Редуктор цилиндрический одноступенчатый кривозубый




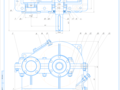
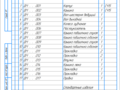
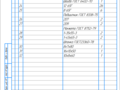
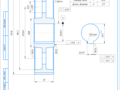
- Добавлен: 24.01.2023
- Размер: 444 KB
- Закачек: 0
Описание
Редуктор цилиндрический одноступенчатый кривозубый
Состав проекта
![]() |
![]() |
![]() ![]() ![]() ![]() |
![]() ![]() ![]() ![]() |
![]() ![]() ![]() ![]() |
![]() ![]() ![]() ![]() |
![]() ![]() ![]() ![]() |
![]() ![]() ![]() |
![]() ![]() ![]() ![]() |
Дополнительная информация
+Спецификация2.cdw

Вал ведомый.cdw

Допуски на размеры с неуказаными допусками валов -JT14
Колесо.cdw

Редуктор.cdw

Наименьшее пятно контакта зацепления по длине и высоте зуба 60%
Суммарный осевой зазор в подшипниках быстроходного вала
Суммарный осевой зазор в подшипниках тихоходного вала редуктора
должен быть в пределах 0
Валы собраного редуктора должны проворачиваться от руки плавно
Редуктор обкатать без номинальной нагрузки при частоте вращения
бытроходного вала 670 обмин в течении 1 ч
Сопряженные поверхности корпуса и крышки при окончательной сборке
покрыть тонким слоем герметика УТ-34 ГОСТ 24285-80
Покрытие необработаных поверхностей редуктора:
наружных - эмаль ПФ-115 черная ГОСТ 6465-76;
крышки смотрового лючка
головки маслоуказателя
- эмаль ПФ-115 красная ГОСТ 6465-76
л масла И40-А ГОСТ 17479.4-87
Техническая характеристика
Номинальный крутящий момент на выходном валу 187
Частота вращения выходного вала редуктора 280 обмин
Передаточное число редуктора 3
Нагрузка реверсивная
Корпус.cdw

Неуказанные радиусы скруглений 6 мм
Толщина ребер жесткости 10 мм
Формовочные уклоны по ГОСТ 3212-57
Литье должно быть плотным - раковины и рыхлости
Овальность и конусность отверстий не
Неуказанные предельные отклонения размеров диаметров
На всех резьбовых отверстиях снять фаски под углом
и диаметром на 1 мм больше диаметра резьбы
Обработку по размерам в квадратных скобках производить
совместно с крышкой редуктора. Детали применять совместно
Редуктор ПЗ.doc
Выбор двигателя. Кинематический расчет двигателя
Расчет плоскоременной передачи
Расчет зубчатых передач редуктора
Проектный расчет валов
Расчетная схема валов редуктора. Определение реакций в опорах подшипников
Проверочный расчет подшипников
Конструирование зубчатых колес
Конструирование корпуса редуктора
Проверочный расчет шпонок
Проверочный расчет валов
Смазывание редуктора
Список использованной литературы
Рассчитать и спроектировать одноступенчатый редуктор с плоскоременной передачей валами на подшипниках качения для привода ленточного конвейера.
- полезное усилие передаваемое лентой конвейера Р = 25кН
- скорость ленты V = 22мс
- диаметр приводного барабана Dб = 015м.
- тип ременной передачи – плоскоременная
- режим работы – легкий
- реверсивность – реверсивный
- продолжительность включения 20%
- коэффициент использования привода
Редуктором называют механизм состоящий из зубчатых или червячных передач выполненный в виде отдельного агрегата и служащий для передачи мощности от двигателя к рабочей машине. Кинематическая схема может включать помимо редуктора открытые зубчатые передачи цепную или ременную передачу.
Назначение редуктора – понижение угловой скорости и повышение вращающего момента ведомого вала по сравнению с валом ведущим. Механизмы для повышения угловой скорости выполненные в виде отдельных агрегатов называются ускорителями или мультипликаторами.
Редуктор состоит из корпуса (литого чугунного или сварного стального) в котором помещают элементы передачи – зубчатые колеса валы подшипники и т. д. В отдельных случаях в корпусе редуктора размещают также устройства для смазки зацеплений и подшипников (например внутри корпуса редуктора может быть помещен шестеренчатый масляный насос) или устройства для охлаждения (например змеевик с охлаждающей водой в корпус червячного редуктора).
Редуктор проектирует либо для привода определенной машины либо по заданной нагрузке (моменту на выходном валу) и передаточному числу без указания конкретного назначения. Второй случай характерен для специализированных заводов на которых организовано серийное производство редукторов.
Редукторы классифицируются по следующим признакам: тип передачи (зубчатые червячные или зубчато-червячные); число ступеней (одноступенчатые двухступенчатые и т. д.); тип зубчатых колес ( цилиндрические конические коническо-цилиндрические и т.д.); относительное расположение валов редуктора в пространстве (горизонтальные вертикальные); особенности кинематической схемы (развернутая соосная с раздвоенной ступенью и т. д.).
Возможности получения больших передаточных чисел при малых габаритах передачи обеспечивают планетарные и волновые редукторы.
Спроектируем одноступенчатый горизонтальный цилиндрический редуктор который передает вращающий момент с электродвигателя через зубчатую передачу.
1 Принципиальная схема ленточного конвейера
Одноступенчатый редуктор
2 Кинематическая схема
Выбор электродвигателя и кинематический расчет
1 Определяем общий h привода:
По таблице приведенной в приложении 2 принимаем КПД всех передач входящих в привод.
Согласно принципиальной схемы
- КПД ременной передачи принимаем 097;
- КПД зубчатой передачи принимаем 098;
- КПД подшипниковых опор всех валов принимаем для подшипников качения 0995;
n - число пар подшипниковых опор валов
(для данной схемы n = 3)
- КПД муфты принимаем 098;
2 Мощность на валу барабана Р4 кВт
3 Мощность на валу электродвигателя Р1 кВт
4 Из таблицы приложения 3 выбираем по величине P1 асинхронный эл. двигатель серии 4А.
Выбираем электродвигатель марки 4А132М6970 мощностью 75кВт и диаметром выходного конца вала 38мм синхронной частотой вращения 1000обмин скольжение s = 32%
Номинальная частота вращения вала двигателя мин:
где s – относительное скольжение %.
дв = 1000· (1 – 32100) = 968 обмин
5 Угловая скорость барабана на выходе
6 Частота вращения вала барабана:
7 Определяем общее передаточное число привода
Передаточное число всего привода состоит из частных передаточных чисел передач входящих в привод согласно разработанной кинематической схемы
Принимаем ориентировочное значение Uз.пер = 315 и определяем передаточное число гибкой передачи
8 Определяем кинематические характеристики валов.
Для разработанной кинематической схемы величины числа оборотов вала n угловой скорости мощности на вале Р и передаваемого момента Т определяются по следующим зависимостям :
Число оборотов вала:
Передаваемый момент:
Данные кинематического расчета сведем в таблицу 2.1
Расчет ременной передачи
1. Для расчета ременной передачи выбираем плоскоременную передачу.
- вращающий момент на валу ведущего шкива Т1 = 592Н·м;
-частота вращения вала ведущего шкива n1 = 968обмин;
-передаточное число ременной передачи uпер = 11;
2 Диаметр малого шкива:
= 6×(592×103)13 =209 мм
принимаем по ГОСТ 17383-73 [1c. 120] d = 200 мм
3 Диаметр большого шкива:
d2 = d1·u·(1-e) = 200×11×(1–001) = 2178 мм
4 Уточняем передаточное отношение:
u = d2d1(1–e) = 220200×(1–001) = 11.
5 Межосевое расстояние:
a = 2(d1+d2) = 2×(200+220) = 840 мм.
L = 2a+05p(d1+d2)+(d2–d1)2(4a) =
= 2×840 + 05p(200+220)+(220–200)2(4×840) = 2340 мм.
7 Угол обхвата малого шкива:
a1 = 180–57(d2–d1)a = 180–57×(220–200)840 = 178°
V = pd1n160000 = p×200×96860000 = 101 мс.
Ft = PV = 60×103101 = 594 Н.
Выбираем ремень Б800 с числом прокладок z = 3 dо = 15 мм ро = 3 Нмм
Коэффициент угла обхвата:
Ca = 1–0003(180–a1) = 1–0003×(180–178) = 099.
Коэффициент учитывающий влияние скорости ремня:
Cv = 104–00004V2 = 104–00004×1012 = 100.
Коэффициент угла наклона передачи СН = 10.
Коэффициент режима работы Ср = 10 – при постоянной нагрузке.
Допускаемая рабочая нагрузка на 1 мм ширины прокладки:
[p] = poCaCНСрСv = 3×099×100×10×10 = 297 Нмм.
b > Ft(z×[p]) = 594(3×297) = 666 мм примем b = 71 мм [1c. 258].
11 Предварительное натяжение ремня:
F0 = s0×b×d = 18×71×45 = 575 Н
где s0 = 18 МПа – для кожаных ремней
d = 45 мм – толщина ремня.
Fв = 3F0sina12 = 3×575·sin178°2 =1725 Н.
Расчет зубчатой передачи
1. Исходными данными для расчета зубчатой косозубой передачи являются вращающий момент на колесе Т3 = 1877 частота вращения колеса n3 = 280 передаточное число = 315 Р3 = 55.
2. На основании исходных данных для расчета определяем материал и вид термообработки для шестерни и колеса и твердости по НВ. Выбрать материал со следующими механическими характеристиками: для шестерни ст. 45 термообработка - улучшение твердость НВ 230; для колеса - ст. 45 термообработка - улучшение твердость - НВ 200.
3. Допускаемое контактное напряжение определяется для шестерни и для колеса по зависимости
где - предел контактной выносливости;
КHL – коэффициент долговечности для редуктора с длительной эксплуатацией KHL = 10;
коэффициент безопасности 115 для улучшенной стали.
Величина - определяется 2НВ+70
4. Для цилиндрических передач с непрямыми зубьями;
[H] = 045·([H]1 +[H]2) = 045·(461+409) = 3915 МПа
[H] = 123·[H]2 = 123·409 = 5031МПа
Выбираем наименьшее из полученных значений [H] = 3915 МПа
5. Допускаемое напряжение на изгиб для колеса и для шестерни определяется по формуле
[SF] - коэффициент безопасности (запаса прочности)
5 для улучшенной стали
Для материала шестерни
6 Определение расчетного крутящего момента
где Т2 = Т3 = 1877Нм
КНк = 12·КН - коэффициент неравномерности распределения нагрузки по ширине венца принимается в зависимости от коэффициента ширины зуба bd.
ba – коэффициент ширины зуба по межосевому расстоянию. Принимаем ba = 04.
Принимаем КН = 109 при НВ≤ 350.
КНк = 12·КН = 12· 109 = 131
Т2Н = 1877·131 = 2459Нм
7. Определяем межосевое расстояние мм
где = 430 для косозубых передач
ТН = 2459 вращающий момент на валу колеса.
Ближайшее межосевое расстояние по ГОСТ2185-66
6. Нормальный модуль зацепления
Принимаем по ГОСТ 9563-60 mt = 25мм.
8. Определяем суммарное число зубьев
Предварительный угол наклона зубьев принимается = 10о.
Уточненное значение угла наклона зубьев
9. Уточненное значение передаточного числа зубчатой передачи
Отклонение от заданного
u = uф-u u 100% = 31-315 315 100% = 15% ≤ 4%
Проверяем значение величины межосевого расстояния мм
= (27+83)·25(2·0982) = 140мм
10. Уточненное значение передаточного числа ременной передачи
Отклонения от принятого ранее нет.
11. Делительные диаметры шестерни и колеса в косозубых колесах
d1= 27·250982 = 69мм
d2 = 83·250982 = 211мм
12. Диаметры вершины зубьев шестерни и колеса мм
dа1= 69 + 2·25 = 74мм
dа2 = 211 + 2·25 = 216мм
13. Диаметры впадин зубьев
df1 = d1-25m; df2 = d1-25m
df1 = d1-25m = 69-25·25 = 628 мм
df2 = d2-25m = 211-25 · 25 = 2048 мм
14.Ширина шестерни и колеса мм
b2 = 04·140 = 56мм b1 = 56+5 = 61мм (по стандартному ряду принимаем b1 = 63мм).
15. Коэффициент ширины шестерни по диаметру
16.Окружная скорость колеса V мс
17. Выбираем 8-ю степень точности зацепления зубчатых колес.
18. Коэффициент нагрузки КН = КН · КНα · КНV
КН -уточненное значение величины коэффициента неравномерности распределения нагрузки по ширине венца 1075.
КНα -коэффициент учитывающий неравномерность нагрузки для косозубых колес КНα = 11.
КНV -коэффициент учитывающий влияние динамической нагрузки 1025 – для косозубых колес при V10 мс
Кн = КН· КНα· КНV = 1075·11·1025 = 121
19. Проверяем величину контактных напряжений в зацеплении
Н = ≤ [Н] где Ка = 270 для косозубых передач
20. Силы действующие в зацеплении:
окружная сила Ft = Н
радиальная сила Fr1 = Ft1 · tg αcos Н
Fr1 = Ft1 · tg αcos = 18116·03640982 = 6715Н
Fa1=Fa2= Ft1·tgα = = 18116·0364= 6638 Н
Радиальная сила с которой муфта действует на вал:
FM025Ft = 02518116 = 4529Н
21.Проверяем зубья на выносливость по напряжениям изгиба.
Для косозубых колес F =
KF = Kf · KFV - коэффициент нагрузки где
Kf - коэффициент концентрации нагрузки;
KFV -коэффициент динамичности;
YF - коэффициент формы зуба в зависимости от Zэ.
В результате выполненных расчетов получены следующие параметры цилиндрической передачи:
межосевое расстояние aw = 140 мм;
делительные диаметры:
шестерни d1 = 69 мм;
ширина шестерни b1 = 63 мм;
модуль зубчатых колес mn = 25 мм;
фактическая окружная скорость V = 37 мс;
на быстроходном валу Т1 = 592 Нм
на тихоходном валу Т2 = 625Нм
Проектный расчет валов редуктора
Редукторный вал представляет собой ступенчатое цилиндрическое тело количество и размеры ступеней которого зависят от количества и размеров установленных на вал деталей.
Проектный расчет ставит целью определить ориентировочно геометрические размеры каждой ступени вала: ее диаметр d и длину l.
Проводится расчет на кручение по пониженным допускаемым напряжениям без учета влияния изгиба.
1. Расчет геометрических параметров тихоходного вала
Рис.5.1. Типовая конструкция быстроходного вала редуктора.
-я ступень вала под элемент открытой передачи d1 мм
Для стали 45 значение допускаемого напряжения для вала шестерни [k] = 20.
Принимаем из стандартного ряда dВ1 = 26мм.
Вторая ступень вала под уплотнение крышки с отверстием и подшипник
Принимаем из стандартного ряда d2 = 35 мм.
-яступень под шестерню
Принимаем d3 = 45 мм
l3 определяем графически при эскизной компоновке
dу = d3 + 1-3 мм = 45 + 3 = 48 мм
-я ступень под подшипник.
Принимаем dп1 = 35мм.
Предварительно выбираем радиальный шариковый однорядный подшипник 207 легкой серии по ГОСТ 8338-75:
D = 72 В = 17 r = 20 С = 255 С0 = 137.
2. Расчет геометрических параметров тихоходного вала
Рис.5.2. Типовая конструкция тихоходного вала редуктора.
Ступень под полумуфту
dв2 = где [k] = 25 МПа.
Расчетное значение dв2 округляем до ближайшего стандартного в большую сторону dв2 = 34мм.
Принимаем из стандартного ряда d2 = 45 мм.
-я ступень под колесо
Принимаем d3 = 55 мм
dу = d3 + 1-3 мм = 55 + 3 = 58 мм
Принимаем dп2 = 45мм.
Предварительно выбираем радиальный шариковый однорядный подшипник 209 легкой серии по ГОСТ 8338-75:
D = 85 В = 19 r = 20 С = 332 С0 = 186.
Выполняем эскизную компоновку.
Расчетная схема валов редуктора
1. Определение реакций в опорах подшипников
Вертикальная плоскость
Определим опорные реакции Н:
Строим эпюру изгибающих моментов относительно оси Х в характерных сечениях 1 4.
Мх2 = RAYlb2 = -100851122 = -565Н·м
Мх3 = -Fоп lоп = -1725·85 = -1276Н·м
Мх2 = -Fоп(lоп+lb2)+RBYlb2 = -1725(85+1122) +16801122 = -1302 Н·м
Горизонтальная плоскость
Строим эпюру изгибающих моментов относительно оси У в характерных сечениях 1 3.
Му2 = -RАХlb2=-9058·1122=-507Н·м
Строим эпюру крутящих моментов.
Определяем суммарные радиальные реакции
Определяем суммарный изгибающий момент
2. Определение реакций в опорах подшипников
Мх2 = Fмlм = 4529·74 = 335Н·м
Мх3 = Fм*(lм+lt2) = 4529·(74+1102) = 584Н·м
Мх3 = RDY·lt2= 6056·1102= 333Н·м
Му2 = Fмlм = 4529·85 = 385Н·м
Му3 = -Fм·(lм+lt2)+RCXlt2 = -4529·(85+1102) – 14821102 = -715Н*м
1. Определение эквивалентной динамической нагрузки
Быстроходная ступень:
Подшипник выбирается по наиболее нагруженной опоре 1 намечаем радиальный шариковый однорядный подшипник 207 легкой серии по ГОСТ 8338-75:
а) Определяем отношение
V – коэффициент вращения
Rr2 - суммарная реакция.
б) Определяем отношение
по табл. 9.2 [1] интерполированием находим е = 0211 Y = 2294.
в) По соотношению > е выбираем формулу и определяем эквивалентную динамическую нагрузку наиболее нагруженного подшипника:
RE = (XVRr2 + + YRa)КбКт = (056 1 19086 +186638)171 =33198 Н
г) Определяем динамическую грузоподъемность:
Расчетная долговечность ч.
2. Определение эквивалентной динамической нагрузки
Подшипник выбирается по наиболее нагруженной опоре 1 намечаем радиальный шариковый однорядный подшипник 209 легкой серии по ГОСТ 8338-75: D = 85 В = 19 r = 20 С = 332 С0 = 186.
Определяем отношение
Rr1 - суммарная реакция.
находим е = 023 Y = 186.
в) По соотношению >е выбираем формулу и определяем эквивалентную динамическую нагрузку наиболее нагруженного подшипника:
RE = (XVRr1 + + YRa)КбКт = (056113535 +1866638)171 = 33875 Н
Конструктивные размеры шестерни и колеса
1. Шестерня выполняется за одно целое с валом а ее размеры:
Z = 27 аw = 140мм делительный диаметр d1 = 69мм диаметр вершин зубьев dа1 = 74мм ширина шестерни b1 = 63мм диаметр впадин зубьев df1 = 77мм.
2. Колесо изготавливается из поковки
Делительный диаметр d2 = 211мм dа2 = 216мм ширина колеса b2 = 56мм диаметр впадин зубьев df2 = 2048мм dк = 55мм.
3. Размеры ступицы колеса
dcm - диаметр ступицы dcm = 16·dк2 = 16·55 = 88мм;
lcm - длина ступицы lcm = (12 15) ·dк2 = 12·55= 66мм.
4. Толщина обода o = (25 4)·m o = 625 10 принимаем 8 мм.
5. Толщина диска колеса С = 03 · b2 = 03·56 = 168мм
6. Диаметр центровой округлости
Dотв = 05 (Do + dcm) = 05·(1888+88) = 1284 мм.
где Do = df2 - 2 o = 2048 – 2·8 = 1888мм
7. Диаметр отверстий dотв =
8. Результаты расчета сведем в таблицу.
Направление линии зуба
Нормальные исходные контура
Коэффициент смещения
Конструктивные размеры корпуса редуктора
1. Толщина стенок корпуса и крышки
= 0025 aw + 1 = 0025·140+1= 45 принимаем = 6мм
= 002 aw + 1 = 002·140+1= 38 принимаем 1 = 6мм
2. Толщина верхнего пояса (фланца) корпуса и крышки корпуса
в = 15 = 15·6 = 9 мм в1 = 151 = 15·6 = 9 мм.
3. Толщина нижнего пояса (фланца) крышки корпуса
р = 235 = 235·6 = 141мм принимаем р = 16мм.
4. Толщина ребер основания корпуса
m = (085 1)· = 51 6мм принимаем m = 6мм.
5. Толщина ребер крышки
m1 = (085 1)·1 = 51 6мм принимаем m1 = 6мм.
6. Диаметр фундаментных болтов
d1 = (003 0036)· аw + 12 = 162 1704 принимаем болты с резьбой М16.
Число фундаментных болтов ≥ 4.
7. Диаметр болтов крепления крышки корпуса к корпусу у подшипников
d2 = (07 075)·d1= 112 120мм
Принимаем болта с резьбой М12
8. Диаметр болтов соединяющих основание корпуса с крышкой
d3 = (05 06)·d1=80 96мм
Принимаем болты с резьбой М8
9. Болты крепления крышки подшипников в количестве 4-6.
10. Наименьший зазор между наружной поверхностью колеса и внутренней стенкой корпуса:
–по диаметру А = (1 12)· = 12·6 = 72мм
–по торцам А 1 А = 72 мм
11. Расстояние от торца подшипника до внутренней стенки корпуса v = 12 мм - для смазки подшипников пластичным смазочным материалом (V2мс).
Проверка прочности шпоночных соединений
1. Размеры шпонок и пазов принимаются по ГОСТ 23360-78.
Шпонка ведущего вала
Шпонка 8х7х80 глубина паза вала t1 = 40мм глубина паза втулки t2 = 33.
2. Материал шпонок - сталь 45 нормализованная
3. Напряжение смятия для ведущего вала
[Gсм ]= 100 120 МПа 10 МПа
4. Расчет шпонок ведомого вала.
Выбираем шпонку под колесо 16х10х40 t1 = 60; t2 = 43.
Напряжение смятия для ведущего вала
[Gсм ]= 100 120 МПа 27 МПа
Выбираем шпонку под полумуфту
Шпонка 10х8х75 глубина паза вала t1 = 50мм глубина паза втулки t2 = 33.
[Gсм ]= 100 120 МПа 368 МПа
Уточненный расчет валов
При уточненном расчете принимается что нормальные напряженияот изгиба изменяются по симметричному циклу а касательные от кручения - по пульсирующему.
Цель уточненного расчета - определить коэффициент запаса прочности S для опасных сечений каждого вала и проверить соблюдение условия S ≥ [S] . Допускаемое значение [S] = 25.
1. Ведущий вал изготовлен из того же материала что и шестерня (конструкция вал-шестерня) - сталь 45 улучшенная. Величина предела прочности в = 780Нмм .
2. Предел выносливости при симметричном цикле изгиба:
-1 = 043в = 043· 780 = 335МПа
3. Предел выносливости при симметричном цикле касательных напряжений
-1 = 058-1=058·335 = 193МПа
4. Для ведущего вала расчетным сечением принимается сечение в середине посадочной части вала А-А т.к. наличие шпоночного паза вызывает концентрацию напряжений. Вал рассчитываем на кручение.
5. Момент сопротивления кручения
6. Амплитуда и среднее напряжение пульсирующего цикла
7. Эффективный коэффициент концентрации нормальных напряжений K = 1785 для валов с одной шпоночной канавкой.
8. Масштабный фактор = 0739.
9. Коэффициент = 01.
10.Коэффициент запаса прочности
11. Величина изгибающего момента от радиальной консольной нагрузки в середине посадочной части вала в одноступенчатом зубчатом редукторе на быстроходном валу Н мм
l - длина посадочной части под шкив ременной передачи.
12. Момент сопротивления изгибу
13. Амплитуда цикла нормальных напряжений
15. Среднее напряжение цикла нормальных напряжений m =0
16. Коэффициент запаса прочности по нормальным напряжениям
17. Результирующий коэффициент запаса прочности
Запас прочности достаточен.
18. Материал ведомого вала - сталь 45 нормализованная.
20. Пределы выносливости МПа
-1= 043 в = 780·043=3354МПа
-1= 058 -1 = 058·3354 = 1945МПа
21. Для расчета выбираем сечение вала А-А в зоне установки зубчатого колеса концентрация напряжений обусловлено наличием шпоночной канавки.
22. Выбираем значение коэффициентов K = 179 и K = 168; = 0856 и = 0738. Величину = 01 и = 02. Величина крутящего момента Т3 =1877.
23. Изгибающий момент в горизонтальной плоскости
М' = -Fм·(lм+lt2)+RCXlt2 = -4529·(85+1102) – 14821102 = -715Н·м
24. Изгибающий момент в вертикальной плоскости
М'' = RDY·lt2= 6056·1102= 333Н·м
25. Суммарный изгибающий момент в сечении А-А
26. Выбираем шпонку 18х10х50 t1 = 60; t2 = 43.
27. Момент сопротивления кручению
28. Момент сопротивления изгибу
29. Амплитуда и среднее напряжение цикла касательных напряжений
30. Амплитуда нормальных напряжений изгиба
31. Коэффициент запаса прочности по нормальным напряжениям
32. Коэффициент запаса прочности по касательным напряжениям
33. Результирующий коэффициент запаса прочности для сечения А-А
Расчет вала в сечении К-К вызван тем что в данном сечении концентрация напряжений вызвана посадкой подшипника с гарантированным натягом.
34. По таблице 11.5 [1. стр300] для валов с напрессованными деталями определяется отношение K. = 356
35. Определяется отношение
K = 06 K + 04 = 06·356+04= 254
36. Принимаем значения = 01 и = 02.
37. Изгибающий момент
М4 = Fмlм = 4529·74 = 335Н·м
38. Осевой момент сопротивления
39. Амплитуда нормальных напряжений
40. Полярный момент сопротивления
Wp = 2W = 2·89416 = 178832мм
41. Амплитуда и среднее напряжение цикла касательных напряжений
42. Коэффициент запаса прочности по нормальным напряжениям
43. Коэффициент запаса прочности по касательным напряжениям
44. Результирующий коэффициент запаса прочности сечения К-К
45. В сечении Л-Л концентрация напряжений возникает в связи с переходом от одного диаметра к другому. От ø 45мм к ø 34мм. Dd = 4534 = 132 и rd = 2534 = 007 K = 168; K=132;
46. Осевой момент сопротивления
47. Амплитуда нормальных напряжений
48. Полярный момент сопротивления
Wp = 2W = 2·38567 = 77134мм
49. Амплитуда и среднее напряжение цикла касательных напряжений
50 Коэффициент запаса прочности по нормальным напряжениям
51. Коэффициент запаса прочности по касательным напряжениям
52. Результирующий коэффициент запаса прочности сечения Л-Л
53. Концентрация напряжений в сечении Б-Б обусловлена наличием шпоночной канавки.
Пределы выносливости МПа
-1= 043 в = 780*043=3354МПа
-1= 058 -1 = 058*3354 = 1945МПа
54. Выбираем значение коэффициентов K = 179 и K = 168; = 0862 и = 0746. Величину = 01 и = 02. Величина крутящего момента Т3 =1877.
55. Изгибающий момент
М2 = Fмlм = 4529·85 = 385Н·м
56. Выбираем шпонку 10х8х60 t1 = 50; t2 = 33.
57. Момент сопротивления кручению
58. Момент сопротивления изгибу
59. Амплитуда и среднее напряжение цикла касательных напряжений
60. Амплитуда нормальных напряжений изгиба
61. Коэффициент запаса прочности по нормальным напряжениям
62. Коэффициент запаса прочности по касательным напряжениям
63. Результирующий коэффициент запаса прочности для сечения Б-Б
Смазывание зубчатого зацепления производится окунанием зубчатого колеса в масло заливаемого внутрь корпуса до уровня обеспечивающего погружение колеса примерно на 10 мм. Объем масляной ванны V определяем из расчета 025 дм масла на 1кВт передаваемой мощности:
По таблице устанавливаем вязкость масла. При контактных напряжениях [н] = 392 МПа и скорости V= 22 мс рекомендуемая вязкость масла должна быть примерно равна 34·10-6 м2с. По таблице принимаем масло индустриальное И-40А (по ГОСТ 20799-75).
Камеры подшипников заполняем пластичным смазочным материалом УТ-1. периодически пополняем его шприцем через пресс-масленки.
Перед сборкой внутреннюю полость корпуса редуктора тщательно очищают и покрывают маслостойкой краской.
Сборку производят в соответствии со сборочным чертежом редуктора начиная с узлов валов:
на ведущий вал мазеудерживающие кольца и шарикоподшипники предварительно нагретые в масле до 80-100 °С;
в ведомый вал закладывают шпонку и напрессовывают зубчатое колесо до упора в бурт вала; затем надевают распорную втулку мазеудерживающие кольца и устанавливают шарикоподшипники предварительно нагретые в масле.
Собранные валы укладываются в основание корпуса редуктора и надевают крышку корпуса покрывая предварительно поверхности стыка крышки и корпуса спиртовым лаком. Для центровки устанавливают крышку на корпус с помощью двух конических штифтов; затягивают болты крепящие крышку к корпусу.
После этого на ведомый вал надевают распорное кольцо в подшипниковые камеры закладывают пластичную смазку ставят крышки подшипников с комплектом металлических прокладок для регулировки.
Перед постановкой сквозных крышек в проточки закладывают войлочные уплотнения пропитанные горячим маслом. Проверяют проворачиванием валов отсутствие заклинивания подшипников (валы должны проворачиваться от руки) и закрепляют крышки винтами.
Далее на конец ведомого вала в шпоночную канавку закладывают шпонку устанавливают шкив и закрепляют его торцевым креплением; винт торцового тления стопорят специальной планкой.
Затем ввертывают пробку маслоспускного отверстия с прокладкой и новый маслоуказатель.
Заливают в корпус масло и закрывают смотровое отверстие крышкой с прокладкой из технического картона; закрепляют крышку болтами.
Собранный редуктор обкатывают и подвергают испытанию на стенде по программе устанавливаемой техническими условиями.
В данном курсовом проекте был спроектирован редуктор цилиндрический одноступенчатый с передаточным числом u = 315.
Редуктор цилиндрический одноступенчатый входит в состав рабочего механизма привода ленточного конвейера.
Расчетами были определены: кинематическая схема машинного агрегата выбран двигатель произведен кинематический расчет двигателя выбор материалов зубчатых передач определение допускаемых напряжений нагрузки валов редуктора. Произведен проектный расчет валов эскизная компоновка редуктора проверочный расчет подшипников основные геометрические передачи проверочные расчеты.
Основные технические характеристики привода
Тип двигателя: 4А132М6970 (Рном = 75кВт nном = 1000 обмин);
Передаточные числа: привода u =346 редуктора uзп = 315 ременной передачи uоп = 11.
Основные технические характеристики редуктора
Передаточное число u = 315
Вращающий момент на ведомом валу Т = 1877 Н·м
Вращающий момент на ведущем валу Т = 625 Н·м
Частота вращения ведомом валу n = 280 обмин
Частота вращения ведущем валу n = 880 обмин
Мощность на ведомом валу Р = 55 кВт
Мощность на ведущем валу Р = 57 кВт
Материал изготовления зубчатых колес Ст. 45
Материал изготовления валов Ст. 45
Чернавский С.А. - Курсовое проектирование деталей машин. - М.: Машиностроение 1988. - 416 .с
Дунаев П.Ф. Леликов О.П. Детали машин. Курсовое проектирование – М.: Машиностроение 2004 г. – 560 с.
Шейнблит А. Е. Курсовое проектирование деталей машин: Учеб. пособие для техникумов.- М.: Высш. шк. 1991. - 432 с: ил. ISBN 506-001514-9
Анурьев В.И. - Справочник конструктора - машиностроителя: в 3-х томах. Том 3 - М.: Машиностроение 1991. - 398 с.
Анурьев В.И. - Справочник конструктора - машиностроителя: в 3-х томах. Том 1 - М.: Машиностроение 1991. - 483 с.
+Спецификация1.cdw

Крышка подшипника глухая
Крышка подшипника сквозная