Привод главного движения зубофрезерного станка




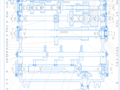
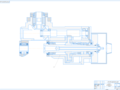
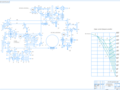
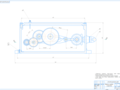
- Добавлен: 25.01.2023
- Размер: 2 MB
- Закачек: 0
Описание
Состав проекта
![]() |
![]() |
![]() |
![]() |
![]() ![]() ![]() ![]() |
![]() |
![]() ![]() ![]() |
![]() ![]() ![]() ![]() |
![]() ![]() ![]() ![]() |
![]() ![]() ![]() ![]() |
![]() ![]() ![]() |
![]() ![]() ![]() |
![]() ![]() ![]() |
![]() |
Дополнительная информация
Свертка.cdw

Поверхность соединения "корпус-крышка" перед сборкой
покрыть уплотнительной пастой типа Герметик.
Перед установкой опорную поверхность корпуса протереть.
После сборки валы должны проворачиваться свободно
Спецификация 1моя.DOC
Крышка подшипника сквозная
Крышка подшипника глухая
КП КРС.3601.03.14.200
Кинематика.cdw

схема зубофрезерного
График частот вращения шпинделя
Суппорт.cdw

Развёртка.cdw

Спецификация 2 моя.DOC
Кольцо дистанционное
Крышка подшипника сквозная
КП КРС.3601.03.14.200
Записка.doc
Выбор и описание компоновки станка 9
Синтез кинематической структуры станка 11
Определение основных технических характеристик станка 12
Проектирование кинематики привода главного движения 14
Описание системы управления станком 19
Динамические и прочностные расчеты узлов разрабатываемых конструктивно 21
Описание кинематической схемы станка 49
Описание конструкций спроектированных узлов 50
Курсовое проектирование – важная составная часть учебного процесса. В ходе курсового проектирования студенты приобретают опыт самостоятельного решения практических задач изучают современные конструкции технических устройств и тенденции их развития приобретают навыки использования средств вычислительной техники при решении задач.
Современные металлорежущие станки – это высокоразвитые машины включающие механические электрические электронные гидравлические пневматические и другие методы осуществления движения и управления циклом.
В данном курсовом проекте необходимо спроектировать зубофрезерный станок нормальной точности для обработки зубчатых колес из стали и чугуна.
Зубофрезерные станки используются для обработки цилиндрических зубчатых колес с прямым и косым зубом а также для обработки червячных колес.
Синтез кинематики формообразования поверхностей резанием
В соответствии с заданием зубофрезерный станок нормальной точности предназначен для обработки зубчатых колес максимальным диаметром 200 мм и наибольшим модулем 3 мм из стали и чугуна.
Зубчатые колеса могут быть изготовлены различными схемами формообразования.
Таблица 1 – Методы формообразования зубьев зубчатых колес
Формообразующие движения
Червячная фреза для обработки шлицевых валов
Метод формообразования строгальным резцом обладает малой производительностью. Из-за наличия возвратно-поступательного движения резца и движения деления заготовки возникают дополнительные инерционные нагрузки что приводит к вибрациям а следовательно к снижению точности. Возможна обработка блоков зубчатых колес.
При обработке долбяком прерывистое движение деления заменяется на непрерывное вращательное движение заготовки но не исключается возвратно-поступательное движение инструмента. Также возможна обработка блоков зубчатых колес.
Наиболее производительным и точным методом является формообразование зубьев червячной фрезой. Точность повышается за счет согласования вращательных движений заготовки и инструмента. Исключается возвратно-поступательное движение фрезы. Не возможно обрабатывать блоки зубчатых колес с малой величиной перебега инструмента.
Модульная фреза не позволяет обрабатывать близко расположенные венцы блока зубчатых колес. Необходимо прерывистое движение деления. При нарезании колес различных модулей необходимо использовать фрезы соответствующие данным модулям.
Обработка косозубых колес требует дополнительного вращения заготовки что усложняет кинематику станка.
Обработка шлицевых валов требует специальные червячные фрезы. Метод аналогичен нарезанию прямозубых колес червячной фрезой.
Также возможна обработка зубьев на торце однозубой фрезой. Для каждого вида профиля зуба необходима отдельная фреза. При увеличении количества зубьев фрезы усложняется ее конструкция.
На основе анализа схем приходим к выводу что наиболее приемлемым способом формообразования является зубофрезерование червячной фрезой прямозубых колес.
В таблице 2 приведем основные технические характеристики зубофрезерных станков близких по типоразмеру.
Таблица 2 – Основные технические характеристики зубофрезерных станков
Наибольший диаметр обрабатываемой детали мм
Наибольший модуль обрабатываемых зубчатых колес мм
Мощность электродвигателя кВт
Предельные частоты вращения обмин
Габаритные размеры станка мм:
В качестве станка-прототипа принимаем зубофрезерный полуавтомат 5К310 исходя из его технических и точностных характеристик предназначенный для фрезерования цилиндрических колес из стали чугуна легированных сталей легких сплавов методом обката.
Выбор и описание компоновки станка
Компоновка станка в значительной степени влияет на технико-экономические показатели. От компоновки зависит жёсткость конструкции тепловой баланс и температурная деформация универсальность станка и его переналаживаемость металлоёмкость трудоёмкость изготовления сборки ремонтопригодность.
Рассмотрим три варианта компоновки зубофрезерного станка.
Рис.1 – Схемы компоновок зубофрезерного станка
Для схемы (а) структурная формула имеет вид: ВОХRGFC.
Для схемы (б) структурная формула имеет вид: ВХОRGFC.
Для схемы (в) структурная формула имеет вид: ВFXОRGC.
Схема (а). Достоинства: малая занимаемая площадь из-за вертикального расположения заготовки; возможность отдельного изготовления и сборки основания и коробки скоростей с коробкой подач.
Недостатки: большая масса перемещаемых узлов.
Схема (б). Достоинства: малая занимаемая площадь из-за вертикального расположения заготовки; малая масса перемещаемых узлов.
Недостатки: совместное изготовление и сборка основания с коробкой скоростей и коробкой подач; большая вероятность попадания стружки на направляющие.
Схема (в). Достоинства: не большая высота; малая вероятность попадания стружки на направляющие; малая масса перемещаемых узлов.
Недостатки: ограниченная длина заготовки.
Из анализа достоинств и недостатков данных схем приходим к выводу что наиболее приемлемой схемой является схема (в).
Синтез кинематической структуры станка
Рис.2 – Структурная схема зубофрезерного станка
Основным формообразующими движениями при зубофрезеровании являются: согласованные движения фрезы и заготовки В1 и В2 и движение подачи фрезы П3. Кинематические цепи осуществляющие эти движения имеют самостоятельные органы настройки iv is ix и iy посредством которых устанавливается необходимая скорость вращения инструмента заготовки и его подача. Движение П4 необходимо для перемещения фрезы вдоль своей оси чтобы обеспечить обновление режущих кромок. Это движение осуществляется вручную. Органы Р1 предназначены для изменения направления вращения и перемещения инструмента соответственно. Все рабочие движения в станке осуществляются от электродвигателя М1.
Определение основных технических характеристик станка
По ГОСТ 9324-80 выбираем размеры фрез с модулем до 3 мм включительно и сводим в таблицу 3.
Таблица 3 – Червячные фрезы
Быстрорежущая сталь
Из технической характеристики станка-прототипа выбираем максимальную и минимальную подачи: .
Определяем максимальную и минимальную скорости резания для фрезерования червячной фрезой по стали и чугуну:
где - нормативная скорость резания [123 с. 30 карта 5];
Таблица 4 – Нормативная скорость резания
- поправочные коэффициенты на нормативную скорость резания для стали и чугуна [123 с. 30 карта 5];
Таблица 5 - Максимальная и минимальная скорость резания
Определяем частоты вращения
где - скорость резания ммин;
Таблица 6 – Частоты вращения
Определяем главную составляющую силы резания:
где - поправочный коэффициент и показатели степеней соответственно [1 с.291 табл.41];
- ширина фрезерования;
- поправочный коэффициент учитывающий качество обрабатываемого материала;
Определяем мощность резания:
где - нормативная мощность для стали 45 и чугуна;
- поправочные коэффициенты на нормативную мощность резания для стали и чугуна [123 с. 30 карта 5];
Проектирование кинематики привода главного движения
1. Определяем диапазон регулирования частот вращения шпинделя
2. Определяем число ступеней коробки скоростей
где - знаменатель геометрического ряда;
Для установленных значений выбираем по [3] стандартный ряд частот: 50 63 80 100 125 160 200 250 315 400 500 630.
3. Уточняем значение диапазона регулирования
4. Проверяем возможность осуществления простой множительной структуры
где - коэффициент для прямозубых колес;
Поскольку условие выполняется то принимаем простую множительную структуру.
Для выбранного значения записываем структурную формулу: .
5. Проверяем осуществимость принятого варианта структуры привода по диапазону
где - характеристика последней в порядке переключения группы;
- число передач этой группы;
Так как условие выполняется поэтому данный вариант осуществим.
6. Строим структурную сетку привода
Рис.3 – Структурная сетка
7. Строим график частот вращения
Рис.4 – График частот вращения
8. Определяем передаточные отношения
Для привода главного движения во избежание больших диаметров колес установлены предельные значения передаточного отношения: .
9. Определяем числа зубьев зубчатых колес
Для случая когда зубчатые колеса в группе прямозубые одного модуля и нарезаны без смещения исходного контура числа зубьев определяются:
где и - взаимно простые числа через которые выражается данное передаточное отношение т.е. ;
- сумма чисел зубьев в рассматриваемой группе;
Сумма чисел зубьев определяется как наименьшее общее кратное сумм данной группы.
9.1. Определяем числа зубьев зубчатых колес первой группы
Определяем сумму чисел зубьев
Увеличиваем числа зубьев по правилу при этом сохраняя передаточное отношение. Числа зубьев будут соответственно равны:
9.2. Определяем числа зубьев зубчатых колес второй группы
9.3. Определяем числа зубьев зубчатых колес третьей группы
Рис.5 – Кинематическая схема привода главного движения
Описание системы управления станком
Главным движение в станке является вращение фрезы которое он получает от электродвигателя мощностью кВт через одиночную зубчатую передачу коробку скоростей и клиноременную передачу. Вращение фрезы с определённой частотой вращения осуществляется за счёт переключения блоков зубчатых колёс при помощи барабана. Первая вилка осуществляет передвижение первого блока колёс вторая вилка – второго третья – третьего. Исходя из этого первая вилка имеет три положения вторая и третья - два. Чтобы получить необходимую частоту вращения шпинделя необходимо повернуть барабан в определённое положение. Обозначим левое положение тройного блока -1 среднее – 0 правое - +1; левое положение первого двойного блока – 0 правое - +1; левое положение второго двойного блока – 0 правое - +1
Таблица 4 – Управление коробкой скоростей
Положение первого рычага
Положение второго рычага
Положение третьего рычага
Частота вращения шпинделя обмин
Согласно таблице 4 строим профиль впадин барабана.
Рис.6 – Профиль впадин барабана
После построения профиля впадин изготавливают барабан.
Рис.7 – Схема системы управления коробкой скоростей
Динамические и прочностные расчеты узлов разрабатываемых конструктивно
Следует отметить что при динамическом расчете привода главного движения максимальный крутящий момент на выходе коробки скоростей определяется не по номинальной а по расчетной частоте его вращения которая принимается равной первой ступени второй четверти диапазона регулирования скорости т.е. n4 = 100 обмин.
1. Определяем частоты вращения на валах
2. Определяем угловые скорости валов
3. Определяем мощности на валах
где - КПД одной пары подшипников качения;
- КПД зубчатой передачи;
По [4 табл. 1.2.1 с. 13] принимаем .
4. Определяем крутящие моменты на валах
5 Расчет одиночной зубчатой передачи.
5.1. По [4 табл. 4.1.2 с. 43] принимаем для шестерни: сталь 40Х 260 280 НВ улучшение; для зубчатого колеса: сталь 40Х 230 260 НВ улучшение.
5.2. Определяем допускаемые контактные напряжения
5.2.1. Определяем базовое число циклов. По [4 рис. 4.1.3 с. 43] принимаем .
5.2.2. Определяем эквивалентное число циклов
где - продолжительность работы передачи час;
- число зацеплений зуба за один оборот колеса;
- коэффициент учитывающий изменение нагрузки передачи;
Принимаем . По [4 рис. 4.1.5 с. 43] принимаем .
где - количество лет работы станка;
- количество смен работы станка;
- коэффициент использования станка в год и в сутки соответственно;
5.2.3. По [4 с. 42] принимаем коэффициент долговечности .
5.2.4. Определяем предел контактной выносливости
5.2.5. Определяем допускаемые контактные напряжения
где - коэффициент запаса прочности;
По [4 с. 42] принимаем .
5.2.6. Определяем расчетные контактные напряжения
5.3. Определяем допускаемые изгибные напряжения
5.3.1. По [4 с. 42] принимаем базовое число циклов .
5.3.2. Определяем эквивалентное число циклов
5.3.3. По [4 с. 42] принимаем коэффициент долговечности .
5.3.4. Определяем предел выносливости зубьев при изгибе
5.3.5. Определяем допускаемые изгибные напряжения
где - коэффициент учитывающий влияние двухстороннего приложения нагрузки;
5.3.6. Определяем допускаемые напряжения при действии максимальной нагрузки
5.4. Определяем модуль зацепления
- число зубьев шестерни;
- коэффициент ширины шестерни относительно её диаметра;
- коэффициент учитывающий неравномерность распределения нагрузки по ширине венца;
- коэффициент внешней динамической нагрузки;
- коэффициент учитывающий форму зуба;
- передаточное число передачи;
Принимаем по [4 табл. 4.2.6 с. 51] по [4 рис. 4.2.3 с. 51] - по [4 табл. 4.2.9 с. 52] - по [4 рис. 4.2.5 с. 524 - .
Расчет производим для элемента пары «шестерня-колесо» у которого меньшая величина отношения
Принимаем по [4 табл. 4.2.2 с. 51] .
5.5. Определяем диаметры зубчатых колес
5.6. Определяем межосевое расстояние
5.7. Определяем ширины венцов
5.8. Определяем окружную силу в зацеплении
5.9. Определяем окружную скорость колес
5.10. По [4 табл. 4.2.14 с. 52] устанавливаем восьмую степень точности.
5.11. Принимаем по [4 табл. 4.2.8 с. 51] коэффициент учитывающий динамическую нагрузку в зацеплении .
5.12. Определяем удельную расчетную окружную силу при изгибе
5.13. Определяем расчетные напряжения изгиба зуба
Условие выполняется.
5.14. Определяем максимальные напряжения изгиба
По [4 табл. 16.7.1 с. 283] принимаем .
5.15. По [4 табл. 4.2.8 с. 51] принимаем коэффициент учитывающий динамические нагрузки в зацеплении .
5.16. По [4 рис. 4.2.3 с. 51] принимаем коэффициент учитывающий неравномерность распределения нагрузки по ширине венца (для контактной прочности) .
5.17. Определяем удельную расчетную окружную силу
5.18. Определяем расчетные контактные напряжения
где - коэффициент учитывающий форму сопряженных поверхностей зубьев;
- коэффициент учитывающий механические свойства материалов колес МПа05;
По [4 с. 47] принимаем .
5.19. Определяем максимальные контактные напряжения
5.20. Определяем окружные силы
5.21. Определяем радиальные силы
6. Расчет зубчатой передачи ( ).
6.1. По [4 табл. 4.1.2 с. 43] принимаем для шестерни: сталь 40Х 260 280 НВ улучшение; для зубчатого колеса: сталь 40Х 230 260 НВ улучшение.
6.2. Определяем допускаемые контактные напряжения
6.2.1. Определяем базовое число циклов. По [4 рис. 4.1.3 с. 43] принимаем .
6.2.2. Определяем эквивалентное число циклов
6.2.3. По [4 с. 42] принимаем коэффициент долговечности .
6.2.4. Определяем предел контактной выносливости
6.2.5. Определяем допускаемые контактные напряжения
6.2.6. Определяем расчетные контактные напряжения
6.3. Определяем допускаемые изгибные напряжения
6.3.1. По [4 с. 42] принимаем базовое число циклов .
6.3.2. Определяем эквивалентное число циклов
6.3.3. По [4 с. 42] принимаем коэффициент долговечности .
6.3.4. Определяем предел выносливости зубьев при изгибе
6.3.5. Определяем допускаемые изгибные напряжения
6.3.6. Определяем допускаемые напряжения при действии максимальной нагрузки
6.4. Определяем модуль зацепления
- коэффициент учитывающий неравномерность распределения
нагрузки по ширине венца;
Принимаем по [4 табл. 4.2.6 с. 51] по [4 рис. 4.2.3 с. 51] - по [4 табл. 4.2.9 с. 52] - по [4 рис. 4.2.5 с. 52] - .
6.5. Определяем диаметры зубчатых колес
6.6. Определяем межосевое расстояние
6.7. Определяем ширины венцов
6.8. Определяем окружную силу в зацеплении
6.9. Определяем окружную скорость колес
6.10. По [4 табл. 4.2.14 с. 52] устанавливаем шестую степень точности.
6.11. Принимаем по [4 табл. 4.2.8 с. 51] коэффициент учитывающий динамическую нагрузку в зацеплении .
6.12. Определяем удельную расчетную окружную силу при изгибе
6.13. Определяем расчетные напряжения изгиба зуба
6.14. Определяем максимальные напряжения изгиба
6.15. По [4 табл. 4.2.8 с. 51] принимаем коэффициент учитывающий динамические нагрузки в зацеплении .
6.16. По [4 рис. 4.2.3 с. 51] принимаем коэффициент учитывающий неравномерность распределения нагрузки по ширине венца (для контактной прочности) .
6.17. Определяем удельную расчетную окружную силу
6.18. Определяем расчетные контактные напряжения
6.19. Определяем максимальные контактные напряжения
6.20. Определяем окружные силы
6.21. Определяем радиальные силы
7. Расчет зубчатой передачи ( ).
7.1. По [4 табл. 4.1.2 с. 43] принимаем для шестерни: сталь 40Х 260 280 НВ улучшение; для зубчатого колеса: сталь 40Х 230 260 НВ улучшение.
7.2. Определяем допускаемые контактные напряжения
7.2.1. Определяем базовое число циклов. По [4 рис. 4.1.3 с. 43] принимаем .
7.2.2. Определяем эквивалентное число циклов
7.2.3. По [4 с. 42] принимаем коэффициент долговечности .
7.2.4. Определяем предел контактной выносливости
7.2.5. Определяем допускаемые контактные напряжения
7.2.6. Определяем расчетные контактные напряжения
7.3. Определяем допускаемые изгибные напряжения
7.3.1. По [4 с. 42] принимаем базовое число циклов .
7.3.2. Определяем эквивалентное число циклов
7.3.3. По [4 с. 42] принимаем коэффициент долговечности .
7.3.4. Определяем предел выносливости зубьев при изгибе
7.3.5. Определяем допускаемые изгибные напряжения
7.3.6. Определяем допускаемые напряжения при действии максимальной нагрузки
7.4. Определяем модуль зацепления
7.5. Определяем диаметры зубчатых колес
7.6. Определяем межосевое расстояние
7.7. Определяем ширины венцов
7.8. Определяем окружную силу в зацеплении
7.9. Определяем окружную скорость колес
7.10. По [4 табл. 4.2.14 с. 52] устанавливаем восьмую степень точности.
7.11. Принимаем по [4 табл. 4.2.8 с. 51] коэффициент учитывающий динамическую нагрузку в зацеплении .
7.12. Определяем удельную расчетную окружную силу при изгибе
7.13. Определяем расчетные напряжения изгиба зуба
7.14. Определяем максимальные напряжения изгиба
7.15. По [4 табл. 4.2.8 с. 51] принимаем коэффициент учитывающий динамические нагрузки в зацеплении .
7.16. По [4 рис. 4.2.3 с. 51] принимаем коэффициент учитывающий неравномерность распределения нагрузки по ширине венца (для контактной прочности) .
7.17. Определяем удельную расчетную окружную силу
7.18. Определяем расчетные контактные напряжения
7.19. Определяем максимальные контактные напряжения
7.20. Определяем окружные силы
7.21. Определяем радиальные силы
8. Расчет зубчатой передачи ( ).
8.1. По [4 табл. 4.1.2 с. 43] принимаем для шестерни: сталь 40Х 260 280 НВ улучшение; для зубчатого колеса: сталь 40Х 230 260 НВ улучшение.
8.2. Определяем допускаемые контактные напряжения
8.2.1. Определяем базовое число циклов. По [4 рис. 4.1.3 с. 43] принимаем .
8.2.2. Определяем эквивалентное число циклов
8.2.3. По [4 с. 42] принимаем коэффициент долговечности .
8.2.4. Определяем предел контактной выносливости
8.2.5. Определяем допускаемые контактные напряжения
8.2.6. Определяем расчетные контактные напряжения
8.3. Определяем допускаемые изгибные напряжения
8.3.1. По [4 с. 42] принимаем базовое число циклов .
8.3.2. Определяем эквивалентное число циклов
8.3.3. По [4 с. 42] принимаем коэффициент долговечности .
8.3.4. Определяем предел выносливости зубьев при изгибе
8.3.5. Определяем допускаемые изгибные напряжения
8.3.6. Определяем допускаемые напряжения при действии максимальной нагрузки
8.4. Определяем модуль зацепления
8.5. Определяем диаметры зубчатых колес
8.6. Определяем межосевое расстояние
8.7. Определяем ширины венцов
8.8. Определяем окружную силу в зацеплении
8.9. Определяем окружную скорость колес
8.10. По [4 табл. 4.2.14 с. 52] устанавливаем восьмую степень точности.
8.11. Принимаем по [4 табл. 4.2.8 с. 51] коэффициент учитывающий динамическую нагрузку в зацеплении .
8.12. Определяем удельную расчетную окружную силу при изгибе
8.13. Определяем расчетные напряжения изгиба зуба
8.14. Определяем максимальные напряжения изгиба
8.15. По [4 табл. 4.2.8 с. 51] принимаем коэффициент учитывающий динамические нагрузки в зацеплении .
8.16. По [4 рис. 4.2.3 с. 51] принимаем коэффициент учитывающий неравномерность распределения нагрузки по ширине венца (для контактной прочности) .
8.17. Определяем удельную расчетную окружную силу
8.18. Определяем расчетные контактные напряжения
8.19. Определяем максимальные контактные напряжения
8.20. Определяем окружные силы
8.21. Определяем радиальные силы
9. Размеры остальных колес рассчитываем аналогично и заносим в таблицу 5.
Таблица 5 – Основные размеры зубчатых колес
10. Определяем фактический ряд чисел частот вращения и сравниваем его со стандартным рядом
Уравнение кинематической цепи УКЦ
В результате проверочных расчётов фактическое значение n не превышает 5 % от стандартного.
11. Предварительный расчет валов
11.1. Определяем диаметры валов
где - допускаемое напряжение при кручении МПа;
Выбираем материал: сталь 45. Термообработка: улучшение 170 220 НВ.
12. Основной расчет валов
Для расчета выбираем второй вал на котором размещены три одиночных колеса и блок из двух зубчатых колес.
Рис.8 – Схема рассчитываемого вала
12.1. Определяем окружные силы в зацеплении
12.2. Определяем радиальные силы в зацеплении
12.3. Опорные реакции в горизонтальной плоскости
12.4. Опорные реакции в вертикальной плоскости
12.5. Изгибающие моменты в горизонтальной плоскости
12.6. Изгибающие моменты в вертикальной плоскости
12.7. Суммарный изгибающий момент
12.8. Эквивалентные моменты
Принимаем по [4 табл. 16.2.1 с. 271] .
12.9. Крутящий момент
12.10. На рис. 9 изображаем расчетную схему вала эпюры изгибающих моментов эквивалентных моментов и крутящих моментов.
Рис. 9 – Расчетная схема вала
13. Выбор подшипников качения
13.1. Предварительно принимаем подшипник шариковый радиальный 1000902 по ГОСТ 8338: .
13.2. Определяем осевые составляющие от радиальных нагрузок в опорах А и В
где - коэффициент осевого нагружения;
- радиальная нагрузка на опоре Н;
13.3. Величина и направление результирующей осевой силы
и направлена от опоры В к опоре А.
13.4. Осевая нагрузка воспринимаемая подшипником А
Осевая нагрузка воспринимаемая подшипником В
13.5. Для каждой опоры определяем
где - коэффициент вращения;
принимаем и - коэффициенты радиальной и осевой нагрузок.
13.6. Эквивалентная динамическая радиальная нагрузка
где - температурный коэффициент по [4 табл. 7.5.4 с. 86];
- коэффициент безопасности по [4 табл. 7.5.3 с. 86];
Дальнейший расчет проводим для большей из величин или . Обозначим её .
13.7. Эквивалентная динамическая радиальная нагрузка с учетом изменения внешней нагрузки привода
где - коэффициент учитывающий данные циклограммы изменения внешней нагрузки привода;
13.8. Расчетная долговечность работы подшипника
где - динамическая грузоподъемность подшипника Н;
Работа подшипников обеспечена.
14. Проверка прочности шлицевого соединения
Предварительно выбираем шлицевое соединение 6х16х20 (z=6 – количество шлицев d=16 мм – внутренний диаметр D=20 мм – наружный диаметр)
где - передаваемый крутящий момент Н мм;
- средний радиус шлицев мм;
- ширина ступицы мм;
- полная высота шлица мм;
- радиус галтели мм;
По [4 табл. 9.2.1 с. 125] принимаем .
Прочность шлицевого соединения обеспечена.
15. Проверка прочности шпоночного соединения
Длину шпонки принимаем на 5 мм меньше длины ступицы. Шпонку проверяем на смятие
где - крутящий момент на валу Н мм;
- рабочая длина шпонки мм;
- глубина шпоночного паза мм;
- допускаемые напряжения смятия МПа;
15.1. Для диаметра вала выбираем шпонку ( ).
15.2. Рабочая длина шпонки
где - длина шпонки мм;
15.3. Проверка шпонки на смятие
Прочность шпонки обеспечена.
Описание кинематической схемы станка
Кинематическая схема станка разрабатывается на основе его структурной схемы и компоновки.
Вал II коробки скоростей (КП КРС.36.01.03.14.200) связан с электродвигателем М1 мощностью 3 кВт зубчатой передачей 63-71.
Четырехваловая коробка скоростей имеет тройной и два двойных блоков зубчатых колес Б1 Б2.и Б3 Вал III получает вращение от вала II через шестерни 20-40 когда блок Б1 как показано на схеме сдвинут влево либо через шестерни 23-37 при крайнем левом положении блока Б1 или через шестерни 27-33 в среднем положении блока Б1. Вал IV получает вращение от вала III через шестерни 18-18 когда блок Б2 сдвинут вправо либо через шестерни 18-36 при крайнем левом положении блока Б2. Вал V получает вращение от вала IV через шестерни 55-44 когда блок Б3 сдвинут вправо либо через шестерни 24-75 при крайнем левом положении блока Б3.
Шпиндель фрезы связан с коробкой скоростей через три пары конических передач 25-2524-24 и 24-24. Далее через цилиндрическую передачу 20-80 вращение передаётся на шпиндель.
Непрерывное движение деления заготовки снимается с вала V и через червячную передачу и гитару деления a-b c-d e-f подается на вал IX.
Движение подачи фрезы снимается с вала XXIII и через зубчатую передачу гитару подач a1-b1 c1-d1 дифференциальный механизм ДМ.
Перемещение стола осуществляется отдельным электродвигателем М2 посредством цилиндрических пар зубчатых колес и червячной передачи.
Ускоренные перемещения инструмента осуществляются от электродвигателя М3.
Описание конструкций спроектированных узлов
Суппорт крепится на торце фрезерной стойки и может поворачиваться на 180° с помощью червячного колеса. Вращение шпинделя фрезы осуществляется от приводного вала стойки через конические шестерни и цилиндрическую пару. Шпиндель смонтирован на подшипниках качения. Для поддержки конца оправки инструмента служит контрподдержка втулка которой установлена на радиально-упорных подшипниках.
Шпиндель фрезы может перемещаться вдоль оси вместе с пинолью. Автоматическое перемещение производится от гидроцилиндра через шток-рейку обгонную муфту винтовую пару и ходовой винт связанный с пинолью только слева направо. Возврат в исходное положение производится вручную за квадрат . При этом необходимо расцепить обгонную муфту рукояткой 1.
Величина перемещение за каждый цикл настраивается винтом. Общая величина перемещение ограничивается конечным выключателем по упорам.
В ходе курсового проектирования были проанализированы схемы формообразования зубьев зубчатых колес был выбран наиболее приемлемый способ обработки (червячной фрезой). Для выбранного способа был взят станок-прототип 5А310 для которого спроектирована коробка скоростей обеспечивающая необходимые режимы резания. Проведены динамические и прочностные расчеты передач. Сделано описание кинематической схемы зубофрезерного станка. Рассмотрен суппорт.
Справочник технолога–машиностроителя. В 2-х т. Т. 2Под ред. А.Г. Косиловой и Р.К. Мещерякова. - 4-е изд. перераб. и доп.-М.: Машиностроение 1986. 496 с. ил.
Данилов В.А. Методические указания к курсовому проекту по курсу «Металлорежущие станки и промышленные роботы» для студентов специальности 0501. Новополоцк 1987 г.
Металлорежущие станкиПод ред. Тепинкичиева В.К. – М.: Машиностроение 1973.
Детали машин. Проектирование: Учебн. пособиеЛ.В. Курмаз А.Т. Скойбеда. – 2-е изд. испр. и доп. – Мн.: УП «Технопринт» 2002. – 290 с.
Металлорежущие станки: Учебник для машиностроительных втузовПод ред. В.Э. Пуша. – М.: Машиностроение 1985. – 256 с. ил.
Общемашиностроительные нормативы резания для технического нормирования работ на металлорежущих станках в 2-х ч. – М.: Машиностроение 1974.
Кочергин А.И. Конструирование и расчет металлорежущих станков и станочных комплексов. Курсовое проектирование: Учеб. пособие для вузов. – Мн.: Выш. шк. 1991. – 382 с.: ил.
Свирщевский Ю.И. Макейчик Н.Н. Расчет и конструирование коробок скоростей и подач. Минск «Вышэйш. школа» 1976.
Анурьев В.И. Справочник конструктора-машиностроителя: В 3 т. Т 1 – 8-е изд. перераб. и доп. Под ред. И.Н. Жестковой. – М.: Машиностроение 2001. – 920 с.: ил.
Рекомендуемые чертежи
- 22.11.2015
- 07.06.2021