Полуавтомат для разрезания рулонов ткани на бобины




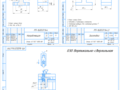
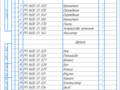
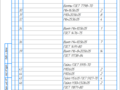
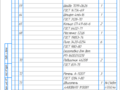
- Добавлен: 24.01.2023
- Размер: 12 MB
- Закачек: 0
Описание
Полуавтомат для разрезания рулонов ткани на бобины
Состав проекта
![]() |
![]() |
![]() ![]() ![]() |
![]() ![]() ![]() |
![]() ![]() ![]() |
![]() ![]() ![]() |
![]() |
![]() ![]() ![]() |
![]() |
![]() ![]() ![]() |
![]() ![]() ![]() |
![]() ![]() ![]() |
![]() ![]() ![]() |
![]() ![]() ![]() |
![]() ![]() ![]() |
![]() ![]() ![]() |
![]() ![]() ![]() |
![]() |
![]() |
![]() |
![]() ![]() ![]() |
![]() |
![]() |
![]() |
![]() |
![]() |
![]() |
![]() |
![]() |
![]() |
![]() |
![]() |
![]() |
![]() |
![]() |
![]() |
![]() |
![]() |
![]() |
![]() ![]() ![]() |
![]() ![]() ![]() ![]() |
![]() ![]() ![]() |
![]() ![]() ![]() ![]() |
![]() ![]() ![]() ![]() |
![]() |
![]() ![]() ![]() ![]() |
![]() ![]() ![]() ![]() |
![]() ![]() ![]() |
![]() ![]() ![]() |
![]() ![]() ![]() ![]() |
![]() ![]() ![]() |
![]() ![]() ![]() ![]() |
![]() ![]() ![]() ![]() |
![]() ![]() ![]() |
![]() ![]() ![]() ![]() |
![]() ![]() ![]() ![]() |
![]() ![]() ![]() ![]() |
![]() ![]() ![]() ![]() |
![]() ![]() ![]() |
![]() ![]() ![]() ![]() |
![]() ![]() ![]() |
![]() ![]() ![]() ![]() |
![]() |
![]() |
![]() |
![]() |
![]() ![]() ![]() |
![]() ![]() ![]() ![]() |
![]() ![]() ![]() |
![]() ![]() ![]() |
![]() ![]() ![]() ![]() |
![]() ![]() ![]() ![]() |
![]() ![]() ![]() ![]() |
Дополнительная информация
1.doc
Анализ технической литературы и патентных материалов по оборудованию для раскроя длинномерных изделий.
Проектирование кинематической схемы машины для раскроя рулона на полосы.
1 Проектирование гидравлической системы управления.
1 Расчет технологический усилий резания и определение мощности двигателя привода ножа.
2 Расчет усилий подачи и определение параметров гидроцилиндра привода отрезной головки.
3 Расчет усилий перемещения отрезной головки и определение мощности двигателя привода для позиционирования отрезной головки.
4 Расчет привода вращения рулона и определение мощности приводного двигателя.
5 Расчет параметров гидроцилиндров равнения кромки.
6 Расчет производительности.
7 Расчет на прочность.
Раздел технологии машиностроения.
Раздел технико-экономических расчетов.
Раздел охрана труда и промэкология.
Кинематическая схема машины-1.
Гидравлическая система управления-1.
Общий вид машины-15-2.
Сборочный чертеж отрезной головки-1.
Технология машиностроения-2.
3 разделы к 5 апреля.
1.1.doc
(72) СЕ. Столяр Р. Е. Столяр и Э. Е. Вайн-
(71) Одесское специальное конструкторское
бюро полиграфического машиностроения
(56) 1. Паспорт и инструкция по эксплуатации бобинорезальной машины 2БП—120.
Авторское свидетельство СССР № 848511 кл. D 06 Н 704 1979 (прототип).
(54) (57) 1. УСТРОЙСТВО ДЛЯ ПРОДОЛЬНОЙ РЕЗКИ РУЛОННЫХ МАТЕРИАЛОВ содержащее станину со стойками дисковые ножи установленные на параллельных валах один из которых смонтирован в стойках станины а другой — на концах параллельных поворотных рычагов свободные концы которых связаны со стойками станины посредством осей одна из которых выполнена в виде винта жестко связанного с поворотной рукояткой и соединена с соответствующим ей рычагом посредством закрепленной в нем гайки отличающееся тем что с целью повышения надежности устройства вторая ось выполнена с упорной поверхностью обращенной к соответствующей ей стойке станины и снабжена свободно установленной на ней с возможностью взаимодействия с упорной поверхностью опорой зафиксированной в соответствующем ей рычаге а поворотная рукоятка связана со стойкой станины пружиной.
Устройство по п. 1 отличающееся тем что ось с упорной поверхностью связана с соответствующей ей стойкой станины регулировочной винтовой парой.
(46) 07.11.83. Бюл. № 41 (72) Н. А. Якунин и С. 3. Мараны (71) Кишиневское ордена Трудового Красного Знамени производственное трикотажное объединение "Стяуа рошие* (53) 621.937 (088.8) (56) 1. Авторское свидетельство СССР Ns 151291 кл. D 06 Н 704 1962.
Авторское свидетельство СССР Ni 166458 кл. D 06 Н 704 1963 (прототип).
( 54) (57) УСТРОЙСТВО ДЛЯ ПЙРДОЛЬ- ! НОГО РАЗРЕЗАНИЯ РУЛОННОГО ПОЛОТНА содержащее рулонодержатель .барабаны для намотки лент ' ножевой валик с набором дисковых ножей и пары прижимных валиков отлвчающ е в-с я тем что с целью 'расширения технологических возможностей за счет получения лент различней ширины оно имеет смонтированную перед ножевым валиком по направлению перемещения полотна направляющую плиту с продольными пазами .расположенными между дно- новыми ножами и валик с набором клиновидных прижимов размещенных над пазами направляющей плиты и подпружиненных к ней.
(46) 30.08.85. Бюя.» 32 (72) П.А.Ыевинов и С.Д.Куна (53) 621.967 (088t3) (56) Авторское свидетельство СССР № 804430 кл. D 06 Н 7041979. (5*0(57) 1.УСТРОЙСТВО ДЛЯ ПРОДОЛЬНОЙ РАЗРЕЗКИ ЛЕНТОЧНЫХ МАТЕРИАЛОВ содержащее раму на которой закреплены посредством оси поворотные звенья несущие лезвия и механизм перемещения звеньев отличающееся тем что с целью повышения производительности труда за счет сокращения времени на монтировкулезвий и повышения удобства обслуживания механизм перемещения содержит угловой рычаг с рукояткой на одном плече смонтированной на раме шарнирно а другое плечо закреплено на оси поворотных звеньев и фиксатор положения рычага.относительно рамы.
Устройство по п.^отличающееся тем что оно имеет зубчатое колесо и зубчатый сектор взаимодействующий между собой причем зубчатое колесо установлено на оси поворотных звеньев а зубчатый сектор закреплен на раме на оси поворота рычага.
этом свободные необжатые хомутами 15 и кольцами 34 участки гофрирован-5-ной трубки 32 либо необжатые гайками 35 участки пружины 33 равномерно изменяются в осевом направ- 5 лении. Следовательно шаг между звеньями 12 с лезвиями 13 равномерно и одновременно изменяется на необходимую величину.
При значительном изменении шири- 10 ны разрезаемых полос звенья 12 с лезвиями 13 переставляются по шагу относительно упругой оправки 16 (либо гофрированной трубки 32 либо пружины 33 ) путем раскрепления на ней 15 хомутов 15 и закрепления их на . новом месте. Необходимая точность установки шага между лезвиями 13 обеспечивается путем осевого смещения звеньев 12 относительно хому- 20 тов 15 путем перезакрепления их относительно друг друга например винтового соединения (не показано).
Переналадка производится во время отведения лезвий 13 от ленты 7 25 для чего рукоятка 22 поднимается и поворачивает звено на оси 21 влево; установленное на оси 11 зубчатое колесо 19 обкатывается по неподвижно установленному зубчатому сек- з© тору 20 поворачивается против часовой стрелки и отводит вверх звенья 12 с лезвиями 13 под кожух (не показан ). В конце хода собачка 31 упирается в кромку паза 30 и звенья 12 3J надежно фиксируются в отведенном . положении. После окончания заправкиленты 7 собачка 31 отводится вправо звенья 12 поворачиваются по часовой ' .стрелке и надежно фиксируются в рабочем положении винтами 26 и 27 с гайками 24 и 25 и пружинами 28 и 29. Лезвия 13 при затуплении заменяются путем снятия держателей 14 со штырями 36. Замена лезвий 13 производится при отводе звеньев 12 от разрезаемого материала 7.
Настройка необходимого угла резания т.е. изменение угла между лезвиями 13 и разрезаемым материалом 7 производится вращением винтов 26 и 27 (при незначительном изменении положения лезвий 13 относительно разрезаемого материала 1) Такая настройка может осуществляться даже в момент разрезки материала 7 т.е. в процессе работы устройства.
При необходимости больших изменений угла резания для повышения удобства переналадки сектор 20 открепляется от корпуса устройства путем вывода из них фиксаторов 37 и 38. В этом случае установка необходимого угла резания обеспечивается вращением одного из винтов 26 или 27 после чего фиксаторы 37 и 38 вновь вводятся в неподвижный корпус устройства.
Положительный эффект от использования предлагаемого устройства выражается в повышении производительности за счет сокращения времени на монтировку лезвий и повышении удобства обслуживания.
(46)15.09.91. Бюл. №34
(71) Уфимский завод резиновых технических
изделий им. М.В. Фрунзе
№ 3710454 кл. D 06 Н 702 1987.
(54) СТАНОК ДЛЯ РЕЗКИ РУЛОННОГО ПОЛОТНА
(57) Изобретение относится к резке рулонов ткани разных размеров и позволяет повысить качество резки за счет обеспечения колебательного движения ножей. Оправка ножедержателей закреплена на поворотных рычагах и имеет роликодержатели с двумя парами роликов упирающихся в наматываемый рулон и удерживающих плоские ножи в рабочем положении. Опорные ролики имеют эксцентриситет 2-3 мм для обеспечения колебательного движения плоских ножей. Резка ткани в момент намотки ее в рулон осуществляется с небольшими усилиями на ножах поскольку они погружаются в прорезанный паз разрезая только один слой ткани. 4 ил.
Изобретение относится к устройствам для резки рулонов ткани разных размеров.
Цель изобретения - повышение качества резки за счет обеспечения колебательного движения ножей.
На фиг. 1 представлен станок общий вид; на фиг. 2 и 3 - разрез А-А на фиг. 1 соответственно начало резки и конец резки; на фиг. 4 - узел опорных роликов.
На станине 1 установлены раскаточные (тормозные) головки 2 и головка 3 (приводная) для закрепления квадратной оправки 4 с резиновыми шайбами 5. Привод 6 имеет цепную передачу 7 кинематически связанную с головкой 3.
Рычаги 8 закрепленные на осях 9 и образующие поджимной несущий кронштейн имеющий два пневмоцилиндра 10 и оправку 11 для держателей 12 ножей 13 с их фиксаторами 14. На оправке 11 закреплены подвижно два роликодержателя 15 с парой эксцентричных опорных роликов 16 (эксцентриситет 3 мм) с подшипниками 17 на осях 18. Фиксатор 19 крепит роликодержатели за счет паза 20 в оправке 11 которая в свою очередь крепится к рычагам 8 болтами 21 как и штанги 22 для пневмоцилиндров 10.
Исходный рулон устанавливается в рас-каточных головках 2 а конец полотна (ткани)' наматывается на резиновые шайбы 5 одетые на оправку 4 приводной головки 3. Роликодержатели 15 фиксируются по краям ткани на оправке 11 с помощью фиксаторов 19 а ножедержатели 12 устанавливаются по необходимой ширине нарезаемых полос ткани и фиксируются винтами 14. Вылет ножей 13 (величина врезания в рулон ткани) должен быть 5-7 относительно касания ро- ' ликов 16 поверхности разрезаемого рулона Г т.е. эксцентриситет роликов равный 3 мм не перекрывается.
Включается привод 6 вращения оправки 4 разрезаемого рулона и одновременно подается воздух на пневмоцилиндры 10 которые прижимают оправку 11 ножедержателей и роликов к вращающейся оправке 4 с резиновыми шайбами 5 на закаточной головке 3 при этом ролики 16 упираются в навиваемую ткань а ножи 13 прорезают эту ткань по заданной ширине.
Процесс резания ткани осуществляется посредством колебательного движения ножей 13 за счет эксцентричности опорных роликов.
Это обеспечивает оптимальный режим резания ткани в момент ее намотки в рулон с небольшими усилиями на ножах поскольку они погружаются в прорезанный паз разрезая только один слой ткани. Лезвие ножа работает не одной точкой а определенной зоной так что стойкость его увеличивается и сохраняется чистота реза и роаная кромка.
После разрезания рулона он снимается с оправки 4 а набор резиновых шзйб 5 позволяет я.еп.о разделить нарезанные бухты из рулона.
Плоские ножи практически разрезают один слой ткани при своем колебательном движении за счет эксцентриситета роликов. Лезвия ножей работают не одной точкой а некоторым участком по длине равным величине эксцентриситета роликов. Разрезать можно рулоны практически всех размеров ' а нарезанные ленты автоматически удерживаются между ножами т.е. сохраняется ров-5 ность намотки. Деформация ткани отсутствует так как усилия резания минимальные.
Станок для резки рулонного полотна
содержащий раскаточную и закаточную головки и смонтированный с возможностью поворота на горизонтальной оси поджимной кронштейн несущий на своем конце
держатели плоских ножей и опорные ролики установленные с возможностью вращения от контакта с поверхностью разрезаемого рулона отличающийся тем что с целью повышения качества резки
за счет обеспечения колебательного движения ножей опорные ролики выполнены с эксцентриситетом при этом кронштейн установлен с возможностью поджима опорных роликов к рулону на закаточной головке.
Фиг. 34 поясняют роль колебательных движений и прижимной рессоры 10 в процессе разрезания рулонного тонкопленочного материала на узкие полосы. Из фиг. 3 4 видно что колебательные движения осуществляемые радиально образующей поверхности бобины с разрезанным пленочным материалом и пружинящее свойство рессоры стремятся высвободить режущую кромку ножей от толщи разрезанных полос пленки а обратному внедрению режущей кромки на прежнее место препятствуют сомкнувшиеся под режущей кромкой слои разрезанных полос и пружинящие свойства прижимной рессоры. Перемещению верхних разрезанных слоев вслед за режущей кромкой препятствует прижимная рессора 10.
Таким образом режущая кромка ножа
находится в такой толще разрезанных слоев где усилия от прилегающих к боковой поверхности режущей кромке ножа верхних слоев разрезанной пленки недостаточны для защемления ножа.
Использование предлагаемого устрой-
ства позволяет повысить качество реза за счет исключения заклинивания и непрореза пленки. (56) Авторское свидетельство СССР
№ 340727 кл. D 04 Н 704 1969.
Формула изобретения "УСТРОЙСТВО ДЛЯ РЕЗКИ РУЛОННОГО ПЛЕНОЧНОГО МАТЕРИАЛА содержащее рулонодержатели неразрезанного и разрезанного материала блок ножей с установленными между ними прокладкамиотличающееся тем что с целью повышения качества блок ножей снабжен пово-20 ротным нагружателем и источником колебательных движений а прокладки снабжены прижимными рессорами.
(46) 23.02.85. Бюл. № 7
(72) В. П Голов Л. В Балин С. И- Семак
(56) I. Авторское свидетельство СССР .№ 914290 к л. В 29 С 1714 1980.
Авторское свидетельство СССР № 107741 кл. D 06 II 704 1956 (прототип).
(54) (57) УСТРОЙСТВО ДЛЯ ПРОДОЛЬНОЙ -РЕЗКИ ЛЕНТЫ ПОЛИМЕРНОГО МАТЕРИАЛА содержащее установленныйна оси приемный барабан закрепленные шарнирно на основании поводки с ножами с режущем кромкой и следящие элементы отличающееся тем что с целью повышения качества резки материала устройство снабжено тягами одним концом шарнирно установленными на основании а каждый нож выполнен в виде двуплечего рычага огибающего приемный барабан и установленного на поводке на оси с возможностью поворота вокруг нее при этом режущая кромка выполнена на наружной поверхности одного плеча а другое ею плечо шарнирно соединено с тягой причем следящий элемент выполнен в виде ролика закрепленного между поводками на одной оси с ножами.
Форма режущей кромки 10 ножа 8 определяется из условия постоянства угла резания а и минимального расстояния зоны резания от приемного барабана 6
Пружина 15. одним концом соединена . с поводком 4 а другим — с основанием I и служит для прижатия следящего ролика 5 к барабану 6 установленному на кронштейне 16.
Устройство работает следующим образом.
Ленту Материала (преирега) 17 и под- 0 ложку 3 закрепляют на приемном барабане 6 При этом ножи 8 острым участком 12 прорезают материал 0 а подложка 3 проходит поя следящим роликом 5. Пружина 15 прижимает поводки 4 вместе со следующим (5 роликом 5 к барабану 6 которому затем придают вращательное движение например от электродвигателя (не показан).
Лента материала 17 движется от подающего барабана (не показан) на приемный барабан 6 перед которым происходит его 20 резка на полосы радиусным участком 11 ножа 8. ' .
При возможном заедании или соединении уточных ниг'н в жгут материал 17 под нимается по радиусному участку П раз- 25 резается на заостренном участке 12 и возвращается и исходное положение.
Минимальное расстояние до точки укладки материала 17 (пренрега) на подложку 3 намотанную на барабан 6 и перемещение точки роза но режущей кромке ножа обес- 3° починаются в предлагаемом устройстве следующим образом.
Ролик 5 находится в постоянном контакте с подложкой 3 за счет усилия пружины 15 воздействующей на поводок 4 который вместе с ножами 8 поворачивается по мере увеличения диаметра приемного барабана 6. Кроме того за счет поворота ножей 8 вокруг оси следующего ролика 5 Посредством подвижного ' четырехугольника производится коррекция положения ножа 8 при изменении диаметра приемного барабана б с целью обеспечения минимальн- го расстояния от ножа 8 до подложки 3 и перемещения точки реза по режущей кромке ножа. Второе плечо 13 ножа 8 необходимо для соединения подвижного четырехугольника.
В случае его отсутствия с изменением диаметра приемного барабана изменяется расстояние между ножом и подложкой И точка реза не перемешается по режущей кромке ножа. .
Длина элементов подвижного четырехугольника определяется исходя из реальной конструкции устройства и разности диаметров приемного барабана.
Таким образом в предлагаемой конструкции изобретения предусмотрено минимальное расстояние от ножа до барабана что обеспечивает повышение качества укладки ирепрега и перемещение точки реза ю кромке ножа улучшающее качество решения при Налипании связующего на режущую кромку ножа Кроме того предотвращается осевое смещение слоев и расслоение продольных волокон ленты за счет того что производится точная намотка ленты на приемный барабан устраняется возможность перерезания продольных волокон И лента препрега получается с эквидистантными и ровными краями.
Назначение и область применения полуавтомат а.doc
Полуавтомат предназначен для раскроя рулонов на полосы в бобинах. Область применения – кожгалантерейная промышленность.
Техническая характеристика
Средняя производительность бобинчас
Минимальная ширина нарезаемых полос мм
Точность отрезания мм
Габаритные размеры исходного рулона мм
Высота оси вала главного над уровнем пола мм
Продольная подача ножа
Поперечная подача ножа
Частота вращения ножа мин-1
привод вала главного:
частота вращения мин-1
привод продольной подачи ножа:
привод поперечной подачи ножа:
привод заточки ножа:
Суммарная мощность установленных электродвигателей кВт
Габаритные размеры мм
Норма обслуживания чел
Описание работы на полуавтомате
В исходном положении отрезное устройство должно находиться в крайнем правом положении иглодержатели установленные на диске главного вала сняты.
РЛ.doc
1 Обзор конструкций машин для декоративной обработки кромки ткани
Для раскроя ткани на детали швейных изделий наиболее распространенными являются стационарные ленточные машины. Кроме раскройных машин на отдельных предприятиях швейной промышленности для вырубания настилов применяются штампы резаки и др.
В швейной промышленности используется несколько типов стационарных раскройно-ленточных машин: трехшкивная ленточная машина РЛ-2 и четырехшкивные машины РЛ-3 РЛ-4 и РЛ-5. Эти машины служат для чистового вырезания деталей из частей настила предварительно разрезанного передвижными раскройными машинами. Двухшкивная раскройная машина имеет по сравнению с трехшкивной небольшой вылет.
Орловский машиностроительный завод им. Медведева выпускает стационарную четырехшкивную ленточную машину РЛ-3 в двух вариантах: с вариатором позволяющим регулировать скорость движения ленточного ножа (модель РЛ-3Б) и без вариатора (с постоянной скоростью движущегося ножа модель РЛ-3А). Машина применяется для окончательного выкраивания деталей швейных изделий из ткани и трикотажа содержащих все виды волокон в том числе и синтетические. Техническая характеристика данной машины приведена в таблице 1.1.
Машина снабжена устройствами обеспечивающими безопасный труд работающего и способствующих получению высокого качества кроя. К ним относятся (см. рис. 1.1) механизм привода ножа лентоулавливатель устройство для предохранения рук от пореза заточное устройство устройство для регулирования натяжения ленты.
Механизм привода ножа
Привод ножа осуществляется от асинхронного электродвигателя 1 на валу 2 которого расположен в зависимости от модели машины вариатор 3-4 или сдвоенный шкив.
Таблица 1.1 - Техническая характеристика машины РЛ-3
Производительность машины (длина реза в смену)
Скорость движения ленточного ножа
Регулирование скорости ленточного ножа
Размеры ленточного ножа (длина)
Рабочий вылет машины
Мощность электродвигателя
Размеры раскройного стола (длина ширина высота над уровнем пола)
Габаритные размеры (длина ширина высота)
Далее посредством клинового ремня движение передается шкиву 5 который расположен на валу 7. На валу расположен ведущий шкив ножа 8 и тормозной барабан 6. С помощью трех ведомых шкивов 9 осуществляется перемещение ножа 10.
Рисунок 1.1 – Механизм привода ножа
Ограждение ножа состоит из двух частей: верхнего и нижнего ограждения. Оно представляет собой открывающийся коробчатый желоб расположенный вдоль контура ножа.
На рисунке 1.2 показана конструкция вариатора который состоит из шкивов 3 и 4 один из которых подпружинен и имеет возможность осевого перемещения относительно вала другой жестко закреплен на валу. Клиновой ремень 15 выполнен более широким чем в машине без вариатора. Скорость ножа регулируется сближением либо удалением конусов вариатора с помощью специального маховичка.
В машине РЛ-3А (см. рис.1.1) электродвигатель закреплен на рычаге 11 на котором крепится кронштейн 12. Последний посредством тяги 13 шарнирно связан с винтом 14. Винт перемещается в отверстиях кронштейна 15 с помощью гайки и контргайки. Тем самым регулируется натяжение клинового ремня.
Рисунок 1.2 – Схема вариатора
Лентоулавливатель состоит из верхнего ЭМ2 и нижнего ЭМ1 электромагнитных ловителей и контактного выключателя КВ. Последний взаимодействует с рычагом который опирается на нож своим весом. В процессе работы КВ касаясь рычага обеспечивает разомкнутое положение контактов переключателя. При обрыве ленточного ножа рычаг падает КВ замыкает цепь включая электромагниты ЭМ1 и ЭМ2. Одновременно отключается электродвигатель 1 и срабатывает электромагнит ЭМ3 воздействующий на тормозные колодки которые в свою очередь контактируют с тормозным барабаном 6.
Устройство для предохранения рук от пореза
Устройство состоит из кронштейна 1 (см. рис. 1.3) с втулкой для направления движения ножа 2.
Этот кронштейн должен быть опущен как можно ниже касаясь куска настила. Кронштейн 1 закреплен винтами на цилиндрической зубчатой рейке 3. Рейка имеет возможность перемещения в направляющих корпуса. Для того чтобы избежать ее поворота служит направляющая 4 закрепленная в корпусе. Рейка взаимодействует с шестерней 5 закрепленной на оси. Маховик 6 служит для перемещений рейки. С помощью специальной рукоятки выполненной в виде клеммы охватывающей рейку 3 происходит фиксация устройства в определенном положении.
Рисунок 1.3 – Устройство для предохранения рук от пореза
Устройство для регулировки натяжения ножа
Нож 1 (см. рис. 1.4) перекинут через барабан 2 который имеет ось 3 закрепленную в каретке 4.
Рисунок 1.4 – Устройство для регулировки натяжения ножа
Каретка перемещается в направляющих в вертикальном направлении. В ней имеется резьбовое отверстие куда вставлен винт 5 на который одета пружина 6. Верхней частью пружина упирается в каретку нижней – в гайку 7. Гайка имеет отросток перемещающийся в направляющих каретки что не допускает ее проворачивания. Для фиксации системы звеньев 1-7 в заданном положении служит втулка 8 закрепленная на винте. Также на винте крепится маховик 9 предназначенный для регулировки натяжения ножа. При вращении маховика гайка 7 перемещается воздействуя на пружину 6. Последняя воздействует на каретку 7 барабан 2 и нож 1. Натяжение ножа изменяется.
Вдоль машины расположена ось 1 (см. рис. 1.5) на которой закреплены две педали 2 и 3.
Рисунок 1.5 – Заточное устройство
В педали 2 имеются отверстия в которые вставлены тяги 4 которые посредством гаек 5 связаны с тягами 6. Тяги связаны посредством осей с рычагами 7. Оси крепятся в отверстиях ползуна 8 который движется по направляющей относительно корпуса машины. Для перемещения ползуна служит маховик 10 а для фиксации – винт 9. На осях рычагов 7 расположены кронштейны 11 12 13. На кронштейнах 13 крепятся оси абразивных кругов 14. Кронштейны 11 соединяются посредством пружины 15 которая стремится отвести абразивные круги от ножа. При нажатии на педаль 2 или 3 тяги 4 и 6 опускаются рычаги 7 поворачиваются. Кронштейны 11 12 13 перемещаются и круги 14 соприкасаются с ножом. Усилие давления кругов на нож зависит от давления ноги работающего на педаль что может негативно сказываться на качестве заточки и долговечности ножа.
Однако необходимый контур разрезания обеспечивается ручной подачей и тесно связан с навыками рабочего. На практике требуется часто вырезание по заданному контуру. Такое вырезание достигается на различных прессах с использованием резаков.
2 Обзор способов изготовления декоративной обработки кромки ткани
Для обработки швейных материалов резанием используются следующие виды энергии: механическая электрическая химическая тепловая. Вид используемой энергии определяет название способа обработки. Классификация способов резания сведена в таблицу 1.2.
Таблица 1.2 – Обзор способов резания текстильных материалов
Сверление фрезерование
Катком или ротационный
Механическое резание представляет собой расклинивание материала режущим инструментом имеющим всегда форму клина. В результате взаимодействия инструмента с материалом в зоне их прикосновения происходит сложный процесс деформаций и разрушения материала. Механическое резание швейных материалов выполняют способами которые определяются взаимным расположением режущего инструмента и заготовки в пространстве а также характером их изменения во времени. В зависимости от этого все способы механического резания можно разделить на четыре группы.
К первой группе относится простое резание. Простое резание представляет собой разрушение материала режущим инструментом имеющим одну режущую кромку и совершающим только рабочее движение определяемое конфигурацией линии резания. В эту группу включены: резание ножом (см. рис. 1.6а) пробивание (прорубание) иглой вырубание резаками (см. рис. 1.6б) или вырезание деталей с их помощью путем прокатывания валика (см. рис. 1.6в).
Рисунок 1.6 – Схемы взаимодействия режущего инструмента и
материала при простом резании
Во вторую группу включены способы резания предусматривающие сложное движение режущего инструмента состоящее из рабочего и дополнительного движений преимущественно перпендикулярно поверхности обрабатываемой детали. Режущим инструментом при обработке этим способом могут служить ножи пилы (см. рис. 1.7а) сверла (см. рис. 1.7б) ленты а также струя жидкости (гидравлический или гидроструйный способ см. рис. 1.7в). По характеру действия эти инструменты универсальны.
Рисунок 1.7 – Схемы взаимодействия режущего инструмента и
материала при сложном резании
Третью группу образует парное резание. При парном резании материал разрушается по одному контуру одновременно двумя режущими кромками. При обработке парным резанием используют инструменты универсального действия (ручные и механические ножницы различных типов см. рис. 1.8а) а также специальные (штампы содержащие пуансон и матрицу см. рис. 1.8б).
Рисунок 1.8 – Схемы взаимодействия режущего инструмента и
материала при парном резании
В четвертую группу входит комбинированное резание которое включает в себя комбинацию указанных способов (пиления и резания ножницами см. рис.1.9).
Рисунок 1.9 – Схемы взаимодействия режущего инструмента и
материала при комбинированном резании
Термический характер механизма разрушения вызываемого подводом в зону резания различной по природе физических явлений энергии и предопределил название способа резания – термофизический. Способа термофизической обработки материалов резанием различаются по виду режущего инструмента и носят одноименные с ним названия.
Существует два вида способа резания лучей: электронным лучем и лучем оптического квантового генератора (ОКГ) или лазера. Резание электронным лучем практически неприемлемо при изготовлении изделий легкой промышленности вследствие необходимости применения вакуумных камер. С помощью луча лазера (см. рис.1.10а) резание текстильных материалов можно выполнять последовательным параллельно-последовательным или параллельным методом обработки. Выбор метода зависит от способа фокусировки луча (в точку или линию) а также от способа подачи излучения на заготовку. Например мощный световой поток можно не фокусируя направить через контур шаблона вырезаемой детали на материал. В зависимости от способа подачи потока излучения на материал луч лазера может быть использован как специальный или универсальный режущий инструмент.
Плазменный способ резания (см. рис.1.10б) по виду разрушения сходен с лазерным но уступает ему по производительности однако способ резания плазмой гораздо проще и дешевле в осуществлении.
Для обработки швейных материалов резанием плазмой применяется косвенная низкотемпературная плазменная дуга – микроплазменная струя где в качестве плазмообразующегося газа применяется преимущественно аргон.
Прямое использование электрической энергии для резания рассматриваемых материалов практически невозможно из-за их диэлектрических свойств. Поэтому резание текстильных материалов с помощью электричества возможно только путем подвода электроэнергии в зону разрушения через промежуточное преобразование ее в другой вид энергии преимущественно в тепловую. В этом случае режущим инструментом служит электрический разряд (см. рис.1.10в) возникновение которого сопровождается значительным тепловым эффектом. Материал помещенный в поле разряда между электродами разрушается с заметными следами термического воздействия. Использование электроразряда в качестве режущего инструмента более эффективно при выполнении перфорирования.
При плазменном способе обработки как правило используется режущий инструмент универсального действия. При электроразрядной обработке материала резанием режущий инструмент может быть универсального действия (например два электрода формы игла-игла) или специального когда один из электродов имеет конфигурацию заданной линии реза.
Рисунок 1.10 – Схемы взаимодействия режущего инструмента и
материала при термофизическом резании
Термомеханический способ резания предполагает разрушение (разделение) материала с одновременным использованием для этой цели двух и более видов энергии. Сущность его заключается в том что разрушение материала происходит в основном термическим способом а разделение его – с помощью дополнительного механического воздействия режущего инструмента.
Нагрев материала в зоне резания достигается либо токами высокой частоты (ТВЧ) либо путем контактной передачи тепла от нагретого режущего инструмента (электротермический способ) либо с помощью ультразвука. Высокий износ режущего инструмента в этих способах ограничивает их использование при резании текстильных материалов.
Рисунок 1.11 – Схемы взаимодействия режущего инструмента и
материала при термомеханическом резании
Помимо описанных способов существует и другие (химические газолазерный газоплазменный) однако возможность их применения при раскрое текстильных материалов не изучена.
4+5+6.doc
1 Описание конструкции детали
В данном разделе дипломного проектирования требуется разработать технологический маршрут изготовления детали “направляющая”. Вид детали изображен на рисунке 4.1.
Деталь изготовляют из стали марки сталь 45 ГОСТ 1050-88 у которой предел прочности при растяжении равен 598 МПа предел текучести при растяжении равен 353 МПа относительное удлинение 16% твердость НВ равна 229 кгсмм2 (2246 МПа).
Изготовление детали из стали литьем позволяет получить требуемую конфигурацию наружного контура поверхности заготовки без значительных трудностей. Отсутствие разъемов значительно упрощает процесс получения заготовок.
Проведем размерный анализ чертежа детали предварительно кодировав поверхности детали (рисунок 4.2).
Для размерного анализа требуется выявить ошибочную или недостающую информацию используя исходные графы размерных связей по каждой координате отдельно. Исходные графы размерных связей представлены на рисунках 4.3-4.5. По каждой координатной оси обнаруживаем разрыв размерной связи. Исправляем ошибочную и недостающую информацию и строим исправленные графы размерных связей приведенные на рисунках 4.6-4.8.
Рисунок 4.1 – Эскиз кронштейна
Рисунок 4.2 – Анализ поверхностей детали в выбранной системе координат
Рисунок 4.3 - Исходный граф по оси К
Рисунок 4.4 - Исходный граф по оси М
Рисунок 4.5 - Исходный граф по оси N
Рисунок 4.6 – Исправленный граф размерных связей по оси К
Рисунок 4.7 – Исправленный граф размерных связей по оси М
Рисунок 4.8 – Исправленный граф размерных связей по оси N
2 Технологический процесс изготовления детали
2.1 Методы обработки поверхностей детали
Разрабатываемый маршрут технологического процесса устанавливает последовательность обработки поверхностей детали с целью получения требуемого качества поверхностей и наименьшей себестоимости. Маршрут представлен в таблице 4.1.
Таблица 4.1 - Методы обработки
Технические требования
Параметры поверхности
2.2 Дифференциация операций и базирование
Базирование – процесс определения поверхностей объекта производства от которых следует настраивать формообразующий элемент для получения требуемой точности размера.
Дифференциация операций.
Этап 2(предварительный).
5 горизонтально фрезерная операция ФРЕЧ Мр10 представленная на рисунке 4.9.
Рисунок 4.9 – Схема базирования операции 005
0 горизонтально фрезерная операция ФРЕЧ Nр11 представленная на рисунке 4.10.
Рисунок 4.10 – Схема базирования операции 010
5 вертикально фрезерная операция ФРЕЧ Кр1 представленная на рисунке 4.11.
Рисунок 4.11 – Схема базирования операции 015
В ходе первых операций 005 010 015 был сформирован единый комплект технологических баз относительно которого в большинстве случаев дальше будет производиться базирование для следующих операций механической обработки. Приведем некоторые из них.
0 сверлильная операция СВЕР No6 Np6 Кo2 Кр2 Кo5 Кр5 представленная на рисунке 4.12.
Рисунок 4.12 – Схема базирования операции 030
5 сверлильная операция СВЕР Мo8 Nо8 Мр8 Nр8 представленная на рисунке 4.13.
Рисунок 4.13 – Схема базирования операции 035
3 Размерный анализ технологического процесса
Размерный анализ проводится при составлении размерной схемы (рисунок 4.14) технологического процесса по координате М.
Рисунок 4.14 – Размерная схема технологического процесса по оси М
Составляем исходный и производный технологические графы приведенные на рисунке 4.15 4.16. Видим отсутствие замкнутых контуров отсутствие оторванных связей - технологический маршрут выбран верно.
Рисунок 4.15 – Исходный технологический граф
Рисунок 4.16 – Производный технологический граф
4 Составление и решение уравнений размерных цепей
Используя данные исходных и производных технологических графов составляем уравнения размерных цепей.
Операционным припуском называют слой материала удаляемый при выполнении отдельного перехода (операции). Его наименьшее значение достаточное для компенсации предшествующей погрешности называется минимальным припуском Zmin.
Минимальные припуски снимаемые с детали отображены в таблице 4.2.
Таблица 4.2 - Минимальные припуски по координате М
Минимальный припуск Zmin
Уравнения размерных цепей по оси М:
АМ2=-ОМ5+ОМ2-ОМ1+ЗМ2-ЗМ1+ЗМ3
ZМ2= ОМ7+ОМ6-ОМ5+ОМ2-ОМ3-ОМ4
РМ2= ОМ6-ОМ5+ОМ2-ОМ3
ZМ7=ОМ2-ОМ3+ОМ5- ОМ6
ОМ1нм= ОМ1нб-ОМ1=10-003=997
ЗМ6нм= ЗМ6нб-ЗМ6=18-05=175
АМ5= ОМ9 (отверстие)
ОМ9нб= ОМ9нм+ОМ9=8+0025=8025
Решение всех остальных уравнений размерных цепей технологического процесса позволяет судить о целесообразности выбора маршрута.
Расчет режимов резания для окончательной обработки поверхности будем производить по справочным материалам. Все результаты сведены в таблицу 4.3.
Таблица 4.3- Режимы резания
На основании расчетов заполняются операционные карты (см. приложение)
Технико-экономический расчет
Произведем расчет затрат на монтаж нового механизма. Номинальный годовой фонд рабочего времени механика находится по формуле
Тв – число выходных и праздничных дней в году Тв = 112 дней;
Тк – число календарных дней в году Тк = 365 дней;
а – продолжительность рабочей смены а = 8 часов;
Полезный фонд времени:
Тня- неявки на работу Тня=24дня
Тп=Тн-Тня=253-24=229.
Время демонтажа электропривода полуавтомата и монтажа гидропривода с наладкой Твр=113 часа.
Определим затраты на заработной плате механика.
Зозп=ЧТС×Твр=1750×113=19750 рублей
Затраты дополнительной заработной платы составляют 40% от основной заработной платы налоги и отчисления в фонд социальной защиты также 40% от основной заработной платы. Итого затраты на заработной плате составляют Ззп=18Зозп=18×19750=35550 руб.
Тогда величина экономического эффекта будет определяться по формуле Э=(Эс-Ззп)Т где Т - срок службы проектируемого полуавтомата в годах. Значение экономического эффекта будет составлять Э=(186750-35550)10=15120руб.
Таблица 5.1 – Смета изъятых и добавленных деталей (механизмов)
Редуктор червячной передачи
Муфта соединительная
Муфта соединительная
Охрана труда и промышленная экология
Охрана труда - это система законодательных актов социально - экономических организационных технических гигиенических и лечебно-профилактических мероприятий и средств обеспечивающих безопасность сохранение здоровья и работоспособности человека в процессе труда. Охрана труда создание безопасных и здоровых условий на предприятии лёгкой промышленности способствует повышению эффективности труда и улучшению качества выпускаемой продукции. Поэтому на всех предприятиях необходимо внедрение современных средств техники безопасности и обеспечение санитарно-гигиенических условий. Особое внимание должно уделяться вопросам улучшений условий труда санитарно-оздоровительным мероприятиям. При проектировании оборудования используемого на предприятиях легкой промышленности следует учитывать соответствие создаваемых конструкций требованиям норм охраны и гигиены труда. Охрана труда является социальной дисциплиной т.к. условия труда во многом определяют экономические показатели производства престижность специальностей психологический климат в коллективах текучесть кадров и трудовую дисциплину производства. Знание законов охраны труда позволяет применять их на практике при решении вопросов обеспечение безопасности и безвредных условий труда при одновременном повышении производительности труда предупреждение производственного травматизма профессиональных заболеваний аварий пожаров и взрывов. Таким образом основное направление охраны труда - это внедрение системы управления охраной труда создание безопасной техники технологий комплексная механизация и автоматизация производства.
2 Характеристика полуавтомата для раскроя рулонов ткани
Общая характеристика проектного варианта машины для нарезания полос из текстильных материалов приведена в таблице 6.1.
Таблица 6.1- Общая характеристика машины
Характеристика параметра
Опасные и вредные факторы имеющиеся в конструкции изделия либо проявляющиеся при его эксплуатации
Наличие вредных опасных или токсичных веществ
Да (см. таблицу 6.2)
Наличие источников ионизирующего излучения
Да (см. таблицу 6.3)
Наличие источников электромагнитных полей
Наличие возможности поражения человека электрическим током
Да (см. таблицу 6.4)
Наличие опасностей при работе изделия на холостом ходу и при обработке изделий
Да (см. таблицу 6.5)
Утвердительное содержание некоторых ячеек в графе “характеристика параметра” требует развернутого описания тех или иных преобладающих вредных или опасных производственных факторов имеющихся в конструкции или появляющихся при эксплуатации проектируемого закрепочного полуавтомата. Все данные о наличии таких факторов сведены в таблицы 6.2 - 6.6.
Таблица 6.2- Характеристика вредных опасных и токсичных веществ
Характеристика рассматриваемого параметра
Наименование вещества
Масло индустриальное И-12А ГОСТ 20799-79 или другие масла имеющие кинематическую вязкость 10-14 сСт при 50°С
Агрегатное состояние
Класс опасности вещества
Предельно допустимая концентрация мгм3
Температурные пределы воспламенения 0С
Категория взрывоопасности смеси
Группа взрывоопасной смеси
Температура вспышки паров 0С
Температура самовоспламенения 0С
Количество вещества на проектируемом объекте кг
Количество вещества выделяющегося в воздух рабочей зоне мгм3 не более
Таблица 6.3 - Характеристика производственного шума
Характеристика реализуемого параметра
Характеристика рабочего места
Рабочее место оператора машины
Механизм привода дискового ножа тянульного вала и привода накатных устройств
Уровни звукового давления на проектируемом участке дБА
Допустимые уровни звукового давления дБА
Мероприятия по достижению нормируемых параметров производственного шума
своевременная смазка механизмов машины замена изношенных деталей
Таблица 6.4 - Характеристика опасности поражения персонала электрическим током
Класс помещения по опасности поражения электрическим током
С повышенной опасностью
Напряжение электрического тока питания электросистем изделия В
Сеть электропривода 380
Мощность источника электрического тока кВт
Тип исполнения электрооборудования
Класс электрооборудования по способу защиты человека от поражения электрическим током
Средства коллективной защиты от поражения электрическим током
Заземление закрытие щитками изоляция токоведущих частей
Способ отключения электрооборудования от сети
Общий рубильник кнопка ”стоп” штепсельные розетки
Сопротивление изоляции токоведущих частей МОм
Удельное сопротивление грунта Ом×м
Нормируемое значение сопротивления защитного заземления Ом
Cопротивление защитного заземления Ом
Индивидуальные средства защиты
Нет из вспомогательных - резиновый коврик
Рассчитаем схему заземления выполненную вертикальными стержнями d=6 см l=25 м грунт – суглинок ρ=100 Ом. Заземляющее устройство предполагается выполнить в виде прямоугольника 2836 м2. Стержни соединены между собой стальной полосой 40×5 мм2 и зарыты на глубину t0=07 м. Коэффициент сезонности Кс=1. Расчёт ведётся по методике изложенной в литературном источнике [24].
Сопротивление растеканию тока для одного вертикального стержневого заземлителя:
Расстояние между стержнями a принимаем равным 4 м.
Определяем предварительно число стержней. Длина соединительной полосы равна периметру прямоугольника м.
Коэффициент использования заземлителей ст=063.
Необходимое число труб для системы заземления при Rзаз=4 Ом:
Сопротивление растеканию соединительной стальной полосы Ом находится по формуле:
где ln – длина соединительной полосы м
d – эквивалентный диаметр d=006 м
Требуемое сопротивление системы заземления:
Таблица 6.5 - Характеристика опасностей при работе машины
на холостом ходу и при обработке деталей
Средства защиты исключающие попадание человека в опасную зону
Способ крепления детали в изделии при ее обработке
Масса обрабатываемой детали кг
Средства механизации при установке креплении и снятии обрабатываемой детали
погрузчик средства механизации к нему
Средства защиты человека при обработке заготовки
от пыли - общая вентиляция
Сухой вручную щёткой
Средства механизации используемые при монтаже ремонте и демонтаже изделия
3 Санитарно-гигиенические мероприятия. Вентиляция. Отопление
При разработке санитарно-гигиенических мероприятий необходимо выбрать соответствующие параметры микроклимата рабочей зоны помещения и предусмотреть для их обеспечения системы вентиляции и отопления. Данные сведены в таблицу 6.7.
Таблица 6.7 - Метеорологические условия на участке. Вентиляция. Отопление
Наименование производственного помещения
Характеристика тяжести работы
Средней тяжести работы категория IIа
Пара-метры микрок-лимата
Температура воздуха рабочей зоны °С
Относительная влажность воздуха %
Скорость движения воздуха мс
Система вентиляции в помещении и на рабочем месте
Приточно–вытяжная естественная
Кратность обмена воздуха ч-1
Система отопления в помещении
Теплоноситель и его параметры
3 Санитарно-гигиенические мероприятия. Освещение
Данные мероприятия сведены в таблицу 6.7.
Таблица 6.7 - Искусственное освещение на участке
Наименование помещения и рабочего места
Раскройный цех рабочее место оператора
Площадь помещения м2
Разряд зрительной работы
Освещенность при рабочем освещении лк
(общее + местное) –750
Освещенность при аварийном освещении: на рабочих местах %
на путях эвакуации лк
Источник питания аварийного освещения
Сеть аварийного освещения
Люминесцентная лампа ЛБ-40
Исполнение светильников
Мощность лампы светильника Вт
Количество светильников шт
- при двухламповых светильниках;
– при трехламповых светильниках
Расчёт количества светильников ведём используя метод светового потока по методике изложенной в литературном источнике [13].
Рассчитаем общее люминесцентное освещение для цеха площадью 5030 м2 имеющего высоту 6 м. Напряжение осветительной сети 220 Вт.
Исходные данные: требуемая освещённость по нормам Ен=300 лк.; коэффициенты использования светового потока n=70% с=50%; hр =08 м hс=05 м; отношение расстояния между светильниками к расчётной высоте подвеса L: h = 15м.
Принимаем светильник с люминесцентными лампами ЛБ–40–4 имеющими световой поток Fл= 3000 лм.
Расчётная высота подвеса:
Оптимальное расстояние между светильниками при многорядном расположении
Светильники размещают в три ряда вдоль помещения.
Индекс площади помещения рассчитывается по формуле:
где А и В – длина и ширина помещения А = 50 м В = 30 м
Нр – высота подвеса светильника Нр = 47 м.
При i=399 коэффициент использования светового потока 50%.
Число ламп находится по формуле:
где N – количество светильников или количество ламп накаливания шт.;
Ен – нормируемая освещённость Ен=300 лк.;
S – площадь помещения S = 1500 м2;
z – коэффициент неравномерности освещения z = 125;
k – коэффициент запаса. Выбирается в зависимости от атмосферы в производственном помещении k = 15;
Fл – световой поток группы ламп в светильнике или лампы накаливания Fл = 3000 лм.;
– коэффициент использования светового потока зависящий от характеристики источника света ограничивающих способностей интерьера помещения кривой распределения света а так же индекса помещения i.
Число светильников в каждом ряду:
- при двухламповых светильниках:
- при трёхламповых светильниках:
4 Мероприятия по пожарной безопасности
Данные мероприятия сведены в таблицу 6.9.
Таблица 6.9 - Пожарная безопасность. Молниезащита
Класс помещения по пожароопасности
Категория производства по пожароопасности
Характеристика материалов стен по сгораемости
Характеристика материалов перекрытий по сгораемости
Степень огнестойкости стен здания и их огнестойкость ч
Расстояние от рабочего места до эвакуационного выхода м не более
Средства пожаротушения
Пожарный щит вода огнетушители
Категория молниезащиты здания
Сопротивление заземляющего устройства Ом
5 Компенсация профессиональных вредностей. Индивидуальная защита. Личная гигиена
Данные мероприятия сведены в таблицу 6.10
Таблица 6.10 - Компенсация профессиональных вредностей. Средства индивидуальной защиты. Личная гигиена
Продолжительность рабочей недели ч
Дополнительный отпуск дни
Пенсионный возраст лет
Обеспечение лечебно-профилактическим питанием
Халат (хлопчатобумажный)
Индивидуальные средства защиты органов зрения
Индивидуальные средства защиты головы
Средства обеззараживания кожи
Метод обеззараживания кожи
При разработке машины для разрезания на полосы текстильных материалов были учтены общие требования безопасности труда и промышленной экологии а также действующие санитарные нормы и правила нормы пожарной безопасности нормы электробезопасности Республики Беларусь.
6 Промышленная экология
Среди различных показателей целесообразности внедрения в производство проектируемой машины различают показатели экологии охраны труда и окружающей среды. Дипломное проектирование предусматривает анализ таких показателей выявление возможных несоответствий их допустимым значениям а также проведение мер по ликвидации таких несоответствий.
Производится проектирование машины для разрезания на полосы текстильных материалов. Климатическое исполнение машины - УХЛ4 и 04 (при поставке машин в районы с тропическим климатом по ГОСТ 15150).
Учитывая что применение машины для разрезания на полосы текстильных материалов предназначено для производства ламелей для вертикальных и горизонтальных жалюзи следует заметить что сырье недефицитное и доступное для предприятий республики. На все виды обрабатываемого сырья есть сертификаты качества. Что касается самого машины МРТ то для ее конструирования требуются металлы сплавы полимеры (в основном сталь 45 40Х сплав Д16 полиамид) которые также являются недефицитными и доступными материалами.
В процессе раскроя изделий в воздух выделяется незначительное количество мелкодисперсной пыли (результат разрушения волокон полиамидных волокон ГОСТ 6309-93). Её количество соответствует требованиям санитарных норм. Поэтому дополнительные средства для пылеулавливания не предусматриваются. Достаточно естественной приточно-вытяжной вентиляции.
Вода в процессе не используется следовательно не загрязняются и водные ресурсы.
По окончанию срока службы машины все детали и узлы перерабатываются на месте их образования или на других предприятиях имеющих соответствующую технологию. Лом и отходы черных и цветных металлов отличаются от других видов отходов тем что они представляют собой особо дорогостоящее сырье. Образующийся при ликвидации швейных машин лом черных металлов сдается в организацию «Вторчермет». Лом цветных металлов сдается в организацию «Белцветмет». Требования к лому сдаваемому на утилизацию регламентируются ГОСТ 1639-78 «Лом и отходы металлов и сплавов».
В конструкции используется масло И-12А по ГОСТ 20799-88 (агрегатное состояние жидкое класс опасности 4 количество вещества в объекте 05 кг предельной допустимой концентрации не более 5 мгм2 группа взрывоопасности смеси Т3) или другие аналогичные по назначению масла имеющие кинематическую вязкость 10-14 сСт при 50°С. Масла и смазки применяемые в машинах предназначенных для районов с тропическим климатом должны соответствовать ГОСТ 15156-84.
В соответствии с рядом принятых постановлений и директивных органов все предприятия и организации обязаны осуществлять сбор учет и сдачу отработанных нефтепродуктов. Отработанные масла перерабатываются с целью получения масляных компонентов. Наиболее перспективным и рациональным направлением использования отработанных масел является их переработка на масло перегонных заводах с получением отдельных компонентов для повторного использования. К методам обработки масел относятся отстаивание центрифугирование фильтрация вакуумная перегонка и т.д.
Остальные материалы такие как пластмассы также подлежат переработке либо утилизации.
Экологическая экспертиза внедряемого проекта показала что машина для разрезания на полосы текстильных материалов не загрязняет окружающую среду и является экологически безопасным.
В результате проведенного дипломного проектирования рассмотрены все поставленные вопросы и задачи.
Во «Введении» проведено обоснование необходимости разработки полуатомата для разрезания на полосы текстильных материалов.
В разделе «Обзор литературы» рассмотрены различные машины и полуавтоматы предназначенные для раскроя рулонов как цельных так и предварительно разматываемых.
В «Проектной части» дипломного проекта разработаны пространственная кинематическая схема проектируемой машины пневмогидравлическая схема управления полуавтоматом аргументирован выбор метода раскроя спроектированы нож и ножевое устройство.
Раздел «Расчетная часть» посвящен расчетам технологических усилий машины – усилия резания. Проведен расчет привода дискового ножа рассчитаны параметры гидропривода. Определено высокое значение теоретической производительности.
В разделе дипломного проекта «Технология машиностроения» составлен технологический процесс изготовления детали входящей в конструкцию люльки проведены расчеты уравнений размерных цепей режимов резания составлены операционные карты и операционные эскизы.
В «Экономической части» определен экономический эффект от внедрения спроектированной машины на производство.
Раздел «Охрана труда и промышленная экология» связан с рассмотрением вопросов касающихся отдела «Охраны труда и промышленной экологии» предприятия с учетом использования в производстве проектной машины.
Базюк Г.П. Резание и режущий инструмент в швейном производстве. – М.: Легкая индустрия 1980.
Вальщиков Н.М. Зайцев Б.А. Вальщиков Ю.Н. Расчет и проектирование машин швейного производства. – Л.: Машиностроение 1973.
Вредные вещества в промышленности: Справочник для химиков инженеров и врачей. В 3-х т.Под ред. Н.В.Лазарева. Э.Н. Левиной.-7-е изд. перераб. И доп.- Л.: Химия1976 .
Гидравлика и гидропневмопривод. В 2-х частях. Ч.2: Гидравлические машины и гидропневмопривод: учебник под ред. А.А. Шейпака. – М.:МГИУ2007.
ГОСТ 12566-88. Изделия швейные бытового назначения. Определение сортности.
ГОСТ 20521-75. Технология швейного производства (Термины и определения).
ГОСТ 4103-82. Изделия швейные. Методы контроля качества.
ГОСТ 9176-77 Изделия трикотажные. Методы испытания швов.
Детали машин в примерах и задачах: Учеб. пособие Под общ. ред. С.Н. Ничипорчика. – 2-е изд. – Мн.: Выш. школа 1981.
Иванов М.Н. Детали машин. – М.: Высшая школа 1984.
Кнорринг Г.М. Осветительные установки. - Л.: Энергоиздат Ленингр. Отд-ние1981.
Краснощеков Л.Ф. Расчет и проектирование воздухонагревательных установок для систем приточной вентиляции. - Л.: Стройиздат 1972.
Курсовое проектирование деталей машин: Справ. пособие. Часть 1А. В. Кузьмин Н. Н. Макейчик В.Ф. Калачев и др. – Мн.: Выш. школа 1982.
Курсовое проектирование деталей машин: Справ. пособие. Часть 2А. В. Кузьмин Н. Н. Макейчик В.Ф. Калачев и др. – Мн.: Выш. школа 1982.
Новичихина Л.И. Справочник по техническому черчению. – Мн.: Выш. школа 1976.
Оборудование швейного производства. Вальщиков Н.М. Шарапин А.И. Идиатулин И.А. Вальщиков Ю.Н. – М.: Легкая индустрия 1977.
Охрана труда в машиностроении:Учеб. для студ. машиностроит. спец. ВУЗов Е.Я.Юдин С.В.Белов С.К.Баланцев и др.; Под ред. Е.Я.Юдина С.В.Белова.-2-е изд. перераб. и доп. - М.: Машиностроение 1983.
ОСТ 17-835-80. Изделия швейные. Технические требования к стежкам строчкам и швам.
Полтев М.К. Охрана труда в машиностроении: Учеб. для студ. машиностроит. спец. ВУЗов.- М . : Высш. шк. 1980.
Правила устройства электроустановок Минэнерго СССР.- 6-е изд. перераб. и доп. - М .: Энергоатомиздат 1987.
Савостицкий А. В. Меликов С. Х. Технология швейных изделий Под редакцией А. В. Савостицкого. – М.: Легкая и пищевая промышленность 1982.
Справочник химика: в 3-х т. - 2-е изд. перераб. и доп.-М. - Л.: Госхимиздат 1963.
ССБТ. ГОСТ 12.1.005-88.Общие санитарно-гигиенические требования к воздуху рабочей зоны. - М.: Издательство стандартов 1988 .
ССБТ. ГОСТ 12.1.006-84. Электромагнитные поля радиочастот. Допустимые уровни на рабочих местах и требования к проведению контроля. - М.: Издательство стандартов 1984.
ССБТ. ГОСТ 12.1.007-76. Вредные вещества. Классификация и общие требования безопасности. - М.: Издательство стандартов 1976 .
ССБТ. ГОСТ 12.1.011-78. Смеси взрывоопасные. Классификация и методы испытаний. - М.: Издательство стандартов 1978.
ССБТ. ГОСТ 12.2.007.0-75. Изделия электротехнические. Общие требования безопасности. - М.: Издательство стандартов 1977.
ССБТ. ГОСТ 12.4.011-89. Средства защиты работающих. Общие требования и классификация. - М.: Издательство стандартов 1989.
ССБТ. ГОСТ 12.4.034-85. Средства индивидуальной защиты органов дыхания. Классификация и маркировка. - М.: Издательство стандартов 1985.
Экономика машиностроительного производства И.М. Бабук Э.И. Горнаков Б.И. Гусаков А.М. Панин. Под общ ред. И. М. Бабука. – Мн.: Вышейшая школа 1990.
Рисунок 1.5.doc
Рисунок 1.12 – Кинематическая схема полуавтомата для раскроя рулонов ткани
Рисунок 3.2 – Кинематическая схема полуавтомата для раскроя рулонов ткани
3 Расчетная часть.doc
1.1 Определим Vн – скорость дискового ножа.
1.2 Определим скорость резания Vр.
Скорость поперечной подачи Vп является скоростью движения штока гидроцилиндра поперечной подачи. Скорость резания (см. рисунок 3.1) определится по формуле
Схема взаимодействия ножа и рулона приведена на рисунке 3.2.
Рисунок 3.1 – План скоростей
Рисунок 3.2 – Схема взаимодействия ножа и рулона
1.3 Для определения усилия подачи ножа на материал мощности подачи ножа момента вращения ножа и мощности вращения ножа составим уравнения сил для материала и для ножа. Схемы сил действующих на рулон материала и на дисковый нож представлены на рисунках 3.3 3.4
где о – конструктивный угол резания
р – рабочий угол резания
N1 – сила нормального давления материала на нож (или нормальная реакция давления ножа на материал для рис. 3.4) Н
F1 – сила трения материала о боковые грани ножа (или сила трения ножа о материал для рис. 3.4) Н
N2 – сила нормального давления материала на подшипники главного вала Н
F2 – сила трения в подшипниках главного вала Н
N3 –нормальная реакция подшипников ножа Н
F3 – сила трения в подшипниках ножа Н
Pp – усилие поперечной подачи ножа Н
Pн - сила от момента вращения ножа Н.
Np – мощность поперечной подачи ножа Н
Nн - мощность вращения ножа Н
f1 - коэффициент скольжения материала о боковые грани ножа f1=095 [1 c. 78]
f3 - коэффициент трения качения в подшипниках ножа f1=001 [1 c. 78]
Из динамики резания дисковым ножом получаем следующие формулы для расчета необходимых усилий и мощностей:
В свою очередь нормальная реакция давления ножа на материал составит
где q – удельное усилие резания Нм [1 c.50];
L – средняя линия резания м примем
k1 – коэффициент учитывающий притупление кромки ножа [1 c.50];
k2 – коэффициент учитывающий влияние угла заострения на усилие резания [1 c.50];
Рисунок 3.3 – Схема сил действующих на рулон ткани
Рисунок 3.4 – Схема сил действующих на дисковый нож
1.4 Расчет клиноременной передачи
Для передачи крутящего момента от электродвигателя к дисковому ножу в проектируемом приводе используется клиноремённая передача.
Исходя из номограммы условий работы ремня выбираем тип сечения А [9 c.146].
Крутящий момент на ведущем шкиву:
Диаметр ведущего шкива рассчитываем по формуле:
Принимаем диаметр шкива равным d1 = 71 мм.
Диаметр ведомого шкива рассчитывается по выражению:
где – коэффициент проскальзывания ремня.
Выбираем диаметр ведомого вала равным d2=140 мм и уточняем передаточное отношение ремённой передачи:
Минимальная величина межосевого расстояния:
amin = 055·(d1 + d2) + T0 = 055·(71+140)+105 = 127 мм
где T0 – высота сечения ремня для выбранного типа сечения [9 c. 147].
Максимальная величина межосевого расстояния [9 c. 144]:
amax =2 (d1 + d2)=2(71+ 140) = 422 мм.
Принимаем величину рабочего межосевого расстояния aр=400 мм. Расчётная длина ремня составляет [9 c. 144]:
Принимаем величину длины ремня из стандартного ряда по ГОСТ 1284.1-80 равной L=1120 мм. Уточняем значение межосевого расстояния по формуле [9 c. 145]
где w = 05··(d1 + d2) = 05··211 = 331 мм;
y = (d2 – d1)2 = (140 – 71)2 = 4761 мм2.
При монтаже передачи необходимо обеспечить возможность уменьшения межосевого расстояния на 001·L=11 мм для облегчения надевания ремней на шкивы и возможность его увеличения на 0025·L=28 мм для увеличения натяжения ремней.
Произведём расчёт силовых характеристик ремённой передачи. Угол обхвата меньшего шкива составит:
Коэффициент угла обхвата C =09 [9 c. 151];
коэффициент режима работы CP =10 (легкий режим) [9 c. 151];
коэффициент учитывающий влияние длины ремня CL =0 92[9 c. 151];
коэффициент учитывающий число ремней Cz =075 [9 c. 151].
Необходимое число ремней в передаче вычисляется по выражению:
где P0 – мощность допускаемая для передачи одним ремнём
P0 = 088 кВт [9 c. 152].
принимаем число ремней равное z=2.
Предварительное натяжение ветвей клинового ремня
где v – окружная скорость ведущего шкива
– коэффициент учитывающий центробежную силу =018 Н·с2м2.
Сила действующая на валы:
Fв = 2·F0·z·sin(12) = 2·117·3·sin(170°2) = 699 Н.
Ширина обода шкива находится по формуле:
Bш= (z–1)·e + 2f = (3–1)·15 + 2·10 = 50 мм
где e=15 мм f=10 мм – размеры канавок [9 c. 152].
1.5 Расчет мощности привода
Режим нагружения ротора электродвигателя – непрерывный.
Мощность приводного двигателя определяется по формуле
– общий КПД привода.
Так как движение передается рабочему органу передается только клиноременной передачей то
Тогда мощность двигателя будет равна
Угловая скорость вращения двигателя определяется по формуле где n0 - синхронная частота вращения ротора.
По рассчитанным значениям подбираем электродвигатель 4А80В693 1М 3081 ГОСТ 19523-81 (N=11кВт n=920 мин-1).
2 Расчет усилий подачи и определение параметров гидроцилиндра привода отрезной головки
Дисковый нож 1 (рисунок 2.1) получает поперечную подачу от гидроцилиндра 10. Усилие подачи определяется по формуле
где Fт - сила тяжести каретки дискового ножа Fт=1375Н;
f – коэффициент скольжения каретки по направляющим f=04;
Fр - сила резания Н
Тогда Fп=137504+75=625Н.
Исходными данными для расчета параметров гидроцилиндра поперечной подачи являются
давление в системе pн=4МПа
скорость перемещения Vп=0125 мс
усилие перемещения Рр=625Н.
Диаметр поршня гидроцилиндра определяется по формуле
где k – коэффициент запаса (k=15-2)
φ0 – соотношение между диаметром поршня и штока гидроцилиндра (φ0=03-05).
Тогда по стандартному ряду DП=25 мм тогда диаметр штока составит
Рабочий ход поршня равен величине максимального отклонения кромки материала то есть Δ=20 мм тогда длина внутренней полости гидроцилиндра составляет где λ – толщина поршня.
Расход гидроцилиндра определится
Диаметр стенок гидроцилиндра определится из условия для стали 20Х
Тогда наружный диаметр гидроцилиндра составит
3 Расчет усилий перемещения отрезной головки и определение мощности двигателя привода для позиционирования отрезной головки
Перемещение отрезной головки по направляющему валу вдоль рулона осуществляется с помощью гидромотора 12 через ходовой винт 11 (рисунок 2.1). Усилие продольной подачи определяется по формуле
Fп=Fтf где Fт - сила тяжести каретки дискового ножа Fт=2400Н;
f – коэффициент скольжения каретки по направляющим f=04.
Тогда Fп=240004=960Н.
Для начала проведем расчет винтовой передачи.
3.1 Выбираем материалы:
Винта – сталь 18 ХГТ азотированный [14 с.29-30];
Гайка - бронза Бр ОФ-10-1 [14 с.29-30].
3.2 Определяем допускаемые напряжения:
Допускаемое давление в резьбе [q]=10МПа;
[t]=40МПа – напряжение на срез;
[sсм]=80 МПа – напряжение на смятие;
[sр]=40 МПа – напряжение на растяжение;
[s]=sт[n] - напряжение на растяжение и срез;
sт=400 МПа – предел текучести;
[n]=3- коэффициент запаса;
3.3 Выбираем профиль резьбы –трапецеидальная.
yН=05 - коэффициент высоты гайки [14 с.30]; принимаем гайку цельную.
3.4 Из условия обеспечения износостойкости определяем средний диаметр резьбы [14 с.30]
где Fa – осевое усилие передачи Н Fa=Fп=960Н;
yh – коэффициент высоты резьбы для трапецеидальной yh=05 [14 с.30].
Исходя из конструктивных соображений принимаем диаметр трапецеидальной резьбы равным d=40 мм шаг t=12мм с числом заходов P=4[14 таблица 2.3].
3.5 Определяем угол подъема винтовой линии по формуле [14 с.31]:
g=arctg(t·Pp·d2)=arctg(12·4314·37)=0392 рад.
3.6 Определяем приведенный угол трения r[14 с.31]:
где f=01 - коэффициент трения скольжения;
d=150 - угол наклона рабочей стороны профиля резьбы;
3.7 Определяем к.п.д. передачи с учетом потерь в опорах и в резьбе [14 с.31]:
где h=tggtg(g+r)=tg(0392)tg(0392+0103)=0766.
hв.п.=095·h=095· 0766=0728.
3.8 Определяем требуемую мощность для вращения винта [14 с.32]
N=Fa·v1000·h=960·01251000·0728=0165 кВт
3.9 Определяем необходимое число оборотов винта:
nвр=60·v2t·p=(60·125)(12·4)=156 мин-1;
Проверочный расчет винт-гайка.
Основным критерием работоспособности передачи является износостойкость которая оценивается по среднему давлению между витками резьбы винта и гайки [14 с.30]
где Н1 – рабочая высота профиля мм
определяется для трапецеидальной резьбы Н1=05t=0512=6мм [14 с.30];
z – число витков резьбы в гайке определяется по формуле z=Hгt
где Нг – высота гайки.
3710 винт удовлетворяет условию .
где Т – крутящий момент Нм
определяется Т=05d2Fatg(g+r)=0537960tg(0392+0103)=959Нм.
4133 винт удовлетворяет условию прочности.
По полученным значениям частоты вращения и необходимой мощности подбираем роторный гидромотор 4МГ 15-13 [4 c. 273].
4 Расчет привода вращения рулона и определение мощности приводного двигателя
Расчет ведется для главного вала представленного позицией 15 на рис. 2.2. Для обеспечения необходимой динамики намотки рулона на главный вал должно обеспечиваться условие где МКР – крутящий момент на валу; k – коэффициент запаса примем равным 12; МС – момент сил сопротивления. В свою очередь момент сил сопротивления составляет сумму моментов сил трения и моментов сил инерции .
Момент сил инерции рассчитывается
Момент сил трения определится с учетом радиальной составляющей реакции в шарикоподшипнике
Тогда требуемый крутящий момент должен быть не меньше .
Кинематическая схема привода представлена на рисунке 3.2. Режим нагружения ротора электродвигателя – непрерывный.
где Мн – номинальный момент развиваемый на валу электродвигателя Нм;
– синхронная угловая скорость ротора;
где n0 - синхронная частота вращения ротора
По рассчитанным значениям подбираем электродвигатель 4А90С987 1М 3081 ГОСТ 19523-81 (N=16кВт n=1000 мин-1).
5 Расчет параметров пневмоцилиндров равнения кромки
В системе управления полуавтоматом применяются два пневмоцилиндра (поз. 25 28 на рисунке 2.2) для равнения кромки устройства размотки рулона и устройства раскатки рулона. Пневмопривод имеет следующие преимущества по отношению к гидроприводу: более высокая скорость перемещения поршня (02 05мс); отсутствуют утечки масла которое способно загрязнить рабочее место; более низкая стоимость из – за отсутствия индивидуальной насосной станции и менее высоких требований к качеству аппаратуры пожаро- и взрывобезопасность.
Основными недостатками пневмопривода по сравнению с гидроприводом: небольшие усилия на штоке (20 60Нсм2); неравномерное движение поршня при изменяющейся на штоке нагрузке за счет сжимаемости воздуха; более низкий КПД за счет утечек сжатого воздуха.
Структура пневмопривода. Носителем механической энергии в пневмоприводе является сжатый воздух. На промышленных предприятиях имеются компрессорные станции которые осуществляют централизованное снабжение всех технологических устройств и оборудования. Разводка воздуха осуществляется по магистральным трубопроводам связывающим емкость наполненную сжатым воздухом (ресивер) с потребителями сжатого воздуха.
Выбираем давление воздуха в рабочей полости пневмоцилиндра Рм(20 30 40 50 60)Нсм2 принимаем Рм =50Нсм.
Определяем диаметр D пневмоцилиндра по формуле
где к – коэффициент запаса равный 15 2 и учитывающий потери трения на уплотнениях падение давления за счет утечек воздуха.
рпол – максимальное усилие на штоке Н определяется Рпол=mgf+ma= mgf+mΔVΔt= Fрf+m(V2-V1)Δt
где m – масса передвигаемой части устройства размотки кг
f – коэффициент трения скольжения вала размотки в направляющих f=018 [14 c.224]
a – ускорение разгона штока пневмоцилиндра мс2
V2 – скорость установившегося движения штока мс
V1 – скорость движения штока в начале разгона мс
Δt – время разгона штока с.
Рпол=mgf+ma=880018+88(005-001)05=484Н.
ра – 981 Нсм2 – давление атмосферное.
Полученное по формуле значение диаметра в (мм) округляют до ближайшего из ряда стандартных по ГОСТ 6540 – 64. В этом ряду имеем следующие значения 5 10 12 16 20 25 32 40 50 63 80
Из имеющихся значений берем 63 мм.
Из конструкторских соображений выбираем диаметр d= =(02 03)D полученное значение округляем до приведенного выше ряда.
d=025×63=1575мм. Принимаем d=16мм.
Определяем параметры трубопроводов dтр исходя из уравнения неразрывности потока сжатого воздуха
где V – рекомендуемая скорость течения воздуха в трубах мс; Vp – средняя скорость движения поршня в течении такта мс
Vp =40-(Рм-10)2490=293мс
V = Lt где L – ход поршня а t – необходимое время
Принимаем по стандартному ряду ГОСТ 6540 – 64 dтр=5мм.
Определяем расход воздуха в цепи приведенной к атмосферному давлению
Подбираем пневмоаппаратуру: фильтр-влагоотделитель 22У 16×80 УХЛ4 ГОСТ 17437-81 глушитель шума П-ГII16063 УХЛ4 маслораспылитель В44-14 УХЛ4 пневмодроссели 06-2 УХЛ4ГОСТ 19485-81 пневмораспределители ПВ64-23М клапан 122-16 УХЛ4.
6 Расчет производительности полуавтомата
При расчете производительности следует определить время затрачиваемое на получение одной бобины. Для этого зададимся данными:
ширина рулона составляет b=2м;
диаметр рулона D=036м;
ширина бобины a=004м;
метраж материала в рулоне
скорость раскатки (размотки) рулона Vраз =
скорость поперечной подачи ножа Vрез=0125мс;
скорость продольной подачи ножа Vпр=003мс;
время установки рулона на вал размотки (раскатки) tуст=275мин;
время съема одной бобины tсъем=10с.
Время на изготовление bа бобин со всего рулона составляет
где tраз – время раскатки (размотки) рулона;
tрез – время резания одной бобины;
tпр – время продольной подачи от одной линии резания к другой.
Тогда время на изготовление одной бобины составляет
Производительность полуавтомата составляет
7 Расчет на прочность детали конструкции
В графической части имеется чертеж вала РП-1600.01.028. Вал представляет собой вал крепления дискового ножа с помощью прямобочного шлицевого соединения. На валу также крепятся два фланца и шкив клиноременной передачи. Проведем расчет на прочность различных элементов конструкции вала: шпоночного соединения шлицевого прямобочного соединения.
7.1 Расчет шпоночного соединения на валу
Передача крутящих моментов от шкивов на валы осуществляется посредством шпонок. В связи с этим необходимо проверить прочностные свойства шпоночных соединений на смятие по наиболее нагруженной шпонке. Рассматриваемая шпонка имеет размеры bhl=161127 мм глубина паза t1=5 мм. Передаваемый крутящий момент T2= T1i=114×102=57Нм.
Проверим по условию прочности на смятие шпонки
Шпонка условию прочности на смятие удовлетворяет.
Проверим по условию прочности на срез шпонки
Шпонка условию прочности на срез удовлетворяет.
7.2 Расчет шлицевого прямобочного соединения на валу
Шлицевые соединения с зубьями прямобочного профиля в соответствии с ГОСТ 21425-75 рассчитываются на смятие и износ что соответствует их основным предельным состояниям.
Условие прочности на смятие выглядит
где – среднее давление на рабочих плоскостях МПа;
Т – передаваемый крутящий момент Нмм;
SF - удельный суммарный статический момент площади рабочих поверхностей соединения относительно оси вала мм3мм;
где dср – средний диаметр шлицевого соединения мм;
h - рабочая высота зубьев мм;
l – рабочая длина соединения
РПЗ.doc
Анализ технической литературы и патентных материалов по оборудованию для раскроя длинномерных изделий
1 Проектирование кинематической схемы полуавтомата для раскроя рулонов на полосы
2 Проектирование пневмогидравлической системы управления
1 Расчет технологических усилий резания и определение мощности двигателя привода ножа
2 Расчет усилий подачи и определение параметров гидроцилиндра привода отрезной головки
3 Расчет усилий перемещения отрезной головки и определение мощности двигателя привода для позиционирования отрезной головки
4 Расчет привода вращения рулона и определение мощности приводного двигателя
5 Расчет параметров пневмоцилиндров равнения кромки
6 Расчет производительности
7 Расчет деталей на прочность
Технологическая часть
1 Описание конструкции детали
2 Технологический процесс изготовления детали
2.1 Методы обработки поверхностей детали
2.2 Дифференциация операций и базирование
3 Размерный анализ технологического процесса
4 Составление и решение уравнений размерных цепей
Технико-экономический расчет
Охрана труда и промышленная экология
2 Характеристика машины
3 Санитарно-гигиенические мероприятия
4 Мероприятия по пожарной безопасности
5 Компенсация профессиональных вредностей. Индивидуальная защита
6 Промышленная экология
Введение и обоснование темы проекта
В швейной промышленности среди раскройного оборудования имеется множество машин для раскроя настилов ткани однако операция раскроя рулонов на полосы или бобины менее механизирована как в этом можно убедиться из обзорной части дипломного проекта. Наиболее распространенным среди отечественного оборудования раскроя рулонов материала является полуавтомат РП-1600 сконструированный минским ЭКТБ КФП в 1985 году. Поэтому назрела необходимость в создании отвечающего современным условиям и техническим требованиям оборудования для раскроя рулонов на основании имеющейся базы.
Целью дипломного проекта является проектирование кинематической и пневмогидравлической схем полуавтомата для раскроя рулонов ткани на бобины проектирование конструкции отрезной головки проведение проектных и поверочных расчетов для определения целесообразности конструкции. Помимо этих целей требуется спроектировать технологический процесс изготовления детали конструкции полуавтомата провести расчет экономического эффекта полуавтомата провести анализ соответствия проектируемого полуавтомата требованиям охраны труда и промышленной экологии.
Среди оборудования для раскроя рулонов имеется разнообразные устройства машинного полуавтоматического или автоматического действия.
По патенту ФРГ № 3710454 кл. D 06 Н 702 1987 описан станок для резки рулонного полотна.
На рисунке 1.1 представлен станок общий вид; на рисунках 1.2 и 1.3 - разрез А-А на рисунке 1.1 соответственно начало резки и конец резки.
На станине 1 установлены раскаточные (тормозные) головки 2 и головка 3 (приводная) для закрепления квадратной оправки 4 с резиновыми шайбами 5. Привод 6 имеет цепную передачу 7 кинематически связанную с головкой 3.
Рычаги 8 закрепленные на осях 9 и образующие поджимной несущий кронштейн имеющий два пневмоцилиндра 10 и оправку 11 для держателей 12 ножей 13 с их фиксаторами 14. На оправке 11 закреплены подвижно два роликодержателя 15 с парой эксцентричных опорных роликов 16 (эксцентриситет 3мм) с подшипниками 17 на осях 18. Фиксатор 19 крепит роликодержатели за счет паза 20 в оправке 11 которая в свою очередь крепится к рычагам 8 болтами 21 как и штанги 22 для пневмоцилиндров 10.
Исходный рулон устанавливается в раскаточных головках 2 а конец полотна (ткани) наматывается на резиновые шайбы 5 одетые на оправку 4 приводной головки 3. Роликодержатели 15 фиксируются по краям ткани на оправке 11 с помощью фиксаторов 19 а ножедержатели 12 устанавливаются по необходимой ширине нарезаемых полос ткани и фиксируются винтами 14. Вылет ножей 13 (величина врезания в рулон ткани) должен быть 5-7мм относительно касания роликов 16 поверхности разрезаемого рулона т.е. эксцентриситет роликов равный 3 мм не перекрывается.
Включается привод 6 вращения оправки 4 разрезаемого рулона и одновременно подается воздух на пневмоцилиндры 10 которые прижимают оправку 11 ножедержателей и роликов к вращающейся оправке 4 с резиновыми шайбами 5 на закаточной головке 3 при этом ролики 16 упираются в навиваемую ткань а ножи 13 прорезают эту ткань по заданной ширине.
Процесс резания ткани осуществляется посредством колебательного движения ножей 13 за счет эксцентричности опорных роликов.
Это обеспечивает оптимальный режим резания ткани в момент ее намотки в рулон с небольшими усилиями на ножах поскольку они погружаются в прорезанный паз разрезая только один слой ткани. Лезвие ножа работает не одной точкой а определенной зоной так что стойкость его увеличивается и сохраняется чистота реза и ровная кромка.
После разрезания рулона он снимается с оправки 4 а набор резиновых шайб 5 позволяет легко разделить нарезанные бухты из рулона.
Плоские ножи практически разрезают один слой ткани при своем колебательном движении за счет эксцентриситета роликов. Лезвия ножей работают не одной точкой а некоторым участком по длине равным величине эксцентриситета роликов. Разрезать можно рулоны практически всех размеров а нарезанные ленты автоматически удерживаются между ножами т.е. сохраняется ровность намотки. Деформация ткани отсутствует так как усилия резания минимальные.
Рисунок 1.1 – Конструктивно-кинематическая схема станка для резки рулонов ткани
Рисунок 1.2 – Кинематика резания в начале резки
Рисунок 1.3 – Кинематика резания в конце резки
Рисунок 1.4 – Взаимодействие дискового ножа и раскраиваемого материала в момент резания
Кинематическая схема транспортной части полуавтомата представлена на рисунке 1.5 где позициями обозначены: 1 – раскатное устройство 2 – обводное устройство 3 – обводное устройство 4 – обводной ролик 5 – устройство вала выдавливания 6 – дисковый нож (устройство ножа на рисунке 2.1) 7 – обводной ролик 8 – устройство тянульного вала 9 – обводной ролик 10 – верхнее накатное устройство 11 – нижнее накатное устройство. Следует заметить что использование двух накатных устройств улучшает процесс резания поскольку накатные устройства направляют разрезаемые соседние ламели в разные стороны.
Схожий транспорт и механику резания имеет устройство для продольного разрезания рулонного полотна (описание изобретения SU 10525920 авторское свидетельство СССР №151291) содержащее рулонодержатель барабаны для намотки лент ножевой валик с набором дисковых ножей и пары прижимных валиков (рисунок 2.6). Особенность устройства состоит в том что с целью расширения технологических возможностей за счет получения лент разной ширины оно имеет смонтированную перед ножевым валиком по направлению перемещения полотна направляющую плиту 13 (рисунок 1.7 1.8) с продольными пазами 18 расположенными между дисковыми ножами 5 и валик 16 с набором клиновидных прижимов 17 размещенных над пазами направляющей плиты и подпружиненных к ней с помощью пружины 15 закрепленной в кронштейне 14.
Рисунок 1.6 – Конструктивно-кинематическая схема устройства для резки рулонов ткани
Рисунок 1.7 – Взаимодействие ножей и материала
По авторскому свидетельству СССР № 914290 кл. B 29 С 1714 1980 описано устройство для продольной резки ленты полимерного материала. На рисунке 1.8 дано устройство в начальный момент резки ленты вид сбоку на рисунке 1.9 — устройство в момент окончании резки общий вид; на рисунке 1.10 — устройство общий вид; на рисунке 1.11 — сечение А-А на рисунке 1.9 (в зоне радиусной кромки ножа) и сечение Б-Б на рисунке 1.9 (в зоне острой кромки ножа).
Устройство состоит из основания 1 на оси которого размещен барабан 2 с подложкой 3 и шарнирно закреплены поводки 4. На втором конце поводков 4 соосло установлены следящий ролик 5 контактирующий через подложку 3 с разрезаемым материалом на приемном барабане 6. На поводках 4 на оси 7 установлены с возможностью поворота вокруг них ножи 8 в виде двуплечих рычагов огибающих приемный барабан 6. На наружной поверхности криволинейного плеча 9 выполнена режущая кромка 10 которая состоит их радиусного участка 11 и заостренного участка 12 расположенного на конце. Второе плечо 13 шарнирно соединено с тягой 14 установленной на основании 1 и является звеном подвижного четырехугольника. Следящий ролик 5 установлен между ножами 8 на оси 7.
Рисунок 1.8 – Конструктивно-кинематическая схема устройства для резки рулонов ткани
Форма режущей кромки 10 ножа 8 определяется из условия постоянства угла резания и минимального расстояния зоны резания от приемного барабана 6. Пружина 15 одним концом соединена с поводком 4 а другим — с основанием 1 и служит для прижатия следящего ролика 5 к барабану 6 установленному на кронштейне 16.
Устройство работает следующим образом.
Ленту материала 17 и подложку 3 закрепляют на приемном барабане 6. При этом ножи 8 острым участком 12 прорезают материал 6 а подложка 3 проходит под следящим роликом 5. Пружина 15 прижимает поводки 4 вместе со следующим роликом 5 к барабану 6 которому затем придают вращательное движение например от электродвигателя (не показан).
Лента материала 17 движется от подающего барабана (не показан) на приемный барабан 6 перед которым происходит его резка на полосы радиусным участком 11 ножа 8.
При возможном заедании или соединении уточных нитей в жгут материал 17 поднимается по радиусному участку 11 разрезается на заостренном участке 12 и возвращается и исходное положение.
Минимальное расстояние до точки укладки материала 17 на подложку 3 намотанную на барабан 6 и перемещение точки реза на режущей кромке ножа обеспечиваются в предлагаемом устройстве следующим образом.
Ролик 5 находится в постоянном контакте с подложкой 3 за счет усилия пружины 15 воздействующей на поводок 4 который вместе с ножами 8 поворачивается по мере увеличения диаметра приемного барабана 6. Кроме того за счет поворота ножей 8 вокруг оси следующего ролика 5 посредством подвижного четырехугольника производится коррекция положения ножа 8 при изменении диаметра приемного барабана б с целью обеспечения минимального расстояния от ножа 8 до подложки 3 и перемещения точки реза по режущей кромке ножа. Второе плечо 13 ножа 8 необходимо для соединения подвижного четырехугольника.
В случае его отсутствия с изменением диаметра приемного барабана изменяется расстояние между ножом и подложкой и точка реза не перемешается по режущей кромке ножа.
Длина элементов подвижного четырехугольника определяется исходя из реальной конструкции устройства и разности диаметров приемного барабана.
Таким образом в предлагаемой конструкции изобретения предусмотрено минимальное расстояние от ножа до барабана что обеспечивает повышение качества укладки материала и перемещение точки реза по кромке ножа улучшающее качество резания при налипании связующего на режущую кромку ножа. Кроме того предотвращается осевое смещение слоев и расслоение продольных волокон ленты за счет того что производится точная намотка ленты на приемный барабан устраняется возможность перерезания продольных волокон и лента материала получается с эквидистантными и ровными краями.
Рисунок 1.9 – Схема резания
Рисунок 1.10 – Общий вид устройства
Рисунок 1.11 – Сечения кромок ножа
Кинематическая схема отрезной головки полуавтомата РП-1600 для разрезания рулонов сконструированного минским ЭКТБ КФП в 1985 году представлена на рисунке 1.12. Вращение дисковый нож 1 получает от двигателя 5 через клиноременную передачу (шкивы 2 4 ремень 3). Заточка дискового ножа производится шлифовальным кругом 6 получающим движение от двигателя 7. Подвод заточного устройства к ножу обеспечивается винтом 8. Поперечная подача ножа осуществляется от гидроцилиндра 10 который перемещает каретку 9 с ножевым устройством. Продольную подачу ножа обеспечивает двигатель 13 который передает движение отрезному устройству с помощью червячной передачи 11-12 и винтовой передачи 14.
Рисунок 1.12 – Кинематическая схема отрезной головки
Для примера использования различной конфигурации ножей рассмотрим некоторые виды передвижных раскройных машин применяемых в швейной промышленности для раскроя плоских деталей. В таблице 1.1 приведены технические данные трех типов раскройных машин фирмы «Паннония».
Таблица 1.1 – Техническая характеристика передвижных раскройных машин
Максимальная ширина разрезаемого настила
Величина хода ножа мм
Размеры ножа (длина ширина толщина)
Электродвигатель: мощность Вт
частота вращения вала обмин
По своему устройству эти машины аналогичны они отличаются только техническими данными. Рассмотрим устройство и работу наиболее распространенной машины типа CS 529-1А с заточным устройством. К передней части платформы прикреплены подпружиненный козырек который отделяет нижнее полотно настила в процессе работы машины от поверхности стола и узкая стойка. Для облегчения передвижения машины по столу снизу платформы к пластинчатым пружинам присоединены ролики с встроенными игольчатыми подшипниками. Игольчатые подшипники облегчают плавное передвижение машины по крыше настилочного стола. Пластинчатые пружины служат для гашения вибрации при работе машины. Для удобства перемещения машины по столу имеется рукоятка изготовленная из эбонита. Пуск электродвигателя производится нажатием на кнопку включения расположенную сзади рукоятки. Сверху на стойку (рисунок 1.13) установлен трехфазный короткозамкнутый асинхронный электродвигатель 1.
Передний конец вала 2 электродвигателя выполнен в виде конуса на который надет кривошип (маховик) 3. В отверстие этого кривошипа вставлен палец запрессованный в шарикоподшипниках. На палец надета верхняя головка шатуна 4 соединенная с ползуном 5 который расположен в направляющих. К отростку ползуна 5 винтом прикреплен нож 6. Нож установлен в направляющих пазах стойки.
Устройство перемещения лапки. Передняя часть машины закрыта кожухом в пазу которого установлена зубчатая рейка 22. К нижней части этой рейки прикреплена лапка 27. Высота лапки фиксируется рукояткой 26 в таком положении чтобы лапка слегка нажимала на ткань не давая верхним полотнам настила смещаться вверх и вниз при движении ножа. Рукоятка закреплена на рычаге 25 который связан с подпружиненным штоком 23. В исходном положении шток 23 контактирует с зубчатой рейкой 22 под действием пружины. При нажатии на рукоятку 26 рейка 22 вместе с лапкой получает возможность вертикального перемещения в направляющих. Прижимное устройство с лапкой одновременно служит и для предохранения пальцев работающего от пореза ножам. Лезвие ножа имеет двустороннюю заточку с общим углом 15-20о.
Заточное устройство. С маховиком 3 взаимодействует ролик 7 расположенный на валу 8. На переднем конце вала закреплен червяк 9 находящийся в зацеплении с червячным колесом 10. Система звеньев 7-9 расположена в корпусе который имеет возможность поворота относительно оси червячного колеса 10. В исходном положении пружина стремится отвести ролик 7 от маховика 3. Зубчатое колесо 10 закреплено на ходовом винте 11 который выполнен с двумя нарезками: левой и правой. При движении гайки 12 по ходовому винту в крайних нижнем и верхнем положениях происходит переход ее на другую ветвь нарезки. Тем самым обеспечивается возвратно-поступательное движение гайки 12. Винт 11 расположен в направляющих корпуса.
Рисунок 1.13 – Кинематическая схема машины CS-313
Отросток гайки 12 закреплен на втулке 13 на которой расположен кронштейн 15 с абразивными кругами 16. Во втулку 13 входит направляющий стержень 14 закрепленный в корпусе. Также гайка 12 имеет второй отросток в отверстии которого расположен подпружиненный толкатель 20. Толкатель может взаимодействовать с кулачком 21 а тот – с рычагом 19. Также на рычаг 19 может воздействовать кулачок 18 связанный с кнопкой 17.
Работа устройства происходит следующим образом. При нажатии на кнопку 17 кулачок 18 воздействует на рычаг 19 заставляя его повернуться и подвести ролик 7 к маховику 3. Происходит вращение червяка 9 червячного колеса 10 и ходового винта 11. Гайка 12 перемещается снизу вверх и обратно одновременно перемещаются втулка 13 кронштейн 15 и абразивные круги 16. Происходит заточка ножа. При подходе в крайнее верхнее положение толкатель 20 взаимодействует с кулачком 21 и последний отводит рычаг 19 в исходное положение.
Машины с прямыми ножами обеспечивают большую точность раскроя. Однако их производительность зависит от остроты лезвия. При незначительном затуплении лезвие нуждается в правке и заточке. Затупление лезвия особенно заметно при раскрое толстых и жестких тканей тканей с пропиткой и синтетических материалов. Для разрезания не очень жестких тканей используется гладкое лезвие для разрезания тяжелых тканей идущих на спецодежду – зубчатое лезвие и для разрезания синтетических тканей – полнообразное лезвие.
В машинах CS 529 и CS 530 применена фитильная центральная смазка кривошипно-шатунного механизма. Для этого вверху корпуса машины установлен масляный резервуар с размещенным в нем фитилем. Масло из резервуара поступает по фитилям заключенным в полихлорвиниловые трубки концы которых закреплены в направляющих ползуна 5. Размещение фитилей в пазах направляющих обеспечивает равномерную смазку ползуна 5. Как сверху так и снизу направляющих установлены войлочные прокладки препятствующие вытеканию масла и защищающие ткань от загрязнения. Заливка масла в резервуар производится с помощью масленки.
В машинах с вертикальным ножом скорость движения ножа непостоянна она изменяется в пределах от 0 до 4 мс. Среднюю скорость Vср определяют по формуле:
где n - частота вращения вала двигателя (n=2800 обмин);
h – величина хода ножа (h=40 мм).
Раскройные машины с дисковым ножом
Передвижная машина с дисковым ножом марки ЭЗДМ-1 (рисунок 1.14) предназначена для разрезания низких настилов высотой до 50 мм по прямым линиям и для вырезания деталей имеющих небольшую кривизну. Рабочим органом машины является дисковый нож 6 диаметром 120 мм и толщиной 15 мм. Он установлен в широкой стойке поэтому разрезание настила по траектории с небольшим радиусом закругления невозможно так как произойдет смещение соседних участков настила. Область применения машин ЭЗДМ-1 меньше чем машин ЭЗМ-2.
Диск 6 получает вращение от трехфазного электродвигателя 1 мощностью 220 Вт (напряжением 220380 В) через конические шестерни 3 и 4 с передаточным отношением i=1:1. Электродвигатель установлен сверху на стойке машины стойка имеет форму диска несколько большего диаметра чем дисковый нож. Нижняя часть стойки винтами и контрольными шпильками закреплена на платформе.
Платформа снабжена козырьком и снизу имеет четыре ролика для легкости передвижения машины. Кроме дискового ножа на платформе установлен неподвижный призматический нож 7 прижимающийся под действием пружины 9 к режущей кромке дискового ножа 6. Частота вращения вала электродвигателя 1400 обмин.
Рисунок 1.14 – Кинематическая схема машины ЭЗДМ-1
Окружная скорость дискового ножа диаметром 120 мм составит:
Дисковый нож в процессе работы машины получает вращение в одном направлении обеспечивая прижим настила к поверхности стола.
Для включения и останова электродвигателя в рукоятке вмонтирован выключатель. Рукоятка одновременно служит для перемещения машины по поверхности стола. Заточка режущей кромки дискового ножа производится специальным приспособлением состоящим из двух небольших шлифовальных кругов 13 смонтированных под рукояткой машины.
Для приведения в действие точильного приспособления большим пальцем правой руки нажимают на пусковую кнопку 14. Шлифовальные камни подводят к вращающемуся дисковому ножу. При повороте пусковой кнопки шлифовальные камни поочередно подходят к дисковому ножу обеспечивая его двустороннюю заточку.
Полуавтомат предназначен для раскроя рулонов на полосы в бобинах. Область применения – кожгалантерейная промышленность.
Технические характеристики полуавтомата
Средняя производительность бобинчас
Минимальная ширина нарезаемых полос мм
Точность отрезания мм
Габаритные размеры исходного рулона мм
Высота оси вала главного над уровнем пола мм
Продольная подача ножа
Поперечная подача ножа
Частота вращения ножа мин-1
привод вала главного:
частота вращения мин-1
привод заточки ножа:
Суммарная мощность установленных электродвигателей кВт
Габаритные размеры мм
Норма обслуживания чел
Кинематическая схема отрезной головки полуавтомата для разрезания рулонов представлена на рисунке 2.1.
Вращение дисковый нож 1 получает от двигателя 5 через клиноременную передачу (шкивы 2 4 ремень 3). Заточка дискового ножа производится шлифовальным кругом 6 получающим движение от двигателя 7. Подвод заточного устройства к ножу обеспечивается винтом 8. Поперечная подача ножа осуществляется от гидроцилиндра 10 который перемещает каретку 9 с ножевым устройством. Продольную подачу ножа обеспечивает двигатель 13 который передает движение отрезному устройству с помощью червячной передачи 11-12 и винтовой передачи 14.
Помимо отрезной головки полуавтомат снабжен механизмом главного вала механизмом раскатки и механизмом размотки. На кинематической схеме полуавтомата (рис. 2.2 позиции продолжаются) передана сборная конструкция главного вала 15 две части которого соединены шарнирной муфтой 16 для отсоединения рабочей части вала и отвода ее в сторону вокруг шарнира 17 для снятия бобин. Движение главный вал получает от электродвигателя 21 через клиноременную передачу (шкивы 18 20 ремень 19).
Механизм раскатки и механизм размотки по назначению выполняют одинаковые функции. Рулоны на палках укладываются на барабаны механизма раскатки а рулоны с картонными гильзами насаживаются на вал механизма размотки и поднимаются с двух сторон конусными зажимами. Механизм размотки представляет собой сборную конструкцию 22 состоящую из двух
Рисунок 2.1 – Кинематическая схема отрезной головки
валов соединенных между собой шарнирной муфтой 23 что обеспечивает отсоединения частей вала между собой и поворот одной из них вокруг шарнира 24. Для равнения кромки материала механизм оснащен пневмоцилиндром 25. Механизм раскатки представляет собой два барабана 26 соединенных между собой хомутами и соединенных со штоком пневмоцилиндра 27 устройства для выравнивания кромки материала.
2 Проектирование пневмогидравлической системы управления
Гидравлическая схема управления полуавтоматом приведена на рисунке 2.3. Исполнительными органами на ней являются цилиндр Ц1 поперечной подачи дискового ножа цилиндр Ц2 механизма раскатки цилиндр Ц3 механизма размотки роторный реверсивный гидромотор М механизма продольной подачи дискового ножа. Возвратно поступательное движение поршень со штоком цилиндра Ц1 получает от магистрали через пневмораспределитель Р1 (в обратную сторону – Р2) пневмодроссель ДР1 (в обратную сторону – ДР2) и пневмогидроусилитель ПГУ. Система управления другими исполнительными органами в силу независимости их движений друг от друга аналогична описанной для цилиндра Ц1 поперечной подачи дискового ножа за исключением того что в остальных случаях потребность в пневмогидроусилителе отпадает.
Рисунок 2.3 – Пневмогидравлическая схема управления полуавтоматом
1.1 Определим Vн – скорость дискового ножа.
1.2 Определим скорость резания Vр.
Скорость поперечной подачи Vп является скоростью движения штока гидроцилиндра поперечной подачи. Скорость резания (см. рисунок 3.1) определится по формуле
Схема взаимодействия ножа и рулона приведена на рисунке 3.2.
Рисунок 3.1 – План скоростей
Рисунок 3.2 – Схема взаимодействия ножа и рулона
1.3 Для определения усилия подачи ножа на материал мощности подачи ножа момента вращения ножа и мощности вращения ножа составим уравнения сил для материала и для ножа. Схемы сил действующих на рулон материала и на дисковый нож представлены на рисунках 3.3 3.4
где о – конструктивный угол резания
р – рабочий угол резания
N1 – сила нормального давления материала на нож (или нормальная реакция давления ножа на материал для рис. 3.4) Н
F1 – сила трения материала о боковые грани ножа (или сила трения ножа о материал для рис. 3.4) Н
N2 – сила нормального давления материала на подшипники главного вала Н
F2 – сила трения в подшипниках главного вала Н
N3 –нормальная реакция подшипников ножа Н
F3 – сила трения в подшипниках ножа Н
Pp – усилие поперечной подачи ножа Н
Pн - сила от момента вращения ножа Н.
Np – мощность поперечной подачи ножа Н
Nн - мощность вращения ножа Н
f1 - коэффициент скольжения материала о боковые грани ножа f1=095 [1 c. 78]
f3 - коэффициент трения качения в подшипниках ножа f1=001 [1 c. 78]
Из динамики резания дисковым ножом получаем следующие формулы для расчета необходимых усилий и мощностей:
В свою очередь нормальная реакция давления ножа на материал составит
где q – удельное усилие резания Нм [1 c.50];
L – средняя линия резания м примем
k1 – коэффициент учитывающий притупление кромки ножа [1 c.50];
k2 – коэффициент учитывающий влияние угла заострения на усилие резания [1 c.50];
Рисунок 3.3 – Схема сил действующих на рулон ткани
Рисунок 3.4 – Схема сил действующих на дисковый нож
1.4 Расчет клиноременной передачи
Для передачи крутящего момента от электродвигателя к дисковому ножу в проектируемом приводе используется клиноремённая передача.
Исходя из номограммы условий работы ремня выбираем тип сечения А [9 c.146].
Крутящий момент на ведущем шкиву:
Диаметр ведущего шкива рассчитываем по формуле:
Принимаем диаметр шкива равным d1 = 71 мм.
Диаметр ведомого шкива рассчитывается по выражению:
где – коэффициент проскальзывания ремня.
Выбираем диаметр ведомого вала равным d2=140 мм и уточняем передаточное отношение ремённой передачи:
Минимальная величина межосевого расстояния:
amin = 055·(d1 + d2) + T0 = 055·(71+140)+105 = 127 мм
где T0 – высота сечения ремня для выбранного типа сечения [9 c. 147].
Максимальная величина межосевого расстояния [9 c. 144]:
amax =2 (d1 + d2)=2(71+ 140) = 422 мм.
Принимаем величину рабочего межосевого расстояния aр=400 мм. Расчётная длина ремня составляет [9 c. 144]:
Принимаем величину длины ремня из стандартного ряда по ГОСТ 1284.1-80 равной L=1120 мм. Уточняем значение межосевого расстояния по формуле [9 c. 145]
где w = 05··(d1 + d2) = 05··211 = 331 мм;
y = (d2 – d1)2 = (140 – 71)2 = 4761 мм2.
При монтаже передачи необходимо обеспечить возможность уменьшения межосевого расстояния на 001·L=11 мм для облегчения надевания ремней на шкивы и возможность его увеличения на 0025·L=28 мм для увеличения натяжения ремней.
Произведём расчёт силовых характеристик ремённой передачи. Угол обхвата меньшего шкива составит:
Коэффициент угла обхвата C =09 [9 c. 151];
коэффициент режима работы CP =10 (легкий режим) [9 c. 151];
коэффициент учитывающий влияние длины ремня CL =0 92[9 c. 151];
коэффициент учитывающий число ремней Cz =075 [9 c. 151].
Необходимое число ремней в передаче вычисляется по выражению:
где P0 – мощность допускаемая для передачи одним ремнём
P0 = 088 кВт [9 c. 152].
принимаем число ремней равное z=2.
Предварительное натяжение ветвей клинового ремня
где v – окружная скорость ведущего шкива
– коэффициент учитывающий центробежную силу =018 Н·с2м2.
Сила действующая на валы:
Fв = 2·F0·z·sin(12) = 2·117·3·sin(170°2) = 699 Н.
Ширина обода шкива находится по формуле:
Bш= (z–1)·e + 2f = (3–1)·15 + 2·10 = 50 мм
где e=15 мм f=10 мм – размеры канавок [9 c. 152].
1.5 Расчет мощности привода
Режим нагружения ротора электродвигателя – непрерывный.
Мощность приводного двигателя определяется по формуле
– общий КПД привода.
Так как движение передается рабочему органу передается только клиноременной передачей то
Тогда мощность двигателя будет равна
Угловая скорость вращения двигателя определяется по формуле где n0 - синхронная частота вращения ротора.
По рассчитанным значениям подбираем электродвигатель 4А80В693 1М 3081 ГОСТ 19523-81 (N=11кВт n=920 мин-1).
Дисковый нож 1 (рисунок 2.1) получает поперечную подачу от гидроцилиндра 10. Усилие подачи определяется по формуле
где Fт - сила тяжести каретки дискового ножа Fт=1375Н;
f – коэффициент скольжения каретки по направляющим f=04;
Fр - сила резания Н
Тогда Fп=137504+75=625Н.
Исходными данными для расчета параметров гидроцилиндра поперечной подачи являются
давление в системе pн=4МПа
скорость перемещения Vп=0125 мс
усилие перемещения Рр=625Н.
Диаметр поршня гидроцилиндра определяется по формуле
где k – коэффициент запаса (k=15-2)
φ0 – соотношение между диаметром поршня и штока гидроцилиндра (φ0=03-05).
Тогда по стандартному ряду DП=25 мм тогда диаметр штока составит
Рабочий ход поршня равен величине максимального отклонения кромки материала то есть Δ=20 мм тогда длина внутренней полости гидроцилиндра составляет где λ – толщина поршня.
Расход гидроцилиндра определится
Диаметр стенок гидроцилиндра определится из условия для стали 20Х
Тогда наружный диаметр гидроцилиндра составит
Перемещение отрезной головки по направляющему валу вдоль рулона осуществляется с помощью гидромотора 12 через ходовой винт 11 (рисунок 2.1). Усилие продольной подачи определяется по формуле
Fп=Fтf где Fт - сила тяжести каретки дискового ножа Fт=2400Н;
f – коэффициент скольжения каретки по направляющим f=04.
Тогда Fп=240004=960Н.
Для начала проведем расчет винтовой передачи.
3.1 Выбираем материалы:
Винта – сталь 18 ХГТ азотированный [14 с.29-30];
Гайка - бронза Бр ОФ-10-1 [14 с.29-30].
3.2 Определяем допускаемые напряжения:
Допускаемое давление в резьбе [q]=10МПа;
[t]=40МПа – напряжение на срез;
[sсм]=80 МПа – напряжение на смятие;
[sр]=40 МПа – напряжение на растяжение;
[s]=sт[n] - напряжение на растяжение и срез;
sт=400 МПа – предел текучести;
[n]=3- коэффициент запаса;
3.3 Выбираем профиль резьбы –трапецеидальная.
yН=05 - коэффициент высоты гайки [14 с.30]; принимаем гайку цельную.
3.4 Из условия обеспечения износостойкости определяем средний диаметр резьбы [14 с.30]
где Fa – осевое усилие передачи Н Fa=Fп=960Н;
yh – коэффициент высоты резьбы для трапецеидальной yh=05 [14 с.30].
Исходя из конструктивных соображений принимаем диаметр трапецеидальной резьбы равным d=40 мм шаг t=12мм с числом заходов P=4[14 таблица 2.3].
3.5 Определяем угол подъема винтовой линии по формуле [14 с.31]:
g=arctg(t·Pp·d2)=arctg(12·4314·37)=0392 рад.
3.6 Определяем приведенный угол трения r[14 с.31]:
где f=01 - коэффициент трения скольжения;
d=150 - угол наклона рабочей стороны профиля резьбы;
3.7 Определяем к.п.д. передачи с учетом потерь в опорах и в резьбе [14 с.31]:
где h=tggtg(g+r)=tg(0392)tg(0392+0103)=0766.
hв.п.=095·h=095· 0766=0728.
3.8 Определяем требуемую мощность для вращения винта [14 с.32]
N=Fa·v1000·h=960·01251000·0728=0165 кВт
3.9 Определяем необходимое число оборотов винта:
nвр=60·v2t·p=(60·125)(12·4)=156 мин-1;
Проверочный расчет винт-гайка.
Основным критерием работоспособности передачи является износостойкость которая оценивается по среднему давлению между витками резьбы винта и гайки [14 с.30]
где Н1 – рабочая высота профиля мм
определяется для трапецеидальной резьбы Н1=05t=0512=6мм [14 с.30];
z – число витков резьбы в гайке определяется по формуле z=Hгt
где Нг – высота гайки.
3710 винт удовлетворяет условию .
где Т – крутящий момент Нм
определяется Т=05d2Fatg(g+r)=0537960tg(0392+0103)=959Нм.
4133 винт удовлетворяет условию прочности.
По полученным значениям частоты вращения и необходимой мощности подбираем роторный гидромотор 4МГ 15-13 [4 c. 273].
4 Расчет привода вращения рулона и определение мощности приводного двигателя
Расчет ведется для главного вала представленного позицией 15 на рис. 2.2. Для обеспечения необходимой динамики намотки рулона на главный вал должно обеспечиваться условие где МКР – крутящий момент на валу; k – коэффициент запаса примем равным 12; МС – момент сил сопротивления. В свою очередь момент сил сопротивления составляет сумму моментов сил трения и моментов сил инерции .
Момент сил инерции рассчитывается
Момент сил трения определится с учетом радиальной составляющей реакции в шарикоподшипнике
Тогда требуемый крутящий момент должен быть не меньше .
Кинематическая схема привода представлена на рисунке 3.2. Режим нагружения ротора электродвигателя – непрерывный.
где Мн – номинальный момент развиваемый на валу электродвигателя Нм;
– синхронная угловая скорость ротора;
где n0 - синхронная частота вращения ротора
По рассчитанным значениям подбираем электродвигатель 4А90С987 1М 3081 ГОСТ 19523-81 (N=16кВт n=1000 мин-1).
В системе управления полуавтоматом применяются два пневмоцилиндра (поз. 25 28 на рисунке 2.2) для равнения кромки устройства размотки рулона и устройства раскатки рулона. Пневмопривод имеет следующие преимущества по отношению к гидроприводу: более высокая скорость перемещения поршня (02 05мс); отсутствуют утечки масла которое способно загрязнить рабочее место; более низкая стоимость из – за отсутствия индивидуальной насосной станции и менее высоких требований к качеству аппаратуры пожаро- и взрывобезопасность.
Основными недостатками пневмопривода по сравнению с гидроприводом: небольшие усилия на штоке (20 60Нсм2); неравномерное движение поршня при изменяющейся на штоке нагрузке за счет сжимаемости воздуха; более низкий КПД за счет утечек сжатого воздуха.
Структура пневмопривода. Носителем механической энергии в пневмоприводе является сжатый воздух. На промышленных предприятиях имеются компрессорные станции которые осуществляют централизованное снабжение всех технологических устройств и оборудования. Разводка воздуха осуществляется по магистральным трубопроводам связывающим емкость наполненную сжатым воздухом (ресивер) с потребителями сжатого воздуха.
Выбираем давление воздуха в рабочей полости пневмоцилиндра Рм(20 30 40 50 60)Нсм2 принимаем Рм =50Нсм.
Определяем диаметр D пневмоцилиндра по формуле
где к – коэффициент запаса равный 15 2 и учитывающий потери трения на уплотнениях падение давления за счет утечек воздуха.
рпол – максимальное усилие на штоке Н определяется Рпол=mgf+ma= mgf+mΔVΔt= Fрf+m(V2-V1)Δt
где m – масса передвигаемой части устройства размотки кг
f – коэффициент трения скольжения вала размотки в направляющих f=018 [14 c.224]
a – ускорение разгона штока пневмоцилиндра мс2
V2 – скорость установившегося движения штока мс
V1 – скорость движения штока в начале разгона мс
Δt – время разгона штока с.
Рпол=mgf+ma=880018+88(005-001)05=484Н.
ра – 981 Нсм2 – давление атмосферное.
Полученное по формуле значение диаметра в (мм) округляют до ближайшего из ряда стандартных по ГОСТ 6540 – 64. В этом ряду имеем следующие значения 5 10 12 16 20 25 32 40 50 63 80
Из имеющихся значений берем 63 мм.
Из конструкторских соображений выбираем диаметр d= =(02 03)D полученное значение округляем до приведенного выше ряда.
d=025×63=1575мм. Принимаем d=16мм.
Определяем параметры трубопроводов dтр исходя из уравнения неразрывности потока сжатого воздуха
где V – рекомендуемая скорость течения воздуха в трубах мс; Vp – средняя скорость движения поршня в течении такта мс
Vp =40-(Рм-10)2490=293мс
V = Lt где L – ход поршня а t – необходимое время
Принимаем по стандартному ряду ГОСТ 6540 – 64 dтр=5мм.
Определяем расход воздуха в цепи приведенной к атмосферному давлению
Подбираем пневмоаппаратуру: фильтр-влагоотделитель 22У 16×80 УХЛ4 ГОСТ 17437-81 глушитель шума П-ГII16063 УХЛ4 маслораспылитель В44-14 УХЛ4 пневмодроссели 06-2 УХЛ4ГОСТ 19485-81 пневмораспределители ПВ64-23М клапан 122-16 УХЛ4.
6 Расчет производительности полуавтомата
При расчете производительности следует определить время затрачиваемое на получение одной бобины. Для этого зададимся данными:
ширина рулона составляет b=2м;
диаметр рулона D=036м;
ширина бобины a=004м;
метраж материала в рулоне
скорость раскатки (размотки) рулона Vраз =
скорость поперечной подачи ножа Vрез=0125мс;
скорость продольной подачи ножа Vпр=003мс;
время установки рулона на вал размотки (раскатки) tуст=275мин;
время съема одной бобины tсъем=10с.
Время на изготовление bа бобин со всего рулона составляет
где tраз – время раскатки (размотки) рулона;
tрез – время резания одной бобины;
tпр – время продольной подачи от одной линии резания к другой.
Тогда время на изготовление одной бобины составляет
Производительность полуавтомата составляет
7 Расчет на прочность детали конструкции
В графической части имеется чертеж вала РП-1600.01.028. Вал представляет собой вал крепления дискового ножа с помощью прямобочного шлицевого соединения. На валу также крепятся два фланца и шкив клиноременной передачи. Проведем расчет на прочность различных элементов конструкции вала: шпоночного соединения шлицевого прямобочного соединения.
7.1 Расчет шпоночного соединения на валу
Передача крутящих моментов от шкивов на валы осуществляется посредством шпонок. В связи с этим необходимо проверить прочностные свойства шпоночных соединений на смятие по наиболее нагруженной шпонке. Рассматриваемая шпонка имеет размеры bhl=161127 мм глубина паза t1=5 мм. Передаваемый крутящий момент T2= T1i=114×102=57Нм.
Проверим по условию прочности на смятие шпонки
Шпонка условию прочности на смятие удовлетворяет.
Проверим по условию прочности на срез шпонки
Шпонка условию прочности на срез удовлетворяет.
7.2 Расчет шлицевого прямобочного соединения на валу
Шлицевые соединения с зубьями прямобочного профиля в соответствии с ГОСТ 21425-75 рассчитываются на смятие и износ что соответствует их основным предельным состояниям.
Условие прочности на смятие выглядит
где – среднее давление на рабочих плоскостях МПа;
Т – передаваемый крутящий момент Нмм;
SF - удельный суммарный статический момент площади рабочих поверхностей соединения относительно оси вала мм3мм;
где dср – средний диаметр шлицевого соединения мм;
h - рабочая высота зубьев мм;
l – рабочая длина соединения
В данном разделе дипломного проектирования требуется разработать технологический маршрут изготовления детали “кронштейн” являющейся одной из корпусных деталей люльки. Вид детали изображен на рисунке 4.1.
Деталь изготовляют из стали марки сталь 45 ГОСТ 1050-88 у которой предел прочности при растяжении равен 598 МПа предел текучести при растяжении равен 353 МПа относительное удлинение 16% твердость НВ равна 229 кгсмм2 (2246 МПа).
Изготовление детали из стали литьем позволяет получить требуемую конфигурацию наружного контура поверхности заготовки без значительных трудностей. Отсутствие разъемов значительно упрощает процесс получения заготовок.
Проведем размерный анализ чертежа детали предварительно кодировав поверхности детали (рисунок 4.2).
Для размерного анализа требуется выявить ошибочную или недостающую информацию используя исходные графы размерных связей по каждой координате отдельно. Исходные графы размерных связей представлены на рисунках 4.3-4.5. По каждой координатной оси обнаруживаем разрыв размерной связи. Исправляем ошибочную и недостающую информацию и строим исправленные графы размерных связей приведенные на рисунках 4.6-4.8.
Рисунок 4.1 – Эскиз кронштейна
Рисунок 4.2 – Анализ поверхностей детали в выбранной системе координат
Рисунок 4.3 - Исходный граф по оси К
Рисунок 4.4 - Исходный граф по оси М
Рисунок 4.5 - Исходный граф по оси N
Рисунок 4.6 – Исправленный граф размерных связей по оси К
Рисунок 4.7 – Исправленный граф размерных связей по оси М
Рисунок 4.8 – Исправленный граф размерных связей по оси N
Разрабатываемый маршрут технологического процесса устанавливает последовательность обработки поверхностей детали с целью получения требуемого качества поверхностей и наименьшей себестоимости. Маршрут представлен в таблице 4.1.
Таблица 4.1 - Методы обработки
Технические требования
Параметры поверхности
Базирование – процесс определения поверхностей объекта производства от которых следует настраивать формообразующий элемент для получения требуемой точности размера.
Дифференциация операций.
Этап 2(предварительный).
5 горизонтально фрезерная операция ФРЕЧ Мр10 представленная на рисунке 4.9.
Рисунок 4.9 – Схема базирования операции 005
0 горизонтально фрезерная операция ФРЕЧ Nр11 представленная на рисунке 4.10.
Рисунок 4.10 – Схема базирования операции 010
5 вертикально фрезерная операция ФРЕЧ Кр1 представленная на рисунке 4.11.
Рисунок 4.11 – Схема базирования операции 015
В ходе первых операций 005 010 015 был сформирован единый комплект технологических баз относительно которого в большинстве случаев дальше будет производиться базирование для следующих операций механической обработки. Приведем некоторые из них.
0 сверлильная операция СВЕР No6 Np6 Кo2 Кр2 Кo5 Кр5 представленная на рисунке 4.12.
Рисунок 4.12 – Схема базирования операции 040
Рисунок 4.13 – Схема базирования операции 025
Отверстие Кр6 (N6) теперь тоже может выступать в качестве базы для формирования тех или иных плоских поверхностей детали. С учетом этого схемы базирования для следующих операций почти повторяются за исключением использования отверстия в качестве базы.
Проведем расчет уравнений размерных связей технологического процесса для одной координаты предварительно составив размерную схему технологического процесса по координате М.
Размерный анализ проводится при составлении размерной схемы (рисунок 4.14) технологического процесса по координате М.
Рисунок 4.14 – Размерная схема технологического процесса по оси М
Составляем исходный технологический граф приведенный на рисунке 4.15. Обнаруживаем наличие замкнутого контура что свидетельствует о неправильном выборе маршрута обработки детали по координате М. Исправляем маршрут в результате размерная схема технологического процесса примет вид представленный на рисунке 4.16. Составим для исправленного технологического процесса исходный и производный технологические графы приведенные на рисунках 4.17 4.18.
Рисунок 4.15 – Исходный технологический граф по координате М
Рисунок 4.16 – Размерная схема технологического процесса по оси М после исправления
Рисунок 4.17 – Исходный технологический граф по координате М после исправления
Рисунок 4.18 – Производный технологический граф по координате М после исправления
Используя данные исходных и производных технологических графов составляем уравнения размерных цепей.
Операционным припуском называют слой материала удаляемый при выполнении отдельного перехода (операции). Его наименьшее значение достаточное для компенсации предшествующей погрешности называется минимальным припуском Zmin.
Минимальные припуски снимаемые с детали - кронштейн отображены в таблице 4.2.
Таблица 4.2 - Минимальные припуски по координате М
Минимальный припуск Zmin
Уравнения размерных цепей по оси М:
ZМ3= ЗМ1- ЗМ2+ОМ1- ОМ4
ZМ6= ЗМ3- ЗМ2+ОМ1- ОМ2
ZМ7=ОМ2-ОМ3+ОМ5- ОМ6
ОМ7нм= ОМ7нб-ОМ7=5-003=497
ОМ6нм= ОМ6нб-ОМ6=9-004=896
Решение всех остальных уравнений размерных цепей технологического процесса позволяет судить о целесообразности выбора маршрута.
Расчет режимов резания для окончательной обработки поверхности будем производить по справочным материалам. Все результаты сведены в таблицу 4.3.
Таблица 4.3- Режимы резания
На основании расчетов заполняются операционные карты (см. приложение)
Технико-экономический расчет
Используя данные таблицы получаем снижение стоимости машины на Эс=454900-268750=186750руб. Тогда величина экономического эффекта будет определяться по формуле Э=ЭсТ где Т - срок службы проектируемого полуавтомата в годах. Значение экономического эффекта будет составлять Э=18675010=18675руб.
Таблица 5.1 – Смета изъятых и добавленных деталей (механизмов)
Редуктор червячной передачи
Муфта соединительная
Муфта соединительная
Охрана труда - это система законодательных актов социально - экономических организационных технических гигиенических и лечебно-профилактических мероприятий и средств обеспечивающих безопасность сохранение здоровья и работоспособности человека в процессе труда. Охрана труда создание безопасных и здоровых условий на предприятии лёгкой промышленности способствует повышению эффективности труда и улучшению качества выпускаемой продукции. Поэтому на всех предприятиях необходимо внедрение современных средств техники безопасности и обеспечение санитарно-гигиенических условий. Особое внимание должно уделяться вопросам улучшений условий труда санитарно-оздоровительным мероприятиям. При проектировании оборудования используемого на предприятиях легкой промышленности следует учитывать соответствие создаваемых конструкций требованиям норм охраны и гигиены труда. Охрана труда является социальной дисциплиной т.к. условия труда во многом определяют экономические показатели производства престижность специальностей психологический климат в коллективах текучесть кадров и трудовую дисциплину производства. Знание законов охраны труда позволяет применять их на практике при решении вопросов обеспечение безопасности и безвредных условий труда при одновременном повышении производительности труда предупреждение производственного травматизма профессиональных заболеваний аварий пожаров и взрывов. Таким образом основное направление охраны труда - это внедрение системы управления охраной труда создание безопасной техники технологий комплексная механизация и автоматизация производства.
2 Характеристика полуавтомата для раскроя рулонов ткани
Общая характеристика проектного варианта машины для нарезания полос из текстильных материалов приведена в таблице 6.1.
Таблица 6.1- Общая характеристика машины
Характеристика параметра
Опасные и вредные факторы имеющиеся в конструкции изделия либо проявляющиеся при его эксплуатации
Наличие вредных опасных или токсичных веществ
Да (см. таблицу 6.2)
Наличие источников ионизирующего излучения
Да (см. таблицу 6.3)
Наличие источников электромагнитных полей
Наличие возможности поражения человека электрическим током
Да (см. таблицу 6.4)
Наличие опасностей при работе изделия на холостом ходу и при обработке изделий
Да (см. таблицу 6.5)
Утвердительное содержание некоторых ячеек в графе “характеристика параметра” требует развернутого описания тех или иных преобладающих вредных или опасных производственных факторов имеющихся в конструкции или появляющихся при эксплуатации проектируемого закрепочного полуавтомата. Все данные о наличии таких факторов сведены в таблицы 6.2 - 6.6.
Таблица 6.2- Характеристика вредных опасных и токсичных веществ
Характеристика рассматриваемого параметра
Наименование вещества
Масло индустриальное И-12А ГОСТ 20799-79 или другие масла имеющие кинематическую вязкость 10-14 сСт при 50°С
Агрегатное состояние
Класс опасности вещества
Предельно допустимая концентрация мгм3
Температурные пределы воспламенения 0С
Категория взрывоопасности смеси
Группа взрывоопасной смеси
Температура вспышки паров 0С
Температура самовоспламенения 0С
Количество вещества на проектируемом объекте кг
Количество вещества выделяющегося в воздух рабочей зоне мгм3 не более
Таблица 6.3 - Характеристика производственного шума
Характеристика реализуемого параметра
Характеристика рабочего места
Рабочее место оператора машины
Механизм привода дискового ножа тянульного вала и привода накатных устройств
Уровни звукового давления на проектируемом участке дБА
Допустимые уровни звукового давления дБА
Мероприятия по достижению нормируемых параметров производственного шума
своевременная смазка механизмов машины замена изношенных деталей
Таблица 6.4 - Характеристика опасности поражения персонала электрическим током
Класс помещения по опасности поражения электрическим током
С повышенной опасностью
Напряжение электрического тока питания электросистем изделия В
Сеть электропривода 380
Мощность источника электрического тока кВт
Тип исполнения электрооборудования
Класс электрооборудования по способу защиты человека от поражения электрическим током
Средства коллективной защиты от поражения электрическим током
Заземление закрытие щитками изоляция токоведущих частей
Способ отключения электрооборудования от сети
Общий рубильник кнопка ”стоп” штепсельные розетки
Сопротивление изоляции токоведущих частей МОм
Удельное сопротивление грунта Ом×м
Нормируемое значение сопротивления защитного заземления Ом
Cопротивление защитного заземления Ом
Индивидуальные средства защиты
Нет из вспомогательных - резиновый коврик
Рассчитаем схему заземления выполненную вертикальными стержнями d=6 см l=25 м грунт – суглинок ρ=100 Ом. Заземляющее устройство предполагается выполнить в виде прямоугольника 2836 м2. Стержни соединены между собой стальной полосой 40×5 мм2 и зарыты на глубину t0=07 м. Коэффициент сезонности Кс=1. Расчёт ведётся по методике изложенной в литературном источнике [24].
Сопротивление растеканию тока для одного вертикального стержневого заземлителя:
Расстояние между стержнями a принимаем равным 4 м.
Определяем предварительно число стержней. Длина соединительной полосы равна периметру прямоугольника м.
Коэффициент использования заземлителей ст=063.
Необходимое число труб для системы заземления при Rзаз=4 Ом:
Сопротивление растеканию соединительной стальной полосы Ом находится по формуле:
где ln – длина соединительной полосы м
d – эквивалентный диаметр d=006 м
Требуемое сопротивление системы заземления:
Таблица 6.5 - Характеристика опасностей при работе машины
на холостом ходу и при обработке деталей
Средства защиты исключающие попадание человека в опасную зону
Способ крепления детали в изделии при ее обработке
Масса обрабатываемой детали кг
Средства механизации при установке креплении и снятии обрабатываемой детали
погрузчик средства механизации к нему
Средства защиты человека при обработке заготовки
от пыли - общая вентиляция
Сухой вручную щёткой
Средства механизации используемые при монтаже ремонте и демонтаже изделия
3 Санитарно-гигиенические мероприятия. Вентиляция. Отопление
При разработке санитарно-гигиенических мероприятий необходимо выбрать соответствующие параметры микроклимата рабочей зоны помещения и предусмотреть для их обеспечения системы вентиляции и отопления. Данные сведены в таблицу 6.7.
Таблица 6.7 - Метеорологические условия на участке. Вентиляция. Отопление
Наименование производственного помещения
Характеристика тяжести работы
Средней тяжести работы категория IIа
Пара-метры микрок-лимата
Температура воздуха рабочей зоны °С
Относительная влажность воздуха %
Скорость движения воздуха мс
Система вентиляции в помещении и на рабочем месте
Приточно–вытяжная естественная
Кратность обмена воздуха ч-1
Система отопления в помещении
Теплоноситель и его параметры
3 Санитарно-гигиенические мероприятия. Освещение
Данные мероприятия сведены в таблицу 6.7.
Таблица 6.7 - Искусственное освещение на участке
Наименование помещения и рабочего места
Раскройный цех рабочее место оператора
Площадь помещения м2
Разряд зрительной работы
Освещенность при рабочем освещении лк
(общее + местное) –750
Освещенность при аварийном освещении: на рабочих местах %
на путях эвакуации лк
Источник питания аварийного освещения
Сеть аварийного освещения
Люминесцентная лампа ЛБ-40
Исполнение светильников
Мощность лампы светильника Вт
Количество светильников шт
- при двухламповых светильниках;
– при трехламповых светильниках
Расчёт количества светильников ведём используя метод светового потока по методике изложенной в литературном источнике [13].
Рассчитаем общее люминесцентное освещение для цеха площадью 5030 м2 имеющего высоту 6 м. Напряжение осветительной сети 220 Вт.
Исходные данные: требуемая освещённость по нормам Ен=300 лк.; коэффициенты использования светового потока n=70% с=50%; hр =08 м hс=05 м; отношение расстояния между светильниками к расчётной высоте подвеса L: h = 15м.
Принимаем светильник с люминесцентными лампами ЛБ–40–4 имеющими световой поток Fл= 3000 лм.
Расчётная высота подвеса:
Оптимальное расстояние между светильниками при многорядном расположении
Светильники размещают в три ряда вдоль помещения.
Индекс площади помещения рассчитывается по формуле:
где А и В – длина и ширина помещения А = 50 м В = 30 м
Нр – высота подвеса светильника Нр = 47 м.
При i=399 коэффициент использования светового потока 50%.
Число ламп находится по формуле:
где N – количество светильников или количество ламп накаливания шт.;
Ен – нормируемая освещённость Ен=300 лк.;
S – площадь помещения S = 1500 м2;
z – коэффициент неравномерности освещения z = 125;
k – коэффициент запаса. Выбирается в зависимости от атмосферы в производственном помещении k = 15;
Fл – световой поток группы ламп в светильнике или лампы накаливания Fл = 3000 лм.;
– коэффициент использования светового потока зависящий от характеристики источника света ограничивающих способностей интерьера помещения кривой распределения света а так же индекса помещения i.
Число светильников в каждом ряду:
- при двухламповых светильниках:
- при трёхламповых светильниках:
Данные мероприятия сведены в таблицу 6.9.
Таблица 6.9 - Пожарная безопасность. Молниезащита
Класс помещения по пожароопасности
Категория производства по пожароопасности
Характеристика материалов стен по сгораемости
Характеристика материалов перекрытий по сгораемости
Степень огнестойкости стен здания и их огнестойкость ч
Расстояние от рабочего места до эвакуационного выхода м не более
Средства пожаротушения
Пожарный щит вода огнетушители
Категория молниезащиты здания
Сопротивление заземляющего устройства Ом
5 Компенсация профессиональных вредностей. Индивидуальная защита. Личная гигиена
Данные мероприятия сведены в таблицу 6.10
Таблица 6.10 - Компенсация профессиональных вредностей. Средства индивидуальной защиты. Личная гигиена
Продолжительность рабочей недели ч
Дополнительный отпуск дни
Пенсионный возраст лет
Обеспечение лечебно-профилактическим питанием
Халат (хлопчатобумажный)
Индивидуальные средства защиты органов зрения
Индивидуальные средства защиты головы
Средства обеззараживания кожи
Метод обеззараживания кожи
При разработке машины для разрезания на полосы текстильных материалов были учтены общие требования безопасности труда и промышленной экологии а также действующие санитарные нормы и правила нормы пожарной безопасности нормы электробезопасности Республики Беларусь.
Среди различных показателей целесообразности внедрения в производство проектируемой машины различают показатели экологии охраны труда и окружающей среды. Дипломное проектирование предусматривает анализ таких показателей выявление возможных несоответствий их допустимым значениям а также проведение мер по ликвидации таких несоответствий.
Производится проектирование машины для разрезания на полосы текстильных материалов. Климатическое исполнение машины - УХЛ4 и 04 (при поставке машин в районы с тропическим климатом по ГОСТ 15150).
Учитывая что применение машины для разрезания на полосы текстильных материалов предназначено для производства ламелей для вертикальных и горизонтальных жалюзи следует заметить что сырье недефицитное и доступное для предприятий республики. На все виды обрабатываемого сырья есть сертификаты качества. Что касается самого машины МРТ то для ее конструирования требуются металлы сплавы полимеры (в основном сталь 45 40Х сплав Д16 полиамид) которые также являются недефицитными и доступными материалами.
В процессе раскроя изделий в воздух выделяется незначительное количество мелкодисперсной пыли (результат разрушения волокон полиамидных волокон ГОСТ 6309-93). Её количество соответствует требованиям санитарных норм. Поэтому дополнительные средства для пылеулавливания не предусматриваются. Достаточно естественной приточно-вытяжной вентиляции.
Вода в процессе не используется следовательно не загрязняются и водные ресурсы.
По окончанию срока службы машины все детали и узлы перерабатываются на месте их образования или на других предприятиях имеющих соответствующую технологию. Лом и отходы черных и цветных металлов отличаются от других видов отходов тем что они представляют собой особо дорогостоящее сырье. Образующийся при ликвидации швейных машин лом черных металлов сдается в организацию «Вторчермет». Лом цветных металлов сдается в организацию «Белцветмет». Требования к лому сдаваемому на утилизацию регламентируются ГОСТ 1639-78 «Лом и отходы металлов и сплавов».
В конструкции используется масло И-12А по ГОСТ 20799-88 (агрегатное состояние жидкое класс опасности 4 количество вещества в объекте 05 кг предельной допустимой концентрации не более 5 мгм2 группа взрывоопасности смеси Т3) или другие аналогичные по назначению масла имеющие кинематическую вязкость 10-14 сСт при 50°С. Масла и смазки применяемые в машинах предназначенных для районов с тропическим климатом должны соответствовать ГОСТ 15156-84.
В соответствии с рядом принятых постановлений и директивных органов все предприятия и организации обязаны осуществлять сбор учет и сдачу отработанных нефтепродуктов. Отработанные масла перерабатываются с целью получения масляных компонентов. Наиболее перспективным и рациональным направлением использования отработанных масел является их переработка на масло перегонных заводах с получением отдельных компонентов для повторного использования. К методам обработки масел относятся отстаивание центрифугирование фильтрация вакуумная перегонка и т.д.
Остальные материалы такие как пластмассы также подлежат переработке либо утилизации.
Экологическая экспертиза внедряемого проекта показала что машина для разрезания на полосы текстильных материалов не загрязняет окружающую среду и является экологически безопасным.
В результате проведенного дипломного проектирования рассмотрены все поставленные вопросы и задачи.
Во «Введении» проведено обоснование необходимости разработки полуатомата для разрезания на полосы текстильных материалов.
В разделе «Обзор литературы» рассмотрены различные машины и полуавтоматы предназначенные для раскроя рулонов как цельных так и предварительно разматываемых.
В «Проектной части» дипломного проекта разработаны пространственная кинематическая схема проектируемой машины пневмогидравлическая схема управления полуавтоматом аргументирован выбор метода раскроя спроектированы нож и ножевое устройство.
Раздел «Расчетная часть» посвящен расчетам технологических усилий машины – усилия резания. Проведен расчет привода дискового ножа рассчитаны параметры гидропривода. Определено высокое значение теоретической производительности.
В разделе дипломного проекта «Технология машиностроения» составлен технологический процесс изготовления детали входящей в конструкцию люльки проведены расчеты уравнений размерных цепей режимов резания составлены операционные карты и операционные эскизы.
В «Экономической части» определен экономический эффект от внедрения спроектированной машины на производство.
Раздел «Охрана труда и промышленная экология» связан с рассмотрением вопросов касающихся отдела «Охраны труда и промышленной экологии» предприятия с учетом использования в производстве проектной машины.
Базюк Г.П. Резание и режущий инструмент в швейном производстве. – М.: Легкая индустрия 1980.
Вальщиков Н.М. Зайцев Б.А. Вальщиков Ю.Н. Расчет и проектирование машин швейного производства. – Л.: Машиностроение 1973.
Вредные вещества в промышленности: Справочник для химиков инженеров и врачей. В 3-х т.Под ред. Н.В.Лазарева. Э.Н. Левиной.-7-е изд. перераб. И доп.- Л.: Химия1976 .
Гидравлика и гидропневмопривод. В 2-х частях. Ч.2: Гидравлические машины и гидропневмопривод: учебник под ред. А.А. Шейпака. – М.:МГИУ2007.
ГОСТ 12566-88. Изделия швейные бытового назначения. Определение сортности.
ГОСТ 20521-75. Технология швейного производства (Термины и определения).
ГОСТ 4103-82. Изделия швейные. Методы контроля качества.
ГОСТ 9176-77 Изделия трикотажные. Методы испытания швов.
Детали машин в примерах и задачах: Учеб. пособие Под общ. ред. С.Н. Ничипорчика. – 2-е изд. – Мн.: Выш. школа 1981.
Иванов М.Н. Детали машин. – М.: Высшая школа 1984.
Кнорринг Г.М. Осветительные установки. - Л.: Энергоиздат Ленингр. Отд-ние1981.
Краснощеков Л.Ф. Расчет и проектирование воздухонагревательных установок для систем приточной вентиляции. - Л.: Стройиздат 1972.
Курсовое проектирование деталей машин: Справ. пособие. Часть 1А. В. Кузьмин Н. Н. Макейчик В.Ф. Калачев и др. – Мн.: Выш. школа 1982.
Курсовое проектирование деталей машин: Справ. пособие. Часть 2А. В. Кузьмин Н. Н. Макейчик В.Ф. Калачев и др. – Мн.: Выш. школа 1982.
Новичихина Л.И. Справочник по техническому черчению. – Мн.: Выш. школа 1976.
Оборудование швейного производства. Вальщиков Н.М. Шарапин А.И. Идиатулин И.А. Вальщиков Ю.Н. – М.: Легкая индустрия 1977.
Охрана труда в машиностроении:Учеб. для студ. машиностроит. спец. ВУЗов Е.Я.Юдин С.В.Белов С.К.Баланцев и др.; Под ред. Е.Я.Юдина С.В.Белова.-2-е изд. перераб. и доп. - М.: Машиностроение 1983.
ОСТ 17-835-80. Изделия швейные. Технические требования к стежкам строчкам и швам.
Полтев М.К. Охрана труда в машиностроении: Учеб. для студ. машиностроит. спец. ВУЗов.- М . : Высш. шк. 1980.
Правила устройства электроустановок Минэнерго СССР.- 6-е изд. перераб. и доп. - М .: Энергоатомиздат 1987.
Савостицкий А. В. Меликов С. Х. Технология швейных изделий Под редакцией А. В. Савостицкого. – М.: Легкая и пищевая промышленность 1982.
Справочник химика: в 3-х т. - 2-е изд. перераб. и доп.-М. - Л.: Госхимиздат 1963.
ССБТ. ГОСТ 12.1.005-88.Общие санитарно-гигиенические требования к воздуху рабочей зоны. - М.: Издательство стандартов 1988 .
ССБТ. ГОСТ 12.1.006-84. Электромагнитные поля радиочастот. Допустимые уровни на рабочих местах и требования к проведению контроля. - М.: Издательство стандартов 1984.
ССБТ. ГОСТ 12.1.007-76. Вредные вещества. Классификация и общие требования безопасности. - М.: Издательство стандартов 1976 .
ССБТ. ГОСТ 12.1.011-78. Смеси взрывоопасные. Классификация и методы испытаний. - М.: Издательство стандартов 1978.
ССБТ. ГОСТ 12.2.007.0-75. Изделия электротехнические. Общие требования безопасности. - М.: Издательство стандартов 1977.
ССБТ. ГОСТ 12.4.011-89. Средства защиты работающих. Общие требования и классификация. - М.: Издательство стандартов 1989.
ССБТ. ГОСТ 12.4.034-85. Средства индивидуальной защиты органов дыхания. Классификация и маркировка. - М.: Издательство стандартов 1985.
Экономика машиностроительного производства И.М. Бабук Э.И. Горнаков Б.И. Гусаков А.М. Панин. Под общ ред. И. М. Бабука. – Мн.: Вышейшая школа 1990.
Рисунок 2.3.doc
Выводы.doc
Проведенные расчеты демонстрируют целесообразность использования данного полуавтомата для раскроя рулонов ткани. Предварительно можно сказать о значительном росте производительность данного полуавтомата по сравнению с традиционными способами раскроя рулонов.
Рисунок 3.2.doc
Литература.doc
Вальщиков Н.М. Зайцев Б.А. Вальщиков Ю.Н. Расчет и проектирование машин швейного производства. – Л.: Машиностроение 1973.
Гарбарук В.П. Расчет и конструирование основных механизмов челночных швейных машин. – Л.: Машиностроение 1977.
Гжиров Р.И. Краткий справочник конструктора: Справочник – Л.: Машиностроение Ленинград. отд-ние 1984.
Машины и аппараты швейного производства (часть 1) Смирнова В.Ф. Буевич Т.В. УО «ВГТУ» Витебск 2001.
Обзор способов резания текстильных материалов и материалов из кожи.docx
Для обработки швейных материалов резанием используются следующие виды энергии: механическая электрическая химическая тепловая. Вид используемой энергии определяет название способа обработки. Классификация способов резания сведена в таблицу 1.1.
Таблица 1.1 – Обзор способов резания текстильных материалов
Сверление фрезерование
Катком или ротационный
Механическое резание представляет собой расклинивание материала режущим инструментом имеющим всегда форму клина. В результате взаимодействия инструмента с материалом в зоне их прикосновения происходит сложный процесс деформаций и разрушения материала. Механическое резание швейных материалов выполняют способами которые определяются взаимным расположением режущего инструмента и заготовки в пространстве а также характером их изменения во времени. В зависимости от этого все способы механического резания можно разделить на четыре группы.
К первой группе относится простое резание. Простое резание представляет собой разрушение материала режущим инструментом имеющим одну режущую кромку и совершающим только рабочее движение определяемое конфигурацией линии резания. В эту группу включены: резание ножом (см. рис. 1.1а) пробивание (прорубание) иглой вырубание резаками (см. рис. 1.1б) или вырезание деталей с их помощью путем прокатывания валика (см. рис. 1.1в).
Рисунок 1.1 – Схемы взаимодействия режущего инструмента и
материала при простом резании
Во вторую группу включены способы резания предусматривающие сложное движение режущего инструмента состоящее из рабочего и дополнительного движений преимущественно перпендикулярно поверхности обрабатываемой детали. Режущим инструментом при обработке этим способом могут служить ножи пилы (см. рис. 1.2а) сверла (см. рис. 1.2б) ленты а также струя жидкости (гидравлический или гидроструйный способ см. рис. 1.2в). По характеру действия эти инструменты универсальны.
Рисунок 1.2 – Схемы взаимодействия режущего инструмента и
материала при сложном резании
Третью группу образует парное резание. При парном резании материал разрушается по одному контуру одновременно двумя режущими кромками. При обработке парным резанием используют инструменты универсального действия (ручные и механические ножницы различных типов см. рис. 1.3а) а также специальные (штампы содержащие пуансон и матрицу см. рис. 1.3б).
Рисунок 1.3 – Схемы взаимодействия режущего инструмента и
материала при парном резании
В четвертую группу входит комбинированное резание которое включает в себя комбинацию указанных способов (пиления и резания ножницами см. рис.1.4).
Рисунок 1.4 – Схемы взаимодействия режущего инструмента и
материала при комбинированном резании
Термический характер механизма разрушения вызываемого подводом в зону резания различной по природе физических явлений энергии и предопределил название способа резания – термофизический. Способа термофизической обработки материалов резанием различаются по виду режущего инструмента и носят одноименные с ним названия.
Существует два вида способа резания лучей: электронным лучем и лучем оптического квантового генератора (ОКГ) или лазера. Резание электронным лучем практически неприемлемо при изготовлении изделий легкой промышленности вследствие необходимости применения вакуумных камер. С помощью луча лазера (см. рис.1.5а) резание текстильных материалов можно выполнять последовательным параллельно-последовательным или параллельным методом обработки. Выбор метода зависит от способа фокусировки луча (в точку или линию) а также от способа подачи излучения на заготовку. Например мощный световой поток можно не фокусируя направить через контур шаблона вырезаемой детали на материал. В зависимости от способа подачи потока излучения на материал луч лазера может быть использован как специальный или универсальный режущий инструмент.
Плазменный способ резания (см. рис.1.5б) по виду разрушения сходен с лазерным но уступает ему по производительности однако способ резания плазмой гораздо проще и дешевле в осуществлении.
Для обработки швейных материалов резанием плазмой применяется косвенная низкотемпературная плазменная дуга – микроплазменная струя где в качестве плазмообразующегося газа применяется преимущественно аргон.
Прямое использование электрической энергии для резания рассматриваемых материалов практически невозможно из-за их диэлектрических свойств. Поэтому резание текстильных материалов с помощью электричества возможно только путем подвода электроэнергии в зону разрушения через промежуточное преобразование ее в другой вид энергии преимущественно в тепловую. В этом случае режущим инструментом служит электрический разряд (см. рис.1.5в) возникновение которого сопровождается значительным тепловым эффектом. Материал помещенный в поле разряда между электродами разрушается с заметными следами термического воздействия. Использование электроразряда в качестве режущего инструмента более эффективно при выполнении перфорирования.
При плазменном способе обработки как правило используется режущий инструмент универсального действия. При электроразрядной обработке материала резанием режущий инструмент может быть универсального действия (например два электрода формы игла-игла) или специального когда один из электродов имеет конфигурацию заданной линии реза.
Рисунок 1.5 – Схемы взаимодействия режущего инструмента и
материала при термофизическом резании
Термомеханический способ резания предполагает разрушение (разделение) материала с одновременным использованием для этой цели двух и более видов энергии. Сущность его заключается в том что разрушение материала происходит в основном термическим способом а разделение его – с помощью дополнительного механического воздействия режущего инструмента.
Нагрев материала в зоне резания достигается либо токами высокой частоты (ТВЧ см. рис. 1.6а) либо путем контактной передачи тепла от нагретого режущего инструмента (электротермический способ см. рис. 1.6б) либо с помощью ультразвука. Высокий износ режущего инструмента в этих способах ограничивает их использование при резании текстильных материалов.
Рисунок 1.6 – Схемы взаимодействия режущего инструмента и
материала при термомеханическом резании
Помимо описанных способов существует и другие (химические газолазерный газоплазменный) однако возможность их применения при раскрое текстильных материалов не изучена.
ПРМ.doc
Для раскроя ткани наиболее распространенными являются передвижные раскройные машины с вертикальным и дисковым ножами и стационарные ленточные машины. Кроме раскройных машин на отдельных предприятиях швейной промышленности для вырубания настилов применяются штампы резаки и др.
Раскройные машины с прямым ножом
В промышленности применяют следующие виды передвижных раскройных машин с прямым ножом – ЭЗМ-2 CS 529 и CS 530. Они предназначены для разрезания настила на части а также для вырезания отдельных крупных деталей изделия.
В таблице 1 приведены технические данные трех типов раскройных машин фирмы «Паннония».
Таблица 1 – Техническая характеристика передвижных раскройных машин
Максимальная ширина разрезаемого настила
Величина хода ножа мм
Размеры ножа (длина ширина толщина)
Электродвигатель: мощность Вт
частота вращения вала обмин
По своему устройству эти машины аналогичны они отличаются только техническими данными.
Рассмотрим устройство и работу наиболее распространенной машины типа CS 529-1А с заточным устройством. К передней части платформы прикреплены подпружиненный козырек который отделяет нижнее полотно настила в процессе работы машины от поверхности стола и узкая стойка. Для облегчения передвижения машины по столу снизу платформы к пластинчатым пружинам присоединены ролики с встроенными игольчатыми подшипниками. Игольчатые подшипники облегчают плавное передвижение машины по крыше настилочного стола. Пластинчатые пружины служат для гашения вибрации при работе машины. Для удобства перемещения машины по столу имеется рукоятка изготовленная из эбонита. Пуск электродвигателя производится нажатием на кнопку включения расположенную сзади рукоятки.
Механизм привода ножа
Сверху на стойку (рисунок 1) установлен трехфазный короткозамкнутый асинхронный электродвигатель 1.
Рисунок 1 – Машина CS-313
Передний конец вала 2 электродвигателя выполнен в виде конуса на который надет кривошип (маховик) 3. В отверстие этого кривошипа вставлен палец запрессованный в шарикоподшипниках. На палец надета верхняя головка шатуна 4 соединенная с ползуном 5 который расположен в направляющих. К отростку ползуна 5 винтом прикреплен нож 6. Нож установлен в направляющих пазах стойки.
Устройство перемещения лапки
Передняя часть машины закрыта кожухом в пазу которого установлена зубчатая рейка 22. К нижней части этой рейки прикреплена лапка 27. Высота лапки фиксируется рукояткой 26 в таком положении чтобы лапка слегка нажимала на ткань не давая верхним полотнам настила смещаться вверх и вниз при движении ножа. Рукоятка закреплена на рычаге 25 который связан с подпружиненным штоком 23. В исходном положении шток 23 контактирует с зубчатой рейкой 22 под действием пружины. При нажатии на рукоятку 26 рейка 22 вместе с лапкой получает возможность вертикального перемещения в направляющих. Прижимное устройство с лапкой одновременно служит и для предохранения пальцев работающего от пореза ножам. Лезвие ножа имеет двустороннюю заточку с общим углом 15-20о.
С маховиком 3 взаимодействует ролик 7 расположенный на валу 8. На переднем конце вала закреплен червяк 9 находящийся в зацеплении с червячным колесом 10. Система звеньев 7-9 расположена в корпусе который имеет возможность поворота относительно оси червячного колеса 10. В исходном положении пружина стремится отвести ролик 7 от маховика 3. Зубчатое колесо 10 закреплено на ходовом винте 11 который выполнен с двумя нарезками: левой и правой. При движении гайки 12 по ходовому винту в крайних нижнем и верхнем положениях происходит переход ее на другую ветвь нарезки. Тем самым обеспечивается возвратно-поступательное движение гайки 12. Винт 11 расположен в направляющих корпуса.
Отросток гайки 12 закреплен на втулке 13 на которой расположен кронштейн 15 с абразивными кругами 16. Во втулку 13 входит направляющий стержень 14 закрепленный в корпусе. Также гайка 12 имеет второй отросток в отверстии которого расположен подпружиненный толкатель 20. Толкатель может взаимодействовать с кулачком 21 а тот – с рычагом 19. Также на рычаг 19 может воздействовать кулачок 18 связанный с кнопкой 17.
Работа устройства происходит следующим образом. При нажатии на кнопку 17 кулачок 18 воздействует на рычаг 19 заставляя его повернуться и подвести ролик 7 к маховику 3. Происходит вращение червяка 9 червячного колеса 10 и ходового винта 11. Гайка 12 перемещается снизу вверх и обратно одновременно перемещаются втулка 13 кронштейн 15 и абразивные круги 16. Происходит заточка ножа. При подходе в крайнее верхнее положение толкатель 20 взаимодействует с кулачком 21 и последний отводит рычаг 19 в исходное положение.
Машины с прямыми ножами обеспечивают большую точность раскроя. Однако их производительность зависит от остроты лезвия. При незначительном затуплении лезвие нуждается в правке и заточке. Затупление лезвия особенно заметно при раскрое толстых и жестких тканей тканей с пропиткой и синтетических материалов. Для разрезания не очень жестких тканей используется гладкое лезвие для разрезания тяжелых тканей идущих на спецодежду – зубчатое лезвие и для разрезания синтетических тканей – полнообразное лезвие.
В машинах CS 529 и CS 530 применена фитильная центральная смазка кривошипно-шатунного механизма. Для этого вверху корпуса машины установлен масляный резервуар с размещенным в нем фитилем. Масло из резервуара поступает по фитилям заключенным в полихлорвиниловые трубки концы которых закреплены в направляющих ползуна 5. Размещение фитилей в пазах направляющих обеспечивает равномерную смазку ползуна 5. Как сверху так и снизу направляющих установлены войлочные прокладки препятствующие вытеканию масла и защищающие ткань о т загрязнения. Заливка масла в резервуар производится с помощью масленки.
В машинах с вертикальным ножом скорость движения ножа непостоянна она изменяется в пределах от 0 до 4 мс. Среднюю скорость Vср определяют по формуле:
где n - частота вращения вала двигателя (n=2800 обмин);
h – величина хода ножа (h=40 мм).
Раскройные машины с дисковым ножом
Передвижная машина с дисковым ножом марки ЭЗДМ-1 (рисунок 2) предназначена для разрезания низких настилов высотой до 50 мм по прямым линиям и для вырезания деталей имеющих небольшую кривизну. Рабочим органом машины является дисковый нож 6 диаметром 120 мм и толщиной 15 мм. Он установлен в широкой стойке поэтому разрезание настила по траектории с небольшим радиусом закругления невозможно так как произойдет смещение соседних участков настила. Область применения машин ЭЗДМ-1 меньше чем машин ЭЗМ-2.
Диск 6 получает вращение от трехфазного электродвигателя 1 мощностью 220 Вт (напряжением 220380 В) через конические шестерни 3 и 4 с передаточным отношением i=1:1. Электродвигатель установлен сверху на стойке машины стойка имеет форму диска несколько большего диаметра чем дисковый нож. Нижняя часть стойки винтами и контрольными шпильками закреплена на платформе.
Платформа снабжена козырьком и снизу имеет четыре ролика для легкости передвижения машины. Кроме дискового ножа на платформе установлен неподвижный призматический нож 7 прижимающийся под действием пружины 9 к режущей кромке дискового ножа 6. Частота вращения вала электродвигателя 1400 обмин.
Рисунок 2 – Машина ЭЗДМ-1
Окружная скорость дискового ножа диаметром 120 мм составит:
Дисковый нож в процессе работы машины получает вращение в одном направлении обеспечивая прижим настила к поверхности стола.
Для включения и останова электродвигателя в рукоятке вмонтирован выключатель. Рукоятка одновременно служит для перемещения машины по поверхности стола. Заточка режущей кромки дискового ножа производится специальным приспособлением состоящим из двух небольших шлифовальных кругов 13 смонтированных под рукояткой машины.
Для приведения в действие точильного приспособления большим пальцем правой руки нажимают на пусковую кнопку 14. Шлифовальные камни подводят к вращающемуся дисковому ножу. При повороте пусковой кнопки шлифовальные камни поочередно подходят к дисковому ножу обеспечивая его двустороннюю заточку.
Для предохранения рук от порезов установлен щиток который в зависимости от толщины настила может перемещаться вверх и вниз. Щиток закреплен на оси стойки машины.
Подводка электроэнергии к передвижным раскройным машинам производится двумя способами: кольцевым и троллейным. При кольцевом способе подводки электроэнергии шнур над столом пропускают через кольца которые подвешены на металлической проволоке натянутой под потолком параллельно столу. Такой способ подводки рекомендуется когда требуется частое изменение технологического процесса связанного с перестановкой оборудования. При троллейном способе подводки электроэнергии под потолком параллельно столу смонтирована трехфазная линия. По оголенным проводам находящимся под током при движении машины перемещается токоприемная каретка изготовленная из диэлектрика. Токоприемная каретка смонтирована на роликах. От этой каретки идет гибкий шнур соединенный со штепсельным вводом раскройной машины. При этом способе подводки тока применяется устройство автоматически отключающее ток при обрыве провода.
Кинематическая схема.frw

Пневмогидравлическая схема.frw

Кран муфтовый 15 ГОСТ 22508-77
Пневмодроссель 06-2 УХЛ4 ГОСТ 19485-81
Регулятор потока с обратным гидроклапаном МПГ55-32 ТУ2-053-1422-79Е
Манометр ЭКМ-1У-60 ТУ25.02-31-75
Маслораспылитель В44-14 УХЛ4
Пневмогидроусилитель
Пневмораспределитель ПВ64-23М
Цилиндр поперечной подачи ножа
Цилиндр механизма раскатки
Цилиндр механизма размотки
Распределитель ПК24-11М
Пневмогидравлическая
Спецификация приспособление.DOC
Винт прижимной ГОСТ 1876-78
Пластина ГОСТ 12196-66
Призма опорная ГОСТ 12195-66
Специфик02.cdw

ТМ2.frw

5 ВЕРТИКАЛЬНО-ФРЕЗЕРНАЯ
Вертикально-сверлильный
Головка ножевая - 2 лист.frw

Общий вид.frw

Спецификация ОВ.DOC
Винт прижимной ГОСТ 1876-78
Пластина ГОСТ 12196-66
Призма опорная ГОСТ 12195-66
Механизм главного вала
РП-1600.02 00000..СБ
Полуавтомат для резания рулонов
приспособа в РПЗ.doc
На рисунке 4.19 приведена конструкция установочно-прижимного приспособления для операции сверления.
Рисунок 4.28 – Конструкция установочно-зажимного приспособления
Деталировка.frw

Покрытие Хим. Окс. прм.
Размеры для справок
Сталь 45 ГОСТ 1050-88
Бр.АЖ9-4 ГОСТ 18175-78
Сталь 45 ГОСТ 1050-74
техмаш.frw
Отливка 2 категории сложности.
Литейные радиусы 1мм
0 Вертикально-сверлильная
Вертикально-сверлильный
Вертикально-фрез. 6Р12
5 ВЕРТИКАЛЬНО-ФРЕЗЕРНАЯ
Головка ножевая.frw

солидолом Ж ГОСТ 1033-79.
Размеры для справок.
Специфик03.cdw

Динамика резания.frw

Специфик01.cdw

КС - А1.cdw

NewКинематическая схема.frw

полуавтомата для резания рулонов
Специфик04.cdw

тп.doc
Оборуд. устройство ЧПУ
Обозначение программы
5 Вертикально-фрезерная ИОТ1-05
)Установить и закрепить деталь в приспособление.
Приспособление специальное - тиски эксцентриковые.
) Фрезеровать поверхность выдерживая размер 1
Фреза торцевая 40 ГОСТ 9304-69
) Снять деталь контролировать.
Штангенциркуль ШЦ 111-250 ГОСТ 166-68
) Уложить деталь в тару
5 Вертикально-фрезерная
0 Вертикально-фрезерная ИОТ5-03
) Фрезеровать поверхность выдерживая размер 2
0 Вертикально-фрезерная
ТМ1-доб.frw

Кинематика резания.frw

ТМ1.frw

Литейные радиусы 1мм
0 Вертикально-сверлильная
Сталь 45 ГОСТ 1050-88
Вертикально-сверлильный
Спецификация приспособление.DOC
Винт прижимной ГОСТ 1876-78
Пластина ГОСТ 12196-66
Призма опорная ГОСТ 12195-66
ТМ2.frw

5 ВЕРТИКАЛЬНО-ФРЕЗЕРНАЯ
Вертикально-сверлильный
приспособа в РПЗ.doc
На рисунке 4.19 приведена конструкция установочно-прижимного приспособления для операции сверления.
Рисунок 4.28 – Конструкция установочно-зажимного приспособления
тп.doc
Оборуд. устройство ЧПУ
Обозначение программы
5 Вертикально-фрезерная ИОТ1-05
)Установить и закрепить деталь в приспособление.
Приспособление специальное - тиски эксцентриковые.
) Фрезеровать поверхность выдерживая размер 1
Фреза торцевая 40 ГОСТ 9304-69
) Снять деталь контролировать.
Штангенциркуль ШЦ 111-250 ГОСТ 166-68
) Уложить деталь в тару
5 Вертикально-фрезерная
0 Вертикально-фрезерная ИОТ5-03
) Фрезеровать поверхность выдерживая размер 2
0 Вертикально-фрезерная
ТМ1-доб.frw

ТМ1.frw

Литейные радиусы 1мм
0 Вертикально-сверлильная
Сталь 45 ГОСТ 1050-88
Вертикально-сверлильный
маршр. карта.frw

наименование операции
Обозначение документа
сборочной единицы или матер.
Рекомендуемые чертежи
Свободное скачивание на сегодня
Другие проекты
- 30.08.2014
- 09.07.2014