Разработка элементов качественных показателей редуктора цилиндрического одноступенчатого



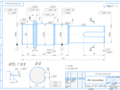
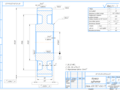
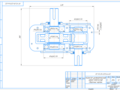
- Добавлен: 24.01.2023
- Размер: 995 KB
- Закачек: 0
Описание
Состав проекта
![]() |
![]() ![]() ![]() ![]() |
![]() ![]() ![]() ![]() |
![]() ![]() |
![]() ![]() ![]() ![]() |
![]() ![]() |
![]() ![]() ![]() |
![]() ![]() ![]() |
![]() ![]() |
Дополнительная информация
Редуктор444вариант.cdw

инженерный факультет
КР НТиТИ-2011.444.02
Колесо444вариант.cdw

Коэффициент смещения
Степень точности по ГОСТ 1643-81
Межосевое расстояние
Сталь 45Х ГОСТ 4543-71
инженерный факультет
КР НТиТИ-2011.444.01
Вал444вариант.cdw

Содержание .doc
УО «Барановичский государственный университет»
Кафедра «Технологии машиностроения»
РАСЧЕТНО-КОНСТРУКТОРСКАЯ РАЗРАБОТКА
ЭЛЕМЕНТОВ КАЧЕСТВЕННЫХ ПОКАЗАТЕЛЕЙ
РЕДУКТОРА ЦИЛИНДРИЧЕСКОГО
Расчетно-пояснительная записка КР НТиТИ-2011
старший преподаватель студент 3 курса
Сергей К.К. группы ТО(з) - 37
Данные для расчета по варианту 101 .3
Функциональное назначение и применение узла 4
Расчёт и выбор посадок для сопрягаемых элементов узла . 5
1. Расчёт посадки с натягом . .. 5
2. Расчёт переходной посадки . . 8
3. Расчет предельных размеров для деталей цилиндрических сопрягаемых
4. Расчёт посадки подшипников качения .. .. 13
5. Выбор посадок для гладких цилиндрических сопряжений .. . .15
Расчёт калибров . .. . 17
1. Расчёт калибров для отверстия .. ..17
2. Расчёт калибров для вала и контркалибров для них 18
Расчёт предельных отклонений призматического шпоночного соединения ..21
Расчёт предельных отклонений резьбового соединения .. . .. 22
Расчет элементов зубчатой передачи . . 23
1. Расчет зазоров сопряжения.. . .23
2. Расчёт некоторых размеров разноименных профилей зубьев . . 25
Расчет конструкторской размерной цепи вала тихоходного . . ..27
Назначение средств измерений для вала тихоходного .. ..29
Нормативные ссылки . .. .. ..31
Список используемой литературы .. . .. . 31
Сидорова_записка_2011.doc
Число зубьев шестерни z1
Число зубьев колеса z2
Материал колеса сталь
Материал вала тихоходного сталь
Модуль передачи m мм
Диаметр шейки вала тихоходного под колесом D мм
Длина сопряженной поверхности колеса вала l мм
Ширина венца колеса B мм
Передаваемый вращающий момент T Нм
Диаметр выходного конца вала тихоходного dвт мм
Тип шпоночного соединения на выходном конце вала тихоходного
Резьба на выходном конце вала быстроходногогайка
Скорость окружная колеса V мс не более
Температура подшипников °C
Температура корпуса °С
Температура колеса °С
Степень точности зубчатой передачи по ГОСТ 1643-81
Номер подшипников на валу тихоходном
Радиальная нагрузка на подшипники вала тихоходного F Н
Переходная посадка (диаметр) мм
Посадка с зазором (диаметр) мм
Посадка с натягом (диаметр) мм
Калибры для отверстия диаметром мм
Калибры для вала диаметром мм
Функциональное назначение и применение узла
Редуктор – это механизм состоящий из зубчатых или червячных передач заключённые в отдельный закрытый корпус и работающий в масляной ванне.
Редуктор предназначен для понижения частоты вращения и соответственно повышения вращающего момента. Механизмы для повышения частоты вращения выполненные в виде отдельного агрегата называются ускорителями или мультипликаторами.
Основными параметрами всех редукторов являются: передаточное число коэффициенты ширины колес модули зацепления углы наклона зубьев коэффициенты диаметров червяков (для червячных).
Тип редуктора параметры и конструкцию определяют в зависимости от его места в силовой цепи привода машины передаваемой мощности и угловой скорости назначение машины и условия эксплуатации. Необходимо стремиться использовать стандартные редукторы которые изготавливаются на специализированных заводах и поэтому дешевле.
Цилиндрические редукторы нужно предпочитать другим ввиду более высоких значений к. п. д. При больших передаточных числах используют червячные или глобоидные редукторы.
Корпуса (картеры) редукторов должны быть прочными и жесткими их отливают из серого чугуна. Для удобства сборки корпуса редукторов выполняют разъемными.
Опорами валов редукторов как правило являются подшипники качения.
Обычно передаточные числа в редукторах находятся в следующих пределах: для одноступенчатых цилиндрических – 2 для двухступенчатых цилиндрических – 63 для червячных – 8u80.
Редуктор широко применяется в различных отраслях машиностроения. Например в грузоподъёмных кранах – редукторы механизмов подъёма грузов и стрелы и т.д.
Редуктор состоит из зубчатой передачи смонтированной на валах с подшипниками в литом чугунном корпусе. Корпус состоит из двух частей: нижней части – картера и верхней – крышки. Разъём горизонтальный в месте соединения пришабрены при окончательной сборке покрыты герметиком; собирают корпус без прокладок. Крышка с картером скрепляется болтами. Положение крышки относительно корпуса фиксируется двумя коническими штифтами расположенными по диагонали.
Редуктор является широко распространённым механизмом используемым в приводах современных машин. Будучи сравнительно простым по конструкции редуктор тем не менее требует при проектировании определённых навыков является базовой моделью для развития первоначального конструкторского мышления в процессе обучения конструированию.
Расчёт и выбор посадок для сопрягаемых элементов узла
1 Расчёт посадки с натягом
Произвести расчёт посадки с натягом для неподвижного неразъёмного соединения зубчатого колеса и тихоходного вала для передачи вращающего момента Т=2000 Нм.
Материалы сопрягаемых деталей: колеса – Сталь 45X вала – Сталь 20. При этом модуль упругости для стали: Е1=Е2=2105 МНм2.[16]
Коэффициенты Пуассона соответственно принимаем: 1=2=03. [16]
Пределы текучести материалов: т1=320 МНм2 (Сталь 15 – вал) т2=315 МНм2 (Сталь 20Х – колесо). [16]
Коэффициент трения сопрягаемых деталей =014. [16]
Номинальные размеры сопрягаемых деталей принимаем по заданию:
D=70 мм – номинальный диаметр соединения
d2=mz2-25m= 455 – 254 = 210 мм – диаметр впадин зубьев колеса
d1=0 – внутренний диаметр охватываемой детали
L=60 мм – длина сопряжённой поверхности вала и колеса.
Решение. Исходя из условия что T≤Мтр величина расчётного наименьшего натяга Nmin расч обеспечивающего прочность соединения определяется по формуле:
Nmin расч=РD (С1E1+ С2E2) мкм (2.1)
где Р – давление на поверхности контакта колеса и вала возникающее под влиянием натяга;
Е1 Е2 – модули упругости материала МНм2;
C1 C2 – коэффициенты определяемые по формулам:
С2 = (D2+d22)( D2-d22)+1 (2.3)
где 1 = 2 = 03 коэффициенты Пуассона.
С2 = (702+2102)( 2102-702)+03 = 143
Давление P на поверхности контакта колеса и вала определяется из неравенства:
где T – максимальный передаваемый вращающийся момент;
L' = 0.94L - длина поверхности контакта зубчатого колеса и вала за вычетом фасок;
f – коэффициент трения =014;
D –диаметр шейки вала;
C учетом подстановки полученных значений получаем:
р = 22000314007²094006014 = 3293 МНм2.
Далее путём подстановки полученных данных в формулу (2.1) находим наименьший расчётный натяг Nmin расч:
Nmin расч=3293106007( 072105+1432105) = 2455 мкм
С учётом неровностей контактирующих поверхностей расчётный минимальный натяг должен приниматься большим на величину поправки иш которая для материалов с разными механическими свойствами определяется из выражения:
иш =55 (Ra1+Ra2) мкм (2.5)
где Ra1=08; Ra2=08 – величины шероховатости сопрягаемых поверхностей вала и ступицы колеса. Где иш – поправка на обмятие микронеровностей деталей
иш =55 (08+08)=88 мкм
Т.о. наименьший функциональный натяг Nmin ф при котором обеспечивается прочность соединения:
Nmin ф=2455+88=3335 мкм
Для учёта случайных нагрузок наименьший функциональный натяг увеличиваем на величину коэффициента запаса прочности k=15. Тогда:
Nmin ф=k Nmin ф(2.6)
Nmin ф=153335=50025 мкм
Выбор посадки с натягом осуществляем в системе отверстия по седьмому квалитету ввиду отсутствия особых требований (по ГОСТ 25346-82) – 70 H7r6.
иt – поправка учитывающая различие температурных деформаций деталей соединения
иt = dн·[αD·(tpD – tсб) – αd·(tpd – tсб)]
где: αD и αd – коэффициенты линейного расширения
tpD и tpd – рабочие температуры деталей
tсб – температура сборки деталей =20ºС
dн – номинальный диаметр соединения
иt = 0070·[115·10-6·(70-20) - 11·10-6·(70-20)] = 175
иуд – поправка учитывающая увеличение контактного давления у торцев охватывающей детали определяется из графика [2 рис 1.68] иуд = 095
Наименьший функциональный натяг (Nmin ф) при котором обеспечивается передача вращающего момента за счёт сил трения :
Nmin ф = Nmin расч + иш + иt + иуд
Nmin ф = 2455+88+175+095 = 3605мкм
Для учёта случайных нагрузок наименьший функциональный натяг увеличиваем на величину коэффициента запаса прочности k = 15. Тогда:
Nmin ф = k Nmin ф (2.6)
Nmin ф = 153605=54075 мкм
Для данной посадки: диаметр отверстия 70+0030 диаметр вала 70+0043+0062(выбор осуществляется по ГОСТ25346-82)
Наименьший натяг Nmin: Nmin=dmin-Dmax (2.7)
Nmin=70043-70030=13 мкм
Наибольший натяг Nmax: Nmax=dmax-Dmin (2.8)
Nmax=70062-70000=62 мкм
Рисунок 1 – Схема расположения полей допусков посадки с натягом 70 H7r6
Произведём проверку прочности соединённых деталей при наибольшем полученном натяге. Условие прочности деталей заключается в отсутствии пластической деформации на контактной поверхности колеса и вала. Удельное давление Pmax возникшее в нашем сопряжении с посадкой 70 H7r6 определим по формуле:
Pmax = Nmax D( c1E1+ c2E2)
Pmax= 006270( 072105+1432105)=832 МНм2(2.9)
Допускаемые наибольшие давления Pдоп 1 и Pдоп 2 на контактирующих поверхностях вала и ступицы колеса которые без возникновения пластических деформаций выдерживают детали определим по формулам
Pдоп 1≤058 т1[1-(d1D)2](2.10)
Pдоп 1=058250 [1- (070)2]=145 МНм2
Pдоп 2≤058 т2[1-(Dd2)2](2.11)
Pдоп 2=058350[1-(70210)2]=1804 МНм2
где т1 = 250 МНм2 т2 = 350 МНм2 - пределы текучести материалов соответственно (для стали 20– вал и стали 45Х колесо).
Сравнение допускаемого давления Pдоп 1 и Pдоп 2 с давлением возникающим при наибольшем натяге Pmax и наименьшем натяге Pmin показывает что запас прочности для вала:
Таким образом посадка 70 H7r6 не вызовет повреждения деталей.
2 Расчёт переходной посадки
Рассчитать ожидаемую при сборке долю соединений с натягом (вероятность натяга) и долю соединений с зазором (вероятность зазора) для посадки 27 H8m7.
При расчёте вероятностей натягов и зазоров переходной посадки исходят обычно из нормального закона распределения.
Рассмотрим отверстие: номинальный диаметр 27 мм по ГОСТ 25346-82 EI=0 IТ8=33 мкм.
Dmax =27000+0033=27033 мм
Dmin =27000+0000=27000 мм
Для вала: dном=27 мм e
dmax= dном+ es (2.16)
dmax =27000+0029=27029мм
dmin= dном+ei (2.17)
dmin =27000+0008=27008 мм
Nmax= dmax- Dmin(2.18)
Nmax=27029-27000=0029 мм
Smax= Dmax- dmin(2.19)
Smax =27033-27008=0025мм
Средний натяг в соединении:
Nc=( Nmax- Smax)2(2.20)
Nc =(0029-0025)2=0002 мм=2 мкм
Среднее квадратичное отклонение натяга:
Рисунок 2 – Схема расположения полей допусков сопряжения 27H8m7
Предел интегрирования:
По значению Z находим значение Ф(Z): [3]
Вероятность натягов рассчитываем из условия что Z>0:
РS =05+01217=06217 6217 %
РN =05-01217=03783 3783 %
Следовательно при сборке примерно 6217 % всех соединений (6217 из 10000) будут с натягом и 3783 %соединений (3783 из 10000) – с зазором.
Предельные значения натягов и зазоров:
Наибольший зазор переходной посадки часто представляют в виде отрицательного наименьшего натяга:
Sвmax = - Nвmin = 1756 мкм.
Рисунок 3 - Вероятность получения зазоров и натягов в посадке 27H8m7
3 Расчёт предельных значений для деталей цилиндрических соединений узла.
Определить предельные размеры допуски зазоры и натяги в соединениях при посадках с зазором и натягом.
Посадка с зазором 45 Н9d9
Dном= 45 мм; EI=0; ТD=62 мкм; ES=62;
Dmax=45000+0062=45062 мм
Dmin =45000+0000=45000 мм
dном=45 мм es=-80мкм e td=62 мкм
ei= -80-(-142)= 62 мкм
dmax=45000-0080=4492 мм
dmin=45000-0142=44858 мм
Smax= Dmax- dmin(2.31)
Smax=45062-44858=0204 мм
Smin= Dmin- dmax(2.32)
Smin=45000-4492=008 мм
TS= Smax- Smin(2.33)
Рисунок 4 – Схема расположения полей допусков сопряжения 45H9d9
Посадка с натягом 450H8v7
Dном=450мм; EI=0 TD=97 мкм ES=97 мкм.
Dmin=450000+0000=450000 мм
Dmax=450000+0097=450097 мм
dном=450мм ei=595 мкм Td=63 мкм es=658 мкм
dmin=450000+0595=450595 мм
dmax=450000+0658=450658 мм
Nmax=450658-450000=0658 мм
Nmin=450595-450097= 0498 мм
Рисунок 5 – Схема расположения полей допусков сопряжения 450H8v7
4 Расчёт посадки подшипника качения
Произвести расчёт посадки шарикоподшипника радиального 6-313 при радиальной нагрузке F = 2200 Н..
По таблице ГОСТ 8338-75 находим значения параметров подшипника:
d=65 мм; D=140 мм; B=33 мм; С=913 кН; r=35 мм.
Разность температур вала и подшипника для определения величины натяга в посадке подшипника на вал находим из условия t=15С.
Температура подшипников°C---------65
Температура корпуса °C ---------------50
Nmin=[(d+3)d] (008+d00015t)(2.35)
где F – радиальная нагрузка на подшипники вала тихоходного H;
B -- рабочая ширина посадочного места за вычетом фaсок;
d – минимальный диаметр отверстия подшипника (или вала);
B = B - 2r = 33 - 235 = 26 мм (2.36)
Nmin=[6865] (008+650001515)=774мкм
Вводим поправочный коэффициент 11
Nmin расч=77411=8514 мкм
По ГОСТ 520-02 выбираем предельное отклонение диаметров в мкм.
Внутреннее кольцо подшипника 65 по табл. 32
Верхнее отклонение : 0 мкм. Нижнее отклонение : -12 мкм
Наружное кольцо подшипника 140 по табл. 33
Верхнее отклонение : 0 мкм. Нижнее отклонение : -15 мкм
Вал: EI =20 мкм; ES = 39 мкм ; Корпус; EI=0; ES= 40 мкм
Для 6-го класса точности по ГОСТ 3325-85 выбираем посадку L6n6.
Рисунок 6–– Схема расположения полей допусков для посадки внутреннего кольца шарикоподшипника радиального 313 на вал.
По ГОСТ 3325-85 находим основное отклонение и квалитет отверстия в корпусе для наружного кольца: 140 H7.
Рисунок 7 – Схема расположения полей допусков для соединения наружного кольца подшипника с корпусом редуктора.
Во избежание разрыва кольца выбранную посадку следует проверить чтобы максимальный натяг (мм) посадки не превышал значения допускаемого прочностью кольца
где: k – коэффициент принимаемый приближенно для подшипников легкой серии – 28; средней – 23; тяжелой – 2;
d – диаметр внутреннего кольца подшипника;
[p] – допускаемое напряжение на растяжения = 400 Мпа;
Определим отклонения формы и шероховатость посадочных поверхностей под подшипники качения.
Шероховатость посадочных поверхностей валов и отверстий корпусов принимаем по таблице 4.95 [3] – для вала 65 класса точности подшипника 6 в интервале «до 80» равен Ra 063 для отверстия корпуса 140 класса точности подшипника 6 в интервале «св. 80 до 500» равен Ra 125 для опорных торцов заплечиков валов и корпусов - для вала 65 класса точности подшипника 6 в интервале «до 80» равен Ra 125 для отверстия корпуса 140 класса точности подшипника 6 в интервале «св. 80 до 500» равен Ra 25.
Отклонения формы и расположения поверхностей валов и корпусов приводят при установке подшипников качения к деформации колец и дорожек качения нарушению нормальной работы узла. Допуски формы посадочных мест валов и отверстий корпусов в радиусном измерении:
допуск круглости не должен превышать значения в таблице 4 по ГОСТ 3325-85 для вала 65 класса точности подшипника 6 в интервале «от 50 до 80» равен 5 мкм для отверстия корпуса 140 класса точности подшипника 6 в интервале «св. 120 до 180» равен 10 мкм.
допуск профиля продольного сечения не должен превышать значения в таблице 4 по ГОСТ 3325-85 для вала 65 класса точности подшипника 6 в интервале «от 50 до 80» равен 5 мкм для отверстия корпуса 140 класса точности подшипника 6 в интервале «св. 120 до 180» равен 10 мкм.
Допуски формы посадочных мест валов и отверстий корпусов в диаметральном измерении:
допуск непостоянства диаметра не должен превышать значения в таблице 4 по ГОСТ 3325-85 для вала 65 класса точности подшипника 6 в интервале «от 50 до 80» в поперечном сечении равен 10 мкм в продольном сечении равен 10 мкм для отверстия корпуса 140 класса точности подшипника 6 в интервале «св. 120 до 180» в поперечном сечении равен 20 мкм в продольном сечении равен 20 мкм.
Допуск торцового биения опорных торцовых поверхностей заплечиков валов и отверстий корпусов должны соответствовать указанным в таблице 5 и 6 по ГОСТ 3325-85 для вала 65 класса точности подшипника 6 в интервале «от 50 до 80» равен 19 мкм для отверстия корпуса 140 класса точности подшипника 6 в интервале «св. 120 до 180» равен 40 мкм.
Значения допустимых углов взаимного перекоса колец для нашего подшипника (радиальный однорядный шариковый с нормальным радиальным зазором) max= 8.
5 Выбор посадок для гладких цилиндрических сопряжений
Исходя из функционального назначения соединений методом аналогов выбираем посадки для гладких цилиндрических соединений.
а) для соединения крышек и корпуса принимаем посадку с зазором Н7f9 ;
б) для соединения внутренних колец шариковых подшипников с валом принимаем переходную посадку
в) для соединения наружных колец подшипников с корпусом назначаем посадку с зазором Н7
г) для соединения штифтов и крышки H7m6.
1 Расчёт калибров для отверстия
Калибрами называют бесшкальные измерительные инструменты предназначенные для контроля размеров формы и расположения поверхностей деталей. Калибры бывают предельные и нормальные.
Определить размеры рабочих калибров-пробок для отверстия 45 Н8.
По ГОСТ 25346-89 находим допуск и основное отклонение для детали: IТ8 = 39 мкм EI = 0 .
Следовательно наибольший и наименьший предельные размеры отверстия:
Dmax=45+0039=45039 мм
Формулы для определения исполнительных размеров калибров возьмем из таблицы 1 ГОСТ 24853-81: Z=6 мкм Y=5 мкм H=4 мкм.
Z – отклонение середины поля допуска на изготовление проходного калибра для отверстия относительно наименьшего предельного размера изделия;
Y – допустимый выход размера изношенного проходного калибра для отверстия за границу поля допуска изделия;
H – допуск для изготовления калибров для отверстий.
Исполнительные размеры калибров-пробок определяют по соответствующим формулам таблицы 1 ГОСТ 24853-81.
В нашем случае наибольший предельный размер пробки:
ПРmax=Dmin+Z+Н2(3.4)
ПРmax =45+0006+00042=45008 мм
Исполнительный размер калибра ПР 45008-0004
Наименьший размер изношенной пробки:
ПРизн =45-0005=44995 мм
Когда калибр будет иметь диаметр равный ПРизн его нужно изъять из эксплуатации.
Наибольший размер непроходного калибра-пробки:
НЕmax =45039+00042=45041 мм
Исполнительный размер калибра НЕ 45041-0004
Рисунок 8 – Схема расположения полей допусков калибров-пробок для
2 Расчёт калибров для вала и контркалибров для них
Определить размеры рабочих калибров-скоб для вала 40 d8.
По ГОСТ 25346-89 находим предельные отклонение ei = 80 мкм IN8 = 39 мкм значит es = 119 мкм.
Предельные размеры вала:
dmax =40+0119=40119 мм
dmin =40+0080=40080 мм
По таблице 2 (ГОСТ 24853-81) для Td8 и 40 мм находим данные для расчёта размеров калибров-скоб: Z1=6 мкм Y1=5 мкм Н1=7 мкм.
Z1 – отклонение середины поля допуска на изготовление проходного калибра для вала относительно наименьшего предельного размера изделия;
Y1 – допустимый выход размера изношенного проходного калибра для вала за границу поля допуска изделия;
H1 – допуск для изготовления калибров для валов.
Предельные размеры калибров-скоб определяем по соответствующим формулам таблицы 1 ГОСТ 24853-81.
Наименьший размер проходного калибра-скобы:
ПРmin=dmax-Z1-H12(3.10)
ПРmin =40119-0006-00072=401095 мм
Исполнительный размер калибра-скобы ПР 401095+0007
Наибольший размер изношенного проходного калибра-скобы:
ПРизн =40119+0005=40124 мм
Когда калибр будет иметь размер рабочей части равный ПРизн его нужно изъять из эксплуатации.
Наименьший размер непроходного калибра-скобы:
НЕmin=dmin-H12(3.12)
НЕmin =40080-00035=400765мм
Исполнительный размер калибра-скобы НЕ 400765+0007
Определить размеры контрольных калибров для рабочих калибров-скоб для вала 40 d8 .
По таблице 2 (ГОСТ 24853-81) находим данные для расчёта размеров контрольных калибров :
Z1=6 мкм;Y1=5мкм; Нр=25 мкм.
Нр – допуск для изготовления контр-калибров для вала.
Предельные размеры контр-калибров определяются по формулам:
К-ПРmax=dmax-Z1+Hp2(3.13)
К-ПРmax =40119-0006+000125=4011425 мм
Исполнительный размер контр-калибра К-ПР 4011425 -00025
Определим размер калибра для контроля износа гладкого проходного калибра-скобы:
К-И=dmax+Y1+Hp2(3.14)
К-И =40119+0005+000252=4012525 мм
Исполнительный размер К-И 4012525 -00025
Предельные размеры контр-калибров:
К-НЕmax=dmin+Hp2(3.15)
К-НЕmax =40080+000252=4008125 мм
Исполнительный размер К-НЕ 4008125 -00025
Рисунок 9 – Схема расположения полей допусков калибров-скоб для вала 40d8 и контрольных калибров для этих скоб
Расчёт предельных отклонений призматического шпоночного соединения
Шпоночные соединения втулок шкивов муфт и других деталей машин с валами должны передавать заданный крутящий момент. Их применяют когда к точности центрирования соединяемых деталей не предъявляют особых требований.
Установлены следующие три типа шпоночных соединений: свободное нормальное и плотное. Шпоночное соединение собирается в системе вала. В нашем случае тип шпоночного соединения на тихоходном валу нормальный. Шпонки делаются из специального проката имеющего точность изготовления по ширине по h9. Поля допусков для паза на валу N9 и для паза во втулке js 9. Для диаметра выходного конца вала d = 55 мм по ГОСТ 23360-78 выбираем шпонку сечением b × h = 16 × 10 мм. Глубина паза во втулке 43 мм а на валу – 6. Размеры соединения и поля допусков представлены на рисунке 10.
Таблица 4– предельные размеры шпоночного соединения
Наименование элемента соединения
Рисунок 10 – Поля допусков шпоночного соединения
Расчёт предельных отклонений резьбового соединения
Определить предельные размеры и построить поля допусков для резьбового соединения М24×25. Ввиду того что по ГОСТ 8724-81 не существует метрической резьбы М24 с шагом 25; принимаем близкую к ней : М24×2
Номинальные значения диаметров резьбы М24×2 с мелким шагом равным Р = 2 по ГОСТ 9150-59 [21]: наружный диаметр резьбы соответственно болта и гайки d = D = 24 мм внутренний диаметр резьбы соответственно болта и гайки d1 = D1 = 21835 мм средний диаметр резьбы d2 = D2 = 22701 мм.
Ввиду отсутствия указания о степени точности резьбы принимаем сопряжение с зазором и грубый класс точности как более экономичный: 7H8g.
Таблица 5.1 – Предельные отклонения размеров болта и гайки:
Таблица 5.2 – Предельные размеры болта и гайки:
Рисунок 11 – Схема расположения полей допусков резьбового соединения М24×2-7H8g
Расчёт элементов зубчатой передачи
1 Расчет зазоров сопряжения
Расчёт гарантированного бокового зазора определяющего вид сопряжения должен производиться с учётом:
температурного режима работы передачи;
способа смазывания и окружной скорости зубчатых колёс;
допустимого свободного поворота зубчатых колёс в пределах бокового зазора [3].
Величина бокового зазора jn1 соответствующая температурной компенсации определяется по формуле:
jn1= a[αp1 (t1-20º)- αp2 (t2-20º)]2sinα(6.1)
jn1= 0684a [αp1 (t1-20º)- αp2 (t2-20º)](6.2)
где а – межосевое расстояние передачи мм;
αp1 αp2 – коэффициенты линейного расширения для материалов соответственно зубчатых колёс и корпуса ºС-1. Принимаем αp1=115·10-6 ºС-1 для стальных зубчатых колёс и αp2=105·10-6 ºС-1 для чугунного корпуса [табл. 1.62 3];
t1 t2 – предельные температуры для которых рассчитывается боковой зазор соответственно зубчатых колёс и корпуса.
Межосевое расстояние a определяется по формуле:
a=05m(z1+z2) мм(6.3)
где m=4 – модуль передачи;
z1 – число зубьев шестерни;
z2 – число зубьев колеса.
а=054 (25+55)=160 мм
jn1=1600684 [11510-6 (85-20)-10510-6 (50-20)]=0047 мм(6.4)
Величину бокового зазора (мкм) необходимого для размещения слоя смазки ориентировочно можно определить по формуле:
jn2=(10÷30)m мкм(6.5)
Причём 10m принимают для тихоходных передач и до 30 m – для особо высокоскоростных передач. Принимаем для нашего случая коэффициент перед m равным 10:
Таким образом гарантированный боковой зазор:
jn min≥ jn1+ jn2 мкм(6.6)
Наибольший возможный боковой зазор jn max определяется по формуле:
jn max= jn min+(Тн1+Тн2+2a)2sinα(6.7)
jn max= jn min+(Тн1+Тн2+2a)0684 (6.8)
где Тн1 Тн2 – допуски на смещение исходного контура соответственно для 1-го и 2-го колёс;
a – предельное отклонение межосевого расстояния для данного вида сопряжения.
Для степени точности зубчатой передачи 8-Н имеем следующие данные показателей норм кинематической точности:
Fr1=50 мкм Fr2=71мкм [таблица 6 8] ГОСТ 1643-81 для делительных диаметров:
Тн1=120 мкм Тн2=300 мкм [таблица 15 8]
а=20 мкм [таблица 13 8]
jn max=87+(120+300+220)0684=40164 мкм
В случае необходимости (для кинематических передач) могут быть определены:
наименьший свободный угловой поворот зубчатого колеса (α=20º)
φmin=(2 jn min(mzcosα))206(6.11)
для колеса тихоходного:
наибольший свободный угловой поворот зубчатого колеса (α=20º)
φmax=(2 jn maxmzcosα)206 (6.12)
φmax2=(240164455094)206=800=1320.
2 Расчёт некоторых размеров разноимённых профилей зубьев
Определить некоторые отклонения для зубчатого колеса.
Диаметр вершин зубьев da определяется по формуле: (для колеса тихоходного)
da =220+24(1+0)=228 мм
где d – делительный диаметр колеса
hа=1 – коэффициент высоты головки зуба;
Т.к. количество зубьев большое то х = 0.
В таблице 3 ГОСТ 1643-81 предусмотрен учет значений номинального коэффициента осевого перекрытия . Для прямозубой передачи определяется по формуле:
= bwm = 504314=40 (6.14)
Граничные значения коэффициента приведены в таблице 4 ГОСТ 1643-81
Так как коэффициент осевого перекрытия расчетный больше граничного значения коэффициента тогда определяем следующие параметры:
По заданию зубчатая передача имеет точность 8-Н ГОСТ 1643-81 и исходя из этого мы должны выбрать показатели точности колес:
а) показатель кинематической точности: - колебание измерительного межосевого расстояния находим в зависимости от степени точности колеса (8) величины делительного диаметра (100 мм и 220 мм – входят в интервал «до 125» и «свыше 125 до 400») модуля (4) равным = 71 мкм = 100 мкм.
б) показатель плавности работы: fpt – отклонение шага находим в зависимости от степени точности колеса (8) величины делительного диаметра (100 мм и 220 мм – входят в интервал «до 125» и «свыше 125 до 400») модуля (4) равным fpt = ±25 мкм fpt = ±28 мкм
в) показатель контакта зубьев: Fk – суммарная погрешность контактной линии находим в зависимости от степени точности колеса (8) величины ширины зубчатого венца (40 мм – входит в интервал « до 40») модуля (4) равным Fk = 40 мкм
Длина общей нормали для прямозубых колёс без смещения (W) косвенно характеризующая толщину зуба и окружной шаг мм
где W1 – длина общей нормали цилиндрических прямозубых колес модулем =1 мм
при m = 4 мм. Значение W1 в зависимости от числа зубьев колеса (z = 55) и число зубьев охватываемых при измерении (zn = 7) состоят в соответствии с таблицей 5.30 [13]:
W = 199592 40 = 79837мм
Длина общей нормали имеет отклонение. Чтобы не произошло заклинивания в передаче это отклонение имеет отрицательное значение. Наименьшее отклонение длины общей нормали (EWs) находим по таблице 16 ГОСТ 1643-81
Таким образом наименьшее отклонение длины общей нормали EWs = 14 мкм. Допуск на длину общей нормали TW определим по таблице 19 ГОСТ 1643-81
Допуск на длину общей нормали TW = 28 мкм.
Значит верхнее отклонение длины общей нормали EWs min = -14 мкм.
Нижнее отклонение длины общей нормали:
EWs max = - EWs - TW = -14-28 = -42мкм. (6.16)
Таким образом в таблице чертежа должно быть проставлено для длины общей нормали: W = 79837-0014-0042.
Расчёт конструкторской размерной цепи вала тихоходного
Размерные цепи решают прямой и обратной задачей согласно заданию решаем обратную задачу.
Рассчитать конструкторскую размерную цепь вала тихоходного. Неуказанные предельные отклонения валов h14 остальные ±IT142.
Рисунок 12 – Схема конструкторской размерной цепи вала тихоходного
При расчете размерной цепи учитываем что замыкающее звено является наименее точным. В качестве замыкающего звена выбираем выходную шейку т.к. в собранном узле положение свободного конца данной шейки имеет возможность продольного смещения. Находим номинальное значение (А ном) замыкающего звена:
А ном = Σ Аув – Σ Аум мм (7.1)
где Аув – увеличивающие звенья размерной цепи;
Аум – уменьшающие звенья размерной цепи.
А ном = 274-(39+8+60+47) = 120 мм
Находим максимальное (А max) и минимальное (А min) значения замыкающего звена:
А min = Σ Аув min – Σ Аум max мм. (7.3)
Наибольшие значения размеров звеньев: 274000; 39310; 8000; 59630; 47310.
Наименьшие значения размеров звеньев: 272700; 38690; 7640; 60370; 46690.
А max =274000-(38690+7640+60370+46690)=12061 мм
А min =272700-(39310+8000+59630+47310)=11845мм
Находим верхнее предельное отклонение (esА) замыкающего звена:
esА = А max- А ном мм (7.4)
esА = 12061 – 120 = 061мм
Находим нижнее предельное отклонение (eiА ) замыкающего звена:
eiА = A min-A ном мм (7.5)
eiА =11845 – 120 = - 155 мм
Допуск (IT ) замыкающего звена равен:
IT = А max - A min =12061 –11845 = 216мм
Таким образом значение замыкающего звена и его предельные отклонения равны:
Назначение средств измерения для вала тихоходного
Назначение средств измерения выполняется в зависимости от масштаба производства .В данной курсовой работе задан еденичный тип производства. Для единичного производства применяются универсальные СИ и контрольные приспособления.
Контролю подлежат(см. чертёж «Вал тихоходный»):
а) диаметральные размеры –90h14 70s6 65n6 55
б) линейные–274 8 39± 60+ 47± 70± 26± 49-02; 16
в) шероховатость поверхностей Ra 16; Ra 32; Ra0 63;
г) радиус R 16 и фаски 2×45°;16×45°;
д) допуск формы и расположения поверхностей :1) допуск соосности 2) допуск цилиндричности 3)допуск торцового биения.
Назначаем средства контроля :
Для диаметральных размеров 65 70 55k6– микрометр рычажный типа МР и МРИ скоба рычажная типа СР; 90h14– штангенциркуль ШЦ-
для линейных размеров – 39± 60+ 47± 70± 26± - штангенциркуль ШЦ- 16N9– глубиномер 274 8 49-02– штангенциркуль ШЦ-
для контроля шероховатостей поверхностей Ra 063; Ra 16; Ra32 используем образцы шероховатостей по ГОСТ 2789;
для радиусов R 16 и фасок 16×45°;2×45°- штангенциркуль типа ШЦ-I;
для контроля отклонения формы и расположения –(допуск цилиндричности допуск соосности и допуск торцового биения)-прибор-биениемер ПБМ-500М.
Данные диаметральных и линейных размеров заносим в таблицу 8.
Таблица 8 — Выбор универсальных СИ для вала тихоходного
Наименование и обозначение выбранного СИ
Нутромер индикаторный (НИ) с ценой деления отсчетного устройства 001 мм
Штангенциркуль с отсчетом по нониусу 005 мм – ШЦ-II
Штангенциркуль ШЦ-III с ценоой деления 01 мм
Скоба рычажная типа СР при использовании в стойке или при обеспечении теплоизоляции от рук оператора при настройке на ноль по установочной мере длины 3-го класса
В настоящей курсовой работе использованы ссылки на следующие нормативные документы:
ГОСТ 520-89 Подшипники качения. Технические условия.
ГОСТ1643-81 Основные нормы взаимозаменяемости. Передачи зубчатые цилиндрические. Допуски.
ГОСТ 3325-85 Подшипники качения. Поля допусков и технические требования к посадочным поверхностям валов и корпусов. Посадки.
ГОСТ 9150-2002 Основные нормы взаимозаменяемости. Резьба метрическая. Профиль.
ГОСТ 16093-2004 Основные нормы взаимозаменяемости. Резьба метрическая. Допуски. Посадки с зазором.
ГОСТ 23360-78 Основные нормы взаимозаменяемости. Соединения шпоночные с призматическими шпонками. Размеры шпонок и сечений пазов. Допуски и посадки.
ГОСТ 24853-81 Калибры гладкие для размеров до 500 мм. Допуски.
ГОСТ 25346-89 Основные нормы взаимозаменяемости. ЕСДП. Общие положения. Ряды допусков и основных отклонений.
Список использованной литературы
Анурьев В.И. Справочник конструктора-машиностроителя: В 3-х т. Т.1. – 5-е изд. перераб. и доп. – М. Машиностроение 1979. –728 с. ил.
Анурьев В.И. Справочник конструктора-машиностроителя: В 3-х т. Т.2. – 5-е изд. перераб. и доп. – М. Машиностроение 1979. –559 с. ил.
Анурьев В.И. Справочник конструктора-машиностроителя: В 3-х т. Т.3. – 5-е изд. перераб. и доп. – М. Машиностроение 1979. –557 с. ил.
Болдин Л.А. Основы взаимозаменяемости и стандартизации в машиностроении: Учебное пособие для вузов. – 2-е изд. перераб. и доп. – М.: Машиностроение 1984. – 272 с. ил.
Общетехнический справочник Е.А.Скороходов В.П.Зотов А.Б.Пикнис и др.; Под общ. Ред. Е.А. Скороходова. – 3-е изд. перераб. и доп. – М.: Машиностроение 1989. – 512 с. ил.
Покровский Б.С. Механосборочные работы и их контроль: Учеб. Пособие для ПТУ. – М.: Высш. шк. 1989. – 271 с. ил.
Справочник технолога-машиностроителя. В 2-х т. Т. 1 Под ред. А.Г.Косиловой и РК.Мещерякова. – 4-е изд. перераб. и доп. – М.: Машиностроение 1986. – 656 с. ил.
Справочник технолога-машиностроителя. В 2-х т. Т. 2 Под ред. А.Г.Косиловой и РК.Мещерякова. – 4-е изд. перераб. и доп. – М.: Машиностроение 1986. – 496 с. ил.
Точность и производственный контроль в машиностроении: Справочник И.И.Балонкина А.К.Кутай Б.М.Сорочкин Б.А.Тайц; Под общ. ред. А.К.Кутая Б.М.Сорочкина. – Л.: Машиностроение 1983. – 368 с. ил.
Якушев А.И. и др. Взаимозаменяемость стандартизация и технические измерения: Учебник для втузов А.И. Якушев Л.Н.Воронцов Н.М.Федотов – 6-е изд. перераб. и дополн. – М. Машиностроение 1987. – 352с. ил.
Якушев А.И. Взаимозаменяемость стандартизация и технические измерения. Изд. 3-е перераб. и доп. – М. Машиностроение 1974. – 472с. ил.
ГОСТ 2.402-68 Единая система конструкторской документации. Условные изображения зубчатых колес реек червяков и звездочек цепных передач;
ГОСТ 2.403-75 Единая система конструкторской документации. Правила выполнения чертежей цилиндрических зубчатых колес;
ГОСТ 8.050-73 ГСОЕИ Нормальные условия выполнения линейных и угловых измерений.
ГОСТ 1643-81 ОНВ Передачи зубчатые цилиндрические. Допуски.
ГОСТ 2015-84 Калибры гладкие нерегулируемые. Технические требования. М. Издательство стандартов 5 с.
ГОСТ 24642-81 ОНВ Допуски формы и расположения поверхностей. Основные термины и определения. М. Издательство стандартов 1990. –68 с. ил.
ГОСТ 24643-81 ОНВ Допуски формы и расположения поверхностей. Числовые значения. М. Издательство стандартов 1981. –14 с.
ГОСТ 24851-81 Калибры гладкие для цилиндрических отверстий и валов. Виды. М. Издательство стандартов 8 с. ил.
Рекомендуемые чертежи
- 24.01.2023