Проектирование технологического процесса по изготовлению детали Шестерня




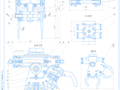
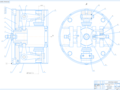
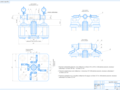
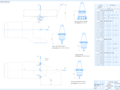
- Добавлен: 24.01.2023
- Размер: 363 KB
- Закачек: 1
Описание
Состав проекта
![]() |
![]() ![]() ![]() ![]() |
![]() ![]() ![]() ![]() |
![]() ![]() ![]() ![]() |
![]() ![]() ![]() ![]() |
![]() ![]() ![]() |
![]() ![]() ![]() ![]() |
![]() ![]() ![]() ![]() |
Дополнительная информация
Схватец.cdw

подвески колёсного тягача
относительно продольной оси -180
относительно поперечной оси -
Наибольшая ошибка позиционирования-
захватное устройство
ХАРАКТИРИСТИКА ЗАХВАТНОГО УСТРОЙСТВА
Номинальная грузоподъемность-40кг.
Наибольшее угловое перемещение :
Время зажима разжима-1с
Диапазон размеров захватываемых деталей-25-80 мм
Давление пневмоприводов -P=0.5-0.6 МПа
Резьбы выполнить по 7H
Сварные швы по ГОСТ 5264-80.
Нерабочие поверхности красить в зелёный цвет
эмалью ПФ-223 ГОСТ 14923-78.
наладка 005(фрезерн)2.cdw

Цикл оьработки: 0-1-2-1-0.
Цикл обработки: 0-1-2-1-0.
Сверло 2301-1764 ГОСТ 12121-77
Цикл обработки: 0-1-2-1-0.
Зенкер 2301-1764 ГОСТ 12489-71
Цикл обработки: 0-1-3-1-0.
Зенковка 158.2353-2059
Компоновка РТК.cdw

МОД.СМ40 Ф2.80.01 И СТАНКА МОД.16К20Ф3
Промышленный робот мод. СМ40 Ф2.80.01.
Токарный патронно-центровой станок
Магазин-накопитель заготовок.
Устройство приёма деталей (тара).
Устройство управления промышленным роботом
Производственная площадь S=23 м
Производительность РТК Q=137 штсмену
Техническая характеристика робота
Грузоподъемность 40кг
Число степеней подвижности (без захватного устройства) 4
Число рук (захватных устройств на руку) 2
Тип привода - гидравлический.
Управление - позиционное.
Число программируемых координат 3
Способ программирования перемещений - обучение.
Вместимость памяти системы 51
Погрешность позиционирования 1мм.
Наибольший вылит руки R 1900мм
Деталь обрабатываемая на РТК
контр.приспособление.cdw

Взаимная неперпендикулярность осей отверстий не более 0
на 100 мм. (Абсолютная разность показаний
индикатора I на длине 300 max - не более 0
Взаимное непересечение осей отверстий с точностью 0
(Абсолютная разность показаний индикатора II
Разность размеров от оси шлицевого отверстия до проушин не более 0
мм. (Абсолютная разность показаний
индикатора III не более 0
Обработать в одну плоскость (в сборе)
Записка.doc
Курганский Государственный Университет
Кафедра «Технологии машиностроения»
Расчетно-пояснительная записка
Тема: «Проектирование технологического процесса по изготовлению детали «шестерни».
Студент группы Т-4110 .
Доцент канд.техн.наук .
Ученое звание ученая степень Фамилия И.О.
Технологическая часть
1. Определение типа производства .
2. Анализ технологичности детали
3. Анализ базового технологического процесса
5. Разработка маршрутного и операционного технологических процессов
6. Расчет припусков
7. Расчет режимов резания
8. Техническое нормирование операций
9 Технико-экономическое обоснование проектного технологического процесса
10. Проектирование инструментальных наладок
Конструкторский раздел ..
1. Проектирование станочных приспособлений .
Машиностроение – одна из важнейших отраслей промышленности. Её основная продукция – машины различного типа и назначения которые обслуживают все отрасли народного хозяйства. Рост промышленности и народного хозяйства а так же темпы перевооружения их новой техникой в значительной степени зависят от уровня развития машиностроения.
Технический прогресс в машиностроении характеризуется не только улучшением конструкции машин но и непрерывным совершенствованием технологии их производства. В настоящее время важно качественно дешево и в заданные сроки с минимальными затратами живого и овеществленного труда изготовить машину применив современное высокопроизводительное оборудование инструмент технологическую оснастку средства механизации и автоматизации производства. От принятой технологии производства во многом зависят долговечность и надежность работы выпускаемых машин а также экономика их эксплуатации. Совершенствование технологии машиностроения определяется потребностями производства необходимых обществу машин.
Теоретические разработки и практика показали что в условиях единичного мелкосерийного и серийного производства характерного для 80% машиностроительных и приборостроительных предприятий наиболее рациональным является организация группового производства базирующегося на унификации его объектов технологических процессов и оснастки а также на создании подетально-специализированных участков и многономенклатурных групповых поточных и автоматизированных линий. Групповое производство дает возможность наиболее полно осуществлять работы по механизации и автоматизации оборудования и труда. Особенно эффективно его применение в условиях концентрации производства и создании объединений.
Сегодняшними требованиями к машиностроению являются создание высоко производительных машин и оборудования снижение их материало- и энергоемкости внедрение малоотходных и безотходных технологических процессов уменьшение трудоемкости изготовления продукции за счет широкого внедрения различных средств автоматизации и механизации в том числе робототехники ГАП.
Весьма актуальна проблема повышения и технологического обеспечения точности в машиностроении. Точность в машиностроении имеет большое значение для повышения эксплуатационных качеств машин и для технологии их производства. В зависимости от потребности в той или иной продукции машиностроения существуют три вида серийности производства:
У каждого из трёх типов производств своя заготовительная технология своё оснащение оборудованием и своя организация производства.
Задачи дипломного проектирования – выполнить комплекс конкретных прикладных и теоретических разработок в области машиностроительных производств. В дипломном проекте рассматриваются операции в двух альтернативных вариантах с расчетами сравнительной экономической эффективности; выполняются необходимые расчеты при проектировании станочного приспособления.
Приобретаются практические навыки решения различных технологических задач подготовки производства деталей машин и разработки технической документации. Закрепляется умение пользоваться справочной литературой стандартами и другой литературой.
Исходя из проблем обозначенных выше в данном дипломном проекте была рассмотрена тема «Проект участка на базе станков с ЧПУ по изготовлению деталей трансмиссии транспортной машины».
Технологический раздел.
1. Определение типа производства.
Важным этапом в разработке технологии изготовления деталей является определение типа производства.
В зависимости от широты номенклатуры регулярности и объема выпуска продукции различают следующие типы производства: единичное серийное массовое.
Тип производства по ГОСТ 3.1121-84 характеризуется коэффициентом закрепления операций (Кзо):
Кзо=1 – массовое производство;
Кзо10 – крупносерийное производство;
Кзо20 – среднесерийное производство;
Кзо40 – мелкосерийное производство;
Кзо – единичное производство.
Тип производства определяем приближенно по таблице 4.1 12.
Исходные данные (деталь «Полуось»):
- годовой объем выпуска N=7200 шт.
Тип производства – среднесерийное.
В производство запускают партию деталей в размере:
где - число запусков в год
Установив тип производства можно приступить к анализу технологичности изделия выбору заготовки и оборудования и т. д.
2. Анализ технологичности детали.
Обработка конструкции детали на технологичность – это комплекс мероприятий предусматривающих взаимосвязанные решения конструкторских и технологических задач направленных на повышение производительности труда снижение затрат и сокращение времени на изготовление изделия при обеспечении необходимого его качества.
Оценка технологичности проводится качественно и количественно с расчетом показателей технологичности по ГОСТ 14.201-83.
Деталь подвергаемая обработке резанием будет технологична в том случае когда ее конструкция позволяет применять рациональную заготовку форма и размер которой максимально приближены к форме и размерам деталей. К основным требованиям технологичности можно отнести: обоснованный выбор материала детали обеспечение жесткости конструкции сокращение числа установов заготовки при обработки простота формы поверхностей подлежащих обработке возможность использования стандартизованных и нормализованных измерительных вспомогательных режущих инструментов и т.д.
Деталь «Полуось» удовлетворяет всем перечисленным выше требованиям технологичности.
Количественная оценка технологичности проводится по показателям:
- коэффициент использования материала:
- коэффициент точности обработки
где - средний квалитет точности обработки детали по всем поверхностям.
- коэффициент шероховатости поверхности.
где - среднее числовое значение параметров шероховатости всех поверхностей детали.
Данные анализа рабочего чертежа детали «Полуось».
Наименования поверхностей
Количество поверхностей
Параметр шероховатости мкм
Наружные поверхности:
Шлицевая поверхность 50
Широкий паз (162 мм)
Сравнивая полученные показатели с нормативными () можно установить что деталь «Полуось» технологична как по качественной так и по количественной оценке.
Методика анализа детали на технологичность произведена по рекомендациям 12.
3. Анализ базового технологического процесса.
Общая последовательность обработки в базовом технологическом процессе составлена правильно. Сначала обрабатываются технологические базы затем ведется обработка основных и вспомогательных поверхностей.
После операций механообработки следует промывка и контроль.
Технологические базы выбраны правильно соблюдаются принципы совмещения и постоянства баз.
Режимы резания указанные в базовом технологическом процессе соответствуют рекомендуемым в справочной литературе.
Достаточно рационально используются станочные установочно-зажимные приспособления.
В процессе анализа выявлена недостаточная концентрация операций и технологических переходов. Предлагается объединить операции которые выполняются на одинаковом оборудовании в которых используется одно приспособление что позволяет уменьшить штучное время на изготовление детали а также уменьшить количество установов.
Недостатком базового технологического процесса является использование станков с ручным управлением. Предлагается заменить часть оборудования с ручным управлением на станке с ЧПУ.
Рациональным методом получения данной заготовки при котором форма и размеры детали были бы максимально приближены к форме и размерам заготовки в условиях среднесерийного производства будет являться горячая штамповка.
Получим заготовку на кривошипном горячештамповочном прессе (КГШП) так как он обладает высокой производительностью дает высокую экономию металла позволяет изготовить детали к которым предъявляются высокие требования по точности и технологичности. При горячей штамповки структура материала заготовки получается более однородной ее размеры стабильны а конфигурация близка к конфигурации детали.
Приблизительную стоимость заготовки рассчитываем по методике изложенной в 12.
где – базовая стоимость одной тонны заготовок;
- массы заготовки и детали соответственно;
– коэффициенты зависящие соответственно от класса точности группы сложности массы марки материала и объема производства.
5. Разработка маршрутных и технологических процессов.
Разработка маршрутных и операционных технологических процессов механической обработки является основой данного проекта. От правильности и полноты разработки технологического процесса во многом зависит организация производства и дальнейшие технико–экономические показатели.
Технологический процесс представляет собой совокупность различных операций в результате выполнения которых изменяется форма размеры выполняется соединение деталей в сборочные единицы и изделия осуществляется контроль требований чертежа и технических условий. Исходными данными являются рабочий чертеж детали анализ служебного назначения заготовка тип производства.
Маршрутный технологический процесс составляется на основе типового технологического процесса. Изготовление деталей данного типа (детали относятся к типу валов) осуществляется в следующей последовательности 16:
Подрезка торца и создание центровых конусных отверстий.
Черновая обработка первой а затем второй половины детали на токарной операции.
Чистовая обработка первой а затем второй половины детали на токарной операции.
Черновая и чистовая обработка фасонных поверхностей: нарезание зубьев шлицев и т.д.
Выполнение операций по обработке второстепенных поверхностей: сверление отверстий нарезание в них резьбы обработка шпоночных каналов и т.д.
Термическая обработка детали и отдельных ее поверхностей.
Зачистка центровых отверстий (при необходимости).
Черновое и чистовое шлифование внутренних и наружных цилиндрических и конических поверхностей.
Чистовое шлифование фасонных поверхностей.
Доводка особоточных поверхностей.
Современные металлорежущие станки с ЧПУ обладают высокой жесткостью что позволяет совмещать черновую и чистовую обработку детали в одну операцию.
На основании принятого варианта маршрутного технологического процесса производится выбор основного технологического оборудования подробно разрабатывается содержание операций: выбор технологических баз; выбор технологической оснастки; определение рациональной последовательности и содержания технологических переходов; расчет припусков; расчет режимов резания; техническое нормирование операций разработка инструментальных наладок.
При выборе конкретной модели станка следует учитывать следующие рекомендации:
Соответствие габаритных размеров заготовки размером рабочей зоны станка.
Соответствие точности и качества обрабатываемой детали точностным параметром станка.
Соответствие оптимальных режимов и производительности обработки мощности жесткости и производительности станка.
Соответствие схемы построения операции обработки детали технологическим возможностям станка. 30
Выбор технологических баз имеет первостепенное значение при проектировании технологических процессов. При выборе баз учитывается класс детали вид операции точность и производительность обработки. Технологические базы должны быть выбраны так чтобы обеспечивать устойчивое и однозначное положение заготовки на станке или в приспособлении а также надежность ее закрепления с минимальными деформациями. Погрешность установки должна быть исключена или сведена к минимуму. При выборе технологических баз необходимо стремиться к принципу постоянства и совмещения баз.
Содержание технологических переходов и их последовательность определяется многими факторами: формой размерами и точностью обрабатываемых поверхностей величиной припуска и др. при проектировании операционной технологии выбор метода обработки отдельных поверхностей и числа необходимых переходов производится на основе таблиц экономической точности обработки.
Эффективность использования станков с ЧПУ во многом зависит от правильного выбора станочных приспособлений режущего вспомогательного инструмента и др.
К приспособлениям для станков с ЧПУ предъявляют ряд требований:
Полная и точная ориентация заготовки относительно системы координат станка возможность контроля ее положения на этапах наладки и подналадки.
Повышенная точность и жесткость приспособлений для обеспечения высокой точности обработки при максимальном использовании точности станка.
Возможность быстрой переналадки установочных и зажимных элементов приспособления при переходе на обработку новой партии заготовок.
Открытый подход инструмента к различным сторонам заготовки при одном ее установе.
К режущему инструменту для станков с ЧПУ предъявляются повышенные требования в отношении точности размеров геометрической формы качества затачивания стабильной стойкости а также требуется обеспечение предварительной (вне станка) настройка на заданные размеры точность настройки и жесткость контракции универсальность применения и т. д. Предпочтение отдается стандартному режущему инструменту.
К системе вспомогательного инструмента относятся: оправки втулки державки и т. п. Они должны обеспечивать установку разнообразных режущих инструментов на станок (в шпиндель магазин и т. д.); обеспечивать требуемые параметры точности жесткости и виброустойчивости и т. д.
Для станков с ЧПУ рекомендуется применять унифицированный1 вспомогательный инструмент. 30
Учитывая изложенные выше рекомендации и требования разрабатываем маршрутные и операционный технологические процессы изготовления деталей подвески колесного тягача которые представлены в комплектах технологической документации.
6. Технологические расчеты.
6. 1. Расчет припусков и операционных размеров.
Определение припусков аналитическим методом.
При проектировании технологических процессов изготовления деталей определяют промежуточные операционные и общие припуски. Промежуточный припуск – это припуск удаляемый при выполнении одного технологического перехода. Операционный припуск представляет собой сумму припусков на переходы механической обработки рассматриваемой поверхности одной технологической операции. Общий припуск определяется суммированием операционных припусков технологического процесса от исходной заготовки до готовой детали.
Методика расчета припуска изложена в 4. Рассчитаем припуски на размеры 65js6(±00095); 226±058.
Пользуясь рабочим чертежом детали и картами технологического процесса механообработки записать в расчетную карту обрабатываемые элементарные поверхности заготовки и технологические переходы обработки в порядке последовательности их выполнения по каждой элементарной поверхности от черновой заготовки до окончательной обработки.
Записать значения Rz Т и ρ.
Определить расчетные минимальные припуски на обработку по всем технологическим переходам.
Записать для конечного перехода в графу «Расчетный размер» наименьший предельный размер детали по чертежу.
Для перехода предшествующего конечному определить расчетный размер прибавлением к наименьшему размеру по чертежу расчетного припуска .
Последовательно определить расчетные размеры для каждого предшествующего перехода прибавлением к расчетному размеру расчетного припуска следующего за ним смежного перехода.
Записать наименьшие предельные размеры по всем технологическим переходам округляя их увеличением расчетных размеров.
Определить наибольшие предельные размеры прибавлением допуска к округленному наименьшему предельному размеру.
Записать предельные значения припусков как разность наибольших предельных размеров и как разность наименьших предельных размеров предшествующего и выполняемого переходов.
Определить общие припуски и суммируя промежуточные припуски на обработку.
Проверить правильность расчетов по формулам:
Определить общий номинальный припуск по формулам:
где - нижнее отклонение размера заготовки и детали мкм.
Последовательная обработка противоположных или отдельно расположенных поверхностей:
Обработка наружных или внутренних поверхностей:
где Rz – параметр шероховатости мкм (табл. 4.3 4.4 );
Т – величина дефектного слоя мкм (табл. 4.3 4.4 4);
ρ – пространственное отклонение мкм (табл. 4.3 4.4 4);
– погрешность установки.
Все расчёты выполняем с помощью табличного процессора “EXCEL” пакета «Microsoft Office XP».
Результаты вычислений представлены в таблице 2.2.
Припуски на обработку остальных поверхностей назначаются табличным методом по 27.
Чертеж заготовки представлен в комплекте технологической документации.
6. 2. Расчет режимов резания.
Расчет режимов резания производится по методике изложенной в 28.
При назначении режимов резания учитывается характер обработки тип и размер инструмента материал его режущей части материал и состояние заготовки тип оборудования.
Определим режимы резания для 010 токарной с ЧПУ операции.
Точение черновое (резец Т5К10 ГОСТ 21151-75).
где Сv m х y – коэффициенты учитывающие вид обработки материал режущей части резца и характеристику подачи;
Сv =340; m=02; х=015; y=045;
Расчет припусков и предельных размеров.
Технологические переходы обработки поверхностей
Элементы припуска мкм
Расчетный припуск () мкм
Предельный размер мм
Предельное значение припусков мкм
Номинальный припуск мм
T –стойкость инструмента Т=50 мин.;
t – глубина резания t=13 мм;
S – подача резания ммоб S=08 ммоб; (табл. 1128)
- коэффициент на скорость резания;
где Кмv – коэффициент учитывающий материал заготовки;
KИV – коэффициент учитывающий состояние поверхности;
KПV – коэффициент учитывающий материал инструмента
Число оборотов шпинделя:
Где D – диаметр обрабатываемой поверхности мм;
Уточняем скорость резания.
где - коэффициенты учитывающие обрабатываемый материал материал рабочей части резца вид обработки.
– коэффициент на силу резания
где - коэффициенты учитывающие обрабатываемый материал геометрии резца на составляющие силы резания.
Аналогично рассчитывается радиальная сила осевая сила ( - тангенсальная сила).
Аналогично рассчитываются режимы резания при чистовой обработке детали и прорезании канавки. Результаты расчетов сведены в таблицу 2.3.
Определим режимы резания для 060 вертикально-фрезерной с ЧПУ операции.
Фрезерование (фреза 50 Р6М5 ГОСТ 17026-71).
Скорость резания (окружная скорость фрезы):
Режимы резания на 010 операцию.
Вид обработки и инструмент
Скорость резания V ммин
Мощность резания N кВт
Точение черновое (резец проходной Т5К10 ГОСТ 21151-75)
Точение чистовое (резец копировальный Т15К6 ГОСТ 20872-80)
Прорезание канавки (резец канавочный Т15К6 ТУ2-035-77)
где Сv m х y u р q – коэффициенты учитывающие материал режущей части инструмента вид обработки параметры срезаемого слоя.
Сv =467; m=033; х=05; y=05; u=01; р=01; q=045. (табл. 3928)
D – диаметр инструмента мм;
Т=180 мин; (табл. 4028)
Sz – подача на зуб фрезы Sz=02 ммзуб;
В – ширина фрезерования В=4 мм; (табл. 35 28)
Z – число зубьев фрезы Z=6;
Число оборотов фрезы определяем по формуле 2.9 учитывая что D – диаметр фрезы.
Уточняем скорость резания по формуле 2.10
Ср х y u w q – коэффициенты учитывающие вид (тип) инструмента материал режущей части инструмента.
Ср =682; х=086; y=072; u=01; w=0; q=086. (табл. 4128)
Величина остальных составляющих силы резания: горизонтальной (силы подачи) вертикальной радиальной осевой устанавливают из соотношения с главной составляющей по таблице 42 .
Крутящий момент на шпинделе:
Мощность резания определяется по формуле 2.12:
Сверление (сверло центровочное 8 Р6М5 ГОСТ 14952-75).
где Сv m y q – коэффициенты зависящие от вида обработки материала режущей части инструмента.
D – диаметр инструмента;
S=014 ммоб; (табл. 2528)
Т=25 мин; (табл. 3028)
Сv=70; m=02; y=07; q=04. (табл. 2828)
где - коэффициент учитывающий фактические условия обработки.
где Ср См х y q – коэффициенты учитывающие обрабатываемый материал инструмента.
См=00345; у=08; q=2. (табл.32 28)
Нарезание резьбы (метчик М14х15 Р6М5 ГОСТ 3266-81).
Скорость резания определяем по формуле 2.16 учитывая что
Сv=41; m=09; y=05; q=12; Т=90 мин. (табл. 2828)
Число оборотов метчика определяем по формуле 2.9:
Крутящий момент определяем по формуле 2.17 учитывая что:
См=0027; у=15; q=14. (табл.51 28)
Для остальных переходов 060 вертикально-фрезерной с ЧПУ операции режимы резания находятся аналогично рассмотренным выше примерам. Результаты расчетов сводим в таблицу 2.4.
Режимы резания на остальные операции рассчитываются по методике изложенной в 28 а также пользуясь рекомендациями 25.
6. 3. Техническое нормирование операций.
Техническое нормирование операций производим по методике изложенной в 27.
Пронормируем 010 – токарную с ЧПУ операцию.
где – штучное время обработки детали мин;
- основное время на операцию;
Глубина резания t мм
Ширина фрезерования В мм
Чмсло зубьев фрезы Z
Число оборотов фрезы
Радиаль-ная сила Рy Н
Крутящий момент Мкр Нм
Фрезерование фреза 50 Р6М5 ГОСТ 17026-71
Фрезерование фреза 28 Р6М5 ГОСТ 17026-71
Сверление сверло центровочное 8 Р6М5 ГОСТ 14952-75
Сверление сверло 125 Р6М5 ГОСТ 20696-81
Нарезание резьбы метчик М14х15 Р6М5 ГОСТ 3266-81
Режимы резания на 060 операцию.
- основное время на выполнение
где (L+l) – длина резания (с учетом длины врезания и перебега инструмента).
i – число рабочих ходов.
где - вспомогательное время мин;
- время на установку и снятие летали мин;
- время связанное с выполнением вспомогательных ходов и перемещений мин;
- время на обслуживание рабочего места и личные потребности (берется в процентах от оперативного времени ) мин.
Время работы станка по программе:
Штучно-калькуляционное время:
где - подготовительно-заключительное время
Для станка 16К20Ф3 ускоренное перемещение составляет 001 мин. На 100 мм принимаем время холостых ходов ; время поворота револьверной головки на одну позицию – 002 мин значит
Также во вспомогательное время входит время на выполнение следующих приемов:
- включить станок выключить – 003 мин;
- включить пульт лентопротяжного механизма выключить – 003мин;
- включить лентопротяжной механизм выключить – 003 мин;
- задвинуть оградительный щиток отвести – 003 мин;
- подвести инструмент в исходное положение отвести – 01 мин;
- перемотать перфоленту в исходное положение – 02 мин.
составляет 10% от (табл. 1327)
Рассчитаем подготовительно-заключительное время:
где - элементы подготовительно-заключительного времени мин.
включает приемы: (табл. 1327)
- получить наряд – 4 мин;
- инструктаж мастера ознакомление с документацией – 2 мин;
- получение инструмента – 7 мин;
- замена зажимного приспособления – 7 мин;
- установка перфоленты – 2 мин.
включает приемы: (табл. 1227)
- установка инструмента (одного) – 3 мин.
- время пробной обработки детали;
По формуле 2.25 учитывая что (см. подраздел 2.1) определяем :
Пронормируем 060 вертикально-фрезерную с ЧПУ операцию.
Для станка СВМ1Ф4 ускоренное перемещение составляет 004мин. На 100 мм принимаем время холостых ходов ; время смены инструмента 02 мин. значит
- перемотать перфоленту в исходное положение – 02 мин;
- установить координаты X Y Z – 06мин.
составляет 12% от (табл. 1327)
- установка и подключение приспособления – 12 мин;
- установка инструмента (одного) – 05 мин.
Пронормируем 085 – контрольную операцию.
Техническое нормирование контрольной операции производим по методике изложенной в 31.
Штучное время измерения детали:
где - сумма основного времени на выполнение приемов контрольной операции;
- соответственно время на обслуживание рабочего места время на отдых и личные потребности время на дополнительные функции данные времена берутся в % от и составляют:
К – поправочный коэффициент учитывающий выпуск изделий в месяц; К=1.
Техническое нормирование остальных операции производит аналогично по методике изложенной в 27 а также пользуясь рекомендациями 14.
7. Технико-экономическое обоснование проектного технологического процесса.
Целесообразность разрабатываемого технологического процесса механической обработки деталей определяется на основе сравнительной экономической эффективности двух вариантов: базового и проектного.
Расчет ведем по методике изложенной в 15.
Общим экономическим показателем эффективности варианта является величина годовой экономии на приведенных затратах
где - соответственно сумма годовых приведенных затрат базового и проектного варианта при выполнении равных объемов работы руб.
Сумма приведенных затрат по каждому варианту рассчитывается по формуле:
- годовая технологическая сибестоимость i-ой операции по вариантам руб.
где - нормативы затрат по заработной плате станочников наладчиков электронщиков рубч;
- нормативы затрат на амортизацию оборудования ремонт и электроэнергия рубч;
- нормативы затрат на амортизацию и ремонт приспособлений и рабочего инструмента рубч;
- годовые затраты на техническое обслуживание и ремонт устройств ЧПУ руб.;
- годовые затраты на амортизацию и содержание производственных помещений руб.;
- нормативный коэффициент эффективности капитальных вложений ;
- сумма годовых капитальных затрат на i-ой операции по вариантам руб.
где - расчетное количество станков требуемых для изготавления годового выпуска деталей на
- номинальные вложения в оборудование (технологическое подъемно-транспортное средства оснащения и контроля);
- стоимость производственного помещения занимаемого станком на i-ой операции.
- стоимость управляющих программ для операций выполняемых на станках с ЧПУ.
Расчет производим с применением ЭВМ по программе разработанной выпускником кафедры «Технология машиностроения» Котохиным Д.И.
Сравнение вариантов технологического процесса.
а) годовой объем выпуска: 7200 шт.;
б) базовый технологический процесс:
Технол. себестоимость руб.
Приведенные затраты руб.
в) проектный технологический процесс:
Величина годовой экономии: 751312510 руб.
Примечание. Расчёт произведён в ценах 1992 года.
8. Проектирование инструментальных наладок.
Для иллюстрации технологического процесса обработки детали «Полуось» на 005 – фрезерно-центровальной 010 – токарной с ЧПУ 060 – вертикально-фрезерной с ЧПУ 065 – горизонтально-фрезерной с ЧПУ операциях спроектированы инструментные наладки (инструментные наладки представлены в графической части дипломного проекта).
На чертежах инструментных наладок показывается: обрабатываемая деталь в рабочем положении; установочные зажимные направляющие элементы станочного приспособления; рабочий (режущий инструмент) с вылетами по координатным осям а также вспомогательный инструмент; схемы движения режущего инструмента; размеры обробатываемых поверхностей шероховатость отклонение формы и взаимного расположения поверхностей; таблица с данными по оборудованию режущему инструменту режима обработки нормам времени а также в таблице указываются координаты опорных точек движения инструмента.
Конструкторский раздел.
1. Проектирование станочных и контрольного приспособлений.
Проектируемые приспособления должны обеспечивать:
- требуемую производительность;
- необходимую точность обработки и измерений;
- удобство обслуживания установки и снятия деталей;
- быстрое и надежное удаление стружки.
Приспособление фрезерное.
Спроектируем станочное приспособление на 060 вертикально-фрезерную с ЧПУ операцию.
Любое приспособление состоит из трех основных конструктивных элементов: корпусных установочных и зажимных.
Описание приспособления.
Приспособление состоит из корпуса 1. заготовка устанавливается во втулке 6 и 8 фиксируется от поворота винтами 20. зажим осуществляется с помощью прихватов 9 которые работают от двух гидроцилиндров 25. для зажима заготовки в полость гидроцилиндра подается под давлением масло а для разжима – воздух. Привязка инструмента к приспособлению осуществляется обкатыванием по торцу и внутренней поверхности втулки 6.
Центрирование приспособления на столе станка зажима и т. д. в приспособлении применяются болты гайки шайбы пружины шпильки и др.
Подбор рабочей жидкости (масло воздух) осуществляется через систему труб. Подключение приспособления к гидростанции и компрессору осуществляется через штуцера 2 и 3.
Расчет приспособления.
При сверлении отверстия 125 мм на 060 вертикально-фрезерной с ЧПУ операции возникает наибольшая мощность резания (см. таблицу 2.4) значит расчет приспособления проведем при сверлении. На рисунке 3.1 представлена расчетная схема.
Условие неподвижности заготовки при сверлении:
где К – коэффициент заноса К=3;
- крутящий момент при сверлении (см. таблицу 2.4);
Р – сила зажима заготовки Н;
- коэффициент трения ;
D=704 мм (см. рисунок 3.1).
Рис. 2.1 Расчетная схема.
Из формулы 3.1 найдем силу зажима заготовки:
Сила зажима заготовки от одного гидроцилиндра: Р=3000 Н.
Сила на штоке гидроцилиндра:
где - геометрические параметры приспособления
r=25 мм (стр. 173 3)
Определим диаметр штока гидроцилиндра из уравнения (зависимости) для нахождения действительной силы на штоке:
где р – давление рабочей жидкости в сети МПа;
d – диаметр штока гидроцилиндра мм.
Принимаем гидроцилиндр с d=50 мм по ГОСТ 19899-74 использование данных гидроцилиндров позволит сохранить неизменное однозначное положение заготовки в процессе обработки а действительная сила на штоке по формуле 3.4 равна:
Спроектируем станочное приспособление на 010 и 070 токарную с ЧПУ операцию.
Деталь на данных операциях устанавливается (базируется) по центровым отверстиям и торцу фланца детали.
Планшайба крепится к шпинделю болтами 3 ее центрирование относительно шпинделя производится по конусному отверстию. Вращательный момент от шпинделя на планшайбу передается через платик 2 и болты 4 а непосредственно на деталь через бобышки планшайбы.
Производить расчет бобышек планшайбы на срез (смятие) не целесообразно т. к. из конструкции планшайбы видно что она обладает достаточной жесткостью и прочностью.
Державка выглаживателя.
На 070 токарной с ЧПУ операции производят процесс выглаживания для выглаживания наружных поверхностей с упругим закреплением инструмента используют пружинную оправку которую устанавливают и закрепляют в резцедержатель токарного станка. 19.
В корпусе 1 по скользящей посадке установлен шток 3. левый конец штока 3 предназначен для крепления выглаживающего инструмента 8. давление инструмента на обрабатываемую деталь обеспечивается пружиной 9.
Фиксация углового положения штока 3 осуществляется по средствам винта 7. настройка инструмента на заданное усилие производится регулировочной гайкой 2. усилие прижима контролируется по вылету правого конца штока относительно штока гайки 2.
В процессе выглаживания основную роль играет правильно выбранное усилие натяга:
где В – коэффициент зависящий от вида обработки исходных поверхностей (для точения - 12);
R – радиус инструмента мм;
- предел текучести материала МПа;
- шероховатость исходной поверхности по параметру мм;
Принимаем Р=150 Н (15 кгс).
Для обеспечения усилия натяга подберем пружину 9 – пружина 7039-2030 ГОСТ 13165-67 которая обеспечит усилие натяга (максимальное) до 600 Н (60 кгс).
Контрольное приспособление.
Длля контроля технических требований предъявляемых к детали (симметричность расположения пазов 32Н8 и 162К7 относительно оси детали – 015 мм; допуск перпендикулярности поверхности относительно оси детали 01100 мм; допуск параллельности боковых сторон паза 32Н8 – 015 мм) спроектировано контрольное приспособление.
Приспособление состоит из корпуса 1. деталь устанавливается во втулке 8 и центр 12 угловое положение детали определяется винтами 27. датчик цифровых измерений устанавливается в державку 10.
Измерение параметров производится косвенно через планки 9 путем перемещения державки 10 вдоль планок 4 и 5 (анализируется разность показаний датчика 33).
Рассчитываем контрольное приспособление на точность по методике изложенной в 5.
Суммарная погрешность контрольного приспособления может быть рассчитана по формуле:
Систематические погрешности учитываются при настройке контрольного приспособления они исключаются из расчета.
Пари данной схеме установки и закрепления детали погрешность базирования равна половине максимального зазора между деталью и втулкой 8 а погрешность закрепления
Погрешность передаточных устройств .
Погрешность изготовления эталона .
Погрешность метода измерения при использовании датчика .
Суммарная погрешность не должна превышать 20 30% допуска контролируемого параметра.
Произведенный расчет показал что точность приспособления позволяет контролировать технические требования предъявляемые к детали.
Чертежи станочных и контрольного приспособления представлены в графической части дипломного проекта.
наладка 005(фрезерн)1.cdw

Сверло 2300-7005 ГОСТ 886-77
Цикл обработки: 0-1-2-3-4-0.
Цикл лбработки: 0-5-6-5-7-8-7-9-10-9-0.
Метчик 2620-1419Н2 ГОСТ 3266-81
Цикл обработки: 0-5-13-5-9-14-9-0.
Цикл обработки: 0-5-11-5-9-12-9-0.
приспособление.cdw

Рекомендуемые чертежи
- 24.01.2023
- 05.01.2022
- 24.01.2023
- 24.01.2023
- 04.06.2017
Свободное скачивание на сегодня
Другие проекты
- 25.09.2011