Проектирование редуктора ленточного конвейера




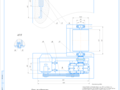
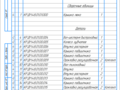

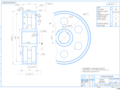
- Добавлен: 24.01.2023
- Размер: 2 MB
- Закачек: 0
Описание
Проектирование редуктора ленточного конвейера
Состав проекта
![]() |
![]() |
![]() ![]() ![]() |
![]() |
![]() ![]() ![]() ![]() |
![]() ![]() ![]() ![]() |
![]() ![]() ![]() ![]() |
![]() ![]() ![]() ![]() |
![]() ![]() ![]() ![]() |
![]() ![]() ![]() ![]() |
![]() ![]() ![]() ![]() |
![]() ![]() ![]() |
![]() ![]() ![]() |
![]() |
Дополнительная информация
Курсовой ДМ .docx
Кинематический расчёт привода 5
Расчет закрытой прямозубой цилиндрической передачи 7
Расчет клиноременной передачи 12
Проектировочный расчет валов привода 18
1 Проектиорвание быстроходного вала редуктора20
2 Проектиорвание тихоходного вала редуктора 21
Подбор и расчёт шпоночного соединения 22
Проверочный расчёт быстроходного вала24
Построение эпюр быстроходного вала27
Расчёт подшипников29
Разработка конструкции крышек подшипников32
Выбор смазочных материалов и системы смазки редуктора 33
Описание сборки и регулировки редуктора34
Проектируемый привод ленточного конвейера состоит из асинхронного электродвигателя 1 клиноременной передачи 2 передающей вращательное движение от электродвигателя к быстроходному валу Б через одноступенчатую закрытую прямозубую цилиндрическую передачу редуктора З. На тихоходном валу редуктора Т на выходном валу которого установлена муфта зубчатая 4 передающая вращательное движение к приводному валу привода ленточного конвейера 5. Привод устанавливается на сварной раме. Рабочая нагрузка привода постоянная. Пусковая нагрузка до 125% от номинальной. Работа привода односменная.
Рис. 1 Эскиз ленточного конвейера
Кинематический расчет привода.
1 Последовательность соединения элементов привода:
2 Принимаем значения КПД элементов привода:
оn=095 – КПД открытой ременной передачи;
цзп=097 – КПД цилиндрической зубчатой передачи;
пк=099 – КПД пары подшипников качения;
3 Определим общий КПД привода:
пр = оп цзп м пк3=0950970980993=088
4 Определим требуемую мощность электродвигателя:
5 Предварительно принимаем передаточные числа передач привода:
Uоп = 25 – передаточное число открытой клиноременной передачи;
Uцзп = 5 – передаточное число цилиндрической зубчатой передачи;
6 Определим предварительное значение передаточного числа привода.
Uпр = U оп U цзп = 255 =125.
7 Определим требуемую частоту вращения электродвигателя:
n тр = n в U тр = 155125 = 19375 мин-1.
8 По требуемой мощности Ртр= 568 кВт и частоте вращения n тр = 19375 мин-1 выбираем ближайшую стандартную. Перегрузка асинхронных двигателей допускается до 8%. [6 стр. 7]
При подсчёте перегрузки электродвигателя с меньшей мощностью которая составляет Рэд= 55 кВт будет равна:
что не превышает 8%.
Выбираем электродвигатель трехфазный асинхронный короткозамкнутый типа 4A112М4У3 с мощностью РДВ = 550 кВт и номинальной частотой вращения nДВ=1445 мин-1
Габаритные размеры электродвигателя (мм.):
2х310х260 мм. высота оси вала до основания h=112 мм. вес 56 кг. [4 табл.2.5 стр. 28]
9 Определим действительное передаточное число привода.
10 Передаточное число ременной передачи оставляем равным ранее принятому:
11 Определим передаточное число цилиндрической зубчатой передачи:
12 Определим частоты вращения валов привода:
nдв = 1445 мин-1 - вал двигателя;
мин-1- быстроходный вал редуктора;
мин-1- тихоходный вал редуктора;
= 155 мин-1 - приводной вал;
13 Определим мощности на валах привода:
РДВ= 55 кВт - вал двигателя ;
PБ=Pдвоппк=55095099=517 кВт - быстроходный вал редуктора ;
PТ=PБцзппк=517097099=496 кВт - тихоходный вал редуктора ;
РВ=Pтмпк=496098099=481 кВт - приводной вал.
14 Определим крутящие моменты на валах привода:
Тдв= = 3787 Нм - на валу электродвигателя;
ТБ=9950 Нм – на быстроходном валу;
Тт=9950 Нм – на тихоходном валу редуктора;
Тв=9950=30877 Нм –на приводном валу;
15 Результаты расчётов сводим в таблицу:
Таблица 1. Мощности частоты вращения вращающие моменты.
Частота вращения n мин-1
Крутящий момент Т Нмм
Расчёт закрытой прямозубой цилиндрической передачи.
Исходные данные для расчёта:
– Крутящий момент на ведущем элементе передаче (шестерне)
– Крутящий момент на ведущем элементе передаче (колесе)
Т2 = 31848·103 Н·мм;
– частота вращения ведущего элемента передачи (шестерни)
– частота вращения ведомого элемента передачи (колеса)
– срок службы передачи Lh = 7500 часов;
– Передаточное число зубчатой передачи UЦЗП = U= 373
1 Выбираем в качестве материала колеса – сталь 45 с термообработкой в виде нормализации с твердостью Н2=179 207 HB. Имеющую следующие механические характеристики: предел прочности в=600 Нмм2 и предел текучести T =320 Нмм2. [1 с.13 табл.7].
2 Выбираем в качестве материала шестерни ту же сталь 45 с термообработкой в виде улучшения с твердостью Н1 =192 240 HB. Имеющую следующие механические характеристики: предел прочности в =750 Нмм2 и предел текучести T = 450 Нмм2 [1 с.13 табл.7].
3 Определим средние значения твердости шестерни НВ1 ср и колеса НВ2 ср.
НВ1 ср=05(Н1 min + H1 max)=05(192+240)=216.
НВ2 ср=05(Н2 min + H2 max)=05(179+207)=193.
Необходимая разность твердостей (20 НВ) шестерни и колеса обеспечена.
4 Определим числа циклов перемены контактных напряжений для шестерни NHO1 и NHO2.
NHO1=30(Н1 ср)24=30(216)24=12106
NHO2=30(Н2 ср)24=30(193)24=92106.
5 Определим действительное число циклов перемены напряжений для шестерни.
N1= 60n1Lh= 605787500 = 2601106.
где n1=nб=578 мин-1 – частота вращения шестерни.
6 Определим действительное число перемены напряжений для колеса.
N2= 60n2Lh = 601557500 = 6975106.
где n 2= nт = 155 мин-1 – частота вращения колеса.
7 Определим коэффициенты долговечности для шестерни KHL1 и колеса KHL2.
Если полученные результаты KHL1 и KHL2 1 то принимаем KHL=1.
8 Определим длительные пределы контактной выносливости для активных поверхностей шестерни Hlim1 и колеса Hlim2
Hlim1=2НВ1 ср+70=2216+70=502 Нмм2
Hlim2=2НВ2 ср+70=2193+70=456 Нмм2.
9 Принимаем коэффициенты безопасности для шестерни [SH]1=11 и колеса [SH]2=11
10 Определим допускаемые контактные напряжения для шестерни [H]1и колеса [H]2.
[H]1= KHL1= = 45636 Нмм2
[H]2= KHL2= = 414545 Нмм2
11 Определим расчетное допускаемое контактное напряжение.
[H]=05([H]1+[H]2)=05(45636+414545)=4355 Нмм2
Полученное значение [H] 125[H]2=125414545=5182 Нмм2
значит принимаем в качестве расчетного допускаемого контактного напряжения [H]=435 Нмм2 округлённое до целого числа. [1 стр. 15]
12 Принимаем приведенный модуль упругости для стальных колес Епр=21105 Нмм2.
13 В цилиндрическом зубчатом редукторе расположение зубчатых колес относительно опор симметричное поэтому при твердости поверхности зубьев шестерни Н1 ср 350 HB принимаем коэффициент ширины колеса относительно межосевого расстояния передачи =04 [1 с.17 табл.10] и предварительное значение коэффициента неравномерности распределения нагрузки по ширине колеса KH=107 [1 с.18 табл.11].
14 Определим предварительное значение межосевого расстояния передачи из условия контактной усталости зубьев [2 с.135].
где U =UЦЗП = 373– передаточное число цилиндрической зубчатой; T2 = TT = 31848 Hмм – крутящий момент на колесе передачи.
15 Определим предварительное значение ширины зубчатого колеса передачи.
Принимаем стандартное ближайшее значение ширины зубчатого колеса из ряда нормальных линейных размеров =65 мм [6 стр.363 табл.19.1].
16 Определение диапазона рекомендуемых значений окружного модуля передачи [1 с.19 табл.13].
17 Принимаем стандартное значение нормального модуля mn=2 мм. [1 с.19 табл.14].
18 Oпределяем предварительное значение числа зубьев шестерни. [4 стр. 46]
Полученное значение числа зубьев шестерни округлим до ближайшего целого числа .
19 Определяем предварительное значение числа зубьев колеса:
20 Определяем действительное передаточное число зубчатой передачи:
21 Определяем отклонение действительного передаточного числа передачи U от заданного U [1 стр. 17; 7 стр. 60]
где = 3% - допускаемое отклонение передаточного числа от заданного [1 стр. 22]
22 Определяем действительное значение межосевого расстояния передачи. [7 стр. 60].
23 Определяем делительные диаметры шестерни d1 и колеса d2 [1 стр.116; 7 стр. 60]
d1= mn Z1 =234 =68 мм. ;
d2 = mn Z2 =2126 =252 мм .;
24 Определяем диаметры окружностей вершин зубьев шестерни da1 и колеса da2 .[1 стр. 117; 7 стр. 61]
25 Определяем диаметры окружностей впадин зубьев шестерни и колес [1 стр. 117; 6 стр. 18; 7стр. 61]
26 Определяем диапазон рекомендуемых значений ширины шестерни. [7 стр. 61; 8 стр. 44]
Принимаем из ряда нормальных линейных размеров стандартное значение ширины шестерни b1 входящих в диапазон рекомендуемых значений b1
2. Производим проверочный расчёт закрытой прямозубой цилиндрической передачи.
2.1 Определяем окружную скорость зубчатых колёс:[6 стр. 18; 8 стр. 44)
2.2 Назначаем степень точности ST передачи в зависимости от окружной скорости зубчатых колёс V (табл. 15)
2.3 Определяем окружную силу в зацеплении зубчатых колес: [1 с. 132 133] [3 с.197] [2 с. 119] [5 с. 53] [6 с. 23]
2.4 Определяем радиальную силу в зацеплении [1 с. 132 133] [3 с.197] [5 с. 54] [6 с. 23]
- стандартный угол зацепления [1 с. 115 116] [5 с. 44] [6 с. 23]
2.5 Определим значение коэффициента ширины шестерни относительно его диаметра.
2.6 Принимаем значение коэффициента неравномерности распределения нагрузки по ширине колеса [5 стр. 19 табл 2.7]
2.7 Принимаем значение коэффициента динамической нагрузки передачи
2.8 Определяем коэффициент нагрузки передачи:
2.9 Определяем действительное контактное напряжение в зацеплении зубчатых колёс[1 стр. 134]
2.10 Проверяем отклонение действительного контактного напряжения в зацеплении зубчатых колес от расчетного допускаемого:
Допускается от 5% перегрузки до 10% недогрузки цилиндрической зубчатой передачи по контактным напряжениям. Условие выполнено.
Эскиз зубчатой передачи представлен на рисунке 2
Рисунок 2. Геометрические размеры прямозубой цилиндрической передачи и силы в зацеплении: силы Ft и Fr действующие на шестерню быстроходного вала.
Расчёт открытой клиноременной передачи.
Рис.3. Клиноременная передача.
1.1 Определяем коэффициент Ср учитывающий динамичность нагружения передачи и режим её работы [8 табл. 3.8]. Конвейер ленточный режим работы – односменный тогда
1.2 Определяем расчётный вращающий момент на ведущем валу Т1р :
1.3 Выбираем сечение клинового ремня по расчётному вращающему моменту Т1р [8 табл. 5.1] Выбираем ремни узкого сечения марки SPZ (УА)
1.4 Минимально допустимые диаметры ведущего шкива D1min для принятых сечений ремня определяем по табл. 5.1
1.5 Определяем коэффициент пропорциональности С=20;
1.6 Определяем рекомендуемый диаметр ведущего шкива
7 Принимаем стандартное значение диаметра ведущего шкива D1 ближайшее к рекомендуемому значению удовлетворяющее условию d1>d 1min находим по таблице 5.2
1.8 Коэффициент упругого скольжения ремня для клиновых кордшнуровых ремней узкого сечения
1.9 Определяем предварительное значение диаметра ведомого шкива передачи.
Округляем предварительное значение диаметра ведомого шкива до ближайшего стандартного значения по табл. 3.1
1.10 Определяем действительное значение передаточного числа ременной передачи:
1.11 Определяем отклонение действительного значения передаточного числа ременной передачи от заданного значения :
где - допускаемое отклонение передаточного числа передачи. Условие выполняется.
1.12 Определяем минимально допустимое межосевое расстояние передачи.
1.13 Определяем рекомендуемое межосевое расстояние передачи (мм).
557- условие выполняется.
1.14 Определяем предварительное значение длины ремня передачи ;
Предварительное значение длины ремня передачи округляем до ближайшего большего стандартного значения по ГОСТ 1284.1-89 (табл. 5.3);
1.15 Определяем действительное межосевое расстояние передачи a(мм.):
1.16 Определяем скорость ремня где –максимально допустимая скорость ремня.
Условие выполняется.
1.17 Определяем число (частоту) пробегов ремня в единицу времени где =15 - допускаемое число пробегов ремня:
15 - условие выполняется.
1.18 Определяем угол обхвата ремнём ведущего шкива передачи(рис. 3)
где =120 - допускаемый угол обхвата ремнём ведущего шкива передачи.
- условие выполняется.
Определяем полезное усилие передаваемое комплектом клиновых ремней передачи:
1.20 Выбираем по таблице 5.4 номинальную мощность (кВт) передаваемую одним клиновым ремнём принятого сечения эталонной длины в стандартных условиях эксплуатации.
1.21 Определяем коэффициент учитывающий влияние длины ремня на его долговечность[8 табл. 5.5]
1.22 Определяем коэффициент учитывающий влияние угла обхвата на тяговую способность передачи [8 табл. 5.6]
1.23 Определяем коэффициент учитывающий передаточное число u передачи[8 табл. 5.7)
24 Определяем мощность передаваемую одним клиновым ремнём в заданных условиях эксплуатации передачи: ;
1.25 Определяем коэффициент учитывающий неравномерность распределения нагрузки между ремнями передачи [8 табл. 5.8]
1.26 Определяем требуемое число ремней передачи :
где =55 кВт- мощность на валу ведущего шкива передачи;
1.27 Требуемое число ремней в передаче округляется до ближайшего большего целого числа Z=3.
1.28 Определяем натяжение ремней центробежными силами:(H)где - плотность материала ремня А- площадь сечения ремня V- скорость ремня.
1.29 Определяем силу предварительного натяжения одного ремня:
1.30 Определяем силы натяжения ведущей и ведомой ветвей ремня передачи:где – полезное усилие
1.31 Определяем силы давления на валы передачи:
2 Проверка прочности ремней и их долговечность.
2.1 Определяем растягивающее напряжение в ведущих ветвях ремней от рабочего натяжения:
2.2 Oопределяем напряжение при изгибе ремней на ведущем шкиве передачи:где = 100- модуль продольной упругости ремня при изгибе;
2.3 Определяем напряжение в ремнях от центробежных сил:
2.4 Определяем максимальное напряжение в ведущей ветви ремня: =10 МПа – допускаемое напряжение при изгибе ремня;
2.5 Определяем ресурс времени (срок службы ременной передачи):
где - временный предел выносливости ремня - коэффициент учитывающий влияние режима работы передачи на долговечность при переменной нагрузке
- допустимое условие выполняется.
3 Сечение ремня и шкивы передачи.
Рис.4 .Поперечное сечение клинового ремня.Ремень SPA- 1120 IV ГОСТ 1284.1-89. Количество ремней Z=3.
3.1 Из таблицы 5.9 выбираем углы клина канавок ведущего φ1 и ведомого φ2 шкивов:
3.2 Из таблицы 5.10 выбираем размеры канавок шкивов:b=33 мм.h=13 мм.f=10 мм.t=15 мм.
3.3 Определяем наружные диаметры ведущего и ведомого шкивов:мм.мм.
3.4 Определяем ширину ведущего и ведомого шкивов передачи: мм.B= мм.3.3.5 Выбираем материал и способ изготовления шкивов:при скорости ремней выбираем литые шкивы согласно ГОСТ 1412-85 из чугуна марки СЧ15.
3.6 Выбираем конструкцию и размеры ведущего и ведомого шкивов передачи:шкивы с наружным диаметром мм. изготавливаются с диском для снижения массы.
Рис 5. Шкив клиноременной передачи.
3.7 Размеры кинематические и силовые параметры передачи сводим с таблицу:
SPA- 1120 IV ГОСТ 1284.1-89
Диаметр ведущего шкива мм.
Диаметр ведомого шкива мм.
Угол обхвата ремнём ведущего шкива град.
Межосевое расстояние передачи а мм.
Число пробегов ремня v
Начальное натяжение ремня H
Сила давления ремней на валы H
Максимальное напряжение в ремне H
1 Предварительный расчет валов.
Рис. 6. Эскиз быстроходного вала редуктора.
Рис. 7. Эскиз тихиходного вала редуктора.
1.1 Определяем предварительный минимальный диаметр концевого участка быстроходного вала редуктора под шкив из условия прочности на кручение мм.:
где Тб- крутящий момент на быстроходном валу редуктора Нмм
=25Нмм2 –допускаемое напряжение на кручение; пониженное значение для компенсации неучтенных на данном этапе напряжений изгиба.
1.2 Полученное значение диаметра входного участка быстроходного вала округлим до ближайшего большего стандартного значения d1 из ряда нормальных линейных размеров: (табл. 1) [3 с.54] [4 с.272 табл. 12.1] [5 с.363 табл. 19.1]:
1.3 Определяем минимальное значение диаметра выходного участка тихоходного вала редуктора под полумуфту из условия прочности на кручение мм.:
где – допускаемое напряжение кручения;
- крутящий момент тихоходного вала;
Для входных и выходных концов валов = 20 25 Нмм2.
Расчётный момент (при подборе муфты):
где коэффициент режима в случае ленточного транспортера приводимого в движение электродвигателем К=15 2 [3 с. 377 табл. 15.2].
1.4 Полученное значение диаметра концевого участка тихоходного вала округлим до ближайшего большего стандартного значения из ряда нормальных линейных размеров под зубчатую муфту [11 стр.7 табл.10.1]. Принимаем зубчатую муфту МЗ №1 передающую крутящий момент 710 Нм с диаметром насадочного отверстия d1=40 мм.и длиной соответствующего участка l=55 мм.
2 Проектирование быстроходного вала редуктора.
2.1. Определяем рекомендуемое значение диаметра быстроходного вала под уплотнение мм
где t=3мм- высота буртика вала[1 табл. 11.1]
2.2 Полученное значение диаметра быстроходного вала под уплотнение округлим до ближайшего большего стандартного значения [5 с.9 табл.5]. Принимаем d2=30мм.
2.3 Определяем диапазон рекомендуемых значений быстроходного вала под подшипник качения.
d 3=d2+(2 5)=30+(2 5)=32 37 мм.
2.4 Принимаем стандартное значение диметра вала под подшипник d3=35 мм ближайший к диапазону полученных значений.
2.5 Выбираем предварительно подшипники лёгкой серии по таблице 11.2 ширину подшипника в зависимости от внутреннего диаметра d3=35мм.В=17 мм.
2.6 Найдем отношение диаметра окружности вершин зубьев шестерни da1 к диаметру вала под подшипник d3.
2.7 Так как отношение получилось менее двух то шестерня выполняется заодно с валом.
2.8 Определим диаметр упорного буртика вала для фиксации подшипника качения в осевом направлении.
=d3+2 =35+235=42 мм.
где = 35 мм.- высота буртика фиксирующего внутреннее кольцо подшипника(метод 43 табл. 11.3)
2.9 Определим длину входного участка быстроходного вала редуктора [7 c.108табл.7.1].
=15d1=1526=39 мм. принимаем 40 мм
2.10 Предварительно определяем длину участка под уплотнение:
3 Проектирование тихоходного вала редуктора.
3.1 Определим значение диаметра тихоходного вала под уплотнение:
d2=d1+2t=40+23 =46мм.
3.2 Полученное значение диаметра тихоходного вала под уплотнение округлим до ближайшего большего стандартного значения [5 с.9 табл.5]. Принимаем d2=45 мм.
3.3 Определим диапазон рекомендуемых значений быстроходного вала под подшипник качения:
=d2+(2 5)=45+(2 5)=47 50 мм.
3.4 Так как диаметр насадочного отверстия подшипника качения выражается целым числом мм оканчивающимся на 0 или 5 диаметр вала под подшипником
3.5 Выбираем предварительно подшипники лёгкой серии по таблице 11.2 ширину подшипника в зависимости от внутреннего диаметра: d3=50мм.В=20 мм.
3.6 Найдём отношение диаметра окружности вершин зубьев шестерни к диаметру вала под подшипник :
Т.к. значение получилось больше 2-ух то шестерня изготавливается отдельно от вала и будет надеваться на него.
3.7. Определим диаметр вала под зубчатое колесо принимаем из ряда нормальных линейных размеров [3 с. 272 табл. 12.1] [8 с. 7 табл. 1] ближайший размер
=d3+2 =50+230=56 мм;
где = 30 мм.- высота буртика фиксирующего внутреннее кольцо подшипника[1 табл. 11.3]
3.8 Определим диаметр упорного буртика вала фиксирующего подшипник качения в осевом направлении [8 с. 12 табл. 7]
где размер фаски подшипника качения. Округляем диаметр до ближайшего целого числа:
3.9 Определим длину ступицы зубчатого колеса:
Ближайшее значение из ряда нормальных линейных размеров:
3.10 Колесо фиксируется заплечиком высоту его выбираем по табл. 1:
3.11 Диаметр заплечика определяем по формуле:
3.12 Определяем расстояние от торцев подшипника до торцев ступицы колеса и торца заплечика фиксирующего колесо:
Подбор и расчёт шпоночных соединений.
Рис. 8. Эскиз шпоночного соединения.
1 Расчет шпонки быстроходного вала редуктора.
1.1 Выбираем размеры шпонки в зависимомти от диаметра быстроходного вала редуктора по табл.11.4[6 с.369 табл.19.11].
где h-высота шпонки;
1.2 Находим рабочую длину шпонки быстроходного вала редуктора:
где h-высота рабочей части шпонки
=100- допускаемое напряжение на смятие;
1.3 Найдём общую длину шпонки добавив два радиуса скругления торцов шпонки:
1.4 Принимаем значение длины шпонки из ряда стандартных длин: l=32 мм.
1.5 Проверяем условие прочности шпонки на смятие:
2 Расчёт шпонок тихоходного вала редуктора.
2.1 Расчет шпонки выходного участка тихоходного вала для d=40 мм.
2.2 Находим рабочую длину шпонки тихоходного вала редуктора:
2.3 Найдём общую длину шпонки с учётом радиусов скруглений:
2.4 Принимаем значение длины шпонки из ряда стандартных длин: l=50 мм.
2.5 Проверяем условие прочности шпонки на смятие:
3 Расчёт шпонки под колесо.
3.1 Расчет шпонки тихоходного вала под колесо для d=56 мм.
2.2 Находим рабочую длину шпонки тихоходного вала редуктора под колесо:
2.3 Найдём общую длину шпонки добавив два радиуса скругле-
2.4 Принимаем значение длины шпонки из ряда стандартных длин: l=60 мм.
Проверочный расчёт быстроходного вала.
1. На быстроходный вал редуктора действуют (со стороны зубчатого зацепления) окружная сила на колесе и радиальная сила на колесе . Радиальная сила приложена в полюсе зацепления и действует перпендикулярно к оси вала. Окружная сила приложена в полюсе зацепления и действует по касательной к делительной окружности в сторону вращения вала (направление вращения принимается самостоятельно). Полюс зацепления берется в середине образующей делительного цилиндра колеса. Кроме того со стороны зубчатой муфты действует на конце вала сила [1 с. 298] направляемая противоположно окружной силе ее величина:
2 выпишем длины участков быстроходного вала:
=39мм. – длина выходного участка;
=42мм. – длина вала под уплотнение;
=17мм. – ширина подшипника;
=150мм. – длина вала для фиксации подшипника;
=67мм.- ширина ступицы ведущей шестерни;
L – длина быстроходного вала L=207
3 Определяем реакции от сил опор в зацеплении в плоскости YOZ:
-реакции найдены правильно;
4 Определяем суммарные реакции опор:
- реакции найдены правильно;
5 Определяем суммарные реакции опор:
6 Определяем реакции от силы :
7 Определяем реакции опор для расчёта подшипников:
Построение эпюр моментов быстроходного вала.
1Определяем значения изгибающих моментов в характерных сечениях в горизонтальной плоскости XOZ:
2 Определяем значения изгибающих моментов в характерных сечениях в вертикальной плоскости YOZ:
3 Определяем значения изгибающих моментов от нагружения ременной передачи:
4 Определяем передачу вращающего момента которое происходит вдоль оси быстроходного вала со стороны входного участка до середины шестерни:
5 Опасное сечение вала либо сечение С либо сечение Б а именно сечение где действует наибольший суммарный изгибающий момент (крутящий момент в этих сечениях одинаков):
Опасное сечение – сечение С. Диаметр вала в этом сечении:
6 Сравним общий запас выносливости в сечении С и сравним с допускаемым [S] [1 с. 299] [3 с. 278] [7 с. 61]:
где [S] – требуемый коэффициент безопасности; если при расчете учтены только основные нагрузки действующие на вал [S]=18 [3 с. 282] [7 с. 61];
запасы выносливости при изгибе и кручении [1 с. 299] [3 с. 278] [7 с. 60 61]:
Здесь - пределы выносливости материала вала при изгибе и кручении (в условиях симметричного цикла нагружения [1 стр. 300] [3 стр. 291 табл. 12.13] [7 стр. 60 табл. 12.3]);
для вала изготовленного из стали 45; пределы выносливости -амплитуда и среднее напряжение циклов нормальных напряжений для принятого симметричного цикла изменения напряжений[1 с. 300] [3 с. 281] [7 с. 61]
(момент сопротивления сечения вала при изгибе для круга );
-амплитуда и среднее напряжение циклов касательных напряжений для принятого пульсирующего цикла изменения напряжений [1 с. 300] [3 с. 281] [7 с. 61]
(полярный момент сопротивления сечения вала для круга );
коэффициенты характеризующие чувствительность материала вала к асимметрии цикла нагружения для стали 45 [7 стр. 60 табл. 12.3];
- коэффициент учитывающий поверхностное упрочнение вала без поверхностного упрочнения =1[3 стр. 280 табл. 12.9];
- коэффициенты учитывающие влияние посадки детали (например подшипника качения) на вал при изгибе и кручении (учитывают влияние концентрации напряжений и размеров деталей) подшипники на вал устанавливаются по переходной посадке К7 исходя из этого принимаем и [3 с. 280 табл. 12.8].
Запас сопротивления усталости обеспечен.
1 Для опор валов цилиндрических колёс редуктора принимают первоначально шариковые радиальные подшипники лёгкой серии: для быстроходного вала – 207 (ГОСТ 8338-75) для тихоходного вала – 210 (ГОСТ 8338-75)
Рис. 10. Эскиз однорядного шарикового радиального подшипника.
Принимаем рекомендуемую схему установки подшипников для одноступенчатых цилиндрических конических и червячных редукторов «враспор». Осевая фиксация осуществляется в двух опорах причём в каждой опоре в одном направлении.
2 Определяем долговечность подшипников для быстроходного вала:
где С – динамическая грузоподъёмность С = 255 кН для подшипника 207;
р – показатель степени для шарикоподшипников – р = 3;
Р – эквивалентная нагрузка.
V = 1- коэффициет вращения при вращении внутреннего кольца подшипника;
Fr =925 Н – радиальная нагрузка;
коэффициенты радиальной и осевой нагрузок: X=1 Y- не выбираем т.к.
[6 табл. 6.1 стр. 101]
коэффициент безопасности учитывающий характер нагрузки (для редукторов всех типов КБ =13 15) принимаем КБ =15.
–температурный коэффициент [6 табл. 6.4 стр. 105]
3 Определяем срок службы подшипников:
что больше заданного по ГОСТ 16162-85
4 Для данного типа редуктора наиболее простой в конструктивном исполнении является установка подшипников по схеме «враспор». При такой схеме установки вал фиксируется в двух опорах причем в каждой опоре в одном направлении. Чтобы не происходило защемления вала в опорах из-за его нагрева предусматривают осевой зазор «а». Величина этого зазора колеблется в пределах 02 05 мм. Регулирование осевого зазора осуществляется путем изменения числа прокладок.
5 Выбор посадок подшипников качения для валов редуктора
В проектируемом редукторе внутренние кольца подшипников имеют циркуляционное нагружение наружные – местное.
По таблице 6.5 [6] при циркуляционном нагружении внутреннего кольца подшипника выбираем поля допусков вала: k6 – для быстроходного и тихоходного валов.
По таблице 6.6 [6] поля допусков отверстий корпуса редуктора N7.
Зубчатые муфты применяются для соединения валов нагруженных большим крутящими моментами при различной комбинации радиальных угловых и осевых смещений. Зубчатые муфты выбираются из таблиц по ГОСТ 5006-55.
Ранее выбранную муфту МЗ1 производим проверку по напряжениям смятия рабочих поверхностей зубьев:
[9 стр. 202 табл.6.6]
Для стандартных зубчатых муфт допускаемые напряжения ;
где K=14 – коэффициент режима работы; [6 с.267]
Tн=Тт=3184 Нм – номинальный длительно действующий момент.
m-модуль зацепления m=2;
z-число зубьев z=20;b-длина зуба b=30 мм.
условие выполняется.
Выбираем из таблицы основные размеры муфты МЗ1 в мм.[4 табл. 6.6 стр. 202]
Разработка конструкции крышек подшипников.
На рисунке 11 изображена глухая торцовая крышка редуктора. Расчёт произведём для глухой торцовой крышки тихоходного вала редуктора.
В зависимости от диаметра наружного кольца подшипника D= 90 мм. выбираем:
– толщина стенки =8 мм.
d – диаметр крепёжных винтов d=М8;
Z – число крепёжных винтов Z=6;
DK – диаметр фланца крышки DK= D+35 мм.=90+35=125 мм.
– ширина канавки 2=(09 1) =6 мм.
=12=128=96 мм. толщина фланца при креплении крышки болтами.
сd=8мм.-расстояние от центрирующего пояска до оси крепления винта.
L=20 мм. – принимается конструктивно.
Рис. 11. Эскиз глухой торцовой крышки редуктора.
Выбор смазочных материалов и системы смазки редуктора
Для уменьшения потерь мощности на трение в зацеплении и снижения интенсивности износа трущихся поверхностей для предотвращения их от заедания охлаждения зубчатых колес удаления продуктов износа предохранения от коррозии и лучшего отвода теплоты трущиеся поверхности деталей должны иметь надежную смазку.
Наиболее простым и надежным способом является картерная смазка применяемая при окружной скорости колес до 15 мс. В корпус редуктора заливают масло через верхний люк так чтобы венцы колес были в него погружены. При их вращении масло увлекается зубьями разбрызгивается попадает на внутренние стенки корпуса откуда стекает в нижнюю его часть. Внутри корпуса образуется взвесь частиц масла в воздухе которая покрывает поверхность расположенных внутри корпуса деталей.
При работе передачи масло постепенно загрязняется продуктами износа с течением времени оно стареет свойства его ухудшаются. Поэтому масло налитое в корпус редуктора периодически меняют. Для слива масла в корпусе редуктора предусмотрено сливное отверстие закрываемое пробкой.
Чем выше окружная скорость колеса тем меньше должна быть вязкость масла чем выше контактное давление в зубьях тем большей вязкостью должно обладать масло. Поэтому требуемую вязкость масла определяем в зависимости от контактного напряжения и окружной скорости колес. В данном случае имеем контактное напряжение до 600 МПа и окружную скорость () свыше 2 мс по которым выбираем– индустриальное масло И-Г-А-46. [6 стр. 135 табл. 8]
Колесо должно быть погружено в масло на величину
Описание сборки и регулировки редуктора
Перед сборкой внутреннюю полость корпуса редуктора тщательно очищают и покрывают маслостойкой краской.
Сборку производят в соответствии с чертежом общего вида редуктора начиная с узлов валов:
на ведущий вал насаживают шариковые радиальные подшипники предварительно нагретые в масле до 80-100° С;
в ведомый вал закладывают шпонку и напрессовывают зубчатое колесо до упора в бурт вала; затем надевают распорную втулку и устанавливают шариковые радиально-упорные подшипники предварительно нагретые в масле.
Собранные валы укладывают в основание корпуса редуктора и надевают крышку корпуса покрывая предварительно поверхности стыка крышки и корпуса герметиком. Для центровки устанавливают крышку на корпус с помощью двух штифтов; затягивают болты крепящие крышку к корпусу.
После этого вставляют распорные втулки и крышки подшипников с комплектом металлических прокладок; регулируют положение зубчатого зацепления. Перед постановкой сквозных крышек закладывают в них резиновые манжеты. Проверяют проворачивание валов отсутствие заклинивания подшипников (валы должны проворачиваться от руки) и закрепляют крышки винтами.
Ввертывают пробку маслоспускного отверстия с медной прокладкой и устанавливают круглый маслоуказатель. Заливают в редуктор масло и закрывают смотровое отверстие крышкой-отдушиной с прокладкой; закрепляют крышку болтами.
Собранный редуктор обкатывают и подвергают испытанию на стенде по программе устанавливаемой техническими условиями.
Детали машин: методические указания к курсовому проектированию для студентов технологических специальностей дневной и заочной форм обучения с расчетами зубчатых передач. Часть 2. Федосеев Г.Н. Бабаев В.С. Карпушко А.В. Витебск УО «ВГТУ»2003 г.
Иванов М.Н. Детали машин: Учебник для студентов втузов. М.: Высш. шк. 1991 г.
Детали машин в примерах и задачах : Учеб. пособие С.Н. Ничипорчик М.И. Корженцевский В.Ф. Калачев и др.; Под общ.ред. С.Н. Ничипорчика. – Мн.:Выш.шк. 1981 г.
Курсовое проектирование деталей машин. Справочное пособие. Ч.1 А.В. Кузьмин Н.Н. Макейчик В.Ф. Калачев и др. – Мн.: Выш.шк. 1982 г.
Детали машин: методические указания к курсовому проектированию с эскизной компоновкой редуктора для студентов технологических специальностей. Часть 4. Федосеев Г.Н. Бабаев В.С. Карпушко А.В. Витебск УО «ВГТУ»2005 г.
Дунаев П.Ф. Леликов О.П. Детали машин. Курсовое проектирование: Учеб. пособие для машиностроит. спец. техникумов. – М.: Высш.шк. 1990 г.
Шейнблинт Л.В. Курсовое проектирования деталей машин: Учеб. пособие для техникумов. – М.:Высш.шк. 1991.
Методические указания к расчету передач гибкой связью по курсу «Детали машин» для студентов механических и технологических специальностей. Бабаев В.С. Шкляр Е.Н. Орлов В.Н. Мурков О.С. Витебск УО «ВГТУ» 1988 г.
Курсовое проектирование деталей машин. Справочное пособие. Ч.2 А.В. Кузьмин Н.Н. Макейчик В.Ф. Калачев и др. – Мн.: Выш.шк. 1982 г.
Расчет и проектирование деталей машин: Учебное пособие для втузов Под ред. Г.Б. Столбина и др. – М.:Высш. школа 1978.
Прикладная механика техническая механика основы конструирования и проектирования. Методические указания к расчётно-графическим работам для студентов дневной и заочной формы обучения. Федосеев Г.Н. Бабаев В.С. Карпушко А.В. Витебск УО «ВГТУ»2005 г.
МИНИСТЕРСТВО ОБРАЗОВАНИЯ РЕСПУБЛИКИ БЕЛАРУСЬ
УО «ВИТЕБСКИЙ ГОСУДАРСТВЕННЫЙ ТЕХНОЛОГИЧЕСКИЙ УНИВЕРСИТЕТ»
Расчётно-пояснительная записка
к курсовому проекту по деталям машин
Тема: «Спроектировать привод ленточного конвейера»
Курсовой проект по деталям машин
Редуктор вид сбоку.cdw

Передаваемая мощность
Частота вращения быстроходного вала
Частота вращения тихоходного вала
Передаточное число редуктора 3
Крутящий момент на тихоходном валу
Поверхность Б красить белой эмалью.
Ведущий вал собранного редуктора должен проворачиваться без
Перед обкаткой залить масло индустриальное И-Г-А-46 ГОСТ
799-75. Уровень масла контролировать маслоуказателем поз. 22.
Редуктор обкатать на стенде согласно ТУ.
Шум передачи должен быть равномерным без металлических стуков.
Уровень звуковой мощности не выше 98 дБа по ОСТ 7189-5-79.
Течь масла в местах неподвижных соединений не допускается.
Требования к манжетным уплотнениям валов по ГОСТ 8752-79. Перед
окончательной сборкой редуктора фланцы корпуса и крышки покрыть
герметиком ВГК-18 №2 МРТУ 07-6012-63.
Общий вид редуктора.cdw

Непараллельность осей шкивов
мм. на длине 100 мм.
Смещение рабочих поверхностей шкивов
Привод обкатать без нагрузки в течении 1 часа. Стук и резкий
После обкатки масло из редуктора слить и залить новое до
уровня заполнения смотрового глазка.
Масло индустриальное И-Г-А-46 по ГОСТ 20799-73.
Ограждение ременной передачи и зубчатой муфты условно не
показаны. Огражденя должны быть окрашены белой эмалью.
Техническая характеристика
Мощность на приводном валу Р
Частота вращения приводного вала n
Диаметр приводного барабана D=320 мм.
Ширина приводного барабана В=432 мм.
Срок службы привода 7
Редуктор вид с верху.cdw

Вал.cdw

Сталь 45 ГОСТ 1050-88
улучшение HB 192 240.
Общие допуски по ГОСТ 30893.1-2002:
Острые кромки скруглить
Колесо.cdw

Сталь 45 ГОСТ 1050-88
нормализация HB 179 207.
Общие допуски по ГОСТ 30893.1-2002:
Острые кромки скруглить
Спецификация.spw

Вал-шестерня быстроходный
Прокладка регулировочная
Шпонка ГОСТ 23360-78
Манжета ГОСТ 8752-79
Подшипник ГОСТ 8338-75
Крышка.cdw

Формовочные уклоны по ГОСТ 3212-57.
Общие допуски по ГОСТ 30893.1-2002:
Общий вид редуктора черновик.cdw
Непараллельность осей шкивов
мм. на длине 100 мм.
Смещение рабочих поверхностей шкивов
Привод обкатать без нагрузки в течении 1 часа. Стук и резкий
После обкатки масло из редуктора слить и залить новое до
уровня заполнения смотрового глазка.
Масло индустриальное И-Г-А-46 по ГОСТ 20799-73.
Ограждение ременной передачи и зубчатой муфты условно не
показаны. Огражденя должны быть окрашены белой эмалью.
Техническая характеристика
Мощность на приводном валу Р
Частота вращения приводного вала n
Диаметр приводного барабана D=320 мм.
Ширина приводного барабана В=432 мм.
Срок службы привода 7
Эпюры б.х. вала к ДМ.doc
Рис. 7. Эпюры быстроходного вала редуктора.
Рекомендуемые чертежи
- 24.01.2023
- 19.01.2021