Расчет элементов привода с редуктором и цепной передачей




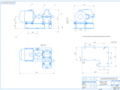

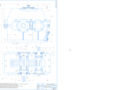
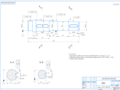
- Добавлен: 24.01.2023
- Размер: 354 KB
- Закачек: 0
Описание
Расчет элементов привода с редуктором и цепной передачей
Состав проекта
![]() |
![]() |
![]() ![]() ![]() ![]() |
![]() |
![]() |
![]() ![]() ![]() |
![]() |
![]() ![]() ![]() ![]() |
![]() ![]() ![]() ![]() |
![]() ![]() ![]() ![]() |
Дополнительная информация
Спецификация .spw

Расчетно-пояснительная
Крышка смотрового окна
Маслоуказатель жезловый
Вал-шестерня ведущий
Крышка подшипника сквозная
Крышка подшипника глухая
Колесо зубчатое цилиндрическое
Болт М12 х 38 ГОСТ 15589-70
Гайка М12 ГОСТ 15526-70
Гайка М16 ГОСТ 15526-70
Подшипник 207 ГОСТ 8338-75
Подшипник 1000909 ГОСТ 8338-75
Шайба 12 Н ГОСТ 6402-70
Шайба 16 Н ГОСТ 6402-70
Шпилька М16 х 85 ГОСТ 22034-76
Шпонка 8 х 7 х 28 ГОСТ 23360-78
Шпонка 12 х 8 х 45 ГОСТ 23360-78
Шпонка 14 х 9 х 45 ГОСТ 23360-78
Штифт 5 х 30 ГОСТ 3129-70
Прокладка регулировочная
Курсовая по деталям машин.docx
Расчет зубчатой передачи7
Расчет передачи роликовой цепью13
Расчет тихоходного вала15
Расчет подшипников качения20
Основные конструктивные размеры корпуса редуктора22
Список литературы ..26
Объектом изучения расчетов и проектирования является привод транспортера состоящий из двигателя одноступенчатого цилиндрического редуктора муфты. Зубчатые редукторы подобного типа широко используются в приводах различных машин (транспортеры металлорежущие станки и т.д.). Рассматриваемый привод служит для передачи крутящего момента на исполнительный орган – транспортер.
Для проектирования редуктора выполнены проектные и проверочные расчеты зубчатых передач. На основе эскизного проектирования получены данные для прочностных расчетов валов и подшипников качения. Расчеты выполнены на основании современных подходов по проектированию зубчатых передач с использованием критерия работоспособности – прочности по контактным напряжениям.
Конструкторская часть проекта выполнена с применением системы автоматизированного проектирования «Компас».
Выбор электродвигателя и расчет основных параметров
1Выбор электродвигателя
Принимаем двигатель – 44 кВт
По требуемой мощности из табл. П1 приложения выбираем асинхронный электродвигатель 4А112М4 с ближайшей большей стандартной мощностью Рэ = 55 кВт; синхронной частотой вращения nc = 1500-1 и скольжением S = 3.7%
2Частота вращения вала двигателя
3Общее передаточное число
4Передаточное число зубчатой передачи
Передаточное число цилиндрической зубчатой передачи редуктора рекомендуется выбирать из диапазона 25U5 с округлением до стандартного значения
5Передаточное число
6Частоты вращения валов
8Крутящие моменты передаваемые валами
Крутящий момент на валу определяется по формуле:
Расчет зубчатой передачи
1Выбор материала зубчатых колес
Определим размеры характерных сечений заготовок принимая что при передаточном числе зубчатой передачи U > 2.5 шестерня изготавливается в виде вал-шестерни. Тогда
Диаметр заготовки колеса равен
Выбираем материалы зубчатых колёс по табл. 1.1
Принимаем для колеса и шестерни – сталь 45
HB1 = 0.5 (HB1min + HB1max) = 0.5 (179 + 207) = 193
HB2 = 0.5 (HB2min + HB2max) = 0.5 (179 + 207) = 193
2Определение допускаемых напряжений
Допускаемые контактные напряжения
Для их определения используем зависимость
Пределы контактной выносливости
Коэффициент безопасности
Коэффициент долговечности
Базовые числа циклов при действии контактных напряжений
Эквивалентные числа циклов напряжений
где – коэффициент эквивалентности для среднего равновероятного режима работы
Суммарное число циклов нагружения
где - суммарное время работы передачи
В результате расчетов получим
Определим допускаемые контактные напряжения для шестерни и колеса:
Допускаемые контактные напряжения для косозубой передачи:
Условие выполняется
Допускаемые напряжения изгиба
Пределы изгибной выносливости зубьев:
Коэффициенты безопасности при изгибе:
Коэффициенты для реверсивного двигателя:
Коэффициенты долговечности:
где q – показатель степени кривой усталости
– базовое число циклов при изгибе
Эквивалентное число циклов напряжений при изгибе
где - коэффициенты эквивалентности для среднего равновероятного режима работы
В результате получим:
Определим допускаемые напряжения изгиба для шестерни и колеса:
3Проектный расчет передачи
Межосевое расстояние
где - для косозубых передач
коэффициент ширины зубчатого венца для косозубых передач принимаем
Коэффициент контактной нагрузки
Принимаем межосевое расстояние 140 мм.
Модуль числа зубьев колёс и коэффициенты смещения
Выберем стандартный модуль m = 2 мм учитывая что для силовых передач модуль меньше 2 мм применять не рекомендуется.
Суммарное число зубьев передачи:
Полученное значение округлим до ближайшего целого числа и определим делительный угол наклона зуба:
Число зубьев шестерни:
Округлим полученное значение до ближайшего целого числа
Число зубьев колеса:
Фактическое передаточное число:
Поскольку примем коэффициенты
Ширина зубчатых венцов и диаметры колёс
Ширина зубчатого венца колеса
Округлим до ближайшего числа из ряда нормальных линейных размеров . Ширину зубчатого венца шестерни принимаем на 2 .5 мм больше чем Примем
Диаметры окружностей зубчатых колёс
делительные окружности:
Окружности вершин зубьев:
Окружности впадин зубьев:
Окружная скорость в зацеплении и степень точности передачи
Для полученной скорости назначим степень точности передачи .
4Проверочный расчет передачи
Проверка контактной прочности зубьев
Для проверочного расчета зубьев на контактную прочность используем формулу:
где для косозубых передач.
Коэффициент контактной нагрузки
Коэффициент неравномерности распределения нагрузки между зубьями
где А =015 для косозубых передач
Kw – коэффициент учитывающий приработку зубьев
При для определения Kw используем выражение:
Коэффициент неравномерности распределения нагрузки по ширине колеса:
где – коэффициент неравномерности распределения нагрузки в начальный период работы.
Для определения – найдем коэффициент ширины венца по диаметру
По значению определим методом линейной интерполяции
Окончательно найдем
Поскольку выполним расчет недогрузки по контактным напряжениям
Проверка изгибной прочности зубьев
Напряжение изгиба в зубе шестерни
Коэффициент формы зуба при
Коэффициент учитывающий влияние угла наклона зуба на его прочность:
Коэффициент торцевого перекрытия
Коэффициент учитывающий перекрытие зубьев
Коэффициент нагрузки при изгибе
Для определения составляющих коэффициентов используем следующие зависимости:
В результате получим
Напряжение изгиба в зубьях колеса:
Расчет передачи роликовой цепью
Определение числа зубьев звездочек и шага цепи
1Число зубьев ведущей звездочки
2Число зубьев ведомой звездочки
3Фактическое передаточное число
4Коэффициент эксплуатации
где КД = 1 – динамический коэффициент при безударной нагрузке;
КН = 1 – коэффициент учитывающий наклон передачи к горизонту при Y = 00;
КР – коэффициент учитывающий способ регулирования натяжения цепи при периодическом регулировании КР = 125;
КСМ – коэффициент способа смазки при периодической смазки КСМ = 15;
КРЕЖ – коэффициент режима работы при односменном режиме КРЕЖ = 1;
В результате расчета получили: КЭ = 1*1*125*15*1=1875.
Расчетное значение шага цепи определим по формуле:
где mP – коэффициент рядности для однорядной цепи;
[P] – допускаемое давление в шарнире цепи на первом этапе расчета ориентировочно принимаем [P] = 20 МПа.
По таблице выберем цепь ПР- 254-60 с ближайшим большим к tP- шагом имеющая следующие характеристики: шаг t = 254 мм площадь опорной поверхности шарнира цепи А = 179 мм2 масса одного погонного метра цепи qm = 26 кгм.
Допускаемое давление в шарнире цепи [P] определим методом линейной интерполяции [P] = 26 МПа.
Для нового значения [P] уточним расчетный шаг цепи:
Поскольку полученное значение tP t и tP > tmin где tmin = 1905 мм – ближайший меньший по отношению к t стандартный шаг цепи то оставляем без изменения первоначально выбранный шаг цепи.
Геометрические параметры цепи
Принимаем Lt = 113.
8Межосевое расстояние
9Диаметры делительных окружностей звёздочек
Проверочный расчет передачи
11Окружное усилие в цепи
12 Усилие от провисания цепи
где Kf = 625 – коэффициент учитывающий наклон передачи к горизонту.
13Центробежное усилие
14Давление в шарнире цепи
15Условие статической прочности цепи
Поскольку это условие выполняется то цепь обладает необходимой статической прочностью.
16Сила нагружаемая валы передачи
Расчет тихоходного вала
1Проектный расчет и конструирование тихоходного вала.
Расчет выполняется на кручение по пониженным допускаемым напряжениям .
Ориентировочно определим диаметр вала в опасном сечении мм.
T2 – крутящий момент на тихоходном валу
Полученное значение округлим до мм;
1.1Уточнённый расчет вала
Рассчитаем на усталостную прочность вал изображенный на рисунке 2 при следующих исходных данных:
Расстояние между опорами
Расстояние до точки приложения консольной нагрузки
Диаметр вала в опасном сечении
Крутящий момент на валу
Силы приложенные к валу со стороны зубчатого зацепления:
Передача крутящего момента с тихоходного вала на вал цепной передачи осуществляется посредством муфты. Нагрузка от муфты рассчитывается по формуле:
Диаметр делительной окружности зубчатого колеса
1.2Определение опорных реакций
Горизонтальная плоскость
Вертикальная плоскость
Построение эпюр изгибающих и крутящих моментов
Изгибающий момент в сечении 1 (вертикальная плоскость)
Изгибающий момент в сечении А (вертикальная плоскость)
На основании выполненных расчетов построим эпюры изгибающих и крутящих моментов (рис. 3).
2Расчет тихоходного вала на усталостную прочность
Рассмотрим сечение А в качестве опасного т.к. в нём действуют наибольшие изгибающие мометы и имеется концентратор напряжений – шпоночный паз.
)Определение нагрузок
Суммарный изгибающий момент:
В сечении также действует крутящий момент Т = 1425 Нм и осевая сила Fa = 0257 kH
)Геометрические характеристики сечения
В сечении А имеется шпоночный паз со следующими размерами: b = 14 мм; h = 9 мм; t1 =55 мм; dk = диаметр вала в сечении А.
Осевой момент сопротивления
Полярный момент сопротивления
)Определение напряжений
Напряжения изгиба меняются по симметричному циклу с амплитудой:
Средние нормальные напряжения
Касательные напряжения меняются по отнулевому циклу
2.1Пределы выносливости
Пределы выносливости углеродистых сталей при симметричном цикле изгиба и кручения:
2.2Эквивалентные коэффициенты концентрации напряжений и коэффициенты влияния размера поперечного размера
В опасном сечении имеется два концентратора напряжений: посадка с натягом и шпоночный паз. Для посадки с натягом определим методом линейной интерполяции по табличным данным:
Для шпоночного паза эффективные коэффициенты концентрации напряжений определим также методом линейной интерполяции по табличным данным:
Коэффициенты влияния размера поперечного сечения вычислим по формуле:
Для шпоночного паза:
Из всех полученных значений для дальнейшего расчета выбираем наибольшие значения:
2.3Коэффициенты влияния шероховатости поверхности
Примем что поверхность вала под зубчатое колесо получена чистовым обтачиванием с Ra =32 мкм. По величине Ra найдем KF = 125 ( по табличным данным при b > 700 МПа
2.4Коэффициенты чувствительности к ассиметрии цикла
2.5Коэффициенты влияния упрочнения
Примем что на участке вала с опасным сечением упрочнение отсутствует. Тогда KV = 1.
2.6 Коэффициенты перехода от пределов выносливости образца к пределам выносливости детали
2.7Коэффициенты запаса прочности
Значения определим по формулам:
Общий коэффициент запаса прочности найдем по формуле:
Расчетный коэффициент запаса прочности по усталостным разрушениям S больше допускаемого коэффициента [S] = 2. Усталостная прочность вала в сечении А обеспечена.
Расчет подшипников качения
Рассчитать подшипники тихоходного вала горизонтального одноступенчатого цилиндрического редуктора.
Частота вращения вала n = 288 обмин
Крутящий момент на валу Т = 1425 Нм
Силы приложения к валу со стороны зубчатого зацепления: окружная Ft = 1223 кН; распорная Fr = 0455; осевая Fa = 0257 кН.
Диаметр делительной окружности зубчатого колеса d2 = 233 мм
Передача крутящего момента с тихоходного вала на вал исполнительного механизма осуществляется посредством муфты
Режим нагружения привода – средний равновероятный
Температура подшипникового узла до 1000 С
1Определение опорных реакций
Вал опирается на два шариковых радиально – упорных подшипника установленных в «распор». Первоначально приняты подшипники легкой серии 36209 со следующими параметрами (ГОСТ 831-75): внутренний диаметр d = 45мм; наружный D = 85 мм; ширина В = 19 мм; С = 332 кН; С0 = 216 кН.
Суммарные опорные реакции:
2Расчет подшипника на долговечность
2.1Параметр осевого нагружения
Определим е по формуле:
2.2Коэффициент вращения
При вращении внутреннего кольца подшипника V = 1.
2.3Коэффициент нагрузки
2.4Температурный коэффициент
При рабочей температуре подшипника t 1050C принимаем КТ = 1.
2.5Коэффициент безопасности
Примем что зубчатая передача имеет 8-ю степень точности. Коэффициент безопасности в этом случае Кб = 13
2.6Эквивалентная динамическая нагрузка
2.7Долговечность подшипника при максимальной нагрузке
где m = 3 – показатель степени кривой усталости для шарикоподшипников.
2.8Эквивалентная долговечность подшипника
где - коэффициент эквивалентности для среднего равновероятного режима работы.
Поскольку то выбранный подшипник удовлетворяет заданным условиям работы.
Основные конструктивные размеры корпуса редуктора
Толщина стенок корпуса и крышки редуктора:
Толщина фланцев поясов корпуса и крышки:
верхнего пояса корпуса и пояса крышки
нижнего пояса корпуса
принимаем p = 20 мм.
принимаем болты с резьбой М20;
Крепящих крышку к корпусу у подшипников:
принимаем болты с резьбой М14.
Соединяющих крышку с корпусом:
Принимаем болты с резьбой М12.
Зазор между торцом шестерни и внутренней стенкой корпуса
Принимаем зазор от окружности вершин зубьев колеса до верхней стенки корпуса
Примем расстояние между наружным кольцом подшипника ведущего вала и внутренней
Для удобства транспортировки редуктора предусмотрены захваты под крюки на крышке
редуктора. Толщина захватов в 2 раза больше толщины стенок крышки редуктора 16 мм.
Так же на крышке редуктора спроектировано смотровое окно закрываемое крышкой – отдушиной.
В корпусе редуктора предусмотрены устройства контроля уровня масла – маслоуказатель жезловый и слива отработанного масла – сливная пробка.
Для уменьшения потерь мощности на трение и снижения интенсивности износа трущихся поверхностей а также для предохранения их от заедания коррозии и лучшего отвода теплоты от трущихся поверхностей детали должны иметь надежную смазку.
Смазка зубчатых колёс:
)Для редуктора применяем непрерывное смазывание жидким маслом картерным непроточным способом.
)Сорт масла выбираем в зависимости от значения контактного напряжения в зубчатом зацеплении и окружной скорости колёс.
Принимаем масло И – Г – А – 32 по ГОСТ 17479 – 87
)Глубина погружения зубчатого колеса в масляную ванну
)Уровень масла контролируем с помощью жезлового маслоуказателя с двумя рисками min и max.
)При работе передачи масло постепенно загрязняется продуктами износа деталей передачи. С течением времени оно стареет и теряет свои свойства. Масло необходимо сливать. Для слива масла служит отверстие у дна корпуса закрываемое резьбовой маслосливной пробкой с прокладкой.
)Для компенсации избыточного давления воздуха внутри редуктора конструкцией предусмотрена отдушина.
)Для заливки масла и осмотра зубчатого венца в крышке редуктора предусмотрено смотровое окно закрываемое крышкой – отдушиной.
Смазка подшипников запроектирована разбрызгиванием масла от зубчатого колеса так как окружная скорость больше 2 мc.
Перед сборкой внутреннюю полость корпуса редуктора тщательно очищают и покрывают маслостойкой краской.
Сборку производят в соответствии со сборочным чертежом редуктора начиная с узлов валов: на ведущий вал насаживают мазеудерживающие кольца и шарикоподшипники предварительно нагретые в масле до 80 – 1000С;
В ведомый вал закладывают шпонку и напрессовывают зубчатое колесо до упора в бурт вала надевают втулку и аналогично валу – шестерне напрессовывают подшипники.
Далее собранные валы устанавливают в корпус редуктора. Надевают крышку редуктора для точной фиксации которой относительно корпуса используют два конических штифта. Затягивают болты крепящие крышку редуктора к его корпусу. Надевают глухие крышки. Затем вкручивают все болты крепящие крышки к корпусу и затягивают их попарно симметрично относительно центра крышки.
Далее на валы ставят сквозные крышки подшипниковых узлов с комплектом металлических прокладок между крышками и корпусом для регулирования. Закрепляют сквозные крышки болтами. На конец ведомого вала в шпоночную канавку закладывают шпонку устанавливают звёздочку и закрепляют ее торцевым креплением; винт торцевого крепления стопорят специальной планкой.
Проверяют проворачивание валов от руки отсутствие заклинивания подшипников.
Ввертывают пробку маслосливного отверстия устанавливают маслоуказатель.
Заливают в корпус масло и закрывают смотровое отверстие крышкой с прокладкой из технического картона; закрепляют крышку болтами.
Собранный редуктор обкатывают и подвергают испытанию на стенде по программе устанавливаемой техническими условиями.
В конструкторской части проекта рассчитана зубчатая передача с межосевым расстоянием 140 мм передаточным числом 5. Расчеты передачи валов шпонок удовлетворяют условиям прочности чем подтверждается работоспособность конструкции. В проектной части выполнены чертежи редуктора в разрезе и его вид спереди рабочий чертеж тихоходного вала общий вид установки в трех проекциях. Для сборочного чертежа составлена спецификация. Данный проект является учебным. Полученные знания по расчету проектирования будут использованы при изучении спецдисциплин и выполнении выпускной квалификационной работы.
Технические характеристики спроектированного редуктора:
)Крутящие моменты на валах редуктора:
Быстроходный Т1 = 29 Н.м;
Тихоходный Т2 = 1425 Н.м.
)Частоты вращения валов
Быстроходного n1 = 1444 обмин;
Тихоходного n2 = 288 обмин.
) Казанский Г.И. Детали машин: Методические указания по выполнению курсового проекта. Свердловск: УПИ 1991г. 28 с.
)Курсовое проектирование деталей машин. Чернавский С.А. Боков К.Н. Чернин И.М. и др. М.: Машиностроение 1988г. 416 с.
)Цехнович Л.И. Петриченко И.П. Атлас конструкций редукторов. Киев: Вища школа 1978г 128 с.
)Решетов Д.Н. Атлас конструкций деталей машин. М: Машиностроение 1979 г 370 с.
)Расчет деталей машин: Учебное пособие по курсам «Детали машин и основы конструирования» и «Механика». Баранов Г.Л. Екатеринбург: ГОУ ВПО УГТУ – УПИ 2005г. 172с.
)Решетов Д.Н. Детали машин М.: Машиностроение 1989. 496с.
)Допуски формы и расположении поверхностей деталей машин: Методические указания. Баранов Г.Л. Песин Ю.В. Екатеринбург: ГОУ ВПО УГТУ – УПИ 2006г. 26с.
Вал.cdw

Неуказанные допуски формы и расположения поверхностией по ГОСТ 30893.2 - 2002
Острые кромки притупить
Сталь 45 ГОСТ 1050-88
Кафедра Детали машин
редуктор 2.cdw

В редуктор залить индустриальное масло И-Г-А-32 ГОСТ 17479-87
Допускается эксплуатировать редуктор с отклонением от горизонтального положения до 5 градусов. При этом
необходимо обеспечить уровень масла достаточный для смазки зацепления.
Валы собранного редуктора должны поворачиваться от руки без заедания.
Поверхности корпуса сопряженные по плоскости разъема покрыть тонким слоем герметика.
Необработанные наружные поверхности редуктора покрыть серой эмалью.
Редуктор обкатать в течении 4 часов. Масло после обкатки поменять.
Редуктор цилиндрический
Кафедра Детали машин
общий вид установки.cdw

Схема установочных размеров фундаментных болтов
Рекомендуемые чертежи
- 24.01.2023
- 15.02.2021
- 18.04.2023