Разработка ТП мех. обработки детали корпус насоса 0210.22.003-2




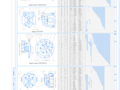
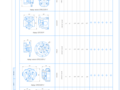
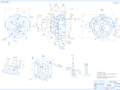
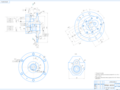
- Добавлен: 24.01.2023
- Размер: 1 MB
- Закачек: 1
Описание
Состав проекта
![]() |
![]() |
![]() |
![]() ![]() ![]() ![]() |
![]() |
![]() |
![]() ![]() ![]() ![]() |
![]() ![]() ![]() ![]() |
![]() |
![]() ![]() ![]() ![]() |
![]() |
![]() ![]() ![]() ![]() |
![]() |
![]() |
![]() ![]() ![]() ![]() |
![]() |
![]() |
![]() |
![]() ![]() ![]() ![]() |
![]() ![]() ![]() ![]() |
![]() |
![]() ![]() ![]() ![]() |
![]() ![]() ![]() ![]() |
![]() |
![]() |
![]() |
![]() ![]() ![]() ![]() |
![]() |
![]() ![]() ![]() ![]() |
![]() ![]() ![]() |
![]() |
![]() |
![]() ![]() ![]() ![]() |
![]() |
![]() ![]() ![]() |
Дополнительная информация
Карта экизов 010.frw

Карта экизов 015.frw

Карта экизов 020.frw

Карта экизов 025.frw

Размерный анализ.cdw

Информационная модель детали
Корпус насоса 0210.22.003-2
Корпус насоса 0390.22.001-5
Корпус 0390.35.001-5
Крышка 0390.35.002-5
1 лист.cdw

Неуказанные предельные отклонения размеров Н14
Маркировать обозначением детали шрифтом ПО-5
-СП.spw

3-х кулачковый патрон.cdw

Анализ детали.cdw

фрезерно-сверлильно-
-расточная программная
Эскиз и название детали
Анализ исходных данных деталей
Коэффициент точности
Корпус насоса 0390.22.001-5
Технологический маршрут обработки
радиально-сверлильная
Анализ гр.cdw

фрезерно-сверлильно-
-расточная программная
Анализ группы деталей
Эскиз и название детали
Анализ исходных данных деталей
Коэффициент точности
Корпус насоса 0210.22.003-2
Корпус насоса 0390.22.001-5
Корпус 0390.35.001-5
Крышка 0390.35.002-5
Технологический маршрут обработки
радиально-сверлильная
0251.35.011.cdw

Неуказанные предельные отклонения размеров Н14
Маркировать обозначением детали шрифтом ПО-5
0210.22.003-2.cdw

Неуказанные предельные отклонения размеров Н14
Маркировать обозначением детали шрифтом ПО-5
0390-35-002-5.CDW

0390-35-001-5.cdw

Неуказанные предельные отклонения размеров Н14
Маркировать обозначением детали шрифтом ПО-5
ГОСТ 2930-62 0390.35.001-5.
Записка изм.doc
Технология машиностроения развивалась с развитием крупной промышленности накапливая соответствующие методы и приемы для изготовления машин. В прошлом технология машиностроения получила наибольшее развитие в оружейных мастерских и заводах где изготавливалось оружие в больших количествах.
Так на Тульском оружейном заводе еще в 1761 г. впервые в мире было разработано и внедрено изготовление взаимозаменяемых деталей и их контроль с помощью калибров.
К технологии машиностроения относятся следующие области производства: технология литья технология обработки давлением технология сварки технология механической обработки технология сборки машин т.е. технология машиностроения охватывает все этапы процесса изготовления машиностроительной продукции.
Однако под технологией машиностроения обычно понимают научную дисциплину изучающую преимущественно процессы механической обработки заготовок и сборки машин и попутно затрагивающие вопросы выбора заготовок и методы их изготовления Это объясняется тем что в машиностроении заданные формы деталей с требуемой точностью и качеством их поверхностей достигаются в основном механической обработкой.
В процессе механической обработки возникает наибольшее число проблем связанных с выполнением требований к качеству машин заданных конструктором. Процесс механической обработки реализуется достаточно сложной технологической системой включающей в себя металлорежущий станок станочную технологическую оснастку режущий инструмент заготовку. Это объясняет направление развития технологии машиностроения как научной дисциплины в первую очередь в сторону изучения механической обработки со снятием стружки и сборки.
Сложность процесса механической обработки и физической природы происходящих при этом явлении вызвана трудностью изучения всего комплекса вопросов в пределах одной технологической дисциплины и обусловила образование нескольких таких дисциплин: резание металлов; режущие инструменты; металлорежущие станки; конструирование приспособлений; проектирование машиностроительных цехов и заводов; взаимозаменяемость стандартизация и технические измерения; технология конструкционных материалов; автоматизация и механизация технологических процессов.
Определение типа производства
В зависимости от широты номенклатуры регулярности стабильности и объема выпуска изделий современное производство подразделяется на следующие типы: единичное серийное и массовое. От типа производства во многом зависит характер технологического процесса и его построение. Тип производства характеризуется количеством закрепленных операций за одним рабочим местом или за единицей оборудования. Тип производства зависит от 2 факторов: заданной программы и трудоемкости изготовления изделия.
- коэффициент серийности [1 стр.16] где
- такт выпуска изделия
- средняя трудоемкость по операциям. По существующему базовому техпроцессу завода мин.
- действительный годовой фонд времени оборудования
шт. - годовая программа выпуска.
- номинальный фонд работы оборудования при двухсменном режиме час.
% - коэффициент учитывающий потери номинального времени на ремонт оборудования.
- рабочих дней в году.
час – продолжительность рабочей смены.
- количество рабочих смен в день.
При производство принимается крупносерийное.
Определим оптимальное количество детали в партии для одновременного запуска на изготовление:
- рекомендуемый запас деталей на цеховом складе (для крупных деталей 2-3 дня для средних-4-6 для мелких- 7-10 дней);
Так как партия деталей представляет их количество которое изготавливается на рабочем месте с однократной затратой подготовительно-заключительного времени то ее размер оказывает существенное влияние на технико-экономические показатели и организацию производства.
На основании расчетов принимаем производство крупносерийным оптимальное количество деталей в партии для запуска –130штук.
Корпус насоса 0390.22.001-5
Анализ исходных данных.
Служебное назначение детали и условия его работы в сборочной единице.
Деталь Корпус насоса 0390.22.001-5 Корпус насоса является ответственной деталью дизеля СЧН2121 и входит в сборочную единицу насосов. В частности деталь 0390.22.001-5 входит в «Насос топливоподкачивающий». В отверстие 20Н7 устанавливается шейка валика ведомого зубчатого колеса в расточку 52Н7 устанавливаются сами зубчатые колеса. В отверстие 40Н7 устанавливаются два радиальных шарикоподшипника на которых вращается шейка вал-шестерни. В это же отверстие между подшипниками устанавливается уплотнительный узел состоящий из уплотнительных колец и манжет на плоскость разъема через прокладку устанавливается крышка которая закрепляется к корпусу с помощью восьми шпилек М8. С другой стороны устанавливается шайба которая предохраняет подшипниковый и уплотнительный узел от осевого смещения и закрепляется к корпусу тремя болтами М6. Корпус устанавливается на переднюю крышку блок-картера закрепляется к ней шестью шпильками М10 и фиксируется в определенном положении двумя цилиндрическими штифтами 8 мм. Резьбовые отверстия М24х2 служат для подвода и отвода топлива.
Конструкторский контроль чертежа детали.
Конструкторский контроль чертежа производится исходя из требований ЕСКД и ГОСТов на разработку и оформление конструкторской документации.
Для детали 0390.22.001-5 Корпус насоса.
Допуск радиального биения поверхности 52H7 относительно оси отверстия 40H7 не более 003 мм. Не выполнение этого требования ведет к преждевременному износу. Допуск торцевого биения относительно оси отверстия 40H7 не более 003 мм на базовом диаметре 50. Допуск радиального биения поверхности 20H7 относительно оси отверстия 52H7 не более 003. Невыполнение этих требований ведёт к преждевременному износу трущихся деталей в узле.
Допуск непараллельности поверхности 52H7 относительно оси отверстия 40H7 не более 002 мм. Допуск непараллельности торцевой поверхности относительно дна отверстия 20H7 не более 0025 мм на базовой длине 100 мм. Невыполнение этих требований ведёт к неправильному функционированию узла в целом.
Допуск неплоскостности торцевой поверхности не более 002 мм. Невыполнение этого требования ведёт к неплотности прилегания торцевых поверхностей.
Анализ технических требований на изготовление детали.
Технический контроль чертежей производится исходя из требований ЕСКД и ГОСТов на разработку и оформление конструкторской документации. Технические требования указаны над штампом.
Для детали 0390.22.001 имеются следующие требования:
Для детали Корпус насоса 0390.22.001-5:
*Размеры для справок. Данное требование показывает что размеры помеченные звездочкой являются справочными. Справочными называют размеры не подлежащие выполнению по данному чертежу и указываемые для большего удобства пользования чертежом.
Неуказанные предельные отклонения размеров Н14 h14 ± углов - ±АТ162. Требование показывает предельные отклонения на чертеже у которых отсутствуют допуски. Верхнее и нижнее отклонения размеров находят по таблице.
Маркировать обозначением детали шрифтом ПО-50 ГОСТ 2930-62 исполнения 0390.22.001-5. Данное техническое требование показывает что после всей механической обработки после контроля изделие необходимо промаркировать гравером обозначение детали шрифтом ПО высотой 5мм требования к шрифту описаны в ГОСТ 2930-62. Это требование необходимо выполнить чтобы при сборке не возникало путаницы с установкой детали т.к. существует много похожих изделий.
Анализ конструкции детали на технологичность
Технологический анализ конструкции обеспечивает улучшение технико-экономических показателей разрабатываемого технологического процесса. Поэтому технологический анализ является одним из важнейших этапов технологической разработки в том числе и курсового проектирования.
Основные задачи решаемые при анализе технологичности конструкции обрабатываемой детали сводятся к возможному уменьшению трудоемкости и металлоемкости возможности обработки детали высокопро-изводительными методами. Таким образом улучшение технологичности конструкции позволяет снизить себестоимость ее изготовления без ущерба для служебного назначения.
Каждая деталь должна изготавливаться с минимальными трудовыми и материальными затратами. Эти затраты можно сократить в значительной степени правильным выбором варианта технологического процесса его оснащения механизации и автоматизации применение оптимальных режимов обработки. На трудоемкость изготовления детали оказывают особое влияние ее конструкция и технические требования на изготовление.
Оценку технологичности проводят по количественным и качественным показателям.
1 Качественная оценка технологичности
Таблица 1 - качественная оценка технологичности
Требования технологичности
Характеристика технологичности
Деталь должна изготавливаться из стандартных или унифицированных заготовок.
Свойства материала детали должны удовлетворять существующей технологии изготовления хранения и транспортировки.
Конструкция детали должна обеспечить возможность применения типовых групповых или стандартных технологических процессов.
Конструкция детали должна обеспечивать возможность многоместной обработки.
Возможность обработки максимального количества размеров высокопроизводительными методами и инструментами.
Перепад размеров должен быть минимальным.
Отсутствие глубоких отверстий малого диаметра.
Форма конструктивных элементов детали (КЭД) – фасок канавок и т.п. Элементов должна обеспечивать удобный подвод инструмента.
Унификация КЭД для использования при обработке станков с программным управлением.
Вывод: данная деталь имеет конструкцию которую надо признать технологичной т.к. удовлетворяет 89% требований при отработке конструкции на технологичность.
2. Количественная оценка технологичности
Характеризуется расчетом ряда показателей характеризующих отдельные свойства. Для оценки технологичности конструкции могут быть использованы следующие показатели:
Коэффициенты унификации.
- Для детали Корпус насоса 0390.22.001-5
- число унифицированных элементов детали шт.
- общее число конструктивных элементов детали шт.
Коэффициенты точности обработки детали:
где - средний квалитет;
- число размеров соответствующего квалитета.
Коэффициенты шероховатости:
- Для детали Корпус насоса 0390.22.001-5:
где - средний класс шероховатости;
- класс шероховатости;
- число поверхностей соответствующего класса шероховатости
Коэффициенты использования материала:
- масса заготовки кг.
Вывод по результатам анализа технологичности: количественная оценка технологичности показала что сложность изготовления деталей средняя т. к. Кт=092%; коэффициент унификации входит в допустимые пределы 04-06; при выборе метода изготовления детали % - средний показатель использования материала. Деталь относятся к технологичному .
Анализ базового технологического процесса изготовления детали.
Деталь по своим конструкторским особенностям относятся к типу корпусных деталей. За аналог технологического процесса принимается базовый технологический процесс завода изготовителя (ОАО «Волжский дизель имени Маминых»).
а) методом получения заготовки является литье в песчано-глинистые формы;
б) применяемое оборудование соответствует требованиям технологического процесса и позволяет выполнить все технологические требования чертежа оборудование на всех операциях с числовым программным управлением;
в) некоторые операции выполняются с применением универсальных и специальных приспособлений мерительных инструментов;
г) соблюдение технологической дисциплины обеспечивает качественное изготовление деталей в основном брак происходит по техническим причинам из-за грубых ошибок исполнителей.
На основании вышесказанного можно сделать вывод что существующий на базовом заводе технологические процесс на сегодняшний день в некоторой степени устарел и требует изменений и усовершенствований при реорганизации самого процесса производства.
Анализ размерных связей и выбор технологических баз по ТП.
База - это поверхность или сочетание поверхностей ось точка принадлежащие заготовке или изделию и используемые для базирования. В зависимости от числа идеальных опорных точек с которыми база находится в контакте различают установочную базу контактирующую с тремя опорными точками направляющую базу контактирующую с двумя опорными точками и упорную базу контактирующую с одной опорной точкой.
Конструкторская база - это база используемая для определения положения детали или сборочной единицы в изделии.
Технологической базой используемой при обработке заготовок на станках называется поверхность линия или точка заготовки относительно которых ориентируются ее поверхности обрабатываемые на данном установе.
Измерительной базой называется поверхность линия или точка от которых производится отсчет выполняемых размеров при обработке или измерении заготовки а также при проверке взаимного расположения поверхностей детали или элементов изделия.
Если конфигурация заготовки не дает возможности выбрать технологическую базу позволяющую удобно устойчиво и надежно ориентировать и закрепить заготовку в приспособлении или на станке то прибегают к созданию искусственных технологических баз. Характерным примером служат центровые отверстия не требующиеся для готового вала и необходимые исключительно из технологических соображений.
Разработка маршрутного технологического процесса.
Для разработки технологического процесса обработки детали требуется предварительно изучить ее конструкцию и функции. Разрабатываемый технологический процесс должен обеспечивать повышение производительности труда и качества детали сокращение материальных и трудовых затрат на его реализацию уменьшение вредных воздействий на окружающую среду. Технологический процесс обработки деталей подобного типа включает в себя несколько этапов: обработка наружных поверхностей при установке на необработанные и предварительно обработанные поверхности получение базовых поверхностей используемых в дальнейшем на других операциях.
Намечая технологический процесс обработки детали следует придерживаться следующих правил:
Обрабатывать наибольшее количество поверхностей данной детали за одну установку и т. д.
Использовать по возможности только стандартный режущий инструмент.
Не проектировать обработку на уникальных станках. Применение уникальных и дорогостоящих станков должно быть технологически и экономически оправдано.
С целью экономии труда и времени технологической подготовки производства использовать типовые процессы обработки.
Таблица 4 - Технологический маршрут обработки детали Корпус насоса 0390.22.001-5
Технологические базы
Токарная (черновая):
- сверлим отверстие 20;
- растачиваем 39 405 34 и канавки.
Сверлильно –фрезерная –расточная :
-фрезеруем контур детали;
- фрезеруем два отв. в размер 51H9 растачиваем в размер 52
-центруем и сверлим отв. 18 зенкеруем развёртываем в размер 20 H7
-центруем и сверли м два отв. 30
-центруем торец под 8 отверстий сверлим 8 отв. и нарезаем в них резьбу М6
H7 мм габариты детали
Сверлильно – фрезерно - расточной станок с ЧПУ.
Фрезерно - сверлильно-расточная :
-растачиваем отв. в размер
-Центруем торец под 11 отв сверлим 4 отв. 15 сверлим и нарезаем резьбу М6 в пяти отв. сверлим два отв. 8
Радиально-сверлильная:
-центруем и сверлим 3 отв. 4
мм 52H7 мм торец детали
окончательный контроль по чертежу
Расчет припусков и промежуточных размеров.
Разность размеров заготовки и окончательно обработанной детали определяет величину припуска т.е. слоя который должен быть снят при механической обработке.
Припуски разделяют на общие и межоперационные. Под общим понимают припуск снимаемый в течение всего процесса обработки данной поверхности - от размера заготовки до окончательного размера готовой детали. Межоперационным называют припуск который удаляют при выполнении отдельной операции.
В производственных условиях размеры припусков устанавливают на основании опыта используя данные по массе и габаритам детали а также в зависимости от необходимого квалитета точности и требуемой шероховатости поверхности. Такой метод определения припусков называют табличным в отличие от аналитического при котором общая величина припуска определяется путем расчета его по составным элементам с использованием различных коэффициентов.
Аналитический способ расчета является более точным так как учитывает конкретные условия выполнения операций технологического процесса.
Рассчитаем припуски на обработку и промежуточные предельные размеры для 90g6() мм.
Операция 010 Токарная
Переход 1 - Черновое точение
Переход 2 - Чистовое точение
Для выполнения расчетов данные располагают в виде таблицы в которой указывают операции технологического процесса и все искомые параметры поверхностного слоя как для заготовки так и для поверхностей детали по всем операциям.
Таблица 9 - расчетная таблица элементов припуска
заготовки и техноло-гическая
обработан-ной по-верхности
Элементы припуска мкм
Промежуточные размеры
Промежуточные припуски мм
Где Rz – параметр шероховатости;
Т – глубина дефектного слоя;
r - пространственное отклонение;
e - погрешности установки.
Качество поверхности отливок 1 класса размерами до 12м Rz+Т=600мкм; [1 стр.42 табл.17]. Допустимые отклонения по размерам для данных габаритах отливки ±06 мм [1 стр.25 табл.7].
Механическая обработка
Точность и качество поверхности после механической обработки.
Черновое обтачивание-квалитет 12; Rz = 50 мкм; Т = 50 мкм;
чистовое обтачивание-квалитет 6; Rz = 30 мкм; Т = 30 мкм; [1 стр.43 табл.19]
Минимальные промежуточные припуски
1.Черновая токарная обработка
Zmin= [1 cтр.41] где
rSi-1-суммарные пространственные отклонения на предшествующем переходе
ei - погрешность установки заготовки на выполняемом переходе.
Определение величины rSi-1 для заготовки
rSi-1 = [1 cтр.44 табл.21] где
rкор - погрешность заготовки от коробления;
rсм – погрешность заготовки по смещению;
rкор=Dк×В [1 cтр.44 табл.21] где
Dк=07÷1 – удельная кривизна заготовки [1 стр.48 табл.22]
В – толщина обрабатываемой заготовки.
rкор=1×0063=0063 мм.
rсм=d=12 мм [1 cтр.44 табл.21]
В результате rSi-1 = мм.
Погрешность установки определяется по формуле:
мкм - погрешность базирования [1 стр.53 табл.26]
мкм - погрешность закрепления [1 стр.53 табл.26]
мкм - погрешность положения заготовки [1 стр.52]
Итого 2Zmin = 2(600+
2. Чистовая обработка
Остаточную сумму погрешностей после чернового обтачивания можно получить при помощи эмпирической формулы rSi-1=kу×rSi [1 стр.51]
где kу – коэффициент уточнения формы kу=004 [1 стр.51]
Итого 2Zmin = 2(50+50+
Определение максимальных промежуточных припусков
Величина максимального припуска определяется:
1 Черновая токарная обработка:
Zmax = 3883+1200 = 5083 мкм » 51 мм
2 Чистовая токарная обработка:
Zmax = 1161 + 400 = 1561 мкм » 16 мм
Промежуточные межоперационные размеры
Минимальные и максимальные размеры получают прибавлением к предельным размерам минимальных и максимальных припусков по операциям (переходам)
Dmin = Dmin + 2Zmin
Dmax = Dmax + 2 Zmax
Dmin = 89961 + 12 = 91161 мм
Dmax = 89986 + 16 =91586 мм
Dmin = 91161 + 39 = 95061 мм
Dmax = 91586 + 51 = 96686 мм
Исходя из расчетов принимаем диаметр заготовки 97 мм.
Припуска на остальные поверхности заготовки назначаем по таблицам на отливку 1 класса точности по ГОСТ 1855-55.
Таблица 10. Графическое представление припусков для детали Корпус насоса 0390.22.001-5.
Построение операций и выбор оборудования.
Операция 050 Заготовительная
Операция 010 Токарная (черновая)
Оборудование: станок токарно-винторезный 16К20
Приспособление: специальное патрон 3-х кулачковый ГОСТ 2675-80
Режущий инструмент: резец проходной упорный ГОСТ 18870-73
резец проходной отогнутый ГОСТ 18868-73
резец расточной ГОСТ 18062-72
резец канавочный ГОСТ 18884-73
Измерительный инструмент: штангенциркуль ШЦ-1-150 ГОСТ 166-89
Технологическая база – габариты заготовки
Точить 90 g6 с подрезкой торца предварительно;
Подрезать торец как чисто;
Расточить 385 предварительно;
Расточить 39H7 окончательно;
Расточить канавку под угол 30 градусов на глубину 4 мм;
Расточить канавку b=3 мм до 48H9
Расточить канавку b=3 на глубину 405
Операция 015 Сверлильно-фрезерная-расточная с ЧПУ
Оборудование: станок вертикально-фрезерный ГФ2171С3
Приспособление: специальное стол поворотный;
Режущий инструмент: фреза концевая 10 мм ГОСТ 17025-71;
фреза торцевая 100 мм ГОСТ 24359-80;
сверло 9 ГОСТ 10903-77;
сверло 68 ГОСТ 10903-77;
Технологическая база –39H7 торец.
Фрезеровать торец выдерживая размер 87 мм;
Фрезеровать два отверстия 30 на глубину 325 мм;
Фрезеровать два отверстия 51Н9 на глубину 30 мм;
Расточить два отверстия в размер 52
Центровать торец под 8 отв. 68;
Нарезать резьбу M8 в 8-ми отв.
Фрезеровать поверхности по контуру в размер 135;
Центровать поверхность под сверление отв. 18;
Сверлить отв. 19 на глубину 545;
Зенкеровать отв. в размер 198;
Развернуть отв. в размер 20Н7;
Операция 020 Сверлильно-фрезерная-расточная с ЧПУ
Технологическая база –отв. 52H7 торец.
Центровать торец под сверление 11-ти отверстий;
Сверлим 5 отв. под резьбу М6;
Нарезаем резьбу М6 в 5-ти отв.;
-центруем сверлим и нарезаем резьбу в 2 отв. М24х15
Операция 025 Радиально- сверлильная
Оборудование: станок радиально-сверлильный 2М55
Приспособление: специальное стол поворотный
Режущий инструмент: сверло спиральное 4 ГОСТ 10903-77;
зенковка ГОСТ 15599-70; метчик ГОСТ 3266-81
Технологическая база – наружный диаметр и торец червяка
Центруем поверхность под сверление 3 отв. 4;
Операция 030 Слесарная
Оборудование: верстак слесарный
Приспособление: тиски
Режущий инструмент: напильник.
Притупить острые кромки
Операция 035 Моечная
Оборудование: ванна моечная
Операция 040 Контрольная
Окончательный контроль по чертежу.
Операция 045 Маркировочная
6.5. Характеристика применяемого оборудования
Токарно-винторезный станок 16К20
Станок используется для токарной обработки различных заготовок типа валы и диски нарезки различных резьб дуг конусов и внутренних и внешних криволинейных поверхностей с высокой точностью обработки.
В конструкции станков применены горизонтальные закаленные направляющие суппорт базируется на направляющих TSF
В главном приводе применяются двухскоростные электродвигатели с частотным преобразователем.
Точность подач обеспечивается за счет применения шарико-винтовых пар приводимых в действие серводвигателями.
Допустима установка вертикальных 4-х и 6-ти позиционных резцедержателей и 6-ти позиционных горизонтальных резцедержателей.
Все механические электрические и гидравлические системы станка объединены в одном корпусе.
Таблица1 5 . Характеристики токарно-винторезного станка 16К20
Наибольший диаметр устанавливаемого изделия над станиной мм.
Наибольшая длина устанавливаемого изделия в центрах мм.
Наибольший диаметр обрабатываемого изделия над станиной мм
Наибольший диаметр обрабатываемого изделия над суппортом мм.
Наибольший ход суппортов по оси Хпо оси Z мм.
Максимальная скорость быстрых перемещений мммин:
МинимальнаяМаксимальная скорость рабочих подач мммин:
Количество ступеней регулирования частот вращения шпинделя
Частоты вращения шпинделя на ступени IIIIII (с эл.двигателем 1500 обмин) обмин
Мощность электродвигателя кВт:
Габаритные размеры станка мм:
Сверлильно-фрезерно-расточной станок ГФ2171С3
Станки предназначены для выполнения разнообразных фрезерных сверлильных работ при обработке деталей любой формы из стали чугуна цветных металлов их сплавов и других материалов. Поворотная шпиндельная головка станков оснащена механизмом ручного осевого перемещения гильзы шпинделя что позволяет производить обработку отверстий ось которых расположена под углом до ±45° к рабочей поверхности стола. Мощность приводов и высокая жесткость станков позволяют применять фрезы изготовленные из быстрорежущей стали а также инструмент оснащенный пластинками из твердых и сверхтвердых синтетических материалов.
Таблица 16. Характеристика Сверлильно-фрезерно-расточного станка с ЧПУ ГФ2171С3.
Размеры рабочей поверхности станка мм
Наибольшее перемещение стола мм:
Число скоростей шпинделя
Частота вращения шпинделя обмин
(продольная и поперечная вертикальная)
Мощность электродвигателя привода главного движения кВт:
3. Радиально-сверлильный станок 2М55
Станки предназначены для сверления рассверливания зенкерования развертывания нарезания различных резьб при обработке деталей любой формы из стали чугуна цветных металлов их сплавов и других материалов. Поворотная шпиндельная головка станков оснащена механизмом ручного осевого перемещения гильзы шпинделя что позволяет производить обработку отверстий ось которых расположена под углом до ±45° к рабочей поверхности стола. Мощность приводов и высокая жесткость станков позволяют применять фрезы изготовленные из быстрорежущей стали а также инструмент оснащенный пластинками из твердых и сверхтвердых синтетических материалов.
Таблица 17. Характеристики радиально-сверлильного станка 2М55
Наибольший диаметр сверления в стали мм
Расстояние от образующей оси шпинделя до колонны мм:
Расстояние от нижней образующей шпинделя до рабочей поверхности плиты мм:
Наибольшее вертикальное перемещение шпинделя мм
Наибольший поворот шпиндельной головки °
Число подач шпинделя
Подача шпинделя ммоб:
7. Определение рациональных режимов резания.
При назначении режимов резания необходимо учитывать характер обработки тип и размер инструмента материал его режущей части и состояние заготовки. При черновой обработке назначают по возможности максимальную глубину резания и максимально возможную подачу исходя из жесткости системы СПИД мощности станка и других ограничивающих факторов.
Аналитический метод:
Операции 010 токарная (черновая). Установ А переход 1.
Глубина резания - мм.
Подачу принимаем ммоб; [2 том 2 стр.364 табл.11]
Стойкость инструмента мин.
[2 том 2 стр.363] где
- общий поправочный коэффициент на скорость резания.
[2 том 2 стр.369] где
- коэффициент учета материала заготовки.
- коэффициент учета состояния поверхности заготовки.
- коэффициент учета материала инструмента.
[2 том 2 стр.358 табл.1] где
[2 том 2 стр.359 табл.2]
;[2 том 2 стр.361 табл.5]
;[2 том 2 стр.361 табл.6]
;[2 том 2 стр.368 табл.17]
Частота оборотов шпинделя расчетное:
По паспорту станка принимаем обмин
Фактическая скорость резания:
Окружная сила резания:
;[2 том 2 стр.371] где
- поправочный коэффициент на качество обрабатываемого материала.
- коэффициенты учитывающие фактические условия резания.
; ; [2 том 2 стр.362 табл.9]
; [2 том 2 стр.374 табл.23]
; [2 том 2 стр.373 табл.22]
Эффективная мощность резания:
кВт т.е. имеем запас по мощности.
Операция 015 Сверлильно – фрезерная - расточная с ЧПУ.
Диаметр фрезы число зубьев .
Подачу принимаем ; [2 том 2 стр.406 табл.80]
Стойкость инструмента ; [2 том 2 стр.411 табл.82]
Скорость резания определяется:
; [2 том 2 стр.406] где
- коэффициент учета качества обработанной поверхности.
[2 том 2 стр.409 табл.81]
По паспорту станка принимаем
Окружная сила при фрезеровании:
[2 том 2 стр.406] где
; [2 том 2 стр.412 табл.83]
Величины остальных составляющих силы резания: горизонтальной Рh ; вертикальной Рv ; радиальной Рy ; осевой Рх устанавливаются из соотношения с главной составляющей Pz. По справочнику [2 том 2 стр.413 табл.84].
Крутящий момент на шпинделе:
; [2 том 2 стр.411]
Для остальных операций режимы резания определяем по машиностроительным нормативам.
Операция 025 Радиально-сверлильная. Переход 1. Сверлить отв. 4 мм
Подачу принимаем ммоб [4 стр.111 карта С-2].
Скорость резания [3 cтр.115 карта С-4] где
- коэффициент зависящий от обрабатываемого материала.
- коэффициент зависящий от стойкости инструмента.
- коэффициент зависящий от отношения длины к диаметру.
Число оборотов шпинделя расчетное:
Осевая сила резания [3 cтр.124 карта С-5]
Мощность резания где
т.е. имеем запас по мощности.
Аналогично выбираем режимы резания для других операций результаты заносим в табл.18.
Таблица 18. Режимы резания для детали Корпус 0390.22.001-5
Операция 015 Сверлильно-фрезерно-расточная с ЧПУ.
Сверлить отв. 18 на глубину 545;
Операция 020 Сверлильно-фрезерно-расточная с ЧПУ.
Операция 025 Радиально-сверлильная.
Под технически обоснованной нормой времени понимают время необходимое для выполнения заданного объема работ при определенных организационно-технических условиях и наиболее эффективном использовании всех средств производства.
В серийном производстве определяется норма штучно-калькуляционного времени. Для расчета норм штучно-калькуляционного времени ()к норме штучного времени следует добавить подготовительно-заключительное время.
- подготовительно-заключительное время на партию деталей;
- число деталей в настроечной партии;
- штучное время на деталь.
- время на установку и снятие детали;
- время на закрепление и открепления детали;
- время на измерение детали;
- время приемы управления;
- время на обслуживание рабочего места и отдых.
Операция 010 токарная
Рассчитаем нормы штучного времени по укрупненным машиностроительным нормативам.
мин[8 стр.285 карта 136]
мин [8 стр.303 карта 141]
мин [8 стр.313 карта 143]
мин [8 стр.279 карта 134]
[8 стр.273 карта 131]
Основное время определяется по формуле: :
Переход 1. Точить 90 g6 мм
мин мм; [8 стр.322 карта 145]
Переход 2. = 084 мин
Переход 4. = 018 мин
Переход 7. = 015 мин
Переход 8. = 132 мин
Переход 10. = 015 мин
Операция 015 Сверлильно-фрезерно-расточная с ЧПУ
мин[9 стр.73 карта 1]
мин [9 стр.77 карта 2]
мин [9 стр.208 карта 54]
мин [9 стр.279 карта 77]
Переход 9. = 065 мин
Переход 10. = 01 мин
Переход 11. = 065 мин
Переход 12. = 01 мин
Операция 020 Сверлильно-фрезерно-расточная с ЧПУ
мин[9 стр.25 карта 2]
Переход 1. = 055х4=22 мин
Переход 2. = 01х4=04 мин
Переход 3. = 04х2=08 мин
Переход 4. = 04х2=08 мин
Переход 5. = 05х4=2 мин
Операция 025 Радиально-сверлильная
Переход 1. = 144 мин
Переход 2. = 051 мин
Переход 5. = 015 мин
Все расчеты норм времени сведем в таблицу 11
Таблица 23. Нормирование операций для детали Корпус насоса 0390.22.001-5
Операция 010 Токарная
В результате выполнения данной курсовой работы был разработан технологический процесс изготовления детали Корпус насоса 0390.22.001-5. Был обоснован способ получения заготовки разработан маршрутный процесс изготовления детали произведен выбор необходимого оборудования и технологических баз. Была обоснована серийность производства - среднесерийное и экономически рассчитано оптимальное количество деталей в партии для запуска – 64 штуки. Рассчитали припуски на мех. обработку режимы резания проведено нормирование технологических операций.
В результате расчетов сократилось время обработки детали что ведет к снижению ее себестоимость.
Горбацевич А.Ф. Шкред В.А. Курсовое проектирование по технологии машиностроения: [ Учеб. пособие для машиностроит. спец. вузов]. - 4-е изд. перераб. и доп.- Мн.: Выш. школа 1983.- 256 с. ил.
Дальский А.М. Суслов А.Г. Косилова А.Г. и др.; Под редакцией Дальского А.М. Косиловой А.Г. и Мещерякова Р.К. Справочник технолога- машиностроителя. В 2-х т. - 5-е изд. исправленное. - М.; Машиностроение 2003. - 1857 с. ил.
Добрыднев И.С. Курсовое проектирование по предмету «Технология машиностроения» - М.; Машиностроение 1985. - 184 с. ил.
Барановский Ю.В. Брахман Л.А. Бродский Ц.З. и др. Режимы резания металлов. Справочник. - 3-е изд. доп. и перераб. - М.; Машиностроение 1972. - 408 с. ил.
Анурьев В.И. Справочник конструктора-машиностроителя - М.; Машиностроение 1999. - 875 с. ил.
Жуков Э.Л. Козарь И.И. Мурашкин С.Л. Розовский Б.Я. Технология машиностроения: В 2 кн. Учеб. Пособ. Для вузов. –М.: Высш. шк. 2003.-295 с.: ил.
Базров Б. М. Основы технологии машиностроения: Учебник для вузов. М.: Машиностроение 2005г. – 736с.: ил.
Общемашиностроительные укрупненные нормативы времени на работы выполняемые на металлорежущих станках; Под редакцией Грязнова Ю.А. - М.; Типография при НИИ труда 1989. 430 с.
Общемашиностроительные нормативы времени на работы выполняемые на фрезерных и сверлильных станках; Под редакцией Ульянова Р.Г. - М.; Типография при НИИ труда 1973. 400 с.
Общемашиностроительные нормативы времени для технического нормирования работ на шлифовальных и доводочных станках; Под редакцией Ушанова С.Н. - М.; Типография ВНИИТЭМР 1985. 376 с.
Рекомендуемые чертежи
- 24.01.2023
- 20.08.2014