Расчёт привода с одноступенчатым цилиндрическим косозубым редуктором и цепной передачей


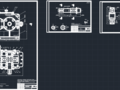
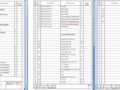
- Добавлен: 11.12.2022
- Размер: 669 KB
- Закачек: 0
Описание
Курсовой проект по дисциплине “Техническая механика”
Расчёт привода с одноступенчатым цилиндрическим косозубым редуктором и цепной передачей.
Состав проекта
![]() ![]() ![]() |
![]() ![]() ![]() |
![]() ![]() ![]() |
![]() ![]() ![]() ![]() |
![]() |
![]() ![]() ![]() |
Дополнительная информация
спецификация 2.docx
Шайба мазеудерживающая
Подшипники ГОСТ 8338-75
Пояснительная записка.docx
Расчёт передачи с гибкой связью 6
Расчёт зубчатых колес редуктора 8
Предварительный расчёт валов редуктора 11
Конструктивные размеры шестерни и колеса 12
Конструктивные размеры корпус редуктора 13
Первый этап компоновки редуктора 14
Проверка долговечности подшипников 15
Проверка прочности шпоночных соединений19
Уточненный расчет валов 21
Посадки деталей редуктора 22
Выбор сорта масла 23
Список использованных источников25
При выполнении проекта используются математические модели базирующиеся на теоретических и экспериментальных исследованиях относящихся к объемной и контактной прочности материаловедению теплотехнике гидравлике теории упругости строительной механике. Широко используются сведения изсопротивления материалов теоретической механики машиностроительного черчения и т. д. Все это способствует развитию самостоятельности и творческого подхода к поставленным проблемам.
В настоящее время в Республике Беларусь отсутствует собственное производство редукторов общего использования. Между тем в республике имеется ряд разработок которые позволили бы организовать такое производство.
Из всех видов передач зубчатые передачи имеют наименьшие габариты массу стоимость и потери на трение. Коэффициент потерь одной зубчатой пары при тщательном выполнении и надлежащей смазке не превышает обычно 001. Зубчатые передачи в сравнении с другими механическими передачами обладают большой надежностью в работе постоянством передаточного отношения из-за отсутствия проскальзывания возможностью применения в широком диапазоне скоростей и передаточных отношений. Эти свойства обеспечили большое распространение зубчатых передач; они применяются для мощностей начиная от ничтожно малых (в приборах) до измеряемых десятками тысяч киловатт.
Одной из целей выполненного проекта является развитие инженерного мышления в том числе умение использовать предшествующий опыт моделировать используя аналоги.
Наиболее полно требования снижения массы и габаритных размеров удовлетворяет привод с использованием электродвигателя и редуктора с внешним зацеплением.
ВЫБОР ЭЛЕКТРОДВИГАТЕЛЯ И КИНЕМАТИЧЕСКИЙ
Определяем общий КПД редуктора:
подш. = 099 –КПД одной пары подшипников качения
з.п. = 098 – КПД зубчатой передачи
ц.п. = 095 – КПД цепной передачи
общ.= подш.3· з.п.· ц.п. = 0993· 098 · 095 = 0903
Ориентировочно назначаем передаточные числа: uз.п. =4 uц.п. = 5
uприв= uз.п.·uц.п=4·5=20
Находим частоту вращения быстроходного вала:
n1 = n3 ·іприв. = 110· 20 = 2200 мин-1
n3 = 150мин-1 – частота вращения выходного вала
Вычисляем мощность на быстроходном валу:
Pтр= P3общ. = 460903=51 кВт
Принимаем асинхронный электродвигатель 112М4 у которого мощность Р = 51 кВт и синхронная частота вращения 1500мин-1 и S= 37%Определяем передаточное отношение привода:
nдвиг. = nс(1S) = 1500(10037) = 14445мин-1
і = nдвиг.n3 = 14445110 =1313
Принимаем передаточные отношения передач:
із.п. = 315 – передаточное отношение зубчатой передачи
іц.п. = i із.п. = 1313315=417 – передаточное отношение цепной передачи.
Определяем мощность угловую скорость частоту вращения и вращающий момент для всех валов привода:
P1 = PТР ·.подш = 51·099= 505 кВт
= n130 = 3141444530 = 151191 с-1
Т1= Р1 1 = 505103151191 =334 Нм
Р2 = Р1 з.п. подш. = 505098099 = 490 кВт
n2 = n1 із.п. = 14445315= 4585с-1
= n230 = 314 458530 = 4798 с-1
Т2 = Р2 2 = 4901034798=1021Нм
Р3 = Р2 ц.п. подш. = 49095099 = 46 кВт
n3 = n1 іц.п. = 4585417= 110 мин-1
= n330 = 31411030 = 115 с-1
Т3 = Р3 3 =46103115 =400 Нм
Таблица 1 – Расчетные величины привода
РАСЧЕТ ПЕРЕДАЧИ C ГИБКОЙ СВЯЗЬЮ
Выбираем приводную роликовую однорядную цепь.
Вращающий момент на ведущей звездочке:
Передаточное число было принято ранее:
Рассчитываем число зубьев:
- ведущей звездочки:
z3 = 312 uц. = 31-241723 (10)
- ведомой звездочки:
z4 = z3 uц. = 23417=95(11)
Принимаем: z3 = 23; z4 = 95
uц. = z4 z3 = 9523=413
(uц.u.uц.)100% =(417 413417) = 095% что допустимо.
Рассчитываем расчетный коэффициент нагрузки:
Kэ = kд· kа· kн· kр· kсм· kп (13)
kд = 1 – динамический коэффициент при спокойной нагрузке;
kа = 1 – учитывает влияние межосевого расстояния;
kн= 1 – учитывает влияние угла наклона линии центров;
kр– учитывает способ регулирования натяжения цепи;
kр= 125 при периодическом регулировании натяжения цепи;
kсм= 1 при непрерывной смазке;
kп–учитывает продолжительность работы в сутки при односменной
Определяем шаг однорядной цепи: t ≥ 28 (14)
[p] – допускаемое давление в шарнирах цепи; [p] задано в зависимости от частоты вращения n ведущей звездочки;
Выбираем цепь имеющую шаг t = 1905мм;
разрушающую нагрузку Q=318 кН; массу q = 19 кгм; Аоп =1058 мм2.
Определяем скорость цепи:
Находим окружную силу:
Fтц= Р2 v=Т2· 2v= 1021·1905334 = 582 Н (16)
Проверяем давление в шарнире:
р = Fтц·KэАоп = 582·1251058= 687МПа (17)
Уточняем допускаемое давление [p] = 22[1+001(z317)] = 22[1+001(2317)] = 2332МПа. Условие p [p] выполнено.
Определяем число звеньев цепи:
Lt = 2·at+05·z+2at (18)
z = z3+z4 = 23+95 = 118; (20)
= z4z32 = 95232·314 = 1146. (21)
Lt = 2·50+05·118+1146²50 = 16162
Округляемдочетногочисла Lt = 162
Уточняем межосевое расстояние цепной передачи:
ац = 025·t·[Lt05·z+] = =025·1905·[16205·118+] =956 мм
Определяем диаметры делительных окружностей звездочек:
dд3 = = = 140 мм (22)
Определяем диаметры наружных окружностей звездочек:
De3 = t·(ctg+07)03·d1 где (23)
d1 = 1191 мм – диаметр ролика цепи.
De3 = 1905·(ctg+07)03·1191 = 14836мм
De4 = 1905·(ctg+07) 03·1191 =585.61мм
Силы действующие на цепь:
окружнаяFтц = 582 Н – определена выше;
от центробежных сил F = q·v² = 19 ·334² 2119 Н где q = 19 кгм
от провисания Ff = 981·kf·q·aц = 981·1·19·0956= 10691 Н где kf = 1при горизонтальном расположении цепи.
Расчетная нагрузка на валы
Fв = Fтц+2·Ff = 582+2·10691 = 61762 Н (24)
Проверяем коэффициент запаса прочности цепи:
Это больше чем нормативный коэффициент запаса [s] 94;
следовательно условие s> [s] выполнено.
РАСЧЕТ ЗУБЧАТЫХ КОЛЕС РЕДУКТОРА
Выбираем материал для шестерни сталь 45 термическая обработка – улучшение HB 230; для колеса – сталь 45 термическая обработка – улучшение HB 200.
Допускаемые контактные напряжения:
[H] = Hlimb·KHL[SH] где
KHL – коэффициент долговечности принимаем равным 1; [SH] – коэффициент безопасности; [SH] = 11;
[H1] = (2HB1+70)·KHL[SH] = (2·230+70)·111 482МПа;
[H2] = (2HB+70)·KHL[SH] = (2·200+70)·111 428МПа;
[H] = 045([H1]+[H2]) =045·(482+428) = 410МПа;
Межосевое расстояние из условия контактной выносливости активных поверхностей зубьев:
а = Ka·(u+1)· = 43·(315+1)· = 102 мм
Принимаема = 100 мм и mn = 1.25 мм.
Нормальный модуль зацепления:
mn = (001÷002)·а = (001÷002)·100 = 1÷2 мм
Принимаем предварительно угол наклона зубьев =10
Определяем число зубьев:
Определим основные размеры шестерни и колеса:
делительные диаметры:
d1=mn·z1=2·2908571=48 мм (31)
d2= mn·z2=2·9108571=152 мм
Проверим межосевое расстояние:
a = = (48+152)2=140 мм
диаметры вершин зубьев:
da1 = d1 + 2 · mn =48+25= 505 мм (33)
da2 = d2 + 2 · mn= 152+25= 1545 мм
Определим ширину колеса и шестерни
b2 = ba·a= 04·100 = 40 мм; (34)
b1 = b2 + 5 мм = 28 + 5 = 45 мм; (35)
Определяем коэффициент ширины шестерни по диаметру:
Окружная скорость колес:
Принимаем 8-ю степень точности.
Коэффициент нагрузки: KH = KH·KHα·KH (38)
Значения KH = 109;KHα = 109KH = 1.
Таким образом KH= 109·1·109 = 1188
Проверка контактных напряжений:
H=H]-H)H] ·100%=2682%
Силы действующие в зацеплении:
окружная Ft = = =1392H; (40)
радиальнаяFr = Ft ·tgα=1392· tg20º= 512 Н; (41)
Проверяем зубья на выносливость по напряжениям изгиба:
Здесь коэффициент нагрузки KF = KF·KF. При bd=04 твердости HB 350 и несимметричном расположении зубчатых колес относительно опор KF = 112 KF = 13
YF – коэффициент учитывающий форму зуба и зависящий от эквивалентного числа зубьев z:
z1 = z1=38098753=39 z2 = z2120098753=125
YF1 = 388 и YF2 = 36
Допускаемое напряжение:
Для стали 45 улучшенной при твердости HB 350 Flimb = 18HB.
Для шестерни Fl для колеса Flimb = 18·200 = 360МПа.
[SF] = [SF][SF] - коэффициент безопасности где [SF] = 175 [SF] = 1. Следовательно [SF] = 175.
Допускаемые напряжения:
для шестерни F1] = = 237МПа;
для колеса F2] = =206МПа;
для шестерни = 61МПа;
для колеса = 575 МПа;
Коэффициенты Y = 094; KFα = 092.
Проверяем прочность зуба колеса:
ПРЕДВАРИТЕЛЬНЫЙ РАСЧЕТ ВАЛОВ РЕДУКТОРА
Предварительный расчет проведем на кручение по пониженным допускаемым напряжениям.
Диаметр выходного конца при допускаемом напряжении [к] = 25 МПа.
Принимаемdв1= 28 мм. Примем под подшипники dп1 = 30 мм.dk1=35
Принимаем [к] = 20 МПа.
Диаметр выходного конца вала
Принимаем dв2 = 30 мм. Диаметр вала под подшипниками принимаем dп2 = 35 мм под зубчатым колесом dк2 = 40 мм.
Диаметры остальных участков валов назначают исходя из конструктивных соображений при компоновке редуктора.
КОНСТРУКТИВНЫЕ РАЗМЕРЫ ШЕСТЕРНИ И КОЛЕСА
Шестерня d1 = 48мм; da1 = 505 мм; b1 = 45 мм. Шестерня выполнена насадной на вал
Колесо кованое: d2 = 152 мм; da2 = 1545 мм; b2 = 40 мм.
Толщина обода 0 = (25 4)·mn = (25 4)·125= 31255 мм принимаем 0 = 5 мм.
Толщина диска C = 03·b2 = 03·40 = 12мм.
КОНСТРУКТИВНЫЕ РАЗМЕРЫ КОРПУСА РЕДУКТОРА
Толщина стенок корпуса и крышки:
= 0025·aw + 1 = 0025·100 + 1 = 45 мм принимаем = 8 мм;
= 002·a + 1 = 002·100 + 1 = 3 мм принимаем 1 = 8 мм.
Толщина фланцев поясов корпуса и крышки:
верхнего пояса корпуса и пояса крышки
b = 15· = 15·8 = 12 мм;
b1 = 15·1 = 15·8 = 12 мм;
нижнего пояса корпуса
p = 235· = 235·8 = 19 мм;
принимаем p = 20 мм.
Диаметр болтов: фундаментных
d1 = (003 0036)·a + 12 = (003 0036)·100 + 12 = 15156 мм;
принимаем болты с резьбой М16;
крепящих крышку к корпусу у подшипников
d2 = (07 075)·d1= (07075)·16 = 11212 мм;
принимаем болты с резьбой М12;
соединяющих крышку с корпусом
d3 = (05 06)·d1 = (05 06)·16 = 896 мм
принимаем болты с резьбой М10.
ПЕРВЫЙ ЭТАП КОМПОНОВКИ РЕДУКТОРА
Компоновку обычно проводят в два этапа. Первый этап служит для приближенного определения положения зубчатых колес относительно опор для последующего определения опорных реакций и подбора подшипников.
Компоновочный чертеж выполняем в одной проекции – разрез по осям валов при снятой крышке редуктора; желательный масштаб 1:1 чертить тонкими линиями.
Примерно посередине листа параллельно его длинной стороне проводим горизонтальную осевую линию; затем две вертикальные линии – оси валов на расстоянии a = 100 мм.
Намечаем радиальные шарикоподшипники средней серии. Вычерчиваем упрощенно шестерню и колесо в виде прямоугольников.
Очерчиваем внутреннюю стенку корпуса:
а) принимаем зазор между торцом шестерни и внутренней стенкойкорпуса
А1 = 12·; при наличии ступицы зазор берется от торца ступицы;
Таблица 2 – Основные параметры подшипников
б) принимаем зазор от окружности вершин зубьев колеса до внутренней стенки корпуса А = ;
в) принимаем расстояние между наружным кольцом подшипника ведущего вала и внутренней стенкой корпуса А = ; если диаметр окружности вершин зубьев шестерни окажется больше наружного диаметра подшипника то расстояние А надо брать от шестерни.
Решаем вопрос о смазывании подшипников. Принимаем для подшипников пластичный смазочный материал. Для предотвращения вытекания смазки внутрь корпуса и вымывания пластичного смазочного материала жидким маслом из зоны зацепления устанавливаем мазеудерживающие кольца.
ПРОВЕРКА ДОЛГОВЕЧНОСТИ ПОДШИПНИКОВ
Ведущий вал: Из предыдущих расчетов имеем Ft = 1392 Н Fr = 512 Н;Fа= 220 Н из первого этапа компоновки.
Рассмотрим силы действующие в горизонтальной плоскости:
RАх=RСх=Ft2=13922=696 Н
Рассмотрим силы действующие в вертикальной плоскости:
Эквивалентная нагрузка:
V = 1 (вращается внутреннее кольцо); Кб = 15Кт=1. Рa=601
Отношение этой величине соответствует e = 019.
Отношение; X = 056; Y = 23.
Расчетная долговечность:
= =44540 млн.об. (48)
Ведомый вал:Ft = 1392 Н Fr = 512 Fв=10691 Н. l1 = 51l2 =52 мм l3 =56 мм. Рассмотрим силы действующие в горизонтальной плоскости:
RAy=1813 Н; RDУ= 4376Н
Расчетная долговечность млн. об.
= =5957435 млн.об. (52)
Расчетная долговечность ч.
здесь n– частота вращения ведомого вала.
Рисунок 1- Расчет ведущего вала
Рисунок 2- Расчет ведомого вала
ПРОВЕРКА ПРОЧНОСТИ ШПОНОЧНЫХ СОЕДИНЕНИЙ
Шпонки призматические со скругленными торцами. Размеры сечений шпонок и пазов и длины шпонок – по ГОСТ 23360-78 [1 с 132]:
Материал шпонок – сталь 45 нормализованная. Проверяем более нагруженные шпонки.
Напряжения смятия и условие прочности по [2 с 128]:
Допускаемые напряжения смятия при стальной ступице [см] = 100 120 МПа.
Ведущий вал:d = 28 мм; bh= 87 мм; t1 = 4 мм; длина шпонки
[3 с 23]; момент на ведущем валу T1 = 334·103H·мм;
Из двух шпонок – под зубчатым колесом и на выходе редуктора – более нагружена вторая (меньше диаметр вала и поэтому меньше размеры поперечного сечения шпонки).
d = 30мм; bхh = 8х7 мм; t1 = 4 мм; длина шпонки T2 = 1021·103H·мм;
см = = 1134 МПа [см]
Условие см [см] выполнено.
УТОЧНЕННЫЙ РАСЧЕТ ВАЛОВ
Примем что нормальные напряжения от изгиба изменяются по симметричному циклу а касательные от кручения – по от нулевому.
Уточненный расчет состоит в определении коэффициентов запаса прочности s для опасных сечений и сравнений их с требуемыми значениями [s]. Прочность соблюдена при s [s].
Будем производить расчет для предположительно опасных сечений каждого из валов.
Материал вала сталь 45 термическая обработка – нормализация среднее значение в=780 МПа.
Предел выносливости при симметричном цикле изгиба:
-1=043·В=043·780=335 МПа (55)
-1=058·-1=058·335=193 МПа (56)
Сечение Л-Л. Концентрация напряжений обусловлена переходом диаметров при и . Масштабные факторы:;
Осевой момент сопротивления сечения:
Амплитуда нормальных напряжений:
Полярный момент сопротивления:
Амплитуда и среднее значение цикла касательных напряжений:
Коэффициенты запаса прочности:
Результирующий коэффициент запаса прочности:
Материал вала сталь 45 термическая обработка – НОРМАЛИЗАЦИЯ среднее значение в=570 МПа.
-1=043·В=043·570=245 МПа
-1=058·-1=058·245=142 МПа
Сечение К-К. Проверяем ведомый вал в сечении под подшипником:
dп2 = 40мм. В сечении действует изгибающий момент Мизг.в =7782Нм.
При = 27и = коэффициентt= 01 .
Амплитуда нормальных напряжений сечения:
Момент сопротивления кручению сечения нетто:
Результирующий коэффициент запаса прочности для сечения
ПОСАДКИ ДЕТАЛЕЙ РЕДУКТОРА
Посадки и квалитеты точности назначаются в соответствии с
рекомендациями [6 с. 327328].
Шейки валов на подшипники выполняют с отклонением вала к6.
Для посадочного места вала под манжетное уплотнение h8.
Наружные кольца подшипников качения в корпусе Н7.
Посадка колеса на вал Н7р6.
Смазывание передач редуктора осуществляется окунанием зубчатого колеса в масло которое заливают внутрь на всю длину зуба.
При контактных напряжениях Н = 399МПа и окружной скорости
V =362 мс вязкость масла должна быть приблизительно равна 28 мс [5 с.253]. Принимаем масло индустриальное И-30A [5 с.253].
Подшипники качения смазываются из картера в результате разбрызгивания масла зубчатым колесом образуется масляный туман и растекание масла по валам.
Для редукторов при смазывании окунанием объем масляной ванны определяется из расчета 04 08 л. Масла на 1 кВт передаваемой мощности.
V = (04 08)505= 202 404 л.
принимаем V = 303 л.
Перед сборкой внутреннюю полость корпуса редуктора тщательно очищают и покрывают маслостойкой краской.
Сборку производят в соответствии со сборочным чертежом редуктора начиная с узлов валов.
Собранные валы и крышки подшипниковых узлов укладывают в основание корпуса редуктора в подшипниковые камеры закладывают пластичную смазку и закрывают крышкой редуктора покрывая предварительно поверхности стыка крышки герметиком или корпуса спиртовым лаком. Затягивают болты крепящие крышку к корпусу. Перед постановкой сквозных крышек в проточки закладывают уплотнения.
Проверяют проворачиванием валов отсутствие заклинивания подшипников (валы должны проворачиваться от руки).
Затем ввертывают пробку масловыпускного отверстия с прокладкой. Заливают в корпус масло и закрывают смотровое отверстие крышкой с прокладкой из технического картона; закрепляют крышку болтами.
Собранный редуктор обкатывают и подвергают испытанию на стенде по программе устанавливаемой техническими условиями.
СПИСОК ИСПОЛЬЗОВАННЫХИСТОЧНИКОВ
Дунаев П.Ф. Леликов О.П. Конструирование узлов и деталей машин: учебное пособие Дунаев П.Ф. Леликов - Москва.: Академия 2004.-407 с.
Кузьмин А.В. Чернин И.М. Козенцов Б.С. Расчет деталей машин:
Справочное пособие Кузьмин А.В. Чернин И.М. Козенцов Б.С- Москва.: Высшая школа 1986.-415 с.
Куклин Н.Г. Куклина Г.С. Житков В.К. Детали машин: учебник Куклин Н.Г. Куклина Г.С. Житков В.К. -Москва.: Высшая школа2005.-445 с.
Скойбеда А.Т. Кузьмин А.В. Макейчик Н.Н. Детали машин и основы
конструирования: учебное пособие Скойбеда А.Т. Кузьмин А.В. Макейчик Н.Н.- Москва.: Высшая школа 2006.-345с
Чернавский С.А. Боков К.Н. Чернин И.М. Ицкович Г.М. Казинцов В.П. Курсовое проектирование деталей машин: учебное пособие Чернавский С.А. Боков К.Н. Чернин И.М. Ицкович Г.М. Казинцов В.П. - Москва.: Машиностроение 1988.-312 с.
Шейнблит А.Е. курсовое проектирование деталей машин: учебник Шейнблит А.Е.- Курск .: Янтарный сказ 2005.-434с.
Чертёж.dwg

Поверхность соединения "корпус-крышка" перед сборкой покрыть уплотнительной пастой типа Герметик. 2. После сборки валы редуктора должны проварачиваться свободно без стуков и заедания. 3. Редуктор обкатать по 10-15 мин на всех режимах нагрузки.
Техническая характеристика
Редуктор цилиндрический Сборчный чертеж
HB 190 . 2. *Размер обеспеч. инстр. 3. Радиусы закруглений 1 2 мм. 4. ГОСТ 30893.1-2002-m.
Число зубьев Z 120 Исходный контур - ГОСТ13755-81 Коэф. смещения X 0 Угол накл. зубьев 9° Степень точности - 9-B Делит. диаметр d 152 Обозначение чертеж. сопряжонного кол.
HB 200 . 2. Радиусы скруглений 5 мм max. 4. ГОСТ 30893.1-2002-m.
Рекомендуемые чертежи
- 24.01.2023
- 15.02.2021
- 18.04.2023
- 24.01.2023
- 04.11.2022