Разработка конструкции крана подвесного настенного




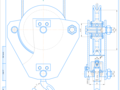
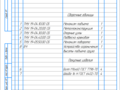
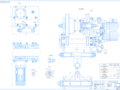
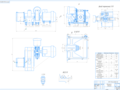
- Добавлен: 25.01.2023
- Размер: 2 MB
- Закачек: 0
Описание
Разработка конструкции крана подвесного настенного
Состав проекта
![]() |
![]() ![]() |
![]() ![]() |
![]() ![]() ![]() ![]() |
![]() ![]() ![]() ![]() |
![]() ![]() ![]() ![]() |
![]() |
![]() ![]() ![]() |
![]() ![]() ![]() ![]() |
![]() |
![]() ![]() ![]() ![]() |
![]() ![]() ![]() ![]() |
![]() ![]() ![]() ![]() |
![]() ![]() ![]() |
![]() |
![]() ![]() ![]() |
Дополнительная информация
Стрела.cdw

Сварные швы N1 выполнять по ГОСТ 8713-79.
Стрелу красить согласно заводским требованиям.
*Размеры для справок
Лист1.cdw

кафедра "Детали машин
Шкив тормозной (1:1)
Спецификация 19(4).spw

Кран подвесной поворотный
Расчетно-пояснительная
Устройство ограничения
высоты подъема груза
Болт М16х60 ГОСТ 7798-70
Шайба 16 Н ГОСТ 6402-70
Расчетное сечение.frw

ВО.cdw

Механизм поворота.cdw

Опорные узлы 19(4).cdw

Полости опор заполнить пластичной смазкой "Литол 24" по ГОСТ
Крюковая.cdw

РПЗ 19(4).doc
Московский ордена Ленина ордена Октябрьской Революции и ордена Трудового Красного Знамени
ГОСУДАРСТВЕННЫЙ ТЕХНИЧЕСКИЙ УНИВЕРСИТЕТ имени Н. Э. БАУМАНА
ФАКУЛЬТЕТ РК (Робототехника и комплексная автоматизация)
КАФЕДРА РК3(Детали машин)
РАСЧЕТНО-ПОЯСНИТЕЛЬНАЯ ЗАПИСКА
К КУРСОВОМУ ПРОЕКТУ НА ТЕМУ:
Разработка конструкции
крана подвесного настенного
Студент (Калугин ) Группа МТ8-71
(фамилия инициалы) (индекс)
В данном курсовом проекте предлагается разработать консольный неполноповоротный кран с постоянным вылетом который состоит из механизма подъема металлоконструкции. Кран крепится к стене.
Консольный неполноповоротный кран применяют для проведения подъемно-транспортных работ в производственных помещениях цехах и на открытом воздухе при обслуживании технологического оборудования и пр. Управление краном осуществляется с пульта управления на уровне 15 м до пола.
Расчет механизма подъема груза .4
1 Выбор электродвигателя
3 Определение основных размеров барабана
4 Передаточное отношение привода
8 Конструирование блоков
Металлоконструкция 10
1 Определение основных размеров
2 Проверка статического прогиба
3 Проверка прочности
4 Подбор подшипников опорного узла
5 Расчет соединения стрелы крана с опорным узлом.
6 Расчет болтового соединения крепления крана к стене.
Расчет соединений 14
1 Шпоночные соединения
2 Винты крепления каната на барабане.
Механизм поворота 15
3 Сопротивление передвижению
Расчет открытой передачи 24
Список литературы 20
Механизм подъема груза.
1 Выбор электродвигателя.
Рекомендации по выбору полиспаста: стреловые краны и электротали обычно выбирают двукратные (а = 2) одинарные (m = 1) полиспасты. Отклоняющих блоков (t = 3).
КПД полиспаста и отклоняющих блоков:
Мощность (кВт) при подъеме номинального груза весом FQ (Н) с установившейся скоростью V (ммин) – статическая мощность:
Где Gзахв – масса грузозахватного устройства:
Проверку времени пуска не проводим.
При управлении с пола применяют двигатели типа 4АС (трехфазные асинхронные с повышенным скольжением).
Из соображений экономической целесообразности выбираем двигатель с синхронной частотой вращения 1000 обмин (4АС80А6У3 Р=10 кВт при ПВ=15% n=860 обмин m=2.1 масса 20.4 кг).
Наибольшая сила натяжения в канате:
Коэффициент запаса К (табл.7 [1c.25]) принимаем равным 5.
Разрушающая нагрузка:
Канат ЛК-Р0 dкан=63 мм (маркировочная группа 1764-180).
Диаметр барабана по дну канавки (е=16 по табл. 8[1c.26]):
округляем до 05 мм: р=7 мм.
Толщина стенки барабана для чугуна (СЧ15) но не менее 8 мм:
Длина барабана на который наматывается одна ветвь каната:
Где zp – число рабочих витков:
Число рабочих витков округляют в большую сторону: zp=19.
Длина барабана получилась значительно больше диаметра. Это нежелательно так как ведет к увеличению консодьной силы на тихоходном валу редуктора. Из этих соображений увеличиваем диаметр барабана. Принимаем диаметр барабана по стандартному ряду чисел (табл.6 [1c.22])
Прочность барабана. Напряжение сжатия в стенке барабана должно быть меньше допускаемого (130 МПа для СЧ15):
Условие прочности выполнено.
Определяем коструктивные размеры барабана.Длина барабана если на него наматывают одну ветвь каната т.е. при одинарном полиспасте где:
- - расстояние до начала нарезки;
- - длина рабочей части барабана;
- - длина части барабана где размещаются разгружающие витки;
- - длина части барабана на которой размещается крепление каната.
Радиус канавок нарезки . Принимаем R=4 мм.
4 Передаточное отношение привода.
Частота вращения барабана
Необходимое передаточное отношение привода:
Для двигателя с 1000 обмин (под нагрузкой – 860 обмин):
При таком передаточном числе возможно применение зубчатого двухступенчатого редуктора.
Крутящий момент на барабане:
Наибольший крутящий момент на тихоходном валу редуктора:
Предварительно выбираем редуктор Ц2У-100
Номинальный вращающий момент на выходном валу выбранного редуктора должен удовлетворять условию где ТНЕ – эквивалентный момент.
Для зубчатых редукторов:
Т.к. коэффициент долговечности должен удовлетворять условию то принимаем
Номинальный вращающий момент на выходном валу выбранного редуктора удовлетворяет условию .
Фактическая скорость подъема:
Отличается от заданной (V=63 ммин) на 0411% в меньшую сторону что допустимо.
Проверка выбранного редуктора по консольной нагрузке. Нагрузка лимитируется подшипником тихоходного вала расположенным на стороне консольной силы.
При консольном расположении барабана
где Fном – номинальная консольная радиальная сила для выбранного редуктора (по каталогу);
Выбранный редуктор проходит по консольной нагрузке.
Если использовать двигатель со встроенным тормозом то установка дополнительного тормоза не требуется.
Момент от груза на валу тормозного шкива:
Требуемый тормозной момент тормоза:
Где Кторм=1.6 [1 c.33 табл.9]:
Тормозной момент встроенного тормоза электродвигателя:
Тормоз электродвигателя следует отрегулировать на меньший тормозной момент – 112 Н*м.
Тормоз установлен между двигателем и редуктором поэтому тормозной шкив выполняется на редукторной полумуфте.
Нормализованную муфту выбираем в соответствии с условиями
где d=22 мм - диаметр вала электродвигателя; - наибольший допустимый диаметр отверстия в полумуфте или втулке; - номинальный момент муфты (по каталогу); - наибольший момент передаваемый муфтой.
Из [2c.23] предварительно выбираем упругую втулочно-пальцевую муфту с тормозным шкивом DT=100 мм с пальцами d=8 мм выдерживающими нагрузку до 31.5 Н*м.
Упругие элементы проверяют на смятие в предположении равномерного распределения нагрузки между пальцами
где Тк – вращающий моментНм; dп-диаметр пальцамм; lвт-длина упругого элементамм
Пальцы муфты изготавливают из стали 45 и рассчитывают на изгиб:
Допускаемые напряжения изгиба где sт – предел текучести материала пальца МПа; зазор между полумуфтами С=4 мм.
Окончательно принимаем упругую втулочно-пальцевую муфту с тормозным шкивом DT=100 мм с пальцами d=8 мм выдерживающими нагрузку до 31.5 Н*м.
Диаметр блока по дну ручья
Принимаем диаметр блока 140 мм по табл.6 [1 с. 22] т.к. диаметр блока должен быть больше либо равен диаметру барабана.
Для одного крана желательно все блоки унифицировать.
Крюк выбираем по ГОСТ 6627-66 в соответствии с грузоподъемностью и группой режима работы. Дополнительных расчетов крюка не требуется.
Q=63 кН режим работы 2М: выбираем крюк №4 [2 с.14].
1 Определение основных размеров
Основные размеры металлоконструкции назначаем по эмпирическим формулам соответствующим опытным данным и обеспечивающие жесткость конструкции близкую к нормированной.
Исходными данными для расчета является вылет стрелы L=4000 мм грузоподъемность Q=6300 Н высота подъема груза Н=3000 мм скорость передвижения крановой тележки (тали) V=8 ммин.
Кран балочного типа с постоянным вылетом (с внешней опорой).
Высота балки по условиям жесткости:
Принимаем стандартный швеллер №22 ГОСТ 8240-89 (меньшие сечения не проходят проверку по изгибу в горизонтальной плоскости).
Масса 1мп швеллера - 21 кг.
Для определения веса стрелы необходимо подсчитать вес швеллеров и массу приваренных пластин.
Обьем приваренных пластин:
Вес металлоконструкции (значение увеличим на 10% учитывая таким образом массу сварных швов):
Определим координаты центра тяжести сечения стрелы: т.к. сечение имеет симметричную форму
y0 = h2+7 = 1602 +7= 87 мм
Момент инерции сечения
2. Проверка статического прогиба.
Фактический прогиб определяем по методу Верещагина перемножая площадь соответствующих эпюр на ординату единичной эпюры против ее центра тяжести.
Формулу применяем стандартную из [6] для показанной на рисунке расчетной схемы.
Как видно фактический прогиб не превышает допустимый.
3 Проверка прочности.
Допускаемое нормальное напряжение:
Допускаемое касательное напряжение в том числе и для сварных швов:
Для подвесного крана с опорой на круговой рельс моменты в вертикальной плоскости (при постоянном вылете):
Горизонтальный инерционный момент:
Напряжение изгиба в вертикальной плоскости
Условие выполняется.
Напряжение изгиба в горизонтальной плоскости:
Следовательно стрела с приведёнными выше геометрическими размерами обладает достаточной прочностью.
4 Подбор подшипников опорного узла.
Рассчитаем нагрузку действующую на подшипники (опора А –подшипник опора Б – крепление тележки).
Выбираем шариковые радиально-упорные однорядные подшипники с α=26°.
Подшипник 46210. d = 50 Сr =406H C0r =249 H.
Определяем эквивалентную статическую нагрузку. Подшипники рассчитываем по статической грузоподъёмности так как скорость вращения менее 10 обмин.
Для расчета принимаем [5 с.115].
Статическая прочность обеспечена т.к. .
Расчет оси на смятие [7]
sсм [s]см=04sт=140*04=56 МПа
Принимаем [tср] = 03sт = 0.3 * 140 = 42МПа
Ось отвечает необходимым требованиям по прочности.
Необходимая сила затяжки болта из условия несдвигаемости:
где Kcц – коэффициент запаса сцепления;
z – число болтов; f – коэффициент трения для стыка металл – бетон;
i – чило рабочих стыков.
Необходимая сила затяжки болта из условия нераскрытия стыка:
Внешние нагрузки (MF) распределяются между резьбовыми деталями и стыком. на резьбовые детали действует часть нагрузки обозначаемая и называемая коэффициентом основной нагрузки.
Условие нераскрытия стыка выраженное через напряжение на стыке принимает вид:
min ст = зат ± Fn - M > 0
Напряжение сжатия зат на стыке от затяжки болтов (винтов или шпилек):
где z - число болтов на стыке; Аст - номинальная площадь стыка (без учета наличия отверстий под болты).
Напряжение Fn на стыке от действия внешней нормальной к стыку силы: Fn = FN =0
Максимальное напряжение M на стыке от опрокидывающего момента:
где Wст - момент сопротивления стыка относительно нейтральной оси.
Если нейтральная ось обозначена х-х то
где J ymax - расстояние от нейтральной оси до наиболее удаленных точек стыка с разгружаемой стороны стыка.
После введения коэффициента запаса по нераскрытию k и преобразований условие нераскрытия стыка принимает вид:
Принимаем силу затяжки болта Fзат = 5625 Н большую из двух необходимых.
Условие прочности болта имеет вид:
где А1 – площадь болта по диаметру
Суммарная внешняя нагрузка приходящаяся на один болт:
Необходимый диаметр болта из засчёта необходимой площади:
где [s]p = sт Sт – допускаемое напряжение для расчёта на растяжение;
sт = 320 – предел текучести материала болта для болтов класса прочности 4.8
Sт = 4 – коэффициент запаса прочности для болтов с d 30мм.
Внутренний диаметр болта больше d1
По результатам расчета выбираем болт М16 т.к. у которого d1 = 14294.
Проверка на прочность бетонного основания.
smax ст = sзат + sм [s]см
где [s]см = 1.8 МПа – допустимое для бетона напряжение смятия.
Бетонное основание достаточно прочное.
1 Расчет шпоночных соединений.
1.1 Соединение вал электродвигателя - муфта.
Для диаметра вала d=22 принимаем призматическую шпонку по ГОСТ 23360-78 b=6 мм h=6 мм.
Определяем расчетную длину призматической шпонки:
Примем длину шпонки l=28 мм.
1.2 Соединение муфта – вал редуктора.
Для диаметра вала d=20 принимаем призматическую шпонку по ГОСТ 23360-78 b=6 мм h=6 мм. Определяем расчетную длину призматической шпонки:
2 Винты для крепления каната на барабане.
Определим силу затяжки винтов:
где z – кол – во винтов.
Принимаем класс прочности винтов 6.9 тогда предел текучести =540 МПа. Допустимое напряжение сжатия МПа
Расчётный диаметр винтов:
Болты М6 изображенные на чертеже недостаточны! Переделать.
Число оборотов мин-1
Машинное время работы ч
Ходовая балка – двутавр №20.
Привод механизма представляет из себя электродвигатель со встроенным тормозом закрытый одноступенчатый редуктор открытую зубчатую пару колесо которой является ребордой колеса тележки. Будем использовать механизм передвижения с тремя колесами при этом одно сделаем приводным.
Применим одноребордные колеса с бочкообразным ободом. При точечном начальным контакте для стальных колес предварительный диаметр:
где — наибольшая нагрузка на колесо.
Gстр = 2447 Н (см. выше)
Предварительный диаметр колес
Для определения скорости механизма передвижения по рельсу воспользуемся формулой:
Контактное напряжение при точечном контакте
– эквивалентная нагрузка
m =0113 – коэффициент зависящий от отношения .
Допускаемое напряжение определяем по формуле
- допускаемое напряжение при наработке N=104 циклов для поковки из стали 50 [1 с. 39]
tS - машинное время работы ч;
b = 0.85 – коэффициент учитывающий уменьшение средней частоты вращения в периоды неустановившихся движений.
3 Сопротивление передвижению.
Сопротивление передвижению при установившейся скорости и ходовых колесах с ребордами без направляющих роликов Н
m=015 – (при материале колес – сталь ) коэффициент трения качения.
Приведенный коэффициент трения f в подшипниках качения принимаем f=001 – шариковый подшипник.
Диаметр подшипников колес d=02D=20 мм.
Коэффициент kр учитывает трение реборд о рельс.
kр=25 – механизм с тележкой.
Мощность при установившемся движении кВт:
где h= 093 – КПД при зубчатом редукторе.
Предварительный выбор мощности двигателя:
Выбираем двигатель со встроенным электромагнитным тормозом 4А63B24E2У12 с мощностью: РН=012 кВт nдв=1360 мин-1Tma Тma исполнение IM 3001
Требуемое передаточное отношение привода:
Наибольший момент на тихоходном валу редуктора:
где = 3 - передаточное отношение открытой зубчатой передачи.
- передаточное отношение закрытой зубчатой передачи.
Номинальный момент двигателя:
m – кратность максимального момента двигателя
Максимальный момент на тихоходном валу закрытой ступени:
Максимальный момент на приводном колесе:
Частота вращения тихоходного вала закрытой ступени:
Расчет закрытой передачи был произведен с помощью ЭВМ. Рассчитан зубчатый цилиндрический одноступенчатый редуктор внешнего зацепления с прямым зубом.
Вращающий момент на тихоходном валу6Нм
Частота вращения тихоходного вала288обмин
Передаточное отношение механизма4.72
Данные полученные в результате проектного расчёта редуктора представлены в распечатке:
Выбираем вариает №2 (по небольшой массе межосевому расстоянию и окружной силе).
Расчет открытой зубчатой передачи.
Открытая зубчатая передача представляет собой зубчатое колесо нарезанное на реборде катка тележки и шестерню нарезанную на валу тихоходного вала закрытого редуктора.
1. Геометрические параметры зацепления:
Делительный диаметр:
Диаметр вершин зубьев:
Диаметр впадин зубьев:
х — коэффициент смещения (.
Межосевое расстояние:
Ширина зубчатого венца:
Примем bw = 25 мм по стандартному ряду чисел.
где — коэффициент ширины зубчатого венца.
По настойчивому требованию руководителя проекта диаметр шестерни уменьшен до 10 мм как в редукторе.
2. Проверочный расчет на контурную выносливость.
Выбор материала шестерни и колеса:
sb=900 МПа sт=900 МПа
для прямозубых передач
— коэффициент нагрузки
— коэффициент динамической нагрузки.
— коэффициент учитывающий неравномерность распределения нагрузки по линии контакта.
Удовлетворяет условию.
3. Проверочный расчет на выносливость при изгибе.
— коэффициент формы.
Список использованной литературы.
Снесарев Г.А. Тибанов В.П. Зябликов В.М. Расчет механизмов кранов Под ред. Д.Н. Решетова: Учебное пособие. – М.: Изд-во МГТУ 1994.
Подъемно-транспортные машины: Атлас конструкций: Учеб. пособие для студентов втузов М.П. Александров Д.Н. Решетов Б.А. Байков и др.; Под ред. М.П. Александрова Д.Н. Решетова. – М.: Машиностроение 1987.
Атлас конструкций узлов и деталей машин: Учеб. пособие Б.А. Байков А.В. Клыпин И.К. Ганулич и др.; Под ред. О.А. Ряховского. – М.: Изд-во МГТУ им. Н.Э. Баумана 2005.
Снесарев Г.А. Тибанов В.П. Учебное пособие по проетированию и расчету металлоконструкций подъемно-транспортных устройств. – М: Изд-во МГТУ им. Н.Э. Баумана 1985.
Конструирование узлов и деталей машин: Учеб. пособие для студ. техн. спец. вузов П.Ф. Дунаев О.П. Леликов. – М.: Издательский центр «Академия» 2004.
Расчет на прочность деталей машин. Справочник. Биргер И.А. Иосилевич Г.Б. - М.: Машиностроение 1993г 639с
Эпюры изгибающих моментов.frw

Рекомендуемые чертежи
- 29.03.2024