Метрологическое обеспечение современного производства по изготовлению детали Колесо зубчатое




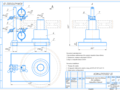
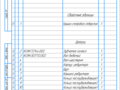
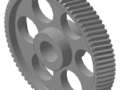
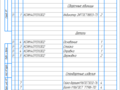
- Добавлен: 24.01.2023
- Размер: 3 MB
- Закачек: 1
Описание
Метрологическое обеспечение современного производства по изготовлению детали Колесо зубчатое
Состав проекта
![]() |
![]() ![]() ![]() ![]() |
![]() ![]() ![]() |
![]() ![]() ![]() ![]() |
![]() |
![]() ![]() ![]() ![]() |
![]() ![]() ![]() ![]() |
![]() |
![]() ![]() ![]() ![]() |
Дополнительная информация
кип.cdw

Приспособление предназначено для контроля торцевого биения детали.
Погрешность измерения индикаторов 0
Допуск на торцевое биение 0
Контрольное приспособление
ИжГТУим. Калашникова
*Размеры для справок.
На трущиеся поверхности нанести смазку ЦИАТИМ-201 ГОСТ-6267-74.
Острые кромки не допускаются.
Технические требования:
ПЗ.docx
РЕДУКТОР ЦИЛИНДРИЧЕСКИЙ ОДНОСТУПЕНЧАТЫЙ ЗУБЧАТОЕ
КОЛЕСО СРЕДСТВА КОНТРОЛЯ МЕТРОЛОГИЧЕСКИЙ АНАЛИЗ
Объект исследования – деталь цилиндрического одноступенчатого редуктора зубчатое колесо.
Цель работы: метрологическое обеспечение современного среднесерийного машиностроительного производства по изготовлению изделия «Редуктор цилиндрический
В пояснительной записке приведено служебное назначение и описание работы редуктора проведен метрологический анализ и выбраны специальные средства контроля разработано контрольно-измерительное приспособление для проверки торцевого биения детали«Колесо зубчатое».
В графической части работы представлены чертежи: сборочный чертеж редуктора
чертеж детали зубчатое колесо 3D – модель детали контрольно-измерительное приспособление размерный анализ КИП.
В работе представлена карта технологического контроля на зубчатое колесо.
Содержание Введение 3
Исходные данные по курсовой работе . 4
1Чертеж изделия и детали 4
2Общие технические параметры и характеристика данных по изделию 5
3 Перечень материалов и их содержание полученных в ходе работы в Internet по современному технологическому оборудованию инструменту технологиям и средствам измерений 6
4 Технические требования на изделие и деталь. Материал детали и его свойства 9
1Техническое описание изделия и детали обоснование служебного назначения
описание условий работы и рабочих режимов эксплуатации 10
2 Основные требования к параметрам точности для соединений деталей редуктора назначение целесообразных посадок на основе анализа и обоснование сделанного выбора. Требования к параметрам точности детали .. .11
Технологическая часть ..13
1 Описание типового технологического процесса контроля детали . 13
2 Выбор схем и методов измерения 13
3 Метрологический анализ и экспертиза контролепригодности детали. Выбор согласно РД 50-98-86 универсальных средств измерения линейных размеров 15
4 Определение согласно ГОСТ 8.051-81 параметров разбраковки «m n c» при приемочном контроле детали .. 22
5 Выбор средств контроля шероховатости поверхностей отклонений формы и расположения поверхностей детали а также других параметров заданных чертежом 28
6 Выбор средств измерения твердости детали 31
7 Составление карты контроля .33
8 Контроль правильности сборки редуктора испытания редуктора 33
Конструкторская часть 36
1 Обзор и анализ научно-технической информации по контрольно-измерительным приспособлениям (КИП) 36
2 Анализ исходных данных для проектирования КИП. Основные требования предъявляемые к приспособлению . 38
3 Описание конструкции КИП его принцип действия .. 39
Заключение 50 Список литературы 51
Метрология изучает широкий круг вопросов связанных как с теоретическими проблемами так и с задачами практики. К их числу относятся: общая теория измерений единицы физ. Величин и их системы методы и средства измерений методы определения точности измерений основы обеспечения единства измерений и единообразия средств измерений эталоны и образцовые средства измерений методы передачи размеров единиц от эталонов к рабочим средствам измерения. Большое значение имеет изучение метрологических характеристик средств измерений влияющих на результаты и погрешности измерений.
Измерения являются инструментом познания объектов и явлений окружающего мира. Объектами измерений являются физические объекты и процессы окружающего нас мира. Вся современная физика может быть построена на семи основных величинах которые характеризуют фундаментальные свойства материального мира. К ним относятся: длина масса время сила электрического тока термодинамическая температура количество вещества и сила света. С помощью этих и двух дополнительных величин – плоского и телесного углов – введенных исключительно для удобства образуется все многообразие производных физических величин и обеспечивается описание свойств физических объектов и явлений [2 стр. 202].
Данная курсовая работа является актуальной так как связанна с выбором современных измерительных средств и разработкой оптимальной конструкции контрольно-измерительного приспособления а также модернизации процесса контроля деталей общемашиностроительного применения.
Исходные данные по курсовой работе.
1 Чертеж изделия и детали.
Сборочный чертеж редуктора цилиндрического одноступенчатого шевронного представлен на рисунке 1.
Рис. 1. Сборочный чертеж редуктора.
Рабочий чертеж детали «Зубчатое колесо» представлен на рисунке 2.
Рис. 2. Чертеж детали зубчатое колесо.
2 Общие технические параметры и характеристика данных по изделию.
Редукторы такого типа могут быть использованы в приводах машин общего машиностроения в изделиях подъемно-транспортного оборудования а также для ремонтно-эксплуатационных нужд действующего оборудования.
Технические характеристики редуктора.
Электродвигатель 4А112МВ6
Межосевое расстояние – 250мм.
3 Перечень материалов и их содержание полученные в ходе работы в глобальной сети Internet по современному оборудованию инструменту технологиям и средствам измерений.
Современные тенденции в конструкции зубчатых колес и технологии их обработки.
Требования к точности изготовления зубчатого венца определяются эксплуатационными требованиями к зубчатому зацеплению. К этим требованиям крупнено можно отнести: износостойкость виброустойчивость шумность передаваемый крутящий момент надежность и плавность. Все эти требования ужесточаются по мере развития техники. Соответственно ужесточаются и требования по точности к зубчатым венцам и совершенствуются методы контроля этих требований.
В настоящий момент совершенно четко прослеживаются несколько тенденций в изменении технологических и точностных требований к зубчатым колесам. В основе лежит ужесточение требований к зубчатым передачам обусловленное повышенными требованиями к конечному продукту куда входят детали с зубчатым венцом (редукторам коробкам передач):
-снижение стоимости;
-снижение уровня шума;
-снижение габаритных размеров;
-повышение надежности;
-увеличение передаваемого момента мощности;
-улучшение динамических характеристик;
-повышение коэффициента полезного действия;
-увеличение срока службы;
-увеличение ремонтопригодности.
Повышенные требования к изделиям определяют соответствующее повышение требований к зубчатым колесам входящим в состав современных изделий. Отклонения отдельных параметров зуба и зубчатого венца влияют на функциональные возможности зубчатого колеса или пары колес в зубчатом зацеплении. Проще говоря только зубчатое колесо с правильным эвольвентным профилем и точным шагом обеспечивает передачу вращения с постоянной угловой скоростью.
Основные характеристики зубчатых колес которые должны быть обеспечены конструктивными и технологическими методами:
- точность (динамика плавность работы);
- передача больших моментов (трение высокие нагрузки знакопеременные нагрузки);
- минимальная стоимость;
- дополнительные функции (синхронизация — наличие дополнительных венцов).
Эти требования должны быть обеспечены соответствующим контролем в процессе изготовления деталей с зубчатыми венцами.
Основные современные тенденции в измерении зубчатых колес:
- не просто измерение детали с заключением «годная — негодная» а анализ отклонений с обратной связью с производством;
- более высокая точность измерений;
-более высокая скорость измерения (в автомобильной промышленности не более 3 минут на деталь);
-возможность контроля непосредственно в производстве (сокращение времени ожидания решения);
-возможность измерения модификаций и топографии зуба;
-внедрение новых стандартов измерения и оценки;
-достоверность измерений;
-выдача стандартизованных протоколов (прослеживаемость результатов на различных стадиях производства и при поставке изделия потребителю);
-эти тенденции привели к появлению новых методов контроля зубчатых венцов;
-современные средства контроля зубчатых венцов.
Совершенствование систем управления и повышение точности а также необходимость повторяемости измерений привело к широкому внедрению зубоизмерительных машин (рис. 5) – универсальных приборов для контроля зубчатых венцов.
Зубоизмерительные машины.
Зубоизмерительная машина является средством аналитического контроля отклонений зубчатого венца. Применение этого средства контроля обеспечивает оптимальное качество контроля и представления результатов проверки параметров зубчатого венца. Получаемые результаты дают полную информацию о причинах возникновения погрешностей и позволяют использовать эту информацию для соответствующей корректировки технологии изготовления детали. К недостаткам данного метода проверки следует отнести длительный цикл измерения и сложность в применении зубоизмерительной машины непосредственно около станка – являясь метрологическим средством очень высокой точности машина требует установки в специально подготовленное помещение.
Принцип работы зубоизмерительной машины и традиционных приборов для контроля эвольвенты направления зуба и шага зубьев во многом схож. В процессе измерения щуп измерительной машины сканирует боковую поверхность зуба по профилю (рис. 3) по линии зуба (рис. 4) и последовательно касается всех боковых сторон зубьев. В результате этих основных проверок определяется погрешность профиля погрешность линии зуба отклонения шагов и погрешность радиального биения.
Получаемые при измерении детали протоколы дают широкие возможности для оценки причин возникновения погрешностей. Для этого существуют определенные методики. Например при получении диаграммы профиля можно определить пять основных причин возникновения данной погрешности:
- биение фрезы на оправке (может быть вызвано плохой фрезой поврежденной оправкой или загрязнением оправки при монтаже);
- неправильная заточка фрезы (фреза была переточена с радиальным биением из-за установки с перекосом на оправку или оправки на заточной станок);
- слабо закрепленная или изношенная оправка в противоопоре станка;
-слишком большой люфт шпинделя фрезы фрезерного станка;
-слишком большой люфт стола фрезерного станка.
Рис.5 – Зубоизмерительная машина
Современные средства измерения зубчатых колес – зубоизмерительные машины – позволяют выполнить основные требования которые определяются современной конструкцией и технологией изготовления. На обеих боковых поверхностях трех или четырех зубьев измеряются погрешности профиля и линии зуба. На всех зубьях измеряются погрешности шага по обеим боковым поверхностям и погрешности радиального биения. Кроме этого производится измерение толщины зуба (размера по шарикам). Время измерения зубчатого колеса составляет около 3 мин. Зубоизмерительная машина обеспечивает измерение зубчатых колес при замене инструмента на стыке рабочих смен и при изменениях в технологическом процессе. Зубоизмерительная машина также обеспечивает измерение топографии зуба с оценкой пятна контакта.
Зубоизмерительная машина не имеет ограничений в части измерения колес с нестандартными параметрами профиля и линии зуба (модификации по профилю и линии зуба).
Практически зубоизмерительная машина как современное средство измерения заменяет все ранее применявшиеся приборы для контроля зубчатых колес и позволяет измерять кроме цилиндрических колес также конические колеса червяки червячные колеса и зуборезные инструменты (червячные фрезы долбяки и шеверы).
4 Технические требования на изделие и деталь. Материал детали и его свойства.
Технические требования на изделие:
Плоскости разъема покрыть тонким слоем герметика УТ-34 ГОСТ 24285-80 при окончательной сборке.
Наружные поверхности редуктора покрыть атмосферостойким покрытием Эмаль МЛ-152 зеленая II.V.
Общие допуски по ГОСТ 30893.1: H14 h14.
Допускается опорные поверхности редуктора не окрашивать.
Для смазки подшипников применять Литол – 24 ГОСТ 21150-87.
В редуктор залить 9 л. Масло И-Г-А-50 ГОСТ 20799-88. 7.Остальные ТТ по ГОСТ Р 50891-96.
Технические требования на деталь типа зубчатое колесо:
Твердость поверхности зубьев HRC 45 50.
Неуказанные размеры радиусов не более 06 мм.
Острые кромки притупить 04*45 max.
Остальные технические требования по ГОСТ 1643-81. 5.Общие допуски по ГОСТ 30893.1: H14 h14 +- IT142.
Зубчатое колесо изготовлено из стали 40Х ГОСТ 4543-71
Сталь 40Х характеристики
Химический состав в % Стали 40Х ГОСТ 4543-71
Технологические свойства Стали 40Х ГОСТ 4543-71
1Техническое описание изделия и детали обоснование служебного назначения описание условий работы и рабочих режимов эксплуатации.
Служебное назначение изделия «Редуктор цилиндрический одноступенчатый».
Редуктором называют механизм состоящий из зубчатых или червячных передач выполненный в виде отдельного агрегата и служащий для передачи вращения от вала двигателя к валу рабочей машины.
Редуктор одноступенчатый цилиндрический состоит из корпуса и верхней крышки соединяясь при помощи крепежных болтов для предотвращения протекания масла плоскости раздела смазывают спиртовым лаком или жидким стеклом.
Назначение редуктора – понижение угловой скорости и соответственно повышение вращающегося момента ведомого вала по сравнению с ведущим.
Редукторы широко применяют в различных отраслях машиностроения поэтому число разновидностей их велико.
Редукторы применяют также и в других отраслях промышленности.
Редукторы определяются составом передач порядком их размещения в направлении от быстроходного вала к тихоходному валу и положением осей валов в пространстве.
Типоразмер редуктора определяется типом и главным параметром тихоходной ступени.
Исполнение редуктора определяется передаточным числом вариантом сборки и
формой концевых участков вала.
Основная энергетическая характеристика редуктора – номинальный вращающий момент Т на его тихоходном валу при постоянной нагрузке.
Цилиндрические редукторы благодаря широкому диапазону передаваемых мощностей долговечности простоте изготовления и обслуживания получили широкое распространение в машиностроении.
Техническая характеристика редуктора: двигатель 4А112МВ6 мощность электродвигателя 4 кВт; частота вращения вала электродвигателя 950 обмин; передаточное отношение 1654; число зубьев шестерни 19; число зубьев зубчатого колеса 77; модуль зубьев 5; угол зацепления 20°; угол наклона зубьев 16°16' класс точности 3; общий вес 122 кг; коэффициент полезного действия не менее 096.
Служебное назначение детали типа зубчатое колесо.
Зубчатое колесо КСИН.721444.002 служит для передачи вращательного движения. Колеса образуют зубчатые зацепления с помощью которых передается вращательное движение валам и изменяется частота вращения.
Техническая характеристика детали типа зубчатое колесо:
Габариты: ширина B = 80мм; диаметр вершин dma материал: сталь 40Х; твердость не менее 45 50 НRC модуль m=5 мм; число зубьев: z=77; коэффициент смещения: делительный диаметр колеса d0 = 40104 мм; масса 2928 кг.
Редуктор допускает применение в следующих условиях:
Нагрузка постоянная или переменная одного направления и реверсивная;
Работа постоянная (до 24 ч в сутки) и с периодическими остановками;
Вращение валов в любую сторону;
Умеренный сухой и влажный тропический климат по ГОСТ 15150-69;
Влажность при температуре 20 - до 95%.
Эксплуатация и техническое обслуживание редуктора.
Перед началом эксплуатации редукторов вращающиеся детали на внешних концах валов должны быть ограждены.
Места редуктора с температурой наружных поверхностей выше 70 °C доступные для обслуживающего персонала должны быть ограждены или промаркированы символом и дополнительной табличкой с указанием температуры.
Зубчатые передачи и подшипниковые узлы редукторов аварийный отказ которых может привести к жертвам или значительным экономическим потерям следует непрерывно или периодически контролировать с целью своевременного получения информации о приближении их к предельному состоянию.
Правила технического обслуживания должны предусматривать:
-контроль температурного режима;
-контроль уровня смазочного масла;
-периодичность замены смазки и данные по ее замене;
-контроль отсутствия течи масла;
- контроль чистоты отверстия отдушины; - контроль и обслуживание системы охлаждения (при необходимости);
- контроль давления масла при смазке под давлением; - рекомендации по контролю и диагностике технического состояния передач и
подшипников по оценке вибрации в процессе эксплуатации редуктора.
Смазочные материалы в машинах применяют с целью уменьшения интенсивности изнашивания снижения сил трения отвода от трущихся поверхностей теплоты и продуктов изнашивания а также для предохранения деталей от коррозии. Снижение сил трения благодаря смазке обеспечивает повышение КПД машин.
В редукторах общего назначения обычно применяется комбинированное смазывание. Смазывание зацеплений производится окунанием в масляную ванну. Для предотвращения протекания масла плоскость разъема покрывают щелочным лаком или жидким стеклом.
Данный редуктор заполняется индустриальным маслом И-Г-А-50 по ГОСТ 20799-88. Стакан шестерни и роликоподшипники заполняют смазкой Литол– 24 ГОСТ 21150-87.
2 Основные требования к параметрам точности для соединений деталей редуктора назначение целесообразных посадок на основе анализа и обоснование сделанного выбора. Требования к параметрам точности детали.
Для передачи нагрузки с колеса на вал применяют посадки с натягом и шпоночные соединения. Посадки с натягом предназначены для получения неподвижных соединений без дополнительного крепления деталей. Для повышения надежности соединения дополнительно используются шпонки. Относительная неподвижность деталей обеспечивается силами сцепления.
Посадки с натягом зубчатых колес выбираются из ряда предпочтительных в соответствии с точностью изготовления деталей. Основными являются посадки (в порядке увеличения натяга): H7p6 H7r6 H7s6 H7s7. Следующие за ними посадки характеризуются большим натягом и применяются при очень больших нагрузках [1 стр 20.].
Посадку H7r6 используют в соединениях без крепежных деталей при небольших нагрузках (втулка в головке шатуна пневматического двигателя) и с крепежными деталями при больших нагрузках (посадка на шпонке зубчатых колес в прокатных станах).
Применение по цилиндрической поверхности посадок с зазором при передаче вращающего момента шпоночным соединением недопустимо т.к. происходит обкатывание поверхностей вала и отверстия и взаимное скольжение что приводит к смятию шероховатостей развальцовыванию отверстия износу контактных поверхностей.
Требования к параметрам точности зубчатого колеса.
Предусмотрено 12 степеней точности более точные колеса имеют меньшие степени точности.
Каждая степень точности регламентирует три нормы — кинематической точности плавности работы и контакта зубьев в передаче а также шесть видов сопряжений и восемь видов допусков на боковой зазор. Возможно комбинирование степеней точности например 8-7-6-Ва (8 – степень кинематической точности 7 – плавности работы 6 – по нормам контакта с видом сопряжения В и видом допуска на боковой зазор).
Нормы точности могут назначаться в зависимости от области применения зубчатого колеса. При этом меняется характер допустимых погрешностей и величина погрешности например для делительных и планетарных передач важна кинематическая точность для высокоскоростных передач главным является плавность работы передачи для тяжело нагруженных тихоходных передач необходимо обеспечить полноту контакта зубьев а для реверсивных отсчетных передач важна величина бокового зазора.
Для каждой нормы точности ГОСТ определяет основные отклонения зубчатого колеса которые влияют на данную норму. Всего стандартом определено 24 погрешности подлежащих контролю. 7 погрешностей определяют кинематическую точность (кинематическая погрешность зубчатого венца F’ir накопленная погрешность шага колеса Fpr накопленная погрешность k шагов Fpkr погрешность обката Fcr колебание длины общей нормали FvWr радиальное биение зубчатого венца Frr колебание измерительного межосевого расстояния за оборот колеса F’’ir). Плавность работы зависит также от 7 погрешностей (местная кинематическая погрешность колеса f’ir циклическая погрешность зубцовой частоты колеса fzz r циклическая погрешность зубчатого колеса fzkr погрешность профиля зуба ffr отклонение шага зацепления fpbr отклонение шага fptr колебание измерительного межосевого расстояния на одном зубе f’’ir). Точность контакта зубьев определяется 4 параметрами (погрешность направления зуба Fr погрешность контактной линии Fkr отклонение осевых шагов по нормали Fpknr суммарное пятно контакта). Боковой зазор в передаче определятся 6 параметрами (дополнительное смещение исходного контура Ehr отклонение длины общей нормали Ewr отклонение средней длины общей нормали Ewmr отклонение толщины зуба Ecr предельные отклонения измерительного межосевого расстояния Ear отклонение размера по роликам Emr).
Технологическая часть.
1Описание типового технологического процесса контроля детали.
Технологический процесс контроля детали — совокупность последовательно выполняемых операций образующих вместе единый процесс проверки параметров детали на соответствие предъявляемым требованиям. Технологический процесс – последовательность технологических операций необходимых для выполнения определенного вида работ. Технологический процесс состоят из рабочих операций которые в свою очередь складываются из рабочих движений (приемов).
Типовой технологический процесс контроля детали типа зубчатое колесо представлен в таблице 3.
Приемочный контроль заготовок на
соответствие чертежам:
- Линейных размеров квалитетов:
Нутромеры микрометры
Измерительные линейки
Отклонения формы и расположения
2 Выбор схем и методов измерения.
Схема контроля – совокупность схемы установки сборочной единицы или детали и связанных с их измерительными базами СК. Для каждого контролируемого параметра необходимо привести со ссылками на соответствующие справочные и методические материалы возможные схемы контроля этих параметров. При этом возможно применение нескольких альтернативных схем для контроля заданных параметров.
Основным требованием при выборе схем контроля является применение таких схем для которых возможна реализация комплексной проверки нескольких параметров с использованием одного СИ.
Наиболее часто используемые схемы контроля параметров качества продукции для деталей типа диск приведены в таблице 6.
Выбор СК основывается на обеспечении заданных показателей процесса ТК при условии минимальных затрат на его реализацию (Р50-609-39-88). К обязательным показателям процесса контроля относят точность измерения достоверность трудоемкость и стоимость контроля. Кроме того учитывают объем полноту периодичность продолжительность и другие показатели контроля.
Применение специальных СК (приспособлений и оборудования) целесообразно при отсутствии стандартизованных и универсальных СК и в случаях если оправдано экономически а также из – за преимуществ в точности надежности и производительности.
Процесс выбора включает следующие основные этапы:
- подготовка исходных данных контроля т. Е. сбор исходных данных об операции объекте контроля и контролируемых параметрах (номинальное значение степень или квалитет точности);
- выбор СК по виду контролируемого параметра по диапазону по способу точности измерения.
Допустимые погрешности измерения (ДПИ) в зависимости от квалитета размера (допуска на изготовление детали) и его номинального значения определяют по ГОСТ 8.051 – 81.
В связи с тем что одну и ту же метрологическую задачу можно решить с помощью различных СИ и СК которые имеют не только разную стоимость .но и разные точность .и другие метрологические показатели дают неодинаковые результаты выбор точности СК имеет первостепенное значение. Точность СК должна быть примерно на порядок выше точности контролируемого параметра изделия.
При сопоставлении ДПИ и погрешности измерения СК должно выполняться условие: ДПИ.
По результатам сопоставления ограничивают номенклатуру СК.
Если контролируемый параметр является окончательным то увеличение погрешности измерения недопустимо. Если же контролируемый параметр является неокончательным и будет подвергаться дальнейшей обработке (изменению) то увеличение ДПИ измерения возможно для тех случаев когда погрешность была меньше установленной для окончательного параметра продукции.
Пределы ДПИ можно увеличить если для использования низкоточных СК введен уменьшенный производственный допуск или если изделия подлежат рассортировке на размерные группы при селективной сборке. Следует помнить что ДПИ по ГОСТ 8.051 – 81 являются наибольшими допускаемыми погрешностями включающими в себя все составляющие зависящие от измерительных средств установочных мер температурных деформаций базирования измерительных усилий субъективности оператора и т. Д.;
-выбор СК по конфигурации детали (габаритным размерам) массе деформируемости детали. Для деформируемых деталей целесообразна реализация бесконтактного метода; либо сопоставление деформируемости детали с допустимым измерительным усилием;
-выбор СК по числу контрольных точек (КТ) количество которых определяют из условия обеспечения контроля каждого контролируемого параметра.
3Метрологический анализ и экспертиза контроле пригодности детали. Выбор согласно РД 50-98-86 универсальных средств измерения линейных размеров.
Контролируемые размеры зубчатого колеса
-штангенциркуль с отсчетом по нониусу 005мм.
а-нутромер индикаторный с ценой деления 0001мм.
б- нутромер индикаторный с ценой деления 001 мм.
а-- нутромер индикаторный с ценой деления 001 мм.
- штангенглубиномер с отсчетом по нониусу 005мм.
На размер 41104 h7 выбираем средство измерения скоба индикаторная (рис. 6):
Рис.6 – Скоба индикаторная СИ-500
Диапазон измерений: 400 – 500 мм; цена деления: 001 мм.
Скобы индикаторные предназначены для линейных измерений. Измерительные поверхности оснащены твердым сплавом. В комплект изделия входят переставные пятки для индикаторных скоб с верхним пределом измерения: до 100мм - 1шт от 100 до 700мм - 2шт свыше 700мм - 3шт.
Данной средство измерения можно заменить на более современное. В нашем случае заменяем скобу индикаторную на скобу микрометрическую цифровую TESA (рис. 7).
Рис.7 – Скоба микрометрическая
Диапазон измерений: 400 – 500 мм; цена деления: 0001 мм; точность: ±0009.
Цифровые микрометрические скобы TESA для больших размеров (с вольфрамовым покрытием измерительных поверхностей). Данная модель доступна с нониусом или цифровым микрометром а также с часовым индикатором. В комплект входят четыре сменных стержня 0-100 мм которые также доступны отдельно.
На размеры 180 h11 60 h11 выбираем средство измерения – микрометр гладкий с величиной отсчета 001 мм.(рис.8).
Рис.8 – Микрометр гладкий
Диапазон измерений: 50 – 75 мм; 150 - 200 мм.; цена деления: 001 мм; предел (±) допускаемой погрешности: 001 мм.
Микрометры гладкие типа МК предназначены для измерения наружных размеров изделий. Измерительные поверхности оснащены твердым сплавом. Для установки микрометров в начальное положение предназначены установочные меры. Приборы с интервалом измерений не более 25 мм (от 50 до 300 мм) комплектуются одной установочной мерой а с диапазоном измерений 100 мм (свыше 300 мм) комплектуются двумя установочными мерами и четырьмя сменными пятками. Скобы микрометров оснащены термоизолирующими накладками и обеспечивают повышенную жесткость. Цена деления 001мм. Отсчет - по шкалам стебля и барабана.
Данной средство измерения можно заменить на более современное. В нашем случае заменяем микрометр гладкий на микрометр гладкий электронный типа МКЦ (рис.9).
Рис.9 - Микрометр гладкий электронный типа МКЦ 125.
Диапазон измерений: 50 – 75 мм; 150 - 200 мм; цена деления: 0001 мм; предел (±) допускаемой погрешности: 0003 мм.
Микрометры гладкие электронные типа МКЦ предназначены для измерения наружных размеров изделий. Микрометры оснащены электронным цифровым отсчетным устройством более удобным и быстрым при считывании показаний а также позволяющим проводить относительные измерения за счет установки нулевого значения на любом размере в диапазоне измерений. Функции электронного блока: кнопочное управление метрическая и дюймовая система исчисления кнопка выключенияавтоматическое отключение установка абсолютного нуля абсолютные и относительные измерения установка пределов допуска и классифицированное измерение функция удержания данных на экране разъем для вывода данных. Измерительные поверхности микрометров оснащены твердым сплавом. Укомплектованы установочной меройдвумя. Цена деления 0001 мм000005".
На размеры 80 345H14 выбираем средство измерения штангенциркуль (рис. 10):
Рис. 10 – Штангенциркуль
Диапазон измерений: 0 – 500 мм; цена деления: 005 мм; предел (±) допускаемой погрешности: 006 мм.
Штангенциркули с отсчетом по нониусу типа ШЦ-1 предназначены для наружных и внутренних измерений а также для измерения глубин. Имеют двойную шкалу: в миллиметрах и дюймах. Имеют губки наружные для измерения наружных размеров и кромочные для измерения внутренних размеров а также встроенный глубиномер. Нониус регулируемый. Длина губок стандартная.
Данной средство измерения можно заменить на более современное. В нашем случае заменяем штангенциркуль на штангенциркуль типа ШЦЦ (рис. 11).
Рис.11 - Штангенциркуль типа ШЦЦ-1-500 PRO.
Диапазон измерений: 0 – 500 мм; цена деления: 001 мм; вылет нижних губок: 60 мм; предел (±) допускаемой погрешности: 004 мм.
Штангенциркули ШЦЦ-1 Pro предназначены для особенно требовательных заказчиков использующих инструмент в экстремальных условиях. Он имеет защитное исполнение предохраняющее инструмент от воздействия среды. IP65 предотвращает проникновение пыли металлических частиц капель воды или СОЖ внутрь электронного блока благодаря эффективной инкапсуляции основных элементов. Цифровой блок предоставляет возможность установки нуля в любом положении и выбора системы исчисления ммдюйм.
На размер 140Н7 выбираем средство измерения нутромер индикаторный (рис. 7):
Рис.12 – Нутромер индикаторный.
Диапазон измерений: 100 – 150 мм; наибольшая глубина измерения: 150 мм; цена деления: 0001 мм; предел (±) допускаемой погрешности: 0004 мм.
Нутромеры индикаторные повышенной точности типа НИ-ПТ предназначены для измерения внутренних размеров изделий двухточечным контактом с измеряемыми поверхностями относительным методом. Отсчетное устройство - индикатор часового типа. На измерение требуемого размера нутромер настраивается с помощью одного из входящих в комплект сменных стержней. Настройка производится по аттестованным кольцам или блокам концевых мер длины с боковиками
Данной средство измерения можно заменить на более современное. В нашем случае заменяем нутромер индикаторный на нутромер трехточечный электронный типа НМТЦ (рис. 13).
Рис.13 - Нутромер трехточечный электронный типа НМТЦ
Диапазон измерений: 125 – 150 мм; наибольшая глубина измерения: 114 мм; цена деления: 0001 мм; предел (±) допускаемой погрешности: 0005 мм; установочное кольцо: 87мм; удлинитель: 150мм.
Нутромеры трехточечные электронные типа НМТЦ с реализованной с помощью цифрового индикатора системы считывания значений. Предназначены для особо точных измерений проходных глухих отверстий центрирующих кромок. Головка - самоцентрирующаяся. Измерительные щупы упрочнены твердым сплавом. Могут применяться для абсолютных и относительных измерений. В комплект поставки входят удлинитель установочное кольцо алюминиевый кейс.
На размеры 36 50H14 выбираем средство измерения нутромер индикаторный (рис. 14):
Рис.14 – Нутромер индикаторный.
Диапазон измерений: 18 – 50 мм; наибольшая глубина измерения: 150 мм; цена деления: 001 мм; предел (±) допускаемой погрешности: 0015 мм.
Нутромеры индикаторные типа НИ предназначены для измерения внутренних размеров изделий двухточечным контактом с измеряемыми поверхностями относительным методом. Отсчетное устройство - индикатор часового типа. На измерение требуемого размера нутромер настраивается с помощью одного из входящих в комплект сменных стержней. Настройка производится по аттестованным кольцам или блокам концевых мер длины с боковиками.
Данной средство измерения можно заменить на более современное. В нашем случае заменяем нутромер индикаторный на нутромер для внутренних измерений типа НВЦ (рис. 15).
Рис.15 - Нутромер для внутренних измерений типа НВЦ.
Диапазон измерений: 20 – 50 мм; наибольшая глубина измерения: 80 мм; цена деления: 0005 мм; предел (±) допускаемой погрешности: 003 мм.
Нутромер для внутренних измерений типа НВЦ применяется для внутреннего измерения в двух точках контакта методом сравнения. Нутромер оказывается незаменимым инструментом там где необходимо произвести измерения в труднодоступных участках изделия. Прибором можно измерять сквозные и глухие отверстия пазы и канавки а также выемки с плоскими параллельными поверхностями. В качестве измерительных щупов используются два остроконечных рычага. В качестве отсчетного устройства в нутромере применяется электронный цифровой индикатор. Электронный блок обладает набором функций в т.ч. даёт возможность производить абсолютные и относительные измерения и др.
На размер 20 1484Н14 выбираем средство измерения штангенглубиномер (рис.16)
Рис.16 - Штангенглубиномер
Диапазон измерений 0-250 мм.
В отличие отштангенциркуля штанга глубиномера не имеет губок и измерительными поверхностями являются торцы штанги и основания. Точность измерений штангенглубиномером с обычнымнониусомтакая же как и штангенциркулем — 01 мм.
4 Определение согласно ГОСТ 8.051-81 параметров разбраковки «m n c» при приемочном контроле детали.
Предельные значения параметров разбраковки «m n c» определяем по [3 стр.27
Примечание: При определении параметров т п и с рекомендуется принимать Амет = 16 % для квалитетов 2 – 7; Амет = 12 % - для квалитетов 8 9; Амет = 10 % - для квалитетов 10 и грубее.
где т — часть измеренных деталей имеющих размеры выходящие за предельные размеры принята в числе годных (неправильно принятые);
п — часть деталей имеющих размеры не превышающие предельных размеров забракованы (неправильно забракованные);
с—вероятностная предельная величина выхода размера за предельные размеры у неправильно принятых деталей.
Размер ø411.04h7(-0.063)
Допускаемая погрешность =0018 мм. Относительная погрешность измерения: Амет=16%
Вероятное количество неправильно принятых деталей: m=5.0%
Вероятное количество неправильно забракованных деталей: n=7.8%
Вероятностная величина выхода размера за границы допуска неправильно принятых деталей: С=T·CIT=0063·025=0016 мм.
Верхнее отклонение для параметра m: 0+0018=0018 мм.
Нижнее отклонение для параметра m: -0063-0018= -0081 мм.
Верхнее отклонение для параметра n: 0-0018= -0018 мм.
Нижнее отклонение для параметра n: -0063+0018= -0045 мм.
Рис. 17. Определение приемочных границ для размера 411.04h7( -0.063) .
Среди годных деталей может оказаться до 5.0% неправильно принятых деталей с
предельными отклонениями и до 7.8% деталей могут быть неправильно
забракованных с предельными отклонениями .
Размер ø180h11(-0.25)
Допускаемая погрешность =005 мм. Относительная погрешность измерения: Амет=10%
Вероятное количество неправильно принятых деталей: m=3.1%
Вероятное количество неправильно забракованных деталей: n=4.5%
Вероятностная величина выхода размера за границы допуска неправильно принятых деталей: С=T·CIT=025·014=0035 мм.
Верхнее отклонение для параметра m: 0+005=005 мм.
Нижнее отклонение для параметра m: -025-005= -03 мм.
Верхнее отклонение для параметра n: 0-005= -005 мм.
Нижнее отклонение для параметра n: -025+005= -02 мм.
Рис.18 - Определение приемочных границ для размера 180h11( -0.25) .
Среди годных деталей может оказаться до 31% неправильно принятых деталей с
предельными отклонениями и до 45% деталей могут быть неправильно
Размер 60h11(-0.19)
Допускаемая погрешность =004 мм. Относительная погрешность измерения: Амет=10%
Вероятностная величина выхода размера за границы допуска неправильно принятых деталей: С=T·CIT=019·014=0027 мм.
Верхнее отклонение для параметра m: 0+004=004 мм.
Нижнее отклонение для параметра m: -019-004= -023 мм.
Верхнее отклонение для параметра n: 0-004= -004 мм.
Нижнее отклонение для параметра n: -019+004= -015 мм.
Рис.19 - Определение приемочных границ для размера 60h14( -0.19)
Размер 80h14(-0.71)
Допускаемая погрешность =016 мм. Относительная погрешность измерения: Амет=10%
Вероятностная величина выхода размера за границы допуска неправильно принятых деталей: С=T·CIT=071·014=0099 мм.
Верхнее отклонение для параметра m: 0+016=016 мм.
Нижнее отклонение для параметра m: -071-016= -087 мм.
Верхнее отклонение для параметра n: 0-016= -016 мм.
Нижнее отклонение для параметра n: -019+016= -055 мм.
Рис.20 - Определение приемочных границ для размера 80h14( -0.71)
Размер ø140Н7(+004)
Допускаемая погрешность =0012 мм. Относительная погрешность измерения: Амет=16%
Вероятностная величина выхода размера за границы допуска неправильно принятых деталей: С=T·CIT=004·025=001 мм.
Верхнее отклонение для параметра m: 004+0012=0052 мм.
Нижнее отклонение для параметра m: 0-0012= -0012 мм.
Верхнее отклонение для параметра n: 004-0012= 0028 мм.
Нижнее отклонение для параметра n: 0+0012= 0012 мм.
Рис.20 - Определение приемочных границ для размера ø140Н7(+004)
Допускаемая погрешность =0016 мм.
Относительная погрешность измерения: Амет=12%
Вероятное количество неправильно принятых деталей: m=375%
Вероятное количество неправильно забракованных деталей: n=54%
Вероятностная величина выхода размера за границы допуска неправильно принятых деталей: С=T·CIT=062·017=0105 мм.
Верхнее отклонение для параметра m: 0062+0016=0078 мм.
Нижнее отклонение для параметра m: -0062-0016= -0078 мм.
Верхнее отклонение для параметра n: 0062-0016= 0046 мм.
Нижнее отклонение для параметра n: -0062+0016= -0046 мм.
Рис.21 - Определение приемочных границ для размера 36Н7(±0062)
Среди годных деталей может оказаться до 375% неправильно принятых деталей с
предельными отклонениями и до 54% деталей могут быть неправильно
Размер ø345Н14(+14)
Допускаемая погрешность =028 мм.
Относительная погрешность измерения: Амет=10%
Вероятное количество неправильно принятых деталей: m=31%
Вероятное количество неправильно забракованных деталей: n=45%
Вероятностная величина выхода размера за границы допуска неправильно принятых деталей: С=T·CIT=14·014=0196 мм.
Верхнее отклонение для параметра m: 14+028=168 мм.
Нижнее отклонение для параметра m: 0-028= -028 мм.
Верхнее отклонение для параметра n: 14-028= 112 мм.
Нижнее отклонение для параметра n: 0+028= 028 мм.
Рис.22 - Определение приемочных границ для размера ø345Н14(+14)
Размер ø50Н14(+062)
Допускаемая погрешность =014 мм.
Вероятностная величина выхода размера за границы допуска неправильно принятых деталей: С=T·CIT=062·014=0087 мм.
Верхнее отклонение для параметра m: 062+014=076 мм.
Нижнее отклонение для параметра m: 0-014= -014 мм.
Верхнее отклонение для параметра n: 062-014= 048 мм.
Нижнее отклонение для параметра n: 0+014= 014 мм.
Рис.23 - Определение приемочных границ для размера ø50Н14(+062)
Допускаемая погрешность =012 мм.
Вероятностная величина выхода размера за границы допуска неправильно принятых деталей: С=T·CIT=052·014=0073 мм.
Верхнее отклонение для параметра m: 052+012=064 мм.
Нижнее отклонение для параметра m: 0-012= -012 мм.
Верхнее отклонение для параметра n: 052-012= 04 мм.
Нижнее отклонение для параметра n: 0+012= 012 мм.
Рис.24 - Определение приемочных границ для размера ø20Н14(+052)
Размер 1484Н14(+10)
Допускаемая погрешность =02 мм.
Вероятностная величина выхода размера за границы допуска неправильно принятых деталей: С=T·CIT=10·014=014 мм.
Верхнее отклонение для параметра m: 10+02=12 мм.
Нижнее отклонение для параметра m: 0-02= -02 мм.
Верхнее отклонение для параметра n: 10-02= 08 мм.
Нижнее отклонение для параметра n: 0+02= 02 мм.
Рис.25 - Определение приемочных границ для размера ø1484Н14(+10)
5 Выбор средств контроля шероховатости поверхностей отклонений формы и расположения поверхностей детали а также других параметров заданных чертежом.
Измерения шероховатости поверхности.
Портативный измеритель шероховатости TIME3221 (рис. 26) является актуальной разработкой 2014 г. компании TIME Group Inc. Устройство снабжено выносным датчиком и может применяться как в условиях научных отделов и лабораторий так и на местах производства и в полевых условиях.
Измеритель шероховатости TIME3221 выполняет вычисления параметров в точном соответствии с выбранной методикой и отображает на дисплее с высокой точностью график исследуемого профиля и все необходимые данные.
Полученные результаты можно передать на компьютер или сохранить в интегрированной памяти устройства.
Профилометр работает по следующему принципу: для измерения шероховатости какого-либо элемента на его поверхность помещают датчик с иглой который определяет неровность поверхности при перемещении. После того как информация о неровности получена она обрабатывается микропроцессором и выводится на экран прибора в виде заданных параметров.
Основные характеристики измерителя шероховатости модели TIME3221:
-способность к измерению 40 параметров профиля в том числе Ra Rt Rp Rv Rz Rc Rq Rsk Rku RPc и др.;
-проведение измерений с высокой точностью;
-совместимость устройства с действующими международными стандартами: DIN ISO JIS а также
-индикация графика профиля и параметров среды;
-возможность подключения к компьютеру или принтеру через RS232 и
-языки: английский и китайский;
- автоматическое или ручное отключение питания.
Рис. 26. Измеритель шероховатости TIME 3221.
Технические характеристики TIME 3221.
Диапазон измерения иглы датчика мкм
Радиус измерительного пера мкм
Материал измерительного пера
Измерительное усилие мН
Угол измерительного пера град.
Максимальная длина прохода ммдюйм
8; 025; 08; 25; авто
Скорость перемещения ммс
Возвращение = 1 мм с
Количество длин оценки
от 1 до 5 длин (выбираемая)
Встроенный ионно-литиевый (LI-ion)
Диапазон рабочих температур °С
Относительная влажность %
5.4 x 75 x 53 (осн. блок)
0.5 x 25.5 x 28.5 (измер. элемент)
Измерения отклонений формы и расположения поверхностей зубчатого колеса а также других параметров заданных чертежом изделия.
Зубоизмерительные машины WGT-350 и WGT-500 (Германия) (рис. 27) разработаны на базе хорошо зарекомендовавшей себя технологии которая усилиями инженеров фирмы получила новое развитие. Сегодня предлагаются универсальные простые в использовании и компактные измерительные машины с широкими техническими возможностями которые способны решать любые задачи по измерению зубчатых колес диаметром до 600 мм. Надежность технологии WENZEL гарантирует пользователю отличные результаты с наименьшими затратами. Простое и удобное программное обеспечение позволяет работать на машине без длительного обучения. Программное обеспечение составлено и согласовано со специалистами фирмы WELTER.
Возможность измерения:
-цилиндрические зубчатые колеса всех видов;
-конические зубчатые колеса всех видов;
-червяки и червячные колеса;
- валы (размер форма положение);
- распределительные валы;
- кулачки с наружным и внутренним рабочим контуром;
- неизвестные контуры.
Характеристики и компоненты машины:
- трехкоординатная измерительная система;
- аэростатические опоры по всем осям;
- базовая плита и все оси машины изготовлены из натурального черного гранита;
- эргономичное рабочее место;
- специально разработанная для зубоизмерения система управления;
- автоматическая смена измерительных щупов (опция);
- короткое время измерения при высокой точности;
- широкий рабочий диапазон;
- большой пакет программного обеспечения.
Рис. 27. Зубоизмерительная машина WGT-350.
Технические характеристики WGT-350.
Диаметр измеряемого колеса мм:
- с наружным зацеплением;
с внутренним зацеплением.
Угол наклона зуба град.
Высота зубчатого венца мм
в соответствии с нормами
VDIVDE 26122613 группа I
Перемещение по осям мм:
Электрооборудование Гц
Потребляемая мощность ВА
Габаритные размеры мм
6 Выбор средств измерения твердости детали.
Для контроля и измерения твердости выбираем твердомер ТН170 (рис. 28) производитель - Time Group.
Компактный твердомер TH170 для измерения твердости металлов оборудован коммуникационным портом USB программным обеспечением и возможностью программной калибровки.
Для удобства использования в условиях недостаточной освещенности твердомер имеет подсветку экрана. Имеется функция автоотключения.
Особенности твердомера TH170:
-встроенное ударное устройство типа D;
-связь с персональным компьютером через интерфейс
-автоматическое определение пространственного положения ударного устройства;
-встроенная память на 270 усредненных результатов в 9 групповых файлах;
-возможность задания верхней и нижней границ измерения;
-функция автоотключения;
-для удобства работы в неосвещенных местах имеется подсветка ЖК дисплея;
-твердомер ТН170 имеет функцию программной калибровки;
-индикация степени разрядки источника питания;
- широкий диапазон измерений в числах HLD и непосредственное отображение преобразованных значений в числах твердости HB HRB HRC HV
-диапазон измерений по большинству металлов;
-электрическое питание от элементов типа ААА 1.5 В;
-программа обработки результатов на ПК (на заказ ).
Цена прибора: 54500 руб. согласно [5].
Рис. 28. Твердомер TH 170.
Технические характеристики TH 170.
Стандартное ударное устройство
HLD HB HRC HRB HV HS
Пространственное положение прибора при
Абсолютная погрешность измерений
единиц HLD ± 6 (760 ± 30 HLD)
единиц HLD ± 10 (530 ± 40 HLD)
Количество результатов измерений в памяти
0 усредненных результатов в 9 групповых
Вывод результатов измерений
Минимальная шероховатость измеряемой
Максимальная твердость измеряемой детали
5 единиц по Виккерсу
Минимальный радиус кривизны измеряемой
R = 50мм (при использовании опорного
поверхности (выпуклая вогнутая) мм
Время непрерывной работы час
Электрическое питание
элементы питания типа ААА 1.5 (2 шт.) В
Масса электронного блока гр.
7 Составление карты контроля.
Карта контроля оформлена согласно ГОСТ 3.1502-85. В ней указаны основные операции контроля контролируемые размеры средства измерения применяемое оборудование. Карта составлена для зубчатого колеса.
8 Контроль правильности сборки редуктора испытания редуктора.
Контроль качества сборки изделий.
При проектировании технологических процессов общей и узловой сборки важное место занимает технический контроль качества производимой продукции. Качество обеспечивается предупреждением и своевременным выявлением брака продукции на всех этапах производственного процесса. Профилактический контроль направлен на проверку комплектующих изделий полуфабрикатов и деталей смежных производств на проверку сборочного оборудования и оснастки а также на систематическую проверку правильности протекания технологического процесса сборки. Качество продукции в сборочных цехах контролируют рабочие наладчики оборудования и мастера участков. Меньший объем работ выполняют контролеры производя промежуточный и окончательный контроль. В маршрутной технологии указывают операции контроля и элементы контроля включаемые в сборочные операции.
При узловой и общей сборке проверяют:
) наличие необходимых деталей в собранных соединениях (выполняют осмотром);
) правильность положения сопрягаемых деталей и узлов (выполняют осмотром);
) зазоры в собранных сопряжениях (щупом);
) точность взаимного положения сопряженных деталей (на радиальное и осевое биение и др. производят в контрольных приспособлениях);
) герметичность соединения в специальных приспособлениях и плотность прилегания поверхностей деталей на краску в процессе сборки;
) затяжку резьбовых соединений плотность и качество постановки заклепок плотность вальцовочных и других соединений;
) размеры заданные в сборочных чертежах;
) выполнение специальных требований (уравновешенности узлов вращения подгонки по массе и статическому моменту проверку щупом производят в процессе сборки и после ее окончания);
)выполнение параметров собранных изделий и их составных частей (производительности и развиваемого напора насосов точности делительных механизмов качества контакта в электрических соединениях и др.);
)внешний вид собранных изделий (отсутствие повреждений деталей загрязнений и других дефектов которые могут возникнуть в процессе сборки).
В функцию контроля входит также проверка предписанной последовательности выполнения сборочных переходов (порядок затяжки резьбовых соединений последовательность наложения сварных швов и др.) и проверка обязательного выполнения вспомогательных операций (промывки и очистки сопрягаемых деталей промывки трубопроводов и др.). Задача проектирования технологии сборки связана с выбором организационно - технической формы и средств контроля.
Средства контроля выбирают с учетом их метрологических характеристик (пределов и точности измерения) конструктивных особенностей (габаритных размеров массы) экономических соображений а также с учетом улучшения условий труда контролеров.
При проектировании операций контроля исходными данными являются точность контроля (допустимая погрешность контроля обычно не превышает 20% допуска на контролируемую величину) и его производительность. Технолог устанавливает объект метод и средства контроля. Он дает техническое задание на конструирование специальных контрольно-измерительных инструментов и приспособлений; выбирает схему контрольного приспособления с учетом наименьшей себестоимости выполнения контрольной операции.
На контрольные операции составляют инструкционные карты в которых подробно указывают метод и последовательность контроля используемые средства контроля.
Испытание собранных изделий.
Испытание собранных изделий - заключительная контрольная операция качества их изготовления. Машины испытывают в условиях приближающихся к эксплуатационным. Все виды испытаний можно свести к приемочным контрольным и специальным.
При приемочных испытаниях выявляют фактические эксплуатационные характеристики машины (точность производительность мощность затраты энергии и т. п.) а также правильность работы различных механизмов и устройств машины.
Контрольным испытаниям подвергают изделия у которых ранее были обнаружены дефекты. При особо высоких требованиях к изделиям их подвергают после сборки обкатке и испытывают. Затем разбирают (частично или полностью) проверяют состояние деталей вторично собирают и подвергают кратковременным контрольным испытаниям.
Испытания ведут на специальных стендах.
Примеры испытательных стендов для испытания и обкатки редукторов представлены на рисунке 29.
При необходимости испытания проводятся в соответствии со стандартом API или DIN. Стенды оборудованы системой охлаждения фильтрации масла и безопасным баком для хранения масла. Уровни вибрации каждого вала определяются отдельно. Измеряется уровень шума. Определяется расход масла при номинальном давлении. Эффективность может быть измерена путем определения крутящего момента или калибровкой электродвигателя и вспомогательных устройств. При проведении необходимых испытаний используются надежное и проверенное измерительное оборудование такое как датчики уровня вибрации и температуры.
Рис. 29. Стенды для испытаний редукторов BCSA (Франция).
Конструкторская часть
1Обзор и анализ научно-технической информации по контрольно-измерительным приспособлениям (КИП).
Контрольные приспособления - специальные производственные средства измерения представляющие собой конструктивное сочетание базирующих зажимных и измерительных устройств.
Контрольные приспособления предназначены для проверки точности выполнения размеров и технических требований на изготовление деталей и узлов машин.
Современное производство характеризуется все возрастающими требованиями к точности геометрических параметров изготавливаемых деталей. Проверка точности этих параметров требует применения более совершенных средств контроля. Контроль точности выполняется как на промежуточных этапах обработки (операционный контроль) так и на этапе окончательной приемки продукции (окончательный контроль). Многие детали имеют сложную конструктивную форму и малые допуски. Поэтому для их контроля часто применяют контрольно - измерительные приспособления (КИП) которые являются специальными производственными средствами измерения и контроля представляющие собой конструктивное сочетание базирующих зажимных и измерительных устройств. Их основное назначение заключается в измерении погрешности геометрических параметров деталей и сборочных единиц при их изготовлении на этапах промежуточного и окончательного контроля.
С помощью КИП проверяют:
- линейные размеры: наружные и внутренние диаметры высоту ширину глубину выступы длину различных элементов деталей которые невозможно либо нецелесообразно измерять предельными калибрами или универсальными измерительными средствами;
- точность формы поверхностей;
-точность расположения поверхностей;
- параметры зубчатых колес резьбовых соединений фасонных поверхностей и деталей со сложным профилем.
Также с помощью КИП можно:
- выполнять активный контроль размеров заготовок непосредственно при обработке на станках;
- проверять одновременно несколько параметров деталей; - производить сортировку деталей по точности параметров на группы в пределах заданных допуска;
- настраивать режущий инструмент на заданный размер и осуществлять контроль
размеров заготовок при обработке на станках с ЧПУ.
Приспособления могут быть классифицированы:
а) по габаритам и условиям работы (стационарные и накладные или переносные одномерные и многомерные);
б) по принципу работы (со шкальными и бесшкальными измерениями);
в) по технологическому назначению (для приемочного контроля обработанных деталей контроля правильности обработки деталей на станках и воздействия на технологический процесс контроля правильности наладки станка и протекания процесса сборки).
На заводах и в технической литературе КИП принято классифицировать по следующим признакам.
-иверсальные КИП – используются для контроля заданных параметров заготовок или деталей различной конфигурации в определенном диапазоне размеров.
-специализированные КИП – имеют ограниченную универсальность и используются для контроля параметров однотипных заготовок или деталей принадлежащих к определенной классифицированной группе или классу. При контроле каждого наименования заготовки приспособление переналаживается.
-специальные КИП – используются для контроля параметра или параметров заготовок или деталей одного наименования.
) По виду контролируемых геометрических параметров заготовок или деталей приспособления можно классифицировать в соответствии со схемой представленной ниже.
) По уровню механизации и автоматизации КИП разделяют на ручные
механизированные автоматизированные и автотические.
Ручные КИП – контроль осуществляется непосредственно человеком. Уровень
механизации и автоматизации нулевой.
Механизированные КИП – контроль осуществляется с разной степенью участия
человека. Уровень механизации и автоматизации может быть малый средний и большой.
Автоматизированные КИП – контроль осуществляется с частичным непосредственным
участием человека. Уровень механизации и автоматизации высокий.
Автоматические КИП – контроль осуществляется без непосредственного участия
человека. Уровень автоматизации и механизации полный.
Чем выше уровень автоматизации и механизации тем меньше доля ручного труда при
этом увеличивается объективность и производительность контроля.
) По числу изменяемых параметров: одномерные и многомерные.
) По способу измерения: статические кинематические и динамические.
Под статическими понимают такие способы измерения при которых ни измеряемая
деталь ни элементы измерительного устройства не совершают во время измерения каких –
При кинематических способах измеряемая деталь или измерительный элемент
приспособления перемещаются с малой и практически постоянной скоростью во время
2 Анализ исходных данных для проектирования КИП. Основные требования предъявляемые к приспособлению.
Проектированию специальных средств технологического оснащения для механосборочного производства предшествует этап разработки рационального варианта процесса или операции ТК.
В разделе по ТК курсового и дипломного проектов по технологии машиностроения может проектироваться единичный или групповой технологический процесс контроля детали или деталей на которые разрабатываются технологические процессы механической обработки и сборки сборочных единиц или изделий в условиях мелкосерийного серийного или массового производства на базе использования универсальных специальных и автоматических средств измерения и контроля.
При анализе исходных данных необходимо осветить следующие вопросы:
-вид объекта контроля (деталь сборочная единица технологический процесс);
-вид контролируемого признака (геометрические параметры физико - химические параметры внешние и внутренние дефекты);
- номинальные значения и допуски на контролируемые параметры; - допускаемая погрешность измерения (ДПИ);
- возможные и допустимые дефекты;
- технологичность конструкции при ТК (конструктивные особенности: конфигурация поверхностей повреждаемость или деформируемость при контроле масса и транспортабельность особые требования к объекту контроля особые требования к рабочему месту контролера по температурному режиму освещенности
контролепригодности и т. п. особые требования к СК и т. п.);
- измерительная база и обеспечение единства конструкторских технологических и измерительных баз;
- существующие и перспективные методы средства и процессы контроля возможность и целесообразность их применения для заданного объекта контроля при определенном типе производства;
- производственные инструкции на проведение контроля.
Основные требования к КИП.
Основными требованиями предъявляемыми к КИП являются следующие:
- обеспечение оптимальной точности и производительное контрольных операций; - удобство в эксплуатации; - технологичность в изготовлении; - износоустойчивость;
- экономическая целесообразность.
3 Описание конструкции КИП его принцип действия.
Биение торцовых и периферийных рабочих поверхностей зубчатых колес проверяют на контрольном приспособлении с вращающейся оправкой. Проверяемое колесо устанавливают на оправку 4 на котором он центрируется оправкой. Оправка 4 закрепляется с натягом в основании 2 . Биение верхнего торца проверяют измерительной головкой (ИГ) 1. Эта ИГ 1 установлена на подвижной планке 5 монтируемой на стойке основания 3. Рабочее положение планки с ИГ 1 регулируется болтом 7 и гайкой 6. Биение нижнего торца проверяют также ИГ которая устанавливается также как ИГ для проверки биения верхнего торца.
Для определения биения рабочих поверхностей колеса его вращают на оправке 4. По разности показаний ИГ определяют биение рабочих поверхностей зубчатого колеса относительно оси отверстия.
Рис. 30 - Схема контроля конструкции КИП.
При выполнении курсовой работы было проведено метрологическое обеспечение современного среднесерийного машиностроительного производства по изготовлению изделия «Редуктор цилиндрический одноступенчатый».
Впояснительной записке приведено служебное назначение и описание работы редуктора проведен метрологический анализ обзор научно - технической и интернет - информации по тематике работы и выбраны наиболее эффективные средства контроля шероховатости твердости. Назначены параметры разбраковки и определены приемочные границы для различных размеров детали зубчатое колесо.
Вграфической части работы представлены чертежи: сборочный чертеж редуктора детали зубчатое колесо 3D - модель детали контрольно-измерительное приспособление.
Вработе представлена карта технологического контроля на зубчатое колесо.
На основании разработанной документации имеется возможность сформулировать рекомендации по изготовлению контрольно-измерительного приспособления для контроля торцевого биения детали зубчатое колесо которые позволят увеличить производительность контроля за счет увеличения его скорости и качества.
Результаты данной курсовой работы могут быть полезны инженерно-техническим работникам современных машиностроительных предприятий.
Аверьянов И.Н. Болотин А.Н. Прокофьев М.А.Проектирование и расчет станочных и контрольно-измерительных приспособлений в курсовых и дипломных проектах. Издательство: РГАТА Страниц: 220 с.: ил. Год: 2010.
Анухин В.И. Допуски и посадки. Выбор и расчет указание на чертежах: СП-б: Издательство СПбГТУ 2010 - 219 с. ил.
Димов Ю.В. Метрология стандартизация и сертификация: Учебник для студентов технических специальностей: Издательство «Питер» 2012 - 432с. ил.
Палей М.А. и др. Единая система допусков и посадок: Справочник: В 2 т. Т.2. М: Издательство стандартов 2008. – 208 с. ил.
Редуктор.cdw

Общие допуски по ГОСТ 30893.1:
Наружные поверхности редуктора покрыть атмосферостойким
покрытием Эмаль МЛ 152 зеленая
Допускается опорные поверхности редуктора не окрашивать.
Для смазки подшипников применять Литол-24 ГОСТ 21150-87.
л. масла И-Г-А 50 ГОСТ 20799-88.
Плоскости разъема покрыть тонким слоем герметика УТ-34
ГОСТ 24285-80 при окончательной сборке.
Контрольное приспособление для проверки торцевого биения _ КСИН.401131.002.spw

ИжГТУ им.Калашникова
Индикатор 2ИГГОСТ18833-73
Гайка-барашекМ16ГОСТ3032-76
Болт М16ГОСТ 7798-70
Зубчатое колесо.cdw

Сталь40Х ГОСТ4543-71
Твердость поверхности зубьев HRC 45 50.
Общие допуски по ГОСТ30893.1:
Остальные технические требования по ГОСТ 1643-81.
Неуказанные радиусы скругления 0
Острые кромки притупить 0
Спецификация.spw

Кольцо маслоудерживающее1
Кольцо маслоудерживающее2
Крышка подшипника глухая
Крышка подшипника сквозная
Подшипник7318ГОСТ27365
Подшипник7614ГОСТ333-79
Болт М14 ГОСТ7798-70
Гайка М14 ГОСТ5915-70
Шайба 14 ГОСТ6402-70
Болт М10 ГОСТ7798-70
Гайка М10 ГОСТ5915-70
Шайба 10 ГОСТ6402-70
Прокладка ГОСТ15180-86
Шпонка20х12 ГОСТ23360-78
Шпонка36х20 ГОСТ23360-78
Гайка М56х4ГОСТ5915-70
Рекомендуемые чертежи
- 22.05.2015
- 10.03.2024
- 24.01.2023
- 24.01.2023