Модернизация привода главного движения токарно-винторезного станка модели 165




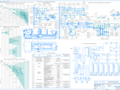
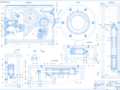
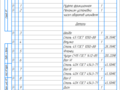
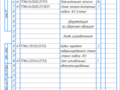
- Добавлен: 25.01.2023
- Размер: 2 MB
- Закачек: 2
Описание
Состав проекта
![]() |
![]() |
![]() ![]() ![]() |
![]() ![]() ![]() ![]() |
![]() ![]() ![]() ![]() |
![]() ![]() ![]() ![]() |
![]() ![]() ![]() ![]() |
![]() ![]() ![]() |
![]() ![]() ![]() |
![]() ![]() ![]() ![]() |
![]() ![]() ![]() |
![]() ![]() ![]() |
![]() ![]() ![]() ![]() |
![]() ![]() ![]() ![]() |
![]() ![]() ![]() |
Дополнительная информация
РЕФЕРАТ в рамке.doc
ТОКАРНЫЙ СТАНОК КОРОБКА СКОРОСТЕЙ СТРУКТУРА ПРИВОД КИНЕМАТИКА КОМПОНОВКА ВАЛ ПОДШИПНИК ЗУБЧАТОЕ КОЛЕСО ГИДРАВЛИЧЕСКОЕ УПРАВЛЕНИЕ
Объект исследования и разработки – токарный станок модели 165.
Цель работы – спроектировать привод главного движения токарного станка на базе модели 165.
Проведен анализ и кинематический расчет привода главного движения станка-прототипа и вновь разрабатываемого привода. Произведены силовые расчеты валов зубчатых колес шлицевых и шпоночных соединений выбраны и рассчитаны подшипники качения гидроцилиндры для переключения частот вращения шпинделя. В пояснительной записке приведены описания работы электрической схемы и системы смазки.
В графической части курсового проекта представлены схемы станка-прототипа и вновь разрабатываемого привода; свертка и развертка коробки скоростей вновь разрабатываемого привода; гидравлическая схема управления переключением частот вращения шпинделя.
ТПЖА.210120.257CБ Развёртка 2.cdw

Порядок включения электромагнитов гидрораспределителей
Схема гидравлическая принципиальная переключения частот вращения шпинделя
Клапан предохранительный
Гидрораспределитель двухпозиционный
Гидрораспределитель трехпозиционный
ТПЖА.220140.257СБ Зажим заготовки.cdw

передаваемое гидроцилиндром
Суммарная сила зажима в кулачках
Радиальное биение оси конического отверстия
- у торца шпинделя - 0
- на длине оправки 300 мм - 0
Нагрев подшипников шпинделя при обкатке в течение часа при
не должен превышать 70
Уровень шума не должен превышать 80 дБ.
Проверить все частоты вращения шпинделя с кратковременной
работой на каждой частоте в течение 2-3 мин с вращением шпинделя
по часовой и против часовой стрелки.
Утечки масла из гидроцилиндра поз.1 не допускаются.
Техническая характеристика
Технические требования
СП ТПЖА.220140.257.spw

Сталь 45 ГОСТ 1050-88
Чугун СЧ15 ГОСТ 1412-85
Сталь 40Х ГОСТ 4543-71
Чугун СЧ15 НОСТ 1050-88
Сталь 20Х ГОСТ 4543-71
Корпус передней бабки
Блок зубчатый двойной Z
МБС-С-2 ГОСТ 7338-90
Cталь 40Х ГОСТ 4543-71
Блок зубчатый двойной
Войлок ГИ ГОСТ 6418-81
Колесо зубчатое сменное
Смесь резиновая В-14 ТУ 005.1166-87
Сталь 35 ГОСТ 1050-88
Сталь 20 ГОСТ 1050-88
Винт М12-6gх25.48.026
Кольца стопорные наружные
Кольца стопорные внутренние
Кольца уплотнительные
Подшипники шариковые
радиальные однорядные
Подшипники радиальные
с короткими цилиндрическими
Подшипники роликовые
конические однорядные
Шпонки ГОСТ 23360-78
ТПЖА.210120.257CБ Развёртка 1.cdw

Пределы частот вращения шпинделя
Переключение частот вращения шпинделя
Вращение валов после сборки должно быть плавным
Радиальное биение оси конического отверстия
- у торца шпинделя - 0
- на длине оправки 300 мм - 0
Нагрев подшипников шпинделя при обкатке в течение часа при
не должен превышать 70
Уровень шума не должен превышать 80 дБ.
Проверить все частоты вращения шпинделя с кратковременной
работой на каждой частоте в течение 2-3 мин с вращением шпинделя
по часовой и против часовой стрелки.
Техническая характеристика
Технические требования
расчет шлицев и подш 48 изм.1.doc
Боковые поверхности зубьев шлицевого соединения работают на смятие а их основание на изгиб и срез. Решающее значение имеет расчет на смятие.
Напряжения смятия для шлицевого соединения определяются по формуле 3:
где- наибольший крутящий момент передаваемый соединением Нм;
- коэффициент учитывающий неравномерность распределения усилий по рабочим поверхностям зубьев;
- рабочая длина зубьев м;
- проекция рабочей поверхности зуба длиной 1 м на его среднюю диаметральную плоскость м2.
где- величина фаски на углах зубьев м;
- радиус закругления для впадин м;
- наружный диаметр вала м;
- внутренний диаметр вала м;
- допускаемое напряжение на смятие МПа.
Для неподвижных соединений под нагрузкой - МПа 3.
Для подвижных соединений под нагрузкой - МПа 3.
Неподвижное шлицевое соединение 8х32х38х6:
Неподвижное шлицевое соединение 8х42х48х8:
Подвижное шлицевое соединение 8х52х60х10:
Неподвижное шлицевое соединение 8х52х60х10:
Подвижное шлицевое соединение 8х56х65х10:
Неподвижное шлицевое соединение 8х56х65х10:
Неподвижное шлицевое соединение 8х46х54х9:
Подвижное шлицевое соединение 10х72х82х12:
Неподвижное шлицевое соединение 10х72х82х12:
Подвижное шлицевое соединение 10х102х112х16:
Неподвижное шлицевое соединение 10х112х125х18:
8 Расчет шпоночных соединений
Выбранные шпонки проверяются на смятие 4:
где МПа – допускаемое напряжение смятия при стальной ступице;
- рабочая длина шпонки при скругленных концах м.
b – ширина шпонки м.
где h – высота шпонки м;
- глубина паза вала м.
Диаметр посадочного вала тройного блока мм.
Для шпонки 32х18х56: мм; мм
Для шпонки 32х18х63: мм; мм
Для двух шпонок 32х18х63
Для шпонки 45х25х100: мм; мм.
Для двух шпонок 45х25х100
Диаметр посадочного вала мм.
Для шпонки 45х25х100; мм; мм.
9 Расчет подшипников качения
При расчете подшипников качения определяется номинальная долговечность подшипника в часах 3:
где - номинальная динамическая грузоподъемность Н;
- эквивалентная нагрузка Н;
- расчетная частота вращения рассчитываемого вала обмин;
- коэффициент эквивалентной нагрузки: - для шариковых подшипников; - для роликовых подшипников.
Номинальная долговечность должна быть не менее рекомендуемого для металлорежущих станков ресурса подшипников ч.
Эквивалентная нагрузка определяется по формуле
где - коэффициент радиальной нагрузки зависящий от типа подшипника;
- коэффициент вращения;
- радиальная нагрузка Н;
- коэффициент безопасности;
- температурный коэффициент.
Для шарикового радиального подшипника 208 ГОСТ 8338-75
Для двух подшипников 208 ГОСТ 8338-75
Для шарикового радиального подшипника 209 ГОСТ 8338-75
Для конического роликового подшипника 7209 ГОСТ 333-71
Для конического роликового подшипника 7210 ГОСТ 333-71
Для шарикового радиального подшипника 216 ГОСТ 8338-75
Для конического роликового подшипника 7309 ГОСТ 333-71
Для конического роликового подшипника 7311 ГОСТ 333-71
Для шарикового радиального подшипника 212 ГОСТ 8338-75
Для конического роликового подшипника 7217 ГОСТ 333-71
Для конического роликового подшипника 7218 ГОСТ 333-71
расчеты валов эпюры 37 изм.1.doc
Рисунок 12 – Расчетные схемы I вала
Горизонтальная плоскость X
Из уравнения моментов относительно опоры А
Из уравнения моментов относительно опоры В
Вертикальная плоскость У
Строятся эпюры изгибающих моментов в обеих плоскостях.
Определяется суммарный изгибающий момент по формуле 3
Строится эпюра суммарного изгибающего момента .
Строится эпюра крутящего момента .
Определяется приведенный момент по четвертой теории прочности 3
Строится эпюра приведенного момента.
Определяется опасное сечение. Это сечение под колесом .
Из уравнения прочности 3 определяется диаметр вала в опасном сечении.
где - допускаемое напряжение для стальных валов.
По 3 для вала из закаленной стали 40Х МПа.
Принимается диаметр вала под зубчатыми колесами мм. Зубчатые колеса устанавливаются на вал по шлицевому соединению 8х42х48х8. Слева от зубчатых колес на вал I устанавливаются по диаметру мм подшипники и по шлицевому соединению 8х32х38х6 втулка получающая вращение от шкива клиноременной передачи.
Результаты расчета остальных валов сводятся в таблицу 5.
Таблица 5 – Результаты расчета валов
Схемы нагружения эпюры моментов для валов II III IV V VI приведены на рисунках 13 14 15 16 17.
Рисунок 13 – Расчетные схемы вала II
Вал III – трёхопорный. Рассчитывается как статически неопределимый.
Для этого средняя опора С заменяется реакциями в горизонтальной плоскости и в вертикальной плоскости .
Условием совместимости деформаций являются уравнения
где и - прогибы в горизонтальной и вертикальной плоскостях опоры С.
Горизонтальная плоскость.
Прогиб опоры С складывается из трёх прогибов: вызванного действием силы ; вызванного действием силы и вызванного действием реакции .
где - модуль упругости материала вала Нмм2;
- осевой момент инерции поперечного сечения вала относительно оси Х мм4.
Реакция определится из уравнения
Вертикальная плоскость.
Рисунок 14 – Расчетные схемы вала III
Вал IV – трёхопорный. Рассчитывается как статически неопределимый.
Рисунок 15 – Расчетные схемы вала IV
Рисунок 16 – Расчетные схемы вала V
Рисунок 17 – Расчетные схемы вала VI
5 Расчет шпинделя на прочность
Шпиндель станка (вал VII) является полым. Расчет на прочность шпинделя токарного станка ведется как проверочный поскольку внутренний и внешний диаметры шпинделя выбраны не в результате предварительного расчета на прочность а приняты конструктивно.
Наружный диаметр шпинделя мм.
Диаметр отверстия в шпинделе мм.
Уравнение прочности для полого вала 3
где – момент сопротивления в опасном сечении при изгибе м3.
Для круглого полого сечения
Уравнение прочности выполняется.
6 Расчёт шпинделя на жесткость
Расчётная схема шпинделя представлена на рисунке 18.
Суммарный прогиб конца шпинделя (в точке E – месте резца) определяется по формуле 3
где Нмм2 – модуль упругости стали;
- средний момент инерции сечения шпинделя в пролёте и на консоли мм4;
- внешняя нагрузка (тангенциальная сила резания) Н;
- нагрузка на шпиндель от зубчатой передачи Н;
- расстояние между опорами мм;
- расстояния от места приложения нагрузки до опор мм.
Рисунок 18 – Расчётная схема шпинделя
Тангенциальная сила резания при точении определяется по формуле
где – скорость резания при точении ммин.
При обработке заготовки диаметром мм при частоте вращения шпинделя мин-1 скорость резания будет равна
Средний момент инерции определяется по формуле 3
мм – радиус отверстия шпинделя мм.
где – наружные радиусы первого второго k-го участков шпинделя мм;
– длины первого второго k-го участков шпинделя мм.
Полученное значение прогиба сравнивается с допускаемыми значениями
где – экономический допуск наиболее характерной для универсального станка чистовой обработки (наружное точение заготовки диаметром ) мм;
Условия (49) (50) (51) выполняются.
Определяется угол наклона упругой оси шпинделя в передней опоре как наиболее ответственный и сравнивается с допустимыми значениями.
Угол наклона в передней опоре (точка В)
Условие (53) выполняется.
ДКП.spw

движения токарно-винторезного
станка на базе модели 165
Пояснительная записка
Станок токарно-винторезный
по сборочным единицам
модернизированного станка
сложенная 24-1,26-1200 изм.1.doc
ГОСУДАРСТВЕННОЕ ОБРАЗОВАТЕЛЬНОЕ УЧРЕЖДЕНИЕ
ВЫСШЕГО ПРОФЕССИОНАЛЬНОГО ОБРАЗОВАНИЯ
ВЯТСКИЙ ГОСУДАРСТВЕННЫЙ УНИВЕРСИТЕТ
ФАКУЛЬТЕТ АВТОМАТИЗАЦИИ МАШИНОСТРОЕНИЯ
КАФЕДРА ТЕХНОЛОГИЯ АВТОМАТИЗИРОВАННОГО МАШИНОСТРОЕНИЯ
МОДЕРНИЗАЦИЯ ПРИВОДА ГЛАВНОГО ДВИЖЕНИЯ
ТОКАРНО-ВИНТОРЕЗНОГО СТАНКА НА БАЗЕ МОДЕЛИ 165
по дисциплине “Металлорежущие станки”
ПОЯСНИТЕЛЬНАЯ ЗАПИСКА
Техническое описание станка-прототипа
1 Назначение и технологические возможности ..
2 Техническая характеристика ..
3 Анализ компоновки и кинематики разрабатываемого привода станка-прототипа
Кинематический расчет разрабатываемого привода главного движения ..
Конструкторские расчеты .
1 Расчёт крутящих моментов на валах .
2 Предварительный расчёт валов на прочность ..
3 Расчёт модулей зубчатых колёс .
4 Уточнённый расчёт валов ..
5 Расчёт шпинделя на прочность ..
6 Расчёт шпинделя на жесткость ..
7 Расчёт шлицевых соединений
8 Расчёт шпоночных соединений .
9 Расчёт подшипников качения
Описание конструкции проектируемой коробки скоростей токарно-винторезного станка модели 165 .
Расчёт механизмов системы управления .
Описание работы электрической схемы ..
Описание системы смазки станка-прототипа и разработанного привода
Описание устройства автоматического зажима заготовки .. ..
Приложение А. Список литературы
Приложение Б. Спецификация
Машиностроение является основой научно-технического прогресса в различных отраслях народного хозяйства. Непрерывное совершенствование и развитие машиностроения связано с прогрессом станкостроения поскольку металлорежущие станки вместе с некоторыми другими видами технологических машин обеспечивают изготовление любых новых видов оборудования.
Металлорежущий станок – машина для размерной обработки заготовок в основном путем снятия стружки.
Универсальные металлорежущие станки называемые станками общего назначения предназначены для изготовления широкой номенклатуры деталей обрабатываемых небольшими партиями в условиях мелкосерийного и серийного производства. Универсальные станки с ручным управлением требуют от оператора подготовки и частичной или полной реализации программы а также выполнения функции манипулирования (смена заготовки и инструмента) контроль и измерение.
Помимо основной рабочей операции связанной с изменением формы и размеров заготовки на станке необходимо осуществлять вспомогательные операции для смены заготовок их зажима измерения операции по смене режущего инструмента контроля его состояния и состояния всего станка.
Совершенствование современных станков должно обеспечивать повышение скоростей рабочих и вспомогательных движений при соответствующем повышении мощности привода главного движения.
Повышение скоростей рабочих и вспомогательных движений связано с дальнейшим совершенствованием привода станков шпиндельных узлов тяговых устройств и направляющих прямолинейного движения.
Современные металлорежущие станки обеспечивают высокую точность обработанных поверхностей. Однако требования к точности в машиностроении постоянно растут и это в свою очередь ставит новые задачи перед станкостроением.
Специалисты в области технологии машиностроения металлорежущих станков и инструментов находятся на одном из самых ответственных участков всего научно-технического прогресса. Необходимо ясно представлять общие важнейшие свойства и качества определяющие технический уровень металлорежущих станков с тем чтобы создавать лучшие образцы и новые модели станков.
Задача заключается в том чтобы в результате коренного совершенствования технологии обработки создания новых металлорежущих станков с микропроцессорным управлением станочных модулей для гибких производственных систем обеспечить техническое и организационное перевооружение всех отраслей машиностроения и на этой основе обеспечить существенное повышение производительности труда.
ТЕХНИЧЕСКОЕ ОПИСАНИЕ СТАНКА-ПРОТОТИПА
1 Назначение и технологические возможности
Универсальный токарно-винторезный станок модели 165 предназначен для выполнения разнообразных токарных работ в мелкосерийном и индивидуальном производствах в том числе для точения конусов и нарезания резьб: метрической дюймовой и модульной.
Техническая характеристика и жесткость станка позволяют полностью использовать возможности быстрорежущего и твёрдосплавного инструмента при обработке чёрных и цветных металлов.
На рисунке 1 представлен эскиз представительной детали обрабатываемой на станке.
Рисунок 1 – Деталь представительная
2 Техническая характеристика
Класс точности станка по ГОСТ 8-71 .. Н
Наибольший диаметр обрабатываемого изделия над станиной мм 1000
Наибольший диаметр обрабатываемого изделия над суппортом мм .. 600
Наибольшая длина обрабатываемого изделия мм .. . 2800 5000
Центр в шпинделе передней бабки по ГОСТ 13214-67 метрический 100
Конец шпинделя по ГОСТ 12593-72 1-15М
Диаметр прутка проходящего через отверстие в шпинделе мм 80
Наибольшее перемещение суппорта мм:
продольное . 2520; 4500
Скорость быстрого перемещения суппорта мммин:
при продольном ходе .. 216; 153
при поперечном ходе .. 0735; 0523
Наибольшее перемещение резцовых салазок мм .. 240
Число резцов устанавливаемых в резцедержателе 4
Высота резца установленного в резцедержателе мм .. 50
Количество скоростей шпинделя 24
Пределы частоты вращения шпинделя обмин . 5 - 500
Количество подач . 32
продольных . 020 - 305поперечных . 007 - 104
Наибольшее усилие резания допускаемое механизмом подач Н:
Шаги нарезаемых резьб:
метрических мм . 1 - 120
модульных модуль 05 - 30
дюймовых ниток на дюйм.. . 28 – 14
Диаметр отверстия в шпинделе мм 85
Электродвигатель главного движения:
тип . . .. АО2-71-4М101мощность кВт 22число оборотов мин-1 . .. 1460
Электродвигатель быстрых перемещений суппорта:
тип . . .. 4АХ80В4У3мощность кВт 15число оборотов мин-1 . .. 1400
Охлаждение от электронасоса
Электронасос системы охлаждения:
производительность лмин . . 22
Род тока трехфазный переменный 380 В
Наибольшая масса обрабатываемого изделия кг .. 5000
Габаритные размеры мм:
ширина . 2100высота . 1760
Масса кг .. . 12500; 15650
3 Анализ компоновки и кинематики разрабатываемого привода станка-прототипа
Токарно-винторезный станок модели 165 имеет традиционную для токарных станков компоновку (рисунок 2).
Рисунок 2 – Общий вид станка с обозначением его составных частей
Токарно-винторезный станок модели 165 состоит из отдельных узлов.
Станина станка поз.1 является базовой сборочной единицей на которой монтируются все остальные сборочные единицы и механизмы станка.
На верхней части станины расположены три призматические направляющие из которых передняя и средняя являются базой каретки а задняя – базой задней бабки.
Внутри станины имеются наклонные люки для отвода стружки и охлаждающей жидкости в сторону противоположную рабочему месту.
Под левой головной частью станины находятся ниши в одной из которых смонтирован электродвигатель главного движения а в другой электронасос охлаждения с резервуаром для охлаждающей жидкости. Корыто для сбора охлаждающей жидкости выполнено монолитным с корпусом станины.
В правой части станины на передней стенке смонтирован кронштейн со встроенными в него опорами ходового винта и ходового вала и редуктором ускоренного перемещения суппорта с фланцевым электродвигателем поз.15.
Передняя бабка поз.2 установлена на левой головной части станины. В её корпусе смонтированы: коробка скоростей шпиндельный узел звено увеличения шага в восемь раз механизм изменения перемещения каретки при нарезании резьб механизм настройки скоростей шпинделя электромагнитная муфта поз.17 для торможения шпинделя смазочная система и электрошкаф.
Шпиндель смонтирован на трёх опорах качения из которых передняя и задняя – регулируемые.
Настройка частоты вращения шпинделя а также настройка на нарезание правой и левой резьб нормального и увеличенного шага производится перемещением зубчатых колёс по шлицевым валам с помощью рукояток расположенных на передней стенке передней бабки (рисунок 3).
Включение звена увеличения шага возможно только при работе с перебором.
Комплект сменных зубчатых колёс поз.8 с позволяющий выполнять на станке все резьбы и подачи установлен на боковой стенке передней бабки.
Коробка подач поз.7 установлена на передней стенке в левой части станины. Коробка подач – закрытого типа со съёмной передней стенкой. Механизм коробки подач позволяет получить все подачи и нарезаемые на станке резьбы не прибегая к изменению настройки сменных шестерён.
Суппорт поз.4 крестовой конструкции имеет продольное перемещение вместе с кареткой поз.5 по направляющим станины а поперечное – по направляющим каретки. Оба перемещения осуществляются механически (с рабочей подачей и использованием механизма быстрого перемещения) и вручную.
Резцовые салазки несущие четырёхпозиционный резцедержатель перемещается вручную по направляющим поворотной части которую можно повернуть вокруг вертикальной оси на любой угол.
Движение суппортной группе передаётся механизмом фартука поз.6 от ходового вала или ходового винта.
Фартук – закрытого типа со съёмной передней стенкой.
Благодаря наличию в фартуке четырёх электромагнитных муфт управление механическим перемещением суппортной группы сосредоточено и осуществляется одной рукояткой поз.23 (рисунок 3). Дополнительным нажатием кнопки поз.24 (рисунок 3) встроенной в рукоятку поз.23 можно включить быстрый ход суппорта. Благодаря обгонной муфте вмонтированной в коробку подач включение быстрого хода возможно при включённой подаче.
Гайка ходового винта – разрезная и включается рукояткой поз.21 (рисунок 3) через кулачковое устройство.
Для предотвращения одновременного включения гайки ходового винта и подачи имеется электромеханическая блокировка.
В фартуке смонтирован механизм предохранительной муфты исключающий поломку станка при перегрузках.
Задняя бабка поз.3 перемещается по направляющим станины от редуктора ручного перемещения вращением валика поз.26 (рисунок 3). Крепление бабки к станине производится двумя прихватами. Для жесткой фиксации в осевом направлении в задней бабке имеется упор который можно вводить в литые впадины станины рукояткой поз.27 (рисунок 3). Корпус задней бабки можно смещать по мостику в поперечном направлении. В пиноль задней бабки встроен вращающийся шпиндель у которого подшипники передней опоры регулируются с помощью гаек.
Для закрепления обрабатываемых изделий с состав станка входит четырехкулачковый несамоцентрирующий патрон поз.9 диаметром 1000 мм.
Для обработки нежестких деталей станок снабжён двумя люнетами: подвижным поз.10 и неподвижным поз.14. Подвижный люнет крепится на каретке и поддерживает деталь непосредственно около резца. Неподвижный люнет устанавливается на направляющих станины в любом месте и закрепляется болтом с помощью прихвата.
Подвод охлаждающей жидкости от электронасоса непосредственно в зону резания осуществляется по трубопроводу поз.11.
Для безопасной работы на станке имеются ограждение патрона поз.13 и ограждение зоны резания поз.12.
Электрооборудование станка предназначено для подключения к трёхфазной сети переменного тока с заземлённым или изолированным нейтральным проводом.
Схема расположения органов управления токарно-винторезного станка модели 165 представлена на рисунке 3.
Рисунок 3 – Органы управления станка модели 165
Органы управления станка модели 165 и их назначение:
2 3 4 - рукоятки установки частоты вращения шпинделя;
- рукоятка установки нормального и увеличенного шага резьбы;
- рукоятка установки правой и левой резьбы;
- рукоятка выбора вида работ (резьбы или подачи) и типа резьбы;
10 13 – рукоятки установки величины подачи и шага резьбы;
– включение и выключение накладного колеса Нортона;
– рукоятка установки величины подачи шага резьбы и включения ходового винта напрямую;
– рукоятка установки вида работ (резьбы или подачи);
– табличка: ходовой валходовой винт;
– кнопка “Стоп” (дублирующая);
– кнопка “Шпиндель назад” (дублирующая);
- маховик ручного перемещения каретки;
- кнопка “Шпиндель вперёд”;
– рукоятка включения гайки ходового винта;
- кнопка “Шпиндель назад”;
– рукоятка управления механическими ходами каретки и суппорта;
– кнопка включения быстрых ходов каретки и суппорта;
– валик ручного перемещения задней бабки;
– рукоятка упора задней бабки;
– толкатель стопорения шпинделя задней бабки с пинолью;
– маховик быстрого перемещения пиноли задней бабки;
– рукоятка включения медленного или быстрого перемещений пиноли задней бабки;
– рукоятка медленного перемещения пиноли задней бабки;
– винт поперечного перемещения задней бабки;
– рукоятка стопорения пиноли задней бабки;
– рукоятка ручного перемещения резцовых салазок;
– тумблер включения местного освещения;
– рукоятка поворота и крепления резцовой головки;
– рукоятка ручной поперечной подачи суппорта;
- вводный выключатель;
– кнопка “Шпиндель – прерывистое вращение”;
- кнопка “Шпиндель вперёд” (дублирующая);
– кнопка “Охлаждение пуск”;
- кнопка “Охлаждение стоп”;
– табличка “Сцепить гайку с винтом”;
- табличка “Расцепить гайку с винтом”.
В приводе главного движения станка-прототипа реализована множительная структура со звеном увеличения шага с двумя значениями знаменателя геометрического ряда со структурной формулой
Определяются знаменатели геометрического ряда по формуле 2
где - диапазон регулирования;
- число частот вращения шпинделя.
Диапазон регулирования определяется по формуле 2
гдеи - максимальная и минимальная частоты вращения шпинделя мин-1.
Для крайнего верхнего участка ГЧВ: ; мин-1;
Для центрального участка ГЧВ: ; мин-1;
Ближайшее стандартное значение .
Для крайнего нижнего участка ГЧВ: ; мин-1;
Структурная сетка привода главного движения станка-прототипа представлена на рисунке 4.
Кинематическая схема привода главного движения станка-прототипа представлена на рисунке 5.
С вала электродвигателя вращение через клиноременную передачу 215280 передается на вал I коробки скоростей.
Коробка скоростей сообщает шпинделю 24 различные частоты вращения как прямого так и обратного вращения. Реверс шпинделя осуществляется электродвигателем.
Вал II коробки скоростей получает вращение от вала I через зубчатую передачу 3254. На вал III движение передаётся через одно из включений двойного зубчатого блока Б1 (2149 или 3535). На вал IV движение передаётся через одно из включений тройного зубчатого блока Б2 (3549; 1838 или 4242). На вал V движение передаётся через одно из включений двойного зубчатого блока Б3 (2159 или 3636). Таким образом вал V получает 12 высших частот вращения.
Рисунок 4 – Структурная сетка привода главного движения
Движение шпинделю VII станка передаётся по двум кинематическим цепям:
- напрямую через зубчатую передачу 5075;
- через звено увеличения шага – передачи 2448 и 20120.
При этом шпиндель VII получает 12 низших частот вращения.
В коробку подач движение передаётся с вала IX коробки скоростей через сменные зубчатые колёса.
На вал IX коробки скоростей вращение передаётся по двум кинематическим цепям:
- шпиндель VII - зубчатая передача 6040 – вал VIII – зубчатая передача 3857;
- вал V (при включении звена увеличения шага) - зубчатая передача 5050 – зубчатая передача 4040 – вал VIII – зубчатая передача 3857.
Вал IX при этом получает соответственно один или восемь оборотов на один оборот шпинделя.
Блок зубчатых колёс Б4 (35 и 35) предназначен для изменения направления перемещения каретки при нарезании резьбы.
График частот вращения станка-прототипа изображен на рисунке 6.
Рисунок 5 – Кинематическая схема привода главного движения
Характеристики основной и переборных групп передач определяются по формуле 2
где - число передач в группе;
и - максимальное и минимальное передаточное отношение в группе.
Для первой переборной группы
Для второй переборной группы
Передаточное отношение звена увеличения шага
Структурная формула коробки скоростей станка-прототипа имеет вид
Рисунок 6 - График частот вращения станка-прототипа
КИНЕМАТИЧЕСКИЙ РАСЧЕТ РАЗРАБАТЫВАЕМОГО ПРИВОДА ГЛАВНОГО ДВИЖЕНИЯ
- число скоростей шпинделя ;
- структура сложенная;
- значение знаменателя геометрического ряда ;
- максимальная частота вращения шпинделя мин-1.
1Определяется диапазон регулирования 2
2Определяется минимальная частота вращения шпинделя 2
Согласно 2 для стандартный ряд частот вращения начиная с мин-1 имеет вид:
0; 375; 475; 600; 750; 950; 1180 мин-1
3 Уточняется диапазон регулирования 2
4 Для получения сложенной структуры для и применяются следующие структурные формулы:
Анализ структурных формул показывает что сложенные структуры ; и ; имеют наименьшее число зубчатых колёс валов и зубчатых блоков.
Принимается сложенная структура (класс вид ); структурная формула - у которой конструктивный порядок в основной группе совпадает с прототипом.
5Определяется количество конструктивных вариантов 2
где - количество групп передач соответственно в основной первой и второй дополнительной структурах;
- количество групп передач с одинаковым количеством передач
соответственно в основной первой и второй дополнительной структурах.
Принимается конструктивный вариант у которого конструктивный порядок в основной группе совпадает с прототипом.
6 Определяется число кинематических вариантов 2
Это следующие варианты для выбранного конструктивного варианта:
Наиболее целесообразным является первый вариант в которой кинематический порядок совпадает с конструктивным.
7 Назначаются характеристики групп передач.
Характеристика основной группы .
Характеристика первой переборной группы равна числу передач в основной группе 2
Характеристика первой и второй дополнительных структур 2
где и - число передач соответственно в основной и первой переборной группах.
Структурная формула модернизированного привода имеет вид
8 В соответствии со структурной формулой строится предварительно кинематическая схема привода (рисунок 7).
Рисунок 7 – Предварительная кинематическая схема разрабатываемого привода главного движения со структурой
9 На основании кинематической схемы и структурной формулы строится структурная сетка СТС (рисунок 8).
Рисунок 8 – Структурная сетка структуры
10 Выбирается трехфазный асинхронный электродвигатель АИР180S4У3 мощностью кВт и частотой вращения мин-1.
11 Строится график частот вращения привода главного движения c множительной структурой (рисунок 9).
Рисунок 9 – График частот вращения привода главного движения
cо сложенной структурой
Структурная сетка и график частот вращения модернизированного привода главного движения изображены на чертеже ТПЖА.045000.257ДПЛ.
12 Определяются предельные значения передаточных отношений и сравниваются с допустимыми значениями 2
Условие (11) выполняется.
13 Определяются числа зубьев зубчатых колес основной группы основной структуры.
Для основной группы основной структуры
определится по формуле 2
Для первой переборной группы основной структуры
определится по формуле
Аналогично определяются числа зубьев в первой и второй дополнительных структурах.
Результаты расчетов приведены в таблице 1.
Таблица 1 – Результаты расчета чисел зубьев зубчатых колес
14 Определяются диаметры шкивов ременной передачи.
Передаточное отношение ременной передачи равно:
Диаметр меньшего шкива принимается равным мм.
С учетом проскальзывания ремней и погрешностей возникающих при определении чисел зубьев принимается мм.
15 Для каждой частоты вращения записываются УКБ определяются действительные частоты вращения и их отклонения от стандартных по формуле 2:
Отклонения не должны превышать допустимое значение равное 2:
Результаты расчетов приведены в таблице 2.
Таблица 2 – Результаты расчетов частоты вращения шпинделя
Уравнения кинематического баланса
Продолжение таблицы 2
Вывод: как видно из таблицы отклонения всех частот вращения не выходят за предельные значения % ; зубчатые колеса подобраны правильно.
16 Кинематическая схема в окончательном виде представлена на рисунке 10.
Рисунок 10 – Окончательная кинематическая схема привода главного
движения со сложенной структурой
расчеты моментов и силы 24.doc
1Расчет крутящих моментов на валах
В токарных станках на движение подачи тратится 3 4% от мощности главного движения станка а остальная мощность идет на привод главного движения. Тогда мощность привода главного движения определится как:
Мощность на валу электродвигателя
Мощность передаваемая валом коробки скоростей определяется по формуле 3:
где - КПД участка кинематической цепи равный произведению КПД отдельных элементов привода расположенных между двигателем и рассчитываемым валом.
где - КПД ременной передачи;
- КПД зубчатой передачи;
- КПД пары подшипников качения.
Расчетное значение частоты вращения 3:
где- минимальная частота вращения мин-1;
- диапазон регулирования.
По длинной кинематической цепи мин-1
Расчетное значение округляется до ближайшего стандартного значения:
Расчет числа оборотов валов коробки скоростей ведется по нижней ветке ГЧВ:
Крутящий момент относительно оси любого вала коробки скоростей определяется по формуле 3:
где- передаваемая мощность рассматриваемого вала коробки скоростей кВт;
- частота вращения рассматриваемого вала коробки скоростей мин-1.
Силовой расчет основных элементов рассматриваемого привода ведется исходя из крутящих моментов соответствующих расчетной частоте вращения шпинделя.
Крутящие моменты на валах коробки скоростей:
2 Предварительный расчет валов на прочность
Предварительный расчет валов производят только на кручение поскольку на данном этапе проектирования невозможно определить изгибающие моменты от сил действующих на валы в виду неопределенности положения зубчатых колес и опор на валах.
Предварительный расчет валов на кручение ведется по пониженным допускаемым напряжениям на кручение при расчетной частоте вращения шпинделя:
Исходя из рекомендаций 3 диаметр вала определяется по формуле:
где - крутящий момент на
- допускаемое напряжение на кручение представленное в таблице 3 Нм2.
Таблица 3 – Допускаемые напряжения на кручение для проектируемой коробки скоростей
Допускаемое напряжение на кручение Нм2
Расчетные диаметры валов округляются до нормальных линейных размеров:
мм; ; мм; мм; мм; мм.
3 Расчет модулей зубчатых колес
Расчету в групповых передачах подлежат наиболее нагруженные зубчатые передачи. Предварительно определяется ориентировочное значение модуля по контактным напряжениям и напряжениям изгиба.
Модуль по напряжениям изгиба рассчитывается по формуле 3:
где - вспомогательный коэффициент 7;
- передаваемый крутящий момент Н·м;
- коэффициент учитывающий распределение нагрузки по ширине венца 8;
- коэффициент учитывающий форму зуба и зависящий от числа зубьев ;
- число зубьев шестерни;
- вспомогательный параметр;
- ширина зубчатого венца мм;
- делительный диаметр шестерни мм;
– допускаемое напряжение изгиба МПа.
Допускаемое напряжение изгиба при реверсивной работе обеими сторонами зубьев определяется по формуле 4:
где - коэффициент учитывающий реверсивную работу;
- предел длительной выносливости материала шестерни МПа;
- коэффициент безопасности.
Для изготовления шестерен и зубчатых колес применяется сталь 20Х ГОСТ 4543-71.
Для стали 20Х подвергнутой цементации и имеющей твердость зубьев:
- на поверхности - 57 62
- в сердцевине - 32 45 HRC.
Определяется напряжение изгиба для цилиндрической передачи и сравнивается с допускаемым.
Проверяется выбранный модуль по контактным напряжениям.
Допускаемое контактное напряжение определяется по формуле 4:
где - предел длительной выносливости шестерни МПа;
- на поверхности - 57 62 HRC
Контактное напряжение определяется по формуле 4:
- коэффициент учитывающий расположение зубчатых колес на валу относительно опор;
- передаточное число.
Результаты расчета всех других передач приводятся в виде таблицы 4.
Таблица 4 - Результаты расчета валов
Расчетное контактное
Расчетное напряжение
напряжение изгиба зубьев FP МПа
Расчетный модуль для групп передач мм
Принятый модуль для групп передач мм
Допускается превышение расчётного напряжения над допускаемым в пределах .
Превышение расчётного напряжения изгиба над допускаемым для V вала
Условие выполняется.
4 Уточненный расчет валов
Целью этого расчета является проверка приближенно определенных диаметров с учетом изгибающих и крутящих моментов от всех сил действующих на вал в различных сечениях.
Расчет вала ведется в следующем порядке.
Рассчитываются усилия действующие в передачах. Для цилиндрических прямозубых передач окружная Р и радиальная Т составляющие действующей в зацеплении силы соответственно равны 3:
где - крутящий момент на рассчитываемом валу Н·м;
- диаметр начальной окружности зубчатого колеса установленного на рассчитываемом валу м.
где - угол зацепления град (для прямозубых колес ).
Схема свертки валов коробки скоростей с передачами оказывающими наибольшее влияние на деформацию валов приводится на рисунке 11.
Рисунок 11 – Схема свертки валов коробки скоростей
Расчет проекций сил действующих: на второй вал коробки скоростей от зубчатого зацепления между вторым и третьим валами; на третий вал коробки скоростей от зубчатого зацепления между вторым и третьим и т. д.
Горизонтальная плоскость Х
Вертикальная плоскость У
Суммарные проекции сил действующих на вал в данной точке определяют по формуле:
где- проекция окружной силы для
- проекция радиальной силы для
- проекция окружной силы для
- проекция радиальной силы для i- вала на ось У Н.
Составляются схемы нагружения валов. Для этого действующие на валы силы раскладываются на горизонтальные и вертикальные составляющие подсчитываются реакции в опорах и изгибающие моменты в горизонтальной и вертикальной плоскостях.
ТПЖА.210120.257CБ Свёртка.cdw

ТПЖА.045000.257ДПЛ Схемы.cdw

Кинематическая схема привода главного движения
Структурная формула станка-прототипа Z=2
Сменные зубчатые колеса
Индустриальное И-30А
периодическая при ремонте
Солидол синтетический
Направляющие станины под каретку
Задняя опора ходового винта
Механиз редуктора быстрого
перемещения суппорта
Направляющие каретки под нижнюю
Винт и гайка верхней части
суппорта и его направляющие
Механизм резцедержателя
Опоры ходового винта салазок
Опоры ходового винта каретки
Винт и гайка каретки
Подшипники передней опоры шпинделя
Подшипники задней опоры шпинделя
Механизм редуктора перемещения
Механизм редуктора перемещения пиноли
Ролики пиноли люнета
Солидол синтетеческий
Станок токарно-винторезный
Структурная сетка станка после модернизации
График частот вращения (ГЧВ) станка после модернизации
Схема электрическая принципиальная
Кинематическая схема модернизированного станка модели 165
График частот вращения (ГЧВ) станка-прототипа
Общий вид станка с местами смазки
смазка, прочее, литература 56 изм.1.doc
Чертеж модернизированного привода главного движения представлен на чертеже ТПЖА.210120.257СБ.
Коробка скоростей собрана в корпусе передней бабки поз.20. Передняя бабка устанавливается на станину на два штифта поз192. и крепится болтами поз135.
Коробка скоростей состоит из семи валов которые приводятся во вращение шкивом поз.15 посредством клиноременной передачи от электродвигателя привода главного движения станка.
Вращение с вала I коробки скоростей передается на вал II через одно из включений двойного зубчатого блока поз.22 расположенного на валу II (передачи 2946 или 3342).
Вращение с вала II коробки скоростей передается на вал III через одно из включений сборного тройного зубчатого блока расположенного на валу III (передачи 2153; 2945 или 3737).
С вала III вращение на вал VI передаётся по двум кинематическим цепям:
- короткой - через зубчатые передачи 7839 или 3978;
- длинной – на вал IV через передачу 2665 через одно из включений сборного двойного зубчатого блока расположенного на валу IV (передачи 2270 или 5141) на вал V и далее на вал VI через передачу 2080.
С вала VI через передачу 5050 вращение передаётся на шпиндель VII.
Вал I установлен на шариковых радиальных подшипниках валы II III IV V и VI – на конических роликовых подшипниках.
В качестве передней и задней опор шпинделя поз.43 использованы двухрядные роликовые подшипники с короткими цилиндрическими роликами. Они установлен на конических шейках шпинделя с конусностью 1:12. Для восприятия осевых нагрузок в передней опоре шпинделя установлены два шариковых упорных подшипника.
На шлицевых валах коробки скоростей располагаются подвижные и неподвижные зубчатые колёса и блоки зубчатых колёс.
Коробка скоростей сообщает шпинделю двадцать четыре различных частоты вращения.
Со шпинделя VII вращение передаётся на коробку подач станка.
Вращение на вал VIII со шпинделя передаётся через передачу 6040.
От вала VIII вращение передаётся на вал IХ непосредственно при прямом вращении через передачу 3857 или при обратном вращении через паразитный зубчатый блок поз.82 расположенный на оси Х поз.87. На валу IХ расположено сменное зубчатое колёсо поз.85 через которое вращение передаётся на коробку подач.
Переключение скоростей производится четырьмя гидроцилиндрами которые управляются гидрораспределителями с электромагнитным управлением.
Расчет механизмов системы управления
По заданию управление переключением частот вращения шпинделя - гидравлическое.
Применение гидроцилиндров для переключения блоков зубчатых колес позволяет сократить габаритные размеры коробки скоростей.
Для переключения двух двойных блоков без нейтрального положения используются двухпозиционные гидроцилиндры для переключения двух тройных блоков – трехпозиционные гидроцилиндры.
Размеры гидроцилиндров выбираются конструктивно с учетом чтобы усилие на штоке было не менее Н.
Тяговое усилие поршневого гидроцилиндра определяется по формуле:
где- диаметр поршня гидроцилиндра м;
- диаметр штока гидроцилиндра м;
- давление в цилиндре Па
- механический КПД учитывающий трение в уплотнениях.
Управление гидроцилиндрами осуществляется гидрораспределителями с электромагнитным управлением.
Описание работы электрической схемы
Принципиальная электрическая схема модернизированного станка модели 165 представлена на чертеже ТПЖА.045000.257ДПЛ.
Перечень элементов электроаппаратуры представлен в таблице 6.
Таблица 6 – Перечень элементов электроаппаратуры
Выключатель системы охлаждения
Электродвигатель привода главного движения АИР180S4У3
Электродвигатель быстрых перемещений
Электронасос системы охлаждения ПА-22
Электродвигатель гидропривода АИР90L4У3
Предохранители силовой цепи
Предохранители цепей управления освещения
Переключатель пакетный
Выключатель лампы освещения
Выключатель кнопочный “ПУСК М1”
Выключатель кнопочный “ПУСК М2”
Выключатель кнопочный “СТОП”
Электромагниты гидрораспределителей
Переключатель галетный (поворотный)
Электромагнитная муфта
Электроаппаратура станка питается от трехфазной сети переменного тока промышленной частоты напряжением 380 вольт. На представленной электрической схеме имеется две цепи – силовая к функциям которой относится питание электроэнергией двигателя главного движения М1 двигателя быстрых перемещений М2 двигателя насоса охлаждения М3 и двигателя насоса гидравлической системы М4; а также цепь управления служащая для питания коммутирующей аппаратуры.
Автоматический выключатель Q1 служит для подготовки электрической схемы станка к работе. Кроме того данный автоматический выключатель снабжен максимальным токовым реле которое защищает элементы схемы от токов короткого замыкания.
Нажатием на кнопку SB4 «Стоп» электродвигатели М1 и М4 отключаются. Отключаются реле времени РВ1 и магнитный пускатель КМ1 разрывая при этом цепь питания электродвигателей М1 и М4. Электродвигатель М1 отключается от сети и включается тормозная муфта ЭМ1. происходит торможение шпинделя. По истечении выдержки времени 12 15 с полного торможения двигателя М1 реле времени РВ1 размыкает свой временной контакт и отключает муфту ЭМ1.
Электродвигатель М2 быстрых перемещений и электронасос М3 включаются в работу выключателями SB2 и Q2 соответственно.
Электролампа EL1 освещения зоны обработки работает от напряжения 36 вольт. Для понижения промышленного напряжения до требуемого значения в схеме применен понижающий трансформатор ТV1. Для включения и выключения электролампы используют переключатель КО1.
Тепловые реле КК1 КК3 служат для защиты двигателей от перегрузок. Размыкающий контакт включен в цепь питания обмоток контакторов. При перегрузке двигателя элементы теплового реле включенные в цепь обмотки статора двигателя нагреваются срабатывают и отключают контактор который в свою очередь отключает двигатель от трехфазной сети. Повторное включение двигателя возможно только после остывания нагревательного элемента реле и замыкания его контакта вручную или автоматически.
В системе установлены плавкие предохранители F1 F6 которые предохраняют электрооборудование станка от перегорания. Для выпрямления напряжения установлен диодный мост VD1 VD4.
Переключение блоков зубчатых колес осуществляется гидроцилиндрами которые управляются гидрораспределителями Р1 Р4 с электромагнитным управлением (электромагниты YA1 YA4). Включение электромагнитов в определенном порядке осуществляется галетным (поворотным) переключателем SA1. Порядок включения электромагнитов приведен на гидравлической схеме. Для уменьшения токов возникающих при включении электромагнитов YA1 YA4 гидрораспределителей установлены сопротивления R1–R6 и диоды VD5–VD10.
Описание системы смазки станка-прототипа и разработанного привода
Карта смазки и места смазки приведены в графической части на чертеже ТПЖА.045000.257ДПЛ.
Система смазки разработанного привода не отличается от системы смазки станка-прототипа.
Перед пуском станка его следует тщательно протереть после чего в соответствии с картой смазки наполняются резервуары до рисок “уровень масла” и специальным шприцем заполняются все маслёнки согласно схеме смазки.
Смазка станка обеспечивается следующими системами.
Циркуляционной системой смазки механизмов зубчатых колёс и подшипниковых опор бабки передней. Лопастной насос системы приводится в действие от вала I коробки скоростей через зубчатую передачу. Масло от насоса подаётся в распределительную ванну а из неё в подшипниковые опоры шпинделя и другим смазываемым точкам. Кроме того смазка деталей производится разбрызгиванием. Пройдя через смазываемые части масло собирается на дне корпуса бабки.
Циркуляционной системой смазки механизма коробки подач и сменных зубчатых колёс. Плунжерный насос системы приводится в действие от эксцентрика выполненного за одно целое с зубчатым колесом. Масло от насоса подаётся к сменным зубчатым колесам и в ванну для фитилей из которой с помощью фитилей по трубкам и непосредственно через отверстия поступает к смазываемым точкам. Пройдя через смазываемые части масло собирается на дне корпуса коробки подач.
Циркуляционной системой смазки механизма фартука и направляющих станины. Плунжерный насос системы приводится в действие от эксцентрика связанного с валом фартука. Масло от насоса подаётся к направляющим станины и в ванну из которой с помощью фитилей по трубкам поступает к смазываемым точкам. Пройдя через смазываемые части масло собирается на дне фартука.
Фитильной системой смазки направляющих каретки под нижнюю часть суппорта состоящей из ванночки и фитилей подводящих масло к смазываемым точкам.
Периодической системой смазки наливом направляющих поворотной части суппорта и винтовой пары поперечного перемещения суппорта.
Периодической системой смазки наливом: пиноли подшипниковых опор шпинделя зубчатой муфты и винтовой пары перемещения пиноли бабки задней.
Периодической системой смазки винтовой пары каретки опор винта каретки механизма резцедержателя подвижного и неподвижного люнетов и редуктора ручного перемещения бабки задней.
Масло заливается через заливные отверстия и растекается к смазочным точкам.
Фитильной системой смазки правой опоры ходового винта состоящей из ванночки и фитиля.
Периодической системой густой смазки подшипников шкива бабки передней механизма перемещения пиноли задней бабки механизма редуктора быстрого перемещения суппорта роликов пинолей люнета осуществляемой набивкой вручную консистентной смазки.
Направляющие станины под заднюю бабку ходовой винт и ходовой вал смазываются периодическим поливом из маслёнки.
В процессе эксплуатации станка необходимо следить за тем чтобы смазка станка производилась в сроки указанные в схеме смазки. Один раз в три месяца масло следует менять.
Масло залитое в смазочные места не должно содержать грязи и посторонних примесей должно быть отфильтровано от посторонних частиц с абсолютным размером не более 40 мкм.
Характеристики масел и сроки смазки указаны в карте смазки на чертеже ТПЖА.045000.257ДПЛ.
Описание устройства автоматического зажима заготовки
Конструкция зажимного устройства к шпинделю токарно-винторезного станка показана в графической части курсового проекта (чертеж ТПЖА.220140.257СБ).
Зажимное устройство представляет собой трёхкулачковый клиновой механизированный полый патрон устанавливаемый на передний конец шпинделя поз.5 и вращающийся зажимной полый гидроцилиндр устанавливаемый на задний конец шпинделя.
Настройка на необходимый диаметр зажима осуществляется переустановкой накладных закалённых или незакалённых кулачков поз.10 по рифлениям основных кулачков поз.8 с обеспечением выходной точности патрона.
Точность патрона с незакаленными кулачками достигается путём расточки накладных кулачков после их переустановки на необходимый диаметр зажима.
Перемещение кулачков осуществляется от поршня поз.2 через тягу поз.15.
Подвод и отвод масла в полости гидроцилиндра поз.1 осуществляется через коллектор поз.20 закреплённый на кронштейне поз.16.
В ходе выполнения курсового проекта была проведена модернизация привода главного движения токарно-винторезного на базе модели 165.
Проведен анализ и кинематический расчет привода главного движения станка.
Произведены силовые расчеты валов зубчатых колес шлицевых и шпоночных соединений выбраны и рассчитаны подшипники качения.
В процессе работы потребовалось детальное ознакомление с конструкцией и руководством по эксплуатации токарно-винторезного станка 165.
Модернизированный вариант коробки скоростей несет в себе ряд преимуществ по сравнению с конструкцией данного узла станка-прототипа:
-применение сложенной структуры позволило сохранить неизменной конструкцию основных узлов привода: электромагнитной тормозной муфты взаиморасположение валов основной структуры коробки скоростей в тоже время модернизированная коробка скоростей не имеет внутренних зубчатых зацеплений на шпинделе VII и валу
-управление переключением частот вращения шпинделя осуществляется посредством электрической и гидравлической схем что открывает возможности по частичной автоматизации процесса управления частотой вращения шпинделя;
-автоматизирован зажим заготовки.
Станок универсальный токарно-винторезный. Модель 165. Руководство по эксплуатации. – М.: НИИ информации по машиностроению 1978. – 103 с.
Казенин Г.П. Шиврин Ю.П. Методические указания по курсовому проекту курса “Металлорежущие станки” (ч.1 – Кинематический расчет и анализ структурных схем). – Киров: КирПИ 1978. – 50 с.
Шиврин Ю.П. Методические указания к курсовому проекту дисциплины “Металлорежущие станки” (ч.2 – Силовой расчет основных элементов станков). – Киров: КПИ 1979. – 36 с.
Чернавский С.А. Снесарев Г.А. Проектирование механических передач. – М.: Машиностроение 1984. – 560 с.
Бейзельман Р.Д. Подшипники качения. Справочник. – М.: Машиностроение 1975. – 572 с.
Земцов М.И. Казенин Г.П. Основные принципы проектирования систем дистанционного (кнопочного) управления автоматизированного оборудования. Методические указания к курсовому проектированию по МОАП. – Киров: РИО ВятГТУ 1995. – 32 с.
ГОСТ 21354-75. Передачи зубчатые цилиндрические эвольвентные внешнего зацепления. Расчет на прочность. – 96 с.
Анурьев В.И. Справочник конструктора-машиностроителя: В 3-х томах. Т.1 – М.: Машиностроение 1978. – 728 с.
Пуш В. Э. Конструирование металлорежущих станков. – М.: Машиностроение 1977. – 390 с.
Свешников В. К. Усов А. А. Станочные гидроприводы. Справочник. –М.: Машиностроение 1988. – 512 с.
Рекомендуемые чертежи
- 25.01.2023
- 29.05.2022
- 10.02.2022
- 25.10.2022
- 16.11.2023