Модернизация горизонтально-фрезерного станка




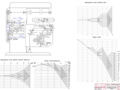
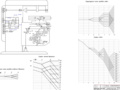
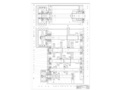
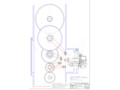
- Добавлен: 25.01.2023
- Размер: 2 MB
- Закачек: 0
Описание
Состав проекта
![]() |
![]() |
![]() |
![]() ![]() ![]() |
![]() ![]() ![]() |
![]() ![]() ![]() |
![]() ![]() ![]() ![]() |
![]() ![]() ![]() |
![]() ![]() ![]() ![]() |
![]() ![]() ![]() |
![]() ![]() ![]() |
![]() ![]() ![]() |
![]() ![]() ![]() |
![]() ![]() ![]() |
![]() |
![]() |
![]() ![]() ![]() ![]() |
![]() ![]() ![]() |
![]() ![]() ![]() |
![]() ![]() ![]() ![]() |
![]() ![]() ![]() ![]() |
![]() ![]() ![]() |
![]() ![]() |
![]() ![]() ![]() |
![]() |
![]() ![]() ![]() |
![]() ![]() ![]() |
![]() ![]() ![]() |
![]() ![]() ![]() ![]() |
Дополнительная информация
6К81Г_P6_z16_часть4.doc
Расчетная схема шпинделя приведена на рис . Уточненное значение крутящего момента на данном валу Mкр1=392.37 Н·м. На данный вал действуют два силовых фактора – от сил резания и от ременной передачи.
Сила от ременной передачи
Py1 = Px1·0.5=3278.08 Н.
Результирующая сила от ременной передачи
Q1 =1.1· Px1= 7211.78 Н.
от ременной передачи
Q1x = Q1·cos(60)= 6482.63 Н
Q1y= Q1·sin(60)= 3159.95 Н
Реакция Rbx находится из уравнения моментов относительно т. А
-3165.4465 + 0.45 Rbx = 0
Реакция Rax из уравнения моментов относительно т. В
51.737 - 0.45 Rax = 0
Уравнение моментов в плоскости x
Mx1=-Q1x·x=-400.0 Н·м
Mx2= -Q1x·(0.1+x)+Rвx·x= -648.26 Н·м
Mx3= -Q2x·x= -648.26 Н·м.
Рассмотрим плоскость y:
Реакция Rby из уравнения моментов относительно т. А
-1537.9725 + 0.45 Rby = 0
Реакция Ray из уравнения моментов относительно т. В
4.005 - 0.45 Ray = 0
Уравнение моментов в плоскости y
My1 = -Q1у·у= -200.0 Н·м
My2 = Q1у·(0.1+у)- Ray·x= -316.01 Н·м
My3 = -Q2у·у =-316.01 Н·м.
Эпюра моментов в плоскости y показана на рис.
По предварительным расчетам прочностным требованиям удовлетворяет диаметр вала d=5 см.
Расчет на жесткость для шпинделя сводится к определению радиального биения переднего конца шпинделя по формуле:
где PZ=4000 H тангенциальная составляющая силы резания Н; JA JB осевые моменты инерции в сечениях А и В мм4; jA jB жесткости в сечениях А и В Нмм; a=100 мм величина консоли; b=450 мм межопорное расстояние; E=2·105 МПа модуль упругости материала шпинделя.
Радиальная жесткость:
Согласно рекомендациям справочной литературы наименьшее поле допуска деталей обрабатываемых на данном станке должно быть .
6К81Г_P6_z16_бжд.doc
труда на рабочем месте станочника.
При организации труда станочника необходимо предусматривать комплекс мероприятий обеспечивающих высокую производительность и полную безопасность работы.
Основные из этих мероприятий следующие:
) рациональная планировка рабочего места обеспечивающая взаимосвязь основного и вспомогательного оборудования естественное и искусственное их освещение в соответствии с действующими нормами возможность поддержания зрительной связи между работающими на участке а также размеры рабочей площадки и разрывов между станкам;
) организация бесперебойного питания рабочего места необходимыми материалами инструментами а также удаления (транспортирования) с рабочего места готовых изделий и отходов в виде стружки;
) инструктаж станочника мастером или бригадиром обеспечивающий наиболее производительные и безопасные приемы работы. Этот инструктаж должен производиться в соответствии с инструкциями по безопасности труда станочников.
В соответствии с нормами технологического проектирования и правилами безопасности металлорежущие станки следует располагать так чтобы на участке по возможности не было встречных и перекрещивающихся грузопотоков. Разрывы между станками определяются в зависимости от наличия и числа рабочих мест в проходе размера станков и обрабатываемых деталей а также других специфических условий работы.
При размещении станков не допускается ставить их вплотную к стенам колоннам и друг к другу торцевыми или задними сторонами. Необходимо предусматривать разрывы обеспечивающие безопасность условия наладки смазывания и ремонта станка. Величина таких разрывов должна быть не менее 500 мм.
При определении разрывов между станками и необходимой рабочей зоны должны быть дополнительно учтены: максимальный вылет подвижных столов ползунов и других частей станка а также площадь для вспомогательных устройств (стеллажей для заготовок и готовых изделий инструментальных шкафчиков и других ).
При установлении безопасной ширины проезда между станками следует учитывать особенности транспортных средств характер их движения (встречное или одностороннее) наличие или отсутствие рабочих мест в проезде.
При использовании колесного транспорта (тележек электрокары и другие). Минимальную ширину проезда надо рассчитывать исходя из ширины тележки и необходимых разрывов между тележками а также тележкой и станком границей рабочей зоны и тележкой что транспортируемые детали не выступают за габариты тележки.
Для создания высокопроизводительных и безопасных условий труда станочника большое значение имеет наличие на рабочем месте рациональных вспомогательных устройств ( инструментальных шкафчиков полок тары и
тому подобное) для хранения заготовок готовых изделий инструментов и приспособлений. Отсутствие вспомогательного оборудования его нерациональное устройство или расположение приводят к захламленности и загрязнению рабочего места что препятствует росту производительности труда и способствует возникновению несчастных случаев.
Для обеспечения безопасности при перемещении заготовок и готовых изделий следует всемерно стремиться к механизации межоперационных транспортных операций. В тех случаях когда общецеховые подъемно-транспортные устройства применять не целесообразно следует предусматривать индивидуальные подъемно-загрузочные устройства. Выбор типа таких устройств зависит от конструкций станка его габаритов массы заготовки и расстояния на которое она перемещается.
Правила техники безопасности запрещают производить измерение деталей на ходу станка так как это связано с опасностью травмирования рабочих режущим инструментом обрабатываемой деталью или приспособлениями.
Для измерения размеров обрабатываемых деталей станок необходимо останавливать. Однако частые остановки и пуски станка вредно отражаются на механизмах и увеличивают время обслуживания станка. Поэтому в процессе резания следует как можно шире применять приборы автоматического
При работе на станках широкое применение находят защитные очки индивидуальные щитки и спецодежда которая предназначается для защиты рабочих при обработке металлов резанием. Защитные очки и индивидуальные щитки используют главным образом для защиты органов зрения от металлического и теплового воздействия различных факторов производственной среды. Применение очков и щитков предупреждает ранение глаз отлетающими частицами обрабатываемой детали и инструмента (стружкой абразивной пылью различными металлическими осколками) ожоги глаз раскаленными частицами металлов.
Средства индивидуальной защиты глаз необходимо применять особенно в тех случаях когда станки не снабжены устройством автоматически отводящим стружку из зоны резания или ограждением зоны резания препятствующим рассеянию стружки в направлении станочника.
Искусственное освещение металлорежущих станков.
Одним из факторов способствующих росту производительности труда предусматривающих травматизм на производств является хорошее освещение рабочих мест. Особенно важное значение имеет искусственное освещение для предприятия где работа требует большого напряжения зрения и выполняется в вечернюю или ночную смену. К этой категории работ относится обработка металлов резанием.
Недостаточная освещенность необходимость рассматривать обрабатываемую деталь и измерительный инструмент чрезмерно приближая их к глазам может привести к близорукости.
Искусственное освещение металлорежущих станков должно выполняться в строгом соответствии с требованиями действующих норм освещенности рабочих зон станочника. Для металлорежущих станков необходимо предусматривать комбинированную систему освещения то есть сочетание общего и местного освещения.
Местное освещение станочника должно быть безопасным. Для питания пристроенных светильников местного освещения с лампами накаливания следует применять напряжение не более 42 В (24 В для станков устанавливаемых в металлообрабатывающих цехах и не более 12 В для станков устанавливаемых в металургических цехах.
Подводка электрических проводов к светильнику осуществляется внутри кронштейна. Открытая подводка не допускается.
Специальные указания по технике безопасности.
) Необходимо следить за тем чтобы выступающие подвижные шпинделя насадок с инструментом были всегда закрыты кожухом;
) не допускается работа на станке до тех пор пока рабочий обслуживающий станок полностью не освоит технику управления и обслуживания последнего;
) при установке обрабатываемой детали в кондуктор необходимо строго следить за тем чтобы рука не находилась на месте движения пневматического зажима;
) работать на станке разрешается только в защитных очках;
) боковые дверки станины открывать после выключения станка поворотом рукоятки главного рубильника на панели управления.
Расчет заземляющего устройства.
Расчет заземляющего устройства при проектировании защитного заземления сводится к определению числа вертикальных электродов и определению сопротивления заземляющего устройства состоящего из рассчитанного числа вертикальных электродов соединенных металлической полосой и заземляющего проводника.
Определение числа вертикальных электродов
Число одиночных необъединенных вертикальных электродов одинаковых по размерам и симметрично расположенных в однородном грунте рассчитывают методом последовательного приближения по формуле (1):
где n - число вертикальных электродов;
RО - измеренное сопротивление одиночного вертикального электрода;
RЗ.Д - предельно допустимая величина сопротивления заземляющего устройства;
hС - коэффициент сезонности (табл. 1 Приложения А );
hТ - коэффициент экранирования (взаимного влияния) вертикальных
электродов. (рис.1 рис2 Приложения А ).
Метод последовательного приближения состоит в том что на первом шаге
принимают hТ =1 и определяют n1 . По n1 находят соответствующее ему значение hТ2 (рис.1 рис.2 Приложения) и по формуле (1) определяют новое значение n2 . По n2 находят соответствующее значение hТ3 и по формуле (1) новое значение n3. Так продолжают расчет до тех пор пока разница между двумя последующими числами электродов будет меньше единицы (т.е. ni - ni-1 1). Полученное число электродов округляют до ближайшего большего их числа что является фактическим количеством одиночных электродов.
1.6 Расчет сопротивления заземляющего устройства
Сопротивление не объединенных в один контур вертикальных заземлителей рассчитывают по формуле:
где Ro =50 - сопротивление одиночного вертикального заземлителя Ом;
n=13- число вертикальных электродов (заземлителей);
hс =14- коэффициент сезонности;
hТФ=055-фактический коэффициент использования вертикальных заземлителей.
Длина соединительной полосы определяется из выражения:
- при расположении вертикальных электродов по контуру или
- при расположении вертикальных электродов в ряд
где A=2 - расстояние между электродами м;
n - число вертикальных электродов.
Сопротивление растеканию тока полосы считая ее единичным горизонтальным заземлителем рассчитывают по формуле:
где r=2102 - удельное сопротивление грунта Ом×м (табл.2 Приложения);
hП =055 - коэффициент использования полосы (рис.3 рис.4 Приложения);
b =004 - ширина полосы м;
h =008 - глубина заложения полосы.
Сопротивление заземляющего устройства определяют по формуле:
где R =875 - суммарное сопротивление всех вертикальных заземлителей;
RП =2862 - сопротивление соединительной полосы;
RЗ.П. =09- сопротивление заземляющего проводника.
Полученное сопротивление заземляющего устройства не должно превышать допустимого значения RЗ.У. RЗ.Д..
Так как разница между двумя последующими числами электродов будет больше единицы (т.е. n2 - n1 =1186-70=486>1)то по n2 находят соответствующее значение hТ3 =055 и определяют новое значение n3.
Так как разница n2 -n1 =1273-1186=0871) то полученное число электродов округляют до ближайшего большего их числа что является фактическим количеством одиночных электродов (nф=13).
Полученное сопротивление заземляющего устройства не превышает допустимого значения RЗ.У.=797 RЗ.Д=10 Ом что подтверждает правильность расчетов.
Оборудование подлежащее защитному заземлению
Защитному заземлению в соответствии с ГОСТ 12.1.030-81 подлежат металлические части электроустановок (с изолированной нейтралью) доступные для прикосновения человека и не имеющие других видов защиты обеспечивающих электробезопасность.
Защитное заземление следует выполнять:
при номинальном напряжении 300 В и выше переменного тока и 440В и выше постоянного тока - во всех случаях;
при номинальном напряжении от 42 В до 300 В переменного тока и от 110 В до 440 В постоянного тока при работах в условиях с повышенной опасностью и особо опасных;
во взрывоопасных помещениях заземление выполняется независимо от значения напряжения.
Проверка заземляющего устройства осуществляется по окончании монтажа а затем периодически в процессе эксплуатации устройства не реже одного
раза в год в период наименьшей проводимости почвы: летом - при наибольшем просыхании а зимой - при наибольшем промерзании.
Требования к величине сопротивления заземляющих устройств
Согласно ПУЭ в электроустановках напряжением до 1000 В с изолированной нейтралью сопротивление заземляющего устройства должно быть не более 4 Ом.
При суммарной мощности источников тока до 100 кВ·А заземляющие устройства могут иметь сопротивление не более 10 Ом.
val1.dwg

6К81Г_Р5_z16__sv.dwg

Техническая характеристика 1.Мощность электротродвигателя N=5
кВт. 2.Пределы частот вращения шпинделя n =2000 мин
n =60 мин. 3.Число скоростей z=16. 3.Селективный механизм управления
ПензГу 1.151002(120200).044СБ2
Свертка коробки скоростей
Кафедра:"МСиК" гр. 99ЗМИ1
6К81Г_P6_z16_спецификация1.doc
Селективный механизм
ПензГУ 1.151002.001Д001
ПензГУ 1.120200.044Д002
ПензГУ 1.120200.044Д003
ПензГУ 1.120200.044Д004
ПензГУ 1.120200.044Д005
ПензГУ 1.120200.044Д006
ПензГУ 1.120200.044Д007
ПензГУ 1.120200.044Д008
ПензГУ 1.120200.044Д009
ПензГУ 1.120200.044Д010
ПензГУ 1.120200.044Д011
ПензГУ 1.120200.044Д012
ПензГУ 1.120200.044Д013
ПензГУ 1.120200.044Д014
ПензГУ 1.120200.044Д015
ПензГУ 1.120200.044Д016
ПензГУ 1.120200.044Д017
ПензГУ 1.120200.044Д018
ПензГУ 1.120200.044Д019
ПензГУ 1.120200.044Д020
ПензГУ 1.120200.044Д021
ПензГУ 1.120200.044Д022
ПензГУ 1.120200.044Д023
ПГУ 1.120200.044 СБ1
ПензГУ 1.120200.044Д028
ПензГУ 1.120200.044Д029
ПензГУ 1.120200.044Д030
ПензГУ 1.120200.044Д031
ПензГУ 1.120200.044Д032
ПензГУ 1.120200.044Д033
ПензГУ 1.120200.044Д034
ПензГУ 1.120200.044Д035
ПензГУ 1.120200.044Д036
ПензГУ 1.120200.044Д037
ПензГУ 1.120200.044Д038
ПензГУ 1.120200.044Д039
ПензГУ 1.120200.044Д040
ПензГУ 1.120200.044Д041
ПензГУ 1.120200.044Д042
ПензГУ 1.120200.044Д043
ПензГУ 1.120200.044Д044
ПензГУ 1.120200.044Д045
ПензГУ 1.120200.044Д046
ПензГУ 1.120200.044Д047
ПензГУ 1.120200.044Д048
ПензГУ 1.120200.044Д049
ПензГУ 1.120200.044Д050
ПензГУ 1.120200.044Д051
Винт М8х25 ГОСТ 11378-84
Кольца ГОСТ 13941-86
Кольца ГОСТ 13942-86
ПГУ 1. 120200.0044СБ1
Подп.пдшипник ГОСТ 9890-75
Манжета ГОСТ 8752-79
Подшипник ГОСТ 8838-75
Подшипник 7312 37.006.162.162-89
Шайба 14Н ГОСТ 6402-70
Шайба20.08кп05ГОСТ 11872-80
Шпонка ГОСТ 23360-78
Шпонка 41-45 ГОСТ 24071-97
Подшипник ГОСТ 9890-75
6К81Г_Р5_z16__rv.dwg

6К81Г_P6_z16_часть3.doc
Расчетная схема вала 1 приведена на рис. Исходные данные для расчета: уточненное значение крутящего момента на данном валу Mкр1=392.37 Н·м делительный диаметр зубчатого колеса d2=0.278 м. На данный вал действуют два силовых фактора – от зубчатой и от ременной передачи.
Окружная сила в зубчатом зацеплении
Px2=2·Мкрd= 2392.370.287=2906.44 Н
Сила от ременной передачи
Py1 = Px1·0.5=1453.22 Н.
Py2 = Px2·0.5=566.660.5=3269. Н.
Результирующая сила от зубчатой передачи
Q2 = 1.1· Px2=1.1· 2906.44=3197.08 Н.
Результирующая сила от ременной передачи
Q1 =1.1· Px1= 7193.45 Н.
от ременной передачи
Q1x = Q1·cos(60)= 3600.01 Н
от зубчатой передачи
Q2x = Q2·cos(26)= 2873.84 Н
Q1y= Q1·sin(60)= 6227.82 Н
Q2y = Q2·sin(26)= 1400.85 Н
Реакция Rbx находится из уравнения моментов относительно т. А
-1096.30685 + 0.464 Rbx = 0
Реакция Rax из уравнения моментов относительно т. В
33.24973 + 0.464 Rax = 0
Уравнение моментов в плоскости x
Mx2= Q1x·(0.12+x)-Rax·x= 447. Н·м
Mx3= Rbx·x= 447. Н·м.
Рассмотрим плоскость y:
Реакция Rby из уравнения моментов относительно т. А
-144.13095 + 0.464 Rby = 0
Реакция Ray из уравнения моментов относительно т. В
83.83383 + 0.464 Ray = 0
Уравнение моментов в плоскости y
My1 = -Q1у·у= 529 Н·м
My2 = Q1у·(0.12+у)- Ray·x= 58.7 Н·м
My3 = Rbу·у= 58.7 Н·м.
Эпюра моментов в плоскости y показана на рис.
Максимальный момент Н·м
Расчет на жесткость проводим определив угол наклона упругой линии в опасном сечении d0 = 5 см. Тогда по рекомендации [3] предполагаемый диаметр вала в опасном сечении
Результирующий угол наклона упругой линии в плоскости x
Угол наклона упругой линии в плоскости y от каждой силы
Результирующий угол наклона упругой линии в плоскости y
Результирующий угол наклона
По рекомендации [4] допустимый угол наклона упругой линии [q]=0.001 тогда и рассчитываемый вал проходит по данному критерию прочности.
Прогиб в плоскости x от каждой силы
Результирующий прогиб в плоскости x
Прогиб в плоскости y
Результирующий прогиб в плоскости y
Результирующий прогиб
Т.о. вал удовлетворяет условию прочности по прогибу.
6К81Г_P6_z16_часть1.doc
Требование максимально высокой производительности обусловило ряд основных и наиболее резко выраженных тенденций в современном станкостроении.
Поэтому важно уметь проектировать металлообрабатывающее оборудование с учетом технологических особенностей обработки на данном станке. Эту цель преследует все более распространяющееся применение бесступенчатых приводов главного движения и подач станков.
В данном дипломном проекте сравниваются две конструкции коробок скоростей горизонтально-фрезерного станка по типу базового 6К81Г. Первый вариант предполагает ступенчатое регулирование частоты вращения шпинделя посредством шестнадцатискоростной коробки скоростей. Во втором варианте используется комбинированное регулирование частоты вращения шпинделя. При этом в качестве механизмов переключения скоростей выступают гидроцилиндры.
Спроектировать приводы главного движения и подач горизонтально-фрезерного станка по типу базовой модели 6К81Г.
Типы приводов – разделенный ступенчатый и разделенный с комбинированным регулированием частоты вращения шпинделя.
Пределы частот вращения:
Максимальная частота вращения шпинделя: nma
Минимальная частота вращения шпинделя: nm
Мощность привода P = 5.2 кВт;
Число скоростей: z = 16;
Механизмы управления:
Для ступенчатого регулирования – селективный механизм.
Для комбинированного регулирования – гидроцилиндры.
Горизонтально-фрезерный станок 6К81Г
Назначение станка. Станок предназначен для фрезерования различных деталей сравнительно небольших размеров в основном цилиндрическими дисковыми угловыми фасонными и модульными фрезами в условиях индивидуального и серийного производства. Наличие поворотного стола позволяет нарезать винтовые канавки при изготовлении косозубых колес фрез зенкеров разверток и тому подобных деталей.
Техническая характеристика станка
Размеры рабочей площадки стола мм250х1000
Пределы угла поворота стола град±45
Наибольшие перемещения стола мм:
Расстояние от оси шпинделя до стола в мм:
Расстояние от оси шпинделя до хобота мм .150
Число скоростей вращения шпинделя 16
Пределы чисел оборотов шпинделя в минуту 65—2000
Мощность главного электродвигателя кВт 58
Количество величин подач стола ..16
Пределы величин подач мммин:
продольных .35 — 980
поперечных .25 — 765
вертикальных.12 — 380
Скорость быстрого продольного перемещения стола мммин 2900
Мощность электродвигателя привода подач кВт 17
Рисунок 1. Горизонтально-фрезерный станок 6К81Г
Основные узлы станка (см. рис. ). А — станина с коробкой скоростей и шпиндельным узлом; Б—хобот с подвесками; В—дополнительная связь консоли с хоботом; Г — поворотная часть стола; Л — поперечные салазки; Е — стол; Ж— консоль с коробкой подач; 3 — основание с резервуаром для охлаждающей жидкости.
Органы управления. 1— рукоятка переключения коробки скоростей; 2—рукоятка включения коррекции шпинделя; 3 — рукоятка ручного продольного перемещения стола; 4 - рукоятка управления продольной подачей стола; 5 — рукоятка управления поперечной подачей; 6 — рукоятка управления вертикальной подачей 7 - рукоятка ручного вертикального перемещения стола; 8 — маховичок ручного поперечного перемещения стола; 9 — маховичок переключения коробки подач; 10—рукоятка переключения перебора коробки подач.
Движения в станке. Движение резания — вращение шпинделя с фрезой. Движения подач — продольное поперечное и вертикальное поступательные перемещения стола. Вспомогательные движения —все указанные перемещения стола выполняемые на быстром ходу или вручную.
Принцип работы. Обрабатываемые детали закрепляются непосредственно на столе в машинных тисках или специальных приспособлениях устанавливаемых на столе станка. При необходимости делить заготовку на несколько равных частей применяют универсальную делительную головку.
Насадные фрезы закрепляют на консольных или опорных оправках. Для поддержания шпиндельных оправок применяют хобот с центральной и концевой подвесками. Хвостовые фрезы закрепляют непосредственно в конусе шпинделя или в цанговом патроне. Торцовые фрезерные головки устанавливают и закрепляют на торце шпинделя.
Настройка станка в соответствии с конфигурацией и размерами обрабатываемой детали производится за счет быстрых механических или ручных перемещений стола Е поперечных салазок Д и консоли Ж. При нарезании спиральных канавок поворачивают стол в соответствии с углом наклона фрезеруемой спиральной канавки. При работе на тяжелых режимах для повышения жесткости узла консоли устанавливают дополнительную связь В.
Механизм автоматического устранения зазора. В приводе продольной подачи стола установлен механизм для автоматического устранения зазора между винтом и маточными гайками (см. рис. в). В кронштейне поперечных салазок стола установлены две маточные гайки 2 и 3 которые могут свободно поворачиваться в подшипниках кронштейна. На гайках нарезаны зубья г которые входят в зацепление с рейками 4 и 10 связанными между собой шестерней 5. Таким образом поворот одной из гаек в каком-либо направлении вызывает поворот другой гайки в обратном направлении. Рейки 4 и 10 поджимаются пружинами 6 и 9.
Рисунок 2. Механизм автоматического устранения зазора
При рабочей подаче в зависимости от ее направления одна из гаек благодаря возникшему трению между витками винта 1 и гайки начнет поворачиваться и поворачивать через рейки и шестерни вторую гайку до тех пор пока последняя не упрется своими витками в противоположные стороны витков винта и не устранит полностью зазор. По окончании подачи действие сил трения между витками гайки и винта прекратится и пружины вернут рейки и гайки в исходное положение восстановив зазор необходимый для легкости холостого перемещения стола. Регулируемые упоры 7 и 8 служат для ограничения величины перемещения реек и соответственно поворота гаек во избежание создания чрезмерного натяга* между винтом и гайками.
Подвеска. На хоботе станка 6К81Г для поддержки шпиндельных оправок можно устанавливать одну или две подвески.
Разрез одной из подвесок показан на рис. г. Полый шпиндель 1 монтирован на двух шариковых радиальных упорных подшипниках 6 между наружными кольцами которых установлена шайба 3. Предварительный натяг в подшипниках необходимый для повышения жесткости системы создается гайкой 5. Крышки 7 закрепляют наружные кольца подшипников и служат одновременно для лабиринтного уплотнения. Вкладыш 2 надевается на шпонке на фрезерную оправку и благодаря наружной конической поверхности заклинивается в полом шпинделе 1 подвески 4.
Привод главного движения со ступенчатым регулированием
1 Кинематический расчет
Проектируемый привод сочетает ступенчатую коробку скоростей с асинхронным двигателем. По рекомендации [1] предполагаемый диапазон регулирования привода можно найти по формуле
где nma nmin=40 мин-1 максимальная и минимальная частоты вращения шпинделя соответственно.
По рекомендации [6] подбирается асинхронный двигатель 4А112М4УЗ имеющий мощность Р=5.5 кВт и частоту вращения n=1445 мин-1. Тогда согласно [1] знаменатель ряда j
По стандартному ряду принимается φ=126. Расчетная частота вращения шпинделя nрасч=118 мин-1:
В соответствии со структурной формулой привода коробка позволяет реализовать восемнадцать скоростей вращения выходного вала
Рисунок 4. Структурная сетка привода главного движения
График частот вращения шпинделя и кинематическая схема коробки показаны на рис. 2 и 3.
Рисунок 5. График частот вращения шпинделя.
Рисунок 6. Кинематическая схема коробки скоростей
Подбор чисел зубьев осуществляется по нормалям станкостроения [1] и [2]. Откуда для рассматриваемых передач можно записать:
Определение потерь на каждом валу привода.
Известна формула для определения потерь на валах привода [2]:
где h hзп = 098 – КПД зубчатой передачи; hп = 099 – КПД подшипников. Тогда можно записать
Передаваемая валом мощность находится по формуле [5]
Предварительно диаметры валов находятся по формуле (см. [1]).
где K Pi – мощность на валу кВт ni – частота вращения вала мин–1.
Крутящие моменты можно найти по формулам
Определение модуля зубчатой передачи.
Коэффициент зависящий от материала зубчатых колес по [1] Kd = 770
Число зубьев шестерни z1 = 41 крутящий момент Mк1 = 28.05 Н·м коэффициент зависящий от распределения нагрузки по ширине зуба khb = 1.0. Коэффициент зависящий от распределения нагрузки по длине зуба kfb = 1.01. Передаточное отношение u = 1.26 отношение ширины венца к делительному диаметру = 0.2. Принимаем материал сталь 40ХH. При этом допускаемые контактные напряжения соответствующие базовому числу циклов нагружения по [1] H = 1000 МПа. Допускаемые изгибные напряжения соответствующие базовому числу циклов нагружения по [1] F = 320 МПа. Базовое число циклов нагружения для контактных напряжений по Nho = 100000000. Базовое число циклов нагружения для изгибных напряжений по [1] Nho = 4000000. Частота вращения n = 1250 мин-1. Коэффициент формы зуба по [1] Yf = 3.7. Коэффициент учитывающий тип колеса-прямозубые Km=14 по [1]. Коэффициент для контактных напряжений по [1] Khl = 1. Допускаемые контактные напряжения H=1000·1=1000 МПа. Расчетный коэффициент для изгибных напряжений Kfl=1. Допускаемые изгибные напряжения F=320·1=320.
Значение модуля по контактным напряжениям
Значение модуля по изгибным напряжениям
Из конструктивных соображений принимается m=2 мм.
Определение модуля зубчатой передачи
Коэффициент зависящий от материала зубчатых колес по [1] Kd = 770. Число зубьев шестерни z1 = 37. Крутящий момент M = 33.97Нм. Коэффициент зависящий от распределения нагрузки по ширине зуба по [1] khb = 1.0. Коэффициент зависящий от распределения нагрузки по длине зуба по [1] kfb=1.01. Передаточное отношение u = 1.26. Отношение ширины венца к делительному диаметру = 0.2. Материал сталь 40ХH. Допускаемые контактные напряжения соответствующие базовому числу циклов нагружения по [1] H = 1000 МПа. Допускаемые изгибные напряжения соответствующие базовому числу циклов нагружения по [1] F = 320 МПа. Частота вращения n=1000 мин-1. Коэффициент формы зуба по [1] Yf=3.71. Коэффициент учитывающий тип колеса - прямозубые Km=14 по [1].
Коэффициент для контактных напряжений Khl = 1. Допускаемые контактные напряжения H=1000·1=1000. Расчетный коэффициент для изгибных напряжений Kfl=1. Допускаемые изгибные напряжения F = 320·1=320 МПа.
Из конструктивных соображений принимается m=2.5 мм.
Коэффициент зависящий от материала зубчатых колес по [1] Kd = 770. Число зубьев шестерни z1 = 20. Крутящий момент M = 52.59 Н·м. Коэффициент зависящий от распределения нагрузки по ширине зуба по [1] khb = 1.02. Коэффициент зависящий от распределения нагрузки по длине зуба по [1] kfb=1.04. Передаточное отношение u = 4.00. Отношение ширины венца к делительному диаметру = 0.4. Материал сталь 40ХH. Допускаемые контактные напряжения соответствующие базовому числу циклов нагружения по [1] H=1000. Допускаемые изгибные напряжения соответствующие базовому числу циклов нагружения по [1] F = 320. Базовое число циклов нагружения для контактных напряжений по [1] Nho = 100000000. Базовое число циклов нагружения для изгибных напряжений по [1] Nho = 4000000. Частота вращения n = 630 мин-1 . Коэффициент формы зуба по [1] Yf = 4.08. Коэффициент учитывающий тип колеса - прямозубые Km=14 по [1]. Расчетное число циклов нагружения Nhe=75600000. Коэффициент для контактных напряжений Khl=1. Допускаемые контактные напряжения H=1000·1=1000 МПа. Коэффициент для изгибных напряжений Kfl=1. Допускаемые изгибные напряжения F= 320·1=320 МПа.
Из конструктивных соображений принимается m=3 мм.
Коэффициент зависящий от материала зубчатых колес Kd = 770. Число зубьев шестерни z1 = 20. Крутящий момент M = 203.37 Нм. Коэффициент зависящий от распределения нагрузки по ширине зуба по [1] khb = 1.02. Коэффициент зависящий от распределения нагрузки по длине зуба по [1] kfb=1.04. Передаточное отношение u = 4.00. Отношение ширины венца к делительному диаметру =0.6. Материал сталь 40ХH. Допускаемые контактные напряжения соответствующие базовому числу циклов нагружения по [1].H=1000.Допускаемые изгибные напряжения соответствующие базовому числу циклов нагружения по [1] F = 320. Базовое число циклов нагружения для контактных напряжений по [1]. Nho = 100000000. Базовое число циклов нагружения для изгибных напряжений по [1] Nho = 4000000. Частота вращения n = 125 мин-1. Коэффициент формы зуба по [1] Yf = 4.08. Коэффициент учитывающий тип колеса - прямозубые Km=14 по [1]. Расчетное число циклов нагружения Nhe= 15000000. Коэффициент для контактных напряжений Khl=1. Допускаемые контактные напряжения H = 1000 ·1=1000 МПа. Коэффициент для изгибных напряжений Kfl = 1. Допускаемые изгибные напряжения F = 320 ·1=320 МПа.
Из конструктивных соображений принимается m=3.5 мм.
Геометрические параметры зубчатых передач рассчитываются по следующим формулам:
Делительный диаметр d=m·z мм.
Внешний диаметр da=d-2.25·m мм.
Внутренний диаметр dv=d+2·m мм.
Таблица 1. Геометрические параметры зубчатых передач
6К81Г_P6_z16_экономика.doc
1 Источники экономического эффекта
В данном дипломном проекте проведен сравнительный анализ экономической эффективности внедрения двух конструкций приводов главного движения горизонтально-фрезерного металлорежущего станка. Первый вариант конструкции (его эффективность и исследуется) имеет гидроцилиндры как механизмы переключающие скорости вращения. Расчеты проводятся по отношению к базовому варианту за который принята коробка скоростей выполненная по второму варианту в которой в качестве механизмов переключения скоростей используются электромагнитные муфты.
Необходимо отметить что экономический анализ сопоставляемых способов и средств – это анализ их сравнительной экономичности. Его содержанием является определение и анализ производственных ресурсов (материальных трудовых природных и др.) потребных по вариантам затрат общественного труда по отдельным элементам и в целом обусловленных осуществлением каждого варианта экономического эффекта получаемого в народном хозяйстве и на предприятии в результате применения предусматриваемых вариантом средств и способов по сравнению с другими и экономической эффективности дополнительных капиталовложений если они требуются.
В связи с этим расчет себестоимости коробки скоростей проводится в следующей последовательности.
Основными источниками экономического эффекта являются высокая производительность проектируемой коробки скоростей и возможность существенно расширить диапазон обрабатываемых материалов за счет возможности работать любой скоростью резания в заданном диапазоне. В конечном итоге это приводит к уменьшению себестоимости продукции повышению производительности проектируемой коробки скоростей по сравнению с базовой за счет самой конструкции. Все это подтверждено расчетами определена себестоимость продукции рассчитаны затраты на производство и определен срок окупаемости двух рассматриваемых вариантов коробок скоростей.
Эффективность создания и внедрения проектируемой коробки скоростей должна устанавливаться на основе комплексного анализа путем сравнения с вариантом принятым в качестве базового.
Способ или средство с которым сравнивают рассматриваемый вариант производства принято называть базой для сравнения (базовым вариантом) Соответственно создаваемый либо улучшаемый способ называют новым вариантом.
Экономический анализ сопоставляемых способов и средств – это анализ их сравнительной экономичности. Его содержанием является определение и анализ производственных ресурсов (материальных трудовых природных и др.) потребных по вариантам затрат общественного труда по отдельным элементам и в целом обусловленных осуществлением каждого варианта экономического эффекта получаемого в народном хозяйстве и на предприятии в результате применения предусматриваемых вариантом средств и способов по сравнению с другими и экономической эффективности дополнительных капиталовложений если они требуются.
Себестоимость продукции – это текущие затраты предприятия на ее производство и реализацию выраженные в денежной форме.
В себестоимость продукции находят свое отражение стоимость потребленных оборотных фондов и основных фондов снашиваемых в процессе производства (амортизация) часть стоимости живого труда выплачиваемая работникам в виде заработной платы часть стоимости продукции для общества в виде отчислений на социальное страхование. Себестоимость продукции является часть ее стоимости.
Себестоимость продукции включает кроме стоимости потребленных сырья и материалов затрат необходимого труда выраженных в заработной плате и совокупности израсходованных производственных фондов в виде амортизационных отчислений часть прибавочного продукта например выплаченные предприятием банковские проценты отчисления на социальное страхование рабочих расходы на рекламу.
В зависимости от цели (планирование учет анализ и т.д.) используются показатели: себестоимости валовой товарной или реализованной продукции себестоимость той или иной доли объема производства сравнимой товарной продукции или незавершенного товарного производства себестоимость работ или услуг.
По последовательности формирования себестоимости различают: технологическую цеховую производственную и полную себестоимость.
Технологическая себестоимость определяется суммой затрат данного цеха непосредственно связанных с выполнением данной операции.
Цеховая себестоимость образуется из всех текущих затрат цеха на производство продукции.
В производственную себестоимость помимо производственных затрат цехов включаются расходы по управлению предприятием.
Полная себестоимость включает в себя производственную себестоимость и коммерческие расходы.
Для экономической оценки вариантов новой техники и выбора наиболее эффективного из них исчисляется технологическая (операционная) себестоимость.
Основные и вспомогательные материалы (за вычетом возвратных отходов)
Основная заработная плата производственных рабочих
(фабрично - заводская)
Дополнительная заработная плата производственных рабочих
Отчисления на социальное страхование
Топливо и энергия для технологических целей
Расходы по содержанию и эксплуатации оборудования
Общезаводские расходы
Коммерческие расходы
Рис.2.1 Формирование себестоимости продукции
Цеховая себестоимость коробки скоростей определяется по формуле
СЦ=М+Пф-Оо+Тт+Эт +Зо+Зд+Зсс+Ри+Рзо+Ропр
где М затраты на основное сырье и материалы; Пф стоимость покупных комплектующих изделий и полуфабрикатов; Оо стоимость возвратных отходов; Тт Эт затраты на топливо и энергию технологические ЗоЗд заработная плата основных и вспомогательных рабочих; Зсс отчисления на социальное страхование; Ри возмещение инструмента и приспособлений; Рзо расходы на содержание и эксплуатацию оборудования; Ропр общепроизводственные расходы.
Затраты на основные и вспомогательные материалы для изготовления.
Таблица 2.1 Материальная ведомость проекта.
Для вычисления экономического эффекта нужно также знать затраты на комплектующие изделия и полуфабрикаты. Соответствующая ведомость затрат приведена в таблице 3.2.
Стоимость возвратных отходов при технологических процессах используемых для изготовления коробки скоростей определяется укрупненно полагая что возврат данной марки материала 12 %.
Таблица 2.1 Стоимость возвратных отходов.
Таблица 2.2. Ведомость затрат на комплектующие изделия и полуфабрикаты.
Калькуляция затрат на изготовление деталей коробки приведена в таблице 2.3.
Таблица 2.3 Калькуляция затрат на изготовление деталей коробки
Часовая тарифная ставка руб.
При 1295 нчас изготовления коробки основная заработная плата составляет 266875 руб. Дополнительная заработная плата рабочим изготовляющим коробку
Расчет затрат предприятия на электроэнергию затрат на подачу масла приведен в таблице 3.6.
Отчисления на социальное страхование
Зсс=(Зо+Зд)·0356=(266875+32025)·0356=1064084 руб.
Таблица 2.4 Топливо и энергия для технологических целей затраты на водоснабжение и сжатый воздух.
Наименование показателей
Значение показателей
Годовой фонд времени час
Стоимость 1 кВтчас электроэнергии
Затраты на электроэнергию
Стоимость 1 м3 масла Цв руб.
Затраты на подачу масла
ИТОГО: Затраты на энергоресурсы
Расчет затрат предприятия на содержание техническое обслуживание оборудование и его амортизацию. Норма отчислений на обслуживание ремонт и амортизацию Нр=10 %. Тогда
Цеховые расходы включают в себя все текущие затраты цеха на производство продукции. Расчет цеховых расходов
Общехозяйственные затраты на производство продукции включает в себя зарплаты персонала заводоуправления амортизация и текущий ремонт зданий производственного назначения почтово-телеграфные расходы и др. Расчет общехозяйственных затрат
Производственные расходы на изготовление продукции включает в себя: затраты на материал основную и дополнительную зарплаты отчисления на социальное страхование амортизацию и расходы на обслуживание цеховые расходы общехозяйственные расходы. Расчет производственных затрат приведен в таблице 3.11.
Таблица 2.5 Цеховая себестоимость.
Затраты на материал Зм руб.
Стоимость возвратных отходов
Затраты на комплектующие изделия и полуфабрикаты
Дополнительная заработная плата
Отчисления на социальное страхование Зс руб.
Затраты на энергоресурсы Зэр руб
Расходы на обслуживание ремонт и амортизацию Рр руб.
Цеховые расходы Рц руб.
Цеховая себестоимость изделия
Производственная себестоимость
Спр=Cц+Робх=38169443+42700=42439443
Расчет коммерческих расходов приведен в таблице2.6.
Таблица 2.6 Коммерческие расходы.
Норма отчислений на коммерческие расходы Нк %.
при 1 месяце изготовления
Коммерческие расходы
Полная себестоимость
Сп=Cпр+Рк=42439443+79519=42518962
Таблица 2.6 Сравнительный анализ показателей проектируемой коробки и базовой
Наименование показателя
Проектируемая модель
Число скоростей резания
Предположим что цена изготавливаемой детали Ц=300 руб. Тогда срок окупаемости
6К81Г_P6_z16_часть2.doc
Межосевые расстояния валов коробки (мм) находятся по зависимости
Расчет клиноременной передачи.
По табл. 6.11 [4] принимаем тип ремня А.
Окружная скорость ремня:
где d1 = 120 мм – диаметр меньшего шкива;
n1 = 1455 мин-1 – частота вращения электродвигателя.
Диаметр большего шкива по [4]:
Угол обхвата ремнем малого шкива вычисляется по формуле [4]:
где а = 200 мм – межосевое расстояние.
Мощность передаваемая одним ремнем в условиях эксплуатации вычисляем по формуле:
где No – номинальная мощность передачи с одним ремнем кВт. No = 135 кВт (по таблице для ремня В);
ca = 1 – коэффициент угла обхвата;
cj = 093 – коэффициент учитывающий длину ремня (L = 1600 мм);
cp = 10 – коэффициент динамичности и режима работы.
Количество ремней необходимых для передачи рабочей мощности определяем по формуле:
где сk = 095 – коэффициент учитывающий число ремней.
Рисунок 1. Расчетная схема вала 1
Расчетная схема вала 1 приведена на рис. Исходные данные для расчета: уточненное значение крутящего момента на данном валу Mкр1=28.05 Н·м делительный диаметр зубчатого колеса d2=0099 м. На данный вал действуют два силовых фактора – от зубчатой и от ременной передачи.
Окружная сила в зубчатом зацеплении
Px2=2·Мкр2= 566.66 Н
Сила от ременной передачи
Py1 = Px1·0.5= 233.750 Н.
Py2 = Px2·0.5=566.660.5= 283.334 Н.
Результирующая сила от зубчатой передачи
Q2 = 1.1· Px2=1.1· 566.66=623.334 Н.
Результирующая сила от ременной передачи
Q1 =1.1· Px1= 514.250 Н.
от ременной передачи
Q1x = Q1·cos(60)= 257.320 Н
от зубчатой передачи
Q2x = Q2·cos(26)= 560.31 Н
Q1y= Q1·sin(60)= 445.218 Н
Q2y = Q2·sin(26)= 273.123 Н
Реакция Rbx находится из уравнения моментов относительно т. А
-16.724144 + 0.330 Rbx = 0
Реакция Rax из уравнения моментов относительно т. В
-253.107616 + 0.330 Rax = 0
Уравнение моментов в плоскости x
Mx1= -Q1x·x= -18.0 Н·м
Mx2= -Q1x·(0.07+x)+ Rax·x= 13.6 Н·м
Mx3= Rbx·x= 13.6 Н·м.
Рассмотрим плоскость y:
Реакция Rby из уравнения моментов относительно т. А
231634 + 0.330 Rby = 0
Rby = -43.126 Н (здесь и далее знак «минус» указывает на то что данная реакция направлена вниз).
Реакция Ray из уравнения моментов относительно т. В
-251.284164 + 0.330 Ray = 0
Уравнение моментов в плоскости y
My1 = -Q1у·у= 529 Н·м
My2 = -Q1у·(0.07+у)+ Rax·x= 58.7 Н·м
My3 = Rbу·у= 58.7 Н·м.
Эпюра моментов в плоскости y показана на рис.
Максимальный момент Н·м
Расчет на жесткость проводим определив угол наклона упругой линии в опасном сечении d0 = 4 см при этом эмпирические коэффициенты K1x = 1. K2x = -0.12 K1y = 1. K2y = -0.12. Тогда по рекомендации [3] предполагаемый диаметр вала в опасном сечении
Результирующий угол наклона упругой линии в плоскости x
Угол наклона упругой линии в плоскости y от каждой силы
Результирующий угол наклона упругой линии в плоскости y
Результирующий угол наклона
По рекомендации [4] допустимый угол наклона упругой линии [q]=0.001 тогда [q]>q или 0001000068. Т.о. рассчитываемый вал проходит по данному критерию прочности.
Проверка по прогибу выполняется по формуле
Прогиб в плоскости x от каждой силы
Результирующий прогиб в плоскости x
Прогиб в плоскости y
Результирующий прогиб в плоскости y
Результирующий макс. прогиб
Максимально допустимый прогиб
Т.о. вал удовлетворяет условию прочности по прогибу.
Расчетная схема вала 2 приведена на рис. Исходные данные для расчета: уточненное значение крутящего момента на данном валу Mкр1=33.97 Н·м
делительные диаметры зубчатых колес d1=0.085 м d2=0.082 м.
Рисунок 2. Расчетная схема вала 2
Окружные силы действующие в зубчатом зацеплении
Py1 = Px1·0.5= 799.294·0.5=399.647 Н.
Py2 = Px2·0.5=828.536·0.5=414.268 Н.
Результирующие силы
Q1 =1.1· Px1=1.1· 799.294= 879.223 Н
Q2 = 1.1· Px2=1.1· 828.536=566.66=911.390 Н.
Q1x = Q1·cos(26)= 790.329 Н
Q2x = Q2·cos(26)= 819.244 Н
Q1y= Q1·sin(26)= 385.245 Н
Q2y = Q2·sin(26)= 399.339 Н
3.841932 + 0.446 Rbx = 0
-504.027626 - 0.446 Rax = 0
Mx1= - Rax·x = -63.29 Н·м
Mx2= - Rax·(0.056+x)+ Q1x·x = -114.6 Н·м
Mx3= -Rbx·x=-114.6 Н·м.
-61.089453 + 0.446 Rby = 0
-54.803529 - 0.446 Ray = 0
My1 =-Raу·x =-6.88 Н·м
My2 =-Raу·(0.056+у)+Q1у·у =32.7 Н·м
My3 =Rbу·у= 32.7 Н·м.
Расчет на жесткость проводим определив угол наклона упругой линии в опасном сечении d0 = 2.3 см. Тогда по рекомендации [3] предполагаемый диаметр вала в опасном сечении
00140-0.00058=0.00082 рад
00068+(-0.00028)=0.0004 рад
Результирующий максимальный прогиб
Расчетная схема вала 3 приведена на рис. Исходные данные для расчета: уточненное значение крутящего момента на данном валу Mкр1=52.59 Н·м
делительные диаметры зубчатых колес d1=0.068 м d2=0.158 м.
Рисунок 3. Расчетная схема вала 3
Px1 =2·Мкрd=2·52.590.068=1546.76 Н
Px2 =2·Мкрd=2·52.590.158=665.696 Н
Py1 = Px1·0.5= 1546.76·0.5=773.380 Н.
Py2 = Px2·0.5=665.696·0.5=332.848 Н.
Q1 =1.1· Px1=1.1· 1546.76= 1701.44 Н
Q2 = 1.1· Px2=1.1· 665.696=732.266 Н.
Q1x = Q1·cos(26)= 1529.42 Н
Q2x = Q2·cos(26)= 658.230 Н
Q1y= Q1·sin(26)= 745.511 Н
Q2y = Q2·sin(26)= 320.853 Н
-380.960810 + 0.446 Rbx = 0
4.731090 - 0.446 Rax = 0
Mx1= Rax·x = 213.4 Н·м
Mx2= Rax·(0.16+x)-Q1x·x =204.1 Н·м
Mx3= Rbx·x=204.1 Н·м.
-52.865189 + 0.446 Rby = 0
6.532279 - 0.446 Ray = 0
My1 =Raу·x =48.98 Н·м
My2 =Raу·(0.056+у)-Q1у·у =28.32 Н·м
My3 =Rbу·у= 28.32 Н·м.
Расчет на жесткость проводим определив угол наклона упругой линии в опасном сечении d0 = 2.8 см. Тогда по рекомендации [3] предполагаемый диаметр вала в опасном сечении
-0.00048-0.00021=-0.00069 рад
-0.00024+(-0.00010)= -0.00034 рад
Расчетная схема вала 4 приведена на рис. Исходные данные для расчета: уточненное значение крутящего момента на данном валу Mкр1=203.37 Н·м
делительные диаметры зубчатых колес d1=0.228 м d2=0.080 м.
Рисунок 4. Расчетная схема вала 4
Px1 =2·Мкрd=2·203.370.228=1783.95 Н
Px2 =2·Мкрd=2·203.370.080=5084.24 Н
Py1 = Px1·0.5= 1783.95·0.5=891.975 Н.
Py2 = Px2·0.5=5084.24·0.5=2542.12 Н.
Q1 =1.1· Px1=1.1· 1783.95= 1962.34 Н
Q2 = 1.1· Px2=1.1· 5084.24=5592.66 Н.
Q1x = Q1·cos(26)= 1763.94 Н
Q2x = Q2·cos(26)= 5027.21 Н
Q1y= Q1·sin(26)= 859.829 Н
Q2y = Q2·sin(26)= 2450.51 Н
94.33221 + 0.450 Rbx = 0
-1461.68529 - 0.450 Rax = 0
Mx1= -Rax·x = -519.7 Н·м
Mx2= -Rax·(0.16+x)+Q1x·x =-669.6 Н·м
Mx3= -Rbx·x=-669.6 Н·м.
-502.01047 + 0.450 Rby = 0
3.795980 - 0.450 Ray = 0
My1 =Raу·у =76.02 Н·м
My2 =Raу·(0.16+у)+Q1у·у =210.8 Н·м
My3 =Rbу·у= 210.8 Н·м.
Расчет на жесткость проводим определив угол наклона упругой линии в опасном сечении. Тогда по рекомендации [3] предполагаемый диаметр вала в опасном сечении
Т.о. рассчитываемый вал проходит по данному критерию прочности.
6К81Г_P6_z16_литература.doc
Кинематический расчет приводов станков. Учебное пособие. Пенза: ПГУ 2003.
Проектирование металлорежущих станков и систем. Под ред. А.С. Проникова. Справочник-учебник в трех томах. Том 12. М.: Высшая школа 1994.
Михеев И.И. “Приводы главного движения и шпиндельные узлы МРС”. Учебное пособие. Пенза: ПГТУ 1994.
Ицкович Г.М. Курсовое проектирование деталей машин. М.: Машиностроение 1970.
Дунаев П.Ф. “Конструирование узлов и деталей машин”. Учебное пособие. М.: Высшая школа 1982.
Н.С. Ачеркан “Металлорежущие станки”. М.: Машиностроение 1953.
И. И. Михеев Е. Н. Ярмоленко В. О. Трилисский А. В. Липов. Альбом примеров конструкций узлов металлорежущих станков. Методические указания. Пенза 2001 г.
Оформление учебно-конструкторской документации. Методические указания для выполнения курсовых и дипломных проектов. Пенза: ПГУ1998.
6К81Г_Р5_z16__vid.dwg

ПензГу 1.151002(120200).044СБ1
Изм.Лист №докум. ПодписьДата
Кафедра:МСиК" гр. 99ЗМИ1
D-8x32x38xH12a11 x8xF10j7
D-8x40x45xH12a11 x8xF10j7
D-8x46x52xH12a11 x8xF10j7
Структурная схема привода
График частот вращения
ПензГу 1.151002(120200).044СК2
Кафедра:"МСиК" гр. 99ЗМИ1
горизонтально-фрезерного
Кинематическая схема
Структурная схема привода подач
6К81Г_Р5_z4__vid.dwg

ПензГу 1.151002(120200).044СБ1
Изм.Лист №докум. ПодписьДата
Кафедра:МСиК" гр. 99ЗМИ1
D-8x32x38xH12a11 x8xF10j7
D-8x40x45xH12a11 x8xF10j7
D-8x46x52xH12a11 x8xF10j7
Структурная схема привода
График частот вращения
Кафедра:"МСиК" гр. 99ЗМИ1
ПензГу 1.151002(120200).044СК1
Кинематическая схема
горизонтально-фрезерного
Структурная схема привода подач
6К81Г_P6_z4_arhitect.dwg

ПензГу 1.151002(120200).044ВО
Кафедра:"МСиК" гр. 99ЗМИ1
6К81Г_P6_z16_часть5.doc
Кинематический расчет привода главного движения.
В данном случае привод имеет комбинированное регулирование. Он сочетает ступенчатую коробку скоростей с регулируемым двигателем постоянного тока двигателем. Согласно [1] предполагаемый диапазон регулирования привода главного движения
где nma nmin=40 мин-1 максимальная и минимальная частоты вращения шпинделя соответственно.
По рекомендации [1] и [2] подбирается приводной двигатель постоянного тока 2ПБ180L имеющий следующие характеристики: максимальную частоту вращения nДВma номинальную частоту вращения nДВном=750 мин-1; номинальную мощность Pном=52 кВт. Далее определяется число групп передач коробки скоростей при условии что диапазон регулирования каждой группы равен 8 по формуле
Далее рассчитываются диапазоны регулирования групп передач при условии что их значения одинаковы
Находим величину с по формуле с=
Принимаем с=3. Тогда Km=
Принимаем Km=7; т.к. это последняя группа (m=b) то принимаем Kb=7 откуда Ka=7. При этом фактические диапазоны регулирования коробки скоростей будут равны
Находим величину К1 с по формуле
Принимаем величину К1=2
Принимаем величину К2=17. Следовательно общее число интервалов К=К1+К2=17+2=19. Откуда график должен иметь 20 горизонтальных линий с интервалом равным логарифму 1.26 в соответствующем принятом масштабе.
График чисел оборотов показан на рис.
Диапазон регулирования электродвигателя при постоянной мощности равен R=
Диапазон регулирования коробки
Число скоростей коробки равно
Рисунок 1. График чисел оборотов
Число скоростей принимается равным 4. Окончательно принимаем φ=1.26
Находим величину с по формуле
Находим величину Кm с по формуле
Принимаем величину Кm=9 оставшиеся 5 интервалов можно получить регулированием с постоянным моментом
Рисунок . Кинематическая схема коробки скоростей
Для обеспечения требуемых частот вращения шпинделя надо реализовать следующие передаточные отношения
или принимая по стандартному ряду [1]
Подбор чисел зубьев осуществляется по нормалям станкостроения [1] и [2]. Откуда для рассматриваемых передач можно записать:
Известна формула для определения потерь на валах привода [2]:
где h hп = 099 – КПД подшипников. Тогда можно записать что потери на валах (безразмерные)
Передаваемая валом мощность находится по формуле [5]
Крутящие моменты передаваемые на валы Н·м
где расчетная частота вращения
nрасч =nmin·R0.25= мин-1
Предварительно диаметры валов находятся по формуле (см. [1]).
где K Pi – мощность на валу кВт ni – частота вращения вала мин–1.
Расчет зубчатых передач сводится к определению модуля по методикам изложенным в курсе «Детали машин» [5] . Для коробок скоростей определяют модуль по контактным напряжениям:
и проверяют на изгиб: .
Исходные данные для расчета:
Коэффициент зависящий от материала зубчатых колес
Крутящий момент Mкр= Н·м;
Коэффициент зависящий от распределения нагрузки по ширине зуба
Коэффициент зависящий от распределения нагрузки по длине зуба
Передаточное отношение u = 3.99.
Принимается отношение ширины венца к делительному диаметру
Материал зубчатых колес сталь 45.
Допускаемые контактные напряжения соответствующие базовому числу циклов нагружения
базовое число циклов нагружения для изгибных напряжений
Частота вращения n = 315 мин-1
коэффициент формы зуба
Коэффициент учитывающий тип колеса - прямозубые Km=14
Расчетное число циклов нагружения
Расчетный коэффициент для контактных напряжений
Тогда принимаем Khl = 1. Допускаемые контактные напряжения
Тогда принимаем Kfl = 1. Допускаемые изгибные напряжения
Модуль по контактным напряжениям
Окончательно принимаем m=4.5 мм.
Частота вращения n = 80 мин-1
m = 4.122 мм и при проверке на изгиб
Геометрические параметры зубчатых передач рассчитываются в следующей последовательности
Межосевые расстояния мм
6К81Г_P6_z16_спецификация2.doc
ПензГУ 1.120200.044Д001
ПензГУ 1.120200.044Д002
ПензГУ 1.120200.044Д003
ПензГУ 1.120200.044Д004
ПензГУ 1.120200.044Д005
ПензГУ 1.120200.044Д006
ПензГУ 1.120200.044Д007
ПензГУ 1.120200.044Д008
ПензГУ 1.120200.044Д009
ПензГУ 1.120200.044Д010
ПензГУ 1.120200.044Д011
ПензГУ 1.120200.044Д012
ПензГУ 1.120200.044Д013
ПензГУ 1.120200.044Д014
ПензГУ 1.120200.044Д015
ПензГУ 1.120200.044Д016
ПензГУ 1.120200.044Д017
ПензГУ 1.120200.044Д018
ПензГУ 1.120200.044Д019
ПензГУ 1.120200.044Д020
ПензГУ 1.120200.044Д021
ПензГУ 1.120200.044Д022
ПензГУ 1.120200.044Д023
ПГУ 1.120200.044 СБ3
ПензГУ 1.120200.044Д028
ПензГУ 1.120200.044Д029
ПензГУ 1.120200.044Д030
ПензГУ 1.120200.044Д031
ПензГУ 1.120200.044Д032
ПензГУ 1.120200.044Д033
ПензГУ 1.120200.044Д034
ПензГУ 1.120200.044Д035
ПензГУ 1.120200.044Д036
ПензГУ 1.120200.044Д037
ПензГУ 1.120200.044Д038
ПензГУ 1.120200.044Д039
ПензГУ 1.120200.044Д040
ПензГУ 1.120200.044Д041
ПензГУ 1.120200.044Д042
Винт М8х25 ГОСТ 11378-84
Кольца ГОСТ 13941-86
Кольца ГОСТ 13942-86
Манжета ГОСТ 8752-79
Подшипник ГОСТ 8838-75
ПГУ 1. 120200.0044СБ3
Подшипник 7312 37.006.162.162-89
Шайба 14Н ГОСТ 6402-70
Шайба20.08кп05ГОСТ 11872-80
Шпонка ГОСТ 23360-78
Шпонка 41-45 ГОСТ 24071-97
Подшипник ГОСТ 9890-75
Раздел1.doc
Реферат.doc
СТАНОК ГОРИЗОНТАЛЬНО-ФРЕЗЕРНЫЙ КОРОБКА СКОРОСТЕЙ РАЗДЕЛЕННЫЙ ПРИВОД МЕХАНИЗМ УПРАВЛЕНИЯ.
Объектом разработки является привод главного движения горизонтально-фрезерного станка.
Цель работы – сравнительный анализ конструкций коробок скоростей с комбинированным и ступенчатым регулированием.
В процессе работы были проведены кинематические расчеты проектируемых приводов главного движения. Выполнены необходимые силовые прочностные и жесткостные расчеты а также динамический расчет коробок скоростей.
Эффективность конструкции привода с комбинированным регулированием определяется его высокой производительностью и возможностью работать в очень широком диапазоне скоростей резания.
6К81Г_P6_z16_ведомость.doc
Пояснительная записка
Кинематическая схема
Горизонтально-фрезерный станок. Ведомость дипломного проекта.
6К81Г_P6_z16_часть6.doc
Рисунок . Расчетная схема вала 1
Расчетная схема вала 1 приведена на рис. Исходные данные для расчета: уточненное значение крутящего момента на данном валу Mкр1=64.22 Н·м делительный диаметр зубчатого колеса d2=0.217 м. На данный вал действуют два силовых фактора – от зубчатой и от ременной передачи.
Окружная сила в зубчатом зацеплении
Сила от ременной передачи
Py1 = Px1·0.5= 482.80 Н.
Py2 = Px2·0.5=591.880.5= 295.94 Н.
Результирующая сила от зубчатой передачи
Q2 = 1.1· Px2=1.1· 566.66=651.07 Н.
Результирующая сила от ременной передачи
Q1 =1.1· Px1= 1062.16 Н.
от ременной передачи
Q1x = Q1·cos(60)= 531.57 Н
от зубчатой передачи
Q2x = Q2·cos(26)= 585.25 Н
Q1y= Q1·sin(60)= 919.579 Н
Q2y = Q2·sin(26)= 285.279 Н
Реакция Rbx находится из уравнения моментов относительно т. А
41058092 + 0.264 Rbx = 0
Реакция Rax из уравнения моментов относительно т. В
-302.2514511 + 0.264 Rax = 0
Уравнение моментов в плоскости x
Mx1= Q1x·x= 42.5 Н·м
Mx2= Q1x·(0.08+x)+ Rax·x= -5.73 Н·м
Mx3=-Rbx·x= -5.73 Н·м.
Рассмотрим плоскость y:
Реакция Rby из уравнения моментов относительно т. А
44958711 + 0.264 Rby = 0
Rby = -213.82 Н (здесь и далее знак «минус» указывает на то что данная реакция направлена вниз).
Реакция Ray из уравнения моментов относительно т. В
-374.5322749 + 0.264 Ray = 0
Уравнение моментов в плоскости y
My1 = Q1у·у= 73.6 Н·м
My2 = Q1у·(0.08+у)-Rax·x= -43.6 Н·м
My3 = -Rbу·у= -43.6 Н·м.
Эпюра моментов в плоскости y показана на рис.
Максимальный момент Н·м
Расчет на жесткость проводим определив угол наклона упругой линии в опасном сечении d0 = 3 см при этом эмпирические коэффициенты берутся по рекомендации [3].
Результирующий угол наклона упругой линии в плоскости x
Угол наклона упругой линии в плоскости y от каждой силы
Результирующий угол наклона упругой линии в плоскости y
Результирующий угол наклона
По рекомендации [4] допустимый угол наклона упругой линии [q]=0.001 тогда [q]>q или 0001000062. Т.о. рассчитываемый вал проходит по данному критерию прочности.
Проверка по прогибу выполняется по формуле
Прогиб в плоскости x от каждой силы
Результирующий прогиб в плоскости x
Прогиб в плоскости y
Результирующий прогиб в плоскости y
Результирующий макс. прогиб
Максимально допустимый прогиб
Т.о. вал удовлетворяет условию прочности по прогибу.
Рисунок 1. Расчетная схема вала 5
Расчетная схема шпинделя приведена на рис . Уточненное значение крутящего момента на данном валу Mкр1=392.37 Н·м. На данный вал действуют два силовых фактора – от сил резания и от ременной передачи.
Py1 = Px1·0.5=3278.08 Н.
Q1 =1.1· Px1= 7211.78 Н.
Q1x = Q1·cos(60)= 6482.63 Н
Q1y= Q1·sin(60)= 3159.95 Н
-3165.4465 + 0.45 Rbx = 0
51.737 - 0.45 Rax = 0
Mx1=-Q1x·x=-400.0 Н·м
Mx2= -Q1x·(0.1+x)+Rвx·x= -648.26 Н·м
Mx3= -Q2x·x= -648.26 Н·м.
-1537.9725 + 0.45 Rby = 0
4.005 - 0.45 Ray = 0
My1 = -Q1у·у= -200.0 Н·м
My2 = Q1у·(0.1+у)- Ray·x= -316.01 Н·м
My3 = -Q2у·у =-316.01 Н·м.
По предварительным расчетам прочностным требованиям удовлетворяет диаметр вала d=5 см.
Расчет на жесткость для шпинделя сводится к определению радиального биения переднего конца шпинделя по формуле:
где PZ=4000 H тангенциальная составляющая силы резания Н; JA JB осевые моменты инерции в сечениях А и В мм4; jA jB жесткости в сечениях А и В Нмм; a=100 мм величина консоли; b=450 мм межопорное расстояние; E=2·105 МПа модуль упругости материала шпинделя.
Радиальная жесткость:
Согласно рекомендациям справочной литературы наименьшее поле допуска деталей обрабатываемых на данном станке должно быть .
6К81Г_P6_z4_svert.dwg

nmin=20 мин 4. Регулирование комбинированное при помощи коробки скоростей и регулируемого электродвигателя.
Технические требования 1.Производить динамическую балансировку шпинделя в сборе
остаточная неуравновешенность не более 10гмм. 2.Условия и методы испытания по ГОСТ 16162-85. 3.Допустимый уровень шума не более 60 Дб. 4.Вращение шпинделя плавное без рывков. 5.Система смазки комбинированная: разбрызгиванием и поливом. 6.В коробку залить 5 литров масла И-20А ГОСТ 20799-85. 7.Течь масла не допускается.
ПензГу 1.151002(120200).044СБ
Кафедра:"МСиК" гр. 99ЗМИ1