Разработка проекта цеха и участка для производства детали Вилка




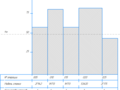
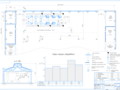
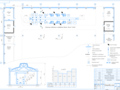
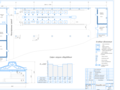
- Добавлен: 24.01.2023
- Размер: 2 MB
- Закачек: 0
Описание
Состав проекта
![]() |
![]() |
![]() |
![]() ![]() ![]() |
![]() |
![]() ![]() ![]() |
![]() ![]() |
![]() ![]() ![]() ![]() |
![]() ![]() ![]() ![]() |
![]() ![]() ![]() |
![]() ![]() ![]() |
![]() ![]() ![]() |
![]() |
![]() ![]() |
![]() ![]() ![]() ![]() |
![]() ![]() |
![]() ![]() |
![]() ![]() ![]() ![]() |
![]() ![]() ![]() |
![]() ![]() ![]() ![]() |
![]() ![]() ![]() ![]() |
![]() ![]() |
![]() ![]() ![]() |
![]() ![]() ![]() ![]() |
![]() ![]() |
![]() ![]() ![]() ![]() |
![]() ![]() ![]() ![]() |
![]() ![]() ![]() |
![]() ![]() |
![]() ![]() |
![]() ![]() ![]() |
![]() ![]() ![]() ![]() |
Дополнительная информация
Вариант 93.doc
Кафедра: технологии и организации машиностроительного производства
Семестровое задание
По дисциплине: «Основы проектирования участков и цехов»
Определение метода производства
Определение потребного количества оборудования в условиях поточного производства
Определение типа производства
1Предметна целевая специализация участка
2Выбор способа расположения станков в зависимости от формы специализации участка
3Выбор ориентации станков относительно магистрального проезда
4Выбор расстояний между станками
5Определение площади участка
Выбор и обоснование транспортных средств
Проектирование системы сборки стружки
Проектирование вспомогательных отделений
1Проектирование ремонтного отделения
2Проектирование заточного отделения
3Проектирование контрольного отделения
4Проектирование отделение СОЖ
5Проектирование складского хозяйства
6Проектирование инструментально – раздаточной кладовой (ИРК)
Обоснование и выбор основных характеристик производственного здания.
2Выбор высоты пролётов
Проектирование административно-бытовых помещений
Расчет количества оборудования в условиях непорочного производства.
Наименование операции
Время перехода рабочего от станка к станку при многостаночном обслуживании = 02 мин.;
Материал заготовки Сталь 40Х;
Годовая программа выпуска = 120000 (штгод);
Масса заготовки 107 кг;
Существует два метода производства: поточное и непоточное (партионное) производство.
Для организации поточного производства необходимо единственное немаловажное условие: достаточная загрузка рабочих мест одной деталью (одним изделием).
Определяем минимальную программу выпуска обеспечивающую заданный коэффициент загрузки по формуле из (2 стр. 20)
где – эффективный фонд времени оборудования для универсального оборудования 4015 часов;
- оптимальный коэффициент загрузки для поточного производства.
- среднее штучное время 75%.
Так как то это поточное производство
Минимальная программа выпуска будет равна:
Учитывая тип метод производства определяем потребное количество станков по исходным данным.
Количество станков рассчитываем отдельно для каждой операции по формуле и округляем до целого числа из(2 стр. 14):
где- расчетное время итой операции.
- такт выпуска расчетной линии.
где 4015 часов – эффективный фонд времени.
Таблица 1 – количество оборудования на участке.
где - коэффициент загрузки оборудования .
Расчетный коэффициент загрузки не должен превышать нормативного значения для данного типа станка. из (2 прил. Б2 стр.38).
Составляем график загрузки оборудования для поточной линии.
Тип производства влияет на выбор оборудования (универсальное специальное специализированное) на выбор характера оснастки (универсальное специальное либо вообще отсутствует) на выбор режущего инструмента и мерительного инструмента на квалификацию рабочих на выбор транспортных средств.
Предпочтительно в начале проектирования тип производства можно определить укрупнённо из (1 табл. 31). Так как 114 и годовая программа выпуска 120000 штгод тогда у нас массовый тип производства.
1 Предметная целевая специализация участка
Для массового и крупносерийного производства где естественной является предметная целевая специализация цехов и участков. Такая структура обеспечивает прямоточность производственного процесса когда в конце поточных линий обработки располагаются участки узловой сборки а дальше выполняется сборка агрегатов или изделий.
2 Выбор способа расположения станков в зависимости от формы специализации участка
Метод расположения оборудования зависит от метода производства и от вида специализации участка.
В поточном производстве оборудование располагается по ходу технологического процесса детали которая обрабатывается на поточной линии.
3 Выбор ориентации станков относительно магистрального проезда
Ширину магистральных проездов по которым осуществляются межцеховые перевозки принимают равной 4000 мм. Относительно продольного проезда станки могут располагаться вдоль поперёк и т.д.
Принимаем продольное расположение тогда станок фронтальной стороной отражен к проезду так как это наибольше приемлемый вариант. При таком расположении облегчается подача к станку заготовок инструмента удаление отходов подвод коммуникаций.
4 Выбор расстояний между станками
При размещении оборудования в соответствии с выбранным вариантом необходимо обеспечить установленное расстояние между оборудованием при различных вариантах размещения а также ширину проездов. (1. табл. 49 с. 116) От проезда до тыльной стороны 500 мм.
Между станками при расположении боковыми сторонами друг к другу 900 мм.
От стен колон до тыльной стороны станка 800 мм.
5 Определение площади участка
Площадь станочного отделения механического цеха определяется укрупнено по формуле:
где. – общее число станков = 120 шт;
. – удельная площадь на единицу оборудования (2. с. 21) = 12 .
Средства межоперационного транспорта (МОТ) применяются для обрабатываемых деталей между рабочими местами.
В поточном производстве средства межоперационного транспорта должны обеспечивать бесперебойную поштучную передачу деталей от станка к станку а также размещение на них транспортных и страховых заделов.
Для данного участка в качестве межоперационных транспортных средств принимаем конвееры.
Несмотря на то что в настоящее время на машиностроительных заводах малоотходные технологические процессы обработки интенсивность стружкообразования достаточна высока. Стружку необходимо убирать с рабочего места и удалять за пределы производственных участков. В зависимости от количества стружки и площади на которой она образуется применяют различные системы её уборки и транспортировки.
Количество стружки производимое на поточной линии можно определить по формуле:
где - выход стружки кгчас;
– масса заготовки =107 кг;
– масса детали =75 кг;
– годовой выпуск =120000 шт.год;
– эффективный фонд времени оборудования =4015 час.
В частных целях применяем комбинированную систему убора стружки: стружка удаляется от станков и пере транспортируется на линию конвейеров и убирается в специальную тару которая по мере заполнения вывозится из цеха.
Вид и группу стружки для участка или линии определяют по (2. табл. 2.3 с. 23) группа стружки 3 (автоматный жгутик мелкий вьюн).
Зная группу стружки по (2 табл. 2.4 стр. 24) принимаем тип конвейера для транспортировки стружки: пластинчатый.
Проектирование вспомогательных отделений ведется укрупнено по нормам технологического проектирования.
1 Проектирование ремонтного отделения
Служит для ремонтного обслуживания оборудования а также для несложного приспособления и инструмента.
Площадь ремонтной мастерской можно определить по формуле:
где – число станков для мастерской = 4(шт.);
– удельная площадь приходящаяся на один станок. = 27 ()
Располагается мастерская для ремонта станка и инструмента смежно с инструментальной мастерской (ИРК). Ограждается мастерская металлической сеткой.
2 Проектирование заточного отделения
Заточное отделение предназначено для централизованной заточки режущего инструмента.
Заточное отделение располагается рядом с ИРК и ограждается стеклянными перегородками.
Площадь заточного отделения можно рассчитать по формуле:
где =6шт. – число станков в заточном отделении;
=11м. – удельная площадь на один станок.
3 Проектирование контрольного отделения
Контрольное отделение предназначено для организации приёмного контроля годных деталей. По оценки охвата применяемый контроль подразделяется на сплошной и выборочный.
Выборочный контроль требует значительного объема выпуска для формирования корректных выводов или проб. Выборочный контроль как правило принимают при операционном контролем.
Потребное количество контролёров в серийном и массовом производстве:
где – число станочников обслуживающим контрольным отделением.
где - общие число станков в цехе =120шт;
– эффективный фонд времени оборудования =4015час;
– средний коэффициент загрузки оборудования =0704;
– эффективный годовой фонд времени рабочего.=1840 часов;
– средний коэффициент многостаночного обслуживания =12;
– норма обслуживания приходящаяся на одного контролёра =15;
(2 табл. 2.7 стр. 27);
– коэффициент сложности=1 (2 стр. 26).
Площадь контрольного отделения определим по формуле:
=6. – удельная площадь приходящаяся на одного контролёра.
Размещается контрольное отделение в конце цеха ограждается стеклянными перегородками. Также предусматривается площадка контрольных пунктов 1010 .
4 Проектирование отделение СОЖ
Отделение для приготовления к раздачи смазочно-охлаждающих жидкостей (СОЖ) проектируют для небольших цехов мелко серийного и средне серийного производства. Для крупных цехов проектируют эмульсионное хозяйство включающую эмульсионную станцию систему регуляции.
Укрупнено площадь отделения СОЖ может быть определена в зависимости от количества производственного оборудования (2 стр. 28).
Площадь склада масел для смазки оборудования можно принять 10 20 м. Отделение СОЖ является пожароопасным потому его ограждают несгорающими перегородками (кирпич бетон) и размещают у наружной стены здания с отдельным выходом наружу.
5 Проектирование складского хозяйства
Складское хозяйство состоит из комплекса складов разного функционального назначения. Непосредственно в цехе целесообразнее всего размещать площадки для хранения минимального запаса (2 – 3 дня) заготовок. Эти площадки устанавливают в каждом пролёте в начале станочного отделения.
Размеры площадок для одного пролёта определяем по формуле (2 стр. 30):
где - масса заготовок обрабатываемых на участке (в пролёте в течение года):
– время хранения деталей на складе =3 дня (2. табл. 2.8 с. 31);
– допускаемая загруженность пола=2;
– коэффициент использования площади =04
Размещается склад готовой продукции в конце цеха смежного с контрольным отделением. Ограждается металлическими сетками.
Площадь склада готовой продукции:
где - масса готовых деталей обрабатываемых в цехе в течении года;
где =3 дня – время хранения деталей на складе (2. табл. 2.8 с. 31).
– время хранения деталей на складе =5 дней (2. табл. 2.8 с. 31);
6 Проектирование инструментально – раздаточной кладовой (ИРК)
Инструментально – раздаточная кладовая (ИРК) служит для хранения всех видов инструмента и оснастки а также выдачи их на рабочем месте.
Для небольших цехов и средних (до 200 станков) устанавливается комплексная ИРК для всех видов инструментов. Расчет площади комплексной ИРК производится по нормам приведенным в (2 табл. 2.5 стр. 25).
Обоснование и выбор основных характеристик производственного здания
Факторами определяющими основные тенденции при проектировании совместных промышленных зданий являются: сокращение времени на проектирование; улучшение бытовых условий работающих.
В значительной степени факторам соответствуют производственные здания имеющие размеры и параметры установленные на основании единой модульной системы (ЕМС). Базой ЕМС является основной строительный модуль (М) который равен 100 мм. Основной модуль (М) служит для получения производных модулей – укрупнённых и дробных.
Согласно ЕМС размеры ширины пролётов и шагов принимаются кратными укрупнённым модулям 60М (6м) и 30М (3м). Высота этажей производственных помещений принимается кратной укрупнённым модулям 12М (12м) и 6М (06м) зданий административно-бытового назначения – кратной модулю 3М (03м).
Реализуя принцип блокирования в одном производственном здании обычно размещают несколько цехов с однородными технологическими процессами. Габариты здания рекомендуется формировать из унифицированных типовых секций (УТС). Одна УТС имеет размеры 7272 м. и площадь 5184 . Если требуется здание с большей площадью то к УТС добавляют еще одну секцию 7272 м. в направлении ширины здания.
2 Выбор высоты пролётов
Высота пролёта определяется как расстояние от уровня пола здания до нижней затяжки несущей фермы или расстояние от уровня пола до головки подкранового рельса. Предварительно высоту пролёта рассчитывают исходя из типа оборудования габаритов деталей. Окончательно принимается унифицированное значение высоты пролёта секции ближе к расчетному значению. Действующими нормами технологического проектирования (Госстрой СССР СН 223 - 62) установлены основные строительные характеристики которыми необходимо руководствоваться при проектировании машиностроительных заводов.
Исходя из этих положений по (2. стр. 8 табл. 2.1) принимаем высоту пролётов в пределах 8 м.
Сетка колон характеризует соотношение шага колонн и ширины пролёта (АВ). Расстояния А и В измеряются между осями колонн.
Для производственных зданий механических и сборочных цехов рекомендуется применять унифицированные сетки колонн с размерами: 1218 м.; 1224 м.; 1230 м.; 1236 м.
Принимаем сетку колонн равной 1218 м. так как она является основной сеткой предпочтительного применения.
Здание принимаем одноэтажное.
Кровли зданий могут быть скатными и плоскими; могут быть светоаэрационные фонари (фонарные кровли) и могут не иметь таковых (бес фонарные).
Для нашего производственного здания принимаем скатной тип кровли.
В состав административных (служебных) и бытовых помещений входят все виды бытовых помещений и устройств (гардеробные умывальные душевые санитарные узлы столовые и буфеты и т.д.) цеховые административно-конторские и инженерные службы а также помещения общественных организаций и культурно-массового обслуживания.
Административно-бытовые помещения размещаются в специальных зданиях которые могут быть пристроены к производственному зданию или отдельно стоящими. На предприятиях машиностроения где производственные вредности незначительны административные и бытовые помещения располагают в пристроенных зданиях.
Пристроенные здания компонуются из унифицированных секций которые характеризуются шириной 12 м. длинной 36 48 60 м. сетка колонн принимается 66 м. высота этажей 33 м. и 42 м. число этажей 23 и 4.
На первом этаже обычно размещают умывальные санузлы медпункты столовые а на верхних этажах – гардеробные душевые административно-конторские и инженерные службы пункты питания помещения культурно-массового назначения.
Питьевое водоснабжение должно соответствовать санитарным нормам. Устройства питьевого водоснабжения размещают в проходах производственных помещений в помещениях для отдыха и других удобных местах на расстоянии не более 75 м. от наиболее удаленного рабочего места.
Столовая устраивается в цехах с количеством работающих в наиболее многочисленной смене 250 человек и более. Для цехов с меньшим количеством работающих (как в данном случае) устраиваются буфеты.
Расчет площадей бытового обслуживания производится по следующим нормам: гардеробные блоки (хранение одежды душевые умывальные) 26 28на одного работающего; санузлы 02 на одного работающего в наиболее многочисленной смене помещения общественного питания 07 на одного работающего; медпункт 008 на одного работающего но не менее 50.
Площадь служебных помещений принимается из расчета: рабочих комнат СКП и ИТР на одного работающего в этом помещении; рабочих комнат КБ 6 на один чертёжный стол; залов совещаний 09 12 на одно место; вестибюлей-гардеробных 027 на одного служащего; комнат для учебных занятий 175 на одно место; кабинетов техники безопасности 25.
Площадки отдельных рабочих помещений и кабинетов должны быть не менее 9.
Площадь комплекса бытовых и служебных помещений можно определить по формуле из (2 стр. 34):
где - общее число работающих в цехе =174человека;
- суммарная удельная площадь административно бытовых помещений =486 ().
санитарно-гигеенические помещения =268 ();
помещения питания =07 ();
медицинские помещения =268 ();
помещения культурно-массового обслуживания =04 ();
служебные помещения =1 ();
Определим площадь каждого этажа административного здания
где площадь лестничных площадок ;
Рисунок 9.1 – Площадь комплекса бытовых и административных помещений.
Определим этажность административного здания:
Принимаем n=2 этажа.
Расчет количества оборудования в условиях непоточного производства
Штучно калькуляционное время мин.
Программа выпуска шт.год.
Определяем программу запуска:
Определяем месячную программу запуска:
Определяем среднюю трудоёмкость операции:
Определяем среднюю загрузку рабочего места данной деталью в месяц:
Определяем удельную трудоёмкость месячной программы запуска детали:
где – эффективный фонд времени оборудования часов при числе смен в месяц
Определяем продолжительность выпуска детали за месяц:
Принимаем Ф=1 смены.
Определяем месячный эффективный фонд времени оборудования соответствующий продолжительности выпуска детали час:
Определяем расчетное количество станков каждой модели по формуле:
где - суммарное штучно-калькуляционное время использования станка данной модели по технологическому процессу.
Так как не превышает нормативных значений принятое количество станков оставляем без изменения. Средний коэффициент загрузки станков при обработке детали определяется по формуле:
Составляем график загрузки оборудования на участке.
Количество станков принятое
Рисунок 10.2 – График загрузки оборудования в условиях не поточного производства.
Мельников Г. Н. Вороненко В. П. Проектирование механосборочных цехов; Учебник для студентов машиностроительных специальностей вузовПод рад. А. М. Дальского – М.: Машиностроение 1990. – 352 с.: ил. – (Технология автоматезировонного машиностроения).
А. А. Егоров С. Ю. Стародубов Основы проектирования механосборочных участков и цехов: Учеб. Пособие (для студ. спец. 7.090.202 «Технология машиностроения»). – Алчевск: ДГМИ 2002. – 48 с.
Тимплеты.frw

Чертеж.cdw

Площадка для хранения заготовок
Участок обработки колеса зубчатого F=341 м
Перегородка из стеклоблоков
Перегородка из металлической сетки
Конвейер для уборки стружки
Технологическое оборудование
Подвод питьевой воды
Фрезерно-центровальный
График загрузки оборудования
График загрузки.frw

Модель станка 2Г942 1Н713 1Н713 53А20 2Г175
Количество станков 1 1 1 3 1
Тимплеты 2.frw

Основы проектирования участков и цехов.docx
Донбасский Государственный Технический Университет
Индивидуальное задание
на тему: «Основы проектирования участков и цехов»
ст. гр. ТОМ – 03 – 2
Определение метода производства
Расчет потребного количества оборудования
Определение типа производства
Проектирование станочного отделения
1 Выбор специализации участка
2 Выбор метода расположения оборудования
3 Выбор способа ориентации станков относительно
4 Выбор расстояний между станками
5 Ширина продольного проезда
6 Площадь станочного отделения механического цеха
7 Установка оборудования при монтаже
Выбор и обоснование транспорта
Проектирование системы уборки стружки
Проектирование вспомогательных отделений
1 Проектирование складской системы
2 Проектирование ремонтной базы
3 Проектирование заточного отделения
4 Проектирование контрольного отделения
5 Проектирование отделения СОЖ
Выбор и обоснование характеристик производственного
Определение потребного количества оборудования в условиях
мелкосерийного производства
Список использованной литературы.
Шифр задания – 04Б120.
Таблица 1 – Исходные данные для проектирования линии механической
обработки детали 09 – ступица
Наименование операции
Фрезерно-центровальная
Масса заготовки – 121 кг
Рисунок 1 – Ступица
Определим минимальную программу выпуска целесообразную для организации поточного производства:
где Fэф – эффективный фонд времени оборудования
з. ср. – средний коэффициент загрузки оборудования на
линии или участке з. ср. = 065 ÷ 075;
tшт. ср. – штучное средне время основных операций:
Так как Nзад > Nmin то принимаем поточную форму организации производства для которой характерна: поштучная обработка деталей передача детали на следующую операцию сразу же после окончания предыдущей операции расположение оборудования по ходу технологического процесса организация производства на поточных линиях.
Необходимое число станков на каждую операцию:
где tшт. – штучное время на каждую операцию;
Округлим принятое число станков – Cпр.
Коэффициент загрузки станков:
Результаты расчетов сведем в таблицу 2.
Таблица 2 – Результаты расчетов необходимого количества
Определим средний коэффициент загрузки станков:
Рисунок 2 – График загрузки оборудования
Тип производства определим по коэффициенту закрепления операций:
где nд.о. – число деталь - операций закрепленных за цехом в
течение месяца nд.о. = 5;
Принимаем массовый тип производства характеризуемый: непрерывным изготовлением ограниченной номенклатуры изделий на узкоспециализированных рабочих местах что позволяет увеличивать объемы производства; применением специального и специализированного оборудования и режущего инструмента; автоматизацией операций контроля; квалификация рабочих невысокая.
Принимаем предметную специализацию участка т. к. она характерна принятому выше массовому типу производства. Предметной специализации характерна обработка конкретной детали на участке называемом линией.
Преимуществами предметной специализации являются:
- минимальные транспортные перемещения по ходу изготовления
- заинтересованность бригад в получении конечного результата.
Основным принципом при составлении плана расположения оборудования является обеспечение прямоточности движения деталей в процессе обработки в соответствии с технологическим процессом.
Принимаем расположение оборудования по ходу технологического процесса (технологически замкнутый участок) характерный крупносерийному и массовому типу производства. При этом на участке обрабатываются детали сходные по технологическому и размерному признакам.
Рисунок 3 – Схема расположения станков по технологическому
3 Выбор способа ориентации станков относительно продольного проезда
Примем продольное расположение станков относительно продольного проезда т. к. при этом облегчается подача к станку заготовок инструмента удаление отходов подвод коммуникаций. Крупные станки не должны устанавливаться возле окон т. к. это приводит к затемнению цеха.
3 Выбор расстояний между станками
Расстояния между станками выберем по нормам технологического проектирования [3 с.116].
- от проезда до тыльной и боковой стороны станка 500 мм;
- от проезда до фронтальной стороны станка 1000 мм;
- между станками при их расположении «в затылок» 1600 мм;
- между станками при их расположении боковыми сторонами друг к
- от колон до боковой стороны станка 900 мм.
Рисунок 4 – Расположение оборудования относительно стен проезда и
Ширина продольного проезда зависит от вида межоперационного транспорта и устанавливается нормами технологического проектирования. В среднем ширина проезда составляет 2 3 м. Принимаем ширину продольного проезда 3000 мм а магистральных проездов – 4000 мм .
6 Площадь станочного отделения
Площадь станочного отделения механического цеха определим укрупнено по формуле:
где Спр общ – общее количество принятых станков Спр общ = 12;
fуд – удельная площадь на один станок fуд = 25 м2 [4 с. 21].
Установка оборудования при монтаже производится по монтажным планам на которых указана «привязка» оборудования к осям колонн и метод установки.
Оборудование на участке устанавливают на общую бетонную подушку изготовленную из армированной железными прутьями сетки 25×25 см толщиной 250 – 300 мм. Отдельного фундамента не требуется так как на участке нет станков массой привышаюшей 10 т.
Размеры фундаментов в плане определяют по размерам основания оборудования. Расстояние от боковой плоскости опор станины до границы фундамента должно быть не менее 100 мм. Оборудование устанавливаемое на отдельные фундаменты крепят к фундаменту анкерными болтами. Остальное оборудование целесообразно устанавливать на виброизолирующие опоры. что упрощает перестановку станков.
Выбор и обоснование транспортных средств
Средством межоперационного транспорта примем роликовый конвейер (рольганг) неприводной. Рольганг представляет собой универсальный и конструктивно простой тип конвейера предназначенный для транспортирования деталей массой до 100 кг с плоской опорной поверхностью а также мелких деталей в таре. Высота секций рольганга 400 1000 мм ширина 400 450 мм. Для обслуживания рабочих мест в виду того что заготовка весит 121 кг применим консольные краны грузоподъемностью 025 3 т с вылетом стрелы 6 м. Время крановой операции 1 мин.
Несмотря на то что в настоящее время на машиностроительных заводах все шире внедряются малоотходные технологические процессы обработки интенсивность стружкообразования довольно велика. Стружку необходимо убирать с рабочего места и удалять за пределы производственных участков. В зависимости от количества стружки и площади на которой она образуется применяют различные системы ее уборки и транспортировки.
Количество стружки производимое на участке определим по формуле :
где : QЗ - масса заготовки QЗ = 121 кг;
QД - масса детали QД = 85 кг;
N - годовой выпуск деталей; N = 120000 штгод;
FЭ – эффективный фонд времени работы оборудования
Принимаем автоматизированную систему уборки стружки А. Система А - автоматизированная - применяется при выходе стружки более 800 кгч с площади более 3000 м2. Стружка удаляется от станков и транспортируется в отделение переработки с помощью линейных и магистральных конвейеров.
Вид и группу стружки для участка определяем по справочным данным [4 с. 23]. При обработке стали - элементообразная (мелкая крошка кусочки высечка) – I группа стружки. Принимаем конвейер шнековый одновитковый [4 с. 24].
Проектирование вспомогательных отделений ведется укрупненно по нормам технологического проектирования.
Складское хозяйство состоит из комплекса складов различного функционального назначения. Склады обеспечивающие непрерывное производство: склады материалов и заготовок межоперационные склады и склады готовой продукции - наиболее крупные. В серийном производстве склад материалов и заготовок предназначен для хранения их не значительного запаса. Чтобы не занимать дорогостоящую производственную площадь под склады их размещают под специальными эстакадами при механических цехах.
При небольшом объеме производства организуют единый общезаводской склад материалов и заготовок совместно с раскройно-заготовительным отделением (цехом). В любом случае непосредственно в цехе целесообразнее всего размещать площадки для храпения минимального запаса (2-3 дня) заготовок. Эти площадки устраивают в каждом пролете в начале станочного отделения.
Определим площадь склада заготовок для одного пролета по формуле:
где Qз – годовая потребность в заготовках:
t – число дней хранения; t = 2 дня;
q – допускаемая грузонапряженность пола q = 3 тм2;
Д – число рабочих дней в году Д = 253 дня;
k – коэффициент использования площади; k =04.
Склад размещается в начале технологического участка.
Определяем площадь склада готовой продукции по формуле:
где Qд - масса деталей проходящих через данный склад в
t – число дней хранения t = 1 день [4 с. 31];
q – допускаемая грузонапряженность пола q = 2 тм2;
k – коэффициент использования площади k = 04.
Размещается склад готовой продукции в конце цеха смежно с контрольным отделением. Ограждаются все перечисленные склады металлическими сетками.
Ремонтное отделение служит для проведения межремонтного обслуживания оборудования а также для несложного текущего ремонта приспособлений и инструмента. Число станков для ремонта оснастки и инструмента составляет 2 4 единицы. Учитывая количество станков в цехе принимаем централизованную форму организации ремонта оборудования. При количестве станков до 200 принимаем 3 обслуживающих станка в ремонтном отделении.
Определяем площадь ремонтного отделения:
где Ср - число станков для ремонта оснастки и инструмента
fуд – удельная площадь на один станок fуд = 30 м2;
Располагаем мастерскую для ремонта оснастки и инструмента смежно с инструментально-раздаточной кладовой (ИРК). Ограждается мастерская перегородками из металлической сетки.
Заточное отделение предназначено для централизованной заточки режущих инструментов.
Количество заточных станков определяется по нормам Сзо равно 4 % от общего количества станков в цехе [4 с. 25]. Площадь отделения определим по формуле:
где Сn.общ - общее число станков в цехе
f уд – удельная площадь на один станок fуд = 10 м2;
Заточное отделение располагается рядом с ИРК и ограждается стеклянными перегородками.
Контрольное отделение предназначено для организации приемочного контроля готовых деталей. В цехе принимаем выборочный контроль. Выборочный контроль позволяет уменьшить число контролеров и дает хороший результат при наличии стабильного технологического процесса. Выборочный контроль требует значительного объема выпуска для формирования корректных выборок или проб. Выборочный контроль как правило применяют при операционном контроле.
Определим потребное количество контролеров RK:
где Но норма обслуживания приходящаяся на одного
контролера Но = 18 % [4 с. 27];
Ксл - коэффициент сложности Ксл = 09 (при контроле
Rcт – число станочников обслуживаемых контрольным
Количество станочников Rcт в цехе укрупнено определяем по количеству станков:
где Cп.общ.– общее число станков в цехе Cп.общ. = 200 станков;
FЭ– эффективный годовой фонд времени оборудования
Kз.ср. – средний коэффициент загрузки оборудования
Kз.ср = 085 [4 c. 27];
FЭ.р.– эффективный годовой фонд времени рабочего
FЭ.р.=1840 ч [4 c. 27];
Км – средний коэффициент многостаночного
обслуживания Км =12 [4 c. 27].
Принимаем количество контролеров в цехе RК = 19 чел.
Определим площадь контрольного отделения по формуле:
где RК – число контролеров RК = 19 чел.;
fуд – удельная площадь приходящаяся на одного
контролера fуд. = 5 м2;
Размещаем контрольное отделение в конце цеха; отделение ограждается стеклянными перегородками. Контрольные пункты располагаем в конце участка. Размеры площадок для контрольных пунктов – 22 м.
Отделение для приготовления и раздачи смазочно-охлаждающих жидкостей проектируют для небольших цехов серийного производства. Укрупнено площадь отделения СОЖ определим в зависимости от количества производственного оборудования: 50 м2.
Площадь склада масел для смазки оборудования принимаем 15 м2. Отделение СОЖ является пожароопасным поэтому его выгораживают несгораемыми перегородками (кирпич бетон) и размещают у наружной стены здания с отдельным выходом наружу.
6 Проектирование инструментально-раздаточной кладовой
Инструментально-раздаточная кладовая (ИРК) служит для хранения всех видов инструмента и оснастки а так же выдачи их на рабочие места.
Для небольших и средних цехов (до 200 станков) устраивается комплексная ИРК для всех видов инструментов. Расчет площади комплексной ИРК производится по нормам [4 с. 25].
где Собщ - общее число станков в цехе Собщ = 200;
НИ – норма расчета площади кладовой инструментов на один станок НИ = 023;
НО – норма расчета площади кладовой оснастки на один станок НО = 05.
Размещается ИРК в стороне от основных грузопотоков но не далее 70 м от наиболее удаленного рабочего места; ограждается металлической сеткой.
Выбор и обоснование характеристик производственного здания
Стоимость производственных зданий составляет значительную часть (приблизительно 40%) стоимости основных фондов машиностроительного предприятия.
Факторами определяющими основные тенденции при проектировании современных промышленных зданий являются: сокращение времени на проектирование улучшение бытовых условий работающих.
В значительной степени перечисленным факторам соответствуют производственные здания имеющие размеры и параметры установленные на основании единой модульной системы (ЕМС). Базой единой модульной системы (ЕМС) является основной строительный модуль (М) который равен 100 мм. Основной модуль (М) служит для получения производных модулей - укрупненных и дробных.
Согласно ЕМС размеры ширины пролетов и шагов принимаются кратными укрупненным модулям 60М (6 м) и ЗОМ (3 м). Высота этажей производственных помещений принимается кратной укрупненным модулям 12М (12 м) и 6М (06 м) зданий административно-бытового назначения кратной модулю ЗМ (0Зм).
Для размещения механосборочного производства применяются одноэтажные и многоэтажные здания. Одноэтажные здания имеют ряд преимуществ перед многоэтажными зданиями и составляют в общем объеме промышленного строительства приблизительно 85% причем крановые - 20 25% а бескрановые - 60 65%. Многоэтажные здания применяются в легком машиностроении при ограниченной площади строительного участка. Одноэтажные здания могут иметь полный или неполный каркас. У зданий с полным каркасом вертикальными несущими элементами являются колонны; внешние стены выполняют функции ограждающих элементов.
При массовом типе производства применяют главным образом схему с полным каркасом которая позволяет использовать унифицированные строительные конструкции и соответствует всем требованиям ЕМС.
Реализуя принцип блокирования в одном производственном здании обычно размещают несколько цехов с однородными технологическими процессами. Габариты здания по рекомендациям формируем из унифицированных типовых секций (УТС). Одна УТС имеет размеры 72 х 72 м и площадь 1584 м2. Если потребуется здание с большей площадью то к УТС добавим еще одну секцию 72х72 м в направлении ширины здания.
Сетка колонн характеризует соотношение шага колонн и ширины пролета (А х В). Расстояния А и В измеряются между осями колонн.
Для производственных зданий механических и сборочных цехов рекомендуется применять унифицированные сетки колонн с размерами: 12 х 18 м 12 х 24 м; 12 х 30 м; 12 х 36 м.
Сетка колонн 12 х 18 м является основной сеткой предпочтительного применения. По периметру здания (под стенами) унифицированный шаг А равный 12 м следует уменьшить до 6 м.
Высота пролета определяется как расстояние от уровня пола здания до нижней затяжки несущей фермы (для бескрановых зданий) или расстояние от уровня пола до головки подкранового рельса (для крановых зданий).
Рисунок 5 – Схема определения высоты кранового пролета
оснащенного краном консольным поворотным с
Предварительно высоту пролета рассчитаем исходя из типа подъемно-транспортного оборудования (кран консольный поворотный с электроталью) габарита обрабатываемых деталей и высоты технологического оборудования. На рисунке 5 представлена схема определения высоты кранового пролета Н.
Н = А1 + А2 ++ А4 + А5 + А6
где Н - высота пролета;
А1 - высота оборудования по паспорту А1 = 3872 мм;
А2 - страховой зазор в пределах 400 мм;
A3 - габарит детали (груза) 200 мм;
А4 - высота стропов А4 1000 мм;
А5 - резерв при верхнем положении крюка А5= 300 мм;
А6 – определяется по паспорту крана или по
ГОСТ 7890-67 но не менее 12м.
Н = 3872 + 400 + 200 + 1000 + 300 + 1200 = 6972 мм.
Окончательно принимаем унифицированное значение высоты пролета секции ближайшее к расчетному значению Н = 72 м.
Определение потребного количества оборудования в условиях мелкосерийного производства
Зная массу детали и тип производства определим программу выпуска N = 1200 штгод.
Определим программу запуска:
Месячная программа запуска:
Средняя трудоемкость операций:
где – сумма всех штучных времен на всех операциях
n – количество операций n = 5.
Средняя загрузка одного рабочего места:
Определим удельную трудоемкость месячной программы запуска:
где Fэ.м. – эффективный фонд времени оборудования при
числе смен в месяц j = 45 Fэ.м. = 300 ч.
Продолжительность выпуска деталей за месяц:
Принимаем Ф = 1 смены.
Месячный эффективный фонд времени оборудования соответствующий продолжительности выпуска детали:
Расчетное количество станков каждой модели:
где - суммарное штучно-калькуляционное время
использования станка данной модели по технологическому
Расчетное количество станков модели 2Г942 (операция 005):
Коэффициент загрузки:
Расчетное количество станков модели 1Н713 (операция 010):
Расчетное количество станков модели 1Н713 (операция 015):
Расчетное количество станков модели 53А20 (операция 020):
Расчетное количество станков модели 2Г175 (операция 025):
Так как Кз не превышает нормативных значений Кз.н. [1 с. 65] то принятое количество Сn оставляем без изменений.
По результатам расчетов строим график загрузки оборудования (рисунок 6).
Рисунок 6 - График загрузки оборудования при мелкосерийном
Список использованной литературы
Демьянюк Ф. С. Технологические основы поточно-автоматизированного производства 1968
Мамаев В. С. Осипов Е. Г. Основы проектирования машиностроительных заводов 1974
Мельников Г. Н. Вороненко В. П. Проектирование механосборочных цехов. Учебник для студентов машиностроит. специальностей вузов Под ред. А. М. Дальского – М. Машиностроение 1990. – 352 с.
Основы проектирования механосборочных участков и цехов Уч. Пособие. 2002 А. А. Егоров С. Ю. Стародубов
Проектирование машиностроительных заводов и цехов. Справочник в 6-ти Т. Т. 4 Под ред. Е. С. Ямпольского 1975
Фрагмент12.frw

Планировака цеха Дж..cdw

Участок по выпуску детали " вилка" F =595 м
Коэффициент загрузки
6Т82Г Горизонтально-фрезерный 8
2Г175 Вертикально-сверлильный 2
53А20 Шлицефрезерный 1
- Стол контрольный 1
Магистральный проезд
Условные обозначения
- Перегородка с сеткой
- Перегородка из стеклоблоков
- Ворота одностворчатые
- Колонна железобетонная
График загрузки оборудования
22363.frw

6Т82Г Горизонтально-фрезерный 8
2Г175 Вертикально-сверлильный 2
53А20 Шлицефрезерный 1
- Стол контрольный 1
Магистральный проезд
Условные обозначения
- Перегородка с сеткой
- Перегородка из стеклоблоков
- Ворота одностворчатые
- Место складирования деталей
- Колонна железобетонная
График загрузки оборудования
Участок по выпуску детали " вилка" F =595 м
Записка по цехам.doc
Кафедра: технологии и организации машиностроительного производства
Семестровое задание
По дисциплине: «Основы проектирования участков и цехов»
Определение метода производства
Определение потребного количества оборудования в условиях поточного производства
Определение типа производства
1 Выбор специализации участка
2 Выбор метода расположения оборудования
3 Выбор способа ориентации станков относительно магистрального проезда
4 Выбор расстояний между станками
5 Ширина продольного проезда
6 Площадь станочного отделения механического цеха
7 Установка оборудования при монтаже
Выбор и обоснование транспортных средств
Проектирование системы уборки стружки
Проектирование вспомогательных отделений
1 Проектирование складской системы
2Проектирование ремонтного отделения
3Проектирование заточного отделения
4Проектирование контрольного отделения
5Проектирование отделение СОЖ
6 Проектирование инструментально – раздаточной кладовой (ИРК)
Обоснование и выбор основных характеристик производственного здания
3 Выбор сетки колонн
4Выбор высоты пролётов
Расчет количества оборудования в условиях мелкосерийного производства
Наименование операции
Время перехода рабочего от станка к станку при многостаночном обслуживании = 015 мин.;
Материал заготовки Сталь 40Х;
Годовая программа выпуска = 120000 (штгод);
Масса заготовки 69 кг;
Существует два метода производства: поточное и непоточное (партионное) производство.
Для организации поточного производства необходимо единственное немаловажное условие: достаточная загрузка рабочих мест одной деталью (одним изделием).
Определяем минимальную программу выпуска обеспечивающую заданный коэффициент загрузки по формуле из (2 стр. 20)
где – эффективный фонд времени оборудования для универсального оборудования 4015 часов;
- оптимальный коэффициент загрузки для поточного производства.
- среднее штучное время 70%.
Так как то это поточное производство
Минимальная программа выпуска будет равна:
Учитывая тип метод производства определяем потребное количество станков по исходным данным.
Количество станков рассчитываем отдельно для каждой операции по формуле и округляем до целого числа из(2 стр. 14):
где- расчетное время итой операции.
- такт выпуска расчетной линии.
где 4015 часов – эффективный фонд времени.
Таблица 1.1 – количество оборудования на участке.
где - коэффициент загрузки оборудования .
Расчетный коэффициент загрузки не должен превышать нормативного значения для данного типа станка. из (2 прил. Б2 стр.38).
Составляем график загрузки оборудования для поточной линии.
Рисунок 1.1 – График загрузки оборудования
Тип производства влияет на выбор оборудования (универсальное специальное специализированное) на выбор характера оснастки (универсальное специальное либо вообще отсутствует) на выбор режущего инструмента и мерительного инструмента на квалификацию рабочих на выбор транспортных средств.
Тип производства в реальных условиях определяется по стандартному коэффициенту закрепления операций.
Где - количество деталь-операций закрепленных за цехом в течении одного месяца; =5;
- принятое число единиц оборудования.
Так как входит в пределы 0-5 то принимаем массовый тип производства.
Тип производства можно также определить укрупнённо из (1 табл. 31). Так как 49 и годовая программа выпуска 120000 штгод тогда у нас массовый тип производства.
Проектирование станочного отделения
Для массового и крупносерийного производства где естественной является предметная целевая специализация цехов и участков. Такая структура обеспечивает прямоточность производственного процесса когда в конце поточных линий обработки располагаются участки узловой сборки а дальше выполняется сборка агрегатов или изделий.
Метод расположения оборудования зависит от метода производства и от вида специализации участка.
В поточном производстве оборудование располагается по ходу технологического процесса детали которая обрабатывается на поточной линии. При этом руководствуются следующими правилами:
) Участки занятые станками должны быть наиболее короткими:
) Технологические линии могут располагаться как вдоль так и поперек:
) Станки могут располагаться вдоль участка в 23 и более ряда. При расположении станков в 2 ряда между ними должен быть проезд для транспорта.
Принимаем продольное расположение тогда станок фронтальной стороной отражен к проезду так как это наибольше приемлемый вариант. При таком расположении облегчается подача к станку заготовок инструмента удаление отходов подвод коммуникаций.
При размещении оборудования в соответствии с выбранным вариантом необходимо обеспечить установленное расстояние между оборудованием при различных вариантах размещения а также ширину проездов. (1. табл. 49 с. 116) Между тыльными сторонами станков 800 мм.
Между станками по фронту 900 мм.
От стен колон до тыльной стороны станка 800 мм.
Ширину магистральных проездов по которым осуществляются межцеховые перевозки при транспортировке электротележкой принимаем равнойА=3000 мм Б=3400мм. Относительно продольного проезда станки могут располагаться вдоль поперёк и т.д.
Рисунок 4.1 – Ширина магистрального проезда
6 Определение площади участка
Площадь станочного отделения механического цеха определяется укрупнено по формуле:
где. – общее число станков = 105 шт;
. – удельная площадь на единицу оборудования (2. с. 21) = 12 .
Принимаем установку оборудования на:
) На полу устанавливаем легкие станки общего назначения с массой до 3 тонн(6Т82Г m=2530кг);
) На общие фундаменты устанавливаем остальные станки так как их масса меньше 10 тонн(2Г175 m=4250кг; 1Н713 m= 4700кг; 53А20 m=6800кг).
Средства межоперационного транспорта (МОТ) применяются для перемещения обрабатываемых деталей между рабочими местами.
В поточном производстве средства межоперационного транспорта должны обеспечивать бесперебойную поштучную передачу деталей от станка к станку а также размещение на них транспортных и страховых заделов.
Для данного участка в качестве межоперационных транспортных средств принимаем конвееры роликовые однорядные.
В качестве внутрицехового транспорта (для перемещения грузов внутри цеха между участками и складскими помещениями) принимаем подвесные однобалочные краны с грузоподъемностью 1 - 5 тонн и пролетом 3 – 12 м так как такой тип подъемно-транспортного оборудования наиболее приемлем в данном случае. Подвесные кран балки имеют ряд преимуществ: они не требуют установки колонн для подкрановых путей что увеличивает полезную площадь цеха; имеют малые габариты по вертикали что позволяет получить большую высоту подъема груза и т.д.
Проектирование системы сборки стружки
Несмотря на то что в настоящее время на машиностроительных заводах малоотходные технологические процессы обработки интенсивность стружкообразования достаточна высока. Стружку необходимо убирать с рабочего места и удалять за пределы производственных участков. В зависимости от количества стружки и площади на которой она образуется применяют различные системы её уборки и транспортировки.
Количество стружки производимое на поточной линии можно определить по формуле:
где - выход стружки кгчас;
– масса заготовки =69 кг;
– масса детали =49 кг;
– годовой выпуск =120000 шт.год;
– эффективный фонд времени оборудования =4015 час.
В частных случаях применяем комбинированную систему убора стружки: стружка удаляется от станков и перетранспортируется на линию конвейеров и убирается в специальную тару которая по мере заполнения вывозится из цеха.
Вид и группу стружки для участка или линии определяют по (2. табл. 2.3 с. 23) группа стружки 2 (в виде витков нагартованная колечки).
Зная группу стружки по (2 табл. 2.4 стр. 24) принимаем тип конвейера для транспортировки стружки: шнековый одновинтовой.
Проектирование вспомогательных отделений ведется укрупнено по нормам технологического проектирования.
1 Проектирование складского хозяйства
Складское хозяйство состоит из комплекса складов разного функционального назначения. Непосредственно в цехе целесообразнее всего размещать площадки для хранения минимального запаса (2 – 3 дня) заготовок. Эти площадки устанавливают в каждом пролёте в начале станочного отделения.
Размеры площадок для одного пролёта определяем по формуле (2 стр. 30):
где - масса заготовок обрабатываемых на участке (в пролёте в течение года):
– время хранения деталей на складе =3 дня (2. табл. 2.8 с. 31);
– допускаемая загруженность пола=2;
– коэффициент использования площади =04
Размещается склад готовой продукции в конце цеха смежного с контрольным отделением. Ограждается металлическими сетками.
Площадь склада готовой продукции:
где - масса готовых деталей обрабатываемых в цехе в течении года;
где =3 дня – время хранения деталей на складе (2. табл. 2.8 с. 31).
1 Проектирование ремонтного отделения
Служит для ремонтного обслуживания оборудования а также для несложного приспособления и инструмента.
Площадь ремонтной мастерской можно определить по формуле:
где – число станков для мастерской = 3(шт.);
– удельная площадь приходящаяся на один станок. = 30 ()
Располагается мастерская для ремонта станка и инструмента смежно с инструментальной мастерской (ИРК). Ограждается мастерская металлической сеткой.
2 Проектирование заточного отделения
Заточное отделение предназначено для централизованной заточки режущего инструмента.
Заточное отделение располагается рядом с ИРК и ограждается стеклянными перегородками.
Площадь заточного отделения можно рассчитать по формуле:
где =5шт. – число станков в заточном отделении;
=12м. – удельная площадь на один станок.
3 Проектирование контрольного отделения
Контрольное отделение предназначено для организации приёмного контроля годных деталей. По оценки охвата применяемый контроль подразделяется на сплошной и выборочный.
Выборочный контроль требует значительного объема выпуска для формирования корректных выводов или проб. Выборочный контроль как правило принимают при операционном контролем.
Потребное количество контролёров в серийном и массовом производстве:
где – число станочников обслуживающим контрольным отделением.
где - общие число станков в цехе =105шт;
– эффективный фонд времени оборудования =4015час;
– средний коэффициент загрузки оборудования =085;
– эффективный годовой фонд времени рабочего.=1840 часов;
– средний коэффициент многостаночного обслуживания =12;
– норма обслуживания приходящаяся на одного контролёра =20;
(2 табл. 2.7 стр. 27);
– коэффициент сложности=11 (2 стр. 26).
Площадь контрольного отделения определим по формуле:
=5. – удельная площадь приходящаяся на одного контролёра.
Размещается контрольное отделение в конце цеха ограждается стеклянными перегородками. Также предусматривается площадка контрольных пунктов 1010 .
4 Проектирование отделение СОЖ
Отделение для приготовления к раздачи смазочно-охлаждающих жидкостей (СОЖ) проектируют для небольших цехов мелко серийного и средне серийного производства. Для крупных цехов проектируют эмульсионное хозяйство включающую эмульсионную станцию систему регуляции.
Укрупнено площадь отделения СОЖ может быть определена в зависимости от количества производственного оборудования (2 стр. 28).
Площадь склада масел для смазки оборудования можно принять 10 20 м. Отделение СОЖ является пожароопасным потому его ограждают несгорающими перегородками (кирпич бетон) и размещают у наружной стены здания с отдельным выходом наружу.
Инструментально – раздаточная кладовая (ИРК) служит для хранения всех видов инструмента и оснастки а также выдачи их на рабочем месте.
Для небольших цехов и средних (до 200 станков) устанавливается комплексная ИРК для всех видов инструментов. Расчет площади комплексной ИРК производится по нормам приведенным в (2 табл. 2.5 стр. 25).
Факторами определяющими основные тенденции при проектировании совместных промышленных зданий являются: сокращение времени на проектирование; улучшение бытовых условий работающих.
В значительной степени факторам соответствуют производственные здания имеющие размеры и параметры установленные на основании единой модульной системы (ЕМС). Базой ЕМС является основной строительный модуль (М) который равен 100 мм. Основной модуль (М) служит для получения производных модулей – укрупнённых и дробных.
Согласно ЕМС размеры ширины пролётов и шагов принимаются кратными укрупнённым модулям 60М (6м) и 30М (3м). Высота этажей производственных помещений принимается кратной укрупнённым модулям 12М (12м) и 6М (06м) зданий административно-бытового назначения – кратной модулю 3М (03м).
Здание принимаем одноэтажное. Одноэтажные здания имеют ряд преимуществ перед многоэтажными зданиями. Многоэтажные применяются только в легком машиностроении при ограниченной площади строительного участка. Одноэтажные здания могут иметь полный или не полный каркас. У зданий с полным каркасомвертикальными несущими элементами являются колонны; внешние стены выполняют ограждающую функцию. У зданий с неполным каркасом колонны размещаются внутри здания а по его периметру функции несущих элементов выполняют стены.
Кровли зданий могут быть скатными и плоскими; могут быть светоаэрационные фонари (фонарные кровли) и могут не иметь таковых (безфонарные).
Принимаем одноэтажное здание с полным каркасом и светоаэрационным фонарем.
Реализуя принцип блокирования в одном производственном здании обычно размещают несколько цехов с однородными технологическими процессами. Габариты здания рекомендуется формировать из унифицированных типовых секций (УТС). Одна УТС имеет размеры 7272 м. и площадь 5184 . Если требуется здание с большей площадью то к УТС добавляют еще одну секцию 7272 м. в направлении ширины здания.
Сетка колон характеризует соотношение шага колонн и ширины пролёта (АВ). Расстояния А и В измеряются между осями колонн.
Для производственных зданий механических и сборочных цехов рекомендуется применять унифицированные сетки колонн с размерами: 1218 м.; 1224 м.; 1230 м.; 1236 м.
Принимаем сетку колонн равной 1218 м. так как она является основной сеткой предпочтительного применения.
2 Выбор высоты пролётов
Высота пролёта определяется как расстояние от уровня пола здания до нижней затяжки несущей фермы или расстояние от уровня пола до головки подкранового рельса. Предварительно высоту пролёта рассчитывают исходя из типа оборудования габаритов деталей. Окончательно принимается унифицированное значение высоты пролёта секции ближе к расчетному значению. Действующими нормами технологического проектирования (Госстрой СССР СН 223 - 62) установлены основные строительные характеристики которыми необходимо руководствоваться при проектировании машиностроительных заводов.
где А1=3385 мм ( высота самого высокого станка на участке);
А2 = 400мм (страховой зазор);
А3 = 1000мм (габарит груза);
А4 = 1000мм (высота стропов);
А5 = 500 мм (резерв при верхнем положении крюка);
А6 = 2000 мм (по ГОСТ 7890-67).
Н=3385+400+1000+1000+500+2000=8285 мм
Из стандартных значений по (2. стр. 8 табл. 2.1) принимаем высоту пролётов в пределах 84 м.
.рисунок 8.1 – Высота пролетов здания
Расчет количества оборудования в условиях непоточного производства
Программа выпуска шт.год.
Определяем программу запуска:
Определяем месячную программу запуска:
Определяем среднюю трудоёмкость операции:
Определяем среднюю загрузку рабочего места данной деталью в месяц:
Определяем удельную трудоёмкость месячной программы запуска детали:
где – эффективный фонд времени оборудования часов при числе смен в месяц
Определяем продолжительность выпуска детали за месяц:
Принимаем Ф=2 смены.
Определяем месячный эффективный фонд времени оборудования соответствующий продолжительности выпуска детали час:
Определяем расчетное количество станков каждой модели по формуле:
где - суммарное штучное время использования станка данной модели по технологическому процессу.
Таблица 9.1 – количество оборудования на участке.
Так как не превышает нормативных значений принятое количество станков оставляем без изменения. Средний коэффициент загрузки станков при обработке детали определяется по формуле:
Составляем график загрузки оборудования на участке:
Количество станков принятое
Рисунок 9.1 – График загрузки оборудования в условиях непоточного производства.
Мельников Г. Н. Вороненко В. П. Проектирование механосборочных цехов; Учебник для студентов машиностроительных специальностей вузовПод рад. А. М. Дальского – М.: Машиностроение 1990. – 352 с.: ил. – (Технология автоматезировонного машиностроения).
А. А. Егоров С. Ю. Стародубов Основы проектирования механосборочных участков и цехов: Учеб. Пособие (для студ. спец. 7.090.202 «Технология машиностроения»). – Алчевск: ДГМИ 2002. – 48 с.
Планировака цеха Дж1,1,2.frw

22363.dwg

6Т82Г Горизонтально-фрезерный 8
2Г175 Вертикально-сверлильный 2
53А20 Шлицефрезерный 1
- Стол контрольный 1
Магистральный проезд
Условные обозначения
- Перегородка с сеткой
- Перегородка из стеклоблоков
- Ворота одностворчатые
- Место складирования деталей
- Колонна железобетонная
График загрузки оборудования
Участок по выпуску детали " вилка" F =595 м
пл1.frw

цех нах.cdw

Вертикально-сверлильный
Установка автоматического
Площадка для хранения заготовок
Кран консольный поворотный
Станочное отделение по обработке детали "Вилка" F=548м
Перегородка из стеклоблоков
Перегородка из металлической сетки
Технологическое оборудование
Подвод питьевой воды
схема транспортных грузопотоков.frw

загрузка2.frw

расчётно-пояснительная записка по механосборочным цехам.doc
Донбасский государственный технический университет
Кафедра: технологии и организации машиностроительного производства
По дисциплине: «Основы проектирования участков и цехов»
Алчевск 2009Содержание
Определение метода производства4
Расчёт потребного количества оборудования6
Определение типа производства9
Проектирование станочного отделения11
1 Выбор специализации участка
2 Выбор метода расположения оборудования
3 Выбор способа ориентации станков относительно продольного проезда
4Выбор расстояний между станками
5Ширина продольного проезда
6Площадь станочного отделения механического цеха
7Установка оборудования при монтаже
Выбор и обоснование транспорта
Проектирование системы уборки стружки
Проектирование вспомогательных отделений
1Проектирование складской системы
2Проектирование ремонтной базы
3Проектирование заточного отделения
4Проектирование контрольного отделения
5Проектирование отделения СОЖ
6Проектирование инструментально – раздаточной кладовой
Выбор и обоснование основных характеристик производственного здания
Определение потребного количества оборудования в условиях мелкосерийного производства
Исходные данные для проектирования линии механической обработки детали 03 –«Вилка» (рисунок 1.1). Маршрут механической обработки детали представлен в таблице 1.
Таблица 1 – Маршрутный технологический процесс обработки детали 03 «Вилка»
Материал детали – сталь 40Х.
Масса заготовки - 85 кг.
Масса детали – 60 кг.
Программа выпуска: 100000 деталей в год.
Время перехода рабочего от станка к станку при многостаночном обслуживании tпер=015мин.
Рисунок 1.1 – Эскиз детали 03 - «Вилка».
Определение метода производства
Определим минимальную экономически целесообразную программу выпуска изделий для организации поточного производства по формуле:
где Fэф – эффективный фонд времени работы оборудования принимаем Fэф=4015 часов;
зср – средний коэффициент загрузки оборудования принимаем зср=0.65
tшт.ср – штучное среднее время изготовления детали по основным механическим операциям определяется по формуле:
где tштi – время выполнения механической операции
n – количество механических операций.
Подставив в формулы известные величины получим:
Сравним Nmin с заданной программой:
Так как Nз> Nmin принимаем поточную форму производства.
Характерные признаки организации поточного производства: расчленение процесса изготовления продукции на ряд составных частей на более или менее простые операции и закрепление их за отдельными рабочими местами (станками) или за группой одинаковых рабочих мест; повторение одних и тех же процессов на каждом рабочем месте; оснащение рабочих мест поточной линии специальным оборудованием инструментом приспособлениями обеспечивающими высокопроизводительное выполнение закрепленных операций; транспортная направленность регламентирующая все производство во времени и в пространстве; высокая степень механизации и автоматизации процессов производства; непрерывно повторяющееся единообразие всех производственных факторов качества и форм материалов инструментов и приспособлений; равномерность выпуска продукции на основе единого расчетного такта поточной линии; одновременное выполнение всех составных частей процесса.
Синхронизация выравнивание длительности всех операций необходима для того чтобы каждое предыдущее рабочее место потока непрерывно давало работу каждому последующему рабочему месту без пролеживания предметов труда и простоев оборудования.
Расчет потребного количества оборудования
В поточном производстве потребное количество станков рассчитывается для каждой операции по формуле:
где tштi – штучное время выполнения операции мин.
tв – такт выпуска мин. определяется по формуле:
Nз – заданная программа выпуска детали «Вилка» Nз=100000 штук.
Подставив в формулы известные и ранее найденные величины получим:
Приведём расчётное число станков Cр для каждой операции к принятому округлив расчётное значение до ближайшего большего Cпр и найдём коэффициент загрузки по операциям:
Рассчитаем средний коэффициент загрузки оборудования на участке:
Результаты расчётов сведём в таблицу 2.1
Таблица 2.1 – Оборудование участка
Наименование операции
Зная количество станков каждой модели найдём средний коэффициент загрузки оборудования на участке:
Построим график загрузки оборудования и обозначим на графике средний коэффициент загрузки оборудования зср (рисунок 2.1). Он позволяет наглядно продемонстрировать загрузку каждой единицы оборудования на участке и в цеху в целом:
Рисунок 2.1 – График загрузки оборудования на участке
Определение типа производства
Рассчитаем коэффициент серийности (коэффициент закрепления операций) по формуле:
где nдо – число деталь – операций закреплённых за цехом в течении 1 месяца принимаем nдо=5 деталь – операций;
Cпр – принятое число станков на участке Cпр=14 станков; подставив в формулу найденные величины получим:
Kсер показывает количество операций закреплённых в среднем за одним рабочим местом уровень специализации рабочих мест.
Так как Kсер 1 то принимаем массовый тип производства. Массовое производство отличается наибольшей специализацией и характеризуется изготовлением ограниченной номенклатуры деталей в больших количествах. Цехи массового производства оснащаются наиболее совершенным оборудованием позволяющим почти полностью автоматизировать изготовление деталей. Большое распространение получили здесь автоматические поточные линии.
Технологические процессы механической обработки разрабатываются более тщательно по переходам. За каждым станком закрепляется относительно небольшое количество операций что обеспечивает наиболее полную загрузку рабочих мест. Оборудование располагается цепочкой по ходу технологического процесса отдельных деталей. Рабочие специализируются на выполнении небольшого количества операций. Детали с операции на операцию передаются поштучно. В условиях массового производства возрастает значение организации межоперационной транспортировки технического обслуживания рабочих мест. Постоянный контроль за состоянием режущего инструмента приспособлений оборудования - одно из условий обеспечения непрерывности процесса производства без которого неизбежно нарушается ритмичность работы на участках и в цехах. Необходимость поддержания заданного ритма во всех звеньях производства становится отличительной особенностью организации процессов при массовом производстве.
Массовое производство обеспечивает наиболее полное использование оборудования высокий общий уровень производительности труда самую низкую себестоимость изготовления продукции.
Проектирование станочного отделения (линии)
Применительно к механообработке и сборке в массовом и крупносерийном производстве в основном создают механосборочные предметно-специализированные цехи. При предметной специализации участков участки специализируют по признаку изготовляемых изделий (деталей) ; при этом в одном цехе сосредотачивается всё оборудование необходимое для полного изготовления сборочной единицы (детали).
Для цехов и участков массового и крупносерийного производства естественной является предметная целевая специализация участков (участок изготовления деталей и сборки коленчатого вала с маховиком участок изготовления деталей и сборки масляного насоса и другие). Такая структура обеспечивает прямоточность производственного процесса когда в конце поточных линий получают готовую деталь или сборочную единицу.
Ориентация участков на законченный конечный результат существенное уменьшение внешних связей значительно упрощают решение проблем разделения и согласования труда и способствуют приобретению ими свойств самоорганизации и саморегулирования.
Подетальная и предметная формы организации участков линий и цехов обеспечивают организационные и социальные преимущества по сравнению с технологической формой так как при этих формах в большей степени обеспечиваются непрерывность прямоточность и ритмичность производственного процесса а коллективы бригад и участков в большей степени могут влиять на конечные результаты труда. При этих формах организации создаются более благоприятные условия для внедрения хозяйственного расчета в бригадах линий и участков.
В условиях массового и крупносерийного производства основной организационной формой являются предметно-специализированные поточные линии.
Основным принципом при разработке плана расположения оборудования на участке является обеспечение прямоточности движения деталей в процессе их обработки в соответствии с технологическим процессом а также определение расстояний между оборудованием и колоннами и стенами.
Метод расположения оборудования зависит от метода производства и от вида специализации участка.
В поточном производстве оборудование располагается по ходу технологического процесса детали которая обрабатывается на поточной линии (рисунок 4.1):
Рисунок 4.1 – Схема расположения оборудования по ходу техпроцесса.
Продольное расположение когда станок фронтальной стороной обращён к проезду – наиболее удобный вариант. При таком расположении облегчается подача к станку заготовок инструмента удаление отходов подвод коммуникаций. Примем продольное расположение для станков так как их количество невелико и сформированный таким способом участок возможно будет вписать в типовой цех.
4 Выбор расстояний между станками
Для осуществления обслуживания и ремонта оборудования необходимо предусмотреть достаточные расстояния между станками колоннами и стенами. По [1. табл. 4.9 с. 116] принимаем:
-от проезда до фронтальной стороны станка (а) – 1000 мм;
-между станками при расположении их боковыми сторонами друг к другу (б) – 900 мм;
-от стен колон до тыльной стороны станка (в) - 800 мм (рисунок 4.2).
Рисунок 4.2 – Расстояния между станками и строительными конструкциями
5 Ширина продольного проезда
Примем по рекомендациям [1 c. 116]. Ширину продольного проезда принимаем 3 метра для проезда внутрицехового транспорта – электротележки. Ширину магистральных проездов по которым осуществляются межцеховые перевозки принимаем равной 5 метров.
6 Площадь станочного отделения механического цеха
Определим площадь станочного отделения укрупнено по формуле:
Где Сп.пр – число станков данного типоразмера на участке:
-средние станки – 10;
fуд – удельная производственная площадь:
-для малых станков – 12м2;
-для средних – 25 м2;
Точная площадь станочного отделения определённая по плану расположения оборудования в цеху составляет F=548 м2.
7 Установка оборудования при монтаже
Для лёгких станков общего назначения с массой до 3 тонн (6Т82Г m=2530кг) принимаем установку на полу.
На общие фундаменты устанавливаем остальные станки так как их масса находится в пределах 3-10 тонн (2Г175 m=4250кг; 1Н713 m= 4700кг; 53А20 m=6800кг).
Выбор и обоснование транспортных средств
Обрабатываемая деталь «Вилка» имеет массу 6 кг и относится к средним по массе деталям. По форме деталь «Вилка» является представителем класса вилок. Для удобства загрузочно-разгрузочных операций деталь будет транспортироваться на поддонах. Деталь «Вилка» выполнена из твёрдого металлического материала.
Для данного участка в качестве межоперационных транспортных средств принимаем конвейеры роликовые однорядные (рольганги) обладающие следующими свойствами и возможностями:
-по назначению – межоперационный вид транспорта;
-по способу перемещения грузов - как в таре так и без тары;
-по принципу движения – периодическое;
-по направлению движения – прямоточное;
-по уровню расположения – эстакадный (на уровне руки рабочего);
-по принципу работы – грузонесущая транспортная система;
-по схеме движения – линейная;
-по конструктивному исполнению – безрельсовая.
Так как заготовка имеет массу 85 кг на первых операциях для перемещения заготовок принимаем подвесной однобалочный кран грузоподъёмностью до 5 т. И пролётом 3-12 м.
Схема транспортных грузопотоков приведена на рисунке 4.3.
В качестве внутрицехового транспорта принимаем электрические тележки с подъёмником так как они просты в управлении бесшумны обладают высокой манёвренностью не требуют широких проездов и больших радиусов закруглений обладают грузоподъёмным краном который позволяет снизить трудоёмкость погрузочно-разгрузочных работ.
Рисунок 5.1 – Схема транспортных грузопотоков на участке
Найдём количество стружки производимое на поточной линии:
Где qс – выход стружки в кгчас;
Qз – масса заготовки 85 кг;
Qд – масса детали 6 кг;
N – годовой выпуск 100000в год;
Fэ – эффективный годовой фонд времени оборудования 4015 час.
Подставив в формулу известные величины получим:
Так как на участке большинство станков – фрезерные то будет образовываться преимущественно стружка группы 1 - элементообразная (мелкая крошка кусочки высечка). Так как скорость образования стружки на участке невелика это позволит отказаться от механизированной системы уборки стружки. В проектируемом участке стружка будет собираться в ящики для стружки и периодически вывозиться электрокарами.
1 Проектирование складского хозяйства
Складское хозяйство состоит из комплекса складов разного функционального назначения. Непосредственно в цехе целесообразнее всего размещать площадки для хранения минимального запаса (2 – 3 дня) заготовок. Эти площадки устанавливают в каждом пролёте в начале станочного отделения.
Размеры площадок для одного пролёта определяем по формуле (2 стр. 30):
где t – время хранения деталей на складе t=3 дня (2. табл. 2.8 с. 31);
g – допускаемая загруженность полаg=2;
k – коэффициент использования площади k=04;
Д – число рабочих дней в году 253 дня;
Qз - масса заготовок обрабатываемых на участке в течение года определяется по формуле:
где N – программа выпуска деталей N=100000шт;
Gз – масса заготовки 8.5 кг;
Подставив в уравнение известные величины получим:
Размещается склад готовой продукции в конце цеха смежного с контрольным отделением. Ограждается металлическими сетками.
Площадь склада готовой продукции:
где t – время хранения деталей на складе t=3 дня (2. табл. 2.8 с. 31);
k – коэффициент использования площади k=04;
Qд - масса готовых деталей обрабатываемых в цехе в течении года: определяется по формуле:
где Gд – масса готовой детали 6 кг; подставив ранее найденные значения в формулу получим:
Склад готовой продукции принимаем по укрупнённым данным:
2 Проектирование инструментально – раздаточной кладовой (ИРК)
Инструментально – раздаточная кладовая (ИРК) служит для хранения всех видов инструмента и оснастки а также выдачи их на рабочем месте.
Для небольших цехов и средних (до 200 станков) устанавливается комплексная ИРК для всех видов инструментов. Расчет площади комплексной ИРК производится по нормам приведенным в (2 табл. 2.5 стр. 25).
Размещается ИРК в стороне от основных грузопотоков но не далее 70 м от наиболее удалённого рабочего места ограждается металлической сеткой.
3 Проектирование заточного отделения
Заточное отделение предназначено для централизованной заточки режущих инструментов. Количество заточных станков определяется по нормам [2 стр. 25 табл. 2.6]. Принимаем 4 заточных станка. Площадь заточного отделения определяется по формуле:
Где Cзо – число станков в заточном отделении 4 станка;
fуд – удельная площадь на один заточной станок принимаем 12 м2 подставив значения в формулу получим:
Заточное отделение располагается рядом с ИРК и ограждается стеклянными перегородками.
4 Проектирование контрольного отделения
Контрольное отделение предназначено для организации приёмного контроля годных деталей. По степени охвата приёмочный контроль подразделяется на сплошной и выборочный.
Выборочный контроль требует значительного объема выпуска для формирования корректных выводов или проб. Выборочный контроль как правило принимают при операционном контроле.
Потребное количество контролёров в серийном и массовом производстве определяется по формуле:
где Но – норма обслуживания приходящаяся на одного контролёра по [2 табл. 2.7 стр. 27] принимаем Но=20;
Kсл – коэффициент сложности Kсл=11 (2 стр. 26);
Rст – число станочников обслуживаемых контрольным отделением определяется по формуле:
Где Сп.общ - общие число станков в цехе Сп.общ=70 шт;
Fз – эффективный фонд времени оборудования Fз =4015час;
Кз.ср – средний коэффициент загрузки оборудования Кз.ср=085;
Fэр – эффективный годовой фонд времени рабочего Fэр=1840 часов;
Км – средний коэффициент многостаночного обслуживания Км=12;
Подставив в формулы найденные значения величин и коэффициентов получим:
Площадь контрольного отделения определяется по формуле:
Где fуд=5. – удельная площадь приходящаяся на одного контролёра.
Окончательно получим:
Размещается контрольное отделение в конце цеха ограждается стеклянными перегородками. Контрольные пункты располагаются в конце участка. Размеры площадок для контрольных пунктов -2x2 метра.
5 Проектирование ремонтного отделения
Ремонтное отделение служит для проведения межремонтного обслуживания оборудования а также для несложного текущего ремонта приспособлений и инструмента.
Площадь ремонтной мастерской можно определить по формуле:
где Сn.м. – число станков для мастерской Сn.м. = 3(шт.);
fуд. – удельная площадь приходящаяся на один станок. fуд. = 30 ()
Располагается мастерская для ремонта станка и инструмента смежно с инструментальной мастерской (ИРК). Ограждается мастерская металлической сеткой.
6 Проектирование отделения для приготовления и раздачи смазочно-охлаждающих жидкостей
Укрупнено площадь отделения СОЖ может быть определена в зависимости от количества производственного оборудования по рекомендациям [2 стр. 28]: принимаем площадь отделения СОЖ равной 48м2.
Площадь склада масел для смазки оборудования можно принять 10 20м2. Отделение СОЖ является пожароопасным потому его выгораживают несгораемыми перегородками (кирпич бетон) и размещают у наружной стены здания с отдельным выходом наружу.
Выбор и обоснование характеристик производственного здания
Одноэтажные здания имеют ряд преимуществ перед многоэтажными зданиями. Многоэтажные здания применяются только в легком машиностроении при ограниченной площади строительного участка поэтому принимаем одноэтажное здание. Одноэтажные здания могут иметь полный или не полный каркас. У зданий с полным каркасом вертикальными несущими элементами являются колонны; внешние стены выполняют ограждающую функцию. У зданий с неполным каркасом колонны размещаются внутри здания а по его периметру функции несущих элементов выполняют стены. В массовом строительстве принимают главным образом схему с полным каркасом которая позволяет использовать унифицированные строительные конструкции и соответствует всем требованиям ЕМС поэтому применяем схему с полным каркасом.
Кровли зданий могут быть скатными и плоскими; могут быть светоаэрационные фонари (фонарные кровли) и могут не иметь таковых (безфонарные). Принимаем скатную кровлю со светоаэрационным фонарем так как такая кровля позволит улучшить освещение и аэрацию цеха.
Реализуя принцип блокирования в одном производственном здании обычно размещают несколько цехов с однородными технологическими процессами. Габариты здания рекомендуется формировать из унифицированных типовых секций (УТС). Одна УТС имеет размеры 72×72 м. и площадь 5184 м2. Если требуется здание с большей площадью то к УТС добавляют еще одну секцию 72×72 м. в направлении ширины здания. Для проектируемого цеха принимаем производственное здание состоящее из одной УТС 72×72.
Сетка колон характеризует соотношение шага колонн и ширины пролёта (АВ). Расстояния А и В измеряются между осями колонн.
Для производственных зданий механических и сборочных цехов рекомендуется применять унифицированные сетки колонн с размерами: 1218 м.
Принимаем сетку колонн равной 1218 м. так как она является основной сеткой и её применение предпочтительно. По периметру здания (под стенами) унифицированный шаг А равный 12 м следует уменьшить до 6 м.
Высота пролёта определяется как расстояние от уровня пола здания до нижней затяжки несущей фермы. Предварительно высоту пролёта рассчитывают исходя из типа подъёмно-транспортного оборудования габаритов обрабатываемых деталей высоты технологического оборудования. Окончательно принимается унифицированное значение высоты пролёта секции ближайшее к расчетному значению.
где А1=3530 мм ( высота станка 2Г175 - самого высокого на участке);
А2 = 400мм (страховой зазор);
А3 = 1000мм (габарит груза);
А4 = 1000мм (высота стропов);
А5 = 500 мм (резерв при верхнем положении крюка);
А6 = 1500 мм (по ГОСТ 7890-67).
Н=3530+400+1000+1000+500+1500=7930 мм
В соответствии с действующими нормами технологического проектирования (Госстрой СССР СН 223 - 62) по [2. стр. 8 табл. 2.1] принимаем высоту пролётов в пределах 84 м (рисунок 8.1).
Рисунок 8.1 – Высота пролёта здания цеха
Исходные данные приведены в таблице 9.1
Таблица 9.1 – Исходные
Программа выпуска шт.год.
Определяем программу запуска:
Определяем месячную программу запуска:
Определяем среднюю трудоёмкость операции:
Определяем среднюю загрузку рабочего места данной деталью в месяц:
Определяем удельную трудоёмкость месячной программы запуска детали:
где Fэм =300 часов - эффективный фонд времени оборудования при числе смен в месяц j=45;
Определяем продолжительность выпуска детали за месяц:
Принимаем Ф=2 смены.
Определяем месячный эффективный фонд времени оборудования соответствующий продолжительности выпуска детали час:
Определяем расчетное количество станков каждой модели по формуле:
где tki - суммарное штучное время использования станка данной модели по технологическому процессу.
Округлим расчётное число станков до ближайшего большего целого Cn и определим коэффициент загрузки для каждой операции по формуле
Полученные значения сведём таблицу 9.2.
Таблица 9.2 – Количество оборудования на участке.
Так как Кзi не превышает нормативных значений Kзni принятое количество станков оставляем без изменения. Средний коэффициент загрузки станков при обработке детали «Вилка» определяется по формуле:
В соответствии с данными таблицы 9.2 построим график загрузки оборудования (рисунок 9.1).
Рисунок 9.1 – График загрузки оборудования в условиях не поточного
Мельников Г. Н. Вороненко В. П. Проектирование механосборочных цехов; Учебник для студентов машиностроительных специальностей вузовПод рад. А. М. Дальского – М.: Машиностроение 1990. – 352 с.: ил.
А. А. Егоров С. Ю. Стародубов Основы проектирования механосборочных участков и цехов: Учеб. Пособие (для студ. спец. 7.090.202 «Технология машиностроения»). – Алчевск: ДГМИ 2002. – 48 с.
Мамаев В. С. Осипов Е. Г. Основы проэктирования машиностроительных заводов. М.: «Машиностроение» 1974. – 290 с. с ил.
Демъянюк Ф. С. Технологические основы поточно-автоматизированного производства. – М.: Высшая школа 1968. – 700 с.
Проектирование машиностроительных заводов и цехов. Справочник. В 6-ти т. Т. 4. Под ред. Е. С. Ямпольского. – М.: Машиностроение 1975. -326с.
эскиз детали.frw

График загрузки.frw

Рекомендуемые чертежи
- 08.01.2024
- 03.06.2021
- 27.11.2021
- 24.01.2023