Расчет привода конвейера с одноступенчатым косозубым редуктором




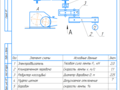
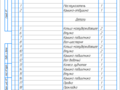

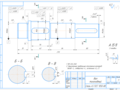
- Добавлен: 24.01.2023
- Размер: 1 MB
- Закачек: 0
Описание
Расчет привода конвейера с одноступенчатым косозубым редуктором
Состав проекта
![]() |
![]() ![]() ![]() ![]() |
![]() ![]() ![]() ![]() |
![]() ![]() ![]() ![]() |
![]() ![]() ![]() ![]() |
![]() ![]() ![]() |
![]() ![]() ![]() ![]() |
![]() ![]() ![]() ![]() |
![]() ![]() ![]() ![]() |
Дополнительная информация
Редуктор.cdw

Передаточное число редуктора u = 5.
Крутящий момент на тихоходном
Скорость вращения быстроходного
Технические требования
Редуктор залить маслом: индустриальное И-Г-А-68
В подшипниковые узлы при сборке заложить консталин
жировой УТ-1 ГОСТ 1957-73
Привод допускается эксплуатировать с отклонением от
горизонтального положения на угол до 5
штифт и болт условно не показаны
Схема кинематическая 5-4.cdw

Клиноременная передача
Допускаемое отклонение
Срок службы привода L
ленточному конвейеру
Схема кинематическая
Компановка.cdw

Редуктор. 2.cdw

Расчет 5-4.doc
2Срок службы приводного устройства
Привод к ленточному транспортеру устанавливается в заводском цеху и предназначен для транспортировки сыпучих грузов работа в одну смену по 8 часов нагрузка маломеняющаяся режим реверсивный.
Срок службы привода определяется по формуле
где LГ = 4 года – срок службы привода;
КГ – коэффициент годового использования;
где 300 – число рабочих дней в году;
tc = 8 часов – продолжительность смены;
Lc = 2 – число смен;
Кс = 1 – коэффициент сменного использования.
Lh = 365·4·082·8·2·1 =19200 часа
Принимаем время простоя машинного агрегата 15% ресурса тогда
Lh = 19200·085 = 16300 час
Рабочий ресурс принимаем 16500 часов
Эксплуатационные характеристики машинного агрегата
С малыми колебаниями
Выбор двигателя кинематический расчет привода
1Определение требуемой мощности.
Требуемая мощность рабочей машины
Ррм = Fv = 20·11 = 22 кВт
2Общий коэффициент полезного действия
где м = 098 – КПД муфты [1c.40]
з.п = 097 – КПД закрытой цилиндрической передачи
о.п = 096 – КПД открытой ременной передачи
пк = 0995 – КПД пары подшипников качения
пс = 099 – КПД пары подшипников скольжения.
= 098·097·09952·096·099 = 0894.
3Требуемая мощность двигателя
Ртр = Ррм = 220894 = 246 кВт.
Для проектируемых машинных агрегатов рекомендуются трехфазные асинхронные короткозамкнутые двигатели серии 4А. Эти двигатели наиболее универсальны. Закрытое и обдуваемое исполнение позволяет применить эти двигатели для работы в загрязненных условиях в открытых помещениях и т. п.
Ближайшая большая номинальная мощность двигателя 30 кВт
4Определение передаточного числа привода и его ступеней
Двигатели серии 4А выпускаются с синхронной частотой вращения 750 1000 1500 и 3000 обмин.
Выбор типа электродвигателя
Синхронная частота вращения обмин
Номинальная частота вращения
Частота вращения барабана
nрм = 6·104v(D) = 6·104·11(225) = 93 обмин
Общее передаточное число привода
где n1 – частота вращения вала электродвигателя.
Принимаем для зубчатой передачи u1 = 5 тогда для открытой передачи
Анализируя полученные значения передаточных чисел делаем выбор в пользу варианта 3 – электродвигатель 4A112M6 так как только в этом случае передаточное число клиноременной передачи попадает в рекомендуемые границы (2÷3).
5Определение силовых и кинематических параметров привода
Числа оборотов валов и угловые скорости:
n1 = nдв = 955 обмин w1 = 95530 =1000 радс
n2 = n1u1 = 955205 = 465 обмин w2=46530 = 487 радс
n3 = n2u2 =46550 = 93 обмин w3= 9330 = 974 радс
Фактическое значение скорости вращения рабочего вала
v = Dn36·104 = ·225·936·104 = 11 мс
Отклонение фактического значения от заданного
Мощности передаваемые валами:
P2 = Pтро.ппк = 246·096·0995 = 235 кВт
P3 = P2з.ппк = 235·097·0995 = 227 кВт
Pрв = P3мпс = 227·098·099 = 220 кВт
Т1 = P1w1 = 24601000 = 246 Н·м
Т2 = 2350440 = 483 Н·м
Т3 = 2270880 = 2331 Н·м
Трв = 2200880 = 2259 Н·м
Результаты расчетов сводим в таблицу
Силовые и кинематические параметры привода
Вал электродвигателя
Ведущий вал редуктора
Ведомый вал редуктора
Выбор материалов зубчатых передач и определение допускаемых напряжений
Принимаем согласно рекомендациям [1c.52] сталь 45:
шестерня: термообработка – улучшение – НВ235÷262 [1c.53]
колесо: термообработка – нормализация – НВ179÷207.
Средняя твердость зубьев:
НВ1ср = (235+262)2 = 248
НВ2ср = (179+207)2 = 193
Допускаемые контактные напряжения:
где KHL – коэффициент долговечности
где NH0 = 1·107 [1c.55]
N = 573Lh = 573·974·165·103 = 921·107.
Так как N > NH0 то КHL = 1.
[]H1 = 18HB+67 = 18·248+67 = 513 МПа.
[]H2 = 18HB+67 = 18·193+67 = 414 МПа.
[]H = 045([]H1 +[]H2) = 045(513+414) = 417 МПа.
Допускаемые напряжения изгиба:
где KFL – коэффициент долговечности
Так как N > NF0 = 4·106 то КFL = 1.
[]F01 = 103HB1 = 103·248 = 255 МПа.
[]F02 = 103HB2 = 103·193 = 199 МПа.
[]F1 = 1·255 = 255 МПа.
[]F2 = 1·199 = 199 МПа.
Механические характеристики материалов зубчатой передачи
Расчет закрытой цилиндрической передачи
Межосевое расстояние
где Ка = 430 – для косозубых передач [1c.58]
ba = 0315 – коэффициент ширины колеса
КН = 10 – для прирабатывающихся колес.
аw = 430(50+1)[2331·103·10(4172·502·025)]13 = 155 мм
принимаем согласно ГОСТ 2185-66 [2 c.52] аw = 160 мм.
где Km = 58 – для косозубых колес
d2 – делительный диаметр колеса
d2 = 2awu(u+1) = 2·160·50(50 +1) = 267 мм
b2 = baaw = 025·160 = 40 мм.
m > 2·58·2221·103267·40·199 = 127 мм
принимаем по ГОСТ 9563-60 m = 20 мм.
Основные геометрические размеры передачи
min = arcsin(35mb2) = arcsin(35·240) = 801°
Суммарное число зубьев:
zc = 2·160cos8°20 = 158
Число зубьев шестерни:
z1 = zc(u+1) = 158(50 +1) = 26
Число зубьев колеса:
z2 = zc–z1 = 158 – 26 =132;
уточняем передаточное отношение:
u = z2z1 =13226 = 508
Отклонение фактического значения от номинального
(508 – 50)10050 = 16% меньше допустимого 3%
Действительное значение угла наклона:
Фактическое межосевое расстояние:
aw = (z1+z2)m2cos = (132+26)·202cos 906° = 160 мм.
делительные диаметры
d1 = mz1cos = 20·2609875= 5266 мм
d2 = 20·13209875= 26734 мм
da1 = d1+2m = 5266+2·20 = 5666 мм
da2 = 26734+2·20 = 27134 мм
df1 = d1 – 24m = 5266 – 25·20 = 4766 мм
df2 = 26734 – 25·20 = 26234 мм
b2 = ybaaw = 025·160 = 40 мм
b1 = b2 + (3÷5) = 40+(3÷5) = 45 мм
v = 2d22000 = 974·267342000 = 13 мс
Принимаем 8-ую степень точности.
Силы действующие в зацеплении
Ft = 2T1d1 = 2·483·1035266 = 1834 H
Fr = Fttgacos = 1834tg20º09875= 676 H
Fa = Fttgb = 1834tg 906° = 292 Н.
Проверка межосевого расстояния
аw = (d1+d2)2 = (5266+26734)2 = 160 мм
Проверка пригодности заготовок
Dзаг = da1+6 = 5666+6 = 6266 мм
Условие Dзаг Dпред = 125 мм выполняется
Для колеса размеры заготовки не лимитируются
Расчетное контактное напряжение
где К = 376 – для косозубых колес [1c.64]
КНα = 106 – для косозубых колес
КН = 10 – для прирабатывающихся зубьев
КНv = 102 – коэффициент динамической нагрузки [1c.65].
H = 376[1834(50+1)106·10·102(26734·40)]12 = 389 МПа.
Недогрузка (417 – 389)100417 = 67% допустимо 10%.
Расчетные напряжения изгиба
F2 = YF2YFtKFαKFKFv(mb2)
где YF2 – коэффициент формы зуба
Y = 1 – 140 = 1 – 906140 = 0935
KFα = 191 – для косозубых колес
KF = 1 – для прирабатывающихся зубьев
KFv = 105 – коэффициент динамической нагрузки [1c.64].
Коэффициент формы зуба:
при z1 = 26 zv1 = z1(cos)3 = 26098753 = 27 YF1 = 385
при z2 =132 zv2 = z2(cos)3 =132098753 = 135 YF2 = 361.
F2 = 361·0935·1834·10·10·10520·40 = 813 МПа []F2
F1 = F2YF1YF2 = 813·385361 = 866 МПа []F1.
Так как расчетные напряжения H [H] и F []F то можно утверждать что данная передача выдержит передаваемую нагрузку и будет стабильно работать в нормальных условиях весь срок службы.
Расчет и проектирование клиноременной передачи открытого типа
По номограмме [1c83] выбираем ремень сечения А
Минимальный диаметр малого шкива d1min =125 мм [1c84]
Принимаем диаметр малого шкива на 1 2 размера больше
Диаметр большого шкива
d2 = d1u(1-) =100205(1-001) = 203 мм
где = 001 – коэффициент проскальзывания
принимаем d2 = 200 мм
a > 055(d1+d2) + h = 055(200+140) + 80 = 173 мм
h = 80 мм – высота ремня сечением А
принимаем а = 200 мм
w = 05(d1+d2) = 05(100+200) = 471
y = (d2 - d1)2 = (200 – 100)2 = 10000
L = 2200 + 471 +100004200 = 883 мм
принимаем L = 900 мм
Уточняем межосевое расстояние
a = 025(L – w) + [(L – w)2 – 2y]05 =
= 025(900 – 471) +[(900 – 471)2 - 210000]05 = 208 мм
Угол обхвата малого шкива
α1 = 180 – 57(d2 – d1)a = 180 – 57(200-100)208 = 152º
v = d1n160000 = 10095560000 = 50 мс
Ft = Рv = 24610350 = 492 H
Допускаемая мощность передаваемая одним ремнем
Cp = 10 – спокойная нагрузка
Cα = 092 – при α1 = 152º [1c.82]
Cl = 10 – коэффициент влияния длины ремня
Сz = 095 – при ожидаемом числе ремней 2÷3
P0 = 095 кВт – номинальная мощность передаваемая одним ремнем
[Р] = 09510092·095 = 083 кВт
Z = Р[Р] = 246083 = 296
Натяжение ветви ремня
= 85024635009210 =152 H
Сила действующая на вал
Fв = 2FZsin(α12) = 21523sin(1522) = 882 H
Прочность ремня по максимальным напряжениям в сечении
max = 1 + и+ v []p = 10 Нмм2
– напряжение растяжения
= F0A + Ft2zA =15281 +4922381 = 289 Нмм2
А =138 мм2– площадь сечения ремня
и – напряжение изгиба
и = Eиhd1 = 8080100 = 640 Нмм2
Eи = 80 Нмм2 – модуль упругости
v = ρv210-6 = 130050210-6 = 003 Нмм2
ρ = 1300 кгм3 – плотность ремня
max = 289+640+003 = 932 Нмм2
условие max []p выполняется
Нагрузки валов редуктора
Силы действующие в зацеплении цилиндрической косозубой передачи
Консольная сила от клиноременной передачи действующая на быстроходный вал
Горизонтальная и вертикальная составляющие консольной силы от ременной передачи действующие на вал
Fвв = Fвcos15° = 882cos15° = 852 H
Fвг = Fвsin15° = 882sin15° = 228 H
Консольная сила от муфты действующая на тихоходный вал
Fм = 125·Т312 = 125·233112 = 1908 Н
Рис. 6.1 – Схема нагружения валов цилиндрического редуктора с наклонным разъемом корпуса
Разработка чертежа общего вида редуктора.
Материал быстроходного вала – сталь 45
термообработка – улучшение: в = 780 МПа;
Допускаемое напряжение на кручение []к = 10÷20 МПа
Диаметр быстроходного вала
где Т – передаваемый момент;
d1 = (16·483·10310)13 = 29 мм
принимаем диаметр выходного конца d1 = 30 мм;
длина выходного конца:
l1 = (1015)d1 = (1015)30 = 3045 мм
принимаем l1 = 50 мм.
Диаметр вала под уплотнением:
d2 = d1+2t = 30+2×22 = 344 мм
где t = 22 мм – высота буртика;
принимаем d2 = 35 мм:
длина вала под уплотнением:
l2 » 15d2 =15×35 = 52 мм.
Диаметр вала под подшипник:
Вал выполнен заодно с шестерней
Диаметр выходного конца тихоходного вала:
d1 = (16·2331·10315)13 = 43 мм
принимаем диаметр выходного конца d1 = 45 мм;
l1 = (1520)d1 = (1520)45 = 6890 мм
принимаем l1 = 80 мм
d2 = d1+2t = 45+2×28 = 506 мм
где t = 28 мм – высота буртика;
принимаем d2 = 50 мм .
Длина вала под уплотнением:
l2 » 125d2 =125×50 = 63 мм.
Диаметр вала под колесом:
d3 = d2 + 32r = 50+32×30 = 596 мм
принимаем d3 = 60 мм.
Предварительно назначаем радиальные шарикоподшипники легкой серии №207 для быстроходного вала и №210 для тихоходного вала.
Расчетная схема валов редуктора
Рис. 8.1 – Схема нагружения быстроходного вала
Горизонтальная плоскость.
Сумма моментов сил и реакций опор относительно опоры А
mA = 60Ft – 120BX + 62Fвг = 0
Отсюда находим реакцию опоры В в плоскости XOZ
BX = (1834·60+228·62)120 = 1035 H
Сумма моментов сил и реакций опор относительно опоры В
mВ = 60Ft – 120АX –182Fвг = 0
Отсюда находим реакцию опоры А в плоскости XOZ
АX = (1834·60 – 228·182)120 = 571 H
Изгибающие моменты в плоскости XOZ
MX1 =1035·60 = 621 Н·м
MX1 = 228·62 = 141 Н·м
АХ – Ft +BX + Fвг = 571 – 1834 +1035+228 = 0
Вертикальная плоскость.
mA = 60Fr + 120BY – Fa1d12 – 62Fвв = 0
Отсюда находим реакцию опор В в плоскости YOZ
BY = (-676·60 +292·52662 + 852·62)120 =166 H
Сумма моментов сил и реакций опор относительно опоры B
mA = 60Fr – 120AY + Fa1d12 + 182Fвв = 0
Отсюда находим реакцию опор A в плоскости YOZ
AY = (676·60 +292·52662 + 852·182)124 = 1694 H
Fвв + BY + Fr – AY = 852+166+676 – 1694 = 0
Изгибающие моменты в плоскости YOZ
MY = 852·62 = 528 Н·м
MY = 852·122 – 1694·60 = 23 Н·м
Суммарные реакции опор:
А = (АХ2 + АY2)05 = (5712 +16942)05 =1788 H
B= (BХ2 + BY2)05 = (10352 +1662)05 =1048 H
Рис. 8.2 – Схема нагружения тихоходного вала.
Горизонтальная плоскость. Сумма моментов сил и реакций опор относительно опоры С
mС = 62Ft + 124DX – 254Fм = 0
Отсюда находим реакцию опоры D в плоскости XOZ
DX = (254·1908 – 62·1834)124 = 2991 H
Реакция опоры С в плоскости XOZ
CX = DX + Ft– Fм = 2991+1834 – 1908 = 2917 H
MX1 =2917·62 =1809 Н·м
MX2 =1908·130 =2480 Н·м
СХ – Ft – DX + Fм = 2917 – 1834 – 2991 +1908 = 0
Вертикальная плоскость. Сумма моментов сил и реакций опор относительно опоры С
mС = 62Fr+ Fad22 – 124DY = 0
Отсюда находим реакцию опоры C и D в плоскости XOZ
DY = (62·676 +292·267342)124 = 653 H
CY = Fr – DY = 676 – 653 = 23 H
MX1 = 23·62 = 14 Н·м
MX2 = 653·62 = 405 Н·м
СY – Ft + DY = 23 – 676 + 653 = 0
C = (29172 + 232)05 =2917 H
D = (29912 + 6532)05 = 3061 H
Проверочный расчет подшипников
Проверяем наиболее нагруженный подшипник А.
Отношение FaА =2921788 = 020 e следовательно Х=10; Y= 0
Эквивалентная нагрузка
P = (XVFr + YFa)KбКТ
где Х – коэффициент радиальной нагрузки;
V = 1 – вращается внутреннее кольцо;
Fr – радиальная нагрузка;
Y – коэффициент осевой нагрузки;
Kб =15– коэффициент безопасности;
КТ = 1 – температурный коэффициент.
Р = (00·1·1788 + 0)15·1 = 2682 Н
Требуемая грузоподъемность подшипника
где m = 30 – для шариковых подшипников
Стр = 2682(573·487·16500106)13 =20710 Н C = 255 кН
Расчетная долговечность подшипников
= 106(255×103 2682)360×465 = 30806 часов
больше ресурса работы привода равного 16500 часов.
Проверяем наиболее нагруженный подшипник С.
Отношение FaС =2923061= 010 e следовательно Х=10; Y= 0
Р = (10·1·3061+ 0)15·1 = 4592 Н
Стр = 4592(573·974·16500·106)13 = 20734 Н C = 351 кН
= 106(351×103 4592)360×93 = 80035 часов
Конструктивная компоновка привода
1 Конструирование зубчатых колес
Конструктивные размеры колеса
dст = 155d3 = 155·60 = 93 мм.
lст = (10÷15)d3 = (10÷15)60 = 60÷90 мм принимаем lст = 60 мм.
S = 22m+005b2 = 22×2+005·40 =64 мм
С = 025b = 025·40 = 10 мм
2 Конструирование валов
Основные размеры ступеней валов (длины и диаметры) рассчитаны в пункте 7.
Переходные участки между ступенями выполняются в виде канавки шириной b = 3 мм или галтели радиусом r = 1 мм.
Шестерня выполняется заодно с валом.
Размеры шестерни: dа1 = 5666 мм b1 = 68 мм = 906°.
Фаска зубьев: n = 05m = 0520 = 10 мм
принимаем n = 10 мм.
В проектируемом редукторе для соединения валов с деталями передающими вращающий момент применяются шпоночные соединения.
Используем шпонки призматические со скругленными торцами по ГОСТ 23360-78. Длина шпонки принимается на 5 10 мм меньше длины ступицы насаживаемой детали. Посадка для косозубого колеса Н7r6.
4Конструирование подшипниковых узлов
В проектируемом редукторе используется консистентная смазка подшипниковых узлов. Для изолирования подшипникового узла от внутренней полости редуктора применяются мазудерживающие кольца шириной 10 12 мм а изоляция выходных участков валов от окружающей среды достигается с помощью манжетных уплотнений по ГОСТ 8752-79. Внутренне кольцо подшипника упирается в мазеудерживающее кольцо а наружное фиксируется распорной втулкой между подшипником и врезной крышкой подшипника.
5 Конструирование корпуса редуктора 2
Толщина стенок корпуса и крышки редуктора
d = 0025ат + 1 = 0025·160 + 1 = 50 мм принимаем d = 8 мм
b = 15d = 15·8 = 12 мм
Толщина нижнего пояса корпуса
р = 235d = 235·8 = 20 мм
d1 = 0036aт + 12 = 0036·160 + 12 = 178 мм
принимаем болты М20;
- крепящих крышку к корпусу у подшипников
d2 = 075d1 = 075·20 = 15 мм
принимаем болты М16;
- соединяющих крышку с корпусом
d3 = 06d1 = 06·20 = 12 мм
принимаем болты М12.
6Конструирование элементов открытых передач
Диаметр шкива d1 = 100 мм
Диаметр шкива конструктивный de1 = d1 + 2t = 100 + 233 = 1066 мм
Ширина шкива B = (z – 1)p + 2f = (3 – 1)15 + 210 = 50 мм
Толщина обода = (11 13)е = (11 13)12 = 132 156 мм
Толщина диска С = (12 13) = (12 13)15 = 18 195 мм
принимаем С = 18 мм.
Диаметр ступицы внутренний d = dдв = 32 мм
Диаметр ступицы наружный dст = 16d = 1632 = 512 мм
принимаем dст = 50 мм
Длина ступицы lст = lдв = 80 мм.
Диаметр шкива d1 = 200 мм
Диаметр шкива конструктивный de1 = d1 + 2t = 200 + 233 = 2066 мм
Диаметр ступицы внутренний d = d1 = 30 мм
Диаметр ступицы наружный dст = 16d = 1630 = 48 мм
Длина ступицы lст = l1 = 50 мм.
Для соединения выходных концов тихоходного вала редуктора и приводного вала рабочей машины применяется цепная муфта по ГОСТ 20742-81 с допускаемым передаваемым моментом [T] =500 Н·м.
Расчетный вращающий момент передаваемый муфтой
Тр = kТ1 = 125·2331 = 291 Н·м [T]
где k = 125– коэффициент режима нагрузки для ленточных конвейеров.
Смазка зубчатого зацепления
Смазка зубчатого зацепления осуществляется путем окунания зубчатых колес в масляную ванну. Объем масляной ванны
V = (0508)N = (05 08)235 » 15 л
Смазка подшипниковых узлов.
Так как надежное смазывание подшипников за счет разбрызгивания масла возможно только при окружной скорости больше 3 мс то выбираем пластичную смазку по подшипниковых узлов – смазочным материалом УТ-1.
1 Проверочный расчет шпонок
Выбираем шпонки призматические со скругленными торцами по ГОСТ 23360-78.
Материал шпонок – сталь 45 нормализованная.
Напряжение смятия и условие прочности
где h – высота шпонки;
Шпонка на выходном конце вала: 8×7×40.
Материал шкива – чугун допускаемое напряжение смятия []см = 50 МПа.
см = 2·483·10330(7-40)(40-8) = 335 МПа
Шпонка под колесом 18×11×50. Материал ступицы – сталь допускаемое напряжение смятия []см = 100 МПа.
см = 2·2331·10360(11-70)(50-18) = 607 МПа
Шпонка на выходном конце вала: 12×8×70. Материал ступицы – сталь допускаемое напряжение смятия []см = 100 МПа.
см = 2·2331·10345(8-50)(70-12) = 595 МПа
Во всех случаях условие см []см выполняется следовательно устойчивая работа шпоночных соединений обеспечена.
2 Проверочный расчет стяжных винтов подшипниковых узлов
Стяжные винты рассчитывают на прочность по эквивалентным напряжениям на совместное действие растяжения и кручения.
Сила приходящаяся на один винт
Fв = 05Cx = 052917 =1459 H
Принимаем коэффициент затяжки Кз = 15 – постоянная нагрузка коэффициент основной нагрузки х=03 – для соединения чугунных деталей без прокладки.
Механические характеристики материала винтов: для стали 30 предел прочности в = 500 МПа предел текучести т = 300 МПа; допускаемое напряжение:
[] = 025т = 025300 = 75 МПа.
Расчетная сила затяжки винтов
Fp = [Kз(1 – х) + х]Fв = [15(1 – 03) + 03]1459 = 1969 H
Определяем площадь опасного сечения винта
А = dp24 = (d2 – 094p)24 = (12 – 094175)24 = 84 мм2
Эквивалентное напряжение
экв = 13FpA = 13196984 = 30 МПа [] = 75 МПа
3Уточненный расчет валов
Рассмотрим сечение проходящее под опорой А. Концентрация напряжений обусловлена подшипником посаженным с гарантированным натягом.
Материал вала сталь 45 улучшенная: sВ = 780 МПа [2c34]
Пределы выносливости:
-при изгибе s-1 » 043×sВ = 043×780 = 335 МПа;
-при кручении t-1 » 058×s-1 = 058×335 = 195 МПа.
Суммарный изгибающий момент
Ми = (Мх2+МY2)05 = (1412+5282)05 = 547 Н·м
Осевой момент сопротивления
W = d332 = 35332 = 421·103 мм3
Полярный момент сопротивления
Wp = 2W = 2·421·103 = 842·103 мм3
Амплитуда нормальных напряжений
v = MиW = 547·103421·103 = 130 МПа
Амплитуда и среднее напряжение цикла касательных напряжений
tv = tm = T22Wp = 483·1032·842·103 = 57 МПа
ke = 35; ktet = 06 ke + 04 = 06·35 + 04 = 25
Коэффициент запаса прочности по нормальным напряжениям
s = -1(kve) = 33535·130 = 74
Коэффициент запаса прочности по касательным напряжениям
st = t-1(kttvet + yt tm) = 195(250·57 + 01·57) =132
Общий коэффициент запаса прочности
s = sst(s2 + st2)05 =132·74(742 +1322)05 = 64 > [s] = 27
Рассмотрим сечение проходящее под опорой D. Концентрация напряжений обусловлена подшипником посаженным с гарантированным натягом.
W = d332 = 50332 = 123·103 мм3
Wp = 2W = 2·123·103 =246 мм
v = MиW = 2480·103123·103 = 202 МПа
tv = tm = T22Wp =2331·1032·246·103 = 47 МПа
ke = 40; ktet = 06 ke + 04 = 06·40 + 04 = 28
s = -1(kve) = 33540·202 = 41
st = t-1(kttvet + yt tm) = 195(280·47 + 01·47) =143
s = sst(s2 + st2)05 =143·41(412 +1432)05 = 39 > [s] = 25
Технический уровень редуктор
Условный объем редуктора
V = LBH = 440200340 = 30106 мм3
L = 440 мм – длина редуктора;
В = 200 мм – ширина редуктора;
Н = 340 мм – высота редуктора.
m = φρV10-9 = 04073003010610-9 = 88 кг
где φ = 040 – коэффициент заполнения редуктора
ρ = 7300 кгм3 – плотность чугуна.
Критерий технического уровня редуктора
γ = mT2 = 882331 = 038
При γ > 02 технический уровень редуктора считается низким а редуктор морально устаревшим.
Шейнблит А.Е. Курсовое проектирование деталей машин.–М.: Высш. шк. 1991.–432 с.
Курсовое проектировании деталей машин. С.А. Чернавский К.Н. Боков И.М. Чернин и др. – М.: Машиностроение 1988. – 416 с.
Чернилевский Д.В. Проектирование деталей машин и механизмов. – М.: Высш. шк. 1980.
Леликов О.П. Курсовое проектирование. – М.:Высш.шк.1990.
Дунаев Н.В. Детали машин. Курсовое проектирование. – М.:Высш. шк. 2002.
Альбом деталей машин.
Анурьев В.И. Справочник конструктора-машиностроителя. Т.1-3 – М.:Машиностроение 1978.
Федоренко В.А. Шошин А.И. Справочник по машиностроительному черчению. – Л.: Машиностроение 1988.
Кинематическая схема машинного агрегата
Расчет технического уровня редуктора
Спецификация редуктор 5-4.spw

одноступенчатый с нак-
лонным разъемом корпуса
Кольцо мазеудерживающее
Винт М8х22.48 ГОСТ1491-80
Шайба 16.65Г ГОСТ6402-70
Манжета ГОСТ 8752-79
Подшипник ГОСТ 8338-75
Шпонка ГОСТ 23360-78
Вал 5.cdw

Сталь 45 ГОСТ 1050-88
Колесо 5.cdw

Нормальный исходный контур
Коэффициент смещения
Радиусы скруглений 2
Неуказанные предельные отклонения размеров:
валов -t; отверстий +t
Сталь 45 ГОСТ 1050-88
Рекомендуемые чертежи
- 24.01.2023
- 24.01.2023
- 15.02.2021