Разработка технологического процесса по обработке детали Винт




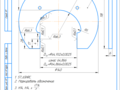



- Добавлен: 24.01.2023
- Размер: 870 KB
- Закачек: 1
Описание
Состав проекта
![]() |
![]() |
![]() ![]() ![]() |
![]() ![]() ![]() |
![]() |
![]() ![]() ![]() ![]() |
![]() ![]() ![]() ![]() |
![]() ![]() ![]() ![]() |
![]() |
![]() ![]() ![]() ![]() |
![]() ![]() ![]() ![]() |
![]() ![]() ![]() ![]() |
![]() ![]() ![]() ![]() |
![]() ![]() ![]() ![]() |
![]() ![]() ![]() ![]() |
![]() ![]() ![]() |
![]() ![]() ![]() ![]() |
![]() ![]() ![]() ![]() |
![]() ![]() ![]() ![]() |
![]() ![]() ![]() ![]() |
![]() ![]() ![]() ![]() |
![]() ![]() ![]() |
![]() ![]() ![]() ![]() |
Дополнительная информация
Винт_ПЗ.doc
1.Описание конструкции детали и её назначение4
2.Анализ детали на технологичность.5
2.Характеристика материала8
Технологическая часть9
1 Определение типа производства9
2. Выбор заготовки11
3. Определение припусков табличным методом15
4. Обоснование выбора баз.16
5. Заводской маршрут обработки детали.18
6 Анализ заводского техпроцесса.20
7. Принятый маршрут обработки детали21
8. Выбор оборудования22
9.Выбор режущего инструмента30
10.Выбор мерительного инструмента30
11 Расчет режимов резания и нормирование операции31
11.2. Операция 040 Радиально - сверлильная31
10.2. Операция 080 - Горизонтально - фрезерная31
Конструкторская часть.31
1 Конструирование и расчёт режущего инструмента.31
2. Конструирование и расчет приспособления31
3. Расчет мерительного инструмента31
Технологический процесс охватывает работы непосредственно связанные с превращением сырья в готовую продукцию. Технологический процесс — основная часть производства (производственного процесса).
Технологический процесс состоит из целого ряда производственных операций которые выполняются в строго определенной последовательности. Производственной операцией называется часть технологического процесса выполняемая на определенном рабочем месте определенным инструментом или на определенном оборудовании.
Операции следуют в технологическом процессе в строго установленном порядке. Например за разметкой следует раскрой досок на заготовки для деталей далее идет строгание оторцовывание выработка шипов выдалбливание гнезд и т. д. Никто не станет запиливать шипы у нестроганых деталей или шлифовать деталь прежде чем ей не придана окончательная форма строганием.
Степень пооперационной расчлененности технологического процесса зависит от объема работы по изготовлению данного изделия от количества рабочих занятых изготовлением изделия от размеров производственного помещения (рабочей площади) от характера оборудования рабочих мест и других условий производства. Самым глубоким расчленением технологического процесса на операции нужно считать такое когда каждая операция выполняется за один прием без смены инструмента. Чем меньше операция тем она проще и доступнее для выполнения. Поэтому чем глубже пооперационное расчленение технологического процесса тем выше производительность труда и меньше потребность в высокой квалификации работающих.
Технологический процесс может быть общим на изготовление всего изделия или охватывать например только операции обработки деталей только операции сборки или операции отделки изделий.
Не следует смешивать технологический процесс с технологией производства. Под технологией производства нужно понимать не только последовательность выполняемых операций но также приемы и способы выполнения этих операций. Технология производства должна строиться на основе новейших достижений науки и техники с учетом опыта работы новаторов и рационализаторов.
Целью данного курсового проекта является разработка оптимального технологического процесса изготовления детали.
1.Описание конструкции детали и её назначение
Деталь «Винт» массой 45 кг изготовлена из жаропрочного сплава ХН35ВТЮ и предназначена для соединения деталей.
Деталь имеет форму тела вращения Dmax = 135 мм длина 220 мм. Деталь состоит из 4 ступеней:
-первая цилиндрическая ступень 135-04 мм длиной 70 мм с двумя зубьями расположенными по вертикальной оси симметрии.
-вторая с посадочным диаметром 65е9мм длиной 58 мм
-третья ступень резьбовая с метрической резьбой М64-8g.
-четвертая цилиндрическая ступень 56 мм имеет кольцевую канавку R25 и паз с max R=315 мм шириной 10мм и глубиной 25 мм.
В центе детали имеется сквозное четырехступенчатое отверстие:
- первая ступень – цилиндрическая 110 и длиной 35+1 мм
- вторая 74 длиной 25 мм с кольцевой проточкой 76 длиной 2 мм
- третья ступень 40H12 длиной 20 мм
- четвертая ступень 33 длиной 140 мм
2.Анализ детали на технологичность.
Каждая деталь должна изготавливаться с минимальными трудовыми и материальными затратами. Эти затраты можно сократить в значительной степени правильным выбором варианта технологического процесса его оснащения механизации и автоматизации применение оптимальных режимов обработки. На трудоемкость изготовления детали оказывают особое влияние ее конструкция и технические требования на изготовление.
Оценку технологичности проводят по количественным и качественным показателям.
Качественная оценка технологичности
Требования технологичности
Характеристика технологичности
Деталь должна изготавливаться из стандартных или унифицированных заготовок.
Свойства материала детали должны удовлетворять существующей технологии изготовления хранения и транспортировки.
Конструкция детали должна обеспечить возможность применения типовых групповых или стандартных технологических процессов.
Конструкция детали должна обеспечивать возможность многоместной обработки.
Возможность обработки максимального количества размеров высокопроизводительными методами и инструментами.
Перепад размеров должен быть минимальным.
Отсутствие глубоких отверстий малого диаметра.
Форма конструктивных элементов детали (КЭД) – фасок канавок и т.п. Элементов должна обеспечивать удобный подвод инструмента.
Унификация КЭД для использования при обработке станков с программным управлением.
Вывод: данная деталь имеет конструкцию которую надо признать технологичной т.к. удовлетворяет всем требованиям при отработке конструкции на технологичность.
Количественная оценка технологичности
Количественная оценка определяется расчетом ряда показателей характеризующих отдельные свойства. Для оценки технологичности конструкции могут быть использованы следующие показатели:
Коэффициенты унификации.
где - число унифицированных элементов детали шт.
- общее число конструктивных элементов детали шт.
Коэффициенты точности обработки детали:
где - средний квалитет;
- число размеров соответствующего квалитета.
Коэффициенты шероховатости:
где - средний класс шероховатости;
- класс шероховатости;
- число поверхностей соответствующего класса шероховатости
Коэффициенты использования материала при существующем методе получения заготовки:
где - масса детали кг
- масса заготовки кг.
Вывод: количественная оценка технологичности показала что сложность изготовления деталей средняя т. к. Ктч=093%; коэффициент унификации не выходит за допустимые пределы 04-06; КИМ = 018 не удовлетворяет требованиям при которых должно достигаться условие КИМ ³ 06. Следовательно требуется пересмотреть метод получения заготовки.
2.Характеристика материала
Сплав жаропрочный ХН35ВТЮ – ВД (ТУ 14-1-1589-76) применяется для изготовления рабочих лопаток газотурбинных и других двигателей работающих при температуре до 700-800°С компрессорных лопаток работающих до 700-800°С дисков дефлекторов колец работающих при температуре до 750°С.
Химический состав %:
Механические свойства при Т=20ºС:
Технологические свойства материала:
Трудносвариваемая. Способ сварки - РДС электродами ЦТ-22. Для снятия сварочных напряжений рекомендуется последующая термообработка.
Температура ковки: Начала - 1110°С конца - 900°С. Сечения до 450 мм охлаждаются на воздухе.
Технологическая часть
1 Определение типа производства
Предварительно тип производства можно определить по таблице в зависимости от массы детали ритма ее выпуска сложности изготовления и программы.
Масса детали определяется по чертежу детали. Ритм выпуска по формуле:
где - действительный годовой фонд времени оборудования
шт. - годовая программа выпуска.
где - номинальный фонд работы оборудования при двухсменном режиме час.
K=3 % - коэффициент учитывающий потери номинального времени на ремонт оборудования.
- рабочих дней в году.
час – продолжительность рабочей смены.
- количество рабочих смен в день.
Учитывая анализ детали на технологичность рассмотренный в разделе 1.2. по таблице 1 принимаем среднюю сложность изготовления.
Продолжительность ритма
От 1 смены до 1 суток
От 1 суток до 1 нед.
Вывод: производство - серийное.
При выборе метода получения заготовки нужно придерживаться таких вариантов при которых изготовление детали было бы целесообразно и экономически выгодно.
Оптимальный метод получения заготовки выбирают анализируя ряд фактов:
-технические требования на ее изготовление
-объем и серийность выпуска
-форму поверхностей и размеры детали.
Все эти показатели сводятся к одному получение детали с наименьшей себестоимостью.
Рассмотрим два варианта получения заготовки для детали «Винт»:
– прокат 2 – штамповка.
Рис. 1 Контур штампованной заготовки
Масса обработанной детали Q=45 кг
Определим массу детали из проката:
Определим массу детали из штамповки:
Анализ на металлоемкость
Критерий габаритности
Критерий толщины тела связи
Критерий точности и чистоты обработки
Точность и чистота заданные чертежом
Сплав жаропрочный ХН35ВТЮ
Масштаб производства
Критерий полноты механической обработки
Таблица 4 – Коэффициенты соответствия
Коэффициенты соответствия
К1 – коэффициент веса;
К2 – коэффициент габаритности;
К3 – коэффициент толщины тела связи;
К4 – коэффициент геометрии;
К5 – коэффициент точности и чистоты обработки;
К6 – коэффициент материала;
К7 – коэффициент серийности;
К8 – коэффициент полноты механической обработки поверхностей деталей;
КЗО= К1· К2· К3· К4· К5· К6· К7 –оперативный коэффициент использования материала
К3=КЗб· К1· К2· К3· К4· К5· К6· К7·К8 –коэффициент использования металла заготовки на реальную деталь
где:Q3 – вес заготовки кг;
К3 – коэффициент толщины тела связи
Стоимость заготовки:
где Сприв =С3+СУМО – приведенная стоимость руб.
С3= Q3·CC23 – стоимость заготовки
СУМО – стоимость условной мехобработки
Скгз – средне - удельная стоимость 1кг заготовки
СУМО=(Q3- Q3min)·tуб·К10·К11·К12·ССЧ=(245-14)·035·1·1·09=33
tуб – базовое средне - удельное время необходимое для снятия 1кг стружки
ССЧ – средне – удельная стоимость 1 станко-часа на черновых и получистовых операциях
К10 – коэффициент серийности
К11 – коэффициент оборудования
К12 – коэффициент удельного веса металла
Вывод: Из анализа на металлоемкость и приведенную стоимость видно что наиболее выгодной является заготовка из штамповки т. к. ее себестоимость ниже чем из проката.
3. Определение припусков табличным методом
Таблица 5 Расчет припусков табличным методом.
Поверхности и переходы
Отклонения допуска на р-р
Растачивание черновое
Растачивание чистовое
4. Обоснование выбора баз.
Для обеспечения заданной точности получения готовой детали необходимо правильно выбрать схему базирования заготовки в процессе механической обработки как для черновой обработки так и для чистовых операций. На выбор схем базирования влияет в первую очередь расположение баз самой готовой детали. То есть расположение тех поверхностей относительно которых задаются основные отклонения формы и размеров готовой детали. Также на выбор баз влияет метод получения заготовки т.е. те суммарные погрешности которые даёт метод получения заготовки.
При установлении последовательности обработки необходимо придерживаться следующих рекомендаций:
-в первую очередь обрабатываются те поверхности которые являются базовыми при дальнейшей обработке;
-при невысокой точности исходной заготовки сначала следует обрабатывать поверхности имеющие наибольшую толщину удаляемого металла (для раннего выявления литейных и других дефектов например раковин включений трещин волосовин и т.п. и отсеивания брака);
-далее выполняют обработку поверхностей снятие металла с которых в наименьшей степени повлияет на жесткость заготовки;
- последовательность операций необходимо устанавливать в зависимости от требуемой точности поверхности: чем точнее должна быть поверхность тем позднее её необходимо обрабатывать так как обработка каждой последующей поверхности может вызвать искажение ранее обработанной поверхности (снятие каждого слоя металла с поверхности заготовки приводит к перераспределению остаточных напряжений что и вызывает деформацию заготовки);
-последней обрабатывают ту поверхность которая является наиболее точной и ответственной для работы детали в машине;
-операции обработки поверхностей имеющих второстепенное значение и не влияющих на точность основных параметров детали (сверление мелких отверстий снятие фасок прорезание канавок удаление заусенцев и т.п.) следует выполнять в конце технологического процесса но до операций окончательной обработки ответственных поверхностей;
-в конец маршрута желательно также выносить обработку легкоповреждаемых поверхностей (наружные резьбы наружные зубчатые поверхности наружные шлицевые поверхности и т.п.);
-поверхности обработка которых связана с точностью и допусками относительного расположения (соосности перпендикулярности и т.п.) изготавливают при одной установке;
-совмещение черновой (предварительной) и чистовой (окончательной) обработок в одной операции и на одном и том же оборудовании нежелательно – такое совмещение допускается при обработке жестких заготовок с небольшими припусками;
-при выборе установочных (технологических) баз следует стремиться к соблюдению двух основных условий: совмещение технологических баз с конструкторскими (например отверстие в корпусе насадной цилиндрической фрезы одновременно служит посадочным местом для оправки в процессе эксплуатации и базой для большинства операций); постоянству баз т.е. выбору такой базы ориентируясь на которую можно произвести всю или почти всю обработку (например центровые отверстия вала оси или хвостовики режущего инструмента).
5. Заводской маршрут обработки детали.
0 Токарно-винторезная
5 Токарно-винторезная
5 Термообработка (закалка)
5 Вертикально-фрезерная с ПУ
0 Координатно-расточная
0 Вертикально-фрезерная с ПУ
0 Термообработка (старение)
5 Токарно-винторезная с ПУ
5 Горизонтально-фрезерная
6 Анализ заводского техпроцесса.
Деталь по своим конструкторским особенностям относятся к типу валов. За аналог технологического процесса принимается базовый технологический процесс завода.
Методом получения заготовки в заводском техпроцессе является прокат (пруток). Предлагаемый метод – штамповка позволит вдвое сократить существующий техпроцесс и улучшить качество обрабатываемой детали.
Соблюдение технологической дисциплины обеспечивает качественное изготовление деталей в основном брак происходит по техническим причинам из-за грубых ошибок исполнителей.
На основании вышесказанного можно сделать вывод что существующий на базовом заводе технологические процесс на сегодняшний день устарел и требует изменений и усовершенствований при реорганизации самого процесса производства.
7. Принятый маршрут обработки детали
5 Вертикально-фрезерная с ЧПУ
0 Радиально-сверлильная
0 Вертикально-фрезерная с ЧПУ
5 Термообработка (старение)
0 Горизонтально-фрезерная
8. Выбор оборудования
Токарный станок 16К20Ф3 с ЧПУ.
Станок 16К20Ф3 патронно-центровой предназначен для токарной обработки наружных и внутренних поверхностей деталей типа тел вращения со ступенчатым и криволинейным профилями в один или несколько проходов в замкнутом полуавтоматическом цикле а также для нарезания крепежных резьб (в зависимости от возможностей системы ЧПУ). Станок используют в единичном мелко- и среднесерийном производстве.
Технические характеристики:
Наибольший диаметр обрабатываемой заготовки мм.:
Наибольшая длина обрабатываемой заготовки мм1000
Частота вращения шпинделя мин-135-1600
Число автоматически переключаемых скоростей9
Скорость быстрых перемещений суппорта мммин.:
Скорость подачи мммин.:
продольного хода3-1200
поперечного хода3-500
Перемещение суппорта на один импульс мм.:
Модернизированный фрезерный станок с ЧПУ - ГФ2171С5
Предназначен для многооперационной обработки деталей сложной конфигурации из стали чугуна цветных и легких металлов а также других материалов. Наряду с фрезерными операциями на станке можно производить точное сверление растачивание зенкерование и развертывание отверстий.
Большая мощность привода главного движения широкий диапазон подач и частот вращения шпинделя высокая жесткость конструкции станка позволяют применять фрезы изготовленные из быстрорежущей стали а также инструмент оснащенный пластинками из твердых и сверхтвердых синтетических материалов.
Станок оснащен трехкоординатным устройством ЧПУ и электроприводами подач что позволяет производить обработку сложных криволинейных поверхностей.
Технические характеристики
Размеры рабочей поверхности стола мм 400х1600
Наибольшая масса детали
устанавливаемой на столе станка (вместе с приспособлением) кг 400
Наибольшее перемещение стола мм
продольное (координата X) 1000
поперечное (координата Y) 400
вертикальное (установочное) 240
Перемещение ползуна (координата Z) мм 260
Скорость быстрого перемещения узлов по координатам: X Y Z мммин 6000
Пределы подач по координатам: Х Y Z мммин 3-7000
Частота вращения шпинделя мин -1 50-2500
Мощность двигателя главного движения кВт 11
Наибольший диаметр инструмента мм 250
Отклонение от круглости
при контурном фрезеровании цилиндрической поверхности мм 005
Максимальная масса инструмента кг 15
Количество одновременно управляемых координат
при линейной интерполяции 3
при круговой интерполяции 2
при линейно-круговой интерполяции 3
Габаритные размеры мм
Масса станка кг 5700
Установленная мощность кВт 18
Координатно-расточной станок 2А450
Предназначен для обработки отверстий в кондукторах приспособлениях и деталях с точным расположением осей и для легких фрезерных работ. Наличие точных измерительных приборов дает возможность использовать станок в качестве измерительной машины.
Для обработки наклонных отверстий и отверстий заданных в полярной системе координат к станку прилагаются поворотные столы.
Рабочее и ускоренное перемещение стола в продольном и поперечном направлениях осуществляется электрическими приводами с широким диапазоном регулирования.
Точная установка стола на заданную координату производится вручную маховичком. Станок снабжен точными оптическими измерительными приборами дающими возможность оператору производить отсчет на экранах с растровой сеткой с точностью до 0001 мм в двух взаимно перпендикулярных направлениях.
Имеющиеся на станке оптические коррекционные устройства разрешают повысить гарантируемую точность станка.
Расстояние от торца шпинделя до поверхности стола мм:
Расстояние от оси шпинделя до стойки (вылет) мм710
Наибольший диаметр сверления мм 30
Наибольший диаметр расточки мм 250
Наибольший диаметр фрезы мм110
Наибольший вес обрабатываемого изделия кг600
Точность установки координат мм 0004
Рабочая поверхность стола (ширина Х длина) мм630х1100
Наибольшее перемещение стола мм:
Диаметр универсального поворотного стола мм440
Диаметр горизонтального поворотного стола мм600
Конус отверстия шпинделяСпециальный
Наибольший конус инструментаМорзе № 4
Наибольшее перемещение шпинделя мм250
Наибольшее перемещение шпиндельной коробки (от руки) мм250
Пределы числа оборотов шпинделя в минуту50—2000
Пределы подач шпинделя ммоб003—016
Скорость перемещения стола мммин:
рабочая (при фрезеровании) 30—200 (бесступенчатое регулирование)
Общая мощность электродвигателей переменного тока кВт198
Число электродвигателей постоянного тока3
Общая мощность электродвигателей постоянного тока кВт249
Мощность электродвигателя привода шпинделя (постоянного тока) кВт 2
Общая мощность электромашинных усилителей (2 шт.) кВт1
включая ход стола и салазок (длина х ширина х высота) мм 2670X3305X2660
Габарит электрошкафа (длина х ширина х высота) мм834х660x1610
Вес станка (без электрошкафа поворотных столов и принадлежностей) кг 7300
Вес электрошкафа и электрооборудования кг440
Вес нормальных принадлежностей и поворотных столов кг814
Горизонтально фрезерный станок 6Р82Г
Предназначен для выполнения разнообразных фрезерных работ цилиндрическими торцевыми концевыми фасонными и другими фрезами. Применяются для обработки горизонтальных и вертикальных плоскостей пазов рамок углов зубчатых колес спиралей моделей штампов пресс-форм и других деталей из стали чугуна цветных металлов их сплавов и других материалов.
Высокая жесткость станков позволяет применять фрезы изготовленные из быстрорежущей стали а также инструмент оснащенный пластинками из твердых и сверхтвердых синтетических материалов. Большая мощность привода главного движения и тяговое усилие продольной подачи стола позволяют производить за один проход обработку широких горизонтальных поверхностей набором цилиндрических или фасонных фрез установленных на горизонтальной оправке.
Размеры рабочей поверхности стола мм 1250х320
Наибольшее перемещение стола мм
- продольное800 (850*)
Расстояние от оси горизонтального
шпинделя до рабочей поверхности стола мм 30-450 (280-650*)
Пределы частот вращения шпинделя мин -1315-1600 (50-2500*)
Диапазон подач стола мммин:
- продольных 125-1600
- продольных (бесступенчато регулируемый)5-3150
- поперечных 125-1600
- поперечных (бесступенчато регулируемый)5-3150
- вертикальных 41-530
- Ускоренное перемещение стола мммин:
- вертикальное 1330
Мощность электродвигателей приводов КВт
- основного шпинделя75
Конус шпинделя по ГОСТ 30064-93 ISO 50
обрабатываемой детали с приспособлением кг 1000
Максимальное тяговое усилие приводов стола Н:
- продольное и поперечное 40000
- вертикальное25000
- длина х ширина х высота мм2280 х 1965 х 1690
Масса станка с электрооборудованием кг 3050
9.Выбор режущего инструмента
10. Выбор мерительного инструмента
Измерения на черновых операциях
11 Расчет режимов резания и нормирование операции
11.2. Операция 040 Радиально - сверлильная
Расчет режимов резания отверстия на диаметр 16мм (сквозное отверстие). Шероховатость Ra = 63 мкм.
Исходные данные: деталь «Винт» из стали ХН35ВТЮ.
Заготовка - «штамповка».
Обработка производится на координатно-расточном станке модели «2А450»
Режущий инструмент – сверло зенкер.
Материал режущего инструмента Р6М5.
Для сверления выбираем сверло D=145 мм.
Глубина резания при сверлении t=05D=05·145=725 мм.
Подачу на оборот находим по справочникуS0=017 - 02 ммоб принимаем S0=02 ммоб
По таблицам находим коэффициенты для определения скорости главного движения резания;
где Cv=35; q=05; y=045; m=012
Значение периода стойкости T=45 мин.
Общий поправочный коэффициент на скорость резания учитывающий фактические условия резания
КV= КМV КИV КLV=1·1·071=071
где KМv – коэффициент на обрабатываемый материал;
KИv – коэффициент на инструментальный материал
КLv – коэффициент учитывающий глубину сверления
Частота вращения обмин
Действительная скорость ммин
Эффективная мощность кВт
Крутящий момент и осевую силу рассчитывают по формулам
Крутящий момент равен: Мкр=10·0041·1452·0207·071=1983 Н·м
Осевая сила: Po=10·143·1451·0207·071=4772 H
Мощность двигателя кВт
Гдеl1=D2·ctgφ+(05 2)=1452·0+1=1
Зенкерование отверстия материал зенкера Р6М5
Для зенкерования выбираем зенкер D=16 мм.
Глубина резания t=05(D-d)=05·(16-145)=075 мм.
Подачу на оборот находим по справочнику S0=06-07 ммоб принимаем S0=07 ммоб
Скорость главного движения резания:
где Cv=163; q=03; y=05; m=03
Значение периода стойкости T=30 мин.
Крутящий момент равен: Мкр=10·0106·1608·0709·075·071=376 Н·м
Осевая сила: Po=10·140·07512·07065·071=5582 H
Гдеl1=D2·ctgφ+(05 2)=202·0+1=1
Нормирование операции
Вспомогательное время на установку и снятие детали передвижение детали под сверло
tуст = 012+007+007=026 мин
Вспомогательное время на измерение
tизм = 03·2 = 06 мин
Общее вспомогательное время
Tв = tуст + tизм = 026 + 06 = 086 мин
Время на обслуживание рабочего места и время перерывов на отдых и личные надобности в процентах от оперативного времени аабс = 4%
Тобсл.= (То + ТВ)· аабс100= (033 + 086) · 4100 = 005 мин
ТО=ТО1+ ТО2=026+007=033
Тшт = Т0 + ТВ + Тобсл= 026 + 086 + 005= 117 мин
Подготовительно-заключительное время
Полученные значения сводим в таблицу:
10.2. Операция 080 - Горизонтально - фрезерная
Фрезеровать паз 10х25мм R=315max.
Выбираем концевую фрезу диаметром D = 60 мм.
Глубина фрезерования t=25 мм
По справочникам определяем подачу s = 002ммзуб.
Количество зубьев z = 4
Находим частоту вращения шпинделя
Частота вращения фрезы
Корректируем частоту вращения по данным станка: nп=100 обмин.
Действительная скорость главного движения резания:
Определяем скорость движения подачи
SM=SZ·z·nП=002·4·100=8 мммин
Находим основное время
где l – длина обрабатываемой поверхности мм
l1 – величина врезания инструмента мм
l2 – величина перебега инструмента мм
Вспомогательное время на установку и снятие детали
Вспомогательное время на смену инструмента
ТВ= tуст+ tинст+ tизм= 035 + 03 + 015 = 08 мин
Время на обслуживание рабочего места и время перерывов на отдых и личные надобности в процентах от оперативного времени аобсл= 4%
Тобсл.= (То + ТВ)· аабс100= (3 + 08) · 4100 = 015 мин
Тшт = Т0 + ТВ + Тобсл = 3+ 08 + 015 = 395 мин
Тпз1= 6 – на наладку станка и установку приспособления
Тпз2= 5 – получение инструмента и приспособлений до начала и сдача их после обработки партии деталей
Конструкторская часть.
1 Конструирование и расчёт режущего инструмента.
Конструктивные элементы спиральных сверл стандартизованы. В необходимых случаях разрабатывают специальные сверла. Стандарты регламентируют следующее основные размеры спиральных сверл: номинальный диаметр т. е. диаметр рабочей части общую длину сверла L длину рабочей части l размеры шейки и хвостовика.
Диаметр сверла принимаем равным 145-0046 мм.
Определяем номер конуса Морзе хвостовика. Осевую силу найденную которую мы определяли в разделе расчета режимов резания можно разложить на две силы: Q – действующую нормально к образующей конуса: где – угол конусности хвостовика и силу R – действующую в радиальном направлении и уравновешивающую реакцию на противоположной точке поверхности конуса.
Сила Q создает касательную составляющую Т силы резания; с учетом коэффициента трения поверхности конуса о стенки втулки .
Момент трения между хвостовиком и втулкой равен крутящему моменту создающемуся при работе затупившимся сверлом который увеличивается до 3 раз по сравнению с моментом принятым для нормальной работы сверла.
=0096 – коэффициент трения стали по стали; угол для большинства конусов Морзе равен приблизительно 1°30’; s Δ=5’ – отклонение угла конуса.
Подставив значения МТr и Мкр и решая его относительно dср получим для сверла:
По таблице 5 выбираем конус Морзе с ближайшим большим значением dср. То есть Конус Морзе №1 с dср=106 мм.
Рассматриваем момент трения :
Условие выполняется.
Определяем длину сверла. Общая длина сверла L; длины рабочей части l0 и шейки l2 могут быть приняты по ГОСТ 10903-77. Минимальную длину рабочей части сверла определяют по расстоянию от дна обрабатываемого отверстия до правого торца детали с увеличением (03 1)dc для выхода стружки. Для повышения долговечности сверл при проектировании следует предусматривать запас на переточки Dl. В общем случае сверла могут быть переточены до 075 от первоначальной длины рабочей части. Поэтому следует принимать сверло большей длины но учитывать при этом снижение жесткости сверла.
Принимаем L=144 мм l=63 мм.
Определяем геометрические и конструктивные параметры рабочей части сверла. По нормативам находим форму заточки Н (нормальная без подточек). Угол наклона винтовой канавки = 30°. Углы между режущими кромками: 2φ=118°; 2φ0=70°. Задний угол α=14°.
Шаг винтовой канавки H = pDtgw=314·145tg30°788 мм.
Толщину dс сердцевины сверла выбирают в зависимости от диаметра сверла:
D мм 15 до 120dc мм (019-015)D
Принимаем толщину сердцевины у переднего конца сверла равной 017D тогда dc=25 мм.
Утолщение сердцевины по направлению к хвостовику 14-18 мм на 100 мм длины рабочей части. Принимаем 15 мм.
Обратная конусность сверла (уменьшение диаметра по направлению к хвостовику) на 100 мм длины рабочей части должна составлять:
D мм свыше 6Обратная конусность мм 004-010
Принимаем обратную конусность 004 мм.
Ширину ленточки (вспомогательной задней поверхности лезвия) f0=10 мм и высоту затылка по спинке К=04 мм
Геометрические элементы профиля фрезы для фрезерования канавки сверла определяем упрощенным аналитическим методом.
Больший радиус профиля
Следовательно R0=059·145=855 мм.
Меньший радиус профиля RK=CKD где СК=0015075=0015·30075=0167
RK=0167·145=24 мм. Ширина профиля В= R0+RК=855+24=1095 мм.
2. Конструирование и расчет приспособления
Кондуктор предназначен для закрепления деталей в процессе сверления отверстия диаметром 16 мм выдерживая расстояние до центра отверстия 22±05 мм.
Приспособление крепится к столу станка при помощи двух винтов вставляемых в “Т” – образные паз стола и пазы установочной плиты (1). На призму (3) устанавливается заготовка (4) до опоры (6) которая расположена на “Г” - образной направляющей (5). “Г” - образной направляющей (5) закреплена на установочной плите (1) с помощью винта (7) и штифта (13). Заготовка (4) фиксируют при помощи прижима (2) который находится на шпильке (12) в месте с пружиной (10). В “Г” – образной направляющей (5) запрессована направляющая втулка (8) которая направляет сверло во время сверления.
Расчёт погрешности базирования.
Погрешность базирования возникает в результате несовпадения конструкторских и установочных баз в данном случае измерительной базой является детали в которой и производится упор детали во время обработки.
В данном случае конструкторская и технологическая базы совпадают
поэтому погрешности базирования отсутствует:
– допуск на диаметр
Расчёт усилия зажима
В данном приспособлении используется поворотный винтовой зажим с резьбой М12. Будем рассчитывать зажимную силу винта исходя из следующей формулы:
Mкр = = – крутящий момент
- средний диаметр резьбы
=’ – угол подъема резьбы
=’ – угол трения резьбовой пары
Кф= 07 – коэффициент фиксации
Данный зажим вполне удовлетворяет всем требованиям и обеспечивает необходимую зажимную силу которая превосходит силы резания.
Точностной расчёт приспособления
Для получения требуемой точности изготавливаемой детали в приспособлении необходимо выбрать такую схему приспособлении при которой действительные погрешности базирования заготовки в приспособлении были бы меньше или равны допустимым значениям погрешности базирования.
Погрешность приспособления вычисляется по формуле:
– Допуск на размер обрабатываемого отверстия
k – Коэффициент учитывающий возможное отступление от нормального
распределения отдельных составляющих
k1 – Коэффициент погрешности базирования
– Погрешность базирования
– Погрешность закрепления
– Погрешность установки
S – наибольший зазор между шпонкой приспособления и пазом стола станка
L – расстояние между осями пазов
– Погрешность износа инструмента
Расчёт слабого звена
Самым слабым звеном приспособления является резьбовое соединение так как на него действует большая сила при зажатии заготовки. Для того что бы быть уверенным в надежности данного соединения необходимо произвести расчеты на допустимое усилие зажатия по условиям прочности для основной метрической резьбы:
- Максимальная сила среза
- Текучесть материала резьбового соединения
Подставляя значение в расчетную формулу получим
3. Расчет мерительного инструмента
Расчет калибра - скобы для контроля вала на размер 65е9
Определяем номинальный размер проходной и непроходной части.
Dmin = 64866 мм – наименьший предельный размер вала
Dmax = 6494мм – наибольший предельный размер вала
По табл. ГОСТ 24853-81 для 9 квалитета и интервала размеров свыше 50-до 80 мм находим данные для определения необходимых размеров калибра:
Z1= 8 мкм – отклонение середины поля допуска на изготовление проходного калибра для вала относительно наибольшего предельного размера изделия.
Н1 = 5 мкм - допуск на изготовление калибра для валов.
Y1 = 0 мкм – допустимый выход размера изношенного проходного калибра для вала за границу поля допуска изделия.
Рассчитываем предельные размеры для новой проходной части скобы:
Рассчитываем изношенную проходную сторону:
Рассчитываем предельные размеры непроходной части калибра – скобы:
Вычертим расположение полей допусков калибра относительно поля допуска детали.
Алексеев Г. А Аршинов В. А. Кричевская Р. М. Конструирование инструмента. М.: Машиностроение 1979.
Балабанов А.Н. Краткий справочник технолога машиностроителя – М.1992
Горбацевич А.Ф. Шкред В.А. Курсовое проектирование по технологии машиностроения – М.1983
Егоров М.С. Дементьев В.И. Дмитриев В.Д. Технология машиностроения. – М. 1976
Косилова А.Г. Мещеряков Р.К. Точность обработки заготовки и припуски в машиностроении. – М. 1976
Нефедов Н.А. Осипов К.А. Сборник задач и примеров по резанию металлов и режущему инструменту. - М.1990
Справочник технолога-машиностроителя. Т. 12В. Б. Борисов Е. И. Борисов В. Н. Васильев и др.Под ред. А. Г Косиловой и Р. К. Мещерякова. М.: Машиностроение 1985.
Общемашиностроительные нормативы режимов резания для технического нормирования работ на металлорежущих станках. Часть 1 Часть 2. Изд. 2-е: М.: Машиностроение 1974.
Миллер Э. Э. Техническое нормирование труда в машиностроении. Уч. пос. для техникумов Изд. 3-е: М.: Машиностроение 1972.
Спецификация.doc
Винт М10 х25 ГОСТ 17475-80
гладкая 1032-2451 0-10-11
-10 H7 m6 ГОСТ 13120-83
Гайка М8 ГОСТ 5927-70
Шайба 8 ГОСТ 9649-78
Штифт 6 х 26 ГОСТ 3128-70
Винт.cdw

Получение заготовки методом штамповки или ковки.
42 HRC (277-388HB). Режимы термообработки (закалки и старения) по технологии
согласованной с НИКИЭТ. Контроль твердости в объеме 100%.
Производить 100% ультразвуковой контроль заготовки по ПНАЭГ-7-014-89 на отсутствие
внутренних дефектов по ГОСТ 24507-80
Производить контроль на одной заготовке от партии (плавки
садки) отбираемой после
термообработки: - на величину зерна. Номер зерна должен быть не крупнее №3 по шкале 3
ГОСТ5639-82. Метод контроля по технологии завода-изготовителя. Допускается величину зерна
определять после закалки перед старением. - на соответствие механических свойств
определяемых при комнатной температуре:
При обработке поверхности Е допускается врезание инструмента не более 1мм.
Расположение паза Д по окружности произвольное.
Допускается наличие окисной пленки от старения в защитной атмосфере или в вакууме.
Маркировать шрифтом 5-Пр3 ГОСТ26.008-85.
Остальные требования по РБМ-К5.Сб.15Ту.
*Размер для справок.
Сверло 14_5.cdw

другой марки по ГОСТ 19265-73
Материал хвостовой части - сталь 40Х по ГОСТ 4543-71
Сверло должно удовлетворять техническим требованиями по
Сварка контактно-стыковая
допускается сварка трением
Маркировать: диаметр сверла
марку стали режущей части
товарный знак завода-изготовителя (14
Шаг винтовой канавки 78
Скоба.cdw

КЭ(055).cdw

КЭ(020).cdw

КЭ(015).cdw

КЭ(025).cdw

КЭ(030).cdw

КЭ(010).cdw

тех карты_Винт.doc
На всех операциях отходы собрать и сложить в короб с учетом марки материала
Код наименование операции
Обозначение документа
Код наименование оборудование
Проверить наличие сертификатов на материал протоколов хим. анализа материала протоколов проверки баллов зерна
0 Токарно-винторезная ИОТ №11
К20 06100 3 07 1 1 1 1 1 140 36
Патрон 3-х кулачковый РГ.7808-4268 Ящик Ограждение станочное РГ.6999-4001 крючок
Установить закрепить снять
Р6М5 сверло 8135-0928 6Н14 пробка
D=4 L=5 t=15 I=1 S=0.06 N=300 V=3 Тв=05 То=10
ВСЕ ВИДЫ ОБРАБОТКИ К РОМЕ СБОРКИ ( ЛИСТ 1-Й)
Транспортировку заготовок и деталей выполнять по СТП РГ 165-88 СТП РГ 349-81 и ИОТ№61
Первую деталь предъявить мастеру и контролеру с отметкой в МПК о контроле
Поджать деталь центром
02-0177 ВК8: резец ШЦ-I-125-01 ГОСТ 166-89 70-2.0
D=70 L=160 t=2 I=1 S=01 N=51 V=136 Тв=08 То=333
Контроль 06030 3 01 1 1 1 1 06
К20Ф3 06100 2 07 1 1 1 1 250 23
Патрон 3-х кулачковый РГ.7808-4262 Ящик
Подрезать торец на верность
Точить поверхность выдерживая р-ры : D=136h14
40-0009 Т5К10 Резец ШЦ-I-0-250-01 ГОСТ 166-89 136h14
D=136 L=8 t=5 Lp=13 I=2 S=01 N=102 V=506 Тв=14 То=255
Точить поверхность выдерживая р-ры : D=120-0.1 4
РГ.2140-0009 Т5К10 Резец 01.8141-4251Пр 01.8141-4253Не 160Н8 Пробки
D=120 L=8 t=1 Lp=20 I=2 S=01 N=128 V=643 Тв=21 То=312
ВСЕ ВИДЫ ОБРАБОТКИ (ПОСЛЕДУЮЩИЙ ЛИСТ)
Расточить отверстие выдерживая р-ры : D=108+0.5
40-0009 Т5К10 Резец ШЦ-I-0-250-01 ГОСТ 166-89 108+0.5
D=108 L=8 t=5 Lp=13 I=2 S=01 N=102 V=506 Тв=14 То=255
Расточить отверстие выдерживая р-ры : D=71H14
РГ.2140-0009 Т5К10 Резец ШЦ-I-0-250-01 ГОСТ 166-89 71h14
D=71 L=8 t=1 Lp=20 I=2 S=01 N=128 V=643 Тв=21 То=312
Сверлить отв. выдерживая размеры: D=38Н14
50-0001 Патрон 6100-0143; 6100-0146 Втулки
00-0210 38Р6М5 Сверло 8133-0923 38Н14 Пробка
D=38 L=23 t=51 Lp=29 I=1 S=008 N=630 V=202 Тв=12 То=23
Притупить острые кромки.
К20Ф3 06100 2 07 1 1 1 1 170 20
Подрезать торец выдерживая размер 22075-02
02-0327 Т5К10 Резец 8102-0153 ШЦ-I-0-250-01 ГОСТ 166-89 22075-02
D=685 L=35 t=2 I=1 S=01 N=128 V=824 Тв=08 То=234
Точить поверхность выдерживая р-ры : D=66-01
40-0009 ВК8 Резец ШЦ-I-0-250-01 ГОСТ 166-89 66-01
D=66 L=150 t=15 I=2 S=01 N=102 V=506 Тв=14 То=255
Сверлить отв. выдерживая размеры: D=31Н14
00-0210 31Р6М5 Сверло
D=31 L=140 t=155 I=1 S=008 N=200 V=202 Тв=11 То=24
Зенкеровать отв. выдерживая размер D=33Н14
00-0210 33Р6М5 Зенкер 8133-0923 33Н14 Пробка
D=33 L=140 t=1 I=1 S=008 N=200 V=202 Тв=11 То=24
Контроль 06030 3 01 1 1 1 1 08
5 Вертикально-фрезерная с ЧПУ ИОТ№50
ГФ2171С5 06120 2 07 1 1 1 1 200 34
Тиски станочные РГ.7808-4262 Ящик
Установить деталь закрепить снять
Фрезеровать контур предварительно выдерживая размеры 122h14
23-0019 40;Р6М5 Фреза 6103-0004 Втулка 122h14 ШЦ-I-125-01 ГОСТ166-80
D=40 L=92 t=3 Lp=132 I=1 S=100 N=250 V=314 Тв=06 То=132 Торм=02
Фрезеровать контур окончательно выдерживая размеры 120h14
23-0019 20;Р6М5 Фреза 6103-0004 Втулка 120h14 Калибр-скоба СПМ.03.59.000
D=20 L=92 t=3 Lp=122 I=1 S=100 N=250 V=314 Тв=06 То=07
Контроль 06030 2 01 1 1 1 1 03
0 Слесарная 0108 ИОТ№59
Верстак 09113 2 01 1 1 1 1 15
РГ.7808-4262 Ящик Слесарный инструмент
Опилить острые кромки
Контроль 06030 2 01 1 1 1 1 01
5 Токарная с ЧПУ ИОТ№11
К20Ф3 06100 2 07 1 1 1 1 160 28
Подрезать торец выдерживая р-ры : 6975±05 D=136h14
40-0009 Т5К10 Резец ШЦ-I-0-250-01 ГОСТ 166-89 6975±05 136h14
D=136 L=68 t=5 I=2 S=01 N=102 V=506 Тв=14 То=30
Точить поверхность выдерживая р-ры : D=135-0.15 (технол)
РГ.2140-0009 Т5К10 Резец ШЦ-I-0-250-01 ГОСТ 166-89 D=135-0.15
D=135 L=68 t=1 Lp=20 I=1 S=01 N=128 V=643 Тв=11 То=112
Расточить отверстие выдерживая размеры D=110Н11; R3 35+1
РГ.2140-6050 Р6М5;резец D=110Н11 Пробка R3 Шаблон 35+1 Шаблон
D=110 L=35 t=1 Lp=40 I=2 S=01 N=163 V=199 Тв=12 То=393
Расточить отверстие выдерживая размеры D=735 60Н12
63-3508 Р6М5 Резец РГ.8133-4170 735 пробка 60Н12 Шаблон
D=735 L=25 t=1 I=1 S=05 N=255 V=30 Тв=06 То=322
Расточить отверстие выдерживая размеры: D=40H12
РГ.2140-6050 Р6М5 Резец РГ.8133-4180 40Н12 пробка
D=40 L=20 t=1 Lp=30 I=1 S=01 N=128 V=20 Тв=13 То=219
Расточить фаску выдерживая размеры: 1x45°
РГ.2140-4056 Т5К10 Резец 8371-0186 112х90° Шаблон
D=110 L=1 t=1 Тв=01 То=037
Расточить фаску выдерживая размеры: 42Н14 угол 30º
РГ.2140-4056 Т5К10 Резец РГ.8371-4106 42Н14 30° Шаблон
D=42 L=2 t=1 Тв=02 То=049
Расточить канавку выдерживая размеры: 76Н12 2Н14 40Н12
РГ.2140-4056 Т5К10 Резец РГ.8371-4106 76Н12 Нутромер 40Н12 Шаблон 2Н14 Шаблон
D=76 L=2 t=175 Тв=015 То=05
Точить поверхность выдерживая размеры: 5±015 угол 15º 120h14
РГ.2140-4056 Т5К10 Резец РГ.8371-4106 5 15° Шаблон
D=120 L=2 t=1 Тв=01 То=049
Точить поверхность выдерживая размеры: 4±015 угол 30º 135-0.15
РГ.2140-4056 Т5К10 Резец РГ.8371-4106 4±015 30° Шаблон
D=135 L=4 t=1 Тв=04 То=051
0 Радиально-сверлильная 0566 ИОТ№11
А450 06090 2 07 1 1 1 1 40 116
РГ.7342-6601 Приспособление РГ.7808-4262 Ящик
Сверлить отв. выдерживая размеры: D=145Н14 135-0.15; 22±05;
01-0054 145;Р6М5 Сверло 8133-0930 145H14 Пробка
D=145 L=125 t=725 Lp=16 I=1 S=02 N=300 V=137 Тв=086 То=026
Зенкеровать отв. выдерживая р-ры: 16Н12
53-0112 16 Р6М5 Зенкер 8371-0167 16Н12 Пробка 6150-0001 Патрон
D=16 L=125 t=075 Lp=3 I=1 S=07 N=300 V=1213 Тв=10 То=007
Контроль 06030 2 01 1 1 1 1 06
5 Слесарная 0108 ИОТ№55
0 Вертикально-фрезерная с ЧПУ ИОТ№50
Приспособление фрезерное РГ.7808-4262 Ящик
Фрезеровать контур зуба выдерживая размеры угол 16º±1º; 9+1 15 R3 R1.5 19 135h12
23-0019 25;Т5К10 Фреза 6103-0004 Втулка 9+1 Шаблон 16º±1º Шаблон ШЦ-I-125-01 ГОСТ166-80
R3 R1.5 Радиусный шаблон
D=25 L=92 t=1 Lp=132 I=1 S=100 N=250 V=314 Тв=06 То=132 Торм=02
Переустановить деталь повторить переход 3
5 Термообработка (старение)
Старение согласно тех. Процесса «Термическая обработка детали Винт РБМ-К15.15-1»
Провести УЗК детали по карте контроля 11-08 с выдачей заключения.
РГ.7808-4262 Ящик Слесарный инструмент Шлифмашинка
Зачистка поверхности для замера твердости. Глубина зачистки не более 05мм
Прибор Роквелл ТК2М ГОСТ9013-59
Замерить твердость согласно карте эскизов 30-42 НRC
Обработку поверхности для контроля величины зерна провести согласно т. процессу ТПР-105-2009 Технология
металлографического исследования с целью определения величины зерна РБМ-К15-1Винт
Патрон 3-х кулачковый Цанга РГ.7808-4262 Ящик
Подрезать торец выдерживая р-ры : 220h14 150+1
40-0009 ВК8 Резец ШЦ-I-0-250-01 ГОСТ 166-89 6975±05 136h14
D=56 L=5 t=1 I=1 S=01 N=102 V=506 Тв=14 То=12
Расточить фаску выдерживая размеры: 35Н14 угол 30º
РГ.2140-4056 ВК8 Резец РГ.8371-4106 35Н14 30° Шаблон
D=35 L=2 t=1 Тв=02 То=049
Точить поверхность выдерживая р-ры : D=65е9 150+1
РГ.2140-0009 ВК8 Резец 150+1 ШЦ-I-0-250-01 ГОСТ 166-89 D=65е9 скоба
D=65 L=150 t=1 Lp=158 I=1 S=01 N=128 V=643 Тв=11 То=112
Точить поверхность выдерживая р-ры : D=120h14 l=5±015 угол 15º
РГ.2140-0009 ВК8 Резец ШЦ-I-0-250-01 ГОСТ 166-89 D=120 h14 скоба 5±015 угол 15º шаблон
D=120 L=5 t=1 Lp=160 I=1 S=01 N=200 V=150 Тв=11 То=08
РГ.2140-4056 ВК8 Резец РГ.8371-4106 4±015 30° Шаблон
Точить поверхность выдерживая р-ры : D=63h14 l=28±026 R3
РГ.2140-0009 ВК8 Резец D=63h14 скоба 28±026 ШЦ-I-0-250-01 ГОСТ 166-89 R3 Шаблон
D=63 L=122 t=1 Lp=130 I=1 S=01 N=250 V=50 Тв=11 То=112
Точить поверхность выдерживая р-ры : D=64h14 100
РГ.2140-0009 ВК8 Резец D=64h14 скоба 150 ШЦ-I-0-250-01 ГОСТ 166-89
D=64 L=100 t=05 Lp=108 I=1 S=01 N=250 V=640 Тв=11 То=08
Точить поверхность выдерживая р-ры : D=56h14 l=30 45º
РГ.2140-0009 ВК8 Резец D=56h14 скоба 30 45º Шаблон
D=56 L=30 t=4 Lp=38 I=2 S=01 N=250 V=640 Тв=10 То=09
Точить поверхность выдерживая р-ры : D=56h14 l=10 2х45º 45º
РГ.2140-0009 ВК8 Резец D=56h14 скоба 2х45º Шаблон
D=56 L=10 t=4 Lp=104 I=2 S=01 N=200 V=640 Тв=10 То=09
Расточить канавку выдерживая размеры: 52h12 R2.5
РГ.2140-4056 25ВК8 Резец РГ.8371-4106 R2.5 Шаблон
D=52 L=10 t=1 Тв=015 То=05
Нарезать резьбу М64-8g
20-1435 ВК8 Резец М64-8g Калибр-кольцо ПР НЕ
D=64 L=80 t=05 То=100
Для обеспечения соосности резьбы М64-8g и 65е9 эти поверхности точить за одну установку без перезакрепления
Контроль 06030 2 01 1 1 1 1 15
0 Горизонтально-фрезерный ИОТ №50
Р82Г 06120 2 07 1 1 1 1 110 395
Тиски станочные Втулки Вкладыши РГ.7808-4262 Ящик
Фрезеровать паз выдерживая размеры 10х25 R315max
23-0019 60;Р6М5 Фреза 10х25 Шаблон R315max Шаблон
D=60 L=10 t=25 Lp=50 I=1 S=002 N=100 V=20 Тв=08 То=3
Промыть деталь по техн. Инструкции 0713-09
Проверить правильность заполнения МПК
Плита 1-2 630х400 ГОСТ 10905-86
Проверить правильность маркирования
Проверить шероховатость поверхностей
Образцы шероховатости ГОСТ 9378-75
Проверить все размеры
Клеймить годную деталь
Упаковать дет. в парафиновую бумагу (ГОСТ 9569)
Уложить деталь в тару СПМ 10.14.000СБ
КЭ(040).cdw

КЭ(050).cdw

КЭ(035).cdw

КЭ(045).cdw

Заготовка.cdw

Неуказанные радиусы R=4 мм
Смещение по плоскости разъема штампа 0
Коробление не более 0
Остаток от облоя по периметру среза не более 0
Зачистка местных дефектов на глубину не более
% припуска на механическую обработку
технологический процесс.docx
К О М П Л Е К Т Д О К У М Е Н Т О В
НА ТЕХНОЛОГИЧЕСКИЙ ПРОЦЕСС (ОПЕРАЦИЮ)
МЕХАНИЧЕСКОЙ ОБРАБОТКИ
Чертёж приспособления.cdw

Рекомендуемые чертежи
- 29.07.2014
- 24.01.2023
- 25.01.2023
- 13.12.2022
- 24.01.2023