Привод главного движения вертикально-фрезерного станка




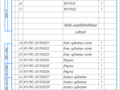
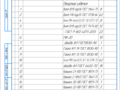
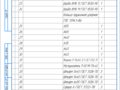
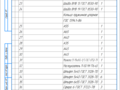
- Добавлен: 04.11.2022
- Размер: 2 MB
- Закачек: 0
Описание
Состав проекта
![]() |
![]() ![]() ![]() |
![]() |
![]() ![]() ![]() |
![]() ![]() ![]() |
![]() ![]() ![]() |
![]() ![]() ![]() |
![]() ![]() ![]() |
![]() ![]() ![]() |
![]() ![]() ![]() |
![]() ![]() ![]() ![]() |
Дополнительная информация
Spets1.cdw
Винт В.М5-6gx16 ГОСТ 11644-75
Винт М10-6gx35 ГОСТ 11738-84
Винт М8-6ex40.32 ОСТ 92-0737-72
Винт В.М5-6gx20 ГОСТ 17475-80
ГОСТ Р ИСО 4017-2013
Шайба 8Л ГОСТ8530-90
Гайка KM 19 ГОСТ 8530-90
Гайка KM 13 ГОСТ 8530-90
Болт М10-6ex30.35 ОСТ 92-0718-72
Шайба 8Л ГОСТ 6402-70
Крышка 21-100 ГОСТ 18511-73
Крышка 2-110x51 ГОСТ 11641-73
Крышка 20-100 ГОСТ 18511-73
Крышка 22-100 ГОСТ 18511-73
Подшипник ГОСТ 8338-75
Привод главного движения
вертикально-фрезерного
List2.cdw
Подшипник 3067713А ГОСТ 27365-87
Штифт 6x18 ГОСТ 3128-70
Шайба BMB 13 ГОСТ 8530-90
Шайба BMB 19 ГОСТ 8530-90
Кольцо пружинное упорное
Манжета 1.1-114x145-15 ГОСТ 8752-79
Маслоуказатель 11-50 МН 176-63
Штифт 5x45 ГОСТ 3128-70
Штифт 5x40 ГОСТ 3128-70
Штифт 6x55 ГОСТ 3128-70
Сфера 6 ГОСТ 3722-78
Пружина 30 ГОСТ 18793-80
Гайка накидная 14-22 ГОСТ 13957-74
Проходник прямой 12-31 ГОСТ 20188-74
Переходник прямой 18-22-22 ГОСТ 13961-74
Штифт 5x11 ГОСТ 3128-70
List3.cdw
Вновь разрабатываемые
Блок зубчатых колес
Лист 2.cdw
Подшипник 3067713А ГОСТ 27365-87
Штифт 6x18 ГОСТ 3128-70
Шайба BMB 13 ГОСТ 8530-90
Шайба BMB 19 ГОСТ 8530-90
Кольцо пружинное упорное
Манжета 1.1-114x145-15 ГОСТ 8752-79
Маслоуказатель 11-50 МН 176-63
Штифт 5x45 ГОСТ 3128-70
Штифт 5x40 ГОСТ 3128-70
Штифт 6x55 ГОСТ 3128-70
Сфера 6 ГОСТ 3722-78
Пружина 30 ГОСТ 18793-80
Гайка накидная 14-22 ГОСТ 13957-74
Проходник прямой 12-31 ГОСТ 20188-74
Переходник прямой 18-22-22 ГОСТ 13961-74
Штифт 5x11 ГОСТ 3128-70
Пояснительная записка.docx
Выбор электродвигателя привода главного движения и построение кинематической схема привода.5
Расчётная нагрузка станка.6
Автоматизированный расчет зубчатых передач станочных передач.7
Предварительная компоновка КП.16
Проектирование ременной передачи.17
Шлицевое соединение.24
Расчет на точность.26
Радиальное биение.27
Расчет на жесткость.27
Радиальная жесткость.28
Расчет прогиба в плоскости XOZ используя принцип суперпозиций:32
Расчет прогиба в плоскости XOY используя принцип суперпозиций:34
Суммарный прогиб шпинделя и его жесткость36
Анализ результатов.37
Система смазывания.38
Система управления.39
Анализ конструкции станков-аналогов
Фрезерные станки предназначены для обработки деталей и заготовок с плоскими и фасонными поверхностями. Широко распространены в металлообрабатывающей области промышленной сферы.
Вертикально-фрезерные станки предназначены для металлообработки заготовок с помощью торцевых фасонных цилиндрических и концевых фрез. Не исключено выполнение сверлильных работ. Применяется для обработки зубчатых колес и пазов углов и рамок вертикальных и горизонтальных плоскостей выполненных из чугуна стали цветных металлов и различных сплавов.
Вертикально-фрезерные станки делятся на две категории отличающиеся наличием в конструкции консоли. Их наименования соответственно:
бесконсольные вертикально-фрезерные станки;
вертикальные консольно-фрезерные станки.
Обычно шпиндель совершает только главное движение (движение резания) а стол может перемещаться перпендикулярно к оси шпинделя в горизонтальном и вертикальном направлениях и вдоль оси параллельной ей. Но есть модель станков которые имеют дополнительные установочные движения шпинделя.
Коробка скоростей шпиндельного узла устанавливается на станину а двигатель выносится за нее в противоположную сторону от шпинделя для смещения центра масс коробки скоростей и уменьшения вибраций от двигателя за счет ременной передачи и демпфирующих прокладок.
В современных станках используются асинхронные двигатели с плавным регулированием хода что заметно уменьшает габариты коробки скоростей.
Смазывание зубчатых колес и подшипников осуществляется централизовано или индивидуально.
Реверс осуществляется зубчатой передачей или двигателем торможение – аналогично.
Выбор электродвигателя привода главного движения и построение кинематической схема привода.
Необходимая мощность двигателя вычисляется по формуле:
– коэффициент полезного действия механической части который на стадии разработки технического предложения в зависимости от предлагаемой конструктивной сложности привода принимают равным 075 085.
Минимальная частота вращения выходного вала привода:
Из каталога асинхронных нерегулируемых двигателей серии 4А выбираем двигатель марки: 4А112М2 У3.
Табл. №1. Характеристики двигателя.
Синхронная частота вращения обмин
Находим число ступеней скорости Z привода:
По ГОСТ 8032-84 и рекомендациям нормали Н11-1 наиболее предпочтительными значениями знаменателя для ПГД при потери скорости резания будет равно 156.
Тип кинематической структуры: с совпадением части ступеней скорости.
Структурная формула: нормальная множительная структура.
Материал шестерён и колес: Сталь 25ХГТ; без автоматического регулирования с твердостью зубьев на поверхности 56 60 HRC в сердцевине у основания 37 45 предел контактной выносливости 1380 МПа предел выносливости зубьев на изгибную прочности 750 МПа.
Рис.1. Окна ввода параметров привода в программе кинематического расчета.
Рис.2. Картина частот вращения с выбранным числом зубьев
Рис.3. Кинематическая схема привода
Расчётная нагрузка станка.
Коэффициент мощности при легких режимах нагружения: .
Срок службы привода:
Для зубчатых передач базовое число циклов нагружения:
При контактном нагружении для закаленных сталей с твердостью поверхности 56 60 HRC
Показатель степени в уравнении кривой усталости:
При изгибе для поверхностно упрочненных сталей m=9
При контактном нагружении m=6.
Коэффициент режима работы для фрезерного станка с неравномерным характером нагрузки: 1.2
Коэффициент долговечности при контактном нагружении:
Коэффициент долговечности при изгибе:
Динамический коэффициент:
Рис.4. Расчет нагрузки станка общие данные
Между 1 и 2 валом самая нагруженная цепь имеет передаточное отношение .
Частота вращения самой нагруженной шестерни на 1 валу:
Коэффициент неравномерности работы:
Число поочередности работающих передач в группе: n=3
Коэффициент учитывающий место расположения рассчитываемого элемента в приводе при:
Контактном нагружении
Рис.5. Расчет нагрузки станка расчетные данные для расчета зубчатой передачи на 1 и 2 валу
В данной работе используется самая нагруженная цепь между 2 и 3 валом самая нагруженная цепь имеет передаточное отношение .
Частота вращения самой нагруженной шестерни на 2 валу:
Число поочередности работающих передач в группе: n=2
Рис.6. Расчет нагрузки станка расчетные данные для расчета зубчатой передачи на 2 и 3 валом
Автоматизированный расчет зубчатых передач станочных передач.
Все расчеты производим для зацеплений с наибольшей редукцией.
Проектировочный расчет передачи.
Число зубьев шестерни:
Число зубьев колеса:
Эквивалентный момент при расчете на контактную прочность:
Эквивалентный момент при расчете на изгибную прочность:
Частота вращения шестерни:
Отношение ширины к модулю
Коэффициент неравномерности распределения нагрузки по длине контактных линий при расчете (несимметричное расположение):
На контактную выносливость
На изгибную прочности
Коэффициент запаса прочности
Предел контактной выносливости:
Базовый предел выносливости зубьев на изгибную прочность
Код реверса передачи: нет.
Рис.7. Ввод данных для проектировочного расчета 1 передачи
Коэффициент долговечности при контактном нагружении
Рис.8. Ввод данных для проектировочного расчета 2 передачи
Степень точности передачи
Число передачи в группе
Максимальный вращающий момент на шестерне
Коэффициент учитывающий распределения нагрузки между зубьями
Коэффициент учитывающий влияние вида зубчатой передачи при расчете:
На контактную прочность
На изгибную прочность
Коэффициент учитывающий влияние разности шагов зацепления шестерни и колеса
Коэффициент учитывающий влияние шлифование переходной поверхности зуба (нитроцементация с закалкой чистовой режим)
Коэффициент запаса прочности (поковка)
Допускаемое контактное напряжение при действии максимальной нагрузки
Базовое значение предельного напряжения зубьев при изгибе максимальной нагрузки
Рис.11. Ввод данных для проверочного расчета 1 передачи
Рис.12. Ввод данных для проверочного расчета 2 передачи
Получаем расчет передач:
Предварительная компоновка КП.
Для обеспечения наименьших габаритных размеров и проектирования дополнительных частей КП таких как ременная передача органы управления и т.д. необходимо определиться с видом позиционирования валов в КП и примерными размерами.
Для того что бы составить предварительную развертку определимся с некоторыми размерами и формами:
Расположение валов в КП:
Учитывая расположения колес и валов в кинематической схеме привода можно предположить что получится укомплектовать валы в КП «Л»-образным способом. Причем валы с подвижными блоками колес (1 2) буду с левой стороны а шпиндельный узел (3) будут чуть углублены за 1 и 2 вал (т.е. справа). Тем самым мы придали КП более компактные формы и уменьшили количество неиспользуемого свободного места. Рычаги управления будут слева от КП..
Станина будет иметь вид буквы «Г» так как итоговый размер от оси вращения шпинделя до места крепления станины меньше основного параметра станка. Примем толщину станины примерно равной недостающему расстоянию оси шпинделя до основного параметра плюс половина толщины ШУ под опору плюс запас равный половине наибольшего диаметра фрезы: (320-260)+5002+1602=390 мм.
Расстояние от плоскости опор асинхронного двигал до оси вращения ротора h=112 мм. Примем запасное расстояние между креплением двигателя и КП в 30 мм. Примерная толщина стенки КП 10 мм. Крепиться двигатель будет за КП на станину. Это было принято с целью снижения нагрузки на элементы НС так как центр тяжести не будет выходить за пределы опорной поверхности.
Проектирование ременной передачи.
Проектировать ременную передачу и расчет нагрузок будем производить в программе «Kompas 3d». Межосевое расстояние будет равно сумме расстояний от осей вращения вала КП и ротора:
Также для расчета необходимы диаметры посадочных отверстий:
Где – допускаемое напряжение при кручении. Для стали 45 это значение равно 15 Нмм2.
Тип ремня – классический клиновый сечение E(B).
Число ремней 4. Скорость . Эффективность 092. Проскальзывание 5. Коэффициент характера нагрузки 1.1 (на ведомом – равномерные; на ведущем – легкие нагрузки). Расчетный диаметр ведущего шкива 125 мм.
Рис.15. Входные конструктивные параметры.
Расчет валов будем производить в программе Val_pr.exe для вала который передает момент шпиндельному узлу (2). Рассчитаем минимальный диаметр вала передающий самый большой момент 438 нм и допускаемым напряжением материала 15 МПа.
Рис.15. Проектировочный расчет 1-го вала.
Рис.16. Проектировочный расчет 2-го вала.
Так как 2-ой вал воспринимает большие нагрузки то дальнейшие расчеты будем производить с ним. С помощью программы считаем минимальный допустимый диаметр вала который после округления равен 55 мм. Фиксировать положение колес будем кольцами наружными упорными плоскими эксцентричные. По ГОСТ 13942-86 оперируя данными о минимальном диаметре вала выбираем Кольцо 37 ГОСТ 13942-86. По этому же кольцу выбираем диаметр шейки вала который равен 53 мм. Передавать крутящий момент будем с помощью шпонки на неподвижных колесах и с помощью шлифов на подвижных блоках колес.
Выбираем вариант нагружения опора-нагрузка-нагрузка-опора. Указываем округленный крутящий момент и примерные расстояния между колесами и подшипниками. Эти данные взяли из предварительной развертки данной КП.
Рис.17. Общие сведения при проектировании вала.
Дальше указываем диаметры колес работающие при самом нагруженном режиме. Получаем значения проекций действующих сил на валу и проекцию сил реакции опор.
Рис.18. Расчет проекций сил зацепления.
Указываем положение колес в свертке:
Рис.19. Свертка третьего вала КП.
Дальше указываем материал вала его состояние поверхности и виды концентраций напряжения. Пользуясь рекомендациями из [АРСП с.62] выберем материал вала: сталь 45. Вал с различными концентраторами напряжения полированный.
Рис.20. Выбор материала и состояния поверхности вала.
Дальше проведем эскизную компоновку третьего вала.
Рис.21. Эскизная компановка вала.
Рис.22. Эпюры моментов.
Рассчитаем значения изгибающих моментов в местах крепления зубчатых колес:
Таким образом изучив эпюры и эскиз вала можно выделить два опасных сечения в его конструкции: места сопряжения с зубчатыми колесами. В обоих сечениях есть концентраторы напряжения: паз под шпонку и шлицы. Рассчитаем эти сечения на усталостную прочность пользуясь программой «Расчет вала».
Рис.24. Подробный результат расчетов на устолостную прочность 9 сечения.
Расчет подшипников.
Расчитаем подшипник на динамическую грузоподъемность на 2 валу.
Рис.25. Исходные данные и резульаты расчета подшипников на грузоподъемность
Так как осевые силы на валу передающий момент шпиндельному узлу отсутствуют то будем использовать радиальные шариковые либо радиальные роликовые подшипники. Посадочный диаметр высчитанный на прошлом этапе равен 55 мм.
Примем радиально-шариковый подшипник ГОСТ 8338-75:
– динамическая грузоподъёмность
– статическая грузоподъёмность
Вычисляем эквивалентную динамическую нагрузку используя значения:
– коэффициент при вращении внутреннего кольца.
– коэффициент радиальный.
– реакция левой опоры
– реакция правой опоры
– коэффициент учитывающий характер нагрузки
– коэффициент учитывающий температурный режим (100).
Рассчитываем ресурс подшипников для самого нагруженного режима работы:
Определяем скорректированный по уровню надежности и условию применения расчетный ресурс:
– коэффициент учитывающий вероятность безотказной работы в 90% случаев;
– коэффициент учитывающий условия применения подшипников;
– степень для шариковых подшипников.
Скорректированный ресурс больше заданного.
Определять параметры шпиндельного узла будем исходя из основного параметра фрезерного станка: ширина стола. Ширина стола равна 160 мм. Подберем торцевую фрезу для данного стола из условия
Пользуясь ГОСТ 24359-80 выбираем фрезу с диаметром 160 мм. Посадочный диаметр 50 мм. И длиной при углах 60-12 =48 мм.
Рис. 25. Конструктивная схема шпинделя.
Ориентировочные размеры шпинделя:
Диаметр шейки вала под роликовый подшипник переднего конца шпинделя:
Диаметр шейки вала под радиальный подшипник переднего конца шпинделя:
Диаметр шейки вала под подшипник на конце шпинделя:
Межопорное расстояние (между центрами опор):
Расстояние между опорой на конце шпинделя и левым колесом:
Расстояние между опорой на начале шпинделя и правым колесом:
Расстояние между опорой на начале шпинделя и левым колесом:
Геометрическая точность ШУ – точность вращения без нагрузки – характеризующаяся осевым и радиальным биениями базирующих поверхностей переднего конца. Главенствующая роль в формировании данного параметра безусловно принадлежит одноименным погрешностям подшипников опор. Данный расчет нацелен на то чтобы по его результатам подобрать класс точности подшипников опор. Допуски на биения нормированы.
Рассчитаем радиальное биение в самом не благоприятном случае: вариант когда радиально биение конца шпинделя достигает максимальное значение а именно когда они лежат в одной плоскости и направлены в противоположные стороны.
Радиальное биение для фрезерных станков нормальной точности с основным параметром станка меньше 250 мм
Радиальное биение будем считать по формуле:
Радиальное биение внутреннего кольца подшипников по ГОСТ 520-89; 6 класса точности:
Для данной разновидности параметра геометрической точности нормируемым чаще всего является осевое биение переднего конца ШУ. Оно обусловлено в основном соответствующей погрешностью подшипников в продольном направлении под действием направлении.
Допуск на фрезерные станки нормальной точности:
Осевое биение внутреннего кольца шарикового радиального подшипника в сборе по ГОСТ 520-89; 4 класса точности:
Выполняется неравенство:
Расчет на жесткость.
Параметр жесткости является нормированным только для станочной системы в целом. При расчете жесткости ШУ чаще сего ограничиваются определением упругих перемещений в сечении его переднего конца под действием нагрузок. В перемещениях учитывают только деформации обрабатываемой заготовки оснастки инструмента и различных соединений со шпинделем во внимание не принимают относя и к самостоятельным задачам исследований. Как правило оценке подлежит жесткость и в радиальном и в осевом направлении.
Радиальная жесткость.
Определение радиальной жесткости ШУ сводится к вычислению деформаций изгиба переднего конца. При этом все силы раскладывают на составляющие в двух взаимно перпендикулярных плоскостях Y и Z проходящих через ось вращения шпинделя. Для каждой плоскости разрабатывают отдельную расчетную схему. Находят прогиб конца в этих плоскостях а затем суммарное перемещение.
Формализация геометрических параметров.
С целью упрощения расчетов его можно представить в виде балки постоянного поперечного сечения с моментом инерции вычисляемым по формуле:
Считаем момент инерции учитывая диаметр шейки в конусах как значение диаметра в центре длины:
Определение направления и места приложения внешних сил.
Рис.26. Схема резания при фрезеровании. Деталь и инструмент.
Рис.27. Схема сил на шпинделе с зубчатой передачей.
Определение моментов и сил в ШУ:
Наличие в передней и задней опоре группы подшипников создается защемляющий момент m препятствующий свободному повороту конца шпинделя со знаком противоположным знаку момента нагрузки. С учетом этого при переходе от реальных опор к идеализированным из заменяют на упругие шарнирные с радиальной жесткостью
Высота торцевой фрезы с учетом оправки примерна равна:
Так как нас интересует деформация переднего конца то при переносе силы P в требуемое сечение на конце балки появляется дополнительно изгибающий момент:
Реактивный момент m составляет часть активного создаваемого в общем случае силами P и Q. Характер и степень влияния Q экспериментально не подтверждены поэтому при определении значения m обычно используют выражение:
Где k = 04 – коэффициент защемления для данной схемы размещения подшипников.
На восприятие радиальной нагрузки в опорах ШУ служат роликовые двурядные подшипники. Рассчитаем жесткость в опорах:
Где – коэффициент контактной податливости 1;
– для роликовых подшипников;
- коэффициент контактной податливости 2;
Расчет прогиба в плоскости XOZ используя принцип суперпозиций:
Рис. 28. Расчетная схема шпинделя в плоскости XOZ
Рассчитаем реакции опор в плоскости XOZ:
Уравнение прогиба конца шпинделя в плоскости XOZ:
Расчет прогиба в плоскости XOY используя принцип суперпозиций:
Рис. 29. Расчетная схема шпинделя в плоскости XOY
Рассчитаем реакции опор в плоскости XOY:
Уравнение прогиба конца шпинделя в плоскости XOY:
Суммарный прогиб шпинделя и его жесткость
Осевая жесткость полностью зависит от жесткости установленных в опорах подшипников поэтому данный расчет фактически сводится к определению жесткости подшипников воспринимающих нагрузку в осевом направлении.
Минимальная величина предварительного натяга:
По графику [Автоматизированный расчет станочного привода стр.94 рис.5.6б] определяем осевую жесткость шпинделя:
Упругое смещение конца шпинделя:
Величина [] допустимой погрешности для фрезерного станка с шириной стола 160 мм нормального класса точности составляет 160 мкм [ГОСТ 17734-88]. Данная величина включает упругие деформации несущей системы станка и собственно заготовки износ инструмента и температурные погрешности. На долю упругих деформаций конца ШУ приходит максимум 30% от всех погрешностей технологической системы:
Суммарная осевая и радиальная погрешность вызванная силами на ШУ
Таким образом сконструированный ШУ отвечает поставленным показателям качества.
Система смазывания привода: И (Индивидуальная). Так как компоновка ШУ вертикальная и окружные скорости превышают допустимые скорости для использования консистентных смазок то будем использовать общую смазку ШУ. Смазывать будем масляным туманом. Что бы добиться такого способа смазки нужно добиться скорости потока жидкости превышающий скорость при турбулентном режиме течения. Данная скорость равна 6-8 мс.
Для проверки работы смазки ШУ установим прозрачную крышку на корпусе. Также для распределения потока смазки установим маслораспределитель в корпусе и два штуцера для подачи и слива смазки.
От маслораспределителя через трубки масло с большим напором поливает все зубчатые зацепления подшипники 1 2 и 3 вала задний подшипник шпинделя. Передние подшипники шпинделя смазываются отдельным штуцером установленным в опоре этих подшипников.
Где – мощность двигателя в кВт;
– разность температур масла на входе и выходе.
Итоговая производительность насоса:
Где – коэффициент запаса.
Диаметр трубопровода:
Где – скорость потока жидкости.
Где – время работы насоса.
Система управления приводом: Р (Ручная). В данной компоновке ШУ имеется 2 подвижных блока требующих ручное управление. Эти блоки располагаются вдоль боковой стенки. Управлять будем с помощью обхватывающих вилок. Три ручки управления располагаются на провой стенке ШУ. Две из них имеют две фиксированные позиции а третья – три. Угол поворота ручки для изменения передаточного отношения примерно равен: .
С.В. Птицин Ю. С. Чесов Б. Ф. Ноговицин. Проектирование привода главного движения металлообрабатывающего оборудования: Учеб. Пособие Новосиб. Гос. Техн. Ун-т. – Новосибирск 1993. – 54.
Автоматизированный расчет станочных приводов: Учеб. Пособие Под ред. Ю. С. Чёсова; Новосибирск; Изд-во НГТУ 1996. – 98 с.
Кочергин А. И. Конструирование и расчет металлорежущих станков и станочных комплексов. Курсовое проектирование: Учеб. Пособие для вузов. – Мн.: Высш. Шк. 1991 - 382 с.:ил.
Расчет нагрузки станков: Метод. Указания С. В. Птицин; Новосиб. Электротехн. Ин-т. – Новосибирск 1984.
Атлас шпиндельных узлов металлорежущих станков: Метод. Руководство С. В. Птицин Г. М. Лазутина; Новосиб. Электротехн. Ин-т. Новосибирск 1985.
Дунаев П. Ф. Леликов О. П. Конструирование узлов и деталей машин: Учеб. Пособие для машиностроит. Спец. Вузов. – 4-е изд. перераб. И доп. – М.:Высш.шк. 1985 – 416 с.ил.
Привод главного Движения вертикально- фрезерного станка.cdw
Осевая жесткость переднего конца шпинделя не менее 4*10
Радиальная жесткость переднего конца шпинделя не менее 13*10
Осевое биение переднего конца шпинделя не более 6 мкм.
Радиально биение переднего конца шпинделя не более 30 мкм.
Техническая характеристика
Электродвигатель серии 4А
частота вращения n=1500обмин
Диапазон регулирования привода: D=5
Максимальная частота вращения: n=1600 обмин
движения вертикально-
КП-РКС-07.19.00.00 ВО
развкртка.cdw

Рекомендуемые чертежи
- 07.06.2021