Регулировка для токарного станка с ЧПУ




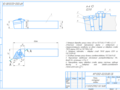
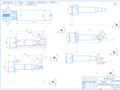
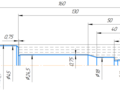
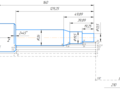
- Добавлен: 25.01.2023
- Размер: 197 KB
- Закачек: 0
Описание
Состав проекта
![]() |
![]() ![]() ![]() ![]() |
![]() ![]() ![]() ![]() |
![]() ![]() ![]() ![]() |
![]() ![]() ![]() |
![]() ![]() |
![]() ![]() ![]() |
![]() ![]() ![]() |
![]() ![]() ![]() |
![]() ![]() ![]() ![]() |
![]() ![]() ![]() ![]() |
![]() ![]() ![]() ![]() |
![]() ![]() ![]() |
![]() ![]() ![]() ![]() |
Дополнительная информация
per5.frw

zony2.frw

list2_1.cdw

per1.frw

per2.frw

per3.frw

per4.frw

zony2_1.frw

list3.cdw

Материал державки резца сталь 40Х по ГОСТ4543-71 HRCэ 42 47.
Пластина сменная трёхгранной формы с отверстием и
стружколомающими канавками на одной стороне из твёрдого сплава
Т5К10 формы 0359 по ГОСТ19042-80.
Материал подкладки - твёрдый сплав Т5К10 форма 0359 по
Основные размеры резца должны соответствовать ГОСТ26611-82.
Неуказанные предельные отклонения размеров:отверстий H14
Маркировать марку твёрдого сплава
товарный знак завода-изготовителя
per1_2.frw

Записка.doc
2. Выбор технологического оборудования5
3. Определение числа переходов6
Расчет координат опорных точек9
Назначение режимов резания17
Список используемой литературы21
Развитие автоматизации производства в серийном мелкосерийном и индивидуальном производствах базируется на применении станков оснащенных системами числового программного управления (ЧПУ).
Эффективность станков с программным управлением объясняется высокой их производительностью; повышением производительности труда обслуживающего персонала; сокращением потребности в специальной технологической оснастке; уменьшением оборотных средств вкладываемых в незавершенное производство; высвобождением значительной части производственных площадей.
Внедрение станков с ЧПУ для автоматизации технологических процессов механической обработки позволяет обрабатывать с меньшими затратами детали такой же широкой номенклатуры как и на универсальных станках соответствующих типов.
Имеющейся опыт применения оборудования с ЧПУ показывает что наибольший эффект достигается при объединении его в большие участки обслуживаемые группой технологов и программистов. В этих условиях срок окупаемости оборудования не превышает пяти лет что вполне приемлемо при его сравнительно высокой стоимости.
Именно указанными тенденциями обусловлена тема данной курсовой работы. В ходе ее выполнения необходимо разработать управляющую программу для станка с ЧПУ на одну операцию.
Обоснование последовательности переходов
В качестве заготовки выбирают в зависимости от диаметра детали
(45 мм) и отношения длины детали к диаметру (LD4) в соответствии с рекомендациями ( [1] табл. 16.4 стр. 584). Принимаем диаметр заготовки D0=48 мм.
Допуск на диаметр заготовки устанавливаем по ГОСТ 2590-71. Для D0=48 мм при прокатке обычной точности es=04 мм; ei=-07 мм. Качество поверхности сортового проката обычной точности Rz=160 мкм (Ra 40).
Заготовка принимается отрезанной с обработанными торцами и зацентрованная. Длина заготовки L=160 мм c допуском по h14. Центровочные отверстия А25 по ГОСТ 14034-74.
Рис 1.1 Эскиз заготовки
2. Выбор технологического оборудования
Изготовление детали осуществляется на токарно-винторезном станке модели 16К20Ф3С5. Характеристики указанного станка приведены в
Характеристики технологического оборудования
Наибольший диаметр обрабатываемой заготовки мм:
Наибольшая длина обрабатываемой заготовки мм
Высота расположения центров мм
Наибольший диаметр прутка мм
Шаг нарезаемой резьбы:
дюймовой число ниток на один дюйм
Диаметр отверстия шпинделя мм
Внутренний конус шпинделя
Частота вращения шпинделя мин-1
Конус отверстия пиноли
Диаметр патрона (ГОСТ 2675-80) мм
Мощность электродвигателя кВт
Габаритные размеры станка мм:
Устройство числового программного управления
Устройство преднабора и цифровой индикации
Число управляемых координат
Дискретность задания размеров (мм) по оси
Дискретность цифровой индикации мм
Постоянства диаметра образца (мкм) в сечении:
Отклонение от плоскостности торцевой поверхности образца мкм
3. Определение числа переходов
При проектировании переходов обрабатываемая область ограниченная контурами детали и заготовки разделяется на отдельные зоны в зависимости от требований к чистоте и точности поверхностей детали режущего инструмента и способа крепления заготовки на станке.
Каждая зона ограничивается замкнутым контуром состоящим из основного и вспомогательного участков. Основным считается тот контур зоны который является границей траектории инструмента при обработке.
Все многообразие зон может быть представлено зонами выборки объемов металла и зонами контурной обработки детали. Зоны выборки служат для многопроходной обработки при больших съемах припуска. Они делятся на открытые полуоткрытые и закрытые. Основной участок контура открытой выборки ограничивает ее с одной стороны полуоткрытой – с двух а закрытой – с трех сторон.
Контурные зоны состоят из припуска на получистовую или чистовую обработку поверхностей и служат для прохода инструмента эквидистантно к участкам контура детали.
На рис 1.2. приведена схема разделения снимаемого припуска на зоны обработки участков заготовки.
На основании рис 1.2. составляем план обработки по переходам на токарной операции (таблица 1.2.). Характеристики применяемых резцов приводим в таблице 1.3.
План обработки по переходам
Диаметр обработки мм
Резец проходной правый CTLBR2525M22 по ГОСТ 26176-85
Чистовое точение контура
Резец контурный правый 2101-0637 по ГОСТ 20872-80
CTJCR2525M22 по ГОСТ 26176-85
Чистовая обработка фаски
Резец контурный левый 2101-0638 по ГОСТ 20872-80
CTJCL2525M22 по ГОСТ 26176-85
Характеристики режущих инструментов
Материал режущей пластины
Геометрические параметры лезвия
Расчет координат опорных точек
В соответствии с планом обработки произведем расчет координат опорных точек.
переход (черновое точение)
Координаты опорных точек первого перехода
Приращение координат
переход (чистовое точение)
Координаты опорных точек второго перехода
Рис 2.2 Схема перехода чистового точения контура.
переход (чистовое точение фаски)
Рис 2.3 Схема перехода чистового точения фаски.
Координаты опорных точек третьего перехода
переход (точение канавок)
Рис 2.4. Схема перехода точения канавок.
Координаты опорных точек четвертого перехода
-й переход (нарезание резьбы)
Рис 2.5. Схема перехода нарезания резьбы.
Координаты опорных точек пятого перехода
Назначение режимов резания
Выбор режимов резания состоит в определении для заданных условий обработки глубины резания числа проходов подачи скорости резания и мощности требуемой на резание.
Рентабельными называют такие режимы резания при которых получается наименьшая трудоемкость т.е. затрачивается наименьшее количество времени на изготовление изделии с учетом минимальной себестоимости его.
Рентабельность режима резания достигается правильным выбором конструкции инструмента геометрических параметров его рабочей части материала инструмента качественной заточкой и доводкой его правильной установкой и креплением инструмента и заготовки вполне исправным состоянием станка целесообразной конструкцией технологической оснастки.
Выбранный режим резания может быть уточнен в процессе работы с тем чтобы обеспечить наибольшую возможную производительность труда при наименьших затратах на обработку детали.
Для назначения режимов резания на рабочих чертежах подлежащего изготовлению изделия должны быть указаны требуемая точность размеров и формы и чистота поверхностей после обработки характеристики материала изделия т.е. его марка состояние и механические свойства. Нужны также сведения о состоянии поверхностного слоя заготовки.
Определение подачи проводим на основании следующей математической модели:
где - подача ммоб; t – глубина резания мм; Dз – диаметр заготовки мм; Dc – наибольший обрабатываемый на станке диаметр заготовки мм; СS – коэффициент пропорциональности ZS PS XS – показатели степени.
Результаты расчета подачи приведены в таблице 3.1
Результаты расчета подачи
Рассчитанное значение подачи умножаем на различные поправочные коэффициенты. Результаты расчета приводим в таблице 3.2.
Поправочные коэффициенты на величину подачи
Определение скорости резания проводим на основании следующей математической модели:
где - скорость резания ммин; t – глубина резания мм; s – подача ммоб; - коэффициенты.
Результаты расчета скорости резания приведены в таблице 3.3
Результаты расчета скорости резания.
Рассчитанное значение скорости резания умножаем на различные поправочные коэффициенты. Результаты расчета приводим в таблице 3.4.
Поправочные коэффициенты на величину скорости резания
При точении канавок принимаем значение скорости резания и подачи по рекомендациям [2] S= 01 ммоб =83 ммин.
Определяем силы резания используя математические модели приведенные в таблице 3.5.
Формулы для расчета сил резания при точении
t – глубина резания мм;
- поправочные коэффициенты зависящие от обрабатываемого материала;
– скорость резания в ммин;
и - показатели степени
Результаты расчета сил резания приведены в таблице 3.6
Результат расчета сил резания
Определяем мощность резания по формуле
Результаты расчета приведены в таблице 3.7.
Результаты расчета мощности резания
Окончательные результаты расчета режимов резания приведены в таблице 3.8
Результаты расчета режимов резания
Список используемой литературы
Обработка металлов резанием: Справочник технолога А.А. Панов В.В. Аникин Н.Г. Бойм и др.; Под общ. ред. А.А. Панова. – М.: Машиностроение. 1988. – 736 с.: ил.
Каштальян И. А. Клевзович В.И. Обработка на станках с числовым программным управлением: Справочное пособие. – Мн.: Выш. шк. 1989. – 271 с.: ил.
Фельдштейн Е.Э. Режущий инструмент и остнастка станков с ЧПУ: Справочное пособие. – Мн.: Выш. шк. 1988.-336с.: ил.
Общемашиностроительные нормативы режимов резания: Справочник: В 2-х т.: Т. 1 А.Д. Локтев И.Ф. Гущин В.А. Батеув и др. – М: Машиностроение 1991. – 640 с: ил.
Общемашиностроительные нормативы режимов резания: Справочник: В 2-х т.: Т. 2 А.Д. Локтев И.Ф. Гущин В.А. Батеув и др. – М: Машиностроение 1991. – 304 с: ил.
Программа на языке PEPS 2.
MAT C3 – задание материала заготовки
ppl fan10t – выбор постпроцессора
win z-10 x-30 z250 x30 – задание размеров графического окна
k1 p1 ts1 ts4 ts5 ts6 ts7 ts8 ts9 ts10 ts11 ts12 ts13 ts2 p4 ek
stk billet z160 d48.4 l200 – выбор заготовки
tai z70 x0 – задняя бабка
dta – визуализация задней бабки
tsb u – подвод задней бабки
p20= z210 x-70*2 – точка смены ин-та
from z210 x-70*2 - установка точки смены ин-та в точку p20
tool iso cbma090610 cclbr t7 z0 x0 1 – установление проходного резца
rap z161 x-70*2 – быстрый подвод ин-та
rap z161 x-21.25*2 – быстрый подвод ин-та
fed t0.527 f0.527 – установление подачи
sur 115.4 – установление скорости резания
got z30.75 x-21.25*2
got z28.25 x-23.25*2
got z30.75 x-18.25*2
got z30.75 x-23.25*2
got z30.75 x-15.25*2
got z112.418 x-12.25*2
got z140.75 x-9.25*2
got z140.75 x-9.75*2
got z120.11 x-9.75*2
got z140.75 x-6.75*2
got z140.75 x-12.25*2
goh – возврат в точку смены ин-та
inp '' w1 d1 – пауза в выполнении программы (в целях наглядности)
era – очистка экрана
dra k1 k2 – прорисовка контура детали
stk billet z160 d48.4 l200 – прорисовка контура заготовки
tai z70 x0 - установка задней бабаки
dta – прорисовка задней бабаки
tool iso tcma160210 ctlbr t7 z0 x0 1 – установка правого контурного резца
p21= z161 x-70*2 – точка быстрого подвода ин-та
rap p21 – быстрый подвод ин-та подвод
rap z161 x-3*2 – быстрый подвод ин-та подвод
fed t0.368 f0.368 – подача
sur 217 – скорость резания
goh – возврат ин-та в точку смены
era – очистка экрана
dra k1 k2 – прорисовка контура заготовки
stk billet z160 d48.4 l200 - прорисовка контура заготовки
tai z70 x0 - установка задней бабки
dta – прорисовка контура задней бабки
tool iso tcma160210 ctlbl t1 z0 x0 1 – установка левого контурного резца
fed t0.1 f0.1 - подача
sur 83 – скорость резания
goh – возврат в точку смена ин-та
dra k1 k2 – прорисовка контура заготовки
stk billet z160 d48.4 l200 - прорисовка контура заготовки
dta – прорисовка контура задней бабки
tool gro int 3 z0 x0 1 – установка канавочного резца
sur 83 – скорость резания
goh – возврат в точку смены
tool thr int r1.25 b60 z0 x0 4 – установка резьбового резца
rap p21 – быстрый подвод ин-та
rap z161 x-6*2 – быстрый подвод ин-та
fed t1.25 f1.0 - подача
thr 1 z160 z144 x-6*2 h1 d0.25 l1 b0 1 – нарезание резьбы
stop – остановка шпинделя.
Управляющая программа
N20 G50 X--140.0 Z210.0
N40 G00 X140.0 Z161.0
N80 G01 Z30.75 F0.527
N320 G00 X24.5 Z161.0
N380 G00 X--140.0 Z210.0
N400 G50 X--140.0 Z210.0
N420 G00 X140.0 Z161.0
N460 G01 X12.0 Z158.0 F0.368
N560 G00 X--140.0 Z210.0
N580 G50 X--140.0 Z210.0
N620 G00 X140.0 Z-1.0
N640 G01 X49.0 Z3.0 F0.1
N660 G00 X--140.0 Z210.0
N680 G50 X--140.0 Z210.0
N720 G00 X20.0 Z210.0
N830 G00 X--140.0 Z210.0
N850 G50 X--140.0 Z210.0
N870 G00 X140.0 Z161.0
N910 G76 X--12.0 Z144.0 I0.0 K1.0 D250 E1.0 A60
N920 G00 X--140.0 Z210.0
zagotovka.frw

Рекомендуемые чертежи
- 25.01.2023