Расчёт оптимальных режимов резания


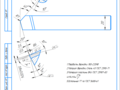
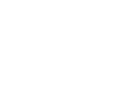
- Добавлен: 25.01.2023
- Размер: 2 MB
- Закачек: 0
Описание
Состав проекта
![]() |
![]() |
![]() ![]() ![]() |
![]() ![]() ![]() |
![]() ![]() ![]() |
![]() ![]() ![]() ![]() |
![]() ![]() ![]() |
![]() ![]() ![]() |
![]() |
![]() ![]() ![]() |
![]() |
![]() |
![]() |
![]() |
![]() |
![]() |
![]() |
![]() |
![]() |
![]() |
![]() |
![]() |
![]() |
![]() |
![]() |
![]() |
![]() |
![]() |
![]() |
![]() |
![]() |
![]() |
![]() |
![]() |
![]() |
![]() |
![]() |
![]() |
![]() |
![]() |
![]() |
![]() |
![]() |
![]() |
![]() |
![]() |
![]() |
![]() |
![]() |
![]() |
![]() |
![]() |
![]() |
![]() |
![]() |
![]() |
![]() |
![]() |
![]() |
![]() |
![]() |
![]() |
![]() |
![]() |
![]() |
![]() |
![]() |
![]() |
![]() |
![]() |
![]() |
![]() |
![]() |
![]() |
![]() |
![]() |
![]() |
![]() |
![]() |
![]() |
![]() |
![]() |
![]() |
![]() |
![]() |
![]() |
![]() |
![]() |
![]() |
![]() |
![]() |
![]() |
![]() |
![]() |
![]() |
![]() |
![]() |
![]() |
![]() |
![]() |
![]() |
![]() |
![]() |
![]() |
![]() |
![]() |
![]() |
![]() |
Дополнительная информация
yjvjuhfvvf.frw

ПЗ1111.doc
к курсовой работе по курсу:
Вариант № 3 Группа: 5ТМ-39
Головачёв С.Ю. Трехгорный: ТТИ НИЯУ МИФИ ТМ 2011 16 л. Библиография литературы – 10 наименований 1 лист формата А4.
В курсовой работе рассмотрен расчёт оптимальных режимов резания при точении аналитическим и табличным методами приведено сравнение режимов резания полученных двумя выше указанными методами дан анализ и сделаны выводы.
Построена номограмма зависимости V = f (Dn) .
В графической части курсовой выполнен чертёж прямого проходного резца.
Табличный метод расчета 3
Аналитический метод расчёта 5
Построение номограммы 13
Библиографический список
Графическая часть 1 листе формата А4.
Вид обработки — обточка по диаметру.
Материал детали — СЧ18-36.
Диаметр детали — 92.5 h12 мм.
Длина обработки — 140 мм.
Шероховатость поверхности — Rz20.
Диаметр заготовки — 97 мм.
Длина заготовки — 360 мм.
Способ закрепления заготовки — в центрах.
Определить табличным методом режим резания построить номограмму V=f(nD) выполнить чертёж резца.
По справочной литературе [6 9] определим предел прочности при растяжении материала детали sв=950 Нмм2 (950 МПа) и допуск на изготовление d=016мм.
Табличный метод расчета
Для достижения заданной точности и шероховатости поверхности детали её обработку производим в два прохода: первый проход — предварительный черновой второй — окончательный получистовой.
Определим параметры инструмента режимы обработки и выберем оборудование для выполнения второго прохода.
Для окончательной обработки детали изготовляемой из серого чугуна выбираем твердосплавную пластинку марки ВК6 (прилож. 2).
Выбираем (по прилож. 3) форму передней поверхности резца — плоскую с фаской.
По прилож. 4 определяем геометрические параметры режущей части резца:
f = 05 мм; gf = –4; g = 12°; a = 8°; j = 40°; j1 = 20°; r = 10.
По ГОСТ 6743 принимаем резец правый прямой проходной с сечением державки ВН = 2020 мм2 длиной L = 170 мм оснащённый твердосплавной пластиной толщиной С = 55 мм.
Припуск на обработку детали h =6 мм удаляется за два прохода. Глубина резания t на втором проходе должна быть не более 2 мм при этом на черновом проходе должна удаляться большая часть припуска. В связи с этими требованиями назначаем глубину резания на первом проходе равной 44 мм на втором — t=16мм.
Величину подачи обеспечивающей получение заданной шероховатости определим по прилож. 5 предполагая при этом что скорость резания при окончательной обработке будет попадать в любой диапазон скоростей.
Подача допускаемая шероховатостью поверхности
Принимаем Sшп = 03 ммоб.
Полученное значение подачи проверим по прочности резца и твердосплавной пластинки а также по допускаемому прогибу детали.
Величину подачи допускаемой прочностью державки резца определим по прилож. 6 приняв при этом вылет резца lp = 1 H = 20 мм:
Подачу допускаемую прочностью пластинки твёрдого сплава определим
Подача допускаемая по прогибу детали (прилож. 10):
Sжд = Sт × KL × Kj × KS
где Sm — табличное значение подачи Sт = 16 мм;
KL Kj KS — коэффициенты учитывающие влияние длины детали угла j способа закрепления детали KL = 12 Kj = 1 KS = 10.
Подача выбранная из условия получения заданной шероховатости поверхности детали удовлетворяет и другим рассмотренным ограничениям и может быть принята за технологическую.
Скорость резания V=Vт×К1×К2
где Vт — табличное значение скорости Vт = 147 мс (прилож. 11);
К1 — коэффициент учитывающий влияние обрабатываемого материала К1=07;
К2 — коэффициент учитывающий влияние материала инструмента К2=115;
V = 147×07×115 = 118 мс.
Эта скорость резания достигается при частоте вращения шпинделя
Мощность затрачиваемая на процесс резания определим по прилож. 12: N = 20 кВт.
Мощность привода станка при к.п.д. h = 075
Nст = 20075 = 266 кВт.
Усилие подачи (прилож. 13)
где Qт — табличное значение усилия подачи Qт = 1300 Н;
Кg — коэффициент учитывающий влияние угла g Кg = 1;
Для обработки детали выбираем станок модели 1К62 имеющий следующие технические характеристики:
высота центров — 210 мм;
расстояние между центрами — 700 мм;
высота от опорной поверхности резцедержателя до линии центров — 21 мм;
мощность привода — 28 кВт;
наибольшее усилие подачи — 3050 Н;
диапазон частот вращения шпинделя — 20 2000 обмин;
диапазон подач — 006 107 ммоб.
Определённые ранее значения подачи и частоты вращения корректируем по имеющимся в станке.
Принимаем S = 03 ммоб n = 1380 обмин.
Тогда скорость резания
Основное или машинное время необходимое для выполнения второго прохода
где L — длина обрабатываемой поверхности детали L = 360 мм;
lп — длина набега принимаем lп = 2 мм.
Определённые параметры инструмента оборудования режим и время обработки заносим в табл. 1–3.
Геометрические параметры режущей части
Резец правый прямой проходной
Расстояние между центрами
Высота от опорной поверхности до линии центров
Мощность привода кВт
Допустимое усилие подачи Н
Диапазон частот вращения шпинделя обмин
Частота вращения шпинделя обмм
Аналитический метод расчета.
Для проведения расчётов на ПК определяются параметры входящие в блок исходных данных (табл. 4).
Значения параметров процесса обработки занесены в 4 и 5 колонки табл. 4. Расчеты на ПК следует выполнять согласно инструкции (приложение 20). Результаты расчёта представлены в табл. 5.
Анализируя полученные результаты видим что наибольшая производительность обработки достигается при частоте вращения шпинделя n = 1380 обмин и подаче S = 03 ммоб при этом величина подачи ограничивается точностью обработки.
Анализируя влияние параметров входящих в это ограничение приходим к выводу что величину подачи наиболее просто можно увеличить изменив метод закрепления детали.
При закреплении детали в центрах с люнетом жёсткость системы СПИД увеличивается следовательно увеличивается и подача допускаемая по этому ограничению.
Одновременно с этим есть ещё возможность дополнительно увеличить величину подачи. Это можно сделать увеличив главный угол в плане до 45°. Увеличение угла j ведёт к уменьшению длины активной части режущей кромки резца а следовательно к уменьшению радиальной составляющей сил резания. Уменьшение сил резания уменьшит изгиб заготовки что позволяет дополнительно увеличить величину подачи. Результаты повторного расчёта представлены в табл.
Исходные данные для расчёта на ЭВМ
Вид обработки (прилож. 19)
Стойкость инструмента
Материал инструмента
Радиус вершины резца
Главный угол в плане
Вспомогательный угол в плане
Ширина и высота сечения державки
Диаметр державки резца D*
Твёрдость материала (СЧ 18-36)
Состояние обрабатываемой поверхности (прилож.8)
Диаметр заготовки под обработку
Вид закрепления заготовки
начальное положение резца**
Конечное положение резца
Количество наружн. ступеней обработки
Диаметр длина 1-й ступени
Количество внутренних ступеней
* Для резцов с прямоугольной формой поперечного сечения державки указать диаметр державки равным 0. Для резцов с круглой формой поперечного сечения державки необходимо указывать В и Н равным 0.
** Указывать начальное положение резца при обработке относительно правого торца в мм. Если обработка начинается с торца то указать любое число например 001. Не допускается введение начального положения равного 0.
Наименьшее время обработки Т = 072 мин достигается при частоте вращения шпинделя n = 1380 обмин и подаче S = 03ммоб. При этом скорость резания V= 238 мс.
Вид обработки - наружное продольное точение
Стойкость инструмента (мин) = 30
Длина обработки (мм) = 140
Глубина резания (мм) = 2.25
Допуск на обработку (мм) = 0.16
Вид закрепления - в центрах
Вид СОЖ - на водной основе
Материал режущей части - ВК6
Радиус при вершине резца (мм) = 1
Главный угол в плане (град) = 40
Вспомогат. угол в плане (град) = 20
Угол заострения (град) = 78
Сечение державки - прямоугольное
Ширина сечения (мм) = 20
Высота сечения (мм) = 20
Вылет резца (мм) = 30
Материал детали - СЧ18-36
Твердость материала (HB) = 200
Шероховатость поверхности (Rz) = 20
Состояние поверхности заготовки - без корки
Длина заготовки (мм) = 360
Диаметр под обработку (мм) = 97
Начальное положение резца (мм) = 0.01
Конечное положение резца (мм) = 140
Кол. наружн. ступеней (мм) = 1
Кол. внутр. ступеней (мм) = 0
N Скорость Ограничение подачи по
V точности прочности стойкости мощности шероховатости
Оптимальные режимы резания:
Машинное время Т мин : 0.510
Толщина пластинки твердого сплава не менее (мм): 0.996
Сила резания Pz = 69.481
Вид закрепления - в центрах с люнетом
Радиус при вершине резца (мм) = 2
Главный угол в плане (град) = 60
Машинное время Т мин : 0.394
Толщина пластинки твердого сплава не менее (мм): 1.014
Сила резания Pz = 103.910
Анализ данных полученных при расчете аналитическим методом.
Анализ первого расчета.
Данные для расчета были взяты из таблицы
Выбранные параметры являются оптимальными для данных условий обработки. Машинное время=0.510 ммин.сила резания = 69б481Н
Толщина пластинки твердого сплава не менее 0996 удовлетворяет выбранной величине при сохранении всех параметров результаты расчета позволяют уменьшить ее толщину тем самым сэкономить дорогостоящий сплав.
Анализ второго расчета.
При втором расчете был увеличен главный угол с 40 до 60 изменён радиус при вершине резца с 1 до 2 мм а так же был изменён вид закрепления заготовки. Толщина пластинки твердого сплава не менее 1014 также удовлетворяет выбранной величине.
Глубина резания t мм
Частота вращения n обмин
Скорость резания V мc
Несовпадение параметров режима резания полученных аналитическим и табличным методами объясняется тем что при аналитическом расчете более полно учитываются все факторы процесса обработки.
Построение номограммы зависимости V= f(n D)
Зависимость V от D и n выражается формулой:
номограмма строится в логарифмических координатах. По оси ординат откладывается скорость резания lg V по оси абсцисс – диаметр детали lg D.
После логарифмирования получим уравнение прямой линии наклонной к оси абсцисс под углом L2 = 45 0 (tg 45 = 1):
Для различных значений n получим ряд прямых линий. При построении номограммы удобно принять D = 97мм тогда
Подставляя в формулу различные значения чисел оборотов (по станку) получим соответствующие им значения V:
Значения всех входящих в уравнение параметров приведены в
Построенная система является номограммой V= f(n D)
Список использованной литературы
АврутинС.В. Краткий справочник металлиста: С.В. Аврутин.-М.: «Машиностроение» 1978.-456с.
Грановский Г.И. Резание металлов: Г.И. Грановский В.Г. Грановский.-М.: «Высшая школа» 1985.-304с.
Козлов А.В. «Расчет режимов резания на ПК»: Учебное пособие
А.В.Козлов И.П.Дерябин И.Н.Миронова.-Челябинск.: Изд-во ЮУрГУ 2004.-54с.
OTчёт 1.doc
Стойкость инструмента (мин) ? 30
Длина обработки (мм) ? 140
Глубина резания (мм) ? 2.25
Допуск на обработку (мм) ? 0.16
Вид закрепления - в центрах
Вид СОЖ - на водной основе
Материал режущей части - ВК6
Радиус при вершине резца (мм) ? 1
Главный угол в плане (град) ? 40
Вспомогат. угол в плане (град) ? 20
Угол заострения (град) ? 78
Сечение державки - прямоугольное
Ширина сечения (мм) ? 20
Высота сечения (мм) ? 20
Вылет резца (мм) ? 30
Материал детали - СЧ18-36
Твердость материала (HB) ? 200
Шероховатость поверхности (Rz) ? 20
Состояние поверхности заготовки - без корки
Длина заготовки (мм) ? 360
Диаметр под обработку (мм) ? 97
Начальное положение резца (мм) ? 0.01
Конечное положение резца (мм) ? 140
Кол. наружн. ступеней (мм) ? 1
Кол. внутр. ступеней (мм) ? 0
N Скорость Ограничение подачи по
V точности прочности стойкости мощности шероховатости
Оптимальные режимы резания:
Машинное время Т мин : 0.510
Толщина пластинки твердого сплава не менее (мм): 0.996
Сила резания Pz = 69.481
резец 12 Kыы.cdw

Матриал державки Сталь 45 ГОСТ 2590-71
Материал пластины ВК6 ГОСТ 25987-83
Остальные ТТ по ГОСТ 5688-61
OTчёт 2.doc
Стойкость инструмента (мин) ? 30
Длина обработки (мм) ? 140
Глубина резания (мм) ? 2.25
Допуск на обработку (мм) ? 0.16
Вид закрепления - в центрах с люнетом
Вид СОЖ - на водной основе
Материал режущей части - ВК6
Радиус при вершине резца (мм) ? 2
Главный угол в плане (град) ? 60
Вспомогат. угол в плане (град) ? 20
Угол заострения (град) ? 78
Сечение державки - прямоугольное
Ширина сечения (мм) ? 20
Высота сечения (мм) ? 20
Вылет резца (мм) ? 30
Материал детали - СЧ18-36
Твердость материала (HB) ? 200
Шероховатость поверхности (Rz) ? 20
Состояние поверхности заготовки - без корки
Длина заготовки (мм) ? 360
Диаметр под обработку (мм) ? 97
Начальное положение резца (мм) ? 0.01
Конечное положение резца (мм) ? 140
Кол. наружн. ступеней (мм) ? 1
Кол. внутр. ступеней (мм) ? 0
N Скорость Ограничение подачи по
V точности прочности стойкости мощности шероховатости
Оптимальные режимы резания:
Машинное время Т мин : 0.394
Толщина пластинки твердого сплава не менее (мм): 1.014
Сила резания Pz = 103.910
задание на курсач.doc
Южно-Уральский государственный университет
Филиал в г.Златоусте
Кафедра «Технология машиностроения станки и инструмент»
А.В.Козлов И.П.Дерябин И.Н.Миронова
РАСЧЕТ РЕЖИМОВ РЕЗАНИЯ НА ПК
УДК 621.9(075.8) + 621.9.02(075.8)
Козлов А.В. Дерябин И.П. Миронова И.Н. Расчет режимов резания на ПК: Учебное пособие. — Челябинск: Изд-во ЮУрГУ 2002. — 54 с.
Рассмотрены методы расчета режимов резания при точении резцами из быстрорежущей стали и твердого сплава приведены рекомендации по выбору режущего инструмента и необходимые справочные материалы. Программы расчета разработаны применительно к современным персональным компьютерам.
Учебное пособие предназначено для выполнения курсовой работы студентами специальностей 120100 210200.
Ил. 4 табл. 8 список лит. — 10 назв.
Одобрено учебно-методической комиссией филиала ЮУрГУ в г.Златоусте.
Рецензенты: В.Ф.Пепеляев В.М.Истомин.
Издательство ЮУрГУ 2002.
Дальнейшее развитие экономики нашей страны будет происходить за счет интенсификации производства. В машиностроении и в частности при обработке металлов резанием одним из путей интенсификации производства является более полное использование технологических возможностей всех составляющих процесса производства.
Себестоимость обработки детали зависит от многих факторов в число которых входят и режимы резания. Назначение элементов режима резания обеспечивающих минимальную себестоимость обработки — задача сложная решение которой в большинстве случаев возможно только после полного анализа конкретной операции а иногда и целого ряда связанных с ней процессов.
Одним из этапов решения этой задачи является определение элементов режима резания допускаемых возможностями оборудования и инструмента. Назначение величин элементов режима резания как правило выполняют в следующей последовательности: определяют глубину резания затем выбирают подачу и стойкость инструмента и далее определяют скорость резания соответствующую принятым величинам глубины резания подачи и стойкости. После согласования величин подачи и скорости резания с возможностями кинематических цепей станка определяют основное (машинное) время обработки.
В практической деятельности технолог назначая режим резания пользуется одним из методов расчета — аналитическим табличным или графическим. Широкое применение персональных компьютеров позволяет назначить режим резания более точно так как аналитические зависимости связывающие элементы режима резания создают возможность более полного учета и анализа факторов влияющих на процесс обработки.
В предлагаемом студентам пособии описаны методы расчета параметров режима резания в последовательности соответствующей порядку проведения расчета. Аналитический метод расчета изложен применительно к выполнению его на современных персональных компьютерах.
ТАБЛИЧНЫЙ МЕТОД ОПРЕДЕЛЕНИЯ РЕЖИМА РЕЗАНИЯ
Определение режима резания по специальным таблицам [1 2] производится в следующей последовательности.
1. Назначение параметра режущего инструмента
Выбор материала режущей части её геометрических параметров размеров державки и типа резца производятся в следующей последовательности [3 4].
Тип резца назначают в зависимости от вида технологического перехода. При этом необходимо обеспечить условия наиболее удобной обработки поверхности детали.
Марка материала режущей части и форма передней поверхности резца назначаются в зависимости от вида и условий обработки обрабатываемого материала и его механических характеристик.
Геометрические параметры режущего клина резца определяются исходя из характеристик обрабатываемого материала и условий обработки.
2. Выбор глубины резания
В процессе обработки с поверхности заготовки удаляется слой металла называемый припуском. Наименьшая величина припуска необходимого для получения детали с заданными параметрами обработанной поверхности определяется расчётом.
Припуск с заготовки удаляется за один или несколько проходов обеспечивающих постепенное уточнение обработанной поверхности например черновой получистовой и чистовой переходы. В свою очередь на каждом технологическом переходе припуск может быть удалён за один или несколько проходов.
Для сокращения времени обработки припуск желательно удалять за один проход.
Глубина резания на каждом проходе
t = 05×(Di – Di+1) (1)
где Di Di+1 — диаметры до и после обработки на выполняемом проходе.
Обычно на черновых проходах (шероховатость обработанной поверхности Rz80 320 с точностью менее 12 квалитета) глубина резания ограничивается мощностью станка прочностью инструмента жёсткостью детали и другими факторами.
При получистовых проходах (Rz 20 40 точность 8 12 квалитета) глубина резания не более 2 мм.
При чистовой обработке (Rz 125 25 точность выше 8 квалитета) глубина резания не более 01 04 мм.
3. Определение величины подачи
Подачей при точении называется перемещение резца вдоль обработанной поверхности за один оборот детали.
Для снижения времени обработки целесообразно максимальное увеличение подачи но возрастающие при этом нагрузки и ряд других факторов ограничивают её величину.
При черновой обработке подача ограничивается силами действующими при резании. Величина подачи назначается в зависимости от глубины резания размеров сечения державки резца материала и диаметра детали.
При чистовой обработке величина подачи выбирается в зависимости от шероховатости получаемой поверхности обрабатываемого материала принятых геометрических параметров инструмента и предлагаемой скорости резания.
Выработанное значение подачи как при черновой так и чистовой обработке корректируется умножением на коэффициенты учитывающие влияние обрабатываемого материала и условий обработки.
В некоторых случаях например когда производится обработка деталей с большим вылетом инструмента большим сечением срезаемого слоя или обрабатываются детали большой длины полученные значения подачи дополнительно проверяются по условиям учитывающим специфику обработки.
Обычно резец устанавливается с вылетом lp15 Н где Н — высота державки резца. При установке резца с большим вылетом производится проверка подачи по прочности державки резца. При этом величина подачи определяется в зависимости от предела прочности или твёрдости обрабатываемого материала глубины резания и сечения державки резца. Влияние вылета резца учитывается поправочным коэффициентом.
При срезании стружки большого сечения резцом оснащённым твердосплавной пластиной производится проверка подачи по прочности пластинки. Величина подачи при этом выбирается в зависимости от характеристик обрабатываемого материала главного угла резца в плане глубины резания и толщины пластинки твёрдого сплава.
При обработке маложёстких деталей подача проверяется: при черновой обработке — по жёсткости системы “станок — приспособление — инструмент — деталь” или “СПИД”; при чистовой обработке — по допустимому прогибу детали. При проверке учитывается влияние диаметра и длины детали главного угла резца в плане материала заготовки и его характеристик глубины резания способа закрепления детали на станке и другие параметры.
В качестве технологической принимается подача удовлетворяющая всем рассмотренным ограничениям.
4. Определение скорости резания
Скоростью резания при токарной обработке называется линейная скорость точек обрабатываемой поверхности.
Скорость резания выбирается в зависимости от обрабатываемого и инструментального материала выбранных значений глубины резания подачи и главного угла резца в плане.
Найденное значение скорости корректируется умножением на коэффициенты учитывающие влияние материала детали и инструмента периода его стойкости и состояния поверхности заготовки.
По найденному значению скорости резания определяют соответствующую ей частоту вращения шпинделя станка:
5. Определение мощности станка
Мощность потребляемая при токарной обработке зависит от материала заготовки и его механических характеристик материала и геометрических параметров резца режимов обработки.
Мощность привода станка для обеспечения его нормальной работы должна удовлетворять условию:
где h — КПД станка h = 07 08.
6. Определение усилия подачи
Для осуществления процесса резания механизм подач станка должен развивать усилие Px зависящее от режима резания геометрии и материала режущей части инструмента обрабатываемого материала. Наибольшее усилие допускаемое прочностью механизма подач станка Q должно удовлетворять условию
7. Выбор оборудования
Для обработки детали выбирается станок с технологическими характеристиками обеспечивающими установленные выше режимы резания. Исходными данными для выбора модели станка являются: диаметр и длина детали требуемые частота вращения шпинделя станка и величина подачи мощность усилие подачи а также размеры резцедержателя. При выборе модели станка предпочтение отдаётся той мощность привода главного движения которой используется наиболее полно. При отсутствии оборудования удовлетворяющего всем предъявляемым требованиям выбирают модель станка с наиболее близкими к расчётным характеристиками.
Поскольку определённые выше частота вращения шпинделя и подача могут не соответствовать значениям этих параметров принятой модели станка величины их корректируются по станку. При этом допускается увеличение частоты вращения шпинделя до 5% а подачи — до 10% по сравнению с выбранными выше.
8. Определение основного технологического времени
Основное или технологическое время одного прохода
Тм = (L + lв + lп) nS мин (5)
где L — длина обрабатываемой поверхности детали мм;
lп — перебег резца lп = 1 5 мм.
Величина перебега зависит от глубины резания и главного угла в плане.
Найденные параметры режущего инструмента оборудования режимов резания и времени обработки заносятся в табл. 1 3 (см. пример расчёта на с. 14).
АНАЛИТИЧЕСКИЙ МЕТОД РАСЧЁТА РЕЖИМА РЕЗАНИЯ
Аналитический метод расчёта заключается в определении параметров режима резания по эмпирическим зависимостям.
Аналитический метод позволяет наиболее точно определить параметры режима обработки но большой объём выполняемых при этом вычислений делает его довольно трудоёмким. Использование ПК позволяет значительно сократить время вычислений и оптимизировать режимы резания.
Расчёт режима обработки при аналитическом методе производят в три этапа:
)определяют параметры режущего инструмента оборудования и глубину резания;
)вычисляют величины максимально допустимых подач и основное технологическое время;
)определяют наивыгоднейший режим резания.
1. Выбор параметров инструмента
Параметры режущего инструмента выбираются по таблицам приведённым в справочной и нормативной литературе. Последовательность выбора параметров рассмотрена ранее (см. п. 1.1).
Глубина резания при аналитическом методе расчёта выбирается также как и при табличном (см. п. 1.2).
3. Выбор оборудования
Если оборудование на котором будет производиться обработка детали не задано то модель станка выбирают исходя из габаритов обрабатываемой детали параметров инструмента предполагаемой частоты вращения шпинделя величины подачи и мощности затрачиваемой на процесс резания [5] из перечисленных в прилож. 18.
4. Определение величины подачи
Увеличение подачи позволяет сократить время на обработку детали то есть увеличить производительность процесса но имеется ряд ограничений определяющих её максимальную допустимую величину.
При токарной обработке величина подачи как правило ограничивается:
)прочностью державки резца;
)шероховатостью обработанной поверхности;
)точностью обработки;
Ограничение подачи по мощности станка
где — коэффициент резания (прилож. 14);
— показатели степени при глубине резания и подаче (см. прилож. 14);
Nz — мощность затрачиваемая на резания кВт;
t — глубина резания мм;
— поправочный коэффициент
КPz = КМр × Кjр × Кgр × Кrp × Knp × Кгр ×
KMp — коэффициент учитывающий влияние обрабатываемого материала;
Kjp — коэффициент учитывающий влияние главного угла в плане;
Kgp — коэффициент учитывающий влияние переднего угла;
Krp — коэффициент учитывающий влияние радиуса при вершине резца;
Knp — коэффициент учитывающий влияние износа резца;
Kгр — коэффициент учитывающий влияние группы обрабатываемости.
Значения всех коэффициентов даны в прилож. 14.
Ограничение подачи по прочности державки резца
где В — ширина державки резца мм;
Н — высота державки резца мм;
[s]и — допустимое напряжение изгиба Нмм2;
lp — вылет резца мм.
Подача ограниченная шероховатостью поверхности
где R — радиус при вершине резца в плане; Rz — шероховатость поверхности;
где j1 — вспомогательный угол в плане; j — главный угол в плане.
Вычисление происходит следующим образом: в качестве начального (стартового) значения подачи используется минимальная подача определённая ранее по условиям мощности станка прочности державки резца точности обработки и стойкости резца.
В случае невыполнения условия значение подачи уменьшается на одну позицию и вновь происходит проверка. Подача удовлетворяющая условию ограничения по шероховатости поверхности выводится в печать результатов.
Подача ограниченная точностью обработки
где a — коэффициент выражающий допустимую долю погрешности обработки зависящей от режимов резания в суммарной погрешности обработки (05);
d — величина допуска исполняемого размера;
CPz — коэффициент в формуле расчёта силы резания (см. прилож. 14);
t — глубина резания;
XPz — показатель степени при глубине резания (см. прилож. 14);
gст — жёсткость станка;
К1 К2 — коэффициенты влияния деформаций элементов технологической системы на точность обработки;
Е — модуль упругости Нмм2;
l — длина детали мм.
Жёсткость детали находится по формуле
где J — момент инерции сечения заготовки; Кж — коэффициент жёсткости
Dпр — приведённый диаметр ступенчатого вала мм.
Для деталей с утолщением посередине
Для деталей с односторонним утолщением
Коэффициент жёсткости для закрепления детали:
— в патроне консольно
где Хр — расстояние от правого торца детали до резца в мм;
— в патроне с передним центром
—в центрах с люнетом посередине
Жёсткость инструмента находится по формуле
Подача ограниченная стойкостью резца
Скорость резания допускаемая инструментальным материалом при заданной стойкости инструмента определяется эмпирической зависимостью:
где СV — коэффициент стойкости;
КV — поправочный коэффициент;
Т — стойкость инструмента при токарной обработке Т = 60 мин;
KV = KмV × KuV × KrV × KqV × KjV × KoV × KфV × KпV.
Здесь KмV KuV KrV KqV KjV KoV KфV KпV — коэффициенты учитывающие влияние обрабатываемого материала материала инструмента радиуса при вершине резца размеров сечения державки резца главного угла в плане вида обработки формы передней поверхности состояния поверхности.
Подставляя (2) в (20) и решая относительно S получаем
Система неравенств (6) (7) (8) (9) (21) ограничивающих значения допустимых подач и ограничения по кинематике станка n³nm nnma SSmax представляет математическую модель процесса обработки.
Геометрическая интерпретация математической модели представлена на рис.2.
Область возможных сочетаний частот вращения шпинделя и подач станка представлена заштрихованным многоугольником. Каждая из точек этого многоугольника обеспечивает получение детали с заданными параметрами то есть заштрихованный многоугольник является многоугольником решений.
Для достижения минимального времени обработки детали из множества точек многоугольника решений нужно найти такую точку то есть такое сочетание частот вращения шпинделя и подач при котором производительность процесса будет максимальной.
Для станков с дискретным регулированием частоты вращения шпинделя и подачи множество из возможных сочетаний является конечным. Это множество можно представить в виде ряда узловых точек лежащих в области ограниченной кинематическими параметрами станка. При этом часть узловых точек будет расположена в многоугольнике решений.
Очевидно что наибольшая производительность процесса обработки при данной частоте вращения шпинделя n1 будет достигнута при величине подачи S1 образующей узловую точку ближайшую к верхней границе многоугольника решений.
Задавая частоту вращения шпинделя определим величины подач максимально допускаемых по ограничениям. Наименьшая из этих подач будет являться максимально допустимой Smax доп. Найденное значение максимально допустимой подачи скорректируем по имеющейся ближайшей подаче станка причём Sст не должна превосходить Smax доп более чем на 10%. По заданному числу оборотов шпинделя подаче станка и длине обработки определим по зависимости (5) Тмаш.
Максимальная производительность процесса будет достигаться при таких значениях частоты вращения шпинделя и подаче при которых время обработки будет минимальным.
При наличии нескольких значений частот вращения шпинделя обеспечивающих минимальное время обработки принимают наименьшую из них так как при этом обеспечивается большая стойкость режущего инструмента.
О возможных направлениях совершенствования процесса обработки можно судить по величине подач допускаемых по ограничениям. При необходимости увеличения производительности процесса обработки производят корректировку параметров влияющих на соответствующие ограничения.
РАСЧЁТ РЕЖИМОВ РЕЗАНИЯ ПО НОМОГРАММАМ
Табличный и аналитический методы расчёта позволяют определить режимы обработки с учётом многих особенностей процесса но эти расчёты довольно трудоёмки что ограничивает их применение в единичном и мелкосерийном производстве. Определение режимов в таких случаях целесообразно производить по номограммам графически отображающим закономерности процесса.
Номограммы строятся для определённого цеха участка группы станков или отдельного станка.
1. Построение номограмм
Закономерности процесса резания аналитически отображаются преимущественно степенными зависимостями. Для упрощения разработки номограмм их построение производится в двойной логарифмической системе координат.
Порядок построения номограмм рассмотрим на примере зависимости
Аналитически эта зависимость выражается уравнением
Pz =10 CPztXpz SYpz VZp2 KPz. (22)
При постоянной глубине резания это уравнение преобразуется к виду
где C = 10 CPz×tXp×Kpz.
Логарифмируя выражение (23) получаем
lg Pz = lg C+Yp×lg S. (24)
Полученное уравнение представляет уравнение прямой линии тангенс угла наклона которой равен Yp.
Последовательно изменяя глубину резания от tmin до tmax при постоянном значении подачи S получаем ряд точек лежащих на прямой параллельной оси ординат (рис. 3). Через эти точки проводят линии под углом
на оси откладываются значения подач а на оси ординат — значения Pz.
Эта система графиков является номограммой зависимости Pz = f (t S).
Аналогично производится построение номограмм и других зависимостей.
2. Определение параметров по номограмме
Номограмма позволяет определить один из параметров зависимости по двум известным. Так номограмма представленная на рис. 3 позволяет определять: величину силы Pz по известным значениям подачи S и глубины резания t; S по Pz и t; t по известным Pz и S. Рассмотрим как определяется неизвестный параметр. Допустим что известна сила Pz1 и глубина резания t1 нужно определить соответствующую им величину подачи S1. Через точку соответствующую значению Pz проведём прямую параллельную оси абсцисс. Эта прямая пересекается с лучом соответствующим значению t1 в точке 1 проекция которой на ось абсцисс и есть определяемое значение S1.
Вид обработки — обточка по диаметру.
Материал детали — сталь 40Х.
Диаметр детали — 30 h11 мм.
Длина обработки — 300 мм.
Шероховатость поверхности — Rz20.
Диаметр заготовки — 40 мм.
Длина заготовки — 360 мм.
Способ закрепления заготовки — в центрах.
Определить табличным и аналитическим методами режимы резания построить номограмму Pz=f (t S) выполнить чертёж резца.
По справочной литературе [6 9] определим предел прочности при растяжении материала детали sв=980 Нмм2 (980 МПа) и допуск на изготовление d=016мм.
1. Табличный метод расчёта
Для достижения заданной точности и шероховатости поверхности детали её обработку производим в два прохода: первый проход — предварительный черновой второй — окончательный получистовой.
Определим параметры инструмента режимы обработки и выберем оборудование для выполнения второго прохода.
Для окончательной обработки детали изготовляемой из легированной стали выбираем твердосплавную пластинку марки Т15К6 (прилож. 2).
Выбираем (прилож. 3) форму передней поверхности резца — радиусную с фаской.
По прилож. 4 определяем геометрические параметры режущей части резца:
f = 06 мм; gf = –5; g = 15°; a = 10°; j = 30°; j1 = 15°; r = 10.
По ГОСТ 6743 принимаем резец правый прямой проходной с сечением державки ВН = 2020 мм2 длиной L = 100 мм оснащённый твердосплавной пластиной толщиной С = 55 мм.
Припуск на обработку детали h =5 мм удаляется за два прохода. Глубина резания t на втором проходе должна быть не более 2 мм при этом на черновом проходе должна удаляться большая часть припуска. В связи с этими требованиями назначаем глубину резания на первом проходе равной 35 мм на втором — t=15мм.
Величину подачи обеспечивающей получение заданной шероховатости определим по прилож. 5 предполагая при этом что скорость резания при оконча-тельной обработке будет больше 08 мс.
Подача допускаемая шероховатостью поверхности
Принимаем Sшп = 035 ммоб.
Полученное значение подачи проверим по прочности резца и твердосплавной пластинки а также по допускаемому прогибу детали.
Величину подачи допускаемой прочностью державки резца определим по прилож. 6 приняв при этом вылет резца lp = 15 H = 30 мм:
Подачу допускаемую прочностью пластинки твёрдого сплава определим по прилож. 7:
Подача допускаемая по прогибу детали (прилож. 10):
Sжд = Sт × KL × Kj × KS
где Sm — табличное значение подачи Sт = 16 мм;
KL Kj KS — коэффициенты учитывающие влияние длины детали угла j способа закрепления детали KL = 1 Kj = 072 KS = 1.
Подача выбранная из условия получения заданной шероховатости поверхности детали удовлетворяет и другим рассмотренным ограничениям и может быть принята за технологическую.
Скорость резания V=Vт×К1×К2
где Vт — табличное значение скорости Vт = 208 мс (прилож. 11);
К1 — коэффициент учитывающий влияние обрабатываемого материала К1=09;
К2 — коэффициент учитывающий влияние материала инструмента К2=155;
V = 208×09×155 = 29 мс.
Эта скорость резания достигается при частоте вращения шпинделя
Мощность затрачиваемая на процесс резания определим по прилож. 10: N = 29 кВт.
Мощность привода станка при к.п.д. h = 08
Nст = 2908 = 36 кВт.
Усилие подачи (прилож. 13)
где Qт — табличное значение усилия подачи Qт = 450 Н;
Кg — коэффициент учитывающий влияние угла g Кg = 1;
Для обработки детали выбираем станок модели 1616 имеющий следующие технические характеристики:
высота центров — 160 мм;
расстояние между центрами — 750 мм;
высота от опорной поверхности резцедержателя до линии центров — 20 мм;
мощность привода — 45 кВт;
наибольшее усилие подачи — 3050 Н;
диапазон частот вращения шпинделя — 44 1980 обмин;
диапазон подач — 006 107 ммоб.
Определённые ранее значения подачи и частоты вращения корректируем по имеющимся в станке.
Принимаем S = 036 ммоб n = 1380 обмин.
Тогда скорость резания
Основное или машинное время необходимое для выполнения второго прохода
где L — длина обрабатываемой поверхности детали L = 300 мм;
lп — длина набега принимаем lп = 3 мм.
Определённые параметры инструмента оборудования режим и время обработки заносим в табл. 1–3.
Геометрические параметры режущей части
Резец прямой проходной
Расстояние между центрами
Высота от опорной поверхности до линии центров
Мощность привода кВт
Допустимое усилие подачи Н
Диапазон частот вращения шпинделя обмин
Режим и время обработки
Частота вращения шпинделя обмм
2. Аналитический метод расчета
Для проведения расчётов на ПК определяются параметры входящие в блок исходных данных (табл. 4).
Значения параметров процесса обработки занесены в 4 и 5 колонки табл. 4. Расчеты на ПК следует выполнять согласно инструкции (приложение 20). Результаты расчёта представлены в табл. 5.
Анализируя полученные результаты видим что наибольшая производительность обработки достигается при частоте вращения шпинделя n = 2000 обмин и подаче S = 012 ммоб при этом величина подачи ограничивается точностью обработки.
Анализируя влияние параметров входящих в это ограничение приходим к выводу что величину подачи наиболее просто можно увеличить изменив метод закрепления детали.
При закреплении детали в центрах с люнетом жёсткость системы СПИД увеличивается следовательно увеличивается и подача допускаемая по этому ограничению.
Одновременно с этим есть ещё возможность дополнительно увеличить величину подачи. Это можно сделать увеличив главный угол в плане до 45°. Увеличение угла j ведёт к уменьшению длины активной части режущей кромки резца а следовательно к уменьшению радиальной составляющей сил резания. Уменьшение сил резания уменьшит изгиб заготовки что позволяет дополнительно увеличить величину подачи. Результаты повторного расчёта представлены в табл. 6.
Исходные данные для расчёта на ЭВМ
Вид обработки (прилож. 19)
Стойкость инструмента
Материал инструмента
Радиус вершины резца
Главный угол в плане
Вспомогательный угол в плане
Ширина и высота сечения державки
Диаметр державки резца D*
Состояние обрабатываемой поверхности (прилож.8)
Диаметр заготовки под обработку
Вид закрепления заготовки
начальное положение резца**
Конечное положение резца
Количество наружн. ступеней обработки
Диаметр длина 1-й ступени
Количество внутренних ступеней
* Для резцов с прямоугольной формой поперечного сечения державки указать диаметр державки равным 0. Для резцов с круглой формой поперечного сечения державки необходимо указывать В и Н равным 0.
** Указывать начальное положение резца при обработке относительно правого торца в мм. Если обработка начинается с торца то указать любое число например 001. Не допускается введение начального положения равного 0.
Наименьшее время обработки Т = 057 мин достигается при частоте вращения шпинделя n = 2000 обмин и подаче S = 026 ммоб. При этом скорость резания V= 20724 ммин.
Режимы резания определённые табличным и аналитическим методами указаны в табл. 7.
Скорость резания V ммин
Ограничение подачи по
Оптимальные режимы резания: S = 0134 ммоб; N = 2 000000 обмин; U = 207240 ммин; машинное время Т = 1119 мин; толщина пластинки твердого сплава не менее 1005 мм; Срz = 300000.
Оптимальные режимы резания: S = 0215 ммоб; N = 2 000000 обмин;
U = 207240 ммин; машинное время Т = 0698 мин; толщина пластинки твердого сплава не менее 1015 мм; Срz = 300000.
Глубина резания t мм
Частота вращения n обмин
Скорость резания V мc
Несовпадение параметров режима резания полученных аналитическим и табличным методами объясняется тем что при аналитическом расчете более полно учитываются все факторы процесса обработки.
3. Построение номограммы Pz = f(t S)
Зависимость усилия резания Рz от глубины резания t и подачи выражается уравнением
Pz =10 CPz×tXpz SYpz VZp2 KPz.
Значения всех входящих в уравнение параметров приведены в прилож. 14. Принимая S = 05 ммоб и задавая значения t определим величину усилия резания Pz (табл. 8).
Полученные значения усилия резания отложим на прямой пересекающей ось S в точке соответствующей S = 05 ммоб (см. рис. 3) через эти точки проводим прямые образующие с осью S угол
Построенная система является номограммой Pz = f(t S).
ОФОРМЛЕНИЕ КУРСОВОЙ РАБОТЫ
Курсовая работа оформляется в виде расчетно-пояснительной записки выполненной на листках белой нелинованной бумаги размером 297210 мм.
Текст записки выполняется на одной стороне листа в соответствии с [10].
Распечатки исходных данных и результатов расчета на компьютере подшиваются в записке в последовательности их получения. Номограмма строится на листе масштабно-координатной бумаги произвольного формата. Чертеж инструмента выполняется на листе ватмана формата А4 А3. Чертеж выполняется в соответствии с требованиями ЕСКД с указанием технических требований на изготовление. Пример выполнения чертежа резца показан на рис.4.
Титульный лист записки показан на с. 23.
Технические требования по ГОСТ 5688-88.
Филиал в г. Златоусте
ПОЯСНИТЕЛЬНАЯ ЗАПИСКА
«РЕЗАНИЕ МАТЕРИАЛОВ»
Общемашиностроительные нормативы режимов резания для технического нормирования работ на металлорежущих станках. — 2-е изд. — М.: Машиностроение 1974. — Ч. I. — 406 c.
Режимы резания металлов: Справочник — 3-е изд. перераб. и доп. Под ред. Ю.В. Барановского. — М.: Машиностроение 1972. — 405 с.
Справочник технолога-машиностроителя. — В 2 т. Под ред. А.Г. Косиловой Р.К. Мещерякова. — М.: Машиностроение 1985. — Т. 2. — 496 с.
Справочник инструментальщика Под общ. ред. И.А. Ординарцева. — Л.: Машиностроение 1987. — 846 с
Справочник технолога-машиностроителя. — В 2 т. Под ред. А.Г. Косиловой Р.К. Мещерякова. — М.: Машиностроение 1985. — Т. 1. — 656 с.
Краткий справочник металлиста. — 3-е изд. перераб. и доп. Под ред. П.Н. Орлова Е.А. Скороходова. — М.: Машиностроение 1987. — 960 с.
Справочник металлиста. — 3-е изд. перераб. Под ред. А.Н. Малова. — М.: Машиностроение 1976. — Т. 2. — 720 с.
Анурьев В.И. Справочник конструктора-машиностроителя. — 5-е изд. перераб. и доп. — М.: Машиностроение 1978. — Т. 1. — 728 с.
Допуски и посадки: Справочник. — 6-е изд. перераб. и доп. Под ред. В.Д. Мягкова. — Л.: Машиностроение 1982. — Т. 1. — 544 с.
Стандарт предприятия. Курсовое и дипломное проектирование. Общие требования к оформлению. СТП ЮУрГУ 04-2001 Составители: Н.В. Сырейщикова В.И. Гузеев И.В. Сурков Л.В. Винокурова. — Челябинск: Изд-во ЮУрГУ 2001. — 49 с.
Варианты контрольных заданий
Способ крепле-ния детади
Диаметр заготовки мм
Шероховатость обработанной поверхности
Обрабатываемый материал
Выбор марки инструментального материала
Рекомендуемые марки инструментальных материалов
углеродистой и легированной стали
трудно-обрабатываемых
цветных металлов и их сплавов
Черновое точение по корке при неравномерном сечении среза и прерывистом резании
Черновое точение по корке при неравномерном сечении среза и непрерывном резании
Получистовое и чистовое точение при прерывистом резании
Получистовое и чистовое точение при непрерывном резании
Форма передней поверхности резцов
Обозначение наименование
Эскиз передней поверхности
Для резцов из быстрорежущей стали
Обработка чугуна обработка стали при S02 ммоб
Обработка стали при S>02 ммоб
Обработка стали с обеспечением стружкозавивания
Для резцов с пластинами из твердых сплавов
Обработка стали с GB>800 Hмм2 при достаточной жесткости и виброустойчивости заготовки
Обработка серого и ковкого чугуна обработка стали с GB>800 Hмм2 при достаточной жесткости заготовки
Обработка стали с GB≤80 Hмм2 при t=1 5 мм S≥03 ммоб. Лунка для стружкозавивания: В=2 25 мм; R=4 6 мм; h = 01 015 мм
Геометрические параметры режущей части резцов
Углы в главной секущей плоскости и наклона режущей кромки
Материал резца* и форма пе-редней поверхности
Параметры режущей части
Сталь конструкционная углеродистая легированная: НВ340
Труднообрабатываемый материал
Значения угла j в зависимости от вида обработки
Чистовая обработка с малыми глубинами резания при высокой жёсткости СПИД
Точение строгание в условиях достаточной жёсткости СПИД
Точение строгание в условиях пониженной жёсткости СПИД
Обработка поверхностей в условиях малой жёсткости (большая длина заготовки)
Значение угла j1 в зависимости от условий обработки
Обточка напроход быстрорежущими резцами
Обточка напроход твердосплавными резцами
Расточка подрезка быстрорежущими резцами
Расточка подрезка твердосплавными резцами
Прорезка отрезка немерных заготовок
Прорезка мерных пазов
* БС — быстрорежущая сталь; ТС — твердые сплавы.
Подачи в зависимости от шероховатости поверхности
Подачи при черновой обработке
Размер державки резца мм
сталь углеродистая и легированная
Подача при глубине резания
Подачи при чистовой обработке
Диапазон скоростей резания мс
Шерохова-тость по-верхности
Радиус при вершине резца r мм
Сталь углеродистая и легированная
Чугун и алюминиевые сплавы
Весь диапазон скоростей
Подачи допускаемые прочностью державки резца
Глубина резания t мм до
Резцы с пластинками твердого сплава
Резцы из быстро-режущей стали
Резцы с державкой (В × Н)
Подача допускаемая прочностью державки S ммоб
Поправочные коэффициенты на подачу в зависимости от длины вылета резца lp выраженную через его высоту Н
Длина вылета резца lp
Примечание. При одновременной работе несколькими резцами (деление припуска по глубине резания) допускаемые подачи определять по максимальной глубине резания приходящейся на каждый резец.
Подачи допустимые прочностью пластинки твердого сплава
Главный угол в плане φ
Толщина пластинки твердого сплава мм
Примечание. При работе с ударами табличные подачи умножать на поправочный коэффициент 08.
База данных о состоянии обрабатываемой поверхности
Состояние поверхности
Отливка с нормальной коркой
Отливка с загрязненной коркой
Медные и алюминиевые сплавы
База данных вида закрепления заготовки
В патроне с задним центром
Подачи допустимые жесткостью детали. Обработка предварительная в патроне
Поправочный коэффициент на подачу в зависимости от
главного угла в плане j
Продолжение прилож. 10
Подачи допустимые жесткостью детали при обработке в патроне
Предел прочности s Нмм2
Поправочный коэффициент в зависимости от
главного угла в плане
Окончание прилож. 10
Подачи допустимые жесткостью детали при обработке в центрах
Глубина резания t мм
Поправочный коэффициент в зависимости от длины детали
главного угла в плане
Главный угол в плане j°
Скорость резания V=Vm K1 K2
Быстро-режущая сталь
Табличная скорость резания Vm мc при угле в плане j°
Продолжение прилож. 11
Коэффициент К1 для определения скорости резания
силумин и литейные сплавы
Окончание прилож. 11
Коэффициент К2 для определения скорости резания
К2 при стойкости Т в минутах резания
Мощность потребная на резание
Сталь. Резцы с пластинами твердого сплава
Мощность резания N кВт
Поправочный коэффициент
Продолжение прилож. 12
Чугун серый и ковкий. Резцы с пластинами твердого сплава
Скорость резания V мc до
Окончание прилож. 12
Алюминиевые сплавы. Резцы из быстрорежущей стали
Скорость резания V мc
Усилие подачи. Сталь. Резцы с пластинами твердого сплава
Предел прочности sВ Нмм2
Скорость резания V мс
Поправочные коэффициенты на силу подачи в зависимости от
угла наклона главной режущей кромки
Расчетные зависимости для определения сил резания
Коэффициенты и показатели степеней в формулах для расчета силы РZ
Сталь конструкционная и стальное литье sв=750 Нмм2
Поправочный коэффициент КМР при обработке стали и чугуна
Сталь конструкционная и
Показатели степени UP в формулах
Твердый сплав при точении стали
Быстрорежущая сталь при точении стали
Твердый сплав при точении чугуна
Быстрорежущая сталь при точении чугуна
Поправочный коэффициент КМР для алюминиевых сплавов при обработке резцами из быстрорежущей стали
Дюралюмин при sв Нмм2
Окончание прилож. 14
Поправочные коэффициенты для сил резания
Параметры влияющие на коэффициент
Геометрия режущей части инструмента и его износ
Величина в зависимости от материала инструмента
Радиус при вершине резца в плане r мм
Износ по задней поверхности hз мм
Обрабатываемый материал (стали)
Хромомарганцовистые (ХГ)
Хромокремнистые (ХС)
Хромомолибденовые (ХМ)
Хромокремнемарганцовистые (ХГС)
Хромоникелемолибденовые (ХНМ)
Хромоникелевольфрамовые (ХНВ)
Расчетные зависимости для определения скорости резания
Материал режущей части резца
Характеристика подачи S
Коэффициент и показатели степени
Сталь конструкционная углеродистая sв=750 Нмм2
Алюминиевые сплавы sв=100 200 Нмм2 дюралюминий sв=300 400 Нмм2
Поправочный коэффициент КUV учитывающий материал резца
Значение коэффициента КUv в зависимости от марки инструментального материала
Сталь конструкционная
Чугун серый и ковкий
Коэффициент КnV учитывающий состояние поверхности
Литье стальное и чугунное
с загрязненной коркой
Продолжение прилож. 15
Поправочные коэффициенты для расчета скорости резания
Коэффициенты учитывающие влияние параметров резца
Радиус при вершине r мм
Сечение державки резца
С отрицательной фаской
Плоская отрицательная
Плоская или радиусная без фаски
Коэффициент КOV учитывающий влияние вида обработки
Отношение обрабатываемого диаметра к диаметру заготовки
Поправочный коэффициент КMV
учитывающий свойства обрабатываемого материала
Сталь конструкционная углеродистая и легированная
Окончание прилож. 15
Значение коэффициента СМ и показатели степени nV
Показатель степени nV
углеродистая (С06%) никелевая
углеродистая (С>06%) хромистая марганцовистая
хромоникельмолибденовая
хромомарганцовистая хромокремнистая хромокремнемарганцовистая
Чугун: серый и ковкий
Поправочный коэффициент КMV для алюминиевых сплавов
sВ=40 50 Нмм2 НВ>100
База данных материала режущего инструмента
Углеродистая инструментальная сталь ГОСТ 14235-74
Легированная инструментальная сталь ГОСТ 5950-73
Однокарбидные твёрдые сплавы ГОСТ 3882-74
Быстрорежущая инструментальная сталь ГОСТ 19265-73
- и 3- карбидные твёрдые сплавы ГОСТ 38820-74
Окончание прилож. 16
Синтетические сверхтвёрдые поликристаллы
База данных материала детали
Стали обыкновенного качества
Сталь рессорно-пружинная
Сталь легированная (марганцовистая)
Высоколегирован-ные жаропроч-ные жаростойкие коррозионные стали и сплавы
Сталь коррозион-ная прочная жа-ростойкая
Шарикоподшип-никовая
Сталь углеродистая качественная
Сталь конструкционная качественная (хромоникелевая)
Окончание прилож. 17
Сплавы на основе титана
База данных оборудования
База данных вида обработки
Наружное продольное точение
Наружное поперечное точение
Внутреннее продольное точение (расточка)
Внутреннее поперечное точение
Внутреннее прорезание
Инструкция по работе на ПК
Запустить команду REGREZ.EXE. Появится заставка с краткой инструкцией. Выполните команду «Нажмите любую клавишу».
В появившемся окне «Данные обработки» вводим соответствующие данные либо из предлагаемых вариантов либо численные значения. После каждого ввода не забывайте нажать клавишу «Enter». В меню предлагаемых вариантов перемещение осуществляется клавишами «» и «». Внизу в окне постоянно имеются подсказки.
После ввода данных появляется меню «Исправить данные — Начать расчет». Для просмотра и исправления данных выбираем «Исправить данные». Если исходные данные набраны правильно то приступаем к расчету — «Начать расчет».
После расчета появляется меню «Просмотреть отчет — Распечатать отчет — Данные».
Для просмотра расчета выбираем «Просмотреть отчет».
Для продолжения работы выбираем — «Дальше».
Появляется меню «Выполнить новый расчет — Изменить данные расчета — Закончить работу».
Для начала нового расчета выбираем «Выполнить новый расчет». Если после просмотра отчета появилась необходимость изменить исходные данные то выбираем команду «Изменить данные расчета».
Окончание работы и выход из программы — команда «Закончить работу».
Введение . . . . . . . . . . . . . . . . . . . . . . . . . . . . . . . . . . . . . . . . . . . . . . . . . . . . . . . .3
Табличный метод определения режима резания . . . . . . . . . . . . . . . . . . . . . . . .3
Аналитический метод расчета режима резания . . . . . . . . . . . . . . . . . . . . . . . . .7
Расчет режимов резания по номограммам . . . . . . . . . . . . . . . . . . . . . . . . . . . . .12
Пример расчета . . . . . . . . . . . . . . . . . . . . . . . . . . . . . . . . . . . . . . . . . . . . . . . . . . .14
Оформление курсовой работы . . . . . . . . . . . . . . . . . . . . . . . . . . . . . . . . . . . . . . .21
Литература . . . . . . . . . . . . . . . . . . . . . . . . . . . . . . . . . . . . . . . . . . . . . . . . . . . . . . .24
Приложения . . . . . . . . . . . . . . . . . . . . . . . . . . . . . . . . . . . . . . . . . . . . . . . . . . . . . .25
Оглавление . . . . . . . . . . . . . . . . . . . . . . . . . . . . . . . . . . . . . . . . . . . . . . . . . . . . . . .54
расчет-реж-рез.doc
Себестоимость обработки детали зависит от многих факторов в число которых входят и режимы резания. Назначение элементов режима резания обеспечивающих минимальную себестоимость обработки — задача сложная решение которой в большинстве случаев возможно только после полного анализа конкретной операции а иногда и целого ряда связанных с ней процессов.
Одним из этапов решения этой задачи является определение элементов режима резания допускаемых возможностями оборудования и инструмента. Назначение величин элементов режима резания как правило выполняют в следующей последовательности: определяют глубину резания затем выбирают подачу и стойкость инструмента и далее определяют скорость резания соответствующую принятым величинам глубины резания подачи и стойкости. После согласования величин подачи и скорости резания с возможностями кинематических цепей станка определяют основное (машинное) время обработки.
В практической деятельности технолог назначая режим резания пользуется одним из методов расчета — аналитическим табличным или графическим. Широкое применение персональных компьютеров позволяет назначить режим резания более точно так как аналитические зависимости связывающие элементы режима резания создают возможность более полного учета и анализа факторов влияющих на процесс обработки.
В предлагаемом студентам пособии описаны методы расчета параметров режима резания в последовательности соответствующей порядку проведения расчета. Аналитический метод расчета изложен применительно к выполнению его на современных персональных компьютерах.
ТАБЛИЧНЫЙ МЕТОД ОПРЕДЕЛЕНИЯ РЕЖИМА РЕЗАНИЯ
Определение режима резания по специальным таблицам [1 2] производится в следующей последовательности.
1. Назначение параметра режущего инструмента
Выбор материала режущей части её геометрических параметров размеров державки и типа резца производятся в следующей последовательности [3 4].
Тип резца назначают в зависимости от вида технологического перехода. При этом необходимо обеспечить условия наиболее удобной обработки поверхности детали.
Марка материала режущей части и форма передней поверхности резца назначаются в зависимости от вида и условий обработки обрабатываемого материала и его механических характеристик.
Геометрические параметры режущего клина резца определяются исходя из характеристик обрабатываемого материала и условий обработки.
2. Выбор глубины резания
В процессе обработки с поверхности заготовки удаляется слой металла называемый припуском. Наименьшая величина припуска необходимого для получения детали с заданными параметрами обработанной поверхности определяется расчётом.
Припуск с заготовки удаляется за один или несколько проходов обеспечивающих постепенное уточнение обработанной поверхности например черновой получистовой и чистовой переходы. В свою очередь на каждом технологическом переходе припуск может быть удалён за один или несколько проходов.
Для сокращения времени обработки припуск желательно удалять за один проход.
Глубина резания на каждом проходе
t = 05×(Di – Di+1) (1)
где Di Di+1 — диаметры до и после обработки на выполняемом проходе.
Обычно на черновых проходах (шероховатость обработанной поверхности Rz80 320 с точностью менее 12 квалитета) глубина резания ограничивается мощностью станка прочностью инструмента жёсткостью детали и другими факторами.
При получистовых проходах (Rz 20 40 точность 8 12 квалитета) глубина резания не более 2 мм.
При чистовой обработке (Rz 125 25 точность выше 8 квалитета) глубина резания не более 01 04 мм.
3. Определение величины подачи
Подачей при точении называется перемещение резца вдоль обработанной поверхности за один оборот детали.
Для снижения времени обработки целесообразно максимальное увеличение подачи но возрастающие при этом нагрузки и ряд других факторов ограничивают её величину.
При черновой обработке подача ограничивается силами действующими при резании. Величина подачи назначается в зависимости от глубины резания размеров сечения державки резца материала и диаметра детали.
При чистовой обработке величина подачи выбирается в зависимости от шероховатости получаемой поверхности обрабатываемого материала принятых геометрических параметров инструмента и предлагаемой скорости резания.
Выработанное значение подачи как при черновой так и чистовой обработке корректируется умножением на коэффициенты учитывающие влияние обрабатываемого материала и условий обработки.
В некоторых случаях например когда производится обработка деталей с большим вылетом инструмента большим сечением срезаемого слоя или обрабатываются детали большой длины полученные значения подачи дополнительно проверяются по условиям учитывающим специфику обработки.
Обычно резец устанавливается с вылетом lp15 Н где Н — высота державки резца. При установке резца с большим вылетом производится проверка подачи по прочности державки резца. При этом величина подачи определяется в зависимости от предела прочности или твёрдости обрабатываемого материала глубины резания и сечения державки резца. Влияние вылета резца учитывается поправочным коэффициентом.
При срезании стружки большого сечения резцом оснащённым твердосплавной пластиной производится проверка подачи по прочности пластинки. Величина подачи при этом выбирается в зависимости от характеристик обрабатываемого материала главного угла резца в плане глубины резания и толщины пластинки твёрдого сплава.
При обработке маложёстких деталей подача проверяется: при черновой обработке — по жёсткости системы “станок — приспособление — инструмент — деталь” или “СПИД”; при чистовой обработке — по допустимому прогибу детали. При проверке учитывается влияние диаметра и длины детали главного угла резца в плане материала заготовки и его характеристик глубины резания способа закрепления детали на станке и другие параметры.
В качестве технологической принимается подача удовлетворяющая всем рассмотренным ограничениям.
4. Определение скорости резания
Скоростью резания при токарной обработке называется линейная скорость точек обрабатываемой поверхности.
Скорость резания выбирается в зависимости от обрабатываемого и инструментального материала выбранных значений глубины резания подачи и главного угла резца в плане.
Найденное значение скорости корректируется умножением на коэффициенты учитывающие влияние материала детали и инструмента периода его стойкости и состояния поверхности заготовки.
По найденному значению скорости резания определяют соответствующую ей частоту вращения шпинделя станка:
5. Определение мощности станка
Мощность потребляемая при токарной обработке зависит от материала заготовки и его механических характеристик материала и геометрических параметров резца режимов обработки.
Мощность привода станка для обеспечения его нормальной работы должна удовлетворять условию:
где h — КПД станка h = 07 08.
6. Определение усилия подачи
Для осуществления процесса резания механизм подач станка должен развивать усилие Px зависящее от режима резания геометрии и материала режущей части инструмента обрабатываемого материала. Наибольшее усилие допускаемое прочностью механизма подач станка Q должно удовлетворять условию
7. Выбор оборудования
Для обработки детали выбирается станок с технологическими характеристиками обеспечивающими установленные выше режимы резания. Исходными данными для выбора модели станка являются: диаметр и длина детали требуемые частота вращения шпинделя станка и величина подачи мощность усилие подачи а также размеры резцедержателя. При выборе модели станка предпочтение отдаётся той мощность привода главного движения которой используется наиболее полно. При отсутствии оборудования удовлетворяющего всем предъявляемым требованиям выбирают модель станка с наиболее близкими к расчётным характеристиками.
Поскольку определённые выше частота вращения шпинделя и подача могут не соответствовать значениям этих параметров принятой модели станка величины их корректируются по станку. При этом допускается увеличение частоты вращения шпинделя до 5% а подачи — до 10% по сравнению с выбранными выше.
8. Определение основного технологического времени
Основное или технологическое время одного прохода
Тм = (L + lв + lп) nS мин (5)
где L — длина обрабатываемой поверхности детали мм;
lп — перебег резца lп = 1 5 мм.
Величина перебега зависит от глубины резания и главного угла в плане.
Найденные параметры режущего инструмента оборудования режимов резания и времени обработки заносятся в табл. 1 3 (см. пример расчёта на с. 14).
АНАЛИТИЧЕСКИЙ МЕТОД РАСЧЁТА РЕЖИМА РЕЗАНИЯ
Аналитический метод расчёта заключается в определении параметров режима резания по эмпирическим зависимостям.
Аналитический метод позволяет наиболее точно определить параметры режима обработки но большой объём выполняемых при этом вычислений делает его довольно трудоёмким. Использование ПК позволяет значительно сократить время вычислений и оптимизировать режимы резания.
Расчёт режима обработки при аналитическом методе производят в три этапа:
)определяют параметры режущего инструмента оборудования и глубину резания;
)вычисляют величины максимально допустимых подач и основное технологическое время;
)определяют наивыгоднейший режим резания.
1. Выбор параметров инструмента
Параметры режущего инструмента выбираются по таблицам приведённым в справочной и нормативной литературе. Последовательность выбора параметров рассмотрена ранее (см. п. 1.1).
Глубина резания при аналитическом методе расчёта выбирается также как и при табличном (см. п. 1.2).
3. Выбор оборудования
Если оборудование на котором будет производиться обработка детали не задано то модель станка выбирают исходя из габаритов обрабатываемой детали параметров инструмента предполагаемой частоты вращения шпинделя величины подачи и мощности затрачиваемой на процесс резания [5] из перечисленных в прилож. 18.
4. Определение величины подачи
Увеличение подачи позволяет сократить время на обработку детали то есть увеличить производительность процесса но имеется ряд ограничений определяющих её максимальную допустимую величину.
При токарной обработке величина подачи как правило ограничивается:
)прочностью державки резца;
)шероховатостью обработанной поверхности;
)точностью обработки;
Ограничение подачи по мощности станка
где — коэффициент резания (прилож. 14);
— показатели степени при глубине резания и подаче (см. прилож. 14);
Nz — мощность затрачиваемая на резания кВт;
t — глубина резания мм;
— поправочный коэффициент
КPz = КМр × Кjр × Кgр × Кrp × Knp × Кгр ×
KMp — коэффициент учитывающий влияние обрабатываемого материала;
Kjp — коэффициент учитывающий влияние главного угла в плане;
Kgp — коэффициент учитывающий влияние переднего угла;
Krp — коэффициент учитывающий влияние радиуса при вершине резца;
Knp — коэффициент учитывающий влияние износа резца;
Kгр — коэффициент учитывающий влияние группы обрабатываемости.
Значения всех коэффициентов даны в прилож. 14.
Ограничение подачи по прочности державки резца
где В — ширина державки резца мм;
Н — высота державки резца мм;
[s]и — допустимое напряжение изгиба Нмм2;
lp — вылет резца мм.
Подача ограниченная шероховатостью поверхности
где R — радиус при вершине резца в плане; Rz — шероховатость поверхности;
где j1 — вспомогательный угол в плане; j — главный угол в плане.
Вычисление происходит следующим образом: в качестве начального (стартового) значения подачи используется минимальная подача определённая ранее по условиям мощности станка прочности державки резца точности обработки и стойкости резца.
В случае невыполнения условия значение подачи уменьшается на одну позицию и вновь происходит проверка. Подача удовлетворяющая условию ограничения по шероховатости поверхности выводится в печать результатов.
Подача ограниченная точностью обработки
где a — коэффициент выражающий допустимую долю погрешности обработки зависящей от режимов резания в суммарной погрешности обработки (05);
d — величина допуска исполняемого размера;
CPz — коэффициент в формуле расчёта силы резания (см. прилож. 14);
t — глубина резания;
XPz — показатель степени при глубине резания (см. прилож. 14);
gст — жёсткость станка;
К1 К2 — коэффициенты влияния деформаций элементов технологической системы на точность обработки;
Е — модуль упругости Нмм2;
l — длина детали мм.
Жёсткость детали находится по формуле
где J — момент инерции сечения заготовки; Кж — коэффициент жёсткости
Dпр — приведённый диаметр ступенчатого вала мм.
Для деталей с утолщением посередине
Для деталей с односторонним утолщением
Коэффициент жёсткости для закрепления детали:
— в патроне консольно
где Хр — расстояние от правого торца детали до резца в мм;
— в патроне с передним центром
—в центрах с люнетом посередине
Жёсткость инструмента находится по формуле
Подача ограниченная стойкостью резца
Скорость резания допускаемая инструментальным материалом при заданной стойкости инструмента определяется эмпирической зависимостью:
где СV — коэффициент стойкости;
КV — поправочный коэффициент;
Т — стойкость инструмента при токарной обработке Т = 60 мин;
KV = KмV × KuV × KrV × KqV × KjV × KoV × KфV × KпV.
Здесь KмV KuV KrV KqV KjV KoV KфV KпV — коэффициенты учитывающие влияние обрабатываемого материала материала инструмента радиуса при вершине резца размеров сечения державки резца главного угла в плане вида обработки формы передней поверхности состояния поверхности.
Подставляя (2) в (20) и решая относительно S получаем
Система неравенств (6) (7) (8) (9) (21) ограничивающих значения допустимых подач и ограничения по кинематике станка n³nm nnma SSmax представляет математическую модель процесса обработки.
Геометрическая интерпретация математической модели представлена на рис.2.
Область возможных сочетаний частот вращения шпинделя и подач станка представлена заштрихованным многоугольником. Каждая из точек этого многоугольника обеспечивает получение детали с заданными параметрами то есть заштрихованный многоугольник является многоугольником решений.
Для достижения минимального времени обработки детали из множества точек многоугольника решений нужно найти такую точку то есть такое сочетание частот вращения шпинделя и подач при котором производительность процесса будет максимальной.
Для станков с дискретным регулированием частоты вращения шпинделя и подачи множество из возможных сочетаний является конечным. Это множество можно представить в виде ряда узловых точек лежащих в области ограниченной кинематическими параметрами станка. При этом часть узловых точек будет расположена в многоугольнике решений.
Очевидно что наибольшая производительность процесса обработки при данной частоте вращения шпинделя n1 будет достигнута при величине подачи S1 образующей узловую точку ближайшую к верхней границе многоугольника решений.
Задавая частоту вращения шпинделя определим величины подач максимально допускаемых по ограничениям. Наименьшая из этих подач будет являться максимально допустимой Smax доп. Найденное значение максимально допустимой подачи скорректируем по имеющейся ближайшей подаче станка причём Sст не должна превосходить Smax доп более чем на 10%. По заданному числу оборотов шпинделя подаче станка и длине обработки определим по зависимости (5) Тмаш.
Максимальная производительность процесса будет достигаться при таких значениях частоты вращения шпинделя и подаче при которых время обработки будет минимальным.
При наличии нескольких значений частот вращения шпинделя обеспечивающих минимальное время обработки принимают наименьшую из них так как при этом обеспечивается большая стойкость режущего инструмента.
О возможных направлениях совершенствования процесса обработки можно судить по величине подач допускаемых по ограничениям. При необходимости увеличения производительности процесса обработки производят корректировку параметров влияющих на соответствующие ограничения.
РАСЧЁТ РЕЖИМОВ РЕЗАНИЯ ПО НОМОГРАММАМ
Табличный и аналитический методы расчёта позволяют определить режимы обработки с учётом многих особенностей процесса но эти расчёты довольно трудоёмки что ограничивает их применение в единичном и мелкосерийном производстве. Определение режимов в таких случаях целесообразно производить по номограммам графически отображающим закономерности процесса.
Номограммы строятся для определённого цеха участка группы станков или отдельного станка.
1. Построение номограмм
Закономерности процесса резания аналитически отображаются преимущественно степенными зависимостями. Для упрощения разработки номограмм их построение производится в двойной логарифмической системе координат.
Порядок построения номограмм рассмотрим на примере зависимости
Аналитически эта зависимость выражается уравнением
Pz =10 CPztXpz SYpz VZp2 KPz. (22)
При постоянной глубине резания это уравнение преобразуется к виду
где C = 10 CPz×tXp×Kpz.
Логарифмируя выражение (23) получаем
lg Pz = lg C+Yp×lg S. (24)
Полученное уравнение представляет уравнение прямой линии тангенс угла наклона которой равен Yp.
Последовательно изменяя глубину резания от tmin до tmax при постоянном значении подачи S получаем ряд точек лежащих на прямой параллельной оси ординат (рис. 3). Через эти точки проводят линии под углом
на оси откладываются значения подач а на оси ординат — значения Pz.
Эта система графиков является номограммой зависимости Pz = f (t S).
Аналогично производится построение номограмм и других зависимостей.
2. Определение параметров по номограмме
Номограмма позволяет определить один из параметров зависимости по двум известным. Так номограмма представленная на рис. 3 позволяет определять: величину силы Pz по известным значениям подачи S и глубины резания t; S по Pz и t; t по известным Pz и S. Рассмотрим как определяется неизвестный параметр. Допустим что известна сила Pz1 и глубина резания t1 нужно определить соответствующую им величину подачи S1. Через точку соответствующую значению Pz проведём прямую параллельную оси абсцисс. Эта прямая пересекается с лучом соответствующим значению t1 в точке 1 проекция которой на ось абсцисс и есть определяемое значение S1.
Вид обработки — обточка по диаметру.
Материал детали — сталь 40Х.
Диаметр детали — 30 h11 мм.
Длина обработки — 300 мм.
Шероховатость поверхности — Rz20.
Диаметр заготовки — 40 мм.
Длина заготовки — 360 мм.
Способ закрепления заготовки — в центрах.
Определить табличным и аналитическим методами режимы резания построить номограмму Pz=f (t S) выполнить чертёж резца.
По справочной литературе [6 9] определим предел прочности при растяжении материала детали sв=980 Нмм2 (980 МПа) и допуск на изготовление d=016мм.
1. Табличный метод расчёта
Для достижения заданной точности и шероховатости поверхности детали её обработку производим в два прохода: первый проход — предварительный черновой второй — окончательный получистовой.
Определим параметры инструмента режимы обработки и выберем оборудование для выполнения второго прохода.
Для окончательной обработки детали изготовляемой из легированной стали выбираем твердосплавную пластинку марки Т15К6 (прилож. 2).
Выбираем (прилож. 3) форму передней поверхности резца — радиусную с фаской.
По прилож. 4 определяем геометрические параметры режущей части резца:
f = 06 мм; gf = –5; g = 15°; a = 10°; j = 30°; j1 = 15°; r = 10.
По ГОСТ 6743 принимаем резец правый прямой проходной с сечением державки ВН = 2020 мм2 длиной L = 100 мм оснащённый твердосплавной пластиной толщиной С = 55 мм.
Припуск на обработку детали h =5 мм удаляется за два прохода. Глубина резания t на втором проходе должна быть не более 2 мм при этом на черновом проходе должна удаляться большая часть припуска. В связи с этими требованиями назначаем глубину резания на первом проходе равной 35 мм на втором — t=15мм.
Величину подачи обеспечивающей получение заданной шероховатости определим по прилож. 5 предполагая при этом что скорость резания при оконча-тельной обработке будет больше 08 мс.
Подача допускаемая шероховатостью поверхности
Принимаем Sшп = 035 ммоб.
Полученное значение подачи проверим по прочности резца и твердосплавной пластинки а также по допускаемому прогибу детали.
Величину подачи допускаемой прочностью державки резца определим по прилож. 6 приняв при этом вылет резца lp = 15 H = 30 мм:
Подачу допускаемую прочностью пластинки твёрдого сплава определим по прилож. 7:
Подача допускаемая по прогибу детали (прилож. 10):
Sжд = Sт × KL × Kj × KS
где Sm — табличное значение подачи Sт = 16 мм;
KL Kj KS — коэффициенты учитывающие влияние длины детали угла j способа закрепления детали KL = 1 Kj = 072 KS = 1.
Подача выбранная из условия получения заданной шероховатости поверхности детали удовлетворяет и другим рассмотренным ограничениям и может быть принята за технологическую.
Скорость резания V=Vт×К1×К2
где Vт — табличное значение скорости Vт = 208 мс (прилож. 11);
К1 — коэффициент учитывающий влияние обрабатываемого материала К1=09;
К2 — коэффициент учитывающий влияние материала инструмента К2=155;
V = 208×09×155 = 29 мс.
Эта скорость резания достигается при частоте вращения шпинделя
Мощность затрачиваемая на процесс резания определим по прилож. 10: N = 29 кВт.
Мощность привода станка при к.п.д. h = 08
Nст = 2908 = 36 кВт.
Усилие подачи (прилож. 13)
где Qт — табличное значение усилия подачи Qт = 450 Н;
Кg — коэффициент учитывающий влияние угла g Кg = 1;
Для обработки детали выбираем станок модели 1616 имеющий следующие технические характеристики:
высота центров — 160 мм;
расстояние между центрами — 750 мм;
высота от опорной поверхности резцедержателя до линии центров — 20 мм;
мощность привода — 45 кВт;
наибольшее усилие подачи — 3050 Н;
диапазон частот вращения шпинделя — 44 1980 обмин;
диапазон подач — 006 107 ммоб.
Определённые ранее значения подачи и частоты вращения корректируем по имеющимся в станке.
Принимаем S = 036 ммоб n = 1380 обмин.
Тогда скорость резания
Основное или машинное время необходимое для выполнения второго прохода
где L — длина обрабатываемой поверхности детали L = 300 мм;
lп — длина набега принимаем lп = 3 мм.
Определённые параметры инструмента оборудования режим и время обработки заносим в табл. 1–3.
Геометрические параметры режущей части
Резец прямой проходной
Расстояние между центрами
Высота от опорной поверхности до линии центров
Мощность привода кВт
Допустимое усилие подачи Н
Диапазон частот вращения шпинделя обмин
Режим и время обработки
Частота вращения шпинделя обмм
2. Аналитический метод расчета
Для проведения расчётов на ПК определяются параметры входящие в блок исходных данных (табл. 4).
Значения параметров процесса обработки занесены в 4 и 5 колонки табл. 4. Расчеты на ПК следует выполнять согласно инструкции (приложение 20). Результаты расчёта представлены в табл. 5.
Анализируя полученные результаты видим что наибольшая производительность обработки достигается при частоте вращения шпинделя n = 2000 обмин и подаче S = 012 ммоб при этом величина подачи ограничивается точностью обработки.
Анализируя влияние параметров входящих в это ограничение приходим к выводу что величину подачи наиболее просто можно увеличить изменив метод закрепления детали.
При закреплении детали в центрах с люнетом жёсткость системы СПИД увеличивается следовательно увеличивается и подача допускаемая по этому ограничению.
Одновременно с этим есть ещё возможность дополнительно увеличить величину подачи. Это можно сделать увеличив главный угол в плане до 45°. Увеличение угла j ведёт к уменьшению длины активной части режущей кромки резца а следовательно к уменьшению радиальной составляющей сил резания. Уменьшение сил резания уменьшит изгиб заготовки что позволяет дополнительно увеличить величину подачи. Результаты повторного расчёта представлены в табл. 6.
Исходные данные для расчёта на ЭВМ
Вид обработки (прилож. 19)
Стойкость инструмента
Материал инструмента
Радиус вершины резца
Главный угол в плане
Вспомогательный угол в плане
Ширина и высота сечения державки
Диаметр державки резца D*
Состояние обрабатываемой поверхности (прилож.8)
Диаметр заготовки под обработку
Вид закрепления заготовки
начальное положение резца**
Конечное положение резца
Количество наружн. ступеней обработки
Диаметр длина 1-й ступени
Количество внутренних ступеней
* Для резцов с прямоугольной формой поперечного сечения державки указать диаметр державки равным 0. Для резцов с круглой формой поперечного сечения державки необходимо указывать В и Н равным 0.
** Указывать начальное положение резца при обработке относительно правого торца в мм. Если обработка начинается с торца то указать любое число например 001. Не допускается введение начального положения равного 0.
Наименьшее время обработки Т = 057 мин достигается при частоте вращения шпинделя n = 2000 обмин и подаче S = 026 ммоб. При этом скорость резания V= 20724 ммин.
Режимы резания определённые табличным и аналитическим методами указаны в табл. 7.
Скорость резания V ммин
Ограничение подачи по
Оптимальные режимы резания: S = 0134 ммоб; N = 2 000000 обмин; U = 207240 ммин; машинное время Т = 1119 мин; толщина пластинки твердого сплава не менее 1005 мм; Срz = 300000.
Оптимальные режимы резания: S = 0215 ммоб; N = 2 000000 обмин;
U = 207240 ммин; машинное время Т = 0698 мин; толщина пластинки твердого сплава не менее 1015 мм; Срz = 300000.
Глубина резания t мм
Частота вращения n обмин
Скорость резания V мc
Несовпадение параметров режима резания полученных аналитическим и табличным методами объясняется тем что при аналитическом расчете более полно учитываются все факторы процесса обработки.
3. Построение номограммы Pz = f(t S)
Зависимость усилия резания Рz от глубины резания t и подачи выражается уравнением
Pz =10 CPz×tXpz SYpz VZp2 KPz.
Значения всех входящих в уравнение параметров приведены в прилож. 14. Принимая S = 05 ммоб и задавая значения t определим величину усилия резания Pz (табл. 8).
Полученные значения усилия резания отложим на прямой пересекающей ось S в точке соответствующей S = 05 ммоб (см. рис. 3) через эти точки проводим прямые образующие с осью S угол
Построенная система является номограммой Pz = f(t S).
ОФОРМЛЕНИЕ КУРСОВОЙ РАБОТЫ
Курсовая работа оформляется в виде расчетно-пояснительной записки выполненной на листках белой нелинованной бумаги размером 297210 мм.
Текст записки выполняется на одной стороне листа в соответствии с [10].
Распечатки исходных данных и результатов расчета на компьютере подшиваются в записке в последовательности их получения. Номограмма строится на листе масштабно-координатной бумаги произвольного формата. Чертеж инструмента выполняется на листе ватмана формата А4 А3. Чертеж выполняется в соответствии с требованиями ЕСКД с указанием технических требований на изготовление. Пример выполнения чертежа резца показан на рис.4.
Титульный лист записки показан на с. 23.
Технические требования по ГОСТ 5688-88.
Министерство образования Российской Федерации
Южно-Уральский государственный университет
Филиал в г. Златоусте
Кафедра «Технология машиностроения станки и инструмент»
ПОЯСНИТЕЛЬНАЯ ЗАПИСКА
«РЕЗАНИЕ МАТЕРИАЛОВ»
Общемашиностроительные нормативы режимов резания для технического нормирования работ на металлорежущих станках. — 2-е изд. — М.: Машиностроение 1974. — Ч. I. — 406 c.
Режимы резания металлов: Справочник — 3-е изд. перераб. и доп. Под ред. Ю.В. Барановского. — М.: Машиностроение 1972. — 405 с.
Справочник технолога-машиностроителя. — В 2 т. Под ред. А.Г. Косиловой Р.К. Мещерякова. — М.: Машиностроение 1985. — Т. 2. — 496 с.
Справочник инструментальщика Под общ. ред. И.А. Ординарцева. — Л.: Машиностроение 1987. — 846 с
Справочник технолога-машиностроителя. — В 2 т. Под ред. А.Г. Косиловой Р.К. Мещерякова. — М.: Машиностроение 1985. — Т. 1. — 656 с.
Краткий справочник металлиста. — 3-е изд. перераб. и доп. Под ред. П.Н. Орлова Е.А. Скороходова. — М.: Машиностроение 1987. — 960 с.
Справочник металлиста. — 3-е изд. перераб. Под ред. А.Н. Малова. — М.: Машиностроение 1976. — Т. 2. — 720 с.
Анурьев В.И. Справочник конструктора-машиностроителя. — 5-е изд. перераб. и доп. — М.: Машиностроение 1978. — Т. 1. — 728 с.
Допуски и посадки: Справочник. — 6-е изд. перераб. и доп. Под ред. В.Д. Мягкова. — Л.: Машиностроение 1982. — Т. 1. — 544 с.
Стандарт предприятия. Курсовое и дипломное проектирование. Общие требования к оформлению. СТП ЮУрГУ 04-2001 Составители: Н.В. Сырейщикова В.И. Гузеев И.В. Сурков Л.В. Винокурова. — Челябинск: Изд-во ЮУрГУ 2001. — 49 с.
Варианты контрольных заданий
Способ крепле-ния детади
Диаметр заготовки мм
Шероховатость обработанной поверхности
Обрабатываемый материал
Выбор марки инструментального материала
Рекомендуемые марки инструментальных материалов
углеродистой и легированной стали
трудно-обрабатываемых
цветных металлов и их сплавов
Черновое точение по корке при неравномерном сечении среза и прерывистом резании
Черновое точение по корке при неравномерном сечении среза и непрерывном резании
Получистовое и чистовое точение при прерывистом резании
Получистовое и чистовое точение при непрерывном резании
Форма передней поверхности резцов
Обозначение наименование
Эскиз передней поверхности
Для резцов из быстрорежущей стали
Обработка чугуна обработка стали при S02 ммоб
Обработка стали при S>02 ммоб
Обработка стали с обеспечением стружкозавивания
Для резцов с пластинами из твердых сплавов
Обработка стали с GB>800 Hмм2 при достаточной жесткости и виброустойчивости заготовки
Обработка серого и ковкого чугуна обработка стали с GB>800 Hмм2 при достаточной жесткости заготовки
Обработка стали с GB≤80 Hмм2 при t=1 5 мм S≥03 ммоб. Лунка для стружкозавивания: В=2 25 мм; R=4 6 мм; h = 01 015 мм
Геометрические параметры режущей части резцов
Углы в главной секущей плоскости и наклона режущей кромки
Материал резца* и форма пе-редней поверхности
Параметры режущей части
Сталь конструкционная углеродистая легированная: НВ340
Труднообрабатываемый материал
Значения угла j в зависимости от вида обработки
Чистовая обработка с малыми глубинами резания при высокой жёсткости СПИД
Точение строгание в условиях достаточной жёсткости СПИД
Точение строгание в условиях пониженной жёсткости СПИД
Обработка поверхностей в условиях малой жёсткости (большая длина заготовки)
Значение угла j1 в зависимости от условий обработки
Обточка напроход быстрорежущими резцами
Обточка напроход твердосплавными резцами
Расточка подрезка быстрорежущими резцами
Расточка подрезка твердосплавными резцами
Прорезка отрезка немерных заготовок
Прорезка мерных пазов
* БС — быстрорежущая сталь; ТС — твердые сплавы.
Подачи в зависимости от шероховатости поверхности
Подачи при черновой обработке
Размер державки резца мм
сталь углеродистая и легированная
Подача при глубине резания
Подачи при чистовой обработке
Диапазон скоростей резания мс
Шерохова-тость по-верхности
Радиус при вершине резца r мм
Сталь углеродистая и легированная
Чугун и алюминиевые сплавы
Весь диапазон скоростей
Подачи допускаемые прочностью державки резца
Глубина резания t мм до
Резцы с пластинками твердого сплава
Резцы из быстро-режущей стали
Резцы с державкой (В × Н)
Подача допускаемая прочностью державки S ммоб
Поправочные коэффициенты на подачу в зависимости от длины вылета резца lp выраженную через его высоту Н
Длина вылета резца lp
Примечание. При одновременной работе несколькими резцами (деление припуска по глубине резания) допускаемые подачи определять по максимальной глубине резания приходящейся на каждый резец.
Подачи допустимые прочностью пластинки твердого сплава
Главный угол в плане φ
Толщина пластинки твердого сплава мм
Примечание. При работе с ударами табличные подачи умножать на поправочный коэффициент 08.
База данных о состоянии обрабатываемой поверхности
Состояние поверхности
Отливка с нормальной коркой
Отливка с загрязненной коркой
Медные и алюминиевые сплавы
База данных вида закрепления заготовки
В патроне с задним центром
Подачи допустимые жесткостью детали. Обработка предварительная в патроне
Поправочный коэффициент на подачу в зависимости от
главного угла в плане j
Продолжение прилож. 10
Подачи допустимые жесткостью детали при обработке в патроне
Предел прочности s Нмм2
Поправочный коэффициент в зависимости от
главного угла в плане
Окончание прилож. 10
Подачи допустимые жесткостью детали при обработке в центрах
Глубина резания t мм
Поправочный коэффициент в зависимости от длины детали
главного угла в плане
Главный угол в плане j°
Скорость резания V=Vm K1 K2
Быстро-режущая сталь
Табличная скорость резания Vm мc при угле в плане j°
Продолжение прилож. 11
Коэффициент К1 для определения скорости резания
силумин и литейные сплавы
Окончание прилож. 11
Коэффициент К2 для определения скорости резания
К2 при стойкости Т в минутах резания
Мощность потребная на резание
Сталь. Резцы с пластинами твердого сплава
Мощность резания N кВт
Поправочный коэффициент
Продолжение прилож. 12
Чугун серый и ковкий. Резцы с пластинами твердого сплава
Скорость резания V мc до
Окончание прилож. 12
Алюминиевые сплавы. Резцы из быстрорежущей стали
Скорость резания V мc
Усилие подачи. Сталь. Резцы с пластинами твердого сплава
Предел прочности sВ Нмм2
Скорость резания V мс
Поправочные коэффициенты на силу подачи в зависимости от
угла наклона главной режущей кромки
Расчетные зависимости для определения сил резания
Коэффициенты и показатели степеней в формулах для расчета силы РZ
Сталь конструкционная и стальное литье sв=750 Нмм2
Поправочный коэффициент КМР при обработке стали и чугуна
Сталь конструкционная и
Показатели степени UP в формулах
Твердый сплав при точении стали
Быстрорежущая сталь при точении стали
Твердый сплав при точении чугуна
Быстрорежущая сталь при точении чугуна
Поправочный коэффициент КМР для алюминиевых сплавов при обработке резцами из быстрорежущей стали
Дюралюмин при sв Нмм2
Окончание прилож. 14
Поправочные коэффициенты для сил резания
Параметры влияющие на коэффициент
Геометрия режущей части инструмента и его износ
Величина в зависимости от материала инструмента
Радиус при вершине резца в плане r мм
Износ по задней поверхности hз мм
Обрабатываемый материал (стали)
Хромомарганцовистые (ХГ)
Хромокремнистые (ХС)
Хромомолибденовые (ХМ)
Хромокремнемарганцовистые (ХГС)
Хромоникелемолибденовые (ХНМ)
Хромоникелевольфрамовые (ХНВ)
Расчетные зависимости для определения скорости резания
Материал режущей части резца
Характеристика подачи S
Коэффициент и показатели степени
Сталь конструкционная углеродистая sв=750 Нмм2
Алюминиевые сплавы sв=100 200 Нмм2 дюралюминий sв=300 400 Нмм2
Поправочный коэффициент КUV учитывающий материал резца
Значение коэффициента КUv в зависимости от марки инструментального материала
Сталь конструкционная
Чугун серый и ковкий
Коэффициент КnV учитывающий состояние поверхности
Литье стальное и чугунное
с загрязненной коркой
Продолжение прилож. 15
Поправочные коэффициенты для расчета скорости резания
Коэффициенты учитывающие влияние параметров резца
Радиус при вершине r мм
Сечение державки резца
С отрицательной фаской
Плоская отрицательная
Плоская или радиусная без фаски
Коэффициент КOV учитывающий влияние вида обработки
Отношение обрабатываемого диаметра к диаметру заготовки
Поправочный коэффициент КMV
учитывающий свойства обрабатываемого материала
Сталь конструкционная углеродистая и легированная
Окончание прилож. 15
Значение коэффициента СМ и показатели степени nV
Показатель степени nV
углеродистая (С06%) никелевая
углеродистая (С>06%) хромистая марганцовистая
хромоникельмолибденовая
хромомарганцовистая хромокремнистая хромокремнемарганцовистая
Чугун: серый и ковкий
Поправочный коэффициент КMV для алюминиевых сплавов
sВ=40 50 Нмм2 НВ>100
База данных материала режущего инструмента
Углеродистая инструментальная сталь ГОСТ 14235-74
Легированная инструментальная сталь ГОСТ 5950-73
Однокарбидные твёрдые сплавы ГОСТ 3882-74
Быстрорежущая инструментальная сталь ГОСТ 19265-73
- и 3- карбидные твёрдые сплавы ГОСТ 38820-74
Окончание прилож. 16
Синтетические сверхтвёрдые поликристаллы
База данных материала детали
Стали обыкновенного качества
Сталь рессорно-пружинная
Сталь легированная (марганцовистая)
Высоколегирован-ные жаропроч-ные жаростойкие коррозионные стали и сплавы
Сталь коррозион-ная прочная жа-ростойкая
Шарикоподшип-никовая
Сталь углеродистая качественная
Сталь конструкционная качественная (хромоникелевая)
Окончание прилож. 17
Сплавы на основе титана
База данных оборудования
База данных вида обработки
Наружное продольное точение
Наружное поперечное точение
Внутреннее продольное точение (расточка)
Внутреннее поперечное точение
Внутреннее прорезание
Инструкция по работе на ПК
Запустить команду REGREZ.EXE. Появится заставка с краткой инструкцией. Выполните команду «Нажмите любую клавишу».
В появившемся окне «Данные обработки» вводим соответствующие данные либо из предлагаемых вариантов либо численные значения. После каждого ввода не забывайте нажать клавишу «Enter». В меню предлагаемых вариантов перемещение осуществляется клавишами «» и «». Внизу в окне постоянно имеются подсказки.
После ввода данных появляется меню «Исправить данные — Начать расчет». Для просмотра и исправления данных выбираем «Исправить данные». Если исходные данные набраны правильно то приступаем к расчету — «Начать расчет».
После расчета появляется меню «Просмотреть отчет — Распечатать отчет — Данные».
Для просмотра расчета выбираем «Просмотреть отчет».
Для продолжения работы выбираем — «Дальше».
Появляется меню «Выполнить новый расчет — Изменить данные расчета — Закончить работу».
Для начала нового расчета выбираем «Выполнить новый расчет». Если после просмотра отчета появилась необходимость изменить исходные данные то выбираем команду «Изменить данные расчета».
Окончание работы и выход из программы — команда «Закончить работу».
Введение . . . . . . . . . . . . . . . . . . . . . . . . . . . . . . . . . . . . . . . . . . . . . . . . . . . . . . . .3
Табличный метод определения режима резания . . . . . . . . . . . . . . . . . . . . . . . .3
Аналитический метод расчета режима резания . . . . . . . . . . . . . . . . . . . . . . . . .7
Расчет режимов резания по номограммам . . . . . . . . . . . . . . . . . . . . . . . . . . . . .12
Пример расчета . . . . . . . . . . . . . . . . . . . . . . . . . . . . . . . . . . . . . . . . . . . . . . . . . . .14
Оформление курсовой работы . . . . . . . . . . . . . . . . . . . . . . . . . . . . . . . . . . . . . . .21
Литература . . . . . . . . . . . . . . . . . . . . . . . . . . . . . . . . . . . . . . . . . . . . . . . . . . . . . . .24
Приложения . . . . . . . . . . . . . . . . . . . . . . . . . . . . . . . . . . . . . . . . . . . . . . . . . . . . . .25
Оглавление . . . . . . . . . . . . . . . . . . . . . . . . . . . . . . . . . . . . . . . . . . . . . . . . . . . . . . .54
Рекомендуемые чертежи
- 17.03.2024
- 24.01.2023
- 01.07.2014
- 18.05.2015