марка материала
Сталь 38ХМ ГОСТ 4543-71
Оборудование (наименование модель)
Приспособление (наименование код)
Патрон четырехкулачковый с независимым
перемещением кулачков ГОСТ 3890-82
Круглошлифовальный станок 3У131ВМ
Инструмент (код наименование)
Установить и закрепить
Шлифовать поверхность
Переустановить заготовку
ГОСТ 3.1105-74 Форма 5 а
Кафедра технологии машиностроения
К А Р Т А Э С К И З О В
Вал дифференциала -040 Долбежная.DOC
Кафедра технологии машиностроения
МЕХАНИЧЕСКОЙ ОБРАБОТКИ
НАИМЕНОВАНИЕ ОПЕРАЦИИ
Наименование и марка материала
Сталь 38ХМ ГОСТ 4543-71
Оборудование (наименование модель)
Приспособление (наименование код)
Долбежный станок 7510
Инструмент (код наименование)
Установить и закрепить
Долбить шпоночный паз
ГОСТ 3.1105-74 Форма 5 а
Кафедра технологии машиностроения
К А Р Т А Э С К И З О В
Вал дифференциала -050 Слесарная.doc
МЕХАНИЧЕСКОЙ ОБРАБОТКИ
НАИМЕНОВАНИЕ ОПЕРАЦИИ
Наименование и марка материала
Сталь 38ХМ ГОСТ 4543-71
Оборудование (наименование модель)
Приспособление (наименование код)
Инструмент (код наименование)
Зачистить заходы резьбы у
Карта эскизов - долбление.doc
Кафедра технологии машиностроения
К А Р Т А Э С К И З О В
Вал дифференциала -045 вертикально-фрезерная.DOC
Кафедра технологии машиностроения
МЕХАНИЧЕСКОЙ ОБРАБОТКИ
НАИМЕНОВАНИЕ ОПЕРАЦИИ
Наименование и марка материала
Вертикально-фрезерная
Сталь 38ХМ ГОСТ 4543-71
Оборудование (наименование модель)
Приспособление (наименование код)
Тиски станочные ГОСТ1651896
Вертикально-фрезерный станок 6Т12
Инструмент (код наименование)
Установить и закрепить
ГОСТ 3.1105-74 Форма 5 а
Кафедра технологии машиностроения
К А Р Т А Э С К И З О В
Карта эскизов - фрезерование вд.doc
Кафедра технологии машиностроения
К А Р Т А Э С К И З О В
Карта эскизов - сверление вд.doc
Кафедра технологии машиностроения
К А Р Т А Э С К И З О В
Вал дифференциала -025 Радиально-сверлильный.DOC
Кафедра технологии машиностроения
МЕХАНИЧЕСКОЙ ОБРАБОТКИ
НАИМЕНОВАНИЕ ОПЕРАЦИИ
Наименование и марка материала
Радиально-сверлильная
Сталь 38ХМ ГОСТ 4543-71
Оборудование (наименование модель)
Приспособление (наименование код)
Тиски станочные ГОСТ 16518-65
Радиально-сверлильный станок 2М55
Инструмент (код наименование)
Установить и закрепить
отверстие 505 по оси II-II
ГОСТ 3.1105-74 Форма 5 а
Кафедра технологии машиностроения
К А Р Т А Э С К И З О В
Вал дифференциала -030 Горизонтально-расточная.DOC
Кафедра технологии машиностроения
МЕХАНИЧЕСКОЙ ОБРАБОТКИ
НАИМЕНОВАНИЕ ОПЕРАЦИИ
Наименование и марка материала
Горизонтально-расточная
Сталь 38ХМ ГОСТ 4543-71
Оборудование (наименование модель)
Приспособление (наименование код)
Тиски станочные самоцентрирующиеся с призмати-
Горизонтально-расточной станок 2А660
ческими губками ГОСТ 21168-75
Инструмент (код наименование)
Установить и закрепить
отверстие 180H7(+004)мм
ГОСТ 3.1105-74 Форма 5 а
Кафедра технологии машиностроения
К А Р Т А Э С К И З О В
Карта эскизов - растачивание вд.doc
Кафедра технологии машиностроения
К А Р Т А Э С К И З О В
Карта эскизов - подрезка торца вд.doc
Кафедра технологии машиностроения
К А Р Т А Э С К И З О В
Карта эскизов - шлифование вд.doc
Кафедра технологии машиностроения
К А Р Т А Э С К И З О В
резец.cdw

Материал режущей пластины Т15К6 ГОСТ 3882-74
Материал опорной пластины ВК6 ГОСТ 3882-74
Материал крепежной части 40Х ГОСТ 2590-88
Маркировать: материал режущей части резца
калибр - андриенко.cdw

ностей - Хим.Фос.Прм.
Технические требования по ГОСТ 2015-84.
Неуказанные предельные отклонения
Д.ММ.151001.10.КП.09.06
Заготовка.cdw

Нормализация поковки HB 235 272.
Поковочные уклоны 3-7
Сталь 38ХМ ГОСТ8479-70
Д.ММ.151001.10.КП.09.02
Спецификация.spw

с независимым перемещением
кулачков ГОСТ3890-82
Д.ММ.151001.10.КП.09.08.
Д.ММ.151001.10.КП.09.08.01
Д.ММ.151001.10.КП.09.08.02
Д.ММ.151001.10.КП.09.08.03
Д.ММ.151001.10.КП.09.08.04
Д.ММ.151001.10.КП.09.08.05
Винт М12 Сталь 45 ГОСТ 1477-75
Д.ММ.151001.10.КП.09.08.06
Винт М24 Сталь 40Х ГОСТ 11738-72
Заготовка А2 - 1к 2.cdw

Нормализация поковки HB 235 272.
Поковочные уклоны 3-7
Сталь 38ХМ ГОСТ8479-70
Д.ММ.151001.10.КП.09.02
фреза шпоночная.cdw

Материал хвостовой части - сталь 40Х по ГОСТ4543-71
Неуказанные предельные отклонения размеров
Допускаеться сварка трением.
Д.ММ.151001.10.КП.09.05
Фреза шпоночная 12мм с
цилиндрическим хвостовиком
Шаг винтовой канавки 103
Курсовой 5 курс ваол дифференциала зак. без разм. 1к2 на А2 оконч с изм.cdw

титульник Андриенко.doc
Федеральное агентство по образованию
Государственное образовательное учреждение
высшего профессионального образования
«Магнитогорский государственный технический университет им. Г.И. Носова»
Кафедра: Технологии машиностроения
РАСЧЕТНО-ПОЯСНИТЕЛЬНАЯ ЗАПИСКА
по дисциплине:Технология машиностроения
на тему: Совершенствование технологического процесса механической
Исполнитель:Андриенко МСстудент 5 курса группа КТ-05-1
Руководитель:Налимова М.В. доцент к.т.н.
(Ф.И.О. должность уч. степень уч. звание)
ЗАДАНИЕ НА КУРСОВОЙ ПРОЕКТ
Тема: Совершенствование технологического процесса механической
СтудентуАндриенко Мария Сергеевна
(фамилия имя отчество)
Исходные данные: Материалы практики чертеж детали базовый технологический процесс конспект лекций
Руководитель:Налимова М.В.
(подпись) (расшифровка подписи)
Задание получил:Андриенко м.С.
сверло 50,5.cdw

по ГОСТ 19265-73. Твердость не менее HRC 62 65
Материал хвостовика сталь марки 45 ГОСТ 1050-74. Твердость
Сердцевина сверла утолщается в направлении к хвостовику
мм на каждые 100 мм длины.
Неуказанные предельные отклонения размеров
Д.ММ.151001.10.КП.09.04
Сверло спиральное 50
с коническим хвостовиком
Шаг винтовой канавки 298 мм
режимы механической обработки.cdw

режущего инструмента
Вертикально-фрезерный
Радиально-сверлильный
коническим хвостовиком
Д.ММ.151001.10.КП.09.07
Вертикально-фрезерная
Радиально-сверлильная
ПЗ - вал дифференциала.doc
1 Анализ соответствия технических условий и норм точности служебному назначению вала-дифференциала6
2 Назначение конструкция и условия работы вала-дифференциала7
3 Обоснование выбора материала для изготовления вала-дифференциала7
4 Определение типа производства8
6 Разработка технологического процесса изготовления вала-дифференциала10
7 Расчет межоперационных припусков допусков и размеров заготовки11
8 Определение межоперационных припусков допусков и размеров11
8.1 Расчет припусков на обработку наружной поверхности 100-0022 мм12
8.2 Расчет припусков на обработку по длине L= мм19
8.3 Расчет припусков на обработку по длине L= мм22
9 Расчет режимов резания25
9.1 Расчет режима резания для однократного точения наружной цилиндрической поверхности диаметром 100-0022мм длиной L=152 мм26
9.2 Расчет режимов резания при сверлении сквозного отверстия 505 и длиной L=220 мм29
9.3 Расчет режима фрезерования при фрезеровании шпоночного паза B=12мм на длину L=41мм.34
10 Техническое нормирование операций39
11 Расчёт и конструирование режущего инструмента43
11.1 Расчет и конструирование токарного проходного упорного резца с твердосплавной пластины для обработки цилиндрической поверхности диаметром 100 мм43
11.2 Расчет и конструирование сверла для сверления сквозного отверстия 505мм глубиной L=220мм45
11.3 Расчет и конструирование шпоночной фрезы 12 мм для фрезерования шпоночного паза шириной B=12мм48
12 Расчет четырехкулачкового патрона с ручным приводом для точения поверхности 110мм длиной L=152мм51
13 Выбор конструирование и расчет калибра-пробки для контроля отверстия 180Н7(+004)мм55
Организационный раздел58
1 Организация технического контроля в цехе58
2 Организация инструментального хозяйства в цехе61
3 Организация ремонта оборудования в цехе62
Список используемых источников:65
Машиностроение – важнейшая отрасль современной промышленности. Рост и совершенствование производства различной продукции непосредственно обеспечивается развитием машиностроения так как его продукция – машины различного назначения – поставляются всем другим отраслям промышленности.
Технологами-машиностроителями выполнена большая работа по совершенствованию производства машин самого различного назначения. В настоящее время перед технологами машиностроителями стоят задачи дальнейшего повышения качества машин; снижения трудоемкости себестоимости и материалоемкости их изготовления внедрение механизации и автоматизации производства.
Повышение требований к качеству деталей машин вызывает необходимость поиска новых высокопроизводительных методов обработки поверхности обеспечивающих изготовление детали в соответствии с предъявляемыми требованиями.
Одной из основных завершающих стадий изготовления деталей машин является механическая обработка поверхностей заготовок – совокупность процессов с отделением или без отделения материала заготовки позволяющих достигнуть высоких показателей качества машины.
Технологический раздел
1 Анализ соответствия технических условий и норм точности служебному назначению вала-дифференциала
В моделях автомобилей и картах ведущие колёса находятся на одной общей оси. В повороте внутреннее колесо проходит меньший путь чем внешнее поэтому такая конструкция приводит к пробуксовке внутреннего колеса что негативно сказывается на управляемости автомобиля особенно при движении на больших скоростях. Для того чтобы ведущие колёса вращались несинхронно и применяется дифференциал.
Назначение дифференциала:
- передаёт крутящий момент с двигателя на ведущие колёса.
- служит дополнительной понижающей передачей.
- позволяет колёсам вращаться с разной скоростью (из-за этого дифференциал и получил своё название).
На автомобилях с одной ведущей осью дифференциал располагается на ведущей оси. На автомобилях со сдвоенной ведущей осью два дифференциала по одному на каждой оси. На вездеходах с отключаемым полным приводом по одному дифференциалу на каждой оси. На полноприводных автомобилях есть три дифференциала: по одному на каждой оси (межколесный) плюс один распределяет крутящий момент между осями (межосевой).
Формы и размер детали позволяют в качестве заготовки использовать поковку. Изготовление детали осуществляется в условиях единичного и мелкосерийного производства.
Рассмотрим действующий в цехе технологический процесс изготовления вала дифференциала:
)В кузнечно-термического отделении на молоте свободной ковкой получают необходимую форму заготовки после чего её охлаждают на воздухе.
)Полученную заготовку отправляют на термообработку для последующей нормализации и улучшения.
)Затем фрезеруют поверхности на фрезерном станке.
)Далее проводят разметку отверстия на разметочном столе закрепив деталь в тиски.
)Затем сверлят отверстие на сверлильном станке.
)На расточном станке растачивают отверстие.
)Затем проводят механическую обработку поверхностей и нарезают резьбу на токарно-винторезном станке закрепив заготовку в четырехкулачковом патроне с независимым перемещением кулачков.
)Далее на разметочном столе размечают шпоночные пазы.
)После на горизонтально-фрезерном станке фрезеруют 2 паза.
)На долбёжном станке долбят шпоночный паз.
)Затем зачищают заходы резьбы у пазов закрепив деталь в тисках.
)В завершение контролируют полученные механической обработкой размеры.
2 Назначение конструкция и условия работы вала-дифференциала
Вал-дифференциала представляет собой двуосный вал длиной L=599мм с диаметрами 100h7(-0.022) мм с резьбой М95х2 на концах валов и перпендикулярный первой оси вал длинной L=220мм с диаметром вала 288мм с отверстием 180H7(+0.04) и шпоночным пазом B=45P9
Деталь – вал-дифференциал является составной частью агрегата МЗПП. Данная деталь служит для передачи крутящего момента с двигателя на ведущие колёса. Основную нагрузку испытывают витки резьбы. При работе агрегата корпус вала-дифференциала испытывает высокое напряжение.
3 Обоснование выбора материала для изготовления вала-дифференциала
Сталь конструкционная легированная сталь 38ХМ. Применятся для изготовления валов шестерней шпинделей шпилек фланцев болтов дисков покрышек штоков и других ответственных деталей турбин и турбокомпрессоров работающих в условиях больших нагрузок и скоростях при температуре до 450-500 0С. Предел прочности 660 МПа.
Для изготовления вала выбирается конструкционная легированная сталь 38ХМ по ГОСТ 8479-70
В таблице приведены химический состав и механические свойства стали 38ХМ ГОСТ 8479-70
Таблица 1.2.1 - Химический состав и механические свойства стали 38ХМ.
Обозначение элементов
Механические свойства
Нормализация 880oC воздух отпуск 600oC воздух.
в - предел кратковременной прочности [МПа]
T - предел пропорциональности (предел текучести для остаточной деформации) [МПа]
- относительное удлинение при разрыве [ % ]
- относительное сужение [ % ]
KCU - ударная вязкость [ кДж м2]
HB - твердость по Бринеллю [МПа]
4 Определение типа производства
Тип производства играет очень важную роль при построении технологического процесса определяет характеристики используемого оборудования приспособлений инструмента квалификацию рабочих и многие другие параметры производства изделий. По типам производства машиностроительное производство подразделяется на три большие группы (см. табл. 1.4.1).
По таблице 1.4..1 определяется тип производства. Учитывая то что количество изготавливаемых валов дифференциала дифференциального редуктора равно 1 массой 92кг принимаем единичный тип производства. Он характеризуется использованием универсального оборудования которое оснащается универсальной и специальной оснасткой в зависимости от производственных возможностей. Форма организации производства - по видам оборудования свойственная единичному производству.
Таблица 1.4.1 - Зависимость типа производства от объема годового выпуска и массы детали.
Количество обрабатываемых в год деталей одного
наименования и типа размера
Крупных тяжелых большой трудоемкости массой более 30 кг
Средних размеров и трудоемкости массой от 8 до 30 кг
Небольших легких малотрудоемких массой менее 8 кг
Выбор вида исходной заготовки является ответственным этапом разработки технологического процесса так как коренным образом влияет на технологию механической обработки детали. Правильный выбор заготовки - установление метода ее получения формы и размеров – весьма существенно влияет на расход металла число операций трудоёмкость и себестоимость изготовления детали. При решении этого вопроса необходимо стремиться к тому чтобы форма и размеры заготовки были максимально приближены к форме и размерам готовой детали. Однако повышение точности размеров заготовки и ее усложнение неизбежно приводят к существенному увеличению себестоимости самой заготовки особенно в единичном производстве. Поэтому окончательное решение по выбору заготовки может быть принято только после экономического комплексного расчета себестоимости заготовки и механической обработки в целом.
На выбор метода получения заготовки оказывают влияние: материал детали ее служебное назначение и технические требования на изготовление; объем годового выпуска; форма поверхностей и размеры детали; производственные возможности заготовительных цехов.
Заготовкой для изготовления вала дифференциала является поковка.
Достоинства данного вида заготовки в максимальном приближении её размеров к размерам готовой детали; в более однородной структуре металла благодаря чему деталь будет иметь повышенную прочность.
6 Разработка технологического процесса изготовления вала-дифференциала
В основе разработки нового технологического процесса лежат технологические и экономические соображения. В соответствии с экономическими соображениями при изготовлении стержня затраты на производство должны быть минимальными. По технологическим соображениям проектируемый технологический процесс должен обеспечивать соответствие получаемого изделия чертежу.
Исходными данными для проектирования технологических процессов механической обработки является:
-материал заготовки;
-конструктивные формы и размеры детали;
-технические условия на изготовление детали;
-требования предъявляемые к точности изготовления детали и шероховатости ее поверхностей.
На основании анализа базового варианта технологического процесса изготовления детали и выбора заготовки разрабатывается проектный вариант маршрутного технологического процесса. Основной задачей этапа является составление общего плана технологического оснащения операций.
Технологический процесс изготовления вала-дифференциала состоит из следующих операций:
5 Радиально-сверлильная.
0 Горизонтально-расточная.
5 Горизонтально-фрезерная.
Наиболее подробное описание технологического процесса приведено в комплекте карт разработанного технологического процесса изготовления вала дифференциала.
7 Расчет межоперационных припусков допусков и размеров заготовки
При изготовлении изделия очень важно как можно эффективнее использовать материал заготовки увеличивать коэффициент использования материала. Это связано с тем что экономия материалов является важной задачей машиностроительной промышленности т.к. запасы сырья на нашей планете ограничены.
Величину межоперационного припуска на механическую обработку заготовки допуски на каждую операцию и требуемый размер заготовки выбираем в зависимости от экономической точности применяемого способа обработки конфигурации изделия и вида заготовки. Припуском называют слой материала удаляемый с поверхности заготовки в целях достижения заданных свойств обрабатываемой поверхности. Припуск может быть общим и межоперационным. Общим называют припуск снимаемый в течение всего процесса обработки данной поверхности. Он равен разности размеров заготовки и готового изделия. Межоперационным припуском называют припуск который удаляется при выполнении одной технологической операции.
8 Определение межоперационных припусков допусков и размеров
При изготовлении вала-дифференциала используем ступенчатую поковку.
Величину межоперационного припуска на механическую обработку заготовки допуски на каждую операцию и требуемый размер заготовки выбираем в зависимости от экономической точности применяемого способа обработки конфигурации изделия и вида заготовки. Общим припуском на обработку называется слой материала удаляемый с поверхности заготовки в процессе обработки на всех операциях. Расчет межоперационных припусков на механическую обработку заготовки и определение ее размеров можно проводить статистическим (табличным) и аналитическим (расчетным) методом.
Расчетом припусков аналитическим методом занимаются путем составления таблицы в которую последовательно записываются технический маршрут обработки и все значения элементов припуска (см. табл. 1.8.1 1.8.2 1.8.3).
Рассчитать припуски на обработку для внешнего диаметра вала дифференциала
0-0022 мм и на длины 599±0875 мм и 220±0575мм. Заготовка – поковка массой 219 кг.
8.1 Расчет припусков на обработку наружной поверхности 100-0022 мм
Рассчитаем припуски на обработку размера 100-0022 мм полученные данные занесем в таблицу 1.8.1.1
Число переходов определяется по формуле:
где К –коэффициент ужесточения точности размера:
где Тdз - допуск заготовки мм; Тdз=55 мм. [1. С. 147таблица 23]
Тdд –допуск детали мм; Тdд=0022 мм.
Определяем число переходов:
Принимаем количество переходов равным 5. Таким образом точность промежуточных размеров в процессе механической обработки будет соответствовать:
после первого перехода – 13 квалитет;
после второго перехода – 10 квалитет;
после третьего перехода – 8 квалитет;
после четвертого перехода – 7 квалитет;
после пятого перехода – 6 квалитет;
Качество поверхности для проката выбираем по таблицам [1 С 185 таблица 11]:
Определяем качество поверхности заготовки после механической обработки:
для черного точения по 13 квалитету Rz=250 мкм h=140 мкм;
для получистого точения по 10 квалитету Rz=125 мкм h=120 мкм;
для чистового точения по 8 квалитету Rz=40 мкм h=40мкм;
для тонкого точения по 7 квалитету Rz=5 мкм h=5мкм;
для тонкого точения по 6 квалитету Rz=25 мкм h=5мкм [1 C. 188 таблица 24];
Суммарное отклонение расположения при обработке поковки закрепленной в четырехкулачковом патроне:
где - общее отклонение оси детали от прямолинейности мкм;
- смещение оси заготовки в результате погрешности центрования мкм
Общее отклонение оси от прямолинейности:
где к – отклонение оси детали от прямолинейности [1 С. 186 таблица 16] мкм;
Смещение оси заготовки в результате погрешности центрирования:
где Т - допуск на диаметр базы заготовки используемой при центрование заготовки [1 С.147 таблица 23] Т = 55 мм.
Суммарное отклонение расположения при обработке поковок круглого сечения:
Для механической обработки суммарное отклонение расположения поверхностей рассчитываем по формуле:
Ку – коэффициент уточнения.
Значение коэффициента уточнения для каждого технологического перехода выбираем по справочной литературе [1 С. 190 таблица 29] :
Ку черн. точ.=006 - после чернового точения.
Ку получист. точ.=005 – после получистового точения
Ку чист. точ.=004 - после чистового точения.
Ку тонк. точ.=003 - после тонкого точения.
Ку шлиф. точ.=002 - после шлифования.
Суммарное отклонение расположения при черновом точении:
Суммарное отклонение расположения при получистовом точении:
Суммарное отклонение расположения при чистовом точении:
Суммарное отклонение расположения при тонком точении:
Суммарное отклонение расположения при шлифовании:
Определяем погрешность установки заготовки при закреплении в четырехкулачковом патроне [1 С. 44 таблица 16]. Эта цифра выбирается только для первого перехода. Верхняя строка таблицы с расчетами припусков в этой графе не заполняется.
при получистовом точении:
при чистовом точении:
-Расчетная величина минимальных припусков на обработку рассчитывается по формуле:
eI – погрешность установки заготовки на выполняемом переходе мкм.
Минимальный припуск при черновом точении:
Минимальный припуск при получистовом точении:
Минимальный припуск при чистовом точении:
Минимальный припуск при тонком точении:
Минимальный припуск при шлифовании:
Таблица 1.8.1.1 –Результаты расчета припуска на диаметр мм.
После выполнения всех расчетов необходимо проверить их правильность по формуле:
Tdзагот. – допуск на заготовку мкм;
Tdдетали – допуск на деталь мкм;
Расчет выполнен верно.
Чертежный размер заготовки мм.
Рисунок 1.8.1.1 – Схема графического расположения припусков допусков и предельных отклонений на обработку вала 100-0022 мм.
8.2 Расчет припусков на обработку по длине L= мм
На основании расчетов заполним таблицу 1.8.2.1
Расчет производим аналогично расчету на наружный диаметр.
Вычисляем коэффициент ужесточения точности размера по формуле (1. 1):
Значения допуска заготовки принимаем по таблице допусков для 17 квалитета: Tdзаг=8 (мм) [1.С.180]
Значения допуска детали принимаем по чертежу по 14 квалитету: Tdдет =175 (мм).
Определяем количество переходов по формуле (1.8.1.2):
Принимаем количество переходов равным 1.
Качество поверхности для заготовки:
Rz+ h=2000(мкм); [1 С. 188]
Определяем качество поверхности заготовки после механической обработки [1 С.8 таблица 4]:
для однократного точения по 14 квалитету
Rz=125 мкм h=120мкм[1 С.187 таблица 24].;
Суммарное отклонение расположения при обработке торцевых поверхностей поковок:
где R - радиус торцевой поверхности мм;
- отклонение от перпендикулярности мкммм. [1 С. 187 таблица 21].
Ку однократн. точ..= 005 – после подрезки торца.
Суммарное отклонение расположения при подрезки торца:
Определяем погрешность установки заготовки при закреплении в четырехкулачковом патроне [1 С. 16 таблица 44]. Верхняя строка таблицы с расчетами припусков в этой графе не заполняется.
-Расчетная величина минимальных припусков на обработку длины рассчитывается по формуле :
eI – погрешность установки заготовки на выполняемом переходе (мкм).
Минимальный припуск при однократном точении:
Таблица 1.8.2.1 – Результаты расчетов припусков на обработку вала дифференциала по длине L= мм.
После выполнения всех расчетов необходимо проверить их правильность по формуле: (1.8)
Чертежный размер 610мм.
Рисунок 1.8.1.1 – Схема графического расположения припусков допусков и предельных отклонений на обработку вала L=мм.
8.3 Расчет припусков на обработку по длине L= мм
На основании расчетов заполним таблицу 1.8.3.1
Расчет производим аналогично расчету на наружный диаметр .
Значения допуска заготовки принимаем по таблице допусков для 14 квалитета: Tdзаг=55 мм [1.С.180]
Значения допуска детали принимаем по чертежу по 17 квалитету: Tdдет =115 мм.
Rz+ h=2000 мкм; [1 С. 188]
Rz=125 мкм h=12 мкм[1 С.187 таблица 24].;
Суммарное отклонение расположения при обработке торцевых поверхностей поковок по формуле (1.9):
где H-высота ступени мм;
-Расчетная величина минимальных припусков на обработку длины рассчитывается по формуле:
После выполнения всех расчетов необходимо проверить их правильность по формуле: (1.8.1.8)
Чертежный размер 230мм.
9 Расчет режимов резания
При осуществлении технологических расчетов выбору режимов резания уделяется большое внимание. Параметры режимов резания должны обеспечивать наибольшую производительность труда при наименьшей себестоимости данной операции. Эти условия удается выполнить при работе инструментом рациональной конструкции с оптимальными геометрическими параметрами с максимальным использованием всех возможностей станка. При назначении режимов резания учитывают характер обработки материал и состояние заготовки тип и размеры инструмента материал его режущей части тип и состояние оборудования схему закрепления. Существует два способа определения режимов резания:
-аналитический метод - это метод при котором расчет режимов резания происходит с учетом всех поправочных коэффициентов;
-нормативно-справочный метод при котором режимы резания устанавливаются по таблицам нормативных справочников с использованием поправочных коэффициентов учитывающих изменение условий резания.
Произведем аналитическим способом расчет режимов резания для трех режимов резания:
- черновое точение наружной поверхности 100-0022мм;
- сверление сквозного отверстия 40мм;
- фрезерование шпоночного паза B=12мм l=41мм
9.1 Расчет режима резания для однократного точения наружной цилиндрической поверхности диаметром 100-0022мм длиной L=152 мм
Обработка ведется на токарно-винторезном станке 1М65. Мощность двигателя N=22 кВт; КПД станка =075. Обрабатываемый материал - Сталь 38 ХМ с 660 МПа. Режущий инструмент- токарный проходной упорный резец со сменной твердосплавной пластиной ГОСТ 19046-80 крепежная часть ГОСТ 24996-81 опорная пластина ГОСТ 19046-80. Геометрические параметры: .
Согласно расчету припусков на обработку наружной поверхности диаметром (таблица 1.8.1.1) глубина резания составляет t=531мм.
Подача при черновом точении принимается S=09 ммоб [2 С.364 таблица 11] что соответствует паспорту станка 1М65.
Скорость резания при наружном продольном точении рассчитывается по эмпирической формуле [2 С.265]:
где Т=45 мин- период стойкости резца;
t=531 мм - глубина резания;
- общий поправочный коэффициент на скорость резания [2 С.369]:
где - коэффициент учитывающий качество обрабатываемого материала [2 С.358 таблица1]:
где =08 - коэффициент характеризующий группу стали по обрабатываемости [2 С.359 таблица 2];
=10- показатель степени [2 С.359 таблица 2];
Подставляем найденные коэффициенты в (1.15)
- коэффициент учитывающий состояние поверхности заготовки
= 08 [2 С.361 таблица 5];
- коэффициент учитывающий материал инструмента
= 065[2 С. 361 таблица 6].
Подставляем найденные коэффициенты:
Находим скорость резания подставляя найденные значения в формула (1.13):
Определяем частоту вращения шпинделя соответствующую найденной скорости по формуле
Корректируем частоту вращения шпинделя по паспортным данным станка 1М65 и устанавливаем действительное значение частоты вращения =160обмин.
Определяем действительную скорость резания:
Силу резания при наружном продольном точении рассчитываем по формуле [2 С.371]:
общий поправочный коэффициент на условия резания
где коэффициент учитывающий влияние качества обрабатываемого материала[2 С. 362 таблица 9]
где n- показатель степени n=075 [2 С.362 таблица 9]
коэффициенты учитывающие влияние геометрических параметров режущей части инструмента на силу резания [2 С. 374 таблица 23]:
- коэффициент учитывающий главный угол в плане;
- коэффициент учитывающий передний угол;
- коэффициент учитывающий угол наклона главной режущей кромки;
- коэффициент учитывающий радиус скругления при вершине не учитывается так как используется твердосплавная пластина.
Подставляем выбранные коэффициенты в (1.20)
Находим силу резания по формуле (1. 19)
Мощность резания при точении рассчитывается по формуле [2 С. 371]
Так как мощность резания не превышает мощности на шпинделе станка (кВт) обработка поверхности рассчитанными режимами резания возможна.
9.2 Расчет режимов резания при сверлении сквозного отверстия 505 и длиной L=220 мм
Для сверления отверстия 40мм на радиально-сверлильном станке 2М55 мощностью двигателя 55кВт. Используем спиральное сверло нормальной заточки с коническим хвостовиком. Угол наклона поперечной режущей кромки y принимаем 70º задний угол в наиболее удалённой от оси сверла точке a = 10º в ближайшей к оси точке a = 12º угол при вершине 2φ = 118º угол наклона винтовой канавки =28º по ГОСТ 10903-77 L = 412 мм l = 225 мм.
Определяем глубину резания по формуле:
где t - глубина резания мм;
D - диаметр сверления мм;
S=06 ммоб [2 С. 381 таблица. 35]. Это значение соответствует паспортному значению станка.
Определяем скорость резания по формуле:
где V – скорость резания ммин;
D – диаметр сверла мм;
Т – стойкость резания мин; [2 С. 384 таблица. 40];
Сv - коэффициент учитывающий влияние режимов резания на скорость резания;[2 С.383 таблица. 38];
q-показатель степени характеризующий влияние диаметра сверла на скорость резания; [2 С. 383 таблица. 38];
yv - показатель степени характеризующий влияние подачи на скорость резания; 2 С.383 таблица. 38];
m - показатель степени характеризующий влияние стойкости инструмента на скорость резания; [2 С. 383 таблица. 38];
Kv - коэффициент учитывающий влияние различных факторов резания на скорость резания:
где Kmv – коэффициент учитывающий влияние свойств обрабатываемого материала на скорость резания:
где Кг – коэффициент характеризующий вид обрабатываемого материала;
sв – временный предел прочности обрабатываемого материала МПа;
nv – показатель степени характеризующий вид обрабатываемого материала;
Knv - коэффициент учитывающий влияние состояния поверхности обрабатываемого материала на скорость резания;
Т=110 мин; Сv=98; q=04; yv=05; m=02;
sв=660 МПа для стали 38 ХМ
Кг=08 [2 С. 359 таблица. 2];
nv=1 [2 С. 359 таблица. 2];
Кmv =09 при обработке быстрорежущим сплавом Р6М5 [2 С. 364 таблица. 4];
Кiv =075 при одинарной сверл из быстрорежущей стали.
Определяем частоту вращения шпинделя соответствующую данной скорости резания по формуле:
где n-частота вращения шпинделя обмин;
V-скорость резания ммин;
Корректируем полученную частоту вращения шпинделя по паспортным данным станка. Принимаем значение 90 обмин. Определяем действительную скорость резания по формуле:
где Vд - действительная скорость резания ммин;
D-диаметр сверла мм;
n-частота вращения шпинделя обмин;
Определяем крутящий момент возникающий при обработке по формуле:
где Mkp- крутящий момент возникающий при обработке Н×м;
Cм- коэффициент учитывающий влияние режимов резания на крутящий момент возникающий при обработке; [2 С. 385 таблица. 42];
q-показатель степени характеризующий влияние диаметра сверла на крутящий момент возникающий при обработке; [2 С. 385 таблица. 42];
у- показатель степени характеризующий влияние подачи на крутящий момент возникающий при обработке; [2 С. 385 таблица. 42];
Kp- коэффициент учитывающий влияние различных факторов резания на крутящий момент возникающий при обработке:
где Km–коэффициент учитывающий влияние свойств обрабатываемого материала на крутящий момент:
где sв – временный предел прочности обрабатываемого материала МПа;
n=075 [2 С. 264 таблица. 9];
Cм=00345; q=20; у=08;
sв=660 МПа для стали 38ХМ;
Определяем осевую силу возникающую при обработке по формуле:
где Poc-осевая сила возникающая при обработке Н
Cp- коэффициент учитывающий влияние режимов резания на осевую силу возникающую при обработке; [2 С. 281 таблица. 32];
q-показатель степени характеризующий влияние диаметра сверла на осевую силу возникающую при обработке; [2 С. 281 таблица. 32];
у- показатель степени характеризующий влияние подачи на осевую силу возникающую при обработке; [2 С. 281 таблица. 32];
Kp- коэффициент учитывающий влияние различных факторов резания на осевую силу возникающую при обработке;
Определяем мощность необходимую для обработки по формуле:
где N- мощность необходимая для обработки кВт;
Mkp- крутящий момент возникающий при обработке Н×м;
Проверяем возможность осуществления обработки на станке модели 2М55 по формуле:
Так как мощность резания не превышает мощности на шпинделе станка
кВт - обработка на данных режимах возможна.
9.3 Расчет режима фрезерования при фрезеровании шпоночного паза B=12мм на длину L=41мм.
Для работы на вертикально-фрезерном станке 6Т12 выбираем шпоночную фрезу из быстрорежущей стали Р9. Диаметр фрезы равен ширине шпоночного паза В; т.е. D = B = 12 мм. Принимаем стандартную фрезу с диаметром D =12 мм (ГОСТ 9140-78).
Назначаем подачу на зуб фрезы подачу [2 С. 406 таблица 80]. Для шпоночной фрезы из быстрорежущей стали диаметром 12 мм = 018 мм.
При фрезеровании шпоночной фрезой глубина резания t = 35 мм.
Глубина паза при фрезеровании его за один проход принимается за ширину фрезерования
Период стойкости фрезы Т = 50 мин [2 с. 411 таблица 82].
Определяем скорость резания в метрах в минутах по формуле
= 12 [2 C. 408 таблица 81];
q = 03 [2 C. 408 таблица 81];
m = 026 [2 C. 408 таблица 81];
y = 025 [2 C. 408 таблица 81];
u = 0 [2 C. 408 таблица 81];
p = 0 [2 C. 408 таблица 81];
Подставляем найденные коэффициенты в (1.37)
= 03[2 С. 361 таблица 6].
Определяем скорость фрезерования по формуле (1.35):
Определяем частоту вращения шпинделя соответствующую данной скорости фрезерования по формуле:
Определяем частоту вращения шпинделя соответствующую найденной скорости фрезерования по формуле (1. 38):
Корректируем частоту вращения шпинделя по паспортным данным станка и устанавливаем действительное значение частоты вращения: .Определяем действительную скорость резания по формуле:
Определяем действительную скорость резания по формуле (1. 39).
Рассчитываем окружную составляющую силы резания по формуле
где = 682 [2 C. 412 таблица 83];
= 086 [2 C. 412 таблица 83];
= 072 [2 C. 412 таблица 83];
u = 10 [2 C. 412 таблица 83];
q = 086 [2 C. 412 таблица 83];
w = 0 [2 C. 412 таблица 83];
Определим коэффициент учитывающий влияние качества поверхности обрабатываемого материала на силу резания при фрезеровании:
= 03 [2 C. 362 табл. 9];
Подача на один оборот определяется по формуле:
где z- число зубьев фрезы;
Sz- подача на один зуб мм
Определим подачу на один оборот::
Подача минутная определяется по формуле:
где n-частота вращения шпинделя обмин
S- подача на один оборот ммоб
По паспорта станка 6Т12 сверяем минутную подачу примем SM= 20 мммин.
Определим осевую составляющую силы резания:
Определяем мощность в киловаттах необходимую для осуществления процесса фрезерования по формуле:
Рассчитаем мощность:
Проверяем возможность осуществления обработки на вертикально-фрезерном станке модели 6Т12.
= 75 кВт (по паспорту станка 6Т12);
h = 08 (по паспорту станка 6Т12);
Так как > значит обработка возможна.
10 Техническое нормирование операций
Техническая норма времени – время устанавливаемое на выполнение данной операции при определенных организационно-технических условиях и наиболее эффективном использовании всех средств производства с учетом производственного опыта.
Норма штучного времени – норма времени на изготовление одной детали.
где – основное время выполнения операции;
– вспомогательное время выполнения операции не перекрываемое основным временем;
– время обслуживания рабочего места отнесенное к одной штуке;
– время на организацию рабочего места;
– время учитывающее регламентированные перерывы на отдых и естественные надобности рабочего.
Норму штучного времени также можно рассчитать по формуле
где a - процент потерь времени от учитывающий все остальные составляющие (a=610%).
Рассчитаем основное время Тo рассчитывается для трех режимов (см. пункт 1.9).
а) для токарной операции основное время на обработку поверхности определяется по формуле:
где =1 - число проходов
- расчетная длина рабочего хода инструмента с учетом врезания и перебега инструмента:
где: =115- длина обрабатываемой поверхности в направлении подачи мм;
-длина врезания инструмента мм;
=0 мм(для проходных упорных резцов);
=0-длина перебега инструмента мм;
Подставляем полученные значения в формулу (1.10.3)
б) основное время обработки для сверлильных работ:
- расчетная длина рабочего хода инструмента с учетом врезания и перебега инструмента (1. 48):
где: =220- длина обрабатываемой поверхности в направлении подачи мм;
=3 - длина перебега инструмента мм;
Подставляя значения рассчитываем основное время:
в) основное время обработки для фрезерования:
Определим основное фрезерования по формуле (1.47)
Определим расчетную длину хода инструмента по формуле (1.48)
где: =41- длина обрабатываемой поверхности в направлении подачи мм;
Подставляем полученные значения в формулу (1.47)
Определим норму штучного времени для трех операций по формуле (1.46)
а) для токарной операции:
=105 мин; = 27 мин; =6%
=407 мин; = 17 мин; =6%
в) для фрезерования:
=23 мин; = 172 мин; =6%
Для остальных операции приведено в маршрутной карте технологического процесса обработки данной детали.
11 Расчёт и конструирование режущего инструмента
11.1 Расчет и конструирование токарного проходного упорного резца с твердосплавной пластины для обработки цилиндрической поверхности диаметром 100 мм
Для чернового точения наружной поверхности диаметром 100 мм проектируется токарный проходной упорный резец со сменной твердосплавной пластиной ГОСТ 19046-80 крепежная часть ГОСТ 24996-81 опорная пластина ГОСТ 19046-80. Главный угол в плане j=90° главный задний угол a=0° передний угол g=11°. Расчёт режимов резания провели в разделе 1.9.1 по ним получили =66085 Н
Рассчитаем допустимые размеры сечения державки резца при квадратном сечении (b=h) [4.Стр. 99]:
где sи.д. = 300 МПа – допустимое напряжение на изгиб (для стали 45);
= 66085Н – сила резания;
– вылет резца находится по формуле но т.к. высота резца () на данный момент не известна то примем для расчётов наибольшее значение для станка 1М65 то есть =40мм а значит мм.
Из ГОСТ 29132-91 выбираем b=h=20 мм. А значит действительный вылет резца будет равен:
Расчет крепежно-присоединительной части состоит из расчета на прочность и жесткость.
Максимальная нагрузка допускаемая прочностью резца [4.С. 100]:
Расчёт на прогиб вершины резца:
где = 2×1011 Па – модуль упругости первого рода;
– осевой момент инерции:
Полученная величина прогиба получилась меньше допускаемого значения 01×10-3 м а значит при дальнейших расчётах примем = 01×10-3 м.
Максимальная нагрузка допускаемая жесткостью резца [3.С. 100]:
Сравнивая силу резания и максимальное значение нагрузок допустимые его прочностью и жесткостью приходим к выводу что обработка этим резцом возможна.
Конструктивные размеры резца берём по ГОСТ 29132-81: общая длина резца: 125 мм; расстояние от вершины резца до боковой поверхности в направлении лезвия f = 205+05 мм.
Общепринятое обозначение резца: PTGNR-2020К11-Т.
11.2 Расчет и конструирование сверла для сверления сквозного отверстия 505мм глубиной L=220мм
Для сверления отверстия 505мм на радиально-сверлильном станке 2М55 используем спиральное сверло нормальной заточки с подточкой поперечной кромки и ленточки с коническим хвостовиком. Угол наклона поперечной режущей кромки y принимаем 50º задний угол в наиболее удалённой от оси сверла точке a = 10º в ближайшей к оси точке a = 20º угол при вершине 2φ = 118º угол наклона винтовой канавки =28º. Общая длина сверла L длина рабочей части l принимаем по ГОСТ 10903-77 L = 412 мм l = 225 мм.
Определяем геометрические параметры рабочей части сверла.
Шаг винтовой канавки [4.С. 193]:
Толщина сердцевины dc сверла выбирается в зависимости от диаметра сверла. При D=1380 мм dc =(014 025) D то есть dc = 12 мм.
Утолщение сердцевины 14 – 18 мм на 100 мм длины рабочей части сверла. Принимаем 15 мм.
Обратная конусность сверла на 100 мм длины рабочей части должна составлять 005 – 012 мм. Принимаем 01 мм.
Ширину ленточки fo и высоту затылка по спинке К выбираем в соответствии с диаметром сверла [4. С 194 таблица 63]: fo = 3 мм К = 15 мм.
Ширина пера В [4 С 194]:
Геометрические элементы профиля фрезы для фрезерования канавки сверла определяем аналитическим методом.
Большой радиус профиля [4.С. 193]:
Меньший радиус профиля [4.С. 194]:
Ширина профиля [4.С. 194]:
По данным размерам строится профиль канавочной фрезы. Устанавливаются основные технические требования и допуски на размеры сверла по ГОСТ 10903-77. Предельные отклонения диаметра сверла D = 505h9(-0074) мм. Допуск на общую длину и длину рабочей части сверла равен удвоенному допуску по 14 квалитету с симметричным расположением предельных отклонений (±IT142) по ГОСТ 25347-82. Предельные отклонения размеров конуса хвостовика устанавливается по ГОСТ 2848-75.
Радиальное биение рабочей части сверла относительно оси хвостовика не должно превышать 015мм. Углы 2j=118°±2° угол наклона винтовой канавки w = 28°-1°.
Предельные отклонения размеров подточки перемычки режущей части сверла +05 мм. Твердость рабочей части сверла HRC 63-66.
11.3 Расчет и конструирование шпоночной фрезы 12 мм для фрезерования шпоночного паза шириной B=12мм
Заготовку из материала сталь 38ХМ обрабатываем на вертикально-фрезерном станке 6Т12. Значение предела прочности sв=660 МПа для стали 38ХМ
Стандартная шпоночная фреза с цилиндрическим хвостовиком по ГОСТ 9140-78. Диаметр фрезы D = 12 мм длина рабочей части фрезы l = 16 мм.
Материал режущей части – быстрорежущая инструментальная сталь Р9 (ГОСТ 19265-88).
Таблица 1.11.3.1 -Химический состав стали Р9.
Кобальт (Co) не более
Кремний (Si) не более
Молибден (Mo) не более
Марганец (Mn) не более
Никель (Ni) не более
Твердость HRC = 59. Плотность ρ = 83 гсм3. Теплостойкость T = 620 C.
Материал хвостовика сталь 40Х (ГОСТ 4543-71).Твердость НВ 217. sТ = 785 МПа [ср] = 471 МПа.
Расчет фрезы на кручение
Этот расчет производим для опасного сечения. Опасным сечением является сечение шейки фрезы между рабочей частью и хвостовиком с диаметром d1 = 105 мм. Расчет сводится к определению критического момента опасного сечения:
Мкрит. = Wр · (1.63)
где: Wр – полярный момент инерции мм3;
– касательное напряжение Мпа
По ГОСТ 4543-71 для стали 40Х sТ = 785 МПа; [n]=2.
Подставляя данные значения в формулу получим
[s] = 7852=3925 МПа.
Определяем касательное напряжение
t = (05 – 06)×3925=06 × 3925 = 2355 МПа.
Полярный момент инерции находим по формуле:
Найдем критический момент опасного сечения по формуле (1.11.3.1):
Мкрит. = 0227 10-6 · 2355 10-6 = 535 Нм.
Определяем крутящий момент:
где Pz – сила резания Pz = 2216 Н;
D – диаметр фрезы мм;
Для проверки расчета необходимо учесть условие:
Условие выполняется – расчет сделан правильно.
Расчет фрезы на изгиб
W0 – осевой момент инерции мм3.
Рх = 1411 · Pz. (1.68)
Рх = 1411 · 2216 = 3127 Н.
Определим осевой момент по инерции по формуле:
Рассчитаем предел прочности на изгиб по формуле(1.67)
Проверяем выполнение условия:
Условие выполняется.
Рассчитанная фреза полностью удовлетворяет условиям работы.
12 Расчет четырехкулачкового патрона с ручным приводом для точения поверхности 110мм длиной L=152мм
В качестве приспособления выбирается четырехкулачковый патрон с независимым движением кулачков (Рисунок 1.12.1) на токарно-винторезной операции. Такие патроны обеспечивают надежную установку и закрепление обрабатываемых деталей на шпинделе передней бабки станка.
Определение схемы действия сил на обрабатываемую заготовку.
Рисунок 1.12.1 - Схема действия сил действующих на заготовку
Сила резания создает момент Н м:
где Pz – тангенциальная составляющая силы резания Н;
d1 – диаметр обрабатываемой части заготовки d1=110 мм.
Суммарная сила зажима заготовки четырехкулачковым патроном:
где К – коэффициент запаса (для чернового перехода К=26);
f – коэффициент трения между поверхностями заготовки и кулачков f = 08;
L – размер заготовки зажатой кулачками L=230мм.
Находим силу зажима заготовки одним кулачком патрона:
где n – количество кулачков.
Величину W проверяют на возможность продольного сдвига заготовки силой Px по формуле:
где К – коэффициент запаса;
f – коэффициент трения между поверхностями заготовки и кулачков
Определим силу подачи:
общий поправочный коэффициент на условия резания (см. раздел 1.9.1)
Определим силу ручного зажима ключом.
Для выбранного типа патрона зажим осуществляется винтом. При зажиме в патроне расчет усилия привода зажимного устройства сводится к расчету усилия для зажима гайкой :
где Q – необходимое усилие зажима;
=37 мм - средний диаметр резьбы;
= 40 мм - диаметр винта;
=2о30’ - угол подъема резьбы;
- приведенный угол трения =015;
=012 - коэффициент трения на торце винта (между кулачком и деталью).
Основным параметром винтового зажима будет являться длина рычага обеспечивающая зажим заготовки.
Так как патрон является ручным то зажимная сила ограничивается мускульной силой рабочего осуществляющего данную операцию (150 Н). Для ручного зажима выбираем =150 Н.
Таким образом имеем:
Берем длину рычага =065м=650мм.
Рассчитаем приспособление на точность
Для получения требуемой точности изготавливаемой детали в приспособлении необходимо выбрать такую схему приспособления при которой действительные погрешности базирования eб заготовки в приспособлении были бы меньше или равны допустимым значениям eдоп погрешности базирования:
Допускаемое значение погрешностей базирования обрабатываемой детали в приспособлении находится по формуле:
где d -допуск получаемого размера детали; d=540 мкм (см. раздел 1.8.1);
w -точность обработки детали достигаемая при выполнении данной операции;
eдоп=540-160=380 мкм.
80 следовательно точность закрепления детали в четырехкулачковом патроне удовлетворительная.
13 Выбор конструирование и расчет калибра-пробки для контроля отверстия 180Н7(+004)мм
В качестве контрольного приспособления выбираем коническую калибр – пробку для контроля 180 Н7(+004).
При проектировании контрольных предельных калибров необходимо провести расчёт исполнительных размеров и построить схему взаимного расположения полей допусков измеряемого изделия.
Определяем предельные отклонения допуск и предельные размеры 180 Н7(+004):
Предельные отклонения отверстия мм
- верхнее отклонение ES = 004 мм
- нижнее отклонение EI = 00 мм
Td = ES – EI ; (1.78)
Td = 004 – 00 = 004 мм.
Предельные размеры вала мм
- максимальный размер:
- минимальный размер:
Dmin = D + EI = 180 + 00 = 180 мм.
Выбираем предельные отклонения и допуски калибров мкм (по ГОСТ 24853-81)
квалитет: Z=6 мкм Y=4 мкм H=8 мкм.
Здесь H – допуск на изготовление калибра для отверстия;
– отклонение середины поля допуска на изготовление проходного калибра для отверстия относительно наибольшего предельного размера изделия;
– допустимый выход размера изношенного калибра для отверстия за границу поля допуска изделия;
Наибольшие и наименьшие значения размера проходного калибра-пробки ПР новой с номинальным размером до 180 мм определим по формулам:
Размер калибра ПР проставляемый на чертеже при допуске на изготовление Н=8 мкм равен мм.
Наибольшие и наименьшие значения размера калибра-пробки изношенной при допуске на изготовление 4 мкм определяются:
= 180 – 0004 =179996 мм.
Наибольшие и наименьшие значения размера новой непроходной калибр-пробки определим по формулам:
Размер калибра НЕ проставляемый на чертеже равен мм.
Схема расположения полей допусков калибра представлена на чертеже данной калибр-пробки а также на рисунке 1.14.1.
Рисунок 1.14.1. Схема полей допусков и отклонений калибра – пробки
Схема расположения полей допусков калибра представлена на чертеже данной калибр-пробки.
Организационный раздел
1 Организация технического контроля в цехе
На предприятие проводиться мониторинг и измерение продукции согласно системе менеджмента качества. (СТО МРК СМК 8.2-02-2006)
В процессе изготовления продукция должна подвергаться испытаниям на соответствие физико-механическим свойствам металла отсутствие дефектов металла (неразрушающими методами контроля) соответствие химического состава нормативная документация (НД) на герметичность и т.д. в соответствии с нормативной документацией на продукцию.
Пробы для испытаний отбираются изготавливаются маркируются в соответствии с технологической документацией персоналом цеха. При отборе пробы контролер участок технического контроля (УТК) присваивает ей номер регистрирует в журнале регистрации проб (свободная форма). Пробы в центральной заводской лаборатории (ЦЗЛ) передает производственный мастер участка данного подразделения. Заключение по результатам испытаний ЦЗЛ передает работнику УТК цеха.
Для всех видов контроля методы контроля и выбор средств измерений определяет технолог разработавший технологию на изготовление данного вида продукции. Допускается не указывать методы контроля с применением универсальных средств измерений.
При отсутствии регламентированных видов контрольных записей руководители специалисты и служащие (РСС) отдел технического контроля (ОТК) разрабатывают виды контрольных записей отражающие соответствие установленным параметрам процесса жизненного цикла продукции.
Операционный контроль
При операционном контроле согласно маршрутной карте производственный мастер начальник участка при помощи средств измерений устройств определяет соответствие параметров протекающего процесса требованиям технической документации. Результаты проведения данного вида контроля производственный мастер начальник участка заносит в соответствующую документацию.
В случае выявления несоответствия параметров процесса действия персонала определены в СТО МРК СМК 8.3-01
Не допускается передача продукции на следующую технологическую операцию без подтверждения ее соответствия требованиям НД работником УТК для данной операции.
Инженерный технологический контроль
Данный вид контроля осуществляют:
- производственный мастер;
- технолог разработавший опытный технологический процесс или технологическое письмо на изготовление продукции;
- начальник участка (мастер) технического контроля (ТК).
Разработка оформление технической документации на опытный технологический процесс или изготовление опытного образца введение ее в действие осуществляются согласно СТО МРК СМК 7.3-02 и СТО МРК СМК 7.3-01.
Приемочный контроль продукции осуществляют работники ОТК или производственный мастер начальник участка если отсутствуют работники ОТК в соответствии с требованиями НД на продукцию.
Работник ПРБ (планово-распределительное бюро) цеха представляет всю документацию подтверждающую соблюдение требований к продукции (сертификаты качества на материалы паспорта заключения по результатам исследования). Эти документы регистрируются и хранятся в УТК. Срок хранения - 5 лет.
При приемочном контроле проверяют параметры процесса изготовления документацию подтверждающую качество исходных материалов и полуфабрикатов результаты испытаний соответствие продукции требованиям НД.
Продукция прошедшая операционный контроль и соответствующая требованиям НД должна предъявляться на приемочный контроль на специальных стеллажах контрольных плитах и т.д. обеспечивающих свободный доступ для проведения измерений геометрических размеров визуального осмотра проверки специальными средствами измерений. По требованию работника УТК продукция переворачивается перекладывается работниками цеха.
Готовая продукция должна взвешиваться на весах. Порядок проведения работ по взвешиванию приведен в приложении А.
Целью взвешивания является определение:
- соответствия фактической массы продукции расчетной массе указанной в чертеже;
- затрат на изготовление продукции;
- расходных коэффициентов в заготовительных цехах.
подлежат взвешиванию:
- вся продукция заготовительных цехов (отливки и поковки);
- мехобработанные изделия из отливок поковок металлопроката;
- продукция из цветных металлов.
не подлежат взвешиванию:
- ремонтная продукция (сборочные узлы детали сменное оборудование);
- мехобработанные изделия с расчетной суммарной массой партии менее 10 кг размер партии – не более пяти штук..
Акт взвешивания оформляется на литейную продукцию производственным мастером выполняющим взвешивание при отклонении фактической массы от массы указанной в чертеже и несоответствии допуска массы отливки треблваниям ГОСТ 26645. Акт передается в лабораторию литья металлургии металлов и сплавов служба качества и инжиниринга (СКИ) для пересчета массы и при необходимости фактическая масса согласовывается с заказчиком.
Результаты взвешивания мехобработанной литейной продукции поковок вносятся в чертеж и журнал регистрации взвешенной продукции производственным мастером выполняющим взвешивание с проставлением подписи с расшифровкой и даты. Журнал хранится у производственного мастера в течение 5 лет. Фактической массой изделия считается масса после взвешивания.
Продукция должна иметь маркировку обеспечивающую согласно СТП СМК 2-320-7.5-01 ее идентификацию на всех стадиях изготовления. После проведения приемосдаточного контроля и признания продукции годной соответствующей требованиям НД работник УТК маркирует продукцию собственным клеймом.
Экономист планово-экономического отдела осуществляет учет принятой продукции на основании подписанной работником ОТК накладной формы М-24 акта на сдачу готовой продукции в соответствии с Регламентом.
Продукция считается годной после проведения приемочного контроля и подписания накладной формы М-24 акта на сдачу готовой продукции работником ОТК.
Оформление документов на отгрузку принятой продукции осуществляется в соответствии с ПД ММК 3-ОСА-137.
Требования к оформлению технической документации на изготовление продукции
Требования к оформлению построению содержанию и изложению технологической документации на изготовление продукции приведены в СТП СМК 2-320-7.3-01 и других нормативных документах.
Требования к оформлению чертежа
Чертеж должен содержать следующие данные:
- марку материала подтвержденную технологом лаборатории КП и ТО ПТЦ;
- режим термообработки утвержденный и актуализированный;
- размеры и технические требования чертежа подтвержденные ведущим инженером ППО;
- оформленные требования к проведению исследований;
- штампы «Мех. испытания» «Ростехнадзор» (при необходимости);
- номер заказа наименование узла агрегата предприятия заказчика.
На обратной стороне чертежа перед выдачей в работу инженер ПРБ согласно номенклатурному плану записывает график изготовления продукции данные документа удостоверяющего качество материала (полуфабриката) с подтверждением подписью.
2 Организация инструментального хозяйства в цехе
Инструментальное хозяйство в своём составе имеет инструментально-раздаточную кладовую кладовую приспособлений и абразивов контрольно-проверочный пункт заточное отделение и мастерскую и мастерскую по ремонту приспособлений и инструмента
Кладовые инструментально-раздаточная кладовая предназначается для хранения выдачи и проверки инструмента. .
Инструмент поступающий с рабочих мест до его укладки в стеллажи подвергается проверке силами и средствами контрольно-проверочного пункта после чего в зависимости от технического состояния его укладывают в стеллажи или направляют на переточку и ремонт.
Проверка эталонов а также точного и смежного инструмента и приспособлений осуществляется в лаборатории линейно-угловых измерений.
Заточное отделение. Занимается эксплуатационных переточкой режущего инструмента.
Мастерская по ремонту приспособлений и инструмента предназначается для производства несложного текущего ремонта приспособлений и инструмента. .
Ремонтное хозяйство. B состав ремонтного хозяйства входит мастерская (ремонтная база) предназначенная для межремонтного обслуживания и производства отдельных видов ремонта.
Складское хозяйство. Складское хозяйство состоит из комплекса складов необходимых для обеспечения нормального хода производства Сюда относятся склады металла заготовок и полуфабрикатов межоперационные склады склады готовых деталей.
Склад заготовок и полуфабрикатов предназначен для хранения определённого запаса. Эти склады располагаются в начале пролётов в соответствии с обрабатываемыми деталями. Чтобы не занимать дорогую производственную площадь под склады при механическом цехе предусмотрены специальные эстакады где и размещают склад заготовок и полуфабрикатов. Эстакады открытые и закрытые. В механическом цехе при наличии эстакады предусмотрены площадки для хранения минимального запаса (2-Эдня) которые используются для того чтобы выдержать в цехе крупные детали для доведения их температуры в зимнее время до температуры цеха.
3 Организация ремонта оборудования в цехе
Организация ремонта и обслуживания оборудования основывается на системе планово-предупредительного ремонта (ППР) сущность которой заключается в том что после того как агрегат проработал определённое количество часов он подвергается различным видам профилактики и плановых ремонтов последовательность и периодичность которых определяется назначением агрегата его конструктивными и ремонтными особенностями габаритами и условиями эксплуатации.
Система ППР направлена на предупреждение интенсивного износа оборудования резко сокращает возможности непредвиденного выхода его из строя и позволяет осуществлять ремонтные работы в кратчайший срок путем предварительной их подготовки. В результате применения системы ППР создаются условия для эффективного использования оборудования уменьшения его износа увеличения времени его полезной работы повешения качества ремонтных работ.
Межремонтное обслуживание включает наблюдение за выполнением правил эксплуатации оборудования своевременное устранение мелких неисправностей и регулирование механизмов осуществляемое рабочими обслуживающими агрегаты наладчиками и дежурным персоналом входящим в состав вспомогательных рабочих цеха и выполняемое во время перерывов в работе станка без нарушения производственного процесса.
Осмотры – вид планового технического обслуживания; проводят для проверки состояния оборудования устранения мелких неисправностей и выявления объёма подготовительных работ подлежащих выполнению при очередном плановом ремонте; выполняют ремонтные слесари с привлечением в случае необходимости работающих на оборудовании.
Малый ремонт – вид планового ремонта связанный с заменой или восстановлением изношенных деталей и регулированием механизмов и обеспечивающий нормальную эксплуатацию станка до очередного планового ремонта.
Средний ремонт – вид планового ремонта связанный с частичной разборкой агрегата капитальным ремонтом отдельных его узлов заменой или восстановлением основных изношенных деталей сборкой регулированием и испытанием станка.
Капитальный ремонт – вид планового ремонта при котором производят полную разборку станка замену всех изношенных деталей и узлов ремонт базовых и других деталей и узлов сборку регулирование и испытание под нагрузкой.
4 Организация транспортировки изделий и стружки в цехе
Для обеспечения удовлетворительного отвода стружки из зоны резания и дальнейшей её транспортировки при работе на универсальном и автоматическом оборудовании средней мощности необходимо получать стружку диаметром спирального витка 25-30 и длиной 50-200 мм.
Безопасную для рабочего и удобную для транспортировки стружку получают:
- с помощью уступов различной формы (лунки и «порожки») на передней грани резца;
- специально подобранной формой режущей части инструмента;
- напаянными и накладными стружколомами;
- прерывистым (периодическим) и вибрационным резанием.
Стружка из станка удаляется вручную. Вручную из станков стружку удаляют с помощью крючков скребков совков и щеток. Чугунную стальную и тем более цветную стружку необходимо собирать отдельно потому что их нельзя смешивать между собой по металлургическим требованиям а также и потому что устройства по сбору и переработке стружки из различных материалов также различны. Сбор стальной стружки сложнее ещё и потому что легированную стальную стружку надо отделять от углеродистой. Собирается стружка в ящики контейнеры которые по мере заполнения вывозятся из цеха средствами безрельсового транспорта (карами). При этом тара устанавливается в пролётах цеха с таким расчётом чтобы производственные или подсобные рабочие могли ссыпать в них стружку собираемую совками или в небольшие ящики от нескольких станков.
Все процессы сбора и переработки стружки состоят из удаления стружки от станков; отсоса мелкой стружки и пыли из зоны обработки; удаление стружки из цехов; очистки и переработки стружки.
С целью улучшения условий транспортировки и дальнейшего использования в металлургическом производстве стружку брикетируют для этого используют брикетир-пресс. Брикетирование стружки производиться при высоком удельном давлении. Брикеты имеют плотность 5-65 кгсм.
В результате анализа назначения конструкции и условий работы вала-дифференциала был изменен технологический процесс. В результате рассчитанных припусков были уточнены размеры заготовки вследствие чего был выбрана поковка меньшего размера. Это увеличило коэффициент использования материала.
В результате разработки нового варианта технологического процесса фрезерование торца было заменено подрезкой торцев на токарном станке 1М65.
Режимы резания были рассчитаны для трех операций а для остальных операций режимы были выбраны из справочников.
Было рассчитано три режущих инструмента – проходной резец. сверло и шпоночная фреза.
В организационном разделе приведены организация технического контроля организация инструментального хозяйства организация ремонта оборудования и транспортировки деталей на участке.
Список используемых источников:
Справочник технолога-машиностроителя: В 2 т. Под ред. А.Г. Косиловой и М.Г. Мещерякова. – М.: Машиностроение. 1986. – Т. 1.
Справочник технолога-машиностроителя: В 2 т. Под ред. А.Г. Косиловой и М.Г. Мещерякова. – М.: Машиностроение. 1986. – Т. 2.
Справочник технолога-машиностроителя: В 2 т. Под ред. А.Г. Малова – М.: Машиностроение. 198. – Т. 2
Нефедов К.А. Осипов Н.А. Сборник задач и примеров по резанию металлов и режущего инструмента – М: Машиностроение. 1990.
Курсовое проектирование по деталям машин Чернявский С.А. – М: Машиностроение 1988
Вардашкин Б.Н Станочные приспособление. Справочник в 2-х Т. – М.: Машиностроение 1984
Проектирование технологической оснастки машиностроительного производства: Учеб. пособие для машиностроит. спец. вузов Г.Н. Андреев В.Ю. Новиков А.Г. Схиртладзе.; Под ред. Ю.М. Соломенцева. – М.: Высш. шк. 1999.
Общемашиностроительные нормативы режимов резания для технического нормирования работ на металлорежущих станках. – М.: Машиностроение. 1967.
Марочник сталей и сплавов В.Г. Сорокин А.В. Волосникова С.А. Вяткин и др.; Под общ. ред. В.Г. Сорокина. –М: Машиностроение. 1989. –640с.
Проектирование станочных приспособлений Белоусов А.П. – М.:Высш. школа 1980.
Рекомендуемые чертежи
- 24.01.2023
- 24.01.2023
- 24.01.2023
- 29.07.2014
- 24.05.2017
- 30.08.2014