Разработка технологического процесса Вал нижний




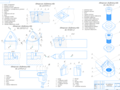

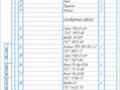
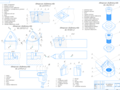
- Добавлен: 24.01.2023
- Размер: 72 MB
- Закачек: 1
Описание
Разработка технологического процесса Вал нижний
Состав проекта
![]() |
![]() ![]() ![]() |
![]() |
![]() |
![]() ![]() ![]() ![]() |
![]() ![]() ![]() ![]() |
![]() ![]() ![]() ![]() |
![]() ![]() ![]() ![]() |
![]() |
![]() |
![]() ![]() ![]() ![]() |
![]() ![]() ![]() ![]() |
![]() ![]() ![]() ![]() |
![]() ![]() ![]() ![]() |
![]() ![]() ![]() ![]() |
![]() ![]() ![]() ![]() |
![]() ![]() ![]() ![]() |
![]() ![]() ![]() ![]() |
![]() ![]() ![]() ![]() |
![]() ![]() ![]() ![]() |
![]() |
![]() ![]() ![]() ![]() |
![]() ![]() ![]() ![]() |
![]() ![]() ![]() ![]() |
![]() ![]() ![]() ![]() |
![]() ![]() ![]() |
![]() ![]() ![]() |
![]() ![]() ![]() |
![]() ![]() ![]() |
![]() ![]() ![]() |
![]() |
![]() ![]() ![]() ![]() |
![]() ![]() ![]() ![]() |
![]() ![]() ![]() ![]() |
![]() ![]() ![]() ![]() |
![]() ![]() ![]() ![]() |
![]() ![]() ![]() |
![]() ![]() ![]() ![]() |
![]() ![]() ![]() ![]() |
![]() ![]() ![]() ![]() |
![]() ![]() ![]() |
![]() ![]() ![]() ![]() |
![]() ![]() ![]() ![]() |
![]() ![]() ![]() ![]() |
![]() ![]() ![]() ![]() |
![]() ![]() ![]() ![]() |
![]() ![]() ![]() ![]() |
![]() ![]() ![]() ![]() |
![]() ![]() ![]() ![]() |
![]() ![]() ![]() ![]() |
![]() ![]() ![]() ![]() |
![]() ![]() ![]() ![]() |
![]() ![]() ![]() ![]() |
![]() ![]() ![]() ![]() |
![]() ![]() ![]() ![]() |
![]() ![]() ![]() ![]() |
![]() ![]() ![]() ![]() |
![]() ![]() ![]() ![]() |
![]() ![]() ![]() ![]() |
![]() ![]() ![]() ![]() |
![]() ![]() ![]() ![]() |
![]() ![]() ![]() ![]() |
![]() ![]() ![]() ![]() |
![]() ![]() ![]() ![]() |
![]() ![]() ![]() ![]() |
![]() ![]() ![]() ![]() |
![]() ![]() ![]() |
![]() ![]() ![]() ![]() |
![]() ![]() ![]() ![]() |
![]() ![]() ![]() |
![]() ![]() ![]() ![]() |
![]() ![]() ![]() ![]() |
![]() ![]() ![]() ![]() |
![]() ![]() ![]() ![]() |
![]() ![]() ![]() ![]() |
![]() ![]() ![]() ![]() |
![]() ![]() ![]() ![]() |
![]() ![]() ![]() |
![]() ![]() ![]() |
Дополнительная информация
Иследовательская часть 06.doc
Наноструктурные покрытия высокопроизводительного инструмента.
Роль покрытий для современного инструмента трудно переоценить. На современные высокопроизводительные режущие инструменты все чаще наносится покрытие на основе титана и алюминия. Разные статистические источники приводят разные цифры но во всех отчетах доля этого покрытия не опускается ниже 25% а по некоторым данным доходит до 55% от общей доли покрываемого инструмента. Причина таких оценок – в уникальных свойствах самого покрытия на основе Ti и Al:
Высокая твердость (примерно 25-38 ГПа) при относительно небольших остаточных напряжениях (3-5 ГПа);
Высокая твердость при нагреве («горячая твердость») определяющая незначительные потери твердости (около 30-40%) при температурах до 800°С;
Высокая стойкость к окислению – та же скорость окисления (около 15-20 мкгсм2) при температуре 800°С что для покрытия T
Низкая теплопроводность (коэффициент относительного температурного расширения на 30% ниже чем у покрытия TiN).
Технология нанесения покрытий на основе титана и алюминия является одной из наиболее быстро развивающихся. Даже за тот относительно небольшой период времени существования покрытия предложено достаточно большое количество решений по улучшению его свойств описанных выше. Отметим только некоторые из них:
Комбинация дугового метода и метода магнетронного осаждения;
Фильтрация микрокапель при дуговом методе;
Оптимизация параметров процесса таких как ток дуги напряжение смещения давления азота и т.д.;
Оптимизация кристаллической структуры для улучшения стойкости к коррозии;
Нанесение многослойных покрытий для увеличения вязкости и толщины покрытия;
Добавление легирующих компонентов таких как:
Хром и иттрий для увеличения окислительной стойкости;
Цирконий ванадий бор и гафний для увеличения износостойкости;
Кремний для увеличения твердости и стойкости к химическим реакциям.
Наиболее важными направлениями совершенствования на основе титана и алюминия представляются работы по нанесению нанослойных покрытий и увеличению доли алюминия.
Эффект от нанесения нанослойных покрытий
Возможность наносить нанослойные покрытия стала следствием развития техники (установок) для нанесения покрытий. При определенной частоте чередования слоев т.е. при определенной толщине нанослоев может быть получено значительное увеличение твердости (рис.1).
Высокая твердость является следствием существенного различия модуля Юнга (модуля упругости) материалов субслоев. Снижение твердости при малых толщинах слоев (около 6-7 Нм) объясняется «грубостью» границ между слоями. Если установка и технология нанесения покрытия позволяет получить «четкие» границы то снижения твердости не наблюдается.
Для нанесения нанослойных покрытий необходимо синхронизировать управление катодом и вращение материала на который наносится покрытие. Это относительно просто если покрываются одинаковые инструменты большими партиями. Но процесс становится значительно сложнее если покрываются различные инструменты в одной партии. Таким образом получение нанослойного покрытия с постоянной периодичностью чередования слоев невозможно если в одной партии в камере находятся одновременно маленькие и большие инструменты пластины штампы пресс-формы и детали машин (а все эти элементы нуждаются в современных покрытиях). Кроме того расстояние между нанослоями изменяется в процессе эксплуатации инструмента из-за изменения температуры что также снижает эффективность такого покрытия.
Увеличение содержания алюминия.
Ведущие изготовители установок для нанесения покрытий постоянно улучшают их давая возможность производителям инструмента увеличивать содержание алюминия в покрытии. Увеличение доли алюминия увеличивает твердость износо- и теплостойкость. Покрытия в которых доля алюминия не превышает 50% обозначаются как TiAN. Если доля алюминия составляет более 50% то используется обозначение AlTiN.однако существует предел содержания алюминия после которого дальнейшее увеличение не дает никакого дополнительного преимущества и не имеет особого смысла. Таким пределом считают 67% 75% а в некоторых источниках – 80% алюминия. Все зависит от такого какой из факторов является преобладающим (рис.2).
И в этом случае предел содержания алюминия определяется периодичностью нанослоев которая может быть практически выдержана в реальных условиях нанесения покрытия в производстве.
Единственным способом превышения предела содержания алюминия в покрытии является применение физически новых решений например нанокомпозитов.
Нанокомпозитные покрытия
В составе нанокомпозитных покрытий наносятся различные материалы (например титан алюминий и кремний). Они не могут быть смешаны. Две различные фазы присутствуют в плазме и в результате нанокристаллический TiAlN оказывается внедренным в аморфную матрицу Si3N4 (как арматура в бетон) (рис.3).
Такая структура обеспечивает крайне высокую твердость (40-50 ГПа) которая сохраняется и при высоких температурах (до 1000°С) даже при небольшом содержании алюминия (50%). Такие характеристики крайне важны при высокопроизводительной обработке без СОЖ. Дальнейшее улучшение свойств такого покрытия возможно если нанокомпозитное покрытие наносится еще и по нанослойному методу. Периодичность слоев в этом случае составляет около 35 ангстрем.
Для получения подобной архитектуры необходимо расположить катоды как можно ближе друг к другу. Эта задача решается с помощью технологии LARC (боковые вращающиеся дуговые катоды).
Оборудование для нанесения нанокомпозитных покрытий экономичным способом в промышленном масштабе должно удовлетворять следующим требованиям:
Катоды должны быть расположены как можно ближе друг к другу;
Плазма должна иметь высокую степень ионизации;
Необходима поддержка сильного магнитного поля;
Требуется очень быстрое пермещение дуги.
Все известные технологии нанесения покрытия не удовлетворяли этим критериям и была создана новая технология – технология LARC. Она реализует новый процесс нанесения покрытия и для этого создано новое оборудование. Оба охлаждаемых водой катода постоянно вращаются. Магнитное поле создается катушками и постоянными магнитами управляемыми в вертикальном и радиальном направлениях (рис.4).
Самые большие преимущества технологии LARC заключаются во вращающихся катодах и их боковом расположении. Они называются – преимуществами. К ним относятся:
Оптимальная адгезия покрытия благодаря Виртуальному Затвору (рис.6). Оптимальная адгезия является одним из основных критериев качества покрытия. Боковое расположение катодов делает возможным реализовать систему Виртуального Затвора работающую без механических элементов. магнитное поле поворачивается на 180° и происходит поджиг дуги. Благодаря этой процедуре становится возможным произвести очистку катодов до начала процесса нанесения покрытий и сбросить наиболее крупные первоначальные частицы (капли) в сторону стенки. В это же время материал на который наносится покрытие очищается интенсивной плазмой. Затем дуга без выключения поворачивается в сторону инструментов. В результате можно уменьшить время ионного травления и наносить покрытие с хорошей адгезией с металлически чистой мишени.
«Широкие» мишени с большим сроком службы (рис.7).
Наиболее очевидным преимуществом вращающихся цилиндрических катодов является их ширина. При тех же габаритах они в раз шире чем плоские катоды. Мишень может быть использована примерно в 200 циклах нанесения покрытия.
Более гладкое покрытие благодаря уменьшению капельной фазы (рис.8). В обычной дуговой технологии большинство капель образуется в начале процесса. Образование капель начинается с момента поджига дуги когда неподвижное пятно
образует самую большую ванну. В данном случае наибольшие капли сбрасываются назад благодаря Виртуальному Затвору. Размер и количество капель образующихся во время процесса зависит в числе прочих причин от скорости перемещения пятна дуги. На установках с плоским катодами перемещение дуги управляется магнитными катушками по периметру мишени. Для вращающихся катодов движение пятна значительно более быстрое и равномерное так как реализуется вращением мишени при вертикальном перемещении магнитного поля.
Нанесение нанокомпозитных покрытий. Вытянутые цилиндрические мишени расположенные сбоку занимают минимальное пространство. Таким образом возможно размещение нескольких катодов в минимальном объеме компактной установки. Это означает возможность нанесения на компактных установках покрытий с различными металлическими компонентами. Благодаря быстрому перемещению дуги можно использовать дешевые мишени состоящие только из одного материала например алюминия или AlSi. Они могут заменить дорогие легированные мишени такие как: Al 25% Ti 75% Al 50% Ti 50% Al 67% Ti 33% и т.д. Мишень из чистого кремния невозможно реализовать по простым механическим причинам. Кремний наносится из легированных мишеней. После высвобождения из мишени алюминий и кремний должны быть разделены. Кремний не растворяется в металлической фазе и нанокристаллические зерна TiAlN оказываются внедренными в аморфную матрицу Si3N4. Именно для этого процесса необходима высоко ионизированная плазма и магнитное поле с высокой интенсивностью. Быстрое перемещение пятна дуги позволяет реализовать такое интенсивное магнитное поле без опасности «прорыва» через мишень (что является реальной проблемой при плоских катодах). В результате в нанокомпозитной структуре нет «промежутков» между нанокристаллическими зернами размер кристаллов минимален а границы четкие. В итоге обеспечивается максимальная твердость. Кроме того образование трещин останавливается на границе зерен.
Нанесение наноградиентных покрытий с программируемым составом (рис.9).
Благодаря быстрому перемещению пятна дуги и использованию «чистых» катодов можно быстро менять состав покрытия даже во время процесса нанесения. такие покрытия называются градиентными так как их свойства постоянно меняются по глубине (толщине) покрытия. например в начале нанесения градиентного покрытия для обеспечения лучшей адгезии алюминия наносится меньше чем титана. Затем доля алюминия постепенно увеличивается и повышается твердость температурная устойчивость и стойкость к оскислению покрытия. В конце цикла содержание алюминия опять уменьшается а содержание титана увеличивается. В результате образуется привлекательная по внешнему виду поверхность.
Нанесение многослойных (в данном случае нанослойных) покрытий (рис.10).
Многослойные покрытия представляют собой градиентные покрытия представляют собой градиентные покрытия с периодически меняющимся свойствами. Они позволяют улучшить качество покрытий. Например увеличение твердости приводит к более высоким остаточным внутренним напряжениям. В многослойных структарах внутренние напряжения остаются на приемлемом уровне (примерно (-3) – (-4) ГПа).
Размер установок для нанесения нанокомпозитных покрытий
Как видно на рисунке 5 первые промышленные установки для нанесения покрытий по технологии LARC достаточно компактны. Отметим основные причины такого подхода:
Покрытия не должны быть привилегией крупных производителей и больших центров по нанесению покрытий. Малые и средние предприятия также должны иметь возможность наносить современные покрытия в своих производствах;
Новые покрытия не вытеснят мгновенно покрытия T
После того как удалось создать технологию и организовать производство катодов с минимальными размерами масштабирование не представляет никаких трудностей. Важно только соблюдать расположение катодов парами на минимальном расстоянии. В этом случае гарантируется нанесение нанокомпозитных покрытий с максимальной производительностью без дорогих легированных мишеней;
В маленьких установках нет необходимости собирать большие партии материала с одинаковой основой для нанесения покрытия. Можно выделить небольшие группы по размеру или по области применения и нанести покрытие на эту небольшую партию изделий. В этом случае а также благодаря минимальному расстоянию между катодами можно наносить нанослойные покрытия с периодом меньше 10 Нм;
Несколько небольших установок обеспечивают ту же производительность что и одна большая. В то же время они более гибкие и надежность производства в этом случае выше;
С точки зрения вложения средств лучше наращивать мощность постепенно по мере необходимости чем единовременно вкладывать большие средства в большую установку.
Преимущества покрытий нанесенных методом LARC.
Приведем несколько примеров (рис.11-13) для того чтобы показать как можно существенно увеличить эффективность механической обработки только за счет применения нового оптимизированного покрытия.
Приведенные примеры также показывают эффект от оптимизации т.е. от подбора наиболее подходящего покрытия для конкретного случая обработки. Отметим что результат может быть получен очень быстро - намного быстрее чем при подборе нового инструмента и новой технологии.
Научно-исслед.часть -05 версия5.cdw

и наносится покрытие
Научно-исследовательская
периодичность нанослоев (нм)
Рис.1 Твердость нанослойного покрытия
Содержание Al (в %) = (Al) (Al + Ti)
Рис.2 Влияние содержания Al на свойства покрытия
Рис.9 Изменение состава покрытия по толщине (градиентные покрытия) LARC
Дверца или задняя стенка
Рис.6 Принцип Виртуального Затвора
Наноструктурные покрытия высокопроизводительного инструмента
Приспособление зажимное.cdw

Размер обеспечить на станке за счет регулировки гайки
дет.№35 для срабатывания переключателя при не попадании
центра в центровое отверстие.
мм обеспечить подшлифовкой
Засверлить при сборке.
Внутреннее полости патрона заполнить смазкой ЦИАТИМ-201
Испытать на безотказный зажим кулачков при частоте
вращения патрона n=200обмин в течении 4-х часов.
Испытать на безотказный разжим кулачков при частоте
вращения шпинделя n=160обмин в течении 4-х часов.
Операция 010 копировальная (А2).cdw

Резец канавочный Т5К10
Операция 010 Токарно-копировальная
Оборудование: токарный гидрокопировальный па мод.1Е713
Приспособление: центр задний
* Размер для справок.
** Размеры обеспечиваются инструментом.
Приспособление зажимное(лист 1).cdw

Патенты новые версия5.cdw

- корпус инструмента
- коническая часть отверстия
- отверстие с цилиндрическим участком
- отверстие под ключ
- резьбовая часть винта
- фиксирующий выступ
- опорная поверхность
- боковая поверхность гнезда
Авторское свидетельство
- наклонная плоскость
- радиальная опорная поверхность
- резьбовое отверстие
- опорная осевая поверхность
- закругленная поверхность
- боковая опорная поверхность
- опорная поверхность гнезда
- боковая поверхность
- выфрезерованная выборка
- нижняя поверхность
- защитная поверхность
Операция 060 Шлицешлифовальная.cdw

Оборудование: шлицешлифовальный ст. мод.3451В
Приспособление: центр передний; центр задний
** Размеры обеспечиваются инструментом.
Приспособление зажимное(лист 2).cdw

Научно-исслед.часть -05.cdw

и наносится покрытие
Научно-исследовательская
периодичность нанослоев (нм)
Рис.1 Твердость нанослойного покрытия
Содержание Al (в %) = (Al) (Al + Ti)
Рис.2 Влияние содержания Al на свойства покрытия
Рис.9 Изменение состава покрытия по толщине (градиентные покрытия) LARC
Дверца или задняя стенка
Рис.6 Принцип Виртуального Затвора
Наноструктурные покрытия высокопроизводительного инструмента
Операция 005 фрез.центровальная (А2).cdw

Оборудование: фрезерно-центровальный па мод.2Г942
Приспособление: спец.приспособление
Фреза торцевая Т5К10
Сверло центровочное Р6М5
Отв. центр. A5 ГОСТ 14034-74
Операция 005 фрез.центровальная (А2) версия5.cdw

Оборудование: фрезерно-центровальный па мод.2Г942
Приспособление: спец.приспособление
Фреза торцевая Т5К10
Сверло центровочное Р6М5
Отв. центр. A5 ГОСТ 14034-74
Приспособление зажимное(лист 3) версия5.cdw

Операция 010 копировальная (А2) версия5.cdw

Резец канавочный Т5К10
Операция 010 Токарно-копировальная
Оборудование: токарный гидрокопировальный па мод.1Е713
Приспособление: центр задний
* Размер для справок.
** Размеры обеспечиваются инструментом.
Операция 020 Шлицефрезерная (А2).cdw

** Размеры обеспечиваются инструментом.
Операция 020 Шлицефрезерная
Оборудование: шлицефрезерный па мод.5350А
Приспособление: центр передний; центр задний
Приспособление зажимное(лист 2) версия5.cdw

Приспособление зажимное(лист 3).cdw

Приспособление зажимное(лист 1) версия5.cdw

Патенты новые.cdw

- корпус инструмента
- коническая часть отверстия
- отверстие с цилиндрическим участком
- отверстие под ключ
- резьбовая часть винта
- фиксирующий выступ
- опорная поверхность
- боковая поверхность гнезда
Авторское свидетельство
- наклонная плоскость
- радиальная опорная поверхность
- резьбовое отверстие
- опорная осевая поверхность
- закругленная поверхность
- боковая опорная поверхность
- опорная поверхность гнезда
- боковая поверхность
- выфрезерованная выборка
- нижняя поверхность
- защитная поверхность
Приспособление зажимное версия5.cdw

Размер обеспечить на станке за счет регулировки гайки
дет.№35 для срабатывания переключателя при не попадании
центра в центровое отверстие.
мм обеспечить подшлифовкой
Засверлить при сборке.
Внутреннее полости патрона заполнить смазкой ЦИАТИМ-201
Испытать на безотказный зажим кулачков при частоте
вращения патрона n=200обмин в течении 4-х часов.
Испытать на безотказный разжим кулачков при частоте
вращения шпинделя n=160обмин в течении 4-х часов.
Конструкторская часть.doc
Строительство материально-технической базы и необходимость непрерывного повышения производительности труда на основе средств современного производства ставит перед машиностроением весьма ответственные задачи. К их числу относятся повышение качества машин снижение их материалоемкости трудоемкости и себестоимости изготовления нормализация и унификация их элементов внедрение поточных методов производства его механизация и автоматизация а также сокращение сроков подготовки производства новых объектов. Решение указанных задач обеспечивается улучшением конструкции машин совершенствованием технологий и их изготовления применением прогрессивных средств и методов производства. Большое значение в совершенствовании производства машин имеют различного рода приспособления.
Приспособлениями в машиностроении называют вспомогательные устройства используемые при механической обработке сборке и контроле изделий. Приспособления рабочие и контрольные инструменты вместе взятые называют технологической оснасткой причем приспособления являются наиболее сложной и трудоемкой его частью. Современные механосборочные цехи располагают большим парком приспособлений в крупносерийном и массовом производстве на каждую обрабатываемою деталь приходится в среднем десять приспособлений. Наиболее значительную их долю (80-90% общего парка приспособлений) составляют станочное приспособления применяемые для установки и закрепления обрабатываемых заготовок. Сложность построения технологических процессов в машиностроении обусловливает большое разнообразие конструкций приспособлений и высокий уровень предъявляемых к ним требований. Недостаточно продуманные технологические и конструкционные решения при создании приспособлений приводят к удлинению сроков подготовки производства к снижению его эффективности.
1.Описание конструкции станочного приспособления.
Самозажимные поводковые патроны. Такие патроны изготавливаются с двумя или тремя эксцентриковыми кулачками насечкой которые в начале обработки под действием сил резания зажимают обрабатываемою деталь установленную в центрах станка и передают ей крутящий момент от шпинделя станка.
При увеличении крутящего момента резания автоматически увеличивается и крутящий момент от шпинделя передаваемый кулачками патрона на деталь. Для удобной установки детали в центрах применяют поводковые патроны с автоматически раскрывающимися кулачками. Равномерный зажим детали всеми кулачками обеспечивается тем что применяют плавающие кулачки или кулачки с независимым перемещением. Самозажимные поводковые патроны позволяют устанавливать кулачки на различный диаметр обработки деталей.
Станочное приспособление – зажимное приспособление для точения - применяется для установки и закрепления детали обрабатываемой на токарном станке. Приспособление на операцию 020- токарную.
Приспособление устанавливается на шпинделе станка. Фиксация приспособления по отверстию шпинделя станка осуществляется опорой позиция 47. Крепление приспособления осуществляется 4 болтами.
Приспособление работает следующим образом: деталь устанавливается в центра позиция 14;22. Когда включается привод станка шток позиция 1 перемещается вниз происходит зажим детали (усилие обеспечивается за счет центробежной силы возникающей при вращении шпинделя и достаточное усилие возникает при n>200 обмин).
Чтобы разжать деталь достаточно остановить шпиндель ( разжим происходит при n=160обмин). При обработке силы резания воспринимает корпус приспособления позиция 12.
2. Силовой расчет станочного приспособления
Зажим детали необходим для передачи вращательного движения. Центробежную силу определяют через массу груза и условную скорость вращения его центра тяжести:
или через массу и линейную скорость
где m-масса груза кг;
w-угловая скорость вращаемого груза относительно оси шпинделя радс;
R-расстояние от центра тяжести груза до оси вращения патрона R=0055м;
v-линейная скорость вращения центра тяжести груза мс;
где n-частота вращения шпинделя n=200обмин;
Определим силу зажима двумя кулачками патрона обрабатываемой детали:
Wсумма=PцZcos 300(5.5)
где 300- угол между силой зажима w приложенной к кулачку и направлением действия центробежной силы.
Z-число кулачков патронат;
Wсумма=102cos30°=176Н
Определим осевую силу зажима кулачками патрона обрабатываемой детали:
Q=MРез[nrmax sin(q +4r0mprmin)](5.6)
где Rmax-максимальный радиус зажатой кулачками детали
q-угол подъема профиля кулачка q=180;
m- коэффициент трения на тыльной упорной поверхности кулачка m=015;
r0-радиус тыльной упорной поверхности кулачка r0=0025м;
Мрез .- момент силы резания возникающий при резании Мрез=45Нм;
Q=45[2000055sin(18+40025015314004)]=362H
Определим угол поворота кулачка при зажиме обрабатываемой детали:
a0=231g(rmaxrmin)(5.7)
a0-угол поворота кулачка при зажиме обратной поверхности детали;
a0=231981(0055004)=31°
3. Точностной расчет станочного приспособления
Допустимая погрешность установки определяется по формуле:
где – технологический допуск на выполняемый размер =120мкм;
Σф - суммарная погрешность формы обрабатываемой поверхности в результате геометрических погрешностей станка и деформаций заготовки при её закреплении ф = 18 мкм;
у – погрешность вызываемая упругими отжатиями технологической системы под влиянием сил резания;
н – погрешность настройки станка;
и – погрешность от размерного износа инструмента;
– погрешность обработки вызываемая тепловыми деформациями технологической системы.
Погрешность вызываемая упругими отжатиями технологической системы под влиянием сил резания определяется по формуле:
где – податливость системы мкм Н;
Ру max Ру min - максимальное и минимальное значения составляющей силы резания совпадающей с направлением выдерживаемого размера Н.
Податливость системы определяется по формуле:
где у - смещение элемента технологической системы у = 40 мкм;
Р - сила упругости Р = 686 Н.
Определяем податливость системы:
Максимальная и минимальная составляющие силы резания определяются по формуле:
где СР - коэффициент СР = 243;
S - подача S = 028 ммоб;
V - скорость резания V = 1039 ммин;
КР - поправочный коэффициент КР = 11;
x y n - показатели степени
Определяем составляющие силы резания:
Определяем погрешность вызываемую упругими отжатиями технологической системы:
Погрешность настройки станка определяется по формуле:
где КР и Ки – коэффициенты учитывающие отклонение закона элементарных величин Р и изм от нормального закона распределения КР = 114 173; Ки = 1;
Р – погрешность регулирования положения инструмента Р=20 мкм;
изм – погрешность измерения размера детали изм = 10 мкм.
Определяем погрешность настройки станка:
Погрешность от размерного износа инструмента определяется по формуле:
где L – полная длина пути резания м;
u0 – относительный размерный износ инструмента u0 = 5 мкмкм.
Полная длина пути резания определяется по формуле:
где Lн – длина начального изнашивания инструмента Lн = 1000 м;
LN – длина пути резания для партии заготовок N обрабатываемых в период между подналадками станка.
Длина пути резания для партии заготовок определяется по формуле:
где Lд – длина пути резания при обработке одной заготовки м;
N – партия заготовок обрабатываемая в период между подналадками станка шт.
Длина пути резания при обработке одной заготовки определяется по формуле:
Lд = V · t0 м.(5.16)
где V- скорость резания V = 1039 ммин;
t 0 – начальное время t0 = 07 мин.
Определяем длину пути резания при обработке одной заготовки:
Lд = 1039 · 07 = 727 м.
Количество заготовок в партии обрабатываемых в период между подналадками станка определяется по формуле:
где Т – стойкость инструмента Т = 100 мин.
Определяем количество заготовок в партии:
Определяем длину пути для партии заготовок:
LN = 727 · 140 = 10000 м
Определяем полную длину пути резания для партии деталей:
L = 1000+10000 = 11000 м
Определяем погрешность от размерного износа инструмента:
Погрешность обработки вызываемая тепловыми деформациями технологической системы определяется по формуле:
= (01 015) Σ мкм (5.18)
Определяем погрешность обработки вызываемую тепловыми деформациями технологической системы:
Определяем допустимую погрешность установки:
Погрешность установки определяется по формуле:
где б – погрешность базирования б = 0;
з – погрешность закрепления з = 0;
пр – погрешность приспособления.
Отсюда у = доп = пр = 72 мкм
Погрешность приспособления определяется по формуле:
где изг.пр. – погрешность характеризующая неточность изготовления деталей в приспособлении его сборки и регулировки;
изн.у.э. – погрешность износа установочных элементов.
Принимаем изн.у.э. пр 2 36 мкм;
ст–погрешность характеризующая точность выверки приспособления на станке ст = 0.
Технические требования на изготовление приспособления следующие:
Радиальное биение в приспособлении не более 01 мм на длине 100 мм.
Таким образом выполненные силовой и точностной расчеты приспособления показали что спроектированное приспособление обеспечивает надёжное закрепление детали и получение размеров с заданными допусками.
4. Описание конструкции контрольного
Контрольное приспособление предназначено для проверки паралелльности боковой поверхности шлица относительно оси детали (005 мм на длине 100 мм).
Проверяемую деталь установить в центра поз.13 и зафиксировать рукояткой поз.20 Стойка поз.4 установить на станину поз.1 щуп индикатора
поз.23 установить на боковую поверхность шлица детали. Перемещая зажим поз.7 определяют по индикатору величину непараллельности шлиц.
Патенты новые.DOC
1. Задание на проведение патентного поиска
Тема курсового проекта. Разработка технологического процесса механической обработки детали «Вал нижний».
Цель патентных исследований. Установить уровень развития прогрессив-ных конструкций токарных режущих инструментов.
Страны патентного поиска:
Российская Федерация США Франция Германия Япония.
Глубина патентного поиска: 2000 – 2009 г.г.: РФ;
США Франция Германия Япония: 2000 – 2005 г.г.
2. Справка о проведении патентного поиска
Справка о результатах поиска
Перечень просмотренных
материалов (что и за какой период)
Бюллетень «Открытия изобретения промышлен-ные образцы и товарные знаки» 2000 - 2005г.
Инструмент для обработки металла резанием
Опубл. 27. 01. 2001г.
Бюллетень «Открытия изобретения промышлен-ные образцы и товарные знаки» 2000 – 2005 г.
Резец с механическим креплением режущей пластины.
Опубл. 27. 01. 2003 г.
Опубл. 27. 06. 2003 г.
Режущий инструмент со сменной перетачиваемой пластиной
Опубл. 10. 09. 2003 г.
Опубл. 10. 08. 2005 г.
Окончание таблицы 3.1
Изобретения стран мира
Аналогов не обнаружено
Условия обработки детали на станке требуют применения режущих инструмен-тов имеющих высокую стойкость и обеспечивающих высокое качество обработки. С целью выполнения данных требований была поставлена задача поиска прогрес-сивных конструкций токарного режущего инструмента. Обзор патентных иссле-дований приведен в таблице 3.2.
Обзор патентных исследований
Наименование и номер авторского свидетельства
Существенные признаки отличия
Примене-ние в курсовом проекте
Улучшить экономичес-кую эффектив-ность обработ-ки резанием за счет установки пластин с раз-личным коли-чеством режу-щих кромок
Инструмент для механической обра-ботки металла резанием содержа-щий одно или несколько гнезд для размещения индексируемых режу-щих пластин при этом каждое гнез-до имеет нижнюю опорную поверх-ность и по крайней мере две боко-вые поверхности которые образуют прямой угол друг с другом и вклю-чают опорные поверхности пред-назначенные для взаимодействия с установленной в гнездо режущей пластиной отличающийся тем что одна из боковых поверхностей вк-лючает по крайней мере две опор-ные поверхности.
может быть рекомендо-вана для точения
продолжение таблицы 3.2
Создание более прогрессивного инструмента поз-воляющего повы-сить точность по-зиционирования режущей пласти-ны резца после ее переточки
Резец с механическим креп-лением режущей пластины со-держащий корпус в V-образ-ном гнезде которого установ-лена режущая пластина с V-образным выступом закреп-ленная с помощью прихвата и прижимного винта при этом боковые стенки гнезда корпуса и грани выступа режущей пластины в продольном нап-равлении выполнены под уг-лом отличающийся тем что угол между боковыми стенка-ми гнезда корпуса и гранями выступа режущей пластины равен углу при вершине резца.
Расширить область применения режу-щего инструмента за счет возможнос-ти его оснащения режущими пласти-нами с более широ-кой гаммой форм и размеров
Режущий инструмент со-держащий корпус режущую пластину и детали крепления отличающийся тем что он снабжен упругим элементом расположенным в гнезде кор-пуса между режущей пласти-ной и одной из деталей крепле-ния и имеющим выступы предназначенные для его зак-репления на одной из деталей крепления.
Режущий инструмент со сменной пере-тачиваемой пластиной
Возможность выдерживания высоких и длительных нагрузок при эксплуатации
Режущий инструмент со смен-ной перетачиваемой пластиной которая установлена в гнезде корпуса и закреплена в нем с по-мощью прижима и винта боко-вая опорная поверхность гнезда выполнена под углом к режущей поверхности регули-ровочный болт служит допол-нительной опорной поверхнос-тью для пластины отличаю-щийся тем что боковая опорная поверхность выполнена под углом к режущей поверхности 12o30o.
окончание таблицы 3.2
Повышение надежности крепления пластины технологичности конструкции и удобства обслуживания.
Режущий инструмент с меха-ническим креплением режу-щей пластины с помощью вин-та контактирующего головкой с коническим участком отверс-тия режущей пластины отли-чающийся тем что он допол-нительно содержит гайку ус-тановленную в отверстии дер-жавки при этом головка винта выполнена Г-образной причем место перехода от вертикаль-ной к горизонтальной поверх-ности и горизонтальная по-верхность контактирующая с коническим участком отверс-тия режущей пластины выпол-нены по радиусу при этом радиусы скругления выполне-ны с возможностью съема ре-жущей пластины без полного откручивания гайки при этом над резьбовой частью винта выполнен фиксирующий выс-туп входящий в паз выпол-ненный на опорной поверх-ности гнезда и направленный к боковым поверхностям гнезда державки причем направления горизонтальной поверхности головки и фиксирующего выс-тупа совпадают при этом сов-падают оси отверстия держав-ки и отверстия в режущей пластине.
для выпол-нения токарной операции
Проведенный патентный поиск позволил выявить 5 конструкций режущего инструмента из которых была выбрана одна наиболее подходящая конструкция которая может быть использована на токарной операции. Конструкция рассмотренных расточных инструментов и их описание смотри в приложенных авторских свидетельствах.
заключение и литература.doc
В технологической части подробно рассмотрены вопросы получения заготовки выбор схем базирования произведен расчет припусков а также режимов резания и норм времени. Был усовершенствован и сокращен технологический маршрут изготовления деталей что позволило сократить время и повысить качество произведенной продукции.
В конструкторской части представлено описание станочного и контрольного приспособления. Выполнены все необходимые расчеты по станочному приспособлению.
В исследовательской части рассмотрены вопросы нанострктурного покрытия.
Произведен патентный поиск по теме «прогрессивный режущий инструмент».
Для выполнения курсового проекта использовались разработки программного обеспечения.
Технико-экономическая эффективность спроектированных или существующих процессов обработки деталей оценивается технико-экономическими показателями.
К числу наиболее характерных технико-экономических показателей относятся следующие:
себестоимость детали слагающаяся из затрат на материал основной заработной платы производственных рабочих и цеховых накладных расходов.
Затраты на материал в предлагаемом технологическом процессе меньше чем в базовом так как масса заготовки уменьшена.
себестоимость (цеховая) обработки детали слагающаяся из величины основной заработной платы производственных рабочих и цеховых накладных расходов.
норма штучного времени полной обработки детали.
Тшт базового т.п. = 363 мин
Тшт предлагаемого т.п. = 2791 мин
В предлагаемом технологическом процессе штучное время на выполнение всех операций обработки данной детали в 13 раза меньше чем в базовом.
основное (технологическое) время по всем операциям данной детали.
То базового т.п. = 266 мин
То предлагаемого т.п. = 1869 мин
В предлагаемом технологическом процессе основное время на выполнение всех операций обработки данной детали в 14 раза меньше чем в базовом.
Коэффициент использования станка по основному (технологическому) времени характеризующий долю основного времени в общем времени станка и тем самым
степень автоматизации процесса на станке равен отношению основного времени к штучному.
о базового т.п. = 091
о предлагаемого т.п. = 107
Необходимо стремиться к тому чтобы этот коэффициент был выше или ближе к единице это значит что в общей затрате времени на обработку относительно большее время приходится на работу машины (станка) чем на вспомогательные (ручные) действия что доказывает более эффективное использование машины (станка) и высокую степень механизации и автоматизации процесса обработки.
коэффициент загрузки оборудования по времени характеризующий занятость оборудования равен отношению расчетного количества станков к принятому (фактическому) количеству.
В предлагаемом технологическом процессе этот коэффициент равен 098.
Необходимо стремиться чтобы величина коэффициента также была ближе к единице. Чем ближе величина этого коэффициента к единице тем в большей мере загружено и использовано оборудование.
Заводской технологический процесс разработан для конкретных производственных условий с использованием оборудования имеющегося в цехах с учетом его износа.
При выполнении курсового проекта мною были проработаны следующие вопросы:
сделан анализ базового технологического процесса;
произведено уменьшение количества операций;
применение автоматизированного и механизированного оборудования;
разработано станочное приспособление на токарную операцию.
Все принятые в проекте организационные и технологические решения позволили уменьшить количество оборудования механизировать и автоматизировать процесс обработки детали что привело к снижению себестоимости детали времени на ее обработку повышению производительности точности обработки и качества поверхности детали.
За счет повышения уровня автоматизации технологического
процесса замены устаревшего технологического оборудования на
более современное разработанный технологический процесс при
соответствующей обработки позволяет снизить себестоимость при одновременном увеличении количества обрабатываемых деталей
что должно привести к снижению трудоемкости и нормальным
срокам окупаемости в разработанном технологическом процессе.
Список использованной литературы
Барановский Ю.В. Режимы резания металлов. М. :Машиностроение 1972.
Белкин И.Г. Допуски и посадки -М. :Машиностроение 1992г
Вестник машиностроения №7 1999г.
Горбацевич А.Ф. Шкред В.А. Курсовое проектирование по технологии машиностроения. Минск: Высшая школа 1983. 256с.
Дипломное проектирование по технологии машиностроенияПод общ. ред. Бабука В.В. - Минск: Высшая школа 1979. 464с.
Добрыднев И.С. Курсовое проектирование по предмету технология машиностроения-М.: Машиностроение 1985г.
Егоров М.Е. Технология машиностроения. М. :Высшая школа 1976.
Корсаков В.С. Основы технологии машиностроения. М.:Машиностроение 1973.
Марочник сталей и сплавовПод ред. В.Г. Сорокина.-М.: Машиностроение 1989.
Маталин А.А. Технология машиностроения. М.:Машиностроение1985
Методические указания к выполнению курсового проекта по технологии машиностроения. Под ред. Гусева В.Г. В.: ВПИ 1991г.
Методические указания к курсовому и дипломному проектированиюПод ред. Гусева В.Г. -Влад. политех. ин-т. Владимир 1984.
Методические указания по оформлению технологической документации при выполнении курсовых и дипломных проектовВлад. гос. ун-т. сост.: Гусев Г.В. Жарков В.Н. Владимир 1998. 68с.
Нормативный документ Станки металлообрабатывающие ГОСТ 12.2.003.-80.
Обработка металлов резанием. Справочник технологаПод ред. Панова А.А.-М.:Машиностроение 1988.
Общемашиностроительные нормативы времени вспомогательного на обслуживание рабочего места и подготовительно-заключительного для технического нормирования станочных работ. Серийное производство. М.: Машиностроение 1975.
Общемашиностроительные нормативы режимов резания для технического нормирования работ на металлорежущих станках. — М.: Машиностроение 1974. Ч.1 — 416 с. Ч.2.
Прилуцкий В.А. Технологические методы снижения волнистости поверхностей. – М.: Машиностроение 1978. - 136с.
Разработка технологических процессов и наладок механической обработки и сборки деталей: Учеб. пособиеВ.В.Морозов А.Г.Схиртладзе В.Н.Жарков и др.; Влад. гос. ун-т. Владимир 2002.
Справочник Приспособления для металлорежущих станков под ред. Горошкина А.К. М.: Машиностроение 1979г.
Справочник технолога машиностроителяПод ред. А.Г.Косиловой Р.К.Мещерякова.- М.:Машиностроение1985.Т1. 656с.
Справочник технолога машиностроителяПод ред. А.Г.Косиловой Р.К.Мещерякова.- М.:Машиностроение1985.Т2. 496с.
Общая часть.doc
Т25Б.21.219 – вал нижний входит в узел муфты сцепления трактора Т30-69. Муфта сцепления обеспечивает передачу крутящего момента от двигателя к главной передаче трактора. Вал нижний передает вращение через шестерню и вал приводной на вал отбора мощности.
Трактор предназначен для различных работ. Его основные характеристики:
расход топлива на 100 км пути – 58 л;
марка и тип – Д21АЭ внутреннего сгорания двигателя – 4-х тактный
число передач – вперед 8 назад – 6.
Вал нижний устанавливается в расточенные отверстия корпуса соединительного. На шлицевую часть переднего конца устанавливается шестерня на шлицевую часть заднего конца – муфта соединительная. На диаметр 25 устанавливается шарикоподшипник и от смещения стопорится стопорным кольцом.
Материал Сталь 18ХГТ ГОСТ4543-71.
Так как к детали предъявляется повышенная точность она должна удовлетворять следующим техническим требованиям:
311 387 НВ ГОСТ8479-70 кроме поверхностей обозначенных особо.
Допуски припуски кузнечные напуски поковки по классу точности Т5 ГОСТ 7505-89. Остальные ТТ к поковке по ГОСТ 8479-70.
На поверхности детали не допускаются трещины плены забоины волосовины и расслоение металла.
Шлифованные поверхности детали не должны иметь рисок черноты и следов резца.
Допуск непостоянства диаметра поверхности Б в продольном и поперечном сечении 0007 мм.
Поверхности Б и Г не должны иметь рисок черновин и следов резца.
Химический состав физические и механические свойства материала детали.
Деталь изготавливается из стали 18ХГТ ГОСТ 4543-71.
Сталь 18ХГТ – введение титана в хромомарганцевую сталь делает ее более мелкозернистой более вязкой и несколько увеличивает прокаливаемость. Это позволяет применять сталь для изготовления ответственных деталей машин – валов шатунов шестерен.
Вследствие некоторой склонности к отпускной хрупкости желательно производить после высокого отпуска ускоренное охлаждение изделий. Сталь марки 18ХГТ может применяться как для цементуемых изделий так и для изделий подвергаемых улучшению.
Горячая деформация производится в интервале 1200 - 900°С. Обрабатываемость резанием хорошая свариваемость удовлетворительная склонность к отпускной хрупкости значительная.
Сталь марки 18ХГТ обладает некоторой склонностью к отпускной хрупкости и флокеночувствительна.
Химический состав стали 18ХГТ в %
Механические свойства стали 18ХГТ
Физические свойства стали 18ХГТ
КСИ (ударная вязкость) – 59Джсм2
Коэффициент линейного расширенияа*10 6 мммм*град в интервале 20-100оС 134
Теплопроводность в калсм*сек*град при 100оС 0111
2. Исходные данные для курсового проектирования.
Исходные данные для разработки технологического процесса механической обработки детали «Вал нижний» включают в себя:
Справочную информацию;
Нормативно-техническую информацию;
Научно-техническую литературу;
Периодическую и патентную литературу.
Базовая информация – это информация которая собирается в условиях базового завода. Сюда входит рабочий чертеж детали с техническими требованиями и техническими условиями; программа выпуска N в моем случае равна 3720 штук в год; заводская технология обработки детали а именно станки приспособления измерительные и режущие инструменты нормы времени режимы резания на каждую операцию припуски; расценки на операцию; имеющаяся производственная площадь; наличие рабочей силы и кадры технологов; место расположения где будет расположен проектируемый технологический процесс; виды источников энергии.
В справочную информацию входит информация содержащаяся в справочниках ТМС нормировщика металлиста конструктора и т.д.; каталоги выпускаемые предприятиями РФ и зарубежными фирмами.
В нормативно-техническую информацию входят ГОСТы стандарт СЭВ стандарты РФ машиностроительные нормы стандарты предприятий и др.
Научно-техническая литература – это монографии научные статьи диссертации журналы «Вестник машиностроения» «Машиностроитель» и др.
Патентная литература – это совокупность авторских свидетельств конвенционных заявок и патентов. Обычно публикуются в бюллетенях «Открытия изобретения образцы и товарные знаки» а также в бюллетенях стран мира.
Кроме этого исходными данными являются трудоемкость и станкоемкость операций механической обработки детали «Вал нижний» необходимые при расчете механического цеха; номенклатура изделий изготовляемых в цехе; действительный фонд рабочего времени оборудования F=20075 часов в год при работе в 1 смену; действительный фонд рабочего времени рабочих F=1840 часов при работе в 1 смену; число смен работы предприятия – 2 смены.
Технологич. часть.doc
1. Определение типа производства.
Тип производства существенно влияет на всю технологию механической обработки а именно на модели станков на силовые и контрольные приспособления на оформление технологической документации.
В массовом производстве следует применять станки-автоматы автоматические линии автоматически действующие силовые и контрольные приспособления специальный режущий и измерительный инструмент вместе со стандартным. Здесь нельзя применять универсальные станки так как они не справятся с программой выпуска.
В крупносерийном производстве следует применять групповую технологию. В этом типе производства следует применять агрегатные станки станки полуавтоматы применяются станки с ЧПУ роботизированные технологические комплексы.
В мелкосерийном производстве применяются универсальные станки и кроме обычной технологи необходимо разработать рабочую управляемую программу для механической обработки детали.
Тип производства определяется коэффициентом закрепления операции Кз.о. при Кз.о. = 1 - производство массовое
Кз.о. 10 – крупносерийное
Кз.о. 20 - среднесерийное
Кз.о. 40 - мелкосерийное
Кз.о. – единичное производство.
где SО – количество операций выполняемых на участке в течении месяца
SР – количество рабочих мест на участке.
Предварительно тип производства выбирается в зависимости от массы и годовой программы выпуска детали по таблице:
Зависимость типа производства от программы выпуска и массы детали.
Годовая программа данной детали 3720масса детали 134 кг следовательно производство будет среднесерийное.
Тип производства характеризуется коэффициентом закрепления операции за одним рабочим местом или единицей оборудования.
Q – число различных операций кроме термической и контрольной;
Р – число рабочих мест.
При серийном производстве изделия изготовляют партиями или сериями состоящими из одноименных однотипных по конструкции и одинаковых по размерам изделий запускаемых в производство одновременно. Основным принципом этого вида производства является изготовление всей партии (серии) целиком как в обработке деталей так и в сборке.
В серийном производстве технологический процесс преимущественно дифференцирован т.е. расчленен на отдельные операции которые закреплены за определенными станками.
Станки здесь применяются разнообразных видов: универсальные специализированные специальные автоматизированные агрегатные.
Серийное производство значительно экономичнее чем единичное так как лучшее использование оборудования специализация рабочих увеличение производительности труда обеспечивают уменьшение себестоимости продукции.
Расчет такта выпуска.
Такт определяется по формуле:
Фд – действительный годовой фонд рабочего времени час.
Фк – календарный годовой фонд рабочего времени час;
Фк = 20075 ч при работе участка в одну смену;
Фк = 4015 ч при работе участка в две смены;
– коэффициент учитывающий простои оборудования при текущем ремонте и техническом обслуживании;
Фд = 4015 * 093 = 3734 ч.
N – годовой объем выпуска продукции.
= 3734*603720 = 60226 (мин).
Расчет оптимальной величины партии детали.
N – годовая программа выпуска;
а – периодичность в запусках в днях а = 6.
n = 3720*6255 = 87 (шт).
2. Обоснование выбора метода
получения заготовки.
При выборе оптимального способа получения заготовок рассмотрим два варианта: деталь изготавливается из проката - первый вариант штампуется в закрытых штампах - второй вариант. Предпочтение следует отдавать заготовке характеризующейся лучшим использованием материала и меньшей стоимостью.
В машиностроении основными способами получения заготовок являются:
отливки чугунные стальные из цветных металлов из пластмасс;
поковки и штамповки;
прокат стали (горячекатаной и холоднотянутой) и цветных металлов.
Выбор вида заготовок зависит от конструктивных форм деталей их назначения условий их работы в собранной машине испытываемых напряжений и т.д.
После анализа технологического процесса мною была выбрана заготовка – штамповка.
Заготовка в виде штамповки получается ковкой в штампах; последняя имеет значительные преимущества перед свободной ковкой.
В штампованной заготовке структура металла более однородна благодаря чему деталь будет более прочной. Штамповкой получаются размеры наиболее близкие к окончательным; в некоторых производствах штампованные заготовки используются без дальнейшей механической обработки или с очень незначительной обработкой.
При изготовлении штамповок лучше используется металл и уменьшается расход его. Процесс изготовления штамповок по сравнению с ковкой значительно быстрее и требует менее квалифицированной рабочей
силы. Себестоимость заготовок меньше чем кованных.
Массу заготовки приближенно можно определить по формуле:
Мзаг = Vзаг · q = 134 кг где
Vзаг – объем заготовки см3;
q – плотность материала г см3.
Vзаг = V1 + V2 + = 1707 см3 где V = (D2 4)· l
V1=(2782 4)· 25=147 см3
V2=(3232 4)· 38=2862 см3
V3=(3862 4)· 08=812 см3
V4=(3342 4)· 152=8619 см3
V5=(3232 4)· 45=3307 см3
Определяем коэффициент использования материала
КИМ = Мдет Мзаг = 134188 = 071
-й способ. Деталь изготавливается из проката затраты на заготовку определяются по его массе и массе сдаваемой стружки.
M = Q S - ( Q – q ) S 1000 ; руб.
где Q– масса заготовки Q= 238 кг;
q– масса готовой детали q= 134 кг;
Sотх– цена 1тонны отходов Sотх= 1000 рубтонну;
S– цена 1 кг материала заготовки; S=35000 рубтонну.
Подставив значения получим:
M =238×35000-(238-134)·1000 1000 = 8226 руб.
-й способ. Заготовку получают горячей штамповкой в закрытых штампах.
Стоимость заготовки получаемой методом горячей штамповки можно определить по формуле:
S заг. =[( Сi 1000) Q k т k с kв kм kп]-(Q-q) (S отх 1000)
kтkсkвkмkп –коэффициенты зависящие от класса точности группы сложности массы марки материала и объема производства заготовок.
Sзаг=[(163561000)·188·120·115·135·127·107]-(188-134)·(10001000)=
В связи с тем что много металла уходит в стружку при заготовке получаемой из проката и коэффициент использования материала становится менее 07 что нежелательно применяем штамповку получаемую в закрытых штампах.
3. Анализ технологичности конструкции детали.
Отработка конструкции на технологичность представляет собой комплекс мероприятий по обеспечению необходимого уровня технологичности конструкции по установленным показателям направлена на повышение производительности труда снижение затрат и сокращение времени на изготовление изделия при обеспечении необходимого его качества.
В соответствии с ГОСТ 18831-80 оценка технологичности состоит из двух видов: качественной и количественной.
3.1 Количественная оценка технологичности.
Показатели технологичности и их определения.
Трудоемкость изготовления детали характеризует количество затраченного труда на ее производство и определяется в единице рабочего времени по формуле:
Тшт – штучное время на каждой операции.
Коэффициент унифицирования конструктивных элементов детали определяется по формуле:
Kуэ = Qуэ Qэ = 1017 = 059 где
Qуэ – число унифицированных типоразмеров конструктивных элементов;
Qэ – общее число типоразмеров конструктивных элементов.
Коэффициент использования материалов:
Ким = Мд Мз = 134188 = 071 где
Мз – масса заготовки.
Коэффициент точности обработки определяется по формуле:
Кт = 1 – 1Аср = ni Ani = 1 – 199 = 09
Аср = Ani ni = (n1 + 2n2 + 3n3 + ) (n1 + n2 + n3 + ) =
= (6+77+10+6)10 = 99 где
Аср – средний коэффициент точности обработки;
А – квалитет обработки;
n – число размеров соответствующего квалитета.
При Кт = 09 – деталь средней трудоемкости.
Коэффициент шероховатости поверхности:
Кш = 1Бср = 154 = 0185
Бср = Бni ni = 54 где
Бср – средняя шероховатость поверхности определяемая в значениях параметра Ra мкм;
Б – числовое значение параметра шероховатости;
n – число поверхностей соответствующих числовым значениям параметра шероховатости.
При Кш = 0185 – деталь средней трудоемкости.
Анализ каждой поверхности детали.
точение окончательное
точение черновое чистовое
3.2 Качественная оценка технологичности.
Технологический анализ конструкции обеспечивает улучшение технико-экономических показателей разрабатываемого технологического процесса. Основные задачи решаемые при анализе технологичности обрабатываемой детали сводится к возможному уменьшению трудоемкости и металлоемкости возможности обработки детали высокопроизводительными методами. Таким образом улучшение технологичности конструкции позволяет снизить себестоимость ее изготовления без ущерба для ее служебного назначения.
Деталь – вал нижний изготовляется из стали 18ХГТ штамповкой поэтому конфигурация наружного контура не вызывает затруднений при получении заготовки. Конструкция детали допускает применение высокопроизводительных методов обработки.
Большинство обрабатываемых поверхностей являются простыми – наружные поверхности плоскости что увеличивает точность и стабильность обработки которые в значительной степени определяются простотой конструктивных форм.
Все поверхности доступны и открыты для инструмента поэтому не требуется применения специального оборудования и специальных инструменнтов.
Деталь обладает высокой жесткостью поэтому возможно использование высоких режимов резания которые в свою очередь повысят производительность обработки.
На основании количественной и качественной оценки детали можно сказать что конструкция детали «Вал нижний» является технологичной.
4. Выбор схем базирования и закрепления.
Базирование заготовки играет исключительную роль так как неправильно выбранная схема базирования и закрепления сказывается на конечной точности обработки детали а следовательно на ее эксплуатационной надежности. Технологические базовые поверхности необходимо выбирать так чтобы заготовка имела устойчивое и однозначное положение относительно инструмента. Для этого при выборе схемы базирования и закрепления необходимо руководствоваться двумя основными схемами базирования: принципом единства баз и принципом постоянства баз. Принцип единства баз заключается в том что при базировании технологическая и измерительная базы совпадали а еще лучше если совпадают технологическая измерительная конструкторская и сборочные базы. При совпадении технологической и измерительной базы погрешность базирования равна нулю и точность обработки повышается.
Принцип постоянства баз – все операции начиная со второй и до последующей используются одни и те же технологические базы. Нельзя на разных операциях непрерывно менять чистовые базы.
При разработке технологического процесса необходимо учесть следующее что основными задачами являются:
Применение специальных и агрегатных станков позволяет сократить время на наладку и установку детали.
Замена устаревшего оборудования на более новое и современное.
Повышение уровня автоматизации за счет модернизации технологической оснастки и средств контроля.
При установке деталей для обработки на станках различают следующие поверхности:
обрабатываемые поверхности с которых режущими инструментами снимается слой металла;
поверхности базы определяющие положение детали при обработке;
поверхности воспринимающие зажимные силы;
поверхности от которых измеряют выдерживаемые размеры;
необрабатываемые поверхности.
Базами могут служить поверхности линии точки и их совокупности.
От правильного выбора технологических баз во многом зависит точность обработки детали.
Рекомендации по выбору баз:
установочная база должна иметь достаточные размеры чтобы обеспечить устойчивое положение заготовки при обработке;
на первой операции обрабатывают поверхность которая в дальнейшем служит основной установочной базой;
при выборе чистовых баз нужно стремиться к тому чтобы установочные базы совпадали с измерительными или конструкторскими базами. В этом случае погрешность базирования равна нулю (принцип совмещения баз);
при выборе чистовых баз нужно стремиться к тому чтобы на всех операциях вести обработку от одних и тех же установочных баз (принцип постоянства баз).
Для данной детали черновые базы – наружный диаметр и торец чистовые базы – центровые отверстия.
5. Критический анализ заводской технологии.
Базовый технологический процесс
Наименование операции
5 фрезерно-центровальная
Фрезерно-центровальный па мод.2Г942
5-1 фрезерно-центровальная
Фрезерно-центровальный мод.МР76АМ
0 токарно-копировальная
Токарно-копировальный мод.ЕМ473
5 токарно-копировальная
0 специальная фрезерная
Шлицефрезерный мод.5А352ПФ2
5 специальная фрезерная
Перемещение деталей в термический цех и обратно
5 круглошлифовальная
Круглошлифовальный мод.3М151
0 круглошлифовальная
0 специальная шлифовальная
Шлицешлифовальный мод.МШ355М
5 специальная шлифовальная
В базовом техпроцессе в основном применяется специальное
технологическое оборудование и специальный режущий инструмент. Деталь обрабатывается на многих станках которые установлены в различных местах цеха а следовательно много времени уходит на транспортировку детали.
6. Разработка технологического маршрута и выбор оборудования.
На основании анализа технологического процесса был разработан технологический маршрут и выбрано современное оборудование и СОЖ для обработки детали.
Технологический процесс обработки детали «Вал нижний».
Фрезерноцентровальный па мод.2Г942
Токарный гидрокопировальный па мод.1Е713
Шлицефрезерный па мод.5350А
0 электрохимзачистная
Электрохимическая установка мод.4407
5 кругло-шлифовальная
Кругло-шлифовальный мод.3М153У
0 кругло-шлифовальная
Шлицешлифовальный мод.3451В
Моечная машина мод.ОСМ-1
При выборе модели станка руководствуются следующими соображениями:
функциональным назначением и технологическими возможностями станка;
обеспечение требующейся точности;
обеспечение необходимой мощности;
уровень механизации и автоматизации;
В последнее время получило широкое распространение обтачивание ступенчатых валов на токарных станках с копировальными устройствами или на токарно-копировальных станках со следящей системой.
Гидрокопировальные станки благодаря значительной жесткости конструкции обеспечивают большую точность и более высокий класс чистоты обработки чем универсальные станки со специальными гидрокопировальными суппортами.
Рассматривая процесс обработки на гидрокопировальных полуавтоматах следует отметить что обтачивание на этих станках имеет во многих случаях ряд преимуществ перед обтачиванием на многорезцовых станках.
Так как для обтачивания на гидрокопировальных полуавтоматах используется обычно один резец установка копира и кинематическая наладка сравнительно просты время на наладку и подналадку таких полуавтоматов значительно (в 2-3 раза) меньше чем на наладку многорезцовых станков; она занимает примерно 20-40 мин.
Помимо этого на гидрокопировальном автомате обработку можно вести с более высокими скоростями чем на многорезцовых станках т.е. при относительно малой затрате основного времени.
Техническое обслуживание гидрокопировальных полуавтоматов проще и не требует меньше времени чем многорезцовых станков.
В результате указанных преимуществ во многих случаях штучно-калькуляционное время на обработку детали на гидрокопировальных полуавтоматах меньше а производительность больше чем на горизонтальных многорезцовых полуавтоматах.
Модели принятых станков и их характеристика.
Шлицешлифовальныймод.3451В
Принято 13 единиц оборудования механизированы все станков – полуавтоматов – 8.
Коэффициент применения станков – полуавтоматов:
Спа = nпа nобщ = 813 = 062.
Выбор универсальной (нормализованной) технологической оснастки.
Сводная ведомость оборудования.
фрезерно-центровальная
Тиски самоцен-трирующие;
токарно-копировальная
Резец проходной упорный
Резец канавочный ВК8
Продолжение таблицы 2.6.3.
Круг ПП600х63х305 В=10
Центр задний Морзе 4;
Центр передний Морзе 4
Центр передний Морзе 4
Центр передний поводковый;
7. Расчёт припусков на механическую
Минимальные значения межоперационных припусков определяем по формуле:
Rz – величина шероховатости полученная на предыдущем переходе
h i-1 - глубина дефектного поверхностного слоя на предшествующим переходе
i – погрешность установки заготовки на выполняемом переходе.
Кривизна заготовки определяется по формуле:
где -удельная кривизна стержня;
Величины припусков на обработку и допуски на размеры заготовок зависят от ряда факторов степень влияния которых различна; к числу основных факторов относятся следующие:
конфигурация и размеры заготовки;
вид заготовки и способ ее изготовления;
требования в отношении механической обработки;
технические условия в отношении качества и класса шероховатости поверхности и точности размеров детали.
Величина общего припуска зависит от толщины дефектного поверхностного слоя подлежащего снятию и припусков необходимых для всех промежуточных операций механической обработки – межоперационных припусков.
Расчет межоперационных припусков.
Продолжение таблицы 2.7.1
8. Расчет режимов резания.
Назначение рационального режима резания заключается главным образом в выборе наиболее выгодного сочетания скорости резания и подачи обеспечивающих в данных условиях с учетом целесообразного использования режущих свойств инструмента и кинематических возможностей оборудования наибольшую производительность общественного труда и наименьшую стоимость операции.
Выбранный режим резания должен удовлетворять условиям:
N ≤ Nэ и 2М ≤ 2Мст где
N – мощность потребная на резание кВт;
Nэ – эффективная мощность станка кВт;
М – двойной крутящий момент при резании кг·м;
Мст – двойной крутящий момент на шпинделе станка кг·м.
Расчет режимов резания (по нормативам) на операцию
5 Фрезерно-центровальная
станок – фрезерно-центровальный па мод.2Г942
обрабатываемый материал – сталь 18ХГТ
обработка – фрезерование торцев центровка отверстий (сверление центровых отверстий)
заготовка – штамповка
Устанавливаем глубину резания.
Припуск снимаем за один рабочий ход; следовательно t=h=3 мм (на обе стороны).
Назначаем подачу на зуб фрезы.
Для стали твердого сплава Т15К6 мощности станка Nд=14 кВт Sz= 018 022 ммзуб. Принимаем Sz= 018 ммзуб. Поправочный коэффициент на подачу КφSz= 1 т.к. угол φ= 60º. Таким образом принятое значение Sz= 018 ммзуб не изменяется.
Назначаем период стойкости фрезы.
Для торцовой фрезы из твердого сплава диаметром D= 160мм рекомендуется период стойкости Т= 240 мин.
Определяем скорость (ммин) главного движения резания допускаемую режущими свойствами фрезы.
Находим табличное значение скорости Vтабл= 194 ммин. Учитываем поправочные коэффициенты на скорость; КМV= 112; КПV= 09. С учетом коэффициентов VU= Vтабл КМV КПV= 1955 ммин.
Частота вращения шпинделя соответствующая найденной скорости главного движения резания:
n= 1000 VU D = 1000*1955314*160= 389 мин-1.
Корректируем частоту вращения шпинделя по данным станка и устанавливаем действительную частоту вращения nд = 500 мин-1.
Действительная скорость главного движения резания.
Vд = D nд 1000 = 314*160*5001000= 2512 ммин.
Корректируем по данным станка: Vд = 250 ммин.
Определяем скорость движения подачи.
VS = SM = SzZnд = 018*6*500= 540 мммин.
Корректируем эту величину по данным станка и устанавливаем действительную скорость подачи VS = 500 мммин.
Определяем мощность затрачиваемую на резание.
Учитываем поправочные коэффициенты на мощность: КφN = 1
т.к. у фрезы принят угол φ= 60º; КγN = 095 т.к. у фрезы принят угол γ = -5º; Nрез = Nтабл КγN = 63*095= 60 кВт.
Проверяем достаточна ли мощность привода станка.
Необходимо выполнить условие Nрез≤ Nшп. Мощность на шпинделе станка Nшп= Nд = 10 кВт*08= 8 кВт. Следовательно обработка возможна (60 80).
Основное время на операцию выполняемую на фрезерных станках подсчитывается по формуле:
L – длина пути проходимого инструментом в направлении подачи;
SM – подача фрезы в 1 мин;
Сверление центровых отверстий
t = 05D = 05*106= 53 мм.
Максимально допустимая подача при сверлении без учета ограничивающих факторов берем из справочника 008 018 принимаем S= 01 ммоб.
Скорость резания рассчитываем по формуле:
V = (CV*Dqv Tm*txv*Syv)*KV (ммин)
KV = KMV*KUV*KlV = 0.8*1*1=0.8
V = (7*10.60.4250.2*5.30*0.10.7)*0.8 = 3787 ммин.
Принимаем V= 35 ммин (по паспорту станка).
Крутящий момент рассчитываем по формуле:
M= CM*DqM*SyM*KP кг м;
PO= CP*DqP*SyP*KP кг
KP= KMP= (7575)075= 1.
М= 00345*10620*0108*1= 062 кг м
РО= 68*10610*0107*1= 14416 кг
Мощность резания определяем по формуле:
n = 1000*35314*106= 510 мин—1
Принимаем по паспорту станка n= 500 мин-1.
N= 062*510975= 317 кВт что соответствует Nрез≤ Nшп.
Основное время на операцию выполняемую при сверлении подсчитывается по формуле:
n – число оборотов инструмента;
s – подача подача инструмента за один оборот;
Сводная ведомость режимов резания
Номер и обозначение операции
подрезка торца точение канавки
Продолжение таблицы 2.8.1
точение поверхности вала
фрезерование 6 шлицев
шлифование поверхности
шлифование поверхности
9. Нормирование технологической
Под техническим нормированием понимается установление нормы времени на выполнение определенной работы или нормы выработки в
штуках в единицу времени.
Правильное нормирование затраты рабочего времени на обработку детали имеет весьма большое значение для производства.
Норму времени определяют на основе технического расчета и анализа исходя из условий возможно более полного использования технических возможностей оборудования и инструмента в соответствии с требованиями к обработке данной детали.
Определяем норму штучного времени на операцию:
Тшт = 11(То +Тв) мин
Тв – вспомогательное время на операцию;
То – основное время необходимое для изменения формы и размера заготовки.
Тв = Туст + Тпр.упр + Тконтр
Туст – время на установку и снятие детали мин;
Тпр.упр – время связанное с управлением станком мин;
Тконтр – время на контроль детали мин.
Тв = 025+015+03=07 мин
Тшт = 11*(07+018) = 096 мин.
0 токарно-копировальная.
Тв = 01+001+0116+007=0224 мин
Тшт = 11*(0224+136) = 18 мин.
5 токарно-копировальная.
Тв = 04+001+024=065 мин
Тшт = 11*(065+122) = 203 мин.
0 электрохимзачистная.
Тв = 01+001+016=027 мин
Тшт = 11*(027+099) = 138 мин.
Тв = 023+017+02=06 мин
Тшт = 11*(06+102) = 199 мин.
Сводная ведомость норм времени
035 версия5.cdw

035-2лист версия5.cdw

055 версия5.cdw

075-2лист.cdw

060-2лист.cdw

контроль2.doc
Наименование операции
Наименование марка материала
Сталь 18ХГТ ГОСТ4543-71
Наименование оборудования
Контролируемые параметры
Наименование средств ТО
Отсутствие заусенцев
ОК Операционная карта технического контроля
Допуск на радиальное биение
Допуск на параллельность шлицев
060-2лист версия5.cdw

055.cdw

065-2лист версия5.cdw

ТП-МАРШРУТНЫЙ-вал нижний.doc
Сталь 18ХГТ ГОСТ4543-71
Код. наименование операции
Обозначение документа
Код. наименование оборудования
69 Фрезерно-центровальная
Фрезерно-центровальный па
17 Токарно-копировальная
Токарный гидрокопировальный па
Шлицефрезерный па 381672.ХХХХ.5350А
Шлицефрезерный па 381672.ХХХХ5350А
90 Электрохимзачистная
Отделочно-зачистной станок
Хххххх Стол контролера
ГОСТ 3.1118—82 Форма 1б
хххххх установка ТВЧ
31 Кругло-шлифовальная
Круглошлифовальный 381311.ХХХХ. 3М153У
ХХХХ Шлицешлифовальная
Шлицешлифовальный станок
xxxxxx моечн.машина ОСМ -1
xxxxxx стол контролера
Владимирский Государственный Университет
Комплект документации
технологического процесса
(фамилия имя отчество)
010 версия5.cdw

** Размеры обеспечиваются инструментом.
045.cdw

020-2лист.cdw

** Размеры обеспечиваются инструментом.
005.cdw

** Размеры обеспечиваются инструментом.
040.cdw

020-2лист версия5.cdw

** Размеры обеспечиваются инструментом.
035-2лист.cdw

025-2лист.cdw

** Размеры обеспечиваются инструментом.
025 версия5.cdw

025-2лист версия5.cdw

** Размеры обеспечиваются инструментом.
055-2лист.cdw

060.cdw

010.cdw

** Размеры обеспечиваются инструментом.
025.cdw

055-2лист версия5.cdw

040 версия5.cdw

075-2лист версия5.cdw

065.cdw

050 версия5.cdw

060 версия5.cdw

065-2лист.cdw

075 весия5.cdw

020 версия5.cdw

015.cdw

065 версия5.cdw

ТП-ОПЕРАЦИОННЫЙ.doc
Наименование операции
Фрезерно-центровальная
Оборудование устройство ЧПУ
Обозначение программы
Фрезерно-центровальный па
Установить и закрепить деталь
Фрезеровать деталь с 2-х сторон выдерживая размеры: 4; 6
хх хххх Поводок ø50х37; хххххх Фреза ø160х57 ; хххххх Скоба 257h14
Центровать деталь с 2-х сторон выдерживая размер 5
хх хххх Оправка; хх хххх Втулка; хх хххх Цанга; хххххх Фреза ø160х57 ; хххххх Сверло ø5;
Токарно-копировальная
Токарный гидрокопировальный па
Установить и закрепить деталь в приспособление
Точить поверхности выдерживая размеры: 2; 3; 4; 6
хх хххх Центр задний; хх хххх Патрон; хх хххх Резец 25х25 Т5К10; хх хххх Пластина; хххххх Скоба 36 хххххх Скоба 308h12
Подрезать торцы и проточить канавки выдерживая размеры: 1; 5; 7 - 20
хх хххх Кулачок; хх хххх Копир;хх хххх Резец канавочный Т5К10; хх хххх Державка; хххххх Скоба 258 хххххх Скоба 235
хххххх Скоба 245 хххххх Скоба295h14
Токарный гидрокопировальный па мод.1Е713
Установить деталь в приспособление и закрепить
Точить поверхности вала выдерживая размеры 1 - 8
хх хххх Центр задний; хх хххх Патрон; х хххх Кулачок; хх хххх Копир; хх хххх Резец проходной упорный Т5К10; хх хххх Пластина;
Хххххх Державка; хххххх Скоба 31 Скоба 6±015; хххххх Шаблон 153±05; хххххх Радиусный шаблон; хххххх Скоба 308
Шлицефрезерный па мод.5350А
Установить деталь в приспособление
Фрезеровать 6 шлицев выдерживая размеры 1 – 5
хххххх Центр передний; хххххх Центр задний; хххххх Оправка; хххххх Втулка; хххххх Фреза Р9; хххххх Скоба 84-011; хххххх Скоба 238-084;
Электрохимический мод.4407
Удалить заусенцы = 5000А
Промыть в растворе РИК струйным методом 2 3 ггсм2; t = 35 40°С
Сушить сжатым воздухом 3 4 ггсм2; t = 30 40°С
Калить деталь 52 HRC.
Круглошлифовальный станок мод.3М153У
Установить деталь в центра и закрепить
Шлифовать поверхность выдерживая размер 1
хххххх Центр передний Морзе 4; хххххх Центр задний Морзе 4; хххххх Поводок; хххххх Круг пп600х63х305; хххххх Скоба 30 хххххх Прибор
хххххх Центр передний Морзе 4; хххххх Центр задний Морзе 4; хххххх Поводок; хххххх Круг ø600х63х305; хххххх Скоба 30 хххххх Прибор
хххххх Центр передний Морзе 4; хххххх Центр задний Морзе 4; хххххх Поводок; хххххх Круг ПП 600х63х305; хххххх Скоба 25 хххххх Прибор
Шлицешлифовальный мод.3451В
Шлифовать 6 шлицев выдерживая размеры 1 - 3
хх хххх Центра; хххххх Втулка; ххххххДержавка; хххххх Оправка; хххххх Круг 4Кх8х20; хххххх Скоба 8; хххххх Приспособление;
хх хххх Приспособление для контроля
хх хххх Центр; хххххх Втулка; ххххххДержавка; хххххх Оправка; хххххх Круг Р14; хххххх Скоба 8; хххххх Приспособление; хххххх Кольцо
035.cdw

075.cdw

контроль1.doc
Наименование операции
Наименование марка материала
Сталь 18ХГТ ГОСТ4543-71
Наименование оборудования
Контролируемые параметры
Наименование средств ТО
Отсутствие заусенцев
ОК Операционная карта технического контроля
Допуск на радиальное биение
допуск на параллельность шлицев
045 версия5.cdw

050.cdw

020.cdw

015 версия5.cdw

010-2лист.cdw

005 версия5.cdw

** Размеры обеспечиваются инструментом.
010-2лист версия5.cdw

Введение.doc
Совершенствование технологических методов изготовления машин имеет при этом первостепенное значение качество машины надежность долговечность и экономичность в эксплуатации зависят не только от совершенства её конструкции но и от технологии производства. Применение прогрессивных высокопроизводительных методов обработки обеспечивающих высокую точность и качество поверхностей деталей машины методов упрочнения рабочих поверхностей повышающих ресурс работы деталей и машины в целом эффективное использование современных автоматических и поточных линий станков с ЧПУ электронных вычислительных машин и другой новой техники - все это направлено на решение главной задачи:
повышения эффективности производства и качества продукции.
Трактор Т-30 предназначен для механизированной обработки полей посева различных культур урожая транспортировки различных грузов и тому подобное. В условиях рыночных экономических отношений возникает объективная жизненно важная необходимость в повышении конкурентоспособности выпускаемой продукции.
Для сохранения конкурентоспособности продукции необходимо постоянно совершенствовать разрабатывать и производить новые реконструировать старые цеха и заводы внедрять прогрессивные технологические процессы.
Решение этих задач в экономике требует также принципиально новых более глубоких хозяйственных и производственных отношений создания эффективной и гибкой системы управления позволяющей полнее реализовать возможности производства.
В данном курсовом проекте разработан рассчитан прогрессивный сборный абразивный инструмент для шлифования шлицев торца и поверхностей вала применение которого позволило повысить качество и производительность технологических операций. Заменено устаревшее оборудование на прогрессивное с ЧПУ. Был усовершенствован и сокращен технологический маршрут изготовления детали. Все эти изменения позволили увеличить режимы резания что позволило уменьшить штучное калькуляционное время повысить качество произведенной продукции и понизить себестоимость детали «Вал нижний».
оглавление.doc
2 Исходные данные для курсового проектирования 5
Технологическая часть . 7
1 Определение типа производства . 7
2 Обоснование выбора метода получения заготовки 10
3 Анализ технологичности конструкции детали .. 15
4 Выбор схем базирования и закрепления детали 18
5 Критический анализ базового техпроцесса 20
6 Разработка технологического маршрута и выбора оборудования 21
7 Расчет припусков на механическую обработку . 26
8 Расчет режимов резания 28
9 Нормирование технологических операций 33
Патентные исследования .. 37
1 Справка о проведении патентного поиска 38
2 Патентный обзор 40
Научно-исследовательская часть . 44
Конструкторская часть . 58
1 Описание конструкции станочного приспособления 59
2 Силовой расчет станочного приспособления . 60
3 Точностной расчет станочного приспособления 61
4 Описание и принцип действия контрольного приспособления 65
Список использованной литературы 70
Рекомендуемые чертежи
- 24.01.2023
- 01.07.2014
- 04.06.2017