Привод подачи токарно-винторезного станка




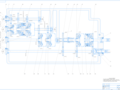
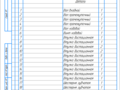
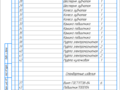
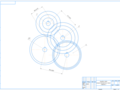
- Добавлен: 25.01.2023
- Размер: 7 MB
- Закачек: 0
Описание
Привод подачи токарно-винторезного станка
Состав проекта
![]() |
![]() |
![]() ![]() ![]() |
![]() |
![]() ![]() ![]() ![]() |
![]() ![]() ![]() ![]() |
![]() ![]() ![]() ![]() |
![]() |
![]() ![]() ![]() ![]() |
![]() ![]() ![]() ![]() |
![]() ![]() ![]() ![]() |
![]() ![]() ![]() ![]() |
Дополнительная информация
Кирс 78 новое .docx
Число скоростей z = 18;
Знаменатель прогрессии φ=112;
Структурная формула z=36-23-31;
Материал заготовки - чугун; сталь
Максимальная ширина обработки Dma
Метод управления – однорукояточный
Включение передач - на всех блоках муфтами
Механизм переключения - однорукояточный с расходящимися дисками
Привод передач - от собственного электродвигателя; применить в коробке и вычертить на чертеже преобразователь
Положение включения - на минимальную частоту вращения.
На станках токарной группы обрабатывают детали типа валов дисков и втулок осуществляя обтачивание наружных цилиндрических поверхностей торцов и уступов прорезание канавок и отрезку растачивание отверстий (цилиндрических конических и фасонных) обтачивание конических и фасонных поверхностей сверление зенкерование и развертывание отверстий нарезание наружной и внутренней резьбы резцом метчиком и плашкой вихревое нарезание резьбы накатывание рифленых поверхностей.
Главным движением определяющим скорость резания является вращение шпинделя несущего заготовку. Оно осуществляется через 18-тиступенчатую коробку скоростей (проектируемый узел). При проектировании будем стремиться разработать конструкцию с максимально возможной точностью передаточных отношений и минимальными габаритами узла применением по возможности наиболее дешёвых материалов обеспечении ремонтоспособности и надёжности работы простоты конструкции и эксплуатации.
ОПРЕДЕЛЕНИЕ ИСХОДНЫХ ДАННЫХ ДЛЯ ПРОЕКТИРОВАНИЯ
Станок предназначен для точения цилиндрических поверхностей с максимальным диаметром Dmax=360 мм. В целях экономичного использования станка примем среднее расчетное значение Dmin = 90 мм исходя из неравенства (стр.106 [1]).
При определении предельных скоростей резания предпочтительно принимать для чистовых работ - для черновых работ соответственно при минимальной подаче и глубине резания (чистовая обработка) и максимальных подаче и глубине резания (черновая обработка).
В качестве материала при наибольшей скорости резания принимаем серый чугун СЧ20 (НВ190) материал режущей части резца – твёрдый сплав ВК6 как наиболее прогрессивный в настоящее время материал по сравнению с быстрорежущей сталью.
1Обработка чугуна (черновая операция)
Инструмент: резец проходной упорный прямой с пластинами из твердого сплава с углом в плане 90º (стр.120 табл.7 [2]) ГОСТ 18879-73:
Принимаем минимальную глубину резания t=2 мм (стр.84 [1]).
Подача (стр.266 табл.11[2]) S=15 ммоб
Скорость резания (стр.265 [2]):
где по табл. 17 стр. 269 [2]:
Стойкость резца принимаем Т=60 мин (стр.268 [2]).
Коэффициент (стр. 268 [2])
где nv=1 (стр.262 табл.2 [2]) HB=190
=08 – табл.5 стр.263 [2] – поковка;
=1 – табл.6 стр.263 [2] – для ВК6;
Частота вращения шпинделя:
2 Обработка чугуна (чистовая операция)
Принимаем минимальную глубину резания t=05 мм (стр.84 [1]).
Подача (стр.266 табл.11[2]) S=02 ммоб.
Стойкость резца принимаем Т=40 мин (стр.268 [2]).
=1 – табл.5 стр.263 [2] – обработка поверхности без корки;
3Обработка стали (черновая операция)
Подача (стр.266 табл.11[2]) S=13 ммоб
4Обработка стали (чистовая операция)
Принимаем минимальную глубину резания t=05 мм (стр.93 [1]).
Подача (стр.266 табл.11[2]) S=08 ммоб.
где по табл. 17 стр. 269 [2]: =324; у=04; m=028.
Определение мощности электродвигателя.
Мощности двигателя кВт определяется по формуле:
где - эффективная мощность кВт;
- коэффициент перегрузки электродвигателя; ;
- КПД привода главного движения; .
Привод главного движения и привод подач обслуживает один двигатель.
Nэд = Nэд(гл) + Nэд(под);
Nэд(под) = (003 005) · Nэд(гл)
Nэд(под) = 003 · 43 = 0129 кВт.
Nэд =0129 + 458 = 471 кВт.
Принимаем за исходный параметр минимальное значение подачи Smin =30мммин.
Тогда максимальное значение подачи:
Из геометрического ряда предпочтительных чисел[1 с. 180] принимаем стандартные значения SmSmax=224мммин
Т. о. исходные данные для проектирования:
= 112;z = 18; dmaSmSmax=224мммин.
КИНЕМАТИЧЕСКИЙ РАСЧЕТ
1 Построение структурной сетки
Определяем требуемые величины подач и принимаем их стандартные значения из ряда предпочтительных чисел для φ = 112 (стр.280[1]): S1=315мммин;S2=355мммин;S3=40мммин;S4=45мммин;S5=50мммин;S6=56мммин;S7=63мммин;S8=71мммин;S9=80мммин;S10=90мммин;S11=100мммин;S12=112мммин;S13=125мммин;S14=140мммин;S15=160мммин;S16=180мммин; S17=200мммин;S18=224мммин.
По заданной структурной формуле z = 36-23-31 строим структурную сетку (рисунок 1) (стр.100 [4]).
Рисунок 2.1 – Структурная сетка
Из структурной сетки получаем следующие отношения для передаточных чисел:
i1 : i2 : i3 = φ6 = 1126 = 19738 i4 : i5 = φ3 = 14049 i6 : i7 : i8 = φ1 = 112
2 Построение графика чисел оборотов
Выбор i должен производиться так чтобы его значения не выходили за допускаемые пределы (для исключения больших размеров зубчатых колес) стр.101[3]:
В соответствии с полученными передаточными отношениями строим график чисел оборотов (рисунок 2).
Рисунок 2.2 — График чисел оборотов
Для кинематической цепи с реечной передачей уравнение кинематического баланса имеет вид (стр.15 [7]):
где nдв – частота вращения электродвигателя (принимаем электродвигатель с частотой вращения nдв=700 мин-1);
i – передаточное отношение расчетной кинематической цепи.
iп – передаточное отношение коробки подач (механизма настройки).
Преобразовав выражение (4) применительно к нашему варианту получим:
Приняв по графику чисел подач (рисунок 2)S18 = 224мммин что соответствует передаточному отношению коробки подач iн = выразим из выражения (5) неизвестное передаточное отношение постоянных передач[7 с. 77]:
По данному передаточному отношению необходимо подобрать соответственно колеса.
3 Определение числа зубьев зубчатых колес
Числа зубьев определяем по таблице 3 стр.121[4]. При этом находим Σz такую чтобы для каждой передачи zmin ≥ 18 межосевое расстояние должно быть одинаковым для всех передач одной группы т. е. сумма зубьев сцепляющихся пар должна быть одинаковой модули для пар одной группы тоже одинаковы. Данные в таблице 2.1.
Таблица 2.1 – Определение чисел зубьев.
4 Определение действительных значений подач
Определяем действительные значения подач с учетом конкретных чисел зубьев колес и сравниваем их со стандартными значениями.
Действительное значение частота вращения может откланяться от стандартного не более чем на ±10( - 1)%. Кроме того в приводе от асинхронного электродвигателя допускается смещение ряда в сторону уменьшения до 5% от чисел ряда подсчитанных по синхронной частоте [6 c.340].
Расчет ведем по формуле:
Результаты расчета сводим в таблицу 2.
Таблица 2 - Расчет действительных значений подач
Относительная погрешность не превышает допускаемое значение 12%. Считаем результат приемлемым т.к. станок не предназначен для автоматической обработки резьбы т. е. не требуется точное согласование движения подачи и главного движения.
СИЛОВОЙ РАСЧЕТ КОРОБКИ ПОДАЧ
1 Расчет тягового усилия
Расчет ведем по наибольшему тяговому усилию необходимому для преодоления сил полезного сопротивления на основании которого определяем с учетом КПД моменты силы мощности приложенные к отдельным звеньям[6 с. 402].
Тяговая сила необходимая для преодоления сил полезного сопротивления [5 с. 402]:
где - составляющая сила резания действующая в направлении подачи
- коэффициент учитывающий влияние опрокидывающего момента возникающего вследствие несимметричного положения силы подачи kn = 115 [5 с. 402 табл. 27]
F – сила трения в направляющих [5 с. 402 табл. 27]:
f– приведенный коэффициент трения (f = 015) [5 с. 402 табл. 27]
Q – вес движущихся частей Н
2 Крутящий момент на валу конечного звена
Крутящий момент на валу конечного звена кинематической цепи воспринимающего тяговую силу (реечное колесо) определяется по формуле [5 с. 402]:
где Р – максимальное значение тяговой силы (Р = 204 кН);
Н – ход кинематической пары преобразующей вращательное движение в поступательное м.
Для реечной пары[5 с. 14]:
3 Мощность на конечном валу
Мощность на валу конечного звена (реечного колеса) определяем по формуле:
где n – число оборотов вала конечного звена в минуту.
где i – передаточное отношение кинематической цепи от шпинделя до реечной шестерни.
По кинематической цепи для ступени подачи S1:
4 Крутящий момент и мощность на выходном валу коробки подач
Крутящий момент и мощность определяем с учетом передаточного отношения червячного зацепления и цилиндрической передачи КПД реечного червячного и цилиндрического зацеплений подшипников.
где u – передаточное число цепи;
где р= ц= 096 – КПД реечной и цилиндрической передачи;
ч= 06 – КПД червячной передачи;
п= 0995 – КПД пары подшипников.
5 Мощность и крутящий момент на каждом валу коробки подач
Принимаем электродвигатель асинхронный закрытый обдуваемый типа 4А71В8У3 фланцевого исполнения со следующими параметрами Nдв=025 кВт nс=700мин -1.
Частота вращения каждого вала
Крутящий момент на каждом валу[5 с. 64]:
6 Расчет модулей зубчатых зацеплений
В коробках подач как правило модуль шестерен определяется из расчета на изгиб mизг [7 с. 81].Расчет ведем по формуле[7 с. 150]:
где пов и изг – допускаемые напряжения по усталости поверхностных слоев и на изгиб Нсм2: изг = 785 Нмм2 = 78500 Нсм2 (стр.194[6]);
N – номинальная передаваемая мощность рассчитываемой шестерни кВт;
n – минимальное число оборотов шестерни при котором передается полная мощность обмин;
у – коэффициент формы зуба (при z = 20 60 у = 0243 0268);
z – число зубьев шестерни;
К = Кд · Кк · Кр = 1 · 13 · 1 = 13 – коэффициент нагрузки который учитывает изменение по сравнению с номинальной от действия различных факторов.
Для валов I – II – колеса z1 и z2 с NI = 447 кВт nI = 730 обмин
Для валов II – III – колеса z7 и z8 с i = 385 NII = 443 кВт nII = 500 обмин:
Для валов III – IV – колеса z11 и z12 с i = 2.21 NIII = 439 кВт nIII = 180 обмин:
Для валов IV – V – колеса z17 и z18 с i = 1405 NIV = 435 кВт nIV = 112 обмин:
На всей цепи передач расчетное значение модуля получилось меньше или равно единице. Поэтому из конструктивных и технологических соображений принимаем для всех ступеней передач одинаковый модуль. Для обеспечения необходимой жесткости валов принимаем конструктивно значение модуля m = 2 мм.
Степень точности колес определяется в зависимости от назначения [6 с. 373]. Для силовых кинематических цепей (коробок скоростей подач) с линейной скоростью ≤10 мс применяются зубчатые колеса 7-й степени точности.
РАСЧЕТ ЭЛЕМЕНТОВ КОРОБКИ ПОДАЧ
1 Расчет геометрических параметров зубчатых колес
По формулам (стр.175[6] табл.3):
) делительный диаметр ;
) диаметр вершин зубьев ;
) диаметр впадин зубьев ;
) межосевое расстояние .
Данные заносим в таблицу 4.1.
Ширина венцов колес (стр.151[7]): 12 мм
Таблица 4.1 – Расчет параметров зубчатых колес
Выполняем предварительную эскизную компоновку коробки по рекомендациям на стр.189[8].
2 Предварительный расчет диаметров валов
Предварительный расчет диаметров валов проводим по (стр.273[6]).
Определяем диаметр вала из условия прочности на кручение при пониженных допускаемых напряжениях:
где Т – крутящий момент Н·мм;
[] – допускаемое условное напряжение при кручении.
[] = 10 15 Нмм2 – для промежуточных валов;
Полученные значения диаметров валов – приблизительные окончательно их значения определяем при прочерчивании развертки коробки подач (ГОСТ 6636-69). Но диаметры участков прочерченных валов не должны быть меньше рассчитанных выше значений.
3 Расчет промежуточного вала на прочность
Уточненный расчет выполняем для четвертого вала так как он является наиболее нагруженным на пятом валу наибольшее значение крутящего момента.
Определяем окружную силу в зацеплении по формуле:
Для 10-го зубчатого колеса:
Для 13-го зубчатого колеса:
Определяем радиальную силу:
где α – угол профиля зубьев α=200
Для -го зубчатого колеса:
Рассмотрим данную расчетную схему вала в двух плоскостях: горизонтальной и вертикальной в которых действуют радиальная и окружная силы.
Составим уравнение равновесия вала в вертикальной плоскости.
По найденным реакциям строим эпюру изгибающих моментов в вертикальной плоскости.
Составим уравнение равновесия в горизонтальной плоскости.
По найденным реакциям строим эпюру изгибающих моментов в горизонтальной плоскости.
Полная нагрузка на опоры вала
Суммарные изгибающие моменты :
Рисунок 4.1 – Схема нагружения и эпюры крутящих и изгибающих моментов рассчитываемого вала
Приведенный момент в опасном сечении вала:
Диаметр вала в опасном сечении[8 с 275]:
где[-1]- допускаемое напряжение
- масштабный фактор;
[s] – коэффициент безопасности: [s]=3;
KL- коэффициент долговечности: КL=1;
К - эффективный коэффициент концентрации напряжений;
- коэффициент учитывающий упрочнение поверхности.
Принимаем в качестве материала вала сталь 45 со следующими техническими характеристиками [8 с. 7 табл. 1.1]: В=700 Нмм2 Т=360 Нмм2 Т=324 Нмм2 -1=270 Нмм2 -1=160 Нмм2.
= 091; = 089 [8 с. 276 табл. 12.2]
К = 16; К=245 [8 с.279 табл. 12.6]
= 09 [8 с. 280 табл. 12.9]
Конструктивно был принят вал диаметром 20 мм прочность вала обеспечена.
Производим проверочный расчет вала. Коэффициент безопасности в опасном сечении:
где sи s- коэффициент безопасности соответственно по изгибу и по кручению.
где а и а – переменные составляющие циклов изменения напряжений.
Т.к. в расчетном сечении крутящий момент передается кулачковой сцепной муфтой то расчет вала ведем только по изгибным напряжениям.
Для реверсивных валов:
Момент сопротивления вала W и полярный момент сопротивления Wопределяем по формулам[8 с. 281]:
Безопасность работы вала обеспечена.
3Выбор элементов передающих крутящий момент
Шлицевые соединения по сравнению со шпоночными обладают более высокой нагрузочной способностью создают меньшую концентрацию напряжений в валах а следовательно обеспечивают более высокую выносливость последних создают лучшую центровку деталей на валах более удобны для массового и серийного производства.
Расчёт шлицевых соединений выполняется обычно как проверочный по напряжениям смятия:
Рисунок 4.2-Шлицевое соединение
φ- коэффициент что учитывает неравномерное распределение нагрузки между шлицами ( обычно принимают 075);
D d z – размеры разреза соединения (внешний внутренний диаметр и количество шлицёв);
f – размер фаски по длине шлица мм;
- рабочая часть шлица мм;
- напряжения смятия что допускаются. Определяются в зависимости от условий эксплуатации принимаем = 40 МПа
Также в коробке подач присутствуют шпоночные соединения которые необходимо проверить на смятие. Расчет проводится по формуле:
Рисунок 4.3- Шпоночное соединение
гдеМкр –крутящий момент на валу Нм;
d – диаметр вала = 20 мм;
h – высота шпонки = 5мм;
[см] – допускаемые напряжения смятия для материала шпонки 45.
Рабочая длина шпонки определяется по формуле:
Подставляем в формулу получаем:
Условие выполняется.
5 Проверочный расчет подшипников
Предварительно принимаем для всех валов радиальные подшипники 203 ГОСТ 8338-75 со следующими параметрами:d = 17мм D = 40мм B = 12 мм допускаемая динамическая грузоподъемность С = 9560 Н.
Эквивалентная нагрузка[8 с. 347]:
где V = 1 - коэффициент вращения;
Fr – радиальная нагрузка;
k = 12 – коэффициент безопасности;
kт = 1 – температурный коэффициент.
Необходимая долговечность подшипников в млн. оборотов при долговечности в часах Lh = 5000 часов и частоте вращения вала n=336 мин -1:
Требуемая динамическая грузоподъемность:
Расчет ведем по наиболее нагруженной опоре.
Р= 190612 1 = 1087 Н
Значение требуемой динамической грузоподъемности не превышает допускаемого значения. Следовательно подшипники работоспособны.
РАСЧЕТ УСИЛИЙ НА РУКОЯТКАХ МЕХАНИЗМА УПРАВЛЕНИЯ
Составляем расчетную схему см. рисунок 5.1.
Рисунок 5.1 – Расчетная схема
Определяем массы подвижных частей механизма переключения.
Массу блоков зубчатых колёс вилок дисков определяем по методике изложенной в литературе [9] разбивая их на элементарные фигуры.
Массы блоков зубчатых колёс: m1m2 m3 = 0.8кг.
Массы вилок: mв2= 1.41 кг mв2= 0.92 кг mв3= 1.02 кг.
Масса дисков: mд= 4.52 кг
Сила трения возникающая при перемещении блоков:
где Мб – суммарная масса блоков Н
f – коэффициент трения (f=0.1)
шл – КПД шлицев (шл =0.95)
Сила трения возникающая при перемещении вилок:
где Мв – суммарная масса вилок Н
Fв=(1.41+0.92+1.02)100.1=3.35 Н
Сила трения возникающая при перемещении дисков:
где Мд– суммарная масса дисков Н
Усилие пружины необходимое для возврата дисков в исходное положение:
Сила трения возникающая при входе зубьев в зацепление:
Fз= Fбf = 2.530.1= 0.25Н
Усилие которое необходимое преодолеть при снятии вилок с фиксаторов (рисунок 7):
Fф=n(Fтр1+ Fтр2)cos45
где n – число одновременно работающих фиксаторов (n = 3)
Рисунок 7 – Расчетная схема
Fтр1 = Fтр2 = (Fпрcos 45)f;
где Fпр – рабочее усилие пружины (принимаем Fпр = 20Н)
Fтр1 = Fтр2 = (20cos45) 0.1 = 1.42 H
Fф = 3 (1.42 + 1.42) cos45 = 6.02 Н
Все силы приводим к рычагу перемещающему диски:
F = Fз + Fбл +Fв + Fф + Fд + Fпр =0.25+2.51+3.35+6.02+4.76+47.58=64.5Н
Уравнение моментов относительно оси поворота рычага
L – длина рукоятки мм;
Fp – усилие на рукоятке Н ( Fp = 40H)
Принимаем L= 250мм .
ОПИСАНИЕ КОНСТРУКЦИИ КОРОБКИ СКОРОСТЕЙ
Механизм коробки подач расположен в корпусе отлитом из серого чугуна марки СЧ20. Коробка состоит из 4-х валов на которых насажены зубчатые колёса и блоки шестерён осуществляющие передачу движения с входного вала на выходной IV. Все валы установлены на радиальных шарикоподшипниках (осевая нагрузка отсутствует). Для увеличения жёсткости валов опоры максимально сближены. Для передачи необходимых крутящих моментов зубчатые блоки колёс установлены на валы с использованием шлицевых соединений неподвижные зубчатые колеса установлены как на шлицевых валах так и с использованием шпонок (где нецелесообразно применение шлицев как наиболее трудоемких при изготовлении). Движения на валы передаются при помощи электромагнитных муфт на ходовой винт движение передается при помощи кулачковой муфты. Неподвижные колеса застопорены от осевого смещения пружинными стопорными шайбами.
Зубчатые колёса изготовлены из стали 45 с термообработкой - нормализация НВ = 170.
Управление переключением скоростей осуществляется механизмом с предварительным набором величины частоты вращения позволяющим подготовить следующее включение частоты вращения (не нарушая предыдущей) и в нужный момент с помощью рукоятки быстро производить переключение. Предварительный выбор величины частоты вращения производится поворотом лимба. Лимб при помощи конической передачи поворачивает сдвоенные диски. Рукоятка при помощи зубчатых секторов и рычагов сдвигает диски которые через штыри передвигают ползуны с вилками входящими в пазы передвижных блоков шестерен.
Фиксация блоков осуществляется с помощью подпружиненных шариков.
Смазка к шестерням и подшипникам подаётся насосом по трубкам (в коробке не показаны).
АНАЛИЗ ТЕХНИКО-ЭКОНОМИЧЕСКОЙ ЭФФЕКТИВНОСТИ
Разработанная коробка подач отвечает следующим показателям эффективности:
- применена бочкообразная форма закругления зуба что приводит к выравниванию эпюр удельных нагрузок повышает долговечность передачи;
- количество деталей сведено к минимуму что повышает надёжность коробки;
- уменьшение потерь вспомогательного времени на приемы управления станком (переключение подач) по сравнению с барабанными и многорукояточными механизмами переключения;
- органы управления расположены с максимальным удобством для рабочего их конструкция проста и надёжна.
СПИСОК ИСПОЛЬЗОВАННЫХ ИСТОЧНИКОВ
Тарзиманов Г. А. Проектирование металлорежущих станков М. Машиностроение 1972.
Справочник технолога-машиностроителя т.2 под ред. Косиловой А. Г. М. Машиностроение 1986.
Кузьмин А. В. и др. Курсовое проектирование деталей машин ч.1 Мн.: Выш. школа1982.
Проников А. С. Расчет и конструирование металлорежущих станков М. Высшая школа 1962.
Колев Н. С. и др. Металлорежущие станки М. Машиностроение 1980.
Детали машин в примерах и задачах под ред. Ничипорчика С. Н. Мн.: Выш. школа 1981.
Проников А. С. и конструирование металлорежущих станков М. Высшая школа 1967.
Атлас конструкций деталей машин под ред. Решетова Д. Н. М. Машиностроение 1979.
Чернин М. М. Расчеты деталей машин Мн.: Выш. школа 1974.
Металлорежущие станки под ред. Пуша В. Э. М. Машиностроение 1985.
Кочергин А. И. Конструирование и расчет металлорежущих станков и станочных комплексов. Курсовое проектирование Мн.: Выш. школа 1991.
Детали и механизмы металлорежущих станков т.2 под ред. Решетова Д. Н. М. Машиностроение 1972.
Перель Л. Я. Подшипники качения. Справочник М. Машиностроение 1983.
Поливанов П. М. Таблицы для подсчета массы деталей и материалов М. Машиностроение 1980.
Спецификация 2.cdw

Спецификация 1.cdw

Чертеж.cdw

После сборки обкатать в течении 6 часов
Заедания при работе и преключении передач не добускается.
Осевая игра валов: выходного - 0
Регулировать осевую игру валов набором прокладок.
Спецификацмя3.cdw

Свётрка.cdw

78 Мех. упр yjdsq.cdw

78.3 ОВ.cdw

Рекомендуемые чертежи
- 29.05.2022