Проектирование цилиндрического одноступенчатого редуктора




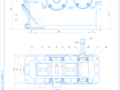
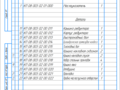
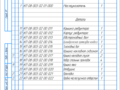
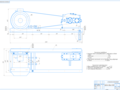
- Добавлен: 04.11.2022
- Размер: 1 MB
- Закачек: 0
Описание
Курсовая работа - Проектирование цилиндрического одноступенчатого редуктора
Состав проекта
![]() |
![]() ![]() ![]() ![]() |
![]() ![]() ![]() ![]() |
![]() |
![]() |
![]() ![]() ![]() |
![]() ![]() ![]() ![]() |
![]() ![]() ![]() |
![]() ![]() ![]() ![]() |
![]() |
![]() ![]() ![]() ![]() |
Дополнительная информация
Чертеж общего вида _ КП.08.003.01.00.000.ВО.cdw

Смещение валов электродвигателя и редуктора не более:
Допускаемая консольная сила на выходном валу редуктора
Техническая характеристика
Общее передаточное число привода u=7
Мощность электродвигателя Рдв=4 кВт
Число оборотов двигателя n
КП.08.003.01.00.000.
Спецификация2.bak.spw

Цилиндрическое прямозубое колдесо
Крышка накладная сквозная
Крышка накладная глухая
Набор стальных прокладок
Пробка маслоспускного отверстия
титульный.docx
образовательное учреждение
«СИБИРСКИЙ ФЕДЕРАЛЬНЫЙ УНИВЕРСИТЕТ»
Проектирование цилиндрического одноступенчатого редуктора
Пояснительная записка
Тихоходный вал _ КП 08.003.00.00.000.cdw

пояснительная записка.docx
Выбор материала и определение допускаемых напряжений для зубчатых колес
Проектный и проверочный расчет закрытой цилиндрической прямозубой передачи .
Расчет плоскоременной передачи от двигателя к редуктору
Схема сил в зацеплении
Предварительный расчет валов
Предварительное конструирование валов
Конструирование зубчатых колес редуктора
Эскизная компоновка привода
Проверочный расчет третьего вала на статистическую прочность .
Проверочный расчет четвертого вала по переменным напряжениям .
Подбор подшипников качения по долговечности .
Расчет шпоночных соединений
Расчет корпусных деталей
Список использованных источников
Целью настоящего учебного пособия является оказание помощи студентам высших учебных заведений при проектировании цилиндрических редукторов.
Учебное пособие содержит краткие теоретические сведения по курсу «Детали машин» примеры расчета передач. Методика расчета сопровождается необходимыми справочными материалами и иллюстрациями.
Кинематический расчет привода
Рисунок 1- Схема передач входящих в привод
1 Определяем требуемую мощность двигателя
где - общий КПД привода определяется по формуле
где - КПД ременной передачи
- КПД закрытой цилиндрической передачи.
2 Выбор электродвигателя. Прежде чем выбрать двигатель по найденной мощности необходимо определить требуемое число оборотов двигателя для данного привода. Для этого вычислим общее передаточное отношение привода
где - передаточное отношение ременной передачи;
- передаточное отношение зубатой цилиндрической передачи.
Первоначально примем величины передаточных отношений из рекомендованных:
Определим общий КПД привода:
Принимаем двигатель 112МВ6 ; 950 обмин.
Теперь уточняем передаточное отношение привода с обмин.
Пересчитываем передаточное отношение ременной передачи:
3 Определяем мощность на каждом валу
4 Определяем обороты каждого вала
5 Определяем угловую скорость каждого вала
6 Определяем моменты на валах
Выбор материала и определение допускаемых напряжений для зубчатых колес
1 Твердость материала шестерни должна быть на 20-30 единиц выше твердости колеса .
Принимаем материал - сталь 40ХН.
2 Пределы выносливости по контактным напряжениям вычисляются по формулам:
3 Вычисляем допускаемые контактные напряжения:
- требуемый коэффициент безопасности принимаем
– коэффициент долговечности учитывающий влияние срока службы и режима передачи для базового числа циклов
4 Пределы выносливости по изгибным напряжениям вычисляются по формулам:
5 Вычисляем допускаемые изгибные напряжения:
– для базового числа циклов.
проектный и проверочный расчет закрытой цилиндрической прямозубой передачи.
1 При симметричном расположении шестерни относительно опор и постоянной нагрузке принимаем коэффициент ширины венца колеса по делительному диаметру . Коэффициент ширины венца колеса по межосевому расстоянию вычисляется по формуле:
2 Из рекомендаций принимаем коэффициенты учитывающие неравномерность распределения нагрузки по длине зуба.
При симметричном расположении шестерни и ; .
3 Определяем межосевое расстояние передачи:
где Т1 крутящий момент на шестерне Нм; меньшее допускаемое контактное напряжение Па.
4 Определяем модуль зубьев
5 Вычисляем суммарное число зубьев:
Число зубьев шестерни и колеса:
6 Вычисляем передаточное число цилиндрической передачи
отклонение составило 0% что допустимо.
7 Вычисляем основные геометрические размеры передачи
а) диаметры делительных окружностей:
б) фактическое межосевое расстояние:
расхождение составило 0% что допустимо.
в) диаметры окружностей вершин:
Полученные диаметры и должны соответствовать принятым диаметрам заготовок.
г) ширина венца колеса:
8 Окружная скорость зубчатых колес:
принимаем 8-ю степень точности. Предельная окружная скорость 6 мс.
9 Вычисляем окружную и радиальную силы:
где угол зацепления для некорригированных передач .
10 Принимаем коэффициенты динамической нагрузки: ; .
11 Расчетное контактное напряжение:
Недонапряжение составило что допустимо так как перенапряжение допустимо до 5 % недонапряжение допустимо до 10%.
12 Выбираем коэффициент формы зуба .
Сравнительная характеристика прочности зубьев на изгиб:
13 Вычисляем расчетное напряжение изгиба в основании ножки зуба колеса.
т. е. прочность зубьев колеса на изгиб обеспечена.
Расчет плоскоременной передачи от двигателя к редуктору.
1 Вычисляем диаметр малого шкива
2 Определяем скорость ремня
3 Определяем диаметр большого шкива
Принимаем коэффициент скольжения = 001.
4 Фактическое передаточное отношение
5 Межосевое расстояние. Для получения меньших габаритов воспользуемся следующей формулой:
6 Расчетная длина ремня
На сшивку длина ремня увеличивается на l = 100 400 мм.
Добавим l = 113 мм тогда общая длина ремня мм.
7 Число пробегов ремня
8 Уточнение межосевого расстояния не выполняется так как ремень не бесконечный а сшивной.
9 Угол обхвата ремнем малого шкива
10 Толщину ремня . для резинотканевых ремней определяем из соотношения
Принимаем толщину ремня мм (3 прокладки с резиновыми прослойками мм).
11 Допускаемая приведенная удельная окружная сила в резинотканевом ремне при МПа вычисляется по формуле:
12 Поправочные коэффициенты:
коэффициент угла обхвата определяется интерполированием для соответствующего угла обхвата.
скоростной коэффициент определяется по формуле:
коэффициент нагрузки и режима работы при умеренных колебаниях.
коэффициент учитывающий вид передачи и ее расположение при вертикальном расположении передачи.
Допускаемая удельная окружная сила:
14 Площадь сечения А и ширина ремня b
15 Сила предварительного натяжения ремня
Схема сил в зацеплении
Рисунок 2 – Схема сил в зацеплении
Предварительный расчет валов
Вал редуктора – это ступенчатое цилиндрическое тело количество и размеры ступеней которого зависят от количества и размеров устанавливаемых на вал деталей.
Цель предварительного расчёта – определить диаметры выходных концов валов из условия прочности при кручении
где Wp 02d 3 – полярный момент инерции мм3; [] – условное допускаемое касательное напряжение. Рекомендуется принимать [] = 1540 МПа. Условное допускаемое касательное напряжение [] определяется по эмпирической формуле
где [] – нормальное допускаемое напряжение определяется по формуле
где оп – опасное напряжение. Для пластичных сталей (углеродистых и легированных при высокой температуре отпуска) за опасное напряжение можно принимать предел текучести т или предел выносливости -1 К = 812 коэффициент запаса прочности учитывающий переменные во времени напряжения. Примем оп = т.
1 Диаметр выходного конца первого вала принимаем равным диаметру выходного конца ранее подобранного двигателя 112МВ6
2 Определяем диаметр выходного конца второго вала. Материал ведущего вала тот же что и для шестерни т. е. сталь 40Х так как они изготовлены как одно целое. Предел прочности в = 900 МПа предел текучести т = 750 МПа диаметр заготовки до 120мм.
Вычисляем диаметр выходного конца вала:
3 Определяем диаметр выходного конца третьего вала. Примем материал третьего вала сталь 40Х. Предел прочности в = 900 МПа предел текучести т = 750 МПа диаметр заготовки любой.
Из-за неизбежной несоосности соединяемых валов цепная муфта нагружает вал дополнительной консольной силой которая вычисляется по формуле:
где Тi – крутящий момент на валу муфты Нмм d1 – делительный диаметр ведущей звездочки цепной муфты мм.
Делительный диаметр ведущей звездочки цепной муфты вычисляется по формуле:
Ширина полумуфты для выбранной цепной муфты ВМ = L2 = 81 мм.
Предварительное конструирование валов
По конструкции валы обычно бывают ступенчатыми. Образование ступеней на валу связано с закреплением деталей или самого вала в осевом направлении а также возможностью сборки деталей. При сборке должно быть обеспечено свободное передвижение детали по валу до места её посадки.
Диаметры валов в местах посадки сопряженных с валом деталей должны быть выравнены до стандартных значений. Диаметры внутренних колец подшипников качения от 20 мм кратны 5.
Для фиксации деталей на валах в осевом направлении служат буртики (рис. 3) высота заплечиков которых ориентировочно может быть принята в пределах .
Радиус галтели r при переходе от диаметра d к большему диаметру D вала в тех местах где нет насаженных деталей (рис. 3) можно принимать по следующей рекомендации:
Рисунок 3 - Размеры свободных участков вала
Рисунок 4 - Размеры участков вала с насаженными деталями
При неподвижном соединении вала и насаженной детали (шкив или зубчатое колесо) вал имеет галтель а насаженная деталь – фаску (рис. 4). В этом случае необходимо чтобы катет фаски с был больше радиуса галтели r (с > r) что обеспечивает плотное прилегание ступицы к буртику. В этом случае величину радиуса галтели r и величину катета фаски с принимают по рекомендации.
Концы валов должны заканчиваться фасками размеры которых также принимаются по выше изложенным рекомендациям.
Величина катета фаски с мм
Галтельные переходы у посадочных мест подшипников принимаются в соответствии с рекомендацией
колец подшипника rп мм
1 Конструкция второго вала (рисунок 5)
Рисунок 5 – Конструкция второго вала.
В соответствии с рекомендациями принимаем: мм мм. Предварительно намечаем подшипник легкой серии диаметров 2 серии ширин 0 206 для которого rп = 2 мм тогда принимаем в соответствии с рекомендациями =1 мм h = 25 мм.
2 Конструирование третьего вала (рисунок 6)
В соответствии с рекомендациями принимаем: мм мм мм. Предварительно намечаем подшипник легкой серии диаметров 2 серии ширин 0 209 для которого rп = 2 мм тогда принимаем в соответствии с рекомендациями =1 мм h = 25 мм.
Рисунок 6 - Конструирование третьего вала.
Конструирование зубчатых колес редуктора
1 Шестерня быстроходной ступени изготавливается заодно с валом.
Основные размеры быстроходной шестерни:
диаметр окружности вершин зубьев шестерни мм;
делительный диаметр мм;
диаметр окружности впадин зубьев шестерни мм;
ширина венца шестерни мм.
2 Колесо быстроходной ступени – литое (рис. 7)
Рисунок 7 - Конструкция колеса быстроходной ступени
Основные размеры быстроходного колеса:
диаметр окружности вершин зубьев колеса мм;
ширина венца колеса мм;
а) диаметр ступицы колеса
б) длина ступицы колеса
В массовом производстве необходимо соблюдать равенства:
в) толщина обода цилиндрических колес
г) толщина диска литых колес
д) внутренний диаметр обода колеса
е) диаметр центровой окружности
ж) диаметр отверстий
Эскизная компоновка привода (рис. 9) служит для определения положения зубчатых колес и шкива ременной передачи относительно опор для последующего выполнения проверочных расчетов валов и подбора подшипников.
Чтобы поверхности вращающихся колес не задевали за внутренние поверхности стенок корпуса между ними оставляют зазор f = 5 мм при мощности Р = 1 кВт и f = 15 мм при мощности Р = 10 кВт.
Принимаем f = 9 мм при мощности Р = 4 кВт.
Для лучшей смазки расстояние между торцовыми поверхностями зубчатых колес также принимается равным f.
Принимаем индивидуальный способ смазки подшипников консистентной смазкой. Для предотвращения её вымывания из подшипникового узла устанавливают подшипники закрытые шайбами. Для более удобного регулирования зацепления зубчатых передач принимаем накладные крышки. Предварительно намечаем следующие серии подшипников:
для быстроходного вала (второй вал) намечаем шарикоподшипники радиальные легкой серии 206 (серии диаметров 2 серии ширин 0).
для промежуточного вала (третий вал) намечаем шарикоподшипники радиальные легкой серии 209 (серии диаметров 2 серии ширин 0).
Данные для определения длины валов:
) ширина шкива В = 50 мм;
) ширина шестерни быстроходной передачи мм;
) ширина шестерни тихоходной передачи мм;
) ширина полумуфты цепной муфты ВМ = L2 = 81 мм;
) ширина подшипника 206 серии на втором валу мм;
) ширина подшипника 209 серии на третьем валу мм.
Рисунок 9 – Эскизная компоновка привода
Проверочный расчет третьего вала на статистическую прочность
1 Составляем расчетную схему вала со всеми действующими на него силами (рис. 10 а).
2 Составляем расчетную схему от сил действующих в вертикальной плоскости. Подшипники заменяем шарнирными опорами: одна подвижная другая неподвижная (рис. 10 б).
а) вычисляем величину опорных реакций в вертикальной плоскости:
б) определяем изгибающие моменты М верт в вертикальной плоскости (рис. 10 в):
3 Составляем схему нагрузок в горизонтальной плоскости (рис. 10 г).
а) вычисляем величину опорных реакций. Силы рисуем вертикально так как на расчетах это не отражается.
Рисунок 10 - Эпюры третьего вала.
Для проверки правильности определения опорных реакций составляем уравнение:
б) составляем уравнения изгибающего момента в горизонтальной плоскости М гор (рис. 10 е)
4 Результирующую эпюру изгибающих моментов строим как геометрическую сумму ординат от моментов в вертикальной и горизонтальной плоскостях (рис. 10 е):
Вычисляем значения ординат Мрез в граничных сечениях:
5 Строим эпюру крутящего момента (рис. 10 ж). Вал имеет один участок – CD на котором Нм.
6 Значение приведенного момента вычисляем в характерных точках по третьей теории прочности:
Эпюра Мприв приведена на рис. 10 з. По эпюре Мприв устанавливается опасное сечение вала. В данном случае опасным является сечение проходящее через точку С т. е. расположенное под шестерней.
7 Выполняем проверочный расчет вала по третьей теории прочности. Вычислим эквивалентное напряжение в опасном сечении вала. Диаметр второго вала в опасном сечении мм.
где Мприв =27309 Нм – приведенный момент в опасном сечении вала; осевой момент сопротивления; МПа.
Условие прочности выполняется.
Проверочный расчет четвертого вала по переменным напряжениям
Проверку прочности вала при переменных напряжениях производим по тем же нагрузкам по которым был выполнен расчет на статическую прочность. Для расчета используем готовые эпюры (рис. 10 е ж з).
В опасном сечении (сечение проходящее через точку С) имеем:
1 Вычисляем величину номинального напряжения от результирующего изгибающего момента Mрез:
Вычисляем величину номинального напряжения от крутящего момента Нм.
Нормальные напряжения от изгибающего момента при вращении вала меняются по симметричному циклу:
Касательные напряжения в нереверсивных валах меняются по отнулевому циклу:
2 Устанавливаем величину пределов выносливости и коэффициентов.
Для углеродистой стали 40ХН: предел прочности МПа предел текучести МПа предел выносливости при изгибе с симметричным циклом нагружения МПа предел выносливости при кручении с симметричным циклом нагружения МПа.
Коэффициенты влияния асимметрии цикла находим из рекомендаций:
Концентраторами напряжений в опасном сечении являются галтель шпоночная канавка напряженная посадка колеса. Из рекомендаций (табл. 16) для стали 40ХН с МПа находим:
галтель – k = 228; k = 237;
шпоночная канавка – k = 201; k = 188;
напряженная посадка колеса – k = 209; k = 171.
Для дальнейшего расчета принимаем k = 228; k = 237.
Масштабные факторы выбираем из рекомендаций для d = 50 мм и углеродистой стали:
3 Вычисляем коэффициент запаса прочности по нормальным напряжениям:
Допускаемый коэффициент запаса прочности принимается равным:
[S] = 1315 для обеспечения прочности;
[S] = 254 для обеспечения жесткости.
Так как для данного вала расчет на жесткость не выполнялся то принимаем [S] = 4.
Вывод: прочность вала по переменным напряжениям и жесткость вала обеспечены.
Подбор подшипников качения по долговечности
1 Величины опорных реакций определяются из уравнений равновесия
Вычисляем суммарные радиальные опорные реакции:
Дальнейший расчет ведется по более нагруженной опоре т. е. по опоре D.
2 По условиям работы подшипникового узла (небольшая угловая скорость отсутствие осевой силы ) намечаем радиальный шарикоподшипник серии 209 (легкая серия диаметров 2 ширин 0) для которого динамическая грузоподъемность кН статическая грузоподъемность кН.
3 Определим эквивалентную нагрузку для более нагруженного подшипника по формуле:
Принимаем так как осевая нагрузка подшипника
По отношению принимаем
Окончательно формула для радиальных шарикоподшипников запишется в виде:
4 Вычисляем действительную долговечность подшипника по формуле:
где расчетная долговечность подшипника (срок службы) ч; угловая скорость радс; С динамическая грузоподъемность Н; приводится в каталогах; эквивалентная (приведенная) нагрузка Н; m показатель степени .
Должно выполняться условие Для цилиндрических редукторов Принимаем
данный подшипник удовлетворяет условию.
Расчет шпоночных соединений
1 Проверочный расчёт шпоночного соединения второго вала под ведомым шкивом ременной передачи.
Принимаем шпонку призматическую со скругленными торцами. Её размеры по ГОСТ 2407180: b = 6 мм; h = 6 мм; t1 = 35 мм; t2 = 28 мм.
Вычисляем длину шпоночного паза:
вычисленная длина шпонки соответствует стандартной длине.
Вычисляем рабочую длину шпоночного паза:
Вычисляем напряжения смятия:
В данном расчете снижаем допускаемые напряжения смятия []см на 50 % так как имеют место повышенные колебания и вибрации при пуске двигателя.
2 Проверочный расчёт шпоночного соединения третьего вала под колесом.
Принимаем шпонку призматическую со скругленными торцами. Её размеры по ГОСТ 2407180: b = 14 мм; h = 9 мм; t1 = 55 мм; t2 = 38 мм.
2 Проверочный расчёт шпоночного соединения третьего вала под муфтой.
Принимаем шпонку призматическую со скругленными торцами. Её размеры по ГОСТ 2407180: b = 10 мм; h = 8 мм; t1 = 5 мм; t2 = 33 мм.
Расчет корпусных деталей
Толщина стенок корпуса:
Толщина стенок крышки
Толщина фланцев (поясов) корпуса:
Толщина фланцев (поясов) крышки:
Толщина нижнего пояса корпуса без бобышек:
Толщина рёбер основания корпуса:
Толщина рёбер крышки:
Диаметры фундаментных болтов:
принимаем болты с резьбой М16.
Диаметр болтов у подшипников
принимаем болты с резьбой М12.
Диаметр болтов соединяющих основание корпуса с крышкой
принимаем болты с резьбой М10.
Размеры определяющие положение болтов d2
где мм – диаметр винтов крепления крышки подшипника. Принимают 4 – 6 винтов.
Высота бобышки h принимается конструктивно так чтобы образовалась опорная поверхность под головку болта и гайку. Желательно у всех бобышек иметь одинаковую высоту h.
Наименьший зазор между наружной поверхностью колеса и стенкой корпуса по диаметру А (1 12) = 8 10 мм по торцам А1 = А.
Два штифта принимаем штифты d = 8 мм (табл. 35).
Длина штифтов принимаем .
Штифты служат для фиксации крышки редуктора относительно корпуса. Они устанавливаются еще до расточки гнезд под подшипники.
Смазывание зацепления и подшипников производится разбрызгиванием жидкого масла. При контактных напряжениях МПа и скорости скольжения мс рекомендуемая вязкость масла должна быть приблизительно равна 3410-6 м2с. Принимаем масло индустриальное И-40А.
Объем масляной ванны определяется из расчета 05 08 л на 1 кВт мощности. В нашем случае V = 2 32 л.
СПИСОК ИСПОЛЬЗОВАННЫХ ИСТОЧНИКОВ
) Дунаев П.Ф. Конструирование узлов и деталей машин: Учеб. пособие для студ. техн. спец. вузов П.Ф.Дунаев О.П.Леликов. 8-е изд. перераб. и доп. — М.: Издательский центр «Академия» 2007. — 496 с.
) Чернавский С.А. Боков К.Н. и др. Курсовое проектирование деталей машин 3-е изд. М.: Машиностроение 2005 415 с.
) Куклин Н.Г. Куклина Г.С. Детали машин М.: Высшая школа 2008 309с.
) Детали машин. Основы проектирования и конструирования: Метод. указания по выполнению курсового проекта Сост. Г. Н. Лимаренко В. И. Сенькин А. А. Максимова и др.; Под ред. Г. Н. Лимаренко А. А. Соломкина. Красноярск: ИПЦ КГТУ 2003. — 64 с.
) Иванов М. Н. Детали машин: Учеб. для студентов высш. техн. учеб. заведений —5-е изд. перераб — М.: Высш. шк. 1991. — 383 с. ил.
) Решетов Д.Н. Детали машин. 4-е изд. М.: Машиностроение 1989 496 с.
) Чернилевский Д.В. Детали машин. Проектирование приводов технологического оборудования Учебное пособие для студентов вузов. М.: Машиностроение 2004. — 560 с.
) Гузова В.В. и др. Прикладная механика Учебное пособие. Красноярск 2003 218 с.
Сборочный чертеж _ КП.008.003.02.00.000.СБ.cdw

Крутящий момент на тихоходном валу редуктора Т
Число оборотов тихоходного вала n
Общее передаточное число редуктора u = 10.
Технические требования
необработанные поверхности литых деталей
красить маслостойкой красной эмалью.
Наружные поверхности корпуса красить серой эмалью ПФ-115
Плоскость разъема покрыть тонким слоем герметика УТ-34
ГОСТ 24285-80 при окончательной сборке.
л масла марки И-40А.
КП.008.003.02.00.000.
сборочный чертеж спецификация.spw

Цилиндрическое прямозубое колдесо
Крышка накладная сквозная
Крышка накладная глухая
Набор стальных прокладок
Пробка маслоспускного отверстия
Рекомендуемые чертежи
- 06.04.2022