Проектирование заготовки



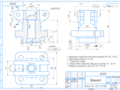
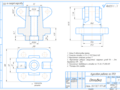
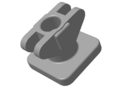
- Добавлен: 24.01.2023
- Размер: 571 KB
- Закачек: 0
Узнать, как скачать этот материал
Подписаться на ежедневные обновления каталога:
Описание
Проектирование заготовки
Состав проекта
![]() |
![]() |
![]() ![]() ![]() ![]() |
![]() |
![]() |
![]() |
![]() ![]() ![]() |
![]() ![]() ![]() ![]() |
Дополнительная информация
Контент чертежей
Лаптева.cdw

Неуказанные предельные отклонения размеров H14
Неуказанные радиусы R 2
* Размер для справок.
Острые кромки притупить радиусом или фаской 0
Материал-заменитель сталь 40Л ГОСТ 977-88.
Лаптева.docx
Государственное образовательное учреждение
высшего профессионального образования
Ижевский государственный технический университет
По курсу: «Производство и проектирование заготовок»
На тему: «Выбор способа получения и проектирования заготовки для детали Крышка 50.002 сб.ед. 59.000СБ в условиях крупносерийного типа производства».
1.Анализ конструкции и описание сб.ед.
2.Назначение тех. требований на сб.ед.
3.Анализ детали на технологичность
4.Функциональный анализ поверхностей детали
5.Назначение тех. требований на деталь
6.Выбор материала для детали
Выбор способа формообразования заготовки
1.Анализ метода получения заготовки
2.Выбор метода получения заготовки методом балльной оценки
3.Экономическое обоснование принятого решения.
Проектирование заготовки.
В настоящее время существует большое количество способов получения заготовок. Это многообразие с одной стороны даёт возможность существенно повысить эксплуатационные характеристики машин и механизмов а в некоторых случаях и улучшить свойства исходного материала с другой – создаёт большие трудности при выборе рационального экономичного способа получения той или иной детали. Правильно выбрать способ получения заготовок – значит определить рациональный технологический процесс ее получения с учетом материала детали требований точности ее изготовления технических условий эксплуатационных характеристик и серийности выпуска.
Решение задачи максимального приближения геометрических форм и размеров заготовки к размерам и форме готовой детали стало одной из главных тенденций технического прогресса в заготовительном производстве.
Также одним из этапов выбора способа формообразования является выбор материала. Материал должен обеспечивать требуемые технические характеристики нормальную работу в заданных условиях. При выборе материала следует стремиться к минимальной его стоимости так как низкая стоимость материала снижает себестоимость самого изделия.
В этой курсовой работе произведен анализ сборочной единицы – гидроаппарата клапанного. Также рассматривается одна из функциональных деталей сборочной единицы - крышка производится анализ ее технологичности и назначаются технические требования на нее.
Основными задачами этой курсовой работы является рациональный выбор материала заготовки и выбор способа ее получения обеспечивающих требуемые механические и технологические свойства детали а также минимальную себестоимость детали за счет низкой стоимости материала.
1 Анализ конструкции и описание сборочной единицы.
Гидроаппарат клапанный предназначен для перекрытия трубопровода гидросистемы. Он состоит из корпуса с прикрепленной к нему крышкой через которую пропущен шпиндель 3. К шпинделю присоединен клапан 6. Чтобы жидкость не просачивалась между корпусом и крышкой установлено кольцо 9. Для устранения течи между крышкой и шпинделем в верхней части крышки выполнено цилиндрическое углубление в которое набивается сальниковое уплотнение. Последнее плотно охватывает шпиндель и поджимается крышкой 4. При вращении шпинделя по часовой стрелке клапан закрывает проходное отверстие при вращении против часовой стрелки – открывает его.
Гидроаппарат клапанный используется в нефтяной и газовой промышленности при температуре от -30 до +50°С.
Гидроаппарат технологичен так как обеспечивается простота сборки и доступность к местам монтажа позволяющая осуществлять сборку без пригонки с полной взаимозаменяемостью деталей и сборочных единиц;
При конструировании изделия предусмотрена четкая разбивка его на самостоятельные законченные и взаимозаменяемые сборочные единицы чтобы трудоемкость сборки этих элементов была одинаковой.
2. Назначение технологических требований на сборку.
Наружные поверхности гидроаппарата должны быть покрыты эмалью ПФ-115 по ГОСТ 9.023-74;
Наружные поверхности не должны иметь рисок забоин заусенцев наплывов и т.п.
Маркировать - название и сокращенный адрес предприятия изготовителя; название и обозначение (децимальный или чертежный номер); символ в соответствии с ГОСТ 2.721-74; номер выпуска (серии) и дата изготовления;
Трущиеся поверхности смазать смазкой ЦИАТИМ 221 ГОСТ 9433-80.
Эксплуатировать при температурах от 30 до +50 0С.
В качестве рабочей жидкости использовать масло АМГ-10 работающее в интервале температур окружающей среды от -60 до +55°С.
Номинальное давление гидроаппарата 05 МПа
Наружную герметичность проверяют давлением не менее 075 МПа. Продолжительность проверки при предварительных приемочных типовых и периодических испытаниях - не менее 3 мин при приемосдаточных - не менее 30 с.
Утечки измеряют не менее чем через 30с после установления заданного значения давления. Измерения проводят в течение не менее 60 с.
Не допускаются утечки в местах соединения гидролиний и присоединения их к гидроаппарату и в местах стыка деталей гидроаппарата между собой.
Проверку виброустойчивости следует проводить по ГОСТ 16962-71 метод 102-1.
Проверку вибропрочности следует проводить по ГОСТ 16962-71 метод 103-1.1.
Проверку ресурса и наработки до отказа проводят при номинальном давлении.
Температура поверхности на которую может попасть рабочая жидкость не должна превышать температуры воспламенения этой рабочей жидкости.
Для гидроаппаратов в которых имеются подвижные выходящие наружу элементы испытания должны проводиться после выполнения не менее пяти полных циклов. При этом потение наружных поверхностей течь по резьбам и стыкам не допускаются.
Класс чистоты жидкости - не хуже 12по ГОСТ 17216-01.
При сборке исключить попадание в рабочую полость металлической стружки инородных частиц.
В качестве набивочного уплотнения применять пеньковую набивку пропитанную коллоидным графитом церезином суспензией фторопласта или жиром ГОСТ 9993-74.
После уплотнения сальниковой набивкой втулка сальника должна войти в гнездо не менее чем на 2 мм и не более чем на 30% высоты цилиндрической части входящей в сальниковую камеру. Затяжка сальника должна обеспечить герметичность при условном или рабочем давлении и не препятствовать свободному движению шпинделя.
Срок службы пеньковой набивки до 800 часов по истечении этого срока заменить уплотнение.
У подвижной системы гидроаппарата клапанного должен быть плавный ход без рывков и заеданий.
Периодичность контроля выполнения требований безопасности не реже одного раза в год.
Проводить подтягивание болтов гаек и других соединений гидроаппарата во время его работы не допускается.
Затяжка винтов соединяющих корпус и крышку 20кгс.
Общие требования к поставке транспортированию хранению и заправке жидких рабочих сред - по ГОСТ Р 50559-93.
Запрещается использовать бывшее в употреблении масло без предварительной проверки его на соответствие требованиям стандартов и технических условий.
Не допускается эксплуатировать гидроаппарат при температурах и вязкостях превышающих указанные в требованиях к рабочей жидкости.
3 Анализ детали на технологичность.
Крышка предназначена для соединения в себе элементов конструкции то есть создания сборочной единицы. Также крышка защищает от воздействия внешних неблагоприятных факторов (загрязнения и т.д.) служит для отвода тепла гашения вибраций.
Основными критериями оценки технологичности конструкции являются трудоемкость и себестоимость изготовления.
Рассматриваемая деталь – крышка в целом технологична так как имеет рациональную форму с легкодоступными для обработки поверхностями с целью уменьшения трудоёмкости и себестоимости механической обработки детали. Конструкция детали позволяет получить заготовку с размерами и конфигурациями наиболее близкими к готовой детали то есть обеспечивающими наиболее высокий коэффициент использования материала и наименьшую трудоемкость механической обработки.
Материал крышки СЧ 15 следует заменить из за его хрупкости на литейную сталь 35Л.
4 Функциональный анализ детали
Наименова-ние пов-ти
Раскрытие полезных ф-ций
Раскры-тие вредных ф-ций
Рекоменда-ции по устранен. вредных
За счет чего достигается пов-ть
Дополн. парамет-ры пов-ти
Гладкое цилиндр. отв.(присоединительная пов.)
место под установку крышки сальника;
Обеспече-ние герме-тичности в соед-ии
Обеспече-ние ци-линдричности не перекрещ. осей
Низкая шероховатость
боткой обработка за одну установку
Резьбовая цилиндри-ческая внут-ренняя пов-ть
Присоединение шпинделя
Присоед. шпинделя к крышке
обеспече-ние герметичности
резьба испытывает напр. среза и смятия витков;
Твердость предел прочности материала шероховатость
За счет материала или то мех. обр-кой
Гладкая цилиндри-ческая наружная пов-ть
Место под уплотни-тельное кольцо
Обеспече-ние герме-тичности
Поверхностное трение износ
наружный конус (свободная пов-ть)
Коррозионная стойкость твердость пов-ти
За счет материалапокрытие эмалью
Присоед. крышки сальника к крышке
Тонкие стенки хрупкость
Отверстия под шпильки
Обеспечение собираемости
Обеспеч.непере-крещива-ния осей
Мех.обработкой обработка за одну установку
Присоединение крышки к корпусу
Ориентирование крышки относительно корпуса
Место для маркировки
5. Назначение технических требований на деталь.
Неуказанные предельные отклонения: линейных размеров ; валов отверстий Н14.
Острые кромки притупить.
Материал – заменитель 40Л ГОСТ 977-88
Наружные поверхности должны быть покрыты эмалью ПФ-115 по ГОСТ 9.023-74;
На поверхности квадрата 36х36 мм маркировать - название и сокращенный адрес предприятия изготовителя; название и обозначение (децимальный или чертежный номер); символ в соответствии с ГОСТ 2.721-74; номер выпуска (серии) и дата изготовления;
Допуск соосности двух отверстий 12мм относительно их общей оси 02мм
Допуск соосности 56 и 72 относительно их общей оси 02мм.
Шероховатость резьбы М24 Ra125
Позиционный допуск 4-х отверстий 16мм 01 мм (допуск зависимый).
Допуск перпендикулярности резьбового отверстия относительно базы 01мм.
Неуказанная шероховатость Ra 63.
Шероховатость поверхности 56 на которую устанавливается корпус Ra 32.
6. Выбор материала для детали.
Основные требования предъявляемые к материалу детали (заготовки):
Высокий предел прочности и предел текучести.
Хорошая обрабатываемость резанием.
Хорошая демпфирующая способность (виброгашение).
Не должны быть токсичны и вредными для производства.
Этими качествами обладают легированные стали и чугуны: 30Л 35Л 45Л СЧ20 СЧ25 и др.
Наиболее подходящими считаются: Сталь 35Л; СЧ 25.
Целесообразно использовать сталь 35Л она обладает относительно хорошей жидкотекучестью хорошо поддается обработке резанием. Чугуны несмотря на то что обладают хорошими технологическими свойствами по сравнению с другими литейными сплавами: хорошая жидкотекучесть малый размер усадки хорошая способность рассеивать вибрационные колебания малочувствительны к концентраторам напряжений но данный материал плохо обрабатывается резанием (при последующей обработке необходимо нарезать резьбу) а также обладают хрупкостью что для данной детали недопустимо.
Таким образом в качестве материала для изготовления заготовки окончательно выбираем сталь 35Л.
Способ получения заготовки
в песчано-глинистые формы
по выплавляемым моделям
– Формы и размеры заготовки масса.
– Точность и качество поверхности заготовок;
– Технологические свойства материалов;
– Характер производства;
– Возможности имеющегося оборудования;
– Длительность технологической подготовки производства.
Литье в песчано-глинистые формы: данный способ не применяется в крупносерийном производстве в основном изготовляют детали крупногабаритные большие по массе от 10кг и выше качество поверхности и точность при этом получаются низкими (шероховатость поверхности Rz = 320 – 40 мкм и с точностью соответствующей 14 – 17-му квалитетам и грубее).
Литье в оболочковые формы: Данный способ литья наиболее рационально применять при массовом и крупносерийном производстве.отливок от 01 50кг отливки имеют чистую поверхность и повышенную точность размеров и формы возможно получения с точностью 12-14 квалитет можно лить как чугуны нелегированные стали так и цветные сплавы но при этом процесс подготовки производства занимает значительное время.
Литье по выплавляемым моделям: Данный способ литья позволяет получать отливки массой от 001 30кг любой сложности где точность размеров и параметры шероховатости поверхности отливок довольно высокие. Могут применяться любые литейные сплавы может применяться в крупносерийном производстве но при этом является наиболее длительным и трудоемким среди всех способов литья.
Литье в кокиль: Данный способ литья позволяет получать отливки массой от 001 30кг простой и средней сложности где точность размеров и параметры шероховатости поверхности отливок довольно высокие могут применяться любые литейные сплавы но в крупносерийном производстве наиболее рационально использовать цветные сплавы имеющие более низкую температуру плавления а следовательно более высокую стойкость формы но при этом является наиболее длительным и трудоемким так как нужно изготовить саму форму.
Литье под давлением: Высокая стоимость пресс-форм сложность и длительность их изготовления невысокая стойкость пресс-форм. Можно лить стали чугуны и цветные сплавы но необходимо учитывать технологические свойства материала детали так как снижаются пластические свойства отливки где в процессе заполнения формы металлом газы образуют газовую пористость что уменьшает плотность и герметичность отливок что недопустимо так как деталь работает со смазочным материалом. Отливки получаются достаточно точные по 13-16 квалитету по форме близкие к готовой детали её не подвергают механической обработке за исключением посадочных мест.
Свободная ковка: Сложность получения необходимой заготовки низкое качество и точность поверхности коэффициент весовой точности поковок не превышает 03-04 не применяется в крупносерийном производстве.
Штамповка: Данный метод наиболее эффективен при крупносерийном производстве деталей массой от нескольких граммов до нескольких тонн. Из поковок изготовляемые штамповкой можно получить заготовку средней сложности при хорошем качестве поверхности и точности поверхности.
Прокат: Низкий коэффициент использования материала большая стоимость механической обработки для придания требуемых свойств материала необходимо проводить термообработку.
Таким образом для сравнения остаются на два способа: литье в оболочковые формы и по выплавляемым моделям. Однако необходимо учесть что литье по выплавляемым моделям – трудоемкий и дорогостоящий способ литья; применение его рационально если отливку невозможно получить другим способом. Поэтому в рассматриваемом случае можно считать наиболее целесообразным литье в оболочковые формы.
Однако данный выбор метода получения заготовки ориентировочен и неточен так как использовалась только качественная оценка сравниваемых способов не используя количественные критерии поэтому более обоснованным и грамотным является проведение технико-экономического анализа сравниваемых сопоставимых вариантов основанного на использовании количественных критериев.
2 Выбор метода получения заготовки.
Метод балльной оценки
Методом балльной оценки рассмотрим виды литья которыми можно получить отливки из стали: литье по выплавляемым моделям и в оболочковые формы. По каждому способу литья определяем суммарное количество баллов соответствующих классификационным индексам с учетом весовых коэффициентов по формуле:
Определение классификационных индексов:
- Тип производства отливок: крупносерийное (КС).
- Материал отливки: МЛ2.
- Назначение: выбираем группу А: отливки обычного назначения.
- Масса: Массу проектируемой отливки ориентировочно определяют по формуле:
где Gдет - масса детали (по чертежу 36 кг);
- коэффициент использования металла отливок принимается равным 075 (независимо от способа литья).
Индекс отливки по массе G2.
- Группа сложности. Показатель сложности (индекс С) определяется по формуле:
где GОТЛ – масса отливки;
GФИГ – масса геометрической фигуры в которую может быть вписана отливка по своим габаритным размерам увеличенным в 104 раза (в данном случае это цилиндр).
По сложности формы отливка относится к группе С4.
- Средняя точность. Среднюю точность размеров в квалитетах (IТСР) определяют по формуле:
где к т n - количество размеров выполняемых с точностью соответственно по ITX ITY тогда:
Данная отливка относится к группе Т1.
Весовые коэффициенты занесем в таблицу:
Обозначение коэффициента
Составляется таблица оценки способа литья по балльной системе:
Исходный параметр (признак)
Классификационный индекс
По выплавляемым моделям
Тип производства (БПj)
Материал отливки (БMj)
Группа сложности (БCj)
Точность отливки (БTj)
Балльный метод показал что наиболее рациональным способом получения отливки является литье в оболочковые формы.
3 Экономическое обоснование выбора заготовки.
Анализ на металлоемкость.
Экономическую оценку рациональной заготовки проведём для литья в оболочковые формы.
Сквозной коэффициент использования металла для литых заготовок:
где K2 – коэффициент выхода годных изделий при производстве. По табл. 1[3] K2=056
K3 – коэффициент использования металла при механической обработке заготовок или коэффициент весовой точности.
КЗ=GДЕТGЗАГ=3648=075
Анализ по приведённым затратам.
Приведённые затраты на производство детали вычисляются по формуле:
где ЗПР –удельные приведённые народнохозяйственные затраты Р.шт.;
ЗТ – удельные текущие затраты на производство Р.шт.;
ЗК – удельные капитальные затраты Р.шт.
Удельные текущие затраты ЗТ рассчитываются по формуле:
ЗТ=CОПТ*GЗАГ+CМО(GЗАГ-GДЕТ)-CОТХ[(GМЕТ-GЗАГ)α+(GЗАГ-GДЕТ)]
где CОПТ – средняя стоимость (оптовая цена производства единицы массы заготовок приводятся в соответствующих прейскурантах цен);
CМО – условная стоимость механической обработки на 1 т. снимаемой стружки;
CОТХ – стоимость единицы массы возвратных отходов;
GМЕТ – масса металла расходуемого на производство одной заготовки вычисляется по формуле:
GДЕТ – масса готовой детали кг;
GЗАГ – масса заготовки определяется расчётным путём по чертежу заготовки;
α - доля возвратных отходов соответственно в заготовительном и в механообрабатывающем производствах включая операцию холодной листовой штамповки.
Удельные капитальные затраты ЗК определяются по формуле:
где ЕН – нормативный коэффициент экономической эффективности принимаемый равным 015;
КСК – удельные капитальные затраты на производство единицы массы заготовок значение КСК для различных видов заготовок приведены в табл. 4[3].
Расчёт ЗПР можно вести по развёрнутой формуле:
ЗПР= CОПТ*GЗАГ+CМО(GЗАГ-GДЕТ)-CОТХ[((GЗАГ K1*K2)-GЗАГ)α+(GЗАГ-GДЕТ)]+ ЕН* *GЗАГ*КСК
Для удобства вычисления числовые значения параметров входящих в формулу записывают в таблицу.
Способ получения заготовок
Параметры входящие в формулу
В результате анализа получилось что литьё в оболочковые формы имеет меньшие приведенные затраты. Следовательно необходимо выбрать именно этот метод изготовления заготовки.
Определение положения отливки в форме и конфигурации плоскости разъёма.
Так как заготовка имеет вертикальную форму то её следует располагать в вертикальном положении.
Выбирается вертикальная плоскость разъема.
Разделение поверхностей элементов на виды.
Поверхности и элементы получаемые литьём окончательно: все внешние поверхности крышки кроме торцевых.
Поверхности отливки требующие дополнительной механической обработки: внутренняя поверхность крышки внешние торцевые поверхности отверстия под крепления и шпильки.
Поверхности не получаемые литьём:
- отверстие 36 под сальниковую набивку
- отверстия 12 под штифты
- отверстия 16 под крепление к корпусу
Определение класса точности размеров и массы ряда припусков.
Класс точности размеров и припусков зависит от способа литья класса материала и габаритного размера отливки. Дополнительно к указанным факторам по ГОСТ 26645-85 включены исходные факторы – тип производства и степень сложности отливки. По табл. 2.3 [1] класс точности размеров – 6 ряд припусков – 2.
Назначение шероховатости поверхностей отливки.
Параметр шероховатости отливки определяются способом литья материалом отливки и другими элементами технологического процесса литья по табл. 2.6 [1].
Определение предельных отклонений смещения элементов
и коробления отливки.
Предельные отклонения смещения назначаются только на те элементы отливки (и их размеры) которые формируются в разных частях литейной формы.
Δс=03 мм [1 таб.2.7]
Степень коробления определяют в зависимости от коэффициента “удлиненности” отливки Ку по таблице 2.8 [1].
Коэффициент “удлинённости” рассчитывают по формуле:
Ку=B(d h t)minL(Dh)max
L(Dh)max – максимальный габаритный размер мм.
Ку=12108=011 => степень коробления – 7.
Предельные отклонения коробления элементов отливок не должны превышать ΔК=±024 (табл. 2.9 [1]).
Назначение основных и дополнительных припусков на механическую
обработку поверхностей отливки.
Основные припуски в зависимости от допуска на размер и ряда припуска назначают для каждого размера индивидуально по табл. 2.10 [1]:
– 16 мм 108 + 13 мм 40 +13 мм 36 – 16 мм.
Дополнительный припуск назначаться не будет т.к. его назначают если наибольшее из предельных отклонений (ΔК Δс) превышает половину допуска на соответствующий размер отливки.
Назначение литейных уклонов на поверхности отливки.
Литейные уклоны назначаются на поверхности отливки перпендикулярные плоскости разъема руководствуясь ГОСТ 3212-80.
Установление радиусов закруглений.
Радиусы закруглений наружных и внутренних углов отливки назначаются по табл. 2.16[1]. Так минимальные радиусы:
для внутренних углов Rв = 3 мм;
для наружных углов Rн – 2 мм.
Определение фактической массы отливки и коэффициента использования материала.
Фактическая масса отливки (определим с помощью программы КОМПАС)
Коэффициент использования металла определяется по общеизвестной формуле:
КИМ=GДЕТGОТЛ=3.64.8=075Заключение.
В курсовой работе была проанализирована конструкция гидроаппарата клапанного его технологичность и назначены технические требования. Также выбран материал на деталь – Сталь 35Л.
В результате анализа различных способов производства заготовок определено что наилучшим способом ее производства для проектируемой детали является литье в оболочковые формы. Несмотря на высокую себестоимость получения заготовки этим способом он обеспечивает требуемую точность размеров достаточно высокий коэффициент использования материала - 075 шероховатость поверхностей чем позволяет уменьшить последующую механическую обработку. В итоге это приводит к повышению производительности и снижению себестоимости готовой детали.
Затем была спроектирована заготовка с учетом выбранного способа литья были назначены припуски на последующую механическую обработку.
Лукин Л.Л. Выбор способа литья и проектирование отливок: Методическое и справочное пособие к выполнению практических занятий. - Изд. 3-е дополн. Ижевск: Изд-во ИжГТУ. - 2003. - 64 с.
Лукин Л.Л. Выбор и экономическая оценка рациональной заготовки: Методическое и справочное пособие к выполнению практических занятий.- Изд.3-е дополн. Ижевск: Изд-во ИжГТУ.-2003.
Афонькин М.Г. Магницкая М.В. Производство заготовок в машиностроении. – Л.: Машиностроение 1987.
отливка Лаптева.cdw

Сталь 35Л ГОСТ 977-88
Литье в оболочковые формы.
Точность отливки 4-5-4-2 ГОСТ26645-85.
Неуказанные литейные уклоны 1
Неуказанные радиусы закруглений: наружных углов Rн - 2мм
внутренних Rв - 3мм.
Технические Требования к отливке по ТУ 26-17-058-89.
Размеры для справок.
Рекомендуемые чертежи
- 09.10.2018
Свободное скачивание на сегодня
Обновление через: 11 часов 34 минуты
- 23.08.2014
- 22.08.2014