Проектирование одноступенчатого редуктора




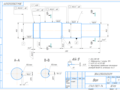
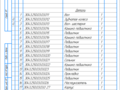
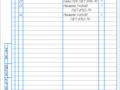
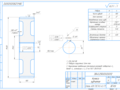
- Добавлен: 24.01.2023
- Размер: 345 KB
- Закачек: 0
Описание
Проектирование одноступенчатого редуктора
Состав проекта
![]() |
![]() |
![]() ![]() ![]() |
![]() |
![]() ![]() ![]() ![]() |
![]() ![]() ![]() ![]() |
![]() ![]() ![]() ![]() |
![]() ![]() ![]() ![]() |
![]() ![]() ![]() ![]() |
![]() ![]() ![]() ![]() |
Дополнительная информация
ОГЛАВЛЕНИЕ.doc
ФГОУ ВПО «Башкирский государственный аграрный университет»
Факультет: энергетический
Кафедра: теоретической и прикладной механики
Специальность: энергообеспечение предприятий
Форма обучения: очная
(Фамилия имя отчество студента)
Проектирование одноступенчатого редуктора
Руководитель: Ахмаров Р.Г.
(ученая степень звание Ф.И.О.)
ВЫБОР ЭЛЕКТРОДВИГАТЕЛЯ И КИНЕМАТИЧЕСКИЙ РАСЧЕТ ПРИВОДА . 5
РАСЧЕТ РЕМЕННОЙ ПЕРЕДАЧИ . . 7
РАСЧЕТ ПРЯМОЗУБОЙ ПЕРЕДАЧИ .. . . 9
ЭСКИЗНАЯ КОМПОНОВКА РЕДУКТОРА . .. ..15
РАСЧЕТ ВАЛОВ . .. 17
РАСЧЕТ ПОДШИПНИКОВ КАЧЕНИЯ .. 21
РАСЧЕТ СОЕДИНЕНИЙ .. 24
ПОРЯДОК СБОРКИ И РАЗБОРКИ РЕДУКТОРА .. ..27
Курсовая работа по прикладной механике посвящена расчету и разработке конструкции привода от электродвигателя к ленточному транспортеру.
Графическая часть включает сборочный чертеж редуктора 1 лист формата А1 рабочий чертеж выходного вала редукторарабочий чертеж колеса выходного вала редуктора А3.
В ходе выполнения курсовой работы использовались материалы многих технических дисциплин: инженерная графика теоретическая механика сопротивление материалов допуски-посадки и технические измерения детали машин материалы многих справочников и стандартов. Выполнение курсовой работы являлось важным этапом в получении практических навыков самостоятельного решения сложных инженерно – технических задач.
ВЫБОР ЭЛЕКТРОДВИГАТЕЛЯ И КИНЕМАТИЧЕСКИЙ
1Потребляемая мощность электродвигателя
- КПД ременной передачи;
- КПД зубчатой передачи;
Частота вращения электродвигателя:
где - передаточное число ременной передачи;
- передаточное число зубчатой передачи.
Выбираем электродвигатель:
серия 4А160М8730 стр.3211
асинхронная частота вращения обмин.
2 Определяем общее передаточное отношения привода:
Разбиваем передаточное число привода по ступеням:
3 Угловые скорости и частоты вращения валов.
4 Крутящие моменты на валах.
РАСЧЁТ РЕМЕННОЙ ПЕРЕДАЧИ
По передаваемой мощности и частоте вращения малого шкива по рис. принимаем сечение ремня
Ориентировочный размер малого шкива:
Принимаем dpI=180 мм (стр 2722)
Принимаем dpII=560 мм
Фактическое передаточное отношение
Межосевое расстояние
Определяем длину ремня
По ряду длин принимаем ближайшее значение:lp=2240 мм по табл. 12.2
Тогда межосевое расстояние:
Угол обхвата ремней малого шкива
Определяем мощность передаваемую одним ремнём:
где P0 – мощность передаваемая одним ремнём при типовых условиях эксплуатации.
Сα – коэффициент угла обхвата; (Сα=088)
Ср – коэффициент режима нагрузки; (Ср=1 12)
где Р – мощность на ведущем валу передачи
Сz – коэффициент числа ремней равный: 09
Находим предварительное натяжение одного ремня:
где U – окружная скорость;
FU – натяжение за счёт центробежных сил
где ρ – мощность материала ремня ρ=1250 кгм3
Равнодействующая нагрузка на вал:
РАСЧЕТ ПРЯМОЗУБОЙ ЦИЛИНДРИЧЕСКОЙ ПЕРЕДАЧИ
1 Выбор материалов и термической обработки зубчатого колеса и шестерни
Целесообразнее применять материалы с твердостью менее 350 НВ причем для обеспечения равной долговечности и лучшей приработки зубов твердость материала шестерни должна быть больше твердости материала колеса на (10 70) НВ. Материал – Сталь 40Х.
По таблице 8.8 1 назначаем:
Для шестерни – улучшение
Твердость поверхности – 260 280 НВ
Предел прочности =950 МПа
Предел текучести =700 МПа
Для колеса – улучшение
Твердость поверхности – 230 260 НВ
Предел прочности =850 МПа
Предел текучести =550 МПа
2 Вычисление допускаемых контактных напряжений зубьев
Определяем допускаемые контактные напряжения для зубьев шестерни и колеса в прямозубой цилиндрической передаче:
где -предел выносливости контактной поверхности зубьев соответствующий базовому числу циклов переменных напряжений МПа;
- коэффициент безопасности для зубчатых колес с однородной структурой материала равен 11;
По рекомендации определяем нормальные допускаемые напряжения:
Н01 = 2*НВ1 +70 = 2*270 + 70 = 610 МПа;
Н02 = 2*НВ2 +70 = 2*245 + 70 = 560 МПа.
Найдем допускаемые контактные напряжения для зубьев шестерни и колеса:
= 555 МПа - для шестерни;
= 509 МПа - для колеса.
За расчетное принимаем 509 МПа
3 Вычисление допускаемых напряжений изгиба зубьев
Допускаемые напряжения изгиба зубьев:
где F0 – базовый предел выносливости зубьев МПа;
SF – коэффициент безопасности;
КFC – коэффициент учитывающий влияние двустороннего приложения нагрузки;
КFL – коэффициент долговечности.
Рекомендуют коэффициент безопасности SF = 175 по табл. 8.9 1. При односторонней нагрузке КFC = 1 а коэффициент долговечности КFL определяется по формуле:
F01 = 18*НВ1 = 18*270 = 486 МПа;
F02 = 18*НВ2 = 18*245 = 441 МПа.
Вычислим допускаемые напряжения изгиба зубьев:
= = 278 МПа - для шестерни;
= 204 МПа - для колеса.
Занесем вычисленные значения в таблицу 1:
Механические свойства материалов зубчатых колес.
Допускаемые контактные
напряжения изгиба зубьев
4 Вычисление межосевого расстояния колес
Предварительный расчет межосевого расстояния выполняем по формуле 8.14 1:
где – передаточное число;
Т2 – крутящий момент на валу колеса Н*м;
- приведенный модуль упругости;
- коэффициент концентрации нагрузки;
- расчетное допускаемое контактное напряжение МПа;
- коэффициент ширины колеса относительно межосевого расстояния.
Коэффициент ширины колеса относительно межосевого расстояния по табл. 8.4 1 равняется: =03 05; принимаем= 04.
По графику 815 1 =105
Для прямозубых цилиндрических зубчатых колес за расчетное значение допускаемого контактного напряжения поверхности зубьев принимается меньшее из двух значений вычисленных для шестерни и колеса
Определяем межосевое расстояние колес:
аw = 085*(4+1)*= 2465 мм.
Принимаем стандартное межосевое расстояние по СТ СЭВ 229-75: аw=250мм.
5 Вычисление геометрических параметров зубчатых колес
Геометрические параметры зубчатых колес: ширина венца bw модуль зацепления m числа зубьев z1 и z2 диаметры – делительный d вершин da впадин df.
5.1 Ширина венца колеса
шестерня: bw1 = * аw = 04*250 = 100 мм;
Принимаем bw1 =100 мм
колесо: bw2 = bw1 – 5 мм = 100 – 5 = 95 мм.
5.2.Диаметр шестерни:
5.2 Максимальный модуль передачи:
Принимаем модуль m=5 мм.
Фактическое число зубьев шестерни:
Фактическое число зубьев колеса:
5.3 Делительные диаметры
шестерня: d1 = m*z1 = 5*20=100 мм;
колесо: d2 = m*z2 = 5*80 = 400 мм.
5.4 Диаметры вершин зубьев
шестерня: dа1=d1+2m=100 + 2*5=110мм;
колесо: dа2=d2+2m=400 + 2*5=410мм.
шестерня: df1=d1–25m=100 – 25*5 = 875мм;
колесо: df2=d2–25m=400 – 25*5=3875мм.
Уточняем величину межосевого расстояния:
Занесем полученные данные в таблицу 2:
Таблица 2. Геометрические параметры прямозубого цилиндрического зацепления.
Параметры зацепления
Межосевое расстояние а мм
Геометрические параметры
Делительный диаметр d1 мм
Делительный диаметр d2 мм
Диаметр вершин зубьев da1 мм
Диаметр вершин зубьев da2 мм
Диаметр впадин зубьев df1 мм
Диаметр впадин зубьев df2 мм
6Проверка зубьев передачи на контактную прочность
Определяем расчетные контактные напряжения по формуле:
где Епр - приведенный модуль упругости равный Епр = 21*105 МПа;
Т1 – крутящий момент на валу шестерни кН*м;
КН – коэффициент расчетной нагрузки;
- допускаемое контактное напряжение МПа;
α = 20º - эвольвентный угол зацепления.
Определяем коэффициент расчетной нагрузки:
Ранее было принято: КН=105.
Для того чтобы найти коэффициент динамической нагрузки по контактным напряжениям Кнv необходимо определить окружную скорость ведущего вала:
По табл.8.21 назначаем 9ую степень точности.
Далее по таблице 8.31 находим: КНv=106.
КН= КН *КНv = 105*106 = 111.
Определяем расчетные контактные напряжения:
= 493 МПа = 509 МПа.
Прочность по контактным напряжениям соблюдается.
7 Проверочный расчет по напряжениям изгиба
Проверяем по формуле:
где YF – коэффициент формы зуба;
Ft – окружная сила передачи кН;
KF – коэффициент расчетной нагрузки;
b – ширина венца колеса мм;
m – модуль зацепления.
Дальнейший расчет ведем по тому из пар колес у которого наименьшее отношение [ ]YF :
Значение YF найдем по рис. 8.20 1:
[ ]YF1 = 27771415=66919
[ ]YF2 =2036375=54281
Расчет ведем по колесу.
Окружную силу передачи вычисляем по формуле:
Вычисляем коэффициент расчетной нагрузки KF:
где КF – коэффициент динамической нагрузки по напряжениям изгиба;
КFv - коэффициент концентрации нагрузки по напряжениям изгиба.
Аналогично КН вычисляем эти коэффициенты назначаем 9ую степень точности.
Далее по таблице 8.31 находим: КFv=115.
Определяем КF по рис. 8.15 1: КF = 124.
КF= КF*КFv = 124*115 = 143.
Вычисляем напряжение изгиба:
F = 109 МПа = 204 МПа.
Прочность по напряжениям изгиба соблюдена.
ЭСКИЗНАЯ КОМПОНОВКА РЕДУКТОРА
1 Определение диаметров участков вала:
а) для быстроходного вала:
Принимаем . (табл. 19.11)
Под подшипник (конический хвостовик). (формула 3.21)
Диаметр буртика подшипника:
r = 25мм. (табл. 3.11)
б) для тихоходного вала:
2 Расстояние между деталями передач.
Зазор между вращающимися деталями и внутренней стенкой корпуса.
L = 2a = 2250 = 500 мм.
Принимаем а = 11 мм.
Расстояние между колесом и днищем редуктором.
3 Выбор подшипников.
Для косозубой цилиндрической передачи назначаем радиальный шариковый однорядный подшипник.
Назначаем по ГОСТ 8338-75 (таблица 19.181)
– для быстроходного вала № 212 B=22 мм;
– для тихоходного вала № 214 B=24 мм.
Схема установки – враспор.
4 Длины участков валов.
а) для тихоходного вала:
–длина посадочного конца вала: .
–длина промежуточного участка: .
–длина цилиндрического участка: .
Наружная резьба конического конца вала (формула 3.91)
По таблице 19.61 выбираем [М48х15].
Длина резьбы: (стр.411).
б) для быстроходного вала:
По таблице 19.61 выбираем [М42х15].
Эпюра Тихоходного вала
Mx2= FМ (x2+1375)+ ZA x2
Mx3= FМ (x3+1375+48)+ ZA ( x3+48)-Fr x3
x3=70мм Mx3=4787(1375+70+70)10-3-5632(70+70)10-3-280870=0.
Определение суммарных изгибающих моментов:
Определяем запас сопротивлению усталости по формуле 15.32
где (формула 15.42)
- запас сопротивлению усталости только изгибу
- запас сопротивлению усталости только кручению
(рекомендация 15.62)
Проверка статической прочности:
- условие выполняется.
РАСЧЕТ ПОДШИПНИКОВ КАЧЕНИЯ
1Расчет подшипника тихоходного вала.
Расчет подшипников ведем по наиболее нагруженной опоре А.
По каталогу (табл. 19.181) выписываем:
динамическая грузоподъемность: Cr = 436 кН
статическая грузоподъемность: Со =25 кН
При коэффициенте вращения V = 1 (вращение внутреннего кольца подшипника)
Коэффициент радиальной силы Х = 1
Коэффициент осевой силы Y = 0
Находим эквивалентную динамическую нагрузку
Рr = (Х.V.Fr + Y.Fa). К. Кб (формула 16.292)
По рекомендации к формуле 16.29 2:
К = 1 – температурный коэффициент;
Кб = 1 – коэффициент безопасности;
Рr = (1.1.81044 + 0).1.1 = 81044Н
Находим динамическая грузоподъемность (формула 16.272):
где L – ресурс млн.об.
a1 – коэффициент надежности
a2–коэффициент совместного влияния качества металла и условий эксплуатации
p=3 (для шариковых)
Lh= 12000 ч (табл. 16.42)
а1 = 1 ( рекомендация стр.3332)
а2=075 (табл. 16.3 2);
Проверяем подшипник на статическую грузоподъемность:
Эквивалентная статическая нагрузка
Ро=Хо. Fr0 + Yo. Fa0 (формула16.33 [2])
к=3 – коэффициент динамичности
Коэффициент радиальной статической силы Хо = 06
Коэффициент осевой статической силы Yо = 05
Ро = 06.3.81044 + 0= 14588 Н 17800 Н
Условия выполняются.
2Расчет подшипника быстроходного вала.
динамическая грузоподъемность: Cr = 255 кН
статическая грузоподъемность: Со =137 кН
Рr = (1.1.3434 + 0.596).1.1 = 3434Н
LhE=Lh.kHE (формула 16.312)
kHE=05 (табл. 8.102)
где Fr0 =к FrFа0=к Fа
Ро = 06.3.3434 + 05.3.596 = 70752 Н 13700 Н
1 Расчет шпоночных соединений.
Найдем диаметр в среднем сечении конического участка длиной l=75 мм на тихоходном валу.
Шпонка призматическая (таблица 19.111):
Длину шпонки принимаем 45 мм рабочая длина lр=l-b=31 мм.
Найдем диаметр в среднем сечении конического участка длиной l=60мм на быстроходном валу.
Длину шпонки принимаем 40 мм рабочая длина lр=l-b=30 мм.
Для данного редуктора выберем упруго-втулочную пальцевую муфту. Ее размеры определяем по таблице 15.21
Нагрузка между пальцами:
В настоящее время в машиностроении широко применяют картерную систему смазки при окружной скорости колес от 03 до 125мс. В корпус редуктора заливают масло так чтобы венцы колес были в него погружены. При их вращении внутри корпуса образуется взвесь частиц масла в воздухе которые покрывают поверхность расположенных внутри деталей.
1 Выбор сорта смазки
Выбор смазочного материала основан на опыте эксплуатации машин. Принцип назначения сорта масла следующий: чем выше контактные давления в зубьях тем большей вязкостью должно обладать масло чем выше окружная скорость колеса тем меньше должна быть вязкость масла.
Поэтому требуемую вязкость масла определяют в зависимости от контактного напряжения и окружности скорости колес.
Окружная скорость колес ведомого вала: V2=05мсек. Контактное напряжение [н]= 509 МПа.
Теперь по окружной скорости и контактному напряжению из таблицы 8.11 выбираем масло И-Г-С-100.
2 Предельно допустимые уровни погружения колес цилиндрического редуктора в масляную ванну:
≤ hM ≤ 025.225 = 56 мм
Наименьшую глубину принято считать равной 2 модулям зацепления.
Наибольшая допустимая глубина погружения зависит от окружной скорости колеса. Чем медленнее вращается колесо тем на большую глубину оно может быть погружено.
Уровень масла от дна корпуса редуктора:
h = в0 + hм =27 + 40 = 67 мм
в0 = 27 мм – расстояние от наружного диаметра колеса до дна корпуса
3 Способ контроля уровня смазки зубчатых колес
Для контроля уровня масла в корпусе необходимо установить круглый маслоуказатель.
Также в нижней части корпуса редуктора предусмотрено отверстие с пробкой для слива отработанного масла а на крышке редуктора – отдушина для снятия давления в корпусе появляющегося от нагрева масла и воздуха при длительной работе.
Подшипники смазывают тем же маслом что и детали передач. Другое масло применяют лишь в ответственных изделиях.
При картерной смазке колес подшипники качения смазываются брызгами масла.
ПОРЯДОК СБОРКИ И РАЗБОРКИ РЕДУКТОРА
Перед сборкой внутреннюю полость корпуса редуктора тщательно очищают и покрывают маслостойкой краской.
Сборку производят в соответствии с чертежом общего вида редуктора начиная с узлов валов:
на ведущий вал насаживают шарикоподшипники предварительно нагретые в масле до 80 100ºС;
в ведомый вал закладывают шпонку и напрессовывают зубчатое колесо до упора в бурт вала; затем надевают распорную втулку и устанавливают шарикоподшипники предварительно нагретые в масле.
Собранные валы укладывают в основание корпуса редуктора и надевают крышку корпуса покрывая предварительно поверхности стыка крышки и корпуса спиртовым. лаком. Для центровки устанавливают крышку на корпус с помощью двух конических штифтов затягивают болты крепящие крышку к корпусу.
После этого на ведомый вал надевают распорное кольцо в подшипниковые камеры закладывают пластичную смазку ставят крышки подшипников с комплектом металлических прокладок для регулировки.
Перед постановкой сквозных крышек в проточки закладывают войлочные уплотнения пропитанные горячим маслом. Проверяют проворачиванием валов отсутствие заклинивания подшипников (валы должны проворачиваться от руки) и закрепляют крышки винтами.
Далее на конец ведомого вала в шпоночную канавку закладывают шпонку устанавливают звездочку и закрепляют ее торцовым креплением; винт торцового крепления стопорят специальной планкой.
Затем ввертывают пробку маслоспускного отверстия с прокладкой и маслоуказатель.
Заливают в корпус масло и закрывают смотровое отверстие крышкой с прокладкой из привулканизированной резины отдушиной и фильтром; закрепляют крышку болтами.
Собранный редуктор обкатывают и подвергают испытанию на стенде по программе устанавливаемой техническими условиями.
Разборка редуктора проводиться в обратном порядке.
П.Ф.Дунаев О.П.Леликов. Детали машин. Курсовое проектирование:Учеб. пособие для машиностроит. спец. техникумов.– М.: Высшая школа 1990 г. – 399с.
М.Н. Иванов Детали машин:Учеб. для студентов высш. техн. учеб. заведений. – М.: Высшая школа 1991 г. – 383с.
С.А. Чернавский К.Н. Боков. Курсовое проектирование деталей машин:Учеб. пособие. – М.: Альянс 2005г. – 416с.
РЕДУКТОР2.cdw

Специф2.cdw

ВАЛ.cdw

Неуказанные предельные отклонения
КОЛЕСО.cdw

Коэффициент смещения
Сталь 40Х ГОСТ45-43-71
Радиусы скруглений 1
Неуказанные предельные отклонения размеров: отверстий +t
Спецификация 11.cdw

Редуктор цилиндрический
Расчетно- пояснительная
РЕДУКТОР1.cdw

Рекомендуемые чертежи
- 06.04.2022