Проектирование и исследование механизмов движения легкового автомобиля




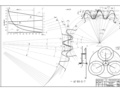
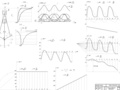
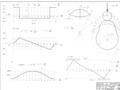
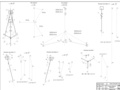
- Добавлен: 24.01.2023
- Размер: 349 KB
- Закачек: 1
Описание
Состав проекта
![]() |
![]() |
![]() ![]() ![]() ![]() |
![]() ![]() ![]() ![]() |
![]() ![]() ![]() ![]() |
![]() ![]() ![]() ![]() |
![]() ![]() ![]() |
Дополнительная информация
L4.dwg

кулачкового механизма
МГТУ им. Н. Э. Баумана
L2.dwg

кулачкового механизма
Теория механизмов и машин
Расчетная схема звенья 2-3
Расечтная схема звенья 4-5
Расчетная схема звенья 6-7
Расчетная схема звено 1
M(F ) + M(F ) + M(F ) + M + M = 0
Ф + F + Ф + F + F + F = 0
L1.DWG

L3.dwg

zapiska.doc
Факультет «Энергетическое машиностроение»
Кафедра «Поршневые двигатели»
Расчетно-пояснительная
записка к курсовому проекту
«Проектирование и исследование
механизмов движения легкового автомобиля»
Данная расчетно-пояснительная записка содержит подробное описание выполнения задания по курсовому проектированию по теме “Проектирование и исследование механизмов движения легкового автомобиля”. В состав курсового проекта входят: данная расчетно-пояснительная записка и 4 листа формата А1 с необходимыми графическими расчетами и зависимостями. Расчетно-пояснительная записка содержит 33 листа машинописного текста в который включено 6 рисунков.
Также расчетно-пояснительная записка содержит расчеты используемые при проектировании механизмов движения легкового автомобиля: определение законов движения звеньев и точек механизма силовой расчет механизма проектирование и исследование зубчатой передачи синтез кулачкового механизма. К расчетно-пояснительной записке прилагаются: техническое задание и результаты работы программ использовавшихся при проектировании механизма.
Техническое задание 4
Определение законов движения механизма
1.Проектирование кривошипно-ползунного механизма 9
2.Определение передаточных функций скоростей
кривошипно-ползунного механизма . 9
3.Построение графической зависимости суммарного приведенного
момента от угла поворота кривошипа .12
4. Построение графика суммарной работы . 12
5. Определение суммарного приведенного момента инерции .. 14
6. Построение графика скорости вращения кривошипа 16
7 Построение графика углового ускорения кривошипа . ..16
1. Определение скоростей точек и звеньев механизма . 20
2. Определение ускорений точек и звеньев механизма .. ..20
3. Определение главных векторов сил инерции и главных моментов
4. Определение усилий в кинематических парах .. 23
5. Определение момента сопротивления 24
Проектирование зубчатой передачи
1. Выбор коэффициентов смещения с учетом качественных
показателей работы зубчатой передачи . 25
2. Станочное зацепление .. 27
3. Зубчатая передача 27
4. Проектирование планетарного редуктора ..29
Проектирование кулачкового механизма
1. Построение графика передаточной функции скорости и
перемещения толкателя 30
2. Построение допустимой области расположения центра
вращения кулачка . 30
3. Построение профиля кулачка .. .31
4. Построение графика изменения угла давления .. 31
Список использованной литературы . ..33
Этот этап нам необходимо выполнить для получения значений параметров движения механизма (угловые скорость и ускорение кривошипа 1) которые нам понадобятся для выполнения силового расчета.
1.Проектирование кривошипно-ползунного механизма
Проектирование кривошипно-ползунного механизма ведется по средней скорости поршня (ползуна). При этом известными являются следующие параметры: средняя скорость поршня Vср=12.0 мс частота вращения вала кривошипа n=73 c-1 отношение длин шатуна и кривошипа 1=lABlOA=3.7 относительное расстояние от центра масс шатуна к длине шатуна l2=1AS1AB=0.77
Время одного оборота вала t=1n равно 0.0137 с а расстояние которое проходит поршень за один оборот S равно 4.lOA. Но Vср=St. Нетрудно заметить что lOA=Vср(4.n) => lОА=0.041 м => lАВ=l2×1OA=0.152 м.
На рис. 1 показаны: 1- кривошип 2- шатун 3- ползун.
2. Определение передаточных функций скоростей кривошипно-ползунного механизма
Искомые передаточные функции находим по следующим формулам:
w1 - угловая скорость кривошипа 1 [радс];
w2 - угловая скорость шатуна 2 [радс];
VQB VQS2 - скорости точек B и S2 соответственно [мс].
Значения передаточных функций получены с помощью программы «AR2». Результаты работы этой прилагаются на следующей странице.
Ниже приведен график передаточных функций.
3. Построение графической зависимости суммарного приведенного момента от угла поворота кривошипа 1
Суммарный приведенный момент является суммой приведенного движущего момента Mдпр и приведенного момента сопротивления Mспр . Для определения Мдпр воспользуемся формулой Мдпр=FдVc. График строится по точкам (12 положений) для 1-го цилиндра. Для двух других цилиндров графики получаем путем сдвига 1-го графика на 120o и 240o соответственно. Зависимость суммарного движущего момента Мдпр (j) получается сложением этих трех графиков. Приведенный момент сопротивления Mспр получаем по формуле где Мсуст -установившийся момент сопротивления [кн×м]. Его определяем графическим интегрированием графика движущего момента и делением результата на 2p. Результатом сложения графиков Мдпр (j) и Mспр (j) будет являться график суммарного приведенного момента Мпр (j).
Вычисление координат точек для построения графиков Мдпр1(j) Мдпр2(j) Мдпр3(j) Мдпр (j) производится с помощью программы “MS Excel” в файле “rashet.xls”. Результаты приведены на следующей странице.
4. Построение графика суммарной работы
Суммарная работа приведенного суммарного момента сил вычисляется по формуле:
Таким образом график суммарной работы можно получить путем графического интегрирования графика суммарного приведенного момента сил.
После получения графика А(j) вычисляется его масштаб следующим методом:
где mj - масштаб по оси абсцисс и а OK - длина отрезка интегрирования и OK=60 мм. => .
Полученный график корректируем в соответствии со значением начальной кинетической энергии кДж (AS=Tн) путем сдвига оси абсцисс на требуемую величину.
5. Определение суммарного приведенного момента инерции
Суммарный приведенный момент инерции всего механизма равен сумме приведенных моментов инерции всех его звеньев. Рассмотрим получение графика приведенного момента инерции на примере первого цилиндра а остальные графики получим сдвигом на 120o и 240o соответственно. Суммарный приведенный момент инерции второй группы звеньев (ползуна 3 и шатуна 2) 1-го цилиндра рассчитывается по формуле: где I3Ппр - приведенный момент инерции ползуна 3 при его поступательном движении; I2Ппр -приведенный момент инерции шатуна 2 при его поступательном движении; I2Врпр - приведенный момент инерции шатуна 2 при его вращательном движении. Приведенные моменты инерции элементов при поступательном движении рассчитываются по формулам:
V-скорость поступательного движения звена [мс];
w -угловая скорость кривошипа 1 [радс];
m -масса звеньев 3 и 2 соответственно [кг].
Приведенный момент инерции шатуна 2 при его вращательном движении рассчитывается по формуле:
w1 и w2 -угловые скорости кривошипа 1 и шатуна 2 [радс];
I2s -момент инерции шатуна 2 относительно оси проходящей через центр тяжести шатуна [кг×м2].
Полный момент инерции второй группы звеньев получаем путем сложения графиков и . Суммарный приведенный момент инерции всего механизма = + где - приведенный момент инерции первой группы звеньев ( кривошипов совершающих только поступательное движение ) задается равным 0.58 кг×м . График (j) получаем из графика (j) параллельным переносом оси абсцисс вниз на величину равную 0.58 кг×м .
Вычисление координат точек для построения графиков I3Ппр(j) I2Ппр(j) I2Врпр(j) (j) (j) (j) (j) производится с помощью программы “MS Excel” в файле “rashet.xls”. Результат расчета приведен на следующей странице.
6. Построение графика скорости вращения кривошипа 1
Зависимость угловой скорости w1 от координаты j можно записать в виде:
- работа суммарного приведенного момента сил приложенных к механизму [Дж];
Tн - кинетическая энергия звеньев в начальном положении [Дж].
Примем начальную кинетическую энергию Тн равную нулю а затем устраним допущенную ошибку путем корректировки графика w(j) в соответствии с начальным значением угловой скорости wнач которое принимаем равным средней угловой скорости кривошипа wср=2pn=458.44 1с. (Т. е. сдвигаем ось абсцисс графика до тех пор пока начальное значение угловой скорости на графике не совпадет с wср=458.44 1с).
Вычисление координат точек для построения графика w1=w1(j) производится с помощью программы “MS Excell” в файле “rashet.xls” и приводится на следующей странице.
Для нахождения зависимости w1=w1(t) используется представление функции w(j) в виде: => .
При tн=0 уравнение упрощается: и найденная зависимость t=t(j) позволяет найти и искомую зависимость w1=w1(t). Решение данного уравнения проводится графически. При графическом интегрировании для решения уравнения используют специальный прием для построений с помощью которого строится график функции t=t(j).Затем находят искомую зависимость w(t) путем исключения переменной j.
7. Построение графика углового ускорения кривошипа 1
Угловое ускорение e1 определяем по формуле: (по свойству производной) где:
МSпр - суммарный приведенный момент сил приложеных к механизму [н×м];
ISпр - суммарный приведенный момент инерции [кг×м2];
w1 - угловая скорость кривошипа [радс];
mI и mj - масштабы графика Iпр(j) по осям ординат и абсцисс соотоветственно mj=30 ; mI=70000 ;
tgj - угол наклона касательной построенной в соответствующей точке к графику Iпр(j). (Для точек соответствующих углам поворота кривошипа равным 30o150o270o tgj=1.07 для точек соответствующих углам поворота кривошипа равным 90o210o330o tgj= -1.07 для остальных точек tgj= 0).
Вычисление координат точек для построения графика e1=e1(j) выполняется в программе “MS Excell” в файле “rashet.xls” и приводится на 19-ой странице.
Силовой расчет механизма проводится для положения механизма соответствующего углу поворота кривошипа j=60о. Из расчета кинематических параметров механизма проведенного на первом листе нам известны угловая скорость w=46203 радс и угловое ускорение e = 086 радс-2 кривошипа в момент соответствующий углу j =60о. Также известны силы давления газа на поршни двигателя: F3= 55 кН; F5= 0 кН; F7=0796 кН и геометрические параметры звеньев механизма: lA2B2= lA4B4 = lA6B6= 0.152 м lO2A2= lO4A4 = lO6A6= 0.041 м.
1. Определение скоростей точек и звеньев механизма
Зная длину кривошипов (OA2 OA4 OA6) и их угловую скорость w=46203радс мы находим скорости точек A2 A4A6 по формулам: V= w×l где:
V - скорость конца кривошипа [мс];
w - угловая скорость кривошипа [радс].
Для нахождения скоростей точки составляем векторное уравнение:
- скорость точки В2 известная нам только по направлению ( направлена вертикально) ;
- скорость точки А2 известная нам и по значению и по направлению (VA2 = w×
- скорость точки В2 вокруг А2 известная нам только по направлению (^B2A2).
Выбираем полюс скоростей pv и в масштабе mv= 5 ммм×с-1 откладываем вектор скорости (на конце этого вектора обозначим точку a2) и прямую на которой лежит вектор . Через конец вектора проводим прямую на которой лежит вектор . Пересечение двух прямых даст нам точку b2 на векторной диаграмме. Модули искомых скоростей получаем по формуле: VB2 = pvb2mv = 1898 мс; VB2A2 = a2b2mv =984 мс .
Аналогично проводим построение планов скоростей для других двух цилиндров приняв за полюс все ту же точку Pv.
Находим: VB4 = 0 мс VB4A4 = 1901 мс
VB6 = 1898 мс VB6A6 =984 мс .
Угловые скорости звеньев 2 4 6 вычисляем по формулам:
w2 = VB2A2 w 4 = VB4A4 w6 = VB6A6lA6B6 .
Получаем w2= 6474 радс w4 = 1251 радс w6 = 6474 радс.
2. Определение ускорений точек и звеньев механизма
Для определения ускорений звеньев механизма разобьем его на три кривошипно-ползунных механизма (ускорения определим отдельно для трех цилиндров а для построения планов ускорений будем использовать один и тот же полюс).
Проведем расчет для первого цилиндра. Для этого составим векторное уравнение:
- нормальная составляющая ускорения точки А2 OA2
и = w2 ×lOA2= 87523 мс-2
- тангенциальная составляющая ускорения точки А2 ^ OA2
- нормальная составляющая ускорения точки В2 вокруг А2
- тангенциальная составляющая ускорения точки В2 вокруг А2
^ A2B2 модуль вектора неизвестен;
- ускорение точки В2. Вектор лежит на вертикальной прямой его модуль неизвестен.
- нормальная составляющая ускорения точки S2 вокруг А2
- тангенциальная составляющая ускорения точки S2 вокруг А2
^ A2B2 =× lA2S2 lA2B2= 59121 мс-2.
- ускорение точки S2.
Из многоугольника ускорений получаем:
aB2 =3211 мс-2; aB2A2 = 5912 мс-2; aS2 = 3880 мс-2 .
Угловое ускорение звена 2 вычисляем по формуле:
e 2 = l A2B2 = 50513 радс-2 .
Аналогичный расчет проводим для других двух кривошипно-ползунных механизмов и получаем:
aB4 = 64354 мс-2 aB4A4 = 23788 мс-2 aS4 = 59449 мс-2
aB6 = 3211 мс-2 aB6A6 = 5912 мс-2 aS6 = 3880 мс-2
e4 = lA4B4 = 0 радс-2 e6= lA6B6= 50513 радс-2.
3. Определение главных векторов сил инерции
и главных моментов сил инерции
При силовом расчете удобно использовать метод с помощью которого уравнениям динамики по форме придается вид уравнений статики вводя в уравнения силы инерции и моменты инерции. В этом случае геометрическая сумма задаваемых сил реакций связи и сил инерции равна нулю. Аналогично сумма моментов от заданных сил реакций связи сил инерции и моментов инерции равна нулю:
Для тела совершающего плоское движение различают главный вектор сил инерции звена приложенный в центре масс и определяемый формулой:
и главный момент сил инерции определяемый формулой:
Определим значения сил и моментов действующих на механизм:
По сравнению с остальными силами силы тяжести пренебрежимо малы при выбранных нами масштабах ошибка при их исключении из рассмотрения не будет превышать 05% поэтому ими мы пренебрегаем и далее не будем упоминать о них.
4. Определение усилий в кинематических парах
Для определения усилий в кинематических парах механизма расчет будем проводить отдельно для трех кривошипно-ползунных механизмов находя для каждого из них реакции действующие в шарнирах A2 A4 A6. Определив значения и направления этих реакций рассмотрим равновесие звена 1 состоящего из трех кривошипов и найдем значение момента сопротивления приложенного к этому звену а также реакцию в шарнире O.
Рассмотрим нахождение реакций в шарнирах A2 A4 A6 на примере первого кривошипно-ползунного механизма (звенья 123).
Для нахождения тангенциальной составляющей реакции в шарнире A2 -- запишем уравнение моментов относительно шарнира B2 . Это уравнение имеет вид:
lF30- плечо силы F30 lF30=0 м так как в противном случае звено 3 вращалось бы вокруг шарнира B2.
Вектора сил F3 Ф3 проходят через центр тяжести звена 3 т. е. через точку B2 и моменты от них относительно этой точки равны нулю.
Из уравнения (*) находим : =8758 н.
Для нахождения полной реакции в шарнире А2 составим векторное уравнение:
- силы найденные выше; - направлены вертикально вниз; направлены в противоположные ускорениям и соответственно стороны; ^ направлена горизонтально).
По полученным данным строим план сил в масштабе mF=003 ммН откуда получаем значения сил:
Для нахождения полной реакции в шарнире B2 (F32) составим векторное уравнение сил действующих на поршень 3:
Строим план сил в масштабе mF=003 ммН откуда получаем значение силы:
Аналогичные операции проводим для двух других кривошипно-ползунных механизмов и получаем следующие результаты:
Для нахождения полной реакции в шарнире O (F10) составим векторное уравнение сил действующих на кривошип 1:
- найденные реакции в шарнирах A2 A4 A6.
5. Определение момента сопротивления
Момент сопротивления определяется из условия равновесия механизма относительно шарнира O. Для этого записывается уравнение моментов относительно точки О:
F12 F14 F16 - силы действующие на шарниры A2 A4 A6:
l12 l14 l16- расстояния от линий действия сил F12 F14 F16 до точки О:
Момент сопротивления равен 1607 Н×м.
Сравним полученное значение момента сопротивления со значением на графике приведенном на листе 1. Mcгр»170 Н×м.=> Сделанная ошибка составляет 55%.
Нам необходимо спроектировать цилиндрическую зубчатую передачу осуществляемую колесами 13 и 14 с соответствующими числами зубьев z13=16 z14=40 и модулем m=4 мм. Для вычисления основных геометрических размеров передачи используется программа SS10’ (результаты работы программы приводятся на следующей странице) по данным которой строятся графики (рис. 4). С помощью графиков производится выбор коэффициента смещения x1 от которого зависят качественные и геометрические показатели проектируемого зубчатого колеса.
1. Выбор коэффициентов смещения с учетом качественных показателей работы зубчатой передачи
При выборе коэффициента смещения x1 необходимо добиться выполнения следующих основных требований:
При работе передачи не должно происходить заклинивания.
У проектируемой передачи должно отсутствовать такое явление как подрезание зубьев и их толщина на окружности вершин не должна быть меньше допустимой.
Коэффициент перекрытия проектируемой передачи должен быть больше допустимого.
Из всех коэффициентов смещения для которых выполняются три этих требования выбирается тот при котором скорости износа шестерни и колеса ближе всего по значениям.
Минимальное смещение при котором отсутствует подрезание: x1min=-002 мм.
Максимальное смещение определяется границей зоны заострения т.е. такой параметр как должен быть больше или равен 02. Границе зоны заострения соответствует смещение x1085 мм. Эта граница отмечена вертикальной линией и штриховкой на запрещенной стороне.
Ограничение коэффициента смещения по коэффициенту торцевого перекрытия [ea]=125 (7 степень точности) составляет x1=11 мм. Эта граница также отмечена вертикальной линией и штриховкой на запрещенной стороне.
Химико-термическая обработка для данных зубчатых колес - нормализация с последующим улучшением.
Выбираем коэффициент смещения x1 из интервала допустимых значений. Принимаем x1=03 (по ГОСТ 16573-70).
2. Станочное зацепление
После вычерчивания ИПК произведено построение сопряженного с ним эвольвентного профиля зуба шестерни один из промежуточных этапов этого построения показан на рис. 5.
3. Зубчатая передача
Вычерчена зубчатая передача с использованием построенного эвольвентного профиля зубьев шестерни и эвольвентного профиля зубьев колеса построенного с помощью обкатки его основной окружности. На чертеже обозначены все основные параметры зубчатой передачи.
рис. 53.4. Проектирование планетарного редуктора
Планетарная коробка передач состоит из двухрядного планетарного редуктора смешанного зацепления с тремя сателлитами. При проектировании редуктора используются следующие данные:
Передаточное отношение U - 192;
Число сателлитов k - 3.
Проектируемый редуктор должен удовлетворять следующим требованиям:
) Он должен обеспечивать необходимое передаточное отношение. Для этого записывают выражение связывающее между собой количество зубьев колес планетарного редуктора (Z1Z2Z3Z4) и заданное передаточное отношение. В нашем случае выражение имеет вид:
) Должно соблюдаться условие соосности т.е. оси центральных колес при назначенных Z должны совпадать с осью водила. В нашем случае выражение условия соосности имеет вид:
) Должно выполняться условие соседства (совместности) т.е. должна быть возможность размещения нескольких сателлитов по общей окружности в одной плоскости без соприкосновения друг с другом. Выражение условия соосности имеет вид:
) Должно соблюдаться условие сборки т.е. должна обеспечиваться возможность одновременного зацепления всех сателлитов с центральными колесами при равных углах между сателлитами:
=n где n - целое число.
) Должно соблюдаться условие отсутствия подрезания т.е. при колесах нарезанных стандартным инструментом без смещения (при ; ) Zmin должно быть больше 17 а Z4min должно быть не меньше 85.
После подбора числа зубьев методом дополнительных сомножителей с проверкой условий исходя из условия наименьших габаритов находим:
В двигателе внутреннего сгорания управление газораспределением осуществляется с помощью кулачкового механизма состоящего из кулачка и поступательно двигающегося толкателя. В техническом задании определен закон изменения ускорения толкателя в зависимости от угла поворота кулачка. Кроме того определены следующие исходные данные:
Угол рабочего профиля кулачка jр - 120 град;
Максимальный ход толкателя h - 00085 м;
Допустимый угол давления J - 30 град.;
Эксцентриситет e - 0 м.
1. Построение графика передаточной функции скорости и перемещения толкателя
Путем последовательного графического интегрирования заданной функции изменения ускорения толкателя получаем графики передаточной функции скорости и перемещения толкателя. По графику перемещения толкателя определяем максимальное значение перемещения которое в данном случае равно Y max=50 мм что соответствует ходу толкателя h=0.0085 м. Исходя из полученного результата находим масштаб графика перемещения толкателя:
b- база графика по оси абсцисс [мм].
Приняв отрезки интегрирования OК равными 50 мм определяем масштабы графиков передаточной функции скорости толкателя и его ускорения.
2. Построение допустимой области
расположения центра вращения кулачка
Для определения допустимой области расположения центра вращения кулачка необходимо произвести построение его фазового портрета. Эта операция сводится к построению зависимости передаточной функции скорости толкателя от его перемещения. Затем проведем вертикальные прямые касательные к крайним точкам фазового портрета и отложим от них допустимые углы давления как это показано на рис. 6. Проведя под этим углом прямые до их пересечения получим точку являющуюся центром кулачка минимальных размеров. Такой кулачок будет обеспечивать прямой и обратный ход толкателя без заклинивания.
Вся область расположенная под этой точкой и ограниченная двумя прямыми является областью каждая точка которой может быть центром вращения кулачка обеспечивающего прямой ход и реверс без заклинивания. Учитывая то что мы стремимся спроектировать механизм с наименьшими габаритами кулачок должен быть минимальных размеров и следовательно центр его вращения должен находиться в точке пересечения прямых.
3. Построение профиля кулачка
Для построения профиля кулачка проведем из полученного центра вращения кулачка окружность радиус которой равен расстоянию между центром вращения кулачка и нулевой точкой фазового портрета ( ro ). Расположим ось толкателя таким образом чтобы она проходила через центр вращения кулачка так как его эксцентриситет равен 0.От произвольной точки О на окружности отложим угол рабочего профиля кулачка jр = 180о и разобьем его лучами на 14 равных частей. Таким образом на окружности получим семейство точек 012 14. Отложив на каждом из лучей отрезки 1B1 2B2 14B14 соответствующие ординатам соответствующие ординатам YSBi с графика перемещения толкателя и соединив точки B1B2 B14 плавной линией получим теоретический профиль кулачка. Для получения конструктивного профиля необходимо обкатать данный профиль роликом. В данном случае радиус ролика Rp=03ro.
4. Построение графика изменения углов давления
График изменения угла давления на фазе удаления толкателя при рабочем направлении вращения кулачка и при его реверсе строим с использованием фазового портрета кулачка и свойств отрезка передаточной функции. Углы давления рассчитываем по формуле:
Список использованной литературы:
С.А. Попов. Курсовое проектирование по теории механизмов и механике машин. - М.: Высшая школа 1986.
Проектирование зубчатых передач и планетарных механизмов с использованием ЭВМ: Учебное пособие для курсового проектирования Под ред. Тимофеева Г.А. - М. : МВТУ 1987.
Учебное пособие для курсового проектирования по теории механизмов Под ред. Архангельской Т.А. - М: МВТУ 1985. - Ч. 1.
Рекомендуемые чертежи
- 10.08.2016
- 25.01.2023
- 05.10.2019
- 13.02.2021
Свободное скачивание на сегодня
Другие проекты
- 26.11.2018