Разработка конструкции вертикального - фрезерного станка




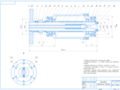
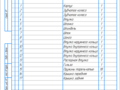
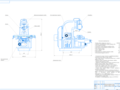
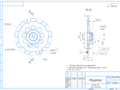
- Добавлен: 25.01.2023
- Размер: 2 MB
- Закачек: 1
Описание
Разработка конструкции вертикального - фрезерного станка
Состав проекта
![]() |
![]() ![]() ![]() ![]() |
![]() ![]() ![]() ![]() |
![]() ![]() ![]() ![]() |
![]() ![]() ![]() ![]() |
![]() ![]() ![]() ![]() |
![]() ![]() ![]() |
Дополнительная информация
Решетка.cdw

Неуказанные радиусы R2*. Неуказанные фаски 2х45
Спецификация(А4).cdw

Втулка внутреннего кольца
Подшипник С224-46217
Станок CIH 1235.cdw

Блок переключения скорости
Техническая характеристика
Размеры рабочей поверхности стола
Мощность электродвигателя главного движения
Число скоростей шпинделя 18
Минимальная частота врашения шпинделя
Максимальная частота вращения шпинделя
Класс точности станка Н
Число Т-образных пазов 3
Максимальный угол поворота фрезерной головки 45
Максимальная нагрузка на стол
Вертикально-фрезерный станок
Технологический ресурс точности по отработанному времени
в ремонтном цикле станка не менее 11200час.
Срок службы станка до 1 капитального ремонта при 2-х сменной
работе не менее 6 лет
Движение столов и суппортов на всех режимах и рабочих
скоростях должно быть без скачков
предназначенные для окраски отчистить от пыли
жировых и других загрязнений
Внешний вид лакокрасочных покрытий по ГОСТ 22133-76
Кнопки "Пуск" углубить на 8мм
расстояние между краями не менее 60мм
сжатого воздуха в местах соединений и
уплотнений не допускается
Станок перед приемно-станочным испытанием установить по
уровню с точностью 0
компоненты вибрации шпиндельной
сборки на максимальной частоте вращения не более:
ммс; виброускорения 7
Приводные ремни МГД перед установкой вытянуть в течении 70
часов при удельной нагрузке 2МПа
Требования к электрооборудованию станка по ГОСТ7599-92
Стол(А2).cdw

Острые кромки притупить фаской 0
Общие допуски по ГОСТ 30893.1-2002 Н12
Шпиндельная сборка(А2).cdw

остальные для справок.
Направление вращения - по часовой стрелке (при наблюдении
Шпиндель обкатать при n=1350 мин
в течении 2-х часов.
Избыточная температура не более 15
хода не более 5 кВт.
Наибольшее торцевое биение внутренних колец подшипников
должно быть направлено в противоположную сторону наибольшего
биения торцев шпинделя.
Записка.docx
федеральное государственное бюджетное образовательное учреждение
«СИБИРСКИЙ ГОСУДАРСТВЕННЫЙ УНИВЕРСИТЕТ НАУКИ И ТЕХНОЛОГИИ ИМ. АКАДЕМИКА М. Ф. РЕШЕТНЕВА»
по дисциплине: «Металлорежущие станки»
Разработка конструкции вертикального – фрезерного станка С06
(подпись дата) (инициалы фамилия)
Диаметр МРИчисло зубьев фезы
Частота вращения n max
Класс вибрации точность 1-ой 2-ой опоры
Длина втулки между 1-ой и 2-ой опорой
Перечень разрабатываемого графического материала:
Деталь «Решетка» – формат А3
Чертеж общего вида станка – формат А1
Шпиндельная сборка – формат А2
Дата выдачи проекта:
В данном курсовом проекте выполнен анализ различных конструкций вертикально фрезерных станков разработан вертикально фрезерный станок повышенного класса точности. Выбран асинхронный электродвигатель разработана кинематическая схема механизма главного движения.
Разработанный вертикально фрезерный станок может быть использован в различных отраслях единичного и мелкосерийного производства имеющих основные и вспомогательные цеха по обработке металлов.
In this course project an analysis of various designs of vertically milling machines is made a vertically developed milling machine of increased accuracy class is developed. An asynchronous electric motor a kinematic scheme of the main motion mechanism has been developed.
Designed milling machine with rotary table can be used in various branches of individual and small-scale production with main and auxiliary plant for the processing of metals.
In diesem Kursprojekt werden verschiedene Konstruktionen von Vertikalfrsmaschinen analysiert und eine vertikal entwickelte Frsmaschine mit erhhter Genauigkeitsklasse entwickelt. Ein asynchroner Elektromotor wurde ausgewhlt ein kinematisches Schema des Hauptbewegungsmechanismus wurde entwickelt.
Eine vertikal entwickelte Frsmaschine kann in verschiedenen Zweigen der Einzel- und Kleinproduktion eingesetzt werden in denen Haupt- und Nebenwerksttten fr die Metallverarbeitung vorhanden sind.
Аналитическая часть7
1 Фрагментарный бизнес- план проекта7
2 Патентно- лицензионный обзор8
3 Системный анализ аналогов и выбор прототипа станка19
4 Конструктивные проработки и описание прототипа26
5 Определение класса точности станка. Расчет радиального биения шпинделя28
Технологическая часть29
1 Определение предельных режимов резания.29
2 Выбор электродвигателя33
3 Разработка кинематической схемы механизма главного движения36
3.1 Построение структурной сетки36
3.2 Построение графика частот вращения38
3.3 Построение кинематической схемы39
Конструкторская часть41
1 Расчет и выбор параметров шпинделя41
2 Выбор подшипников формирование посадок и определение допусков42
3 Расчет долговечности подшипников45
4 Расчет ресурса точности и времени безотказной работы станка46
5 Определение эксцентриситета оси вращения шпинделя47
6 Описание сборочного чертежа МГД операции его сборки47
Безопасность и экологичность проекта49
1 Безопасность эксплуатации проектной разработки49
Исследовательская часть52
1 Построение станочного конфигуратора.52
2 Расчет инструмента на прочность53
Библиографический список56
Приложение A. Параметрическая матрица транзитивности для системного анализа технологического оборудования.58
Приложение Б. Допустимый остаточный удельный дисбаланс.59
Для любого промышленного предприятия большое значение имеет качество его оснащения высокотехнологичным оборудованием которое дает возможность выполнить необходимую обработку разнообразных деталей.
В первую очередь фрезерные станки нужны для точной обработки плоских и фасонных поверхностей тел вращения зубчатых колес и тому подобных металлических и других изделий.
Актуальным является проектирование и производство оборудования удовлетворяющим требованиям машиностроительных производств.
Целью данной работы является разработки конструкции портального обрабатывающего центра.
Для достижения этой цели необходимо решить следующие задачи:
произвести патентно-лицензионный обзор аналогов;
проанализировать аналоги и выбрать прототип станка;
изучить прототип станка;
определить класс точности станка;
рассчитать технологическую часть;
рассчитать и разработать конструкцию станка;
проанализировать разработанную конструкцию.
1 Фрагментарный бизнес – план проекта
Целью данного курсового проекта является разработка конструкции вертикально-фрезерного станка. Для выполнения данного курсового проекта необходимо решить ряд задач - это выполнение расчетов и разработка чертежа общего вида станка стола шпиндельной сборки детали которая будет обрабатываться на данном станке.
Назначение данного станка: фрезерование и сверление сложных корпусных деталей.
Основные технические параметры станка: перемещение по оси Z – 350 мм размер стола – 305x1400 мм максимальная нагрузка на стол – 500 кг максимальная скорость вращения шпинделя – 1350 обмин мощность привода – 11 кВт.
Перечень работ которые необходимо выполнить при разработке вертикально-фрезерного станка: разработка конструкторско-технологической документации на изготовление промышленного образца с выполнением расчетов на прочность и жесткость. Проектирование изготовление деталей механизмов резания. Запрашиваемый объем финансирования: 900 тыс. руб. Срок окупаемости проекта: 20 года. Первичные исследования выполнены на установках базового предприятия и станочной конструкции. СибГУ показала возможность получения поверхностей 7 квалитета точности не уступающих точности станков ведущих мировых производителей.
Отработаны режимы резания. Теоретические проработки выполнены для создания серийного модуля. Направление совершенствования потребительских свойств состоит в увеличении производительности а эксплуатационные характеристики повысить в 12 раза в части ресурса точности гарантийное обслуживание обеспечивается разработчиком по авторскому надзору сроки достижения улучшений 18 месяцев после сдачи в эксплуатацию первого образца. Реализация проекта в виде товарного изделия услуги в освоении технологии силового резания монтажа и запуска в производство.
Ожидаемый результат: документальное обеспечение изготовления и внедрение станка новой модификации.Реализация проекта производится кафедрой ТМС. Организационная форма реализации проекта: демонстрация на региональных выставках; изготовление и распространение рекламных проспектов с описанием технических характеристик станка. Сроки выполнения проекта: 3 года. Рынки сбыта: машиностроительная техника автомобильная промышленность.
Динамика спроса: круглогодичная – постоянная. Социальная эффективность: развитие технологий и общества. Анализ долговременных последствий проекта: увеличение сбыта станков; улучшение технических характеристик станка.Неблагоприятные последствия: изготовление специализированных станков с ограниченным спектром действий.
2 Патентно- лицензионный обзор
Цель патентно-лицензионного обзора – минимизировать риск связанный с дублированием уже существующих технических решений на начальном этапе разработки объекта. [1].
B23C106Одношпиндельные вертикальные станки
Алдонов А.А. Болдырев И.С.
Патентообладатель(и):
Общество с ограниченной ответственностью "РЕАДИ ЛТД
подача заявки: 20.07.2005
публикация патента: 27.11.2005
Универсальный настольный станок содержащий основание установленный на основании с возможностью горизонтального перемещения стол для размещения обрабатываемой заготовки и закрепленную на основании вертикальную стойку на которой установлена с возможностью поворота в вертикальной плоскости и передвижения по вертикали шпиндельная головка снабженная устройством для зажима инструмента кинематически связанным через шпиндель с электродвигателем отличающийся тем что шпиндельная головка установлена на стойке посредством подвижного и снабженного средством фиксации на стойке кронштейна в корпусе шпиндельной головки с возможностью осевого перемещения и фиксации в необходимом положении установлена гильза в которой закреплен на верхней и нижней подшипниковых опорах шпиндель устройство для зажима инструмента расположено на нижнем конце шпинделя а на верхнем конце шпинделя выполнены продольные шлицы электродвигатель расположен на кронштейне вертикально кинематическая цепь от электродвигателя к устройству для зажима инструмента включает последовательно коробку скоростей смонтированную внутри кронштейна и расположенные внутри шпиндельной головки находящиеся в зацеплении друг с другом два двойных блока зубчатых колес один из которых установлен с возможностью управляемого от наружной рукоятки осевого перемещения вдоль вертикального вала имеющего на своем нижнем конце коническое зубчатое колесо находящееся в зацеплении с коническим зубчатым колесом закрепленным на внешнем конце выходного вала коробки скоростей а второй двойной блок закреплен на радиальных подшипниках в корпусе шпиндельной головки и имеет осевое шлицевое отверстие в котором установлен снабженный шлицами верхний конец шпинделя нижний конец гильзы выступает за плоскость нижнего торца шпиндельной головки и в месте расположения нижней подшипниковой опоры шпинделя имеет цилиндрическое утолщение с плоской кольцевой площадкой предназначенной для контакта с плоскостью нижнего торца корпуса шпиндельной головки.
Станок по п.1 отличающийся тем что отношение разности длины гильзы и величины ее максимального хода к диаметру части гильзы установленной в головке может быть выбрано из интервала значений от 08 до 12.
Станок по любому из пп.1 и 2 отличающийся тем что на нижнем торце корпуса шпиндельной головки выполнен кольцевой прилив ограниченный изнутри цилиндрической поверхностью а снаружи - поверхностью усеченного конуса при этом диаметр цилиндрической поверхности прилива соответствует наружному диаметру цилиндрического утолщения гильзы шпинделя.
B23C302Фрезерование поверхностей вращения
Коптев Иван ТихоновичОмигов Борис ИвановичГордон Анатолий МихайловичКольцов Владимир Иванович
Федеральное государственное унитарное предприятие "Государственный космический научно-производственный центр имени М.В. Хруничева" (ФГУП "ГКНПЦ им. М.В. Хруничева")
подача заявки: 17.07.2012
публикация патента: 10.06.2014
Способ фрезерования крупногабаритных нежестких оживальных оболочек сопел жидкостных ракетных двигателей (ЖРД) включающий установку заготовки оживальной оболочки сопла ЖРД на оправке профиль наружной поверхности которой эквидистантен профилю наружной поверхности оживальной оболочки сопла ЖРД фрезерование пазов на ее наружной поверхности и снятие заготовки с оправки отличающийся тем чтоиспользуют оправку состоящую из неподвижной части и подвижной верхней части в виде съемника который устанавливают с возможностью перемещения вверх посредством трех нажимных болтов при упоре их в торец неподвижной части при снятии с оправки отфрезерованной заготовки оживальной оболочки сопла ЖРД при этом для обеспечения жесткости между оправкой и оживальной оболочкой сопла ЖРД используют гипсовый раствор а для предотвращения деформации оболочки обеспечивают Выполнение условия:
Fсцеп.- сила сцепления между гипсом и оживальной оболочкой сопла
Sбок.- площадь боковой поверхности оживальной оболочки сопла ЖРД
расположенная ниже съемника мм2 определяемая как
L - высота конуса оживальной оболочки сопла ЖРД мм;
d1- малый диаметр конуса оживальной оболочки сопла ЖРД мм;
d2- большой диаметр конуса оживальной оболочки сопла ЖРД мм;
- среднее значение угла наклона оживальной оболочки сопла ЖРД
Sсеч.- площадь поперечного сечения оживальной оболочки сопла ЖРД в
месте стыковки подвижной и неподвижной частей оправки мм2;
в- предел прочности материала оживальной оболочки сопла ЖРД
B23C114С вращающимся рабочим столом
Кривилев А.И.Широбоков С.В.
подача заявки: 20.08.1993
публикация патента: 20.06.1996
Изобретение относится к области машиностроения а именно к
многосторонней обработке корпусных деталей на карусельно-фрезерных станках для непрерывного фрезерования.
Известен автомат для непрерывного фрезерования деталей одновременно с двух сторон а также одновременной обработки двух разных групп деталей содержащий карусельный стол с гнездами для подвода заготовок в зону обработки подпружиненные колодки взаимодействующие с головками винтов для зажима заготовок в гнездах стола бункеры для подачи заготовок к столу приводные фрезерные головки для фрезерования пазов в заготовках неподвижные ступенчатые секторы
В описанном выше изобретении предусмотрена бункерная загрузка автоматизированы процесс установки и зажима деталей а также поворот деталей на определенный угол посредством фрикционной ленты для дальнейшей обработки. Перекладывание с одной позиции обработки на другую осуществляется путем опускания детали на следующий сектор.
Автомат для непрерывного фрезерования деталей содержащий станину поворотный стол закрепленное на нем многоместное приспособление с гнездами для обрабатываемых деталей включающими пазы и зажимные элементы автоматический механизм загрузки автоматический механизм разгрузки с кулачковым механизмом управления и двухшпиндельную фрезерную головку отличающийся тем что он содержит консоль с автооператорами по числу обрабатываемых поверхностей детали плюс один размещенную с возможностью поворота на дополнительно введенной и установленной по оси стола стойке которая снабжена фиксирующим консоль относительно многоместного приспособления устройством при этом автоматический механизм загрузки также снабжен кулачковым механизмом управления совмещенным с кулачковым механизмом управления механизма разгрузки и расположенным на стойке соосно с консолью а автооператоры размещены на последней радиально с охватом равного их числу количества гнезд многоместного приспособления.
3 Системный анализ аналогов и выбор прототипа станка
В этом разделе приводится описание конструктивных особенностей станков аналогов.
Для удобства анализа аналогов и выбора прототипа станка составляем карту анализа аналогов подобранных моделей станков. см. табл. 1.1.
Таблица 1.1. Карта анализа аналогов
Размеры рабочей поверхности мм
Наибольший вес обрабатываемой детали кг
Т – образные пазы мм
Наибольшее перемещение станка мм:
Число скоростей подач
Пределы скоростей подач мммин:
Пределы ускорения подач мм:
Расстояние от цента стола до вертикальных направляющих мм
Расстояние от конца шпинделя до поверхности рабочего стола мм
Перемещение гильзы шпинделя мм
Продолжение таблицы 1.1
Расстояние от цента шпинделя до колонны мм
max поворот вертикальной фрезерной головки град
Число скоростей шпинделя
Пределы скоростей шпинделя обмин
Мощность основного двигателя кВт
Мощность двигателя подачи кВт
НапряжениеЧастота ВГц
Вертикально-фрезерный станок 6Л12-1применяется для фрезерования различных деталей из стали чугуна и цветных металлов торцевыми фасонными цилиндрическими дисковыми и другими фрезами. Может использоваться для обработки плоских наклонных поверхностей пазов и шестеренок в ручном режиме а при соответствующих настройках - в полуавтоматических или автоматических циклах работы с возможностью организации многостаночного обслуживания.
Станки модели 6Л12-1 находят применение на механических и ремонтных участках предприятий различных сфер деятельности как в единичном так и в серийном производстве а также в мастерских и учебных классах профтехобразовательных учреждений.
Особенности конструкции
Вертикальное перемещение шпиндельной гильзы;
Автоматическая и ускоренная подачи рабочего стола;
Возможна обработка вертикальных горизонтальных и наклонных плоскостей пазов углов рамок и зубчатых колес;
Высокая мощность двигателей широкий диапазон скоростей и жесткость станков позволяют использовать быстрорежущий и твердосплавный инструмент;
Полная система смазки и охлаждения обеспечивают долгий срок службы всех аппаратных частей станков;
Станокоснащен поворотной вертикальной фрезерной головкой;
Удобное расположение всех элементов управления.
В качестве дополнительного оборудованияна фрезерном станке 6Л12-1возможна установка УЦИ (устройство цифровой индикации).
Универсальный фрезерный станокКорвет-611 предназначен для фрезерных сверлильных и резьбонарезных работ с заготовками из металла всех видов пластмасс и древесины.
Вертикальный и горизонтальный шпиндели.
Для каждого шпинделя отдельный двигатель.
Наклон вертикального шпинделя вправо и в влево.
Регулировка глубины сверления.
Автоматическая подача рабочего стола по оси ХY.
Автоматическая подача шпинделя.
Функция нарезания резьбы.
Защитное ограждение рабочего стола.
Встроенная система подачи СОЖ.
Лампа местного освещения.
Устройство цифровой индикации по 3-м осям
Вертикально-фрезерный станок DMTG XA7140 для решения любых работ по фрезерованию сверлению расточки и т.д. на промышленном производстве.
Настолько простая компоновка станка удивляет он состоит из неподвижной станины станка с широкими прямоугольными направляющими которые увеличивают жесткость станка и уменьшают до минимума вибрации при перемещении салазок и рабочего стола в процессе работы вертикальной колонны очень большим столом с размерами 1400х400 мм а также его большим перемещением по оси Х 1000мм и диапазоном скорости подачи стола 18~627 мммин (9 ступеней) обеспечивает обработку очень больших заготовок в то время как у аналогичных станков стол и перемещение по оси Х меньше что ставит нашу модель ХА7140 на одну ступень выше чем его аналоги.
Также в состав станка входят усовершенствованная подвижная под наклоном 30 градусов влевовправо от вертикали шпиндельная бабка и коробка передач которая дает работу со станком как в ручном режиме так и в автоматическом установлена по последнему слову техники система СОЖ которая обеспечивает бессбойный полив охлаждающей жидкости в зону работы станка. Пиноль выдвигается на 105 мм что не только дает большое преимущество среди аналогов но и очень расширяет технологические работы на станке. Данная модель выдерживает весом 800 кг заготовку на своем столе.
У этой модели станка есть вертикальный шпиндель стандартом DIN 2080 NT50 благодаря которому можно устанавливать оправки под сверло с кМ5 (до диаметра 76 мм) и оправки под торцевую фрезу с посадкой диаметр 60 (фреза диаметр до 300 мм) и вертикальная фрезерная голова с углом наклона +-30 делает данный станок очень производительным.
Благодаря разработке и внедрению в данную модель станок в стандартном исполнении имеет защиту от перегрузки шпинделя аварийной остановки и от нулевого напряжения что обеспечивает полную остановку станка при срабатывании угрозы.
Опционально уже на данную модель станка установлена система (УЦИ) Устройство Цифровой Индикации с оптическими линейками 5 мкм (микрон) по трем осям что способствует не только удобству работы на станке но и точности обработки.
Вертикальный консольно-фрезерный станок Stalex X5032A широко используется в единичном и серийном производстве. Станок данного вида пользуется высокой популярностью предназначен для фрезерования всевозможных деталей из стали чугуна и цветных металлов торцовыми концевыми цилиндрическими радиусными и другими фрезами - используются для обработки плоскостей наклонных плоскостей пазов шестерен и т.д. Вертикальный консольно-фрезерный станок широко используется в единичном и серийном производстве. Станок данного вида пользуется высокой популярностью предназначен для фрезерования всевозможных деталей из стали чугуна и цветных металлов торцовыми концевыми цилиндрическими радиусными и другими фрезами - используются для обработки плоскостей наклонных плоскостей пазов шестерен и т.д. Охлаждение подается двигателем центробежного вертикального насоса по трубопроводам через сопло к инструменту. Обработка винтовой поверхности доступна при установке делительной головки и подключении вала передачи делительной головки к продольному ходовому винту передачи рабочего стола. Обработка кулачков и дуговых пазов доступна при установке поворотного стола. Станок используется в таких областях как: ремонтные станции крупные заводы и так далее. Станок очень удобен в эксплуатации. Продольная поперечная и вертикальная подача стола контролируется ручками а направление ручек совпадает с направлением движения стола. Перед вращением какого-либо маховичка его следует ввести в зацепление. Кнопки START и STOP запускают и останавливают при нажатии кнопки START начинает вращаться только шпиндель а все рычаги находятся в нейтральном положении. Быстрая подача стола запускается кнопкой быстрой подачи стола во время обычной подачи. После отпускания данной кнопки подача возвращается в норму. Быстрая подача стола не запускается без нормальной подачи стола. Сначала необходимо перевести ручку переключателя шпинделя в нейтральное положение подача стола начнется при нажатии кнопки START. Быстрая подача стола запускается при нажатии быстрой подачи после установки ручки на нужное направление.
Вертикальный универсальный фрезерный станок по металлуJET JTM-1254LTSпредназначен для выполнения фрезерных работ различной степени сложности. Голова станка имеет наклон в двух направления что позволяет увеличить гамму обрабатываемых изделий а подвижный хобот позволяет выводить шпиндель на 518 мм.
Станок произведен на Тайване что гарантирует высокое качество компонентов и сборки. Два года гарантии обеспечит Вам спокойствие в работе.
Большой стол 300х1372 мм
Автоматическая система смазки
Автоматическая подача пиноли шпинделя
Реверс для нарезания резьбы
4 Конструктивные проработки и описание прототипа
В стандартную комплектацию станка (рис. 1.1) входит шпиндель 1500 обмин с конусом 7:24 ISO 50(рис.1.2) смазки и подачи СОЖ под давлением регулируется специальным клапаном. Жесткость рамной конструкции состоящей из массивной станины и «Г» образной колонны позволяют добиться высокой стабильности позиционирования и мощности при механической обработке. Точность обработки соответствует 7 квалитету. Станина из модифицированного чугуна основание которой позволяет перемещаться рабочему столу в направлениях X Y и Z в то время как шпиндель совершает движение по оси Z.
Рис. 1.1 – Вертикальный консольно-фрезерный станок Stalex X5032A
Рис. 1.2 – Шпиндель в жестком корпусе
Шпиндель установлен в жестком литом корпусе что исключает наличие вибраций и повышает точность обработки. Пуск и останов шпинделя быстрое перемещение стола имеют видимые кнопки подача стола контролируется ручками или кнопками направление подачи согласовано с направлением поворота ручки управления скорость шпинделя и контролируется регулятором скорости.
Компоновка вертикального консольно-фрезерного станка Stalex X5032A: вертикальная.
Главное движение или движение резания – вращение шпинделя с режущим инструментом; движение подачи –вертикальное перемещения шпинделя с режущим инструментом.
Оси станка: ось Z– ось шпинделя; ось X Y – ось перемещения рабочего стола.
5 Определение класса точности станка. Расчет радиального биения шпинделя
Первый параметр R рассчитывается по данным рабочего чертежа по наиболее точному размеру и качеству поверхности [3 с.55].
где Ra – шероховатость обработанной поверхности;
где es – верхнее предельное отклонение; ei–нижнее предельное отклонение на выдерживаемый размер.
Расчетные значения параметров сравнивают с Rт.е. с ближайшим табличным значением соответствующего класса точности станка из параметрической матрицы транзитивности
Принимаем класс точности металлорежущего станка: Н
Радиальное биение шпинделя:
где А – параметрический показатель станка выбирается из матрицы транзитивности для конкретного класса точности станка.
Радиальное биение 18 мкм.
В ходе выполнения аналитической части был выполнен фрагментный бизнес план проекта патентно-лицензионный поиск системный анализ аналогов и выбор прототипа. Принят класс точности станка: Н. Рассчитано радиальное биение шпинделя которое составило 18 мкм.
Технологическая часть
1 Определение предельных режимов резания.
Операция 020 Фрезерование пазов
Эскиз операции показан на рисунке 2.1.
Рисунок 2.1 – Эскиз операции
Материал заготовки сталь У8.
Сталь инструментальная углеродистая
Химические свойства материала представлены в таблице 2.1.
Таблица 2.1 – Химический состав материала У8
Твердость материала 187 МПа
Режущий инструмент: Фреза концевая 2223-0129 ГОСТ 17026-71 показана на рисунке 2.2.
Материал режущей части фрезы Р6М5.
Рисунок 2.2 – Фреза концевая 2223-0129 ГОСТ 17026-71 период стойкости Т=45 мин.
Расчёт режимов резания
По карте 72 лист 1 выбираем составляющие показатели числа стадий обработки пазов в зависимости от [2.ст 203]:
твердости обрабатываемого материала
отношения вылета фрезы к диаметру
отношение ширины фрезерования к диаметру фрезы
Исходя из допуска на выполняемый размер определяют показатель числа стадий обработки по следующей формуле
где -допуск выполняемого размера в мм
= 0052·115·1·1·2=012;
Полученное значение показателя числа стадий обработки является критерием выбора необходимого количества стадий обработки
где- максимальный и минимальный припуск D-диаметр инструмента
= 01207 (см. карту 72 лист 2. поз №10 инд «ж»)
Требуемая точность может быть достигнута за две (черновую и получистовую) стадии обработки.
Выбор глубины резания.
Для криволинейного участка глубина резания рассчитывается по формуле [2.ст 154]
где r – радиус обработки D – диаметр инструмента П – припуск на обработку «+» – для выпуклой обработки «-» – для вогнутой обработки
Подачу на зуб для черновой обработки пазов выбираем по карте 79 [2.ст 213] для получистовой – по карте 80 [2.ст 215]
=010 ммзуб (Карта 79 поз. №6 инд. «4») – черновой проход.
=004 ммзуб (Карта 80 поз. №5 инд. «б») – чистовой проход.
Выбранное значение подачи корректируют с учетом поправочных коэффициентов по формуле
По карте 82 [2.ст 218] выбирают поправочные коэффициенты для измененных условий работы в зависимости от:
материал режуще части фрезы
отношение фактического числа зубьев к нормативному
отношение вылета фрезы к диаметру 1;
Подача допустимая по шероховатости обработанной поверхности 006 ммоб (карта 83 поз. №8 инд. «б») [2.ст 219]
Окончательно принимаем минимальное значение = 006 ммзуб = 0024 ммзуб.
Выбор скорости и мощности резания.
Скорость и мощность резания выбирают по карте 84 [2.ст 220] с учетом поправочных коэффициентов в зависимости от:
группы обрабатываемого материала
твёрдости обрабатываемого материала
материала режущей части фрезы
периода стойкости режущей части фрезы
отношение фактической ширины фрезерования к нормативной
состояние поверхности заготовки
Табличные значения скорости и мощности резания;
vТ = 25 ммин (карта 84 поз. №12 инд. «в») – для черновой обработки
vТ = 36 ммин (карта 84 поз. №12 инд. «а») – для чистовой обработки
NТ = 081 кВт (карта 84 поз. №12 инд. «г»)
vчерн = vТ·KT = 25·1·115·1·115·115·1·1 = 38 ммин
vчист = vТ·KT = 31·1·115·1·115·115·1·1 = 47 ммин
N = NT·KN = 081·1·090·1·115·115·1·1 = 1 кВт
Выбор окружной силы резания.
Поправочный коэффициент KMP для стали: [2. табл. 19.2]:
По таблице определяем показатели степени= 682; q=086; y=072; w=0;
Частота вращения шпинделя рассчитывается по формуле
где V– скорость резания ммин D – диаметр инструмента.
По паспорту станка прототипа принимаем ближайшее значение nф = 1350 мин-1. С учетом этого фактическая скорость резания
где nф – фактическая частота вращения шпинделя мин-1 D – диаметр инструмента.
Фактическая мощность резания определяется по формуле
2 Выбор электродвигателя
Выбор электродвигателя осуществляется по мощности при выборе двигателя привода механизма главного движения МРС необходимо учитывать четыре основных принципа: мощность должна быть «немалой» чтобы не было перегрева и «не большой» для экономии – недогруз снижает КПД; крутящий момент должен быть достаточным для пуска МРС; частота вращения должна обеспечивать диапазон работы станка; конструкция должна быть удобна для монтажа.
Для выбора электродвигателя для привода главного движения необходимо по максимальной эффективной мощности резания рассчитанной в режимах резания найти приведенную мощность по формуле
где коэффициент полезного действия = 070 085
Выбор двигателя производится по мощности т.е. расчетную приведенную мощность округляют в большую сторону и выбирают двигатель по справочнику.
Учитывая тот факт что на проектируемом оборудовании будут обрабатываться различные детали а расчетное приведенная мощность мала выбор двигателя осуществляем исходя из прототипа.
Выбираем асинхронный двигатель переменного тока АИР100L2 рисунок 2.3.
Рисунок 2.3 – Установочные размеры двигателя АИР100L2
Установочные численные значения которым соответствуют буквенные значения представленные на рисунке приведены в таблице 2.2.
Таблица 2.2 - Установочные численные значения электродвигателя
Концы валов цилиндрические
Электродвигатель АИР 100L2 относится к наиболее распространённых на сегодня в промышленности электродвигателей серии АИР. Они отличаются между собой мощностью и частотой а также соответствующими габаритно-присоединительными размерами. Также каждая модель может быть как в базовом исполнении так и в модификации для использования в особых условиях окружающей среды с необходимым конструктивным исполнением (с повышенным скольжением со встроенной температурной защитой и т.д.). Для соответствия специфике использования электродвигатели данной серии разрабатываются и выпускаются с расчётом на эксплуатацию в том числе в режиме продолжительного безостановочного функционирования.
Технические характеристики данного двигателя представлены в таблице 2.3.
Таблица 2.3 – Технические характеристики электродвигателя АИР100L2
Номинальная частота вращения обмин
Номинальный ток при 380 В
Номинальный крутящий момент Н·м
Окончание таблицы 2.3
Буквы и числа обозначающие марку мотора расшифровываются последующим образом:
Основное исполнение: АИР100 А – асинхронный; И – «Интерэлектро»; Р – увязка мощности к габаритно-присоединительным размерам по РС 3031-71; повышенная защита от пыли и воды 100 – высота оси вращения мм; L – стандартный установочный размер по длине станины длинный; 2 – число полюсов.
3 Разработка кинематической схемы механизма главного движения
3.1 Построение структурной сетки
Структурную сетку строят для наглядного изображения варианта структурной формулы и определения: числа частот вращения на валах привода; числа групповых передач в приводе и порядка их конструктивного расположения; числа передач в каждой группе характеристик групп т.е. их место в порядке кинематического включения.
Знаменатель геометрической прогрессии φ рассчитывается по формуле [3.ст 64]
где z – число частот вращения на шпинделе nmax и nmin – максимальная и минимальная частоты вращения шпинделя.
Из проектного задания нам известно что z = 18 nmax = 1350 обмин
Знаменатель геометрической прогрессии сравниваем с табличным значением [3.ст 63 таб. 3.6]
Порядок построения структурных сеток:
a) на равных расстояниях проводят горизонтальные линии (или вертикальные) на одну больше чем число групповых передач; поле между двумя горизонтальными линиями отводится для одной групповой передачи;
б) на равных расстояниях проводят столько вертикальных линий (или горизонтальных) сколько скоростей имеет привод; расстояние между вертикальными линиями равно
в) рядом с полем в порядке конструктивного расположения групп в приводе указывают число передач в группе P
г) на середине верхней горизонтали (или левой вертикали) намечают точку О из которой симметрично проводят лучи в количестве равном Рi и расстоянием между концами соседних лучей на следующей горизонтали хi
Из этих условий структурная формула принимает следующий вид
где – число передач в каждой группе; – характеристики групп.
Структурная сетка показана на рисунке 2.4
Рисунок 2.4 – Структурная сетка
3.2 Построение графика частот вращения
Для построения графика частот вращения должны быть известны:
– знаменатель ряда частот вращения φ = 126;
– фактические частоты вращения от до ;
– частота вращения выбранного приводного двигателя = 3000 обмин.
Фактические частоты вращения определяют по формулам
и округляют до стандартных значений с учетом φ.
Округляем все значения до стандартного ряда:
n2 = 40 обмин; n3 = 50 обмин; n4 = 63 обмин; n5 = 80 обмин; n6 = 100 обмин; n7 = 125 обмин; n8 = 160 обмин; n9 = 200 обмин; n10 = 250 обмин; n11 = 315 обмин; n12 = 400 обмин; n13 = 500 обмин; n14 = 630 обмин; n15 = 800 обмин; n16 = 1000; n17 = 1265.
График частот вращения представлен на рисунке 2.5
Рисунок 2.5 – График частот вращения
3.3 Построение кинематической схемы
При построении кинематической схемы необходимо обратить внимание: какие блоки зубчатых колес (сдвоенные или строенные) расположены на валах; учитывать передачи в зацеплении на замедление (передача осуществляется с меньшего диаметра зубчатого колеса на больший) на повышение (с большего диаметра передается на меньший) или нейтральная (диаметры зубчатых колес равны); расположение колес (диаметров) на валах не должно препятствовать свободному перемещению блоков по валу и вхождению в зацепление зубчатых колес; расстояние между зубчатыми колесами должно быть не менее двух ширин колеса если расстояние увеличивать то увеличиваются габаритные размеры коробки скоростей.
Кинематическая схема представленная на рисунке 2.6 оформляется с изображенными на нем условными знаками всех кинематических элементов в том числе групповых передач шкивов муфт и т.д.
Рисунок 2.6 – Кинематическая схема привода
При выполнении технологической части были рассчитаны режимы резания для обрабатываемой детали выбран электродвигатель АИР100L2 построена структурная сетки. Построен график частот вращения и кинематическая схема привода.
Конструкторская часть
1 Расчет и выбор параметров шпинделя
Основной узел любого станка – это шпиндель. Работа шпинделя непосредственно влияет на эффективность точность и общую производительность станка.
Материал шпинделя выбирают исходя из требований обеспечить необходимую твердость и износостойкость его шеек и базирующих поверхностей а также предотвратить малые деформации шпинделя с течением времени (коробление).
Шпиндели станков нормальной точности изготовляют из сталей 40Х 45 с закалкой ответственных поверхностей до твердости 48 56 HRCэ с использованием индукционного нагрева. Если его применение вызывает затруднение шпиндели изготавливают из стали 40ХГР или 50Х и подвергают объёмной закалке до твердости 56 60 HRCэ.
При проектировании шпиндельных сборок необходимо определиться с линейными и диаметральными параметрами шпинделя подшипниками частотными характеристиками ротора и рабочей жидкостью.
где l – длина шпинделя определяемая исходя из прототипа станка.
Левая консоль шпинделя со стороны передачи крутящего момента определяется по методу «золотого сечения»
Расстояние между опорами рассчитывается по формуле
Диаметр цапф по условию прочности можно определить по функции:
где k =11 13 – константы конструкции и режимов работы шпинделя; N – мощность кВт; n – частота вращения шпинделя обмин.
Диаметр цапф по условию жесткости можно определить по функции:
Из получившихся значений выбирают большее.
2 Выбор подшипников формирование посадок и определение допусков
Работа шпинделя зависит от выбора его опор. Жесткость шпиндельного узла его виброустойчивость а так де точность вращения связаны с конструкцией опор. В качестве опор шпинделя применяют подшипники качения и подшипники скольжения с жидкостным трением.
Выбор опор осуществляется исходя из основных требований предъявляемый к опорам шпинделей:
Высокая точность вращения.
Опоры шпинделя должны быть долговечны. Нормальный срок службы подшипников качения принимается 5000 часов.
Виброустойчивость опор.
Одинаковая работа во всем диапазоне применяемых скоростей и нагрузок.
Эксплуатационные преимущества.
На точность вращения шпинделя так же влияет точность шейки шпинделя.
Исходя из заданной схемы установки подшипников на шпинделе: 2Т2Х. Для восприятия радиальных нагрузок выбираем шариковые радиально-упорные однорядные подшипники.
В качестве опоры (схема 2Т) со стороны режущего инструмента выбираем шариковый радиально-упорный подшипник легкой серии в количестве 2х штук С224-46217 ГОСТ832–78 Размеры указаны в таблице 3.1.
Таблица 3.1. Размеры
Обозначение подшипников:
Подшипник С224-46217 ГОСТ832–78
С – категория вибрации подшипника
– ряд момента трения;
– группа радиального зазора;
– класс точности подшипника;
– конструктивное исполнение;
– диаметр отверстия.
По ГОСТ 3325-85 для 4-го класса точности выберем посадки и отклонения для них.
Для второй опоры (схема 2Х) со стороны электродвигателя выбираем шариковый радиально-упорный подшипник легкой серии в количестве 2х штук С224-46217 ГОСТ832–78. Размеры указаны в таблице 3.2.
Таблица 3.2. Размеры
На рисунке 3.1 показана кинематическая схема установки подшипников.
Рисунок 3.1 – Кинематическая схема установки подшипников 2Т2Х
3 Расчет долговечности подшипников
Расчетная долговечность подшипника – это время выраженное в часах (расчетный срок службы) в течении которого не менее 90 % партии подшипников должны проработать при идентичных условиях без признаков усталости металла.
Для данного расчета используем ГОСТ 18855-94 «Подшипники качения. Динамическая грузоподъемность и расчетный ресурс (долговечность)».
Для подшипника выполняемого по схеме 2Х:
Условная нагрузка рассчитывается по формуле:
– коэффициент нагрузки
– динамическая грузоподъемность подшипника
Долговечность подшипника рассчитывается по формуле:
4 Расчет ресурса точности и времени безотказной работы станка
где – постоянная времени продолжительности ремонтного цикла согласно планово-предупредительному ремонту ; – коэффициент характеризующий обрабатываемый материал; – коэффициент характеризующий материал инструмента ; – коэффициент характеризующий точность станка (Н-1 П-15 В А С-2); – коэффициент учитывающий категорию массы ; – коэффициент учитывающий возраст до 10 лет ; – коэффициент учитывающий долговечность ; – число средних ремонтов в цикле .
определяем вероятность отказа по геометрической и технологической точности по формуле:
где – отработанные станко-часы
Для станка класса точности Н:
5 Определение эксцентриситета оси вращения шпинделя
Дисбаланс учитывается по эксцентриситету геометрической оси вращения шпинделя с осью проходящей через центры тяжести вращающихся масс элементов конструкции шпиндельно-сборочных единиц (ШСЕ).
Для станка нормального класса точности (Н) принимаем класс точности балансировки G04 [3].
Значение эксцентриситета определяется по зависимости:
где - скоростной параметр выбирается по ГОСТ 1940-1-2007; - собственная частота шпинделя рассчитывается по формуле:
6 Описание сборочного чертежа МГД операции его сборки
Шпиндельная сборка - КП.МРС.18.06.00.00.000. СБ.
К сборке узла шпинделя приступают после тщательной подготовки и проверки всех соединений и деталей шпинделя на соответствие чертежам и техническим условиям.
Внутренние кольца шариковых радиально-упорных подшипников посажены на шпиндель поз.11 между подшипниками поз. 36 со стороны МРИ установлены распорные втулки поз 17 18.
После того шпиндель устанавливается в гильзу поз. 24 и фиксируется крышками поз. 12 и 14 подшипники затягиваются гайкой поз. 29. В свою очередь в них предварительно установлена манжеты поз. 35
После установки внутреннего механизма устанавливается гидроцилиндр поз. 10 который посредством винтов поз. 28 прикручивается к корпусу шпиндельного узла поз. 25 гидроцилиндр закрывается крышкой поз. 12 которая прикручивается винтами поз. 27
После сборки отдельных узлов корпусу шпиндельного узла помещается в корпус и притягивается винтами поз. 27
Крутящий момент от электродвигателя шпинделю передается с помощью шпонки.
При выполнении конструкторской части был произведен расчет и выбор параметров шпинделя выбор подшипников расчет долговечности подшипников расчет ресурса точности и времени безотказной работы станка определен эксцентриситет оси вращения шпинделя и описание сборочного чертежа МГД операции его сборки.
Расчет и выбор параметров шпинделя позволил определить диметры цапф и длины консолей а также межопорное расстояние. Выбран материал шпинделя - Сталь 20Х ГОСТ 1050-88
Выбраны сдвоенные шариковые радиально – упорные подшипники ГОСТ 832-78 для схемы 2Т2Х.
Безопасность и экологичность проекта
1 Безопасность эксплуатации проектной разработки
Согласно ГОСТ ЕН 1005-2-2005 - Безопасность машин. Физические возможности человека. Часть 2. Составляющая ручного труда при работе с машинами и механизмами разработчик и изготовитель машины обязаны:
- Установить имеется ли опасность для операторов при ручном перемещении грузов во время работы на машине или механизме по прямому назначению если таковая опасность существует то должны быть применены методы оценки рисков.
- Устранить опасность путем исключения ручного труда (подъема опускания и переноски) на машине или механизмах; если это невозможно то предусмотреть применение тех или иных вспомогательных приспособлений иили переоснастить или заново оснастить машину и ее составные части согласно требованиям эргономики.
- Предоставить технические спецификации и руководство по эксплуатации с тем чтобы оценка рисков могла быть произведена на их основе.
В каждом случае разработчик должен предусмотреть инструкции по монтажу транспортировке и вводу в эксплуатацию работе и выводу из эксплуатации машины в которых должны содержаться сведения по технике безопасности и охране труда.
Разработчиком на стадии проектирования должна быть предусмотрена техническая оснастка для ручного манипулирования грузами.
Наилучшая возможность защиты здоровья безопасности труда и повышения производительности труда состоит в постоянном соблюдении эргономических требований к рабочей системе.
Согласно ГОСТ 12.2.009-99 - Станки металлообрабатывающие. Общие требования безопасности:
- Конструкция станков должна сводить к минимуму возникновение для работающих опасных ситуаций при его эксплуатации наладке техническом обслуживании и ремонте.
-Изготовитель должен информировать в эксплуатационных документах (далее - ЭД) об опасности неполной эффективности защитных мероприятий и необходимости специального обучения и применения средств индивидуальной защиты.
- Конструкцией станков должна быть устранена возможность возникновения опасных ситуаций для работающих при эксплуатации станка в условиях отличающихся от рекомендованных в ЭД которые можно предотвратить (например применение станка не по назначению).
- Станки должны отвечать требованиям безопасности в течение всего срока службы при выполнении работающими требований установленных в ЭД.
- Станки а также все узлы и элементы станков должны быть устойчивы. При работе станков преднамеренное опрокидывание падение или смещение станков и их узлов не допускаются.
- Конструкция станков (узлов и элементов) должна исключать ошибки соединения и подключения при монтаже узлов и элементов которые могут стать источником опасности.
- Конструкция станков должна обеспечивать безопасность работающего с инструментом а также с частями станков представляющими опасность даже при незначительном весе этих частей.
- В конструкции станков должны рационально использоваться принципы эргономики и средств личной защиты с тем чтобы утомляемость психологическая (стресс) и физическая нагрузки работающих были сокращены до минимума.
- Конструкция станков с числовым программным управлением должна обеспечивать сокращение до минимума влияний внешних факторов (электромагнитных электростатических радиопомех тепла света вибрации и т. д.) на безопасность работы станков.
Согласно ГОСТ 12.2.009-99 - Станки металлообрабатывающие. Общие требования безопасности защитные устройства должны быть:
- быть прочными. Крепление их должно быть надежным исключающим случаи самооткрывания;
- допускать проведение работ по смене заготовок и инструмента техническому обслуживанию и наладке станков (по возможности) без демонтажа защитных устройств. Доступ в рабочую зону должен быть ограничен необходимой операцией;
- находиться на достаточном расстоянии от опасной зоны чтобы обеспечить эффективную защиту работающего;
- обеспечивать безопасное наблюдение за циклом обработки;
- быть такими чтобы их нельзя было избежать или сделать неэффективными.
Защитные устройства не должны:
- становиться источником дополнительных опасностей ограничивать технические возможности станков и вызывать неудобства при их эксплуатации и наладке;
- затруднять удаление отходов там где это необходимо;
- снижать освещенность рабочей зоны;
- ограничивать наблюдение за рабочим процессом более чем это допустимо;
- повышать уровень шума создаваемого движущимися частями станков;
- увеличивать вибрацию станков.
Исследовательская часть
1 Построение станочного конфигуратора
Структурная схема технологического процесса показывает последовательность расположения оборудования в порядке прохождения технологического процесса с количественной характеристикой параметрической геометрической и технологической точности технической характеристикой станка а также других показателей отражающих формирование качества и точности изделия.
Точность техпроцесса характеризуется точностью и стабильностью во времени и пределах соответствием хода процесса и обеспечивается точность заготовки МРС оснастки режущего инструмента измерения наладки режимов обработки базирования а также состояния рабочего пространства.
Структурную схему технологического процесса формируем из одного модуля. Модуль состоит из трех блоков. В верхнем блоке в виде небольших таблиц формируем из стандартов показатели геометрической точности нормы точности и жесткости станка над верхней частью таблицы размещаем знак точности установленного по уровню.
С правой стороны в верхнем квадрате в отдельной таблице указываем элементы параметрической точности.
В нижних квадратах с левой и правой стороны указываем показатели технологической точности станка с учетом анализа показателей аналогов и прототипа а также требований действующих стандартов на нормы технологической точности. В нижних квадратах так же показываем сечение заготовки и детали обрабатываемых на станке.
В среднем блоке даются сведения о станке мощности подачи по бокам ромба указываем диапазон скоростей подач и диапазон частот вращения шпинделя.
Станочный конфигуратор показан на рисунке 5.1.
Рисунок 5.1 – Станочный конфигуратор
2 Расчет инструмента на прочность
Режущий инструмент: Фреза концевая 2223-0129 ГОСТ 17026-71.
Для инструмента нормального сечения определяют: главный центральный момент инерции максимальный и минимальный рассчитывается по формулам:
Площадь поперечного сечения инструмента для усиленного сечения и для нормального сечения рассчитывается по формуле:
Критическую силу определяют по формуле Эйлера
где Е – модуль Юнга; – коэффициент приложения нагрузки зависящий от поведения инструмента =1 2. При = 2 происходит врезание инструмента в металл; l – расчетная длина
где L – длина инструмента; – длина режущей части инструмента.
Расчет на прочность инструмента рассчитывается по формуле;
Данный инструмент подходит для выполнения операции.
При выполнении исследовательской части был разработан станочный конфигуратор и произведен расчет инструмента на прочность.
На основе утвержденного технического задания произведена разработка конструкции вертикально фрезерного станка на базе вертикального консольно-фрезерного станка Stalex X5032A. Был произведен патентно - лицензионный обзор системный анализ аналогов рассчитан класс точности станка.
Ресурс точности составляет 11200 ч. Безопасность эксплуатации обеспечена конструкцией механизмов сборкой по чертежу затяжкой всех крепежных и защитных элементов согласно государственным стандартам и техническим условиям. Выбран асинхронный двигатель АИР100L2 ГОСТ Р ГОСТ Р 51689-3000. с мощностью 55 кВт. Станок обеспечивает получение деталей и изделия по 9-му квалитету. Техническая оснастка отвечает российским и европейским требованиям. Конструкция проработана по ГОСТ ЕН1005-2:2005 «Безопасность машин» части физических возможностей человека и составляющих ручного труда.
В ходе выполнения проекта разработаны чертежи: общий вид станка деталь шпиндельная сборка стол с техническими требованиями; станочный конфигуратор спецификация.
Библиографический список
Гузеев В. И. Режимы резания для токарных и сверлильнофрезерно-расточных станков с числовым программным управлением[Текст]: справочник В. И. Гузеев В. А. Батуев И. В. Сурков; под ред. В. И. Гузеева. – М.: Машиностроение 2005. – 368 с.
Раменская Е.В. Металлорежущие станки. Курсовое проектирование: учеб.- метод.пособие к выполнению курсового проектасост.: Е.В.Раменская Ю.А. Филиппов; Сиб.гос.аэрокосмич.ун-т.- Красноярск 2013.-154с.
Шейнблит А.Е. Курсовое проектирование деталей машин: Учеб. Пособие. – М.: Высш.шк. 2002. - 217с.
Анурьев В.И. Справочник конструктора-машиностроителя. В 3. т. М.: Машиностроение. Т.3. 2004.- 575с.
Ларионов С.Г. Металлорежущие станки: учебное пособие: ЭБ С.Г. Ларионов.-М: Машиностроение2006.-136c.
Металлорежущие станки: учебник. В 2 т.Т.М. Авраамова В.В. Бушуев Л.Я. Гиловой и др.; под ред. В.В. Бушуева. Т. 1. - М.: Машиностроение 2012. - 608с.
Фрезерные станки [Электронный ресурс] - Электрон. дан. - Режим доступа: ru.dmgmori.com - Загл. с экрана.
ГОСТ 31606-2012 Машины электрические вращающиеся. Двигатели асинхронные мощностью от 012 до 400 кВт включительно. Общие технические требования.
ГОСТ 3325-85. Подшипники качения. Поля допусков и технические требования к посадочным поверхностям валов и корпусов. Посадки (с Изменением N 1).
ГОСТ 832-78 Подшипники шариковые радиально-упорные однорядные. Типы и основные размеры (с Изменением N 1).
ГОСТ 18855-94 «Подшипники качения. Динамическая грузоподъемность и расчетный ресурс (долговечность)».
Приложение A. Параметрическая матрица транзитивности для системного анализа технологического оборудования.
Оценочные показатели
Класс точности металлорежущих станков по ISO 230-2 по ГОСТ 7599 ГОСТ 8-82
Виброскорость Ve ммс
Установка по уровню:
Неравномерность вращения %
Перепад скорости при ступенчатом регулировании %
Эксцентриситет центра инерции фундамента с МРС и центра массы подошвы фундамента в сторону уклона %
Температура наружного кольца подшипника С не более
Вероятность безотказной работы
Радиальное биение мкм
Приложение Б. Допустимый остаточный удельный дисбаланс.
Рекомендуемые чертежи
- 24.01.2023
- 13.02.2022