Реконструкция линии выпаривания аммиачной селитры в цехе NPK-2




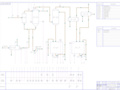
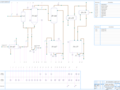
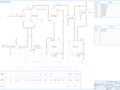
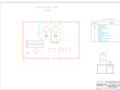
- Добавлен: 25.01.2023
- Размер: 4 MB
- Закачек: 0
Описание
Состав проекта
![]() |
![]() |
![]() ![]() ![]() |
![]() ![]() ![]() |
![]() ![]() ![]() |
![]() |
![]() ![]() ![]() ![]() |
![]() |
![]() ![]() ![]() ![]() |
![]() ![]() ![]() ![]() |
![]() |
![]() ![]() ![]() ![]() |
![]() ![]() ![]() ![]() |
![]() ![]() ![]() ![]() |
![]() |
![]() ![]() ![]() ![]() |
![]() ![]() ![]() ![]() |
![]() |
![]() ![]() ![]() ![]() |
![]() |
![]() |
Дополнительная информация
Спецификация.doc
обозначение документа опросного листа
ПРИБОРЫ И СРЕДСТВА АВТОМАТИЗАЦИИ
Термопреобразователь сопротивления с коммутационной головкой
НСХ 50М длина монтажной части 80 мм пределы измерения -50 – 180 °С
Микропроцессорный вторичный прибор обеспечивающий
реализацию ПИД-закона регулирования
Автоматический запорно-регулирующий односедельный клапан
диапазон рабочей температуры 5–425 °С рабочее давление 16 МПа
Отсечной клапан с электромагнитным приводом
рабочее давление 16 МПа
Преобразователь для измерения давления
ПО «Манометр» г. Москва
Преобразователь для измерения разрежения
«Теплоприбор» г.Рязань
Преобразователь для измерения разности давлений
Микропроцессорный вторичный прибор обеспечивающий ПИД- регулирование
Микропроцессорный вторичный прибор расходомер
Кондуктометрический датчик уровня жидкости
Микропроцессорный вторичный прибор
Магнитный пускатель реверсивный напряжение 380 В частота 50 Гц
Саранский приборостроительный завод
Ключ управления универсальный предназначенный для переключения
цепей питания электрической установки переменного тока
Кнопка управления по месту или на щите предназначена
для дистанционного управления аппаратами переменного тока
Лампа сигнальная напряжение 220В мощность 25 Вт частота 50Гц
Диплом Упарка раствора аммиачной селитры.docx
2 Характеристика предприятия
3 Характеристика продукции
4 Характеристика конкурентов и выбор конкурсной стратегии
5 Производственный план
6Организационные меры по реализации проекта
7. Обеспечение проекта материальными и трудовыми ресурсами
. Описание схемы технологического процесса конструкции и работы оборудования
1 Описание схемы технологического процесса
2 Описание конструкции разрабатываемого оборудования
3 Описание работы оборудования
Выбор конструкционных материалов изготовление деталей и защита от коррозии
1 Выбор конструкционных материалов
2 Изготовление деталей
3 Защита от коррозии
1 Расчет площади теплового элемента
2 Расчет элементов конструкции выпарного аппарата
3 Расчет ситчатой тарелки
4. Расчет конструкции абсорбционной тарелки
Автоматизация технологического процесса
1 Выбор параметров контроля и управления процессом
2 Описание функциональной схемы
Монтаж эксплуатация и ремонт оборудования
1 Монтаж оборудования
2 Эксплуатация разрабатываемых устройств
3 Ремонт оборудования
Безопасность и экологичность проекта
1 Анализ опасных и вредных производственных факторов
2 Экологичность проекта
3 Защита рабочих и материальных ценностей при возникновении чрезвычайных ситуаций
Технико-экономические расчеты
1 Расчет капиталовложений
2 Расчет дополнительных текущих расходов при реализации проекта
3 Расчет экономии текущих затрат
4 Расчет годового экономического эффекта и показателя рентабельности капиталовложений
Список используемых источников
Сегодня химическая промышленность является одной из наиболее динамично развивающихся отраслей промышленности. В последнее время с каждым годом возрастает потребление населением разного вида продукции этой отросли (горюче-смазочные материалы изделия из пластических масс медикаменты удобрения и др.). В связи с ростом спроса на предметы производства химической промышленности возникает потребность в строительстве новых заводов оснащенных новым оборудованием.
Одним из направлений в химической промышленности является производство минеральных удобрений. Для нормального роста и развития растений необходимо их обеспечение достаточным количеством питательных веществ. Основными питательными веществами являются: азот фосфор калий кальций магний и железо. Для поддержания плодородности сельскохозяйственных земель необходимо искусственным способом поддерживать баланс микроэлементов в почве. Для этого используют в данное время всевозможные минеральные удобрения (селитра карбамид азофос аммиачная вода нитроаммофоска полифосфат аммония и др.). Применение комплексных и высококонцентрированных удобрений снижает трудовые затраты на внесенные их в почву уменьшает расходы на транспортировку и хранение повышает общую культуру земледелия.
В настоящее время отечественная промышленность выпускает различные комплексные удобрения включающие некоторые питательные элементы например аммофос диаммофос нитрофоску и т.п. Производство высококонцентрированных и сложных удобрений составляло к 1990 г. не менее 90 % от общего объема выпускаемых в стране удобрений.
Расчеты показывают что при правильном использовании каждый рубль затраченный на производство минудобрений дает дополнительную сельскохозяйственную продукцию на сумму 15 5 руб. при этом существенно повышается ее качество и заметно снижаются затраты на выращивание урожая.
Производство сложных удобрений типа азофоски основано на разложении фосфатного сырья азотной кислоты. Применение этого метода предложено еще в 1908 г. академиком Д. Н. Прянишниковым стало реальным лишь в 20-е годы когда азотную кислоту стали получать из синтетического аммиака.
Основным преимуществом данного метода является то что при азотокислотном разложении фосфатного сырья используются не только химическая энергия кислоты но и ее анионы который переходит в состав удобрения и является источником дополнительного питательного компонента – азота.
В настоящее время наиболее экономической является схема получения азофоски основанная на азотокислотном разложении фосфатного сырья с последующим вымораживанием нитрата кальция. Она позволяет комплексно использовать фосфатное сырье и на ряду с получением NPK-удобрений извлекать такие ценные продукты как стронций редкоземельные элементы фтор а также организовать производство по безотходной технологии.
Одним из самых востребованных минеральных удобрений является нитроаммофоска. Это удобрение содержащее азот фосфор и калий наиболее эффективно повышает содержание минеральных веществ в почве при малом объеме их внесения.
В основу производства нитроаммофоски положен метод азотокислотного разложения апатитового концентрата. Основным сырьем является апатит азотная кислота аммиак и хлористый калий. Содержание питательных веществ в готовой продукции N:=1:1:1.
С 90-х прошлого столетия в нашей стране практически не было построено ни одного химического завода по производству химических удобрений а то оборудование которое было установлено на старых заводах износилось и не отвечает требованиям нынешнего времени.
Строительство новых производств минеральных удобрений в центрально-черноземном экономическом районе обусловлено потребностью в них данного района заявленной на перспективный период и невозможностью их обеспечения за счет действующих и строящихся предприятий и производств в отросли. Строительство Россошанского химического завода началось в 1974 году.
При разработке новых видов удобрений и более прогрессивных технологий их производства используются все достижения научно-технического прогресса. При конструировании и модернизации химической аппаратуры учитываются требования постоянно обновляющихся Государственных и отраслевых стандартов технических условий и других нормативно-технических материалов.
В данном дипломном проекте проведена реконструкция выпарного аппарата и абсорбционной клоны. В отделении выпаривания аммиачной селитры что позволит повысить производительность нитроаммофоски и увеличить производства селитры. Используемые решения уменьшают себестоимость продукции цеха за счет повышения мощности на данном оборудовании.
БИЗНЕС - ПЛАН ПРОЕКТА
Основной задачей является качество продукции и наращивание мощностей производства. В данном проекте рассматриваем повышение мощности производства на участке по выпарке аммиачной селитры.
В данном процессе по выпариванию предлагается произвести реконструкцию выпарного аппарата и абсорбера.
Процесс концентрирования раствора заключающийся в удалении растворителя путем испарения при кипении называется выпариванием. Большей частью из раствора удаляют лишь часть растворителя так как в выпарных аппаратах обычных конструкций упаренный раствор должен оставаться в текучем состоянии.
Нагревание выпариваемого раствора производится путем передачи тепла от нагревающего агента через стенку разделяющих оба вещества либо путем непосредственного соприкосновения веществ. Процесс выпаривания происходит под вакуумом что позволяет снизить температуру кипения раствора и применяется для выпаривания чувствительных к высокой температуре растворов.
Значительной большой поверхностью нагрева в единицу объема обладают змеевиковые выпарные аппараты (Рисунок 1). В корпусе 1 такого аппарата размещены паровые змеевики 2 а в паровом пространстве установлен влагоуловитель 3. При проходе через брызгоуловитель поток вторичного пара изменяет направление своего движения и из него выделяется унесенные паром капли жидкости.
Змеевики выполняют из отдельных секций так как у удлиненных змеевиков в следствии накопления конденсата поверхность нагрева плохо используется. Кроме того при секционировании змеевиков можно последовательно отключить отдельные секции по мере понижения уровня раствора в периодически действующем аппарате.
Змеевиковые аппараты более компактные чем аппараты с рубашками и отличаются несколько большей интенсивностью теплоотдачи. Однако очистка и ремонт змеевиков затруднены. В этих аппаратах также производят выпаривание небольших количеств химически агрессивных веществ.
В аппаратах с выносной нагревательной камерой при размещении нагревательной камеры вне корпуса аппарата имеется возможность повысить интенсивность выпаривания не только за счет увеличения разности плотности жидкости и парожидкостной смеси в циркуляционном контуре но и за счет увеличения кипятильных труб.
Рисунок 2. Выпарной аппарат с выносной нагревательной камерой:
-нагревательная камера; 2-сепаратор; 3-необогреваемая циркуляционная труба; 4-брызгоуловитель.
Данный аппарат имеет кипятильные трубы длина которых часто достигает 7 м. Он работает при более естественной циркуляции которая обусловлена тем что циркуляционная труба не обогревается а подъемный и опускной участки циркуляционного контура имеют значительную высоту.
Выносная нагревательная камера 1 легко отделяется от корпуса аппарата что облегчает и ускоряет ее чистку и ремонт. Ревизию и ремонт нагревательной камеры можно производить без полной остановки аппарата (а лишь при снижении его производительности) если присоединить к его корпусу две камеры.
Скорость циркуляции в аппаратах с выносной нагревательной камерой может достигать 15 мс что позволяет выпаривать в них концентрированные и кристаллизующие растворы не опасаясь слишком быстрого загрязнения поверхности теплообмена. Благодаря универсальности удобству эксплуатации и хорошей теплопередачи аппараты такого типа получили широкое распространение.
Для увеличения производительности предлагаю в аппарат с выносной нагревательной камерой ввести тепловые элементы что позволит повысить площадь выпариваемой поверхности. Этот элемент предлагаем сделать из двух полых пластин шириной 015 м. приваренных между собой под углом 120. Длина теплового элемента 3м. Полость нужна для того что бы подать в них пар температурой 121С.
Рабочая поверхность трех тепловых элементов составляет:
F= 2*0.15*3*3 = 2.7 м
Тогда как площадь выпариваемой селитры в выпарном аппарате равна:
F= r² = 314*199² = 1244 м²
До данной реконструкции аппарата площадь испаряемой селитры составляла 1244м² а с внедрением в аппарат теплового элемента: F= F+F=27 +1244 =1514м². Тем самым повышается площадь испарения селитры на 217% что повысит производительность и создаст запас мощности при дальнейшем развитии предприятия. В данной технологической схеме запас мощности скажется не только на развитии фосфорных удобрений но и селитры.
Аппараты в которых осуществляется абсорбционные процессы называют абсорберами. Как и другие процессы массопередачи абсорбция протекает на поверхности раздела фаз. Поэтому абсорберы должны иметь развитую поверхность соприкосновения между жидкостью и газам. По способу образования этой поверхности абсорберы можно условно разделить на следующие группы: 1) поверхностные и пленочные; 2) насадочные; 3) барботажные (тарельчатые); 4) распыливающие.
В поверхностных и пленочных абсорберах поверхностью соприкосновения фаз является зеркало неподвижной или медленно движущей жидкости или же поверхность текущей жидкости пленки.
Рисунок 3.поверхностный абсорбер.
Поверхностные абсорберы используют для поглощения хорошо растворимых газов. В указанных аппаратах газ проходит над поверхностью неподвижной или медленно движущей жидкости (Рисунок 3). Так как поверхность соприкосновения в таких абсорберах мола то устанавливают несколько последовательно соединенных аппаратов в которых газ и жидкость движутся противотоком друг к другу. Для того чтобы жидкость перемещалась по абсорберам самотеком каждый последующий по ходу жидкости аппарат располагают несколько ниже предыдущего. Для отвода тепла выделяющего при абсорбции в аппаратах устанавливают змеевики охлаждаемые водой или другими охлаждающими агентами либо абсорбенты помещают в сосуды с проточной водой.
Пленочные абсорберы более эффективны и компактны чем поверхностные. В пленочных абсорберах поверхностью контакта фаз является поверхность текущей пленки жидкости. Различают следующие разновидности аппаратов данного типа: 1) трубчатые абсорберы; 2) абсорберы с плоскопараллельной или листовой насадкой.
Рисунок 4 Насадочный абсорбер.
-насадка 2-опорные решетки 3-распределитель жидкости
-перераспределитель жидкости.
Насадочные абсорберы широко распространены в промышленности в качестве колонных аппаратов заполненных насадкой – твердыми телами различной формы. В насадочной колоне (Рисунок 4) насадка 1 укладывается на опорные решетки 2 имеющие отверстия или щели для прохождения газа и стока жидкости. последняя с помощью распределителя 3 равномерно орошает насадочные тела и стекает вниз. По всей высоте слоя насадки равномерное распределение жидкости по сечению колонны обычно не достигается что объясняется пристеночным эффектом – большей плотностью укладки насадки в центральной части колонны чем у ее стенок. Вследствии этого жидкость имеет тенденцию растекаться от центральной части колонны к ее стенкам. Поэтому для улучшения смачивания насадки в колоннах большого диаметра насадки иногда укладывают слоями (секциями) высотой 2-3 м и под каждой секцией кроме нижней устанавливают пререраспределители жидкости 4.
В насадочной колонне жидкость течет по элементу насадки главным образом в виде тонкой пленки поэтому поверхностью контакта фаз является в основном смоченная поверхность насадки и насадочные аппараты можно рассматривать как разновидность пленочных. Однако в последних пленочное течение жидкости происходит по всей высоте аппарата а в насадочных абсорберах – только по высоте элемента насадки. При перетекании жидкости с одного элемента насадки на другой пленка жидкости разрушается и на нижележащем элементе образуется новая пленка. При этом часть жидкости проходит через расположенные ниже слоя насадки в виде струек капель и брызг. Часто поверхность насадки бывает смочена неподвижной (застойной) жидкостью. Ситчатые тарелки имеют достаточно высокую эффективность простотой устройства низкое сопротивление и малую металлоемкость. Они применяются преимущественно в колоннах работающих при атмосферном давлении и вакууме.
Для увеличения производительности и эффективности предлагается дополнительно смонтировать ситчатую решетку в аппарат а также изменить распределитель аммиачной селитры и сделать его по кругу для полного распределения аммиачной селитры в насадках (кольцах Паля).
2Характеристика предприятия
В 1984-1985 годах вошла в строй действующих вторая очередь завода: второй цех слабой азотной кислоты производство нитроаммофоски и многие вспомогательные объекты в числе которых цех по переработке отходов производства нитроаммофоски промышленная котельная и другие.
Цех ПФУ представляет собой комплекс из двух основных агрегатов непосредственно производящих удобрение (ПФУ-1 ПФУ-2) и вспомогательного агрегата (ПФУ-3) включающего в себя складские помещения для готовой продукции и для сырья (апатит азотная кислота диспергатор) средства отгрузки и фасовки удобрения средства транспортировки сырья в основные агрегаты воздушно компрессорную установку и узел по остужению оборотной воды используемой в ПФУ-1 и ПФУ-2.
Проектировщик технологической части оборудования строительной части контроля и автоматизации отопления и вентиляции тепловой изоляции основного производства установки обработки готового продукта диспергатором «НФ» - ОА «ГИАП» г. Москва.
Проектировщик технологической части контроля автоматизации регулирования установку подачи антислеживающего вещества «Лиламин»-ОАО «Минудобрения» г. Россошь.
3Характеристика продукции
Техническое наименование продукта – нитроаммофоска. Требования к качеству этого удобрения предназначенного на экспорт должны соответствовать требованиям договора (контракта) поставка с внешнеэкономической организацией или иностранным покупателем. Массовую долю воды определяют в момент приемки у потребителя. Массовая доля гранул менее 1мм для высшего и первого сортов на момент отгрузки не более 2% (с 01.01.92г.). Нитроаммофоска выпускается только с применением кондиционирующих добавок содержащих кальций магний сульфат или сульфат в сумме с фосфатом. Нитроаммофоска с сульфатной или с сульфатнофосфатной добавками выпускается только с применением поверхностно-активных веществ: диспергатора «НФ» жирных кислот или аминов жирных кислот.
Нитроаммофоска представляет собой серо-розовое вещество с процентным составом N и -18.2:18.2:18.2 соответственно.
Плотность истинная – 1580-1690кг
Плотность насыпная - 1000 кг
Температура плавления – 147.5 С
Теплота плавления – 7042 кДжкг
Теплота образования гранул при t=25С – 357.7кДжкг
Гранулированная нитроаммофоска применяется в сельском хозяйстве как сложное удобрение для внесения в почву таких полезных веществ как азот калий и фосфор. Как вещество нитроаммофоска производимая в цехе ПФУ обладает патентной чистотой в виду её достаточной давней известности.
Проектная мощность нитроаммофоски составляет 1100 тыс. тг. Помимо нитроаммофоски в качестве побочных продуктов в цехе производится аммиачная селитра которая в виде сплава отправляется по трубопроводу на грануляцию в цех по производству аммиачной селитры и мел который после просушки отправляется на дальнейшую переработку.
Производство нитроаммофоски представляет собой сложный технологический комплекс построенный на базе азотокислотного разложения фосфатов. Основные стадии процесса производства сложного гранулированного удобрения нитроаммофоски следующие:
- разложение апатитового концентрата азотной кислотой;
- кристаллизация 4-х водного нитрата кальция;
- фильтрация и промывка кристаллов нитрата кальция;
- нейтрализация раствора нитрофосфата аммиака;
- упаривание раствора нитроаммофоса;
- гранулирование нитроаммофоски;
- рассев охлаждение и кондиционирование готового продукта.
Производимая на проектируемом производстве нитроаммофоска отличается качеством по составу продукта а также низкое слеживаемость что способствует уменьшению потерь при транспортировке хранении и делает легким процесс внесения удобрения в почву.
4. Характеристика конкурентов и выбор конкурентной стратегии
Производство нитроаммофоски на основе азотокислотного разложения фосфатов по технико-экономическому уровню относятся к высшей категории.
Производимые удобрения упаковываются в разнообразную тару: полиэтиленовые пакеты по 3 килограмма двухслойные пакеты по 750 кг 500 кг и 50 кг что позволяет выбирать всевозможные варианты поставки.
5. Производственный план
При производстве нитроаммофоски происходят следующие основные процессы: разложение апатитового концентрата азотной кислотой кристаллизация нитрата кальция. Выделение и промывка кристаллов нитрата кальция нейтрализация раствора нитрофосфата подготовка KCl и его внесения в упаренный раствор нитроаммафоса гранулирование расплава путем разбрызгивания в грануляционной башне классификация гранул кондиционирование упаковка и отгрузка.
Апатитовый концентрат и калийная соль доставляются в хранилище железнодорожным транспортом затем пневмотранспортом подается на переработку в цех.
Азотная кислота поступает из цеха по производству азотной кислоты АК-72М.
Газообразный аммиак поставляется по трубопроводу из цеха по производству аммиака АМ-1.
Антислеживающие добавки которыми обрабатываются гранулы привозится в хранилище автотранспортом а в цех из хранилища с помощью насосов.
Пар и горячая вода поступает из заводской промышленной котельной.
Цех ПФУ рассчитан на производство 1100 тысяч тонн нитроаммофоски в год . Соблюдая все нормы и правила по эксплуатации обслуживанию и ремонту технологического оборудования трудовой коллектив цеха ежегодно перевыполняет план по выпуску удобрения. Этому так же способствует и рационализаторские предложения вносимые работниками цеха. Однако бывают и срывы выполнения производственного плана по вене несвоевременной поставки сырья и оборудования.
Для того чтобы повысить производительность не меняя данного оборудования на участке выпаривания предлагаю ввести тепловой элемент в выпарной аппарат тес самым увеличить площадь выпарки. А абсорбционном аппарате ввести сетчатую тарелку.
6.Организационные меры по реализации проекта
Спроектированное оборудование узлы и детали представляют собой конструкции разработке части которых и изготовление возможно силами и средствами отделов механизации и автоматизации предприятия а некоторая часть из них будет изготавливаться с привлечением сторонних организаций.
Наличие высококвалифицированного персонала работающего в этой службе позволяет в короткие сроки и с хорошим качеством изготовить часть спроектированного оборудования.
ОПИСАНИЕ СХЕМЫ ТЕХНОЛОГИЧЕСКОГО ПРОЦЕССА КОНСТРУКЦИИ И РАБОТЫ ОБОРУДОВАНИЯ
1 Описание технологической схемы упарки раствора аммиачной селитры.
Выпаривание раствора аммиачной селитры требует строгого соблюдения технологических параметров процесса т.е. отклонение от них повышение температуры более 1500С и понижения рН менее 5 может привести к взрыву концентрированного раствора аммиачной селитры. Поэтому принятые технологические параметры схема и аппаратурное оформление процесса направлены на соблюдение условий безопасного ведения процесса упарки.
Раствор аммиачной селитры с откорректированным рН концентрацией 5560% NH4NO3 поступает через подогреватель 1 подается на упарку.
Раствор подается в две параллельно работающие выпарные установки состоящие из греющих камер 2(АВ) и сепараторов 3(АВ).
Далее раствор с температурой 90-1000С поступает в греющую камеру 2 где нагревается до Т=1210С.
В качестве теплоносителя используется пар давлением 08-12 МПа. Конденсат пара из греющей камеры идет на конденсационный емкость . Пар самоиспарения из конденсационной емкости отводится в греющий пар и используется при выпарке.
Подогретый раствор аммиачной селитры из греющей камеры 2 поступает в выпарной аппарат 3.В процессе работы осуществляется естественная циркуляция раствора по контуру: греющая камера – выпарной аппарат – греющая камера (2 – 3 - 2).
В результате кипения раствора аммиачной селитры в выпарном аппарате 3 при температуре 1210С и вакууме 300-500 мм рт.ст. на одной системе испаряется паровоздушная смесь.
Слив 89-93% плава аммиачной селитры в количестве 45 тч – товарная часть осуществляется насосами 4 (АВС) в емкость для хранения 89-93% раствора. Предусмотрен также вывод части аммиачной селитра на нейтрализацию. Плав выпаренной аммиачной селитры из емкости для хранения насосами откачивается потребителями:
-в цех аммиачной селитры (АС-72) для дальнейшего упаривания и получения гранулированного удобрения;
-часть для внутрицехового использования на узел нейтрализации.
Для поддержания при упарке заданного рН=6 плава предусмотрена подача в выпарной аппарат газообразного аммиака для компенсации его потерь при упарке.
Перед подачей аммиака он предварительно нагревается в аппарате.
Пары воды содержащие аммиак и брызги аммиачной селитры из выпарных аппаратов 3 (АВ) отсасываются системой вакуума создаваемого паровым эжектором 9. Система вакуума состоит (по ходу парогазовой смеси из выпарных аппаратов 3 (АВ)) абсорбера 5 поверхностного горизонтального конденсатора 7 парового эжектора 9 струйного конденсатора 10 к этому эжектору.
Для создания герметичности системы установлены два гидрозатвора:
-гидрозатвор 6 с насосами 11 (АВ) к абсорберу 5;
-гидрозатвор 8 с насосами 12 (АВ) к поверхностному конденсатору 7к эжектору 9 конденсатору 10.
Во абсорбере 5 происходит отделение брызг аммиачной селитры из паровоздушной смеси путем орошения раствором аммиачной селитры 5560% исходной конденсации принятой из резервуара и поданной насосом в гидрозатвор 6. Раствор аммиачной селитры циркулирует по контуру: гидрозатвор 6 – насосы 11 (АВ) – абсорбер 5 – гидрозатвор 6.
После отделения брызг аммиачной селитры в абсорбере парогазовая смесь поступает на конденсацию (выделение паров воды из нее) в конденсатор 7. Конденсация ведется охлажденной водой предварительно используемой в теплообменниках с подпиткой “свежей” охлаждающей воды. Полученный конденсат стекает по барометрической трубе в гидрозатвор 8 а несконденсированная отсасывается пароэжекторным насосом 9 и подается вместе с (“рабочим” паром в конденсатор 10 из которого образовавшийся конденсат также поступает по барометрической трубе в гидрозатвор 8).
Конденсат содержащий аммиак неуловленный в абсорбере 5 из гидрозатвора 8 и из цикла выводится ;насосом 12(АВ) в колонну через подогреватель конденсата на отгонку аммиака. Газовая смесь также содержит аммиак из струйного конденсата 10 и через воздушник гидрозатвора 8 отсасывается в скруббер-нейтрализатор.
Для промывки выпарного контура к нему подведен паровой конденсат (технологическая вода).
Выпарные аппараты 3( АВ) и кипятильники 2(АВ) в процессе работы покрываются осадком карбоната кальция и других солей что снижает интенсивность процесса выпарки. Для удаления образовавшегося осадка 1 раз в месяц выполняют промывку аппаратуры подкисленным азотной кислотой конденсатом для чего:
-останавливают установку дренируют систему;
-снижают давление греющего пара до 01-02 МПа с помощью клапана;
-заполняют систему паровым конденсатом;
-открывают подачу азотной кислоты и закисляют паровой конденсат до рН 05-10;
-подачу азотной кислоты повторяют до тех пор пока не прекращается возрастание рН;
-после очистки выпарного аппарата кислый конденсат циркуляционного контура нейтрализуют подачей газообразного аммиака.
В случае сильной забивки кипятильника 2(АВ)производит его очистку с помощью насоса высокого давления. Вода после промывки выводится из контура в сборник.
Для промывки кипятильника выпарного аппарата 2 от осадков содержащих соли и окислы кремния применяется раствор каустической соды (NaOH).
Раствор каустической воды с массовой долей сухого натра 810% готовится в емкости для раствора каустической соды.
В емкость засыпают 600 кг каустической соды и подают паровой конденсат в количестве 5700 кг. Включают насос 4А на циркуляцию. Циркуляцию раствора ведут в течение 15 часов. Отбирают анализ и при получении раствора каустической соды с массовой долей сухого натра 8-10% собирают схему: 4А(В) - 3А(В) – 2А(В).
Включают насос 4А на циркуляцию. Раствор каустической соды подогревается до температуры 80-1000С (TI-401-12 13) подачей пара Р=08-10 МПа (8-10 кгссм2).
Время промывки кипятильника 2А(В) – 8-10 часов.
Частота промывки – 1 раз в месяц.
Упаренный раствор аммиачной селитры с массовой концентрацией 89-93% поступает из отделения упарки в склад раствора аммиачной селитры состоящий из 2-х хранилищ емкостью 330 м3 каждое и обеспечивающий запас раствора примерно на сутки.
2 Описание конструкции разрабатываемого оборудования.
Выпарной аппарат изображенный на (чертеже 01.000.00) имеет цилиндрическую форму. Аппарат вертикального расположения. Он состоит из цилиндрической части к которой приваривается элептическая крышка 3 и коническое днище 1.
На крышке выпарного аппарата (чертеж 01.030.00) находится штуцер 1 для выхода пара. Штуцер 2 для подачи технической воды а 3контроль давления в аппарате.
Ввод аммиачной селитры осуществляется через штуцер Б в цилиндрической части аппарата. Сам штуцер Б (чертеж 01.000.00)входит внутрь аппарата в виде цилиндра (чертеж 01.050.00) что является продолжением этого штуцера до противоположной стенки сепаратора. Крепление цилиндрического ввода на противоположной стенки осуществляется обжимным хомутом. В этой цилиндрическом штуцере внутри аппарата имеется вырез виде сегмента что позволяет увеличить площадь рассеивания селитры. Угол выреза сегмента составляет 120 ширина 3 м. Крепление трубопровода к этому штуцеру осуществляется за счет приваренного фланца 2 (чертеж01.050.00) к цилиндрической части 1. Также в цилиндрической части сепаратора находится смотровой люк Ж.
Тепловой элемент (чертеж01.060.00) монтируется во внутрь аппарата в цилиндрической части. Он состоит из трех полых сегментов в виде угла 1200. Сегмент (чертеж01.060.00) сваривается из основной 2 торцевой 4пластины и пластины покрытия. Вся конструкция сваривается на крепежной пластине 1 сегменты фиксируются между собой перемычками7. Сам тепловой элемент находится под цилиндрическим вводом .
В коническом днище 1 расположен штуцер В для выхода жидкости и штуцер 20 для возврата.
Крепление сепаратора осуществляется за счет приваренной к конической части аппарата цилиндрической опоры 2 (чертеж 01.000.00). К железобетонному основанию выпарной аппарат крепится за счет анкерных болтов по всему кругу цилиндрической опоры.
Абсорбционный колонна (чертеж 02.0000.00) содержит в своей конструкции корпус 2 эллиптическую крышку 3 и днище 1 цилиндрическую опору 4.
Корпус аппарата выполнен в виде цилиндрической обечайки 1диаметром 2600 мм и толщиной стенки 16мм. Корпус снабжен штуцерами расположенных на одной оси и с противоположной.
В корпусе цилиндрической обечайки 6 ( чертеж 02.020.00) расположены опорная решетка 14 и колпачковая тарелка 15 между которыми загружены кольца Паля 13 диаметром 80мм. При увеличении мощности в цилиндрической части аппарата устанавливаем ситчатую решетку 2. Выше колец расположен коллектор (чертеж 02.021.00) который распределяет аммиачную селитру. Штуцер Б распределителя выведен через цилиндрическую обечайку. Для удобства ремонта и обслуживание емкости на стенке цилиндрической части обечайки приварена лестница.
Крышка аппарата изображена на (чертеже 02.030.00). В своей конструкции он состоит из эллиптической крышки 3 изготовленного из листового металла 10мм с отбортовкой по краям. В верхней части аппарата вваривается штуцер 4 для вывода паровоздушной смеси. В нутрии крышки расположен проволочный каплеотбойник 6 в виде сетки.
Эллиптическое днище 1 (чертеж02.000.00) аппарата изготовлено из листового металла 10мм с отбортовкой по краю к которой приваривается цилиндрической обечайке. Нижней части днища вваривается штуцер Г для вывода аммиачной селитры.
К основанию эллиптического днища приваривается цилиндрическая опора 4 для крепления абсорбционного аппарата в вертикальном положении анкерными болтами у основания опоры.
Раствор аммиачной селитры с температурой 90 – 100С поступает в кипятильник. Там температура достигает 121С. Подогрев аммиачной селитры осуществляется паром под давлением 08 – 12 МПа и температурой 160С. Закипая раствор подается через штуцер Б в выпарной аппарат. Там он за счет вырезанного сегмента рассеивается на поверхность испарения. Самопроизвольный перетек возможен благодаря общему перепаду температур. В процессе работы осуществляется естественная циркуляция раствора по контуру: теплообменник – выпарной аппарат - теплообменник. Пары воды содержащие аммиак и брызги аммиачной селитры через штуцер А отсасывается системой вакуума 300 – 500 мм. рт. ст. создаваемого паровым эжектором в абсорбционную колонну.
Технологическая вода вводится сверху через штуцер Г. В случае превышения температуры до опасного 150С она подается в сепаратор и охлаждает его.
Паровоздушная смесь поступает в колонну сбоку через штуцер В и движется вверх противотоком по отношению к аммиачной селитры. Которая подается через штуцер Б. Подаваемая аммиачная селитра равномерно распределяется через коллектора. За счет распределения аммиачной селитры по насадке (площадь массообмена) происходит массообмен аммиачной селитры и паровоздушной смеси. Аммиачная селитры стекает с насадки и попадает сетчатую тарелку где паровоздушная смесь проходит через отверстие и барботирует через слой жидкости на тарелке. Высота слоя аммиачной селитры определяется положением верхним концом переливной трубы.
В верхней части колонны расположен каплеотбойник который препятствует брызгоуносу с паровоздушной смесью. Прореагирующая паровоздушная смесь выводится из верхней части колонны А.
ВЫБОР КОНСТРУКЦИОННЫХ МАТЕРИАЛОВ ИЗГОТОВЛЕНИЕ ДЕТАЛЕЙ И ЗАЩИТА ОТ КОРРОЗИИ
Выбор материала для конструкции является одной из основных задач возникающих в процессе конструктирования. При выборе материала должны учитываться его важнейшие свойства: прочность химическая стойкость технологические качества и структура стоимость и возможность его получения.
Выбор материала начинается с уточнения рабочих условий: температуры давления концентрации обрабатываемых веществ и следовательно агрессивности среды.
При конструировании необходимо помнить что каждый материал наряду с определенными положительными свойствами обладает и отрицательными. Конструкторы стараются обычно найти и применить такой материал который бы отвечал назначению и условиям и условиям работы оборудования. К числу основных требований которые должны удовлетворять материалы используемые в химическом машиностроении относится коррозионная стойкость. Отечественная металлургия имеет обширный выбор материалов.
Сталь - основной конструктивный материал содержащий углероды его составляет до 15%. Химическое машиностроение широко используют сталь обыкновенного качества (ГОСТ 380-94). Она используется для изготовления; фланцев люков пазов опор штуцеров и других деталей машин и аппаратов.
Высоколегированные коррозионностойкие жаростойкие и жаропрочные стали и сплавы (ГОСТ 5632-80) содержат более 10% легирующих элементов. Сталь Х18Н10Т относится к этому классу которая отличается своей стойкостью по отношению к агрессивным средам. Сталь хорошо деформируется в горячем и холодном состоянии легко сваривается. Но хуже подвергается механической обработке.
Исходя из технологического задания руководствуясь экономическими факторами и технической целесообразностью: выбираем материал для корпуса аппарата колонны и ситчатой решетки Х18Н10Т ГОСТ 5632-80 с величиной допускаемого напряжения [] = 12731 МПа при 121С. В качестве прокладок и уплотнителей будет использоваться паронит ПОН-1 (ГОСТ 481-80).
На подачу пара в тепловой элемент агрессивная среда не действует и нет воздействия повышенных температур поэтому для трубопровода подачи и отвода пара выбираем сталь Ст 3 (ГОСТ 380-94).
Для окраски конструкций из стали подверженной коррозии используется грунт ФЛ-013 и эмаль ПФ-68.
После выбора материала заготовки удовлетворяющего всем условиям эксплуатации. осуществляется выбор способа изготовления деталей. приоритетным являются заготовки из стандартных полуфабрикатов которые обрабатываются на специально подобранном или универсальном оборудовании. При этом подбирается инструмент. Приспособления рассчитывается оптимальный режим обработки.
Детали тел вращения целесообразно изготавливать на универсальных вертикальных или горизонтальных (карусельных) токарно-винторезных станках. Станочным приспособлением для закрепления деталей являются патроны трех- или четырехкулачковые. На горизонтальном или вертикальном фрезерном станке производят точение пазов обработку одной или нескольких плоскостей конусных или сферических поверхностей.
В данном разделе приведём краткую последовательность изготовления и обработки деталей представленных в графической части данного дипломного проекта.
Пластина крепежная (ДП – 01.060.01)
Для изготовления крепежной пластины используется Ст3 ГОСТ 14637-89 толщиной 20 мм. Размер заготовки соответствует габаритам будущей детали.
Заготовка вырезается из стали на гильотинных ножницах с учетом припуска на инструмент и обработку по сторонам 920x90 мм. После резки притупляют острые кромки. Затем проверяют размеры в соответствии с черчежем.
Для разметки заготовки под пластину на листе понадобится: металлическая линейка чертилка циркуль керн молоток а также специально подготовленный и вырезанный из более мягкого материала шаблон . Вырезаем из заготовки с помощью дисковых ножниц полуфабрикат под пластину с учётом припусков на дальнейшую обработку запасом 5 мм. Далее заготовку переносят на сверлильный станок на котором рассверливают пять отверстий диаметром 26 мм с шероховатостью инструмента – 20. затем острые кромки притупляют слесарным инструментом. На завершающей стадии деталь клеймят на внешней поверхности с использованием специального ударного штампа.
Фланец (ДП 01.050.00)
Деталь предназначена для соединения водящего патрубка из теплообменника с помощью разъемного соединения в данном случае болтов. Фланец имеет диаметр 875мм.
В качестве заготовки для изготовления фланца выбираем специально приготовленную отливку которая выполнена из стали 3 ГОСТ 14637-89. В качестве заготовки под фланец выбираем отливку с учетом экономии при достаточной высокой цене используемой стали.
Выбранную заготовку устанавливают на горизонтальный токарный карусельный станок где проводят обточку краевой зоны под установку прокладки с использованием комплекта резцов до шероховатости 125.
Далее заготовку снимают со станка и переносят на сверлильно-фрезерный станок типа 6902ПМФ2 на котором рассверливаем 24 отверстия диаметром 27мм с шероховатостью инструмента -20. Затем острые кромки притупляют слесарным инструментом.
По завершению всего комплекса технологических операций. Готовую деталь снимают со станка и проводят её контроль с клеймением на бирке.
Патрубок (ДП 01.050.00)
В качестве заготовки для использования патрубка выбираем стандартный ГОСТированный трубный прокат с диаметром 727мм и толщиной стенки 10мм. С помощью отрезного станка отрезаем заготовку длиной 4200мм с шероховатостью кромок 40. Затем производят разметку для патрубка понадобится: металлическая линейка чертилка. Далее из патрубка вырезают и обрабатывают кроя сегмента шлифовальной машинкой. Готовую деталь проверяют на соответствие размерам чертежа и затем клеймят.
Прокладка (ДП 01.050.03)
В качестве заготовки используют лист паронита ПОН-1 (ГОСТ 481-80) размером 765x765мм и толщиной 3мм. На нем производят разметку. Для которой понадобится циркуль. Далее прокладка вырубывется с помощью молотка и зубила. После чего кроя прокладки обтачивают на шлифовальном станке и проверяют размеры в соответствии с чертежем. На завершающей стадии деталь клеймят с использованием специального ударного штампа.
Большинство применяемых в промышленности металлов и изготовления из них оборудования и приборов неустойчиво к окружающей среде то есть подвергается коррозии. Продление времени их эксплуатации позволит с экономить металл сократить расходы на их производство. Особенно разрушению металлические конструкции.
Коррозией называется процесс разрушение металлов при химическом или электрохимическом воздействии их с окружающей средой. Металлы разрушаются при воздействии с жидкими и газообразными продуктами а также в результате окислительно-восстановительных процессов взаимодействия с окружающей средой.
Для аппаратов химической промышленности коррозионный износ является наиболее частой причиной вывода из строя. По характеру разрушения коррозия может быть сплошной (по всей поверхности металла) и местной (в виде отдельных язвин пятен сквозных отверстий трещин). При сплошной коррозии долговечность материала определяется припуском на коррозию при местной коррозии долговечность аппарата может быть определена только с помощью методов теории надежности.
Для поверхностей работающих при высоких температурах применяется термоизоляция. Она состоит из двух слоем. Первый слой – изоляция минеральной ватой второй – окожушивание листовым алюминием.
Трубопроводы подвода и отвода находятся вне помещения где подвержены вредному влиянию окружающей среды. Поэтому для защиты их от коррозии необходимо произвести покраску.
Технологический процесс окраски состоит из следующих операций:
- подготовка поверхности под окраску;
- грунтовка грунтом ФЛ-013;
- нанесение эмали ПФ-68;
- сушка поверхностей.
Грунт на поверхность изделий наносят непосредственно после очистки пескоструйным аппаратом – краскораспылителем. Технология грунтования должна обеспечивать получение тонкого равномерного слоя (15-20мк) без пропусков.
После того как грунтовка высохнет таким же краскораспылителем наносится и эмаль.
Кистевую окраску производят вручную кистями. Краска используемая при кистевой окраске должна иметь вязкость при которой она легко могла бы сходить с кисти при небольшом нажиме на окрашиваемую поверхность. Во время окраски кисть следует держать под углом 45—60° к поверхности изделий.
Для защиты аппаратов изготовленных из высоколегированных сталей от разрушения вследствие электрохимической коррозии применяется катодная защита металлических конструкций.
1. Расчет площади для тепловых элементов.
Одним из главных расчетов который необходимо произвести является тепловой расчет по выпарке селитры для расчета необходимой площади тепловых элементов.
После увеличения мощности на стадии разложения на выпарной аппарат поступает 6242248 кгч раствора аммиачной селитры которая состоит из:
=37453.5 кгч - (60%)
=2434478 кгч – (39%)
Определим количество выпаренного раствора который содержит и :
где и- начальное и конечное количество раствора кгч;
W – количество выпаренного раствора.
Определим конечное количество выпаренного раствора:
где =60% - концентрация раствора до выпаривания - концентрация раствора после выпаривания.
Тогда по формуле (1.1) определим количество выпаренного раствора:
W=624225 – 374535 = 24969 кгч
Для выпаривания 624225 кгч необходимо 217852 кгч пара что соответствует регламенту цеха.
Найдем поверхность нагрева на основании уравнения теплопередачи:
где – тепловая нагрузка кДжч;
k – 300 Вт - коэффициент теплопередачи пара;
среднее значение процесса К.
Определим среднее значение температуры:
где - температура пара.
- температура раствора.
Подставим полученные значения в (1.4)
Тепловой поток найдем по формуле кДжч:
= 217852 кгч – расход пара.
С = 444 кДжкгК – коэффициент теплопередачи насыщенного пара.
Т=+273=180+273=453К – температура пара.
=217852*444*453=43817008464кДжч
Найдем тепловой поток до реконструкции аппарата по формуле (1.5):
=2069594*444*453=4162615804 кДжч
По формуле (1.3) найдем поверхность нагрева:
Найдем необходимую площадь для тепловых элементов;
F==42288-40835=1453
Получили необходимую площадь для реконструкции 1453 а после реконструкции она составит 1514
2 Расчет элементов конструкции аппарата.
2.1. Определим геометрические параметры аппарата.
Диаметр выпарного аппарата равен 4м выбираем по ГОСТ – 12619-78 коническое днище и ГОСТ 6533 – 78 эллиптическую отбортованную крышку с размерами ( ):
=4м – внутренний диаметр конического днища;
=335м – высота конусного днища;
=01м – высота цилиндрической части днища;
=16608 - вместимость днища;
=4м – внутренний диаметр эллиптической крышки;
=1м – высота выпуклой части крышки;
=008м – высота цилиндрической отбортованной крышки;
=131529 – вместимость крышки.
Определим длину обечайки по формуле м:
где V – объем обечайки определяется по формуле;
где =71.5 – общий объем аппарата; - объем отбортованной крышки;= 131529 ; - объем днища ; = 16608 .
Тогда по формуле (2.2) получаем ;
V=71.5-13.1529-16.608=41.7391
После подставим данные значения в формулу (2.1);
Для аппарата принимаем коэффициент сварного шва φ=1.
Определим гидростатическое давление в аппарате по формуле МПа;
где =1400 кг плотность аммиачной селитры; =9.81мс ускорение свободного падения; высота столба жидкости в обечайке м.
Высота столба жидкости в обечайки м.
где столб жидкости в цилиндрической части аппарата и определяется по формуле:
где - объем жидкости в цилиндрической части аппарата и определяется по формуле ;
где - объем жидкости в аппарате . Общий объем жидкости в аппарате составляет 35% - 25025 от всего общего объема аппарата.
По формуле (2.6) найдем:
Тогда по формуле (2.5) столб жидкости в цилиндрической части аппарата:
Найдем высоту столба жидкости:
Тогда по формуле (2.3) найдем гидростатическое давление;
Найдем расчетное давлении в аппарате. Так как аппарат работает под ваккоумом с остаточным давлением в аппарате до 0.5 МПа то расчетное давление ==0.1 МПа ().
2.2 Расчет цилиндрической обечайки под действием внутреннего давления.
Толщина стенки определяется по формуле м:
где S – исполнительная толщина стенки м; С – величина суммарной прибавки м; - расчетная толщина стенки.
где – прибавка на коррозию м;
где =0.1*мгод – величина коррозии в год;
- время эксплуатации аппарата т. к. среда в аппарате агрессивная.
где - прибавка на эрозию м. ;
- минусовой допуск на материал м. Значение минусового допуска определяется в зависимости от толщины стенки ().
Подставим цифровое значение получим м;
Подставим полученное значение в формулу (2.7) м;
По сортаменту принимаем толщину стенки цилиндрической обечайки S=4*.
Допускаемое внутреннее давление МПа определяется по формуле;
; 0.1 МПа0.139 МПа –условие прочности выполняется.
2.3. Расчет цилиндрической обечайки под действием наружного давления.
Определим толщину стенки обечайки м;
где - коэффициент определяемый в зависимости от
где Е=2.15*МПа модуль упругости
где - расчетная длина обечайки м определяется по формуле;
По расчетной номограмме принимаем =0.36.
Полученное значение подставим в формулу (2.12);
По ГОСТ 5681-75 для стали марки Х18Н10Т с расчетной толщиной стенки 12*м находим минусовой допуск и определяем величину суммарной прибавки по формуле (2.7);
По сортаменту принимаем толщину стенки обечайки S=16*.
Определим допускаемое наружное давление [р] МПа;
где -допускаемое давление из условия прочности МПа;
- допускаемое давление из условий устойчивости в пределах упругости.
Подставим полученные значения в уравнение (2.15) и проверим выполнение условий;
[; 0.1МПа0.196МПа условие устойчивости выполняется.
2.3. Расчет эллиптически отбортованной крышки под действием внутреннего давления.
Толщина стенки крышки определяется м;
где R – радиус кривизны м. Для эллиптически отбортованной крышки R=D=4 м.
По формуле (2.18) определим толщину стенки днища;
Найдем минусовой допуск и определяем величину суммарной прибавки по формуле (2.7);
По сортаменту принимаем толщину стенки эллиптической крышки принимаем S=4*.
Допускаемое внутреннее давление МПа. Определяется по формуле;
При этом должно выполнятся условие МПа; ; 0.1
Условие прочности выполняется следовательно толщина стенки выбрана верно S=4*.
2.4. Расчет эллиптически отбортованной крышки под действием внешнего давления.
За расчетное наружное давление принимаем давление
Определим толщину стенки отбортованного днища S м нагруженным давлением;
где =0.9 –коэффициент приведения радиуса кривизны крышки.
Принимаем за расчетное значение S= Находим минусовой допуск и определяем величину суммарной прибавки.
По сортаменту ГОСТ 5681-75 принимаем толщину стенки эллиптической крышки S=10*.
Определим допускаемое наружное давление
так как 0.1МПа0.254МПа. Условие выполняется.
2.5. Расчет конусного днища нагруженного внутренним давлением.
Толщину стенки конусного днища определяем по формуле м;
Тогда по формуле (2.24) определим толщину стенки конусного днища;
Находим минусовой допуск и определяем величину суммарной прибавки по формуле (2.23);
По сортаменту принимаем толщину стенки конусного днища S=4*
Допускаемое внутреннее давление МПа определяем по формуле;
Условие выполняется.
2.6. Расчет конусного днища под действием наружного давления.
За расчетное наружное давление принимаем давление равное
Определим толщину стенки отбортованного конусного днища S м нагруженного наружным давлением;
где -определяется в зависимости от значений коэффициентов ;
Подставим значения в формулы (2.27) (2.28) и найдем коэффициенты
По расчетной номограмме принимаем =0.3.
Полученное значение подставим в формулу (2.26) м;
Находим минусовой допуск и определяем величину суммарной прибавки по формуле (2.25) м;
По сортаменту принимаем толщину стенки конусного днища S=16*
Определим допускаемое наружное давление [р] МПа по формуле (2.15).
Подставим полученные выражения в формулы (2.29) (2.30) и найдем допускаемое наружное давление;
; 0.10.4МПа – Условие выполняется.
2.7. Укрепление отверстий.
Определим расчетную толщину стенки штуцера нагруженного внутренним давлением м;
Толщина стенки штуцера S м;
Находим минусовой допуск и определяем величину суммарной прибавки по формуле м;
Принимаем по сортаменту S=2*
Расчетный диаметр отверстия не требующего дополнительного укрепления м;
где ширина зоны укрепления в обечайке;
Для эллиптической крышки м;
Расчетный диаметр отверстия не требующего дополнительного укрепления определяем по формуле (2.32);
Определим расчетный диаметр отверстия м;
Так как условие не выполняется то отверстие требует укрепления.
Определим площадь вырезанного отверстия ;
Расчетная площадь укрепляемой стенки ;
где - расчетная величина зоны укрепления в стенке обечайки м;
Расчетная площадь укрепляющего сечения внешней части штуцера
где - расчетная длина внешней части штуцера участвующей в укреплении м;
где - отношение допускаемых напряжений. Так как материал обечайки и материал штуцера одинаковый
Расчетная площадь укрепления сечений внутренней части штуцера определяется по формуле;
Расчетная площадь накладного кольца жесткости формуле;
где - отношение допускаемых напряжений. В качестве конструкционного материала для накладного кольца будем использовать тот же материал тогда =1
- расчетная ширина накладного кольца м определяется по формуле;
где м – толщина накладного кольца
Условие выполняется. На этом расчет укрепления отверстий закончен.
2.8. Расчет и выбор опор
Определим вес аппарата кН;
где - вес металлоконструкции аппарата кН;
- вес арматурной обвязки куда входит вес фланцев выпускного устройства и остальных креплений опор кН.
Определим вес металлоконструкции аппарата кН;
где - вес обечайки кН и находится по формуле;
где -плотность материала обечайки;
= 4.032 м м –соответственно внешний и внутренний диаметр;
= 4 м – высота обечайки.
- вес крышки кН находим по формуле;
где F – площадь внутренней поверхности крышки
- вес конусного днища кН;
- вес крышки люка кН;
Подставим соответствующее значение в выражение (2.43) получим;
Определим вес жидкости в аппарате кН по формуле;
где -1400 - плотность аммиачной селитры;
= 25.025 - объем аммиачной селитры.
-=10830кН – вес арматуры.
Тогда общий вес аппарата составляет кН;
Для выпарного аппарата применяем цилиндрическую опору.
Найдем ширину нижнего опорного кольца м;
Выступающая ширина нижнего опорного кольца должна удовлетворять условию;
Толщину нижнего опорного кольца рассчитаем по формуле м;
Подставим численные значения в формулу (2.48) м;
Произведем подбор анкерных болтов.
Расчетное количество анкерных болтов выбираем 20. Внутренний диаметр анкерного болта определяется по формуле;
Принимаемый диаметр болтов просчитанных по условию. Следовательно подобранный диаметр болтов верный.
3. Расчет теплового элемента.
3.1. Произведем расчет теплового элемента и определим толщину стенки м по формуле;
Подставим численные значения в формулу (3.2);
Находим минусовой допуск и определяем величину суммарной прибавки по формуле (3.1);
По сортаменту принимаем толщину стенки равной S=7мм.
3.2. Определим нагрузки создаваемую тепловым элементом на стенки аппарата.
Определим массу теплового элемента кг;
где = *=3*0.15*0.007*7850=24.7 кг – масса одной пластины;
=*=3*0.016*0.007=2.6 кг – масса вставки между пластинами.
Тогда общую массу тепловых элементов определим по формуле (3.3);
Определим максимальное напряжение от основных нагрузок и реакций опор Па;
где - мембранная нагрузка МПа и определяется по формуле;
зависит от типа опор и выбирается в зависимости от и .
Найдем максимальное напряжение изгиба от реакции опоры Па;
где находится в зависимости от
Подставим найденные значения и проверим условие прочности которое имеет вид;
где А=1 для эксплуатационных условий тогда
Следовательно условие прочности выполняется.
4. Расчет ситчатой тарелки
4.1 Расчет скорости газа и диаметр абсорбера.
Скорость газа в интервале устойчивой работы ситчатых тарелок определяется с помощью уравнений;
Где =680403 кгч – расход аммиачной селитры;
=6804033600=189 кгс;
= 24969 кгч – расход аммиаковоздушного пара;
= 249693600=694 кгс;
=1.12 кгм3 – плотность аммиаковоздушного прара;
=1186 кгм3 – плотность аммиачной селитры 60%.
Подставим найденные значения в уравнение (2)
Коэффициент В равен 2.95 для нижнего и 10 для верхнего пределов нормальной работы тарелки (20). Наиболее интенсивный режим работы тарелок соответствует верхнему пределу когда В=10 однако с учетом возможного колебания нагрузок по газу принимаем В=6-8. Приняв В=8 подставим в (4.1) и получим:
Рабочую скорость газа можно рассчитать по уравнению:
Диаметр колонны с ситчатой тарелкой выбираем из таблицы 8.7 (20) по величине рабочей площади тарелки. Рассчитываем как:
где – объемный расход аммиаковоздушной смеси в аппарате.
Найденные значения подставим в формулу (4.4)
По таблице 8.7 (20) подбираем тарелку ТС-Р:
D=2600 мм – диаметр колонны;
Fp=4.780 м2 – рабочая площадь тарелки;
Fсл=0258 м2 – площадь слива;
П =1.540 м – периметр слива;
d0 =5 мм – диаметр отверстия;
t =18 мм – шаг размещения отверстий;
Н =600 мм – расстояние между тарелками.
Проверим диаметр аппарата по формуле:
Принимаем диаметр аппарата 2.6 м что соответствует подобранному по таблице.
4.2 Расчет светлого слоя жидкости на тарелке
Расчет светлого слоя жидкости на тарелке h находим из следующего соотношения:
где - высота газожидкостного барботажного слоя на тарелке м.
Из формулы (4.7) следует что:
Высоту газожидкостного слоя для ситчатых тарелок определяем из уравнения:
где – критерий Фруда.
Величина С из уравнения равна:
где = 0.03 Нм – поверхностное натяжение;
= 20.44 – вязкость аммиачной селитры 60%;
Подставим значения в формулу (4.11) получим:
Найдем С по формуле (4.10)
Тогда критерий Фруда будет равен:
Найдем высоту газожидкостного слоя:
Газосодержание барботажного слоя находим по следующему уравнению:
Тогда высота газожидкостного слоя будет равна:
Расчет гидравлического сопротивления ситчатой тарелки
Величина гидравлического сопротивления Δ барботажных тарелок рассчитываем как сумму трех частных сопротивлений (20):
где - сопротивление обусловленное силами поверхностного натяжения жидкости;
- сопротивление газожидкостного слоя на тарелке.
Сопротивление поверхностного натяжения определяется по уравнению:
где - скорость газа в отверстиях тарелки;
Значение коэффициента сопротивления Е выбираем из таблицы Е=1.5 для ситчатых тарелок. Полученные значения подставим в формулу (4.15)
Величиной пренебрегаем (20).
Гидравлическое сопротивление газожидкостного слоя на тарелке принимаем равным статическому давлению слоя:
Тогда полное гидравлическое сопротивление будет равно:
4.3 Расчет коэффициента массотдачи
Коэффициент массотдачи определяется по уравнению (20)
где Dx Dy – коэффициент диффузии.
Подсчитаем коэффициент диффузии жидкости:
где - мольная масса аммиачной селитры; Т=273+60=333 К – температура аммиачной селитры; =0.023 м3кмоль - мольный объем аммиачной селитры; В – параметр учитывающий ассоциацию молекул В=1 (20)
Коэффициент диффузии в газе подсчитаем по уравнению:
где =0198 м3кмоль- мольный объем аммиаковоздушной смеси;
=35 - мольная масса аммиаковоздушной смеси; Р=0.1 МПа – давление в абсорбере.
Рассчитаем коэффициент массотдачи по формулам (4.18) и (4.19):
Тогда коэффициент массопередачи определим по уравнению:
5 Расчет элементов конструкции аппарата.
5.1. Определим геометрические параметры аппарата.
По выбранному диаметру D=2.6 м выбираем по ГОСТ 6533 – 78 эллиптически отбортованную крышку и днище с размерами:
=2.6 м – внутренний диаметр эллиптической крышки;
=0.650 м – высота выпуклой части крышки;
=006 м – высота цилиндрической отбортованной крышки;
=2.6087 – вместимость крышки.
где =34.8 – общий объем аппарата; - объем отбортованной крышки;= 2.6087 .
Тогда по формуле (5.2) получаем;
V=34.8-2.6087 -2.6087 =29.6
По формуле (5.1) получим:
Найдем расчетное давлении в аппарате. Так как аппарат работает под ваккоумом с остаточным давлением в аппарате до 0.5 МПа то расчетное давление ==0.1 МПа.
5.2 Расчет цилиндрической обечайки под действием внутреннего давления.
где S – исполнительная толщина стенки м; С – величина суммарной прибавки м; - расчетная толщина стенки м.
- минусовой допуск на материал м. Значение минусового допуска определяется в зависимости от толщины стенки .
По сортаменту принимаем толщину стенки цилиндрической обечайки S=3*.
; 0.1 МПа0.143 МПа –условие прочности выполняется.
5.3. Расчет цилиндрической обечайки под действием наружного давления.
По расчетной номограмме принимаем =0.45.
По сортаменту принимаем толщину стенки обечайки S=14*.
- допускаемое давление из условий устойчивости в пределах упругости МПа.
Подставим полученные значения в уравнение (2.15) и проверим выполнение условий МПа;
[; 0.1МПа0.7МПа условие устойчивости выполняется.
5.3. Расчет эллиптически отбортованной крышки под действием внутреннего давления.
где R – радиус кривизны м. Для эллиптически отбортованной крышки R=D=2.6 м.
По формуле (5.18) определим толщину стенки днища м;
Найдем минусовой допуск и определяем величину суммарной прибавки по формуле (5.7);
По сортаменту принимаем толщину стенки эллиптической крышки принимаем S=3*.
Условие прочности выполняется следовательно толщина стенки выбрана верно S=3*.
5.4. Расчет эллиптически отбортованной крышки под действием внешнего давления.
Подставим полученное значение в уравнение (5.15) и проверим выполнение условий;
так как 0.1МПаМПа. Условие выполняется.
АВТОМАТИЗАЦИЯ ТЕХНОЛОГИЧЕСКОГО ПРОЦЕССА
Одним из факторов повышения производительности труда эффективности общественного производства ускорения научно-технического прогресса является автоматизация технологических процессов в пищевой и химической промышленности.
Автоматизация предполагает передачу приборам и автоматическим устройствам функций управления и контроля выполняемых человеком. Улучшение качества выпускаемой продукции повышение производительности и безопасности использования всех сырьевых ресурсов – главные цели автоматизации.
В настоящее время существует начальная комплексная и полная автоматизация. Начальная автоматизация представляет собой автоматизацию каждого технологического процесса в пределах цеха или участка отдельно независимо от других процессов. Такая автоматизация уходит в прошлое. При комплексной автоматизации все технологические процессы в пределах участка автоматизируются как одно целое. Это наиболее распространенный тип автоматизации в промышленности в настоящее время. Полная автоматизация предполагает работу производства как единой автоматически работающей системы. В наше время уже существуют заводы-автоматы где процесс выработки продукции от начала до конца производят различные машины и механизмы.
В автоматических системах управления человек только следит за состоянием средств автоматизации но не предпринимает непосредственного участия в процессе управления. Наряду с такими системами существуют и применяются автоматизированные системы управления. В таких системах человек активно участвует в самом процессе управления. Таким образом автоматизированные системы управления являются человеко-машинными системами которые преимущественно используют электронно-вычислительные машины (ЭВМ) в качестве технической базы.
Перечень контролируемых и регулируемых параметров
Параметры подлежащие контролю регулированию и сигнализации
Пределы отклонения параметров
Оптимальные значения параметров
Допустимая погрешность контроля
Условия эксплуатации прибора
Особые требования заказчика
Количество однотипных точек контроля
Возможные с учетом аварийных ситуаций
Допустимые по технологии
Температура раствора аммиачной селитры на выходе из подогревателя 1 °С
Температура раствора аммиачной селитры на выходе из кипятильника 2 (АВ) °С
Температура раствора аммиачной селитры на выходе из выпарного аппарата 3 (АВ) °С
Температура раствора аммиачной селитры в гидрозатворе 6 °С
Температура конденсата в гидрозатворе 8 °С
Разрежение в выпарном аппарате аммиачной селитры 3 (АВ) мм рт. ст.
Расход раствора аммиачной селитры в кипятильник 2 (АВ) кгч
Расход раствора аммиачной селитры на входе в гидрозатвор 6 тч
Расход раствора аммиачной селитры после насоса тч
Уровень раствора аммиачной селитры в выпарном аппарате 3 (АВ) %
Уровень раствора аммиачной селитры в гидрозатворе 6 %
Уровень технологического конденсата в гидрозатворе 8 %
2 Описание функциональной схемы автоматизации
Контроль и регулирование температуры раствора аммиачной селитры на выходе из подогревателя 1 осуществляется следующим образом. В качестве датчика используется термопреобразователь сопротивления дТС 015-50М.В3.80 (1а) сигнал с которого поступает на микропроцессорный вторичный прибор ТРМ210 (1б) показывающий текущее значение температуры и реализующий ПИД-закон регулирования. С него управляющий сигнал поступает на автоматический запорно-регулирующий односедельный клапан КЗР (1в) установленный на линии подачи пара.
Контроль температуры раствора аммиачной селитры на выходе из кипятильника 2(АВ) осуществляется следующим образом. В качестве датчика используется термопреобразователь сопротивления дТС 015-50М.В3.80 (2а 4а) сигнал с которого поступает на микропроцессорный вторичный прибор ТРМ210 (2б 4б) расположенный на щите и показывающий текущее значение температуры. Осуществляется сигнализация завышения максимально допустимого значения температуры спомощью индикатора расположенного на лицевой панели вторичного прибора ТРМ210.
Контроль и регулирование температуры раствора аммиачной селитры на выходе из выпарного аппарата 3(АВ) осуществляется следующим образом. В качестве датчика используется термопреобразователь сопротивления дТС 015-50М.В3.80 (3а 7а) сигнал с которого поступает на микропроцессорный вторичный прибор ТРМ210 (3б 7б) показывающий текущее значение температуры и реализующий ПИД-закон регулирования. С него управляющий сигнал поступает на автоматический запорно-регулирующий односедельный клапан КЗР (3в 5в) установленный на линии подачи пара. В случае завышения текущим значением температуры максимально допустимого со вторичного прибора ТРМ210 (3б 7б) поступает сигнал на отсечной клапан КМ (3г 5г) открывающий доступ в аппарат 3(АВ) технической воды.
Контроль температуры раствора аммиачной селитры в гидрозатворе 6 (контур 4) и температуры конденсата в гидрозатворе 8 (контур 5) осуществляется аналогично контуру 2.
Контроль давления пара на входе греющей камеры 2(АВ) осуществляется следующим образом. В качестве датчика используется преобразователь для измерения давления Сапфир-22ДА (8а 10а) унифицированный электрический сигнал с которого поступает на микропроцессорный вторичный прибор ТРМ210 (8б 10б) показывающий текущее значение давления.
Контроль разрежения в выпарном аппарате аммиачной селитры 3(АВ) осуществляется следующим образом. В качестве датчика используется преобразователь для измерения давления Сапфир-22ДВ (9а 11а) унифицированный электрический сигнал с которого поступает на микропроцессорный вторичный прибор ТРМ210 (9б 11б) показывающий текущее значение разрежения.
Контроль давления во влагоуловителе 5 (контур 8) осуществляется аналогично контуру 6.
Контроль и регулирование расхода раствора аммиачной селитры в кипятильник 2(АВ) осуществляется следующим образом. В качестве датчика используется диафрагма камерная ДК-100-06 (18а) создающая перепад давления измеряемый спомощью дифференциального манометра Сапфир-22ДД 2410 (18б) унифицированный электрический сигнал с которого поступает на микропроцессорный вторичный прибор ТРМ210 (18в) показывающий текущее значение расхода и реализующий ПИД-закон регулирования. С него управляющий сигнал поступает на автоматический запорно-регулирующий односедельный клапан КЗР(18г) расположенный на линии подачи раствора аммиачной селитры.
Контроль и регулирование расхода раствора аммиачной селитры на входе в гидрозатвор 6 осуществляется следующим образом. В качестве датчика используется диафрагма камерная ДК-100-06 (20а) создающая перепад давления измеряемый спомощью дифференциального манометра Сапфир-22ДД 2410 (20б) унифицированный электрический сигнал с которого поступает на микропроцессорный вторичный прибор ТРМ210 (20в) показывающий текущее значение расхода и реализующий ПИД-закон регулирования. С него управляющий сигнал поступает на автоматический запорно-регулирующий односедельный клапан КЗР(20г) расположенный на линии подачи раствора аммиачной селитры.
Контроль расхода раствора аммиачной селитры после насоса осуществляется следующим образом. В качестве датчика используется диафрагма камерная ДК-100-06 (15а) создающая перепад давления измеряемый спомощью дифференциального манометра Сапфир-22ДД 2410 (15б) унифицированный электрический сигнал с которого поступает на микропроцессорный вторичный прибор расходомер РМ1 (15в) показывающий текущее и суммарное значение расхода.
Контроль и регулирование уровня раствора аммиачной селитры в выпарном аппарате 3(АВ) осуществляется следующим образом. В качестве датчика используется кондуктометрический датчик уровня жидкости ДС.К-195 (16а 17а) сигнал с которого поступает на микропроцессорный вторичный прибор ТРМ210 (16б 17б) показывающий текущее значение уровня и реализующий ПИД-закон регулирования. С него управляющий сигнал поступает на автоматический запорно-регулирующий односедельный клапан КЗР(16-17в). Осуществляется сигнализация завышения максимально допустимого и занижения минимально допустимого значения уровня спомощью индикаторов расположенных на лицевой панели вторичного прибора ТРМ210.
Контроль и регулирование уровня раствора аммиачной селитры в гидрозатворе 6 (контур 13) и уровня технологического конденсата в гидрозатворе 8 (контур 14) осуществляется аналогично контуру 12.
Электродвигатель М1 запускается в работу при помощи магнитного пускателя ПМЕ-17 (КМ1) который в свою очередь включается через переключатель УП5312 (SA1) с помощью кнопок одна из которых установлена на щите КЕ-014 (SB1) а вторая по месту КЕ-014 (SB2). В момент вращения двигателя загорается лампа РНЦ-53 (HL1). Аналогично осуществляется управление электродвигателями М2-М7.
МОНТАЖ ЭКСПЛУАТАЦИЯ И РЕМОНТ ОБОРУДОВАНИЯ
Выпарной аппарат и абсорбционная колонна устанавливаются на цилиндрических опорах которую закрепляют по периметру проема в перекрытии с помощью анкерных болтов согласно строительному чертежу.
Пред монтажом аппаратов проверяют их комплексность соответствие проектным чертежам состояние корпуса уплотнительных поверхностей штуцеров сборочных единиц отсутствие повреждений поломок и прочих видимых дефектов.
Для подъема в проектное положение аппарат стропят тросовыми петлями охватывающими корпус выше центра тяжести и возможно ближе к фланцу. С помощью грузоподъемных средств аппарат устанавливается на опорную раму.
После того как аппараты смонтированы производят их обвязку трубопроводами.
Трудоемкость монтажа трубопроводов составляет примерно 30% монтажных работ. При монтаже выполняются следующие операции: резка труб сварка труб сборка плетей гидроиспытания. Резка труб осуществляется при монтаже с выполнением прямых и косых резов вырезов гнезд в трубах обработкой штуцеров врезаемых в трубу. Разметка труб осуществляется с использованием шаблонов вырезаемых из бумаги.
Резка труб осуществляется установкой для газопламенной резки и маятниковой пилой с абразивными кругами диаметром 300 и 400мм. Резка труб абразивными кругами может осуществляться на приспособлении имеющим опорные ролики упор-измеритель длины отрезка и вращатель трубы. Для отрезки концов труб и снятие фасок применяется установка. Снабженная оправкой центрирующей установку по внутреннему диаметру трубы. Гнутые детали трубопроводов изготавливаются на заводах монтажных заготовок.
При сборке труб под сварку в следствии отклонений размеров по диаметру и толщине стенки возникает необходимость в калибровке или расточке. Калибровка концов труб осуществляется их раздачей коническими пуансонами в горячем состоянии.
Для вращения труб при автоматической сварки используются вращатели состоящие из рамы и двух опор с катками. Катки одной опоры имеют привод от электродвигателя постоянного тока и прижим трубы. Вторая опора является поддерживающей и может перемещаться в горизонтальном направлении по раме.
При сборке трубных элементов состоящие из прямого участка трубы и трубной заготовки наиболее частой операцией является соединение фланца с трубой. При большем количестве фланцев для сокращении времени на их разметку используют различные приспособления и шаблоны.
Приварку фланцев к трубам ускоряется при использовании поворотного стола. Поворачивая стол. Сварщик из одного положения приворачивает фланец к трубе. Высота стола для удобства выполнения сварки регулируется. Фланец прихваченный к трубе устанавливается для сварки по оси поворотного стола.
Термообработка сварных швов осуществляется гибкими поясами для индуктивно-радиационного нагрева. Индукционный нагреватель представляет собой конструкцию для двух таких пластин коррозионностойкой стали между которыми натянуто несколько рядов нихромовой проволоки уложенной в керамические кольца. Пояс длиной более пяти метров наматывается на стык в виде спирали обеспечивающей не только тепловой но и индукционный нагрев. Сверху пояс укутывается теплоизоляционными материалами. Кроме термообработки эти нагреватели используются для предварительного сопутствующего нагрева кромок при сварке.
Трассы трубопроводов прокладываются либо по эстакадам заблаговременно построенным либо бетонным фундаментом изготовленным по ходу трассы трубопровода. Также при необходимости монтажа трубопровода производится при помощи потолочных подвесок.
После окончания монтажа трубопроводов проводится проверка качества работ промывка или продувка а затем испытания на прочность и плотность. технологическая аппаратура перед испытанием отключается при помощи заглушек концы трубопровода тоже глушатся. Заглушаются все врезки для контрольно измерительных приборов. В наиболее низких точках вворачиваются штуцера с арматурой для спуска воды при гидравлическом испытании а в наиболее высоком для выпуска воздуха. В начальных и концевых точках трубопровода а также на компрессоре устанавливаются манометры с классом точности не ниже 15.
Величина испытательного давления должна быть не меньше 125 максимально рабочего давления. Давление при испытании выдерживается 5 минут. После этого оно снижается до рабочего значения. Трубопровод тщательно осматривается. Сварные швы обстукиваются легким молотком. После испытания открываются воздушники и трубопровод полностью освобождается от воды.
После того как проведены гидравлические испытания трубопроводов к испытанию аппаратов. По окончанию испытаний оборудование сдается в эксплуатацию.
Основным видом колонной аппаратуры является забивка колонны отложением и коррозия её элементов.
Для промывки выпарного контура к нему подводится паровой конденсат (техническая вода). Выпарной аппарат в процессе работы покрывается осадком карбоната кальция и других солей что снижает интенсивность процесса выпарки. Для удаления образовавшегося осадка выполняют промывку аппаратуры раствором каустической соды NaOH с массовой долей сухого натра 8 – 10%. В случае сильной забивки производят его отчистку с помощью насоса высокого давления.
По графику ППР остановка цеха осуществляется раз в год. За этот период времени предусмотрен осмотр выпарных установок на дефекты. Цельносварный выпарной аппарат при ремонте не демонтируется демонтируются только внутренние устройства колонны. После подготовительных операций (пропарки промывки) открываются люки аппарата. Для облегчения труда рабочих занятых на этой работе крышки люков рекомендуется устанавливать на петлях.
Люки нужно открывать в строгой последовательности начиная с верхнего для предотвращения потока воздуха через колонну при одновременном открытии нижнего и верхнего люков.
После пропаривания аппарата промывается водой и проветривается. Проветривание необходимо для охлаждения колонны и доведения концентрации продуктов в ней до допустимых санитарных норм. После окончания проветривания нужно провести анализ проб воздуха взятых из аппарата на разных высотных отметках. К работам внутри колонны разрешается приступать только тогда когда анализ покажет что концентрация вредных газов и паров в ней не превышает предельно допустимых санитарных норм.
Безопасное обслуживание оборудования заключается в правильной его эксплуатации. Поэтому необходимо строго соблюдать требования технологического регламента цеха нарушение которых может привести к аварийной ситуации. При пуске линии проводятся следующие операции в указанном порядке:
Убираются все посторонние предметы с проходов и площадок обслуживания.
Проверяется отсутствие посторонних предметов в аппаратах.
Контролируется наличие защитных ограждений и их состояние.
Исследуется исправность контрольно-измерительных приборов внешним осмотром.
Кратковременным пуском испытывается работа всех устройств линии.
Проверяется исправность системы пожаротушения.
Открывается воздушный вентиль включается вентилятор.
При нормальном ведении технологического процесса аппаратчикам и операторам необходимо:
Контролировать параметры технологического режима согласно цеховым инструкциям при отклонении норм принять меры по восстановлению до заданных значений.
По мере засорения производить чистку оборудования не допуская забивок.
Следить за состоянием оборудования при неисправности во время его отключить.
Останов и ремонт проводится согласно указаниям сменного мастера в обратном порядке пуску. При нормальной работе оборудования следует производить его осмотр для выявления дефектов возникающих во время работы. При их обнаружении необходимо сразу же довести до сведения мастера или начальника смены.
Перед вводом в работу аппарата или колонны необходимо проверить герметичность корпуса фланцевых соединений люков. По правилам техники безопасности запрещается производить ремонтные работы наладку очистку отбор проб в процессе работы механизмов.
Соблюдение этих требований снижает количество выходов оборудования из строя увеличивает его межремонтный пробег увеличивает безопасность обслуживания оборудования. Перед вводом в работу аппарата или колонны необходимо проверить герметичность корпуса фланцевых соединений люков.
В процессе эксплуатации трубопроводы изнашиваются от механического теплового и коррозионного воздействия. При ремонте выполняются следующие основные работы:
- замена износившихся деталей и узлов или исправление их до соответствующих норм допусков и размеров;
- выверка трубопроводов а в случае необходимости подгонка опор и подвесок;
- модернизация или реконструкция трубопроводов с возможной унификацией сменных частей;
- испытание на прочность и плотность;
- окраска трубопроводов.
За 2-3 часа до разборки фланцевых соединений трубопроводов резьбовую часть крепежных деталей необходимо смочить керосином. Отворачивание гаек происходит в два приема: с начало все гайки ослабляются поворотом на 18 оборота затем отворачиваются в любой последовательности.
Раздвижку фланцев можно осуществлять следующим образом. В двух диаметрально противоположных отверстиях фланцах нарезается резьба. В эти отверстия вворачиваются болты а в зазор между фланцами вставляют металлические пластины для упора болтов. При поочередном заворачивании болтов фланцы разжимаются.
Пред удалением участка трубопровода необходимо разделяемые участки закрепить так чтобы предупредить их смещение. Участок подлежащий удалению крепиться в двух местах. После демонтажа участок трубопровода свободные концы оставшихся труб необходимо закрыть пробками или заглушками. При установке нового участка его с начало укрепляют на опорах а затем сваривают.
При ремонте трубопровода замена изношенных участков надземного трубопровода может выполняться по трубно. Возможна также сборка участков из секций которые собирают и сваривают из отдельных труб и их элемента вблизи трассы.
После окончания капитального ремонта трубопроводов производиться его испытания таким же образом как и после монтажа (раздел 6.1).
Ремонт сварных и паяных соединений осуществляется путем подваривания и пайки. Для выявления дефектов сварного соединения применяются различные способы: внешний осмотр рентгеновское просвечивание магнитный и ультразвуковой контроль. Выявление трещин также возможно при опрессовывании трубопроводов. Обнаруженные трещины засверливают по концам а вдоль трещины делают канавку. Затем трещины заваривают.
Демонтаж корпуса цельносварных аппаратов проводится при необходимости замены части корпуса. Наиболее часто в следствии коррозии выходит из строя днища. Замена части корпуса в том числе и днища может осуществляться без демонтажа колонн. Для этого к верхней части колонны крепиться опорная площадка под которую подводятся домкраты. Нижняя часть колонны отрезается и после подъема верхней части на высоту 100мм удаляется. После подведения новой нижней части верхняя часть опускается и сваривается с нижней.
Замена днищ – ответственная операция требующая выполнения необходимых расчетов разработки технической документации соблюдения дополнительных мер безопасности.
Для каждой единицы оборудования на предприятии составляется график планово-предупредительного ремонта (ППР). Основываясь на рекомендациях завода изготовителя о частоте поверок и ремонтов на предприятиях эксплуатирующих то или иное оборудование составляется индивидуальный график этих аппаратов в котором регламентируется время необходимое на ремонт. Частота проведения тех или иных ремонтов и количество трудозатрат.
Так как разрабатываемое в дипломном проекте оборудование работает с агрессивными средами то за ними производится наиболее тщательный контроль. Так помимо ежедневных осмотров в графике ППР предусмотрен капитальный ремонт.
При капитальном ремонте который производится один раз в год производится полный осмотр всех аппаратов. Производится их полная разборка дефектовка всех деталей и узлов с последующим их ремонтом собственными силами или силами специализированных организаций.
БЕЗОПАСНОСТЬ И ЭКОЛОГИЧНОСТЬ ПРОЕКТА
Работоспособность человека находится в прямой зависимости от условий труда. Неудовлетворительное состояние условий труда приводит к нарушению режима технологических процессов снижению производительности труда и качества готовой продукции повышению травматизма и профзаболеваний.
Воздействие опасного фактора на работающего в определенных условиях приводит к травме или к другому внезапному резкому ухудшению здоровья; воздействие вредного фактора приводит заболеванию или снижению работоспособности.
Проанализируем основные опасные и вредные факторы при производстве нитроаммофоски в процессе выпаривания аммиачной селитры.
Большая мощность и последовательная структура агрегата задают повышенные требования к надежности контроля регулирования и защиты так как вывод из строя отдельного элемента зачастую приводит к полной остановке агрегата и как следствие к большим экономическим потерям.
Территориальная разобщенность рабочих мест при большом числе взаимосвязанных узлов регулирования затрудняет координацию действий аппаратчиков. Поэтому требуется единая техническая система с учетом всех взаимосвязей и взаимного влияния отдельных устройств друг на друга. Результатом этого является отказ от традиционных помещений щитовых на отдельных стадиях процесса концентрация управления в руках одного человека. Сосредоточение всей информации и управления агрегатом в руках одного оператора требует организации рационального ее представления. Для этого все органы управления регуляторами и исполнительными механизмами размещены на пульте; здесь же выполнена мнемосхема производства с вмонтированными в нее кнопками вызова параметров и сигнальными лампами.
Для снижения психологической нагрузки на оператора вызвана информационной насыщенностью пульт снабжен системой сигнализации отклонения параметров от нормы и системой группового вызова. Это позволяет оператору при отсутствии сигналов выборочно проверять состояние различных параметров а при наличии сигнала одним нажатием кнопки вызывать на контроль всю группу параметров. Связанных с нарушением параметров. При необходимости дополнительную информацию оператор получает с записывающих приборов.
Безопасность процесса нейтрализации обеспечивает автоматическими блокировками прекращающими подачу сырья в аппараты ИТН при нарушениях соотношение расходов азотной кислоты и газообразного аммиака или при росте температуры в реакционной зоне выше 1400 ; в последнем случае В ИТН автоматически подается конденсат водяного пара.
Подогреватель азотной кислоты предназначен для подогрева 58-60% азотной кислоты от температуры при которой он храниться на складе до температуры 80-900С за счет тепла сокового пара из аппарата ИТН.
Подогреватель газообразного аммиака предназначен для нагрева аммиака до 120-1800С.
Выпарной аппарат в нем получают высококонцентрированный плав в одну ступень. Он предназначен для выпарки аммиачной селитры 58-60% до 90% под вакуумом.
Промывное и фильтрующее оборудование предназначены. Для отмывки пыли аммиачной селитры уносом воздуха из башни аэрозольных частиц аммиачной селитры из паровоздушной смеси выпарного аппарата воздуха из башен сокового пара из аппаратов ИТН а также аммиака их этих потоков.
Аммиачная селитра NH4NO3 – бесцветное кристаллическое вещество содержащее 60% кислорода 5% водорода и 35% азота. Технический продукт содержит не менее 340% азота.
Основные физико-химические свойства аммиачной селитры:
- истинная 169-1725
Насыпная при влажности гранулированного продукта 1% и 200С:
- при плотной упаковке 1164
- при неплотной упаковке 0826
Температура плавления 0С 1696
Теплота плавления кДжкг 7321
Теплота образования при 250С и 0101 МПа кДжмоль 3656
Метеоусловия в производственных помещениях необходимо поддерживать в соответствии с допустимыми нормами. С целью поддержания допустимых параметров: температуры и относительной влажности проектом предусматривается использовании систем вентиляции. Вентиляция в рабочем помещении может быть естественной или искусственной. Естественную вентиляцию применяют если на одного работающего приходится не менее 40 м3 объема помещения и отсутствие вредные вещества в этом помещении. В рассматриваемом цехе необходимо применять искусственную вентиляцию. Схема вентиляции может быть приточной вытяжной и приточно-вытяжной.
Организация рационального освещения рабочих мест является основным вопросом охраны труда. От устройства освещения во многом зависит производительность и безопасность труда а так же качество выполняемых работ.
Необходимая освещенность в цехе достигается путем применение естественного и искусственного освещения. Характеристика освещения рабочих мест представлена в таблице.
Характеристика освещения рабочих мест
Разряд зрительных работ
Естественное освещение
Искусственное освещение лампа накаливания
Коэффициент естественного освещения %
Нормативная освещенность лк
Нормативная освещенность рабочей зоны достигается: периодической частотой светильников; путем своевременной протирки и мытьем остекленных световых проемов; исключение загромождение световых проемов.
По данным инструментальных замеров уровни искусственного освещения не противоречат требованиям СНиП 23-05-95 « Естественное и искусственное освещение»
Если руководствоваться нормативными данными по уровню звука в октавной полосе то для рабочей зоны промышленных предприятий уровень звука (при постоянном требовании в них работающих) не должен превышать 90дБА (СНиП 20-03-2003).
Практически все технологические оборудование является источником шума и вибрации. Для снижения шума систематически проверяют износ трущихся частей деталей (шестеренок втулок роликов и т.д.) принимают соответствующие меры. Шумящие механизмы устанавливаются в звукоизолирующем кожухе. Для борьбы с вибрацией система вентиляции кондиционирования воздуха воздуховоды присоединены к вентиляторам через гибкие вставки а сами вентиляторы установлены на вибрирующих рамках.
По электробезопасности помещения цеха можно отнести к III категории помещений то есть к помещениям особо опасным.
Недоступность токоведущих частей для случайного прикосновения обеспечивается путем применения надежной электрической размещением их на недоступной высоте установкой ограждений.
Для защиты людей от поражений электрическим током в условиях производства применяются следующие меры:
- контролируется изоляция;
- обеспечивается не доступность токоведущих частей;
- применяется защитное заземление зануление;
- применяется защитное отключение и защитные средства.
Электрические разряды часто являются причиной пожаров и взрывов. Кроме того статическое электричество является причиной нарушения технологических процессов снижению производительности агрегатов точности показаний электрических приборов и приборов автоматики. Поэтому защита от статического электричества имеет очень большое значение.
Меры защиты от статического направлены на предупреждение возникновения и накопление зарядов созданий условий рассеивания статического электричества. К основным мерам защиты относятся: заземление оборудования и коммуникаций выполненных из электропроводящих материалов уменьшению электрического сопротивления перерабатываемых веществ снижению интенсивности возникновению зарядов статического электричества нейтрализации зарядов отвод зарядов статического электричества накапливающих на людях.
Свойства веществ образующихся в результате производственного процесса приведено таблице 2.
Таблица 2 – Вредные вещества образующиеся и используемые в технологическом процессе
Воздействие на организм человека
Вызывает ожоги язвы кожи раздражают дыхательные пути
Если концентрация аммиачной селитры будет превышать ПДК – это может привести к заболеваниям. Предупреждение профессиональных заболеваний осуществляют: техническими мероприятиями – герметизация оборудования и коммуникаций; санитарно-техническими мероприятиями – эффективной естественной вентиляцией местной общеобменной вентиляцией; санитарно-гигиеническими мероприятиями: поддержанием гигиенических характеристик на рабочих местах в производственных помещениях; лечебно-профилактическими мероприятиями: соблюдения режима труда и отдыха профилактическое лечение на основе медицинских осмотров.
К психофизическим факторам относятся физические перегрузки опорно-двигательного аппарата; физически недостаточную двигательную активность; физические перегрузки органов кровообращения дыхания голосовых связок; нервно-психологической перегрузки.
Монотонность однообразие приемов в работе например при работе приводят к нарушению различных функций организма. Правильно организованная производственная гимнастика снижает заболеваемость и травматизм.
Некоторые критерии бальной оценки ОВПФ приведены в таблице 3.
Таблица 3- Критерии бальной оценки.
Наименование производственного фактора
Фактическое значение фактора Хфi
Повышение уровня звукового давления
Неоптимальные метеоусловия
Фактические значения фактора Хфi определяются по формуле:
Определим интегральную бальную оценку тяжести труда Uт по формуле:
Uт = (Хфmax + ((6- Хфmax)6(n-1))*Σ Хфi)10
Где Хфma Хф n-число всех учитываемых на РМ элементов производственной среды.
Uт =(4+5*(6-4)6(3-1))10=483
Полученная интегральная бальная оценка соответствует работе при выполнении которой неблагоприятные условия труда приводят к перенапряжению организма. Происходит снижение работоспособность человека и функциональные изменения выходящие за пределы нормы но не ведущие к патологическим нарушениям.
Обеспечение чистоты воздуха – одна из важнейших задач в системе мероприятий по охране окружающей среды т. к. загрязнение атмосферы представляет собой большую опасность.
В качестве защитных мер по предотвращения загрязнения атмосферы выбросами предприятия выступают:
- создание санитарно-защитной зоны между источниками выбросов и жилой застройки которая должна быть озелена;
- правильное взаиморасположение источников выбросов и жилых зон с учетом направления господствующих ветров;
- рассеивание выбросов через высокие дымовые трубы;
- очистка аспирационного воздуха перед выбросом в атмосферу.
3 Защита работающих и материальных ценностей при возникновении чрезвычайной ситуации
ЧС в цехе может стать возникновение пожара. Возгорание и пожары в цеже могут произвести вследствии нарушения правил пожарной безопасности правил эксплуатации электрооборудования (длительные перегрузки и последующие короткие замыкания выбор и монтаж электрических машин без учета категории производства) неисправности электропроводки несоблюдения температурных режимов.
Распространение пожара может осуществляться через оконные проемы двери и воздуховоды системы вентиляции. Рассматриваемый цех относится к категории Б (взрывопожароопасные производства) –производства связанные с возможностью возникновения взрывов и загоранию горючих газов степень огнестойкости здания II(НПБ 105-03).
Пожарная защита предусматривает максимально возможное применение не горючих и трудногорючих веществ изоляцию горючей среды предотвращение распространения пожара за пределы очага применения средств пожаротушения средств коллективной и индивидуальной защиты людей средств пожарной сигнализации.
Для выхода людей из очага возможного пожара и выноса материальных ценностей предусмотрено два эвакуационных выхода. При эвакуации имеют естественное и аварийное освещение.
Для защиты от электростатической индукции все металлически корпуса оборудования присоединяют к специальному заземлению. Сопротивление которого не менее 10 Ом. Защиту от искрения порождаемого электромагнитной индукцией выполняют устанавливая перемычки через каждые 25-30 см в местах опасного сближения (менее 10 см). Перемычки в местах соединений не требуются.
Для обнаружения пожара сообщений о месте его возникновения и вызова пожарных подразделений к месту пожара служит система автоматической пожарной (АПС) и охрано-пожарной сигнализации (ОПС). Предусмотрены первичные средства пожаротушения – огнетушители (ОХП-10. ОУ-2А); ведра емкости с водой ящики с песком ломы топоры лопаты и т. д.
ТЕХНИКО-ЭКОНОМИЧЕСКИЙ РАСЧЕТ
Технико-экономические расчёты
В данном разделе пояснительной записки будут оценены экономические преимущества и целесообразность предлагаемых в дипломном проекта разработок. Для этого необходимо рассчитать экономическую эффективность предлагаемых технологических и конструкционных решений по упариванию исходного раствора при производстве нитроаммофоски и определить срок окупаемости затрат на их реализацию.
Основные показатели необходимые для расчёта экономических величин характеризующих эффективность предлагаемой решений представлены в таблицах 8.1 8.2 и 8.3
1 Расчёт капиталовложений в проект
Основные технико-экономические показатели
Объём производства нитроаммофоски
- до внедрения проекта
- после внедрения проекта
Цена 1 т нитроаммофоски
Себестоимость 1 т нитроаммофоски
Норматив амортизационных отчислений
Норматив затрат на ремонт
Стоимость технических средств для реализации проекта всего
Средний заработок по предприятию
- по дополнительному персоналу
Покупная цена электроэнергии для предприятий
Режим работы предприятия
Стоимость 1 чел.-ч. проектных работ
Норматив экономической эффективности капитальных затрат
Первой из основных технико-экономических характеристик предлагаемого проекта являются капитальные затраты. Они определяют затраты на создание и внедрение проекта которые могут направляться на проектирование изготовление и монтаж новых узлов и оборудования покупку комплектующих и технических средств обеспечение дополнительными производственными площадями и инфраструктурой. Расчёт производим по формуле:
К=Км + Кв + Ки + Кс + Кп + КдКо р (1)
Кб - балансовая стоимость основного оборудования дополнительно устанавливаемое по проекту р;
Кв - стоимость вспомогательного и резервного оборудования р;
Ки - затраты на создание дополнительной инфраструктуры р;
Кс - стоимость зданий и служебных помещений дополнительно необходимых при реализации проекта р;
Кп - предпроизводственные затраты включающие расходы на проектирование и разработку р;
Кд - стоимость демонтируемых основных производственных фондов равная разнице между их остаточной стоимостью ( с учётом стоимости демонтажа ) и выручкой от их реализации р;
Ко - экономия капиталовложений за счёт реализации оборудования технических средств демонтируемых при реализации проекта р. Учитывается по выручке от их продажи на сторону.
Для расчёта составляющих формулы (1) необходимо использовать таблицы 8.2 и 8.3.
Расчёт трудозатрат и средств на оплату труда
Расчёт материальных расходов
Наименование материальных и технико-энергетических элементов
Сырьё материалы комплектующие
Прокат стальной легированный лист
Прокат стальной уголок швелер
Прокат стальной труба
Прокат стальной круг
Теплообменный модуль
Датчики регуляторы и т.д.
Электроэнергия (льготный тариф)
Расчёт Км будем производить по фактической стоимости поступающего на баланс основного устанавливаемого в цехе оборудования с учётом его рыночной стоимости.
Балансовая стоимость основного оборудования совпадает с его полной себестоимостью изготовления которая включает в себя материальные и трудовые затраты а так же накладные расходы.
Спол = (1+Кн)Зп р (2)
Кн - коэффициент учитывающий накладные расходы (Кн = 2030);
Зп - прямые затраты на изготовление оборудования вычисляемые как:
Зо - зарплата основная и дополнительная с начислениями определяемая по формуле:
Кз - коэффициент учитывающий дополнительную зарплату и начисления. Принимаем равным 20.
Тогда используя (2) - (4) получим:
Зо = 26263 2=52526 р
Зп =52526 + 618298 = 670824 р
Кб =(1+25) 670824 = 2347884 р.
В следствии отсутствия полной информации о стоимости приобретаемых технических средств Кв и Ки вычислим по упрощенным формулам:
Кв = 02Кб р Ки = 01Кб р (5)
Кв = 022347884 = 4695768 р
Ки =012347884 = 2347884 р.
Рассчитаем стоимость технических средств которая является общей суммарной стоимостью балансовой стоимости основного оборудования дополнительно устанавливаемое по проекту и стоимостью вспомогательного и резервного оборудования то есть:
Кб+Кв = 2347884 + 4695768 = 28174608 р.
Полученное значение занесём в таблицу 8.1.
Новое оборудование предлагаемое в дипломном проекте будет установлено на уже имеющихся в цехе производственных площадях таким образом для внедрения проектируемого оборудования дополнительной площади не требуется следовательно Кс=0. Устаревшее а также демонтированное оборудование реализовывать не будем следовательно Ко = 0.
Для реализации предлагаемого проекта реконструкции участка требуется работа 2 проектировщиков в течение 20 дней.
Определим затраты на проектирование:
Тп - трудоёмкость проектных работ чел.ч.;
Цчч - средней стоимости человека-часа р;
Ч - число проектировщиков чел.;
В - длительность проектирования рабочих дней;
Для инженерно – технического персонала длительность рабочего дня составляет восемь часов. Значение средней стоимости человека-часа приведено в таблице 8.1. Используя формулы (6) и (7) получим:
Кп = 32080 = 25600 р.
Подставим полученные составляющие в формулу (1).
К = 2347884 + 4695768 + 2347884 + 25600 = 30778492 р.
2 Расчёт дополнительных текущих расходов при реализации проекта
Рассмотрим следующую характеристику отражающую дополнительные средства используемые для реконструкции и модернизации отделения по упариванию раствора которые необходимо учитывать при разработке проекта.
И - дополнительные текущие расходы ргод. Их принято определять по формуле:
И = Из + Иэ + Иат + Иас + Им + Ип р (8)
Из - затраты на содержание персонала дополнительно необходимого для обслуживания оборудования и технических средств после реализации проекта ргод;
Иэ - стоимость дополнительно потребляемых энергоресурсов ргод;
Иат - дополнительные расходы на содержание текущий ремонт и амортизацию оборудования и технических средств ргод;
Иап - дополнительные расходы на содержание текущий ремонт и амортизацию зданий и помещений занимаемым оборудованием и персоналом ргод;
Им - дополнительные расходы основных вспомогательных материалов и приборов ргод;
Ип - прочие дополнительные расходы (стоимость услуг сторонних организаций содержания транспорта и другие административно-управленческие расходы) ргод.
Новое оборудование устанавливаемое по разрабатываемому проекту не является электропотребляющими устройствами и аппаратами кроме того не предусматривается установка оборудования дополнительно потребляющего другие энергоресурсы т. е. Итоп = Ипар = Исв = Ивод=0.
Таким образом Иэ = 0 р.
Предлагаемым проектом не предусматриваются другие дополнительные расходы поэтому Иас = Им = Ип = 0 р.
В связи с тем что данный проект предусматривает внедрение нового оборудования то будут необходимы дополнительные расходы на текущий ремонт содержание и амортизацию этого оборудования. Эти расходы можно рассчитать учитывая действующие нормы и стоимости технических средств принимаемых на баланс предприятия по формуле:
Иат = (Кб +Кв +Ки)Нар р (9)
где Нар = На + Нр - норматив расхода на текущий ремонт содержание и амортизацию (значения На и Нр берём из таблицы 8.1).
Стоимость технических средств является совокупностью следующих величин:
Кб - балансовая стоимость основного оборудования дополнительно устанавливаемого по проекту р;
Ки - затраты на создание дополнительной инфраструктуры р.
Иат = (2347884 + 4695768 + 2347884) 17100 = 5188823 р.
В результате получим:
3 Расчёт экономии текущих затрат
Третья экономическая характеристика разрабатываемого проекта - экономия текущих затрат Эт определяемая на календарный год ргод. В связи с тем что в предлагаемом дипломном проекте разрабатывалось оборудование которое будет гармонично включено в имеющийся технологический процесс то расчёт экономии текущих затрат проведём не общепринятым способом суммирования отдельных составляющих экономии а исходя из практического эффекта от внедрения предложенного проекта.
Годовая программа выпуска нитроаммофоски по внедряемому проекту увеличиться на 5% и составит В2 = 577500 т . Таким образом прирост выпуска продукции составит Ва = 27500 т.
В бизнес-плане было показано что для изготовления нитроаммофоски на новом предлагаемом в дипломном проекте оборудовании будет использоваться уже имеющееся исходное сырьё кроме того предлагаемые в дипломном проекте новые единицы оборудования будут располагаться находится на тех же производственных площадях что и старые.
Вычислим прибыль предприятия от реализации нитроаммофоски с использованием нового оборудования:
П = (Ц1 – Спол)·Ва р (8.17)
П = (6430 – 4620)·27500 = 49775000 р.
Таким образом для внедряемого проекта
Эт = П - И = 49775000 - 5188823 = 49256117.7 р.
4 Расчёт годового экономического эффекта и коэффициента эффективности капиталовложений
Годовой экономический эффект обусловленный внедрением проекта составит:
Эг = Эт - ЕнК ргод (21)
где Ен - нормативный коэффициент экономической эффективности капитальных вложений в проект (значение находится в таблице 8.1).
Эг =49256117.7 - 01530778492 = 4463934.32 р.
Расчётный срок окупаемости капиталовложений с момента начала промышленной эксплуатации после внедрения проекта составит
То =30778492 49256117.7 = 006 года 85 месяца.
Период реализации проекта с начала его финансирования до момента промышленной эксплуатации вычисляется с учётом времени необходимого на проектирование изготовления и получения комплектующих сборку монтаж и наладку а также опытную эксплуатацию по формуле
Тр = Тп + Ти + Тн + Тоэ дней (23)
Тп = 20 дней - время необходимое на проектирование;
Ти = 32 дней - время на изготовление и получение комплектующих;
Тн = 24 дней - время на сборку монтаж и наладку;
Тоэ = 20 дней - время на опытную эксплуатацию.
Тр = 20+32+24+20=96 дней.
Прирост прибыли предприятия обусловленный внедрением проекта составит:
Пп = П = 49775000 р.
Отчисления налога с прибыли 24% и на пользование автодорогами 4%.
Пч = 49775000 - 49775000028=35838000 р.
Показатель эффективности капиталовложений в проект определяется по формуле:
Эк.в. = ПпК 100 % (27)
Эк.в. = 4977500030778492 100 = 1618 %.
Результаты реализации проекта
Наименование показателей
До внедрения проекта
Объём производства нитроаммофоски т в год;
Приращение объёма производства нитроаммофоски %
Окупаемость капиталовложений год
Эффективности капиталовложений в проект %
Годовой экономический эффект р.
Чистая прибыль предприятия р.
Период реализации проекта дней
Капиталовложения в проект р.
Из таблицы 8.4 видно что предлагаемые в проекте решения являются экономически обоснованными и их внедрение приведёт к значительным улучшениям в имеющемся технологическом процессе производства нитроаммофоски. В результате внедрения проекта будет увеличена производительность технологического процесса на 5% при том же расходе исходного сырья.
Период реализации проекта составит 96 дней. Срок окупаемости проекта составляет 0 6 года.
Выполнен расчет теплового элемента который позволит эффективно производить процесс выпаривания что скажется на производительности данного аппарата а так же конструкционный расчет для определения создаваемых нагрузок на выпарной аппарат.
В проекте представлен расчет ситчатой тарелки что позволит унифицировать абсорбционную колонну; использовать его на разной мощности. Использование данного абсорбера позволяет увеличить производительность. Также произведен расчет конструкции колонны.
Данные предложения по реконструкции линии выпаривания приведут к значительному улучшению в имеющемся технологическом процессе производства нитроаммофоски. В результате внедрения проекта будет увеличена производительность технологического процесса на 5%.
СПИСОК ИСПОЛЬЗУЕМЫХ ИСТОЧНИКОВ
Автоматические приборы регуляторы и управляющие системы: Справочное пособие Под ред. Б.Д. Кошарского. – Изд.3-е перераб. И доп. – Л.: Машиностроение Ленинг. отд-ние 1983-464с. ил.
Анурьев В.И. Справочник конструктора машиностроителя: В 3т. – М.: Машиностроение 1982 1999.
Байтон Р.С. Химия и технология извести [Текст]: Сокр.пер.с англ. М. Стройиздат 1972. 239с
Бекин Н.Г. Оборудование заводов химической промышленности [Текст]: Н.Г. Бекин И.П. Шакин– М.: Химия 1978. – 326 с.
Варгафтик Н.Б. Справочник по теплофизическим свойствам газов и жидкостей [Текст]: – М.:Физматиз. 1963. – 708с.
Вольберг Н.Е. Ряполов А.Ф. Монтаж химического оборудования общего назначения[Текст]: Вып. 1. Стройиздат 1971.
Гавриленков А. М. Основы санитарной техники [Текст]: методические указания к выполнению контрольной работы по курсу « Основы стройдела и сантехники» А. М. Гавриленко и др.: ВГТА. – Воронеж 2000
Гайдмак К.М. Тыркин Б.А. Монтаж оборудования предприятий химических производств [Текст]: учеб. для сред. проф. тех. Училищ – 3-е изд. перераб. и доп. – М.: Высш. шк. 1983. – 271с.
Гладких П. А. Борьба с шумом и вибрацией в машиностроении [Текст]: П. А. Гладких. – М.: Машиностроение 1966
ГОСТ 12.1.005-88 ССБТ. Общие санитарно-гигиенические требования к воздуху рабочей зоны.
ГОСТ 12.1.030-88 ССБТ. Электробезопасноть. Защитное заземление. зануление.
ГОСТ 12.2.070-75 ССБТ. Изделия электротехнические. Общие трбования безопасности.
Грузинов Е.В. Рябиков Б.А. Толгеев Т.М. Монтаж технологического оборудования химических заводов[Текст] Госстройиздат. М – 1963.
Дмитриев В.Г. Теория ленточных конвейеров. М.: Наука 1982с.
Долин П. А. Справочник по технике безопасности [Текст]: П. А. Долин.-М.: Энергоатомиздат 1985
Домашенев А.Д. Конструирование и расчет химических аппаратов. (Учебник для вузов по специальности «Машины и аппараты химических производств»). М.: Машгиз 1961.
Ермаков В.И. Технология ремонта химического оборудования [Текст]: В.И. Ермаков В.С. Шеин – Л.: Машиностроение. Ленингр. отд-ние. 1977. – 280 с.
Ермаков В.И. Шеин В.С. Ремонт и монтаж химического оборудования [Текст]:: Учебное пособие для вузов. – Л.: Химия 1981. – 368 с. ил.
Классен П.В. Гришаев И.Г. Шомин Н.Г. Гранулирование. – М.: Химия 1991. – 240с.: ил.
Криворот А.С. Конструкция и основы проектирования машин и аппаратов химической промышленности [Текст]: Учебное пособие для техникумов. М. «Машиностроение» 1976.
Лащинский А.А. Конструирование сварных аппаратов М. «Машиностроение» 1979.
Лащинский А. А. и Толчинский А. Р. Основы конструирования и расчета химической аппаратуры [Текст]:Справочник. Под ред. инж. Н.Н. Логинова. Изд. 2-е переработ и доп. Л. «Машиностроение» 1970.
Методические указания к оформлению расчетно-проектных работ расчетно-графических работ курсовых и дипломных проектов [Текст]. Ю.Н. Шаповалов В. Г. Савенков Е. В. Вьюшина – Воронеж: Воронеж. гос. технол. акад. 2003. -59с.
Машины и аппараты химических производств [Текст]. Под ред. И. И. Чернобыльского – М.: Машиностроение – 1975.-459с.
Машины и аппараты химических производств [Текст]: примеры и задачи под ред. В. Н. Соколова Л.: Машиностроение 1982.-384с.
Методические указания к дипломному проекту [Текст]. Ю. Н. Шаповалов Воронеж: Воронеж. гос. технол. акад. 2001. -28с.
Основные процессы и аппараты химической технологии: пособие по проектированию. Г. С. Борисов В. П. Быков Ю.И. Дытнерский. Под ред. Ю.И. Дытнерского. 2-е изд. М.: Химия 1991.-496с.
Осипов П. И. Безопасность жизнидеятельности в производственной сфере. Охрана труда [Текст]. Учебное пособие – Воронеж: Изд ВГУ 1992.-320с.
Павлов К. Ф. Примеры и задачи по курсу процессов и аппаратов химической технологии [Текст]: Учебное пособие для вузов К. В. Палов П. Г. Романков А. А. Носков; под общ. ред. П. Г. Романкова -10-е изд. перераб. и доп. –Л.: Химия 1987. -576с.
Плановский А. Н. Процессы и аппараты химической технологии [Текст]: -М.: Химия 1967 -847с.
Позин Б. Д. Новые исследования по технологии минеральных удобрений [Текст]: Учебник для вузов -6-е изд. –Л.: Химия 1989.-352с.
Предельно-допустимые концентрации химических веществ в окружающей среде [Текст]: справочник –Л.: Химия 1985.-528с.
примеры и задачи по курсу оборудования заводов химической промышленности [Текст]: под общ. ред. Козулина –М.: Химия 1979-253с.
Руководство к выполнению курсового раздела дипломного проекта по автоматизации [Текст]: Учебное пособие В. К. Битюков – Воронеж: Воронеж. гос. технол. акад. 2001. -70с.
Технология фосфорных и комплексных удобрений [Текст]: Под. ред С.Д. Эвенчика А. А. Бродского М.: Химия 1987. -464с.
Технология химического аппаратостроения [Текст]: Поплавский Ю. В. – М.: Машгиз 1961 -354с.
Уманский Э. С. Сопротивление материалов [Текст]: К.: Высшая школа 1979.-254с.
Федоров П. П. Пожаро- и взрывобезопасность веществ и материалов применяемых в химической промышленности [Текст]: справочник под ред. И. В. Рядова – М.: Химия 1970.-358с.
Яхонтова Е. Л. Кислотные методы переработки фосфатного сырья [Текст]: Е. Я. Яхонтова. И. А. Петропавловский В. Ф. Камышев и др. –М.: Химия 1988. -288с.
ГОСТ 12.2.070-75 ССБТ. Изделия электротехнические. Общие трбования безопасности
автоматизация.doc
Одним из факторов повышения производительности труда эффективности общественного производства ускорения научно-технического прогресса является автоматизация технологических процессов в пищевой и химической промышленности.
Автоматизация предполагает передачу приборам и автоматическим устройствам функций управления и контроля выполняемых человеком. Улучшение качества выпускаемой продукции повышение производительности и безопасности использования всех сырьевых ресурсов – главные цели автоматизации.
В настоящее время существует начальная комплексная и полная автоматизация. Начальная автоматизация представляет собой автоматизацию каждого технологического процесса в пределах цеха или участка отдельно независимо от других процессов. Такая автоматизация уходит в прошлое. При комплексной автоматизации все технологические процессы в пределах участка автоматизируются как одно целое. Это наиболее распространенный тип автоматизации в промышленности в настоящее время. Полная автоматизация предполагает работу производства как единой автоматически работающей системы. В наше время уже существуют заводы-автоматы где процесс выработки продукции от начала до конца производят различные машины и механизмы.
В автоматических системах управления человек только следит за состоянием средств автоматизации но не предпринимает непосредственного участия в процессе управления. Наряду с такими системами существуют и применяются автоматизированные системы управления. В таких системах человек активно участвует в самом процессе управления. Таким образом автоматизированные системы управления являются человеко-машинными системами которые преимущественно используют электронно-вычислительные машины (ЭВМ) в качестве технической базы.
Упарка раствора аммиачной селитры до концентрации 89-93% хранение раствора и перекачка его на окончательное упаривание и гранулирование в производство аммиачной селитры (агрегат АС-72).
Выпаривание раствора аммиачной селитры требует строгого соблюдения технологических параметров процесса т.е. отклонение от них повышение температуры более 150°С и понижения рН менее 5 может привести к взрыву концентрированного раствора аммиачной селитры. Поэтому принятые технологические параметры схема и аппаратурное оформление процесса направлены на соблюдение условий безопасного ведения процесса упарки.
Раствор амселитры очищенной на фильтрах тонкой очистки направляется в сборник N-DC-443 для корректировки рН раствора селитры с доведением его до значения рН-7. Корректировка ведется азотной кислотой с помощью рН метра рН1СА-442. Раствор амселитры с откорректированным рН концентрацией 55н-60% NH4NO3 из сосуда N-FA-443 поступает в сборник N-FA-444 откуда насосами N-GA-445 (АВ) через подогреватель N-EA 461 подается на упарку.
Сборник N-FA-444 обеспечивает запас хранения (при часовом расходе амселитры 55 м3ч на четыре часа).
Раствор поступает в две параллельно работающие выпарные установки состоящие из греющих камер N-EA-463 (АВ) и сепараторов N-EA-462 (АВ).
Раствор из подогревателя с температурой 90-100°С поступает в греющую камеру где нагревается до Т=121 С.
В качестве теплоносителя используется пар давлением 8-12 кгссм2. Конденсат пара из греющей камеры пройдя конденсационный горшок M-FA-464 направляется в сборник Q-FA-702. Пар самоиспарения из конденсационного горшка отводится в греющий пар и используется при выпарке.
Подогретый раствор аммиачной селитры из греющей камеры N-EA-463 поступает в выпарной аппарат N-FA-462.
В процессе работы осуществляется естественная циркуляция раствора по контуру: греющая камера – выпарной аппарат – греющая камера (ЕА 463-FA-462 - ЕА-463).
В результате кипения раствора амселитры в выпарном аппарате N-FA-462 при температуре 121°С (TRCA 462 (АВ)) и вакууме 300-500 мм рт.ст. (PICA-470) на одной системе испаряется около 121 т воды в час.
Слив 89-93% плава аммиачной селитры в количестве 45 тч - товарная часть осуществляется насосами N-GA-465 (АВС) в емкость для хранения 89-93% раствора N-FA-480. Количество раствора амселитры поступающего в емкость M-FA-480 регулируется клапанами LICA-462 (АВ).
Предусмотрен также вывод части амселитры на нейтрализацию в сборник N-FA-042. Установлено две емкости для хранения 89-93% раствора амселитры по 318 м3 каждая емкость оборудована змеевиками для поддержания температуры плава в пределах 121°С (прибор TICAP-480 АВ). Для обогрева этих емкостей используется пар низкого давления (8-10 кгссм2) конденсат этого пара направлен через расширительный сосуд Q-FA-702 в емкость парового конденсата Q-FA-703(A3).
Плав амселитры из сборника N-FA-480 (АВ) насосами N-GA-481 (АВ) откачивается потребителями:
в цех аммиачной селитры (АС-72) для дальнейшего упаривания и получения гранулированного удобрения;
часть для внутрицехового использования на узел нейтрализации в сборник N-FA-042.
Для поддержания при упарке заданного рН=6 плава предусмотрена подача в выпарной аппарат газообразного аммиака для компенсации его потерь при упарке.
Перед подачей аммиака он предварительно нагревается в нагревателе N-EA-460 до 150 С (прибор TIC-460).
Пары воды содержащие аммиак и брызги амселитры из сепараторов выпарных аппаратов N-FA-462 (АВ) отсасываются системой вакуума создаваемого паровым эжектором N-EE-473. Система вакуума состоит (по ходу парогазовой смеси из выпарных аппаратов N-FA-462 (АВ)) влагоуловителя N-DA-466 поверхностного горизонтального конденсатора N-EA-470 парового эжектора N-EE-473 - струйного конденсатора N-EA-474 к этому эжектору.
Для создания герметичности системы установлены два гидрозатвора:
гидрозатвор N-FA-467 с насосами N-GA-468 (АВ) к влагоуловителю N-DA-466;
гидрозатвор N-FA-471 с насосами N-GA-472 (АВ) к поверхностному конденсатору N ЕА-470 к эжектору N-EE-473 конденсатору N-EA 474.
Во влагоуловителе N-DA-466 происходит отделение брызг амселитры из паровоздушной смеси путем орошения раствором амселитры 55+60% исходной конденсации принятой из резервуара N-FA-444 и поданной насосом N-GA-445 (АВ) в гидрозатвор N-FA-467 (по прибору FIC-467). Раствор амселитры циркулирует поконтуру: гидрозатвор N-FA-467 - насосы N-GA-468 (АВ) - влагоуловитель N-DA-466 - гидрозатвор N-FA-467.
После отделения брызг амселитры во влагоуловителе N-DA-466 парогазовая смесь поступает на конденсацию (выделение паров воды из нее) в конденсатор N-EA-470. Конденсация ведется охлажденной водой предварительно используемой в теплообменниках N-EA-412 и N-ЕА-4121 с подпиткой "свежей" охлаждающей воды. Полученный конденсат стекает по барометрической трубе в гидрозатвор N-FA-471 а несконденсированная отсасывается пароэжекторным насосом N-EE-473 и подается вместе с ("рабочим" паром в конденсатор N-EA-474 из которого образовавшийся конденсат также поступает по барометрической трубе в гидрозатвор N-FA-471).
Раствор аммиачной селитры из гидрозатвора N-FA-467 подается в резервуар N-FA-444.А конденсат содержащий аммиак неуловленный во влагоуловителе N-DA-466 из гидрозатвора N-FA 471 и из цикла выводится по уровню (прибор LICA-471); насосом N-GA-472 (АВ) в колонну E-DA-501 через подогреватель конденсата Е-ЕА-500 на отгонку аммиака. Газовая смесь также содержит аммиак из струнного конденсата N-FA-474 и через воздушник от гидрозатворов N-FA-467 471 отсасывается в скруббер-нейтрализатор E-DA-600.
Для промывки выпарного контура к нему подведен паровой конденсат (технологическая вода).
Выпарные аппараты N-FA 462 АВ и кипятильники N-EA 463 в процессе работы покрываются осадком карбоната кальция и других солей что снижает интенсивность процесса выпарки. Для удаления образовавшегося осадка 1 раз в месяц выполняют промывку аппаратуры подкисленным азотной кислотой конденсатом для чего:
останавливают установку дренируют систему;
снижают давление греющего пара до 01-02 МПа с помощью клапана TICA 462 АВ;
заполняют систему паровым конденсатом;
открывают подачу азотной кислоты и закисляют паровой конденсат до рН 05-10;
подачу азотной кислоты повторяют до тех пор пока не прекращается возрастание рН;
после очистки выпарного аппарата кислый конденсат циркуляционного контура нейтрализуют подачей газообразного аммиака.
В случае сильной забивки кипятильника N-EA 463 производит его очистку с помощью насоса высокого давления. Вода после промывки выводится из контура в сборник N-FA-444.
Для промывки кипятильника выпарного аппарата N-Fa 463 от осадков содержащих соли и окислы кремния применяется раствор каустической соды (NaOH).
Раствор каустической воды с массовой долей сухого натра 8+10% готовится в емкости для раствора каустической соды no3.FA463-l.
Выбор параметров контроля и управления процессом
Перечень контролируемых и регулируемых параметров
Параметры подлежащие контролю регулированию и сигнализации
Пределы отклонения параметров
Оптимальные значения параметров
Допустимая погрешность контроля
Условия эксплуатации прибора
Особые требования заказчика
Количество однотипных точек контроля
Возможные с учетом аварийных ситуаций
Допустимые по технологии
Температура раствора аммиачной селитры на выходе из подогревателя ЕА461 °С
Температура раствора аммиачной селитры на выходе из кипятильника ЕА463 °С
Температура раствора аммиачной селитры на выходе из выпарного аппарата FА462 °С
Температура раствора аммиачной селитры в гидрозатворе FА467 °С
Температура конденсата в гидрозатворе FА471 °С
Давление пара на входе греющей камеры ЕА463 Па
Разрежение в выпарном аппарате аммиачной селитры FА462 мм рт. ст.
Давление во влагоуловителе DA466 Па
Расход раствора аммиачной селитры в кипятильник ЕА463 кгч
Расход раствора аммиачной селитры на входе в гидрозатвор FA467 тч
Расход раствора аммиачной селитры после насоса тч
Уровень раствора аммиачной селитры в выпарном аппарате FA462 %
Уровень раствора аммиачной селитры в гидрозатворе FA467 %
Уровень технологического конденсата в гидрозатворе FA471 %
Влажность влажности высушенного продукта на выходе из барабанной сушилки %
ОПИСАНИЕ ФУНКЦИОНАЛЬНОЙ СХЕМЫ АВТОМАТИЗАЦИИ
Контроль и регулирование температуры раствора аммиачной селитры на выходе из подогревателя ЕА 461 осуществляется следующим образом. В качестве датчика используется термопреобразователь сопротивления дТС 015-50М.В3.80 (1а) сигнал с которого поступает на микропроцессорный вторичный прибор ТРМ210 (1б) показывающий текущее значение температуры и реализующий ПИД-закон регулирования. С него управляющий сигнал поступает на автоматический запорно-регулирующий односедельный клапан КЗР (1в) установленный на линии подачи пара.
Контроль температуры раствора аммиачной селитры на выходе из кипятильника ЕА463 осуществляется следующим образом. В качестве датчика используется термопреобразователь сопротивления дТС 015-50М.В3.80 (2а) сигнал с которого поступает на микропроцессорный вторичный прибор ТРМ210 (2б) расположенный на щите и показывающий текущее значение температуры. Осуществляется сигнализация завышения максимально допустимого значения температуры спомощью индикатора расположенного на лицевой панели вторичного прибора ТРМ210.
Контроль и регулирование температуры раствора аммиачной селитры на выходе из выпарного аппарата FА462 осуществляется следующим образом. В качестве датчика используется термопреобразователь сопротивления дТС 015-50М.В3.80 (3а) сигнал с которого поступает на микропроцессорный вторичный прибор ТРМ210 (3б) показывающий текущее значение температуры и реализующий ПИД-закон регулирования. С него управляющий сигнал поступает на автоматический запорно-регулирующий односедельный клапан КЗР (3в) установленный на линии подачи пара. В случае завышения текущим значением температуры максимально допустимого со вторичного прибора ТРМ210 (3б) поступает сигнал на отсечной клапан КМ (3г) открывающий доступ в аппарат FА462 технической воды.
Контроль температуры раствора аммиачной селитры в гидрозатворе FА467 (контур 4) и температуры конденсата в гидрозатворе FА471 (контур 5) осуществляется аналогично контуру 2.
Контроль давления пара на входе греющей камеры ЕА463 осуществляется следующим образом. В качестве датчика используется преобразователь для измерения давления Сапфир-22ДА (6а) унифицированный электрический сигнал с которого поступает на микропроцессорный вторичный прибор ТРМ210 (6б) показывающий текущее значение давления.
Контроль разрежения в выпарном аппарате аммиачной селитры FА 462 осуществляется следующим образом. В качестве датчика используется преобразователь для измерения давления Сапфир-22ДВ (7а) унифицированный электрический сигнал с которого поступает на микропроцессорный вторичный прибор ТРМ210 (7б) показывающий текущее значение разрежения.
Контроль давления во влагоуловителе DA466 (контур 8) осуществляется аналогично контуру 6.
Контроль и регулирование расхода раствора аммиачной селитры в кипятильник ЕА463 осуществляется следующим образом. В качестве датчика используется диафрагма камерная ДК-100-06 (9а) создающая перепад давления измеряемый спомощью дифференциального манометра Сапфир-22ДД 2410 (9б) унифицированный электрический сигнал с которого поступает на микропроцессорный вторичный прибор ТРМ210 (9в) показывающий текущее значение расхода и реализующий ПИД-закон регулирования. С него управляющий сигнал поступает на автоматический запорно-регулирующий односедельный клапан КЗР(9г) расположенный на линии подачи раствора аммиачной селитры.
Контроль и регулирование расхода раствора аммиачной селитры на входе в гидрозатвор FA467 осуществляется следующим образом. В качестве датчика используется диафрагма камерная ДК-100-06 (10а) создающая перепад давления измеряемый спомощью дифференциального манометра Сапфир-22ДД 2410 (10б) унифицированный электрический сигнал с которого поступает на микропроцессорный вторичный прибор ТРМ210 (10в) показывающий текущее значение расхода и реализующий ПИД-закон регулирования. С него управляющий сигнал поступает на автоматический запорно-регулирующий односедельный клапан КЗР(10г) расположенный на линии подачи раствора аммиачной селитры.
Контроль расхода раствора аммиачной селитры после насоса осуществляется следующим образом. В качестве датчика используется диафрагма камерная ДК-100-06 (11а) создающая перепад давления измеряемый спомощью дифференциального манометра Сапфир-22ДД 2410 (11б) унифицированный электрический сигнал с которого поступает на микропроцессорный вторичный прибор расходомер РМ1 (11в) показывающий текущее и суммарное значение расхода.
Контроль и регулирование уровня раствора аммиачной селитры в выпарном аппарате FA462 осуществляется следующим образом. В качестве датчика используется кондуктометрический датчик уровня жидкости ДС.К-195 (12а) сигнал с которого поступает на микропроцессорный вторичный прибор ТРМ210 (12б) показывающий текущее значение уровня и реализующий ПИД-закон регулирования. С него управляющий сигнал поступает на автоматический запорно-регулирующий односедельный клапан КЗР(12в). Осуществляется сигнализация завышения максимально допустимого и занижения минимально допустимого значения уровня спомощью индикаторов расположенных на лицевой панели вторичного прибора ТРМ210.
Контроль и регулирование уровня раствора аммиачной селитры в гидрозатворе FA467 (контур 13) и уровня технологического конденсата в гидрозатворе FA471 (контур 14) осуществляется аналогично контуру 12.
Электродвигатель М1 запускается в работу при помощи магнитного пускателя ПМЕ-17 (КМ1) который в свою очередь включается через переключатель УП5312 (SA1) с помощью кнопок одна из которых установлена на щите КЕ-014 (SB1) а вторая по месту КЕ-014 (SB2). В момент вращения двигателя загорается лампа РНЦ-53 (HL1). Аналогично осуществляется управление электродвигателями М2-М3.
ФСА.cdw

6 листов.dwg

Отвод безшовный DN25
ДП-02068108-280202-46-08-01.060.00
ДП-02068108-280202-46-08-01.000.00-ВО
м 2. Температура - 121 Г 3. Давление - 0.1 МПа 4. Среда нейтральная
Технические характеристики
Ввод аммиачной селитры
Подача технической воды
*Размеры для справок 2 Сварочные швы по ГОСТ 5264-80; N°1-Т4 3 N°2-С2 N°3-У4 3 варить электродом Э42 ГОСТ 9467-75 3 ±t2
*Размеры для справок 2 Сварочные швы по ГОСТ 5264-80; N°1-Т4 3 варить электродом Э42 ГОСТ 9467-75 3 ±t2
Крышка эллиптическая
Тройник безшовный DN25
ДП-02068108-280202-46-08-01.030.00
*Размеры для справок 2 Сварочные швы по ГОСТ 5264-80; N°1-Н2 3 N°2-У4 3 варить электродом Э42 ГОСТ 9467-75 3 ±t2
ДП-02068108-280202-46-08-02.000.00-ВО
для фунд. болтов М30
*Размеры для справок 2 Сварочные швы по ГОСТ 5264-80; N°1-C2 3 N°2-У4 3 варить электродом Э42 ГОСТ 9467-75 3 ±t2
ДП-02068108-280202-46-08-02.020.00
ДП-02068108-280202-46-08-02.030.00
ДП-02068108-280202-46-08-02.021.00
Отвод безшовный DN40
Переход конический DN80
Тройник безшовный DN40
Тройник безшовный DN80
*Размеры для справок 2 Сварочные швы по ГОСТ 5264-80; N°1-Т4 3 N°2-С2 3 варить электродом Э42 ГОСТ 9467-75 3 ±t2
*Размеры для справок 2 Сварочные швы по ГОСТ 5264-80; N°1-Н2 3 N°2-У4 3 N°3-T2 3 варить электродом Э42 ГОСТ 9467-75 3 ±t2
ДП-02068108-280202-46-08-01.060.01
ДП-02068108-280202-46-08-01.050.01
ДП-02068108-280202-46-08-01.050.02
ДП-02068108-280202-46-08-01.050.03
ДП-02068108-280202-46-08-01.050.00
Б-ПН-20 ГОСТ 19903-74
Б-ПН-30 ГОСТ 19903-74
Выход паро-газовой смеси
Орошние аммиачной селитрой
Подача паро-газовой смеси
Выход аммиачной селитры
*Размеры для справок 2 ±t2
Технические характеристики q*; 1.Объем аппарата 43
м 2.Темпертура 60° 3.Давление 0.1 МПа 4.Среда нейтральная
План Без сечения.dwg

ДП-02068108-280202-46-08-01.000.00-ВО
ОАО"Минудобрения". Цех NPK-2
Гидрозатвор абсорбера
Гидрозатвор конденсатора
Струйный конденсатор
Регенерационный насос
Экспликаця оборудования
Участок выпаривания аммиачной селитры
6 листов Откат.dwg

Отвод безшовный DN25
ДП-02068108-280202-46-08-01.060.00
ДП-02068108-280202-46-08-01.000.00-ВО
м 2. Температура - 121 Г 3. Давление - 0.1 МПа 4. Среда нейтральная
Технические характеристики
Ввод аммиачной селитры
Подача технической воды
*Размеры для справок 2 Сварочные швы по ГОСТ 5264-80; N°1-Т4 3 N°2-С2 3 N°3-У4 3 варить электродом Э42 ГОСТ 9467-75 3 ±t2
*Размеры для справок 2 Сварочные швы по ГОСТ 5264-80; N°1-Т4 3 варить электродом Э42 ГОСТ 9467-75 3 ±t2
Крышка эллиптическая
Тройник безшовный DN25
ДП-02068108-280202-46-08-01.030.00
*Размеры для справок 2 Сварочные швы по ГОСТ 5264-80; N°1-Н2 3 N°2-У4 3 варить электродом Э42 ГОСТ 9467-75 3 ±t2
ДП-02068108-280202-46-08-02.000.00-ВО
для фунд. болтов М30
*Размеры для справок 2 Сварочные швы по ГОСТ 5264-80; N°1-C2 3 N°2-У4 3 варить электродом Э42 ГОСТ 9467-75 3 ±t2
ДП-02068108-280202-46-08-02.020.00
ДП-02068108-280202-46-08-02.030.00
ДП-02068108-280202-46-08-02.021.00
Отвод безшовный DN40
Переход конический DN80
Тройник безшовный DN40
Тройник безшовный DN80
*Размеры для справок 2 Сварочные швы по ГОСТ 5264-80; N°1-Т4 3 N°2-С2 3 варить электродом Э42 ГОСТ 9467-75 3 ±t2
*Размеры для справок 2 Сварочные швы по ГОСТ 5264-80; N°1-Н2 3 N°2-У4 3 N°3-T2 3 варить электродом Э42 ГОСТ 9467-75 3 ±t2
ДП-02068108-280202-46-08-01.060.01
ДП-02068108-280202-46-08-01.050.01
ДП-02068108-280202-46-08-01.050.02
ДП-02068108-280202-46-08-01.050.03
ДП-02068108-280202-46-08-01.050.00
Б-ПН-20 ГОСТ 19903-74
Труба 720х10 ГОСТ 3262-75
Б-ПН-30 ГОСТ 19903-74
*Размеры для справок
ФСА_511.cdw

Шаблон.dwg

Отвод безшовный DN25
Штуцер регенеративный
Цилиндр перфорированный
ДП-02068108-280202-46-08-01.060.00
ДП-02068108-280202-46-08-01.000.00-ВО
м 2. Температура - 121 Г 3. Давление - 0.1 МПа 4. Среда нейтральная
Технические характеристики
Ввод аммиачной селитры
Подача технической воды
ДП-02068108-280202-21-08-01.024.00-ВО
*Размеры для справок 2 Сварочные швы по ГОСТ 5264-80; N°1-Т4 3 варить электродом Э42 ГОСТ 9467-75 3 ±t2
ДП-02068108-280202-21-08-01.022.00-ВО
ДП-02068108-280202-21-08-01.024.00
ДП-02068108-280202-21-08-01.022.00
ДП-02068108-280202-21-08-01.000.00
Диапазон рабочей температуры
+18 - +25 Средний уровень жидкости
60х3615х3615аппарата
Техническая характеристика
*Размеры для справок 2 Сварочные швы по ГОСТ 5264-80; N°1-Т3 3 варить электродом Э42 ГОСТ 9467-75 3 ±t2
Вход потока на очистку
Выход потока в атмосферу
Вход озоно-воздушной смеси
*Размеры для справок 2 Сварочные швы по ГОСТ 5264-80; N°1-Т4 3 N°2-С2 3 N°3-У4 3 варить электродом Э42 ГОСТ 9467-75 3 ±t2
Крышка эллиптическая
Тройник безшовный DN25
ДП-02068108-280202-46-08-01.030.00
*Размеры для справок 2 Сварочные швы по ГОСТ 5264-80; N°1-Н2 3 N°2-У4 3 варить электродом Э42 ГОСТ 9467-75 3 ±t2
ДП-02068108-280202-46-08-01.050.00
ДП-02068108-280202-46-08-02.000.00-ВО
для фунд. болтов М30
*Размеры для справок 2 Сварочные швы по ГОСТ 5264-80; N°1-C2 3 N°2-У4 3 варить электродом Э42 ГОСТ 9467-75 3 ±t2
ДП-02068108-280202-46-08-02.020.00
ДП-02068108-280202-46-08-02.021.00
Отвод безшовный DN40
Переход конический DN80
Тройник безшовный DN40
Тройник безшовный DN80
*Размеры для справок 2 Сварочные швы по ГОСТ 5264-80; N°1-Т4 3 N°2-С2 3 варить электродом Э42 ГОСТ 9467-75 3 ±t2
Кип.dwg

Обозначение материальных потоков
Штуцер регенеративный
Цилиндр перфорированный
ДП-02068108-280202-21-08-01.000.00-ВО
Из сборника аммиачной селитры
В сборник аммиачной селитры
воздух под давлением
Обозначение оборудования
Гидрозатвор абсорбера
Гидрозатвор конденсатора
Струйный конденсатор
Регенерационный насос
Аммиако-воздушная смесь
Пар водяной насыщенный
План для диплома.dwg

ФСА_автокад.dwg

Рекомендуемые чертежи
- 14.06.2023
Свободное скачивание на сегодня
Другие проекты
- 22.08.2014