Проектирование технологического процесса изготовления детали типа Цилиндр




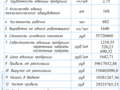
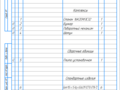
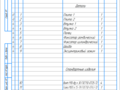
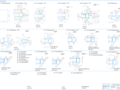
- Добавлен: 24.01.2023
- Размер: 5 MB
- Закачек: 1
Описание
Состав проекта
![]() |
![]() |
![]() ![]() ![]() ![]() |
![]() |
![]() |
![]() ![]() ![]() ![]() |
![]() ![]() ![]() ![]() |
![]() |
![]() ![]() ![]() ![]() |
![]() ![]() ![]() ![]() |
![]() ![]() ![]() ![]() |
![]() |
![]() |
![]() |
![]() ![]() ![]() ![]() |
![]() ![]() ![]() ![]() |
![]() ![]() ![]() ![]() |
![]() ![]() ![]() ![]() |
![]() ![]() ![]() ![]() |
![]() |
![]() ![]() ![]() ![]() |
![]() ![]() ![]() ![]() |
![]() |
![]() |
![]() ![]() ![]() |
![]() ![]() ![]() ![]() |
![]() ![]() ![]() ![]() |
![]() |
![]() |
![]() ![]() ![]() ![]() |
![]() |
![]() |
![]() |
![]() |
![]() ![]() ![]() ![]() |
![]() |
![]() ![]() ![]() |
![]() ![]() ![]() ![]() |
![]() |
![]() ![]() ![]() ![]() |
![]() |
![]() |
Дополнительная информация
СБОРКА патрон (Старый).cdw

Неуказанные предельные отклонения H14
Остальные технические требования по ОСТ1.51896-82
Размерный анализ.cdw

Оп. 30 Слесарная ТЭМ
Оп 40 Термообработка
Оп.10 Токарная с ЧПУ
Оп. 20 Токарная с ЧПУ
Оп.50 Токарная с ЧПУ
Оп.60 Токарная с ЧПУ
Оп. 110 Шифовалная с ЧПУ
Оп. 120 Шифовалная с ЧПУ
РА Схема.frw

ТЭП ЛИСТ.cdw

Себестоимость единицы продукции:
Средняя зарплата рабочего:
рентабельность производ. капитала
рентабельность продукции
Технико-экономические
Технико-экономические показатели цеха
Годовая приведенная программа
Трудоемкость еденицы продукции
Выработка на одного работающего
Стоимость основного капитала
Цена единицы продукции
Прибыль от реализации
Выручка от реализации
Наименование показателей
Тех процесс Новый+.cdw

Оп. 30 Слесарная ТЭМ
Оп 40 Термообработка
Оп. 125 Магнитный контроль
Оп. 126 Дифектоскопия
Оп. 130 Никелирование
Оп. 141 Маркирование
Оп. 150 Гидроиспытания
Оп. 180 Консервация и упаковка
Оп.10 Токарная с ЧПУ
Оп. 20 Токарная с ЧПУ
Оп.50 Токарная с ЧПУ
Оп.60 Токарная с ЧПУ
Оп.70 Сверлильная с ЧПУ
Оп. 80 Фрезерная с ЧПУ
Оп. 90 Токарная с ЧПУ
Оп. 110 Шлифовальная с ЧПУ
Оп. 120 Шлифовальная с ЧПУ
Оп. 140 Полировальная
Заготовка.cdw

Приспособление для фрезерования.cdw

Остальные технические требования по ОСТ1.51896-82
чертеж цеха.cdw

- Токарный с ЧПУ 16К20Ф3C32
- Сверильно фрезерный с ЧПУ МА655А1
- Токарный с ЧПУ SPT-16NC
- Шлифовальный с ЧПУ Studer
Планировка механического
Магистральный проезд
Загрузочтое устройство СП1.spw

-8g х 65.66.019 ОСТ92-0718-72
-8g х 90.66.019 ОСТ92-0718-72
Винт М24-8g х 70.66.019 ОСТ92-0739-72
-6H.66.019 ОСТ92-0742-72
Шайба 92.7870-0392 ОСТ92-3541-74
Шайба 2 Н.24 х 6.02.Ст3кп.019 ГОСТ 13463-77
Шайба 2 Н.31 х 6.02.Ст3кп.019 ГОСТ 13463-77
Контрольное.cdw

Оп. 90 Токарная с ЧПУ
Т.Т. по ОСТ 1.51896-82
Применять с эталоном (L=49
и Индикаторной головкой МИК-1 ГОСТ 9696-82
Фреза клеиная.cdw

Остальные технические требования по ОСТ1.51896-82
Приспособление для фрезерования.spw

Фиксатор цилиндрический
Эксцентриковый зажим
Винт М10-8g х 30 ГОСТ92-0725-72
Тех процесс Старый 1+.cdw

Оп. 190 Дифектоскопия
Оп. 210 Никелирование
Оп. 220 Маркирование
Оп. 500 Контроль магнитопорошковый
Оп. 520 Гидроиспытание
Оп. 550 Консервация и упаковка
Оп. 300 Переникелирование
*-Размер обеспечить инструментом
Оп.10 Токарная с ЧПУ
Оп. 20 Токарная с ЧПУ
Оп.40 Токарная с ЧПУ
Оп.50 Токарная с ЧПУ
Оп. 5 Заготовительная
Оп. 80 Фрезерная с ЧПУ
Оп. 120 Токарная с ЧПУ
Оп. 160 Полировальная
Оп. 230 Шлифовальная
Оп. 240 Полировальная
Оп. 250 Шлифовальная
Оп. 360 Шлифовальная
Оп. 390 Шлифовальная
Оп. 430 Полировальная
Оп. 460 Шлифовальная
Оп. 470 Шлифовальная
Оп. 160 Шлифовальная
Оп. 310 Шлифовальная
Деталь Цилиндр.cdw

Штамповка или поковка 3гр. по ОСТ 1 90176-75.
Неуказанные пред.откл. размеров формы и расположения поверхн.
Фаски резьбы по ОСТ 1 00010-71
*Размер обеспечить инструментом
Толщину покрытия поверхн Л
Ш не контролировать.
Термообработать при 450 500
Контроль магнитопорошковый по 40ТУ-22.
Внутреннюю полость гидроиспытать топливом под давлением.
по ЭС-19301 в течение 5 10 мин.
Клеймить заоперационную приемку способом У
Маркировать шрифтом 3 5.
Допускается изготовлять из прутка по ТУ14-1-4608-89.
Контролировать на станке.
63126-4042 СБ.cdw

ТТ по ОСТ 1.51896-82
Приспособление отбалансировать с обрабарываемой деталью
за счет дет. поз. 2 и высверливания отв. в дет. поз 1;
Дисболанс не более 50гсм.
Применять с планшайбой 53999-139
и установочным шаблоном 63689-1267
Контрольное.spw

Оп. 90 Токарная с ЧПУ
Втулка для индткатора
Винт М8-8g х 28.66.019 ОСТ92-0728-72
Инструмент.frw

Фрера.spw

Записка_new_tsch-Versija_07-06-22.doc
по «Технологии машиностроения»
Технологическая часть.
1 Служебное назначение и конструктивно -технологическая 6
характеристика детали
1.1 Оценка технологичности детали табл.18
2 Список операций «существующий» техпроцесс табл.59
2.1 Список операций “Проектируемый» техпроцесс табл.6 10
3 Анализ «существующего» техпроцесса предполагаемые его изменения
в «проектном» варианте. 11
4 Выбор способа получения исходной заготовки12
5 ТЭМ. Термическое удаление заусенцев13
6 Расчет и назначение припусков на все поверхности
исходной заготовки. 15
7 Примеры расчета режимов резания.25
8 Примеры расчета технологических норм времени. 30
9 Выполнение проектно - точностных расчетов по:
разрабатываемому техпроцессу. 33
10 Расчет приспособления на точность49
11 Загрузочное устройство операция №10 «Токарная с ЧПУ»
11.1 Проектный расчет загрузочного устройства51
11.2 Описание работы загрузочного устройства52
12 Описание режущего инструмента - фрезы 53
13. Трехкулачковый самоцентрирующий патрон.54
Графический раздел. (см. чертежи)
2 Чертеж приспособления №1 операция № 10 «Токарная с ЧПУ»
3 Чертеж приспособления №2 операция № 80 «Сверлильно- фрезерная с ЧПУ»
4 Чертеж приспособления №3 операция № 90 «Токарная с ЧПУ»
5 Чертеж режущего инструмента
6 Чертеж загрузочного устройства
7 Чертеж «Существующий» техпроцесс
8 Чертеж «Проектный» техпроцесс
10 Чертеж «План цеха»
Экономика и организация производства.
2Общее описание предприятия. 59
3Исходные данные для проектирования60
5Производственный план62
5.1.Производственная программа продукции62
5.2.Обоснование типа производства и формы его организации62
5.3.Определение потребного количества оборудования63
5.4.Определение состава и численности работающих цеха (участка)65
5.5.Расчёт площади цеха.69
6.Основные технико-экономические показатели цеха 70
6.1Основные фонды цеха (основной капитал)70
6.2Себестоимость продукции71
6.2.1Затраты на основные материалы71
6.2.2Расчет фондов заработной платы рабочих72
6.2.3Расходы на содержание и эксплуатацию оборудования76
6.2.4Расчет общепроизводственных общехозяйственных
внепроизводственных расходов78
6.2.5Оборотные средства (оборотный капитал)79
6.2.6Производственный капитал80
7.Финансовы й план80
7.1.Расчёт плановой суммы балансовой прибыли80
7.2.Формирование баланса доходов и расходов81
7.3.График достижения безубыточности82
8.Рентабельность проекта82
9.ТЭП работы цеха.83
Проектирование цеха .
1.Исходные данные для проектирования84
2.Режим работы цеха и фонды времени работы оборудования и рабочих84
3.Технологические процессы и новая техника. Основные положения по организации производства на участке85
4.Расчет технологического оборудования86
5.Расчет количества оборудования цеха88
6.Расчет грузооборота механического цеха90
7. Выбор и расчет подъемно-транспортных средств91
8.Вспомогательные службы цеха92
9.Определение численности работающих97
10Расчет площадей промышленного корпуса99
11.Расчет площадей вспомогательного корпуса100
12.Выбор зданий для промышленного и вспомогательного корпусов101
13.План размещения оборудования участка101
14.Расчет энергетики цеха101
Исследовательский раздел.
Выполняется в соответствии с темой исследовательского раздела задания на дипломное проектирование. Оформление графики исследовательского
Раздел по охране труда и безопасности жизнедеятельности.132
Список использованной литературы153
Технологическая часть
1 Служебное назначение и конструктивная технологическая характеристика детали:
Направляющий пневмокалапана «Цилиндр» применяется в авиационном оборудовании и оборудовании на базе авиационного. «Цилиндр» работает в диапазоне температур -60 +200 °С. Конструктивно «Цилиндр» представляет собой тонкостенное тело вращения с центральным отверстием переходного диаметра. С одной стороны диаметр отверстия 30мм на глубину 39мм с другой стороны диаметр 40мм на глубину 29мм. Для отвода топлива «Цилиндр» имеет штуцер расположенного перпендикулярно оси вращения и смещенный вдоль оси вращения ближе к торцу с отверстием диаметром 40мм. «Штуцер» имеет центральное сквозное отверстие переменного диаметра. Отверстие диаметром 5мм и глубиной 20мм после чего переходит в отверстие диаметром 35мм. Для крепления «Цилиндра» в узле имеется два фланца по краям каждый с 4-мя отверстиями. Фланец1 со стороны малого отверстия имеет 4-е отверстия диаметром 85мм расположенных на диаметре 57мм. Фланец2 со стороны большого отверстия имеет 4-е отверстия с резьбой М8 на диаметре 73мм. Для уплотнения при установки «Цилиндра» в узле на его наружной поверхности со стороны торца с большим отверстием между торцом и фланцем располагается канавка для уплотнительного кольца. К изготовлению детали предъявляются высокие требования т.к. деталь работает в условиях перегрузок при вибрациях и повышенных температурах. Цилиндр» должен обладать низкой намагничеваемостью высокой прочностью и твердостью что должно соответствовать требованиям условий эксплуатации. Также предъявляются высокие требования к биению поверхности соосности и цилиндричности это обеспечивается производственным оборудованием представляющим собой высокоточные станки с ЧПУ и 100% контроль размеров после обработки важных поверхностей.
В качестве материала детали используем сплав ЭП678-ВД (03Х11Н10М2Т-ВД ТУ14-1-4608-89) . Основным свойством этого материала является высокая жаростойкость и жаропрочность.
«Термообработка» Таблица 1.
Температура и скорость нагрева
ЭП678-ВД (03Х11Н10М2Т-ВД)
Вакуум с остаточным давлением не выше 10-3 мм рт.ст.
До 400С со скоростью 100С в час далее произвольно под вакуумом до температуры менее 150С
Химический состав сплава ЭП678-ВД (03Х11Н10М2Т-ВД) в соответствии с ТУ14-1-4608-89 (в %)
«Химический состав » Таблица 2.
Основные механические свойства материала Таблица 3.
sв – временное сопротивление разрыву
s02 – предел текучести
d - относительное удлинение
y - относительное сужение
Качественная оценка технологичности детали. Конструкция детали достаточно проста и в упрощении не нуждается. Материал детали также не требует замены поскольку удовлетворяет требованиям к физическим свойствам материала. Ко всем поверхностям имеется свободный доступ инструмента. Для обработки штуцера необходима установка цилиндра на планшайбу.
«Количественная оценка технологичности конструкции » : Таблица 4.
Определение коэффициента точности:
Определение коэффициента шероховатости:
2. Список операций «существующий» техпроцесс Таблица 5.
Заполнение маршрутной карты
Контроль .Дефектоскопия
Контроль магниот порошковый
Консервация Упаковка
Список операций “Проектируемый» техпроцесс» Таблица 6
Сверл.- фрезерная с ЧПУ
Полировальная (Слесарная)
Маркирование (Слесарная)
*** Т штучное (Т шт.) принято условно потому что на практике оно замеряется по секундомеру работником БТЗ непосредственно во время выполнения операции.
3 Анализ существующего техпроцесса и предполагаемые его изменения в проектном варианте :
Анализируя существующий технологический процесс были сформулированы следующие замечания:
- Не применяются устройства позволяющие автоматизировать процесс установки заготовок даже на самых первых неответственных операциях (операции № 1020 )
- На сверлильных операциях № 60 применяются универсальные сверлильные станки с ручной установкой детали в кондуктор.
- Не применяются современные методы зачистки заусенцев
- Ручное нарезание резьбы на операции 120
- Оснастка применяемая в производстве увеличивает долю вспомогательного времени на операциях
- На 60 % операций применяется универсальное оборудование
Проведя анализ технологического маршрута обработки детали «Цилиндр» предлагаю следующие изменения:
- Максимально возможное применение станков с ЧПУ
- изменить размер заготовки по высоте с 80 -4 на 71 -05
- Объединение операций 90 100 и 140 . 90 100 и 140 . 90 100 и 140 .
- Сокращение количества оснастки и повышению качества обработки т.к. появляется возможность обработки за один установ.
- Применение патрона с пневмоприводом. и загрузочным устройством на операции № 1020
- Применить на слесарных операциях № 30100 установку ТЕМ
- Применение современного измерительного инструмента.
- на операции № 1020 заменить модель станка ЧПУ СТП-220 (дискретность перемещений по осям X = 0.005 мм Z = 0.01 мм) на 16К20Ф3С32 т.к у него дискретность перемещений по осям X Z = 0.001 мм
- Оснастить все станки с ЧПУ компьютерами в связи с этим появляется возможность создать компьютерную сеть для передачи управляющих программ и другой информации оперативного их редактирования; снимается вопрос ограничением по объему программы и по созданию архива программ и т.д. ( пример компьютерная сеть на «Авиадвигателе»)
4. Технико-экономическое обоснование способов получения исходной заготовки [1]:
Коэффициент использования материала по чертежу КИМ=012;
Масса детали m=056кг.заготовки m=479кг.
5. ТЭМ. Термическое удаление заусенцев
Устройство для термического удаления заусенцев с изделий
№2149088подачи заявки 1998.11.16
Изобретение относится к машиностроению и может быть использовано в частности для удаления с металлических поверхностей заусенцев остающихся на кромках после механической обработки. Повышение производительности и коэффициента использования вводимой в технологическую установку энергии а также защита окружающей среды от выбросов в атмосферу углекислого газа содержащегося в составе продуктов сгорания углеводородных топлив достигается тем что устройство состоит из рабочей камеры выполненной из верхней неподвижной части (2) имеющей нижний торец (Т) в виде наружного фланца и нижней подвижной части (1) выполненной в виде кольцевого пояса имеющего нижний торец в виде внутреннего фланца опирающийся на дно (4) имеющее каналы (5) для отвода продуктов сгорания из рабочей камеры в атмосферу через тракт (10) полость клапана (11) со сдвоенным плунжером и слой водного раствора щелочи.
6. Расчет припусков на операции механической обработки.
6.1.Расчет припуска на внутреннюю поверхность .
Суммарное значение Rz и Т характеризующее качество поверхности заготовок – штамповок составляет 300 мкм.
Кривизну заготовки при закреплении в трехкулачковом патроне и обточке внутренней поверхности определяем по формуле:
Dк – удельное значение кривизны (07) (табл. 4.8 [1])
Остаточное пространственное отклонение
после чернового растачивания:
после чистового растачивания:
после финишного растачивания:
где - коэффициент уточнения формы после обработки заготовки.(стр. 73 [1])
Погрешность установки заготовки на выполняемом переходе
eб – погрешность базирования
eз – погрешность закрепления
eпр – погрешность приспособления
Для чернового точения e=150 мкм (табл.28 [ ])
Для чистового точения e=50 мкм (табл. 28[ ])
Для финишного точения e=25 мкм(табл. 28[ ])
Технологические переходы обработки пов.
Элементы припуска мкм
Расчетный размер dр мм
Предельный размер мм
Предельные значения припусков мкм
Заготовка (штамповка)
Черновое растачивание
Чистовое растачивание
На основании записанных в таблице данных производим расчет минимальных значений межоперационных припусков пользуясь основной формулой (табл. 4.2[1])
Под черновое точение:
Под чистовое точение:
Под чистовое растачивание:
Максимальный размер детали после финишного растачивания:
Остальные расчетные размеры определяем последовательным вычитанием из расчетного размера расчетного припуска следующего за ним смежного перехода:
Наибольшие предельные размеры вычисляем прибавлением допуска к наименьшему предельному размеру:
Рассчитаем минимальное и максимальное значение припусков они равны разности наибольших и наименьших соответственно предельных размеров выполняемого и предшествующего переходов:
Общие припуски определяем путем суммирования промежуточных припусков (см. табл.).
6.2.Расчет припуска на наружную поверхность .
после чернового точения:
после получистового точения:
после чистового точения:
Для чернового точения e=200 мкм (табл.28 [ ])
Для чистового точения e=80 мкм (табл. 28[ ])
Для финишного точения e=40 мкм(табл. 28[ ])
Получистовое точение
Под получистовое точение:
Расчет припуска на наружную поверхность .
Погрешность установки заготовки на выполняемом переходе:
Для получистового точения e=80 мкм (табл. 28[ ])
Для чистового точения e=40 мкм (табл. 28[ ])
Минимальный размер детали после чистового точения:
Остальные расчетные размеры определяем последовательным прибавлением к расчетному размеру расчетного припуска следующего за ним смежного перехода:
Наибольшие предельные размеры вычисляем прибавлением допуска к наибольшему предельному размеру:
7. Примеры расчета режимов резания .
Операция № 10- переход «сверление отверстия 28 »
( «Токарная с ЧПУ» ).
Предварительная обработка отверстия –сверление до 25 под последующую расточку
Станок 16К20Ф3С32. Мощность двигателя = 5 квт
Обрабатываемый материал – сталь ЭП678У-ВД (03Х11Н10М2Т)
= 1000 МПа охлаждение - 5 % эмульсия
инструмент- сверло 25 быстрорежущая сталь Р18
Длина рабочего хода L px = L рез + y
Длина резания L рез = 76 мм
y= 16мм - длина довода врезания и перебега конус сверла
Подача на оборот инструмента S 0 =0.1 ммоб при d до 25 мм - 4
Vтабл =275ммин при подаче на оборот инструмента ммоб диаметре обрабатываемого отверстия d= 25 мм.
К1=07 при твердости обрабатываемого материала = 1000 МПа при работе инструментом из быстрорежущей стали.
К2=10 при использовании режущего инструмента из быстрорежущей стали Тр=100 мин;
К3=1 при отношении длины резания к диаметру до 5
Расчет числа оборотов шпинделя станка:
n =(1000 x 19.29) 3.14 x 26 =235 обмин
Операция № 80- переход «нарезание резьбы в отверстии 8 »
( «Сверлильно -фрезерная ЧПУ» ).
Станок МА655А1 Мощность двигателя = 10 квт
инструмент- машинный метчик 8 быстрорежущая сталь Р18
где V табл = 5 ммин при шаге резьбы мм и диаметре резьбы 8 мм
К v = 1 -для легированной стали
Принимаем v = 5 ммин;
n =(1000 x 5) 3.14 x 8 =199 обмин
принимаем n= 200 обмин согласно таблице оборотов для станка
Операция № 60- переход «точение 397 +0062 »
Станок 16К20Ф3С32 Мощность двигателя = 5 квт
инструмент- резец Т15К6 глубина резания до 1 мм.
Длина рабочего хода суппорта
Длина резания L рез =25 мм
Длина подвода и перебега мм при точении заготовок
L рх =25 + 6 = 31 мм
Подача суппорта на оборот шпинделя: S 0т = 0.3 ммоб для обработке стали и суммарной глубине резания до 2мм при чистовом точении .
S 0 = S 0т x K1 x K2 x K3 x K4 x K5 (стр. 239 [2] )
K1 – коэффициент учитывающий материал инструмента K1= 1
K2 – коэффициент учитывающий главный угол в плане K2= 1
K3 – коэффициент учитывающий диаметр отверстия - K3 = 07
K4 – коэффициент учитывающий состояние поверхности – K4= 1
K5 – коэффициент учитывающий обрабатываемый материал- K5= 09
S 0 = 03 х 1 х 1 х 07 х 1 х 09 = 018 мм об
где v табл = 155 ммин для точения твердосплавным инструментом с глубиной резания до 1 мм и подаче суппорта до 05ммоб
K1= 0.72 – по группе обрабатываемого материала
K2= 19- для обработки твердосплавным инструментом
K3 = 09 для точения диаметров менее 150 мм
v = 155 x 0.72 x 1.9 x 0.9 =190 ммин.
n =(1000 x 190) 3.14 x 397 =1524 обмин
На все оставшиеся переходы в операциях назначаем режимы резания :
растачивание черновое
растачивание чистовое
8. ПРИМЕРЫ РАСЧЕТОВ ТЕХНИЧЕСКИХ НОРМ ВРЕМЕНИ.
Технические нормы времени в условиях серийного производства устанавливаются расчетно-аналитическим методом определяется норма штучно-калькуляционного времени :
где - предварительно-заключительное время мин;
- количество деталей в партии шт;
Штучное время определяется по формуле
-основное время мин.;
-вспомогательное время мин.;
-время на техническое обслуживание рабочего места мин.;
-время на отдых и личные надобности мин;
Вспомогательное время состоит из затрат времени на отдельные приемы:
где - время на установку и снятие детали мин.;
- время на закрепление и открепление детали мин;
- время на приемы управления мин;
- время на измерение детали мин;
Для операции 70(сверлильная с ЧПУ)
где - длина рабочего хода;
и – чистота вращения шпинделя и подача;
Рассчитываем по переходам на операции
т.к. 4 отверстия то мин.;
Определяем вспомогательное время по переходам
где - вспомогательное время на переход;
– время на смену инструмента;
- время на приемы управления мин. [13 прил. 5.8];
- время на измерение детали мин. [13 прил. 5.10 5.13 5.16];
где – время на установку и закрепление детали мин. [13 прил. 5.2];
- время на открепление и снятие детали мин. [13 прил. 5.7];
мин. [13 прил. 5.20];
мин. [13 прил. 5.22];
9. Выполнение проектно - точностных расчетов по: разрабатываемому техпроцессу.
Расчет размерных цепей
Размерный анализ технологического процесса осуществляют по следующей методике:
Определяют фактическое поле рассеяния замыкающего звена по формуле:
где - количество составляющих звеньев - поле рассеяния (допуск) i-того звена.
Определяют средний размер замыкающего звена – конструкторского размера и средние размеры всех составляющих размеров за исключением определяемого звена можно рассчитать по формуле:
Для замыкающего звена – припуска исходный размер определяют по формуле:
где - минимальный припуск определяется по формуле
- шероховатость поверхности - толщина дефектного слоя оставшиеся от предыдущей обработки
- максимальный припуск определяется по формуле
Средний размер определяемого звена:
Номинальный размер определяемого звена:
Запас по допуску замыкающего звена:
Округляем номинальный размер определяемого звена.
Величина коррекции номинального размера:
Составляем размерную схему
Составляем размерные цепи:
Фактическое поле рассеяния замыкающего звена
(0+0.5)+(0+0.46)=0.96
Исходный средний размер замыкающего звена
Средний размер определяемого звена
Номинальный размер определяемого звена
Запас по допуску замыкающего звена
Величина коррекции номинального размера
Фактический средний размер замыкающего звена
Фактический наименьший размер замыкающего звена
Фактический наибольший размер замыкающего звена
Запас по нижнему пределу замыкающего звена
Запас по верхнему пределу замыкающего звена
Т.к. то относительные показатели дефицита не рассчитываем.
Цепь 2: [Z71]=D1+A0-A2-D0
(0+0.5)+(0+0.46)+(0.05-0)=1.01
75-0.595-69.77+0=0385
73-(0.595-1.012)=9.64
(10.235+1.012)-1.1=9.64
Цепь 3: [Z61]=C1+A0-A2-C0
(0+0.5)+(0+0.46)+(0.2+0.2)= 136
705-(0.77-1.362)= 17.615
(17705+1.362)-1.45=17.615
Цепь 4: [Z51]=-B1-A0+A2+B0
75+0.595-69.77-0=1.5751
515-(0.77-1.362)= 29.195
(29195+1.362)-1.45=29.195
Цепь 5: [Z11]=-A1+A2
(0+0.1)+(0+0.46)=0.56
54-(0.37-0.562)=1.45
Цепь 6: [Z21]=E0-A2+A1-E1
(0+0.46)+(0+0.1)+(0+0.3)=0.86
-67.95+0.95+69.77-0=2.77
67-(0.52-0.862)= 2.58
(3.1+0.862)-0.95=2.58
Цепь 7: [Z31]= A2-A1+E1+F1-H0
(0+0.46)+(0+0.1)+(0+0.3)+(0+0.36)=1.22
77-67.95+0.70+5.35-0=7.87
41-(0.70-1.222)= 0.05
(0.75+1.222)-1.31=0.05
Цепь 8: [Z41]= A2-A1+E1+F1+G1+K0
(0+0.46)+(0+0.1)+(0+0.3)+(0+0.36)+(0+0.43)=1.65
77-67.95+0.915+5.35+7.82-0=15.905
4-(0.915-1.652)= 2.31
(3.225+1.652)-1.74=2.31
10. РАСЧЕТ ПРИСПОСОБЛЕНИЙ НА ТОЧНОСТЬ
( оп.90 «Токарная с ЧПУ») на размер 49 ± 0125 . [14]
Для обеспечения необходимой точности обрабатываемой детали при конструировании приспособления необходимо выбрать такую схему при которой будет соблюдено условие:
где — действительное значение погрешностей базирования заготовки в приспособлении;
доп — допускаемое значение погрешностей базирования заготовки в приспособлении. Допускаемое значение погрешностей базирования заготовки в приспособлении Д0П ориентировочно рассчитывается по формуле:
ТЭМ. Термическое удаление заусенцев дОП= -
где — допуск выдерживаемого размера;
- точность обработки получаемая при выполнении данной
При отсутствии обоснованных данных о точности обработки получаемой при выполнении данной операции может приниматься средне-экономическая точность обработки по табл. 136—154.
Действительное значение погрешностей базирования заготовки. в приспособлении определяют из геометрических связей свойственных схеме базирования. Формулы расчета для наиболее часто встречающихся схем базирования приведены в табл. 69.
Расчетная суммарная погрешность приспособления Δ ПР определяется по формуле :
Δ ПР — (k1 e + Δ уст + k2 )
где — допуск на обрабатываемой детали; (±0125)
k1 — коэффициент равный 08—085;
k2 — коэффициент равный 06—10;
— точность обработки на данной операции;
Δ уст — погрешность установки.
Погрешность установки Δ уст — это смещение заготовки при закреплении. Она зависит от типа приспособления и главным образом от характера зажима и не зависит от схемы базирования и метода обработки.
Значения погрешности установки Δ уст даны в табл. 70—73.
Рассчитав погрешность базирования и определив по таблицам погрешность установки Δ уст и точность обработки рассчитывают
суммарную погрешность приспособления Δ пр которую затем распределяют по отдельным составляющим звеньям размерной цепи.
Суммарная погрешность приспособления Δ пр состоит из следующих погрешностей составляющих звеньев размерной цепи:
Δ пр = Σ и+ у + з + п -
где и — погрешность изготовления деталей приспособления;
у — погрешность установки приспособления на станке;
— погрешность вследствие конструктивных зазоров необходимых для посадки на установочные элементы приспособления;
п — погрешность перекоса или смещения инструмента возникающая из-за неточности изготовления направляющих элементов приспособления если направляющие отсутствуют погрешность п не учитывается.
11 Загрузочное устройство (операция 10 « Токарная с ЧПУ)
11.1 Проектный расчет загрузочного устройства
) Определение количества заготовок помещаемых в магазине :
Т- время работы станка в автономном режиме с.
Т- время обработки заготовок с.
)Определение длины лотка : L=d*Q
d -диаметр заготовки мм.
Q - количество заготовок помещаемых в магазине шт.
) определение зазора в лотке :
Δ = ( D ИЗ 2 + L u 2 )12 · cos α1 - L u = (1052 + 802 )12 · cos 21.8 ° - 80 =42.56
D ИЗ- диаметр заготовки мм;
L u- длина данной части изделия мм.
f- коэффициент трения f =0.4 ; af=p p=arctg f .
Данное значение зазора является максимально допустимым принимаем А=5мм.
Н= d+ 1.5= 105+1.5=1065мм
)Расчет минимального угла наклона магазина :
sinα = R f1 (f1 (2HR) + tg ) =1.5 · 0.4 ( 0.4 ·(2 *106.552.5 ) + tg25 ° =0.75 arcsin 0.75 = 49.11 °
11.2 Описание работы спроектированного загрузочного устройства.
Загрузочное устройство предназначено для автоматизации рабочего труда на станке 16K20ФЗC32 основной принцип работы которого заключается в следующем :
Заготовки из магазина поступают в захват питателя и при подаче сжатого воздуха в пневмоцилиндр происходит перемещение питателя с захваченной из магазина заготовкой на линию центров станка заготовка зажимается в кулачки и происходит непосредственно обработка . После того как обработка будет завершена происходит освобождение от зажима обработанной детали.
Обработанные заготовки падают в специальный поддон для готовых деталей после чего проходят соответствующую стадию контроля.
Затем подается следующая деталь. Загрузочное устройство размещено непосредственно на передней бабке станка.
(чертеж загрузочного устройства представлен в графической части проекта).
Источник см. [3] [4] [5] [6] [7]
12 Описание режущего инструмента - концевая фреза с клеерезьбовым соединением коронки . (стр. 130131 [2] )
( чертеж смотри в графической части проекта)
Фрезерование является одним из широко распространенных и высокопроизводительных методов обработки металлов резанием на фрезерных станках. Все шире применяют фрезерные станки с ЧПУ (20—30% всего числа станков основного производства) на которых выполняется 70—80% всех фрезерных работ. Эффективность использования данных станков сдерживается недостаточно высокой размерной стойкостью инструмента и особенно при фрезеровании деталей из труднообрабатываемых материалов.
Фрезы выпускаемые инструментальной промышленностью в полной мере не отвечают требованиям предъявляемым к инструментам для станков с ЧПУ. Решая эту проблему многие новаторы создали принципиально новые типы фрез и усовершенствовали стандартные фрезы.
Фреза предназначена для фрезерования глубоких пазов карманов и других элементов в деталях из труднообрабатываемых сталей.
Коронки на фрезе из быстрорежущей стали с клеерезьбовым соединением .
Для склеивания применяют клей КИ-78 термостойкостью 300 ° С. Склеивание осуществляется при температуре 200 ° С в течении 3 часов . Корпус фрезы из стали 40Х. Номер конуса хвостовика №3. Фреза устанавливается в специальную оправку с креплением хвостовика.
Углы канавок чередуются через зуб. Количество канавок 6 штук :
- угол наклона винтовой канавки для четных зубьев : = 36 °
- угол наклона винтовой канавки для нечетных зубьев : = 38 °
13. Трехкулачковый самоцентрирующий патрон.
Устройство и принцип работы.
Патрон при помощи тяги проходящей через отверстие шпинделя присоединяется к силовому приводу. При правильном соединении патрона с приводом движение штока в направлении от силового привода должно прекратиться из-за упора поршня привода в торец а не упора в корпус патрона и между торцом штока и корпусом патрона должен оставаться зазор 05-10 мм.
Для расчета патрона возьмем наиболее тяжелые условия обработки. Такие условия возникают на операции 020 (переход 1). Сила резания =12289 н.
Расчет усилия зажима.
В процессе обработки заготовки на нее воздействует система сил. С одной стороны действуют составляющие силы резания которые стремятся вырвать заготовку из кулачков с другой – сила зажима препятствующая этому. Из условия равновесия моментов данных сил и с учетом коэффициента запаса определяются необходимые зажимные и исходные усилия.
Суммарный крутящий момент от касательной составляющей силы резания:
- гарантированный коэффициент запаса; = 15.
- коэффициент учитывающий увеличение сил резания из-за случайных неровностей на обрабатываемых поверхностях заготовки; = 12.
- коэффициент учитывающий увеличение сил резания вследствие затупления режущего инструмента; = 1.
- коэффициент учитывающий увеличение сил резания при прерывистом резании; = 1.
- характеризует постоянство силы развиваемой зажимным механизмом; = 1.
- характеризует эргономику немеханизированного привода для механизированного привода = 1;
- коэффициент трения между заготовкой и сменным кулачком; =016018;
Величина усилия зажима прикладываемая к постоянным кулачкам несколько увеличивается по сравнению с усилием и рассчитывается по формуле:
- вылет кулачка расстояние от середины рабочей поверхности сменного кулачка до середины направляющей постоянного кулачка ; =65.
- длина направляющей постоянного кулачка ; =80.
Расчет зажимного устройства.
При расчете зажимного механизма определяется усилие создаваемое силовым приводом которое зажимным механизмом увеличивается и передается постоянному кулачку
- передаточное отношение по силе зажимного механизма.
Данное отношение для клинового механизма равно:
- углы наклона клина =15°;
- углы трения на поверхностях кулачка и втулки определяются по формуле:
Расчет силового привода.
Диаметр поршня пневмоцилиндра рассчитывается по формуле:
- избыточное давление воздуха ; =04.
Ход поршня рассчитывается по формуле:
- свободный ход кулачков ; =5;
- передаточное отношение зажимного механизма по перемещению;
Значение принимать с запасом 1015 . Значит = 22 .
Графический раздел . (см. чертежи)
. Экономика и организация производства .
Общее описание предприятия
Открытое акционерное общество "Пермское агрегатное объединение "Инкар" образовано в 1992 году и является правопреемником Пермского агрегатного производственного объединения имени М.И. Калинина ведущего свою историю с 1940 года. Начав с изготовления карбюраторов для авиационных поршневых двигателей в настоящее время "Инкар" является ведущим в России предприятием по производству систем агрегатов топливо регулирующей автоматики для авиационных двигателей самолетов конструкторских бюро Туполева Яковлева Сухова Илюшина вертолетов - Микояна и Камова а также комплектующих для ракетных двигателей ракет различного назначения.
Инкар" входит в перечень предприятий военно-промышленного комплекса выпускающих стратегически важную продукцию его вышестоящим органом является Российское Авиационное Космическое Агентство.
Кроме авиационной специализированной техники значительную часть в общем объеме производства предприятия (около 30 %) занимают товары народного потребления; включающие в себя ручной электроинструмент (электропилы дисковые и цепные электрические рыхлители почвы) автомобильная продукция (гидротолкатели и демпфера крутильных колебаний для Горьковского и Волжского автозаводов и газо-топливная аппаратура для автомобилей) а также продукция для нефтедобывающей промышленности (дозатор газа и силовые установки).
Для выпуска новой продукции предприятие использует имеющиеся производственные мощности квалифицированные кадры современную технологию. Длительный срок работы объединения в условиях "военной приемки" позволил наработать серьезный опыт производства бездефектной продукции. Высокое качество обеспечивается строгим соблюдением технологии и испытаний каждого изделия на специальных стендах в соответствии с государственными стандартами.
Система качества действующая на предприятии успешно прошла сертификацию на соответствие требованиям международного стандарта ИСО-9000 в системах Оборонсертифика ГОСТ Р. DAFVTGA.
Исходные данные для проектирования
№ 136-10-018 деталь «Цилиндр»
материал – сталь : ЭП678У – ВД (03Х11Н10М2Т-ВД)
Годовая программа выпуска П=1000 штук .
Годовая трудоемкость работ -100000 нч
Режим работы: 2-х сменный. Коэффициэнт загрузки -08
«Проектируемый ТП» заготовки -479 кг.Масса готовой детали - 056 кг .
«Существующий ТП» заготовки -54 кг.Масса готовой детали - 056 кг .
Разность масс заготовок = 061 кг -(Изменение типоразмеров)
Стоимость 1 т = 109990 руб. (г. Омск) 1 кг = 10999 руб.
Номинальный годовой фонд времени работы оборудования.
Номинальный годовой фонд времени работы оборудования определяется исходя из 40 ч. рабочей недели 8-праздничных и 254 рабочих дня б году.
Фно = (365-112) · 8 · 2 = 4048 ч.
- Действительный годовой фонд времени работы оборудования
Принимаем действительный фонд времени работы оборудования : Fд=3890. (no данным 2002г.)
Технологический процесс механической обработки Таблица 1
наименование операции
Сверл. –фрезерный с ЧПУ
сверлильно-фрезерная
План маркетинга. Спрос на продукцию ожидается равномерный. Это обуславливается постепенным ростом в экономике России. Главным фактором влияющим на сбыт продукции является качество т.к. поломка детали приведёт к серьёзным последствиям а это грозит большими штрафами и навсегда отпугнёт потенциальных покупателей. Стимулированием продаж будет являться политика снижения цен оптовикам льготы российским производителям и последующее снижение себестоимости а следовательно и цены за счёт внедрения оборудования последнего поколения и современных методов обработки.
Производственный план
1 Определение годовой приведённой программы выпуска участка::
2.Выбор типа производства
- серийное производство;[8 стр.9]
- средние затраты на операцию ТП;
- программа выпуска j-й детали;
F д =3890 ч. эффективный фонд времени единицы оборудования;
3 Определение потребного количества технологического оборудования.
Коэффициент загрузки
где Ср - расчетное количество оборудования
Спр - принятое количество оборудования.
- Расчет количества токарных станков с ЧПУ АТ-320 :
- Расчет количества токарных станков с ЧПУ 16К20Ф3С32 :
шт; тогда Сток.=11;
- Расчет количества сверлильно-фрезерных станков с ЧПУ МА655А1 :
- Расчет количества токарных станков с ЧПУ SPT-16NC :
- Расчет количества шлифовальных станков с ЧПУ “Studer” :
- Расчет количества участков
Количество участков определяется по формуле [9стр.13]:
Общее количество станков в цехе: СЦ=168 шт.
Расчет потребного количества оборудования
Наименование оборудования
Трудоёмкость операций н-ч.
Трудоёмкость годовой прогр.н.ч.
Годовой эффект. фонд времени работы одного станка ч.
Планируемый коэффициент выполнения норм
Расчётное количество станков
Принятое количество станков
Коэффициент загрузки
Мощность ЭД кВт одного станка
Мощность ЭД кВт всех станков
Категория ремонтной сложности единицы
Категория ремонтной сложности всех станков
Первоначальная стоимость станка т. руб.
Первоначальная стоимость всех станков т. руб.
Отчисления в рем. Фонд %
Отчисления в рем. Фонд т. руб.
Амортизационные отчисления на полное восстановление %
Амортизационные отчисления на полное восстановление т.руб.
Определение потребного количества оборудования вспомогательных служб
Предусматриваем: 1) мастерская по ремонту оборудования. Количество станков 6(3.5% от основных). 2) Отделение РЕМПРИ: 3станка (распределение как и в пункте 1). 3) Заточное отделение: 6 станка (при мелкосерийном производстве и 200 основных станков). 4) Число верстаков в ремонтной мастерской принимаем 5 единиц (30% от единиц оборудования группы механика).
Мастерская по ремонту оборудования
3.Определение состава и численности работающих цеха
Расчёт фонда времени рабочего
Состав фонда времени рабочего
Календарный фонд времени
Выходные и праздничные дни
Номинальный фонд времени
Целодневные невыходы на работу:
б) дополнительный отпуск
г) выполнение гос. и общественных обязанностей
Явочный фонд рабочего времени
Потери внутри рабочего дня
ИТОГО внутрисменных потерь
Эфф. фонд времени рабочего
Средняя продолжительность рабочего дня
Расчёт списочной численности основных рабочих по трудоёмкости механической обработки по каждой профессии и разряду:
P0- списочная численность рабочих соответствующей профессии и разряда;
Nв- приведённая программа выпуска шт.;
Фэ- эффективный фонд времени работы одного рабочего в год ч;
Квн- коэффициент выполнения норм;
Кm- коэффициент многостаночного обслуживания (среднее количество станков обслуживаемых одним рабочим).
Численность основных рабочих по профессиям и разрядам
Нормированное время на годовую программу ч
Списочная численность рабочих
Р1=(36363 95)1640 1 1 60=35.1- принимаем 35 человек;
Р2=(36363 40)1640 1 1 60=14.78- принимаем 15 человек;
Р3=(36363 30)1640 1 1 60=11.08- принимаем 12 человека;
Расчёт численности вспомогательных рабочих.
- коэффициент перевода явочного числа рабочих в списочное.
Р0=(7476* 2* 123)600=30.65; Р0=31 чел
Р0(7476* 2* 123)1000=1839; Р0=19чел
Таким образом рассчитываются остальные рабочие
Re - количество единиц ремонтной сложности оборудования установленного в цехе;
Re=7166+360=7476 рем.ед.
Измерительные нормы обслуживания
Норма обслуживания на 1 вспом. рабочего
Количество расчётных единиц
Коэффициент пересчёта
Число вспомогательных рабочих
Слесари по ППР и межремонтному обслуживанию
Количество единиц ремонтной сложности
Станочники по ремонту
Наладчики оборудования
Слесари отделения РЕМПРИ
Численность основных рабочих
Станочники отд-я РЕМПРИ
Транспортные рабочие
Кладовщики раздатчики инструмента
Уборщики производственных помещений
Итого: в цехе 239 вспомогательных рабочих
Средний разряд (оклад)
% от общего количества
Вспомогательные рабочие
4.Расчёт площади цеха
- количество станков в цехе;
- удельная площадь на единицу оборудования;
- удельная вспомогательная площадь на единицу оборудования;
(8 станков по 25м2);
(4 станка по 25 м2);
(6 станков по 25 м2);
м2 (5 м2 на человека);
(площадь бытовых и конторских помещений).
5. Основные технико-экономические показатели цеха
Основные фонды цеха (основной капитал)
- стоимость 1 м2 здания;
Стоимость силового оборудования:
- суммарная мощность всех ЭД в цехе;
- стоимость 1кВт установленной мощности;
Наименование основных фондов
Первоначальная стоимость руб.
Силовые машины и оборудование
Рабочие машины и оборудование:
-вспомогательных служб цеха
Транспортные средства
Инструменты и приспособления
Производственный и хозяйственный инвентарь
Всего: основной капитал 55720460 руб.
Себестоимость продукции.
Затраты на основные материалы.
Плановая заготовительная цена 1 тонны руб.
Приведённая годов. Программа
Стоим. осн. материалов (без отходов)
Затр. на прогр. руб.
Расчёт фондов заработной платы рабочих.
Фонд заработной платы рабочих-сдельщиков:
-годовая программа Участка;
-трудоёмкость выполнения
-часовая тарифная ставка;
З1=15 36363 016=872712 руб.
З2=15 36363 03=163633 руб.
З3=15 36363 03=163633 руб.
З4=15 36363 025=136361 руб.
З5=15 36363 025=136361 руб.
З6=20 36363 025=181815 руб.
З7=20 36363 04=290904 руб.
З8=15 36363 025=136361 руб.
З9=20 36363 025=181815 руб.
З10=20 36363 025=181815 руб.
х 6 =9959826 руб (по цеху)
Фонд заработной платы рабочих-повремёнщиков:
-эффективный фонд времени рабочих-повремёнщиков;
З1пр.п=6 1640 8=78720 руб.
З2пр.п=8 1640 16=209920 руб.
З3пр.п=10 1640 76=1246400 руб.
З4пр.п=13 1640 65=1385800 руб.
З5пр.п=18 1640 11=324720 руб.
Сводная таблица заработной платы
Фонд прямой зпл рабочих
Среднегодовая зп одного рабочего
Распределение фонда зарплаты и отчислений на социальные нужды по статьям калькуляции
Сумма отчислений на соц. Нужды 26%
Сумма фонда зп и сумма отчис.на соц. нужды
) Заработная плата основных производственных рабочих
Год. фонд зп осн. рабочих
) Расходы на содержание и эксплуатацию оборудования:
а) содержание оборудования
Деж. персонал наладчики смазчики электронщики и др.
Год. фонд зп рабочих занятых обслуживанием оборудования:
б) ремонт оборудования и технологической оснастки
Слесари станочники занятые ремонтом оборудования и технологической оснастки
Год. фонд зп рабочих занятых ремонтом обор. и 60% год. фонда зп рабочих занятых восстановлением оснастки:
в) внутрицеховое перемещение грузов
Год. Фонд зп транспортных рабочих:
г) износ малоценных и быстроизнашивающихся инструментов
Слесари станочники РЕМПРИ
% год. фонда зп рабочих занятых восстановлением оснастки:
Контролёры ОТК распорядители работ кладовщики и т.д.
Год. Фонд зп прочих категорий вспомогательных рабочих:
а) на содержание прочего персонала
Вспомогательные рабочие ученики МОП
Год. Фонд зп вспом. Рабочих не вошедших в др. статьи себестоимости:
б) на содержание зданий сооружений инвентаря
Год. Фонд зп уборщиков произв. помещений:
Смета расходов на содержание и эксплуатацию оборудования цеха.
) Амортизация на полное восстановление оборудования и транспортных средств дорогостоящего инструмента
Аморт. отч. на полное восст. по действующим нормам от первоначальной стоимости силового основного вспомогательного оборудования транспортных средств дорогостоящего инструмента
Рассматриваем амортизационные отчисления из табл.8
) Эксплуатация оборудования
Затраты на вспомогательные эксплуатационные материалы
Стоимость ээнергии и сжатого воздуха
Зп вспом. рабочих обслуживающих оборудование с отчисл. на соц. страх.
5% от стоимости оборудования
Определяется при расчёте зп рабочих (табл.11)
) Затраты на ремонт оборудования транспортных средств дорогостоящей оснастки
) Внутрицеховое перемещение груза
Зп с отчислениями на соц. страхование транспортных рабочих
Затраты по эксплуатации транспорта
Опред-ся при расчёте фонда зп рабочих (табл.11)
% от год. фонда зп транспортных рабочих
) Износ малоценных и быстроизнашивающихся инструментов и приспособлений
Сумма износа малоценных и быстроизнашивающихся инструментов и приспособлений
Расходы по восстановлению и ремонту
Расчёт исходя из срока службы потребности на годовую программу и стоимости единицы.
% от зп рабочих гр. РЕМПРИ+ отчисления на соц. страхование (табл.11)
Зп и отчисления на соц. страхование контролёров ОТК распределителей работ кладовщиков и т.д.
Определяется при расчёте фонда зп рабочих (табл.11)
ВСЕГО расходов по содержанию и эксплуатации оборудования: 293874876 руб.
Расчёт стоимости электроэнергии и сжатого воздуха.
Затраты на силовую электроэнергию:
- суммарная мощность ЭД технол. и вспом. оборудования цеха;
- средний коэффициент загрузки ЭД по мощности;
- средний коэффициент загрузки ЭД по времени;
- коэффициент одновременной работы ЭД;
- коэффициент потерь электроэнергии в сети;
- эффективный фонд времени работы единицы оборудования;
- средний коэффициент полезного действия ЭД;
- стоимость 1кВт электроэнергии.
Затраты на сжатый воздух для обдувки деталей и узлов на инструменты распылители подъёмники и т.д.:
- средний часовой расход сжатого воздуха для всех воздухоприёмников м3;
- эффективный фонд времени работы оборудования;
- средний коэффициент загрузки оборудования по времени;
- стоимость 1000м3 сжатого воздуха;
Расчёт общехозяйственных общепроизводственных и внепроизводственных расходов.
Общепроизводственные расходы (500% от основной зп осн. рабочих):
505750 * 5 = 72528750 руб.
Общехозяйственные расходы (300% от основной зп основных рабочих):
505750 * 3 = 43517250 руб.
Внепроизводственные расходы (2% от заводской себестоимости товарной продукции):
893485542 * 002 = 517869711 руб.
Калькуляция себестоимости продукции (218178шт).
Наименование статей расхода
Итого прямых материальных затрат
Основная зп основных рабочих
Дополнительная зп основных рабочих
Отчисления на соц. нужды
Итого переменных затрат
Расходы на содержание и эксплуатацию оборудования
Общепроизводственные расходы
Общехозяйственные расходы
Производственная себестоимость
Внепроизводственные расходы
Итого постоянные затраты
Полная себестоимость (С)
Себестоимость всего объема:
061218471 + 52023 * 218178 = 26411355253 руб.
Себестоимость единицы продукции:
023 + 15061218471 218178 = 121055 руб.
Оборотные средства (оборотный капитал).
64389282 руб.- затраты на материалы;
- величина планового периода;
- норма запаса на материал;
411355253 руб.- себестоимость годового объёма продукции;
- норматив на незавершённое производство;
- норматив запаса готовой продукции.
Производственный капитал.
720460 + 1104835493 = 6676881493 руб.
(121055 + 015 * 121055) * 018 + (121055 + 015 * 121055) = 164271 руб
Расчёт плановой суммы балансовой прибыли
4271 * 218178 = =35840209079
Полная себестоимость
Прибыль от реализации продукции
Доходы от внереализационной деятельности
Итого: балансовая прибыль
Баланс доходов и расходов
Доходы и поступление средств руб.
Расходы и отчисления средств руб.
Прибыль от реализации продукции:
Налог на имущество (22%):
(55720460 - 3496808) * 0022 = 114892035
Налог на прибыль(24%):
(3961703288- 114892035) * 024 =
Доходы от внереализационной деятельности: -
Амортизационные отчисления:
Отчисления в ремонтный фонд: 1114409
График достижения безубыточности.
- постоянные затраты определённые на объём производства;
- цена единицы продукции;
- переменные затраты на единицу продукции.
Рентабельность проекта.
Технико-экономические показатели цеха
Наименование показателей
Значения показателей
Годовая приведённая программа
Трудоёмкость единицы продукции
Количество единиц технологического оборудования
Выработка на одного работающего
Стоимость основного капитала
Себестоимость единицы продукции
Цена единицы продукции
Прибыль от реализации
Выручка от реализации
Средняя зарплата рабочего
рентабельность производственного капитала
рентабельность продукции
ВЫСОКОПРОИЗВОДИТЕЛЬНЫЙ СБОРНЫЙ АБРАЗИВНЫЙ
ИНСТРУМЕНТ ДЛЯ СООСНОГО ВНУТРЕННЕГО ШЛИФОВАНИЯ
Актуальность проблемы.
В современном машиностроении одной из актуальных проблем является высокопроизводительная абразивная обработка отверстий деталей машин (например колец подшипников) к которым предъявляются высокие требования по шероховатости волнистости и точности формы.
Обработка отверстий существующими абразивными инструментами сопряжена с рядом трудностей обусловленных прежде всего сложностью подвода смазочно-охлаждающей жидкости (СОЖ) в зону резания через узкую щель между кругом и заготовкой в условиях действия мощных аэродинамических потоков создаваемых вращающимся инструментом. Это приводит к снижению производительности обработки из-за опасности образования тепловых дефектов в поверхностных слоях шлифованных деталей.
Основными путями повышения производительности инструмента для шлифования отверстий являются интенсификация режимов резания и увеличение площади контакта круга с заготовкой.
Традиционная схема внутреннего шлифования эксцентрично расположенным относительно заготовки сплошным абразивным кругом не позволяет обеспечить качественный рост производительности из-за ограничений накладываемых сложностью подвода СОЖ в зону обработки малой площадью контакта круга и заготовки сложностью существенной интенсификации режимов резания без образования прижогов в шлифуемых заготовках и роста дисбалансов инструмента снижающих точность обработанных отверстий.
Поэтому решение проблемы повышения производительности инструмента для внутреннего шлифования за счет увеличения площади контакта круга и заготовки и создания условий надежного поступления СОЖ в зону резания является перспективным направлением.
Целью работы является повышение производительности абразивного инструмента для внутреннего шлифования.
Методы исследования. Исследования проводились на базе фундаментальных положений теории резания теории шлифования материалов с использованием методов линейной алгебры теоретической механики дифференциального и интегрального исчислений теории формообразования динамики теории вероятности технологии машиностроения гидродинамики математической статистики сопротивления материалов многофакторных планируемых экспериментов и компьютерного моделирования.
Достоверность результатов исследований подтверждается экспериментальной проверкой теоретических зависимостей и выводов с применением современных измерительных приборов и установок корректным использованием научных методов исследований компьютерными расчетами а также внедрением новых абразивных инструментов и технологии шлифования в производство.
Научная новизна работы заключается в:
установленных взаимосвязях между кольцевыми потоками СОЖ гидродинамическими клиньями перемещающимися со скоростью резания по обрабатываемой поверхности заготовки и бесприжоговым режимом внутреннего шлифования соосным сборным инструментом с радиально-подвижными абразивными сегментами;
математических моделях процессов съема металла соосным абразивным инструментом формирования геометрической погрешности движения оси шпинделя заготовки виброперемещения радиально-подвижных абразивных сегментов круга учитывающих влияние создаваемых вращающимся инструментом гидродинамических клиньев СОЖ постоянное равенство диаметра рабочей поверхности круга и обрабатываемого отверстия отклонения от соосности осей круга и шлифуемого отверстия а также разброс масс и смещения радиально-подвижных абразивных сегментов круга относительно заготовки и корпуса инструмента;
Практическая значимость работы заключается в:
гарантированном обеспечении повышения производительности внутреннего шлифования в 27-32 раза за счет применения сборных абразивных кругов с радиально-подвижными сегментами;
устранении опасности возникновения прижогов при одновременном повышении скорости съема металла с обрабатываемой заготовки;
сокращении сроков проектирования и трудоемкости технологической подготовки производства за счет использования прикладных компьютерных программ по проектированию сборных абразивных инструментов и процесса соосного внутреннего шлифования.
Апробация работы. Основные положения и наиболее важные результаты исследований докладывались на 47 международных всероссийских и региональных научных конференциях семинарах симпозиумах а также на заседаниях кафедры «Инструментальная техника и технология формообразования» ГОУ ВПО МГТУ «СТАНКИН» и «Технология машиностроения» Владимирского государственного университета.
Публикации. Основные результаты работы опубликованы в 70 печатных работах в том числе в 3 авторских свидетельствах на конструкции инструментов 1 авторском свидетельстве на способ внутреннего шлифования 1 свидетельстве РФ на полезную модель сборного абразивного инструмента и 1 патенте РФ на способ внутреннего шлифования.
ОСНОВНОЕ СОДЕРЖАНИЕ РАБОТЫ
В первой главе выполнен аналитический обзор научно-технической и патентной литературы позволивший выявить ряд крупных научных направлений исследований в области повышения производительности процессов абразивной обработки и качества поверхностного слоя деталей. На основании анализа работ предшественников по указанным направлениям сформулированы цель и задачи исследований.
Существенный вклад в развитие инструментов и процессов обработки внесли отечественные и зарубежные исследователи Н.И.Богомолов Г.В.Бокучава Л.А.Глейзер В.А.Гречишников Б.И.Горбунов В.Г.Гусев Г.М.Ипполитов А.М.Козлов А.В.Королев С.Н.Корчак В.А.Кудинов Г.Б.Лурье Е.Н.Маслов Ю.К.Новоселов В.М.Оробинский В.И.Островский Ю.Н.Полянчиков С.А.Попов С.Г.Редько А.Н.Резников В.А.Рогов С.С.Силин С.С.Сипайлов Ю.М.Соломенцев В.Л.Сосонкин В.К.Старков Ю.С.Степанов О.В.Таратынов Л.Н.Филимонов Л.В.Худобин В.М.Шумячер А.В.Якимов П.И.Ящерицын J.N.Brecker S.K.Dean C.Harzbecker H.Kaliszer G.K.Lai K.Nakayama R.Neugebauer K.Okamura M.C.Shaw N.E.Yo и многие другие.
Повышение производительности абразивной обработки путем интенсификации режимов резания в первую очередь ограничивается необходимостью обеспечения требуемого качества поверхностного слоя шлифуемых деталей.
Большинство существующих способов шлифования и инструментов может использоваться как без применения так и с применением смазочно-охлаждающих технологических средств. Однако практически все исследователи в своих работах так или иначе решают вопросы уменьшения негативного влияния тепла выделяющегося в зоне резания при шлифовании на параметры качества поверхностного слоя шлифованных деталей. Повышение производительности абразивных инструментов при шлифовании в большинстве случаев лимитируется именно возникновением тепловых дефектов при использовании более интенсивных режимов обработки.
Одной из тенденций развития шлифования является повышение экологической безопасности процессов абразивной обработки осуществляемое путем уменьшения (вплоть до полного отказа от применения) количества используемых СОЖ и более эффективного их использования в процессе шлифования. Однако несмотря на ряд преимуществ сухого шлифования подавляющее большинство авторов отмечает более высокую эффективность шлифовальных операций проводимых с использованием СОЖ. Многочисленные исследования большого количества научных коллективов как в нашей стране так и за рубежом направленные на совершенствование рецептур СОЖ и технологий их рационального применения указывают на необходимость более эффективного использования смазочно-охлаждающих жидкостей на водной основе в абразивной обработке и на преждевременность полного отказа от использования СОЖ в производственной практике.
Существующие конструкции абразивных инструментов схемы шлифования и методы подвода СОЖ не обеспечивают гарантированного присутствия достаточного количества жидкости в зоне контакта абразивных зерен с обрабатываемой заготовкой что приводит к необходимости использования косвенных методов отвода образующегося тепла – в частности путем охлаждения круга и самой заготовки вне зоны резания. При этом значительно увеличивается количество СОЖ необходимой для бездефектной реализации процесса абразивной обработки.
В работах Кудинова В.А. Ящерицына П.И. Тимофеева С.М. Гусева В.Г. отмечается что гидродинамические клинья возникающие между кругом и заготовкой при их вращении и создающие определенное давление в зоне резания значительно улучшают условия реализации процесса шлифования.
Для повышения производительности шлифования необходимо увеличить время и площадь контакта абразивных элементов инструмента с заготовкой на протяжении каждого оборота круга путем разработки новых инструментов и схем обработки реализующих многоточечный контакт с заготовкой.
Цельные и сборные абразивные круги с прерывистой режущей поверхностью в целом более эффективны чем круги со сплошной режущей поверхностью по всем основным (кроме геометрических) показателям. Вместе с тем в силу своих конструктивных особенностей круги с прерывистой режущей поверхностью также не обеспечивают гарантированного присутствия достаточного количества СОЖ в зоне обработки. Работы в области применения сборных абразивных кругов с прерывистой режущей поверхностью свидетельствуют о повышенном уровне динамических воздействий на шлифуемую заготовку как из-за прерывистости режущей поверхности так и из-за дисбалансов вращающегося абразивного инструмента;
Повышение производительности абразивной обработки и качества поверхностных слоев шлифованных деталей может быть достигнуто разработкой новых конструкций абразивных инструментов технологий шлифования и схем подачи СОЖ обеспечивающих высокую скорость отвода образующегося тепла из зоны резания путем повышения давления СОЖ в зоне обработки исключения влияния аэродинамических потоков на процесс шлифования обеспечения высокой скорости перемещения потоков СОЖ относительно обрабатываемой детали и максимального увеличения омываемых СОЖ площадей обрабатываемых деталей.
На основе проведенного анализа и в соответствии с целью работы сформулированы следующие задачи:
выполнить теоретическое и экспериментальное обоснование принципиальных схем режущих инструментов и многоточечной абразивной обработки обеспечивающих генерирование вращающимся инструментом гидродинамических кольцевых потоков и клиньев СОЖ в зоне обработки;
разработать математические модели движения оси шпинделя заготовки и пространственного виброперемещения абразивного сегмента относительно заготовки в процессе шлифования разработанным инструментом;
создать математические модели связывающие кинематическую и динамическую составляющие геометрической погрешности обработки с конструктивными параметрами инструмента и режимами шлифования;
создать математические модели процесса съема металла абразивным инструментом с многоточечным контактом с заготовкой позволяющие оценить производительность шлифования с учетом режимов обработки и параметров абразивного инструмента;
выполнить анализ напряженного состояния абразивных инструментов;
разработать конструктивные решения абразивных инструментов провести экспериментальную проверку их производительности и параметров качества поверхностного слоя шлифованных деталей;
разработать практические рекомендации по использованию инструментов генерирующих гидродинамические клинья СОЖ в зоне обработки;
внедрить разработанные инструменты и технологии в производство.
Вторая глава направлена на разработку принципиальных схем абразивных инструментов обеспечивающих повышение производительности и генерирующих гидродинамические кольцевые потоки и клинья СОЖ в зоне резания. Разработанные схемы внутреннего шлифования характеризуются единым принципом генерирования кольцевых потоков и клиньев СОЖ включающим в себя разгон СОЖ до скорости резания самим инструментом и создание условий для формирования и удержания постоянно обновляющихся объемов СОЖ на клиновых участках непосредственно примыкающих к зоне обработки.
Первая (традиционная) схема инструмента и процесса абразивной обработки (рис.1) – круглое внутреннее шлифование стандартным кругом с подачей СОЖ поливом – характеризуется низким давлением СОЖ и одноточечным контактом инструмента и заготовки.
Рис.1 Принципиальные схемы инструментов и процессов внутреннего шлифования.
Во второй схеме применяется сборный круг с прерывистой режущей поверхностью и жестким креплением абразивных сегментов в корпусе инструмента. Данная схема также характеризуется одноточечным контактом инструмента и заготовки. Наличие выступающих из корпуса круга абразивных сегментов разгоняющих поступающую через внутреннюю полость круга СОЖ позволяет незначительно повысить скорость течения и давление СОЖ в зоне обработки.
При разработке и реализации третьей схемы используется сборный круг с жестким креплением абразивных сегментов в корпусе инструмента. Круг размещен в емкости образованной обрабатываемой заготовкой и торцовыми крышками. СОЖ подается через конструкцию инструмента и поступает к заготовке через каналы между смежными сегментами. Использование представленной схемы позволяет повысить давление СОЖ в зоне обработки за счет удержания необходимого объема СОЖ в емкости образования вращающегося совместно с кругом жидкостного кольца и заклинивания накопленной СОЖ между кругом и заготовкой.
В четвертой схеме используется сборный круг с радиально-подвижными абразивными сегментами размещенный соосно обрабатываемой заготовке в емкости образованной заготовкой и торцовыми крышками.
Сборный абразивный круг с радиально-подвижными сегментами располагают вместе с заготовкой в емкости образованной обрабатываемой заготовкой и торцовыми крышками с осевыми отверстиями для подвода и слива СОЖ. Невращающийся круг со сведенными сегментами вводят в емкость и размещают его соосно с заготовкой закрывают крышку подают СОЖ по трубопроводу сообщают кругу возвратно-поступательное и вращательное движение относительно заготовки. Из внутренней полости круга СОЖ поступает по каналам к шлифуемой заготовке. В процессе шлифования проводят черновую и чистовую обработку заготовки ступенчато уменьшая частоту вращения инструмента. Использование данной схемы обеспечивает повышение давления СОЖ в зоне обработки за счет удержания необходимого объема СОЖ в емкости и образования вращающегося совместно с кругом кольцевого потока СОЖ. Радиус режущей поверхности абразивных сегментов выполнен меньше радиуса шлифуемого отверстия благодаря чему между сегментами и заготовкой образуются клиновые зазоры в которые поступает и заклинивается СОЖ.
Давление СОЖ в зоне обработки при четвертой схеме значительно отличается от давления создаваемого в предыдущих схемах. Суммарное давление СОЖ по четвертой схеме определяется выражением
Р = Рц + Ркл() + РК дин (1)
где - циркуляционная составляющая суммарного давления Р обусловленная разгоном СОЖ и вовлечением ее во вращательное движение в замкнутой емкости; – усредненное давление СОЖ в клине между сегментом и обрабатываемой поверхностью; РК дин – составляющая давления обусловленная разгоном СОЖ в диффузорных каналах инструмента.
где W1 W2 - относительные скорости на входе и выходе из канала; U1 U2 - окружные составляющие скорости СОЖ на входе и выходе из канала; z1z2- радиус точки линии тока жидкости на входе и выходе из отверстия соответственно; h1- потери на трение СОЖ в каналах; g- ускорение земного тяготения.
Усредненное давление Ржп СОЖ в правом (набегающем) клине
где - полная несущая способность клина; B - высота сегмента; C C1 - ширина сегмента и длина хорды стягивающей дугу контакта соответственно; lП - длина перебега инструмента Rc – радиус режущей поверхности абразивного сегмента.
Давление СОЖ в левом клине меньше чем в правом и определяется
где Рп – давление СОЖ на входе в инструмент; - плотность СОЖ; - угловая скорость круга; - меридиональные составляющие абсолютных скоростей течения СОЖ на входе и выходе канала R3 – радиус заготовки.
Таким образом четвертая схема характеризуется наличием дополнительной составляющей суммарного давления из-за диффузорных каналов и гидродинамических клиньев СОЖ образующихся у каждого сегмента и являющихся отличительной особенностью четвертой схемы шлифования.
Результаты анализа гидродинамических характеристик схем обработки прошли экспериментальную проверку. Установлено что суммарное P давление СОЖ при четвертой схеме внутреннего шлифования измеряемое в осевом сечении заготовки зависит от частоты вращения круга с увеличением которой давление существенно возрастает (рис. 2).
Рис.2. Влияние частоты вращенияРис.3. Экспериментальное исследование суммарного
круга на суммарное давление СОЖдавления СОЖ при различных схемах обработки
Наибольшая доля 67 70% от суммарного давления P приходится на циркуляционную составляющую PЦ доля давления обусловленного эффектом заклинивания СОЖ составляет 25 28% подача СОЖ через конструкцию шлифовального круга приводит к повышению давления в среднем на 5%.
Экспериментальное сравнение максимальных значений давления СОЖ для всех четырех схем круглого внутреннего шлифования (рис. 3) показало что при четвертой схеме давление распределяется равномерно как по окружности обрабатываемого отверстия так и по его образующей и превышает максимальное давление при шлифовании сплошным кругом (1 схема) в 17 раз при шлифовании по второй схеме – в 115 раз и при третьей схеме – в 525 раза. Сравнение участков стабильного давления СОЖ показало при четвертой схеме давление СОЖ превышает давление при первой схеме в 875 раза давление при второй схеме – в 32 раза давление при третьей схеме – в 175 раза что подтверждает результаты теоретических исследований давления СОЖ и свидетельствует о явных преимуществах четвертой схемы.
Теоретические и экспериментальные исследования гидродинамических характеристик разработанных схем абразивной обработки показали что 4 схема позволяет в наибольшей степени повысить давление СОЖ в зоне обработки вследствие чего она выбрана для проведения дальнейшего исследования.
В третьей главе рассмотрены вопросы формирования геометрии поверхностей шлифуемых кругом с радиально-подвижными абразивными сегментами генерирующим гидродинамические клинья СОЖ. На геометрические показатели шлифованных поверхностей большое влияние оказывает движение элементов технологической системы под действием таких внешних динамических факторов как дисбалансы заготовки отклонение от соосности обрабатываемого отверстия и инструмента разброс массы абразивных сегментов (рис. 4).
Рис.4. Схема шпиндельного узла заготовки под действием рабочей нагрузки.
Движение оси шпинделя заготовки под действием эксцентриситета и разброса массы абразивных сегментов описывается системой дифференциальных уравнений
где М – масса заготовки и приспособления в котором она закреплена;
f – расстояние на котором отстоит центр масс заготовки от передней опоры шпинделя; c1c2d1d2 – коэффициенты жесткости опор шпинделя соответственно в вертикальном и горизонтальном направлении; 3 К - угловая скорость вращения заготовки и круга соответственно; – текущее время шлифования; α - начальное угловое положение суммарного вектора Q центробежных сил действующих на сегмент который включает в себя также суммарный вектор сил давления СОЖ в гидродинамических клиньях; k - коэффициент демпфирования опор шпинделя заготовки; I I1 – осевой и экваториальный момент инерции заготовки с приспособлением соответственно.
Система дифференциальных уравнений описывающих движение оси шпинделя заготовки под действием его главного вектора дисбалансов DCT имеет вид (6) однако в левой части третьего и четвертого уравнения член () заменяется на а столбец в правой части системы (6) заменяется на столбец
где α1 - угол главного вектора дисбалансов DCT .
Решение систем дифференциальных уравнений позволяет получить следующие выражения
где 3 y3 – малые виброперемещения шпинделя заготовки в плоскости проходящей через центр масс заготовки и опорных плоскостях шпинделя обусловленные одновременным действием векторов и Q3 = Dcт.
Геометрические погрешности обрабатываемой поверхности определяются не только виброперемещениями заготовки но и виброперемещениями yc абразивного сегмента (рис. 5): (10)
где Рy - радиальная составляющая силы резания; jk - контактная жесткость системы «абразивный сегмент – заготовка».
Рис. 5. Абразивный сегмент под действием нагрузки в процессе шлифования.
Расчеты на ЭВМ показали что при 4 схеме виброперемещения абразивного сегмента в 3 5 раз меньше перемещений аналогичного по параметрам сборного круга работающего по 2 схеме. Это объясняется тем что в 4 схеме происходит отсечение от абразивного сегмента и заготовки возмущений создаваемых шпинделем шлифовального инструмента. Сравнительно высокий уровень вибрации скоростного шпинделя шлифовального круга не оказывает существенного влияния на процесс шлифования в связи с диссипацией колебаний шпиндельного узла в зоне контакта обоймы сегмента с металлическим корпусом шлифовального круга. В 4 схеме происходит перенос внешней нагрузки со сравнительно нежесткого и скоростного шпиндельного узла шлифовального круга на более жесткий и менее скоростной шпиндельный узел заготовки что позволяет повысить геометрическую точность обработанных поверхностей. Шпиндельный узел шлифовального круга передает сегментам лишь вращательное и возвратно-поступательное движение и разгружен от действия перерезывающих сил поскольку суммарный вектор перерезывающих сил резания примерно равен нулю вследствие их взаимной компенсации.
Геометрическая погрешность в поперечном сечении обрабатываемой поверхности обусловленная элементами режима резания и параметрами круга
где -высота и ширина режущей части абразивного зерна занимающего Sпр Sр - продольная и радиальная подача сегмента соответственно; ; Qc – инерционная центробежная сила действующая на сегмент; m - масса и радиус центра масс сегмента соответственно.
Геометрическая погрешность в продольном сечении обусловленная кинематикой процесса обработки определяется зависимостями (11) – (13) при условии: и
Кинематическая составляющая геометрической погрешности обрабатываемой поверхности возрастает при увеличении продольной подачи (рис.6 а) угловой скорости круга и уменьшается с увеличением угловой скорости заготовки (рис. 6 б). При противоположном направлении векторов и увеличение отношения приводит к уменьшению геометрической погрешности а при одинаковом направлении векторов и – к значительному росту погрешности (рис. 7 а-б).
Рис. 6. Влияние продольной подачи (а) и угловой скорости вращения заготовки (б) на погрешность в поперечном сечении обрабатываемой поверхности
Рис. 7. Влияние отношения угловых скоростей заготовки и круга на погрешность при противоположном (а) и одинаковом (б) направлении векторов и .
Для уменьшения микрогеометрии волнистости и погрешности геометрической формы в продольном и поперечном сечении обработку следует проводить при максимальной угловой скорости заготовки уменьшать продольную и радиальную подачи скорость вращения круга увеличивать отношение а процесс шлифования проводить при противоположном направлении векторов и .
Суммарная геометрическая погрешность формируемая в процессе обработки состоит из кинематической ΔК и динамической ΔД составляющих т.е.
Проанализирована динамическая составляющая погрешности начиная с первого и кончая последним оборотом заготовки в зоне обработки (рис. 8).
Формирование динамической погрешности ΔД носит частотный характер и зависит от отношения . Получены математические модели позволяющие определить значения ΔД при различных и и описать геометрию обработанной поверхности. Для уменьшения ΔД следует назначать режимы шлифования с отношением представляемым в виде иррациональных дробных чисел или конечных десятичных дробей приближающихся к целому числу.
Рис. 8. Формирование геометрии поверхностей шлифуемых кругом с радиально-подвижными сегментами при : а) – 5; б) –51; в) – 65; г) – 83 (3)
В третьей главе также представлены программы для расчета кинематической и динамической составляющих геометрической погрешности поверхностей шлифованных разработанным инструментом и компьютерной визуализации процесса пространственно-временного формирования обрабатываемой поверхности позволяющие контролировать величину геометрической погрешности и выбирать режимы обеспечивающие ее минимальные численные значения.
Четвертая глава посвящена теоретическому и экспериментальному исследованию производительности абразивной обработки отверстий кругами с радиально-подвижными сегментами. Производительность оценивали стандартным критерием – режущей способностью инструмента Wк1 представляющей собой объем материала снятого с заготовки в течение одной минуты и приходящегося на 1 мм высоты инструмента.
При многоточечном контакте снятие материала с заготовки будет происходить значительно быстрее чем при одноточечном контактировании а следовательно при новой схеме обработки следует ожидать повышения производительности процесса шлифования.
Многоточечное шлифование характеризуется непрерывным снятием материала зернами в течение всего цикла (оборота круга) что является также принципиальным отличием новой схемы шлифования.
Каждое абразивное зерно за один оборот относительно заготовки аналогично схеме растачивания оставляет рез в виде правой и левой винтовых линий (при прямом и обратном продольном ходе круга).
Объем недеформированного материала снимаемого единичным зерном в течение одной минуты при реализации разработанной схемы обработки
где B - высота сегмента; lп - длина перебега круга.
При традиционной схеме шлифования объем недеформируемого материала снимаемого в течение одной минуты по данным проф. Е.Н. Маслова
где - угол контакта инструмента с заготовкой; VД Vк - окружная скорость детали и круга соответственно; bср - среднее значение недеформированной ширины канавки нанесенной абразивным зерном; u - минутная продольная подача инструмента; d D - соответственно диаметр режущей поверхности круга и диаметр обрабатываемого отверстия d=2Rk D=2R3.
Анализ зависимостей (15) (16) характеризующих минутный съем единичным зерном недеформированного металла для новой и традиционной схемы внутреннего шлифования показал что минутный съем . Это объясняется многократным увеличением пути проходимого в металле единичным зерном за одно и то же время при обработке новым инструментом.
Выполнив компьютерную рандомизацию последовательности абразивных зерен в элементарном режущем профиле (ЭРП) их разновысотности а также разграничив их на режущие и нережущие определим суммарную площадь поперечных сечений абразивных резов нанесенных зернами одного сегмента на обрабатываемую поверхность
j – порядковый номер элементарного режущего профиля; nр nэ- число режущих зерен ЭРП и число самих элементарных профилей соответственно.
С учетом перебега инструмента совпадения резов и упаковки зерен режущая способность круга с многоточечным контактом и сплошного круга с одноточечным контактом с заготовкой соответственно определится
где kC kY - коэффициент совпадения резов и упаковки зерен соответственно; R0 - радиус округления торцев абразивных сегментов; - усредненное значение высоты и ширины режущей части зерен соответственно; n - число сегментов; N - номер зернистости по ГОСТ 3647-80 «Материалы шлифовальные»; u0 - относительный износ; nK n3 - частота вращения круга и заготовки соответственно; - средневероятный размер абразивного зерна; S - расстояние проходимое инструментом за один оборот заготовки; u - минутная продольная подача инструмент; - время шлифования. При увеличении угловой скорости вращения круга К заготовки 3 силы прижатия QC сегментов номера зернистости N числа абразивных сегментов n в круге режущая способность Wk1 возрастает (рис. 9) а при увеличении длины перебега инструмента – уменьшается. Абсолютные значения режущей способности нового инструмента в 27 – 32 раза больше чем сплошного круга работающего по традиционной одноконтактной схеме а коэффициент шлифования выше в 2 раза что свидетельствует о более высокой производительности и стойкости абразивных кругов генерирующих гидродинамические клинья СОЖ.
Математические модели связывающие производительность кругов генерирующих гидродинамические клинья СОЖ с элементами режима шлифования факторами характеризующими строение абразивного материала износ зерен размеры сегментов обрабатываемой поверхности и др. нашли удовлетворительное подтверждение результатами экспериментов поэтому их можно использовать для прогнозирования производительности процесса обработки новыми инструментами.
Рис. 9. Зависимость производительности инструмента от угловой скорости круга (а) угловой скорости заготовки (б) центробежной силы (в) действующей на сегмент и числа сегментов (г)
Пятая глава посвящена разработке высокопрочных конструкций абразивных кругов генерирующих гидродинамические кольцевые потоки и клинья СОЖ. Разработанный инструмент для многоточечного соосного внутреннего шлифования (рис. 10) генерирующий при вращении кольцевые потоки и многочисленные гидродинамические клинья СОЖ обладает достаточной механической прочностью если выполняются условия:
где - соответственно расчетные и допускаемые напряжения абразивного материала сегментов на растяжение срез и смятие; = 15 - угловая скорость вращения круга при испытании на механическую прочность; hэ c2 Bэ – соответственно высота ширина и длина поджимающего элемента; - плотность материала из которого изготовлен поджимающий элемент и режущий сегмент соответственно; - соответственно радиус центра тяжести поджимающего элемента и абразивного сегмента; Fc – площадь поперечного сечения сегмента; R – реакция действующая на абразивный сегмент со стороны обоймы; α1 – угол наклона боковой грани равнобокой трапеции – поперечного сечения сегмента.
Рис.10. Сборный абразивный круг для внутреннего шлифования генерирующий гидродинамические кольцевые потоки и клинья СОЖ: 1-корпус; 2-крышка круга; 3-абразивные сегменты.
Конструкции абразивных кругов прошли испытания на механическую прочность как на стенде так и в процессе резания что позволило применить их в условиях производства.
В шестой главе приведены методика и результаты экспериментальных исследований качества поверхностного слоя деталей обработанных кругами генерирующими гидродинамические кольцевые потоки и клинья СОЖ.
В процессе экспериментальной проверки теоретических моделей формирования геометрических характеристик поверхностей была установлена удовлетворительная сходимость теории и практики что отражено нанесенными экспериментальными точками на теоретических кривых (см. рис. 3 6). Нашли полное подтверждение основные теоретические положения: значительное уменьшение неровностей поверхности при увеличении угловой скорости заготовки отношения угловой скорости заготовки к угловой скорости круга числа сегментов в инструменте и др.
Уравнения регрессии связывающие среднеарифметическое отклонение профиля Rа и волнистость НВ поверхности с элементами режима резания полученные в результате проведенных планируемых многофакторных экспериментов имеют вид
Ra=0445 + 85*10-5nк – 363*10-4 n3 + 285*10-4 n2.х – 95*10-7nзn2.х (23)
HB=049 + 181*10-4 nк – 594*10-4 n3 + 48*10-4 n2.х (24)
где nк n3 n2.х – соответственно частота вращения круга заготовки и частота двойных ходов инструмента.
Зависимости (23) (24) подтверждают результаты теоретических исследований геометрических погрешностей поверхностей обработанных новым инструментом.
Чистовое шлифование кругом генерирующим многочисленные клинья СОЖ при к =150 радс; 3 = 942 радс Sпр = 14 ммс; m = 007 кг; ρ = 004 м; L3 = 20 мм; B = 24 мм; расходе СОЖ равном 3 × 10-4 м3с характеристике абразивного материала сегментов 25А25ПСМ27К5 с последующим выхаживанием в течение 5 7 секунд при к = 60 радc; 3 = 942 радс Sпр = 04 ммс; обеспечивает получение шероховатости Ra = 014 016 мкм (при более длительном выхаживании до 005 007 мкм) средней высоты волнистости по 10 точкам в поперечном сечении отверстий - Wz = 01 03 мкм погрешности формы поперечного сечения отверстий Δ = 25 29 мкм которые недостижимы при такой же характеристике абразивного материала после шлифования сплошным прерывистым цельнопрессованным либо сборным кругом с жестким креплением сегментов к корпусу инструмента.
Исследования остаточных напряжений в поверхностном слое деталей шлифованных одноточечными сплошным (1 схема) сборным кругом с жестким креплением абразивных сегментов к корпусу инструмента (2 схема) и многоточечным сборным кругом генерирующим гидродинамические клинья СОЖ (4 схема) показали что в первом случае формируются растягивающие остаточные напряжения во втором – сжимающие остаточные напряжения до - 100 МПа в третьем случае – 280 300 МПа. Микротвердость после сплошного шлифования составляет Н = 121 185 ГПа после обработки кругом генерирующим гидродинамические клинья СОЖ Н = 202 215 ГПа а микроструктура образцов практически не отличается от исходной.
Полученные результаты по геометрическим показателям качества деталей объясняются не только увеличением в 18 20 раз числа зерен одновременно участвующих в процессе снятия припуска но и многократным увеличением времени резания каждым зерном в течение одного оборота инструмента относительно заготовки.
Высокие результаты по показателям качества характеризующим физико-механическое состояние поверхностного слоя объясняются тем что при одинаковой интенсивности съема металла кругами трех упомянутых конструкций усредненная температура y поверхности шлифуемой кругом генерирующим гидродинамические кольцевые потоки и клинья СОЖ в 12 16 раза меньше чем при шлифовании по 2 схеме и в 20 37 раза меньше чем при шлифовании по 1 схеме. Вместе с этим аналогичные эксперименты проведенные без использования смазочно – охлаждающей жидкости (при сухом шлифовании) показали обратную картину: усредненная температура поверхности y в течение 15 секунд шлифования кругом с многоточечным контактом с заготовкой достигает 300 – 310оС в то время как при шлифовании одноточечным сплошным кругом – 190оС а одноточечным сборным кругом с жестко закрепленными абразивными сегментами – 145 150оС. Эти результаты свидетельствуют о невозможности использования многоточечной схемы шлифования без генерирования гидродинамических кольцевых потоков и клиньев СОЖ.
В седьмой главе представлены практические рекомендации по применению новых инструментов и технологий внутреннего шлифования. Для обеспечения высокой производительности необходимо применять многоточечную схему обработки. Реализация данной схемы приводит к значительному увеличению тепла выделяющегося в зоне резания поэтому критически важным является создание условий для формирования многочисленных гидродинамических клиньев и кольцевых потоков СОЖ с высокой скоростью перемещающихся относительно обрабатываемой поверхности.
Разработаны рекомендации по рациональному выбору параметров инструмента и режима обработки на основе компьютерной визуализации процесса шлифования. Рекомендации предусматривают построение процессов чернового чистового шлифования и выхаживания отверстий. Компьютерная визуализация становится возможной в результате поэтапного решения ряда задач: обоснования математических моделей абразивных зерен в элементарном режущем профиле режущем контуре сегмента и шлифовальном круге в целом; определения числа абразивных сегментов в инструменте выбора характеристики абразивного материала; определения разновысотности зерен компьютерной рандомизации последовательности зерен в круге; формирования рандомизированных массивов абсцисс и ординат вершин режущей части абразивных зерен.
После ввода факторов процесса Sпр Sр к 3 B ln Q m ρ и др. производится компьютерный расчет параболической (для условий чистового шлифования) либо сферической (для черновой обработки) формы зерен различных фракций и на основании выполнения рандомизации распределения зерен в режущем контуре круга на экран выводится процесс снятия припуска массовым внедрением зерен в обрабатываемый поверхностный слой процесс массового наложения резов и поглощения мелких резов резами более крупных зерен. Процедура компьютерной визуализации процесса формирования шлифуемой поверхности новым инструментом не только вскрывает механизм пространственного образования микро- и макрогеометрии поверхности но и наглядно демонстрирует высокую производительность сборного абразивного инструмента с радиально-подвижными сегментами для соосного внутреннего шлифования.
В результате выполненных теоретических и экспериментальных исследований решен комплекс научно-технических задач имеющих важное народнохозяйственное значение и получены технические и технологические решения обеспечивающие существенное повышение производительности абразивной обработки отверстий на основе использования соосных сборных абразивных инструментов с радиально-подвижными сегментами генерирующих гидродинамические кольцевые потоки и клинья СОЖ перемещающиеся со скоростью резания относительно шлифуемой поверхности заготовки.
Установлены взаимозависимости между наличием кольцевых потоков СОЖ гидродинамическими клиньями СОЖ и бесприжоговым режимом внутреннего шлифования особенностью которых является учет того что при вращении разработанного инструмента генерируются не аэродинамические потоки препятствующие попаданию СОЖ в зону обработки а непрерывные кольцевые гидродинамические потоки и многочисленные клинья СОЖ омывающие заготовку со скоростью резания и (за счет высокого давления СОЖ) способствующие ее проникновению в зону обработки.
Разработанная комплексная математическая модель процесса соосного внутреннего шлифования описывает процессы съема металла соосным абразивным инструментом формирования геометрической погрешности движения оси шпинделя заготовки и виброперемещения радиально-подвижных абразивных сегментов круга с учетом влияния создаваемых вращающимся инструментом гидродинамических клиньев СОЖ постоянного равенства диаметров рабочей поверхности круга и обрабатываемого отверстия отклонения от соосности осей круга и шлифуемого отверстия отсутствия жесткой кинематической связи шпинделя круга и абразивных сегментов а также разброса масс и смещения радиально-подвижных абразивных сегментов круга относительно заготовки и корпуса инструмента.
Экспериментально подтверждено что производительность инструмента для соосного внутреннего шлифования в 27 32 раза выше чем у традиционного сплошного круга аналогичных характеристик что обусловлено увеличением площади контакта круга с заготовкой и многократным увеличением времени контактирования каждого абразивного зерна с заготовкой в течение каждого оборота инструмента.
Установлено что виброперемещения абразивного сегмента при соосном внутреннем шлифовании в 3–5 раз меньше перемещений аналогичного по параметрам сборного шлифовального круга работающего по традиционной схеме прерывистого шлифования. Это объясняется диссипацией колебаний шпиндельного узла в области контакта обоймы сегмента с металлическим корпусом шлифовального круга жестко закреплённым на шпинделе станка.
Доказано что для уменьшения погрешности обработки необходимо назначать режимы резания обеспечивающие отношение угловой скорости круга к угловой скорости заготовки представляемое в виде иррациональных дробных чисел или конечных десятичных дробей приближающихся к целому числу.
Экспериментально доказано что для реализации разработанной модели процесс формообразования при соосном внутреннем шлифовании сборным абразивным инструментом с радиально-подвижными сегментами необходимо осуществлять в следующей последовательности:
сборный инструмент с радиально-подвижными сегментами располагают соосно с заготовкой и вводят в емкость образованную обрабатываемой заготовкой и торцовой крышкой с осевым отверстием для подвода СОЖ закрывают вторую крышку емкости с осевым отверстием для слива СОЖ подают в емкость СОЖ сообщают кругу возвратно-поступательное и вращательное движение относительно заготовки включают вращение заготовки;
проводят черновую и чистовую обработку заготовки ступенчато уменьшая частоту вращения инструмента;
выключают вращение инструмента прочие движения формообразования после чего выключают подачу СОЖ снимают торцовую крышку с емкости отводят инструмент извлекают деталь и промывают торцовую крышку для удаления отходов шлифования.
Экспериментально подтверждено что пакет прикладных программ разработанный для выбора рациональных характеристик сборного абразивного инструмента и режимов соосного внутреннего шлифования обеспечивает возможность прогнозирования величин шероховатости волнистости погрешности формы шлифуемых отверстий и позволяет визуально оценивать результаты принятых решений. Проведенные экспериментальные исследования показали удовлетворительную сходимость теории и практики. Разработанные и изготовленные абразивные инструменты успешно прошли экспериментальную проверку как на испытательных стендах так и в процессе производства и могут использоваться без дополнительных ограничений на существующем оборудовании для абразивной обработки.
Экспериментально установлено что давление СОЖ в зоне обработки в наибольшей степени зависит от угловой скорости вращения инструмента что позволяет получить давление СОЖ в 12 МПа и более. Использование разработанного инструмента с радиально-подвижными сегментами и технологии соосного внутреннего шлифования обеспечивает снижение высотных параметров шероховатости до Ra = 014 016 мкм и менее (при характеристике абразивного материала круга 25А25ПСМ27К5) уменьшение средней высоты волнистости в поперечном сечении отверстий до Wz = 01 03 мкм уменьшение в 15 раза отклонения от круглости а также формирование в поверхностных слоях деталей сжимающих тангенциальных остаточных напряжений до = -300 МПа микротвердости Н = 202 215 ГПа и бездефектной микроструктуры чего невозможно достичь при использовании существующих процессов и абразивных инструментов для внутреннего шлифования.
Раздел по охране труда и безопасности жизнедеятельности.
В соответствии с Конституцией Российской Федерации (статья 37) законом от 17 июля 1999 года №181-ФЗ «Об основах охраны труда в Российской Федерации» все граждане РФ имеют право не только на труд но и на безопасность и гигиену труда.
Безопасность жизнедеятельности (БЖД) выявляет и изучает опасные и вредные производственные факторы на рабочем месте и методы их предотвращения или ослабления до предельно допустимых норм с целью устранения производственных несчастных случаев профессиональных заболеваний аварий пожаров и т. д.
Обеспечение нормальных (комфортных) условий деятельности людей улучшение условий труда и повышение его безопасности приводят к снижению производственного травматизма уменьшению случаев профессиональных заболеваний инвалидности что не только сохраняет здоровье работников но и снижает затраты на оплату льгот и компенсаций за работу в неблагоприятных условиях труда.
В данной части мы исследуем вредные и опасные производственные факторы влияющие на оператора на их рабочем месте при проведении технических испытаний по обработке железографитовых порошковых заготовок инструментом оснащенным пластинами из ПКНБ (поликристаллического кубического нитрида бора) рассчитаем вредность их воздействия и выберем средства личной и коллективной защиты в соответствии с ГОСТами.
2. Анализ вредных и опасных производственных факторов.
2.1. Описание рабочего места оператора станка 16К20Ф3С32
По технологии изготовления детали «Цилиндр» произведём анализ наиболее опасных и вредных производственных факторов действующие на рабочем месте оператора станка 16К20Ф3С32. На данной операции идет токарная обработка новым инструментом оснащенным пластинами из КНБ при повышенной скорости резания. Рабочее место оператора представляет собой: станок; пультом управления станком; камера для обдува деталей сжатым воздухом. Станок имеет конвейер подачи заготовок револьверные инструментальные головки которые оборудованы защитными экранами со смотровыми окнами. Данное рабочее место находится в цехе №26.
Согласно ГОСТ 12.0.003-76 рассмотрим опасные и вредные производственные факторы при работе оператора станка это:
микроклимат рабочей зоны
опасность поражения электрическим током при замыкании на корпус
недостаточная освещённость рабочего места
незащищенные подвижные части оборудования
сосуды работающие под давлением
стружка осколки инструмента и вырывание детали
На оператора станка 16К20Ф3С32 существенное влияние оказывают параметры микроклимата рабочего места а именно температура воздуха температура поверхностей относительная влажность воздуха скорость движения воздуха интенсивность теплового облучения.
Повышенная температура воздуха оказывает отрицательное воздействие на здоровье человека вызывает интенсивное потоотделение что приводит к обезвоживанию организма потере минеральных солей ослабляется внимание ухудшается координация замедляются реакции и т.д.
Длительное воздействие повышенной температуры в сочетании с повышенной влажностью может привести к значительному накоплению тепла в организме (гипертермии). При гипертермии наблюдается головная боль тошнота рвота временные судороги падение артериального давления потеря сознания. Длительное воздействие интенсивного теплового облучения приводит к острой сосудистой патологии – коллапс шок.
При воздействии на организм человека пониженной температуры возникает недостаток водорастворимых витаминов также возникают серьезные и стойкие изменения в деятельности сердечно-сосудистой системы увеличивается частота дыхания ухудшается обмен веществ. Низкие температуры действуют и на внутренние органы вызывая их серьезные заболевания.
Данные стандарты описываются государственной системой санитарно-эпидемиологических норм Российской Федерации в санитарных правилах и нормах СанПиН 2.2.4.548-96.
В соответствии с ГОСТ 12.4.011-89 Средствами коллективной зажиты «Средства защиты работающих» являются вентиляционные и очистные сооружения кондиционеры воздуха отопление дезодорация воздуха автоматически контроль и сигнализация. К СИЗ относятся: специальная одежда обувь средства защиты рук средства защиты головы средства защиты лица и глаз дерматологические защитные средства.
2.3. Электрический ток при замыкании на корпус.
Станок питается от промышленной электрической сети поэтому существует опасность замыкания электрического тока на корпус повреждения защитной изоляции что может привести к поражению электрическим током оператора и как следствие остановка сердца получения ожогов различной степени и летальный исход.
Проходя через живой организм электрический ток производит термическое электролитическое и биологическое действия. Термическое действие проявляется в ожогах наружных и внутренних участков тела нагреве кровеносных сосудов и крови и т.п. что вызывает их серьезные функциональные расстройства. Электролитическое - в разложении крови и других органических жидкостей вызывая тем самым самые значительные нарушения их физико-химического составов и ткани в целом. Биологическое действие выражается в раздражении и возбуждении живых тканей организма что может сопровождаться непроизвольными судорожными сокращениями мышц в том числе мышц сердца и легких.
Согласно ГОСТ 12.4.011-89 «Средства защиты работающих» средствами коллективной защиты являются защитное заземление в сочетании с защитным отключением; автоматическое отключение питания; уравнивание потенциалов; двойная или усиленная изоляция; сверхнизкое (малое) напряжение; защитное электрическое разделение цепей. Токоведущие элементы должны быть покрыты изолирующими материалами и не должны быть доступны для случайного прикосновения а доступные прикосновению открытые и сторонние проводящие части не должны находиться под напряжением представляющим опасность поражения электрическим током как в нормальном режиме работы электроустановки так и при повреждении изоляции.
Все электрооборудование и освещение должно отвечать требованиям ГОСТ 27487-87 (на территории РФ ГОСТ Р МЭК 60204.1-99).
2.4. Незащищенные подвижные части оборудования.
Движущиеся машины и механизмы (такие как погрузочно-разгрузочное оборудование) подвижные части промышленного оборудования (столы фрезерных и шлифовальных станков шпиндели). Могут нанести человеку травмы различного характера вследствие физического контакта с ними.
Так как на данном рабочем месте идет механическая обработка предусмотрено перемещение режущего инструмента и заготовки в больших диапазонах скоростей и нагрузок что может привести к серьезным травмам оператора (переломам конечностей ушибам порезам). Данные стандарты описываются государственной системой санитарно-эпидемиологических норм Российской Федерации в санитарных правилах и нормах СанПиН 2.2.4.540-96 «Технологические процессы сырье материалы и оборудование рабочий инструмент» и в санитарных правилах для механических цехов (обработка металла резанием) №5160-89.
В соответствии с ГОСТ 12.2.003—01 «ССБТ. Оборудование производственное. Общие требования безопасности» производственное оборудование должно обеспечивать требования безопасности при монтаже (демонтаже) вводе в эксплуатацию и эксплуатации как в случае автономного использования так и в составе технологических комплексов при соблюдении требований (условий правил) предусмотренных эксплуатационной документацией.
В соответствии с ГОСТ 12.4.011-89 для предотвращения опасности источника на станке с ЧПУ используется защитный экран предотвращающий попадания в подвижные части станка: шпиндель револьверная головка конвейер для сбора стружки частей тела и одежды оператора. Так же предусмотрена электронная защита не дающая запуск станка без поворота ключа и закрытой двери защитного кожуха. Предусмотрены аварийные кнопки остановки в случаи чрезвычайной ситуации.
2.5. Сосуды работающие под давлением.
Применения сжатого воздуха необходимо для обдувки детали и удаления с нее остатков грязи смазочно-охлаждающей жидкости и стружки.
Анализ производственного травматизма показал что большинство травм - травмы глаз и повреждения кожи рук. Глаза и кожа рук чаще всего повреждаются стружкой реже – кусками абразивов и инструмента. Повреждения носят механический (порезы царапины травма глаз) и термический характер (ожоги от горячей стружки абразива).
Данные стандарт описываются в санитарных правилах для механических цехов (обработка металла резанием) №5160-89.
В соответствии с ГОСТ 12.4.011-89 проектирование обдувки сжатым воздухом изделий (деталей) на новом оборудовании разрешается только в специально оборудованных камерах (шкафах) оборудованных местной вытяжной вентиляцией. Пневмотранспорт изделий допускается только при наличии глушителей сброса воздуха обеспечивающих выполнение нормативов по шуму. Для средств индивидуальной защиты применяются защитные очки перчатки предотвращающие попадание сдуваемых частиц в глаза и на руки.
Основными средствами защиты глаз от отлетающей стружки частиц обрабатываемого материала и инструмента являются защитные очки.
Защитные очки выпускают 3 видов:
Очки открытого типа;
Очки с боковой защитой;
Очки закрытого типа.
Так как данное рабочее место расположено в крытом цеховом помещении то встает вопрос о недостаточности естественного освещения.
Долгое пребывание и проведение работ на мало освещенной территории может привести к ухудшению зрения близорукости дальнозоркости заболеваниям сетчатки глаза.
Не достаточное освещение не только утомляет зрение но и вызывает утомление организма в целом. Нерациональное освещение может кроме того явиться причиной травматизма снижения производительности труда и увеличивает брак продукции.
Данные стандарты описываются государственной системой санитарно-эпидемиологических норм Российской Федерации в санитарных правилах и нормах СанПиН 2.2.12.1.1.1278-03 "Гигиенические требования к естественному искусственному и совмещенному освещению жилых и общественных зданий».
Необходимые уровни освещенности нормируются в соответствии со СНиП 23-05-95 ”Естественное и искусственное освещение” в зависимости от точности выполняемых производственных операций световых свойств рабочей поверхности и рассматриваемой детали системы освещения”.
К средствам коллективной зажиты в соответствии с ГОСТ 12.4.011-89 «Средства защиты работающих» необходимо применить дополнительные источники света: осветительные приборы световые проемы. В качестве источников света при искусственном освещении должны применяться преимущественно люминесцентные лампы типа ЛБ. Допускается применение ламп накаливания в источниках местного освещения. Следует производить очистку оконных стёкол отражателей и рассеивателей световой аппаратуры не реже чем раз в 6 месяцев замену перегоревших и вышедших из строя ламп светильников искусственного освещения по мере перегорания и выхода из строя. Наиболее желательно применение ламп светильников в пределах сроков службы оговорённых производителем.
2.7 Стружка осколки инструмента и вырывание детали.
Стружка обрабатываемых материалов (возникает при обработке на высоких скоростях при точении) может попасть на тело человека и нанести ему травмы как механического (порезы царапины травма глаз) так и термического (ожоги от горячей стружки абразива) характера. Повреждения носят механический и термический характер
Осколки металлорежущего инструмента образуются в процессе обработки вследствие его разрушения. Они могут разлетаться с большой скоростью и тем самым нанести травму человеку.
Травмы наносятся иногда при обработке вследствие того что заготовку вырывает из шпинделя или приспособления закрепляющего ее.
Анализ производственного травматизма показал что большинство травм - травмы глаз. Глаза чаще всего повреждаются стружкой реже – кусками абразивов и инструмента. Основными средствами защиты глаз от отлетающей стружки частиц обрабатываемого материала и инструмента являются защитные очки и ограждения зоны резания.
В соответствии с ГОСТ 21836-88 ограждение зоны резания осуществляется с целью защиты станочников от травмирования отлетающей стружкой и уменьшение рассеивания стружки по станку и рабочему месту. Кроме того такие ограждения позволяют предупредить возможность травмирования режущим инструментом или его осколками в случае разрушения инструмента.
3. Методика оценки безопасности рабочего места
Рабочее место - участок помещения на котором в течение рабочей смены или части ей осуществляется трудовая деятельность. Рабочим местом может являться несколько участков производственного помещения. Если эти участки расположены по всему помещению то рабочим местом считается вся площадь помещения.
Оценка безопасности рабочего места проводится по следующей методике:
Оцениваются все источники опасности (см. п.5.2.);
Записываются все допустимые значения параметров источников (из санитарных норм и правил гигиенических норм и других нормативных документов) ;
1. Мощность источника опасности – это та энергия которой обладает источник опасности (jд - допустимая мощность источника).
2. Приведенное расстояние от работающего до опасности
(rд - допустимое расстояние до источника).
3. Время воздействия источника опасности на человека
(tд - допустимое время воздействия).
Измеряются действующие фактические значения источников опасности (измерения проводятся спец. организациями или лицами имеющими право на осуществление данного вида деятельности);
j - фактическая мощность источника
r - фактическое расстояние до источника
t - фактическое время воздействия источника.
Вычисляются показатели безопасности каждого источника опасности;
Для оценки безопасности рабочего места проводят оценку для каждого источника опасности по формуле (5.1).
Если показатель безопасности b если bi 0 то источник еще опаснее и необходимо предусмотреть дополнительные меры безопасности.
Вычисляется показатель безопасности каждого рабочего места.
Показатель безопасности рабочего места при воздействии на него нескольких источников опасности определяется по формуле:
где М – число источников опасности;
4 Анализ безопасности работающего
4.1 Принципиальная схема рабочего места
На рабочем месте оператора действуют следующие опасные и вредные производственные факторы:
Рис. 5.1. Схема воздействия опасных и вредных производственных факторов на оператора станка5.4.2. Расчет показателей безопасности каждого источника опасности.
4.2.1.Электрический ток при замыкании на корпус.
Все электрооборудование и освещение должно отвечать требованиям ГОСТ 27487-87 (на территории РФ ГОСТ Р МЭК 60204.1-99) а также ССБТ ГОСТ 12.1.030-81.
Для предотвращения опасности источника на рабочем месте разработана инструкция по электробезопасности предусматривающая применение СКЗ и СИЗ. В соответствии с ГОСТ 12.4.011-89 «Средства защиты работающих» применяется защитное заземление в сочетании с защитным отключением все токоведущие элементы покрыты изолирующими материалами. При соблюдении инструкции исправном состоянии средств защиты и контроля параметров их защиты – фактор не опасен. В результате b2 > 0
4.2.2.Незащищенные подвижные части оборудования.
Данные стандарты описываются государственной системой санитарно-эпидемиологических норм Российской Федерации в санитарных правилах и нормах СанПиН 2.2.4.540-96 «Технологические процессы сырье материалы и оборудование рабочий инструмент» и в санитарных правилах для механических цехов (обработка металла резанием) №5160-89.
В соответствии с ГОСТ 12.4.011-89 «Средства защиты работающих» на станке используется защитный экран предотвращающий попадания в подвижные части станка (шпиндель револьверная головка конвейер для сбора стружки) частей тела и одежды оператора так же предусмотрена электронная защита не дающая запуск станка без поворота ключа и закрытой двери защитного экрана. Предусмотрены аварийные кнопки остановки в случаи чрезвычайной ситуации. При соблюдении правил и требований техники безопасности инструкций исправном состоянии средств защиты и контроля их параметров – фактор не опасен. В результате b3 > 0.
4.2.3. Сосуды высокого давления.
В соответствии с ГОСТ 12.4.011-89 «Средства защиты работающих» рабочее место оператора оборудовано камерой для обдувки сжатым воздухом изделий (деталей). При соблюдении правил и требований техники безопасности инструкций исправном состоянии средств защиты и контроля их параметров – фактор не опасен. В результате b4 > 0.
В соответствии с ГОСТ 12.4.011-89 «Средства защиты работающих» на рабочем месте уставлены дополнительные источники искусственного света. При соблюдении правил и требований техники безопасности инструкций исправном состоянии средств защиты и контроля их параметров – фактор не опасен. В результате b5 > 0.
4.2.5. Стружка осколки инструмента и вырывание детали.
В соответствии с ГОСТ 12.4.011-89 «Средства защиты работающих» предусмотрено применение таких средств защиты рабочих как: защитные экраны защитные очки спец. одежда. При соблюдении правил и требований техники безопасности инструкций исправном состоянии средств защиты и контроля их параметров – фактор не опасен. В результате b6 > 0.
4.3. Оценка безопасности рабочего места.
Рассчитаем показатель опасности всего рабочего места оператора:
По результатам расчётов при использовании всех выше перечисленных средств защиты и выполнении требований безопасности делаем вывод что рабочее место оператора станка 16К20Ф3С32 является безопасным.
Для повышения коэффициента безопасности и условии труда трудящихся также предусмотрены средства коллективной защиты которые описываются в «Общих сведениях о производственном оборудовании и технологическом процессе. Опасные и вредные факторы возникающие при эксплуатации оборудования». Применение знаков безопасности труда расширяет круг мероприятий способствующих предотвращению несчастных случаев среди работников.
4.4. Динамическая виброизоляция станка 16К20Ф3С32
ФУНДАМЕНТЫ ПОД МЕТАЛЛОРЕЖУЩИЕ СТАНКИ
Устройство фундаментов. Основанием для фундаментов под станки не чувствительные к неравномерным осадкам может служить грунт с нормативном давлением более 1 кгсм2.
Для уменьшения высоты фундамента можно применять песчаные подушки.
В зависимости от конструкции станки можно устанавливать па жестком подстилающем слое пола (бетонная подготовка) или на отдельно стоящих фундаментах.
Станки весом до 8 т кроме долбежных и поперечно-строгальных чувствительных к вибрациям основания (например коордннатао-расточные станки) допускается устанавливать на бетонном подстилающем слое пола цеха толщиной 15—20 см (бетонный слой под станину без учета чистого пола должен быть не менее 100 мм).
Специальные фундаменты под станки сооружают в виде бетонных плит блоков ИЛЕ лент из бетона марки 100
Требования к виброизоляции металлорежущих станков при бесфундаментной установке.
Укрупненные группы станков по требованию их к виброизоляции
Основные требования к виброизоляции станков и рекомендуемые виброизолирующие опоры
Прецизионные станин имеющие жесткий станины: координатно-расточные зуборезные алмазно-расточные Шлифовальные с плавным характером реверса поступательно движущихся элементов
Устанавливают на упругих резинометаллических опорах ОВ-30 и ОВ-31 такой жесткости чтобы частота собственных колебаний станка на упругих опорах в вертикальном направлении fв составляла 14-18 Гц.
Станки нормальной точности для которых требуется: осуществить бес фундаментную установку и защиту от сбои размерной настройки при ударах вблизи станка. Прецизионные токарные станки на которых не производится обработка деталей с большой неуравновешенностью
Устанавливают на упругих резинометаллических опорах ОВ-30 и ОВ-31 с такой жесткостью чтобы частота собственных колебаний станка на упругих опорах в вертикальном направлении составляла fв =18-22 Гц.
Прецизионные станки с недостаточно жесткими станинами с большими скоростями движения поступательно-движущихся элементов с резкими реверсами. - Прецизионные токарные станки на которых производится обработка деталей с большой неуравновешенностью
Устанавливают па монолитных железобетонных блоках на резиновых виброизолирующих ковриках КВ-1 и КВ-2 в специальной шахте причем между блоком и стенками шахты должны быть оставлены зазоры. Заливку бетонного блока необходимо производить на коврик покрытый гидроизоляционной бумагой и тонким железным листом обеспечивающим равномерное распределение нагрузки на коврик. Собственная частота колебаний массы станок - блок на коврике fв должна быть в пределах 14-22 Гц.
Станки делительные машины и приборы особо высокой точности весьма чувствительные к колебаниям а также другие прецизионные станки при установке в помещениях с очень высоким уровней колебаний
Устанавливают на резинометаллических опорах ОВ-30 с пониженной частотой fв=10-12 Гч
К20Ф3С32 – относиться к 2й группе станков
Номограмма для подбора опор ОВ-30 и ОВ-31 при установки станков:
I — станин токарной группы если на них не должна производиться обработка тяжелых деталей со значительной неуравновешенностью или с ударами; фрезерной группы- горизонтальный вертикальные универсально-фрезерные копировально-фрезерные зубо-фрезерные;
II — станки шлифовальной группы: плоско- кругло- внутри- и резьбо-шлифовальные при плавном реверсе перемещающихся узлов; координатно-расточные станки устанавливаемые на три опорные точки отделочно-расточные;
III - делительные машины высокоточные станка при высоком уровне колебаний основания
При нагрузке на опору 50006=834 Кг требования к виброизоляции удовлетворяет опора
Резинометаллические опоры ОВ-30
Нагрузка а Кг при собственной частоте в Гц
Наибольшая рабочая нагрузка в Кг
Проведенный анализ факторов опасного и вредного воздействия показал что оператор станка 16К20Ф3С32 является подверженным воздействию опасного фактора – поражению электрическим током при замыкании на корпус а также воздействию вредных факторов: микроклимата рабочей зоны недостаточной освещённости рабочего места опасности использования сосудов работающих под давлением разлетающейся стружки осколков инструмента и вырванной заготовки.
Станок 16К20Ф3С32 для оптимальной виброизоляции необходимо установить на 6 опор ОВ-30-3-3.
1 Исходные данные для проектирования
Годовая трудоёмкость участка Т=100000 нч в год
Масса заготовки - 479 кг .готовой детали - 056 кг .
2 Режим работы цеха и фонды времени работы оборудования и рабочих
Принимаем 2-х сменный режим работы т.е. q = 2.
Действительный годовой фонд времени работы оборудования
Фонд времени работы рабочих
Фонды времени работы рабочих
Продолжительность рабочей недели ч.
Продолжительность отпуска дней
Потери номинального фонда бремени %
Действительный фонд бремени Fnp ч
3 Технологические процессы и новая техника. Основные положения по организации производства на участке.
Способ получения заготовки : В проектируемом техпроцессе заготовкой является пруток из которого получают заготовки.
Характер выбранного оборудования : В качестве технологического оборудования принято оборудование- станки с ЧПУ.
Ведомость трудоемкости детали «Цилиндр» Таблица 6
Заготовительная.Токарная с ЧПУ
Сверлильно- фрезерная с ЧПУ
Общее время по типу оборудования :
- Токарный станок с ЧПУ АТ-320 : 10 мин.
- Токарный станок с ЧПУ 16К20Ф3С32 : 70 мин.
- Сверлильно-фрезерный станок с ЧПУ МА655А1 : 40 мин.
- Токарный станок с ЧПУ SPT 16NC : 15 мин.
- Шлифовальный станок с ЧПУ «Studer» : 30 мин.
Общее время : t Σ = 165 мин.
Определение коэффициэнта закрепления операций :
К з.о. = (Fд ·60 · n · ) (t Σ ·П) = (3890 ·60 · 10 ·08 ) (165 ·1000) =1131
Коэффициэнт закрепления операций 10-20 К з.о. =10- 20 11.31 т.е серийное
Определение приведенной программы.
Приведенная программа участка определяется по формуле [1стр.10]:
4 Расчет технологического оборудования.
4 Ведомость оборудования участка. Таблица 3
Сверлильно-фрезерные
5 Расчет количества оборудования цеха
- Ведомость металлообрабатывающего оборудования механического цеха Таблица 4
Сверлильно-фрезерные с ЧПУ
6 Расчет грузооборота механического цеха
- Грузооборот заготовок
- Грузооборот деталей
- Общая масса грузов транспортируемая в ПРОСК и обратно на ТО и обратно
- Определение массы производственных отходов
- Определение общего (годового) грузооборота цеха
Сводная ведомость грузооборота цеха. Таблица 5
Полуфабрикаты из ПРОСК
Полуфабрикаты в ПРОСК
7 Выбор и расчет подъемно-транспортных средств
- Выбор подъемно-транспортных средств для перевозок внутри цеха.
В качестве межоперационного транспортного средства применяют ручные тележки грузоподъемностью 01 т. [9стр.17].
- Выбор подъемно-транспортных средств для цеховых и внутрицеховых перевозок
В качестве межцехового транспортного средства применяют электротележки (электрокары) грузоподъемностью 2 т. и средней скоростью передвижения 10 кмч. и ручные тележки для мелких грузов [9стр.18].
- Расчет подъемно-транспортных средств для межцеховых и внутрицеховых перевозок
где Q - годовой грузооборот т.
К1 - коэффициент неравномерности 120 [9стр19];
К2 - коэффициент использования грузоподъемности ~08 [11стр.89];
QЭ - грузоподъемность тележки т;
Fд - действительный годовой фонд времени работы оборудования.
ТЭ - общее время пробега электротележки в мин:
ТЭ = ТПР + ТП + ТР + ТЗ ;
Время пробежки тележки:
Время погрузки-разгрузки:
Время случайных задержек:
ТЗ = 10%×(ТПРОБЕГ + ТПОГР + ТРАЗГР) = 01×(36 + 10 + 10) = 24 мин.
ТЭ = 36 +10 + 10 + 24 = 26 мин.
8 Вспомогательные службы цеха
- Заточное отделение
-Количество оборудования
Количество основных станков заточного отделения:
Сзат = Сзат.общ + Сзат.спец + Сдов ;
Заточные станки общего назначения:
Сзат.общ = Кобсл × КП ×( Сцех - Сшл -Сспец);
Сзат.общ = 156 шт; - общее количество оборудования механического цеха;
Сспец= 0- количество металлорежущих станков для которых требуется обслуживание специальными заточными инструментами;
Сшл = 0- количество станков инструмент которых не подлежит заточке;
Кобсл = 005 - коэффициент обслуживания металлорежущих станков [2стр.4т.1];
КП = 08 - коэффициент учитывающий использование неперетачиваемых пластин [2стр.4].
Сзат.общ = 005 × 08 ×(168-0-0) = 672 шт.
Принимаем Сзат.об = 7 шт.
Заточные станки специального назначения:
Сзат.спец = 0. Принимается по [10стр.4т.2].
Сдов = 20% (Сзат.общ + Сзат.спец) = 02 ×(7 + 0) =14шт.
Принимаем Сдов = 2 шт.
Общее количество станков заточного отделения:
Сзат = 7 + 0 + 2 =9 шт.
Площадь заточного отделения: Sзат = 9 × 10 =90 м2.
- Отделение ремонта приспособлений и инструмента (РЕМПРИ)
- Количество оборудования
Количество основных станков: СРЕМПРИ =4[10стр.10т.2].
Площадь отделения РЕМПРИ: SРЕМПРИ = 22 × 4 =88 м2.
- Цеховая ремонтная база (ЦРБ)
Количество основных станков:
SЦРБ = SН × СЦРБ = 35 × 8 = 280 м2.
SН = 35 м2 - норма на станок [2стр.11].
- Площадь мастерской по ремонту электрооборудования
SМРЭ = 02 × SЦРБ = 02 × 280 = 56 м2.
- Площадь мастерской по ремонту вентиляции
SМРВ=015 × SЦРБ = 015 × 280 = 42 м2.
- Инструментально - раздаточные кладовые (ИРК)
Площадь ИРК рассчитываем по формуле:
SИРК = SH × Cобщ = 05 × 168 = 84 м2;
SH = 05 м2ед. -норма на один станок основного производства [10стр.13т.6].
К площади ИРК добавляют склада абразивов как отдельное помещение он не создаётся а его функцию выполняет ИРК.
Итоговая площадь ИРК: 84+6=90
- Контрольное отделение
Площадь общецеховых отделений контроля составляет 4% от производственной площади цеха.
SОТК = 004 × 3 120 = 125 м2.
- Служба сбора и переработки стружки
*** Определение системы сбора стружки
Выбираем механизированную систему сбора стружки с использованием ручного труда средств малой механизации и колесного транспорта доставляющего стружку в контейнерах в отделение переработки.
- Площадь отделения сбора и переработки стружки
Sструж. = 95 м2 [10стр.17].
- Кладовая склада ГСМ
SСГСМ = SH × Cобщ = 01 × 168= 16817 м2.
SН = 01 м2ед. [10стр.17].
Площадь отделения для приготовления и раздачи СОЖ может быть укрупнено определена в зависимости от количества металлорежущего оборудования.
SСОТС = 60 м2 [10стр.17].
- Трансформаторная подстанция
SТр.под. = 50 м2 [10стр.26].
Примечание: Если площадь любого помещения в цехе по расчёту меньше 6 м2 то принимаем -6 м2.
- Цеховые склады: металла и заготовок межоперационный (ПРОСК) и готовых деталей
- Площадь цехового склада металлов и заготовок при укрупнённом проектировании [2 стр. 21]:
где Q = 50625 т. - черный вес материалов и заготовок в течение года (обработка);
t = 4 дн. [2 стр. 20 т.8] - норма хранения материала на складе дни;
Ф = 254 дн. - количество рабочих дней в году;
q = 18 тм2 [2 стр. 21] - допустимая нагрузка (грузонапряженность) на пол склада тм2
К - коэффициент использования площади склада учитывающий проходы и способ загрузки транспортного средства;
Принимаем FЗАГ = 6 м2.
t = 2 дн. [10 стр.22 т.9];
q = 22 тм2 [10стр.22т.9];
КИ = 025 [10стр.22];
Принимаем FПРОСК = 23 м2.
- Склад готовых деталей
t = 1 дн. [2 стр.22т.9]
q = 18 тм2 [2 стр.22т.9]
Принимаем FДЕТ = 6 м2.
- Слесарное отделение
SСЛЕС = К × SН × ССЛЕС = 08 × 8 ×25 = 160 м2.
Сводная ведомость вспомогательных площадей цеха Таблица 6
Мастерская по ремонту электрооборудования
Мастерская по ремонту вентиляции
Контрольное отделение
Отделение сбора и переработки стружки
Трансформаторная подстанция
Склад металла и заготовок
Склад готовых деталей
Всего площадь вспомогательных служб
9 Определение численности работающих.
- Численность рабочих - станочников
Количество производственных рабочих - станочников определяем по формуле:
КМС = 1 - коэффициент многостаночности [11стр.148].
Fд.р. =1781 –действительный фонд времени работы рабочих
- Количество слесарей
Количество слесарей определяем по формуле:
Расчёт численности производственных рабочих:
Определение количества основных рабочих занятых в 1 и 2-ю смены.
Во вторую смену: РПР-Рпр1см=319-175=144 чел.
- Численность вспомогательных рабочих
РВСП = 02 × РПР = 02 × 319 = 64 чел. [11стр.149]
РИТР = 011 × РОБЩ = 011 × (319 +64) = 42 чел. [11стр.150]
- Определение количества счётно-конторского персонала:
- Численность служащих
РСлуж =5 чел. [11стр.150]
РМОП = 0016· РПР =0016·319=5 чел. [11стр.150]
РОТК = 006· РПР =006·319=19 чел. [11стр.150]
Сводная ведомость состава рабочих. Таблица 7
Производственные рабочие
Счётно-конторский персонал
10 Расчет площадей промышленного корпуса
Площадь промышленного корпуса механического цеха рассчитывается по указанным ниже формулам и уточняется планировочными решениями.
FПроизв = F Уд.произв. × СПР = 20·168= 3 360 м2.
FУд.произв. = 20 м2ст. [11стр.152]
При модуле 72x72 ширина магистральных проездов 5 м (рядом со вспомогательным корпусом) тогда:
Поперечный проезд - 3 м шириной (рядом со складом): S = 3·72 = 216 м2
и на две стороны 2x216 = 432 м2.
Итого: 360 + 432 = 792 м2.
Расчёт общей площади производственного корпуса:
FОбщ. = FПроизв. + FВсп. + Fмп = 3 360 +(1 182 +792) = 5 334 м2.
11 Расчет площадей вспомогательного корпуса
Расчет площади вспомогательного корпуса. Таблица 8
Группа санитарно-гигиенической характеристики
Норма на одного списочного работающего
Количество работающих по списочному составу
Санитарно - гигиеническая
ИТОГО по санитарно - гигиенической службе
Общественного питания
Культурно-массового обслуживания
ОБЩАЯ площадь корпуса
12 Выбор зданий для промышленного и вспомогательного корпусов
Для промышленного корпуса используем сетку колонн 24 12 м с типовым модулем 72 72 : площадь промышленного корпуса: FПром.к. = 72 72 = 5 184 м2.
(Рассчитанная площадь производственного корпуса 5 083 м2)
Для вспомогательного корпуса используем модуль 12 72 с сеткой колонн
12 количество этажей 3:
Полная площадь вспомогательного корпуса FВсп.к. = 3 × 12 × 72= 2 592 м2.
(Рассчитанная площадь вспомогательного корпуса 2 515 м2)
13 План размещения оборудования участка
Основной принцип размещения оборудования - прямоточность движения детали в процессе обработки и обеспечение нормированных расстояний между станками.
14 Расчет энергетики цеха
- Активная мощность электроприемников
NА = NУСТ × КС =13736× 025 =343 кВт
КС = 025 [12 стр.380]
- Расход энергии на производство
W ПР = NА × FД. × hЗ = 343 × 3890 × 087 =1 160 814 кВт [12стр.378]
- Расход энергии на освещение
W ОСВ. = Nламп × 10 -3 (FПроизв.+ FВсп.)×Ф = 15 × 10 -3 ×( 5 184+2 592)×1300 =151 632 кВт [12стр.378].
- Общий расход электроэнергии
SW = W ПР + W ОСВ =1 160814 + 151 632 =1312 446кВт
- Расход сжатого воздуха
QОбд.ст. = qсж × FД ×hз × СОбщ = 17 × 3890 × 087 × 26 =149 586 м3год.
qсж - действительный среднечасовой расход сжатого воздуха на 1 станок
qсж = 17 м3ч. [12стр.380]
- Пневмотические зажимы
QП.З = qсж. × FД × hз × СОбщ = 351 967 м3год.
qсж = 4 м3ч. [12стр.380].
- Суммарный расход сжатого воздуха
SQ = QОбд.ст. + QП.З. =149586 + 351967 =501 553 м3год.
- Годовой расход воды
- На приготовление СОТС
qв = 06 лчас [12стр.81].
- Промывка деталей в моечных машинах
QПром. = qВ.пром × QДЕТ = 03 ×12217 =3665 м3год.
qВ.пром = 03 м3час. [12стр.381].
Для хоз. - питьевых нужд.
QВ.хоз. = (qВ × РСпис × FДр) 1000× 8 = (25 × 455 × 1781)1000× 8 = 2 532 м3год.
qВ = 25 лчел [12стр.381].
Для групповых умывальников.
QВ.ум. = (qв.ум × РСпис × FДр.) 1000× 8 = (3 × 455× 1781) 1000× 8 = 303 м3год.
qв.ум = 3 лчел. [12стр.381].
- Расход воды для душа
QВ.душ. = (qВ × РСпис × FДр.) 8×1000 = (40 × 455 × 1781)8·1000 = 4 051 м3год.
qВ = 40 лчел [12стр.381] - средний расход воды в душе лчел.
- Суммарный расход воды
SQ = QСОТС + QПром. + QВ.хоз + QВ.ум + QВ.душ. = 341+3665+2532 +303+4051 =
Горбацевич А.Ф. Шкред В.А. Курсовое проектирование по технологии машиностроения: Учебное пособие для машиностроительных специальностей вузов 4-е издание перераб. и доп. – Минск Вышейшая школа 1983 г.
Прогрессивные режущие инструменты и режимы резания металлов Баранчиков В.И. Справочник. М. «Машиностроение» 1990 г.
. Загрузочные устройства для металлорежущих станков. Малов А.Н. Изд. 2-е перераб. И доп. М. «Машиностроение» 1972 400 с
Автоматизация загрузки станков. Камышный Н.И.
«Машиностроение» 1977 268 с.
Транспортные и загрузочные устройства автоматических линий-
Бобров В. П. Чеканов Л. И. Учебное пособие для машиностроительных техникумов. По специальности «Монтаж и эксплуатация металлообрабатывающих станков и автоматических линий». - М.- Машиностроение 1980. - 119 с.
Системы питания автоматов в приборостроении. Гринштейн Я.Г. Вайсман Е.Г. М. «Машиностроение» 1966 180 с.
Комплексная автоматизация производства. Волчкевич Л.И. и др. М.- Машиностроение 1979 190 с.
Технология машиностроения Мельников Н.Ф. и др. М. Машиностроение
Расчеты потребного количества технологического и транспортного оборудования в дипломном проекте : Методические указания. ПГТУ 1985.
Расчеты площадей промышленного и вспомогательного корпусов. План цеха : Методические указания. ПГТУ 1985.
Основы проектирования машиностроительных заводов. Мамаев B.C. Осипов Е.Г. М. "Машиностроение" 1974.
Основы проектирования машиностроительных заводов. . Егоров М.Е. - М; Машиностроение1982.
Режимы резания металлов Барановскийй Ю.В. Справочник. М. «Машиностроение» 1990 г.
Справочник конструктора по расчету станочных приспособлений . Антонюк В.Е. - Беларусь 1969.
Загрузочное устройство_Готово.cdw

Неуказанные предельные отклонения H14
Остальные технические требования по ОСТ1.51896-82
Спец часть.cdw

генерирующий гидродинамические кольцевые потоки и клинья СОЖ:
-корпус; 2-крышка круга; 3-абразивные сегменты.
Рекомендуемые чертежи
- 24.01.2023
- 24.01.2023
- 13.12.2022
- 24.01.2023