Привод главного движения токарно-винторезного ЧПУ станка



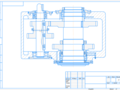
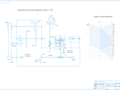
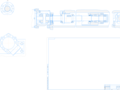
- Добавлен: 25.01.2023
- Размер: 458 KB
- Закачек: 0
Описание
Состав проекта
![]() |
![]() |
![]() ![]() ![]() |
![]() ![]() ![]() ![]() |
![]() ![]() ![]() ![]() |
![]() ![]() ![]() ![]() |
Дополнительная информация
записка Исправленная.doc
1. Предварительный расчет мощности привода 7
2. Проектирование привода подач ..8
Кинематический расчет станка ..8
1. Построение кинематической схемы привода. 8
2. Уточненный расчет мощности привода. ..11
3. Определение мощности на валах . .12
4. Определение передаваемых крутящих моментов 12
Динамические и прочностные расчеты узлов разрабатываемых конструктивно 12
1. Расчет клиноременной передачи ..12
2. Расчет цилиндрических прямозубых передач между валами 14
3. Расчет вала I на прочность. 20
3.1. Расчет и подбор шпоночных соединений .24
4. Расчет вала II на прочность. ..27
4.1. Расчет и подбор шпоночных соединений 33
5. Выбор подшипников по динамической грузоподъемности 33
5.1. Вал I коробки скоростей .33
5.2. Вал II коробки скоростей .. .34
6. Расчет вала шпинделя на жесткость .35
Выбор вида смазывания передач и подшипников .38
Система управления станка ..39
Описание проектируемых узлов ..40
В развитии технологии обработки металлов резанием происходят принципиальные изменения. Интенсификация технологических процессов на основе применения новых конструкций режущих инструментов режущих инструментов из новых инструментальных материалов повышение размерной и геометрической точности достигаемой при обработке таков неполный перечень важнейших направлений развития механической обработки в машиностроении.
Эффективность производства его технический прогресс качество выпускаемой продукции во многом зависит от опережающего развития производства нового оборудования машин станков аппаратов от всемерного внедрения методов технико-экономического анализа. Существующий парк станков насчитывающий в настоящее время около четырех тысяч различных моделей не удовлетворяет все расширяющиеся запросы потребителей. Следовательно в будущем типаж станков будет все время увеличиваться и обновляться. В типаже станков кроме количественных происходят и качественные изменения. В современных станках широко используются как механические так и электрические гидравлические пневматические и другие устройства что приводит к усложнению их конструкции.
Первоначальной базой той или иной конструкции станка является кинематическая структура станка выражаемая кинематической схемой так как назначением станка является создание относительных движений режущего инструмента и заготовки необходимых для получения в процессе резания заданных поверхностей. Следовательно и при конструировании и при эксплуатации нужно прежде всего знать кинематическую структуру станка.
Развитие производственного оборудования предполагает решение вопросов выбора и оптимизации технических характеристик станка проектирования кинематической схемы станка и его узлов обоснование выбранных конструктивных вариантов. Данный проект направлен на решение таких задач.
Определение технических характеристик станка
Предельные расчетные диаметры Dmax и Dmin для токарных станков.
где D- максимальный диаметр обработки над станиной.
где H-высота центров над станиной.
Предельные числа оборотов шпинделя nmax и nmin
Наибольшая скорость резания соответствует чистовой обработке найболее легко обрабатываемого материала найболее теплостойким инструментом.
Согласно задания это будет тонкое точение цветных сплавов твердосплавным инструментом.
Согласно табл.19 стр.271[2] Режимы резания при тонком точении и растачивании
Материал рабочей части реж. инстр.
Параметр шереховатости поверхности Raмкм
Аллюминевые сплавы и бабит
Берем максимальное значение скорости
Наименьшая скорость резания соответствует черновой обработке найболее труднообрабатываемого материала. Согласно заданию это будет наружное продольное точение стали.
Т-среднее значение стойкости инструмента при одноинструментальной обработке.
Т=30-60 мин (стр.268 [2])
Согласно табл. 17 стр.269 значения коэффициентов Сv и показателей степени в формулах скорости резания при обработке резцами следующие:
Cv=340 x=0.15 y=0.45 m=0.2 S=0.7 Материал режущей части резца Т15К6 (без охлаждения) в=750 МПа.
Коэффициент Kv представляет собой:
где Knv – коэффициент учитывающий состояние поверхности Knv=05-0.6 [5 стр.263 табл. 5];
Kиv – коэффициент учитывающий материал инструмента Kиv=1 [5 стр.263 табл. 6];
Kмv – коэффициент учитывающий влияние материала заготовки:
где nv=1 [5 стр. 262 табл. 2];
Тогда коэффициент Kv примет значение:
Тогда минимальная скорость резания по формуле:
Частоту вращения шпинделя определим по формуле:
Диапазон регулирования чисел оборотов.
Выбираем привод главного движения с бесступенчатым регулированием скорости.
nд max=2000 мин-1 nд min=250 мин-1
Rn=Rб*Rc где Rб - диапазон изменения частоты вращения устройства с бесступенчатым изменением скорости; Rc – диапазон регулирования шестеренчатой коробки.
Количество групп передач m и число ступеней z такой коробки определяют по формулам:
Такая коробка изменяет частоту вращения шпинделя по геометрическому ряду со знаменателем
Для выбора промежуточных частот вращения шпинделя пользуемся отраслевым стандартом ОСТ 2 Н11-1-72 «Предпочтительные числа и ряды
предпочтительных чисел» (приложение 1 стр.272 [3]).
1. Предварительный расчет мощности привода.
Максимальное значение силы резания будет соответствовать черновой обработке конструкционной углеродистой стали.
Pz=10·Cp tx ·Sy ·Vn ·Kp стр. 271 [2].
Согласно табл.22 стр. 273 [2]. Значения коэффициента Cp и показателей степени в формулах силы резания при точении.
Cp=300 S=0.8-1.3; t=3
Поправочный коэффициент Kр представляет собой:
- коэффициент учитывающий влияние качества обрабатываемого материала на силовые зависимости [5 стр.264 табл. 9];
- поправочные коэффициенты учитывающие влияние геометрических параметров режущей части инструмента на составляющие силы резания [5 стр.275 табл. 23];
Тогда поправочный коэффициент примет численное значение:
Тогда сила резания примет численное значение:
где - КПД кинематической цепи;
=0.7-0.85 – для станков с вращательным главным движениям (стр.10[4])
2. Проектирование привода подач.
Минимальная подача соответствует чистовой обработке алюминиевых сплавов. согл. табл. 19 т2[2].
Максимальная подача – черновой обработке стали согл. табл.11 т2[2].
Привод подач берем аналогичным приводу подач токарного станка 16К20Т1. Пределы рабочих подач (бесступенчатое регулирование): продольных 001-28 ммоб поперечных 0005-14 ммоб скорость быстрых ходов:
продольных 6000 мммин поперечных 5000 мммин.
Кинематический расчет станка
1. Построение кинематической схемы привода.
Для составления кинематической схемы привода необходимо дополнить групповые передачи одиночными и соединить коробку с двигателем. Одиночные передачи используются в приводе с целью обеспечения требуемой редукции частоты вращения двигателя и получения стандартных значений частоты вращения шпинделя для передачи движения от коробки к шпинделю. В качестве одиночных передач в приводе главного движения необходимо использовать:
ременную передачу для получения частоты из стандартного ряда на входе коробки скоростей.
цилиндрические передачи для понижения частоты вращения.
Для определения передаточных отношений передач привода необходимо в соответствии со структурной формулой построить структурную сетку
Рис. 2.1. Структурная сетка
Затем строится график частот вращения (см. рис. 2.2).
Рис.2.2. График частот вращения.
По этому графику определяются передаточные отношения всех передач и проставляем их на графике.
Передаточные отношения всех передач.
Определяем числа зубьев прямозубых колес.
Определяем найменьшее кратное К суммы для чего используем передаточные отношения выраженные в виде простых дробей.
Проверка: 26+65=35+56=91
Рис. 2.3 Схема коробки скоростей
2. Уточненный расчет мощности привода.
- КПД пары подшипников качения;
- КПД клиноременной передачи;
- КПД пары прямозубых цилиндрических колес;
Мощность электродвигателя.
По табл. 3.3. с.32 принимаем регулируемый электродвигатель постоянного тока типа 4ПФ112L с номинальной мощностью: Nдв=75 кВт. Частотой вращения nдв=2000 мин-1
3. Определение мощности на валах.
4. Определение передаваемых крутящих моментов на валах.
Динамические и прочностные расчеты узлов разработанных конструктивно
1. Расчет клиноременной передачи.
Для рассчитываемой передачи примем клиновые ремни нормального сечения. Принимаем сечение Б.
Диаметр меньшего шкива возьмем (табл.11.1[1]) d1=160 мм диаметр большего шкива при относительном скольжении =0.02 определим по формуле
Расстояние между центрами шкивов по формуле (при U=16 C=1.2)
amin=Cd2=1.2250=300 мм
amax=2(d1+d2)=2(160+250)=820 мм
Длина ремня определится по формуле
Принимаем стандартную длину ремня для сечения Б Lр=1600 мм
Угол обхвата ремнем меньшего шкива по формуле
Скорость ремня по формуле
Число z ремней определим по тяговой способности. Мощность которую можно передать одним ремнем при v=10464 мс и умеренных колебаниях нагрузки P0 =75 кВт (табл. 11.5[1]).
Коэффициент динамической нагрузки kд=1.1(табл. 11.2 [1])
Коэффициент учитывающий влияние угла обхвата kα=1(табл. 11.4 [1])
Коэффициент учитывающий длину ремня kl=0.97.(ll0= 2185.752240=0.97)
Коэффициент учитывающий неравномерность распределения нагрузки по ремням kz=0.95(стр. 142[1])
Принимаем z=3.Проверим ремни на долговечность по частоте пробегов в секунду.
Что вполне допустимо (стр.142 [1])
Определяем размеры шкивов приняв что они изготовлены из чугуна СЧ18-36
Lр=14 мм ; b=4.2мм ; h=12 ; e=19 ; f=12.5 ; r=1 ;
Для ведущего шкива:; b1=17мм
Для ведомого шкива: ; b1=17.4 мм
ширина ободов шкивов мм
2. Расчет цилиндрических прямозубых передач между валами.
Согласно табл. 3.2.стр.83 [5]. Рекомендуем сочетания материалов применяемых для изготовления зубчатых колес и шестерней.
Рекомендуем. Способ термооб.
Рекомендуем. Способ термооб
Улучшен. или нормализ-я НВ350
Согласно табл. 6.14. стр.153 ч1 [6] механические свойства стали для зубчатых колес. Таблица 3.3.
Допускаемые напряжения:
Согласно табл. 6.15. ч1.стр.154[6] предел контактной выносливости
Дальнейший расчет ведем по меньшему значению т.е. для колес.
Допускаемое напряжение ((6.32.)ч1.[6]
SH-коэффициент безопасности SH=11
КHL- коэффициент долговечности КHL=1
Согласно табл. 6.16.ч1.стр.154[6] предел изгибной выносливости зубьев:
Допускаемое напряжение (стр.134 ч.1 [6]):
KFL- коэффициент долговечности KFL=1
KFC- коэффициент учитывающий влияние двухстороннего приложения нагрузки; KFC=1у
SF- коэффициент безопасности; SF=17-22
Межосевое расстояние:
Ка=495 Согласно табл. 6.8. ч.1[6] рекомендуемые значения
Расположение колес относительно опор
Твердость рассматриваемых поверхностей зубьев НВ 300 350
12 или (02 025)·(u+1)
KHB=1.01 в зависимости от по графику (рис.6.11.ч.1[6] )
для коробок скоростей
Для более нагруженной пары в передачах между валами 1 и 2
Основные размеры колес.
По СТ СЭВ 310-76 принимаем m=3 мм. Уточняем межосевое расстояние
Модуль и межосевое расстояние
Определяемые размеры и расчетные формулы
Делительный диаметр мм
Диаметр основной окружности мм
Ширина венцов колес для наиболее нагруженной пары мм
Проверка на выносливость по контактным напряжениям.
Степень точности передачи по нормам плавности (табл. 6.7 [6])
Углы профилей зубьев в точке на окружности вершин (п.20. табл. 6.1 ч1 [6])
Коэффициент торцового биения перекрытия (п.25 табл.6.1 ч1[6])
Аналогично для пары -:
Коэффициент учитывающий суммарную длину контактных линий:
Удельная окружная динамическая сила ((6.10.) ч1 [5])
(табл. 6.10 ч1. [6])
(табл. 6.11 ч1. [6])
Коэффициент учитывающий динамическую нагрузку возникающую в зацеплении ((6.9) ч1[6]):
Удельная расчетная окружная сила ((6.8) ч1[6]):
Расчетные контактные напряжения ((6.7) ч1[6]):
где zM=275 и zH=1.77 (стр. 109 ч1[6]):
т.о. условие прочности выполняется.
Проверка зубьев на выносливость по напряжениям от изгиба.
Коэффициент ширины колеса по модулю (табл. 6.9 ч1[6]) для ступеней
Коэффициент учитывающий форму зуба YF согласно табл. рис. 6.14 ч1 [6] при Х=0
Определяем отношения при для колеса и МПа для шестерни.
т.о. в передаче - расчеты будем вести по шестерне аналогично в передаче - также по шестерне.
Коэффициент учитывающий неравномерность распределения нагрузки по ширине венца принимается по рис. 6.11 ч1[6]
Коэффициент среднего изменения суммарной длины контактных линий
Коэффициент учитывающий перекрытия зубьев (стр. 113 ч1 [6])
Удельная окружная динамическая сила ((6.18) ч1. стр.115 [6])
(табл. 6.18 ч1. [6])
Коэффициент учитывающий динамическую нагрузку ((6.18) ч1. [6])
Удельная расчетная окружная сила ((6.15) ч1. [6])
Напряжения от изгиба для менее прочных шестерней ((6.13) ч1. [6])
т.о. прочность зубьев на изгиб обеспечивается.
3. Расчет вала I на прочность.
Определяем силы действующие на вал:
напряжение от предварительного натяжения (1.2-1.5МПа).
Прямозубая цилиндрическая передача.
Определяем расстояние между опорами.
Рис.3.3. Расчетная схема.
Принимаем: x=10мм LСТ=20мм W=30мм f=70мм.(стр.50[3])
Рис.3.4. Схема нагружений.
Вертикальная плоскость.
; Fr135-Rby(35+110) - Q70 =0
Rby= (Fr135 -Q70 )(35+110)=-3858 Н
; Ray + Fr1 -Rby + Q = 0 ;
Ray=-Q - Fr1-Rby = =-993-3875-386 =-17663Н
Рис.3.5. Эпюра изгибающих моментов вертикальной плоскости.
Горизонтальная плоскость.
Rbx= (105435)145=2544 Н
Rax=Ft1 - Rbx = 1054-2544 = 799.6 Н
Рис.3.6. Эпюра изгибающих моментов горизонтальной плоскости.
Результирующая эпюра изгибающих моментов.
Рис.3.7. Результирующая эпюра изгибающих моментов.
Эпюра эквивалентных моментов.
Рис.3.8. Эпюра эквивалентных моментов.
Определения диаметров вала в опасных сечениях.
( маcштабный фактор учитывающий понижение прочности детали)
(коэффициент учитывающий упрочнение поверхности)
(эффективный коэффициент концентрации напряжений)
Сечение 2 (посадка подшипников) -
Сечение 13 (шпоночная канавка) -
Принимаем коэффициент безопасности
Выполняем вал из стали 45
Тогда диаметры в опасных сечениях:
В опасном сечении 1 (под шкив) принимаем стандартный диаметр .
В опасном сечении 2 (под подшипник) принимаем стандартный диаметр
В опасном сечении 3 с учетом переходов принимаем
Проверка прочности вала:
На кратковременную перегрузку по крутящему моменту.
Сечение 2(под подшипник)
На усталостную прочность.
Т.к S>4 то дальнейшие расчеты вала на прочность не ведутся. Вал вполне прочный.
3.1. Подбор и расчет шпоночных соединений.
Расчет шпоночного соединения “шкив-вал”.
Размеры сечения шпонки (стр.78[3]): .
Рабочая длина шпонки:
Принимаем шпонку со скругленными торцами тогда длина шпонки определится:
Принимаем стандартную длину шпонки L=30мм
Расчет шпоночного соединения “зубчатое колесо-вал”.
Для осевого перемещения зубчатого колеса применяем призматическую направляющую шпонку с креплением на валу(ГОСТ 8790-68)
Принимаем стандартную длину шпонки L=70мм
4. Расчет вала II на прочность.
Рис.3.4. Расчетная схема.
Рис.3.5. Схема нагружения.
; -Fr135+Rby(35+110) - Ррез215 =0
Rby= (Fr135 + Ррез215 )(35+110)=77561 Н
; Ray - Fr1 +Rby - Ррез = 0 ;
Ray= Ррез+ Fr1-Rby = 491129+1963-77561 =-264851Н
Рис.3.6. Эпюра изгибающих моментов вертикальной плоскости.
; -Ft135 - Rbx145 =0
Rbx= (53435)145=-12889 Н
Rax=-Ft1 - Rbx = 12889-534 = 40511 Н
Рис.3.7. Эпюра изгибающих моментов горизонтальной плоскости
Рис.3.8. Результирующая эпюра изгибающих моментов
Рис.3.9. Эпюра эквивалентных моментов.
4.1. Подбор и расчет шпоночных соединений.
Для осевого перемещения зубчатого колеса применяем призматическую направляющую шпонку (ГОСТ 8790-68)
Принимаем стандартную длину шпонки L=35мм
5. Выбор подшипников по динамической грузоподъемности
5.1. Вал I коробки скоростей.
Расчет производим по более нагруженной опоре.
Радиальная нагрузка на подшипник будет равна:
Т.к радиальная нагрузка довольно не большая и значительная осевая нагрузка отсутствует то применяем для вала 1 шариковый радиальный однорядный подшипник. Он предназначен для радиальной нагрузки но может воспринимать и осевую нагрузку в пределах 70% от неиспользованной радиальной. Обеспечивает осевое фиксирование вала в двух направлениях. При одинаковых габаритных размерах работает с меньшими потерями на трение и при большей угловой скорости вала чем подшипники всех других типов.
Эквивалентная нагрузка P определится:
m=1.5(коэффициент приведения осевой нагрузки к радиальной )
Kk=1.0(вращение внутреннего кольца)
(Умеренные толчки кратковременные перегрузки до 150%).
(температурный коэффициент)
Определяем требуемую долговечность подшипника в млн. оборотов.
Принимаем долговечность подшипника Lh=10000 часов
Определяем требуемую динамическую грузоподъемность.
Принимаем подшипник средней серии
Выбираем посадки: внутреннее кольцо вал – 30 н5; внешнее кольцо корпус- 55 H5.
5.2. Вал II коробки скоростей.
Т.к радиальная нагрузка довольно большая то предусматриваем для данного вала роликовый конический двухрядный подшипник.
X=0.4 (коэффициет радиальной нагрузки)
Y=0.4ctg(α)=0.4ctg(16)=1.61(коэффициент осевой нагрузки)
V=1(при вращении внутреннего кольца).
(коэффициент безопасности).
Принимаем подшипник легкой серии
Выбираем посадки: внутреннее кольцо вал – 72 внешнее кольцо корпус- 100 H5
6. Расчет вала шпинделя на жесткость
Расчет на жесткость сводится к определению прогибов у углов наклона оси вала и к сопоставлению их с допускаемыми. Допускаемый прогиб вала не должен превышать 00001—00006 расстояния между опорами или под зубчатыми колесами 001—003 модуля в см. Углы наклона оси вала в опарах не должны превышать 0001 радиана при зубчатых колесах; то же в радианах не более: 00025 — для цилиндрических роликоподшипников; 00016 — для конических роликоподшипников; 0005 — для однорядных шарикоподшипников; 005 — для сферических подшипников.
Угол наклона оси вала и прогиб вала у в расчетной сечения для двух основных схем нагружения определяют по формулам
где в рад.; d и у в см; Q в Н; и — коэффициенты учитывающие связь между точкой приложения силы и точкой в которой определяют деформацию; коэффициенты берут по графикам (рис. 4—7 [6 т2]).
Действительные деформации вала (согласно принципу наложения деформаций) определяют алгебраическим суммированием деформаций от каждой силы.
Рис. 3.6. Схема нагружения.
Угол наклона оси вала будем рассчитывать в найболее нагруженной опоре В. Прогиб вала у- в сечении I-I.
Угол наклона оси вала в опоре В
согл. рис.4 стр. 16 т2 [8].
согл. рис.5 стр. 16 т2 [8].
[Q]=00016 (стр.16 т2 [9])
Т.о. угол наклона оси вала не превышает допустимое значение:
Это позволяет обеспечить жесткость вала шпинделя.
Расчет прогиба оси вала в сечении I-I.
согл. рис.6 стр. 16 т2 [8].
согл. рис.7 стр. 16 т2 [8].
[Y]=(001-003)*m – под зубчатыми калесами (стр.16 т2 [9])
Выбор вида смазывания передач и
Смазочной системой называют совокупность устройств для подачи смазочного материала к трущимся поверхностям и возврата его в резервуар. Систему смазывания жидким материалом выбирают исходя из требуемой быстроходности механизмов исходя из их расположения конструкции уплотнений. Для данной коробки скоростей лучше использовать циркуляционное смазывание т.к. оно обладает рядом преимуществ: используется один и тот же объем масла что уменьшает стоимость оборудования осуществляется подвод смазки ко всем трущимся поверхностям одновременно что обеспечит независимую смазку каждого узла. Данная система смазки использует струйную подачу смазочного материала к зубчатым передачам посредством трубок. Опоры валов смазываются маслом которое подается в подшипник по валам.
При выборе сорта масла особое внимание необходимо уделить вязкости. Для этого учитывается частота вращения деталей их конструкция и температура. Согласно вышеизложенному целесообразно применить масло марки И-30А ГОСТ 20799-75.
Исходя из того что параметр предельной быстроходности dn = 0.8*105 невысокий можно использовать в качестве уплотнений прорезиненные манжеты.
Система управления станка.
Станок оснащен различными устройствами числового программного управления. Контурное устройство ЧПУ Н221М обеспечивает движение формообразования изменение в цикле значений подачи и частот вращения шпинделя индексацию поворотного резцедержателя нарезание резьбы по программе. Число координат (всего одновременно управляемых) 22. Дискретность задания перемещений по оси Х (поперечных) 0.005 мм по оси Z (продольных) 0.01 мм. Программоноситель – восьмидорожковая перфолента под программы ISO.
Описание проектируемых узлов
Главное движение шпиндель получает от электродвигателя М1 (N=7.5 кВт n=2000 мин-1) через клиноременную передачу с диаметрами шкивов D=160 мм. и D=250 мм. автоматическую коробку скоростей. АКС обеспечивает две переключаемых в цикле частот вращения шпинделя за счет включения гидроцилиндра. Вал 2 имеет два значения частоты вращения благодаря переключению подвижного блока (соответственно работают передачи z=2665 или z=5635).
Описание производится для привода продольной подачи.
Чертеж которой представлен на чертеже КП КРС 02.00.00.000 КЗ. Привод продольной подачи состоит из регулируемого электродвигателя передачи винт-гайка качения с шагом 10 мм. Продольная подача регулируется в диапазоне 001 28 ммоб максимальная подача составляет 2000 мммни скорость быстрых перемещений – 600 мммни дискретность подачи – 001 мм. Левая опора ходового винта состоит из упорного шарикового подшипника (поз. 6) который фиксируется стопорным кольцом а регулировка производится подшлифовкой кольца (поз. 7). Правая опора ходового винта состоит из блока радиальных и упорных роликовых подшипников. Их регулировка осуществляется гайкой (поз. 10) Для защиты винта от загрязнения применяется войлочная втулка с резьбой на внутренней поверхности.
Описание коробки скоростей.
Чертеж которой представлен на чертеже КП КРС 02.01.00.000 СБ.
На первом валу коробки скоростей размещен блок зубчатых колес 78 посредством которого расширяется диапазон регулирования частоты вращения шпинделя. Первый вал установлен на два шариковых радиальных подшипников 41 и радиальный роликовый подшипник 42 которые фиксируются стопорными кольцами 28. Левая опора шпинделя состоит из радиального роликового подшипника 44 правая – из двух радиальный шариковых подшипников 45 и радиальный роликовый подшипник 43 регулировка которых производится гайками 2627.
Переключение скоростей осуществляется гидроцилиндром 1.
Ачеркан Н.С. Металлорежущие станки. Т1. М.- Машиностроение. 1965г.
Справочник технолога- машиностроителя. В 2-х т. Под ред. А.Г. Косиловой – 4-е изд. перераб. и доп. - М.: Машиностроение 1986 ил.
Тарзиманов Г.А. Проектирование металлорежущих станков. М. “Машиностроение” 1972 312 стр.
Общемашиностроительные нормативы расчета режимов резания.
Кузьмин А.В. Расчеты деталей машин: Справ. пособие. - 3-е изд. перераб. и доп. - Мн.: Выш. шк. 1986. - 400 с.: ил.
Данилов В.А. Методические указания к курсовому проекту. Новополоцк – 1987.
Анурьев В.И. “Справочник конструктора-машиностроителя”: В 3-х т.- 5-е изд. перераб. и доп.- М.: Машиностроение 1979 ил.
Кочергин А.И. Конструирование и расчет металлорежущих станков и станочных комплексов. Курсовое проектирование: Учеб. пособие для вузов. - Мн.: Выш. шк. 1991. - 382 с.: ил.
Детали машин в примерах и задачах Под ред. С.Н. Ничипорчика. - 2-е изд. - Мн.: Выш. школа 1981 – 432 с. ил.
каробка.cdw

Привод подачи стола.cdw

Кинематическая схема.cdw

Кинематическая схема
Кинематическая схема токарного станка с ЧПУ
График частот вращения
Рекомендуемые чертежи
- 10.02.2022
- 29.05.2022